VACUTAP® VV® On-load Tap-changer Installation & Commissioning Instructions PDF
Document Details
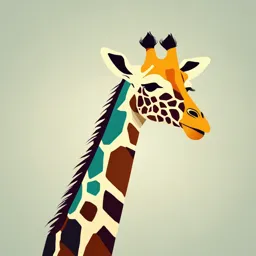
Uploaded by BestSellingBeige
null
Maschinenfabrik Reinhausen
Tags
Related
- OILTAP® M On-load Tap-Changer Installation & Commissioning Instructions PDF
- On-Load Tap Changer Type T Operating Instructions PDF
- OILTAP® V Installation and Commissioning Instructions PDF
- Technical Data On-Load Tap Changer Type H PDF
- Technical Data - TD 107/01 On-Load Tap Changer Type H PDF
- VACUTAP VR On-load Tap-Changer Installation & Commissioning Instructions PDF
Summary
This document provides comprehensive installation and commissioning instructions for the VACUTAP® VV® on-load tap-changer. Detailed procedures are included for various installation scenarios and equipment configurations, ensuring safe and proper operation of the device.
Full Transcript
THE POWER BEHIND POWER. Installation and commissioning instructions VACUTAP® VV®. On-load tap-changer 4349322/04 EN © All rights reserved by Maschinenfabrik Reinhausen Dissemination and reproduction of this document and use and disclosure of its content are strictly prohibited unless expressly pe...
THE POWER BEHIND POWER. Installation and commissioning instructions VACUTAP® VV®. On-load tap-changer 4349322/04 EN © All rights reserved by Maschinenfabrik Reinhausen Dissemination and reproduction of this document and use and disclosure of its content are strictly prohibited unless expressly permitted. Infringements will result in liability for compensation. All rights reserved in the event of the granting of patents, utility models or designs. The product may have been altered since this document was published. We reserve the right to change the technical data, design and scope of supply. Generally the information provided and agreements made when processing the individual quotations and orders are binding. The product is delivered in accordance with MR's technical specifications, which are based on information provided by the customer. The customer has a duty of care to ensure the compatibility of the specified product with the customer's planned scope of application. The original operating instructions were written in German. Table of contents 1 Introduction................................................. 5 5.2 Installing the on-load tap-changer in the 1.1 Manufacturer................................................................. 5 transformer (standard version).............................. 33 1.2 Completeness............................................................... 5 5.2.1 Fastening on-load tap-changer to 1.3 Safekeeping................................................................... 5 transformer cover......................................... 33 1.4 Notation conventions.................................................. 6 5.2.2 Connecting the tap winding and on-load 1.4.1 Hazard communication system....................... 6 tap-changer take-off lead............................. 38 1.4.2 Information system........................................... 6 5.2.3 Performing transformer ratio test before 1.4.3 Instruction system............................................. 6 drying............................................................. 40 5.2.4 Performing DC resistance measurement 2 Safety........................................................... 8 on transformer.............................................. 40 2.1 Appropriate use............................................................ 8 5.2.5 Drying on-load tap-changer in autoclave...... 41 2.2 Inappropriate use......................................................... 9 5.2.6 Drying on-load tap-changer in 2.3 Fundamental safety instructions................................ 9 transformer tank........................................... 46 2.4 Personal protective equipment................................. 10 5.2.7 Filling the oil compartment of the on- 2.5 Personnel qualification............................................... 11 load tap-changer with insulating fluid......... 48 5.2.8 Performing transformer ratio test after 3 Product description.................................... 13 drying............................................................. 50 3.1 Scope of delivery.......................................................... 13 5.3 Installing on-load tap-changer in transformer 3.2 On-load tap-changer................................................... 13 (bell-type tank version)............................................ 51 3.2.1 Function description......................................... 13 5.3.1 Inserting on-load tap-changer into 3.2.2 Setup/models.................................................. 14 supporting structure...................................... 51 3.2.3 Nameplate and serial number......................... 16 5.3.2 Connecting the tap winding and on-load 3.2.4 Protective devices............................................ 16 tap-changer take-off lead............................. 52 3.3 Drive shaft................................................................... 22 5.3.3 Performing transformer ratio test before 3.3.1 Function description........................................ 22 drying............................................................. 53 3.3.2 Design/versions.............................................. 22 5.3.4 Performing DC resistance measurement on transformer.............................................. 53 4 Packaging, transport and storage............. 27 5.3.5 Drying on-load tap-changer in autoclave...... 54 4.1 Packaging.................................................................... 27 5.3.6 Lifting top part of on-load tap-changer 4.1.1 Suitability.......................................................... 27 head off supporting flange (bottom 4.1.2 Markings........................................................... 28 part)................................................................ 59 4.2 Transportation, receipt and handling of 5.3.7 Attaching the bell-type tank and shipments................................................................ 29 connecting the on-load tap-changer to 4.3 Storage of shipments................................................ 30 the top part of the on-load tap-changer 4.4 Unpacking shipments and checking for head................................................................ 62 transportation damages......................................... 30 5.3.8 Drying on-load tap-changer in transformer tank........................................... 66 5 Mounting.................................................... 31 5.3.9 Filling the oil compartment of the on- 5.1 Preparatory work......................................................... 31 load tap-changer with insulating fluid......... 68 5.1.1 Fitting mounting flange on transformer 5.3.10 Performing transformer ratio test after cover................................................................ 31 drying............................................................. 70 5.1.2 Fitting stud bolts on mounting flange........... 32 4349322/04 EN Table of contents 3 5.4 Fitting protective devices and drive 8.2 Technical data for protective relay RS..................... 156 components.............................................................. 71 8.3 Special models of protective relay RS..................... 158 5.4.1 Electrically connecting the temperature 8.3.1 Protective relay with CO change-over sensor.............................................................. 71 contact as tripping switch........................... 158 5.4.2 Connecting tap-change supervisory 8.3.2 Protective relay with several dry-reed control............................................................. 71 magnetic switches....................................... 158 5.4.3 Installing protective relay in piping and 8.4 Technical data for pressure monitoring device.... 160 connecting..................................................... 72 8.5 Limit values for dielectric strength and water 5.4.4 Installing and connecting the pressure content of insulating fluids.................................... 161 monitoring device......................................... 82 5.4.5 Fitting motor-drive unit.................................. 85 9 Drawings.................................................. 162 5.4.6 Fitting drive shaft............................................ 85 9.1 737774........................................................................ 163 5.4.7 Centering on-load tap-changer and 9.2 898863...................................................................... 164 motor-drive unit........................................... 133 9.3 737060........................................................................ 165 5.4.8 Making the electrical connections for the 9.4 738902...................................................................... 166 motor-drive unit........................................... 133 9.5 739172........................................................................ 167 9.6 890183....................................................................... 168 6 Commissioning......................................... 134 9.7 898866...................................................................... 169 6.1 Commissioning the on-load tap-changer at the 9.8 899110........................................................................ 170 transformer manufacturer's site.......................... 134 9.9 899409....................................................................... 171 6.1.1 Bleeding on-load tap-changer head and 9.10 899083..................................................................... 172 suction pipe................................................. 134 9.11 899051...................................................................... 173 6.1.2 Grounding the on-load tap-changer............. 136 9.12 733469..................................................................... 174 6.1.3 Checking motor-drive unit............................. 137 9.13 892916...................................................................... 175 6.1.4 High-voltage tests on the transformer........ 137 6.2 Transporting transformer to the operating site..... 139 Glossary....................................................... 176 6.2.1 Transport with drive removed....................... 139 6.2.2 Transport with full transformer tank and without oil conservator............................... 139 6.2.3 Transport with empty transformer tank..... 140 6.3 Commissioning transformer at operating site...... 142 6.3.1 Filling the oil compartment of the on- load tap-changer with insulating fluid....... 142 6.3.2 Bleeding on-load tap-changer head and suction pipe................................................. 143 6.3.3 Checking motor-drive unit........................... 144 6.3.4 Checking protective relay............................ 144 6.3.5 Checking pressure monitoring device........ 145 6.3.6 Commissioning the transformer................. 146 7 Fault elimination....................................... 147 7.1 Tripping the protective relay and re- commissioning the transformer.......................... 149 7.1.1 Flap valve in OPERATION position.............. 149 7.1.2 Flap valve in OFF position............................. 150 7.1.3 Re-commissioning the transformer............. 150 7.2 Tripping the pressure monitoring device and putting the transformer back into operation....... 151 7.2.1 Sensor in the OPERATION position.............. 151 7.2.2 Sensor in the OFF position............................ 151 7.2.3 Re-commissioning the transformer............. 152 8 Technical data.......................................... 153 8.1 Technical data for on-load tap-changer.................. 153 8.1.1 On-load tap-changer properties.................... 153 8.1.2 Permissible ambient conditions................... 154 8.1.3 Height of the oil conservator........................ 154 8.1.4 Installation height above sea level............... 155 4 Table of contents 4349322/04 EN 1 Introduction This technical file contains detailed descriptions of the safe and proper installa- tion, connection, and commissioning of the product. It also includes safety instructions and general information about the product. Information about operation can be found in the operating instructions. This technical file is intended solely for specially trained and authorized person- nel. 1.1 Manufacturer Maschinenfabrik Reinhausen GmbH Falkensteinstraße 8 93059 Regensburg Deutschland +49 941 4090-0 [email protected] reinhausen.com MR Reinhausen customer portal: https://portal.reinhausen.com. Further information on the product and copies of this technical file are available from this address if required. 1.2 Completeness This technical file is incomplete without the supporting documents. The following documents are considered supporting documents: – Unpacking instructions – Supplement – Routine test report – Connection diagrams – Dimensional drawings – Order confirmation 1.3 Safekeeping Keep this technical file and all supporting documents ready at hand and accessi- ble for future use at all times. 4349322/04 EN Introduction 5 1.4 Notation conventions 1.4.1 Hazard communication system Warnings in this technical file are displayed as follows. 1.4.1.1 Warning relating to section Warnings relating to sections refer to entire chapters or sections, sub-sections or several paragraphs within this technical file. Warnings relating to sections use the following format: WARNING Type of danger! Source of the danger and outcome. Action Action 1.4.1.2 Embedded warning information Embedded warnings refer to a particular part within a section. These warnings apply to smaller units of information than the warnings relating to sections. Em- bedded warnings use the following format: DANGER! Instruction for avoiding a dangerous situation. 1.4.1.3 Signal words in warning notices Signal word Meaning DANGER Indicates a hazardous situation which, if not avoided, will result in death or serious injury. WARNING Indicates a hazardous situation which, if not avoided, could result in death or serious injury. CAUTION Indicates a hazardous situation which, if not avoided, could result in mi- nor or moderate injury. NOTICE Indicates measures to be taken to prevent damage to property. Table 1: Signal words in warning notices 1.4.2 Information system Information is designed to simplify and improve understanding of particular procedures. In this technical file it is laid out as follows: Important information. i 1.4.3 Instruction system This technical file contains single-step and multi-step instructions. Single-step instructions Instructions which consist of only a single process step are structured as fol- lows: 6 Introduction 4349322/04 EN Aim of action Requirements (optional). Step 1 of 1. Result of step (optional). Result of action (optional). Multi-step instructions Instructions which consist of several process steps are structured as follows: Aim of action Requirements (optional). 1. Step 1. Result of step (optional). 2. Step 2. Result of step (optional). Result of action (optional). 4349322/04 EN Introduction 7 2 Safety – Read this technical file through to familiarize yourself with the product. – This technical file is a part of the product. – Read and observe the safety instructions provided in this chapter. – Read and observe the warnings in this technical file in order to avoid func- tion-related dangers. – The product is manufactured on the basis of state-of-the-art technology. Nevertheless, risks to life and limb for the user or impairment of the product and other material assets due to the function may arise in the event of im- proper use. 2.1 Appropriate use The product is an on-load tap-changer and adjusts the transmission ratio of transformers without interrupting the load flow. The product is designed solely for use in electrical energy systems and facilities. If used as intended and in compliance with the requirements and conditions specified in this technical file as well as the warning notices in this technical file and attached to the product, then the product does not present any danger to people, property or the envi- ronment. This applies throughout the service life of the product, from delivery, installation and operation to removal and disposal. The following is considered appropriate use: – Use the product only with the transformer/motor-drive unit specified in the order. – The serial numbers of on-load tap-changer and on-load tap-changer acces- sories (drive, drive shaft, bevel gear, protective relay, etc.) must match if the on-load tap-changer and on-load tap-changer accessories are supplied as a set for one order. – You will find the standard valid for the product and the year of issue on the nameplate. – Operate the product in accordance with this provided technical file, the agreed delivery conditions and technical data. – Ensure that all necessary work is performed by qualified personnel only. – Only use the equipment and special tools included in the scope of delivery for the intended purpose and in accordance with the specifications of this technical file. – The on-load tap-changer is not intended to be used with an oil filter unit. Permitted electrical operating conditions In addition to the design data in accordance with the order confirmation, ob- serve the following limits for the through-current and the step voltage: In the standard version, the on-load tap-changer is designed for sinusoidal 50/60 Hz alternating current with a curve form symmetrical to the zero axis and can switch 2 times the rated through-current Ir at its rated step voltage Uir. Exceeding the rated step voltage Uir by up to 10% for a short period is permitted as long as the rated step capacity PStN permissible for this step voltage is not ex- ceeded. 8 Safety 4349322/04 EN 2.2 Inappropriate use Use is considered inappropriate if the product is used in a way other than as de- scribed in the "Appropriate use" section. In addition, observe the following: Prohibited electrical operating conditions All operating conditions that do not comply with the design data in accordance with the order confirmation are prohibited. Prohibited operating conditions may arise due to short circuits as well as due to inrush current impulses when energizing transformers or other electrical ma- chines. This applies to the affected transformer itself just as it does to trans- formers electrically connected in parallel or serially or other electrical machines. Higher voltages may occur due to transformer overexcitation following load shedding, for example. Operations outside of the permitted operating conditions can lead to injury to persons and damage to the product. – Prevent any such operations outside of the permitted operating conditions by taking suitable measures. 2.3 Fundamental safety instructions To prevent accidents, disruptions and damage as well as unacceptable adverse effects on the environment, those responsible for transport, installation, opera- tion, maintenance and disposal of the product or parts of the product must en- sure the following: Personal protective equipment Loosely worn or unsuitable clothing increases the danger of becoming trapped or caught up in rotating parts and the danger of getting caught on protruding parts. This poses a danger to life and limb. – Wear appropriate personal protective equipment such as a helmet, work gloves, etc. for the respective activity. – Never wear damaged personal protective equipment. – Never wear rings, necklaces, or other jewelry. – If you have long hair, wear a hairnet. Work area Untidy and poorly lit work areas can lead to accidents. – Keep the work area clean and tidy. – Make sure that the work area is well lit. – Observe the applicable laws for accident prevention in the relevant country. Working during operation The product may only be operated in a sound, operational condition. Otherwise it poses a danger to life and limb. – Regularly check the operational reliability of safety equipment. – Comply with the inspection work, maintenance work and maintenance inter- vals described in this technical file. 4349322/04 EN Safety 9 Explosion protection Highly flammable or explosive gases, vapors and dusts can cause serious explo- sions and fire. This increases the danger to life and limb. – Do not install, operate or perform maintenance work on the product in areas where a risk of explosion is present. Safety markings Warning signs and safety information plates are safety markings on the prod- uct. They are an important aspect of the safety concept. – Observe all safety markings on the product. – Make sure all safety markings on the product remain intact and legible. – Replace safety markings that are damaged or missing. Ambient conditions To ensure reliable and safe operation, the product must only be operated under the ambient conditions specified in the technical data. – Observe the specified operating conditions and requirements for the installa- tion location. Auxiliary materials and operating materials Auxiliary materials and operating materials not approved by the manufacturer can lead to personal injury, damage to property and malfunctions of the prod- uct. – Only use insulating fluids [►Section 8.1.2, Page 154] approved by the manu- facturer. – Only use conductive and grounded hoses, pipes and pump equipment that are approved for flammable liquids. – Only use lubricants and auxiliary materials approved by the manufacturer. – Contact the manufacturer. Modifications and conversions Unauthorized or inappropriate changes to the product may lead to personal in- jury, material damage and operational faults. – Only modify the product after consultation with Maschinenfabrik Reinhausen GmbH. Spare parts Spare parts not approved by Maschinenfabrik Reinhausen GmbH may lead to physical injury, damage to the product and malfunctions. – Only use spare parts that have been approved by Maschinenfabrik Rein- hausen GmbH. – Contact Maschinenfabrik Reinhausen GmbH. 2.4 Personal protective equipment Personal protective equipment must be worn during work to minimize risks to health. – Always wear the personal protective equipment required for the job at hand. – Never wear damaged personal protective equipment. – Observe information about personal protective equipment provided in the work area. 10 Safety 4349322/04 EN Protective clothing Close-fitting work clothing with a low tearing strength, with tight sleeves and with no protruding parts. It mainly serves to protect the wearer against being caught by moving machine parts. Safety shoes To protect against falling heavy objects and slipping on slip- pery surfaces. Safety glasses To protect the eyes from flying parts and splashing liquids. Visor To protect the face from flying parts and splashing liquids or other dangerous substances. Hard hat To protect against falling and flying parts and materials. Hearing protection To protect against hearing damage. Protective gloves To protect against mechanical, thermal, and electrical haz- ards. Table 2: Personal protective equipment 2.5 Personnel qualification The person responsible for assembly, commissioning, operation, maintenance and inspection must ensure that the personnel are sufficiently qualified. Electrically skilled person The electrically skilled person has a technical qualification and therefore has the required knowledge and experience, and is also conversant with the applicable standards and regulations. The electrically skilled person is also proficient in the following: – Can identify potential dangers independently and is able to avoid them. – Is able to perform work on electrical systems. – Is specially trained for the working environment in which (s)he works. – Must satisfy the requirements of the applicable statutory regulations for acci- dent prevention. Electrically trained persons An electrically trained person receives instruction and guidance from an electri- cally skilled person in relation to the tasks undertaken and the potential dangers in the event of inappropriate handling as well as the protective devices and safety measures. The electrically trained person works exclusively under the guidance and supervision of an electrically skilled person. Operator The operator uses and operates the product in line with this technical file. The operating company provides the operator with instruction and training on the specific tasks and the associated potential dangers arising from improper han- dling. Technical Service We strongly recommend having maintenance, repairs and retrofitting carried out by our Technical Service department. This ensures that all work is per- formed correctly. If maintenance is not carried out by our Technical Service de- partment, please ensure that the personnel who carry out the maintenance are trained and authorized by Maschinenfabrik Reinhausen GmbH to carry out the work. 4349322/04 EN Safety 11 Authorized personnel Authorized personnel are trained by Maschinenfabrik Reinhausen GmbH to carry out special maintenance. 12 Safety 4349322/04 EN 3 Product description 3.1 Scope of delivery The product is packaged with protection against moisture and is usually deliv- ered as follows: – On-load tap-changer – Motor-drive unit – Drive shaft with coupling parts and bevel gear – Protective device – Technical files Please refer to the delivery slip for full details of scope of delivery. On-load tap-changers can also be provided as an on-load tap-changer set i with a common motor-drive unit. Note the following information: – Check the shipment for completeness on the basis of the shipping docu- ments. – Store the parts in a dry place until installation – The product must remain in its airtight, protective wrapping and may only be removed immediately before installation You will find more information in the "Packaging, transport, and storage" [►Section 4, Page 27] chapter. 3.2 On-load tap-changer 3.2.1 Function description On-load tap-changers are used to adjust the transmission ratio of transformers without interrupting the load flow. This makes it possible to compensate for as- pects such as fluctuations in voltage occurring in the power transmission grid. For this purpose, on-load tap-changers are fitted in transformers and connected to the active part of the transformer. A motor-drive unit which receives a control impulse (e.g. from a voltage regula- tor) changes the operating position of the on-load tap-changer, and the trans- former's transmission ratio is adapted to the prevailing operating requirements as a result. 4349322/04 EN Product description 13 Figure 1: System overview of on-load tap-changer, transformer 1 Transformer tank 6 Gear unit 2 Motor-drive unit 7 On-load tap-changer 3 Vertical drive shaft 8 Protective relay 4 Bevel gear 9 Oil conservator 5 Horizontal drive shaft 10 Active part 3.2.2 Setup/models The following drawing shows the main components of the on-load tap-changer. 14 Product description 4349322/04 EN You will find a detailed drawing of the on-load tap-changer in the "Drawings [►Section 9, Page 162]" section. Figure 2: On-load tap-changer 1 Upper gear unit 2 On-load tap-changer head 3 Supporting flange 4 Connection contact 5 Oil compartment 6 Change-over selector 7 Pipe bend 8 Rupture disk 3.2.2.1 Pipe connections The on-load tap-changer head features 4 pipe connections for different pur- poses. Depending on the order, some or all of these pipe connections are fitted with pipe bends ex factory. All pipe bends can be freely swiveled once the pressure ring is loosened. Figure 3: Pipe connections with pipe bends Pipe connection Q The pipe connection Q is closed with a blank cover. The functions of the R and Q pipe connections can be interchanged. i 4349322/04 EN Product description 15 Pipe connection S The pipe bend on pipe connection S features a vent screw and can be con- nected to a pipe that ends with a drain valve on the side of the transformer tank at operating height. If the on-load tap-changer is fitted with an oil suction pipe, the on-load tap-changer can be completely emptied via pipe connection S. Pipe connection R Pipe connection R is intended for attachment of the protective relay and con- nection of the on-load tap-changer oil conservator and can be interchanged with pipe connection Q. Pipe connection E2 Pipe connection E2 is sealed off with a blank cover. It leads into the oil tank of the transformer, directly under the on-load tap-changer head and can be con- nected to a collective pipe for the Buchholz relay, if necessary. This pipe con- nection serves an additional purpose, namely to equalize the pressure between the transformer tank and the oil compartment of the on-load tap-changer, which is necessary for drying, filling and transporting the transformer. 3.2.3 Nameplate and serial number The nameplate is on the on-load tap-changer head cover. Figure 4: Nameplate with serial number 3.2.4 Protective devices The on-load tap-changer is equipped with the following protective devices. 3.2.4.1 Protective relay 3.2.4.1.1 Function description The protective relay is looped into the circuit breaker tripping circuit. It is tripped when the specified speed of flow from the on-load tap-changer head to the oil conservator is exceeded due to a fault. The flowing insulating fluid actuates the flap valve which tips over into position OFF. The contact in the dry-reed mag- netic switch is thereby actuated, the circuit breakers are tripped, and the trans- former is de-energized. The protective relay is a component of an on-load tap-changer filled with insu- lating fluid and its properties conform to the respective applicable version of IEC publication 60214-1. 16 Product description 4349322/04 EN Diverter switch operations at rated switching capacity or at permissible i overload will not cause the protective relay to trip. The protective relay responds to flow, not to gas accumulated in the pro- i tective relay. It is not necessary to bleed the protective relay when filling the transformer with insulating fluid. Gas accumulation in the protective re- lay is normal. 3.2.4.1.2 Design/versions Front view Figure 5: Protective relay RS 2001 1 Inspection window 2 Pressure equalization element Rear view Figure 6: Protective relay RS 2001 1 Dummy plug 2 Nameplate The protective relay RS 2001/R has an extra inspection window on the rear. i 4349322/04 EN Product description 17 View from above Figure 7: Protective relay RS 2001 1 Gasket 2 Potential tie-in 3 Terminal box cover 4 Slotted head screw for potential tie-in 5 OPERATION (reset) test button 6 Slotted head screw for protective cover 7 OFF (test tripping) test button 8 Cable gland 9 Protective cover 10 Dummy plug 11 Connection terminal 12 Pressure equalization element 13 Cylinder head screw for protective conductor connection The protective relays RS 2003 and RS 2004 have a 1/2"-14NPT adapter in i place of the cable gland. 3.2.4.1.3 Nameplate The nameplate is on the back of the protective relay. Figure 8: Nameplate 18 Product description 4349322/04 EN 3.2.4.2 Pressure monitoring device DW 3.2.4.2.1 Function description The DW 2000 pressure monitoring device protects the on-load tap-changer from impermissible pressure increases, contributing to the safety of the trans- former. The pressure monitoring device is installed on the outside of the on- load tap-changer and is tripped by impermissible static and dynamic pressures in the on-load tap-changer oil compartment. The pressure monitoring device uses a concept where a corrugated tube acts as a barometer together with a spring providing counter force. This assembly is mechanically linked to the sensor on the snap-action switch. The pressure increase activates the sensor on the snap-action switch, which flips into the OFF position. This triggers the circuit breaker and de-energizes the transformer. The sensor on the snap-action switch has to be reset to the initial position by hand after tripping. Low-energy interference does not cause the pressure monitoring device to trip since the required tripping pressure is not reached. The tripping pressure is set at the factory and prevented from being changed. The pressure monitoring device responds to large pressure increases faster than the protective relay. The protective relay is part of the standard MR protec- tion system and comes as standard. Additional use of a pressure monitoring device also requires installation of i the provided protective relay. The features and characteristics of the pressure monitoring device comply with the respective applicable version of IEC publication 60214-1. Diverter switch operations at the rated switching capacity or permitted i overload do not cause the pressure-operated relay to trip. The pressure-operated relay responds to a pressure change and not to gas i accumulation under the pressure-operated relay. Gas accumulation under the pressure-operated relay is normal. 3.2.4.2.2 Design/versions There are two variants of the pressure monitoring device: – DW 2000 for vertical installation – DW 2000 for horizontal installation 4349322/04 EN Product description 19 The housing and the cover cap of the pressure monitoring device consist of lightweight, corrosion-resistant metal. Figure 9: Snap-action switch and pressure measuring element 1 Snap-action switch 2 Pressure measuring element Figure 10: Pressure monitoring device with cover cap and ventilation 1 Ventilation 2 Cover cap 20 Product description 4349322/04 EN 3.2.4.3 Rupture disk The rupture disk is a pressure relief device without signaling contact in accor- dance with IEC 60214-1 and is located in the on-load tap-changer head cover. The rupture disk responds to a defined overpressure in the oil compartment of the on-load tap-changer. 3.2.4.4 Pressure relief device MPREC® On request, MR will supply a pre-fitted MPREC® pressure relief device in place of the rupture disk. This device responds to a defined overpressure in the oil com- partment of the on-load tap-changer. The on-load tap-changer therefore meets the requirements of IEC 60214-1 re- garding pressure relief devices. 3.2.4.5 Tap-change supervisory device The tap-change supervisory device monitors both the drive shaft between on- load tap-changer(s) and motor-drive unit and the correct switching of the di- verter switch. 3.2.4.6 Temperature monitoring The temperature monitoring system monitors the temperature of the insulating fluid in the oil compartment of the on-load tap-changer. 4349322/04 EN Product description 21 3.3 Drive shaft 3.3.1 Function description The drive shaft is the mechanical connection between the drive and the on-load tap-changer/de-energized tap-changer. The bevel gear changes the direction from vertical to horizontal. Accordingly, the vertical drive shaft has to be mounted between drive and bevel gear, and the horizontal drive shaft between bevel gear and on-load tap- changer or de-energized tap-changer. 3.3.2 Design/versions The drive shaft consists of a square tube and is coupled at each end by two cou- pling brackets and one coupling bolt to the driving or driven shaft end of the de- vice to be connected. Figure 11: Components of the drive shaft 1 Bevel gear 2 Hose clip 3 Telescopic protective tube 4 Coupling bracket 5 Square tube 6 Coupling bolt 7 Adapter ring 8 Protective cover 22 Product description 4349322/04 EN 3.3.2.1 Drive shaft without cardan joint and without insulator Figure 12: Drive shaft without cardan joint and without insulator (= standard version) Configuration V 1 min Intermediate bearing Middle of hand crank – middle of bevel 536 mm When the maximum value of gear (maximum permissible axial offset 2472 mm is exceeded, it is 2°) necessary to use an interme- diate bearing. V 1 ≤ 2472 mm (without in- termediate bearing) V 1 > 2472 mm (with inter- mediate bearing) 4349322/04 EN Product description 23 3.3.2.2 Drive shaft without cardan joint and with insulator Figure 13: Drive shaft without cardan joint and with insulator (= special model) Configuration V 1 min Intermediate bearing Middle of hand crank – middle of bevel 706 mm When the maximum value of gear (maximum permissible axial offset 2472 mm is exceeded, it is 2°) necessary to use an interme- diate bearing. V 1 ≤ 2472 mm (without in- termediate bearing) V 1 > 2472 mm (with inter- mediate bearing) 24 Product description 4349322/04 EN 3.3.2.3 Drive shaft with cardan joints, without insulator Figure 14: Drive shaft with cardan joints, without insulator (= special model) Configuration V 1 min [mm] Intermediate bearing for [mm] Middle of hand crank – middle of bevel 798 V 1 > 2564 gear (maximum permissible axial offset 20°) 4349322/04 EN Product description 25 3.3.2.4 Drive shaft with cardan joints, with insulator Figure 15: Drive shaft with cardan joints, with insulator (= special model) Configuration V 1 min [mm] Intermediate bearing for [mm] Middle of hand crank – middle of bevel 978 V 1 > 2772 gear (maximum permissible axial offset 20°) 26 Product description 4349322/04 EN 4 Packaging, transport and storage 4.1 Packaging The products are sometimes supplied with sealed packaging and sometimes in a dry state, depending on requirements. Sealed packaging surrounds the packaged goods with plastic foil on all sides. Products that have also been dried are identified by a yellow label on the sealed packaging. In the dry state, delivery is also possible in a transport container. The information in the following sections should be applied as appropriate. 4.1.1 Suitability NOTICE Property damage due to incorrectly stacked crates! Stacking the crates incorrectly can lead to damage to the packaged goods. The outer marking on the packaging states if, for example, the on-load tap- changer or selector has been packed upright. Never stack these crates. General rule: Do not stack crates above a height of 1.5 m. For other crates: Only stack up to 2 equally sized crates on top of one an- other. The packaging is suitable to ensure undamaged and fully functional means of transportation in compliance with local transportation laws and regulations. The packaged goods are packed in a sturdy crate. This crate ensures that, when in the intended transportation position, the packaged goods are stabilized to prevent impermissible changes in position, and that none of the parts touch the loading surface of the means of transport or touch the ground after unloading. Sealed packaging surrounds the packaged goods with plastic foil on all sides. The packaged goods are protected from humidity using a desiccant. The plastic foil was bonded after the desiccant is added. 4349322/04 EN Packaging, transport and storage 27 4.1.2 Markings The packaging bears a signature with instructions for safe transport and correct storage. The following symbols apply to the shipment of non-hazardous goods. Adherence to these symbols is mandatory. Protect against Top Fragile Attach lifting Center of mass moisture gear here Table 3: Shipping pictograms 28 Packaging, transport and storage 4349322/04 EN 4.2 Transportation, receipt and handling of ship- ments WARNING Danger of death or severe injury! Danger of death or serious injuries due to tipping or falling load. Only transport the crate when closed. Do not remove the securing material used in the crate during transport. If the product is delivered on a pallet, secure it sufficiently. Only trained and authorized persons may select the sling gear and secure the load. Do not walk under the suspended load. Use means of transport and lifting gear with a sufficient carrying capacity in accordance with the weight stated on the delivery slip. In addition to oscillation stress, jolts must also be expected during transporta- tion. In order to prevent possible damage, avoid dropping, tipping, knocking over and colliding with the product. If a crate tips over, falls from a certain height (e.g. when slings tear) or experi- ences an unbroken fall, damage must be expected regardless of the weight. Every delivered shipment must be checked for the following by the recipient be- fore acceptance (acknowledgment of receipt): – Completeness based on the delivery slip – External damage of any type The checks must take place after unloading when the crate or transport con- tainer can be accessed from all sides. Visible damage If external transport damage is found upon receipt of the shipment, proceed as follows: – Immediately record the identified transport damage in the shipping docu- ments and have this countersigned by the carrier. – In the event of severe damage, total loss or high damage costs, immediately notify the manufacturer and the relevant insurance company. – After identifying damage, do not modify the condition of the shipment fur- ther and retain the packaging material until an inspection decision has been made by the transport company or the insurance company. – Record the details of the damage immediately on site together with the car- rier involved. This is essential for any claim for damages. – Photograph damage to packaging and packaged goods. This also applies to signs of corrosion on the packaged goods due to moisture inside the packag- ing (rain, snow, condensation). – NOTICE! Damage to packaged goods due to damaged sealed packaging. If the product is delivered in sealed packaging, check the sealed packaging im- mediately. If the sealed packaging is damaged, do not under any circum- stances install or commission the packaged goods. Either re-dry the dried packaged goods as per the operating instructions, or contact the manufac- turer to agree on how to proceed. – Identify the damaged parts. Hidden damage When damages are not determined until unpacking after receipt of the ship- ment (hidden damage), proceed as follows: – Make the party responsible for the damage liable as soon as possible by tele- phone and in writing, and prepare a damage report. – Observe the time periods applicable to such actions in the respective coun- try. Inquire about these in good time. 4349322/04 EN Packaging, transport and storage 29 With hidden damage, it is very hard to make the transportation company (or other responsible party) liable. Any insurance claims for such damages can only be successful if relevant provisions are expressly included in the insurance terms and conditions. 4.3 Storage of shipments Packaged goods dried by Maschinenfabrik Reinhausen Upon receipt of the shipment, immediately remove the packaged goods dried by Maschinenfabrik Reinhausen from the sealed packaging and store air-tight in dry insulating fluid until used if the packaged goods were not supplied in insu- lating fluid. Non-dried packaged goods Non-dried packaged goods but with a functional sealed packaging can be stored outdoors when the following conditions are complied with. When selecting and setting up the storage location, ensure the following: – Protect stored goods against moisture (flooding, water from melting snow and ice), dirt, pests such as rats, mice, termites and so on, and against unau- thorized access. – Store the crates on timber beams and planks as a protection against rising damp and for better ventilation. – Ensure sufficient carrying capacity of the ground. – Keep entrance paths free. – Check stored goods at regular intervals. Also take appropriate action after storms, heavy rain or snow and so on. Protect the packaging foil from direct sunlight so that it does not disintegrate under the influence of UV rays, which would cause the packaging to lose its sealing function. If the product is installed more than 6 months after delivery, suitable measures must be taken without delay. The following measures can be used: – Correctly regenerate the drying agent and restore the sealed packaging. – Unpack the packed goods and store in a suitable storage space (well venti- lated, as dust-free as possible, humidity < 50% where possible). 4.4 Unpacking shipments and checking for trans- portation damages – NOTICE! Damage to packaged goods due to ineffectively sealed packaging. Transport the packaged crate to the place where the packaged goods are to be installed. Do not open the sealed packaging until just before installation. – WARNING! Serious injuries and damage to the packaged goods due to the packaged goods tipping out. Place the packaged goods in an upright crate and protect it from tipping out. – Unpack the packaged goods and check the condition. – Check the completeness of the accessories kit using the delivery slip. 30 Packaging, transport and storage 4349322/04 EN 5 Mounting WARNING Risk of crushing! When the on-load tap-changer undertakes a tap-change operation, compo- nents – some of which are freely accessible – move on the selector, change- over selector, and potential connection unit. Reaching into the selector, change-over selector, or potential connection unit during a tap-change opera- tion may result in serious injuries. Keep at a safe distance of at least 1 m during tap-change operations. Do not reach into the selector, change-over selector, or potential connec- tion unit during tap-change operations. Do not switch the on-load tap-changer during work on the selector, change-over selector, or potential connection unit. 5.1 Preparatory work Perform the work stated below before installing the on-load tap-changer in the transformer. 5.1.1 Fitting mounting flange on transformer cover A mounting flange is required for fitting the on-load tap-changer head on the transformer cover. This can be supplied as an option or can be produced by the customer. Mounting flanges made by the customer must comply with the in- stallation drawings in the appendix. NOTICE! Fit mounting flange on transformer cover (pressure tight).Ensure that the sealing face makes complete contact and is not damaged. Figure 16: Mounting flange 4349322/04 EN Mounting 31 5.1.2 Fitting stud bolts on mounting flange To attach the stud bolts to the mounting flange, use a tracing template. This can be provided upon request free of charge for the initial installation of the on- load tap-changer. 1. Place tracing template on mounting flange and use the four markings to align. 2. Fit stud bolts on mounting flange. Figure 17: Tracing template, stud bolts 32 Mounting 4349322/04 EN 5.2 Installing the on-load tap-changer in the trans- former (standard version) 5.2.1 Fastening on-load tap-changer to transformer cover Note that only on-load tap-changers with an unscrewed supporting flange i can be fitted in a transformer with the standard design. 5.2.1.1 Lifting top part of on-load tap-changer head off supporting flange (bottom part) NOTICE Damage to the on-load tap-changer! Small parts in the oil compartment may block the diverter switch insert, thereby damaging the on-load tap-changer. Ensure that parts do not fall into the oil compartment. Check that all small parts are accounted for. 1. CAUTION! An unstably positioned on-load tap-changer may tip, resulting in serious injuries and damage. Place on-load tap-changer on a level surface and secure it against tipping. 2. Remove red-colored packaging material and transport material from on-load tap-changer. 3. Ensure that the on-load tap-changer is in the adjustment position. The ad- justment position is indicated in the on-load tap-changer connection diagram included in delivery. 4. Ensure that the inspection window is sealed off with the cover. 5. Remove screws and locking washers on on-load tap-changer head cover. Figure 18: On-load tap-changer head cover 4349322/04 EN Mounting 33 6. Remove on-load tap-changer head cover. Figure 19: On-load tap-changer head cover 7. For design with oil suction pipe, loosen screw connection of R3/4" oil suction pipe. Check for leaks. Figure 20: Oil suction pipe 8. Remove bolts and locking washers between top part of on-load tap-changer head and supporting flange. Figure 21: On-load tap-changer head 34 Mounting 4349322/04 EN 9. Lift top part of on-load tap-changer head off supporting flange. Figure 22: On-load tap-changer head 5.2.1.2 Positioning the top part of the on-load tap-changer head on the trans- former cover 1. Clean sealing surfaces on mounting flange and on-load tap-changer head, place oil-resistant gasket on mounting flange. Figure 23: Mounting flange and on-load tap-changer head 4349322/04 EN Mounting 35 2. Position top part of on-load tap-changer head on mounting flange. Figure 24: On-load tap-changer head For design without oil suction pipe, the on-load tap-changer head can be i turned towards the supporting flange in 15° steps. For design with oil suc- tion pipe, turning at 15° increments is not possible. When positioning the on-load tap-changer head, do however note that the tap-change supervisory control restricts the swivel range of the upper gear unit. 5.2.1.3 Connecting on-load tap-changer to top part of on-load tap-changer head NOTICE Damage to the on-load tap-changer! A missing or damaged o-ring as well as unclean sealing surfaces lead to insu- lating fluid escaping and therefore to damage to the on-load tap-changer. Ensure that the o-ring is positioned untwisted in the on-load tap-changer head cover. Ensure that the o-ring does not become damaged when mounting the cover. Ensure that the sealing surfaces on the on-load tap-changer head cover and on-load tap-changer head are clean. 1. NOTICE! Incorrectly lifting the on-load tap-changer will damage it. Secure 4 ropes of equal length (at least 1 m in length) to the attachment points pro- vided and slowly lift on-load tap-changer from below towards on-load tap- 36 Mounting 4349322/04 EN changer head. Under no circumstances should the on-load tap-changer be lifted up with the fixing bolts. Ensure that all supporting flange stud bolts go easily through the mounting holes of the on-load tap-changer head. Figure 25: On-load tap-changer 2. Screw the top part to the bottom part of the on-load tap-changer head. Figure 26: On-load tap-changer head 3. For design with oil suction pipe, connect oil suction pipe screw connection. Check for leaks. Figure 27: Oil suction pipe 4349322/04 EN Mounting 37 4. Screw the on-load tap-changer head to the mounting flange. The tightening torque depends on the screw connection elements used. Figure 28: On-load tap-changer head 5. Place on-load tap-changer head cover on on-load tap-changer head and se- cure. Figure 29: On-load tap-changer head cover 5.2.2 Connecting the tap winding and on-load tap-changer take-off lead NOTICE Damage to the on-load tap-changer! Connecting leads which place mechanical strain on the on-load tap-changer will damage the on-load tap-changer! Establish and secure connections with care. Do not twist connection contacts. Connect connecting leads without warping or deforming. If necessary use an expansion loop for connecting leads. 38 Mounting 4349322/04 EN The designations of the on-load tap-changer's connection contacts are shown in the connection diagram. The connection contacts are provided with vertical through-holes (11 mm diameter for M10 screws, see appendix). 1. Connect tap winding and on-load tap-changer take-off lead in accordance with the connection diagram included with the delivery. 2. If connection leads have to cross the open surface of the oil compartment/ change-over selector, there must be a clearance of 50 mm between the con- necting leads and the surface of the oil compartment/change-over selector. Figure 30: Minimum distance 4349322/04 EN Mounting 39 5.2.3 Performing transformer ratio test before drying NOTICE Damage to the on-load tap-changer! Damage to the on-load tap-changer due to transformer ratio test being incor- rectly performed. Do not perform more than 250 tap-change operations on the on-load tap- changer. If more than 250 tap-change operations are to be performed, completely fill the oil compartment with insulating fluid and lubricate slid- ing surfaces of contacts on the selector and selector gear with insulating fluid. Only switch the on-load tap-changer from one operating position to the next via the upper gear unit. You can use a short tube (diameter 25 mm) with screwed-in coupling bolt (diameter 12 mm) with a hand wheel or crank for this, for example. When using a drill, do not exceed a maximum speed of 250 rpm. Always check the operating position reached through the inspection win- dow in the on-load tap-changer head cover. Never overshoot the end posi- tions, which are indicated in the connection diagram supplied with the de- livery. For multiple-column applications with a shared drive, link all on-load tap- changer heads to one another using the horizontal drive shaft parts. When actuating the change-over selector, a higher torque is required. i 1. Switch the on-load tap-changer into the desired operating position. The di- verter switch operation can be heard distinctly. 2. NOTICE! An incomplete tap-change operation may damage the on-load tap- changer. After operating the diverter switch, continue to crank the drive shaft of the upper gear unit for 2.5 revolutions in the same direction in order to cor- rectly complete the tap-change operation. 3. Perform the transformer ratio test. 4. Repeat the transformer ratio test in all operating positions. 5. Switch the on-load tap-changer into adjustment position (see the accompa- nying connection diagram for the on-load tap-changer). After the transformer ratio test, open the kerosene drain plug in the oil i compartment if the on-load tap-changer is to be dried with kerosene in the transformer tank. After drying, the diverter switch insert must be removed, the kerosene drain plug in the oil compartment closed and the diverter switch insert refitted. 5.2.4 Performing DC resistance measurement on transformer NOTICE Damage to the on-load tap-changer. Excessive measurement currents overload the contacts of the on-load tap- changer and thus cause damage to the on-load tap-changer. Ensure that the maximum permissible measurement currents specified in the following table are not exceeded. Perform the DC resistance measurement in various on-load tap-changer op- erating positions in accordance with the following table. 40 Mounting 4349322/04 EN Status of oil compartment Without interruption of the With interruption (measured measured current current = 0 A before change of operating position) Oil compartment empty Maximum 10 A DC Maximum 50 A DC Oil compartment filled with Maximum 50 A DC Maximum 50 A DC insulating fluid Table 4: Maximum permitted measured currents when performing DC resistance measurement on trans- former 5.2.5 Drying on-load tap-changer in autoclave NOTICE Damage to the on-load tap-changer! Moisture in the oil compartment reduces the dielectric strength of the insulat- ing fluid and thus leads to damage to the on-load tap-changer. Within 10 hours of drying, seal off oil compartment with on-load tap- changer head cover. Dry on-load tap-changer in accordance with the following instructions to ensure the dielectric values assured by MR for the on-load tap-changer. If drying in an autoclave, the following methods are possible: – Vacuum drying – Vapor-phase drying As an alternative to drying the on-load tap-changer in an autoclave, it can also be dried in the transformer tank. 5.2.5.1 Vacuum-drying in the autoclave If you wish to perform another transformer ratio test after drying, proceed i as described in the section "Performing transformer ratio test following drying" [►Section 5.2.8, Page 50]. 5.2.5.1.1 Moving on-load tap-changer to adjustment position Move the on-load tap-changer to the adjustment position. The adjustment position is indicated in the on-load tap-changer connection diagram included in delivery. 5.2.5.1.2 Removing on-load tap-changer head cover WARNING Danger of explosion! Explosive gases under the on-load tap-changer head cover can deflagrate or explode and result in severe injury or death. Ensure that there are no ignition sources such as open flames, hot surfaces or sparks (e.g. caused by the build-up of static charge) in the immediate surroundings and that none occur. De-energize all auxiliary circuits (for example tap-change supervisory de- vice, pressure relief device, pressure monitoring device) before removing the on-load tap-changer head cover. Do not operate any electrical devices during the work (e.g. risk of sparks from impact wrench). 4349322/04 EN Mounting 41 NOTICE Damage to the on-load tap-changer! Small parts in the oil compartment may block the diverter switch insert, thereby damaging the on-load tap-changer. Ensure that parts do not fall into the oil compartment. Check that all small parts are accounted for. 1. Ensure that the inspection window is sealed off with the cover. 2. Remove the screws and washers from the on-load tap-changer head cover. Figure 31: On-load tap-changer head cover 3. Remove on-load tap-changer head cover. Figure 32: On-load tap-changer head cover 5.2.5.1.3 Drying the on-load tap-changer NOTICE Damage to the on-load tap-changer head cover and on-load tap- changer accessories. Both the on-load tap-changer head cover and the on-load tap-changer acces- sories will become damaged if they are dried. Never dry the on-load tap-changer head cover or the following accessories: motor-drive unit, drive shaft, protective relay, pressure monitoring device, pressure relief device, bevel gear, sensors such as temperature and humid- ity sensors or pressure sensors, oil filter unit. 1. Heat up the on-load tap-changer in air at atmospheric pressure with a tem- perature increase of approximately 10 °C/h to a final temperature of maxi- mum 110 °C. 2. Pre-dry the on-load tap-changer in circulating air at a maximum temperature of 110 °C for a period of at least 20 hours. 3. Vacuum-dry on-load tap-changer at between 105 °C and maximum 125 °C for at least 50 hours. 4. Residual pressure of no more than 10-3 bar. 42 Mounting 4349322/04 EN 5.2.5.1.4 Securing on-load tap-changer head cover NOTICE Damage to the on-load tap-changer! A missing or damaged o-ring as well as unclean sealing surfaces lead to insu- lating fluid escaping and therefore to damage to the on-load tap-changer. Ensure that the o-ring is positioned untwisted in the on-load tap-changer head cover. Ensure that the o-ring does not become damaged when mounting the cover. Ensure that the sealing surfaces on the on-load tap-changer head cover and on-load tap-changer head are clean. Place on-load tap-changer head cover on on-load tap-changer head and se- cure. Figure 33: On-load tap-changer head cover 5.2.5.2 Vapor-phase drying in the autoclave If you wish to perform another transformer ratio test after drying, proceed i as described in the section "Performing transformer ratio test following drying" [►Section 5.2.8, Page 50]. 5.2.5.2.1 Moving on-load tap-changer to adjustment position Move the on-load tap-changer to the adjustment position. The adjustment position is indicated in the on-load tap-changer connection diagram included in delivery. 4349322/04 EN Mounting 43 5.2.5.2.2 Removing on-load tap-changer head cover WARNING Danger of explosion! Explosive gases under the on-load tap-changer head cover can deflagrate or explode and result in severe injury or death. Ensure that there are no ignition sources such as open flames, hot surfaces or sparks (e.g. caused by the build-up of static charge) in the immediate surroundings and that none occur. De-energize all auxiliary circuits (for example tap-change supervisory de- vice, pressure relief device, pressure monitoring device) before removing the on-load tap-changer head cover. Do not operate any electrical devices during the work (e.g. risk of sparks from impact wrench). NOTICE Damage to the on-load tap-changer! Small parts in the oil compartment may block the diverter switch insert, thereby damaging the on-load tap-changer. Ensure that parts do not fall into the oil compartment. Check that all small parts are accounted for. 1. Ensure that the inspection window is sealed off with the cover. 2. Remove the screws and washers from the on-load tap-changer head cover. Figure 34: On-load tap-changer head cover 3. Remove on-load tap-changer head cover. Figure 35: On-load tap-changer head cover 44 Mounting 4349322/04 EN 5.2.5.2.3 Opening kerosene drain plug NOTICE! Never remove the kerosene drain plug completely. Open kerosene drain plug in base of oil compartment counter-clockwise. Figure 36: Kerosene drain plug 5.2.5.2.4 Drying the on-load tap-changer NOTICE Damage to the on-load tap-changer head cover and on-load tap- changer accessories. Both the on-load tap-changer head cover and the on-load tap-changer acces- sories will become damaged if they are dried. Never dry the on-load tap-changer head cover or the following accessories: motor-drive unit, drive shaft, protective relay, pressure monitoring device, pressure relief device, bevel gear, sensors such as temperature and humid- ity sensors or pressure sensors, oil filter unit. 1. Supply kerosene vapor at a temperature of around 90°C. Keep this tempera- ture constant for 3 to 4 hours. 2. Increase the kerosene vapor temperature by approx. 10°C/hour to the de- sired final temperature of max. 125°C at the on-load tap-changer. 3. Vacuum-dry on-load tap-changer at between 105°C and maximum 125°C for at least 50 hours. 4. Residual pressure of no more than 10-3 bar. 5.2.5.2.5 Closing kerosene drain plug NOTICE! An open kerosene drain plug leads to insulating fluid escaping from the oil compartment and therefore to damage to the on-load tap-changer. Close kerosene drain plug (tightening torque 39 Nm). 5.2.5.2.6 Securing on-load tap-changer head cover NOTICE Damage to the on-load tap-changer! A missing or damaged o-ring as well as unclean sealing surfaces lead to insu- lating fluid escaping and therefore to damage to the on-load tap-changer. Ensure that the o-ring is positioned untwisted in the on-load tap-changer head cover. Ensure that the o-ring does not become damaged when mounting the cover. Ensure that the sealing surfaces on the on-load tap-changer head cover and on-load tap-changer head are clean. 4349322/04 EN Mounting 45 Place on-load tap-changer head cover on on-load tap-changer head and se- cure. Figure 37: On-load tap-changer head cover 5.2.6 Drying on-load tap-changer in transformer tank Dry on-load tap-changer in accordance with the following instructions to ensure the dielectric values assured by MR on the on-load tap-changer. If you want to dry the on-load tap-changer in the transformer tank, fully assem- ble the transformer first and then undertake drying. If drying in the transformer tank, the following methods are possible: – Vacuum-drying – Vapor-phase drying As an alternative to drying the on-load tap-changer in the transformer tank, it can also be dried in an autoclave. 5.2.6.1 Vacuum-drying in the transformer tank The on-load tap-changer head cover remains closed during the entire dry- i ing process. 46 Mounting 4349322/04 EN 1. Establish a connecting lead between either connections E2 and Q or connec- tions E2 and R on the on-load tap-changer head. 2. Seal off unused pipe connections and pipe bends with a suitable blank cover. Figure 38: Connecting lead Vacuum-drying in the transformer tank 1. Heat up the on-load tap-changer in air at atmospheric pressure with a tem- perature increase of approximately 10 °C/h to a final temperature of maxi- mum 110 °C. 2. Pre-dry the on-load tap-changer in circulating air at a maximum temperature of 110 °C for a period of at least 20 hours. 3. Vacuum-dry on-load tap-changer at between 105 °C and maximum 125 °C for at least 50 hours. 4. Residual pressure of no more than 10-3 bar. 5.2.6.2 Vapor-phase drying in the transformer tank If you have opened the kerosene drain plug already (e.g. after the transformer ratio test), you can begin the drying right away. Otherwise, you first have to open the kerosene drain plug before you can begin the drying. 1. Remove on-load tap-changer insert. Please request the documents for re- moval from Maschinenfabrik Reinhausen GmbH. 2. Unscrew kerosene drain plug in base of oil compartment clockwise. The kerosene drain plug cannot be unscrewed all the way. Figure 39: Kerosene drain plug 3. Insert on-load tap-changer insert. Please request the documents for installa- tion from Maschinenfabrik Reinhausen GmbH. 4349322/04 EN Mounting 47 4. Connect pipe connections R and Q of on-load tap-changer head to the kerosene vapor lead using one shared lead. Figure 40: Kerosene vapor lead 5. Seal off unused pipe connections and pipe bends with a suitable blank cover. Vapor-phase drying in the transformer tank 1. Supply kerosene vapor at a temperature of around 90°C. Keep this tempera- ture constant for 3 to 4 hours. 2. Increase the kerosene vapor temperature by approx. 10°C/hour to the de- sired final temperature of max. 125°C at the on-load tap-changer. 3. Vacuum-dry on-load tap-changer at between 105°C and maximum 125°C for at least 50 hours. 4. Residual pressure of no more than 10-3 bar. After drying, proceed as follows to close the kerosene drain plug again: 1. Remove on-load tap-changer insert. 2. NOTICE! An open kerosene drain plug leads to oil escaping from the oil compartment and therefore to damage to the on-load tap-changer. Close kerosene drain plug counter-clockwise (tightening torque 39 Nm). 3. Insert on-load tap-changer insert. 5.2.7 Filling the oil compartment of the on-load tap-changer with insulating fluid NOTICE Damage to the on-load tap-changer! Unsuitable insulating fluids cause damage to the on-load tap-changer. Only use insulating fluids [►Section 8.1.2, Page 154] approved by the man- ufacturer. 48 Mounting 4349322/04 EN After drying, completely fill the oil compartment (diverter switch insert fitted) with insulating fluid again as soon as possible so that an impermissible amount of humidity is not absorbed from the surroundings. 1. Establish a connecting lead between pipe connection E2 and one of the pipe connections R, S or Q to ensure equal pressure in the oil compartment and transformer during evacuation. Figure 41: Connecting lead between E2 and Q 2. Fill on-load tap-changer with new insulating fluid using one of the two free pipe connections of the on-load tap-changer head. Figure 42: Pipe connections S and R 4349322/04 EN Mounting 49 5.2.8 Performing transformer ratio test after drying NOTICE Damage to the on-load tap-changer! Damage to the on-load tap-changer due to transformer ratio test being incor- rectly performed. Ensure that the selector / de-energized tap changer is fully immersed in the insulating fluid and that the oil compartment of the on-load tap-changer is completely filled with insulating fluid. Only switch the on-load tap-changer from one operating position to the next via the upper gear unit. You can use a short tube (diameter 25 mm) with screwed-in coupling bolt (diameter 12 mm) with a hand wheel or crank for this, for example. When using a drill, do not exceed a maximum speed of 250 rpm. Always check the operating position reached through the inspection win- dow in the on-load tap-changer head cover. Never overshoot the end posi- tions, which are indicated in the connection diagram supplied with the de- livery. For multiple-column applications with a shared drive, link all on-load tap- changer heads to one another using the horizontal drive shaft part. When actuating the change-over selector, a higher torque is required. i 1. Switch the on-load tap-changer into the desired operating position. The di- verter switch operation can be heard distinctly. 2. NOTICE! An incomplete tap-change operation may damage the on-load tap- changer. After operating the diverter switch, continue to crank the drive shaft of the upper gear unit for 2.5 revolutions in the same direction in order to cor- rectly complete the tap-change operation. 3. Perform the transformer ratio test. 4. Repeat the transformer ratio test in all operating positions. 5. Switch the on-load tap-changer into adjustment position (see the accompa- nying connection diagram for the on-load tap-changer). 50 Mounting 4349322/04 EN 5.3 Installing on-load tap-changer in transformer (bell-type tank version) 5.3.1 Inserting on-load tap-changer into supporting structure 1. Remove the red-colored packaging material and the transport material from the on-load tap-changer. 2. NOTICE! Tensile forces can lead to damage and malfunctions on the on-load tap-changer. Using spacers, insert on-load tap-changer vertically into sup- porting structure (maximum 1° deviation from the vertical) so that the on- load tap-changer reaches its final installation height and only has to be raised a maximum of 5 to 20 mm after fitting the bell-type tank. Figure 43: Supporting structure 1 Supporting flange 2 Spacer 3 Supporting structure 3. Temporarily fasten the on-load tap-changer to the supporting structure. The supporting flange has through holes for this purpose. Figure 44: Temporary fastening 4349322/04 EN Mounting 51 5.3.2 Connecting the tap winding and on-load tap-changer take-off lead NOTICE Damage to the on-load tap-changer! Connecting leads which place mechanical strain on the on-load tap-changer will damage the on-load tap-changer! Establish and secure connections with care. Do not twist connection contacts. Connect connecting leads without warping or deforming. If necessary use an expansion loop for connecting leads. The designations of the on-load tap-changer's connection contacts are shown in the connection diagram. The connection contacts are provided with vertical through-holes (11 mm diameter for M10 screws, see appendix). 1. Connect tap winding and on-load tap-changer take-off lead in accordance with the connection diagram included with the delivery. 2. If connection leads have to cross the open surface of the oil compartment/ change-over selector, there must be a clearance of 50 mm between the con- necting leads and the surface of the oil compartment/change-over selector. Figure 45: Minimum distance 52 Mounting 4349322/04 EN 5.3.3 Performing transformer ratio test before drying NOTICE Damage to the on-load tap-changer! Damage to the on-load tap-changer due to transformer ratio test being incor- rectly performed. Do not perform more than 250 tap-change operations on the on-load tap- changer. If more than 250 tap-change operations are to be performed, completely fill the oil compartment with insulating fluid and lubricate slid- ing surfaces of contacts on the selector and selector gear with insulating fluid. Only switch the on-load tap-changer from one operating position to the next via the upper gear unit. You can use a short tube (diameter 25 mm) with screwed-in coupling bolt (diameter 12 mm) with a hand wheel or crank for this, for example. When using a drill, do not exceed a maximum speed of 250 rpm. Always check the operating position reached through the inspection win- dow in the on-load tap-changer head cover. Never overshoot the end posi- tions, which are indicated in the connection diagram supplied with the de- livery. For multiple-column applications with a shared drive, link all on-load tap- changer heads to one another using the horizontal drive shaft parts. When actuating the change-over selector, a higher torque is required. i 1. Switch the on-load tap-changer into the desired operating position. The di- verter switch operation can be heard distinctly. 2. NOTICE! An incomplete tap-chang