Power Supply Installation PDF
Document Details
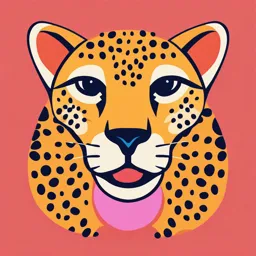
Uploaded by SolicitousOklahomaCity
null
Tags
Summary
This document discusses power supply installation, focusing on remote control equipment and SCADA systems. It covers the history of these systems, various components, and their applications in the electric power industry.
Full Transcript
REMOTE CONTROL EQUIPMENT 7.1 Introduction A Remote Contral Centre (RCC) is set up near the Traffic Control Office on each Division having electric traction, to work in close liaison with the traffic control. The RCC includes the main control room, equipment room Uninterrupted Power Supply (UPS) r...
REMOTE CONTROL EQUIPMENT 7.1 Introduction A Remote Contral Centre (RCC) is set up near the Traffic Control Office on each Division having electric traction, to work in close liaison with the traffic control. The RCC includes the main control room, equipment room Uninterrupted Power Supply (UPS) room. Remote Control Laboratory and Battery Room and is the nerve centre of the Traction Power Control Types Of Equipment The FMVFT equipment (stronger type equipment) was in use for all electrification schemes prior to 1980. Being mainly all relay system. the equipment has become outdated. Salient features of the system can be seen in ealier print of this book. The SCADA equipment based on State of the art technology has come into use after 1980. Considering the fast growth and development of computer based equipment. newer types with enhanced capabilities and new makes are being introduced. Addional facilities at each new RCC is also natural as new features get incorporated. 7.2 SCADA - TRENDS Supervisory Control is generally defined; “ as a form of remote control comprising an arrangement for selective control of remotely located units, by electrical means, over one or more common interconnecting channels”. In the Electric Power industry, supervisory control may be used in as simple an application as controlling a single distribution feeder. In its most complex form, referred to as Supervisory Control and Data Acquisition (SCADA) system, it may control all generation, transmission and distribution over a wide geographical area, from one centralized location. There were undoubtedly many methods of remote control invented by early pioneers in the supervisory control field, and long since forgotten. For sure, SCADA did not begin with electronic sensors and analog to digital coverters; but with a person reading a measurement and taking some mechanical control action as a result of that measurement. From 1900 to early 1920’s many varieties of remote control and supervisory systems were developed. Most of these, however were of one class or the other i.e. either remote control or remote supervision. Perhaps one of the earliest forerunners of modern supervisory control was a system designed by John Harlow in 1921. This system automatically detected a change of status at a remote station and reported this change to a control centre. In 1923, John Bellamy and Rodney Richardson developed a remote control system employing an equivalent of our modern “Check-before-operation” technique to ensure the validity of a selected control point before actual control was inintiated. Perhaps the first logging system was designed in 1927. This system monitored information from a remote location and printed any change in the status of the equipment. together with the time and date when the change took place. At this time, of course, there was a little choice in the type of components available, thus, all of these systems were electro-mechanical. 121 Just as the requirements of supervisory control system years ago were rather simple, so were many of the tecniques employed Naturally, as the scope of the supervisory control applications changed, so did many of the fundamentals of supervisory conrols technology. Coding patterns were improved to provide higher security and more efficiency. Communication tecniques were changed to permit higher speeds of transmission. The advent of solid state circuitry opened vast new possibilities in both operation and capabilities. 7.2.1 WHAT IS SUPERVISORY CONTROL? Supervisory Control is a collection that will provide an operator, at a remote location, with enough information to determine the status of a substation or generating station and to cause actions or operations to take place at that station without being physically present. Although a supervisory control system may exist to perform control and data acquisition at one specific location, the normal arrangement is to have one central location receiving data and exercising control over many remote stations 7.2.2 WHY INSTALL SUPERVISORY CONTROL? The usual reason for installing supervisory control systems is to provide the system operators with sufficient information and control to operate the power system, or some part of it, in a safe, secure and economical manner. Before taking decision to install a SCADA system, certain factors are to be clearly defined. These factors are as follows :- 7.2.2.1 Who are users of data? In a typical case, the user can be Operators for controlling the system, Maintenance deparment for maintaining the power supply equipment, Management for decision making and System Designer for designing a better system. 7.2.2.2 What data is available and/or neccessary? As theoretically it is possible to gather data pertaining to each and every event or activity on the power system, a judicial balance has to be kept between available finances as well as identification of all potential users and there requirements. 7.2.2.3 What are the user requrements? As the SCADA is being designed for the use of power system operators, their needs have to be serviced first. Firstly, the operator requires only that data, which will quickly and positively alert him to a problem and give ‘him the means to take corrective action in a timely manner. So a sort of filter has to be built in the system to isolate and present the useful data only, to the operator. Then the data has to be in real time for the operator. Almost all other users have a need of the data for carrying out some postmortem operations. This imposes a time constraint on the system for collecting and reporting of data. Second important need is orgainsed presentation of the data, which should be made available for which the size of bulk memory has to be fixed. Thirdly, means to get hard copy of data in a chronological order should be made available, for which the size of bulk memory has to be fixed. And lastly, feature for getting summary of varous events/records should be possible. 122 7.2.2.4 What is the type of display required? Data displays are generally visual, recorded, or audible. In visual category would come VDUs, Mimic Diagram Board, strip chart recorders, lights and other forms of displays. The recorded format is generally some sort of hard copy obtained from the logger. Most common audible data output is in the form of a bell or hooter to call the attention of the operator. 7.2.2.5 Other factors These can be regarding training of Operators, maintainance personnel and System designer for carrying out modification in the system, based on the requirement. There can also be cases where a new system is to be put along side and older system, thereby requiring special attention regarding power supply, cable route and related problems of working them in parallel. 7.2.3 CONSIDERATIONS IN APPLYING SUPERVISORY CONTROL AND DATA ACQUISITION SYSTEM TO ELECTRIC UTILITY STATIONS. Supervisory control and telemetering installations have grown conceptually from simple, isolated, remote control facilities interconnecting to nearby stations and telemetering a few key system quanitites to an operations centre to large scale, computerized, supervisory control and data acquisition (SCADA) systems. The data acquisation functions provide access to large portions of the power system, delivering real-time date and high quality input to planning data bases. Control capabilities relieve demands for operating personnel and serve as primary tools for emergency switching and load shedding. In SCADA installations, both large and small, reliability, accuracy, dependability and security are qualities which must be designed into the power station (remoter terminal) end from its inception to realise satisfactory performance. An electric utility SCADA system depends on the interface between the power station and the SCADA Remote Terminal Unit (RTU) to provide and maintain the high level of confidence demanded for power system operation. Following is the description of typical functions provided in utility SCADA systems, and some important considerations in the interface between a power station and SCADA system. 7.2.3.1 Physical consideration the station enviornment The implementation of a SCADA system in an electric utility requires the instatllation of remote terminal units (RTU’s) in generation and switching stations to allow the master station to retrieve data and execute control commands. The RTU interfaces to control station equipment through interposing relays and to measuring circuits through transducers. The environment of a power station or substation is less than ideal for electronic equipment like SCADA system remote teminal units and transducers. The temprerature changes stress the stability of measuring components like analog to digital converters and transducers. Good temperature stability is an important feature of SCADA system equipment. 123 The use of hermetically sealed components, coated cirucit boards and corrosion protected handware should be a consideration selecting SCADA equipment for outdoor installation. The electrical environment of a power station is more servere than its physical environment Large amounts of electrical noise and transients can be generated by the operation of power equipment and their controls. These can be minimised through shielding and surge reduction practices. Ground potentical during faults can also affect electronic equipment in station making a solid ground mass essential. 7.2.3.2 Analog data acquisition Data Acquisition in an electric utility SCADA system concentrates on the power sytem performance quantities, line and transformer load currents, real and sometimes reactive power flow and bus voltage. Secondary quanitites such as transformer temperature, transformer tap position, or other multiple position quanitities are also transmitted in analog format. The principal electrical quantities (volts, amps) are measured from power system instrument transformers with transducers. There are convert to DC voltages or currents which can be readily accepted by the SCADA system remote terminal unit. The value received from scada system measurements is a funtion of the investment made in their measurement sub systems. 7.2.3.2.1 Measuring system performance The overall accuracy of transmitted quantities is affected by a number of factors. These include instrument tranformer errors, transucer performance, analog to digital conversion quantizing error, and offsets introduced in transducers and A/D converters. 7.2.3.2.2 Instrument Transformer Performance Analog quantities can be no more accurate than the instrucment tranformers used for their measurement. When metering grade tranformers are available they will provide the best accuracy. 7.2.3.2.3 Transducers The measuring interface element between a SCADA system and a power system is the transducer. These provide scaled, low energy signal which represents a power system quantity that the RTU can easily accept. Transducers also isolate and buffer the RTU from the power system and station environments. Their outputs are usually D.C. voltages or currents which range upwards of a few tens of volts or milliamperes. Transducers meausing power sytem electical quintities are generally designed to be compatible with instrument transformer outputs. Potential inputs are based around 110 to 120 volts A.C. and current inputs accept 0-5 Amps. These are for the most part, long time steady state ratings. Input circuits are provided with short time, over range, capabilities so that they may survive power system disturbances which may produce abnormally high voltage or currents, many times higher than rated for short durations. 124 7.2.3.3 Status monitoring Status indications are an important function of SCADA systems for electrical utility. Status monitoring is often provided for power circuit breakers, recolsures, interruptor, motor operated isolators, any variety of other ON-OFF functions in a power station. They may be provided with status change memory for between scan monitoring and in some cases, time tagging to provide sequence of events. These indications originate from contacts which are mechanically actuated by the monitored device and are input to the RTU, either directly or through an interposing relay. Interposing relay is required because there are seldom enough spare auxiliary switch contacts available, and the distance between the RTU and the monitored device is often great. The exposure of RTU status point wiring to the switch yard environment is also consideration. 7.2.3.4 Control functions The supervisory control functions of electric utility SCADA system provide routine and emergency switching and operating capability for station equipment. SCADA control is most often provided for circuit breakers, reclosures, interruptors, and motor operated isolators. It is not uncommon to also include control for voltage regulators & tap changing transformers. All these control functions share a common thing that station control functions must be interfaced to the SCADA system remote terminal. The RTU can not execute controls directly form its logic level, but must be interposed to the station control circuits. Also, RTUs generally provide momentrary timed control output thus, latching type interposing is sometimes required. The design of control interface for SCADA system deserves careful attention. The security of the equipment installed must ensure freedom from false operation, and the design of operating and testing procedure must recognise these risks and minimise them. 7.2.4 MASTER/REMOTE FUNCTIONAL DESIGN 7.2.4.1 Communication configuration, media and techniques Communication configuration The configuration of communication systems are dictated by the following :- * Number of RTUs * Number of points at RTUs and required update rates * Location of RTUs * Communication facilities availbale * Communication equipment and technique available 125 The configuration used in Railway SCADA system is party line one-on-a-few configuration. Here master station communicates with the RTUs via party line (shared) communication channel. In this case a unique address is required for each RTU on the channel. This Configuration has the advantages of sharing the master station communication logic and the advantage of sharing the communication channel. 7.2.4.2 Communication Media Availbale communication media options are * Metallic cable pairs * Power line carrier (not used in indian Railways) * Microwave * Leased circuits * Fiber optic cable * Satellites (not used in Indian Railways) As on date only metalic cable pairs and fiber optic cable are of interest, only these options are discussed below :- 7.2.4.3 Metallic cable pairs Cables have the advantage of involving little new technology and so it is easy to consider the use of cable pairs for data transmission, where typically, one such pair can be used for simplex or half duplex transmission at speeds upto 2400 bits per second. Cables, as with S&T installations must typically be protected against induced voltage surges or lightening strikes by protective devices such as gas tube protectors and in addition if entering a high voltage substation, must be protected from huge difference in adjacent ground mat potential during substation fault current conditions through the use of addtional devices such as neutralising transormers. 7.2.4.4 Fiber Optic Cable Fiber optic cable sytems that are used for communications are made of three basic components. The first component is a long fiber of very pure glass or plastic that permits light to travel from the transmitor to the third component i.e. receiver. The reveiver converts the light signals back into electrical signals. The signals can be either analog or digital. In addition to these three components, there are repeater where the light signals are converted to electrical signals amplified and converted back again. Splicing devices are also necessary in order for signals to travel from one fiber to the others with minimum attenuation. 126 The basic principle behind fiber optic is that when light reaches the boundry between the medium that it is in an another medium, it will be reflected back into its own medium, if the other medium has a lower index of refration. Therefore, an optical fiber is constructed as a long cylindrical glass or plastic core surrounded by a concertric layer called the cladding which has lower index of refraction. Most light entering the core at one end will be reflected back forth all the way down the length of the fiber to the other end. 7.2.4.5 Advantages of Optical Fiber communication A prime advantage to electric power utilities is its total immunity to the electromagnetic interferance. The band width available in the visible light region of the electromagnetic spectrum for communications via fiber optics is very wide as compared to metallic cable pairs. Cross talk between cables is impossible Unaffected by lightening and electrical storm Highly flexible and small physical size. As with a metalic cable, “Shorting” of a fiber optic cable cannot lead to invalid control signals or start a fire in hazardous environment. No trapping or waves dropping is possible without physically cutting the cable and coupling in. Long life expectancy. Very high speed of data transmission which is limited principally by the capability of the multiplexing equipment. 7.2.4.6 Disadvantages of optical fiber communication. High Cost. More no. of repeaters are required as compared to metallic cable pairs. Transmitors and receivers are required to convert electrical signals into light and back again. Thus, short run cables would not be cost effective, unless advantages, such as large band width capability, outweight the cost of transmitor and receivers. Special connectors are needed to align fibers and require training to install. 7.2.5 COMMUNICATION TECHNIQUES. 7.2.5.1 In order to convey information from one point to another via a communication channel it is necessary to transmit a signal at one point which is recognised at the other point. 127 This may be accomplished by several methods :- * Change of signal amplitude (Amplitude Modulation) * Change of signal frequency (Frequency Shift Keying) * Change of signal phase (Phase Shift Keying) At the receiving end of the communication chennel, a demodulator detects the change in the signal and outputs the transmitted information. If the information is transmitted in one direction only this is known as Simplex transmission. If the information flow takes place in both directions, but not simultaneously then it is known as half-duplex transmission. However, if transmission takes place in both the directions simultaneously, then it is known as Full-duplex transmission. In Railway we use Half-duplex transmission. For Half & Full-duplex transmission, both a moduloator and demodulator are required at both ends of the channel. From view point of economy, a single communcaion channel is used for transmitting many pieces of information. This techinque is known as Multiplexing. Two basis versions are : * Frequency Division Multiplexing, where each piece of information is transmitted over a dedicated part of the available communication channel. For a voice grade channel, upto 25 separate, sub channels 120 Hz. spacing per channel, can be utilised Additional voice grade channels are required for each 25 pieces of information, therefore, large systems would require an impractical number of channels. * Time Division Multiplexing, where each piece of information is transmitted as part of a serial digital message over a separate span of time and demultiplexed by the receiver into the individual pieces of information. The rate at which data is transmitted is measured in bits per second or baud. However, these two units are not always synonimous. Baud is defined as 1/length of shortest signaling element in seconds; if the shortest element is 0.833m.secs., then the signaling rate is 1200 baud (or changes per second). In order to determine bits per second, following formula is used : Bits/seconds = Baud x bits/baud Where Baud = Signaling rate (changes per second) Bits per baud = Amount of information (bits per change) For transmitting information via a communication channel, two basic types of modems are used : Asynchronous and synchronous. The asynchronouos type utilises separate timing sources such as crystals at each end of a data link to make the receiver to demoudulate the data at approximately the same rate at which it was modulated by the transmitter. Due to this, the data message must 128 be frequently resynchronised by dividing the message into short blocks of characters, each with their own synchronisation bits. This is advantageous where short messages with quick synchronisation is desired. Thus, the efficiency is relatively high. The asynchronous modem is limited to 1800 bps in most applications and is usually of the FSK type. Cost is very low. The synchronous modem on the other hand transmits a synchronising clock signal alongwith the data, so that the receiver is precisely synchronised with the transmitor. This permits very long message and high data rates without any problem of falling out of sync. Sync. modems are generally available from 2400 bps to 1 Mbps and are higher in cost. 7.2.5.2 Communication message formats The transmission of information between master and remote using TDM techniques requires the use of serial digital messges. These message must be efficient, secure, flexible and easily inplemented in hardware and software. Efficiency is defined as - Infromation bits transmitted/total bits transmitted. Security is the ability to detect errors in the original information transmitted, caused by noise on the channel. Flexibility allows different amounts and types of information to be transmitted upon command by the master station. Implementation in hardware and software requires the minimum uncomplicated logic, memory, storage, and speed of operation. 7.2.5.3 All message are divided into three parts as follows * Message establishment, providing the signals for the receiver to select the message transmitted to it at the correct time, from hundreds of other possible messages and channel noise. * Information, which provides the data to be sent to the receiver, in coded form to allow the receiver to decode the information and properly utilise it. * Message termination, which provides the message security checks so that no errors in the message establishment of information fields are accepted by the receiver and provides a mean of denoting the end of the message. Message security checks consists of logical operations on the data which results in a pre-defined number of check bits transmitted with the message. At the reveicer end the same operation are performed on the data and compared with the received check bits. If they are identical, the message is accepted; otherwise, a retransmission of the original message is requested. 129 A typical example of commonly used asynchronous message format is shown below : 2 bits 4 bits 8 bits 12 bits 5 bits 1 bit 8 msec BCH Add. RTU Fund pre Tx S M M Mess Address Code Sec mark Code age Synchronisation End of message (Message Establishment) (Information) (Message Termination) The Message Establishment field has three components : 8 mesc min. pretransmission mark to condition modern receiver for syncbits. Synchronisation, which consists of two bits, a space followed by a mark. RTU address, which allows a receiver to select the message addressed to it from the message to all the RTUs on a party-line. The information field contains 20 bits, of which 8 bits are function code and 12 bits are used for data. For remote to master message, this represents the first message in the sequence; additional messages directly following the first message also transmit information in the RTU address and function code spaces, so that 24 of data are transmitted. These 24 bits may contain two 12 bit analog values or 24 bits 24 device status. 7.2.5.4 The message termination field contains BCH security code, which has 5 bits and allows the receiving logic to detect most message errors. If an error is detected, the message may then be retransmitted to obtain a correct message. End of message mark, which provides the last bit as a mark, so that another message can follow immediately after this message. 7.2.6 INFORMATION TRANSFER 7.2.6.1 Master to remote data transfer : Information transmitted from master to remote is for the purpose of device control, set point control, or batch data transfer. Due to the possible severe consequences of operating the wrong device or receiving a bad control message, additional secruity is required for control, this is provided in the form of a sequence of messages, commonly called select before operate sequence, as shown below :- 130 REMOTE - TO - MASTER CHECKBACK MESSAGE FUNCTION CODE CONTROL ADDRESS SET POINT MASTER-TO-REMOTE EXECUTE MESSAGE FUNCTION CODE CONTROL ADDRESS REMOTE TO MASTER EXECUTE ACKNOWLEDGE MESSAGE FUNCTION CODE CONTROL ADDRESS NOTES :- 1. Message establishment and termination fields are not shown. 2. Function code specifies the operation to be preformed by the RTU. 3. Control address specifies the device or said point to be controlled. 4. SET point provides the value to be aacepted by the RTU. 5. A remote to master check back message is drived from the RTU point selection hardware in order to verify that the RTU has acted correctly in interpreting the control selection. 6. A master to remote execute message is transmitted only upon receipt of proper check back message. 7. A master to remote execute acknowledge message is a positive indication the desired control action was initiated. 131 7.2.6.2The above sequence of message provides additional security by the check back and execute messages, since undetected errors must occur in the control. select, check back, and execute message in order to operate the wrong control device. Prior to transmission of the above sequence a control operator performs a similar select-verify-execute-acknowledge sequence via his control console. Batch data transfers from master to remote include such data as parameters for report by exception and parameters for locally controlled devices. This type of transfer is accomplished by the sequence given below :- MASTER - TO - REMOTE CONTROL MESSAGE FUNCTION CODE DATA ADDRESS REMOTE TO MASTER ACK MESSAGE FUNCTION CODE DATA ADDRESS MASTER-TO-REMOTE CONTROL BATCH DATA TRANSFER MESSAGE FUNCTION CODE DATA ADDRESS DATA REMOTE-TO-MASTER ACK MESSAGE FUNCTION CODE DATA ADDRESS Notes :- 1. Message establishment and message termination fields are not shown. 2. Special security precautions are required if a party line communication channel is used, so that RTUs do not decode a batch data transfer message. The purpose of first two messages is to prepare the RTU to receive the longer than normal message. The third message transmits the data and the fourth indicates that the data was correctly received at the RTU. 132 7.2.6.3 Remote to master data transfer All remote to master data transfer is accomplished with one basic message sequence by using variations in the field definations to accommodate different types of data. The basic seqence is shown below :- MASTER-TO-REMOTE DATA REQUEST MESSAGE FUNCTION CODE DATA IDENTIFICATION REMOTE - TO - MASTER DATA MESSAGE DATA UNIT 1 DATA UNIT 2 DATA UNIT Notes :- 1. Message establishment and message termination fields are shown. 2. Function code specifies the types of data to be transferred by the RTU. 3. Data identification identifies the amount and type of requrested by the master station. On each message transmitted by the RTU (except for message containing only current data) it is necessary to retain the transmitted message in a RTU buffer, so that if the master station does not receive the message correctly, it can request a retransmission. Otherwise this information would be lost. 133 7.3 SCADA EQUIPMENT 7.3.1 General The SCADA equipment at the RCC is called Master Station while that of the controlled station is referred to as Remote Terminal Unit (RTU). 7.3.2 Transmission Path Underground telecommunication trunk cable is provided for transmitting the signals from and to the RCC and the controlled Remote Terminla Units (RTU). Three pairs of conductors (One pair for “Send”, one pair for “receive” and the third as spare) from this cables are made available for remote control operation. These days optical fibre cables are used in most of the divisions instead of above mentioned copper cables. Sometimes, microwave communications is used. 7.3.3 Isolating Transformers To limit the build up of longitudinal induced voltage on account of induction effects of 25 kV traction, isolating transformers are provided on the cable circuit at intervals of 10 to 15 km. The cable is tapped at the RCC and each controlled station and 3 pairs of conductors are terminated on a terminal board. Isolating transformer of impedance ratio 1120 : 1120 is provided at the point of tapping. 7.3.4 Repeater Stations Voice frequency repeaters are provided at intervals of 40 50 km to boost the signal and make good the been attenuation. The amplifier gain at the repeater station is about 20 dB. with an equilser incorporated to compensate upto 0.02 dB/kHz/km Depending upon the distance the repeater gain is state that the signal level at any point enroute is within cenrtain prescribed limits. It the lead is long suitable surge arrestors are provided inside the equipment room to ---- the ----. The metalic sheath of the lead in cable shall also be kept insulated from the earth system of the switching station to prevent induction effect. the insulated conductor alone being led into control panels for the same reason switching station earthing. LT 240 V auxihary transformer neutral earthing and earth of R C equipment are all kept separate and distinct and are NOT interconnected In addition the switching station structure should be solidiy bonded to the track rails by two independent connections. 7.3.5 Microwave Communication In some of the sections on Indian Railways didicated Microwave channel at carner frequency of 18 GHz has been provided for the purpose of communication. 7.3.6 Optical Fibre Cable Optical fibre cable has also been introduced for communication in some sections of Indian Railways which is also used for RC equipment Details of the interface between the latest communication systems and the RCC/RTU equipment may be seen in the relevant technical documents. 7.3.7 Master Station Equipment Hardware Configuration: Dual main micro-computer/mini-computer system. one main and the other hot standby. is provided at the master-station. each system interfaces whtih its front end processors. If any. and modem for communication with RTUs and with the man-machine interface equipment to provied up-to-date network data and to accept commands. Each system has its own 134 system console and hard and floppy disks along wiht their drives. Watch dogs are provided for monitoring the health of the computer system. In case of failure of one omputer system, the standby takes over automatically. Two data-logging printers, one on-line and other as standby, are provided, both being connected to the same online computer system. In case of failure of one printer, the other printer automatically takes over. Man-Machine-Interface : Work Stations Two work-stations, one for each of the two operators each consisting of two semi-graphic colour Visual Display Units (VDUs) and a key-board are provided at the RCC. The key board contains both functional keys for operations that are repeated frequently and alpha-numeric key for input of numerical data and text. Both workstations are connected to the same on-line computer and mee the following requirements: (i) Normally control pre-defined and physically demarcated sections. (ii) In case of complete outage of one workstation. all of its functions can be transferred to the healthy workstation, so that normal operations can continue. (iii) Normally one VDU is on line and the other acts as standby at each work station. However, if so needed, it is possible to have both VDUs of each work station on lines simultaneously, either of the two VDUs being used for viewing diagram for telecontrol purposes and the other for viewing alarm, on-demand trend curves, histograms or any other data. 7.3.8 Mimic Diagram Board (MDB) A mimic diagram board and its associated mimic dnver is provided at the RCC. The MDB depicts the traction power supply diagram, indicating the energize/de energize condition of the sub-sectors of the catenary. status of the interuptors and CBs at TSS & FP, SSP and SP Unlike in the Conventiona ! Mimic Diagram Board used in RCCs prior introduction of SCADA system (See para 20403) all contrll Operations are camed out from the key board(s) provided at the work stations(s) The Mimic Diagram Board’s sole purpose is. therefore to give an overa.” view of the traction power wupply, system to the operator Size of the MDB is therfore very much smaller. It is the intention to do away with the MDB altogether since the system can be viewed in the VDUs 7.3.9 Annunciations Controlled Station “Remote Station Defective” is annunciated by a LED Master Station The following annunciations by LEDs are provided on the MDB i) Main System “ON” ii) Standby System “ON” iii) Main System Defective. iv) Standby System Defective v) Main UPS Failed vi) Standby UPS Failed vii) UPS battery low (below 90% of nominal voltage) viii) 415 V, ac, 3 ph, supply to UPS failed 135 7.3.10 SCADA Software The operating system used is suitable for multi-user, multi-tasking, net working and real time applications. 7.3.11 VDU Display The application software supports a large number of versatile semi-graphic coloured displays for issuing telecommands, blocking/deblocking the controlled points. viewing alarm listing, event listing or for carrying out special functions. For details of these displays. manufacturers Operating Manual may be referred to. Calling any of the VDU displays is by simple keyboard operation, with pre-defined options available for the order and manner in which displays are called. 7.3.12 Transmission and Coding System The master station equipment normally scans continuously all the RTUs in a pre-defined cyclic sequence to update the equipment status, alarms, events and measurands. Exchange of information between Master Station and RTUs takes place on interrogation by master followed by reply from RTU. The communication technique is based on Digital Address Time Division Multiplexing. Every data exchange is based on well defined transmission protocol. Each transmitted contains sufficient parity check bits do detect transmission errors. 7.3.13 Historical Data Storage The SCADA system is designed to cater for historical data storage of traction power supply data for a period of one year. This includes. i) All alams / events / -- of controlled stations and all system alarms ii) Day wise stronge of average feeder current and voltage dating the day maximum demand maximum and minimum feeder voltage in the 25 KV side. total number of operations of feeder protective relays viz OCR. DPR and WPC relays CB trippings and maximum and minimum OHE voltage on both sides of the neutral section A memory capacity of 40 MB is provided for this purpose in the hard disk with provision for further expansion of the memory as required. 7.3.14 UPS and Batteries at Rcc Dual Stand alone UPS System of adequate capacity to supply 240 V and 50Hz single phase supply to the SCADA system at Master Station is provided. Both the UPS work in parallel sharing the load. In case of failure of one. the entire load is automatically taken over by the healthy UPS without affecting the working of the system. In case of both the UPS at the same time. the load of SCADA equipment is directly connected to input mains through a static switch without any break. A single battery is provided with both the UPS with adequate Ah capacity to provide 2 h supply to various equipments in case of failure of input 415 V ac 50 Hz supply. 7.3.15 Remote Terminal Unit (RTU) The RTU is microprocessor based and includes its associated digital input/output modules. alanninput modules. analog input modules. watchdog transducers. memery modules. interposting relays. summation. CTs power supply unit(s). surge arrestors and other items necessary for its proper working. 7.3.16 Storage of Events and Alarms All changes (one or more) in the status of the CBs/interruptors / motor-operated isolators and alarms that may occur between consective polilngs are stores by RTU until they are reported to the master station. This is to eliminate any loss in reporting to the master station due to 136 intermittent failuers of channel or any other reason. In other words, no event is lost without its being reported to master station. 7.3.17 SCADA Equipment Capacity The SCADA equipment is generally disigned for the following tele commands. telesignals and telemetered parameters for a typical TSS. SP & SSP of a double line section : S. No Controlled Telecommand Telesignal Measurands Station 1. TSS 24 64 8 2. SP 8 12 4 3. SSP 8 12 - Number of controlled stations (TSS, SP, SSPs) to be controlled from an RCC will be as per the requirement of the section. Speed of Transmission and Update Time The communication between the master station and the RTUs is at a suitable transmission speed not exceeding 600 baud. Normal polling time for updating status. alarm and measureands for the designed capacity is not more than 4 sec for 20 controlled stations and not more then 6 sec for 30 controlled stations. The actual timings amy slightly vary depanding on communication protocol adoped and the system design. The RCC should be in the middle of the electrified section if the number of controlled stations exceeds 30 so that scanning on either side is possible and update time kept to the minimum. The RCC should be in the middle of the electrified section if the number of controlled stations exceeds 30 so that scanning on either side is possible and update time kept to the minimum. 7.3.18 Modems (i) The modems (modutor/demodulators) provided for communication between the master station and the RTUs utilize frequency shift keying (FSK) modulation and include send, reveive and timing functions. The send and receive functions are independently programmed as required. The modern work satisfactorily upto an input signal level of -45 dBm (ii) The modern also incorporates necessary amplifier having a minimum gain of 30 db to compensate for any signal variation at different points in the system Suitable attencuation is provided within the amplifier to adjust the level through trimpot/rotary switch. It has an output signal level adjustable between 0 and -30 dbm in steps of 1 dbm 7.3.19 Special Features in SCADA Equipment The following additional features are incorporated in the SCADA equipment (i) Tripping of bridging interrupers on under voltage at SP in extended feed condition (ii) Inter lock release request facility for circuit breakers/interruptors control at boundary post (for guidelines for these iner locks see RDSO’s letter No ETI/PSI/RC/SPEC 19 dated 10.3.1989) (iii) Control of shunt capacitor bank and monitoring of power factor (iv) Automatic localization of fault on OHE and isolation of faulty sub sector SCADA systems on Indian Railways are being supplied by various manufacturers Although the 137 systems are different, the basic features of the systems are similar. For details of operating instruction and maintenance the operating technical manuals of the makers should be referred to. 7.4 OPERATION AND MAINTENANCE OF RC EQUIPMENT 7.4.1 Duties of CTFO (RC) He is the senior supervisor working under the control of DEE/AEE (TrD) and directly reponsible for the proper operation and unkeep of the RC equipment. which are vital for the operation of the electric traction system. He shall be thoroughly conversant with all the technical details of the equipment under his control. In particular, he shall perform the following duties. 1. Maintain the RC equipment at the RCC and the controlled stations in accordance with the prescribed schedules. 2. Keep close liasion with the S&T department as to the sound condition of the cable pairs allotted for RC operation. 3. Measures periodically the levels of voice frequency signals at controlled stations and arrange with the S&T deparment for correction. when requried at their repeater stations 4. Keep in constant touch with the TPC on shift duty and ensure prompt rectification of defects reported in the RC system 5. Ensure proper maintenance of UPS/battery sets for uninterrupted operation of the RC equipment and the stand by generating set in the RCC. 6. Inspect the RC equipment at every controlled post once in two months 7. Import neccessory training to the staff under him in the special techniques of maintenance of R. C. Equipments as well as trouble shooting. 8. Ensure that the special instruments and tools provided for maintenance of the R. C. equipments are properly cared for. 9. Keep a watch on stocking of spare parts and other stores required for RC equipments and initiate timely action to recoup stocks. 10. Co-ordinate with SSE (PSI) amd SSE (OHE) or territorial SSE for manning the controlled, posts in the events of persisting faults in the R. C. equipments. 11. Submit prescribed periodical returns on RC equipment to AEE (TrD) and Sr. DEE (TrD). 12. Keep his superior officers fully informed of all important developments and seek their guidence when required. 13. Carry out such other duties as may be alloted by his superior officers. 14. Carry out minimum monthly inspection as per manufacturers recommendations. 7.4.2 Operation of RC Equipment The RCC is the nerve centre of the traction system from which full control over every switching opeation on the entitle electrified route is exercised. It should, therefore be kept in perfect operationg condition at all times. No one other than an authorized official shall at any time operate the equipment. The TPC shall at every change of shift carry out a lamp test and once a day give a general check for all stations and thereby ensure that the indications on the mimic panel are in order. Any defects observed in operation shall be brought to the notice of AEE(TRD) Depending upon upon the nature of the defect TPC shall take adequate precaustions against mal-operation until the defect 138 noticed is rectified. Should Rc equipment of a switching station fail completely, the failure shall be reported to AEE(TRD) and Sr. Dee(TRD) and arrangements made to man the switching station with trained personnel to carry out the switching operations, observing the preacutions prescribled in the Chapter VIII Breakdowns TPC shali once a day contact on telephone the Operators of each Grid sub-station from which traction power supply is obtained and ensure that the communication facilities are intact. 7.4.3 Investigation of Failures by SSE As with any other equipment every failure of RC equipment should be separately registered. investigated and rectified. making a brief note in the failure report of the action taken as well as classifying and finally pin-pointing the exact cause of the failure. The failure should be analyzed every month and any special staps required taken to overcome the trouble and prevent recurrence should be taken. A history sheet showing the faults that have occured on different items of equipment will assist in carrying out detained investigation of recurring troubles in consultation with the Manufacturers of the equipment. 7.4.4 Maintenance Schedule The specific maintenance instruction issued by the repective supplier of SRC/SCADA systems should be observed and changes to be made therein may be decided in consultation with the manufacturer For the batterires used in the remote control centre and the remote terminal units (RTUs) the instructions in Chapter II for forninghtly maintenance and quarterly maintenance shall be applicable. 139 140