Yarn Manufacturing Machinery - III PDF
Document Details
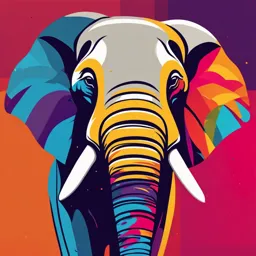
Uploaded by DelightedButtercup
DKTE Society's Textile & Engineering Institute Ichalkaranji
Dr. P. B. Malakane
Tags
Summary
This document from D.K.T.E's Textile & Engg. Inst. Ichalkaranji provides detailed information on yarn manufacturing machinery, particularly focusing on Comber Half Laps and Top Combs. It delves into technical specifications, operation, and self-cleaning effects relating to these specific machines.
Full Transcript
Nipper Movement The nipper with the batt move concentrically to circular comb to avoid unfavorable combing Comber Half Laps Comber Half Laps Nomenclature and specifications of unicomb: 1. Primacomb 5015 Sections No. of rows Diameter mm Surface...
Nipper Movement The nipper with the batt move concentrically to circular comb to avoid unfavorable combing Comber Half Laps Comber Half Laps Nomenclature and specifications of unicomb: 1. Primacomb 5015 Sections No. of rows Diameter mm Surface Total points First 5 second 7 Third 8 85 1110 28475 Fourth 11 Fifth 20 2. Primacomb 4014 Sections No. of rows Diameter mm Surface Total points First 5 second 7 80 900 22580 Third 8 Fourth 20 Comber Half Laps 3. Primacomb 5014 Sections No. of rows Diameter mm Surface Total points First 5 second 7 85 900 22580 Third 8 Fourth 20 4. Primacomb 5025 Sections No. of rows Diameter mm Surface Total points First 5 second 7 Third 8 85 1110 27720 Fourth 10 Fifth 18 Comber Half Laps 5. Primacomb 7015 Sections No. of rows Diameter mm Surface Total points First 3 second 5 85 900 25070 Third 10 Fourth 25 Top Comb Top Comb Density of needles defined as needles per cm Two types top combs are commonly used – 26 needles / cm and 30 needles / cm Top comb available in market are 23, 26, 28, 30, and 32 needles per cm Operation of Combs The circular comb can treat forward portion and top comb trailing portion of fibre fringe Top comb – single row of needles The quality of combing of both portions is the same Self-cleaning effect - During detaching less than 20% of the fibers in the nippers are pulled out Operation of Combs This low percentage of fibers is unable to take the impurities Impurities, neps, and short fibers therefore remain in the sheet During the next combing cycle elimination is performed by the circular comb Self-cleaning effect can be influenced by - Batt weight and degree of fibre parallelization Self-cleaning effect is better for - lower fibre parallelization and more voluminous the batt A thick sheet always exerts a greater retaining power than a thin one. Operation of Combs On the negative side a thick sheet applies a strong load to the comb and uncontrolled combing. The unfavourable effect of overloading the comb is greater than the favourable effect of the retaining power of the sheet. A compromise must therefore be struck between quality and productivity The ideal sheet fineness now normally lies between 55 and 75 ktex.