A Technical Guide on Derailments PDF
Document Details
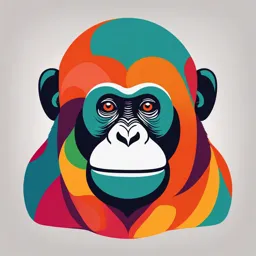
Uploaded by ImaginativePeachTree
STC/JHS
1998
Tags
Summary
This document provides a technical guide on the inspection of rolling stock, focusing on wheel gauge measurements and potential issues, such as bent axles, and tyre profiles. It includes diagrams and tables related to the specifications of the wheel and rolling stock in railways. The document seems to be an excerpt/guide.
Full Transcript
CAMTECH/M/3 34 CHAPTER 3 INSPECTION OF ROLLING STOCK The rolling stock involved in accident must be inspected in the presence of nominated team of supervisors and results should be recorded in the prescribed for...
CAMTECH/M/3 34 CHAPTER 3 INSPECTION OF ROLLING STOCK The rolling stock involved in accident must be inspected in the presence of nominated team of supervisors and results should be recorded in the prescribed format (Appendix ‘A’). The main items of inspection are as under : 3.1 WHEEL GAUGE Wheel gauge is the distance between inside faces of the flange on the right and left side wheels of an axle (Fig. 3.1). There should be no variation in the values of wheel gauge - measured at four points 90 degrees apart on a wheel set. However the actual value of the wheel gauge can vary as per - tolerances given in Table 3.1 (IRCA Part III Para. 2.8.7) : Table 3.1 B.G. M.G. Standard 1600 mm 930mm Maximum 1602mm 932mm Minimum 1599mm 929mm A TECHNICAL GUIDE ON DERAILMENTS April ‘98 CAMTECH/M/3 35 Fig. 3.1 Measurement of Wheel Gauge The wheels are required to be gauged at three or four - quarters (as per possibility) and recorded duly indicating the following: Tightness or slackness of gauge Whether any indication exists about shifting of wheel on the axle. Note : It must be ensured that the back surface of wheels are cleaned thoroughly before measuring the wheel gauge in order to avoid erroneous readings. 3.1.1 If the wheel gauge is more than permissible limit, there exists a possibility of a relatively newer wheel hitting the nose of crossing. This happens because the wheel gauge is one of the parameters affecting the clearance at check rail opposite the nose of crossing. A TECHNICAL GUIDE ON DERAILMENTS April ‘98 CAMTECH/M/3 36 3.1.2 If the wheel gauge is less than minimum value, there is a possibility of wheel hitting at the back of a tongue rail while passing through the switch and thus damaging the tongue rail. 3.1.3 The variation in wheel gauge after lowering the coach body on wheels was examined by RDSO Lucknow and circulated to all Railways vide their letter no. MC/WA/GENL Dated 27.6.88 as follows : “ The question of variation in the wheel gauge under no-load and loaded condition has been examined by RDSO. The calculations for the 15 ton BG axle under tare load condition indicates that a variation of about 3 mm in the wheel gauge when measured at the top and bottom locations in the vertical plane is likely to take place due to bending of axle under coach load This variation in wheel gauge under loaded condition, however, has no bearing on the safety of coach operation. However, if the measurements for wheel gauge are done in horizontal plane passing through the axle then the effect of bending of the axle will not be there. It is therefore clarified that the wheel gauge tolerances of 1600 2 mm as laid down in IRCA rule book A TECHNICAL GUIDE ON DERAILMENTS April ‘98 CAMTECH/M/3 37 is required to be checked under "No-load" conditions. 3.2 BENT AXLE A bent axle starts wobbling during motion causing severe vibrations. In order to confirm whether an axle is bent or not, it must be checked carefully on a sensitive machine or measuring table. 3.3 TYRE PROFILE The outer periphery of a wheel which comes in contact with the rail is known as tyre profile. The standard tyre profile of B.G. is shown in the Fig. 3.2. A TECHNICAL GUIDE ON DERAILMENTS April ‘98 CAMTECH/M/3 38 Fig. 3.2 Tyre Profile of a new Wheel The important features of the tyre profile are as under : 3.3.1 A chamfer of 6 mm at 45 degrees on outer edge. This is provided to avoid sharp edges and also prevent small burs (chips of metal) projecting beyond the outer surface of wheel due to spreading of small thin layer on outer periphery of the tyre. 3.3.2 An upward inclination of 1 in 20 towards inside. It is provided to ensure that the wheels remain in central position of the track and allows the outer wheel to travel on the higher tread diameter and inner wheel on a smaller wheel diameter on curves. 3.3.3 Route radius : A root radius is provided at the bottom of the flange. This radius for B.G. is 15 mm. 3.3.4 Height of wheel flange : The height of wheel flange is measured from the tread of the tyre. It is kept 28.5 mm for B.G. This height also forms an important part in determining the tyre profile. 3.4 WHEEL DEFECTS The following aspects should be checked on the suspected wheels : a) condemning limit b) flat places on tyre/skidding A TECHNICAL GUIDE ON DERAILMENTS April ‘98 CAMTECH/M/3 39 c) flanges - sharp/deep/thin d) radius too small at the root of the flange e) gauge slack/tight. f) cracks The above mentioned defects can be detected with the help of Tyre defect gauge and Wheel gauge meant for this purpose. 3.4.1 Thin Flange When the flange thickness reduces to less than 16 mm for B.G., the flange is called a thin flange. It should be measured at the distance of 13mm below the flange tip (Fig.3.5). Fig. 3.5 Thin Flange A thin flange increases lateral play between the wheel set and track and increases : A TECHNICAL GUIDE ON DERAILMENTS April ‘98 CAMTECH/M/3 40 Lateral oscillations adversely affecting Y/Q and Angularity of wheel set on run 3.4.2 Sharp Flange This occurs when the flange wears in such a way that radius at the tip of the flange becomes less than 5 mm. The flange forms a fine sharp edge. Due to this, the wheel set can take two roads at slightly gaping point or wheel may ride over the chipped tongue rail (Fig 3.4). Fig. 3.4 Sharp Flange 3.4.3 Worn Out Flange When radius at the root of the flange becomes less than 13 mm, it is called worn out flange. A worn out flange increases A TECHNICAL GUIDE ON DERAILMENTS April ‘98 CAMTECH/M/3 41 the value of (Fig. Fig. 3.5 Worn out Flange 3.4.4 Deep Flange When the depth of flange, measured from the flange top to a point on the wheel tread (63.5 mm away from the back of B.G. wheel), becomes greater than 35 mm, it is called a deep flange (35-28.5=6.5 mm ) as shown in Fig. 3.6. Under this condition, the wheel flange would tend to ride on the fish plate and check-block and may damage the track components. A TECHNICAL GUIDE ON DERAILMENTS April ‘98 CAMTECH/M/3 42 Fig. 3.6 Deep Flange 3.4.5 False flange/Hollow Tyre When the projection of outer edge of the wheel tread below the hollow of the tyre exceeds 5 mm, the outer edge of the wheel forms a false flange and the worn tread is called hollow tyre (Fig. 3.7). The hollow tyre has the danger of developing a false flange. There is no effect on angularity or eccentricity but wear on tyres has the effect of increasing the conicity of the wheel tyre. This reduces the critical speed of the rolling stock beyond which excessive hunting and oscillations take place thereby - increasing the flange force ‘Y’ and the chances of derailment. Fig. 3.7 False Flange/Hollow Tyre A false flange may split open the points while travelling in trailing direction while negotiating the crossing (Fig.3.8). It may tend to get wedged in between the tongue rail and the stock rail. A TECHNICAL GUIDE ON DERAILMENTS April ‘98 CAMTECH/M/3 43 The wheel going across the wing rail would then get lifted as instead of travelling on the tread portion,it would be travelling on the false flange. This will make the wheel to suddenly lift up and drop down near the nose of the crossing. False Flange Fig. 3.8 Hollow Tyre on a Switch Crossing Wheels having flats on tyre damage the rails due to impact and cause high contact stresses. This may cause rail fracture leading to derailments. 3.4.6 Flat Places on Tyre The maximum permissible value of flatness on a B.G. wheel tyres is as under (Fig. 3.9) : Goods Stock IRS - 60 mm A TECHNICAL GUIDE ON DERAILMENTS April ‘98 CAMTECH/M/3 44 Coaching Stock - 50 mm Fig. 3.9 Flat Tyre 3.4.7 Difference of Wheel Diameter on Tread Wheel diameter is measured on the tread at a distance of 63.5 mm from the inside face of the wheel in case of B.G. (Fig. 3.10) and 57 mm in case of M.G. Two measurements 180 degrees apart should be taken for each wheel. Fig. 3.10 Measuring Wheel diameter A TECHNICAL GUIDE ON DERAILMENTS April ‘98 CAMTECH/M/3 45 Limits of wheel diameter variation on the same axle The workshop leaving limits for the difference in diameter are indicated in Table 3.2. Table 3.2 Workshop Leaving Limits for Wheel Diameter Type of On the On the On the Wagon/Trolley same Axle same same Trolley Wagon BG MG BG MG BG MG Four Wheeled Trolleys 0.5 0.5 13 10 13 10 Six wheeled Trolleys 0.5 0.5 6 6 6 6 Six wheeled units 0.5 0.5 6 6 6 6 Four wheeled units 0.5 0.5 -- -- 25 13 These limits of variations as prescribed in Rule No. 2.8.14.2 IRCA Part III and Rule No. 2.9.4 IRCA Part IV are to be observed at the time of fitment of freshly reprofiled wheels during periodic overhaul in workshops and repairs requiring wheel changing in sick lines. These limits do not form a part of train examination. The rejection of wheels worn beyond service limits will continue to be determined by the normal wear limits specified in IRCA Rules (Rly. Bd. A TECHNICAL GUIDE ON DERAILMENTS April ‘98 CAMTECH/M/3 46 letter No. 86/M(N)960/8 DATED 22.8.86). 3.5 AXLE BOX LATERAL AND LONGITUDINAL CLEARANCES 3.5.1 Lateral. Play between B/Brass & Journal collar Minimum - 5 mm ; Maximum. - 10 mm 3.5.2 Total lateral clearance between Axle guard and Axle box grove - 10 mm max. 3.5.3 Lateral longitudinal clearance between axle box lug and horn cheek for box type trolly : lateral longitudinal Minimum. 20 mm 12 mm Maximum. 25 mm 18 mm Due to spring suspension, the lateral motion induced by track irregularities is dampened. Experiments have established that the lateral force due to hunting is much higher for a vehicle beyond above clearances. On the other hand, below minimum limits given above, freedom of wheels during run gets restricted beyond desirable limits. Bent axle guards will not be able to move up and down A TECHNICAL GUIDE ON DERAILMENTS April ‘98 CAMTECH/M/3 47 freely and the axle box will get jammed making spring assembly ineffective thus increasing proneness to derailment. 3.6 BUFFING GEAR 3.6.1 Buffer projection limits from head stock For long case buffers For short case buffers Max. 635 mm 456 mm Min. 584 mm 406 mm A. Buffer projection for POH stock should not be less then 625 mm for long case and 445 mm for short case buffers. B. No dead buffers shall be permitted from the sick line. The buffers shall be considered dead when the projection is below the prescribed minimum Limits. C. Buffer heights in BG Stock shall be within the limits shown above and it should be measured on level track. Note: The measurement should be taken from the centre of the buffer socket to the top of the rail head. The buffer height should never be taken from the centre of the buffer face because it will not give correct value. While recording buffer height, it should be ensured that A TECHNICAL GUIDE ON DERAILMENTS April ‘98 CAMTECH/M/3 48 buffer bolts are in tight condition and buffer is not drooping. If it is drooping, the amount of drooping should be measured and recorded. To make up buffer heights to maximum permissible limits, a packing piece of required design and size may be inserted : For Goods stock : between axle box crown & bearing spring buckles. For ICF coaching stock : between lower spring (Dash Pot spring) & axle box wing. 3.6.2 Displaced Buffer Buffer displaced 35 mm in any direction from its normal position in case of goods stock and 38 mm for coaching stock are called displaced buffers. If buffers of adjacent stock are not in the same level due to different conditions of loading or spring characteristics, the buffer draw gear takes an inclined position. In case of sag on the track or brake application on a down gradient, the buffers exert compressive forces. It makes the lighter vehicle prone to derailment due to lifting because of vertical component of the - buffing force. 3.7 SPRING AND SPRING GEAR In four wheeler stock, laminated springs are normally used. However in coaches now, mostly coil springs are used. A TECHNICAL GUIDE ON DERAILMENTS April ‘98 CAMTECH/M/3 49 The defects in these can be classified into three main categories : 3.7.1 Defects affecting the functioning of springs If the defects are such that normal functioning gets hampered, the load transmission system is adversely affected. The particular wheel on which this spring bears can’t adjust itself to any unevenness in the track and the wheel will become prone to derailment due to lack of dampening force. 3.7.2 Variation in performance of different springs on the same vehicle The difference in working camber amongst the four springs under load should not exceed 13 mm. The springs having different cambers may cause derailment due to off- loading effect. DESIGN CHARACTERISTICS OF SPRINGS TABLE 3.3 - B.G. WAGON HELICAL SPRINGS Type of Rolling Stock, Drawing no. Free Outer Solid & location of spring Height Dia. Height CASNUB 22W - Drg. No. WD-83069/S-1 Outer Spring 260 +/- 3 140 167.5 Inner Spring 262 +/- 3 86 168 Snubber Spring 294 +/- 3 98 165 CASNUB 22W HS - Drg No. WD-92058-S-5 Outer Spring 260 +/- 3 147 137 Inner Spring 243 +/- 3 180 88 A TECHNICAL GUIDE ON DERAILMENTS April ‘98 CAMTECH/M/3 50 Snubber Spring 293 +/- 3 171 104 TABLE 3.4 - B.G. WAGON LAMINATED SPRINGS Type of Rolling Stock Drawing Free camber No. of No. plates BOX, BCX, BRH WD-86007-S/1 47 +6/-0 10 CRT WD-87024-S/1 58 +6/-0 9 TABLE 3.5 - B.G. COACH HELICAL SPRINGS Drawing No. Free Test Acceptable Height Load height under load ICF, RCF & BEML AXLE F-0-1-006 360 2000 279-295 WTAC-0-1-202 375 2800 264-282 WLRRM8-0-1-802 360 3000 277-293 RDSO/SK-84262 325 1600 278-291 WLRRM2-0-1202 372 3000 265-282 DL-0-1-002 372 3000 269-284 DD-0-1-001 337 2400 268-284 RDSO/SK-98017 315 1800 276-289 ICF, RCF & BEML BOLSTER F-0-5-002 385 3300 301-317 WTAC-0-5-202 400 4800 291-308 WLRRM8-0-5-802 386 6700 306-322 RDSO/SK-84263 345 2300 300-313 WLRRM2-0-5-202 400 6100 286-304 DL-0-5-002 422 5500 291-311 DD-0-5-03(OUTER) 416 4200 280-299 EMU/M-0-5-004(INNER) 308 4200 280-299 RDSO/SK-98018 : B-15 393 6000 256-272 A TECHNICAL GUIDE ON DERAILMENTS April ‘98 CAMTECH/M/3 51 RDSO/SK-98018 : B-16 286 6000 256-272 TABLE 3.6 - M.G. HELICAL SPRINGS ICF’s Drawing Free Test Acceptable No. Height Load height under load MAN BOGIE - AXLE RDSO/SK-84259 243 2000 198-209 MAN BOGIE - BOLSTERS RDSO/SK-84260(OUTER) & RDSO/SK-84260(INNER) 540 3500 394-417 RDSO/SK-84261(OUTER) & RDSO/SK-84261(INNER) 540 3500 457-476 ICF BOGIE - AXLES MG/T-01-002 260 1000 226-237 (MG/T-0-1-029) MG/PLV-0-1-001 250 1000 232-240 MG/AC-9-0-1-001 270 1000 236-247 ICF BOGIE BOLSTERS MG/T-0-5-002 280 1000 256-267 MG/PLV-0-5-001 280 1000 262-271 MG/AC-9-0-001 292 1000 266-269 3.7.3 Failure of springs Failure of a spring may cause derailment as it results in loss of damping effect and shifts the centre of gravity of the vehicle. A TECHNICAL GUIDE ON DERAILMENTS April ‘98