Workshop Processes, Practices, and Materials PDF
Document Details
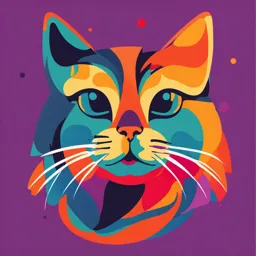
Uploaded by PromptWilliamsite6646
UNZA
2015
Bruce J. Black
Tags
Summary
This book, "Workshop Processes, Practices and Materials", serves as an introduction to workshop processes for engineering students. It covers a range of topics including safe practices, measuring equipment and hand tools. The fifth edition adds updated material on modern measuring techniques and CNC milling/turning.
Full Transcript
Workshop Processes, Practices and Materials CHAPTER 21 An essential guide to the workshop for all mechanical and production engineering students XXHealth and safety chapter covers current best practice and has been...
Workshop Processes, Practices and Materials CHAPTER 21 An essential guide to the workshop for all mechanical and production engineering students XXHealth and safety chapter covers current best practice and has been checked by a certified health and safety examiner. XXAddition of modern measuring techniques using laser scan micrometer, co-ordinate and visual measuring systems. XXAddition of an introduction to CNC milling and turning. Workshop Processes, Practices and Materials is an ideal introduction for entry level engineers and workshop technicians, as well as university engineering students with little or no practical experience. With detailed illustrations throughout and simple, clear language, this is a practical introduction to what can be a very complex subject. It has been significantly updated and revised to include new material on current health and safety legislation, gauging and digital measuring instruments, as well as modern measuring techniques such as laser scan micrometer, co-ordinate and visual measuring systems. A new chapter on an introduction to CNC milling and turning has also been added. This book covers all standard workshop topics, including safe practices, measuring equipment, hand and machine tools, metal and plastics materials, joining methods (including welding), presswork, primary forming, casting and moving loads, making it an indispensable handbook for use both in class and in the workshop. Its broad coverage makes it a useful reference book for many different courses worldwide. Bruce J. Black has over 40 years’ experience as a production engineer in machine tool and aircraft industries, as well as lecturing in production engineering, culminating as workshop director (wood, metal and plastics) at the then Gwent College of Higher Education in South Wales, UK. Now retired, he works as a freelance technical author. 7KLVSDJHLQWHQWLRQDOO\OHIWEODQN Workshop Processes, Practices and Materials Fifth edition Bruce J. Black Fifth edition published 2015 by Routledge 2 Park Square, Milton Park, Abingdon, Oxon OX14 4RN and by Routledge 711 Third Avenue, New York, NY 10017 Routledge is an imprint of the Taylor & Francis Group, an informa business © 2015 Bruce J. Black The right of Bruce J. Black to be identified as author of this work has been asserted by him in accordance with sections 77 and 78 of the Copyright, Designs and Patents Act 1988. All rights reserved. No part of this book may be reprinted or reproduced or utilised in any form or by any electronic, mechanical, or other means, now known or hereafter invented, including photocopying and recording, or in any information storage or retrieval system, without permission in writing from the publishers. First edition published by Newnes 1979 Fourth edition published by Routledge 2010 Trademark notice: Product or corporate names may be trademarks or registered trademarks, and are used only for identification and explanation without intent to infringe. British Library Cataloguing-in-Publication Data A catalogue record for this book is available from the British Library Library of Congress Cataloging in Publication Data Black, Bruce J. Workshop processes, practices & materials / Bruce Black. – 5th edition. pages cm Proudly sourced and uploaded by [StormRG] Kickass Torrents | TPB | ET | h33t Includes index. ISBN 978-1-138-78472-7 (pbk. : alk. paper) – ISBN 978-1-315-76822-9 (ebook) 1. Machine-shop practice. I. Title. II. Title: Workshop processes, practices, and materials. TJ1160.B52 2015 670.42'3–dc23 2014034244 ISBN: 978-1-138-78472-7 (pbk) ISBN: 978-1-315-76822-9 (ebk) Typeset in Univers LT by Servis Filmsetting Ltd, Stockport, Cheshire Dedication To my wife Gillian, children Susan and Andrew, and grandchildren, Alexander and Thomas Hattam, Darcey, Sophie and Bailey Black 7KLVSDJHLQWHQWLRQDOO\OHIWEODQN Contents Preface to the first edition x 1.15 The Reporting of Injuries, Diseases Preface to the second edition xi and Dangerous Occurrences Preface to the third edition xii Regulations 2013 (RIDDOR) 15 Preface to the fourth edition xiii 1.16 Control of Substances Hazardous Preface to the fifth edition xiv to Health (COSHH) Regulations Acknowledgements xv 2002 (as amended) 16 1.17 Control of Noise at Work 1 Safe practices 1 Regulations 2005 17 1.1 Health and Safety at Work Act 1974 1.18 Control of Vibration at Work (HSWA) (as amended) 1 Regulations 2005 20 1.2 Health and safety organisation 1 1.19 Electrical hazards 20 1.3 Employer’s responsibilities 3 1.20 The Health and Safety (Safety 1.4 Safety policy 3 Signs and Signals) Regulations 1.5 Safety Representatives and Safety 1996 23 Committees Regulations 1977 (as 1.21 Safety signs and colours 24 amended) 4 1.22 Fire 25 1.6 Health and Safety (Consultation 1.23 Dangerous Substances and with Employees) Regulations 1996 Explosive Atmospheres (as amended) 4 Regulations (DSEAR) 2002 28 1.7 Employees ’ responsibilities 5 1.24 First aid at work 28 1.8 New regulations for health and 1.25 Causes of accidents 29 safety at work 6 1.26 General health and safety 1.9 Management of Health and Safety precautions 30 at Work (Amendment) Regulations 2006 6 2 Hand processes 33 1.10 Provision and Use of Work 2.1 Engineer’s files 33 Equipment Regulations 1998 2.2 The hacksaw 35 (PUWER) 7 2.3 Cold chisels 37 1.11 Workplace (Health, Safety and 2.4 Scrapers 38 Welfare) Regulations 1992 2.5 Engineer’s hammers 38 (as amended) 9 2.6 Screwdrivers 39 1.12 Working at Height Regulations 2.7 Taps 40 2005 (WAHR) 11 2.8 Dies 40 1.13 Personal Protective Equipment at 2.9 Hand reamer 41 Work Regulations 1992 2.10 Powered hand tools 41 (as amended) 12 1.14 Health and Safety (Display Screen 3 Marking out 45 Equipment) Regulations 1992 (as 3.1 Datum 45 amended) 14 3.2 Co-ordinates 46 3.3 Marking out equipment 46 3.4 Examples of marking out 51 Contents 4 Sheet-Metal operation 55 9.6 Taper turning 140 4.1 Cutting and bending sheet metal 55 9.7 Screw-cutting 142 4.2 Development 57 9.8 Safety in use of lathe 143 5 Standards, measurement and gauging 61 10 Surface grinding 145 5.1 Length 62 10.1 Elements of a surface-grinding 5.2 Angle 67 machine 145 5.3 Dimensional deviation 69 10.2 Controls 147 5.4 Gauging 70 10.3 Workholding 148 5.5 Straightness 74 10.4 Grinding wheels 149 5.6 Flatness 75 10.5 Surface-grinding operations 155 5.7 Squareness 76 10.6 Safety in the use of abrasive 5.8 Roundness 78 wheels 157 5.9 Surface roughness 78 11 Milling 159 6 Measuring equipment 83 11.1 Milling-machine elements 160 6.1 Vernier instruments 84 11.2 Controls 162 6.2 Micrometers 89 11.3 Milling cutters 163 6.3 Dial indicators 94 11.4 Cutter mounting 165 6.4 Modern measuring techniques 96 11.5 Workholding 166 11.6 The dividing head 167 7 Cutting tools and cutting fluids 101 11.7 Milling operations 168 7.1 Cutting-tool materials 101 11.8 Safety in the use of milling 7.2 Cutting tools 105 machines 171 7.3 Cutting-tool maintenance 109 7.4 Cutting speed 111 12 Introduction to computer numerical 7.5 Cutting fluids 112 control 173 7.6 Types of cutting fluid 113 12.1 Manual part programming for 7.7 Application of cutting fluids 114 milling/drilling 175 7.8 Safety in the use of cutting 12.2 Manual part programming for fluids 115 turning 180 8 Drilling 119 13 Joining Methods 185 8.1 The sensitive drilling machine 119 13.1 Mechanical fasteners 185 8.2 Tool holding 120 13.2 Screw threads 188 8.3 Clamping 121 13.3 Locking devices 188 8.4 Cutting tools on drilling 13.4 Riveting 191 machines 122 13.5 Soft soldering 192 8.5 Drilling operations 125 13.6 Solders 193 8.6 Drilling sheet metal 126 13.7 Brazing 193 8.7 Drilling plastics 127 13.8 Welding 195 8.8 Safety in use of drilling machine 127 13.9 Adhesives 199 13.10 Electrical connections 204 9 Turning 129 13.11 Relative merits of joining 9.1 Centre-lathe elements 129 methods 205 9.2 Centre-lathe controls 132 9.3 Guards 133 14 Materials 207 9.4 Workholding 133 14.1 Physical properties 207 9.5 Centre-lathe operations 137 14.2 Mechanical properties 209 viii Contents 14.3 Comparison of properties 210 17.3 Blanking, piercing and 14.4 Non-destructive testing (NDT) 210 bending operations 269 14.5 Plain-carbon steel 213 17.4 Blanking layouts 270 14.6 Heat treatment of plain-carbon steel 213 18 Investment casting, lost foam casting and 14.7 Cast iron 216 shell moulding 273 14.8 Copper and its alloys 217 18.1 Investment casting 273 14.9 Aluminium and its alloys 219 18.2 Metals for investment casting 276 14.10 Die-casting alloys 220 18.3 Lost foam casting 276 14.11 Lead 220 18.4 Shell moulding 277 14.12 Contact metals 220 14.13 Bearing materials 221 19 Die-casting and metal injection 14.14 Metal protection 222 moulding 281 14.15 Corrosion 223 19.1 Gravity die-casting 281 14.16 Protective coatings 224 19.2 Low-pressure die-casting 282 19.3 High-pressure die-casting 283 15 Plastics 233 19.4 Die-casting metals 285 15.1 Thermoplastics and thermosetting 19.5 Special features of die-castings 287 plastics 234 19.6 Advantages and limitations of die- 15.2 Types of plastics 234 castings 289 15.3 Plastics recycling 240 19.7 Choice of a die-casting process 290 15.4 Working in plastics 241 19.8 Metal injection moulding 290 15.5 Plastics welding 241 15.6 Machining 242 20 Moving loads 293 15.7 Heat bending 244 20.1 The Manual Handling Operations 15.8 Plastics moulding processes 244 Regulations 1992 (as amended) 293 20.2 Lifting Operations and Lifting 16 Primary forming processes 251 Equipment Regulations 1998 16.1 Forms of supply of raw (LOLER) 298 materials 251 20.3 The Health and Safety (Safety 16.2 Properties of raw materials 252 Signs and Signals) Regulations 16.3 Sand casting 252 1996 303 16.4 Vacuum casting 254 16.5 Rolling 255 21 Drawing, specifications and data 305 16.6 Extrusion 256 21.1 Standardisation 305 16.7 Drawing 258 21.2 Communicating technical 16.8 Forging 258 information 306 16.9 Selection of a primary 21.3 Interpreting drawings 309 process 260 21.4 Sectional views 311 21.5 Standard conventions 311 17 Presswork 261 17.1 Presses 261 Appendices 315 17.2 Press-tool design 265 Index 319 ix Preface to the first edition I have written this book to cover the objectives of machines and equipment can be demonstrated, the Technician Education Council standard units handled, and used. Questions at the end of each Workshop processes and materials I (U76/055, chapter are directly related to the chapter content which is based on and intended to replace as a means of reinforcing the learning process. U75/001), for students of mechanical/production An extensive coverage of health and safety has engineering, industrial measurement and control, been included, as I feel very strongly that anyone and polymer technology, and Materials and involved in an industrial environment should workshop processes I (U75/002), for students develop a responsible awareness of the hazards of electronic, telecommunication, and electrical which could affect not only his own health and engineering. These two units contain a great deal safety but also that of his fellow workers. of common material, and by covering them both Although specifically written for the TEC I hope that the book will be useful to a larger standard units, the content is also suitable for the number of students and teaching staff. syllabus requirements of the GCE ordinary-level From my own experience I have found the examinations in Engineering workshop theory and content of these units too great to be covered in practice (AEB) and Engineering workshop practice the design length of 60 hours while still leaving (WJEC), as well as a considerable amount of time for adequate practical involvement by the first-year work in the higher national diploma in student, which can best be carried out under the mechanical engineering. guidance of the lecturer. In writing this book, my Finally, I would like to thank my wife for her aim has been to set out in detail the theoretical patience and understanding throughout the aspects of each topic, with appropriate line period of writing the book, my colleagues for illustrations, in the hope that, by using the book as their assistance, and Mrs Brigid Williams for her a course text and for assignments, more time can speedy and skilful typing of the manuscript. be spent by the student in practical work where Preface Main heading to the second edition Preparing the second edition has enabled me to presswork, investment casting, shell moulding update a number of areas and to increase the and die casting. scope of the book by including additional material. I have updated the Safe Practices chapter to It has also afforded the opportunity of resetting to include current Health and Safety Regulations and current popular book size and format. the chapter on Measuring Equipment to include In this second edition I have increased the content electronic instruments. A section on bonded to cover a wider range of topics in order to make abrasive grinding wheels has been added to the book even more comprehensive by providing the chapter on Surface Grinding and moulding additional chapters on processes to include processes has been included in the chapter on sand casting, rolling, extrusion, drawing, forging, plastics. Preface to the third edition The third edition has enabled me to increase the New chapters have been added to cover scope of the book by including additional material Standards, measurement and gauging as well to cover much of the units in the Performing as Moving loads and Drawing specifications and Engineering Operations syllabus. data. Where required, chapters have been updated in I have also taken the opportunity to include review line with current developments, e.g. lost foam questions at the end of each chapter. casting and metal injection moulding. Preface Main heading to the fourth edition In this fourth edition I have included, by request, enhanced and the section on protective coatings additional material including gas welding and the has been enlarged to include plasma electrolytic dividing head. I have updated to the current health oxidation, electrocoating, powder coating and coil and safety legislation in Chapter 1 and in relation coating. Chapter 14 has additions to include the to abrasive wheels, power presses and manual high-performance polymers such as polyimides handling and pictures of machine guards have and PEEK as well as the recycling of plastic been added. The section on adhesives has been materials. Preface to the fifth edition This fifth edition has enabled me to further has been re-written in line with current practice increase the scope of the book. I have updated and the use of high-pressure coolant has been to current health and safety legislation. Chapter included. A description of hand tapping on the 5 has been extended by adding the use of length lathe and knurling has been included by request. bars and angle gauge blocks as well as updating In the materials section I have been requested to some of the text. Some alterations have been include a description of non-destructive testing. made to Chapter 6 and I have included the latest Chapter 16 has been enhanced by the addition digital instruments used in measurement and of the vacuum casting technique. Finally I have added a section on modern measuring techniques added a completely new chapter (Chapter 12) as using the laser scan micrometer, co-ordinate and an introduction to the computer numerical control visual measuring machines. Cutting tool materials of machine tools. Acknowledgements The author and publishers would like to thank the 10.5, 10.6); Saint-Gobain Abrasives (Fig. 10.10); following organisations for their kind permission Engineering Solutions Ltd. (Figs. 15.11, 15.12); to reproduce photographs or illustrations. Hinchley Engineering Co. Ltd. (Fig. 15.13); JSP Ltd. (Fig. 1.7); Crown Copyright (Fig. 1.8); Sweeny & Blockside (Power Pressing) (Fig. 17.2); Chubb Fire Ltd. (Fig. 1.18); Desoutter Brothers Verson International Ltd. (Fig. 17.3); P.J. Hare Ltd. (Fig. 2.22); Neill Tools Ltd. (Figs. 3.10, 3.11, Ltd. (Fig. 17.4); Lloyd Colley Ltd. (Fig. 17.13); 3.14, 6.18, 6.23, 10.7, 10.8); Mitutoyo Ltd. P.I. Castings (Altrincham) (Figs 18.1–18.7); (Figs. 3.15, 5.33, 6.6, 6.9, 6.10, 6.13–17, 6.22, Dennis Castings (Fig. 18.10); Ajax Machine Tools 6.26–28, 6.31–34, 6.36, 6.37, 6.39–41, 6.44, 6.45, International Ltd. (Figs. 12.3, 12.11); Lloyds 6.47); A.J. Morgan & Son (Lye) Ltd. (Figs. 4.2, British Testing Ltd. for information on lifting 4.8); Walton and Radcliffe (Sales) Ltd. (Fig equipment; Fig. 15.10 is based on an ICI technical 4.3); Q-Max (Electronics) (Fig. 4.4); TI Coventry service note by permission of Imperial Chemical Gauge Ltd. (Figs. 5.2, 5.5, 5.7, 5.16, 5.19, 5.21, Industries; Figs. 5.6, 5.7, 5.10 and 15.15 were 5.22); L.S. Starrett & Co./Webber Gage Division photographed by John Kelly; Figs. 1.8 and 20.20 (Figs. 5.11, 5.12); Verdict Gauge Sales (Fig. 5.30); are reproduced by kind permission of HMSO. Rubert & Co. Ltd. (Fig. 5.32); Thomas Mercer Figures 11.15 and 16.14 were drawn by Graeme Ltd. (Figs. 6.38, 6.42); Faro Technologies UK S. Black. Ltd. (Fig. 6.46); Draper Tools Ltd. (Figs. 7.17, 7.19); Sandvik Coromant UK (Figs. 7.22, 7.23); The following are reproduced from or based on W.J. Meddings (Sales) Ltd. (Fig. 8.1); Procter British Standards by kind permission of the British Machine Guards (www.machinesafety.co.uk) Standards Institution from whom copies of the (Figs. 8.3, 9.8, 9.9, 11.6); Clarkson-Osborne complete standards may be obtained. Tools Ltd (8.18, 11.11); TS Harrison (Fig. 9.1); Pratt Burnerd International Ltd. (Figs. 9.10, Table 1.2 and Figs. 1.12–1.16 (BS ISO 3864); 9.12–15); Elliot Machine Tools Ltd. (Figs. 10.1, Tables 5.4 and 5.5 (BS 1134–2010); Table 5.3 (BS 11.1, 11.2); Jones & Shipman Hardinge Ltd (Figs EN ISO 286–1:2010). 7KLVSDJHLQWHQWLRQDOO\OHIWEODQN CHAPTER 1 Safe practices Almost everyone working in a factory has at Its aims are: some stage in his or her career suffered an injury XXto secure the health, safety and welfare of requiring some kind of treatment or first aid. It people at work; may have been a cut finger or something more XXto protect other people against risks to health serious. The cause may have been carelessness or safety arising from the activity of people at by the victim or a colleague, defective safety work; equipment, not using the safety equipment XXto control the keeping and use of dangerous provided or inadequate protective clothing. substances and prevent people from unlawfully Workshop Processes, Practices and Materials, Fifth Edition. 9781138784727. Whatever the explanation given for the accident, having or using them; © 2015 Bruce J. Black. Published by Taylor & Francis. All rights reserved. the true cause was most likely a failure to think XXto control the emission into the atmosphere ahead. You must learn to work safely. Your of noxious or offensive substances from workplace will have its own safety rules so obey premises. them at all times. Ask if you don’t understand any instruction and do report anything which seems What the law requires is what good management dangerous, damaged or faulty. and common sense would lead employers to do anyway, i.e. to look at what the risks are and take sensible measures to tackle them. 1.1 Health and Safety at Work Act 1974 (HSWA) (as amended) 1.2 Health and safety organisation (Fig. 1.1) This Act of Parliament came into force in April 1975 and covers all people at work except The HSWA established two bodies, the Health domestic servants in a private household. It is and Safety Commission and the Health and aimed at people and their activities, rather than Safety Executive (HSE). These were merged in at factories and the processes carried out within 2008 to form a single body, the HSE. The HSE them. is a statutory body established by the HSWA (as amended) which consists of a chairperson and The purpose of the Act is to provide a legal between 7 and 12 executive directors. framework to encourage high standards of health and safety at work. The HSE Board is responsible to appropriate ministers for the administration of the 1974 Act. 1 Safe practices 1 Secretary of State Following guidance is not compulsory, but if followed, will normally be enough to comply with Health and Safety the law. Executive (HSE) Approved codes of practice – offer practical examples of good practice. They give advice on Inspectors how to comply with the law by, for example, providing a guide to what is ‘reasonably practicable’. Issue an Issue a Approved codes of practice have a special legal Advice improvement prohibition Prosecute notice notice status. If employers are prosecuted for a breach of health and safety law, and it is proved that Figure 1.1 Health and safety organisation they have not followed the relevant provisions of the approved code of practice, a court can find them at fault unless they can show that they have The HSE’s mission is: ‘the prevention of death, complied with the law in some other way. injury and ill health to those at work and those affected by work activities ’. Regulations – are law, approved by Parliament. These are usually made under HSWA following HSE’s aims are to protect the health, safety and proposals from HSE. This applies to regulations welfare of people at work, and to safeguard based on EC directives as well as ‘home-grown’ others, mainly members of the public, who may ones. be exposed to risks from the way work is carried out. Health and safety law is enforced by inspectors from HSE. HSE’s statutory functions include: Local authorities also enforce health and safety XXproposing new and updated laws and law in the workplace allocated to them – including standards; offices, shops, retail and wholesale distribution XXconducting research; centres, leisure, hotel and catering premises. XXproviding information and advice; XXmaking adequate arrangements for the Inspectors may visit a workplace without notice enforcement of health and safety laws. at any reasonable time. They may want to investigate an accident or complaint or examine In recent years much of Britain’s health and the safety, health and welfare aspects of the safety law has originated in Europe. Proposals business. They can talk to employees and safety from the European Commission may be agreed representatives and take photographs and by member states who are then responsible for samples. making them part of their domestic law. Where Inspectors may take enforcement action in several HSE consider action is necessary to supplement ways to deal with a breach in the health and existing arrangements, their three main options safety laws. are to provide: In most cases these are: 1. guidance; 2. approved codes of practice (ACOPs); XXInformal: where the breach of the law is 3. regulations. relatively minor – give advice both face to face and in writing. Guidance – can be specific to health and safety XXImprovement notice : where the breach of the problems of an industry or of a particular process law is more serious – requires remedial action used in a number of industries. within a time period. The main purposes of guidance are to: XXProhibition notice : where the activity involves XXhelp people understand what the law says; risk of serious personal injury – prohibit the XXhelp people comply with the law; activity immediately until remedial action is XXgive technical advice. taken. 2 1 Safe practices XXProsecution: where individuals or corporate bodies fail to comply with the regulations – can workplace, the order in which jobs are carried out or special precautions to be taken before 1 lead to a substantial fine or imprisonment or carrying out certain hazardous tasks.) both. 2. Ensure ways in which particular articles and substances (e.g. machinery and chemicals) are The Health and Safety (Fees) Regulations 2012 used, handled, stored and transported are safe puts a duty on the HSE to recover costs from and without risk to health. companies who are found to be in breach of 3. Provide information, instruction, training health and safety law, referred to as Fee for and supervision necessary to ensure health Intervention (FFI) cost recovery scheme. The fee and safety at work. Information means the is based on the amount of time an inspector has background knowledge needed to put the had to spend in identifying the breach, helping to instruction and training into context. Instruction put it right, investigating and taking enforcement is when someone shows others how to do action. Companies who comply with the law will something by practical demonstration. Training not pay a fee for any work that the HSE does with means having employees practise a task to them. improve their performance. Supervision is needed to oversee and guide in all matters 1.3 Employer’s responsibilities related to the task. (Fig. 1.2) 4. Ensure any place under their control and where their employees work is kept in a Employers have a general duty under the HSWA safe condition and does not pose a risk to ‘to ensure, so far as is reasonably practicable, health. This includes ways into and out of the the health, safety and welfare at work of their workplace. employees ’. The principle of ‘so far as is 5. Ensure the health and safety of their reasonably practicable’ applies to all the following employees ’ working environment (e.g. areas and means that an employer does not have heating, lighting, ventilation, etc.). They must to take measures to avoid or reduce the risk if also provide adequate arrangements for the they are technically impossible or if the time, welfare at work of their employees (the term trouble or cost of the measures would be grossly ‘welfare at work ’ covers facilities such as disproportionate to the risk. The HSWA specifies seating, washing, toilets, etc.). five areas which in particular are covered by the employer’s general duty. 1. Provide and maintain machinery, equipment 1.4 Safety policy and other plant, and systems of work that The HSWA requires every employer employing are safe and without risk to health. (‘Systems five or more people to prepare a written of work ’ means the way in which the work statement of their safety policy. The written is organised and includes layout of the policy statement must set out the employer’s aims and objectives for improving health and Entry and exit must be safe safety at work. The purpose of a safety policy is to ensure that Storage must be safe employers think carefully about hazards at the workplace and about what should be done to Plant must be safe and in good reduce those hazards to make the workplace safe working order and healthy for their employees. Safety instruction and training Adequate facilities Another purpose is to make employees aware of must be must be provided provided what policies and arrangements are being made for their safety. For this reason you must be given a copy which you must read, understand and Figure 1.2 Duties of employers follow. 3 1 Safe practices 1 The written policy statement needs to be reviewed and revised jointly by employer and or dangerous occurrence in a workplace or a notifiable disease has been contracted there; employees ’ representatives as appropriate XXrepresenting the employees he or she was working conditions change or new hazards arise. appointed to represent in consultation with inspectors or any enforcing authority; XXattending meetings of safety committees. 1.5 Safety Representatives and Safety Committees Regulations 1977 (as 1.6 Health and Safety amended) (Consultation with Employees) Regulations 1996 1.5.1 Safety representatives (as amended) The Regulations came into force on 1 October The law is different if there are employees 1978 and provide recognised trade unions with within the organisation who are not represented the right to appoint safety representatives to under the Safety Representatives and Safety represent the employees in consultation with their Committees Regulations 1977. employers about health and safety matters of the organisation. For example: Employers have a duty to consult on the following XXThe employer does not recognise trade unions. matters: XXThere are employees who do not belong to a trade union and recognised trade unions have XXthe introduction of any measure at the not agreed to represent them. workplace which may substantially affect the health and safety of employees; Where employees are not represented under the XXarrangements for getting competent people to Safety Representatives and Safety Committee help them comply with health and safety laws; Regulations 1977, the Health and Safety (Consul- XXthe information they must give their tation with Employees) Regulations 1996 will employees on the risks and dangers arising apply. from their work, measures to reduce or If the employer decides to consult the employees eliminate these risks and what the employees through an elected representative, the employees should do if exposed to a risk; have to elect one or more within their group to XXthe planning and organisation of health and represent them. These elected health and safety safety training; representatives are known as ‘representatives of XXthe health and safety consequences of employee safety ’ in the Regulations. The range of introducing new technology. functions of union-appointed representatives and An employer must give safety representatives elected representatives within each Regulation the necessary time off, with pay, to carry out their is similar and it is good practice for employers to functions and receive appropriate training. give equivalent functions, where they agree to them. The functions of an appointed safety representative include: 1.6.1 Safety committees XXinvestigating potential hazards and dangerous occurrences in the workplace; If two or more union-appointed health and safety XXinvestigating complaints relating to an representatives request, in writing, that the employee’s health, safety or welfare at work; employer set up a health and safety committee, XXmaking representations to the employer on then it must be done within 3 months of the matters affecting the health, safety or welfare request. of employees at the workplace; Although there is no such requirement if XXcarrying out inspections of the workplace the employer consults health and safety where there has been a change in conditions representatives elected by the workforce, it is of work, or there has been a notifiable accident good practice to do so. 4 1 Safe practices The main objective of such a committee is to promote co-operation between employers and 1.7 Employees ’ responsibilities (Fig. 1.3) 1 employees in setting up, developing and carrying Under the HSWA it is the duty of every employee out measures to ensure the health and safety at while at work: work of the employees. The committee can consider items such as: XXstatistics on accident records, ill health and sickness absence; XXaccident investigation and subsequent action; Fire appliance XXinspection of the workplace by enforcing authorities, management or employee health and safety representatives; XXrisk assessments; Every employee must take Never interfere with anything XXhealth and safety training; reasonable care of the provided in the interests of XXemergency procedures; safety of himself and safety XXchanges in the workplace affecting the health, others safety and welfare of employees. Figure 1.3 Duties of employees If the health and safety committee is discussing accidents, the aim is to stop them happening XXTo take reasonable care for their own health again, not to give blame. Committees should: and safety and that of others who may be affected by what they do or don’t do. XXlook at the facts in an impartial way; XXconsider what precautions might be taken; This duty implies not only avoiding silly or reckless XXrecommend appropriate action; behaviour but also understanding hazards and XXmonitor progress of any action taken. complying with safety rules and procedures. This means that you correctly use all work items Consulting employees about health and safety can provided by your employer in accordance with the result in: training and instruction you received to enable you XXa healthier and safer workplace – employees to use them safely. can help identify hazards, assess risks and XXTo co-operate with their employer on health develop ways to control or remove risks; and safety. XXbetter decisions about health and safety – based on the input and experience of a range This duty means that you should inform, without of people including employees who have delay, of any work situation which might be extensive knowledge of their own job; dangerous and notify any shortcomings in health XXa stronger commitment to implementing and safety arrangements so that remedial action decisions or actions – since employees have may be taken. been actively involved in reaching these The HSWA also imposes a duty on all people, decisions; both people at work and members of the public, XXgreater co-operation and trust – employers and including children, to not intentionally interfere employees who talk and listen to each other with or misuse anything that has been provided in gain a better understanding of each other’s the interests of health, safety and welfare. views; The type of things covered include fire escapes XXjoint problem solving. and fire extinguishers, perimeter fencing, warning These can then result in real benefits for the notices, protective clothing, guards on machinery business, including: and special containers for dangerous substances. XXincreased productivity; You can see that it is essential for you to adopt XXimprovements in overall efficiency and quality; a positive attitude and approach to health and XXhigher levels of workforce motivation. safety in order to avoid, prevent and reduce risks 5 1 Safe practices 1 at work. Your training is an important way of achieving this and contributes not only to your risks, preventive measures that can be applied and the management and surveillance of health and own but also to the whole organisation’s health safety procedures that should be followed in the and safety culture. event of serious or imminent danger. The Regulations require employers to: 1.8 New regulations for health XXassess the risk to health and safety of and safety at work employees and anyone else who may be Six new sets of health and safety at work affected so that the necessary preventive regulations came into force on 1 January 1993. and protective measures can be identified The new regulations implement European and record the significant findings of the risk Community (EC) directives on health and safety assessment – trivial risks do not need to be at work in the move towards a single European recorded; Union. At the same time they are part of a XXintroduce preventive and protective measures continuing modernisation of existing UK law. to control the risks identified by the risk Most of the duties in the new regulations are assessment; not completely new but clarify and make more XXset up an effective health and safety explicit what is in current health and safety law. A management system to implement their lot of out-of-date law will be repealed by the new health and safety policy to include organising, regulations, e.g. many parts of the Factories Act planning, monitoring, auditing and review, and 1961. Some of these have been updated since keeping records; 1993. XXprovide appropriate health surveillance of employees required by specific health and The six regulations are: safety regulations, e.g. COSHH; XXManagement of Health and Safety at Work XXappoint competent people to help devise and Regulations 1999; apply measures needed to comply with health XXProvision and Use of Work Equipment and safety legislation; Regulations 1998; XXestablish emergency procedures to be XXWorkplace (Health, Safety and Welfare) followed in the event of serious and imminent Regulations 1992; danger to persons at work; XXPersonal Protective Equipment at Work XXarrange necessary contacts with external Regulations 1992; services, e.g. first aid, emergency medical care XXHealth and Safety (Display Screen Equipment) and rescue work; Regulations 1992; XXgive employees information about health and XXManual Handling Operations Regulations 1992. safety matters; XXwork together with other employers who share 1.9 Management of Health and the same workplace; Safety at Work (Amendment) XXgive other employees and self-employed Regulations 2006 people working in that business information about health and safety matters; These Regulations set out broad general duties XXmake sure that employees have adequate which operate with the more specific ones in health and safety instruction and training and other health and safety regulations. They are are capable enough at the job to avoid the risk; aimed mainly at improving health and safety XXprovide health and safety information to management. Under these Regulations employers temporary workers to meet their special are required to assess the risks posed to workers needs; and any others who may be affected by the work XXensure that young persons employed by him or business. are protected at work from risks to their health They focus on risk assessments and how to use and safety which are a consequence of their them affectively to identify potential hazards and 6 1 Safe practices lack of experience, absence of awareness and immaturity. e.g. HSWA and the Workplace (Health, Safety and Welfare) Regulations 1992. 1 The Regulations also: In general terms the Regulations require that XXplace a duty on the employees to follow health equipment provided for use at work is: and safety instructions and training in the use XXsuitable for use, and for the purpose and of equipment. conditions in which it is used; XXsafe for use, maintained in a safe condition and, in certain circumstances, inspected to 1.10 Provision and Use of Work ensure this remains the case; Equipment Regulations 1998 XXused only by people who have received (PUWER) adequate information and training; The Regulations require risks to people’s health XXaccompanied by suitable safety measures, e.g. and safety from equipment they use at work to be protective devices, markings and warnings. prevented or controlled. Although power presses The employer should also ensure that risks are included as work equipment, part IV of created by the use of equipment are eliminated PUWER contains specific requirements for power where possible or controlled by: presses and is dealt with in Chapter 17. In addition to the requirements of PUWER, lifting equipment XXtaking appropriate ‘hardware measures ’ , e.g. is also subject to the requirements of the Lifting providing suitable guards, protection devices, Operations and Lifting Equipment Regulations markings and warning devices, system control 1998 and is dealt with in Chapter 20. devices (such as emergency stop buttons) and personal protective equipment; Work equipment has wide meaning and, generally, XXtaking appropriate ‘software measures ’ any equipment which is used by an employee at such as following safe systems of work (e.g. work is covered: ensuring maintenance is only performed XXmachines such as circular saws, drilling when equipment is shut down) and providing machines, photocopiers, mowing machines, adequate information, instruction and training. tractors, dumper trucks and power presses; XXhand tools such as screwdrivers, hammers and Working with machinery can be dangerous hand saws; because moving machinery can cause injuries in XXlifting equipment such as lift trucks, many ways: elevating work platforms, vehicle hoists and XXworkers can be hit and injured by moving lifting slings; parts of machinery or ejected material, and XXother equipment such as ladders and water parts of the body can be drawn into or trapped pressure cleaners; between rollers, belts and pulley drives; XXan installation such as a series of machines XXsharp edges can cause cuts and severing connected together, an enclosure to provide injuries, sharp pointed parts can stab or sound insulation or scaffolding. puncture the skin and rough surfaces can cause friction or abrasion injuries; Similarly if you allow employees to provide their XXworkers can be crushed both between parts own equipment, it too will be covered and the moving together or towards a fixed part of the employer will need to make sure it complies. machine, wall or other object, and two parts Examples of use of equipment covered by the moving past one another can cause shearing; Regulations include starting and stopping the XXparts of the machine, materials and emissions equipment, programming, setting, repairing, (such as steam or water) can be hot or cold modifying, maintaining, servicing, cleaning and enough to cause burns or scalds and electricity transporting. can cause electrical shock and burns; PUWER cannot be considered in isolation from XXinjuries can also occur due to machinery other health and safety legislation but needs to be becoming unreliable and developing faults considered alongside other health and safety laws, due to poor or lack of maintenance or when 7 1 Safe practices 1 machines are used improperly through inexperience or lack of training. XXinformation, instruction, training and supervision. XXProtection against specified hazards The specific requirements of PUWER include: XXmaterial falling from equipment; XXThe suitability of work equipment – equipment XXmaterial ejected from a machine; must be suitable by design and construction XXparts of the equipment breaking off, e.g. for the actual work it is provided to do and grinding wheel bursting; installed, located and used in such a way as XXparts of equipment collapsing, e.g. to reduce the risk to users and other workers, scaffolding; e.g. ensure there is sufficient space between XXoverheating or fire, e.g. bearing running hot, moving parts of work equipment and fixed ignition by welding torch; and moving parts in its environment. Ensure XXexplosion of equipment, e.g. failure of a that, where mobile work equipment with a pressure-relief device; combustion engine is in use, there is sufficient XXexplosion of substance in the equipment, air of good quality. e.g. ignition of dust. XXMaintenance of work equipment in good XXHigh and very low temperature – prevent repair – from simple checks on hand tools such the risk of injury from contact with hot (blast as loose hammer heads to specific checks furnace, steam pipes) or very cold work on lifts and hoists. When maintenance work equipment (cold store). is carried out it should be done in safety and XXControls and control systems – starting work without risk to health. equipment should only be possible by using XXInformation and instruction on use of the work a control and it should not be possible for it equipment – including instruction sheets, to be accidentally or inadvertently operated manuals or warning labels from manufacturers nor ‘operate itself’ (by vibration or failure of a or suppliers. Adequate training for the spring mechanism). purposes of health and safety in the use of Stop controls should bring the equipment to specific work equipment. a safe condition in a safe manner. Emergency XXDangerous parts of machinery – guarding stop controls are intended to effect a rapid machinery to avoid the risks arising from response to potentially dangerous situations mechanical hazards. The principal duty is to and should be easily reached and activated. take effective measures to prevent contact Common types are mushroom-headed buttons with dangerous parts of machinery by (see Fig. 1.5), bars, levers, kick plates or providing: pressure-sensitive cables. XXfixed enclosing guards; XXother guards (see Fig. 1.4) or protection It should be possible to identify easily what devices; each control does. Both the controls and XXprotection appliances (jigs, holders); Figure 1.4 Guard fitted to vertical milling machine Figure 1.5 Mushroom-headed stop button 8 1 Safe practices their markings should be clearly visible and factors such as colour, shape and position are and safety reasons, e.g. start/stop controls, safe working load on cranes, types of fire 1 important. extinguishers and pipework colour coded to XXIsolation from source of energy – to allow indicate contents. Markings may use words, equipment to be made safe under particular letters, numbers or symbols and the use of circumstances, e.g. when maintenance is to colour and shape may be significant. Markings be carried out or when an unsafe condition should conform to published standards (see develops. Isolation means establishing a break 1.20 The Health and Safety (Safety Signs and in the energy supply in a secure manner, i.e. by Signals) Regulations 1996). ensuring that inadvertent reconnection is not X X Warnings – normally in the form of a possible. Isolation may be achieved by simply permanent printed notice or similar, e.g. ‘head removing a plug from an electrical socket or by protection must be worn ’ (see page 24). operating an isolating switch or valve. Portable warnings are also necessary during temporary operations such as maintenance. Sources of energy may be electrical, pressure (hydraulic or pneumatic) or heat. Warning devices can be used which may XXStability – there are many types of work be audible, e.g. reversing alarms on heavy equipment that might fall over, collapse or vehicles, or visible, e.g. lights on a control overturn unless they are fixed. Most machines panel. They may indicate imminent danger, used in a fixed position should be bolted down. development of a fault or the continued Some types of work equipment such as mobile presence of a potential hazard. cranes may need counterbalance weights. They must all be easy to see and understand, and they must be unambiguous. Ladders should be at the correct angle (a slope of four units up to each one out from the base), correct height (at least 1 metre above the 1.11 Workplace (Health, Safety landing place) and tied at the top or secured at and Welfare) Regulations the foot. 1992 (as amended) XXLighting – if the lighting in the workplace is These Regulations cover a wide range of basic insufficient for detailed tasks then additional health, safety and welfare issues and apply lighting will need to be provided, e.g. local to most workplaces. They aim to ensure that lighting on a machine (Fig. 1.6). workplaces meet the health, safety and welfare XXMarkings – there are many instances where needs of all members of the workforce, including marking of equipment is appropriate for health people with disabilities. Where necessary, parts of the workplace, including in particular doors, passageways, stairs, showers, washbasins, lavatories and workstations, should be made accessible for disabled people. A workplace in these Regulations applies to a very wide range of workplaces, not only factories, shops and offices, but also, for example, schools, hospitals, hotels and places of entertainment, and also includes private roads and paths on industrial estates and business parks. The Regulations set general requirements in three broad areas, which are outlined here. XXHealth XXVentilation: enclosed workspaces should be sufficiently well ventilated. Figure 1.6 Local lighting on a centre lathe 9 1 Safe practices 1 XXTemperature: inside the workplace should provide reasonable comfort without the pits or tanks. Every open-sided staircase should be securely fenced. A secure and need for special clothing. substantial handrail should be provided and XXHot and cold environment: insulate or maintained on at least one side of every provide air cooling or as last resort provide staircase. Falls from height account for a protective clothing. significant number of workplace injuries XXLighting: should be sufficient to enable and unnecessary deaths every year. people to work without experiencing eye Employers must ensure that all work at strain and to safely move about. Provide height is properly planned, supervised and artificial lighting if necessary. carried out by competent people. Duties XXCleanliness and waste materials: regularly relating to falls from height are covered by clean workplace to ensure dirt and refuse Work at Height Regulations 2005 (WAHR). is not allowed to accumulate. Spillages and XXTransparent surfaces: windows and deposits should be removed and cleaned as transparent or translucent surfaces in soon as possible. doors, gates, walls and partitions should be XXRoom dimensions: work rooms should have made of a safety material and marked to enough free space to allow easy access make it apparent. and to move about within the room and XXWindows: it should be possible to reach not restrict the workers‘ movements while or operate skylights, operable windows performing their work. This includes a and ventilators safely. Controls should be adequate ceiling height. placed so that people are not likely to fall XXWorkstations: should be arranged so that through or out of windows. All windows each task can be carried out safely and and skylights in a workplace should be able comfortably and allows adequate freedom to be cleaned safely. of movement. Work surface height and XXOrganisation of traffic routes: there should seating should be arranged appropriate to be enough traffic routes of sufficient width the work and worker. Everything required and headroom to allow people on foot or for the work should be within easy reach vehicles to circulate safely and without without the need for undue bending or difficulty. A traffic route is defined as a stretching. route for pedestrian traffic, vehicles or both, XXSafety and include any stairs, staircases, fixed XXMaintenance: equipment that could fail ladders, doorways, gateways, loading bays and put workers at serious risk should be or ramps. Potential hazards on traffic routes properly maintained and checked at regular used by vehicles and pedestrians should intervals, as appropriate, by inspection, be indicated by suitable warning signs. testing, adjustment, lubrication, repair Suitable road markings and signs should be and cleaning. Equipment which require a used to alert drivers. system of maintenance include emergency XXDoors and gates: should be suitably lighting, fencing, powered doors, fixed constructed and if necessary be fitted with equipment used for window cleaning and safety devices. Doors and gates which anchorage points for safety harnesses. swing in both directions should have a XXCondition of floor: floors and traffic routes transparent panel. Sliding doors should should be sound, not uneven or slippery have a stop to prevent the door coming and should be free of obstructions and off its track. Upward opening doors should substances which could cause a slip, trip or have an effective device to prevent them fall. from falling back. XXFalls: every vessel containing a dangerous XXWelfare substance should be adequately fenced XXToilets: suitable and sufficient toilet or covered to prevent a person falling into facilities shall be provided which are it. A vessel includes sumps, silos, vats, convenient and allow everyone at work to 10 1 Safe practices use them without unreasonable delay. The rooms containing them shall be adequately XXwork above ground/floor level; XXcould fall from an edge, through an opening or 1 ventilated and lit and kept in a clean and fragile surface; orderly condition. Separate conveniences XXcould fall from ground level into an opening in a should be provided for men and women. floor or a hole in the ground. XXWashing: washbasins should have hot, The Regulations apply to all work at height where cold or warm running water. Showers or there is a risk of a fall liable to cause personal baths should be provided if required by the injury. They place duties on employers and those nature of the work, e.g. dirty or particularly who control any work at height activity. strenuous. As part of the Regulation the employer must ensure: XXDrinking water: an adequate supply of wholesome drinking water, normally XXall work at height is properly planned and obtained directly from the mains supply, organised; shall be provided for all persons in the XXthose involved in work at height are competent workplace. (have had instruction and have sufficient skills, XXAccommodation for clothing: provide knowledge and experience); accommodation for work clothing and XXthe risks from work at height are assessed, workers‘ own personal clothing so and appropriate work equipment is selected it can be hung in a clean, warm, dry, and used; well-ventilated place. Where special XXthe risks from working on or near fragile work clothing becomes dirty, damp or surfaces are properly managed; contaminated due to work activities, it XXthe equipment used for work at height is should be accommodated separately properly inspected and maintained. from the workers‘ own clothing. In this Before working at height the following simple case, separate changing rooms should be steps should be considered: provided. XXAvoid working at height where it is reasonably XXRest and eating meals; provide suitable and practicable to do so. sufficient rest facilities equipped with an XXWhere work at height cannot be avoided, adequate number of tables and chairs. prevent falls using either an existing place of Where workers regularly eat meals at work, work that is already safe or the right type of provide suitable and sufficient facilities equipment. which would include preparing or obtaining XXMinimise the distance and consequences of a a hot drink. Good hygiene standards should fall by using the right type of equipment where be maintained in those parts of the rest the risk cannot be eliminated. facility used for preparing or eating food and The surface from which work at height can be drink. carried out is referred to by the Regulations as a working platform. A working platform can be 1.12 Working at Height a roof, floor, plant and machinery with a fixed Regulations 2005 (WAHR) guardrail, platform on a scaffold, tower scaffolds, mobile elevating work platforms and the rungs Falls from height are one of the biggest causes and treads of ladders and stepladders. For the of workplace fatalities and major injuries. purpose of this book I shall restrict coverage to Common causes are falls from ladders and ladders and stepladders. through fragile roofs. The purpose of the Regulations is to prevent death and injury from a The use of ladders and stepladders are not fall from height. banned under health and safety law. The law says that ladders can be used for work at height Work at height means work in any place where, if when a risk assessment has shown that using there were no precautions in place, a person could equipment offering a higher level of fall protection fall a distance liable to cause personal injury. You is not justified because of the low risk and short are working at height if you: 11 1 Safe practices 1 duration of use. For tasks of low risk and short duration, ladders and stepladders can be a sensible ladder (protect the area using suitable barriers or cones). and practicable option. If the risk assessment XXAvoid positioning the ladder where it could be determines it is correct to use a ladder, the risk can pushed over by other hazards such as doors be further minimised by making sure the workers: and windows. XXuse the right type of ladder for the job; XX Make sure the ladder is at 75° – use the one in XXare competent; four rule (i.e. one unit out for every four units up). XXuse the equipment provided safely and follow XXMake sure the ladder is long enough for the a safe system of work; task, at least 1 m (three rungs) above where XXare fully aware of the risks and measures to you are working. help control them. XXTie the ladder to a suitable point, making sure both stiles are tied. Ladders should only be used in situations where XXNever over-reach – be safe, get down and they can be used safely, e.g. where the ladder move it. will be level and stable, and where it is reasonably XXDon’t try to move or extend ladders while practicable to do so, the ladder can be secured. standing on the rungs. The employer needs to make sure that any ladder XXAlways grip the ladder and face the rungs or stepladder is both suitable for the work task while climbing or descending. and is in a safe condition before use. Only use XXDon’t work off the top three rungs (always ladders or stepladders that: maintain a handhold). XXhave no visible defects (pre-use check each XXDon’t stand ladders on movable objects such working day); as pallets, bricks, lift trucks, tower scaffolds XXhave an up-to-date record of regular detailed and excavator buckets. visual inspections by a competent person; XXAvoid holding items while climbing (consider XXare suitable for the intended use (strong and using a tool belt). robust enough for the job); XXMaintain three points of contact while climbing XXhave been maintained and stored in and wherever possible at the work position accordance with the manufacturer’s (this means a hand and two feet). instructions. XXDon’t work within 6 m horizontally of an Before starting a task you should always carry out overhead power line unless it has been made a visual ‘pre-use’ check which should look for: ‘dead’. XXtwisted, bent or dented stiles; XXcracked, worn, bent or loose rungs or treads; 1.13 Personal Protective XXmissing or damaged tie rods; Equipment at Work XXcracked or damaged welded joints, loose rivets Regulations 1992 (as or damaged stays and locking mechanisms; amended) XXmissing or damaged feet; These Regulations require that every employer XXsplit or buckled platform on stepladder. shall ensure that suitable personal protective equipment (PPE) is provided to his employees 1.12.1 Safe use of ladders/ who may be exposed to the risk to their health stepladders and safety while at work. Once a ‘pre-use’ check has been carried out, PPE should always be relied upon as a last resort there are simple precautions that can be taken to to protect against health and safety. Engineering minimise the risk of a fall: controls and safe systems of work should XXAlways position ladder on a firm level base always be considered first. Where the risks are which is clean and free from loose materials. not adequately controlled by other means, the XXTake all necessary precautions to avoid employer has a duty to ensure that suitable PPE is vehicles or people hitting the bottom of the provided, free of charge. 12 1 Safe practices PPE will only be suitable if it is appropriate for the risks and the working conditions, takes account 1 of the worker’s needs and fits properly, gives adequate protection and is compatible with any other item of PPE worn. PPE at Work Regulations do not apply where separate Regulations require the provision and use of PPE against specific hazards, e.g. gloves for use with dangerous chemicals, covered by Control Figure 1.7 Eye protection of Substances Hazardous to Health Regulations 2002. objects; industrial scalp protectors to protect The employer also has duties to: against striking fixed obstacles, scalping or XXassess the risks and PPE intended to be issued entanglement and caps and hairnets to protect and that it is suitable; against scalping and entanglement. Some safety XXmaintain, clean and replace PPE; helmets incorporate or can be fitted with specially XXprovide storage for PPE when it is not being designed eye or hearing protection and can used; include neck protection for use during welding. Do XXensure that PPE is properly used; not use head protection if it is damaged – always XXgive training, information and instruction to have it replaced. employees on the use of PPE and how to look after it. 1.13.1.3 Feet and leg protection Serve to guard against the hazards of electrostatic 1.13.1 Personal protective build-up, abrasion, wet, slipping, cuts and equipment punctures, falling objects, chemical and metal PPE is defined as all equipment which is intended splash. Options include the provision of safety to be worn or held to protect against risk to health boots and shoes with protective toe caps and and safety. This includes most types of protective penetration-resistant mid soles as well as gaiters, clothing and equipment such as: eye protection, leggings and spats. Footwear can have a variety safety helmets, safety footwear, gloves, high- of sole patterns and materials to help prevent slips visibility clothing and safety harness. It does not in difficult conditions including oil and chemical include hearing protection and most respiratory spillage. They can also be antistatic and electrically equipment, which are covered by separate or thermally insulating. It is important to select existing regulations. footwear appropriate for the identified risks. 1.13.1.1 Eye protection 1.13.1.4 Hand and arm protection Serves as a guard against the hazards of impact, Gloves, gauntlets, mitts, wrist cuffs and armlets splashes from chemicals or molten metal, liquid provide protection against a range of hazards such droplets (chemical mists and sprays), dust, gases as abrasion, temperature extremes, cuts and and welding arcs. Eye protectors include safety punctures, impact, chemicals, electric shock, skin spectacles, eye-shields, goggles, visors, welding infection, disease or contamination. Avoid using filters, face shields and hoods (Fig. 1.7). Make gloves when operating machines such as bench sure the eye protection has the right combination drills where gloves can get caught. Barrier creams of impact/dust/splash/molten metal protection for may sometimes be used as an aid to skin hygiene the task and fits the user properly. but are no substitute for proper PPE. Wearing gloves for long periods can lead to skin problems 1.13.1.2 Head protection but using separate cotton inner gloves may help prevent this. Some people may be allergic to Includes industrial safety helmets to protect materials used in gloves, e.g. latex. against falling objects or impact with fixed 13 1 Safe practices 1 1.13.1.5 Body protection 1.14.1 Workstation analysis and controls Types of clothing used for body protection include conventional and disposable overalls, In using DSE, as in any other type of work, ill boiler suits, aprons, high-visibility clothing and health can result from poor equipment or furniture, specialist protective clothing, e.g. chain mail work organisation, working environment, job aprons. They are used to protect against hazards design and posture from inappropriate working such as temperature extremes, adverse weather, methods. Health problems associated with DSE chemical and metal splash, spray from spray can be prevented in the majority of cases by good guns, impact or penetration, contaminated dust or ergonomic design of the equipment, workplace excessive wear or entanglement of own clothing. and job. Ergonomics is the science of making sure The choice of materials includes flame retardant, that work tasks, equipment, information and the antistatic, chain mail, chemically impermeable and working environment are suitable for every worker, high visibility. so that work can be done safely and productively. Risk assessment should first identify any hazard 1.14 Health and Safety (Display and then enable an evaluation of the risks. Risks Screen Equipment) to health may arise from a combination of factors Regulations 1992 (as and are particularly likely to occur when the work, amended) workplace and work environment do not take account of the workers’ needs. These Regulations only apply to employers An employer shall ensure that a workstation whose workers regularly use display screen meets the requirements of DSE Regulations by equipment (DSE) as a significant part of their ensuring, for example: work, e.g. daily, for continuous periods of an XXadequate lighting; hour or more. The Regulations do not apply to XXadequate contrast – no glare or distracting workers who use DSE infrequently or for short reflections; periods of time. DSE are devices or equipment XXdistracting noise minimised; with a graphic display screen and includes XXleg room and clearances to allow postural computer display screens, laptops and touch changes; screens. XXwindow covering if needed to minimise glare; Some workers may experience fatigue, eye XXsoftware appropriate to task, adapted to user, strain, upper limb disorders and backache providing feedback on system status, e.g. error from overuse or improper use of DSE. Upper message; limb disorders include problems of the XXscreen – stable image, adjustable, readable, arms, hands, shoulders and neck linked to glare/reflection free; work activities. These problems can also be XXkeyboard – usable, adjustable, detachable, experienced from poorly designed workstations legible; or working environment. The cause may not XXwork surface with space for flexible be obvious and can be due to a combination of arrangement of equipment and documents – factors. glare free; Any employer who has DSE users must: XXchair – stable and adjustable; XXanalyse workstations to assess and reduce the XXfootrest if the user needs one. risks; Breaking up long spells of DSE work helps prevent XXmake sure controls are in place; fatigue, eye strain, upper limb disorders and back XXprovide information and training; ache. The employer needs to plan so that users XXprovide eye and eyesight tests on request, and can interrupt prolonged use of DSE with changes special spectacles if required; of activity. Organised or scheduled rest breaks XXreview the assessment when the user or DSE may sometimes be a solution. The following may changes. help users: 14 1 Safe practices XXstretch and change position; XXlook into the distance from time to time and work, then the employer must pay for a basic pair of frames and lenses. If the user’s normal 1 blink often; spectacles are suitable for display screen work, XXchange activity before user gets tired; the employer does not have to pay for them. XXshort, frequent breaks are better than longer, infrequent ones. 1.14.4 Review DSE assessments need to be reviewed when: 1.14.2 Training XXmajor changes are made to the equipment, The employer must provide information, furniture, work environment or software; instruction and health and safety training to users XXusers change workstations; to help them identify risks and safe working XXthe nature of the work task changes practices. When training users the following considerably; should be considered: XXit is thought that the controls in place may be XXthe risks from DSE work and the controls put causing other problems. in place; XXhow to adjust furniture, work and equipment 1.15 The Reporting of Injuries, positions; Diseases and Dangerous XXhow to organise the workplace to avoid Occurrences Regulations awkward or frequently repeated stretching 2013 (RIDDOR) movements; XXhow to clean the screen, keyboard and mouse; These Regulations require injuries, diseases and XXwho to contact for help and to report problems occurrences in specific categories to be notified to or symptoms.