Industrial Materials and Processes PDF
Document Details
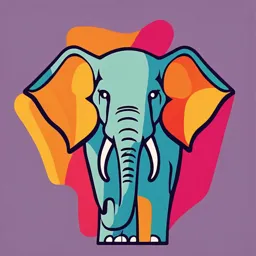
Uploaded by AppreciatedHawthorn2665
University of the Philippines Diliman
Dr. Iris Ann Martinez
Tags
Summary
This document provides an outline for a course on industrial materials and processes, covering topics such as finishing operations, mechanical cleaning, chemical cleaning, and coatings. It is likely lecture notes or class materials for an engineering course.
Full Transcript
Industrial Materials and Processes Finishing Operations: Mechanical Cleaning, Chemical Cleaning, Coatings Department of Industrial Engineering and Operations Research, College of Engineering University of the Philippines Diliman Industrial Materials and Process...
Industrial Materials and Processes Finishing Operations: Mechanical Cleaning, Chemical Cleaning, Coatings Department of Industrial Engineering and Operations Research, College of Engineering University of the Philippines Diliman Industrial Materials and Processes, Dr. Iris 1 Ann Martinez Outline A. Finishing operations B. Mechanical cleaning 1. Blast cleaning 2. Barrel finishing or tumbling 3. Vibratory finishing 4. Belt sanding 5. Wire brushing 6. Buffing Industrial Materials and Processes, 2 Dr. Iris Ann Martinez Outline B. Mechanical cleaning 7. Electropolishing C. Chemical cleaning 1. Alkaline cleaning 2. Solvent cleaning 3. Vapor degreasing 4. Ultrasonic cleaning 5. Acid pickling Industrial Materials and Processes, 3 Dr. Iris Ann Martinez Outline D. Coatings 1. Painting 2. Powder coating 3. Hot-dip coatings 4. Chemical conversion coatings 5. Blackening or coloring metals 6. Electroplating 7. Anodizing Industrial Materials and Processes, 4 Dr. Iris Ann Martinez Outline D. Coatings 8. Electroless plating 9. Mechanical plating 10.Porcelain enameling Industrial Materials and Processes, 5 Dr. Iris Ann Martinez A. Finishing Operations Metal finishing operations involve treatment of a metal workpiece in order to modify its surface properties, impart a particular attribute to the surface, or produce a decoration. They include surface preparation to clean and remove contaminants, and the addition of coatings such as paints and platings. Industrial Materials and Processes, 6 Dr. Iris Ann Martinez Mechanical Cleaning In mechanical cleaning, mechanical methods are used to remove surface contamination resulting from the various manufacturing processes. Such contaminants may include sand from molds and cores used in casting, scale from hot-working processes, and oxides such as rust. Industrial Materials and Processes, 7 Dr. Iris Ann Martinez Mechanical Cleaning Mechanical cleaning processes 1. Blast cleaning 2. Barrel finishing or tumbling 3. Vibratory finishing 4. Belt sanding 5. Wire brushing 6. Buffing 7. Electropolishing Industrial Materials and Processes, 8 Dr. Iris Ann Martinez Blast Cleaning Blast cleaning uses a media (abrasive) propelled into the surface using air, water, or even a wheel (wheel blasting uses a high-rpm blocked wheel to deliver the media). Abrasives, steel grit, metal shot, fine glass shot, plastic beads, and even CO2 are mechanically impelled against the surface to be cleaned. Industrial Materials and Processes, 9 Dr. Iris Ann Martinez Barrel Finishing Barrel finishing or tumbling is an effective means of finishing large numbers of small parts. Parts are loaded into a special barrel or drum until a predetermined level is reached. Additional media of metal slugs or abrasives (such as sand, granite chips, slag, or ceramic pellets) are added. Industrial Materials and Processes, 10 Dr. Iris Ann Martinez Vibratory Finishing Vibratory finishing is a versatile process widely used for deburring, radiusing (corner rounding), descaling, burnishing, cleaning, brightening, and fine finishing. In contrast to the barrel processing, vibratory finishing is performed in open containers. Industrial Materials and Processes, 11 Dr. Iris Ann Martinez Vibratory Finishing Tubs or bowls are loaded with workpieces and media and are vibrated at frequencies between 900 and 3600 cycles per minute. Industrial Materials and Processes, 12 Dr. Iris Ann Martinez Belt Grinder In belt grinding, the workpieces are held against a moving abrasive belt until the desired degree of finish is obtained. Because of the movement of the belt, the resulting surface contains a series of parallel scratches with a texture set by the grit of the belt. Industrial Materials and Processes, 13 Dr. Iris Ann Martinez Wire Brushing High-speed rotary wire brushing is sometimes used to clean surfaces and can also impart some small degree of material removal or smoothing. The resulting surface consists of a series of uniform curved scratches. Industrial Materials and Processes, 14 Dr. Iris Ann Martinez Buffing Buffing is a polishing operation in which the workpiece is brought into contact with a revolving cloth wheel that has been charged with a fine abrasive, such as polishing rouge. Industrial Materials and Processes, 15 Dr. Iris Ann Martinez Buffing polishing rouge Industrial Materials and Processes, Dr. Iris 16 Ann Martinez Electropolishing Electropolishing employs a DC electrolytic circuit with the workpiece as the anode. As current is applied, material is stripped from the surface, with material removal occurring preferentially from any raised location. Industrial Materials and Processes, 17 Dr. Iris Ann Martinez Electropolishing (see https://www.youtube.com/watch?v=0XUS9bRSihM) Industrial Materials and Processes, 18 Dr. Iris Ann Martinez Chemical Cleaning Chemical cleaning operations are effective means of removing oil, dirt, scale, or other foreign material that may adhere to the surface of a product, as a preparation for subsequent painting or plating. Industrial Materials and Processes, 19 Dr. Iris Ann Martinez Chemical Cleaning Chemical cleaning processes 1. Alkaline cleaning 2. Solvent cleaning 3. Vapor degreasing 4. Ultrasonic cleaning 5. Acid pickling Industrial Materials and Processes, 20 Dr. Iris Ann Martinez Alkaline Cleaning Alkaline cleaning is a commonly used method for removing a wide variety of soils (including oils, grease, wax, fine particles of metal, and dirt) from the surfaces of metals. Industrial Materials and Processes, 21 Dr. Iris Ann Martinez Alkaline Cleaning The cleaners are usually complex solutions of alkaline salts, additives to enhance cleaning or surface modification, and surfactants or soaps that are selected to reduce surface tension and displace, emulsify, and disperse the insoluble soils. Uses strong bases like sodium hydroxide or potassium hydroxide. Industrial Materials and Processes, 22 Dr. Iris Ann Martinez Alkaline Cleaning Industrial Materials and Processes, 23 Dr. Iris Ann Martinez Solvent Cleaning In solvent cleaning, oils, grease, fats, and other surface contaminants are removed by dissolving them in organic solvents derived from coal or petroleum, usually at room temperature. Industrial Materials and Processes, 24 Dr. Iris Ann Martinez Solvent Cleaning The common solvents include petroleum distillates (such as kerosene, naphtha, and mineral spirits), chlorinated hydrocarbons (such as methylene chloride and trichloroethylene), and liquids such as acetone, benzene, toluene, and the various alcohols. Industrial Materials and Processes, 25 Dr. Iris Ann Martinez Solvent Cleaning Industrial Materials and Processes, 26 Dr. Iris Ann Martinez Vapor Degreasing In vapor degreasing, the vapors of a chlorinated or fluorinated solvent are used to remove oil, grease, and wax from metal products. A nonflammable solvent, such as trichloroethylene, is heated to its boiling point, and the parts to be cleaned are suspended in its vapors. The vapor condenses on the work and washes the soluble contaminants back into the liquid solvent. Industrial Materials and Processes, 27 Dr. Iris Ann Martinez Vapor Degreasing Industrial Materials and Processes, Dr. Iris 28 Ann Martinez Ultrasonic Cleaning In ultrasonic cleaning the parts are suspended or placed in wire-mesh baskets that are then immersed in a liquid cleaning bath, often a water-based detergent. The bath contains an ultrasonic transducer that operates at a frequency that causes cavitation in the liquid. Industrial Materials and Processes, 29 Dr. Iris Ann Martinez Ultrasonic Cleaning The bubbles that form and implode provide the majority of the cleaning action, and if gross dirt, grease, and oil are removed prior to the immersion, excellent results can usually be obtained in 60 to 200 seconds. Industrial Materials and Processes, 30 Dr. Iris Ann Martinez Ultrasonic Cleaning Industrial Materials and Processes, Dr. Iris 31 Ann Martinez Acid Pickling In acid pickling, metal parts are first cleaned to remove oils and other contaminants and then dipped into dilute acid solutions to remove oxides and dirt that are left on the surface by the previous processing operations. Industrial Materials and Processes, 32 Dr. Iris Ann Martinez Acid Pickling The most common solution is a 10% sulfuric acid bath at an elevated temperature between 150° and 185° F. Muriatic acid is also used, either cold or hot. After the parts are removed from the pickling bath, they should be rinsed to flush the acid residue from the surface and then dipped in an alkaline bath to prevent rusting. Industrial Materials and Processes, 33 Dr. Iris Ann Martinez Acid Pickling acid pickling tanks Industrial Materials and Processes, 34 Dr. Iris Ann Martinez Coatings Surface coatings may be applied to the surface of a workpiece (substrate) for decorative and/or functional purposes such as imparting corrosion resistance. Industrial Materials and Processes, 35 Dr. Iris Ann Martinez Coatings Coating processes 1. Painting 2. Powder coating 3. Hot-dip coating 4. Chemical conversion coating 5. Blackening or coloring metals 6. Electroplating Industrial Materials and Processes, 36 Dr. Iris Ann Martinez Coatings Coating processes 7. Anodizing 8. Electroless plating 9. Mechanical plating 10.Porcelain enameling Industrial Materials and Processes, 37 Dr. Iris Ann Martinez Painting Paints and enamels are by far the most widely used finish on manufactured products, and a great variety are available to meet the wide range of product requirements. Industrial Materials and Processes, 38 Dr. Iris Ann Martinez Paints Most of the paints are synthetic organic compounds that contain pigments and dry by polymerization or by a combination of polymerization and adsorption of oxygen. Water is the most common carrying vehicle for the pigments. Industrial Materials and Processes, 39 Dr. Iris Ann Martinez Paints Nitrocellulose lacquers consist of thermoplastic polymers dissolved in organic solvent. Although fast drying (by the evaporation of the solvent) and capable of producing very beautiful finishes, they are not sufficiently durable for most commercial applications. Industrial Materials and Processes, 40 Dr. Iris Ann Martinez Paints The alkyds are a general-purpose paint but are not adequate for hard-service applications. Acrylic enamels are widely used for automotive finishes and may require catalytic or oven curing. Industrial Materials and Processes, 41 Dr. Iris Ann Martinez Paints Asphaltic paints, solutions of asphalt in a solvent, are used extensively in the electrical industry, where resistance to corrosion is required and appearance is not of prime importance. Industrial Materials and Processes, 42 Dr. Iris Ann Martinez Paint Application Methods Dipping is a simple and economical means of paint application when all surfaces of the part are to be coated. The products can be manually immersed into a paint bath or passed through the bath while on or attached to a conveyor. Industrial Materials and Processes, 43 Dr. Iris Ann Martinez Paint Application Methods Hand spraying is probably the most versatile means of application but can be quite costly in terms of labor and production time. When air or mechanical means provide the atomization, workers must exercise considerable skill to obtain the proper coverage. Industrial Materials and Processes, 44 Dr. Iris Ann Martinez Paint Application Methods In automatic spraying, some form of parts conveyor that transports the parts past a series of stationary spray heads. Industrial robots can be used to move the spray heads in a manner that mimics the movements of a human painter, maintaining uniform separation distance and minimizing waste. Industrial Materials and Processes, 45 Dr. Iris Ann Martinez Paint Application Methods automatic paint spraying Industrial Materials and Processes, Dr. Iris 46 Ann Martinez Paint Application Methods In electrostatic deposition, a DC electrostatic potential is applied between the atomizer and the workpiece. The atomized paint particles assume the same charge as the atomizer and are therefore repelled. The oppositely charged workpiece then attracts the particles, with the actual path of the particle being a combination of the kinetic trajectory and the electrostatic attraction. Industrial Materials and Processes, 47 Dr. Iris Ann Martinez Paint Application Methods electrostatic paint deposition Industrial Materials and Processes, Dr. Iris 48 Ann Martinez Powder Coating Powder coating is another variation of electrostatic spraying, but the particles are solid rather than liquid. Several coats, such as primer and finish, can be applied and then followed by a single baking, in contrast to the baking after each coat that is required in the conventional spray processes. Industrial Materials and Processes, 49 Dr. Iris Ann Martinez Powder Coating https://www.youtube.com/watch?v=m19Bn7UKqqY Industrial Materials and Processes, Dr. Iris 50 Ann Martinez Hot-Dip Coating Hot-dip galvanizing is the most widely used method of imparting corrosion resistance to steel. After the products, or sheets, have been cleaned to remove oil, grease, scale, and rust, they are fluxed by dipping into a solution of zinc ammonium chloride and dried. Next, the article is completely immersed in a bath of molten zinc. The zinc and iron react metallurgically to produce a coating that consists of a series of zinc– iron compounds and a surface layer of nearly pure zinc. Industrial Materials and Processes, 51 Dr. Iris Ann Martinez Hot-Dip Coating https://www.youtube.com/watch?v=UE7zY9JoVIc Industrial Materials and Processes, Dr. Iris 52 Ann Martinez Chemical Conversion Coating In chemical conversion coating, the surface of the metal is chemically treated to produce a nonmetallic, nonconductive surface that can impart a range of desirable properties. The most popular types of conversion coatings are chromate and phosphate. Aluminum, magnesium, zinc, and copper (as well as cadmium and silver) can all be treated by a chromate conversion process that usually involves immersion in a chemical bath. Industrial Materials and Processes, 53 Dr. Iris Ann Martinez Chemical Conversion Coating Industrial Materials and Processes, Dr. Iris 54 Ann Martinez Blackening or Coloring Metals Many steel parts are treated in the process of blackening to produce a black, iron oxide coating—a lustrous surface that is resistant to rusting when handled. Since this type of oxide forms at elevated temperatures, the parts are usually heated in some form of special environment, such as spent carburizing compound or special blackening salts. Industrial Materials and Processes, 55 Dr. Iris Ann Martinez Blackening or Coloring Metals blackening Industrial Materials and Processes, Dr. Iris 56 Ann Martinez Electroplating In electroplating, a DC voltage is applied between the parts to be plated (which is made the cathode) and an anode material that is either the metal to be plated or an inert electrode. Both of these components are immersed in a conductive electrolyte, which may also contain dissolved salts of the metal to be plated as well as additions to increase or control conductivity. (https://www.youtube.com/watch?v=aDkpbB31le k) Industrial Materials and Processes, 57 Dr. Iris Ann Martinez Electroplating In response to the applied voltage, metal ions migrate to the cathode, lose their charge, and deposit on the surface. Virtually all commercial metals can be plated, including aluminum, copper, brass, steel, and zinc-based die castings. Plastics can be electroplated, provided that they are first coated with an electrically conductive material. Industrial Materials and Processes, 58 Dr. Iris Ann Martinez Electroplating Industrial Materials and Processes, Dr. Iris 59 Ann Martinez Anodizing Anodizing is an electrochemical process, that is somewhat the reverse of electroplating, which produces a conversion-type coating on aluminum that can improve corrosion and wear resistance and impart a variety of decorative effects. Industrial Materials and Processes, 60 Dr. Iris Ann Martinez Anodizing If the workpiece is made the anode of an electrolytic cell, instead of a plating layer being deposited on the surface, a reaction progresses inward, increasing the thickness of the hard hexagonal aluminum oxide crystals on the surface. (https://www.youtube.com/watch?v=c11nl 8XcohE) Industrial Materials and Processes, 61 Dr. Iris Ann Martinez Anodizing Industrial Materials and Processes, Dr. Iris 62 Ann Martinez Electroless Plating In the electroless process, complex plating solutions (containing metal salts, reducing agents, complexing agents, pH adjusters, and stabilizers) are brought into contact with a substrate surface that acts as a catalyst or has been pretreated with catalytic material. doesn’t use electric current Industrial Materials and Processes, 63 Dr. Iris Ann Martinez Electroless Plating The metallic ion in the plating solution is reduced to metal and deposits on the surface. Since the deposition is purely a chemical process, the coatings are uniform in thickness, independent of part geometry. The rate of deposition is considerably slower than with electroplating. Industrial Materials and Processes, 64 Dr. Iris Ann Martinez Electroless Plating electroless nickel plating Industrial Materials and Processes, Dr. Iris 65 Ann Martinez Mechanical Plating Mechanical plating, also known as peen plating or impact plating, is an adaptation of barrel finishing in which coatings are produced by cold-welding soft, malleable metal powder onto the substrate. Numerous small products are first cleaned and may be given a thin galvanic coating of either copper or tin. Industrial Materials and Processes, 66 Dr. Iris Ann Martinez Mechanical Plating They are then placed in a tumbling barrel, along with a water slurry of the metal powder to be plated, glass or ceramic tumbling media, and chemical promoters or accelerators. The media particles peen the metal powder onto the surface, producing uniform-thickness deposits. Industrial Materials and Processes, 67 Dr. Iris Ann Martinez Mechanical Plating Industrial Materials and Processes, Dr. Iris 68 Ann Martinez Porcelain Enameling In porcelain enameling, metals are coated with a variety of glassy, inorganic materials that impart resistance to corrosion and abrasion, decorative color, electrical insulation, or the ability to function in high-temperature environments. Multiple coats may be used, with the first or ground coat being selected to provide adhesion to the substrate and the cover coat to provide the surface characteristics. Industrial Materials and Processes, 69 Dr. Iris Ann Martinez Porcelain Enameling The material is usually applied in the form of a multicomponent suspension or slurry (by dipping or spraying), which is then dried and fired. During the firing operation, which may require temperatures in the range of 800° to 8000°F, the coating materials melt, flow, and resolidify. Industrial Materials and Processes, 70 Dr. Iris Ann Martinez Porcelain Enameling Industrial Materials and Processes, Dr. Iris 71 Ann Martinez Industrial Materials and Processes Plastics: Properties, Uses, Thermoplastics, Thermosets Department of Industrial Engineering and Operations Research, College of Engineering University of the Philippines Diliman Industrial Materials and Processes, 1 Dr. Iris Ann Martinez Polymers Polymers are a large class of materials consisting of many small molecules (called monomers) that can be linked together to form long chains, thus they are known as macromolecules. One of the most important group of polymers is plastic. see https://www.youtube.com/watch?v=GirvOmjPZrc Industrial Materials and Processes, 2 Dr. Iris Ann Martinez Sources of Plastics Plastics are either found naturally or are man-made. The majority of everyday plastics are synthetic. The main source of synthetic plastic is crude oil, although coal and natural gas are also used. Industrial Materials and Processes, 3 Dr. Iris Ann Martinez Plastics from Oil During the refining of crude oil, paraffin, lubricating oil and gasoline are the bi- products. These are then broken down into monomers. When monomers are linked together in the process of polymerization, plastics are formed. Industrial Materials and Processes, 4 Dr. Iris Ann Martinez Polymerization Industrial Materials and Processes, 5 Dr. Iris Ann Martinez Chemical Composition of Plastic Most plastics are made from combining carbon with one or more other elements such as hydrogen, chlorine, fluorine or nitrogen. Industrial Materials and Processes, 6 Dr. Iris Ann Martinez General Properties of Plastics Plastics are light in weight; most have a specific gravity between 1.1 and 1.6, as compared with about 1.75 for magnesium. They have good corrosion resistance and resistance to chemicals. Industrial Materials and Processes, 7 Dr. Iris Ann Martinez General Properties of Plastics They have good electrical resistance and are good for insulating electrical materials. Industrial Materials and Processes, 8 Dr. Iris Ann Martinez General Properties of Plastics They have much lower thermal conductivity than metals and thus are good heat insulators. Industrial Materials and Processes, 9 Dr. Iris Ann Martinez General Properties of Plastics They can be obtained in an almost unlimited range of colors, either transparent or opaque. Industrial Materials and Processes, 10 Dr. Iris Ann Martinez General Properties of Plastics Excellent surface finish can be obtained without added operations beyond those required to convert the plastic from raw material into the final shape. Industrial Materials and Processes, 11 Dr. Iris Ann Martinez General Properties of Plastics Objects frequently can be produced from plastics, from raw material to final shape, in only one operation, through several basic processes. Industrial Materials and Processes, 12 Dr. Iris Ann Martinez General Properties of Plastics They are inferior to engineering metals with respect to strength. Their dimensional stability are greatly inferior to metals. Industrial Materials and Processes, 13 Dr. Iris Ann Martinez Uses of plastics Industrial Materials and Processes, 14 Dr. Iris Ann Martinez Uses of Plastics Packaging or container materials where the combination of lightness, color, and ease of production is of great importance Industrial Materials and Processes, 15 Dr. Iris Ann Martinez Uses of Plastics Insulators in electrical equipment and as handles for hot articles: due to their low electrical and/or thermal conductivity Industrial Materials and Processes, 16 Dr. Iris Ann Martinez Uses of Plastics Foam: soft, pliable foams are used extensively as cushioning material, while rigid foams are used inside thin sheet metal structures to provide compression strength Industrial Materials and Processes, 17 Dr. Iris Ann Martinez Uses of Plastics As substitute for more costly metal dies in connection with tooling for various press- working operations for forming sheet metals. Industrial Materials and Processes, 18 Dr. Iris Ann Martinez Types of Plastics Thermosetting plastics: resistant to breakdown from chemical and thermal attack and weathering. Thermoplastics: soften with increasing temperature and become harder and stronger with decreasing temperature; no chemical change is involved. Industrial Materials and Processes, 19 Dr. Iris Ann Martinez Thermoplastics Soften with increasing temperature and become harder and stronger with decreasing temperature; no chemical change is involved Return to their original properties when cooled Industrial Materials and Processes, 20 Dr. Iris Ann Martinez Thermoplastics Industrial Materials and Processes, 21 Dr. Iris Ann Martinez Thermoplastics Acetals Polyethylenes Acrylics Polyimides Acrylonitrile- Polypropylenes Butadiene-Styrene Polystyrenes (ABS) Polysulfones Cellulosics Polyvinyl chloride Fluorocarbons (PVC) Polycarbonates Vinyls Polyesters Industrial Materials and Processes, 22 Dr. Iris Ann Martinez Thermoplastics Acetals: From acetic and alcohol Have good strength, good stiffness, Good resistance to creep, abrasion, moisture, heat and chemicals Typical applications: bearings, cams, gears, bushings, rollers, valves, pipes Industrial Materials and Processes, 23 Dr. Iris Ann Martinez Thermoplastics Acrylics: Highest optical clarity of any of the plastics High impact, flexural, tensile, and dielectric strength Available in a wide range of colors, good optical properties, high transparency but can be made opaque Industrial Materials and Processes, 24 Dr. Iris Ann Martinez Thermoplastics Acrylics: Easily scratched Moderate strength Good weather resistance, resistance to chemicals and electrical resistance Industrial Materials and Processes, 25 Dr. Iris Ann Martinez Thermoplastics ABS: Contains acrylonitrile, butadiene, or styrene Low weight Good strength Exceptional toughness Used in a wide range of applications where in- service conditions are quite severe Industrial Materials and Processes, 26 Dr. Iris Ann Martinez Thermoplastics Cellulosics: Have a wide range of mechanical properties depending on their composition Can be made rigid, strong, and tough Weather poorly and are affected by heat and chemicals Industrial Materials and Processes, 27 Dr. Iris Ann Martinez Thermoplastics Cellulose acetates: Obtainable in unlimited colors Has good insulating qualities Easily molded Has high moisture absorption and is affected by alcohols and alkalis Industrial Materials and Processes, 28 Dr. Iris Ann Martinez Thermoplastics Cellulose acetate butyrate: Developed to have better impact strength and moisture resistance than cellulose acetate Used for applications that must withstand rough usage Industrial Materials and Processes, 29 Dr. Iris Ann Martinez Thermoplastics Ethyl cellulose: Good impact strength and maintains its toughness at low temperatures High electrical resistance In pharmaceuticals they mask the taste of bitter actives, enhance the strength and appearance of tablets and capsules, and enable controlled release formulations Industrial Materials and Processes, 30 Dr. Iris Ann Martinez Thermoplastics Fluorocarbons: Resistant to high temperatures (Teflon – melting point of 327°C) Has a low coefficient of friction Industrial Materials and Processes, 31 Dr. Iris Ann Martinez Thermoplastics Polyamides: From the words poly, amine, and carboxyl acid Two types: nylons and aramids Industrial Materials and Processes, 32 Dr. Iris Ann Martinez Thermoplastics Nylons: Good mechanical properties Good abrasion resistance and toughness Good resistance to most chemicals Hygroscopic - absorbs water Industrial Materials and Processes, 33 Dr. Iris Ann Martinez Thermoplastics Aramids: Very high tensile strength and stiffness Kevlar® is an aramid, it is lightweight and extraordinarily strong, with five times the strength of steel on an equal- weight basis. It is best known for its use in ballistic and stab- resistant body armor Industrial Materials and Processes, 34 Dr. Iris Ann Martinez Thermoplastics Polycarbonates: Versatile High strength and outstanding toughness, high impact resistance Can be made resistant to chemicals Industrial Materials and Processes, 35 Dr. Iris Ann Martinez Thermoplastics Polyesters: Extremely strong Very durable Hydrophobic and quick drying Retains its shape Industrial Materials and Processes, 36 Dr. Iris Ann Martinez Thermoplastics Polyethylenes: Tough and have high electrical resistance Industrial Materials and Processes, 37 Dr. Iris Ann Martinez Thermoplastics Polyethylenes (PE): Low-density PE (LDPE), Medium-density PE (MDPE), High-density PE (HDPE) Industrial Materials and Processes, 38 Dr. Iris Ann Martinez Thermoplastics Polyimides: Great dimensional stability under high heat conditions Excellent chemical resistance Industrial Materials and Processes, 39 Dr. Iris Ann Martinez Thermoplastics Polypropylenes: One of the lightest plastics Improved strength, stiffness and higher temperature capability over polyethylene Industrial Materials and Processes, 40 Dr. Iris Ann Martinez Thermoplastics Polystyrenes: High dimensional stability and very low water absorption Somewhat brittle, inexpensive Citrus juices and cleaning fluids affect it adversely and it burns readily Industrial Materials and Processes, 41 Dr. Iris Ann Martinez Thermoplastics Polysulfones: Stable Heat resistant and self- extinguishing Transparent Used in medical and sterilizing equipment Industrial Materials and Processes, 42 Dr. Iris Ann Martinez Thermoplastics Polyvinyl chloride: Very durable Long lasting Good impact strength and weatherproof attributes Excellent electrical insulation properties Industrial Materials and Processes, 43 Dr. Iris Ann Martinez Thermoplastics Vinyls: Can be obtained in a wide range of types, from thin, rubbery films to rigid forms Resistant to acids and alkalis Industrial Materials and Processes, 44 Dr. Iris Ann Martinez Thermosets Resistant to breakdown from chemical and thermal attack and weathering. Do not become soft to any significant extent with increasing temperature. More rigid and harder than thermoplastics. Industrial Materials and Processes, 45 Dr. Iris Ann Martinez Thermosets Industrial Materials and Processes, 46 Dr. Iris Ann Martinez Thermosets Alkyds Aminos Ureas Epoxies Melamines Phenolics Polyesters Polyimides Silicones Industrial Materials and Processes, 47 Dr. Iris Ann Martinez Thermosets Alkyds: From alkyl, meaning alcohol and acid Possess good electrical insulating properties, impact resistance, low water absorption Typical applications: electrical and electronic components, enamels Industrial Materials and Processes, 48 Dr. Iris Ann Martinez Thermosets Aminos: Generally hard, rigid, and resistant to abrasion, creep Typical applications: small appliance housing, countertops, toilet seats, handles Industrial Materials and Processes, 49 Dr. Iris Ann Martinez Thermosets Urea formaldehyde: Developed to fill the need for a thermosetting plastic that could be produced in light colors not obtained in the phenolics Industrial Materials and Processes, 50 Dr. Iris Ann Martinez Thermosets Urea formaldehyde: Widely used for containers and housings but should not be used outdoors Typical applications: lighting fixtures, adhesives, finishes, medium-density fiberboard (MDF), electrical components and sometimes molded into objects Industrial Materials and Processes, 51 Dr. Iris Ann Martinez Thermosets Epoxies: Good toughness, elasticity, chemical resistance, and dimensional stability Strong adhesive properties Industrial Materials and Processes, 52 Dr. Iris Ann Martinez Thermosets Epoxies: Easily compounded to cure at moderate or room temperatures without the use of pressure Typical applications: tools and dies, adhesives, tanks Industrial Materials and Processes, 53 Dr. Iris Ann Martinez Thermosets Melamines: Resistant to heat, water and many chemicals Have outstanding electrical arc resistance Available in a full range of translucent or opaque colors Typical application: dinnerwares Industrial Materials and Processes, 54 Dr. Iris Ann Martinez Thermosets Phenolics: Fairly hard, relatively strong, low in cost, easily molded Resistant to heat, water, electricity, chemicals Obtainable only in opaque colors Typical applications: knobs, handles, telephones, laminated panels Industrial Materials and Processes, 55 Dr. Iris Ann Martinez Thermosets Polyesters: Stiff, hard, brittle unless laminated Good electrical insulator Resists chemicals well Application: casting and encapsulation, bonding of other materials Industrial Materials and Processes, 56 Dr. Iris Ann Martinez Thermosets Polyimides: Great dimensional stability under high heat conditions Excellent chemical resistance Application: tubing Industrial Materials and Processes, 57 Dr. Iris Ann Martinez Thermosets Silicones: Semi-organic Heat resistant High dielectric properties Low moisture absorption Industrial Materials and Processes, 58 Dr. Iris Ann Martinez Industrial Materials and Processes Plastics: Production Processes, Joining Processes Department of Industrial Engineering and Operations Research, College of Engineering University of the Philippines Diliman Industrial Materials and Processes, 1 Dr. Iris Ann Martinez Constituents in Molded Plastics Materials are added to plastics for purposes of: – improving their properties – reducing cost – improving their moldability, or – imparting color Industrial Materials and Processes, Dr. Iris Ann Martinez 2 Constituents in Molded Plastics Constituents are classified as: – Fillers: added to improve strength or to decrease cost; they also aid in controlling shrinkage; the most common are wood flour, cloth fibers, glass fibers. Industrial Materials and Processes, Dr. Iris Ann Martinez 3 Constituents in Molded Plastics – Plasticizers: added in small amounts to increase and control the flow of the plastic during molding; the amount is held to a minimum because it is likely to affect the stability of the finished product through gradual loss during aging. Industrial Materials and Processes, Dr. Iris Ann Martinez 4 Constituents in Molded Plastics – Coloring agents: may either be dyes, which actually alter the color of the resin, or colored pigments that through their presence impart a desired color. Industrial Materials and Processes, Dr. Iris Ann Martinez 5 Constituents in Molded Plastics – Lubricants: added in small amounts to increase and control the flow of the plastic during molding; wax, stearates, and occasionally soaps are used as lubricants. Industrial Materials and Processes, Dr. Iris Ann Martinez 6 Production Processes Industrial Materials and Processes, Dr. Iris Ann Martinez 7 Casting Casting: simplest of the processes because no fillers are used and no pressure is involved Industrial Materials and Processes, Dr. Iris Ann Martinez 8 Blow Molding Blow molding: used extensively for making hollow products, such as bottles and other containers Industrial Materials and Processes, Dr. Iris Ann Martinez 9 Blow Molding Industrial Materials and Processes, Dr. Iris Ann Martinez 10 Injection Stretch Blow Molding https://www.directindustry.com/prod/nissei-asb-machine-co-ltd/product-74412-1433739.html Industrial Materials and Processes, Dr. Iris Ann Martinez 11 Extrusion Blow Molding Industrial Materials and Processes, Dr. Iris Ann Martinez 12 Cold Molding Cold molding: the raw material is pressed to shape while cold, is then removed from the mold and baked in an oven until curing is complete Industrial Materials and Processes, Dr. Iris Ann Martinez 13 Cold Molding Industrial Materials and Processes, Dr. Iris Ann Martinez 14 Hot-Compression Molding Hot-compression molding: almost exclusively used for thermosetting materials Industrial Materials and Processes, Dr. Iris Ann Martinez 15 Compression Molding Industrial Materials and Processes, Dr. Iris Ann Martinez 16 Transfer Molding Transfer molding: used to avoid the turbulence and uneven flow that often result from the non-uniform, high pressures in hot-compression molding Industrial Materials and Processes, Dr. Iris Ann Martinez 17 Transfer Molding Industrial Materials and Processes, Dr. Iris Ann Martinez 18 Transfer Molding Industrial Materials and Processes, Dr. Iris Ann Martinez 19 Injection Molding Injection molding: used to produce more thermoplastic products than any other process Industrial Materials and Processes, Dr. Iris Ann Martinez 20 Injection Molding Industrial Materials and Processes, Dr. Iris Ann Martinez 21 Injection Molding Industrial Materials and Processes, Dr. Iris Ann Martinez 22 Injection Molding Industrial Materials and Processes, Dr. Iris Ann Martinez 23 Injection Molding polyethylene frisbee Industrial Materials and Processes, Dr. Iris Ann Martinez 24 Reaction Injection Molding Industrial Materials and Processes, Dr. Iris Ann Martinez 25 Jet Molding Jet molding: modified injection molding process used for thermosetting plastics Industrial Materials and Processes, Dr. Iris Ann Martinez 26 Rotational Molding Used to form large or small hollow shapes using powdered plastic Industrial Materials and Processes, Dr. Iris Ann Martinez 27 Rotational Molding Industrial Materials and Processes, Dr. Iris Ann Martinez 28 Extrusion Extrusion: the plastic material is fed from a hopper into a screw chamber from whence the rotating screw conveys it through a preheating chamber, where it is compressed, and then forces it through a heated die and onto a conveyor belt. Industrial Materials and Processes, Dr. Iris Ann Martinez 29 Extrusion Industrial Materials and Processes, Dr. Iris Ann Martinez 30 Extrusion Industrial Materials and Processes, Dr. Iris Ann Martinez 31 Laminating Laminating: process in which sheets of paper, or cloth made from glass or other types of fibers, are impregnated with thermosetting liquid resin and then placed together to build up a desired thickness Industrial Materials and Processes, Dr. Iris Ann Martinez 32 Laminating Industrial Materials and Processes, Dr. Iris Ann Martinez 33 Laminating Industrial Materials and Processes, Dr. Iris Ann Martinez 34 Vacuum Forming Vacuum forming: used extensively to form shapes from thermoplastic materials Industrial Materials and Processes, Dr. Iris Ann Martinez 35 Vacuum Forming Industrial Materials and Processes, Dr. Iris Ann Martinez 36 Foamed Plastics Foamed plastics: made by combining with the plastic resin a foaming agent that releases gas when the combination is heated during molding. Industrial Materials and Processes, Dr. Iris Ann Martinez 37 Structural Foam Molding Industrial Materials and Processes, Dr. Iris Ann Martinez 38 Solvent Bonding Solvent bonding is traditionally only used in joining thermoplastics. Solvent bonding involves coating plastics with a solvent and clamping them together. The solvent softens the plastics and when it evaporates, the plastics are bonded together. Industrial Materials and Processes, Dr. Iris Ann Martinez 39 Solvent Bonding Industrial Materials and Processes, Dr. Iris Ann Martinez 40 Welding Plastics like polypropylene that are difficult to weld are usually bonded by induction welding. To perform an induction weld, plastics are placed around a metal object and run through a magnetic field, which causes the plastics to heat and weld together. Industrial Materials and Processes, Dr. Iris Ann Martinez 41 Plastic Welding Industrial Materials and Processes, Dr. Iris Ann Martinez 42 Welding Vibration welding is efficient but is often only employed when other bonding methods are impractical. Vibration welding involves joining two plastics and vibrating one of them. The vibrations create friction, which heats the plastics and welds them together. Industrial Materials and Processes, Dr. Iris Ann Martinez 43 Plastic Vibration Welding Industrial Materials and Processes, Dr. Iris Ann Martinez 44 Ultrasonic Welding Industrial Materials and Processes, Dr. Iris Ann Martinez 45 Ultrasonic Welding Industrial Materials and Processes, Dr. Iris Ann Martinez 46 Mechanical Fastening Mechanical fastening is used when precision bonding is not required. This is the simplest way of joining plastics. Mechanical fastening is more suited for joining stronger plastics. Mechanical fastening involves joining plastics together with simple fasteners like latches and nails. Industrial Materials and Processes, Dr. Iris Ann Martinez 47 Mechanical Fasteners Industrial Materials and Processes, Dr. Iris Ann Martinez 48 Surface Preparation Wash the plastic object to be painted. Pretreat using abrasives, chemical etching, corona discharge, combustion spray, plasma spray, or lasers. Industrial Materials and Processes, Dr. Iris Ann Martinez 49 Surface Preparation When sanding is used to abrade the substrate, the grit must be fine enough to prevent scratch or gouge marks on the surface that will show through the paint. Industrial Materials and Processes, Dr. Iris Ann Martinez 50 Painting Prime large objects with primer designed specifically for plastic. Even after removing the shine, the new paint needs help adhering. Plastic primer bonds to the plastic and provides a porous surface for the new paint. Industrial Materials and Processes, Dr. Iris Ann Martinez 51 Painting Plastics Add plastic flex agent to your paint if the plastic object is flexible. Roll, brush or spray on the new paint. Industrial Materials and Processes, Dr. Iris Ann Martinez 52 Painting Plastics Industrial Materials and Processes, Dr. Iris Ann Martinez 53 Electroplating The basic problem in attempting to electroplate onto plastics is that they are electrically non-conductive and cannot be immersed in a plating solution and coated in the way that metal objects can. Industrial Materials and Processes, Dr. Iris Ann Martinez 54 Electroplating Plastics Basic steps: – Etch in chromic acid based solution to promote adhesion – Neutralise excess chromic acid – Activate the plastics surface with a solution containing tin and palladium salts that catalyse nickel or copper growth from the subsequent electroless processes. Industrial Materials and Processes, Dr. Iris Ann Martinez 55 Electroplating Plastics Basic steps: – Coat the surface with either nickel or copper (nickel is now generally the preferred commercial process) from an electroless plating solution. Industrial Materials and Processes, Dr. Iris Ann Martinez 56 Plastics for Electroplating Although a wide range of plastics resins can be electroplated the market has always been dominated by acrylonitrile butadiene styrene (ABS). This has been estimated to account for 90% of the material currently used in this application worldwide. Industrial Materials and Processes, Dr. Iris Ann Martinez 57 Electroplated Plastic Products Industrial Materials and Processes, Dr. Iris Ann Martinez 58 Q1. Are there metals that are not suitable to be chemically cleaned under each chemical cleaning process? Yes, some metals are not suitable to be cleaned using chemical cleaning. Examples are: 1. Aluminum. Highly reactive with strong acids and alkalis, which can cause corrosion. 2. Copper and copper alloys. Can be attacked by strong oxidizing agents and acids. 3. Zinc. Susceptible to corrosion by strong acids and alkalis. 4. Magnesium. Highly reactive, especially with strong acids, and can ignite and explode. 5. Lead. Can be corroded by strong acids and https://mavink.com/explore/Periodic-Table-Most-Reactive-Metals oxidizing agents. Industrial Materials and Processes 31/10/2024 4 Prof. Iris Ann Martinez, PhD Q2. What are the differences between cellulosics and cellulose acetates according to properties and processing? Cellulosics Cellulose Acetate Origin Natural from plant cell Cellulose chemically walls modified by acetylation, replacing hydroxyl groups https://www.researchgate.net/figure/Molecular-structure-of-cellulose-and-cellulose-acetate- CA_fig7_356265784 with acetyl groups Properties Insoluble in water; high More soluble in organic tensile strength; good solvents, flexible and thermal stability thermally stable Application Edible fibers; Photographic films, thickeners in food coatings, eyeglass products; structural frames, synthetic fibers component in various for clothing, cigarette https://ph.pinterest.com/pin/discover-the- versatility-of-cellulosics--467881848769504089/ materials filters Processing Minimal chemical More complex chemical modification processes to achieve https://fryucmc.en.made-in-china.com/product/tmLYkRvKbocN/China-Yucmc-Sodium- Carboxy-Cellulose-Sodium-Carboxy-Methyl-Cellulose-CMC-CMC-Powder-Food-Grade- desired properties Carboxymethyl-Cellulose.html Industrial Materials and Processes, 31/10/2024 5 Prof. Iris Ann Martinez, PhD Q3. Are there situations where different chemical finishing operations change or damage the chemical composition of the product? Yes. In many instances, before a product is mass-produced, the manufacturer is aware of this. For example: Metals. Acid pickling. Harsh acids can cause pitting or excessive removal of the metal surface, leading to structural weaknesses Electroplating. Improperly controlled https://www.imetllc.com/steel-hydrogen-embrittlement/video- thumbnail-steel-hydrogen-embrittlement/ electroplating can lead to hydrogen embrittlement, making the metal brittle and prone to cracking Industrial Materials and Processes 31/10/2024 6 Prof. Iris Ann Martinez, PhD Q4. Are the chemicals used for chemical cleaning of metals can be created by us in our homes or the specific compounds can only be bought? What are these chemicals that we can create easily in our homes? Chemical Purpose White vinegar Effective for cleaning and (acetic acid), descaling metals like CH3COOH stainless steel and copper Baking soda Great for scrubbing and (sodium removing stains from bicarbonate) metals NaHCO3 Lemon juice (citric Removes tarnish from acid) C6H8O7 metals like Copper and brass https://mybios.me/homemade-bathroom-cleaner-vinegar-dawn-lemon-juice/ Industrial Materials and Processes 31/10/2024 7 Prof. Iris Ann Martinez, PhD Q5. Are there any instances where metalloids can be used as a substitute to plastics or polymers? Can you give an example or application where metalloids can be substituted to polymers or plastics? Yes. There are instances where metalloids can be used as substitutes for polymers, especially when their properties are advantageous for the application. For example: Silicon. A metalloid widely used in the electronics https://www.howitworksdaily.com/why-are-microchips-made-of-silicon/ industry as a semiconductor material. These are used in place of polymers in applications like solar cells and microchips because of its semiconducting properties. Boron. Used in the production of high-strength, lightweight materials, e.g., boron fibers used as reinforcement in composite materials for use in https://borates.today/boron-sports-equipment/ aerospace and sporting goods. Industrial Materials and Processes 31/10/2024 8 Prof. Iris Ann Martinez, PhD Q6. What can happen to a polymer or plastic if it is created with a mix of a metalloid element? When polymers are created with a mix of metalloid elements, the following can happen: 1. Enhanced mechanical properties. Improved strength, durability, and stiffness. 2. Improved thermal stability. Increased heat resistance, making it more suitable for high-temperature applications. Metalloids: Definition, Properties, Uses, and Applications 3. Electrical conductivity. Some metalloids, like silicon and germanium, can impart semiconducting properties to polymer, making it useful in electronic applications. 4. Chemical resistance. Enhanced chemical resistance, making it less prone to degradation by chemicals. 5. Optical properties. Altered optical properties such as transparency and refractive index, which can be beneficial to optical applications. Industrial Materials and Processes 31/10/2024 9 Prof. Iris Ann Martinez, PhD Q7. Which is more likely used when processing a metalloid element? Is it more on plastic production process or metal production process? I think they have their own processing methods but these are closer to metal production processes. Their applications closer to metal product production. For example: Silicon and germanium are used for electronic devices like transistors and diodes Silicon and boron are used as alloys to improve the properties of metal and metal alloys, such as enhancing strength and corrosion resistance However, when their application is more for plastic products, their processing will be part of that plastic product production. For example: Additives. Metalloids can be used as addtives to enhance certain properties of plastics, but this is less common than the application of metalloids in metal-related processes. Industrial Materials and Processes 31/10/2024 10 Prof. Iris Ann Martinez, PhD