Understanding The Supply Chain PDF
Document Details
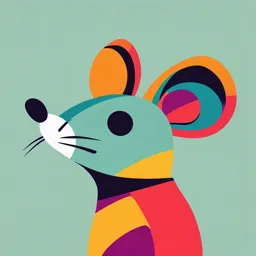
Uploaded by ChivalrousCongas
Tags
Summary
This document provides an overview of supply chain concepts, components, and dynamics. It discusses the goal of a supply chain and its impact on a firm's success, highlighting three key decision phases. The document also details supply chain components, process flow, interactions, and the importance of supply chain in achieving success.
Full Transcript
# Understanding the Supply Chain ## Learning Outcomes * Discuss the goal of a supply chain and explain the impact of supply chain decisions on the success of a firm. * Identify the three key supply chain decision phases and explain the significance of each one. ## What is a Supply Chain * A supp...
# Understanding the Supply Chain ## Learning Outcomes * Discuss the goal of a supply chain and explain the impact of supply chain decisions on the success of a firm. * Identify the three key supply chain decision phases and explain the significance of each one. ## What is a Supply Chain * A supply chain consists of all parties involved, directly or indirectly, in fulfilling a customer request. ## Supply Chain Components | Component | Description | |--------------------|---------------------------------------------------------------------------| | Customers | End-users of the products. | | Manufacturers | Entities producing goods for the supply chain. | | Retailers | Outlets selling products to consumers. | | Warehouses | Storage facilities for inventory management. | | Transporters | Services delivering products to various locations. | | Suppliers | Providers of raw materials and components. | ## Supply Chain Process Flow The process begins with a customer making a request. The manufacturer begins to fulfill the request. Suppliers provide necessary materials or components. Goods are transported to the next stage. Goods are stored in warehouses before distribution. Retailers prepare to sell the goods to customers. * Within each organization, such as a manufacturer, the supply chain includes all functions involved in receiving and filling a customer request. ## Supply Chain Dynamics A supply chain is dynamic and involves the constant flow of: * Information * Product * Funds The flow occurs among different stages. ### Fund Flow The financial transactions that facilitate supply chain operations. ### Information Flow The exchange of data and insights between supply chain entities. ### Product Flow The movement of goods from manufacturers to retailers and customers. ## Supply Chain Interaction Sequence | Interaction | Description | |-----------------------------|-----------------------------------------------------------------------------------------------------| | Walmart Sends Funds to Distributor | Walmart transfers funds to distributor. | | Distributor Receives Order | Distributor receives replenishment order from Walmart. | | Walmart Receives Payment | Walmart processes payment from customer. | | Distributor Sends Delivery Schedule | Distributor sends delivery schedule to Walmart. | | Walmart Sends Sales Data | Walmart sends sales data to distributor. | | Customer Purchases Product | Customer buys product from Walmart. | ## Walmart Supply Chain Process The Walmart Supply Chain consists of: * **Order Creation:** Orders are generated based on data. * **Transportation:** Orders are transported to stores. * **Payment Processing:** Funds are transferred to distributors. * **Information Exchange:** Pricing and schedules are shared. * **Recycling:** Packaging materials are recycled. ## Amazon Online Purchase Supply Chain | Interaction | Description | |---------------------------|----------------------------------------------------------------------------------------------| | Customer Browses Website | Customer views product options online. | | Order Information Processed | Order details are processed by Amazon. | | Suppliers Involved | Suppliers provide necessary products. | | Customer Makes Purchase | Customer completes the purchase transaction. | | Warehouse Fulfills Order | Warehouse prepares the order for shipment. | | Funds Transferred | Payment is processed and funds are transferred. | ## Amazon Supply Chain Journey * **Customer Interaction:** The customer browses the Amazon website for products. * **Order Placement:** The customer places an order and makes a payment. * **Order Processing:** Amazon’s warehouse processes the order using customer information. * **Supplier Coordination:** Suppliers and their suppliers coordinate to fulfill the order. * **Product Delivery:** The product is delivered to the customer. ## What is a Supply Chain? * In fact, the primary purpose of any supply chain is to satisfy customer needs and, in the process, generate profit for itself. ## Improve Customer Satisfaction Supply chain success contributes to customer satisfaction. ## What is a Supply Chain? * The term supply chain may also imply that only one player is involved at each stage. * In reality, a manufacturer may receive material from several suppliers and then supply several distributors. ## How to describe the structure of most supply chains? * **Supply Chain:** Implies a linear flow of products from suppliers to customers. * **Supply Network:** Reflects the interconnectedness of multiple suppliers, manufacturers, and distributors. ## Supply Chain Stages A typical supply chain may involve a variety of stages including the following: * **Customers** * **Retailers** * **Wholesalers/distributors** * **Manufacturers** * **component/raw material suppliers** * Each stage in a supply chain is connected through the flow of **products, information, and funds.** * These flows often occur in both directions and may be managed by one of the stages or an intermediary. ## Supply Chain Stages * For the sale of servers, Dell does not have a separate retailer, distributor, or wholesaler in the supply chain. * For the sale of consumer products such as PCs and tablets, Dell have retailers, wholesaler or distributor between the store and the manufacturer. ## The Objective Of Supply Chain * The objective of every supply chain should be to maximize the overall value generated. * **The value (also known as supply chain surplus) a supply chain generates is the difference between what the value of the final product is to the customer and the costs the entire supply chain incurs in filling the customer’s request.** ### Supply Chain Value * **Customer Value:** Represents the perceived worth of the final product to the customer. * **Supply Chain Costs:** Encompasses all expenses incurred in delivering the product to the customer. ## Supply Chain Surplus = Customer Value - Supply Chain Cost ## Importance of Supply chain * There is a close connection between the design and management of supply chain flows (product, information, and funds) and the success of a supply chain. ### Supply Chain Success * **Funds Flow:** The financial transactions that support and sustain supply chain activities. * **Product Flow:** The movement of goods from suppliers to customers, ensuring availability and efficiency. * **Information Flow:** The exchange of data and insights to optimize decision-making and operations. ## Importance of Supply chain * Walmart, Amazon, and Seven-Eleven Japan are examples of companies that have built their success on superior design, planning, and operation of their supply chain. | Companies | Success or Failure | Description | |----------------------------|-------------------|---------------------------------------------------------------------------------------------------| | Walmart | Success | Superior design, planning, and operation of their supply chain. | | Amazon | Success | Superior design, planning, and operation of their supply chain. | | Seven-Eleven Japan | Success | Superior design, planning, and operation of their supply chain. | | Webvan | Failure | Lack of effective supply chain design, planning, and operation led to failure. | | Borders | Failure | Lack of effective supply chain design, planning, and operation let to failure. | | Dell | Failure | Lack of effective supply chain design, planning, and operation lead to failure. | ## Importance of Supply chain * Walmart, Amazon, and Seven-Eleven Japan are examples of companies that have built their success on superior design, planning, and operation of their supply chain. ### Anatomy of Supply Chain Success * **Design:** The blueprint for supply chain efficiency. * **Planning:** Strategic foresight in supply chain management. * **Operation:** Execution of supply chain processes. ## Importance of Supply chain * Walmart, Amazon, and Seven-Eleven Japan are examples of companies that have built their success on superior design, planning, and operation of their supply chain. ### Achieving Supply Chain Success * **Success:** Achieving a successful and resilient supply chain. * **Adaptation to Change:** Adapting to market changes is vital for long-term success. * **Operational Excellence:** Efficient operations ensure smooth supply chain flows. * **Effective Planning:** Strategic planning is crucial for maintaining competitive advantage. * **Superior Design:** Companies like Walmart and Amazon excel through innovative supply chain design. ## Importance of Supply chain * Seven-Eleven Japan is example of a company that has used excellent supply chain design, planning, and operation to drive growth and profitability. ### Seven-Eleven Japan's Supply Chain Success * **Increase in Profits:** Significant profit growth by 2013. * **Growth in Sales:** Increase in sales revenue over the years. * **Product Availability:** Ensuring products are available as needed. * **Adaptation of Merchandising Mix:** Adjusting product offerings based on demand. * **Outstanding Information System:** Use of advanced technology to manage data. * **Responsive Replenishment System:** Implementation of a system to quickly restock products. ## Importance of Supply chain * As a result, the company has grown from sales of 1 billion yen in 1974 to almost 1.9 trillion yen in 2013, with profits in 2013 totaling 222 billion yen. ## Importance of Supply chain * Dell experienced significant revenue and profit growth due to its innovative supply chain strategies. * Dell achieved rapid customization of PCs, meeting diverse customer needs effectively. * Dell centralized its manufacturing and inventory, allowing for efficient assembly and low inventory costs. * Dell bypassed distributors and retailers to sell directly to customers, enhancing customization and cost efficiency. ## Importance of Supply chain * Supply chain design, planning, and operation decisions play a significant role in the success or failure of a firm. * To stay competitive, supply chains must adapt to changing technology and customer expectations. ### Success in Supply Chain Management * **Effective Adaptation to Change** and **Superior Supply Chain Design** lead to **Successful Companies.** * **Inability to Adapt** and **Weak Supply Chain Design** lead to **Unsuccessful Companies.** * Success in supply chain management leads to business success. ## Ineffective Supply Chain Design and Management * **Poor Planning:** Leads to operational inefficiencies. * **Lack of Integration:** Causes disconnect between product and information flows. * **Weakness in Execution:** Impairs overall supply chain performance. * **Failure to Innovate:** Limits competitiveness in the market. * **Inflexibility to Change:** Hinders adaptation to market demands. * **Ignoring Customer Expectations:** Results in decreased customer satisfaction. ## Supply Chain Strategy Or Design * During this phase, a company decides how to structure the supply chain over the next several years. ### Supply Chain Strategy Design Process | Phase | Description | |-------------------------------------------|------------------------------------------------------------------------------------------------------| | **Decide Supply Chain Configuration** | Determine the overall structure of the supply chain. | | **Allocate Resources** | Distribute resources across the supply chain. | | **Determine Processes** | Define the processes for each stage. | | **Decide Outsourcing vs In-house** | Choose between outsourcing and in-house operations. | | **Select Production Locations** | Identify locations for production facilities. | | **Choose Warehousing Capacities** | Determine storage capacities at various locations. | ## Supply Chain Planning * For decisions made during this phase, the time frame considered is a quarter to a year. ### Supply Chain Planning Process | Phase | Description | |------------------------------------|--------------------------------------------------------------------------------------------------------------------| | **Establish Strategic Configuration** | The strategic phase sets the supply chain’s configuration, establishing constraints. | | **Forecast Demand and Factors** | Companies forecast demand and other market factors for the planning horizon. | | **Decide Market Supply Locations** | Decisions are made on which markets will be supplied from which locations. | | **Determine Subcontracting** | Companies decide on subcontracting manufacturing processes. | | **Set Inventory Policies** | Inventory policies are established to manage stock levels. | | **Plan Marketing and Promotions** | Timing and size of marketing and price promotions are planned. | ## Supply Chain Operation * The time horizon here is weekly or daily. * During this phase, companies make decisions regarding individual customer orders. ### Supply Chain Operational Sequence | Phase | Description | |----------------------------------|--------------------------------------------------------------------------------------------------------------------| | **Receive Customer Orders** | Orders are received from customers. | | **Allocate Inventory or Production** | Inventory or production resources are allocated to orders. | | **Set Order Fulfillment Dates** | Dates for fulfilling orders are established. | | **Generate Pick Lists** | Lists for picking items from the warehouse are created. | | **Allocate Shipping Mode** | Shipping modes are assigned to orders. | | **Set Delivery Schedules** | Schedules for delivering orders are set. | ## Process Views Of a Supply Chain * A supply chain is a sequence of processes and flows that take place within and between different stages and combine to fill a customer need for a product. ### Cycle View Divides processes into cycles at each supply chain stage interface. ### Push/Pull View Categorizes processes based on order anticipation or response. ## Process Views of a Supply Chain ### Cycle View of Supply Chain Processes * Cycle view clearly defines processes involved and the owners of each process. * Specifies the roles and responsibilities of each member and the desired outcome of each process. * The five stages of a supply chain. ### Cycle View of Supply Chain Processes | Cycle | Description | |-----------------------------------------|---------------------------------------------------------------------------------------| | **Procurement Cycle** | Sourcing raw materials at the supplier stage. | | **Replenishment Cycle** | Restocking inventory at the distributor stage. | | **Manufacturing Cycle** | Producing goods at the manufacturing stage. | | **Customer Order Cycle** | Initiating customer orders at the retail stage. | ## Process Views of a Supply Chain ### Cycle View of Supply Chain Processes * All supply chain processes can be broken down into the following four process cycles. * Dell, in contrast, bypasses the retailer and distributor when it sells servers directly to customers. ## Push/Pull View of Supply Chain Processes ### Push Processes Processes initiated based on forecasted demand, operating in uncertainty. ### Pull Processes Processes initiated in response to actual customer orders, reacting to demand. * **Pull:** execution is initiated in response to a customer order (reactive) * **Push:** execution is initiated in anticipation of customer orders (speculative) * **Push/pull boundary** separates push processes from pull processes ## Supply Chain Macro Processes in a Firm Supply chain processes can be classified into: * **Customer Relationship Management (CRM)** * **Internal Supply Chain Management (ISCM)** * **Supplier Relationship Management (SRM)** | Components | Description | |-------------------------|-----------------------------------------------------------------------------------------| | **Supplier:** | **SRM** | | **Source, Negotiate, Buy** | Source, Negotiate and Buy raw materials from suppliers. | | **Design Collaboration** | Collaborates with internal departments for design related specifications. | | **Supply Collaboration** | Collaborates with internal departments for material supply related considerations. | | **Supplier:** | **ISCM** | | **Strategic Planning** | Sets long term strategic plan related to logistics and material management. | | **Demand Planning** | Forecasts demand for product in the market. | | **Supply Planning** | Manages the material supply from suppliers according to demand. | | **Fulfillment** | Fulfill the orders raised by the customers. | | **Field Service** | Provides service to the customers. | | **Supplier:** | **CRM** | | **Market** | Analyze the market demand. | | **Price** | Defines the price of the product for the customers. | | **Sell** | Manages the sales process with the customers. | | **Call Center** | Handles customer inquiries and complaints. | | **Order Management** | Manages customer orders. | ## Examples of Supply Chains * Gateway and Apple * W.W. Grainger and McMaster-Carr * Zara * Toyota * Amazon * 7-Eleven