Transmission PDF - Aviation Australia
Document Details
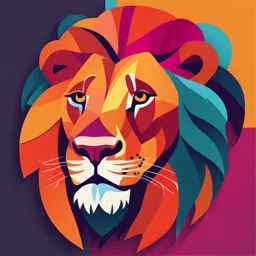
Uploaded by FaultlessMarsh8570
null
2023
CASA
Tags
Summary
This document provides information on different types of gear wear, including overload, pitting, spalling, cracking, and interference. It also discusses abrasive wear, normal wear patterns, backlash, and inspection procedures. It covers pulleys, chains, sprockets, belts, and screw jacks.
Full Transcript
Gears Gear Wear and Inspection When inspecting gears, it is important to understand the types of wear that can occur and what to look for. Aviation Australia The primary wear point of gears are the teeth 2023-11-24 B-07b Maintenance Practices CASA Part 66 - Training Materials Only Page 438 of 498 Ov...
Gears Gear Wear and Inspection When inspecting gears, it is important to understand the types of wear that can occur and what to look for. Aviation Australia The primary wear point of gears are the teeth 2023-11-24 B-07b Maintenance Practices CASA Part 66 - Training Materials Only Page 438 of 498 Overload Wear Overload wear occurs when metal has been removed from the tooth surface by the sliding action of a gear’s teeth. The heavy contact tends to squeeze out the lubricant, the metal forms micro-welds and tiny particles can be torn free. The result may leave a depression, burrs on the tooth edge, or plastic deformations resembling ripples or ridges caused by the metal being forced out of shape. Aviation Australia Gear wear failure - Overload 2023-11-24 B-07b Maintenance Practices CASA Part 66 - Training Materials Only Page 439 of 498 Pitting and Spalling Pitting and spalling are associated with thin oil films and high temperatures. Gear teeth show pitting on the teeth or spalling, which is fine cracking. Spalling is possibly due to faulty hardening, which eventually allows chunks of metal to flake away. Chips may damage other teeth. Aviation Australia Gear wear failure - Pitting and spalling 2023-11-24 B-07b Maintenance Practices CASA Part 66 - Training Materials Only Page 440 of 498 Cracking and Breakage Cracking is usually caused by faulty heat treatment or improper machining during manufacture. Cracks are often very fine and are not readily apparent until the gears have been used for some time. Breakage can be caused by one of many faults, from impact loading to manufacturing faults. Examine the other teeth for clues. Fresh metal over the break area indicates impact overloading, while darker edges indicate fatigue starting from a surface crack. Aviation Australia Gear wear failure - Cracking and breakage 2023-11-24 B-07b Maintenance Practices CASA Part 66 - Training Materials Only Page 441 of 498 Interference Wear Misalignment of gears or mating of the teeth can cause interference wear. Heavy contact is caused in small areas, often at teeth tips and roots. Aviation Australia Gear wear failure - Interference wear 2023-11-24 B-07b Maintenance Practices CASA Part 66 - Training Materials Only Page 442 of 498 Abrasive Wear Abrasive wear includes scratching and scoring and depends on the size of particles carried in the lubricant, which abrade the tooth surface. Scoring is the heavy gouging of metal from the tooth surface as the temperature rises and the lubricant thins out. The metal pieces can then damage other teeth. Note: The main causes of gear failure or premature wear are excessive backlash and poor lubrication. Proper alignment and fit are also important to ensure each tooth absorbs its share of the load. Gears corrode if exposed to corrosive conditions. Often moisture is present in the lubricant along with contaminants, which react to become acidic and corrosive. A complete breakdown or lack of lubrication causes the gear to burn. Friction causes rapid heating past the temperature limits of the metal, resulting in brittle teeth which are easily broken. Aviation Australia Gear wear failure - Abrasive wear 2023-11-24 B-07b Maintenance Practices CASA Part 66 - Training Materials Only Page 443 of 498 Normal Wear Normal wear is a polished appearance over the entire surface of the tooth. The table below is a diagnosis chart for gear tooth contact markings. It shows typical wear patterns that can be found on gear assemblies. Gear wear diagnosis chart Gear Backlash Backlash is the clearance or play between two gears in mesh. A certain amount is required to ensure lubricant penetration between the teeth of the gears and to allow for thermal expansion of the gear train. The illustration below shows exactly where backlash occurs. Backlash 2023-11-24 B-07b Maintenance Practices CASA Part 66 - Training Materials Only Page 444 of 498 Gear backlash must be established in accordance with the relevant maintenance manual. Excessive backlash can be caused by worn gear teeth or by improper meshing of teeth or bearings which do not support the gears properly. Excessive backlash can result in severe impact on the gear teeth from sudden stopping or reversal of load. The diagram below shows the gears are set too far apart, causing excessive backlash. This leads to broken gear teeth, gear bouncing and gear noise. Teeth too high Too little backlash will cause excessive loading on the gear teeth, lubricant will be forced from the gear surface and premature failure will result. Teeth too low A measurable amount of backlash can be detected by hand if one gear is held and the other rocked. Usually this is minimal and a Dial Test Indicator (DTI) is set up to measure it. A typical gear may have.003- to.004-in. backlash. The correct backlash is given in the maintenance publications which must be followed. 2023-11-24 B-07b Maintenance Practices CASA Part 66 - Training Materials Only Page 445 of 498 Gear Wear Patterns The meshing pattern of two gears is important and closely related to backlash. Backlash and pattern checks are done in conjunction and are generally most critical where directional changes are made through the gears (for instance, right angle changes with bevel gears). These gears are adjustable, and shimming or adjusting them inwards and outwards sets their correct relationship. The wear pattern is simply the prints (marks or impressions) that one set of gear teeth leaves on another set when they mate. Wear patterns may be examined: Prior to final assembly During service During overhaul After a failure. Prior to assembly, the pattern of tooth contact may be established by using Prussian blue, a blue-dyed soft paste smeared lightly on the leading side of the driving gear teeth. Other coloured dyes mixed with oil are also sometimes used. The gears are temporarily assembled and turned, and a pattern of contact is left on the teeth. Studying this pattern enables the engineer to set up the correct shimming or assembly relationship. At service intervals, the normal wear on the teeth mating surfaces may be examined for an indication of condition or to see if further maintenance is required. Early correction of abnormal patterns can prevent further deterioration or failure. Normal wear leaves a polished surface on the tooth face. During overhaul, the wear pattern is examined to determine acceptability for further service, and for any indication of problems in the remainder of the assembly. After failure of the gear or assembly, examination of the wear pattern could give clues to the cause of the failure and help determine servicing procedures to prevent future failures. Each tooth of a helical bevel gear has a heel and toe, a coasting side and drive side. The heel is the larger-width outer end of the bevel gear, and the toe the smaller inner end. The coasting side of the tooth is concave and is not under pressure during normal drive; the drive side is convex and under pressure during normal operation. Helical bevel gear 2023-11-24 B-07b Maintenance Practices CASA Part 66 - Training Materials Only Page 446 of 498 Ideal tooth contact – evenly spread over profile nearer to toe than heel Toe contact – Move the drive pinion out of mesh 2023-11-24 B-07b Maintenance Practices CASA Part 66 - Training Materials Only Page 447 of 498 Heel contact – move the drive gear into mesh 2023-11-24 B-07b Maintenance Practices CASA Part 66 - Training Materials Only Page 448 of 498 Pulleys Introduction to Pulleys Pulleys are used in aircraft control systems to change the direction of a cable. They are designated by numbers AN210, AN219, AN229 and AN221. Aircraft pulleys are made of metal and compressed phenolic sheet, Teflon fluorocarbon resins, and other plastic materials. The pulley bearings are usually of the sealed type and require no lubrication. The pulley is bonded to the bearing so that the bearing cannot be removed. When replacing a pulley, the technician must make sure to install the correct type. This can be determined from the manufacturer’s instructions or by the number on the pulley. Pulley 2023-11-24 B-07b Maintenance Practices CASA Part 66 - Training Materials Only Page 449 of 498 Pulley Inspection Pulleys should be inspected in accordance with the manufacturer’s instructions. Conditions to be checked are shown in the following diagram: © Jeppesen Pulley wear patterns If a pulley is worn to an appreciable extent or cracked, it should be replaced. Pulleys should turn freely when the control cables are moved. If a pulley is out of line, it causes wear to both the pulley and the cable. The mountings for such pulleys should be corrected and the cable carefully examined for wear. Wear of pulley bearings, bearing bolts and bushings should be checked for serviceability on a regular basis. All pulleys must be equipped with guards to prevent the cable jumping out of the groove when the cable is slack. 2023-11-24 B-07b Maintenance Practices CASA Part 66 - Training Materials Only Page 450 of 498 © Aviation Australia Belt and pulley inspection 2023-11-24 B-07b Maintenance Practices CASA Part 66 - Training Materials Only Page 451 of 498 Chains Introduction to Chains Control chains are found in a number of applications in aircraft control systems. Usually they are found where there is a short distance between two hardware items (two torque tubes, for example) or the system requires a relatively large amount of force to operate and it is not practical for a small cable run to be installed. The cockpit pedestal area is a common place to find short chain assemblies. Trim wheels driving chains Like bicycle chains, aircraft control chains are made up of multiple links and can be joined together to make an endless loop. They can also be of a terminating type – a single length with a start and finish. Aircraft chains, however, tend to be manufactured to closer tolerance and have more rigorous inspection criteria. They also have components such as chain keepers, similar to cable guards, to stop the chain from coming off the sprockets. They have drive and idler sprockets and a method of maintaining the tension of the assembly. 2023-11-24 B-07b Maintenance Practices CASA Part 66 - Training Materials Only Page 452 of 498 Chains and sprockets Aircraft control chains are usually of the roller type. Rollers are free to rotate around bushes which hold the inner link plates together. Pins are mounted in the outer plates, which are clamped together to join the whole assembly. Chain link assembly 2023-11-24 B-07b Maintenance Practices CASA Part 66 - Training Materials Only Page 453 of 498 Chain sizing parameters Chains are sized according to pitch, width and roller diameter. Non-reversible chains (i.e. not a continuous loop) are joined or connected using end fittings similar to cable terminals, and can only be fitted in one direction. Chains with fixed ends Like cables, chain guards can be fitted to sprockets to prevent the chain from coming adrift when tension is reduced. Stop pieces on the chain guard and non-interchangeable end connectors can prevent incorrect installation of non-reversible chains. 2023-11-24 B-07b Maintenance Practices CASA Part 66 - Training Materials Only Page 454 of 498 Chain Inspection Chains need to be assessed regularly for wear, corrosion and distortion, including elongation. It is always best to clean the chain before checking for wear or damage. Then place the chain on a flat surface to examine its condition. To check for elongation: Apply a specified load to the chain Measure the length of the chain section using the following formula: M − (X × P ) × 100 Extension (%) = X × P Where: M = measured length P = pitch X = number of links Replace the whole chain if elongation is greater than 2%, as elongation can compromise its strength. Chain tension is checked by measuring chain deflection under a given load. Chain tensioning 2023-11-24 B-07b Maintenance Practices CASA Part 66 - Training Materials Only Page 455 of 498 Chain tensioning is adjusted using turnbuckles or with adjustable sprockets such as the one shown above. The chain should be tightened enough to remove any backlash. Too much tension causes the chain rollers to bind on the sprocket teeth. A spring balance or similar is attached to the chain at a specified point. A given value of ‘pull’ is applied to the chain and the deflection from the normal chain run profile is measured. If the deflection is too great, the tension in the cable must be increased. Criteria for rejection of a chain include: The chain section is elongated by more than 2% Any links are stiff or jammed Any part of the chain is kinked or twisted Any plates are cracked, worn or corroded Any rollers are cracked, worn, corroded or jammed. Correct storage of chains is important to minimise the possibility of corrosion or kinking of the links. For storage, chains should be: Cleaned in solvent Dried Soaked in light lubricating oil Coiled without twisting. Check for kinks or twists by freely suspending the chain and sighting along its length. No twist is allowed. 2023-11-24 B-07b Maintenance Practices CASA Part 66 - Training Materials Only Page 456 of 498 Sprockets Introduction to Sprockets Sprockets are used in many aircraft systems and in a variety of different applications. Sprockets Sprockets (depending on their application) are usually made from: Steel Alloy Hard fibre material Plastic. Their primary role is to convert rotary motion into linear motion and/or linear motion into rotary motion. Also, where long chain systems are used, they act as support for the chain in the form of an idler sprocket. 2023-11-24 B-07b Maintenance Practices CASA Part 66 - Training Materials Only Page 457 of 498 Idler Sprocket An idler sprocket is a non-driving sprocket used to support the chain run.IDLER SPROCKET Idler sprocket Sprocket teeth are spaced to align with the chain pitch. The number of teeth on the drive sprocket compared to the number of teeth on the sprocket being driven determines the gearing ratio of the chain system. For example, suppose a drive sprocket has 36 teeth and the driven sprocket has 12 teeth. The driven sprocket rotates three times for every drive sprocket rotation. 2023-11-24 B-07b Maintenance Practices CASA Part 66 - Training Materials Only Page 458 of 498 Sprocket Inspection Chain tension and load have a direct impact on chain and sprocket service life as does dirt and debris. A worn sprocket will produce tight and loose spots as the chain rolls over it. Sprocket wear is usually not uniform. Once wear starts in one place on the chain or sprocket, the rate of wear will accelerate in that area. Aviation Australia Sprocket inspection 2023-11-24 B-07b Maintenance Practices CASA Part 66 - Training Materials Only Page 459 of 498 Belts Introduction to Belts Drive belts are used in a number of applications (for example, in helicopter drive systems). They come in many different shapes and designs. Different belt configurations Belt drives carry a lesser load than chain drives. However, they do not require lubrication, are more shock resistant, and are quieter and smoother during operation. All belts are a variation of two types: Vee belt Non-slip toothed belt. 2023-11-24 B-07b Maintenance Practices CASA Part 66 - Training Materials Only Page 460 of 498 “Vee” and toothed belts Belt drives can come in single or multiple belt and pulley systems. Single and multiple drive belt systems 2023-11-24 B-07b Maintenance Practices CASA Part 66 - Training Materials Only Page 461 of 498 Belt Drive Inspection The following are belt defects that may be encountered during inspection. © Aviation Australia Drive belt inspection conditions (1) Bottom of Belts Cracking - Caused by belt slipping causes heat build-up (friction) and gradual hardening of the under-cord reinforcing fibres. Top of Tie Band Frayed or Damaged - Caused by obstruction on the sheave interfering with normal belt operation. Top of Tie Band Blistered or Perforated - Caused by foreign material accumulating between the belts of the tie band. 2023-11-24 B-07b Maintenance Practices CASA Part 66 - Training Materials Only Page 462 of 498 © Aviation Australia Drive belt inspection conditions (2) Belt Cut on Bottom - Caused by belt that has run over sheave and come off, or belt was forced over sheave flange during installation without proper slack. Belt Riding Outside Sheave Groove - Caution: if belt is allowed to run in this condition, progressive failure results as shown in the diagram above (e.g. separation). Separation - Caused by improper belt tension, misalignment of sheaves and/or foreign object struck belt forcing it from its normal path. 2023-11-24 B-07b Maintenance Practices CASA Part 66 - Training Materials Only Page 463 of 498 Screw Jacks Introduction to Screw Jacks A screw thread that can be used to give high mechanical advantage is known as a screw jack. Screw jacks convert rotational movement into linear movement. In some applications, they are called screw jack actuators or linear actuators. There are three basic types: The worm-and-peg mechanism The worm-and-nut mechanism The recirculating ball mechanism. Aviation Australia Screw jack - Worm and nut mechanism 2023-11-24 B-07b Maintenance Practices CASA Part 66 - Training Materials Only Page 464 of 498 The Worm and Peg Mechanism The worm and peg mechanism is not used much because excessive backlash often results from localised wear on the peg and worm screw. Worm and peg mechanism The Worm and Nut Mechanism The worm and nut mechanism type is often used on aircraft. It usually has an Acme or square thread. Actuation is by turning the shaft to drive the nut, or by turning the nut to drive the shaft. Worm and nut mechanism 2023-11-24 B-07b Maintenance Practices CASA Part 66 - Training Materials Only Page 465 of 498 The Recirculating Ball Mechanism The recirculating ball type is a low-friction variation of the worm-and-nut mechanism. It is sometimes known as a ball screw actuator. The closed pathway for the ball bearings allows them to continually circulate along the mating grooves of the shaft and nut, reducing friction when the mechanism is actuated. This form of screw jack is used in aircraft for many applications, in particular the flap drive system. Recirculating ball mechanism Recirculating ball mechanism - sectional diagram 2023-11-24 B-07b Maintenance Practices CASA Part 66 - Training Materials Only Page 466 of 498 Screw Jack Inspection Always refer to the relevant manufacturer’s maintenance manual for the correct inspection procedures. Inspection normally involves the following: Checking screw shaft for wear Checking ball nut for end float Checking ball nut lubrication level Checking screw jack full travel and stop limits. Ball screw inspection 2023-11-24 B-07b Maintenance Practices CASA Part 66 - Training Materials Only Page 467 of 498 Control Rods Introduction to Control Rods Push-pull rods have many system applications. For example, an aileron and trim tab mechanism has at least three adjustable push-pull rods. Control rods - Aileron and trim tab mechanism installation diagram Push-pull rods and their adjustable end-fittings create a type of rigid linkage that eliminates the problem of varying tension in a control system. They permit the transfer of compression (push) or tension (pull) forces. Push-pull rods are usually made of seamless aluminium alloy tubing. Some are of a fixed length, but most have at least one adjustable end. The type of rod shown below has threaded rod ends riveted to the tube. Adjustable rod ends are screwed onto the threaded ends and locked with a check nut. 2023-11-24 B-07b Maintenance Practices CASA Part 66 - Training Materials Only Page 468 of 498 © Jeppesen Control rod An adjustable push-pull rod may have a left-hand threaded end and a right-hand threaded end. This allows shortening or lengthening the rod when altering system rigging. The check nuts are loosened, enabling the rod to be turned without disturbing the rod eye ends. Adjustable push rods 2023-11-24 B-07b Maintenance Practices CASA Part 66 - Training Materials Only Page 469 of 498 Push-Pull Rod Inspection Push-pull rod inspections include checking for rod straightness, wear in the eye ends, and security of the check nuts and end fittings. Inspect the rod for: Corrosion Scratches Dents Chafing Buckling. A check or witness hole allows the installer to determine whether the adjustable end is screwed onto the threaded portion sufficiently. Witness hole location A piece of lockwire or a thin split-pin can be used. If the wire cannot be inserted into the witness hole, then the adjustable eye end is said to be ‘in safety’, that is, it is screwed onto the threaded portion sufficiently. Another check is to ensure that no more than three threads are exposed after the eye end is tightly screwed onto the threaded portion. As control rod bearings are self-aligning, they are subject to both radial and axial loads and should be inspected for play in both these planes. 2023-11-24 B-07b Maintenance Practices CASA Part 66 - Training Materials Only Page 470 of 498 Subject to radial and axial loads - inspect for play Acceptable wear limits are established in the maintenance manual for a particular aircraft. Control rod bearings require movement in two planes, so a bearing which can align itself to a changing axis is required. Axial and radial play check This rotational movement in two planes must not be mistaken for axial and radial wear. 2023-11-24 B-07b Maintenance Practices CASA Part 66 - Training Materials Only Page 471 of 498 Bell Cranks Introduction to Bell Cranks Bell cranks are used to: Transmit force or motion Permit a change in direction of that force or motion. © Jeppesen Bell crank The bell crank pivots on bearings mounted on a shaft. There is usually no adjustment possible to the bell crank, although the push-pull rods can be adjustable to enable correct system rigging. The torque arm receives the linear motion input from the control system and causes the torque tube to rotate. Thus the torque arm and torque tube can be said to have converted linear motion to rotary motion. The torque tube is directly connected to the control surface and causes it to move. Torque tubes and torque arms are usually of fixed length, diameter and angle. They are usually not adjustable. 2023-11-24 B-07b Maintenance Practices CASA Part 66 - Training Materials Only Page 472 of 498 Elevator control system torque tubes Note: The adjustable push-pull rods connect the rudder balance lever to the rudder balance tab. 2023-11-24 B-07b Maintenance Practices CASA Part 66 - Training Materials Only Page 473 of 498