Control Electronics & Vehicle Diagnostic System PDF
Document Details
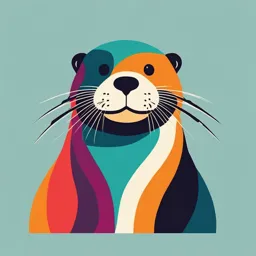
Uploaded by ScenicHummingbird6529
Null
Tags
Summary
This document details the control electronics used in WAP5 and WAG9 locomotives, known as MICAS-S2. It is a distributed control system optimized for electric traction vehicles. The system includes features like signal input/output, signal processing, communication, and a man-machine interface. The document also discusses the system's field of application, hierarchical levels, and characteristics.
Full Transcript
7. CONTROL ELECTRONICS & VEHICLE DIAGNOSTIC SYSTEM The Control electronics used in WAP5 and WAG9 locomotives is known as MICAS–S2 (Micro Computer Automation System Series 2). MICAS–S2 is a process oriented, distributed control system optimized for the application on electric tracti...
7. CONTROL ELECTRONICS & VEHICLE DIAGNOSTIC SYSTEM The Control electronics used in WAP5 and WAG9 locomotives is known as MICAS–S2 (Micro Computer Automation System Series 2). MICAS–S2 is a process oriented, distributed control system optimized for the application on electric traction vehicles. It consists of a number of devices for signal input / output, signal processing and communication systems to exchange data between bus stations (control units). A man- machine interface for the operating system as well as aids for planning, commissioning and maintenance of an installation is also provided. FIELD OF APPLICATION The MICAS-S2 control system is mainly used in electric traction vehicles, such as locomotives, multiple unit trains, tramways and trolley buses. A modern transportation system has high demands on the vehicles. Thanks to its modularity, MICAS-S2 can be adapted to the various requirements. There are three hierarchical levels in the MICAS traction control system (Fig.7.1) train control, vehicle control and drive control level. The train control level coordinates and controls coordination of several similar traction vehicles (multiple traction), interfacing to brake systems and much more. It is the train control level that converts the driver‟s commands (e.g. set speed) into commands for the individual vehicles. These commands are passed on to the vehicle control level for execution. The vehicle control level is responsible for all the vehicle functions. It converts the commands of both the train control level and the driver into actions (contactor control, EP- valves etc) and gives feedback about important events or operating states. To allow the driver to concentrate on his most important task, i.e. observing the track and signals, the vehicle control level automatically reacts as far possible on all events occurring during operation. The third hierarchical level is the drive control level. It receives the set value of the tractive effort required from the vehicle control level and controls the power converters in such a way that the motors will deliver the required torque. MICAS-S2 comprises components for all the three hierarchical levels. Thus all requirements demanded for modern vehicle can be met such as: * Full integration of all control system tasks for a train. - Measuring and conditioning of process values. - Control of all functions. - Drive control. - Power supply. - Data exchange between sub-systems of a vehicle and between several vehicles. TRACTION ROLLING STOCK : THREE PHASE TECHNOLOGY Page 77 - Supervision on inadmissible operating condition. - Protection of components and vehicles. * Integrated diagnosis to support both operation and maintenance. * Safe operation (inherent or user configurable redundancy of the control system) * Easy vehicle maintenance due to high modularity and availability of components. * Efficient vehicle production with extensive test of preassembled modules before integration in the vehicles. *Possibility to adapt to changing needs during the whole life time. CHARACTERISTICS The MICAS–S2 control system takes charge of all tasks necessary for operating,, monitoring and maintaining vehicles. Furthermore, because of it structure and modes of operation it offers exceptional advantages for both the vehicle manufacturer and the customer. Internationally standardized data transfer according to IEC TC9 WG22 (Train Communication Network, MICAS Vehicle Bus and Train Bus). Self-diagnosis of all the devices with centralized processing and the degree of fault tolerance can be widely adapted to requirements regarding availability and safety. Simple configuring and programming of an installation thanks to powerful and user-friendly software tools (Mic Tools). Uniform interface between software and data transfer systems. Access to all devices via MICAS vehicle Bus for commissioning and maintenance. Integration of third-party systems (electronic modules of other manufacturers) into a MICAS-S2 installation. Extensive protection against electromagnetic interferences. Communication is one of the most important functions of a distributed control system Requirements for data transfer between the control electronics component of a vehicle are quite different from the data exchange between different vehicles. Therefore MICAS-S2 includes various data transfer systems that offer optimum adaptations such as the Train Bus, the MICAS Vehicle Bus and the Parallel buses. Data between up to 62 vehicles can be exchanged by the Train Bus. It is possible to control one or several traction vehicles (multiple traction commuter train). The Train Bus flexibly adapts to any configuration alteration of a train. Mixed trains with vehicles having no interface to the Train control bus are possible. The MICAS Vehicle Bus is optimized for the transfer of real-time process values. The cyclic data transfer according to the broadcast principle allows a very efficient utilization of the transmission capacity available. Cycle times between 1 ms and 1024 ms are possible. Upto 127 devices can be connected TRACTION ROLLING STOCK : THREE PHASE TECHNOLOGY Page 78 to a bus. Considerable noise immunity is obtained by linking the modules with fibre optic cables. The Parallel bus (AMS-Bus) is used to control input/output devices in subracks. Another very important function of MICAS-S2 is the drive control electronics. Asynchronous motors mainly used in modern traction vehicles are very dynamically controlled due to the stator-flow-oriented torque control process (direct and indirect self control). This results in maximum adhesion utilization, optimum comfort and minimum wear. Traction vehicles equipped with MICAS-S2 drive control offer universal application both in pulling heavy goods trains or in front of fast passenger trains. HANDLING MICAS-S2 offers uniform user-friendly tools for the design, commissioning and maintenance staff. The Mic Tools package presents a wide variety of programs to fulfill most of their tasks. User programs for general control tasks are programmed in the process oriented Function Block Language (FUPLA). FUPLA is a programming tool using graphic symbols called function blocks. This makes it very simple to write, test and document programs for the automation of process. The shielded subracks, the protective circuits in the electronic modules as well as the shielded cables for analog process signals guarantee and optimum safety of operation even in very harsh environments close to strong sources of electromagnetic radiation. Internal signals and the supply voltages are wired via the rear rack connectors in wire wrapping technique and with back planes. For the remote bus of the MICAS Vehicle Bus and the signals to the power converters fibre cables with ST bayonet connectors are used. PROGRAMMING The Software required to use the MICAS-S2 control system can be divided into three groups. Programs in the control system processors that are independent of the application (operating system firmware). Programs for the project specific task of the control system (user programs for control tasks, diagnosis, visualization). Programs for the planning of installations, i.e., to write the project specific software as well as for testing, commissioning and maintenance purposes (Mic Tools). TRACTION ROLLING STOCK : THREE PHASE TECHNOLOGY Page 79 DIAGNOSIS CONCEPT As part of the distributed control system the MICAS-S2 diagnosis has a decentralized structure. The diagnostic messages are produced by the computers involved in the process and transmitted to the diagnostic computer. The later is equipped with an expert system which evaluates and stores the incoming messages. Special functional blocks in the Function Block Language (FUPLA) are intended to produce the diagnostic messages in the computers. Therefore the programmer can define which disturbances will cause a diagnostic message to be sent. The diagnostic messages of the different devices are evaluated by an expert system. The system processes the incoming messages by means of pre- defined rules considering the present operating state of the system. If a failure occurs the driver is given hints on a driver‟s cab display whether to maintain or to re-start operation. The maintenance staff can be provided with additional information in order to accelerate trouble shooting. MICAS-S2 also comprises programs to test modules and for the commissioning of vehicles. Automatic testing of single racks as well as of complete pre-produced modules is possible. The temporal behaviour of process variables can be registered if necessary for a longer period time. With a workstation (a Personal Computer with an additional equipment) users have access to any device connected to the MICAS Vehicle Bus. Check of correct function, trouble shooting, installation of new program versions and so on are possible without interfering with the hardware. MECHANICAL DESIGN For the modules in 6U double-height Eurocard format (6U=233.35*220mm) the subracks are configured, manufactured and wired in different widths according to the project need. They include one or several processors, input/output boards, bus couplers and one or more power supplies (Fig.7.2). For protection against electromagnetic interferences the subracks are usually integrated into shielded cases. Devices with a special format (e.g. Compact Unit alphanumeric display) are not designed for mounting into subracks. The process signals are connected to the modules by means of front connectors. Common DB9, DB15 and DB25 type connectors according to DIN 41652 are almost exclusively used for process signals. The incoming messages are processed by the expert system on the diagnostic computer. The expert system reaction on message is programmed by means of the Action Diagnostic Language (ADL). Earlier messages or current operating states can be considered as well to take the appropriate conclusion from a certain diagnostic message. One of the possible conclusions of the TRACTION ROLLING STOCK : THREE PHASE TECHNOLOGY Page 80 expert system may results in a message output to the vehicle driver. The diagnostic computer passes the message on the visualization controller (Vico). The latter transmits the message to the alphanumeric display in the driver‟s cab. The diagnostic computer is nor involved in the process control. This allows the system to be operated without diagnostic computer. Furthermore the diagnostic computer has no influence on functions important for the vehicles safety and therefore, redundancy is not required. IMPLEMENTATION ON WAP5/WAG9 LOCOMOTIVE The vehicle control scheme in WAP5/WAG9 loco integrates MICAS-S2 based software and conventional hardware (such as relays, auxiliary contactors etc) for obtaining the desired control functions. It is not proposed to describe the complete control schematic of these locos in this document. The detailed schematics are given in ABB‟s drawing No. 3EHP 281105 and the software specification is given in ABB document No. 3EHP 541681. After software specification is finalized the logical functions to be performed by software are written as “function groups”. Each function group comprises of functional segments written in a graphical language (FUPLA). When all the FUPLA segments are written down, the MICAS-S2 system compiles the program to generate the final vehicle control software. During the design of function groups signal names (variables) are allocated including inputs from the control circuit hardware and these signals are approximately indicated in the control circuit schematics. The control software for converter control are written using FUPLA, „C‟ and assembly language programming, but these are covered in Drive Control Software. For the appreciation of how the software and hardware are integrated in the vehicle control scheme, the pantograph control circuit the schematic of which is shown in Fig.7.3 is explained here as an example. The corresponding software specification is given in Annexure 7.1Wire Nos. 2111A and 2111B are at potential of 110V which get supply from the battery circuit and are connected to the spring loaded pantograph switches (129/1&2) of Cab1 and Cab2 respectively. If the driver drives from Cab 1 and pushes the switch „UP‟ of 129/1, then battery feed takes the path through 2333A, 123/3 (blocking diode which is provided to block the reverse flow), 2319,2309A, 2300 to 412.QJ. The dotted box 412.QJ, which is an auxiliary control processor board and a part of the Central Electronics – 2 represents that it receives a digital input (#) and actives a PCB-mounted relay. The output is in the form of a normally closed contact. The opening of this contact is done through the software by processing the pantograph disable digital signal in the HBB2(Aux. Cubicle Control) processor. Normally closed contact of 412.QJ and 412.JJ can be forced open in certain conditions like software mismatch, MCE fatal, VCB stuck in „ON‟ position etc. thereby disconnecting the feed to the coil of 130.1. So in normal pantograph „UP‟ operation of 129/1 switches, the 110V control signal passes through 412.QJ (explained earlier) and 412.JJ (a software function of STB2 low voltage cubicle processor) to energise the auxiliary contactor coil (130.1) of pantograph and its N/O contact (130.1) connected between wire Nos. 2064 & 2302 closes. Once this contact is made, feed is maintained through wire No. TRACTION ROLLING STOCK : THREE PHASE TECHNOLOGY Page 81 2062, 2061A, 2063, 2061A to energize EP valve (130/2) of pantograph Cab2 side. Thus, pantograph Cab2 side is raised. In case the driver drives from Cab2 then 110V control feed takes the path through electronics 412.QG and EP valve (130/1) is energized and pantograph Cab1 side is raised. Closing of contactor 130.1 is maintained by continuing the feed for energisation of auxiliary contactor coil (130.1) through the path 2064, 2319, 2309, 2300, 2315 and 2301. Status of the pantograph is monitored by the electronics 412.LD and 412.QD. There are two pressure switches of pantographs 130.4/1 is for monitoring the air pressure for pantograph 1. Similarly 130.4/2 is for pantograph 2. If the air pressure falls below 2.5 kg/cm2, 130.4 opens out and corresponding signal is processed by the control electronic 412.QA. The pressure switches (130.4/1 and 130.4/2) are monitored by the Central Electronics-2 (412) through the auxiliary cubicle processor (HBB2) boards 412.QA connected to wire No. 2307 and 412.QA connected to wire No. 2308 which gives the message to the drivers display unit (DDU). Similarly the status of the auxiliary contact pantograph (130.1) is monitored by 412.LD and 412.QD. To energise the EP valve 130/2 and 130/1 for raising the pantograph, it is required to close the contact of 412.LJ or 412.QG. These processors 412.LJ and 412.QG take a digital signal by logical “AND”ing the signals of 412.QA & 412.LJ for pantograph 2 and 412.QA & 412.QD for pantograph 1 respectively. During „Cooling Mode‟ the electronics is in the off state. So raising the pantograph in cooling mode through electronics 412.LJ and 412.QG is not possible because output of 412.LJ and 412.QG are normally open contacts. If driver raises the pantograph from Cab 1 then the feed to the EP valve 130/2 is made through 2111A, contact 130.1, 2103A, 126.6 (safety relay control electronics „ON‟ which is open in driving mode and closed in cooling mode), 2104A, blocking diode 123/2,2105A, 2107A and 2106A. Similarly if the driver raises the pantograph from Cab 2 the feed to the EP valve 130/1 is made through 2111B, 130.1, 2103B, 126.6, 2104B, 123/2, 2105B, 2107B & 2106B. The rotary pantograph selection switch (129.1) has got 3 positions (I, AUTO, II ). I represents pantograph Cab1 side, II represents pantograph Cab2 side and AUTO represents automatic selection, i.e., if Cab1 is activated pantograph Cab2 side will be raised and if Cab2 is activated pantograph Cab1 side will be raised on pushing ZPT switch (129/*) to „UP‟ position. TRACTION ROLLING STOCK : THREE PHASE TECHNOLOGY Page 82 TRACTION ROLLING STOCK : THREE PHASE TECHNOLOGY Page 83 Fig. 7.3 Schematic of Pantograph control Circuit TRACTION ROLLING STOCK : THREE PHASE TECHNOLOGY Page 84 Annexure 7.1/1 SOFTWARE SPECIFICATION OF PANTOGRAPH CONTROL CIRCUIT 2.2.4 Pantograph 2.2.4.1 Pantograph section n2241.01f The rotary switch for pantograph {05A, 129.1) has the following 3 positions: Pos. “I” Pan above cab1 is selected Pos. “AUTO” Pan above the inactive cab will be selected automatically. Pos. “II” Pan above cab2 is selected. n2241.02i The rotary switch is located in the machine room. The selection is hardwired and without MCE control. Only if the pantograph selector is in Pos. “AUTO” then the MCE selects the pantograph, otherwise the selected pan (rotary switch Pos. “I” or Pos. “II”) will raise independently of the selection by the MCE. Multiple unit 284.01f 2.2.4.2. Raise and lower pantograph n2242.01f To handle the pan there is a spring loaded switch (129) with 3 positions Pos. “UP” Raise Pan (spring loaded) Pos. “O” Neutral Pos. “DN” Lower Pan (spring loaded) n2242.02i Both EP valves {05A, 130} to raise the pan are controlled either by the MCE (key switch in Pos. “D”) or by hardware (cooling mode) n2242.03f The driver gives the command to raise the pan with a short push to Pos “UP” of the spring loaded switch (129) He gives the command to lower the pan with a short push to Pos “DN” of the switch. n2242.04f The pulse generated in the “UP” position energises the auxiliary contactor pantograph {05A, 130.1}. The contractor has different effects depending on mode of the locomotive. Cooling mode Contactor {130.1} raise the pantograph above the unoccupied cab Driving mode: Contactor {130.1} transmit the command of the driver to the CEL n2242.05i The auxiliary compressor secures enough air pressure to raise the pantograph 2.5.4 Auxiliary compressor. n2242.06f The pan should be able to be lowered by the driver in each situation without any risk of damages to the loco. n2242.07f It shall be possible to raise the pan at any speed 277.02 Neutral section n2242.08f The MCE shall lower the pan and over write the driver‟s command “pan up” with “pan down” by de-energising the auxiliary contactor pantograph {05A, 130.1} in the following way: - Key switch in Pos. “O” - Emergency stop push button (06B, 244) - Fatal mode of MCE (loco dead) n2242.09f The pan is not lowered automatically in case of the catenary voltage exceeding the upper line voltage. n2242.10f Each pan is monitored by a pressure switch {05A, 130.4} VCB open : After the driver‟s wish to raise the pan, the driver will be informed by a message on the diagnosis display, that the pan is raising. As long as the air pressure of the pan is not ok, the VCB will be disabled. If the pantograph air pressure will not be ok after 20sec, a fault message will be displayed. VCB closed: In case of low pressure with 2 sec delay at raised pan, VCB will be opened and a priority 1 fault message is displayed. The time delay shall be settable during commissioning. n2242.11f If HBB2 isolated, the pan 1 is not available and the pressure switch of pan 2 is not monitored. TRACTION ROLLING STOCK : THREE PHASE TECHNOLOGY Page 85 ABB Transportation System Ltd 3 EHP 541 891 Responsible department Take over department Revision Doc-type File No. BEF3 A * SOS Proposed Checked Approved Language Page 95-04-20 W. Hemmann 95-04-21 Ph. Weber 95-04-21 W. Jaun en 1/9 Vaid tor. Derived From Replaces Classify no. File IR WAP 5/WAG9 P541891.DOC Vehicle Control Software IR WAP5/WAG9 Design FG 31 – Pantograph Control Table of Contents 31.1 Purpose 2 31.2 Reference Documents 2 31.3 Processors and clusters 2 31.4 Normal Functionality 2 31.4.1 General Information 2 31.4.2 Redundancy 2 31.4.3 Pantograph selection 2 31.4.4 Pan up/down wish generation 3 31.4.5 Collection of pan up conditions 3 31.4.6 Collection of pan down conditions 3 31.4.7 Pan control and supervision 4 31.4.8 Simulation mode 4 31.5 Multiple control 4 31.5.1 Normal operation 4 31.5.2 The master loco is in trailing mode 5 31.6 Disturbances 5 31.6.1 HBB2 fails 5 31.6.2 STB 2 fails 5 31.6.3 Disturbance handling in multiple operation 5 31.6.4 Disturbance handling in trailing mode 5 31.7 Interface 5 31.7.1 FG 31 implemented in HBB2 6 31.7.2 FG 31 implemented in STB2 6 32.8 Appendix Principle - Schemes 7 We reserve all right in this document and in the information contained therin. Reproduction, use or disclosure to third parties without express authority is strictly forbidden. (C) 1995 ABB Transportation System Ltd. TRACTION ROLLING STOCK : THREE PHASE TECHNOLOGY Page 86 Revision Language Page A* en 2 3 EHP 541 891 31.1 Purpose This FG controls and monitors the pantograph \(pans) in the driving mode. In the cooling mode all pan functions are hardwired. 31.2 Reference Documents 3EHP 541 681 Vehicle Control Software – Specification 2.2.4 Pantograph selection 2.8.4 Pantograph (Multiple operation) 2.8.13 Trailing mode 3EHP 541 681 Control main apparatus 05A Control circuit pantograph 31.3 Processor and Clusters All processors containing this function group are listed below: Processor Description HBB2 Pan 1 control STB2 Pan 2 control 31.4 Normal Functionality 31.4.1 General Information FG31 is divided in four parts : Pan up/down wish generation Collection of pan up conditions Collection of pan down conditions Pan control and supervision 31.4.2 Redundancy Pan 1 is controlled and monitored by HBB2 and pan 2 by STB2. The pan selection logic, which runs simultaneously in FG31 of HBB2 and STB2, selects the pan to be raised. If one processor fails, the other one will raise the connected pan independently of the pan selection logic. 31.4.3 Pantograph selection With the „Pan Selection‟ switch (, {5A, 129.1}) it is possible to force a pan selection (, 2.2.4.1) - Position “I” The pan above cab 1 will be raised (hardwired) - Position “II” The pan above cab 2 will be raised (hardwired) - Position “AUTO” Depending on the parameter (PA 31_P3102 – PanselecSM) in the pan selection logic of FG31 TRACTION ROLLING STOCK : THREE PHASE TECHNOLOGY Page 87 Revision Language Page A* en 3 3 EHP 541 891 The following table is valid if the „Pan selection‟ switch is in the “AUTO” position and the loco in the single operation mode: Parameter name Value Description PA31 – P3102 - PanSelecSM 1(default) The pan above the unoccupied cab will be raised PA31 – P3102 -PanSelecSM 2 The pan above the occupied cab will be raised 31.4.4 Pan up/down wish generation The pan up/down logic in the driving mode is partly hardwired (, 05A) To generate a pan up wish (LpanUp = 1) following conditions must be fulfilled: - The „Pan disable‟ contactor must be deenergised (BpanDisable = 0) - The „Emergency stop‟ push button (, 05A, 244/1 or 244/2}) is released in the activated cab (hardwired : , {05A, 125/1 or 125/2}) - The driver pushes the „Pan up‟ push button in the activated cab (hardwired: , {05A, 129/1 or 129/2}) If all these conditions are true, the pan wish logic is in the self hold mode. The self hold logic can be manually released (Lpanup = 0) by one of the following actions: - The driver pushes the „Pan down‟ push button in the activated cab (hardwired: {05A, 129/1 or 129/2}) - The driver pushes the „Emergency Stop‟ push button in the activated cab (hardwired: , 05A, 244/1 or 244/2}) The self hold logic can be released by the software if the „Pan disable‟ contactor is energised (BpanDisable = 1) 31.4.5 Collection of pan up conditions In order to raise a pan following requirements must be fulfilled: - The driver generates a Pan up wish (LpanUp = 1) - The MSC (master state chart) node has to be 550: „Pan enable‟ (BPanUpMSC = 1) - The pan selection logic selects the connected pan (the pan above the unoccupied cab is raised) or the other processor which should raise the pan is isolated 31.4.6 Collection of pan down conditions There are three groups of pan down conditions: - Pan down without disturbance - Protective pan down - Pan disable Pan down without disterbance: - The driver generates a pan down wish (LpanUp = 0) - The driver switches the „Cab activation‟ key switch to “0” (Mtrain Occup = 0) In these cases of controlled Pan down commands, the VCB will be opened first (BVCBOffDem = 1) Protective pan down: - The driver pushes the „Emergency stop‟ push button (hardwired : , {05B, 130.1}) - The VCB is stuck on (MVCBStuckOn = 1) TRACTION ROLLING STOCK : THREE PHASE TECHNOLOGY Page 88 Revision Language Page A * en 4 3 EHP 541 891 Pan disable (These signals prevent from raising the pan) - The MSC node is lower than 504 (no cab occupied) or 600, 601, 612 or 613 (loco shut down nodes; BPanDnMSC = 1) - Subsystem 01 (main power) is isolated In the above cases the „Pan disable‟ contactor will be energised (BpanDisable = 1) to inhibit any wish to raise the Pan. 31.4.7 Pan Control and Supervision This part of FG 31 performs following tasks: - Raises or lowers the selected pan according to the pan up and down conditions, the pan down conditions always have the higher priority - Supervises the selected pan (see 31.6) 31.4.8 Simulation mode In the simulation mode (Bsimulation = 1) the pan will not be raised physically. A special signal (BpanUp) is sent to both SLGs to simulate catenary voltage 31.5 Multiple Control 31.5.1 Normal operation The pan up/down generation is working on the master loco only. The up or down wish is transmitted over the Trainbus to the slave loco (,V284.02f). If both „Pan selection‟ switches (, {05A, 129.1}) are in the “AUTO” position then it depends on the parameter (PA31 – P3102 – PanSelecMM) in the pan selection logic of FG31 which pan will be raised. There is a signal from the Trainbus logic (Mside2Con) to detect on which side the loco is coupled. The following table is valid if both „Pan selection‟ switches are in the “AUTO” position and the locos are in multiple operation mode: Parameter name Value Description PA31_P3102 -PanSelecMM 1(default) The most distant pans are raised (pan A and D) PA31_P3102 -PanSelecMM 2 The two most furthest parts from the occupied cab are raised (pan B and D) PA31_P3102 -PanSelecMM 3 The two pans in driving direction are raised (pan A and C) TRACTION ROLLING STOCK : THREE PHASE TECHNOLOGY Page 89 Revision Language Page A * en 5 3 EHP 541 891 31.5.2 The master loco is in trailing mode Only the pan up/down wish generation is working on the master loco. All other functions are only active on the slave loco. The „Pan disable‟ contactor on the master loco is controlled by FG31 on the slave loco (13-BpanDisable). The pan selection is the same as in the normal mode (see 31.5.1). 31.6 Disturbances Since the pan selection can be manually forced, both pressure switches (, {05A, 130.4/1 and 130.4/2}) have to be monitored within FG31 because the software cannot detect which pan is actually raised. If one pan is raised and both pressure switches are open for longer than 2 seconds (the value can be set during commissioning: PA31_P3104-PanPresDel) the VCB will be opened and a priority 1 fault message will be displayed ({1},n2242.10f). 31.6.1 HBB2 fails If HBB2 fails, the HBB2 and Subsystem 14 will be isolated as soon as the driver presses the „Fault acknowledge‟ push button. If the driver has been driving from cab 2 the driver has to change cab. From cab 1 pan 2 will be selected, which will be raised with a command from STB2. 31.6.2 STB2 fails If the driver is driving in cab 1 and the STB@ fails, pan 1 should be raised by HBB2 after pressing the „Pan up‟ push button. In order to make this functionality possible, the pan wish self hold logic must be released by FG31 in HBB2. 31.6.3 Disturbance handling in multiple operation If there is a shut down on the master loco (BPanDnMSC = 1) the driver‟s wish to raise the pan will be reset. This will cause a pan down wish on the slave loco and thereby the pan is lowered on the slave loco as well. After the fault handling and a renewed pan up wish from the driver, the selected pan will be raised on the master and on the slave loco. If there is a shut down on the slave loco, the selected pan will be lowered on the slave loco but the pan on the master loco will stay raised. After the fault handling the selected pan will be raised automatically because the wish to raise the pan is still active from the master loco. 31.6.4 Disturbance handling in trailing mode If there is a protective shut down on the slave loc, the selected pan will be lowered on the slave loco and the wish to raise the pan will be reset on the master loco. After the fault handling and a renewed pan up wish, the selected pan will be raised on the slave loco. TRACTION ROLLING STOCK : THREE PHASE TECHNOLOGY Page 90 Revision Language Page A* en 6 3 EHP 541 891 31.7 Interface Below is a complete list of all input and output signals of this function group, ordered by cluster 31.7.1 FG 31 Implemented in HBB2 Cluster Task: 100 ms Name Type I/O Bus From/To Description type 01-LPanUp BIT IN AMS {05A,130.1} Driver‟s wish to raise/lower the pan 13-LpanUpWish BIT IN TB HBB2,FG31 Driver‟s wish to raise the pan from the (M- >S) STB2,FG31 master loco 13-LpanDnWish BIT IN TB HBB2,FG31 Driver‟s wish to lower the pan from the (M- >S) STB2,FG31 master loco 23-MCAb1Active BIT IN MVB FLGM,FG23 Cab1 active 23-MCAb1Active BIT IN MVB FLGM,FG23 Cab2 active 0895-BpanUpMSC BIT IN INT FG08 Pan up unable from the MSC 0895- BIT IN INT FG08 Pan down command from the MSC Bpan DnMSC 11-MTbMastActv BIT IN MVB FLGM,FG11 This loco is the slave loco in the multiple operation and the Trainbus master is active 12-MTbSlaActv BIT IN MVB FLGM,FG12 This loco is the slave loco in the multiple operation and the Trainbus slave active 13-Mside2Con BIT IN TB FLGM,FG13 Side 2 on this loco is coupled to the other loco 54-BSTB2-Off BIT IN MVB FLGM,FG54 Processor STB2 isolated 23-MtrainOccup BIT IN MVB FLGM,FG23 Train occupied 43-MemgStopShDn BIT IN MVB FLGM,FG43 Emergency stop shut down 32-MVCB On BIT IN MVB HBB1,FG32 VCB on confirmation STB1,FG32 32-MVCB Stuck On BIT IN MVB HBB1,FG32 VCB stuck on STB1,FG32 54-BsubS01-Off BIT IN MVB FLGM,FG54 Subsystem 01 isolated 18-Bsimulation BIT IN MVB FLGM,FG18 Simulation mode is active on the loco 54-MtrailMode BIT IN MVB FLGM,FG54 The master loco is in trailing mode 13-MtrailMode BIT IN TB FLGM,FG54 The master loco is in trailing mode (MS) 13-BpanDisable BIT IN TB HBB2,FG31 Pan disable from the slave loco. Only valid (SM) STB2,FG31 if the master loco is in trailing mode 01-MPrSwPan1 BIT IN AMS {05A,130.4/1} Pressure switch pan 1 activated 01-MprSwPan2 BIT IN AMS {05A,130.4/2} Pressure switch pan 2 activated 31-BVCBOffDem BIT OUT MVB HBB1,FG32 VCB off demand STB1,FG32 31-LpanUpWish BIT OUT MVB FLGM,FG07 Driver‟s wish to raise the pan (MS) TB HBB2,FG31 STB2,FG31 TRACTION ROLLING STOCK : THREE PHASE TECHNOLOGY Page 91 31-LpanDnWish BIT OUT MVB FLGM,FG07 Driver‟s wish to lower the pan (MS) TB HBB2,FG31 STB2,FG31 3104-BEPPan1 BIT OUT AMS {05A,130.A/1} Command to raise pan1 31-BpanDisable BIT OUT AMS {05A,130.1} Releases/disables the pan self hold logic (SM) TB HBB2,FG31 STB2,FG31 3103-Mpan1NoPres BIT OUT INT FG06 Pan 1 has not enough pressure Disturbance with VCB off and priority 1 fault massage 31-BPanUp BIT OUT MVB FLGM,FG21 Simulated pan up feedback in orer to simulate SLGA,FG18 catenary voltage in the SLGs. Only valid in the SLG2,FG18 simulation mode TRACTION ROLLING STOCK : THREE PHASE TECHNOLOGY Page 92 Revision Language Page A en 7 3 EHP 541 891 31.7.2 FG 31 Implemented in STB Cluster Task : 100 ms Name Type I/O Bus type From/To Description 01-LPanUp BIT IN AMS {05A,130.1} Driver‟s wish to raise/lower the pan 13-LpanUpWish HBB2,FG31 Driver‟s wish to raise the pan from the BIT IN TB (M- >S) STB2,FG31 master loco 13-LpanDnWish HBB2,FG31 Driver‟s wish to lower the pan from the BIT IN TB (M- >S) STB2,FG31 master loco 23-MCAb1Active BIT IN MVB FLGM,FG23 Cab 1 active 23-MCAb1Active BIT IN MVB FLGM,FG23 Cab 2 active 0895-Bpan UpMSC BIT IN INT FG08 Pan up unable from the MSC 0895-Bpan DnMSC BIT IN INT FG08 Pan down command from the MSC This loco is the slave loco in the multiple 11-MTbMastActv BIT IN MVB FLGM,FG11 operation and the Trainbus master is active This loco is the slave loco in the multiple 12-MTbSlaActv BIT IN MVB FLGM,FG12 operation and the Trainbus slave active Side 2 on this loco is coupled to the other 13-Mside2Con BIT IN TB FLGM,FG13 loco 54-BSTB2-Off BIT IN MVB FLGM,FG54 Processor STB2 isolated 23-MtrainOccup BIT IN MVB FLGM,FG23 Train occupied 43-MemgStopShDn BIT IN MVB FLGM,FG43 Emergency stop shut down HBB1,FG32 32-MVCB-On BIT IN MVB VCB on confirmation STB1,FG32 HBB1,FG32 32-MVCB StuckOn BIT IN MVB VCB stuck on STB1,FG32 54-BsubS01-Off BIT IN MVB FLGM,FG54 Subsystem 01 isolated 18-Bsimulation BIT IN MVB FLGM,FG18 Simulation mode is active on the loco 54-MtrailMode BIT IN MVB FLGM,FG54 The master loco is in trailing mode 13-MtrailMode (MS) BIT IN TB FLGM,FG54 The master loco is in trailing mode HBB2,FG31 Pan disable from the slave loco. Only 13-Bpan Disable (SM) BIT IN TB STB2,FG31 valid if the master loco is in trailing mode 01-MPrSwPan1 BIT IN AMS {05A,130.4/1} Pressure switch pan 1 activated 01-MprSwPan2 BIT IN AMS {05A,130.4/2} Pressure switch pan 2 activated HBB1,FG32 31-BVCBOffDem BIT OUT MVB VCB off demand STB1,FG32 FLGM,FG07 31-LpanUpWish MVB BIT OUT HBB2,FG31 Driver‟s wish to raise the pan (MS) TB STB2,FG31 FLGM,FG07 MVB 31-LpanDnWish (MS) BIT OUT HBB2,FG31 Driver‟s wish to lower the pan TB STB2,FG31 3104-BEPPan1 BIT OUT AMS {05A,130.A/1} Command to raise pan1 {05A,130.1} 31-BpanDisable AMS BIT OUT HBB2,FG31 Releases/disables the pan self hold logic (SM) TB STB2,FG31 Pan 1 has not enough pressure Disturbance 3103-Mpan1NoPres BIT OUT INT FG06 with VCB off and priority 1 fault massage FLGM,FG21 Simulated pan up feedback in order to 31-BPanUp BIT OUT MVB SLGA,FG18 simulate catenary voltage in the SLGs. SLG2,FG18 Only valid in the simulation mode TRACTION ROLLING STOCK : THREE PHASE TECHNOLOGY Page 93 TRACTION ROLLING STOCK : THREE PHASE TECHNOLOGY Page 94 TRACTION ROLLING STOCK : THREE PHASE TECHNOLOGY Page 95