Building Design and Development Pt. II PDF
Document Details
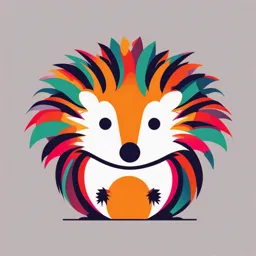
Uploaded by RazorSharpRaleigh
IPG „Mihai Eminescu” Telenești
Tags
Summary
This document covers building system design, focusing on the process and constraints involved. It details design considerations, including owner needs, site limitations, budgetary constraints, and building codes. The text emphasizes legal, zoning, and sustainability regulations.
Full Transcript
Module 1 Building Design and Development Pt. II Building System Design Working with Constraints Building System Design What initiates the building design process? Owner(s) express a need/desire for a building/structure “Owners” can be businesses, individuals, government organization...
Module 1 Building Design and Development Pt. II Building System Design Working with Constraints Building System Design What initiates the building design process? Owner(s) express a need/desire for a building/structure “Owners” can be businesses, individuals, government organizations, educational institutions, military departments, etc… Needs/Desires can range depending on the owner. Business need (new manufacturing process, new market, larger staff needs) Speculative development (new housing developments, new communities) Municipal Infrastructure (new bridges, new hospitals, new roads) Owners work with design teams to create drawings and/or digital models of the building/structure. Design team typically consists of Architect, Engineers, Interior Designers, Landscape Architects Drawings/Models include information on materials and details on how building is to be constructed. Design Constraints Architects and Engineers are able to combine building materials and structural systems to create custom (and often creative) spaces for their clients. Their creativity is limited (or guided) by design constraints Design Constraints can include: Physical limitations of the project site, Budgetary constraints of the owners, Building code restrictions and requirements Zoning regulations Sustainability Objectives Design Constraints Designer Requirements Cost & Market Codes & Legal Building Sustainability Owners Participants Design Constraints What are some typical constraints that need to be considered for a construction project? What is the bearing capacity of the soil? How long of a structural span is possible? How long is required? What materials perform better than others given the environmental conditions? What size of building that will fit the lot? Design Constraints Typical constraints that need to be considered for a construction project? Are there physical obstructions that limit site? Are there site features that should guide building/structure placement? Are there zoning restrictions on sightlines and building heights? What is the client’s budget?? Legal Regulations Building Codes, Zoning, Accessibility Legal Regulations – Zoning Requirements Allowed types of activities The set back Total floor amount from area the property lines Zoning Ordinates Number of Height of parking building spaces Area that can be covered by building Legal Regulations – Building Codes Building Codes are created by Government and Industry stakeholders. They are intended to protect public health and safety by setting minimum standards for construction quality. Source: www.nrc.canada.ca Legal Regulations – Building Codes Federal Government publishes the National Building Code Model Code (setting a national standard) Not enforceable by law First published in 1941 Adopted and enacted by provinces as Provincial Building Codes over the following 20 years. Revised every 5 years by national organization of local building code officials. Published by the National Research Council (NRC) Current Version: 2015 Next Revision: 2020 (not revised as of class date) Source: www.nrc.canada.ca NBC – Divisions and Contents The NBC is made up of 3 Divisions. Division A: defines the scope of the NBC details the objectives and conditions necessary to achieve compliance. Division B: contains acceptable solutions and technical requirements tha meet the objectives outlined in Division A. Division C: outlines administrative provisions relating to application of the Code. NBC – Division B From a design and construction perspective, Division B is the most important Division of the NBC. Some of the most referenced Parts of Division B include: Part 3 – Fire Protection Part 4 – Structural Design Part 6 – Heating, Venting, and Air-Conditioning Part 7 – Plumbing Part 9 – Housing & Small Buildings NBC – Division B Part 9 Division B - Part 9 (Housing and Small Buildings) is such a large portion of the NBC that it is presented in a separate binder This binder is often referenced as Volume 2. Part 9 includes all phases of construction on a typical house or small project. This includes: foundation, framing, building envelope, windows and doors, mechanical and electrical. Legal Regulations – Building Codes The Alberta Building Code (ABC) is governed by Alberta Municipal Affairs. This department of the provincial government decides on which revisions to the NBC will be implemented into the ABC and which will not. Source: www.alberta.ca Legal Regulations – Building Codes Aside from the ABC, other safety codes are also governed by Alberta Municipal Affairs. Some of these include: Electrical Code Fire Code Gas Code Plumbing Code. Alberta Safety Codes Source: www.alberta.ca Legal Regulations – Energy Codes Canada has recently adopted the National Energy Code for Buildings (NECB) NECB outlines technical provisions for building more energy efficient structures. Source: www.nrc.canada.ca Legal Regulations – Energy Codes It was first introduced in 1997, however it is not until recently that more attention has been placed on the NECB as energy efficient homes and green building technologies have developed. 2017 National Energy Code Website Source: www.nrc.canada.ca Legal Regulations – Energy Codes Provisions in Section 9.36 of the NBC also discusses Energy Efficiency. These provisions (which only apply to housing and small buildings) have a similar scope to that of the NECB, except that they do not address lighting and electrical power systems. The NECB is referenced in NBC Section 9.36 as an acceptable solution. 2017 NECB NBC – Building Classification Assembly The NBC Building Classification Simple buildings Business System is based on sub-section 3.1.2 of the 2015 Building Code Residential Use Industry Groups High hazard Mercantile industry Institutional NBC – Building Classification NBC Building Classifications are shown below. Building Classification Exercise Based on the previous table, identify the building classification for these Calgary structures. Calgary Saddledome Foothills Medical Centre Shepard Energy Centre Chinook Mall SAIT Campus Centre Legal Regulations – Safety To ensure the safety of all workers within the province of Alberta, the Alberta Occupational Health and Safety (OHS) Act was enacted in 1976. Over the years it has expanded to include: job site safety, hours of work, work relationship guidelines, technology and equipment guidelines Alberta OHS Act Legal Regulations – Accessibility Accessibility Standards or Barrier Free Design controls the design of building facilities to assure that they are accessible by people with disabilities and with limited mobility. Section 3.8 of the NBC outlines the scope and the design of Barrier Free buildings and the buildings in which these guidelines apply. Barrier Free Design Guide Legal Regulations – Sustainability Sustainability in Building Design has become more common place in the last 10 years. Design is typically based on Green Building practices which take into consideration the environment, people, and the economy. The City of Calgary has a Sustainability Building Policy in place in which all new City owned buildings must exceed the Gold level in the latest LEED rating system. City of Calgary - Sustainability Policy Building Constraint Exercise SAIT Parking Garage Design Constraint Exercise Review the Site Plans for the SAIT Parking Garage and identify what constraints had to be considered prior to construction. What would have been some of the requirements? What would have been some of the restrictions? Group Exercise - SAIT Parking Garage C AN AD A | 2 0 0 8 - 2 0 0 9 AIRSTATE CENTRE Source: www.google.ca/maps Source: www.google.ca/maps SAIT Parking Garage Review the Site Plans for the SAIT Parking Garage and identify what constraints had to be considered prior to construction. Drawings and photos can be found in the link below. SAIT Parkade C AN AD A | 2 0 0 8 - 2 0 0 9 AIRSTATE CENTRE Source: www.google.ca/maps SAIT Parking Garage – Existing Site & Demo Plan C AN AD A | 2 0 0 8 - 2 0 0 9 AIRSTATE CENTRE SAIT Parking Garage – New Construction C AN AD A | 2 0 0 8 - 2 0 0 9 AIRSTATE CENTRE Source: www.google.ca/maps Project Development Phases From Concept to Commissioning Project Delivery Phases There are many ways in which project delivery can be described based on jurisdiction and project size. The phases shown below outline how a project can be executed on a typical building. Pre-design/Conceptual Phase Planning, Scoping, Siting, Stakeholder Consultations Design Phase Design Development Pre-construction/Tendering Contractor selection Construction Phase Fabrication, Construction, Inspection Post Construction Phase Occupancy, Project closeout, Warrantee Pre-Design Phase The Pre-Design Phase is where the project is defined in terms of function, scope, size, and budget. This is managed by the owner and the owner’s team. Tasks include: - Site assessment and selection - Building constraints - Economic assessment - Design team selection Pre-Design/Conceptual Phase Source: www.cwsarchitecture.com Design Phase The Design Phase usually occurs after the selection of an architectural design team along with other consultants. The architect performs the role of Prime Consultant with other specialized consultants providing expertise for complex projects. In most building projects, the design phase consists of 3 sequential steps which are defined as: Schematic Design Stage Design Development Stage Construction Document Stage. Design Phase Pre-Construction Phase The Pre-Construction/Tendering Phase is the point in the project where drawings and specifications are near 100% completion, so the project can be bid on by a General Contractor (GC). The Bid Documents or Bid Package typically needs some clarifications which are addressed by means of: Query Lists sent from GCs to the Architect Addendum documents issued to all bidders. Once the contract has been awarded, the Bid Documents become the Contract Documents. (More on this in CIVL 312 in 2nd year) Contract Documents Construction Phase The Construction Phase of a project begins after the GC has been selected, the contract awarded, and notice to proceed issued. Construction drawings are reviewed, finalized, and used to produce “shop drawings” for components like structural steel members. Fabrication of materials does not begin until the Architect and/or Structural Engineer reviews and approves the shop drawings. Shop Drawing Stamp Construction Phase Documentation and monitoring of construction activities from start to finish is also a critical part of a GC’s scope of work. These documents can include: project correspondence meeting minutes requests for information (RFI) site instructions change orders material lists, etc….. The documentation process has improved greatly with changes in technology such as document management systems, portable drawing viewers, and web-based cameras. Post construction Phase In the Post Construction or Project Closeout Phase, the GC is responsible for ensuring the building is ready for turnover to the owner so that occupancy can begin. The terms Substantial Completion and Punch Lists are commonly used to describe the outstanding activities which are required to be completed by the GC prior to a Certificate of Occupancy being issued by the local building authority such as the City of Calgary. Post construction Phase A final completion inspection is carried out by the architect with assistance from the sub-consultants on the project to ensure all the outstanding items on the punch list have been addressed. Record documents and As-Built Drawings are submitted to the owner at this time as well. These drawings reflect any changes to the building during construction so that future expansions or modifications can be done with the most accurate information. As-built drawings Source: www.constructionspecifier.com Module 1 Building Design and Development Pt. II Building System Design Working with Constraints Building System Design What initiates the building design process? Owner(s) express a need/desire for a building/structure “Owners” can be businesses, individuals, government organizations, educational institutions, military departments, etc… Needs/Desires can range depending on the owner. Business need (new manufacturing process, new market, larger staff needs) Speculative development (new housing developments, new communities) Municipal Infrastructure (new bridges, new hospitals, new roads) Owners work with design teams to create drawings and/or digital models of the building/structure. Design team typically consists of Architect, Engineers, Interior Designers, Landscape Architects Drawings/Models include information on materials and details on how building is to be constructed. Design Constraints Architects and Engineers are able to combine building materials and structural systems to create custom (and often creative) spaces for their clients. Their creativity is limited (or guided) by design constraints Design Constraints can include: Physical limitations of the project site, Budgetary constraints of the owners, Building code restrictions and requirements Zoning regulations Sustainability Objectives Design Constraints Designer Requirements Cost & Market Codes & Legal Building Sustainability Owners Participants Design Constraints What are some typical constraints that need to be considered for a construction project? What is the bearing capacity of the soil? How long of a structural span is possible? How long is required? What materials perform better than others given the environmental conditions? What size of building that will fit the lot? Design Constraints Typical constraints that need to be considered for a construction project? Are there physical obstructions that limit site? Are there site features that should guide building/structure placement? Are there zoning restrictions on sightlines and building heights? What is the client’s budget?? Legal Regulations Building Codes, Zoning, Accessibility Legal Regulations – Zoning Requirements Allowed types of activities The set back Total floor amount from area the property lines Zoning Ordinates Number of Height of parking building spaces Area that can be covered by building Legal Regulations – Building Codes Building Codes are created by Government and Industry stakeholders. They are intended to protect public health and safety by setting minimum standards for construction quality. Source: www.nrc.canada.ca Legal Regulations – Building Codes Federal Government publishes the National Building Code Model Code (setting a national standard) Not enforceable by law First published in 1941 Adopted and enacted by provinces as Provincial Building Codes over the following 20 years. Revised every 5 years by national organization of local building code officials. Published by the National Research Council (NRC) Current Version: 2020 Source: www.nrc.canada.ca NBC – Divisions and Contents The NBC is made up of 3 Divisions. Division A: defines the scope of the NBC details the objectives and conditions necessary to achieve compliance. Division B: contains acceptable solutions and technical requirements tha meet the objectives outlined in Division A. Division C: outlines administrative provisions relating to application of the Code. NBC – Division B From a design and construction perspective, Division B is the most important Division of the NBC. Some of the most referenced Parts of Division B include: Part 3 – Fire Protection Part 4 – Structural Design Part 6 – Heating, Venting, and Air-Conditioning Part 7 – Plumbing Part 9 – Housing & Small Buildings NBC – Division B Part 9 Division B - Part 9 (Housing and Small Buildings) is such a large portion of the NBC that it is presented in a separate binder This binder is often referenced as Volume 2. Part 9 includes all phases of construction on a typical house or small project. This includes: foundation, framing, building envelope, windows and doors, mechanical and electrical. Legal Regulations – Building Codes The National Building Code – Alberta Edition (NBC-AE) is governed by Alberta Municipal Affairs. This department of the provincial government decides on which revisions to the NBC will be implemented into the ABC and which will not. Source: www.alberta.ca Legal Regulations – Building Codes Aside from the NBC-AE, other safety codes are also governed by Alberta Municipal Affairs. Some of these include: Electrical Code Fire Code Gas Code Plumbing Code. Alberta Safety Codes Source: www.alberta.ca Legal Regulations – Energy Codes Canada has recently adopted the National Energy Code for Buildings (NECB) NECB outlines technical provisions for building more energy efficient structures. Source: www.nrc.canada.ca Legal Regulations – Energy Codes It was first introduced in 1997, however it is not until recently that more attention has been placed on the NECB as energy efficient homes and green building technologies have developed. 2020 National Energy Code Website Source: www.nrc.canada.ca Legal Regulations – Energy Codes Provisions in Section 9.36 of the NBC also discusses Energy Efficiency. These provisions (which only apply to housing and small buildings) have a similar scope to that of the NECB, except that they do not address lighting and electrical power systems. The NECB is referenced in NBC Section 9.36 as an acceptable solution. 2020 NECB NBC – Building Classification Assembly The NBC Building Classification Simple buildings Business System is based on sub-section 3.1.2 of the 2015 Building Code Residential Use Industry Groups High hazard Mercantile industry Institutional NBC – Building Classification NBC Building Classifications are shown below. Building Classification Exercise Based on the previous table, identify the building classification for these Calgary structures. Calgary Saddledome Foothills Medical Centre Shepard Energy Centre Chinook Mall SAIT Campus Centre Legal Regulations – Safety To ensure the safety of all workers within the province of Alberta, the Alberta Occupational Health and Safety (OHS) Act was enacted in 1976. Over the years it has expanded to include: job site safety, hours of work, work relationship guidelines, technology and equipment guidelines Alberta OHS Act Legal Regulations – Accessibility Accessibility Standards or Barrier Free Design controls the design of building facilities to assure that they are accessible by people with disabilities and with limited mobility. Section 3.8 of the NBC outlines the scope and the design of Barrier Free buildings and the buildings in which these guidelines apply. Barrier Free Design Guide Legal Regulations – Sustainability Sustainability in Building Design has become more common place in the last 10 years. Design is typically based on Green Building practices which take into consideration the environment, people, and the economy. The City of Calgary has a Sustainability Building Policy in place in which all new City owned buildings must exceed the Gold level in the latest LEED rating system. City of Calgary - Sustainability Policy Building Constraint Exercise SAIT Parking Garage Design Constraint Exercise Review the Site Plans for the SAIT Parking Garage and identify what constraints had to be considered prior to construction. What would have been some of the requirements? What would have been some of the restrictions? Group Exercise - SAIT Parking Garage C AN AD A | 2 0 0 8 - 2 0 0 9 AIRSTATE CENTRE Source: www.google.ca/maps Source: www.google.ca/maps SAIT Parking Garage Review the Site Plans for the SAIT Parking Garage and identify what constraints had to be considered prior to construction. Drawings and photos can be found in the link below. SAIT Parkade C AN AD A | 2 0 0 8 - 2 0 0 9 AIRSTATE CENTRE Source: www.google.ca/maps SAIT Parking Garage – Existing Site & Demo Plan C AN AD A | 2 0 0 8 - 2 0 0 9 AIRSTATE CENTRE SAIT Parking Garage – New Construction C AN AD A | 2 0 0 8 - 2 0 0 9 AIRSTATE CENTRE Source: www.google.ca/maps Project Development Phases From Concept to Commissioning Project Delivery Phases There are many ways in which project delivery can be described based on jurisdiction and project size. The phases shown below outline how a project can be executed on a typical building. Pre-design/Conceptual Phase Planning, Scoping, Siting, Stakeholder Consultations Design Phase Design Development Pre-construction/Tendering Contractor selection Construction Phase Fabrication, Construction, Inspection Post Construction Phase Occupancy, Project closeout, Warrantee Pre-Design Phase The Pre-Design Phase is where the project is defined in terms of function, scope, size, and budget. This is managed by the owner and the owner’s team. Tasks include: - Site assessment and selection - Building constraints - Economic assessment - Design team selection Pre-Design/Conceptual Phase Source: www.cwsarchitecture.com Design Phase The Design Phase usually occurs after the selection of an architectural design team along with other consultants. The architect performs the role of Prime Consultant with other specialized consultants providing expertise for complex projects. In most building projects, the design phase consists of 3 sequential steps which are defined as: Schematic Design Stage Design Development Stage Construction Document Stage. Design Phase Pre-Construction Phase The Pre-Construction/Tendering Phase is the point in the project where drawings and specifications are near 100% completion, so the project can be bid on by a General Contractor (GC). The Bid Documents or Bid Package typically needs some clarifications which are addressed by means of: Query Lists sent from GCs to the Architect Addendum documents issued to all bidders. Once the contract has been awarded, the Bid Documents become the Contract Documents. (More on this in CIVL 312 in 2nd year) Contract Documents Construction Phase The Construction Phase of a project begins after the GC has been selected, the contract awarded, and notice to proceed issued. Construction drawings are reviewed, finalized, and used to produce “shop drawings” for components like structural steel members. Fabrication of materials does not begin until the Architect and/or Structural Engineer reviews and approves the shop drawings. Shop Drawing Stamp Construction Phase Documentation and monitoring of construction activities from start to finish is also a critical part of a GC’s scope of work. These documents can include: project correspondence meeting minutes requests for information (RFI) site instructions change orders material lists, etc….. The documentation process has improved greatly with changes in technology such as document management systems, portable drawing viewers, and web-based cameras. Post construction Phase In the Post Construction or Project Closeout Phase, the GC is responsible for ensuring the building is ready for turnover to the owner so that occupancy can begin. The terms Substantial Completion and Punch Lists are commonly used to describe the outstanding activities which are required to be completed by the GC prior to a Certificate of Occupancy being issued by the local building authority such as the City of Calgary. Post construction Phase A final completion inspection is carried out by the architect with assistance from the sub-consultants on the project to ensure all the outstanding items on the punch list have been addressed. Record documents and As-Built Drawings are submitted to the owner at this time as well. These drawings reflect any changes to the building during construction so that future expansions or modifications can be done with the most accurate information. As-built drawings Source: www.constructionspecifier.com Module 2 Foundations Part I - Function Foundations Learning Objectives: 1. Describe the different loads acting on foundations. 2. Describe the effect of soil type on foundation design and methods of subsurface exploration and soil testing. 3. List different types of foundations with their characteristics. 4. Describe methods of waterproofing and drainage of foundations. 5. State the factors affecting the foundation design. Foundations The Basics Foundation Basics Foundations are the lowest part of the building Also known as The Substructure Primary function is to support and anchor the superstructure above and transmit its loads safely into the earth. Foundation Basics Foundation design is a highly specialized field of Geotechnical Engineering. Foundations must pass the unstable surface soils and reach the underlying subsurface soil that is empty of organic matter and free of frost. The larger/heavier the building, generally, the larger the foundation will be. Foundations Basics Shallow Foundations Suitable for smaller buildings (lighter weight, smaller loads) Unconsolidated soil (Sand, Gravel, Etc…) or Shallow Bedrock Ex: Strip Footings, Pad Footings, Slab-on-Grade Deep Foundations More common with larger buildings with higher weights and/or greater loads. Deep foundations often extend below unconsolidated soil and down to bedrock. Ex: Piles, Caissons Foundation Basics – Deep Foundations When soil underlying the foundation is unstable or of inadequate bearing capacity a deep foundation is required. They extend down through unsuitable soils to transfer building loads to a more suitable bearing stratum (layer) of rock or dense sands and gravel well below the superstructure. Foundation Loads Foundation Loads Dead Live Wind Seismic Other Loads Loads Loads Loads Loads The sum of the Sum of the Horizontal and weights of the weights of people vertical forces Inclined or frame; the floors Horizontal in the building; the Can apply lateral, caused by motion horizontal thrusts and walls; the Buoyant uplift pressures of earth furniture and the downward or of the ground from arches, rigid electrical and forces and water against equipment and upwards relative to the frames, domes or mechanical basement walls. snow, ice and building during tensile structures equipment and the water on the roof. earthquake. foundation. Foundation Requirements In general, foundations should be designed to be: Technically feasible based on soil conditions Practical based on building size and use Economical based on construction costs Having little to no impact on surrounding properties and the environment Foundation Settlement Foundations should not settle and cause damage to the structure or impair the function of the building. Settlement occurs when the foundation and/or underlying soil and rock aren’t able to resist a structural stresses. Two types of settlement can occur: Uniform Settlement Whole foundation settles at a constant rate so is approximately the same from one side of the building to another Building “sinks” into the ground Differential Settlement Commonly occurs as a result of non-uniform movement of underlying soils One or more of the load bearing walls settle by a considerable amount resulting in distortion to the structure Building Tilts (Tipping Settlement) or Cracks (Differential Settlement w/Cracks) Image Credit: Lonely Planet Foundation Settlement Image Credit: InterNachi Foundation Settlement Objective 1 Summary Why and How do Foundations Fail? Unpredictable Loads (under designed, change of use) Differential Settlement All buildings settle but the amount should only be in millimetres What can it look like? Distorted Frames Sloping Floors Cracks Window and Doors tight or change fit Soil Types & Characteristics Soil Characteristics All soil types have different characteristics and properties. Particle sizes and shapes Friction Angle between Soil Particles Resistance to Slide – Shear Resistance Moisture Content Cohesive Soils (Silts & Clays) Strength comes from cohesive forces between the soil particles Exhibit “plasticity” Frictional Soils (Sands and Gravels) Strength comes from friction and interlocking of soil particles Excavations in Construction Soil Characteristics Angle of Repose All soils will have different stability when stockpiled. Some soils will be more stable than others Clay > Coarse Sand > Fine Sand Compacted and loose soils will behave differently Why do volumes for In-Situ, Loose & Compacted vary? Removing air volume Increasing frictional contact Compaction encourages sorting/settling Soil Classification 2 Categories of Soil based on particle size. Fine-Grained Soils Soil particles are 75 micron in diameter) Divided into: Sands and Gravels Soil Classification (Typ.) Sieve Opening Boulder 300 mm Cobbles 300 - 75 mm Gravel: Coarse 75 – 19 mm Gravel: Fine 19 – 5 mm Sand: Coarse 5 – 2 mm Sand: Medium 2 – 0.5 mm Sand: Fine 0.5 – 0.075 mm Silts and Clays 75 micron and less Soil Classification Table Note: The susceptibility to Frost action increases as the soils get finer, because they retain more water. Soil Classification: Boulders Boulder The individual particle of the soil is too large to lift by hand, or requires two hands to lift. Typically greater than 300 mm in diameter. Soil Classification: Cobble Cobble: It takes the whole hand to lift a particle. Typically greater than 75 mm in diameter. Soil Classification: Gravel Gravel A particle can be lifted easily with thumb and forefinger. Particle size ranges from 75 mm to 5 mm in diameter. Crushed gravel will have a higher bearing capacity than washed gravel Soil Classification: Sand Sand Particles can be seen but they are too small to be picked up individually. Particles size range from 75 micron to 5 mm. Coarse and angular sands have more bearing capacity than fine sands Soil Classification: Silts and Clay Silts and Clay Fine-grained soils with particle sizes less than 75 micron. Create “plasticity” in soil Clay = flat particles Silt = round particles Typically low bearing capacity Soil Characteristics It is important that designer knows the distribution of the particle sizes and types. Where are soils of different types located (laterally and vertically) within project area Helps designer to predict the key characteristics of the soils such as: Load-bearing capacity Stability Drainage potential Soil Characteristics: Bearing Capacity Bearing Capacity the capacity of soil to support the loads applied to the ground the maximum average contact pressure between the foundation and the soil which should not produce shear failure in the soil. Load bearing capacity is dependent on factors such as: Percentage of soil moisture Soil type Size of designed foundation Depth of designed foundation Soil Characteristics: Stability Stability the ability of the soil to maintain its engineering properties under varying conditions during the life of the structure. While rock, gravels, sands and many silts tend to be stable soils, many clays are unstable under changing moisture content conditions. Clays can absorb considerable amounts of water and swell, or lose water under pressure and reduce in volume. Soil Characteristics: Drainage Drainage Is important for the prediction of water flow on and under building sites and around substructures. Drainage Fill should be used around foundations to intercept any water moving toward the building which is then redirected to a drainage system. Clay Fill should be used in landfills, dykes and other structures in which a low permeability is required to keep liquids contained. Chapter 2 Reading Read pages 31-39 References/Sources E. Allan, J. Iano, Fundamentals of Building Construction – Materials and Methods, 6th Edition. Hoboken, New Jersey: John Wiley & Sons, 2014, pp. 1-659. Module 2 –Foundation Part II – Soil Testing and Shallow Foundations Foundations Learning Objectives: 1. Describe the different loads acting on foundations. 2. Describe the effect of soil type on foundation design and methods of subsurface exploration and soil testing. 3. List different types of foundations with their characteristics. 4. Describe methods of waterproofing and drainage of foundations. 5. State the factors affecting the foundation design. Surface Exploration and Testing: Test Pits Open Excavations/Test Pits Used determine soil conditions when the foundation is not expected to extend typically lower than 3 metres below grade. The level of the water table will be readily apparent in coarse-grained soils if it falls within the depth of the pit. If the test pit is excavated below the water table in clay, free water will not seep into the pit, as clays are relatively impermeable. Other methods of inspection should be used to find the water level. Load tests can be performed under a test pit to find S ource: http://www.gravelator.com/images/Soil_Evaluation/6- the stress capacity of the soil and the amount of Evaluating%20test%20pit%20conditions.jpg settlement that could be expected under load. Surface Exploration and Testing: Boreholes and Core Samples Boreholes and Core Samples The soil underlying a building site usually consists of superimposed layers Layers contain a mix of soil types from weathering or deposition over (geologic) time Boreholes allow geotechnical engineer can determine the soil profile across the site, and at depths that Test Pits can’t reach. Typically this information is presented on “Borehole Logs” display information relative to depth below grade shows water table elevation Surface Exploration and Testing: Boreholes and Core Samples Boreholes and Core Samples Both boreholes and core samples are holes drilled into the ground to well below final excavation depth. Often multiple boreholes are advanced across a project site to give better resolution to subsurface data. Thickness and locations of the soil strata, Depth and slope of the water table Location of subsurface contaminants (if present) Useful in determining bearing capacity of soil and bedrock below the foundation. During collection, the number of blows on a standard driving hammer required to advance a sampling tube into the soil by a fixed amount can give an indication of the bearing capacity. Surface Exploration and Testing: Boreholes and Core Samples Bore Holes and Core Samples Laboratory-quality samples can be obtained for testing. An example of a modern soils/ground investigation drilling rig is a Soilmec Rig. Image Credit Surface Exploration and Testing: Soil Profiles and Cross Sections Soils Testing Tests to determine the Engineering properties of fine-grained soils: Atterberg Limits Liquid Limit: The water content at which the soil passes from a plastic state to a liquid state. Plastic Limit: The water content at which the soil loses it plasticity and begins to behave as a solid. Shrinkage Limit: The water content below which will not result in a volume reduction (less common) Water content of soil. Permeability of soil Shear and compressive strength. Consolidation capability under load Site Preparation for Foundations How to we prepare sites for foundation construction? Survey with Offsets (Grades are also established) Cut/Fill Project Site Excavate foundation to proper Grade Ensure all organics are removed under building footprint Dewatering may be required if water table is higher than normal Excavations deeper than 1.5m in Canada require Slope Protection Shoring may be required if soil conditions are poor or excavation is in close proximity to other buildings Introduction to Foundations Three major parts of a building for which foundations are designed for: Superstructure: the above-ground portion of the building. Substructure: the habitable, below-ground portion. Foundations: the components of the building that transfer its loads into the soil. Foundation Selection Primary factors affecting the selection of foundations: Subsurface soil and ground water conditions. Structural requirements: e.g. foundation loads, configurations and depth. Secondary factors affecting the selection of foundations Construction methods, access and working room Environmental factors: noise, traffic and disposal of earth and water Codes and regulations Impact on adjacent property Time constraints Construction risks Foundations: Types Shallow foundations: Transferring the load to the earth at the base of the column or wall of the substructure. Applicable when suitable soil is available at the bottom of the substructure. Typically less expensive than deep foundations Deep foundations: Transferring the load at a point some distance under the substructure. Either pile or caissons penetrate through upper layers of unsuitable soil to reach competent bearing soil or bedrock. Foundations: Types Foundations Shallow Deep Column Pad Wall or Strip Mat or Raft Floating Piles Caissons Footing Footing Foundation Footing End Bearing Friction Belled Socketed Types of Shallow Foundations Most shallow foundations are Footings: A wide block of (typically) concrete at the base of a column or wall. Distributes the the loads across an area of soil Area must be large enough that the weight from structure above doesn’t exceed the bearing capacity of the soil Types of Shallow Foundations: Pad/Column Footing Strip Footing Slab on grade climates with small or no ground frost; least expensive. Crawlspace or Basement Floors raised above the ground support is provided by concrete or masonry foundation walls supported on concrete strip footings most common in northern climates. Types of Spread Footings Pad/Column Footing Combined Footing Connecting footing to steel or wood More economical to combine footings columns require cast in place base or base in some instances rather than have plate anchors individual footings Types of Spread Footings Strip/Wall/Perimeter Footing Cantilevered Footing Used around the perimeter of a Used to balance asymmetrical loads building under the foundation wall Where foundations abut a property line Shallow Foundations Shallow Foundations Shallow Foundations: Strip Footing (Wall Footing) Pouring Concrete Footings Shallow Foundations: Step Footings Different types of Foundations Mat or Raft Foundations: Used when allowable bearing capacity of the soil is low in relation to the weight of the building; it is more economical to merge all of the column footings to one mat or raft foundation. (ex. Bow Tower) Image Credit: Dynamic Concrete Pumping Image Credit: Dynamic Concrete Pumping Different types of Foundations Mat or Raft Foundations: Image Credit: Dynamic Concrete Pumping Image Credit: Harris Rebar Matt/Raft Foundation Different types of foundations Floating Foundation: In soils with low bearing capacity and carefully controlled settlement requirement; similar to a mat but placed at a depth such that the weight of excavated soil is equal to the weight of the building, so that the load on the underlying soil changes very little. Reinforcing Steel in Concrete Reinforcing steel in footings requires cover of 25 to 75 mm Typically 10M Reinforcing steel is used for most applications Chapter 2 Reading Read Pages 40-54 References/Sources E. Allan, J. Iano, Fundamentals of Building Construction – Materials and Methods, 6th Edition. Hoboken, New Jersey: John Wiley & Sons, 2014, pp. 1-659. Module 2 - Foundations Part 3 - Deep Foundations and Shoring Foundations – Deep Shoring Methods. Learning Objectives: Describe the different loads acting on foundations. Describe the effect of soil type on foundation design and methods of subsurface exploration and soil testing. List different types of foundations with their characteristics. Describe methods of waterproofing and drainage of foundations. State the factors affecting the foundation design. Deep Foundations Required when soil underlying the foundation is unstable or of inadequate bearing capacity. (Poor unstable soil). extend down through unsuitable soils to transfer building loads to a more suitable bearing stratum (layer) of rock or dense sands and gravel well below the superstructure. Deep Foundations: Types 2 Primary Types Piles: Vertical supports that are driven/drilled into the earth Made from variety of materials: Steel, Concrete, Wood, Composites Caissons Poured concrete & reinforcing steel Deep support, like a pile Deep Foundations: Piles Piles are typically steel, timber, or precast concrete Driven or drilled into the ground until sufficient resistance is encountered 2 Types of Piles based on the mechanism of resistance End Bearing Piles Friction Piles Deep Foundations: Piles End Bearing Pile pile is driven into the ground until it encounters substantial resistance from rock or dense sands and gravels below the pile. Bearing Capacity will vary with the area of the base Common Types: H-Pile, Precast Pile Friction Pile develops extensive load carrying capacity through the frictional resistance between the sides of the pile and the soil, no encountering stiff bearing layer required Common Types: Precast Pile, Timber Pile, Helical Pile Deep Foundations: Caissons Caissons often look like a pile, but typically function like a footing. Support is from uncompacted ground or bedrock Poured concrete, rather than driven/drilled 2 Types of Caissons Belled Caissons Socketed Caissons Deep Foundations: Caissons/Piers Belled Caissons/Piers: a borehole of a fixed width is drilled to a specific depth the bottom of the hole is widened to create a bell shape maximizes displacement on the soil below bearing capacity comes from the bell and frictional forces between the shaft of the caisson and the soil applicable where a bell can be excavated in a cohesive soil (e.g. clay based soils) Socketed Caissons/Piers: a borehole is drilled through surface soils into rock bearing capacity comes from both the end bearing and the frictional forces between the sides of the caisson and the rock. Examples of Deep Foundations Deep Foundations: Installing Piles Driven Piles Heavy hammers, powered by the energy of steam, compressed air or compressed hydraulic fluid, or diesel explosion “drive” a pile into the ground 2 Types: Single-Acting Hammer - Gravity Double-Acting Hammers – Gravity & Explosive Charge Vibration can work instead of driving in some soil types Helical/Screw Piles Diesel powered rotary pile-rig screws the pile into the ground to the desired depth Deep Foundations: Installing Piles Oscillating Caissons Diesel Hammer Driven Piles Deep Foundations: Installing Piles Deep Foundations: Installing Piles Installing Precast Piles Deep Foundations: Steel Wide-Flange Piles Source: http://videoblast.wileypub.com/074688_FundOfBuildConst/Slideshow/soilsfound/pile1.html Deep Foundations: Caisson Installation Caisson Installation Source: http://videoblast.wileypub.com/074688_FundOfBuildConst/Slideshow/soilsfound/caisson9.html Deep Foundations: Pile Caps Pile Caps joins a cluster of piles/caissons at the top to create a single solid structure Reinforced concrete or steel, distributes the load of the columns or walls equally among the piles. Deep Foundations: Pile Caps Deep Foundations: Pile Materials Timber used since Roman times. Economical for lightly loaded foundations; cannot be spliced during driving, hence there is limitation on length (approximately 60 feet). Steel H-Piles special hot-rolled, wide-flange sections from 8-14 inches. Pipe-Piles Large hollow pipes (sizes vary) driven into the ground lower end can be either open or closed with a heavy steel plate. Helical/Screw Piles Steel shaft with at least 1 helix (spiral) plate at base Deep Foundations: Pile Materials Precast Concrete comes in numerous geometric configurations: square, octagonal or round sections in larger sizes, they have open cores to allow for inspection. Most are pre-stressed, but some for smaller buildings are barely reinforced. Size ranges from 10 to 16 in. Site-Cast Concrete made by driving a hollow steel shell into the ground and filling it with concrete corrugation of the shell increases the stiffness. Shoring Holding Back the Earth Shoring: Overview Shoring is: methods to support the sides of an excavation and prevent its collapse. Why do we shore: Constraints on the Building Footprint Poor Shallow Soils Groundwater Infiltration Shoring: Overview For large excavations, the most common types of shoring are: Soldier Beams and Lagging Secant Piles Sheet Piling Shotcrete Slurry Walls. Shoring: Overview Shoring: Shoring Types Soldier Beams and Lagging: Steel H-Piles (Soldier Beams) are driven vertically into the earth at close intervals around an excavation site before digging begins. Heavy wood planks (Lagging) are placed against the flanges of the columns to retain the soil outside the excavation. Shoring: Shoring Types Shoring: Shoring Types Sheet Piling: Consists of vertical sheets of various materials that are aligned tightly against one another edge-to-edge and driven into the earth to form a solid wall. This occurs before excavation begins. Most common material for sheet piling is steel, but wood and other materials may be used. Shoring: Shoring Types Shoring: Shoring Types Shotcrete: soil at the project site is sufficiently cohesive to hold an adequate slope (at least temporarily). soil stability is enhanced by using a stiff concrete mixture called Shotcrete sprayed directly from a hose onto the soil shortly after the soil is excavated. The hardened concrete reinforces the slope and protects against erosion. Shoring: Shoring Types – Slurry Wall Slurry Wall: A more complex method of constructing a complete, steel-reinforced, concrete wall in the ground which can be many stories below the surface. This occurs before excavation takes place. It is a relatively expensive form of excavation support that is usually economical only if it becomes a part of the permanent foundation of the building. Excavation typically performed with a narrow clam shell bucket, operated by a crane that can reach greater depths than a common excavator. Shoring – Slurry Wall Shoring: Bracing and Anchoring Bracing Methods: Cross Lot Bracing temporary steel wide-flange columns that are driven into the earth at points where braces will cross. As the earth is excavated down around the shoring and the columns, tiers of horizontal bracing usually of steel are added. Rakers Sloped braces to push back against the shoring used when the excavation is too wide for Crosslot bracing. Tiebacks Anchors driven through the shoring into the soil behind Steel cables or rods are inserted into holes, grouted to anchor them in place, and stretched tight with hydraulic jacks before they are fastened used instead of bracing to support the shoring while maintaining a fully open excavation. Shoring – Bracing and Anchoring Bracing Methods: Rakers are used when the excavation is too wide for Crosslot bracing. Tiebacks can be used instead of bracing to support the shoring while maintaining a fully open excavation. Steel cables or rods are inserted into holes, grouted to anchor them in place, and stretched tight with hydraulic jacks before they are fastened. Shoring – Bracing and Anchoring Pile & Shoring Summary Prepare a Table of the different Pile & Shoring types: Pile Types Table Pile Type Picture Typical Length Install Method Misc. (Soil Pros Cons Types/Strength) Timber Next Shoring Types Table Shoring Type Typical Length Install Method Misc. (Soil Types/Strength) Pros Cons Pictu re Sheet Piling Next Chapter 2 Reading Read pages 55-65 References/Sources E. Allan, J. Iano, Fundamentals of Building Construction – Materials and Methods, 6th Edition. Hoboken, New Jersey: John Wiley & Sons, 2014, pp. 1-659. Module 2: Foundations Waterproofing and Retaining Walls Foundations Learning Objectives: 1. Describe the different loads acting on foundations. 2. Describe the effect of soil type on foundation design and methods of subsurface exploration and soil testing. 3. List different types of foundations with their characteristics. 4. Describe methods of waterproofing and drainage of foundations. 5. State the factors affecting the foundation design. Waterproofing Methods of Waterproofing & Drainage 2 fundamental approaches to waterproofing: Waterproof Membranes: resist the passage of water even under the more demanding conditions of hydrostatic pressure Drainage Systems typically consists of a combination of: porous rock backfill material (drainage rock) drainage mat, perforated drain piping. Waterproofing: Overview 4 primary types: Sheet Applied Membrane: Plastic, Asphaltic Material, Rubber Liquid Applied Membrane: Polymer Cementitious Plaster: Cement and Polymer Bentonite Clay Membrane Waterproofing: Sheet Applied Membranes Sheet Applied Membranes are typically made of: Plastic Asphaltic Material Rubber generally be applied to the outside of the wall to be supported against water pressure by the wall. Requires inspection with extreme care, as the outside wall cannot be reached after the foundation wall is backfilled with soil. Video: Sheet Membrane Application Waterproofing: Liquid Applied Membranes Spray Applied Membranes: Polymer Material Applied by spray or roller as vicious liquids and allowed to cure in place. Seamless and easy to form around intricate shapes. Subject to inconsistent application thickness or poor curing depending on the ambient conditions and applicator skill/awareness. Video: Liquid Applied Waterproofing Waterproofing: Cementitious Plaster Cementitious Plasters: Cement + Waterproof Polymer An example is BASF - MasterSeal: a crystalline waterproofing product that expands to fill holes Can be used either inside or outside the foundation preference for the inside for inspection reasons. Cementitious Waterproofing Waterproofing: Bentonite Clays Bentonite Clay Membranes: Made from naturally occurring sodium bentonite which is a highly expansive clay. Most often applied as preformed sheets consisting of a dry clay sandwich within corrugated cardboard, geotextile fabric, or plastic sheets When bentonite is contacted by moisture, it swells to several times its dry volume and forms a barrier that in impervious. Bentonite Waterproofing Waterproofing Examples Waterproofing Examples Drainage Drainage of Foundations Typically used in areas with high water table or high precipitation. Usually more effective than water proofing. Uses a combination of drainage gravel, drainage mat, and perforated piping located around the perimeter of the foundation wall and footing. Drainage of Foundations: Drainage Mat is a manufactured sheet product that fastens to the outside of the foundation wall and allows water to pass through and drain through the mat to perforated piping below. Perforated Piping is located on the outside of the footing and is typically 4-6” in diameter. Piping can drain to a municipal storm sewer, sump pit, or swale if a sloped site. Methods of Drainage Section of Foundation Drainage Drainage Best Practices Perforated Pipe must be laid so that the perforations are facing downward so that the groundwater enters the pipe at the lowest possible elevation. Filter fabric can be wrapped around the pipe as well to ensure no soil enters the pipe in the case there are multi perforations around the perimeter of the pipe. Drainage Best Practices Water stops are also beneficial in preventing water from entering concrete between foundation pours. In some instances foundation drainage is used along with a bitumen based roll-on or spray-on damp proofing up to the grade elevation. Only good for moisture resistance however, not water resistance. Example of a Rubber Waterstop Example of a Clay Waterstop Dewatering Construction Sites Some construction sites require removal of standing water from precipitation or groundwater. This is done by means of dewatering. Most commonly done by pumping water out of low points in the excavation pit called sumps. Dewatering Construction Sites In cases where the infiltration of ground water is high, well points are used to depress the water table adjacent to the open excavation. It should be noted that sumps are also used permanently in residential and commercial construction, and are usually located inside the building in the basement. Dewatering and Sump Pits Factors affecting Foundation Design Structural Requirements Soil Conditions Weather and Environmental Conditions Foundation Design Ground Water Estate Technical Constraints Economical Issues Retaining Walls A retaining wall holds back soil where an abrupt change in elevation occurs. The wall must resist earth and groundwater pressures that push on the upward side of the wall. Retaining walls above 1.2 metres in height (bottom of footing to top of wall) are typically required to be designed by a Structural or Geotechnical Engineer. Retaining Walls Retaining walls can be made of preservative treated wood, masonry, precast concrete, or site cast concrete. Design of a retaining wall must consider: Height of wall Underlying soil conditions Earth and hydrostatic pressures acting on the wall Example of Retaining Walls Retaining Walls – Modes of Failure Alternatives to Retaining Walls One type of alternative to a retaining wall is a Earth Reinforced wall or Mechanically Stabilized Earth (MSE) wall. Structural fill is compacted in layers between strips or mesh layers of galvanized metal or other materials which stabilize the soil. Alternatives to Retaining Walls Gabion walls are also another alternative in which corrosion resistant wire baskets are filled with boulders or cobbles and stacked on one another. MSE walls and Gabion walls are typically used in applications where the height of the wall is higher than normal and also subject to higher earth pressures. Design Considerations: Proper drainage of groundwater behind the retaining wall must be taken into account. Installing perforated pipe and drainage gravel as discussed earlier, will help reduce the hydrostatic pressures that will be placed on the upward side of the wall. Design Considerations: Proper compaction of the soil or gravel behind the wall and the thickness of lifts of soil placed will impact the amount of settlement. This is very important in the cases where vehicular traffic or any type of loadings are exerted near the face of the wall. Reinforced Earth Walls Grade Beams A reinforced concrete wall designed to transfer building loads to deep foundations such as piles or caissons. SAIT Thomas Riley Grade Beam Void Forms Void forms are placed under grade beams to allow for expansive soils such as clay to expand without pushing on the underside of grade beam. Typically made of Expanded Polystyrene (EPS) Void Forms Source: www.lifeofanarchitect.com Module 3 - Summary of Key Terms 15. Soldier Beams/Lagging Uniform Settlement 16. Piles Angle of Repose 17. Caissons Coarse grained soils 18. Perimeter Footing Differential Settlement 19. End Bearing Pile Fine grained soils 20. Column Footing USCS Test Pit 21. Friction Pile Boreholes 22. Sheet Piling Liquid Limit 23. Pile Cap Plastic Limit 24. Shotcrete Superstructure 25. Foundation Substructure Waterproofing Shallow Foundations 26. Foundation Drainage Deep Foundations 27. Gabion Wall 28. MSE Wall Chapter 2 Reading Read Pages 66-78 References/Sources E. Allan, J. Iano, Fundamentals of Building Construction – Materials and Methods, 6th Edition. Hoboken, New Jersey: John Wiley & Sons, 2014, pp. 1- 659. Module 3 - Wood Part 1 – Wood Harvesting and Manufacturing Wood Construction Module 3 Learning Objectives: Discuss the types of trees found in Canada and how they are harvested Describe the material properties of wood and wood products Describe the types of Engineering Wood products available Compare the properties of light-frame and heavy-timber construction Introduction Wood in Construction In Canada, Wood is used extensively in the construction industry. Residential Construction Architectural Details Unique Structural Members WHY? Treed Land In Canada Source: www.nrcan.gc.ca Treed Land In Canada About 90% of Canada’s forests are located on provincial and territorial Crown Lands. Crown Land = Land owned by the government Provincial and Territorial governments are therefore responsible for forest management. This is done through Forestry Management Agreements (FMA’s) Leases to Logging Companies The Allowable Annual Cut on a particular area of crown land is specified by the government. This includes both the annual level of harvest and the minimum forest age at the time of harvest. Source: www.nrcan.gc.ca Treed Land In Canada In 2016, about 155 million cubic metres (m3) of timber was harvested in Canada. This equates to only 0.3% of the total standing wood volume in Canada. Provincial and Territorial Lands harvested for commercial timber must be regenerated either naturally or by planting and seeding, or by a combination of these methods. Each province and territory has its own regeneration standards and regulations. Species composition, density and stocking levels, and distribution of various forest types are considered. Source: www.nrcan.gc.ca Softwoods and Hardwoods Softwoods come from Coniferous Trees: Relatively fast growing Needle-like leaves Evergreen trees Cone-bearing Examples in Canada include Spruce, Pine, Fir, Cedar Source: www.wikimedia.org Source: Just Fun Facts Softwoods and Hardwoods Hardwoods come from Deciduous Trees: Broad leaved Change color based on season Shed their leaves in autumn Examples in Canada are Oak, Maple, Birch, Apple, Cherry Aspen, Poplar Source: www.wikimedia.org Softwoods and Hardwoods Softwoods are (generally) softer, less dense and faster growing than hardwoods. Douglas Fir which is a softwood, is denser than some hardwoods Source: www.wikimedia.org Forest Composition In Canada Source: www.nrcan.gc.ca Forest Regions of Canada Source: www.nrcan.gc.ca Forest Regions of Canada Source: www.nrcan.gc.ca Softwoods and Hardwoods Description Softwood Hardwood Appearance Needle shaped leaves Broad leaves Wood Colour Lighter Darker Growth Rate High growth rate Lower growth rate Density Lower density Higher density Cost Less expensive More expensive Fire Resistance Poor Good Uses Home Building, Finishing Trim Flooring, Furniture, Cabinets Structural Strength of Wood Strength is a dependent upon the wood species, the wood grade and the direction of the applied force with respect to the grain of the wood Wood is much stronger parallel to (along) the grain than perpendicular to (across) the grain Structural Strength of Wood Variations between different grades and species of softwood Structural Strength of Wood Compared with other building materials: Factors affecting strength Species of tree The temperature and moisture conditions Size and shape of the piece Application of fire-retardant treatments Wood Terminology: Crown Land Seasoning Boreal Forest Surfacing Montane Forest Grading Coniferous FSC/SFI Deciduous Nominal Dimensions Lumber Actual Dimensions Timber Growth Defects Milling Manufacture Defects For Next Class! Read Chapter 3, pages 84-103 References/Sources E. Allan, J. Iano, Fundamentals of Building Construction – Materials and Methods, 6th Edition. Hoboken, New Jersey: John Wiley & Sons, 2014, pp. 1-659. Module 3 - Wood Wood Manufacturing Lumber Milling The production procedure for lumber starts with the felling of the trees and proceeds as listed: Felling – cutting down the tree and removing the branches Milling – logs are hauled to the sawmill where they are soaked or steamed Sawing Sawing – logs are sawn/sliced into rough dimensional lumber Seasoning – rough lumber is dried to specific moisture content Surfacing – lumber is planed to precision dimensions Seasoning Grading – finished lumber is assessed for quality Surfacing Grading Milling – Early 1900’s Transportation of the logs to the mill Felling Redwood Trees Milling – Present Day Now… Sawing Logs are cut into different sizes depending upon the required application. The bark is stripped from the log The log is passed repeatedly through a saw (a band saw or a circular saw) to produce slabs of lumber The slabs are carried to smaller saws where they are reduced to desired widths that will make most efficient use of the lumber The lumber is rough-textured (or rough-sawn) at this stage and may have slight variations in dimension Sawing Plainsawing produces the most lumber per log and better structural properties per piece of lumber Plain Sawing vs Quarter Sawing Seasoning The moisture content (MC) of wood is the weight of water in the wood as a percentage of the weight of the dry wood Moisture content of growing wood varies from 30% to 200% Reducing the moisture content of lumber causes it to shrink and to gain strength and stiffness Seasoning The moisture content is reduced by air drying or by kiln drying. Most shrinkage is perpendicular to the grain. A piece of lumber will shrink more in width than in length. Lumber that has not been seasoned is known as green lumber Seasoning Kiln drying (KD) is quicker than air drying, taking a few days, and produces fewer distortions and a more uniform quality. It is more expensive. Air drying can take several weeks. Measuring moisture content inside a kiln. Seasoning Standard framing lumber is seasoned to 19% moisture content at the mill Small kiln Stacked lumber for air-drying Heat Treatment The purpose of heat treating lumber is to sterilize the wood so that it eradicates any living organisms in the wood. The internal core of the wood must be heated to 56˚C for 30 minutes. Typically heat treated (HT) lumber may look darker or stained due to the reaction of the sap during the heating process. HT wood has a lower moisture content and is denser and stronger. Surfacing In this process, rough-sawn lumber is put through a planer to make it smooth and more dimensionally precise Surfacing Lumber that is smooth on all four sides is known as S4S (smooth four sides) S2S is lumber that is smooth on two sides; S1S2E is smooth on one side and two edges Surfacing is done by high-speed automatic machines with sharp blades that plane the surface of the piece and round the corners smoothly. Surfacing In order to remove some of the distortion caused by the seasoning process, surfacing is usually performed after seasoning. Then the grade stamp seen on the lumber shows S-DRY (indicating a moisture content less than 19% when surfaced) For some framing lumber, surfacing is performed before seasoning when the lumber is still green. The grade stamp then shows S-GRN (indicating a moisture content more than 19% when surfaced) Grading Grading (assessing) is done either by a machine (computer) or by trained inspectors. Grading is either Structural or Appearance Structural Grading rates the strength and stiffness properties of the lumber Appearance Grading used to rank the visual qualities of lumber such as flooring, trim, or other non-structural visible uses Grading Grades Some common grades with their clear wood requirements: Structural Grade Requirements Select > 80% Clear wood #1 Structural > 75% Clear wood #2 Structural > 66% Clear wood #3 Structural > 50% Clear wood Construction Grade > 57% Clear wood Standard Grade > 43% Clear wood Utility Grade > 29% Clear wood Moisture Content (MC) Moisture content designations on grade stamps specify the condition of seasoning at the time of surfacing: MC15 or KD15 specify a maximum of 15% moisture content S-DRY, KD or KD-HT specify a maximum of 19% moisture content S-GRN or HT specify more than 19% moisture content Note that these designations refer to moisture content when the lumber is shipped from the mill On-site storage of lumber will affect its moisture content Grading Stamp Grading Association: Alberta Forest Products Association (AFPA) 27 identifies the sawmill S-P-F indicates the species (spruce, pine, fir) Moisture content < 19% when surfaced 2 is the grade of lumber Slicing Methods Hancock Lumber Manufacturing Process Which pattern of sawing was demonstrated in the video? Certified Lumber (Eco Stamps) Lumber may have ‘Eco-stamps’ which indicate that they have been harvested sustainably. The Forest Stewardship Council (FSC) certifies lumber that has been grown, harvested and milled in an sustainable manner. Forest Stewardship Council (FSC) Global, not-for-profit organization Promotes responsible forest management worldwide Widely recognized Includes social, economic and ecological principles Forest Stewardship Council (FSC) Addresses criteria related to international treaties, land ownership rights and responsibilities, rights of indigenous peoples, workers’ rights, etc… Seeks to ensure forest management that prevents overharvesting and preserves natural resources and biological diversity Demonstrates Corporate Social Responsibility (CSR) Sustainable Forestry Initiative (SFI) Another type of certification Has the same intent as the Forest Stewardship Council Fully independent accreditation for forestry practices in the USA and Canada Formed in conjunction and support with the American Forest and Paper Association (AF&PA) Governing Bodies Forest Products Association of Canada http://www.fpac.ca Western Wood Products Association http://www.wwpa.org/ National Lumber Grades Authority http://nlga.org/ Alberta Forest Products Association https://www.albertaforestproducts.ca/ DIMENSIONAL LUMBER Lumber Lumber Lumber is defined as lengths of ‘squared’ wood for use in construction Boards Lumber less than 2 inches thick (nominal size) are known as boards Lumber Dimensional Lumber: Lumber between 2 and 4 inches thick (nominal size) Lumber Timbers Lumber greater than 5 inches thick (nominal size) Sizes: Nominal vs. Actual Nominal Size: the ‘named’ size of the board Ex. 2x4, 2x8, 4x4, 5/4 x 6 Lumber is rough sawn from a log, before it has been seasoned and surfaced, into dimensions that are approximately the same as the nominal size Ex. before seasoning and surfacing, a 2x4 is approximately 2’’ thick and 4” wide (50mm x 100mm) Actual Size: the measured size of the finished product. After the board has been seasoned and surfaced, its size is been reduced A seasoned, surfaced 2x4 has an actual size of 1.5” thick and 3.5” wide (38 mm x 89 mm) Lumber Defects Knots Knotholes Caused by growth characteristics Decay Insect Damage Lumber Defects Crooking Splits Bowing Arising from manufacturing Distortions characteristics Cupping Wane Twisting Knots and Knot Holes Decay A wood-decay fungus is any species of fungus that digests moist wood, causing it to rot. Some species of wood-decay fungi attack dead wood, such as brown rot shown here. Splits Checking Wane Wane is an irregular rounding of the edges or faces that is caused by sawing pieces too close to the perimeter of the log Distortions Wood Terminology: Crown Land Seasoning Boreal Forest Surfacing Montane Forest Grading Coniferous FSC/SFI Deciduous Nominal Dimensions Lumber Actual Dimensions Timber Growth Defects Milling Manufacture Defects For Next Class! Read Chapter 3, pages 84-103 References/Sources E. Allan, J. Iano, Fundamentals of Building Construction – Materials and Methods, 6th Edition. Hoboken, New Jersey: John Wiley & Sons, 2014, pp. 1-659. Module 3 - Wood Part 3 – Wood Treatment and Fasteners Wood Construction Learning Objectives: 1. Describe the material properties of wood and wood products 2. List various types of wood construction materials 3. Compare the properties of light-frame and heavy-timber construction Wood Treatments Chemical treatments in lumber products are used to counteract two major weaknesses of wood: combustibility susceptibility decay and insects. Source: www.preservedwood.org Types of Wood Treatments Fire-Retardant Treatment (FRT) Lumber is placed in a vessel and injecting chemical salts under high pressure which greatly reduce its combustibility when used in home construction. Preservative-Treated (PT) Similar pressure treatment process as FRT however preservative chemicals are used instead of salts are used. This increases resistance to decay through exposure to moisture and/or insects. Wood Treatments - FRT PKBoard OSB sheathing, coated at the factory with a fire retardant. When exposed to flames, PKboard will produce a layer of char that insulates the panel and reduces the ability of the fire to spread www.pinkshield.ca Wood Treatments - PT Creosote: oily derivative in coal used in Engineering structures. However due to it’s smell and toxicity, it is not used in building construction. Chromated Copper Arsenate (CCA) used for many decades. Concerns over its toxicity has phased it out of most residential building construction however it is still used in permanent wood foundations. Copper Boron Azole (CBA) Today, most preservatives rely on high concentrations of copper solutions for their preservative properties. Georgia Pacific - PT Lumber Plant Wood Treatments - PWF Permanent Wood Foundations (PWF) an alternative to the more common concrete foundation, which requires CCA preservative treated lumber and plywood Preserved wood may need special fasteners (galvanized or stainless) http://www.abarent.net/wp-content/uploads/2013/01/1.-Preserved-wood-foundation-PWFinterior-reinforcement-wall-constructed.jpg Natural Decay-Resistant Woods The heartwood of some species of wood is naturally resistant to decay and insects. As the sapwood of these species is not resistant, an “All Heart” grade should be specified. The International Building Code (IBC) recognizes redwood, cedar, black locust, and black walnut as decay-resistant species. Redwood and Eastern red cedar are recognized as termite-resistant species. Durable Building Tips Construct and maintain a building so that its components are kept dry. Keep wood away from soil by using concrete piers or foundations. Ventilate attics and crawlspaces to remove moisture Ensure finished building envelope sheds water properly and keeps it outside. Use vapor retarders properly in conjunction with insulation to help prevent condensation. Wood Fasteners Fasteners are often considered the weak link in wood construction. The interlocking timber connections of the past were weaker than the connecting members because of the volume of wood removed. Even with modern nails, screws, and bolts it is usually impossible to develop full strength of the members being joined. Types of Fasteners - Nails Nails sharp-pointed metal pins that are driven into wood with a hammer or a mechanical gun such as a pneumatic Framing Nailer. There are many different types of nails. Common nail and Box nail are used in light frame construction. Casing nails and Finish nails are used in finished woodwork. “Bright” nails are made of plain uncoated steel. Nails exposed to weather should be corrosion resistant such as zinc-coated, aluminum, or stainless steel. Common Nail Types Methods of Fastening Nails Types of Fasteners - Screws spiral-threaded fasteners installed by a turning action where the threads draw the screw tightly into the material being fastened. used in cabinetry, wide plank flooring, and finish carpentry. typically cost more than nails and take longer to install, however they can be inserted with better precision, greater clamping force, and have greater holding power. made of steel that may or may not have a variety of metallic platings (zinc, bronze, brass) may require that a pilot hole be drilled in the lumber first, to avoid splitting. Types of Fasteners - Bolts Bolts are used mainly for structural connections in heavy timber framing and in light framing for fastening beams and ledgers. Typically they are installed into pre-drilled holes with a wrench that tightens the nut opposite the bolt head. Washers are inserted under the head of the bolt to distribute the clamping force to a greater area of the wood and to minimize crushing of the wood fibers. Fasteners - Bolts Fasteners - Toothed Plate Connections Toothed Plate Connectors Used in Truss construction since the 1950s, when they revolutionized the truss industry Require installation with a specially designed press or roller system, requiring a pressure of 7 MPa (100 psi) Cannot be re-installed on-site with a hammer! Fasteners – Joist Hangers Joist Hangers used to make strong connections in floor framing wherever floor and roofing members bear on each other (usually) at right angles They are also frequently used in exterior deck construction They require special, shorter, nails which go through holes in the hanger Fasteners – Joist Hangers Engineered Wood Study Chart Full Name Short Name Type of Wood Product Typical Use Manufacture Glue Laminated Woods Plywood Oriented Strand Board Medium Density Fiberboard Laminated Veneer Lumber Parallel Strand Lumber Laminated Strand Lumber Chapter 3 Reading Read pages 118-125 References/Sources E. Allan, J. Iano, Fundamentals of Building Construction – Materials and Methods, 6th Edition. Hoboken, New Jersey: John Wiley & Sons, 2014, pp. 1-659. Module 3 - Wood Light Framing Light Frame Construction Light Frame Construction Developed in the first half of the 19th century when builders recognized the closely spaced vertical members used to infill the walls of a heavy timber building frame where in themselves strong enough to handle the building loads. Two technological breakthroughs accelerated the growth of light frame construction: Boards and small framing members had recently become inexpensive because of the advent of the water-powered sawmill Machine-made nails had become remarkably cheap compared to hand-forged nails that preceded them. Balloon Frame Construction The Balloon Frame was the earliest wood framing system to be constructed exclusively of slender closely spaced wooden members which included joists, studs, and rafters. The balloon frame used full length studs that ran continuously for two stories from foundation to roof. It became apparent that these members were too long to erect efficiently. As there was often no break between floors, hollow spaces between studs acted as chimneys during a fire and it would blaze rapidly to the upper floor. Balloon Frame Construction Click image to play video Platform Frame Construction The Platform Frame was developed through multiple iterations of improvements on the original balloon frame. A platform frame can be explained through the following steps and procedures: 1st Floor platform is built Loadbearing walls are erected on them 2nd floor platform is built on the walls 2nd set of walls are built upon the 2nd floor Attic and roof are then built upon 2nd set of walls Platform Frame Construction Where it came from…. Where it’s going… Source: HomeTips Platform vs Balloon Frame Example of Light Frame Construction Example of Light Frame Construction Advantages Advantages of Light Frame construction: Buildings are easily and quickly constructed with a minimal amount of investment in tools. Among the most versatile of building systems. Many shapes and sizes can be constructed from light frame construction. It assimilates very well to changes in technology such as central heating, air conditioning, lighting, plumbing, etc. Building codes for light frame construction make light framed houses easy to build without Engineered designs. Image Source: ResearchGate Image Source: EcoHome Disadvantages Disadvantages of Light Frame construction: Buildings are very susceptible to fire damage When exposed to dampness or moisture, light wood construction will decay if not properly treated. Changes in humidity will case wood to expand and contract which typically results in cracks in plaster, shifting door frames, and buckling floors. Not aesthetically pleasing. As such, light frame construction is seldom left exposed. Image Source: KnowYourMeme Foundation Types In North America, most residential and small commercial wood light frame buildings are built on: shallow concrete foundations consisting of spread footings, 8’ basement walls, 4’ frost walls, or slabs on grade. Another type of foundation type is a pier and beam foundation: concrete piers poured on a shallow footing which extend 12-18” above grade and support the main floor beams The type of foundation to be used for light frame construction will depend on the geographic location, local soil conditions, and the size of the building which the foundation will support. Concrete Wall Foundation Concrete Wall Foundation Pier and Beam Foundation Source: http://themusingsofthebigredcar.com Name the Frame Roof sheathing Name the Frame Rafter Fascia Cap plate Top plate Stud Floor sheathing Wall sheathing Floor joist Rim joist Bottom plate Plan View Section View Elevation View Detail View Framing Plans Carpenters work from a set of framing plans Framing member sizes can usually be determined from the building code although more complex building may need to be designed by an engineer Exterior elevations contained in the plans show the outside faces of the building Building sections show a cut completely through the building, showing the relationship between various floor levels and roof planes Framing Procedure Telepost and Beam Many residential building have a beam running along the length of the building, supported at required intervals by adjustable length posts. The beam may be of steel, or a built-up beam of several pieces of dimension lumber or an engineered wood product such as LVL Telepost and Beam Sill Plate A wooden sill plate is attached to the top of the foundation using anchor bolts that were set in the foundation wall as the concrete was poured Ladder Sill A ladder sill is often used instead of a sill plate. The ladder is installed within the formwork. When the forms are stripped, the ladder remains. The floor joists can then be fastened to the wood. Sill Plate and Floor Framing The floor is anchored to the foundation via the sill-plate Sill Plate and Floor Framing Source: CMHC-Canadian Wood Frame Construction Floor Framing Floor Framing The beam is set into a beam pocket in the concrete foundation wall(A) Notice the direction of the joists at the cantilever (B) Notice the double joist at C header joist trimmer joist Floor Framing When the joists have been laid out, the floor frame is checked to make sure that it is ‘square’ (i.e. the corners are 90 degrees) For rectangular floor shapes, this is done by measuring the diagonals (both diagonals should be the same length) Floor Sheathing Floor sheathing is installed with its stronger (8’) edge across (perpendicular) to the joists. The sheathing has a ‘tongue’ along one edge and a ‘groove’ along the opposite edge this allows rows of sheathing lock together (where they are unsupported by joists). The 4’ edge of the sheathing has no tongue or groove and must be supported by a floor joist. Joints in adjacent rows are staggered. Floor Sheathing Source: CMHC-Canadian Wood Frame Construction Chapter 4 & 5 Reading Read pages 140-153 Read pages 172-195 References/Sources E. Allan, J. Iano, Fundamentals of Building Construction – Materials and Methods, 6th Edition. Hoboken, New Jersey: John Wiley & Sons, 2014, pp. 1-659. Module 3 - Wood Part 5 – Light Framing Construction Wood Construction Learning Objectives: Describe the material properties of wood and wood products List various types of wood construction materials Compare the properties of light-frame and heavy-timber construction Wall System A typical light frame wall system is made up of 3 primary components: Studs Plates Sheathing Additional components are used to accommodate openings in wall systems. Lintels Jack/King Studs Cripple Studs Sills Corner Posts Wall Framing Components Wall System - Studs Studs Closely spaced vertical lumber distributes loads from the floors/roof above to the floor and foundation below. Typical 2x6 (Exterior) and 2x4 (Interior) Typical spacing is 24” o.c. or 16” o.c. o.c. = on centre Stud sizing and spacing will vary: Location (exterior/interior) Load bearing / Non-load bearing Height of wall required Wall System - Plates Plates Dimensional lumber running horizontally the length of the wall above and below the studs. Help maintain even stud spacing and allow the even transfer of loads to the studs Typical 3 Plate System: Bottom Plate Top Plate Cap Plate With no cap plate, joists or rafters above must line up directly with the studs below Cap Plate helps interlock walls Wall System - Sheathing Sheathing A panelized product (plywood or OSB) placed on the outside of the studs/plates. Adds rigidity and stability to structure Serves as a base for the cladding/siding Wall System Lintels A simple beam that spans over doors and windows Loads from above are transferred to Jack Studs Depth of the lintel determined by the load supported and the clear span (width) of the opening a.k.a. Header lintel Typical Materials: 2 pieces of 2x10 Lumber (Nail Laminated) Engineered Wood (LVL) Wall System Jack Stud A Jack Stud or Trimmer is a shorter stud that transfers the load from a lintel above to the floor below. Minimum 1½” overlap between stud and lintel Must be continuous from the bottom plate to the lintel Jack Studs King Stud King Studs A King Stud is a regular stud that is fastened to the Jack Stud on either side of the entrance Wall System Cripple Studs A Cripple Stud is a short stud that is above or below a window, or above a door. Cripple studs maintain consistent stud spacing throughout the wall system and provide a structure for the sheathing to fasten to. Wall System Sills A Sill is the bottom horizontal part of a window. Exterior portion typically slopes away from the house. Corner Posts Tie the walls together Provide support for sheathing (exterior) and drywall (interior) Allow space for insulation Most common is the L-Post (3-Post Corner) Load Bearing Studs Note the extra studs beneath a loadbearing wall which is indicated by the double floor joist National Building Code Loads National Building Code of Canada 2005, Table 9.23.10.1 Roof Framing There are 2 methods for installing a light wood frame roof: Stick Framed Roof Individual (sloped) rafters each connected to a top beam. The beam, or the ridge, is the central part of the structure, as all the framing must be connected to it. Truss Roof System Engineered system composed of several individual members (chords and webs) that are either in compression or tension. Most often used with gable and hip roofs. They are made in a fabrication facility prior to installation and usually installed on site with truck booms or cranes. Stick Frame - Gable Style Roof Source: CMHC-Canadian Wood Frame Construction Stick Frame - Hip Style Roof Source: CMHC-Canadian Wood Frame Construction Hips & Valleys Source: Allen, Fundamentals of Building Construction: Materials and Methods, 6 th Ed. Overhang & Lookouts Source: Allen, Fundamentals of Building Construction: Materials and Methods, 6 th Ed. Members of a Truss Source: structuralhelp.com Gable Truss Source: timber-trusses.com Hip Truss Source: timber-trusses.com Stick Frame - Pros & Cons Advantages: More space under the roof for storage or attic space More easily replaced or renovated Easier to trace roof leaks