SIRI Whitepaper (Assessment Matrix, AM) PDF
Document Details
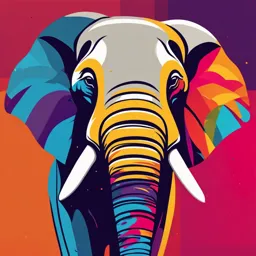
Uploaded by ExquisiteDogwood
2020
Dr Beh Swan Gin
Tags
Related
- Advanced Manufacturing Process (ME F315) - PDF
- Unit 1 Elements of Industry 4.0 - RV College of Engineering PDF
- Frameworks of Industry 4.0 PDF
- Introduction to Manufacturing Systems PDF
- TDF Zusammenfassung WiSe 2021/22 Industrielle Revolution (PDF)
- Digital Manufacturing and Industry 4.0 Assignment 2 PDF
Summary
This document is a whitepaper created by the Singapore Economic Development Board (EDB) describing the Smart Industry Readiness Index (SIRI). It introduces the key concepts of Industry 4.0 transformation.
Full Transcript
THE SMART INDUSTRY READINESS INDEX Catalysing the transformation of manufacturing At a Glance Foreword Executive Summary Introduction Industry 4.0 is transforming manufacturing Manufacturing: A Key Pillar of Singapore’s Economy A national imperative for growth and transformation The Smart Indus...
THE SMART INDUSTRY READINESS INDEX Catalysing the transformation of manufacturing At a Glance Foreword Executive Summary Introduction Industry 4.0 is transforming manufacturing Manufacturing: A Key Pillar of Singapore’s Economy A national imperative for growth and transformation The Smart Industry Readiness Framework The 3 building blocks, 8 pillars and 16 dimensions The LEAD Framework A four-step process towards transformation The Way Forward Businesses must start taking decisive action today Assessment Matrix: The 16 Dimensions Acknowledgements References Glossary Singapore Economic Development Board (EDB), a government agency under the Ministry of Trade and Industry, is responsible for strategies that enhance Singapore’s position as a global centre for business, innovation, and talent. We undertake investment promotion and industry development, and work with international businesses, both foreign and local, by providing information, connection to partners and access to government incentives for their investments. Our mission is to create sustainable economic growth, with vibrant business and good job opportunities for Singapore. For more information, please visit www.edb.gov.sg. Copyright © 2020 Singapore Economic Development Board. All rights reserved. 1 The Smart Industry Readiness Index Foreword Big data, robotics, and additive manufacturing are some of the technologies that are driving the convergence of digital and physical in every industrial sector, from production to logistics, from aerospace to utilities. This convergence, commonly referred to as Industry 4.0, holds immense opportunities for Singapore. It will redefine the nature of manufacturing. Instead of standalone factories, Industry 4.0 will create dense and interconnected networks of facilities, suppliers, partners, and customers. It will create new jobs of tomorrow, where man and machine work together to manage smart facilities and global supply chains. While companies recognise the opportunities, many do not know where and how to start. The pace of transformation is also uneven across industries. The Smart Industry Readiness Index seeks to provide a common framework for all companies to participate in, and benefit from, this transformation. Developed by EDB in partnership with TÜV SÜD and validated by an advisory panel of experts, the Smart Industry Readiness Index will help companies determine where to start and how to scale and sustain their Industry 4.0 efforts. More importantly, we hope that the Smart Industry Readiness Index will be a catalyst for companies, industries, workers, and the Government to come together to prepare for and create Singapore’s future in this new era of Advanced Manufacturing. Dr Beh Swan Gin Chairman Singapore Economic Development Board Catalysing the transformation of manufacturing 2 Executive Summary Manufacturing is on the brink of a new age — arising from the convergence of the physical and digital worlds. This new paradigm, commonly referred to as Industry 4.0, has the power to transform how products are created, how supply chains are managed, and how value chains are defined. For companies around the world, Industry 4.0 presents an opportunity to gain new competitive advantages through greater productivity, agility, and speed. For Singapore in particular, Industry 4.0 creates a window of opportunity to cement its role as a global manufacturing hub and to transform its manufacturing base. The Smart Industry Readiness Index Industry 4.0 is now gathering momentum globally. The SIRI Framework According to the 2016 Industry 4.0 global survey conducted by PwC, nearly three-quarters of The SIRI Framework consists of three layers. The respondents foresaw a high level of digitalisation in topmost layer is made up of the three fundamental their companies over the next five years. However, in building blocks of Industry 4.0: Process, Technology, McKinsey’s 2017 digital manufacturing global expert and Organisation. Underpinning the building blocks survey, companies also pointed out that the lack of a are eight pillars, which represent critical aspects that clear vision, strategy, and a systematic roadmap were companies must focus on to become future-ready the biggest challenges hindering Industry 4.0 adoption. organisations. The third and final layer comprises 16 dimensions that companies should reference when The Smart Industry Readiness Index (SIRI) is a evaluating the current maturity levels of their facilities. deliberate attempt to address these challenges. Created in partnership with global testing, inspection, The Assessment Matrix and certification company TÜV SÜD and validated by an advisory panel of industry and academic experts, Referencing the 16 dimensions in the SIRI Framework, SIRI comprises a suite of frameworks and tools to the Assessment Matrix is the world’s first Industry help manufacturers — regardless of size and industry 4.0 self-diagnostic tool aimed at helping companies — start, scale, and sustain their manufacturing worldwide evaluate the current state of their factories transformation journeys. This white paper introduces and plants. It is designed to strike a balance between three frameworks and tools: the SIRI Framework, the technical rigour and usability. LEAD Framework, and the Assessment Matrix tool. Smart Industry Readiness Index Process Technology Organisation Product Talent Structure & Operations Supply Chain Automation Connectivity Intelligence Lifecycle Readiness Management 1 2 3 4 7 10 13 15 Shop Floor Workforce Learning Inter- and Intra- & Company 5 8 11 Development Collaboration Integrated Vertical Horizontal Product Enterprise Integration Integration 14 16 Lifecycle 6 9 12 Leadership Strategy & The Smart Industry Readiness Index Competency Governance Facility Figure 1: The Smart Industry Readiness Index (SIRI) Framework 3 The Smart Industry Readiness Index The LEAD Framework Transforming and upgrading a manufacturing facility is not a one-off exercise. Rather, it is a continuous and iterative process. This is encapsulated in the LEAD framework — a circular, continuous four-step process that all manufacturers can adopt in their approach towards Industry 4.0 transformation. Evaluate the current Industry 4.0 maturity levels of existing facilities Figure 2: The LEAD Framework 1 Learn the key concepts of Industry 4.0 and build a common language for alignment: SIRI enables this by offering frameworks that help increase the level of understanding of key Industry 4.0 concepts and establishing a common language among individuals, business units, and partners. 2 Evaluate the current Industry 4.0 maturity levels of existing facilities: With a common understanding of Industry 4.0, companies can use the Assessment Matrix to assess the current state of their facilities. Through each dimension, companies can examine their current processes, systems, and structures and place themselves in one of six possible bands. It should be noted that while all dimensions should be taken into account, the relative importance of each one will vary depending on the company’s needs and the industry it is operating in. 3 Architect a comprehensive transformation strategy and implementation roadmap: The SIRI framework acts as a checklist to ensure that all the building blocks, pillars, and dimensions are formally considered. Additionally, the Assessment Matrix doubles as a step-by-step improvement guide, with the six bands within each dimension delineating the intermediate steps needed to progress to higher bands. This helps companies to identify high- impact initiatives and structure robust implementation roadmaps with clearly defined phases, targets, and timelines. 4 Deliver impact and sustain transformation initiatives: Once a company has developed its transformation roadmap, SIRI’s frameworks and tools also serve as a live blueprint that the company can use to measure and refine its Industry 4.0 initiatives over a multi-year period. The Way Forward Companies who seek to embrace Industry 4.0 often have different starting points. Regardless of where they start from or the industry they are in, all companies stand to benefit from Industry 4.0. SIRI offers a suite of practical and usable frameworks and tools for companies to determine where to start, how to scale, and what they could do to sustain growth. Catalysing the transformation of manufacturing 4 Introduction Industry 4.0 is transforming manufacturing The fourth industrial revolution is upon us. Although from scale to flexible production. With product life the first three industrial revolutions of mechanisation, cycles and supply chains digitalised across the value mass production, and computerisation have come to chain, companies can move beyond the mere provision define the world we live in today, the fourth industrial of products and equipment to offer new, disruptive revolution will usher in a new age of innovation and services and business models. Production, too, can transformation. This is characterised by the advent of transcend the factory environment, as manufacturing cyber-physical systems, arising from the convergence systems are vertically integrated with enterprise of the digital and physical worlds. processes and horizontally networked across the value chain. This integration allows companies to respond This new age, commonly known as Industry 4.0, to the needs of customers with greater efficiency, represents a paradigm shift for manufacturing on flexibility, and speed. multiple fronts. Once solely focused on the execution of pre-programmed logic, machines and devices are Collectively, these shifts will have a profound impact now part of intelligent, autonomous networks capable on companies and economies around the world. In the of communicating and interacting with one another. future, Industry 4.0 will create a world where processes Processes are no longer static; instead, they are are increasingly digitalised and integrated; where adaptive, self-corrective, and capable of responding to devices, machines, and systems can autonomously demands in real time. Rigid, centralised factory control optimise processes and manage operations; and where systems also give way to decentralised intelligence and humans and machines work together to create smart decision-making, reshaping the basis of competition facilities that are efficient, flexible, and adaptive. Customer Raw Materials Suppliers Inbound Manufacturing Outbound Sales and After-market Logistics Logistics Marketing Services Industry 3.0 Enterprise Level Operations Level Control & Supervision Level Field/Machine Level Production Process Figure 3: From Industry 3.0 to Industry 4.0 “ The Smart Industry Readiness Index Framework strikes a good balance by offering practical applicability while maintaining both conceptual and technical rigour. “ – Prof Dr -Ing Siegfried Russwurm, University of Erlangen-Nürnberg 5 The Smart Industry Readiness Index Manufacturing: A Key Pillar of Singapore’s Economy A national imperative for growth and transformation Today, Singapore is recognised as a hub for high-value Bloomberg Innovation Index. It is also the fourth-largest manufacturing. Singapore has developed a diverse exporter of high-tech goods in the world, after China, manufacturing industry and occupies a leadership the US, and Germany. position in sectors such as aerospace, semiconductors, chemicals, and biomedical sciences. For instance, 10 According to a study by the Boston Consulting per cent of all the integrated circuit chips in the world Group, Industry 4.0 could add S$36 billion in total are fabricated, assembled, or tested in Singapore. Five manufacturing output, boost labour productivity by of the world’s top 10 drugs are manufactured here. 30 per cent, and create 22,000 new jobs in Singapore And, despite not having any hydrocarbon reserves of by 2024. Industry 4.0 therefore presents an opportunity its own, Singapore’s integrated energy and chemicals for Singapore to cement its position as a global complex — Jurong Island — is the world’s fifth-largest manufacturing hub. With shifting factors of production producer of refined oil and ranks among the top 10 now favouring innovation-intensive economies, globally in terms of chemicals exports by volume. Singapore’s skilled workforce and strengths in innovation position the country well to be amongst With its deep engineering and innovation capabilities, the top locations for companies to design and execute Singapore has been ranked fifth in the world under the their Industry 4.0 strategies. manufacturing value-added category in the 2017 Manufacturing contributes ~20% to Singapore’s GDP Today By 2024 Leadership in high value manufacturing Impact of Industry 4.0 5th largest producer of increase in total S$36bn refined oil globally manufacturing output largest exporter of increase in salaries 4 th high-tech goods in the world 50% for the 22,000 new jobs created 5 out of world’s top 10 boost in labour drugs made in Singapore 30% productivity Source: BP World Statistical Review 2017 and Uncomtrade 2015 Database. Source: BCG Singapore Industry 4.0 Study 2016. Figure 4: The impact of Industry 4.0 on Singapore’s manufacturing industry “ Singapore’s ambition is to be the global hub for manufacturing and one of the best places globally for high-tech innovation. What makes Singapore unique is the strong partnership between industry, the ecosystem of partners, and the government. This allows companies to translate Industry 4.0 concepts and technologies into new value, for Singapore and for the markets around us. – Mr Lim Kok Kiang, Assistant Managing Director, EDB “ Catalysing the transformation of manufacturing 6 The Smart Industry Readiness Index Catalysing the transformation of manufacturing Objectives and intent Industry 4.0 is gathering momentum. Based on a 2017 The Assessment Matrix also defines the end states study conducted in partnership with Accenture, seven and the intermediate steps needed for continual out of 10 manufacturers from the energy, chemicals, improvement. Collectively, the SIRI Framework and and utilities sectors in Singapore plan to deploy Assessment Matrix tool aim to equip companies with Industry 4.0 solutions by 2020. Companies also regard practical knowledge about: Industry 4.0 as a lever to boost both organisational efficiency and business productivity. What Industry 4.0 is and the tangible benefits it could yield; However, the pace of Industry 4.0 adoption is uneven The maturity levels of their organisations across different industries and companies. Companies and facilities; and both globally and locally are grappling with the concept How they can improve in a targeted and of Industry 4.0 and the value it could bring. For these incremental manner. companies, questions such as What is Industry 4.0, and how can it benefit my company? Where should I start? Created in partnership with global testing, inspection, What are my gaps today and where are the opportunities and certification company TÜV SÜD, and validated by tomorrow? remain unanswered. an advisory panel of academic and industry experts, SIRI’s frameworks and tools are designed to help all The Smart Industry Readiness Index (SIRI) Framework companies globally — regardless of size, profile, and and an accompanying Assessment Matrix tool were level of maturity — to determine where to start, how to therefore developed to address these challenges. scale, and what they can do to sustain growth. The SIRI Framework covers the 3 core building blocks (Process, Technology, and Organisation) critical to achieving future-ready facilities, and the Assessment Matrix tool is designed to strike a balance between technical rigour and practical applicability. “ With rapid advancements in digital technologies and the push for process integration, the time for Industry 4.0 is now. For companies globally, disruptive technologies of Industry 4.0 hold the promise of creating smart facilities that are highly efficient and digitally integrated. It is an opportunity to take the lead in shaping one of the most significant shifts in manufacturing that we have ever seen. Mr Raimund Klein, Executive Vice President, Digital Factory & Process Industries & Drives, Siemens “ 7 The Smart Industry Readiness Index Development Process Screen Draft Validate Pilot Launch Research and Design and Key Expert Pilot with Publication of Evaluation Development Validation Industry Whitepaper Literature review Design and Validate with a Pilot the Launch SIRI as a and landscape scan development of a panel of industry framework and tool suite of frameworks of existing concepts practical yet technically and academic experts with Singapore-based and tools for industry and frameworks rigorous framework SMEs and MNCs to learn and apply and tool Figure 5: The five stages of the development process The development process commenced with a To ensure the technical robustness and usability of literature review of a wide range of Industry 4.0 the Assessment Matrix, an advisory panel of experts related concepts and frameworks. These included from industry and academia was also consulted. industry reports, landscape studies, business surveys, The panel’s input was then used to further improve and models produced by leading associations and the Assessment Matrix. Thereafter, the Assessment industry players. At its core, the SIRI Framework Matrix was piloted with a group of Singapore-based and Assessment Matrix draws on the Reference industrial companies. Participating companies ranged Architectural Model for Industry 4.0 (“RAMI 4.0”) from small and medium-sized enterprises (SMEs) to developed by Plattform Industrie 4.0, one of the multinational corporations (MNCs), including both largest Industry 4.0 networks in the world. Today, discrete and process manufacturing facilities. Each RAMI 4.0 has been formally acknowledged by key pilot was conducted through a workshop involving the experts and respected associations to be the company’s senior management and engineering and reference architecture model which best embodies operations teams, alongside the core SIRI development the key concepts and ethos of Industry 4.0. Beyond team. The insights, suggestions, and feedback gained RAMI 4.0, other reference materials included (but from each pilot were then taken into account when were not limited to) the Industrie 4.0 Maturity Index refining the Assessment Matrix. developed by the German Academy of Science and Engineering (acatech) and the Bersin model for human capital development by Deloitte. “ The Smart Industry Readiness Index gives clear orientation to manufacturers on what Industry 4.0 means and how they can initiate their transformation journey. The Assessment Matrix is a world’s first Industry 4.0 tool that is developed by the government for nation-wide transformation of industrial sectors. Strongly aligned with Industry 4.0 and other global manufacturing initiatives, the SIRI Framework and Assessment Matrix have the potential to be the global standard for the future of manufacturing. – Prof Dr -Ing Axel Stepken, Chairman of the Board of Management, TÜV SÜD “ Catalysing the transformation of manufacturing 8 The SIRI Framework Supply Chain Pro du ns ct tio Li fe ra e cy Op Process cl e Struc Smart Automation ture & Managem Industry olo g y Organ Readiness Index hn is a ent ec on T ti ity tiv ec nn Co Ta le nt Re ad ce ine en ss llig Inte Figure 6: The 3 building blocks and the 8 pillars The 3 Building Blocks and the 8 Pillars The SIRI Framework identifies the 3 fundamental Technology remains critical under Industry 4.0. New building blocks — Technology, Process, and digital technologies, such as cloud computing, machine Organisation — that must be considered for any learning, and the Internet of Things (IoT) are creating a factory or plant to transform into a factory/plant-of- hyper-connected industrial landscape where physical the-future. All 3 building blocks must be considered assets and equipment are integrated with enterprise in order to harness the full potential of Industry 4.0. systems to enable the constant and dynamic exchange Underpinning the 3 building blocks are 8 key pillars, and analysis of data. These cyber-physical systems in which represent critical areas that companies must turn make companies more agile and nimble. focus on to become future-ready organisations under the Industry 4.0 reference model. For companies to realise their Industry 4.0 ambitions, a high degree of automation, ubiquitous The Technology Building Block connectivity, and intelligent systems are necessary. To reflect this, the Technology building block has been segmented into the 3 pillars of Automation, Connectivity, Technological advancement has been the and Intelligence. cornerstone of the last three major industrial revolutions. The discovery of steam power enabled the first industrial revolution, while innovations in electric power catalysed the second. In a similar manner, Industry 3.0 was powered by the advent of electronics and Information Technology (IT) systems, which allowed companies to achieve an unrivalled degree of precision and efficiency through automation. 9 The Smart Industry Readiness Index “ One of the key disruptive forces of Industry 4.0 is the ever-increasing volume, velocity and value of data. Looking ahead, traditional manufacturing companies need to change their perception of data, not just as numbers on a screen, but as a strategic asset that can unlock revenue growth and deliver cost savings. Companies who embrace this shift will start building the infrastructure for connectivity and intelligence right away. – Ms Vidya Ramnath, Vice President, Global Plantweb Solutions & Services, Emerson Automation Solutions “ The Automation Pillar achieving this. Companies need to standardise or make use of complementary communication Automation — the application of technology to monitor, technologies and protocols to establish more open, control, and execute the production and delivery of inclusive, and transparent communications networks. products and services — was the hallmark of Industry 3.0. It not only freed workers from mundane and Such deeply interconnected systems also make repetitive tasks, but also enhanced the speed, quality, cyber-physical security an integral aspect of and consistency of execution. Connectivity. Hyper-connected manufacturing operations can increase the number of vulnerable While Automation has been and will continue to be points in a system, which could give cyber-attacks a a key enabler for companies, the role of automation far more extensive impact than before. To mitigate is changing. To cope with rising demand for smaller this risk, secure and resilient cyber-physical security batches and on-demand production, it is no longer architectures will need to be established. sufficient to simply maximise efficiency. To adapt quickly to changing market needs, Automation needs The Intelligence Pillar to be flexible instead of fixed. As automation systems become flexible, they will generate a larger range While Automation provides the muscle for Industry 4.0 of products in smaller batches, without needing to and Connectivity acts as its central nervous system, invest in significant capital or time to overhaul or Intelligence is the brain powering this new age. redesign processes. This puts manufacturers in a more Automation and Connectivity focus on establishing competitive position, helping them to pursue a large linkages between equipment, machines, and variety of global business opportunities and adapt to computer-based systems for the collection and rapidly changing customer needs. integration of data. Intelligence is about the processing and analysis of that data. This is important as modern The Connectivity Pillar manufacturing is no longer just about finding ways to operate faster while reducing expenses; it is also Connectivity measures the state of interconnectedness about doing so in a data-driven and intelligent way. between equipment, machines, and computer- The benefits to be derived from the Intelligence pillar based systems to enable communication and data are significant and far-reaching. With technologies exchange across assets. Like Automation, the concept such as cloud and data analytics, the vast quantities of of Connectivity has taken on a new meaning under data generated can be processed and translated into Industry 4.0. Every day, more and more devices and actionable insights to diagnose problems and identify systems are being converted from wired and analogue opportunities for improvement. With machine learning, formats to wireless and digital ones. Such IoT-enabled highly intelligent systems can assist the workforce in devices are also increasing in both quality and quantity, predicting equipment failures and changes in demand generating enormous amounts of data as a result. patterns. At their best, these intelligent systems can Technological advancements in cloud computing and also autonomously make decisions and respond to wireless infrastructure also make it possible for data to changing internal and external business needs. be centrally collected and managed. Likewise, systems that were once independent or isolated can now be integrated, unifying the various shop floor, facility, and enterprise systems through connected organisation- wide networks. Interoperability — the ability to access data across assets and systems with ease — is key to Catalysing the transformation of manufacturing 10 The Process Building Block company’s goods and services, all the way from the point of origin to the point of consumption. Under To maximise value, Technology must always be applied Industry 4.0, traditional supply chain models will in tandem with effective, well-designed Processes. After become increasingly digital: processes across the all, using technology to digitalise a poorly-designed supply chain will be connected through a sensor process will only result in a poorly-designed digital network and managed through a central data hub process. Conversely, applying technology to a well- and analytics engine. The digitalisation of supply developed process will enhance its efficiency and chains will also allow decisions about cost, inventory, enable the creation of new value. and operations to be made from an end-to-end perspective rather than in isolation. This evolution From the beginnings of modern manufacturing, benefits all players across the value chain, with greater companies have used process improvements to lower speed due to reduced lead times; greater flexibility costs and shorten their time-to-market. Previously, through real-time optimisation for changing needs; companies centred their efforts on improving the greater personalisation; greater efficiency and greater efficiency of individual processes. Under Industry 4.0, transparency, both internally and for partners. the concept of process improvements has expanded to focus on the integration of processes within a firm’s The Product Lifecycle Pillar Operations, Supply Chain, and Product Lifecycle. This stems from the new ethos of connecting intelligent The Product Lifecycle refers to the sequence of stages facilities with every part of the production value chain. that every product goes through from its initial conceptualisation to its eventual removal from the As processes within Operations, Supply Chain, market. These stages range from design, engineering, and Product Lifecycle become integrated, they will and manufacturing to customer use, service, and converge into a single unified system where data is disposal. A robust product lifecycle management shared, processed, and integrated across the product framework has always been integral to manufacturing management, production, and enterprise layers of the operations; however, shorter product cycles and a organisation. This will then generate the next leap growing demand for personalisation have accentuated forward in flexibility and efficiency. the need for greater integration and digitalisation across the different Product Lifecycle stages. The Operations Pillar Advancements in digital tools have made it easier The first pillar, Operations, encompasses the than ever before to bring together data, processes, planning and execution of processes which lead to business systems, and people to create a single the production of goods and services. The end goal unified information backbone that can be managed is to convert raw materials and labour into goods and digitally. Industry 4.0 also introduces the concept of services at the lowest cost. While this objective does a “digital twin”, which is a virtual representation of not change in the context of Industry 4.0, companies the physical assets, processes, and systems involved can now access new technologies and approaches throughout a product lifecycle. A digital twin offers to achieve this goal more rapidly and with better results. two key benefits. Firstly, the information generated For instance, companies can use data analytics to at each stage can be shared seamlessly, facilitating reduce waste by identifying and improving inefficient better decision-making and enabling processes to processes. They can also use wireless communications be dynamically optimised in other stages. This to connect discrete processes and systems, to allows companies to shorten their design and enable the remote monitoring and decentralised engineering cycles and respond to customer demands control of assets. more quickly. Secondly, a digital twin removes the limitations of working with physical prototypes. The Supply Chain Pillar By working off the digital twin, multiple prototypes can be created and tested virtually at speed, at scale, Supply Chain management encompasses the planning and at a much lower cost. and management of raw materials and inventory of a “ Industry 4.0 is driving a paradigm shift — from the optimisation of physical assets and systems to the optimisation of processes, where data is integrated across the operations, enterprise, and product lifecycle layers. This allows for stronger cross-functional integration and closer collaboration not just within the company but also with external stakeholders such as suppliers and customers. – Dr -Ing Gunther Kegel, CEO, Pepperl+Fuchs & President of VDE “ 11 The Smart Industry Readiness Index The Organisation Building Block the latest developments in Industry 4.0. This will allow them to capture new opportunities to drive Organisation is the third building block of Industry 4.0. improvement. Concurrently, the wider workforce needs Often under-regarded, Organisation plays an equally to be multi-skilled and adaptable to manage Industry important role alongside Technology and Processes. 4.0’s dynamic and digitalised operations. This is To remain relevant in the face of increasing competition enabled by formal talent development programmes under Industry 4.0, companies must adapt their that are not only aligned with the company’s business organisational structures and processes to allow and human resource objectives but also foster a their workforce to keep pace. culture of self-learning and personal development. If successful, a skilled, self-learning workforce and Industry 4.0 calls for a greater focus on two key leadership core will be created, one which will be able components that can affect an organisation’s to maximise the value of any transformation initiative. effectiveness. The first component is the people who make up the organisation – the entire workforce The Structure & Management Pillar from the top management down to the operational teams. The second component is the institutional An organisation’s Structure is its system of explicit systems that govern how the company functions. and implicit rules and policies that outline how roles Both components must be taken into account in order and responsibilities are assigned, controlled, and to fully reap the benefits of Industry 4.0. For instance, coordinated. Structure influences how teams act and even a competent leadership team and workforce will interact and how initiatives are to be implemented to be demotivated by rigid structures, inconsistent achieve organisational goals. Just as process design practices, and siloed processes. Likewise, open determines how successful production will be, an channels for collaboration and innovation will not organisation’s Structure determines how successful the be effective unless employees are informed and company will be in achieving its goals. Under Industry incentivised to use them. 4.0, organisations will see greater decentralisation of decision-making, increased openness in information As such, the necessary enhancements must be made sharing, and more collaboration among teams both to people, represented by Talent Readiness, and the internally and with external partners. In the long run, this company, represented by Structure & Management, will enable companies to make decisions in a more agile before a company can implement Industry 4.0 manner and to become more responsive to changes. strategies effectively. Meanwhile, Management is fundamentally about The Talent Readiness Pillar getting people to work together towards a well- defined common goal. Given the paradigm shifts For any transformation to deliver value, Talent on multiple fronts, Industry 4.0 is also a change Readiness — the ability of the workforce to drive management exercise. Strong leadership, supported and deliver Industry 4.0 initiatives — will be a key by a clear strategy and governance framework, is factor for success. As organisations embrace flatter hence essential for any organisation to successfully structures and decentralised decision-making, it navigate this increasingly complex and highly becomes critical to build a competent and flexible networked world. Robust Structure & Management will workforce characterised by continuous learning and make an organisation more flexible, collaborative, and development at all levels. Everyone has a role to play. empowered to design and implement Industry 4.0 Management must put in place systems or practices strategies effectively. that will allow people to constantly stay abreast of “ Companies must embrace Industry 4.0 to prepare the digital foundation needed for a manufacturing future that is like no other — Industry X.0 — which has at its heart highly intelligent, interconnected products and ecosystems that create a fully digital value chain, supplemented by new core innovation competencies and deep cultural change. Therefore, beyond digitalisation, organisational talent, structures and processes will need to be adapted and built across the enterprise to put it on the right trajectory into this future of 'connected everything'. – Mr Senthil Ramani, Managing Director, Accenture “ Catalysing the transformation of manufacturing 12 The 16 Dimensions of Assessment Smart Industry Readiness Index Process Technology Organisation Product Talent Structure & Operations Supply Chain Automation Connectivity Intelligence Lifecycle Readiness Management 1 2 3 4 7 10 13 15 Shop Floor Workforce Learning Inter- and Intra- & Company 5 8 11 Development Collaboration Integrated Vertical Horizontal Product Enterprise Integration Integration 14 16 Lifecycle 6 9 12 Leadership Strategy & Competency Governance Facility Figure 7: The 16 Dimensions of Assessment The 3 building blocks and 8 pillars which we have Dimension 2: Process — just described map onto 16 dimensions, which are Horizontal Integration assessment areas, covered in the Assessment Matrix tool, that companies can use to evaluate the Horizontal Integration, the second key characteristic current readiness of their facilities. A brief description of Industry 4.0, refers to the integration of enterprise of each of the 16 dimensions is provided in this processes across the organisation and with other section, and the full Assessment Matrix tool can be stakeholders along the value chain. Enterprise found on page 22. processes include demand planning, procurement, logistics, and after-market services, while stakeholders Dimension 1: Process — include suppliers, business partners, and customers. Vertical Integration Much like Vertical Integration, Horizontal Integration evaluates the presence of formal channels that enable Vertical Integration is one of the three key information sharing as well as how data is exchanged characteristics of a digitalised facility defined under and analysed. As processes and systems become ever Industry 4.0 by acatech. It can be understood as more defined and digital, the Horizontal Integration the integration of processes and systems across all dimension describes an end state where a company’s hierarchical levels of the automation pyramid within internal processes converge with those of its suppliers a facility to establish a connected, end-to-end data and partners. This creates an interoperable and thread. This dimension seeks to assess the extent transparent network, within which all stakeholders are of formal connections and linkages between and able to coordinate and optimise their processes, tasks, across processes and systems, and it also takes into and decisions across the entire value chain. Besides account how data is exchanged and analysed. In its enabling higher productivity and shorter lead times, ideal form, the Vertical Integration dimension defines such an integrated value chain can also facilitate the a state where all OT and IT systems across the creation of new business and operating models. production and enterprise levels are integrated into automated, interoperable, and flexible networks that Dimension 3: Process — will permit seamless data exchange, analysis, Integrated Product Lifecycle and decision-making. This will in turn allow better communication, flexibility, and operational efficiency, Integrated Product Lifecycle integrates people, and will also enable faster and more concerted processes, and systems along the entire product responses to any changes in resource availability, lifecycle, and also examines how data is collected, operational demands, or product types. managed, and analysed across the different stages of the product lifecycle. These stages include design and development, engineering, production, customer use, service and disposal. 13 The Smart Industry Readiness Index To build an Integrated Product Lifecycle, companies Dimensions 10–12: Intelligence — will need to use digital tools and systems to create Shop Floor, Enterprise, and Facility a production information backbone that can be accessed by employees and their extended enterprise The Intelligence dimensions evaluate the ability of networks. At the most advanced stage, companies IT and OT systems at the Shop Floor, Enterprise and may create “digital twins” of processes and assets. Facility layers to identify and diagnose any deviations By removing physical constraints through these digital and adapt to changing needs. At the lower bands, twins, companies can shorten development cycles, basic intelligence is derived by processing large improve existing systems, and launch new processes quantities of data and detecting any deviations from and products swiftly and at scale. predefined parameters. As more advanced algorithms and models are introduced, computer systems will be For Dimensions 4–12 able to detect deviations, identify likely causes, and even predict potential failures ahead of time. Ultimately, Under the Technology building block, the SIRI IT and OT systems will autonomously learn and adapt Framework and Assessment Matrix segments to new needs while making decisions on their own to the areas of assessment into three layers: the optimise processes, assets and resources. Shop Floor, where the production and management of goods are carried out; the Enterprise, where Dimension 13: Organisation — administrative tasks are carried out; and the Workforce Learning and Development Facility, which is the physical building or premises where production takes place. A Workforce Learning and Development (“L&D”) strategy aims to develop the workforce’s capabilities, skills and competencies to achieve organisational Dimensions 4–6: Automation – excellence. In the context of Industry 4.0, this is Shop Floor, Enterprise, and Facility especially critical as new technologies and processes will fundamentally alter the nature of work and the Across the Shop Floor, Enterprise, and Facility layers, types of skills required. Traditional engineering the Automation dimensions evaluate the degree and capabilities will need to be augmented with new digital flexibility of automation, as well as the extent of its skills, such as data analytics, systems integration, and integration across multiple systems. The lower bands software development. assess the overall automation levels of both production and support processes. Flexibility is then introduced In the long term, the entire workforce needs to have in a higher band, as flexible automation will allow digital confidence, which may include skills such as data processes to be reconfigured and machines to be interpretation and automation management. Employees re-tasked. This allows companies to manufacture will also need to adapt to new types of interactions a greater variety of products with shorter turnaround between people and machines, where humans manage times. At its most advanced stage, automation operations alongside intelligent machines and systems. systems across all three layers will converge and interact dynamically with one another as a single As a proxy to workforce readiness, the Workforce integrated whole. Learning and Development dimension measures the quality of a company’s L&D programmes. To start with, L&D programmes should be structured and Dimensions 7–9: Connectivity — implemented on an ongoing basis; this will provide Shop Floor, Enterprise, and Facility employees with opportunities for continuous learning, helping them to acquire new skills and enhance existing The Connectivity dimensions evaluate the level ones. This is important as occupational needs and job of interconnectedness between the equipment, roles evolve with time. machines, and systems that reside within the Shop Floor, Enterprise, and Facility layers. Once formal To achieve a high level of workforce readiness, L&D connections have been established across assets and programmes must be aligned with business needs and systems, the higher bands measure the interoperability, integrated with other key human resource functions like security, speed, and agility of the network as a whole. talent attraction and career development. They must These qualities allow interconnected systems to also be dynamically updated based on the feedback and communicate with one another seamlessly, and allow insights provided by employees and business teams, them to be reconfigured dynamically in response to and should proactively position the workforce for future changing needs. skills. Integrated and forward-looking L&D programmes allow companies to build a high-performing and future- ready workforce capable of managing and sustaining Industry 4.0 initiatives. Catalysing the transformation of manufacturing 14 Dimension 14: Organisation — At its highest form, cross-functional teams can be Leadership Competency dynamically formed across internal departments and even include partners and customers, with Leadership Competency refers to the readiness of the shared goals, resources, and joint key performance management core to leverage the latest concepts and indicators (KPIs). technologies for the company’s continued relevance and competitiveness. As transformation is a multi-year The benefits of a high level of collaboration run journey that will evolve and adapt over time, it must deep. Through effective and open inter- and intra- be led from the front by a strong leadership core with collaboration, companies can tap into a wider degree commitment, a clear vision, and the right capabilities of expertise and resources to address complex, multi- and knowledge. To unlock their full potential, stakeholder challenges. In the long term, this will shift companies may adopt flatter organisational structures the company from a culture of internal competition to and enable decentralised decision-making. At the a culture of shared goals, accountability, and rewards. lower bands, this dimension examines the management team’s familiarity with the latest concepts and Dimension 16: Organisation — technologies, and the ways by which such knowledge Strategy and Governance is acquired. Companies should establish processes and systems for the acquisition of information on Strategy and Governance relate to the design the latest trends, concepts, and technologies. As a and execution of a plan of action to achieve a set company progresses, this dimension will then measure of long-term goals. It includes identifying priorities, the leadership team’s ability to independently design, formulating a roadmap, and developing a system of execute, and adapt transformation strategies to ensure rules, practices and processes to translate a vision the company’s relevance in the long term. into real business value. Dimension 15: Organisation — This dimension examines how well an organisation Inter- and Intra- Company Collaboration has developed and implemented its strategy, and a robust governance model. Both factors are critical Inter- and Intra- Company Collaboration refers to the and must exist in tandem to manage the complexity process of working together, both internally and with that comes with the increasing interconnectedness external partners, to achieve a shared vision and of processes, systems, and people. purpose. Industry 4.0 has created a connected network of systems and technologies which reduce the cost To navigate change and mitigate risk, companies of collaboration. It has also redefined the basis of will need to define their vision and end-outcomes competition while increasing the pace of change; in while establishing consistent guiding principles and such a highly networked environment, companies must supporting structures. This will guide decision-making be able to collaborate effectively and adapt swiftly. and help determine the approaches needed to achieve the company’s desired outcomes. The different bands However, the biggest barriers to collaboration are often map the natural progression that a company will take, not technical, but cultural and institutional in nature. from the identification of Industry 4.0 as a strategic As such, the Inter- and Intra- Company Collaboration focus to the development, implementation, scaling, dimension assesses the formal channels that enable and continual enhancement of the strategy and employees to share information and work together, governance model. as well as the institutional structures and systems that allow collaborative behaviours and initiatives to flourish. Flatter organisational structures enable faster decision-making, and the alignment of incentives can empower the workforce to collaborate more effectively. “ Industry 4.0 is a global leadership topic that should be on top of any CXO’s agenda. Strong leadership competency is an imperative to drive enterprise transformation, to shift the focus from today’s operational needs to readiness for tomorrow’s opportunities. “ – Mr Amos Leong, CEO, Univac 15 The Smart Industry Readiness Index The LEAD Framework Mapping the Industry 4.0 Transformation Journey “ The SIRI Framework and the Assessment Matrix allow our manufacturing teams to take stock of what we are doing well and where we can do better. This forms a good basis to build a shared Industry 4.0 vision and strategy, enabling us to take decisive action in initiating a multi-year transformation journey. “ – Mr Hashim Baba, Plant Manager, Becton Dickinson Singapore To help manufacturers characterise their transformation journeys, we present a circular, continuous four-step process that all manufacturers can adopt in their approach towards Industry 4.0 transformation. These steps, encapsulated in the LEAD framework, will help companies determine where to start, how to scale, and what they should do to sustain growth in a world powered by Industry 4.0. 1 Learn key concepts and build a common language for alignment 2 Evaluate the current Industry 4.0 maturity levels of existing facilities 3 Architect a comprehensive transformation strategy and implementation roadmap 4 Deliver impact and sustain transformation initiatives Evaluate the current Industry 4.0 maturity levels of existing facilities Figure 8: The LEAD framework “ While the term Industry 4.0 was created several years ago, many manufacturing companies, particularly SMEs, remain unfamiliar with it. The SIRI Framework is an intuitive and realistic reference framework that is useful for all industrial companies, both big and small, to not only learn these new concepts but also to apply them to our facilities. “ – Mr Desmond Goh, Director, People Bee Hoon Factory Catalysing the transformation of manufacturing 16 LEARN key concepts and build a common language for alignment A thorough understanding of key Industry 4.0 This ensures that companies will be equipped concepts will provide companies with a firm foundation with the following knowledge: for transformation. However, according to McKinsey’s 2016 and 2017 Industry 4.0 Global Expert Surveys, there is a high level of uncertainty among manufacturers An understanding of the key principles, concepts and technologies under Industry 4.0; about what is required for the implementation of Industry 4.0. As a consequence, many are still struggling An overview of the tangible benefits and business value that Industry 4.0 can yield; and to get started, and fewer than half the participants in the surveys considered their companies to be well- A guide to illustrate how companies can achieve their ideal end states in a practical, prepared for Industry 4.0. They highlighted their lack stepwise fashion of familiarity with key concepts, combined with the absence of a clear strategy and roadmap, as some of Second, SIRI aims to establish a common language the biggest challenges hindering Industry 4.0 adoption. among the various stakeholders necessary for Industry 4.0 transformation. The new technical terms Even when companies have started their Industry 4.0 and jargon arising from Industry 4.0 can be confusing transformation journeys, knowledge generally remains and counterproductive for companies. By providing confined to the corporate management level or to a few companies with an intuitive and standardised set of in-house experts. However, real transformation requires terms and definitions, SIRI can establish a common the wider workforce within each company to be exposed understanding among companies and the workforce. to Industry 4.0 and to have a sound understanding of This will facilitate more effective communication how this new paradigm can make a positive impact on within the organisation and with external partners their daily work. and customers. A common language also allows technology providers to have more effective and SIRI aims to help companies in this critical first step productive conversations with manufacturers, by strengthening their institutional knowledge about helping them to identify gaps, define priorities, and Industry 4.0 in two ways. First, by examining the structure comprehensive transformation roadmaps. three building blocks, eight pillars, and 16 dimensions presented by the SIRI Framework, companies can be more informed and educated about the core concepts and fundamental principles of Industry 4.0. “ Within many organisations, the level of familiarity towards Industry 4.0 concepts can vary significantly across the different technology and operations teams. Even for companies with considerable expertise, knowledge often resides in specific individuals or teams, rather than being uniformly understood across the entire organisation. The SIRI Framework and Assessment Matrix tool form a good basis to drive alignment towards a common understanding and vision. – Mr Allan Ferrie, Assembly and Test Director, Rolls-Royce Singapore “ EVALUATE the current Industry 4.0 maturity levels of existing facilities Learning the key concepts is an essential first step. process to ensure that the assessment exercise However, that alone will not help companies to devise will produce meaningful results. Companies need to effective transformation strategies. Companies must identify three things: understand where they currently are before they can identify what and how to improve. Thus, to help What to evaluate. Companies need to define the companies conduct comprehensive assessments scope of their assessment, and can choose to of their factories or plants, this whitepaper includes evaluate either an entire manufacturing facility an Assessment Matrix tool incorporating all 16 or break it down to examine each product group dimensions. This Assessment Matrix tool can be independently. The latter is especially relevant for found in the next section of this paper and should companies that own multiple product groups, each take no more than one or two days to complete. of which may be at a different stage of maturity or have its own distinct processes. Ultimately, Before undertaking the assessment, however, however, companies should seek to evaluate companies should go through the following thought their facilities in their entirety. 17 The Smart Industry Readiness Index Who to evaluate. After defining the scope of the assessment, companies should identify The 5 Principles of Assessment the key stakeholders who will participate in this exercise. Due to the comprehensive nature 1 The SIRI Assessment provides a snapshot of a of the Assessment Matrix, the assessment facility's current state but not its future potential. exercise should ideally involve a cross-functional team including key stakeholders like the general 2 The SIRI Assessment uses Industry 4.0 concepts manager and senior leaders from the operations, as the reference points. Future manufacturing and IT facility, and human resource departments. industrial concepts, as well as technologies, should also be taken into consideration, if relevant. How to evaluate. Due to the mix of legacy and new systems within every brownfield 3 All dimensions should be considered, though facility, companies will find that, for certain the importance and relevance of each will vary dimensions, the state of their facilities may depending on the nature of the industry and the not be fully represented in one single band. company's current and future needs. For example, under the facility automation dimension, heating, ventilation and 4 Companies should not feel compelled to achieve air-conditioning (HVAC) systems might be fully automated, which would place them Band 5 across all dimensions. Instead, they should under Band 3. However, lighting systems might strive towards higher bandings based on specific still require manual operation, which is more business needs and aspirations. accurately represented in Band 2. In such cases, it is up to the companies’ discretion to 5 The SIRI Assessment is more than a one-off opt for either banding. exercise — it should be used on an ongoing basis. Conducting a SIRI Assessment, or evaluating Figure 9: The 5 Principles of Assessment the current state of a factory or plant using the Assessment Matrix, must also be based on the five fundamental principles listed in Figure 9. Once these considerations have been taken into Principle 3 is especially important and must be account, companies can begin the assessment. emphasised: while all 16 dimensions should be Through open discussions, companies should formally considered, this does not mean that every measure their existing processes, systems, and dimension is of equal importance. Instead, the structures. They should then score themselves in importance and relevance each dimension will vary one of six bands for each of the 16 dimensions. depending on each company’s needs and cost profile. The Assessment Matrix tool deliberately uses bands instead of scores, each of which represents a distinct For example, if utilities constitute a greater stage of the Industry 4.0 transformation journey. This component of overall operating expenses, facility- is because, in reality, each stage is better represented related dimensions will be of higher priority to that by a range rather than by a discrete point. company. Conversely, if labour costs make up a large portion of overall operating expenses, shop floor automation may warrant more attention. In the same vein, the relative importance of each dimension also varies across industries. For example, approximately 70% of manufacturing costs in the energy and chemicals industry are attributable to raw materials. It is therefore natural for companies in this industry to focus on horizontal integration in order to reduce inefficiencies across their supply chains. Similarly, facility automation will be an important dimension for the semiconductor industry as cold rooms — needed for the management of ambient temperature and humidity — require significant amounts of electricity, and efficient facility automation could translate into significant cost savings. Catalysing the transformation of manufacturing 18 “ As part of our Smart Enterprise program, we have been investing in many initiatives to achieve significant improvements in speed, productivity, and quality. Here, we see this Assessment Matrix as a useful tool to help us to unlock maximum value by not only pushing us to investigate new dimensions that were not considered previously, but also allowing us to pursue our Industry 4.0 strategy in a more targeted fashion. – Mr Laurent Filipozzi, Site Head, Infineon Plant, Singapore “ ARCHITECT a comprehensive transformation strategy and implementation roadmap According to PwC’s 2016 Global Industry 4.0 survey, tend to focus on increasing shop floor automation. global industrial companies plan to invest US$907 Two, teams and companies tend to focus more on billion (S$1260 billion) per year globally in Industry areas they are already familiar with: for example, a 4.0 over the next five years. With a growing number warehouse management team will naturally tend of companies looking to initiate or scale up their to focus on supply chain initiatives. Thus, the SIRI transformation initiatives, the SIRI Framework and Framework serves as a checklist to provide companies Assessment Matrix serve as a timely guide to help with a systematic way to broaden the scope of their them design a comprehensive strategy and roadmap existing or future transformation initiatives. for Industry 4.0 transformation — to ensure that they start out on the right footing. Secondly, the Assessment Matrix doubles as a step- by-step improvement guide, breaking down and laying In this third step, companies can use the SIRI out the intermediate steps of the long-term Industry Framework and Assessment Matrix in two tangible 4.0 transformation journey. These intermediate phases ways. First, the SIRI Framework serves as a checklist are necessary because even though there are many for companies, helping them to ensure that all the frameworks articulating the ideal Industry 4.0 building blocks, pillars, and dimensions are formally end-state, few provide practical guidance on how to considered. While the relative importance of each get there. Without proper guidance, many companies dimension may vary, companies must consider all the will struggle to develop a way to bridge the gap dimensions to ensure that all the ground is covered. between their current “as-is” state and their “to-be” Even if they ultimately decide to deprioritise specific vision. This issue is often amplified for brownfield dimensions and focus on others, it is important that facilities, where limitations and considerations such these decisions be informed choices made after as operational continuity, fragmented systems, and careful consideration. legacy infrastructure often dictate and limit the scale and feasibility of transformation initiatives. Also, many industrial companies often fail to include By providing clear definitions and descriptions for improvements in complementary or adjacent domains all bands across the 16 dimensions, the Assessment that might yield additional benefits. This happens for Matrix aims to address this challenge. It will enable two reasons. One, many companies tend to focus only companies to systematically identify high-impact on the domain directly related to the issue at hand: for initiatives and structure effective implementation plans instance, if a company employs too many low-skilled with clearly defined phases, timelines, and targets. workers engaged in repetitive tasks, that company will “ Often, companies tend to focus excessively on shop floor automation and under-invest in equally important areas such as process design and workforce competency. The SIRI Framework serves as a useful counter-check to ensure that no dimensions are overlooked, in order to capture maximum value from any Industry 4.0 initiatives. – Mr Yeoh Pit Wee, Director for Manufacturing Operations, Rockwell Automation “ 19 The Smart Industry Readiness Index “ There are many grand Industry 4.0 visions and plenty of innovative solutions to achieve these visions. However, it is difficult to translate this into tangible steps that deliver real value to the business. A well-defined roadmap will be a big help in identifying the most appropriate technologies to apply and an execution plan, to achieve both short- and long-term goals. – Mr Lim Hock Heng, Site Director, GSK Singapore “ DELIVER impact and sustain transformation initiatives As with all transformation initiatives, a well-designed their transformation through quick wins, the right strategy is only as good as its execution. Once systems should be put in place to sustain these gains. a company has come up with its transformation Transformation strategies must also adapt and evolve roadmap, the next step is to put the right infrastructure, continually, and companies should therefore consider systems, and processes in place. Companies will need establishing central, cross-functional teams to execute to determine the optimal approach to achieve their initiatives, monitor progress, assess impact, and outcomes across the various phases and initiatives. identify future opportunities for improvement. To ensure sustained impact, SIRI serves as a blueprint for companies to measure and refine their initiatives over a multi-year period. Transformation should not be short-lived but should instead be a long-term endeavour. Even as companies kick-start “ Like us, many companies have already started their transformation journey. Beyond addressing the operational concerns today, SIRI offers a useful framework to also guide our future decisions to deliver sustained impact. It also ensures that we’re always moving in the right direction and focusing on the things that matter. – Mr Goh Koon Eng, General Manager, Chevron Oronite “ Catalysing the transformation of manufacturing 20 The Way Forward Businesses must start taking decisive action today Companies seeking to embrace Industry 4.0 often come from very different starting points, with different capabilities and varying levels of ambition. Some will require a comprehensive transformation of their operations, processes, and business models. Others may need to expand their focus and explore adjacent areas. That said, regardless of the starting point or the nature of the industry, companies of all sizes will benefit from Industry 4.0. Collectively, SIRI’s frameworks and tools offer a systematic approach for companies to start, scale, and sustain their transformation initiatives. Although the relative significance of the 3 building blocks, 8 pillars, and 16 dimensions will vary across different industries, the concepts within SIRI attempt to provide companies with a common language to boost internal alignment and co-innovation with external partners. With the SIRI Framework and the Assessment Matrix, companies have the opportunity to take decisive action today by following the four steps in the LEAD Framework — to set themselves on the right trajectory for transformation and growth. 21 The Smart Industry Readiness Index Assessment Matrix: The 16 Dimensions Process Building Block | Operations Pillar | Vertical Integration Dimension Vertical Integration is the integration of processes and systems across all hierarchical levels of the automation pyramid within a facility to establish a connected, end-to-end data thread. Band Definition Description Resource planning and technical Vertical processes are not production processes are managed and 0 Undefined explicitly defined. executed in silos, based on informal or ad-hoc methods. Vertical processes are Resource planning and technical defined and executed by production processes are managed 1 Defined humans, with the support and executed in silos, based on a set of of analogue tools.1 formally defined instructions. Resource planning and technical Defined vertical processes production processes are managed are completed by humans 2 Digital and executed in silos, by Operations with the support of digital Technology (OT) and Information tools. Technology (IT) systems. Digitised vertical processes OT and IT systems managing resource and systems are securely planning and technical production 3 Integrated integrated across all processes are formally linked; hierarchical levels of the however, the exchange of data and automation pyramid.2 information across different functions is predominantly managed by humans. OT and IT systems managing the resource planning and technical Integrated vertical production processes are formally processes and systems linked, with the exchange of data and 4 Automated are automated, with limited information across different functions human intervention. predominantly executed by equipment, machinery and computer-based systems. Automated vertical OT and IT systems are integrated processes and systems from end to end, with processes being 5 Intelligent are actively analysing and optimised through insights generated reacting to data. from analysis of data. 1 Analogue refers to pre-digital methods of collecting, storing and sharing information (e.g. paper-based tracking systems). 2 The industrial automation pyramid distributes systems in five levels: the field level, control level, production level, operations level, and enterprise planning level. Please refer to the definition of the automation pyramid in the Glossary for details. Catalysing the transformation of manufacturing 22 Process Building Block | Supply Chain Pillar | Horizontal Integration Dimension Horizontal Integration is the integration of enterprise processes across the organisation and with stakeholders along the value chain. Band Definition Description Enterprise processes are managed and Supply chain processes3 0 Undefined executed in silos, based on informal or are not explicitly defined. ad-hoc methods. Supply chain processes are Enterprise processes are managed and