Respiratory Protection Program PDF
Document Details
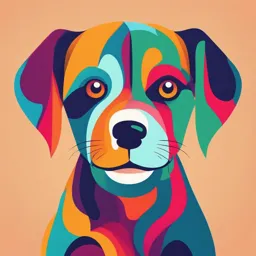
Uploaded by PatriMoldavite
Chesapeake Fire Department
Tags
Related
- Cancer Prevention PDF Chesapeake Fire Department Policy
- Spring Fire Department Guidelines - Self-Contained Breathing Apparatus PDF (SFD.066.REV1)
- Hoffman Estates Fire Department Safety Guidelines - 2022 PDF
- Hoffman Estates Fire Department PDF - Emergencies Involving Asbestos
- Spring Fire Department Self-Contained Breathing Apparatus Guidelines PDF
- Spring Fire Department Post-Incident Air Monitoring Guideline PDF, 2024
Summary
This document is a policy manual for the Chesapeake Fire Department regarding their Respiratory Protection Program. It outlines the different types of respiratory protection equipment, requirements, and guidelines for use. The policy covers definitions, procedures, training, and responsibilities.
Full Transcript
Policy 908 Chesapeake Fire Department Policy Manual Copyright Lexipol, LLC 2023/04/01, All Rights Reserved.Published with permission by Chesapeake Fire Department Respiratory Protection Program - 1 Respiratory Protection Program 908.1 PURPOSE AND SCOPE The purpose of this policy is to i...
Policy 908 Chesapeake Fire Department Policy Manual Copyright Lexipol, LLC 2023/04/01, All Rights Reserved.Published with permission by Chesapeake Fire Department Respiratory Protection Program - 1 Respiratory Protection Program 908.1 PURPOSE AND SCOPE The purpose of this policy is to identify the different types of respiratory protection equipment provided by the Department, the requirements and guidelines for the use of respirators and the other mandates associated with their use. This policy applies to all members whose job duties could require them to use respiratory protection, due to exposure to atmospheres where there is smoke, low levels of oxygen, high levels of carbon monoxide, or the presence of toxic gases or other respiratory hazards (29 CFR 1910.134; 16 VAC 25-60-30; 16 VAC 25-90-1910). The purpose of this policy is to establish guidelines under Virginia Occupational Safety and Health (VOSH), National Institute of Occupational Safety and Health (NIOSH), and the National Fire Protection Administration (NFPA) as outlined in the Chesapeake Fire Department Respiratory Protection Program . 908.1.1 DEFINITIONS Definitions related to this policy include: Immediately dangerous to life or health (IDLH) - Any atmosphere that poses an immediate threat to life, would cause irreversible adverse health effects or would impair an individual's ability to escape from a dangerous atmosphere. Interior atmospheric conditions at structure fires beyond the incipient stage are considered IDLH, as are a variety of rescue types (29 CFR 1910.134; 16 VAC 25-60-30; 16 VAC 25-90-1910). Respiratory protection - Any device that is worn by the user to reduce or eliminate exposure to harmful contaminants through the inhalation of those contaminants. 908.2 POLICY It is the policy of the Chesapeake Fire Department to require members to use the proper level of respiratory protection, as described below, when working in hazardous conditions. The level of protection may be increased or decreased by a Company Officer or Incident Commander (IC) based upon his/her evaluation of the hazard. Members shall not be required, or allowed, to enter or work in hazardous conditions without proper respiratory protection, and shall be trained in the proper use and care of the devices. The Chesapeake Fire Department Respiratory Protection Program details departmental procedure for respirator use, inspection, cleaning, maintenance, and repair, as well as required training, testing and evaluation. 908.3 RESPIRATORY PROTECTION PROGRAM MANAGER The Fire Chief will designate a program manager with sufficient training or experience to oversee the objectives of this policy and the Respiratory Protection Program , and ensure that the Department meets any legal mandates related to respiratory protection. The administrator shall (29 CFR 1910.134; 16 VAC 25-60-30; 16 VAC 25-90-1910): (a) Maintain, implement and administer a written respiratory protection program. Chesapeake Fire Department Policy Manual Respiratory Protection Program Copyright Lexipol, LLC 2023/04/01, All Rights Reserved.Published with permission by Chesapeake Fire Department Respiratory Protection Program - 2 (b) Ensure the written respiratory protection program and related procedures are followed and appropriate. (c) Ensure the procedures and written respiratory protection program address relevant mandates. (d) Ensure selected respirators continue to effectively protect members. (e) Have supervisors periodically monitor member respirator use to make sure members are using them properly. (f) Regularly ask members who are required to use respirators for their input on program effectiveness and whether they have problems with the following: 1. Respirator fit during use 2. Any effects of respirator use on work performance 3. Respirators being appropriate for the hazards encountered 4. Proper use under current work site conditions 5. Proper maintenance (g) Ensure the Department covers the costs associated with respirators, medical evaluations, fit testing, training, maintenance, travel costs and wages, as applicable. (h) Provide direction for respirator selection. (i) Require medical evaluations for members who use respiratory protection as set forth in 29 CFR 1910.134. Additional responsibilities for the Respiratory Protection Program Manager are outlined in the Respiratory Protection Program . 908.4 USE OF RESPIRATORY PROTECTION Members exposed to harmful environments in the course of their assigned activities shall use respiratory protection devices. Members using respiratory protection shall ensure that they have no facial hair between the sealing surface of the facepiece and the face that could interfere with the seal or the valve function. Members also shall ensure that they have no other condition that will interfere with the face-to- facepiece seal or the valve function. Members shall not wear corrective glasses, goggles, or other personal protective equipment (PPE) that interferes with the seal of the facepiece to the face, or that has not been previously tested for use with that respiratory equipment. For all tight-fitting respirators, members shall perform a user seal check each time they put on the respirators, using the procedures in 29 CFR 1910.134, App. B-1 or other department-approved procedures recommended by the respirator manufacturer. Company Officers shall monitor members using respiratory protection and their degree of exposure or stress. When there is a change in work area conditions or when a member's degree Chesapeake Fire Department Policy Manual Respiratory Protection Program Copyright Lexipol, LLC 2023/04/01, All Rights Reserved.Published with permission by Chesapeake Fire Department Respiratory Protection Program - 3 of exposure or stress may affect respirator effectiveness, the Company Officer shall reevaluate the continued effectiveness of the respirator and shall direct the member to leave the respirator use area when: (a) It is necessary for the member to wash their face and the respirator facepiece to prevent eye or skin irritation associated with respirator use. (b) The member detects vapor or gas breakthrough, or when there is a change in breathing resistance or leakage of the facepiece. (c) The member needs to replace the respirator or the filter, cartridge, or canister. Members who detect vapor or gas breakthrough, changes in breathing resistance, or leakage of the facepiece shall replace or repair the respirator before returning to the work area. 908.4.1 USE OF SELF-CONTAINED BREATHING APPARATUS Self-contained breathing apparatus (SCBA) are atmosphere-supplying respirators for which the breathing air source is designed to be carried by the user. Members shall use SCBA when entering an atmosphere that may be IDLH. These situations may include but are not limited to: • Entering an area that may be oxygen deficient such as confined spaces, trenches, unventilated structures, or septic tanks. • Engaging in any firefighting operations, with the possible exception of a vegetation fire. • Entering the hot zone of a hazardous materials incident. • Entering any area where contaminant levels may become unsafe without warning, or any situation where exposures cannot be identified or reasonably estimated. • Any time use is specified by the Company Officer or IC. Facepieces should be donned and regulators attached before entering any smoke-filled area or IDLH environment. Use of SCBA shall not cease until approved by the IC. 908.4.2 USE OF SUPPLIED AIR RESPIRATORS (SAR) These respirators provide breathing air to the user from a remote air source. They provide a high level of respiratory protection and may be used in an IDLH. 908.4.3 USE OF FULL-FACE RESPIRATORS Full-face respirators are respirators that fit over the full face to protect the face and eyes from contaminants at the same time they filter air. Company Officers or the IC may allow the use of full-face respirators in situations where, due to the duration of the incident and level of exposure, the use of SCBA is not necessary or practical. These situations may include but are not limited to: (a) Hazardous materials incidents where members are not working in the hot zone. (b) Incidents involving weapons of mass destruction where members are outside of the hot zone and not directly exposed to any known hazard. Chesapeake Fire Department Policy Manual Respiratory Protection Program Copyright Lexipol, LLC 2023/04/01, All Rights Reserved.Published with permission by Chesapeake Fire Department Respiratory Protection Program - 4 (c) Certain emergency medical responses where additional protection is warranted. Full-face respirators shall not be used when there is a potential for an oxygen-deficient atmosphere. 908.4.4 USE OF AIR PURIFYING RESPIRATORS (APR) AND POWER AIR PURIFYING RESPIRATOR (PAPR) Air Purifying Respirators (APR) use cartridges/filters to remove contaminants as the air passes through them. It does not supply oxygen so it must be used in atmospheres with at least 19.5% oxygen. Power Air Purifying Respirators (PAPR) consist of a face piece, breathing tube, battery-operated blower, and particulate filter (HEPA only). These are a step above APR masks in that the blower creates a positive air pressure inside the mask facilitating a better seal. The blower passes contaminated air through a HEPA filter, which removes the contaminant and supplies purified air to the face piece. APRs only filters particulates; smoke, heat, and hazardous gases may still be inhaled: (a) Do NOT use in atmospheres containing less than 19.5% oxygen. (b) Do NOT use in atmospheres immediately dangerous to life and health (IDLH). (c) Do NOT exceed maximum use concentrations established by regulatory standards. (d) Do NOT use when concentrations of contaminants are unknown. Two cartridges are available to use with the PAPR's: (a) Gas Mask Canister - A Chemical, Biological, Radiological, Nuclear, and high yield Explosives (CBRNE) which protects against chloroacetophenone, chlorobenzylidene, and particulates. (b) Optifilter XL (Type H) - A HEPA P100 particulate filter that is 99.97% efficient against all aerosols, oily and non-oily. This filter is effective against particulates such as dusts and mists but not toxic gases or vapors. CBRNE cartridges can be used for a maximum of 8 hours. HEPA P100 cartridges may be used as long as they pass flow tests. Replacement cartridges can be obtained through the Respiratory Protection Team. 908.4.5 USE OF CARTRIDGE RESPIRATORS Cartridge respirators are a type of air-purifying respirator. They may be fitted with mechanical pre-filters or combination cartridge/filter assemblies for use in areas where gases, vapors, dusts, fumes, or mists are present. The correct cartridge must be selected prior to use. A Company Officer or IC may specify the use of cartridge respirators in situations where the use of an SCBA or a full-face respirator is not necessary. These incidents may include vegetation fires, exposure to a patient with a communicable disease, and certain other incidents. Cartridge respirators shall not be used if there is a potential for an oxygen-deficient atmosphere or a risk of exposure to the member's face or eyes. Chesapeake Fire Department Policy Manual Respiratory Protection Program Copyright Lexipol, LLC 2023/04/01, All Rights Reserved.Published with permission by Chesapeake Fire Department Respiratory Protection Program - 5 Cartridge respirator filters shall be replaced whenever: • The wearer begins to smell, taste, or be irritated by a contaminant. • The wearer begins to experience difficulty breathing due to filter loading. • The cartridges or filters become wet. • The expiration date on the cartridges or canisters has been reached. 908.4.6 TRAINING Members should not use respirators unless they have completed the mandatory training requirements for the selected device (see the Respiratory Protection Program ). 908.5 EQUIPMENT ACQUISITION AND SPECIFICATIONS 908.5.1 SCBA REQUIREMENTS Chesapeake Fire Department's SCBA shall meet the standards found in the most current National Fire Protection Association (NFPA) publication and approved for use by NIOSH. Chesapeake Fire Department The Chesapeake Fire Department shall use only the respirator manufacturer's NIOSH-approved breathing-gas containers, marked and maintained in accordance with the quality assurance provisions of the NIOSH approval for the SCBA as issued in accordance with the NIOSH respirator certification standard at 42 CFR 84.1 et seq. 908.5.2 COMPRESSED BREATHING AIR Compressed breathing air used in SCBA should meet at least the requirements for Grade D breathing air as described in the American National Standards Institute (ANSI) Compressed Gas Association Commodity Specification for Air (G-7.1-2018). 908.6 RESPIRATOR FIT TESTING Fit tests are used to qualitatively or quantitatively evaluate the fit of a respirator on an individual. Each new member shall be fit tested before being permitted to use SCBA in a hazardous atmosphere. Fit tests may only be administered by persons determined to be qualified by the program administrator. After initial testing, fit testing shall be repeated: (a) At least once every 12 months. (b) Whenever there are changes in the type of SCBA or facepiece used. (c) Whenever there are significant physical changes in the user (e.g., obvious change in body weight, scarring of the face seal area, dental changes, cosmetic surgery, any other condition that may affect the fit of the facepiece seal). Chesapeake Fire Department Policy Manual Respiratory Protection Program Copyright Lexipol, LLC 2023/04/01, All Rights Reserved.Published with permission by Chesapeake Fire Department Respiratory Protection Program - 6 908.6.1 RESPIRATOR FIT TESTING PROCEDURES Fit testing is to be done only in a negative-pressure mode. If the facepiece is modified for fit testing, the modification shall not affect the normal fit of the device. Such modified devices shall only be used for fit testing and not for field use (29 CFR 1910.134; 16 VAC 25-60-30; 16 VAC 25-90-1910). Employees shall be fit tested at least annually, or more frequently if they are assigned a different respirator or if they experience a physical condition that could affect respirator fit. Additional testing may be required (see Respiratory Protection Program ). 908.6.2 FIT TESTING RECORDS The Training Director shall be responsible for maintaining records of all fit testing. Current fit test records shall be retained as required by the department records retention schedule, but in all cases at least until the next fit test is administered. Fit test records shall include: (a) Name of person tested. (b) Test date. (c) Type of fit test performed. (d) Description (e.g., type, manufacturer, model, style, size) of the respirator tested. (e) Results of fit tests (e.g., quantitative fit tests should include the overall fit factor and a printout or other recording of the test). (f) The written guidelines for the respirator fit testing program, including pass/fail criteria. (g) Instrumentation or equipment used for the test. (h) Name or identification of test operator. 908.7 RESPIRATOR MEDICAL EVALUATION QUESTIONNAIRE All members who are required to use respiratory protection must complete a medical evaluation questionnaire upon initial fit testing and annually thereafter as well as if any of the following conditions arise between annual tests (29 CFR 1910.134; 16 VAC 25-60-30; 16 VAC 25-90-1910): (a) A member reports medical signs or symptoms that are related to his/her ability to use a respirator. (b) A Physician or Licensed Health Care Professional (PLHCP), supervisor or the respirator program manager informs the employer that an employee needs to be reevaluated. (c) Information from the respiratory protection program, including observations made during fit testing and program evaluation, indicates a need for an employee reevaluation. (d) A change occurs in workplace conditions (e.g., physical work effort, protective clothing, temperature) that may result in a substantial increase in the physiological burden placed on an employee. The questionnaires will be reviewed by a PLHCP selected by the Department to determine which, if any, members need to complete physical examinations. Chesapeake Fire Department Policy Manual Respiratory Protection Program Copyright Lexipol, LLC 2023/04/01, All Rights Reserved.Published with permission by Chesapeake Fire Department Respiratory Protection Program - 7 The Training Director shall be responsible for maintaining records of all respirator medical evaluation questionnaires and any subsequent physical examination results. 908.8 SCBA INSPECTION, MAINTENANCE, AND STORAGE Prior to each shift, members are required to physically inspect and operate all SCBA and respirators that are on frontline fire apparatus. If the equipment is not in daily use, it should be inspected at least once a week and after each cleaning. Inspection should include but is not limited to: (a) All alarm devices on the SCBA should be tested for proper operation. (b) Any SCBA or respirator that is not operating properly or is below department standard air volume shall be taken out of service immediately until the problem is remedied. (c) Rubber facepiece: 1. Excessive dirt 2. Cracks, tears, holes 3. Distortion from improper storage 4. Cracked, loose, or scratched lenses (full facepiece) 5. Broken or missing mounting clips (d) Head straps: 1. Breaks or tears 2. Loss of elasticity 3. Broken or malfunctioning buckles or attachments 4. Excessively worn serrations of the head harness which might allow the facepiece to slip (e) Inhalation and exhalation valves: 1. Detergent residue, dust particles, or dirt on the valve seal 2. Cracks, tears, or distortion in the valve material or valve seal 3. Missing or defective valve covers (f) Filter elements: 1. Proper filter for the hazard 2. Approved designation (NIOSH) 3. Missing or worn gaskets 4. Worn thread 5. Cracks or dents in filter housing 908.8.1 MAINTENANCE, INSPECTION, AND ANNUAL SERVICE Members should thoroughly clean and sanitize all SCBA and respirators after each use. Chesapeake Fire Department Policy Manual Respiratory Protection Program Copyright Lexipol, LLC 2023/04/01, All Rights Reserved.Published with permission by Chesapeake Fire Department Respiratory Protection Program - 8 Respirators should be cleaned and sanitized according to manufacturer recommendations. All partially empty bottles should be replaced with full bottles. Members should perform the inspections noted above before placing an SCBA or respirator back in service. Every SCBA shall be inspected monthly by the Department and serviced on an annual basis by individuals who have been trained and certified by the SCBA manufacturer to perform such annual servicing. SCBA bottles shall be hydrostatically tested pursuant to applicable federal regulations, state standards, and manufacturer recommendations. All maintenance and inspection mandates of 29 CFR 1910.134 shall apply. 908.8.2 STORAGE Respirators in storage shall be protected against: • Dust. • Sunlight. • Heat. • Extreme cold. • Excessive moisture. • Damaging chemicals. Freshly cleaned respirators can be stored in reusable plastic bags or in a storage cabinet. Care must be taken so that distortion of the rubber or elastic parts does not occur. Respirators shall not be stored in lockers or vehicles unless the respirators are stored in individual containers and are protected from damage. All filters, cartridges, and canisters shall be properly labeled and color-coded with NIOSH approval labels. Labels shall not be removed and must remain legible. 908.8.3 FLOW TESTING The Department shall conduct annual flow testing on all SCBA. A flow test, also known as a performance test, ensures that the SCBA is performing to the manufacturer's specifications. Unlike basic inspections and functional testing, flow testing requires specialized equipment. The Department shall use NFPA standards or the SCBA manufacturer's requirements for flow testing, whichever is more stringent. Exposing SCBA to extreme temperatures, water, or chemicals can degrade SCBA performance. If an SCBA is exposed to any type of corrosive material that could lead to a component failure, it should be sent to a certified SCBA technician for testing. If a member suspects that an SCBA has been compromised or damaged, a flow test should be conducted to ensure that it is in good working order. All annual flow testing must be performed by a certified SCBA technician. Chesapeake Fire Department Policy Manual Respiratory Protection Program Copyright Lexipol, LLC 2023/04/01, All Rights Reserved.Published with permission by Chesapeake Fire Department Respiratory Protection Program - 9 908.9 EXPOSURES Any member who is exposed to a hazardous atmosphere should immediately leave the room or area and move to an area containing fresh, uncontaminated air. Physical symptoms of hazardous atmosphere exposure may include but are not limited to: • Difficulty breathing. • Dizziness, headache, or other distress symptoms. • A sense of irritation. • A smell or taste of contaminants. If a member feels ill or impaired in any way, a supervisor should be notified and emergency medical personnel summoned if not already available on-scene. Any time there is a doubt about the need for medical care, medical care shall be obtained. Any injury or exposure must be documented on an injury reporting form. Under most circumstances, the exposed member should not drive a vehicle. An attempt should be made to identify the exposure agent by questioning the facility representative or by reviewing the hazardous materials inventory. A supervisor should attempt to make this determination. If possible, a Safety Data Sheet for the exposure agent should be obtained.