IMCA Safety Flash 12/24 June 2024 PDF
Document Details
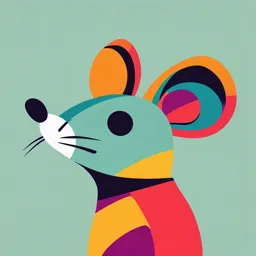
Uploaded by IntelligibleBeige
null
2024
Tags
Summary
This document is an IMCA Safety Flash from June 2024, detailing safety procedures for cargo transfer, welding operations, and the handling of hydrogen sulfide. It highlights common safety issues and provides recommendations for safe practices in an offshore environment.
Full Transcript
Safety Flash 12/2...
Safety Flash 12/24 – June 2024 IMCA Safety Flashes summarise key safety matters and incidents, allowing lessons to be more easily learnt for the benefit of all. The effectiveness of the IMCA Safety Flash system depends on members sharing information and so avoiding repeat incidents. Please consider adding [email protected] to your internal distribution list for safety alerts or manually submitting information on incidents you consider may be relevant. All information is anonymised or sanitised, as appropriate. 1 Swinging load after loss of position What happened During backloading of an empty refrigerated container to a Pipe Supply Vessel (PSV), adverse weather conditions, combined with technical issues and the effect of high thrust wash, resulted in a loss of position of the PSV and an uncontrolled swinging load. There was no damage to equipment and no-one was harmed. This event will also appear as an IMCA DP Incident report. What went wrong Sudden gusts of wind of around 40 knots created high external forces, which resulted in an increased thruster wash towards the PSV, which caused the PSV to lose position; The PSV’s azimuth thruster lost its running DP signal, contributing to the loss of position; The PSV was operating outside its Activity Specific Operation Guidelines (ASOG); The operational limits of PSVs operating alongside were not considered in the Activity Specific Operation Guidelines (ASOG); Container on deck No-one stopped the job: the operation wasn’t stopped despite alarms indicating the PSV was outside defined operational limits. Lessons to learn Review any (project specific) ASOG to include vessel to vessel operations and the effect that thruster wash can have on vessels alongside; Review and update procedures for the lifting of cargo to/from PSVs to reflect the potential for loss of position; Ensure personnel responsible for DP operations review and consider the Container swinging requirements of the ASOGs and document their review process; IMCA store terms and conditions (https://www.imca-int.com/legal-notices/terms/) apply to all downloads from IMCA’s website, including this document. IMCA makes every effort to ensure the accuracy and reliability of the data contained in the documents it publishes, but IMCA shall not be liable for any guidance and/or recommendation and/or statement herein contained. The information contained in this document does not fulfil or replace any individual’s or Member's legal, regulatory or other duties or obligations in respect of their operations. Individuals and Members remain solely responsible for the safe, lawful and proper conduct of their operations. © 2022 Page 1 of 6 Planning, risk assessing and adhering to operational guidelines and limits is crucial to ensuring safe cargo transfer operations. 2 Dropped welding fume extraction hood What happened During pipelay activities onboard a vessel, a welding fume extraction hood (which weighed Applicable 215kg) fell onto a work station below. A crew member working in the welding station was Life Saving struck from behind by the extraction hood causing them to fall to the ground. If the person Rule(s) had been struck in a different manner by the extraction hood, this could have resulted in Line of Fire a fatal injury. Extraction hood above firing line Extraction hood falling towards person beneath What went wrong The fume extraction hood was an in-house modification, and the drawings were not in accordance with existing company procedures; The intended design consisted of the following: ̶ Primary Securing Method: A plate connecting the hood to the beam. The plate is secured to the hood via 6x M10 bolts and the plate secured to the beam by welding. ̶ Secondary Securing Method: One M20 bolt running through the beam and the hood. The hood was not installed as per the drawings (due to the design being misunderstood), which meant that it was secured ONLY by the secondary securing method – a single M20 bolt running through the beam and the hood; A dynamic load was placed upon the single fixing point which allowed the hood to rotate and flex, causing increased stress on the bolt, triggering this to crack and shear, resulting in the hood dropping; The hood had not been added to the vessel DROPS register and so had not been included in the annual DROPS surveys, nor inspected, since installation. Actions and lessons Ensure that in-house modifications are always conducted in accordance with local regulatory requirements, existing company procedures, and that a Management of Change process is followed if modifications are made; IMCA Safety Flash 12/24 Page 2 of 6 Have a through inspection of the vessel or worksite looking for potential dropped objects and plan to remove them where applicable; Look particularly for any unidentified modifications and ensure DROPS registers are updated as required. Members may wish to refer to: Person injured when chain hoist container failed at securing point Equipment found live: drawings incorrect for Lock-out/Tag-out 3 Carriage of Methanol - Dangerous Goods - without proper certification What happened? Applicable Life Saving Methanol was being transported from place to place offshore, without appropriate Rule(s) Dangerous Goods certification. Methanol is very flammable. The incident occurred during Work the refuelling of a LIDAR buoy at an offshore wind farm. This involved carrying methanol Authorisation cannisters on board a vessel, recovering the buoy, loading the methanol into the buoy, and redeploying the buoy. The vessel which carried out the work was not in possession of a Dangerous Goods Document of Compliance. What went wrong The vessel had standard FFE/LSA as a workboat but was ill-equipped to carry over 700 litres of methanol. The principal contractor who hired the vessel did not include carriage of methanol in a Risk Assessment and Method Statement and had cleared the vessel through their own vetting department. The issue was raised internally by the client who recorded it as a High Potential Near Miss given the flammable and toxic properties of methanol. Further investigation found that that this was “not an isolated incident” and that the use of workboats and smaller vessels to carry Class 3 DG for the purpose of refuelling LIDAR buoys had occurred in the industry with other developers. What was the cause There was no intent to mislead. The root cause seemed to be lack of awareness. Our member noted that amongst certain of their suppliers there was a perceived lack of awareness of the hazards posed by Dangerous Goods and of marine operations in general. Lessons and actions What lessons were learnt? Carriage of Methanol requires a DG DOC (or flag state exemption with certain mitigations in place); LIDAR buoys, when fully fuelled, are themselves classed as DG, and as such, ought to be carried only by vessels with DG DOC (as above); The offshore renewables industry has not fully appreciated the hazards of marine operations and the carriage of DG. See below, “Members may wish to refer to”. Importance of raising awareness within the offshore renewables industry, and also within the maritime industry, to remind vessel owners, vessel crew, charterers (including offshore renewable developers) of the requirements for the carriage of DG cargoes. Members may wish to refer to: Spillage of methanol during cargo operations The Carriage of Methanol in Bulk Onboard Offshore Vessels — Marine Safety Forum IMCA Safety Flash 12/24 Page 3 of 6 4 Personnel exposed to hydrogen sulphide during maintenance What happened Applicable Subcontractor personnel were exposed to a high concentration of Hydrogen Life Saving sulphide (H₂S) for a short period during maintenance work in a vessel’s Well Rule(s) Bypassing Confined Treatment System (WTS) room. The incident occurred during annual Safety Space Controls maintenance work being conducted on the system's acid filter units. When the upper vent valve on an acid filter unit was opened, the subcontractor supervisor noted a pressure release from the system and a strong smell. The valve was immediately closed, an “All Stop” called, the extraction fan unit turned on and the team exited the room (no alarms were activated). The subcontractor supervisor notified the company supervisor, who started to suspend the Permit To Work. During this period, the subcontractor supervisor made the decision to re-enter the room and open the acid filter vent slightly to check for pressure. At this point, the supervisor’s personal H₂S alarm sounded and highlighted the presence of H₂S at high concentration (357ppm), and the vessel H₂S alarm in the WTS room also sounded. Personnel evacuated the room and work was suspended. No personnel showed any symptoms nor suffered any adverse health effects. What went right The vessel’s H₂S alarm activated in the incident area; There was a good discussion and agreements with all parties on the bridge following vessel H₂S alarm; Once all parties had been made aware, the correct response was put in place to ensure situation was brought under Acid filter unit in WTS room control. What went wrong – what actually happened There was an unexpected pressure release when the vent valve was opened on acid filter unit; The “All Stop” did not work as intended – there was further uncontrolled action without appropriate consultation and assessment, and this led to exposure to H₂S. ̶ The subcontractor returned to work area after All Stop had been called. Vent valve on top of unit What should have happened? Safe completion of annual maintenance work with no potential for H₂S release because the system had been flushed with fresh water after last use. What was a surprise? The system’s pressure gauges had been broken for a long time and not fixed or replaced; Despite system being flushed and inspected after last project use, low lying water/chemical residue in the system allowed H₂S to form; Actions Be aware of any potential sources of H₂S at your worksite, specifically when working with chemical, sewage or seawater systems; Ensure that all personnel who might be involved fully understand the dangers of Hydrogen Sulphide; Clearly mark any areas that have been identified as a potential source of H₂S with warning signs; IMCA Safety Flash 12/24 Page 4 of 6 If anyone becomes aware of a potential H₂S release, STOP work, leave the area and report the situation immediately. Do not return to the area until it is proven to be safe. Members may wish to refer to: Hydrogen Sulphide detected in a bilge tank Loss of consciousness due to exposure to H₂S Case study: confined space fatalities due to Hydrogen Sulphide 5 MAIB: Person injured during lifting of compressor The UK Marine Accident Investigation Branch (MAIB) has published Safety Digest 1/2024, consisting of lessons from recent Marine Accident Reports. Applicable IMCA has reviewed the report and passes on to members some of the incidents Life Saving in the report. This is one of them. Rule(s) Safe Line of Fire Mechanical What happened Lifting A worker was crushed by heavy equipment under maintenance, when the vessel rolled slightly. On a very large vessel, a team of specialist contractors were working on a compressor in the engine room. The work required the use of chain blocks and other lifting equipment to lift the compressor which weighed 1865kg. This was further complicated by the compressor having an offset centre of mass. Contractor lying on deck to reach and The cable tray lifting point The lifting arrangements disconnect mounts The contractors were working alone without support from the vessel crew. The compressor was raised using two pieces of steel bar passed through the forklift guide arrangements at its base and then supported with three chain blocks. With the compressor suspended, one of the contractors lay on the deck to reach and disconnect the mounts beneath it. At the same time, the vessel began its scheduled departure in rippled sea conditions with the wind gusting to 30kts. Shortly after leaving the berth the vessel rolled slightly and the compressor tilted from its suspended position, crushing the contractor. The other contract workers quickly used the chain blocks to raise the compressor sufficiently for the contractor trapped beneath it to roll free with help. The alarm was raised and medical assistance soon arrived. The injured contractor was extracted from the engine room, stabilised in the ship's medical centre and subsequently airlifted to hospital. The contractor’s injuries included multiple rib fractures to both sides of their chest, a puncture to the chest wall into the pleural space and a fractured collarbone. What went wrong Post-incident examination of the lifting arrangements found that: IMCA Safety Flash 12/24 Page 5 of 6 Only one of two 980kg working load limit deckhead fixed rings had been used, along with lifting attachment points to a cable tray and a pipe bracket. Additionally, the chain blocks used for lifting the aft end of the compressor were hooked on to the chains of other chain blocks. The steel bars did not have any spreader arrangements and the wide forklift truck ‘lifting slots’ allowed movement of the bars. The workers ̶ Were working under a suspended load; ̶ Failed to assess or consider the risks involved of the load shifting when the vessel started moving; ̶ Using wholly unsuitable strong points from which to lift a load. Given the complicated lifting arrangement, and the weight of the compressor, this lift should have been subject to the development of a thorough lifting plan that included input from the vessel’s senior officers and shore-based technical staff. This would likely have identified the correct lifting method and equipment, as well as appropriate timing for the lift in respect to the vessel’s departure from port and the environmental conditions. Working in isolation, including as part of a team, can incur serious consequences. Lessons Lifting operations should be properly planned by a competent person under appropriate supervision and carried out in a safe manner – failure to do this nearly resulted in a fatality; Ensure you are familiar with the regulatory requirements and any relevant codes of practice or guidance before undertaking any lifting operations. Members may wish to refer to: IMCA HSS019 Guidelines for lifting operations Heavy equipment fell over during manual handling Lifting complex loads – offloading third party equipment IMCA Safety Flash 12/24 Page 6 of 6