IMCA Safety Flash 03/24 PDF
Document Details
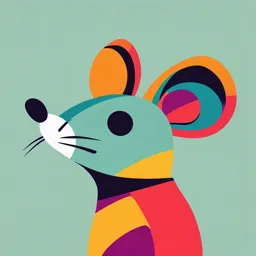
Uploaded by IntelligibleBeige
null
2024
Tags
Summary
This document details safety procedures and incidents in offshore operations. It highlights the importance of proper emergency procedures and equipment, and provides examples of issues found by the United States Bureau of Safety and Environmental Enforcement regarding offshore sites. The publication emphasizes the need for accurate documentation and up-to-date emergency response plans.
Full Transcript
Safety Flash 03/24 – Fe...
Safety Flash 03/24 – February 2024 IMCA Safety Flashes summarise key safety matters and incidents, allowing lessons to be more easily learnt for the benefit of all. The effectiveness of the IMCA Safety Flash system depends on members sharing information and so avoiding repeat incidents. Please consider adding [email protected] to your internal distribution list for safety alerts or manually submitting information on incidents you consider may be relevant. All information is anonymised or sanitised, as appropriate. 1 BSEE: Are your emergency procedures and your emergency equipment good enough? The United States Bureau of Safety and Environmental Enforcement (BSEE) has published Safety Alert 469 relating to readiness for medical evacuation and dealing with emergency hazards. What happened An inspection of offshore sites in the Gulf of Mexico revealed: Inconsistencies in the documentation and recording of injuries and illnesses; Procedural gaps and possible flaws in working practices; Problems with medical support and evacuation resources, All which could affect the emergency response capabilities of facilities. What went wrong Image: https://www.aed.com The BSEE found that: It took an average of 6.8 hours, according to the evacuation reports, from the time an incident occurred to the time evacuees arrived at medical facilities; Medical supplies for facility personnel were inadequate; Offshore workers did not know where first aid kits were located or how to properly use them; Emergency action plans were out of date, difficult for workers to find, and contained incorrect contact information. In some instances, the plan was only known to the person in charge; Many operators could not show proof they had carried out medical emergency drills on a regular basis, even though it was a requirement; Several facilities had equipment obstructing high-traffic areas, creating trip hazards, blocking escape routes, and posing safety risks; Rescue baskets (“Stokes litters”) were found inoperable at several facilities, inconveniently located, unsuitable for hoisting during emergencies, and rarely included in drills; Although all facilities except one had automatic external defibrillators (AEDs), the equipment was not easily accessible, and only medical staff had been trained on proper use of AEDs. What to do next The BSEE recommended: IMCA store terms and conditions (https://www.imca-int.com/legal-notices/terms/) apply to all downloads from IMCA’s website, including this document. IMCA makes every effort to ensure the accuracy and reliability of the data contained in the documents it publishes, but IMCA shall not be liable for any guidance and/or recommendation and/or statement herein contained. The information contained in this document does not fulfil or replace any individual’s or Member's legal, regulatory or other duties or obligations in respect of their operations. Individuals and Members remain solely responsible for the safe, lawful and proper conduct of their operations. © 2022 Page 1 of 6 Have a review and update of medical evacuation procedures, confirming the accuracy of all details, including personnel information, service providers, contact phone numbers, and related data; Ensure all crew are fully aware of the contents of emergency plans; Ensure robust quality checks and inventory management of emergency, first aid and medical equipment and supplies, including checking: ̶ Expiration dates of medicines and other materials; ̶ Evacuation chairs, rescue baskets, Stokes litters, stretchers etc; ̶ Defibrillators. Members may wish to refer to: Blocked emergency exit hatch High potential near miss: Dropped Paraguard stretcher during drill And finishing on a positive note: A CPR success story – “we saved a life that day” 2 High potential: navigation near offshore wind turbines What happened Applicable During survey operations, a chartered vessel entered a wind turbine safety zone on two Life Saving separate occasions whilst attempting to achieve the closest approach line. On the first Rule(s) Bypassing occasion, the breach was dealt with onboard the vessel with a safety stand down. On the Safety Controls second occasion, the vessel was immediately stood down and instructed to leave the work site until safe control measures (actions) had been established and agreed with the client. What went wrong The incident investigation established that the Officer on Watch (OOW) lost situational awareness and turned the wrong way – to port instead of to starboard. Given that the tide was running north to south, the OOW should have changed course to starboard for safe clearance of the wind turbine. Misjudgement resulted in a miscalculation of the vessel track, significantly contributing to the near miss incident. Agreed onboard procedures and standing orders were not followed. What was the cause? Officers while experienced, were new to this vessel. Consequently, the bridge team had not been working together long: ̶ Whilst the OOW was an experienced seafarer / officer, he was new to the vessel. He was not fully familiar with the manoeuvring characteristics of this vessel at slow speed whilst towing equipment; ̶ The Captain was also new to the vessel. The OOW overlooked the need to notify the Captain when control of the vessel was lost; The risks associated with close quarter navigation / working in close proximity to an offshore structure was not fully appreciated by the bridge team - who are responsible for the safe navigation of the vessel; The bridge toolbox talk was not properly implemented at shift change. IMCA Safety Flash 03/24 Page 2 of 6 Corrective Actions Taken / Recommendations Further requirement for enhanced bridge watchkeeping standards and voyage / survey route planning during close quarter navigation; Shift change toolbox talk and handover was realigned to include more detail and time to focus on confidence, awareness, communication and contingency scenarios; Closer assessment and vetting was required for crew competency, experience and suitability by our member and their vessel charter company during the vessel vetting procedure. This was to be checked and rechecked before starting a project. Members may wish to refer to MAIB: Workboat collision with wind turbine platform Yawing of wind turbine nacelle placed ship in line of fire Near miss: vessel approach to wind turbine tower 3 Failure of self-righting frame on Fast Rescue Craft (FRC) What happened? During a routine rescue drill the self-righting frame assembly fell off the Fast Rescue Craft (FRC) into the water while the FRC was transiting at approximately 15 knots. The self-righting frame was recovered by the FRC crew and returned to the vessel, where the cause of failure identified, and repairs completed. What went right The hazards and risks of the rescue drill had been identified and discussed in the Toolbox talk with all personnel involved; Appropriate protocol was followed, and Bridge crew were kept in communication throughout the recovery operation; The FRC was repaired promptly to Original Equipment Manufacturer (OEM) specification. What went wrong Self-righting frame pictured after incident A third-party inspection of the FRC had been completed two months before the incident. The inspection required only a visual check of the self- righting frame and did not include checking the integrity of the frame securing arrangements; Over time the securing arrangements were stressed and showed signs of galvanic corrosion. What lessons were learnt? The integrity of self-righting frames should be periodically inspected. This may involve the removal of the frame; Reviewed FRC inspection checklist and procedure The corroded bracket on the frame and FRC to ensure the self-righting frame is periodically removed and inspected. IMCA Safety Flash 03/24 Page 3 of 6 Members may wish to refer to: Lifting frame detached from fast rescue craft (FRC) A list of 14 safety flash incidents in which galvanic corrosion is a causal factor 4 Fall Protection – Defective Safety Harness What happened Applicable Life Saving During equipment recovery operations on the back deck of a vessel, a technician felt Rule(s) something unexpected around the Dorsal ‘D’ ring on the back of his safety harness. Working at Operations were immediately stopped. On inspection, several points of failure were Height identified on and around the area of the plastic back pad of the harness (see photo). Findings/Lessons Learned Before project mobilisation, the task of inspecting the harnesses was assigned to an untrained short service employee, which was contrary to company requirements; There was a failure to adhere to existing internal requirements and control mechanisms associated with the periodic inspection, maintenance and record keeping associated with fall protection equipment systems; There was no evidence that a pre-use inspection - as was required by the company - had been completed by the technician before putting on the harness and starting work; Wear and tear of the harness and metal components indicated exposure to adverse environmental conditions, suggesting that the harness had not been stored and maintained per the original equipment manufacturer’s instructions. 3M™ DBI-SALA® Delta™ Vest-Style Harness Actions taken (Model:1102000) Ensure thorough visual inspection of fall protection safety harnesses by an appropriately trained person. Safety harnesses found unfit for service should be quarantined or destroyed; Maintain a comprehensive fall protection equipment register; Always store fall protection equipment in an environment protected from the elements and in accordance with the original equipment manufacturer’s requirements. Members may wish to refer to Importance of inspecting fall protection equipment Near-miss: improper use of fall-arrest equipment leads to fall Getting fall arrest equipment right IMCA Safety Flash 03/24 Page 4 of 6 5 MSF: two dropped object incidents Incident 1 – dropped metal wedge A pin was required to be pulled on a hinge system for the dynamic gangway system on a Applicable W2W (walk-to-work) vessel. As part of this task metal wedges were used to hold some of Life Saving the gangway components in place. The job of pulling the pins was not going as expected Rule(s) due to space limitations, the effects of surface corrosion on the pins and the chosen Line of Fire method of pulling the pins. While pulling the pin out, the metal wedge in place was dislodged and fell between the gangway components, 13m to the deck below. No-one was underneath the gangway at the time. MSF Safety alert 23-17 IMCA Safety Flash 03/24 Page 5 of 6 What went wrong The metal wedges did not have a place to secure a tethering device; The method chosen to pull the pin was not optimal; Not all the tools could be secured from dropping and there was no collective dropped object arrest system to catch smaller tools or items; The aft area around the gangway was not fenced off and personnel could have walked underneath the drop zone; Simultaneous operations were taking place in the area on deck around the gangway and there was a risk of someone accidentally walking into the DROPS zone. Actions taken Modified the metal wedges to accept a tethering device; Investigated how a collective dropped object arrest system such as a net could be installed under the gangway for future work; Identified an optimal solution for pulling the pins on gangway; Improved guidance and training for personnel on barriering-off areas in a DROPS zone. Members may wish to refer to Dropped wooden block in conductor support frame Dropped object near-miss: small parts falling from crane rest Incident 2 - Dropped Lightning Rod A lighting rod conductor mounted on top of a dynamic gangway tower for a Walk-To-Walk vessel was found lying on the deck below the tower. No personnel onboard the vessel observed or heard the object fall. The potential for serious injury existed due to: The location of the dropped area (deck is frequented by personnel); The weight of the object (1.5kg) and the distance it fell (26m). What went wrong There was no obvious damage to the rod or fittings, it is assumed that the fittings loosened / unscrewed over time. The incident presents immediate causes such as: Impact of rough or bad weather on the rod securing connections; Lack of inspection/maintenance on the securing of the rod; Design deficiency in terms of a secondary securing mechanism for the rod. Actions taken Ensure checking of lightning rod conductor fittings and other similar fittings such as lights, cameras, wind sensors etc are included in planned maintenance schedule; Install a secondary securing mechanism where necessary. Members may wish to refer to Lightning Conductor Fell – Dropped Object Near Miss Flood light dropped to deck – corrosion IMCA Safety Flash 03/24 Page 6 of 6