Radiographic Film Reviewer PDF
Document Details
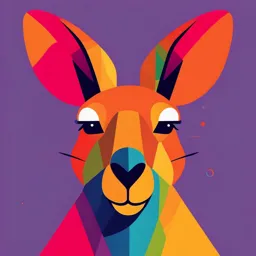
Uploaded by SuitableSparrow8325
Tags
Summary
This document provides an overview of radiographic film, covering its structure, components, historical development, and various types. It details the construction, materials, and characteristics of different types of films, such as screen film, non-screen film, mammography film, and video film. The content explores the historical evolution and current applications of the films.
Full Transcript
Radiographic Film Reviewer Film Construction Radiographic film consists of a base and an emulsion, similar to photographic film but with specific quality control and spectral response requirements. It is manufactured in extremely clean facilities to avoid contaminants that could impact image quali...
Radiographic Film Reviewer Film Construction Radiographic film consists of a base and an emulsion, similar to photographic film but with specific quality control and spectral response requirements. It is manufactured in extremely clean facilities to avoid contaminants that could impact image quality. Key Components: 1. Overcoat: Protective layer. 2. Emulsion: Light and x-ray sensitive layer, 3-5 μm thick. 3. Adhesive Layer: Binds the emulsion to the base. 4. Base: Supports the emulsion, 150-300 μm thick. Base Foundation: Provides a rigid, fracture-resistant structure. Material: Made of polyester for dimensional stability, maintaining size and shape during use and processing. Properties: Semirigid, lucent, and nearly transparent. Blue dye is often added to reduce eyestrain and enhance diagnostic accuracy. Historical Development: Glass Plate: Original material, used until World War I. Cellulose Nitrate: Introduced during World War I, but flammable. Cellulose Triacetate: Introduced in the mid-1920s, safer but less stable. Polyester: Introduced in the 1960s, stronger and more stable. Emulsion Composition: Homogeneous mixture of gelatin and silver halide crystals. Gelatin: High-quality, clear, and porous, extracted from calf skins. Silver Halide Crystals: Made by dissolving metallic silver in nitric acid, then forming silver bromide crystals through chemical reaction. Crystal Characteristics: Silver Bromide: Main component (98%), with some silver iodide. Shapes: Tabular grains are most common, providing large surface area and uniformity. Sensitivity Centers: Imperfections in crystals that help form latent images. Speed of Screen Film Sensitivity: Determined by silver halide grain size, shape, and concentration. Double Emulsion: Emulsion on both sides of the base for higher speed. Covering Power: Modern emulsions use less silver but achieve the same optical density. Screen Film Characteristics Contrast: Inversely proportional to exposure latitude. Films are available with different contrast levels, determined by the size and distribution of silver halide crystals. Spectral Matching: Films must be matched to the light spectrum emitted by intensifying screens (e.g., green-sensitive film for green-emitting screens). Crossover Control: Use of light-absorbing dyes to reduce image blurring from light crossover. Reciprocity Law: Exposure = Intensity x Time. Reciprocity law failure occurs with very long or short exposure times, affecting film speed and requiring technique adjustments. Non-Screen Film (Direct Exposure Film) Usage: Used without intensifying screens for imaging thin body parts with high subject contrast. Emulsion: Thicker than screen film, with higher concentrations of silver halide crystals.Speed: Determined by the concentration and number of silver halide crystals. Mammography Film Overview Mammography film has evolved from using industrial-grade double-emulsion direct-exposure film to specialty single-emulsion film designed for lower radiation doses. The single-emulsion film is used with a single radiographic intensifying screen, typically green-emitting terbium-doped gadolinium oxysulfide screens with green-sensitive film. Key Features Single-emulsion film: Reduces radiation dose compared to double-emulsion film. Antihalation coating: Special light-absorbing dye on the base opposite the screen reduces reflection (halation). This coating is removed during processing. Current technology: All available mammography screen-film systems use green-emitting screens with green-sensitive film. Video Film Overview Video-imaging films are increasingly popular due to advancements in computed tomography, digital radiography, ultrasound, and MRI. These films incorporate single emulsion and are typically exposed using multiformat or laser cameras. Key Features Spectral matching: Some films are spectrally matched for blue or green CRT emission, though most are orthochromatic and can be used with any CRT type. Single emulsion: Thin emulsion allows multiple images on a single sheet. Multiformat/Laser cameras: Enable various image sizes and multiple images per film. Independence from patient dose: Video film is sensitive and can quickly produce images matched to CRT spectral emiss Specialty Films Duplicating Film ○ Purpose: Duplicates existing radiographs. ○ Single-emulsion: Exposed to ultraviolet light for same-size copies. Subtraction Film ○ Use: Primarily in angiography, declining with digital fluoroscopy. ○ Types: One for subtraction mask preparation and one for superimposed images. ○ High contrast: Enhances existing subject contrast. Spot Film ○ Composition: Similar to cine film but larger. ○ Usage: Viewed directly on conventional view boxes. ○ Processing: Compatible with automatic processors for conventional radiographs. Cine Film ○ Use: Cinefluorography, mainly in cardiac catheterization. ○ Sizes: 16 mm and 35 mm. ○ Processing: Requires special movie film processing equipment. Dental X-ray Film ○ Sizes: Standard intraoral (1/4 x 1 5/8) and panoramic (5 x 12 inches). ○ Emulsion: Intraoral films are double-emulsion; panoramic films are single-emulsion. Handling and Storage of Films Key Considerations Handling: Avoid bending, creasing, and rough handling to prevent artifacts. Heat and Humidity: Store below 20°C (68°F) and in 40-60% humidity to prevent fog and ensure quality. Light: Store in complete darkness to avoid exposure artifacts. Radiation: Protect from ionizing radiation to prevent film fog Radiographic Intensifying Screens Overview Radiographic intensifying screens convert x-ray energy into visible light, significantly lowering patient dose and improving image capture efficiency. Key Layers 1. Protective Coating: Transparent to light, resists abrasion, reduces static. 2. Phosphor: Active layer emitting light upon x-ray stimulation. Made from rare earth elements like gadolinium, lanthanum, and yttrium. 3. Reflective Layer: Enhances efficiency by redirecting light toward the film. 4. Base: Provides mechanical support, usually made of polyester. Characteristics Luminescence: Emission of light upon stimulation. Screen Speed: Describes efficiency; ranges from 50 (detail) to 1200 (very fast). Radiation Quality: Effective atomic number of screens increases with x-ray tube potential. Image Processing: Ensures uniform emulsion effect, influencing screen speed. Conclusion Mammography and video films, along with specialty films, offer tailored solutions for various radiographic needs, with specific handling and storage requirements to maintain quality. Radiographic intensifying screens enhance image capture efficiency while minimizing patient dose, crucial for effective and safe diagnostic imaging. Radiographic Intensifying Screen Characteristic Radiation Quality As x-ray tube potential increases, the intensifying factor (IF) also increases.Screens have higher effective atomic numbers than films. At 70 kVp, the IF for a typical par-speed screen is 60, while for a rare Earth screen, it is 150. Image Processing Light exposure affects only the superficial layers of the film emulsion. X-ray exposure affects the emulsion uniformly. Excessive developing time can lower the IF. Temperature Screens emit more light per x-ray interaction at lower temperatures. IF decreases at higher temperatures. Image Noise Appears as a speckled background, often occurring with fast screens and high-kVp techniques. Noise reduces image contrast. Rare Earth screens have higher detective quantum efficiency (DQE) and conversion efficiency (CE). Spatial Resolution Limited by the effective focal spot size. Spatial resolution is measured in line pairs per millimeter (lp/mm). Direct exposure film can resolve 50 lp/mm, while very fast screens can resolve 7 lp/mm, and fine-detail screens can resolve 15 lp/mm. Spatial resolution improves with smaller phosphor crystals and thinner phosphor layers. Screen-Film Combinations Screens and films are manufactured for compatibility. Screens are nearly always used in pairs, with double-emulsion film. Proper selection and handling of screen-film combinations provide several advantages, including flexibility in kVp selection, spatial resolution, and reduced patient dose. Radiographic Exposure Calcium tungstate screens, introduced by Thomas Edison in 1896, exhibit only 5% CE. Light emitted by calcium tungstate screens is absorbed well by conventional radiographic film. Rare Earth Screens Made from elements with atomic numbers 57 to 71, including gadolinium, lanthanum, and yttrium. These screens perform at several speed levels without loss of spatial or contrast resolution. Higher x-ray absorption and efficient conversion of x-ray energy into light are key characteristics. Absorption and Conversion Efficiency Rare Earth screens exhibit better absorption properties than calcium tungstate screens in the energy range of 35 to 70 keV. CE of rare Earth phosphors is approximately 20%, compared to 5% for calcium tungstate. Each rare Earth screen has an absorption curve characteristic of its phosphor. Important Physical Characteristics Rare Earth screens have higher DQE and CE than calcium tungstate screens. Absorption properties vary with the x-ray energy and the phosphor material used. Key Points Higher effective atomic numbers in screens increase relative absorption with increasing kVp.Temperature and image processing techniques can affect the IF and image quality.Rare Earth screens provide higher speed and efficiency with better absorption and conversion properties compared to calcium tungstate screens.