Forms, Scaffolding and Staging PDF
Document Details
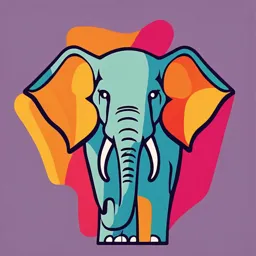
Uploaded by BestSellingKrypton799
OLFU QC Civil Engineering Faculty
Engr. Pheby M. Moog
Tags
Summary
This document discusses different formwork materials used in construction, including timber, plywood, steel, aluminum, plastics, magnesium, and fabric. It analyzes their respective advantages and disadvantages. For example, timber is a traditional and economical formwork material but may absorb water from wet concrete, reducing its strength.
Full Transcript
PROPOSED 2-STOREY RESIDENCE FORMS, SCAFFOLDING AND STAGING Prepared by: ENGR.PHEBY M. MOOG OLFU QC CIVIL ENGINEERING FACULTY Different Formwork Materials Different formwork materials and their advantages and disadvantages are discussed below. Timber ...
PROPOSED 2-STOREY RESIDENCE FORMS, SCAFFOLDING AND STAGING Prepared by: ENGR.PHEBY M. MOOG OLFU QC CIVIL ENGINEERING FACULTY Different Formwork Materials Different formwork materials and their advantages and disadvantages are discussed below. Timber Plywood Steel Aluminum Plastics Magnesium Fabric Timber as Formwork Material Timber is the most used material for formwork. Timber logs, lumber etc. are used as bracing members from ancient times. So, the Timber formwork is also called as traditional formwork. It is most economical material used for formwork. This is used in sites as formwork material for number of years so, the method of constructing timber framework is well known to the workers. Advantages Timber can be cut into any required size easily. Timber is light in weight, and it can be handled easily. Timber has good thermal resistance which prevents the damage of concrete in colder regions. It is easy to understand the construction method of timber formwork hence, skilled workers are not necessary. It is easy to replace the damaged parts of timber forms. Timber formwork can be easily dismantled. Disadvantages Dry timber may absorb water from wet concrete which result in the reduction of strength in concrete structure. Wet timber having high moisture content compress the wet concrete and forms cracks in the structure and grout may leaked through joints when shrinking occurs. Timber forms have limited usage. So, they cannot be useful for more times. Plywood as Formwork Material Plywood which is a manufactured product of timber is also used for formworks. It consists number of veneer sheets or plies in layers. Now a days, the use of plywood formwork increases especially for facing panels. The reason behind it is that the plywood formwork provides smooth finish when compared to normal timber formwork. Hence, finishing cost may reduce by the use of plywood. For formwork, special type of plywood called exterior plywood is used. The veneer sheets of exterior plywood are bonded with strong adhesive to make it watertight. The plywood boards are available in thicknesses from 7mm to 32mm. In general, plywood of size 1220 x 2440 and 18mm thick boards are sufficient for most of the works. For curved structures, special types of plywood with sufficient thickness are also available Advantages Plywood can also be cut into required size easily. Plywood Strong, durable and light in weight. Provides smooth finish on the surface. Very Large size plywood sheets are available which makes the construction of formwork quicker and easier. Curved formworks can also be prepared using plywood. When compared to timber, it gives more number of reuses. Disadvantages When compared to timber it is costly. Thin plywood sheets cannot sustain the weight of concrete they may bow out if proper thickness is not provided. Steel as Formwork Material Steel can also be used as formwork material. It is very costly, but it can be used for a greater number of times than others. They provides excellent finish to the concrete surfaces. For mass strictures like dams, bridges, etc. steel from work is so strong and safe. Advantages Steel forms are durable and stronger. Provides uniform and smooth surface finish to the structure. Great reusability. Easy to fix the formwork and also easy to dismantle. Disadvantages Cost is very much higher. It is heavy in weight and requires lifting equipment for large structure formworks. Corrosion will occur when there is a frequent contact with water. The size and shapes of forms available are limited. Aluminum as Formwork Material Aluminum formwork is used often for pre- fabricated formworks. It is getting more popular because of its light weight and good strength. It requires fewer supports and ties. Advantages Easy to fix and easy to dismantle. It can be handled easily because of its light weight. It can be re-used for many times. The walls and slabs of structures can be casted simultaneously. Monolithic crack free structures can be built using aluminum formwork. Disadvantages When the load reaches its maximum limit, the lighter sections may deflect. Architectural modifications are not possible when aluminum formwork is used. Plastics as Formwork Material Plastic is another type of formwork material which is used for small concrete structures or for complex portions of the structure. It is light in weight and durable for long periods. For complicated concrete structures, Glass reinforced plastics (GRP) and vacuum formed plastics are used. Advantages Plastic is light in weight and can be easily handled. Formwork for complex shaped structures can be prepared easily. Good resistant against water. The damaged plastic sheets can be recycled and useful to make new sheets. Good quality plastic has great re-usability. Disadvantages Plastic is weak against heat. It is costly material. It does not take much load when compared with others. Magnesium as Formwork Material Magnesium is another metal element which is used for formwork. Magnesium is not directly used for formwork and is used with the combination of oxygen atoms which forms magnesium oxide, usually called magnesia or MgO. Magnesium oxide boards or MgO boards are famous in some countries because of their multiple applications. MgO boards are available in required sizes and grades. Advantages Mgo boards are light in weight and easy to handle. They are fireproof and waterproof. Bio friendly boards cause no harm to the environment. They are strong to resist heavy loads. Disadvantages When Mgo boards meet wet concrete, the magnesium chloride present in MgO boards may dissolve and cause corrosion to the reinforcement. Skilled supervision is required for installation. MgO boards cannot sustain in humid conditions. They absorb moisture easily from atmosphere so, they are called as crying boards. Fabric as Formwork Material Fabric formwork is the modern technology in construction sector. Fabric can be mold into any required shapes which makes it more famous formwork for architectural purposes. Advantages It weighs very less when compared to any other formwork material. It is economical. Any complex shape can be constructed using fabric formwork. It is waterproof. Doesn’t affect the concrete properties. Easy to removal after the hardening of concrete. Disadvantages For installation skilled workers are required to form perfect and required complex shapes. Types of Scaffolding used in Construction: Single scaffolding Double scaffolding Cantilever scaffolding Suspended scaffolding Trestle scaffolding Steel scaffolding Patented scaffolding Single Scaffolding Single scaffolding is generally used for brick masonry and is also called as brick layer’s scaffolding. Single scaffolding consists of standards, ledgers, putlogs etc., which is parallel to the wall at a distance of about 1.2 m. Distance between the standards is about 2 to 2.5 m. Ledgers connect the standards at vertical interval of 1.2 to 1.5 m. Putlogs are taken out from the hole left in the wall to one end of the ledgers. Putlogs are placed at an interval of 1.2 to 1.5 m. Double Scaffolding Double Scaffolding is generally used for stone masonry so, it is also called as mason’s scaffolding. In stone walls, it is hard to make holes in the wall to support putlogs. So, two rows of scaffolding is constructed to make it strong. The first row is 20 – 30 cm away from the wall and the other one is 1m away from the first row. Then putlogs are placed which are supported by the both frames. To make it more strong rakers and cross braces are provided. This is also called as independent scaffolding. Cantilever Scaffolding This a type of scaffolding in which the standards are supported on series of needles and these needles are taken out through holes in the wall. This is called single frame type scaffolding. In the other type needles are strutted inside the floors through the openings and this is called independent or double frame type scaffolding. Care should be taken while construction of cantilever scaffolding. Generally cantilever scaffoldings are used under conditions such as When the ground does not having the capacity to support standards, When the Ground near the wall is to be free from traffic, When upper part of the wall is under construction. Suspended Scaffolding In suspended scaffolding, the working platform is suspended from roofs with the help of wire ropes or chains etc., it can be raised or lowered to our required level. This type of scaffolding is used for repair works, pointing, paintings etc.. Trestle Scaffolding In Trestle scaffolding, the working platform is supported on movable tripods or ladders. This is generally used for work inside the room, such as paintings, repairs etc., up to a height of 5m. Steel Scaffolding Steel scaffolding is constructed by steel tubes which are fixed together by steel couplers or fittings. It is very easy to construct or dismantle. It has greater strength, greater durability and higher fire resistance. It is not economical but will give more safety for workers. So, it is used extensively nowadays. Patented Scaffolding Patented scaffoldings are made up of steel but these are equipped with special couplings and frames etc., these are readymade scaffoldings which are available in the market. In this type of scaffolding working platform is arranged on brackets which can be adjustable to our required level. Forms Reinforced concrete structures need forms to construct its structural member such as columns, beams and slabs. Form is a temporary frame used in order for the structural member to produce the design section and shape. Forms must be simple and easy to install, to remove and to reinstall again and again. This is the reason why forms made up of wood such as plywood and phenolic boards nailed on lumber are the most common used forms. The materials used for forms of columns and beams can be computed with the help of table 5.1. The advantages of using wood as forms are: 1) Light in weight 2) Durable and with strength to contain the concrete 3) Easy to cut and to fasten 4) Easy to assemble and disassemble 5) Can be bought anywhere 6) Affordable and reusable 7) Can be dismantle and use for other purposes The kind of lumber used as a form are as follows: 1) Good lumber (rough lumber) 2) Secondhand lumber (slight cheaper but with some holes) 3) Coco-lumber (much cheaper, if the form will be used once or twice only) Steps in finding the forms for square and rectangular columns: 1) Compute the perimeter of the column P + 0.2m for lapping. 2) Multiply this value by the effective height of one column form times the pieces of columns to get the total area of the forms. 3) Divide the total area found in step 2 by the area of 1 plywood which is 2.88. 4) To get the board foot of lumber, multiply the pcs of plywood found in step 3 by the factor stated in table 5.1. 5) For column forms normally we used it twice, thrice or 4 times with additional Sample Problem: A building has 8 columns with sections of 30cm x 30cm each and 4.2m high. Using 1/2" ordinary plywood and 2” x 2” lumber. If the forms will be use twice, calculate the following a) The pcs of plywood needed b) The board foot of lumber needed b) The kilograms of nails needed Solution: a. P= (0.3 x 4 sides)+0.2 lapping =1.4m Area of Form(Plywood) = 1.4m x 2.4m x 8 columns = 26.88m2 No of Form(Plywood) needed= 26.88m2/2.88m2= 9.33 0r 10shts x 1.25% = 13shts of ½” x 4 x 8 Marine Plywood or Phenolic Board By Counting: Form sizes needed for 1 column: 2 pcs - 0.3m x 2.4m and 2pcs- 0.4m x 2.4m From 1 plywood which is 1.2 x 2.4m = 1.25shts No of Plywood for 8 columns= 1.25 x 8 =10shts x 1.25% = 13shts of ½” x 4 x 8 Marine Plywood or Phenolic Board Solution: B. Number of 2’’ x 2’’ x 10ft lumber From table 5.1 : 13shts x 20.33 = 264.29 bd.ft. 1- 2’’ x 2’’ x 10ft lumber =3.33bdft No. of pcs of 2’’ x 2’’ x 10ft lumber: 264.29/3.33= 79.287 or 80 pcs- 2’’ x 2’’ x 10ft lumber By Counting: For 1 column= 2 pcs of 2’’ x 2’’ x 10ft 2 x 8 x 1.25% = 80 pcs- 2’’ x 2’’ x 10ft lumber Solution: c. Nails (CWN) Nails Needed for 16 pcs- 30cm x 2.4m forms 1-1/2’’ CWN = 16 x 45pcs= 720pcs 2’’ CWN = 16 x 28pcs= 448pcs 3” CWN = 16 x 14pcs= 224 pcs Nails Needed for 16pcs- 40cm x 2.4m forms 1-1/2’’ CWN = 16 x 52pcs= 832pcs 2’’ CWN = 16 x 28pcs= 448pcs 3” CWN = 16 x 14pcs= 224pcs Solution: c. Nails (CWN) 1-1/2’’ CWN = (720+832)x 1.25/ 662= 2.93 or 3kgs 2’’ CWN = (448+446) x 1.25/ 397 = 2.82 or 3kgs 3” CWN = (224+224) x 1.25/146 = 3.84 or 4kgs MATERIAL SUMMARY 13shts- ½” x 4’ x 8 ‘ Plywood 80pcs- 2’’ x 2’’ x 10’ lumber 3kgs- 1-1/2’’ CWN 3kgs-2’’ CWN 4kgs- 3’’CWN Steps in finding the forms for rectangular beams: 1) Compute the perimeter of the column, P = 2d + b + 0.1m for lapping. 2) Multiply this value by the effective length of one beam times the pieces of beams to get the total area of the forms. 3) Divide the total area found in step 2 by the area of 1 plywood which is 2.88. 4) To get the board foot of lumber, multiply the pcs of plywood found in step 3 by the factor stated in table 5.1. 5) For beam forms, normally we require to pour the concrete monolithic, which means, all forms per level shall be completely used. Per reuse we add 50%. Sample Problem: A building has 10 pcs of 30cm x 40cm x 4m beams at 2nd floor level. Using 1/2" ordinary plywood and 2” x 2” lumber. Calculate the following quantity of materials for the formworks of the above mentioned beams. a) The pcs of plywood needed b) The board foot of lumber needed c) The kilograms of nails needed Solution: a. P= (0.4 x 2 sides) + 0.3 + 0.2 lapping =1.2m Area of Form(Plywood) = 1.2m x 4m x 10 columns = 48m2 No of Form(Plywood) needed= 48m2/2.88m2= 16.67 x 1.10% = 18.936shts or 19shts of ½” x 4 x 8 Marine Plywood or Phenolic Board By Counting: Form sizes needed for 1 beam: 1 pcs - 0.3m x 2.4m and 2pcs- 0.45m x 2.4m and 1 pcs - 0.3m x 1.6m and 2pcs- 0.45m x 1.6m From 1 plywood which is 1.2 x 2.4m = 1.67shts x 1.10= 1.837shts No of Plywood for 10 beams= 1.837x 10 =18.37sft or 19shts of ½” x 4 x 8 Marine Plywood or Phenolic Board Solution: B. Number of 2’’ x 2’’ x 10ft lumber From table 5.1 : 19shts x 18.66 = 354.54bd.ft. 1- 2’’ x 2’’ x 10ft lumber =3.33bdft No. of pcs of 2’’ x 2’’ x 10ft lumber: 354.54/3.33= 106.47 or 107 pcs- 2’’ x 2’’ x 10ft lumber By Counting: For 1 beam= 10.8 pcs of 2’’ x 2’’ x 10ft 10.80 x 1.10x10= 118.9 or 120 pcs- 2’’ x 2’’ x 10ft lumber Solution: c. Nails (CWN) Nails Needed for 40 pcs- 40cm x 2.4m forms 1-1/2’’ CWN = 40 x 52pcs= 2080pcs 2’’ CWN = 40 x 28pcs= 1120pcs 3” CWN = 40 x 14pcs= 560 pcs Nails Needed for 20pcs- 30cm x 2.4m forms 1-1/2’’ CWN = 20 x 45pcs= 900pcs 2’’ CWN = 20 x 28pcs= 560pcs 3” CWN = 20 x 14pcs= 280pcs Solution: c. Nails (CWN) 1-1/2’’ CWN = (2080+ 900)x 1.10/ 662= 4.95 or 5kgs 2’’ CWN = (1120+560) x 1.10/ 397 = 4.65 or 5kgs 3” CWN = (560+280) x 1.10/146 = 6.33 or 6.5kgs MATERIAL SUMMARY 19shts- ½” x 4’ x 8 ‘ Plywood 120pcs- 2’’ x 2’’ x 10’ lumber 5kgs- 1-1/2’’ CWN 5kgs-2’’ CWN 6.5kgs- 3’’CWN SCAFFOLDING AND STAGING Forms alone are not enough to support the concrete mixture, they need additional supports of braces, shoring, scaffolding and the like. Normally, the common practice of the estimator in dealing with staging and scaffolding is by lump sum considering that this item is time consuming and requires necessary experience of the estimator to visualize those that are not included in the plans such as the braces, the vertical and horizontal supports, the wedges, mudsill, out-reager and etc. Table 5.4 is very helpful in dealing with this item plus the topic in formworks of suspended slab. Sample Problem: Sample Problem: 4.0m 4.0m A reinforced concrete building has 9 columns with a clear height of 4m and with beams and slab as shown in the plan. Determine the required scaffolding under the following 4.5m specifications: 1) Scaffolding for columns using 2” x 3” lumber for vertical support and 2” x 3” lumber for horizontal support and braces. 2) Scaffolding for beams using 2” x 3” umber 4.5m for vertical support and 2” x 2” lumber for horizontal support 3) Forms and Scaffolding for slabs using 3/4" thick Phenolic board and 2” x 4” lumber Solution: a. Scaffolding for columns 4m x 9 columns = 36meters, say we use 12ft lumbers From table 5.4: Vertical Support = 36 x 7= 252bdft/ 5bdft= 51.8x 1.10= 56.98 or 57pcs- 2’’ x 3’’ x 12ft lumber Horizontal support = 36 x 21= 756bdft/4bdft=189x 1.10= 207.9 or 208pcs- 2’’ x 2’’ x 12ft lumber Diagonal Braces= 36 x 11.7= 421bdft/4bdft=105.25x 1.10= 115.78or 116pcs- 2’’ x 2’’ x 12ft lumber Solution: b. Scaffolding for beams (4.5m x 6)+(4m x 6)= 51 meters, say we use 12ft lumbers From table 5.4: Vertical Support = 51 x 6= 306bdft/ 5bdft= 61.2x 1.10= 67.32 or 68pcs- 2’’ x 3’’ x 12ft lumber Horizontal support = 36 x 7= 252bdft/4bdft=63x 1.10= 69.3 or 70pcs- 2’’ x 2’’ x 12ft lumber Solution: c. Scaffolding for Slab Area of Slab= 4.5m x 4m x 4= 72m2 For Support: say we use 12ft lumbers = 72 x 12.2= 878.4bdft/ 8bdft= 109.8x 1.10= 120.78 or 121pcs- 2’’ x 4’’ x 12ft lumber For Slab Forms: Area = 72m2 /2.88m2= 25 x 1.10 = 27.5 or 28shts 0f 3/4’’x 2’x4’ Marine Plywood Nails Needed for 56 pcs- 60cm x 2.4m forms 1-1/2’’ CWN = 56 x 61pcs= 3416pcs 2’’ CWN = 56 x 36pcs= 2016pcs 3” CWN = 56 x 18pcs= 1008 pcs 4” CWN = 56 x 18pcs= 1008 pcs Solution: c. Nails (CWN) 1-1/2’’ CWN = 3416x 1.10/ 662= 5.68 or 6kgs 2’’ CWN = 2016x 1.10/ 397 = 5.58 or 6kgs 3” CWN = 1008 x 1.10/146 = 7.79or 8kgs 4” CWN = 1008 x 1.10/68 = 16.30 or 16.5kgs MATERIAL SUMMARY 28shts-3/4” x 4’ x 8 ‘ Plywood 186pcs- 2’’ x 2’’ x 12’ lumber 68pcs- 2’’ x 3’’ x 12’ lumber 121pcs- 2’’ x 4’’ x 12’ lumber 6kgs- 1-1/2’’ CWN 6kgs-2’’ CWN 8kgs- 3’’CWN 16.5 kgs- 4’’CWN STEEL PIPE SCAFFOLDING Steel pipe Scaffolding can be used freely to prefabricate height and width according to the places and forms to install. Galvanized steel pipe with good strength makes durability and also leads economical delivery and storage. Standard scaffolding frames have 4’ (1.20m) with available in 3 different heights ranging from 0.90 to 1.70m. They are useful for access platforms and concrete support works. COMPUTATION SHEET 3. A. FORMWORKS & SCAFFOLDING 1. Footing 2. Footing Tie Beam 3. Columns (Ground and 2nd Floor) 4. Beams (2nd Floor and Roof Beams) 5. Suspended Slab 6. Stair B. DETAILS OF FORMWORKS AND SCAFFOLDING (A4 Bond paper – Drawn Manually or CAD or SketchUp or Rivet C. SUMMARY of Materials PROPOSED 2-STOREY RESIDENCE CONCRETE Prepared by: ENGR.PHEBY M. MOOG OLFU QC CIVIL ENGINEERING FACULTY CONCRETE – a mixture of cement paste, fine and coarse aggregates. The cement paste consists of cement and water which bind the fine and coarse aggregates. The fine aggregate in concrete consist of natural sand or of inert materials with similar characteristics, having clean, hard and durable, grains, free from organic matters or loam. The coarse aggregate should consist or crushed rocks of durable and strong qualities or clean and hard gravel. The size of the coarse aggregate varies from 20mm to 38mm (3/4in to 1-1/2in) in diameter. Water to be used for mixing concrete should be clean and free from injurious amount of oil, acids, alkalis , salt and other organic matters. PORTLAND AND POZZOLAN CEMENTS PORTLAND CEMENT- A hydraulic cement produced by pulverizing clinker , consisting essentially of hydraulic calcium silicates and usually containing calcium sulphate as an inter ground addition. TYPE I- most common and least costly. 28 days until it reach its full strength. TYPE II- moderate heat Portland cement for large concrete pours TYPE III- high strength TYPE IV- low heat like TYPE II TYPE V- a sulphate resisting Portland cement PORTLAND AND POZZOLAN CEMENTS POZZOLAN CEMENT- A hydraulic cement consisting of a mixture of Portland and definite amount of natural and artificial pozzolanic materials like volcanic tuff, shales, clay, fly ash, blast furnace, slag and burnt clay. TYPE P- use in general construction where high initial strength of the concrete before 28 days ins not required. TYPE 1P- early strength and required for more critical concrete works. ADMIXTURES CHARACTERISTICS OF CONCRETE WORKABILITY STRENGTH DURABILITY ECONOMY Depends on the ratio of water and cement. The ACI Requirements for Concrete; Fresh concrete shall be workable that could freely flow around the reinforcements to fill all the voids inside the form. Hardened concrete shall be strong enough to carry the design load. Hardened concrete could withstand the conditions to which it is expected to perform. Concrete should be economically produced. CLASSIFICTATION OF CONCRETE DESIGNED MIXTURE- the contractor is responsible in establishing the mixture proportion that will achieve the required strength and workability as specified in the plan, PRESCRIBED MIXTURE-the designing engineer specify the mixture proportion. The contractor’s responsibility is to provide a properly mixed concrete containing the right proportions as prescribed in the plan. PROPORTIONS OF CONCRETE CEMENT:SAND: CLASS GRAVEL STRENGTH APPLICTATION PROPORTION (psi) BEAMS, COLUMS, SHEAR CLASS AA 1:1-1/2:3 4000-3500 WALL, RET. WALLS CLASS A 1:2:4 3000-2500 FOUNDATION,COLUMN. BEAM, SOG CLASS B 1:2-1/2:5 2000-1500 FOUNDATION, SOG, LEAN CONCRETE CLASS C 1:3:6 1000-500 MORTAR, LEAN CLASS D 1:3-1/2:7