MR Training Compendium Diagnostics Part I PDF
Document Details
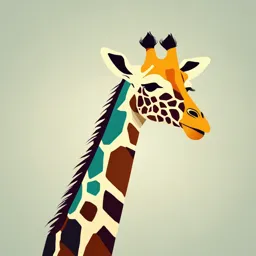
Uploaded by BestSellingBeige
null
2021
Tags
Summary
This document is a training compendium on transformer diagnostics, covering topics such as ohmic resistance, inductance, and capacitance. It is intended for premium service providers.
Full Transcript
Training compendium Premium Service Provider Diagnostics Part I Part I Version 02, 2021-01-19 II Part I Version 02 PSP Diagnostics Compendium Part I_V02_EN.docx Table of contents Table of contents.....................................
Training compendium Premium Service Provider Diagnostics Part I Part I Version 02, 2021-01-19 II Part I Version 02 PSP Diagnostics Compendium Part I_V02_EN.docx Table of contents Table of contents..............................................................................................................................II List of figures................................................................................................................................. VII List of tables................................................................................................................................... IX Formula........................................................................................................................................... X 1 Introduction......................................................................................................................... 11 1.1 "Formulae formulate facts."................................................................................................. 11 1.2 Mathematical presentation and conventions........................................................................ 11 2 Basics you need to know to understand electrical behavior of a transformer........................ 12 2.1 Ohmic resistance................................................................................................................ 12 2.1.1 Measuring circuit................................................................................................................. 12 2.1.2 Ohm's Law.......................................................................................................................... 12 2.1.3 Behavior............................................................................................................................. 12 2.1.4 Exceptions.......................................................................................................................... 12 2.2 Inductance.......................................................................................................................... 13 2.2.1 Measuring circuit................................................................................................................. 13 2.2.2 Behavior of settled sine wave voltage.................................................................................. 13 2.2.3 Behavior with constant DC voltage...................................................................................... 13 2.2.4 Behavior when switching on DC voltage.............................................................................. 14 2.2.5 Behavior when disconnecting DC voltage............................................................................ 15 2.2.6 Correlation of current and magnetic flux density.................................................................. 16 2.3 Capacitance........................................................................................................................ 18 2.3.1 Measuring circuit................................................................................................................. 18 2.3.2 Behavior of settled sine wave voltage.................................................................................. 18 2.3.3 Behavior with constant DC voltage...................................................................................... 18 2.3.4 Behavior when switching on DC voltage.............................................................................. 18 2.3.5 Behavior when disconnecting DC voltage............................................................................ 19 2.3.6 Development of a single-phase transformer equivalent circuit.............................................. 20 2.3.1 Initial situation..................................................................................................................... 20 2.3.2 Step 1: Winding resistors..................................................................................................... 21 2.3.3 Step 2: Leakage inductance................................................................................................ 22 2.3.4 Step 3: Transformation secondary to primary side............................................................... 23 2.3.5 Step 4: Introduction of main impedance............................................................................... 25 2.3.6 Typical quantity correlations of the elements of the equivalent circuit................................... 29 2.4 Behavior of the transformer................................................................................................. 30 2.4.1 Behavior of the transformer in the no-load case................................................................... 30 2.4.2 Behavior of the transformer shorted on the secondary side.................................................. 31 2.4.3 Correlations of time constants on open and short circuits.................................................... 33 2.5 Basic connection methods................................................................................................... 34 2.5.1 WYE connection................................................................................................................. 34 2.5.2 Delta connection................................................................................................................. 34 III Part I Version 02 PSP Diagnostics Compendium Part I_V02_EN.docx 2.5.3 Auto transformer................................................................................................................. 35 2.5.4 Zigzag operation................................................................................................................. 35 2.5.5 Vector groups...................................................................................................................... 35 3 General notes about measurements.................................................................................... 36 3.1 Checking the end positions................................................................................................. 36 3.2 Handling of (dead) pass-through positions and early end positions...................................... 36 3.3 End of work checks............................................................................................................. 36 4 Documentation.................................................................................................................... 37 4.1 Documentation on site......................................................................................................... 37 4.2 Serial numbers and numbers of tap-change operations....................................................... 42 4.3 Data backup........................................................................................................................ 42 4.4 Data storage....................................................................................................................... 42 5 Temperature....................................................................................................................... 44 5.1 General............................................................................................................................... 44 5.2 Measuring temperatures..................................................................................................... 44 5.3 Influencing factors............................................................................................................... 44 5.4 Correction factors for resistance measurements.................................................................. 45 5.5 Correction factors for dissipation factor (tan δ) or power factor (cos ) on the transformer insulation............................................................................................................................ 45 5.6 Correction factors for dissipation factor on bushings............................................................ 46 5.7 Temperature compensation for any other measurement...................................................... 46 6 Winding resistance.............................................................................................................. 47 6.1 Definition of terms............................................................................................................... 47 6.2 Components....................................................................................................................... 47 6.3 Influencing factors............................................................................................................... 47 6.4 Measuring principle............................................................................................................. 49 6.5 Work instructions regarding safety at work.......................................................................... 51 6.6 Converting resistances........................................................................................................ 51 6.6.1 Measurement in the neutral point: Phase conductor and string values................................. 51 6.6.2 Converting phase conductor values to string values in delta................................................ 52 6.7 Impact on other measurements........................................................................................... 53 6.8 Measuring devices at MR.................................................................................................... 53 6.8.1 Controlled voltage and current source, multimeter............................................................... 53 6.8.2 Ibeko DV-Power.................................................................................................................. 54 6.8.3 Series connection of different winding parts for safe magnetization...................................... 54 6.8.4 Improvisation: other voltage sources, series resistances...................................................... 55 6.9 Plausibility........................................................................................................................... 55 6.9.1 Typical process and dimensions.......................................................................................... 56 6.9.2 Further measurements to confirm the values in the case of doubts...................................... 57 6.9.3 Typical errors...................................................................................................................... 57 6.10 Temperature correction....................................................................................................... 58 IV Part I Version 02 PSP Diagnostics Compendium Part I_V02_EN.docx 7 Dynamic resistance measurement....................................................................................... 59 7.1 Definition of terms............................................................................................................... 59 7.2 Components....................................................................................................................... 59 7.3 Influencing factors............................................................................................................... 59 7.4 Measuring principle............................................................................................................. 60 7.5 Typical characteristics and behavior of different OLTC types............................................... 61 7.5.1 Pennant cycle operation...................................................................................................... 63 7.5.2 Flag cycle operation............................................................................................................ 64 7.5.3 Flag-pennant cycle operation.............................................................................................. 64 7.6 Evaluation of measured curves........................................................................................... 65 8 Transformer turns ratio........................................................................................................ 67 8.1 Basic principle..................................................................................................................... 67 8.2 Reference values................................................................................................................ 67 8.3 Influence of vector groups................................................................................................... 67 8.4 Phase displacement between primary and secondary side.................................................. 68 8.5 Phase shifters..................................................................................................................... 68 8.6 Measurement of excitation current....................................................................................... 68 8.7 Selection of measured voltage and connecting leads........................................................... 68 8.8 Premagnetization................................................................................................................ 69 8.9 Evaluation........................................................................................................................... 69 8.10 Improvisation options.......................................................................................................... 70 8.10.1 Two multimeter method....................................................................................................... 70 8.10.2 Multimeter method with three-phase supply......................................................................... 70 8.10.3 Multimeter method with three-phase supply and determination of vector group displacement........................................................................................................................................... 70 9 Short-circuit impedance....................................................................................................... 71 9.1 Definition of terms............................................................................................................... 71 9.2 Time or reason for the measurement................................................................................... 71 9.3 Components....................................................................................................................... 71 9.3.1 Test setup........................................................................................................................... 72 9.3.2 Connection diagram............................................................................................................ 72 9.3.3 Short-circuiting lead............................................................................................................ 72 9.3.4 Automatic short-circuit feature............................................................................................. 74 9.4 Estimate of measured current and transformer turns ratio.................................................... 74 9.5 Plausibility........................................................................................................................... 74 9.6 Special cases...................................................................................................................... 75 10 Frequency response of stray losses FRSL.......................................................................... 77 10.1 General............................................................................................................................... 77 10.1.1 Electromagnetic field........................................................................................................... 77 10.1.2 Eddy current losses............................................................................................................. 77 10.1.3 The Skin effect.................................................................................................................... 77 V Part I Version 02 PSP Diagnostics Compendium Part I_V02_EN.docx 10.1.4 The proximity effect............................................................................................................. 78 10.1.5 Effects................................................................................................................................. 78 10.1.6 Possibilities to reduce these effects..................................................................................... 78 10.2 Practical effects................................................................................................................... 79 10.3 Test setup........................................................................................................................... 79 10.4 Evaluation........................................................................................................................... 79 11 Insulation............................................................................................................................ 81 11.1 General............................................................................................................................... 81 11.2 Steps to perform................................................................................................................. 81 11.3 Polarization......................................................................................................................... 81 11.4 Measuring duration............................................................................................................. 81 11.5 Insulation quotients DAR 15/30, DAR 15/60 and PI............................................................. 82 11.6 Typical error sources........................................................................................................... 82 11.7 Evaluation........................................................................................................................... 83 11.8 Preparation......................................................................................................................... 83 11.9 Example for measured value recording............................................................................... 84 11.10 Template for measured value recording............................................................................... 85 12 Operation of the test equipment.......................................................................................... 86 12.1 General............................................................................................................................... 86 12.2 General principles............................................................................................................... 86 1.1.1 Regulating range settings.................................................................................................... 86 12.2.1 Automatic switching operations........................................................................................... 86 12.3 DV Power........................................................................................................................... 86 12.4 Omicron.............................................................................................................................. 87 12.4.1 Device and Primary Test Manager...................................................................................... 87 12.4.2 Database structure in Omicron Primary Test Manager......................................................... 88 12.4.3 Performing measurements and settings for the measurements............................................ 91 12.5 HIOKI.................................................................................................................................. 94 A Attachments........................................................................................................................ 95 Derivation: Converting phase conductor values to line to neutral values.............................. 96 Vector group compendium.................................................................................................. 98 A.2.1 Y(N) y(n)............................................................................................................................. 98 A.2.2 D d.................................................................................................................................... 100 A.2.3 Y(n) d................................................................................................................................ 102 A.2.4 D y(n)................................................................................................................................ 104 Transmission turns ratio: Multimeter method with three-phase supply and determination of vector group angle............................................................................................................ 106 A.3.1 Measurement.................................................................................................................... 106 A.3.2 Graphical calculation......................................................................................................... 106 A.3.3 Numerical solution............................................................................................................. 109 Factors, powers and names.............................................................................................. 112 VI Part I Version 02 PSP Diagnostics Compendium Part I_V02_EN.docx VII Part I Version 02 PSP Diagnostics Compendium Part I_V02_EN.docx List of figures Figure 1 – Drawing of measuring circuit of an ohmic resistance........................................... 12 Figure 2 – Drawing of measuring circuit of inductive resistance........................................... 13 Figure 3 – Charging a coil, current course........................................................................... 14 Figure 4 – Self-induction when disconnecting source current............................................... 15 Figure 5 – Circuit with N/C contact to interrupt source current.............................................. 15 Figure 6 – Hysteresis curve................................................................................................. 16 Figure 7 – Drawing of measuring circuit of a capacitive resistance....................................... 18 Figure 8 – Energizing process of a capacitance................................................................... 19 Figure 9 – Substitute diagram, single-phase, with two windings........................................... 20 Figure 10 – Substitute diagram, single-phase, with two windings and winding resistances... 21 Figure 11 – Schematic drawing of two windings on one core limb with stray and main fluxes........................................................................................................................................... 22 Figure 12 – Substitute diagram, single-phase, with two windings, winding resistance and leakage inductance............................................................................................................. 22 Figure 13 – Equivalent circuit, secondary quantities converted to primary side..................... 24 Figure 14 – Equivalent circuit, with ideal transformer........................................................... 25 Figure 15 – Equivalent circuit, single-phase, with ideal transformer equal in potential.......... 26 Figure 16 –Equivalent circuit, single-phase, with main inductance in reactance 𝑋h.............. 26 Figure 17 – Substitute diagram, single-phase, with main inductance and iron loss resistance........................................................................................................................................... 27 Figure 18 – Substitute diagram, single-phase, with winding resistance, leakage inductance and main impedance.................................................................................................................. 27 Figure 19 – Substitute diagram, single-phase and complete................................................ 28 Figure 20 – Substitute diagram, neglecting the secondary-side winding impedance............. 30 Figure 21 – Substitute diagram, single-phase, in no-load operation..................................... 31 Figure 22 – Single-phase equivalent circuit of a transformer shorted on the secondary side. 31 Figure 23 – Extended surroundings of the test tap............................................................... 39 Figure 24 – Immediate surroundings of the test tap............................................................. 40 Figure 25 – Detail of test tap................................................................................................ 41 Figure 26 – Screenshot with folder structure........................................................................ 43 Figure 27 – Single-phase equivalent circuit of no-load transformer with DC voltage source.. 49 Figure 28 – Single-phase substitute diagram of a transformer that is short-circuited on the secondary side, with DC voltage source for the point in time t = 0........................................ 49 Figure 29 – Singe-phase substitute diagram, current flow with DC current, secondary short circuit and in settled condition with t > 5 τ............................................................................ 50 Figure 30 – Single-phase substitute diagram; current flow with DC current, secondary short circuit and in settled condition with t → ∞............................................................................. 50 Figure 31 – Measurement in the neutral point: Phase conductor and string values............... 51 Figure 32 – Measurement in delta: Conversion of phase conductor values to string values.. 52 VIII Part I Version 02 PSP Diagnostics Compendium Part I_V02_EN.docx Figure 33 – Example of a delta connection measured in-between phases (UV, VW, WU) and converted to string values (UN, VN, WN)............................................................................. 53 Figure 34 – Winding resistance measurement with primary winding in series with secondary winding; example 1: Vector group YN yn0........................................................................... 54 Figure 35 – Winding resistance measurement with primary winding in series with secondary winding; example 2: Vector group YN d5............................................................................. 55 Figure 36 – Winding resistance with coarse tap connection, good match between reference and measurement............................................................................................................... 56 Figure 37 – Typical progress of winding resistance with reversing change-over selector...... 57 Figure 38 – Errors in the progress of winding resistance...................................................... 57 Figure 39 – DRM in three-phase substitute diagram............................................................ 61 Figure 40 – DRM in three-phase substitute diagram with short circuit on the same limb on the secondary side.................................................................................................................... 61 Figure 41 – DRM in the direction of more windings.............................................................. 62 Figure 42 – DRM sample graphs in direction of fewer windings........................................... 62 Figure 43 – DRM pennant cycle operation VACUTAP VV.................................................... 63 Figure 44 – DRM flag cycle operation OILTAP® M.............................................................. 64 Figure 45 – DRM flag-pennant cycle operation OILTAP® R................................................. 65 Figure 46 – Example diagram for excitation current during transformer turns ratio test......... 68 Figure 47 – Example measurement of voltage ratio with unfavorable proportions................. 69 Figure 48 – Single-phase short circuit on the same core limb in the single-phase equivalent circuit.................................................................................................................................. 71 Figure 49 – Measurement of short-circuit impedance using ammeter, voltmeter and voltage source................................................................................................................................. 72 Figure 50 – Short-circuit lead in neutral connection on the secondary side of the transformer, schematic drawing.............................................................................................................. 73 Figure 51 - Short-circuit lead on the secondary side of the transformer, lead made of wire... 74 Figure 52 – Single-phase, simplified substitute diagram during secondary short circuit........ 75 Figure 53 – Schematic representation of the skin effect in an electrical conductor................ 77 Figure 54 – Examples of conductors of a winding................................................................ 78 Figure 55 – Example of FRSL test results............................................................................ 79 Figure 56 – The database structure "Primary Test Manager" with four levels....................... 88 Figure 57 – Access to create a new job............................................................................... 89 Figure 58 – Load new location from database..................................................................... 90 Figure 59 – Manual measurements..................................................................................... 91 Figure 60 – Intersection points of voltages 1U – 1V / 2V and 1W – 1V / 2V........................ 106 Figure 61 – Intersection points of all seven voltages.......................................................... 107 Figure 62 – Determined secondary-side voltage triangle.................................................... 107 Figure 63 – Parallel shift of the angle bisector 2U in 1U..................................................... 108 IX Part I Version 02 PSP Diagnostics Compendium Part I_V02_EN.docx List of tables Table 1 – Insulation measurement examples autotransformer with PI and DAR................... 84 Table 2 – Insulation resistance primary, ladle furnace transformer as an example............... 84 Table 3 – Insulation resistance secondary, ladle furnace transformer as an example........... 85 Table 4 – Insulation resistance, template for measured value recording............................... 85 X Part I Version 02 PSP Diagnostics Compendium Part I_V02_EN.docx Formula ̅1 R Winding resistance primary, or resistance phase 1 ̅2 R Winding resistance secondary, or resistance phase 2 ̅3 R Resistance phase 3 ̅'2 R Winding resistance secondary, correlated to primary side ̅ X1σ Leakage reactance primary ' ̅2σ X Leakage reactance secondary, correlated to primary side ̅h X Reactance of main inductance ̅ FE R Iron loss resistance ̅W R ̅ W (warm) Ohmic resistance at temperature ϑ ̅k R ̅ k (cold) Ohmic resistance at temperature ϑ ̅ iso R Insulation resistance of transformer ̅W ϑ Temperature warm ̅k ϑ Temperature cold 𝐼0̅ No-load current I̅1 Current, primary or of phase 1 𝐼n̅ Rated current 𝐼m̅ Test current ̅k U Short-circuit voltage in no-load test u ̅k Relative short-circuit voltage ̅ 1n U Rated voltage primary ̅ 2n U Rated voltage secondary ̅ 2m U Measured voltage secondary ̅n U Rated voltage between two phases in three-phase transformer Z̅k Short-circuit impedance Z̅1 Impedance, primary or one Z̅2 Impedance, secondary or two 11/112 Part I Version 02 PSP Diagnostics Compendium Part I_V02_EN.docx 1 Introduction 1.1 "Formulae formulate facts." A physical phenomenon is observed, and a formula is used to describe the relationship. Therefore, a formula is not only a calculation rule but describes behavior when parameters change. Formulas can be used to describe and predict the behavior of different components relative to each other. 1.2 Mathematical presentation and conventions In the present document, components, voltages and currents are defined as mathematical quantities with angles. In other words: as vectors with absolute value and phase. Absolute ̅ 1 |. values are generally written with a vertical bar on each side of the complex quantity, e.g., |U In the present document, absolute values of complex quantities are presented without vertical bars. Therefore, the following convention applies: (1) ̅ 1 | = R1 |R To visualize this convention, the ohmic resistance, now presented as complex quantity, can be viewed: (2) ̅ = R ∢ 0° R Formula (2) should be read as follows: The complex quantity "ohmic resistance" has the absolute value of the ohmic resistance R with phase shift angle Zero. For reasons of clarity, the angle is normally omitted and only used where necessary. 12/112 Part I Version 02 PSP Diagnostics Compendium Part I_V02_EN.docx 2 Basics you need to know to understand electrical behavior of a transformer 2.1 Ohmic resistance Ohmic resistance is used to describe the conversion of electrical energy into heat that a component is expected to produce. 2.1.1 Measuring circuit I Uq ~ R UR Figure 1 – Drawing of measuring circuit of an ohmic resistance 2.1.2 Ohm's Law ̅R 𝑈 𝑅̅ = (3) 𝐼̅ 2.1.3 Behavior Current and voltage always show the same curve shape. There is no time delay. Resistance is the relation of current and voltage; the correlation has linear characteristics. This is expressed in Ohm's law, see formula (3). Depending on the materials used, temperature-dependent correlations can develop. The correlations relevant in this paper will be discussed in a separate chapter below. 2.1.4 Exceptions Voltage dependent resistors are an example for ohmic resistors that vary relative to one parameter. Here, behavior is not linear anymore. This is not discussed further as this application in transformers is not relevant here. 13/112 Part I Version 02 PSP Diagnostics Compendium Part I_V02_EN.docx 2.2 Inductance Inductance describes a physical property or a component. As described in Ampere's law, electric current produces a magnetic field. Periodic change of the magnetic field "induces" electric voltage in the same electric circuit, as defined in the law of induction. 2.2.1 Measuring circuit Iq Uq ~ L XL UL R Figure 2 – Drawing of measuring circuit of inductive resistance 2.2.2 Behavior of settled sine wave voltage Ohm's law applies here too. The sign X is introduced for reactance to differentiate it from ohmic resistance. On the basis of Ohm's law, the following results for reactance as well, and more specifically, for inductive reactance Figure 2 ̅L 𝑈 𝑋̅L = (4) 𝐼q̅ Inductive reactance of an inductance is based on the correlation ̅L = 2 𝜋 f L ∢ 90° X (5) and shows that inductive reactance does not only depend on inductance L but also on the frequency f which activates the inductance. The larger the frequency, the larger becomes inductive reactance. On inductances, fluctuating currents lag in phase by 90° from the applied voltage. 2.2.3 Behavior with constant DC voltage Formula (5) shows the correlation of inductive reactance and frequency. At frequency zero Hertz, inductive reactance reaches the value of zero Ohm. This again means that inductive reactances are not effective for DC currents in stabilized condition, and act like short-circuited conductors. 14/112 Part I Version 02 PSP Diagnostics Compendium Part I_V02_EN.docx 2.2.4 Behavior when switching on DC voltage On inductances, flowing current goes along with a magnetic field. This magnetic field contains energy that cannot change abruptly. Therefore, energy supply is necessary to build up a magnetic field. As consequence, when applying DC voltage, current builds up in an inductance according to the following formula: ̅q U t I̅L = ̅ (1 - e- Τ ) (6) R occurs. Current approaches in an e function from its initial value to a final value. The final value is determined by the applied voltage and the ohmic resistance that is effective in the circuit since, as discussed before, inductive resistance in stabilized condition has the value of 0 Ω. The relevant correlations are shown in the diagram in Figure 3. 1,2 1 I 5 , 99,33% 0,8 Current in A, Voltage in V Uq 0,6 I 1 , 63,21% IL 1τ 0,4 5τ 63,21 % 0,2 99,33 % 0 0 10 20 30 40 50 60 Time in s Figure 3 – Charging a coil, current course In this context, the time constant τ results from 𝐿 τ= ̅ (7) R This means that the time necessary for this process depends on two factors: 1. The total ohmic resistance effective in the circuit, and 2. the size of effective inductance. 15/112 Part I Version 02 PSP Diagnostics Compendium Part I_V02_EN.docx In general, these processes are considered to be completed after a time period of more than 5 τ. 2.2.5 Behavior when disconnecting DC voltage Assume an inductance with stabilized DC current, that is, from t = 30 s in Figure 4. 2,2 2 1,8 1,6 Voltage in V, Current in A 1,4 1,2 1 Uq 0,8 UL 0,6 IL 0,4 0,2 0 0 10 20 30 40 50 60 70 80 90 100 Time in s Figure 4 – Self-induction when disconnecting source current After 50 seconds, the circuit is interrupted using switch S1, as shown in Figure 5. Iq S1 Uq ~ L XL UL R IL Figure 5 – Circuit with N/C contact to interrupt source current Due to the magnetic field, this produces self-induction in the inductance, which is directed in opposite direction to the current change. This causes a very high voltage peak trying to keep up the current flow in this direction and decreasing from the initial value in an e function, see Figure 4 at t = 50. 16/112 Part I Version 02 PSP Diagnostics Compendium Part I_V02_EN.docx This physical effect can cause a hazard when carrying out measurements. Therefore it is very important to ensure that the measuring circuits are not interrupted. This can be ensured by installing grounding for work, which can take over the coil current when removing the test cables. To be very clear about this working instruction, let us emphasize the following two points one more time: 1. Before working on test objects, the test equipment must be disconnected or removed from the test object, and 2. Before changing measurement setups, grounding for work must be installed. 2.2.6 Correlation of current and magnetic flux density Current I flowing through a winding produces the magnetic field strength H. The following correlation applies 𝑛∗𝐼 𝐻 = (8) 𝑙 where the number of windings n and length l are design features of the winding. That is, for a given winding, the resulting magnetic field strength H is proportional to current I. If the winding is wound around an iron core, magnetic flux density B will develop in the iron core. As the correlation follows different formula depending on the direction, it is common practice to present it as diagram, see Figure 6. Figure 6 – Hysteresis curve The change of magnetic flux density B is not only dependent on the change of the magnetic field strength H but also on the respective starting point on the hysteresis curve. The area in the hysteresis curve is called hysteresis losses. This effect can have an impact on the measured results if the AC current used for the measurement is not sufficient to reach magnetic saturation. Therefore, the normally selected test current corresponds to 1.7 times the no-load current I0 of the transformer. 17/112 Part I Version 02 PSP Diagnostics Compendium Part I_V02_EN.docx As a general rule, specific demagnetization should be performed to start measurement in a defined way on hysteresis point "0". If demagnetization was performed even though it was not necessary, this does not influence the measurement. 18/112 Part I Version 02 PSP Diagnostics Compendium Part I_V02_EN.docx 2.3 Capacitance Capacitance is a physical property of a component. It defines the charge between two galvanically isolated charge carriers such as conductors, boards or foils. One conductor already forms a capacitance to ground potential. The same is true for two parallel conductors. 2.3.1 Measuring circuit Iq Uq ~ C L XC UC R Figure 7 – Drawing of measuring circuit of a capacitive resistance 2.3.2 Behavior of settled sine wave voltage Ohm's law applies here too, with the designations in accordance with Figure 7 ̅ U ̅C = C X (9) I̅q Capacitive reactance is based on the following correlation 1 (10) 𝑋̅C = ∢ -90° 2πfC This correlation shows that capacitive reactance does not only depend on capacitance C itself, but also on frequency f. The lower the frequency, the larger becomes the capacitive reactance. On capacitances, voltage and fluctuating currents are 90° out of phase, with current preceding voltage. 2.3.3 Behavior with constant DC voltage Formula (10) shows the correlation of capacitive reactance with frequency. It becomes clear that capacitive reactance has the value of ∞ Ω if frequency is 0 Hz. This again means that, for constant DC currents, capacitive reactances act like an interruption of the current circuit. 2.3.4 Behavior when switching on DC voltage On capacitances, building-up voltage is accompanied by an electric field. This electric field contains energy that cannot change abruptly. Therefore, energy supply is necessary to build up an electric field. As consequence, when applying DC voltage, voltage builds up in a capacitance according to the following formula: 19/112 Part I Version 02 PSP Diagnostics Compendium Part I_V02_EN.docx 𝑡 𝑈C = 𝑈q (1 − 𝑒 − 𝜏 ) (11) Starting from its initial value, voltage approaches its final value in an e function, see Figure 8. As mentioned above, the final value is determined by the applied voltage because no current flows over the effective ohmic resistance in the circuit, since capacitive resistance in settled condition has the value of ∞ Ω. 1,2 1 I 5 , 99,33% 0,8 Uq Voltage in V, Current in A 0,6 I 1 , 63,21% UC 1τ 5τ 0,4 63,21 % 99,33 % 0,2 0 0 10 20 30 40 50 Time in s Figure 8 – Energizing process of a capacitance In this context, the time constant τ results from 𝜏= 𝑅 ∗ 𝐶 (12) 2.3.5 Behavior when disconnecting DC voltage Assume a capacitance with settled DC current. Now if the circuit is interrupted using an NC contact, the stored load is retained, which means that the original voltage on the capacitor terminals is retained. If the two capacitor terminals are now shorted over a resistance, the capacitor will discharge conformant to an e function. Voltages that remain on a capacitor present a hazard when performing the measurements. Therefore, measured voltage should not be disconnected abruptly but turned down slowly, to allow the capacitor to discharge. Here too, groundings for work should be installed before changing the measurement setup. 20/112 Part I Version 02 PSP Diagnostics Compendium Part I_V02_EN.docx 2.3.6 Development of a single-phase transformer equivalent circuit The objective is to get a comparably simple substitute diagram, of which electrical behavior equals electrical behavior of a transformer. This will help to assess the transformer's behavior in various situations. In addition, it will help to find ways to influence the behavior. The entire behavior of a transformer must be reflected in the substitute diagram. Isolated consideration of single elements in the substitute diagram, and establishing any connection with physical components in the transformer is not intended and is affected by errors. 2.3.1 Initial situation Given is a single-phase transformer with primary and secondary winding as shown in Figure 9. I1 X'2 I2 σ U1 Z1 Z2 U2 Figure 9 – Substitute diagram, single-phase, with two windings 21/112 Part I Version 02 PSP Diagnostics Compendium Part I_V02_EN.docx 2.3.2 Step 1: Winding resistors The ohmic resistances actually existing in each of the coils act on the respective side only. Therefore it is allowed to shift these ohmic resistances to the respective supply lead, as shown in Figure 10. I1 R1 R2 I2 X1σ Z1 Z2 X'2 U1 U2 σ Figure 10 – Substitute diagram, single-phase, with two windings and winding resistances 22/112 Part I Version 02 PSP Diagnostics Compendium Part I_V02_EN.docx 2.3.3 Step 2: Leakage inductance What are leakage inductances? It is helpful here to look at the paths of the magnetic field: Φ2σ Φh Φ1σ L2 L1 Figure 11 – Schematic drawing of two windings on one core limb with stray and main fluxes The currents flowing in the windings generate magnetic fields. The total of these fields which includes both windings, will later be summarized as main flux Φh. The shares of the magnetic fluxes that enclose only the generating winding are called stray fluxes. They are named Φσ. The stray fluxes Φσ1 and Φσ2 only act in their own side of the transformer and can therefore also be shifted to the supply leads. This results in the picture shown in Figure 12. R1 X1σ X2σ R2 I1 I2 U1 Z1 Z2 U2 Figure 12 – Substitute diagram, single-phase, with two windings, winding resistance and leakage inductance 23/112 Part I Version 02 PSP Diagnostics Compendium Part I_V02_EN.docx 2.3.4 Step 3: Transformation secondary to primary side In the next step, secondary-side quantities will be transformed – "correlated" in electrical engineering - to the primary side, in order that any subsequent calculations and considerations can be performed without the transformer turns ratio as factor. Generally speaking, the following correlation applies ̅1 U n1 I̅2 n1 (13) ̅2 = and =. U n2 I̅1 n2 Multiplying the two formulas will yield ̅1 I̅2 U n1 n1 ∗ ̅ 2 I1̅ = ∗ U n2 n2 ̅1 U I̅2 n 2 (14) I̅1 ∗ ̅2 U = (n1 ). 2 U ̅ Please remember: The following still holds true Z̅ = I̅. Now, the first expression from left in formula (14) is replaced: ̅1 U = Z̅1 I1̅ ̅ U 1 I̅ The second expression from left in formula (14) is the reciprocal value of Z̅ = I̅ , that is, Z̅ = U̅, and is then presented as follows: I̅2 1 ̅2 = U Z̅2 Now, the expressions developed before are inserted in formula (14) 1 n1 2 Z̅1 ∗ ̅ = ( ) Z2 n2 resulting, via transformation, in the general equation in formula (15) for transforming resistances. Z̅1 n1 2 (15) ̅Z2 = (n2 ) The correlation in formula (15) means that every ohmic resistance, every reactance and every impedance is transformed using the square of the transformer turns ratio: n1 2 (16) 𝑍̅2′ = Z̅2 ( ) n2 Therefore, the components of the secondary side can now be correlated to the primary side. All mathematical quantities converted in this way from the secondary side to the primary side are presented in the following using a horizontal line above it; such as 𝐼2'̅ , 𝑈 ̅2' , 𝑅̅2' , 𝑋̅2σ ' and 𝑍̅2'. This will produce the substitute diagram in Figure 13. Conversion of all secondary quantities 24/112 Part I Version 02 PSP Diagnostics Compendium Part I_V02_EN.docx n1 with the transformer turns ratio now makes it possible to assume a winding ratio of n2 = 1 for the magnetic transmitter in Figure 13. R1 X1σ X'2σ R'2 I1 I'2 U1 Z1 Z'2 U'2 Figure 13 – Equivalent circuit, secondary quantities converted to primary side 25/112 Part I Version 02 PSP Diagnostics Compendium Part I_V02_EN.docx 2.3.5 Step 4: Introduction of main impedance The two vertical impedances in the substitute diagram in Figure 13 represent main inductivity L and the eddy current loss in the transformer core. The iron losses are illustrated by the iron loss resistance 𝑅̅FE , and are drawn on the primary and the secondary side in the substitute diagram in Figure 14, as 𝑅̅1FE and 𝑅̅2FE. Main inductance is also introduced; it is illustrated by the reactances 𝑋̅1h and 𝑋̅2h. I1 R1 X1σ X'2σ R'2 I'2 U1 R1FE X1h X'2h R'2FE U'2 Figure 14 – Equivalent circuit, with ideal transformer By withdrawing leakage inductance, ohmic winding resistance and iron loss, an ideal transformer, that is, a loss-free transformer, with reactances 𝑋̅1h and 𝑋̅2h has resulted. 26/112 Part I Version 02 PSP Diagnostics Compendium Part I_V02_EN.docx Voltages of the primary side are induced on the secondary side with the same direction and the same size via this ideal transformer, of which the transformer turns ratio is one. From this, it can be derived that the potentials at the beginning and end of the windings of both coils are equal. Two points that are equal in potential can be connected with each other. Figure 15 results from this, with connected ideal transformer. I1 R1 X1σ X'2σ R'2 I'2 U1 R1FE X1h X'2h R'2FE U'2 Figure 15 – Equivalent circuit, single-phase, with ideal transformer equal in potential Electrically and seen from outside the transformer, the two reactances 𝑋̅1h and 𝑋̅2h act like a main inductance 𝑋̅h. That is, the two reactances in Figure 15 become one main inductance with reactance 𝑋̅h in Figure 16. I1 R1 X1σ X'2σ R'2 I'2 U1 R1FE Xh R'2FE U'2 ̅h Figure 16 –Equivalent circuit, single-phase, with main inductance in reactance 𝑋 27/112 Part I Version 02 PSP Diagnostics Compendium Part I_V02_EN.docx ̅ In addition, the iron loss resistances 𝑅̅1FE and 𝑅′ 2FE act, to the outside, like a resistance, because of their parallel connection; therefore they can be combined into one iron loss resistance 𝑅̅FE , see Figure 18. I1 R1 X1σ X'2σ R'2 I'2 U1 RFE Xh U'2 Figure 17 – Substitute diagram, single-phase, with main inductance and iron loss resistance Main inductance and iron loss resistance, again, can be combined and seen as one main impedance Z̅h, as shown in Figure 18. Iron losses and the behavior of the core, and also no- load current I0, that is in direct correlation with the main impedance, are now integrated in the equivalent circuit. R1 X1σ X'2σ R'2 I1 I'2 I0 U1 Zh U'2 Figure 18 – Substitute diagram, single-phase, with winding resistance, leakage inductance and main impedance 28/112 Part I Version 02 PSP Diagnostics Compendium Part I_V02_EN.docx By dividing main impedance Zh into main inductance Xh and iron loss resistance RFE , it is possible to examine the behavior of magnetic flux and magnetism in the transformer core in greater detail. Main inductance is fed by the magnetizing current Iμ and describes the hysteresis losses. Iron loss resistance RFE , again, is fed by the iron loss current IFE and describes thermal losses in the core, caused by so-called eddy currents in the iron sheets of the core. This finally results in the single-phase equivalent circuit in Figure 20. R1 X1σ X'2σ R'2 I1 I'2 I0 Iµ IFE U1 Xh RFE U'2 Figure 19 – Substitute diagram, single-phase and complete 29/112 Part I Version 02 PSP Diagnostics Compendium Part I_V02_EN.docx 2.3.6 Typical quantity correlations of the elements of the equivalent circuit Transformer:1 YN yn0 yn0 +d, 115 kV / 10.5 kV / 10.5 kV, 40 MVA network transformer ̅ 1 = 1,208 Ω (in mid-position of the OLTC) R 2 ̅ 2 (n1 ) = 1,793 Ω 𝑅̅2' = R n 2 ̅1σ = X 𝑋̅2σ ' = 45,85 Ω 𝑅̅FE = 1,433 MΩ ̅h = 1,698 MΩ X These absolute numerical values are certainly not applicable to all transformers, but the basic size correlations become clear: ̅ FE and ̅ resistances R Xh are significantly larger than resistances R ̅'2 , ̅ ̅ 1, R X1σ and ̅ ' X2σ , in the short-circuit case, only resistances R ̅'2 , X ̅ 1, R ̅1σ and X ' ̅2σ are effective, ̅ FE and ̅ and in the no-load case, only the resistances R Xh are effective. 1 Siemens Type TLSN 7751, s/n 422332 30/112 Part I Version 02 PSP Diagnostics Compendium Part I_V02_EN.docx 2.4 Behavior of the transformer 2.4.1 Behavior of the transformer in the no-load case "No load" means the transformer operating condition where a three-phase AC voltage is applied to one winding, e.g., the primary-side winding, and no power at all is delivered on any terminals of a further winding that is being considered, such as the secondary-side winding, that is, resistance between the phases goes towards infinity and no secondary-side output flows; in mathematical terms, the following applies during secondary-side no-load condition: (17) I̅2' = 0 Therefore, the horizontal resistances on the no-load side can be neglected, see Figure 20. R1 X1σ X'2σ R'2 I1 I'2 = 0 I0 Iµ IFE U1 Xh RFE U'2 Figure 20 – Substitute diagram, neglecting the secondary-side winding impedance In chapter 2.3.6, the size correlations of the resistances in a transformer were clarified. In accordance with the correlations shown there, the horizontal resistances are very much smaller than the main impedance representing the core. Therefore voltage drop on the horizontal resistances is neglectable. The equivalent circuit in Figure 21 resulting from this shows that the behavior of the transformer with the secondary side open is determined by the main impedance and therefore, main inductance and resulting reactance ̅ ̅ FE. The no-load current 𝐼0̅ in Figure Xh and the iron losses R 21 calculated in this way corresponds approximatively to current I̅1 of Figure 20. 31/112 Part I Version 02 PSP Diagnostics Compendium Part I_V02_EN.docx I1 ≈ I0 Iµ IFE U1 Xh RFE U'2 Figure 21 – Substitute diagram, single-phase, in no-load operation 2.4.2 Behavior of the transformer shorted on the secondary side When a transformer is shorted on the secondary side, the horizontal resistances in the ̅'2 + ̅ secondary path (R ' X2σ ) are connected in parallel to the reactance of main inductance Xh and the iron loss resistance RFE. It should be pointed out that extensive calculations would be necessary here, but the size dimensions of the single resistances 2.3.6 show that ̅'2 and the leakage inductances act as ̅ 1 and R approximatively, only the winding resistances R ' reactances ̅ X1σ and ̅ X2σ that are significantly smaller. R1 X1σ X'2σ R'2 I1 I'2 U1 Figure 22 – Single-phase equivalent circuit of a transformer shorted on the secondary side The equivalent circuit in Figure 22 shows a galvanic connection between the electrical ̅ 1 and X components R ̅'2 and ̅ ̅1σ , and R ' X2σ. This certainly does not mean that the primary and secondary bushings are connected to each other in the short-circuit case. It means that the short-circuit current is limited by the electrical leakage fields in the winding's diffuse channels and the winding resistances of primary and secondary side. Due to the secondary-side short circuit, current I̅1 , influencing the primary winding, flows in the secondary winding of the transformer. This influence is be made transparent in the equivalent circuit in Figure 22. 32/112 Part I Version 02 PSP Diagnostics Compendium Part I_V02_EN.docx Short-circuit impedance would have to be measured in the short circuit at rated voltage. This is not possible due to the forces that would develop in the transformer, and the electrical power and technical measuring equipment that would be needed. Therefore, transformer manufacturers use a modified short-circuit measurement as alternative. To determine short-circuit voltage u ̅ k (uppercase U), the feeding voltage source on the primary side is regulated until the rated currents flow on primary and secondary side. In this process, the secondary side is short-circuited. On transformer nameplates, short-circuit impedance in correlation to rated voltage is specified as short-circuit voltage uk (lowercase u) in percent. For example, relative short-circuit voltage can be specified as uk = 10 % on the transformer ̅ k = 10 % U nameplate. This means that short-circuit voltage was U ̅ n during the short-circuit test. At rated voltage 110 kV, measured short-circuit voltage is 11 kV. In this example, if the secondary rated current is I̅n = 500 A , then the short-circuit current In̅ becomes Ik̅ = = 5 kA. in the short-circuit case. 10 % 33/112 Part I Version 02 PSP Diagnostics Compendium Part I_V02_EN.docx 2.4.3 Correlations of time constants on open and short circuits In section 2.2.4, the time constant of a load curve was calculated, see formula (7). In the following, index 0 is used for the quantities of the open-circuited transformer, index K for the quantities of the short-circuited transformer. This results in: 𝜏K 𝐿K 𝑅̅0 𝐿K 𝑅̅0 = ̅ = (18) 𝜏0 𝑅K 𝐿0 𝐿0 𝑅̅K It becomes clear that time constant τ becomes significantly smaller if the secondary side is short-circuited and the short-circuit resistances are substantially smaller. You can take advantage of this effect for measurements where you have to await a load time period of 5 τ. It is obvious that the necessary waiting period becomes very much less. For devices typically used today, that are especially designed for specific measuring tasks, it is well possible that the transformer's main inductance is needed for the regulating circuits. Those actions should not be used in such cases. If in doubt, consult the user guide of the relevant device. 34/112 Part I Version 02 PSP Diagnostics Compendium Part I_V02_EN.docx 2.5 Basic connection methods On transformers over 45 kV, the three phase windings (U, V, W) of a winding group (primary, secondary etc.) are normally connected in the neutral point ("wye" or "star") or in delta (D). In addition, there is the Zigzag connection (Z) for process and distribution transformers, or an external connection for industrial transformers, where the single windings on both sides are output via bushings (i). Depending on connection method and designation of phases, various ratios and phase angles can be achieved. The phase angle is specified in multiples of 30°. 2.5.1 WYE connection Windings U, V and W are connected together on one side. This connection point is called star point or neutral point (wye point). As an option, the neutral point can be accessible via a bushing. The voltage that is effective on the single winding is √3 times smaller than the specified phase conductor voltage. The voltage loads in the transformer are smaller in wye connections than in delta connections, therefore transformer design is simpler. During normal operation, the OLTC is not stressed from voltage to ground. Depending on power, all three phases can be combined in one diverter switch, as their maximum voltage difference corresponds to one step voltage multiplied by the square root of three (√3). The wye connection can be loaded asymmetrically to a limited extent only; if it is, magnetic unbalance will build up in the transformer core. 2.5.2 Delta connection Windings U, V and W are connected in a circle to the phase conductors. Phase conductor voltage is effective on every winding. Every part of the winding has a voltage to ground of at ̅L 𝑈 ̅= least 𝑈 ̅L. All insulations and also the OLTC must be designed for this permanent up to 𝑈 2√3 load. A delta connection can be loaded 100 % asymmetrically, but it does not have a grounding point. 35/112 Part I Version 02 PSP Diagnostics Compendium Part I_V02_EN.docx 2.5.3 Auto transformer In auto transformers, primary and secondary winding are not separated galvanically. An auto transformer functions like an inductive voltage divider. As parts of the winding act on the primary and on the secondary, influence on the inductances through exterior short circuits is not possible here. There is no shifting of phases between entry and exit of the same winding. 2.5.4 Zigzag operation In Zigzag operation, either primary or secondary winding is divided in the middle. Skillful connection makes it possible here to combine the advantages of wye connection with the asymmetrical qualities of delta connection. Phase displacement angles (similar to wye connection) to secondary wye and delta connections are possible. The Zigzag connection can be loaded 100 % asymmetrically. A single-phase equivalent circuit cannot be used in Zigzag connections, as current always flows simultaneously through the windings of at least two different core limbs. 2.5.5 Vector groups In most cases, vector group information is specified on the transformer nameplates. The information consists of letter codes and numbers. The letters indicate the basic connection of the respective winding and the design of the neutral point conductor. The numbers indicate the phase displacement angle between primary and secondary side as factor of 30°. Examples for vector groups of connection combinations wye, wye-N and D are listed in attachment A.2. 36/112 Part I Version 02 PSP Diagnostics Compendium Part I_V02_EN.docx 3 General notes about measurements 3.1 Checking the end positions When performing measurements, always check in the first place that the OLTC is coupled correctly with the motor-drive unit, and that the end positions work properly. It is well conceivable that a tap-changer is misaligned by one or two tap positions (because the customer has not operated the tap-changer to the end positions) without resulting in damage. But as this is done during measurements, the tap-changer would be operated over the end positions by our service technician and get damaged. 3.2 Handling of (dead) pass-through positions and early end positions As a general rule, the most complete picture possible is necessary to evaluate the transformer. If this can be done within reasonable time and effort, the early end positions should be made inoperable for the time of the measurements, in order to measure those positions as well. Consult with CSTA in cases of doubt. Pass-through positions in the motor-drive unit must always be deactivated, for each tap position is important for the evaluation, especially in the change-over selector. 3.3 End of work checks After performing all measurements, check function of motor-drive unit, end positions and pass- through positions before returning the service permission. 37/112 Part I Version 02 PSP Diagnostics Compendium Part I_V02_EN.docx 4 Documentation 4.1 Documentation on site To be able to interpret, reconstruct or repeat measurements, it is necessary to document the situation and performed work steps transparently and comprehensively. The documentation can consist of (unambiguous) headlines, photographs, handwritten protocols, text files, comments in test software etc. The test object should be documented on the site as unambiguously as possible, using photographs and additional information. The list below is not complete; that is, you can always add additional points to it; and it can be used as memory-aid on site. Further information that you consider essential should be documented in suitable form, e.g., measurements before or / and after oil filling etc. Issue Location Completed Comment Pictures Plate transformer customer designation Overview picture of transformer's overall situation Transformer nameplate (readable and without reflections, with voltage table and connection diagram) Motor-drive unit nameplate Number of tap-change operations on Motor-drive unit's operations counter Nameplate on oil compartment cover Arrangement of bushings with unambiguous name allocation Bushing with test taps (terminal arrangement, guard, grounding cable etc.) Distance of test setup to ground potential o other conductors (important for FRA, Dirana) General Coordinates transformer station Designation / name of transformer station Address of substation Transformer not filled with oil Are fans and oil pumps switched off? Switched off since when (important for equilibrium in core, solid insulation, winding and oil) Temperature When measured? Exact time Where measured? If possible, add drawing 38/112 Part I Version 02 PSP Diagnostics Compendium Part I_V02_EN.docx Measured using what? (Inventory and serial number, when is next calibration due?) On-load tap- MR equipment number with number of tap- changer change operations DSI serial number with number of tap-change operations Oil compartment serial number with number of tap-change operations Tap selector serial number with number of tap- change operations Drawings Test setup and connection The temperatures must be filed together with the data later on, e.g., as comment in the test software, as scan or picture of a handwritten note or as separate text file. Measurements, just like any work performed, must be listed in the service report as usual. A test report is usually offered and handed over separately. Before starting the service assignment, the measurement order should be discussed with the responsible person to clarify the scope of services. For photographs, always take an overview picture first, see Figure 23, then approach the relevant spot, see Figure 24, and finally take the detail picture, see Figure 25. Detail pictures alone are not helpful, because orientation will be impossible for a second or third viewer. As the case may be, write notes and take the pictures with the notes visible for later viewers. 39/112 Part I Version 02 PSP Diagnostics Compendium Part I_V02_EN.docx Figure 23 – Extended surroundings of the test tap 40/112 Part I Version 02 PSP Diagnostics Compendium Part I_V02_EN.docx Figure 24 – Immediate surroundings of the test tap 41/112 Part I Version 02 PSP Diagnostics Compendium Part I_V02_EN.docx Figure 25 – Detail of test tap Test the quality of the pictures on the camera by enlarging, especially if they were taken indoors, for example in transformer cells. In the case of underexposure it is recommended to increase light sensitivity; place the camera on a convenient surface to avoid blurred pictures. 42/112 Part I Version 02 PSP Diagnostics Compendium Part I_V02_EN.docx 4.2 Serial numbers and numbers of tap-change operations The example below illustrates the importance of this part of the documentation. When creating a diagnosis report following a measurement, equipment number and service notification number are used to trace the transformer history in the documentation. It may well be possible to find indications for transformer repairs and similar incidents. It is often not clear which serial numbers and numbers of tap-change operations are actually valid, for example, if a motor-drive unit was removed from a transformer that is identical in design and installed on the repaired transformer, and then a new DSI was installed. Prerequisites for reliable condition analysis and recommendation for action are: MR equipment number, SAP service notification number, serial numbers of DSI, tap selector and oil compartment, and the respective numbers of tap-change operations at the time of the measurement. Always ask the customer on site for differences in the transformer history. Ideally, you should scan or take pictures of the transformer handbook, at least the chapters containing the drawings and FAT. The handbook is usually available on site even if not available on request beforehand. 4.3 Data backup After the measurement, save the test datafiles, documentation, pictures and other relevant files on your laptop and external storage media. To obtain a clear structure it helps to file and name the folders, files and pictures as soon as possible after the measurement if several transformers in the same or different substations are measured. Make sure to check beforehand which data formats have to be filed. In some cases, two formats are required (e.g., Omicron PTM exports always as *.ptm and *.xlsx file). In cases of doubt, always use excel format and in addition, the format of the device manufacturer. 4.4 Data storage On the MR network drive \\mr.corp.dir\mr_messdaten\am_diagnostics\, a folder \000-to-be- sorted is available under the relevant region to store test datafiles and all other relevant archives. We recommend to use the following name for the folder: "Date-of- measurement"_"equipment-number"_"service-notification-number". For example, 20171107_MR1227866_300312345 Use either the method or the used software as name, see structure in the example below: 43/112 Part I Version 02 PSP Diagnostics Compendium Part I_V02_EN.docx Figure 26 – Screenshot with folder structure it is not enough to just move the test files. Having completed data storage on the MR network drive, you should write an e-mail to [email protected], specifying equipment number and service notification number. As of January 2019, CSTA will take care of data storage and coordinate report preparation. 44/112 Part I Version 02 PSP Diagnostics Compendium Part I_V02_EN.docx 5 Temperature 5.1 General The temperature of the measured object often has decisive influence on the values of the measurement. To be able to compare the measurements, it is therefore absolutely necessary to measure the temperature at the time of the measurement and document it. This is the only way to convert measurements that were made at different temperatures in order that they are comparable. Of course, when performing the measurements, beginning and end times must also be documented. Measuring the temperature should be seen as separate measurement. 5.2 Measuring temperatures On site, it is often not possible to measure the temperature directly on the measured object. During resistance measurements, it would be necessary to measure the medium temperature value on the copper windings. But the copper windings are not accessible. In such cases, measure the temperatures on spots around the measured objects that are accessible. During resistance measurement - the winding is across the entire transformer height - it makes sense to measure the temperatures on top, in the middle and on the bottom of the transformer. Care should be taken that the measuring spots are located in the shadow and not cooled by the wind during the entire measuring period. During measurements on bushings, the temperatures are measured on metal parts of bushing head and bottom. Due to reflection characteristics of uncoated metal surfaces, a contact thermometer should be used here to take the temperatures. For measurements that require an extended period of time, the temperatures should be taken at least at the beginning and at the end and, if necessary, also while the measurement lasts. A maximum time interval of approx. ½ hour has proven effective. The appropriate safety distances to live parts must of course be observed during ongoing measurements. 5.3 Influencing factors Selection of the measuring points is often decisive for the usability of temperature measurements. Measuring points should be selected where the least possible influence of external factors such as solar radiation, wind or cooling systems is expected. The type of measuring device used also influences the measurement significantly. Contactless infrared thermometers (pyrometers) are well proven in practice. It should be noted though, that measurement depends on the type of the measured surface. Therefore it is advisable to perform a comparison measurement on at least one of the measured points with the same surface. This way, it is possible to select measuring points where the influence of the surface conditions has the least possible effect on the measuring result. 45/112 Part I Version 02 PSP Diagnostics Compendium Part I_V02_EN.docx The values measured in this way must be documented as specified in the documentation chapter, as they are part of the total measurement and without them, evaluation of the electrical measurements is often impossible. 5.4 Correction factors for resistance measurements Ohmic resistance of conductor materials depends on temperature. The material constant can be used to convert the values to other temperatures. This correlation is expressed in the following formula: k + Tkorr Rkorr = Rmess k + Tmess The following constants should be used: KCU = 235, for copper KAL = 225, for aluminum. Copper is typically used as winding material. In the Eastern part of Germany and in Eastern Europe, transformers with aluminum windings can be found quite frequently. In accordance with the appropriate standards, resistance values are extrapolated to a standard temperature of 75 °C. But in transformer test (FAT, Factory Acceptance Test) protocols, it is quite common to document the temperature during the measurement only, without extrapolating the values. Example: For a correction from 20 °C to 75 °C in a copper winding, the above formula yields a correction factor of ~1.265. That means, the resistance values are increased by 26.5 % in this example. Corrections of this size cannot be neglected. 5.5 Correction factors for dissipation factor (tan δ) or power factor (cos ) on the transformer insulation The dissipation factor of an insulation depends largely on temperature. The calculation formula for this temperature compensation is specified in a publication of the IEEE standard (C57.12.90) of 2006. But since that date, the opinion has developed among experts that this formula does not reflect reality with sufficient precision. Therefore it cannot be found in later versions of this standard. But on the other hand, it is also clear that it does not make sense to evaluate the measurements without temperature compensation. Current procedure is to perform temperature compensation in accordance with the IEEE standard of 2006. But the report includes a note concerning objections and limitations regarding evaluation of these measurements. 46/112 Part I Version 02 PSP Diagnostics Compendium Part I_V02_EN.docx 5.6 Correction factors for dissipation factor on bushings Just as with transformer insulation, dissipation factor tan δ and power fac