Introduction to Production Management PDF
Document Details
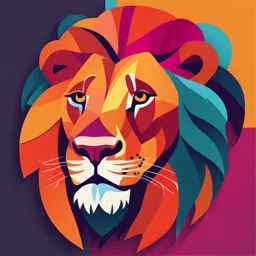
Uploaded by LikableSparkle
Dr. Avni Patel
Tags
Summary
This presentation introduces the key concepts of production management. It defines production as the process of converting raw materials into finished products and then discusses production management. The document also explores the differences between production and operations management.
Full Transcript
Introduction to Production Management Dr Avni Patel Production Production is the process by which raw materials and other inputs are converted into finished products. Production Management Production management refers to the application of management principles...
Introduction to Production Management Dr Avni Patel Production Production is the process by which raw materials and other inputs are converted into finished products. Production Management Production management refers to the application of management principles to the production function in a factory. In other words, production management involves application of planning, organizing, directing and controlling to the production process. Difference b/w Production & Operations Production Operations Conversion of inputs into outputs Implementation of various methods in This term can be used for products the process of conversion only This term can be used for products It is simply concerned with targeted and services both output It adds value to the product Uses various statistical tools (operation research tools) Operations as an organizational function Finance/Accounting Production and Budgets Inventory data Cost analysis Capital budgeting requests Capital investments Capacity expansion and Stockholder Technology plans requirements Product/Service Availability Orders for materials Lead-time estimates Production and delivery Status of order Schedules Quality Delivery schedules Requirements Design/ Suppliers Marketing Operations Material availability Sales forecasts Quality data Customer orders Delivery schedules Customer feedback Designs Promotions Recruitment and Hiring/firing selection Training Performance evaluations Personnel needs Job design/work Skill sets measurement Human Resources History of Production Management Evolution of Production Management Interchangeable Craft production Division of labor parts process of dividing a job standardization handcrafting into a series of of parts initially products or small tasks each as replacement services for performed by a parts; enabled individual different worker mass production customers Evolution of Production Management Scientific Mass production Lean production management systematic high-volume adaptation of analysis of work production of a mass methods standardized production that product for a prizes quality mass market and flexibility History of Production and Operations Management The successful creation of the steam engine by James Watt (1736–1819), a Scottish inventor and mechanical engineer, served as a harbinger of the industrial revolution in Great Britain and the rest of the world. History of Production and Operations Management Charles Babbage (1772–1871), a British inventor, was a firm believer of the merits of division of labour. He promoted the idea of profit sharing with workers based on their productivity and encouraged the use of employee suggestion schemes. He gave 1st Programmable Computer to the world. History of Production and Operations Management Robert Owen (1771–1858), a British social reformer, is remembered for his reforms regarding child labour in factories, providing meals in the factories to on-the-job workers, and creating suitable housing facilities for the workers. History of Production and Operations Management Thomas Alva Edison (1847–1931), an American inventor and businessman, made several significant inventions and had set up the world’s first industrial research laboratory. Some of his prominent inventions are the long-lasting electric bulb, motion picture camera, and the phonograph. History of Production and Operations Management Frederick Winslow Taylor (1856–1915), an American mechanical engineer, is aptly hailed as the father of scientific management. His book The Principles of Scientific Management was published in 1911 and is regarded a cornerstone of management thought. He is famous for his stop watch time studies, in which he measured the time taken by workers in performing various parts of a task. History of Production and Operations Management Henry Ford (1863–1947), an American entrepreneur, engineer and innovator, is best known for his invention of the modern assembly line. In his factory, Ford implemented several concepts of Frederick Taylor, including standardized and interchangeable parts, precision manufacturing, and division of labour. Transformation Process Transformation Process A transformation process is defined as a user of resources to transform inputs into some desired outputs Quality of Inputs Quality of Outputs Monitored Monitored Transformation Inputs Outputs Processes Feedback Mechanisms The Transformation Process For a Service Organization (An MBA Institute) Random disturbances Strikes of students, Quality of Quality of teachers or staff Class rooms outputs inputs Undue interference of monitored Teachers monitored the government in the Raw minds working of institutions (students) Enlightened students with: Compute Transformation Good communication rLibrar lab Process skills Pleasant personalities y Projectors Leadership qualities (OHP, LCD etc) Good analytical ability Administra Team spirit tive staff Feedback Mechanisms Decision making abilities Success at placement interviews Computer skills INPUTS Grades obtained in examinations OUTPUTS Rising career graph of alumni in the industry Number of applications for admission in the institute Ratings of surveys The Transformation Process For a Hybrid Service & Manufacturing Organization (A Restaurant) Random disturbances High turnover of chefs, Quality of Employee Quality of waiters, etc. outputs s Building inputs Inflation monitored Chef monitored Government’s taxation Vegetables policy Furniture. Customers satisfied with: Transformation Good preparation of the Process food Cooking oil, Pleasant behavior and Spices, etc. personality of the waiter Waiters Genuine prices charged Manager Feedback Mechanisms Rising Revenues OUTPUTS INPUTS Repeat Customers Appreciation of customers The Product/Process Continuum Automobil Photocopier e retailers Banks Consultancies Automobile manufacturers & manufacturers service providers Restaurant Airline Undertakers s s Product Process orientatio orientation n Organizations on a Product/Process Continuum PRODUCT DESIGN Research and Development In R&D, fundamental research is the advancement of the state of knowledge in a subject, though it may not be practically converted into commercial applications. Applied research has the objective of developing commercial applications. Most of the corporate houses have a R&D department devoted for this purpose. Development is the process of converting the results of applied research into useful commercial applications Reverse Engineering Reverse Engineering is the process of carefully dismantling an existing product (for a competitor) step by step in order to understand the unique underlying concepts. If helps in designing new products, which are better than those of the competitors. Manufacturability Manufacturability implies designing a product in such a way that its manufacturing assembling can be done easily. While designing a new product, the manufacturing capabilities (such as existing machines, equipment, skills of workers, etc.) of the organization have to be kept in mind. Standardization Standardization refers to less variety in the design of products, i.e., new products are designed such that there is no major variation from the existing products. For example, all computers and typewriters have the same arrangement of keys in the keyboard because it has become a standard consumers are used to. Modular Design Modular Design is another type of standardization, which means designing a product in pars of modules. The modules are sub- assemblies of different components and parts. For e.g., in Personal Computers there are separate modules (small boxes inside which there are various integrated components) for the motherboard, the hard disk, power supply CD drive, floppy drive, etc. Robust Design Robust Design means designing a product that is operational in varying environmental conditions. For eg., if you compare a car with a jeep, the jeep is more robust in design as it can even be used efficiently on hilly areas with poor road conditions. The Japanese engineer Genichi Taguchi emphasized that it is easier to create a product with robust design rather than making changes in the environment to suit the product. Concurrent Engineering Concurrent engineering is the product design approach in which the design team includes personnel from the marketing department (to specify the customer requirements), engineering department (to look at the feasibility of the design), production department (to suggest if production capability exists for the design), materials department (to give inputs material availability according to design specifications), and finance department (to suggest financial feasibility of the design) in addition to the design department. Computer-aided Design CAD is a software which helps the designer to make the three dimensional design of a product on the computer and visualize the design form various angles. Life Cycle of a Product The product life cycle has five stages spread throughout the life of a product. These are incubation, growth, maturity, saturation, and decline. The incubation stage witnesses a low demand of the product owing to the customer not being aware of the new product. As the awareness increases and new features are added to the product over a period of time., the demand starts growing and this phase is called the growth phase. Life Cycle of a Product Next follows the maturity stage, when the demand tends to become stable and even new features do not appeal much to the masses, leading to the saturation phase and eventually the decline phase. PROCESS DESIGN Process Design Types of Processes Continuous Semi-continuous Intermittent Project Process (Repetitive/Assembly Process ) Process Batch Process Job Shop Types of Processes Continuous Process The continuous process as the name suggests is continuous in nature. The set-up time for starting such processes is usually very long, and once started, they continue for a long duration. The products produced by such a process are highly standardized with almost no variety, and are measured on a continuous basis (tonnes per day, meter lengths per day, etc.) rather than in terms of discreet units. Ex: Chemicals, steel, plastic, textiles, sugar, urea etc. Semi-continuous Process Semi-continuous processes are assembly processes, which are repetitive in nature. They produce high volume of output and the products produced have little variety. For example, automobiles, electronic items, white goods, etc. These processes require highly specialized machines, semi-skilled workers, and result in low cost per unit. Intermittent Process Intermittent processes stop at regular intervals of time because the product requires processing on a variety of machines. The products produced are of different varieties, thus making the production process slow in comparison to the continuous/semi-continuous process. They are of two types: Batch process and Job shop Batch process This process is adopted when batches or lots of items are to be produced using the same set of machines in the same sequence. Ex. Bakery Cleaning and adjustments are required after each production run. Job Shop This process can handle a larger variety of products than the batch process. The products may be so different from each other that their processing requirements may be varied processes, on different machines, in different sequences, and with different processing times. The batches of items produced in job shop may vary in size from large, comprising many units, to very small, comprising a single unit. Ex. Restaurant Projects Projects are processes that handle very complex and unique sets of activities or tasks, which have to be completed in a limited span of time. Ex. Construction of Building, R & D Project, construction of Plant, implementation of specialized software in an organization. DUTIES AND RESPONSIBILITIES OF PRODUCTION MANAGER Planning the geographical location of the factory Purchasing production equipment Layout of equipment within the factory Designing production processes and equipment Product design Designing production work and establishing work standards. Capacity planning Production planning and scheduling Production control Inventory Management Emerging Role of the Production & Operations Manager in India Today To act as internal To take part in quality auditors in To implement total strategic decision productive certification making of the maintenance (TPM) programmes like organization ISO 9000 programme Increased attention to technology To take part in the management in view implementation & of JVs of MNCs with use of ERP software domestic companies in the organization New To act as supply Responsibilities To automate the chain managers of Operations processes according in forging long- Managers to the requirements term strategic of the organization relationships with suppliers To enhance the R & D effort of the To act as a organization for member of the becoming self-reliant concurrent in developing new engineering team technologies in new product design To implement the To oversee timely To take care of environmental and implementation of projects To take decisions issues relating to pollution norms (like commissioning of services operations regarding established by the facilities, launching of new outsourcing/ off- management government from products/ services, etc.) in shoring of business time to time view of the increased processes competition Productivity and Employee One of the key ways we judge our operational performance is by using a simple measure, which is productivity. Productivity= Output/Input Labor Productivity= Output/Labor Hours Machine Productivity= Output/Machine Hours Multifactor Productivity= Output/(Labor cost+ Machine Cost+ Material Cost+ Energy Cost) Billco Windows and Doors is preparing their monthly productivity report. Their monthly costs are shown below. Calculate the a) labour productivity (output / labour hours) b) machine productivity (output / machine hours) and c) the multifactor productivity output / (labour cost + material cost + energy cost) of dollars spent on labour, materials, and energy. Average labour rate is $18.00. Units produced: 1800 Labour hours: 1975 Machine hours: 425 Materials cost: $81000 Energy cost: $21600 a) Labour productivity (output / labour hours) = 1800 / 1975 =.91 units per labour hour b) Machine productivity (output / machine hours) = 1800 / 425 = 4.23 units per machine hour c) Multifactor productivity output / (labour cost + material cost + energy cost) = 1800 / (1975 x $18 + $81000 + $21600) =.013 units per dollar spent A company makes seasonal jams and jellies. Yesterday they produced 420 jars of jam with five workers who each worked an 8-hour day. What was the labour productivity? Solution = 420 / (5 workers x 8 hours) = 10.5 jars per worker hour A greeting card company manufactured 3500 cards in one day. Labour cost was $1200, material cost was $90, and overhead was $450. What is the multifactor productivity? Solution = 3500 / ($1200 + $90 + $450) = 2.01 cards per dollar of input Trends in Production Management JIT and TQC Service Quality and Productivity Total Quality Management and Quality Certification Business Process Reengineering Supply Chain Management Electronic Commerce Current Issues in OM Coordinate the relationships between mutually supportive but separate organizations Optimizing global supplier, production, and distribution networks Increased co-production of goods and services Managing the customers experience during the service encounter Raising the awareness of operations as a significant competitive weapon Artificial Intelligence in Production Management AI which stands for artificial intelligence refers to systems or machines that mimic human intelligence to perform tasks and can iteratively improve themselves based on the information they collect. AI manifests in a number of forms. examples : Chatbots use AI to understand customer problems faster and provide more efficient answers Recommendation engines can provide automated recommendations for TV shows based on users’ viewing habits Alphabet – Google Companies Amazon using AI Apple Tesla Although AI brings up images of high- functioning, human-like robots taking over the world, AI isn’t intended to replace humans. It’s intended to significantly enhance human capabilities and contributions. That makes it a very valuable business asset.