Print En Vacutap Vr 2016 PDF Maintenance Instructions
Document Details
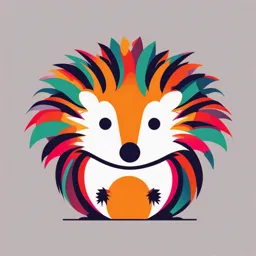
Uploaded by ValuableSugilite
2016
Tags
Related
- OILTAP V-CDS-Komplett Maintenance Instructions PDF
- VACUTAP® VM® On-load tap-changer Operating Instructions PDF
- Print_EN_VACUTAP VR 2016 Maintenance Instructions PDF
- VACUTAP® VM 300 On-load tap-changer Operating Instructions PDF
- VACUTAP® VM® Maintenance Instructions PDF
- VACUTAP® VR I HD Operating Instructions PDF
Summary
This document provides step-by-step instructions for maintaining Vacutap VR 2016 on-load tap-changers. It covers inspections, tests, and replacement criteria for various components, including coupling tubes and contacts. The instructions emphasize safety precautions and require sufficient knowledge and experience for implementation. It ensures proper maintenance of the equipment.
Full Transcript
1 Introduction 1 Introduction NOTICE Risk of personal damage or injury, damage to property or mal- function. If work is performed by insufficiently qualified personnel and/or safety in- structions are not obs...
1 Introduction 1 Introduction NOTICE Risk of personal damage or injury, damage to property or mal- function. If work is performed by insufficiently qualified personnel and/or safety in- structions are not observed, there is a risk of personal damage or injury, damage to property or malfunction. ► Safety, hazard and other information included in the MR operating in- structions for the relevant on-load tap-changer type must be observed! ► Please read the instructions carefully before starting work. ► The realization of the instructions below requires profound knowledge and experience that correspond to the knowledge acquired during a train- ing at MR about maintenance of the relevant on-load tap-changer type. ► It is absolutely necessary that the diverter switch insert (or selector switch insert, respectively) has been removed. EN 1 2 Step-by-Step 2 Step-by-Step 2.1 Introduction NOTICE Risk of personal damage or injury, damage to property or mal- function. If work is performed by insufficiently qualified personnel and/or safety in- structions are not observed, there is a risk of personal damage or injury, damage to property or malfunction. ► Safety, hazard and other information included in the MR operating in- structions for the relevant on-load tap-changer type must be observed! ► Please read the instructions carefully before starting work. ► The realization of the instructions below requires profound knowledge and experience that correspond to the knowledge acquired during a train- ing at MR about maintenance of the relevant on-load tap-changer type. ► It is absolutely necessary that the diverter switch insert (or selector switch insert, respectively) has been removed. 2.2 Tests and condition-based parts replacement at each maintenance 2.2.1 Inspecting coupling tube This measure must be performed during each inspection / each VACUTAP® Condition Assessment. 2 EN 2 Step-by-Step Inspecting the coupling tube requires removing the coupling tube from the di- verter switch insert. To do so, proceed as follows. Figure 1: Screws on the lower shielding ring EN 3 2 Step-by-Step 2.2.1.1 Inspecting coupling tube Inspecting the coupling tube requires removing the coupling tube from the di- verter switch insert. Proceed as follows. 1. Remove the 6 screws holding the lower shielding ring. Figure 2: Screws on the lower shielding ring 4 EN 2 Step-by-Step 2. Lift the lower shielding ring and remove the 6 drive sleeves using pliers. Figure 3: Drive sleeves on the lower shielding ring 3. Pull out the coupling tube. 4. Clean the coupling tube with transformer oil. Note the oil quality limit val- ues. 5. Perform thorough visual inspection of the inside and outside of the cou- pling tube. Check for mechanical or electrical damage (leakage paths, dis- charge marks). The coupling tube is refitted following the instructions for removal but in re- verse order. EN 5 2 Step-by-Step When refitting, ensure alignment of the red adjustment mark (at top of cou- pling tube) and the adjustment mark on the diverter switch insert (energy ac- cumulator, see appendix). Figure 4: Adjustment marks Figure 5: Adjustment marks In order to ensure that the adjustment marks are positioned correctly, when assembling the coupling tube, the parts must be positioned as they were be- fore being disassembled. 2.2.2 Measuring transition resistances This measure must be performed during each inspection / each VACUTAP® Condition Assessment. Measure the transition resistances in all sectors at the measurement points shown in the diagram. To do so, proceed as follows: 6 EN 2 Step-by-Step Measure the transition resistances in all sectors at the measurement points shown in the diagram. To do so, proceed as follows: Figure 6: Measuring transition resistances 1. Use an operating wrench to switch the diverter switch insert to side B. At the side B final end position, the main contact is visible in the window of the right-hand supporting bar of a sector, while the window of the left-hand supporting bar is empty. Figure 7: In final end position on side B 2. Measure values of transition resistances on the non-activated side A. The values are in the region of 0.1 to 30 ohms. 3. Use an operating wrench to switch the diverter switch insert to side A. 4. Measure values of transition resistances on the non-activated side B. The values are in the region of 0.1 to 30 ohms. 5. Compare measurements with details on nameplate. Deviations of up to ± 10 % are permitted. Contact the Technical Service department at Maschi- nenfabrik Reinhausen GmbH in the event of larger deviations. EN 7 2 Step-by-Step 2.2.3 Checking contact wear on main contact and replacement intervals of oil compartment contacts In the following, the contact wear on the main contact, as well as the re- placement criteria of the oil compartment contacts on the on-load tap- changer type VRS, VRM, VRL, VRH, VRX (includes all OLTC VR2) is de- scribed. This check must be performed during every maintenance and documented accordingly in the service report. The oil compartment contacts are replaced depending on condition, but at the latest after 1,200,000 tap-change operations. 2.2.3.1 Details - Checking contact wear on main contact and replacement intervals of oil compartment contacts In the following, the contact wear on the main contact, as well as the re- placement criteria of the oil compartment contacts on the on-load tap- changer type VRS, VRM, VRL, VRH, VRX (includes all OLTC VR2) is de- scribed. This check must be performed during every maintenance and documented accordingly in the service report. The oil compartment contacts are replaced depending on condition, but at the latest after 1,200,000 tap-change operations. General To find out whether condition-based replacement must be carried out before the operations-dependent interval (1,200,000 operations) is reached, contact wear must be measured. There are generally two ways to measure contact wear: ▪ Measurement of wear width b on DSI ▪ Measurement of wear depth t on oil compartment contact NOTICE! Using measured value "Wear depth b on DSI" is only permitted if the number of DSI contact operations exceeds or is equal to the number of oil compartment contact operations. Otherwise, wear depth t on the oil com- partment contact must be measured and evaluated. 8 EN 2 Step-by-Step See the table below for examples. Specific situation Permissible way of determining wear Performing first maintenance Measurement of wear width b on DSI is per- mitted During last maintenance, IEM or DSI Measurement of wear width b on DSI is per- and oil compartment contacts were mitted replaced During last maintenance, IEM or DSI Measurement of wear width b on DSI is NOT were replaced, but not the oil com- permitted. Measurement of wear depth t on partment contacts. oil compartment contact must be performed. Table 1: Examples Measurement of contact wear on main contact Measurement of wear width b on diverter switch insert Measure width b of commutation marks on all moving DSI main contacts (side A and side B) using a caliper (see following figure). The decisive wear criterion as described in section 3 is the widest commutation mark on the complete DSI. Commutation mark Figure 8: Measuring width b of commutation marks on DSI Measurement of wear depth t on oil compartment contact Measure depth t of the commutation marks on all fixed main contacts in the oil compartment (side A and side B) using caliper or depth gauge (see fol- lowing figure). The deepest commutation mark in the complete oil compart- ment is the relevant value for the wear criteria specified in section 3. Commutation mark Figure 9: Measuring depth t of the commutation marks in the oil compartment EN 9 2 Step-by-Step Wear-dependent criteria The oil compartment contacts must always be replaced before reaching the following wear values (further operation is not allowed before the replace- ment): ▪ Width b of a commutation mark on a moving main contact of the DSI > 8.0 mm ▪ Depth t of a commutation mark on a fixed main contact in the oil compart- ment > 0.6 mm Consider the following basic points for your decision whether or not the wear limits will be exceeded before the next maintenance interval is reached: Number of tap-change operations of the oil compartment contacts: 300,000 300,000 operations correspond to the number of tap-change operations of the maintenance interval, up to 350,000 operations are tolerable. Type of measurement Measured value and action Example 1 Example 2 Wear width b DSI < 4.5 mm > 4.5 mm Wear depth t oil compartment con- Not measurable > 0.2 mm tact Contact replacement necessary at Not necessary Necessary next maintenance? Table 2: Number of tap-change operations of the oil compartment contacts: 300,000 Number of tap-change operations of the oil compartment contacts: 600,000 Type of measurement Measured value and action Example 3 Example 4 Wear width b DSI < 6.0 mm > 6.0 mm und < 8.0 mm Wear depth t oil compartment con- < 0.2 mm > 0.2 mm und < 0.3 mm tact Contact replacement during next Not necessary Necessary maintenance? Table 3: Number of tap-change operations of the oil compartment contacts: 600,000 Number of tap-change operations of the oil compartment contacts: 900,000 900,000 operations correspond to the number of tap-change operations of the maintenance interval, up to 950,000 operations are tolerable. 10 EN 2 Step-by-Step Number of tap-change operations of the oil compartment contacts: 900,000 Type of measurement Measured value and action Example 5 Wear depth t oil compart- must be < 0.4 mm ment contact Contact replacement dur- Contacts must be replaced during next maintenance ing next maintenance? because 1,200,000 operations will be reached. EN 11 2 Step-by-Step 2.3 Parts replacement after fixed number of tap-change operations intervals 2.3.1 Vacuum interrupters - Replacement (600,000) The instructions below describe how to replace the vacuum interrupters and supporting structure on a 3-sector diverter switch insert. The same proce- dure applies to diverter switch inserts with 1 or 2 sectors. Depending on on-load tap-changer type and its step capacity, replacement must be performed, as a general rule, after every 300,000 (A) or 600,000 (B) operations (see maintenance manual for specific replacement interval): ▪ After 290,000 (A) or 580,000 (B) operations at the earliest ▪ After 310,000 (A) or 620,000 (B) operations at the latest General Please see chapters Material - IEM [►Section 2.3.1.1, Page 13] and Tools - IEM [►Section 2.3.1.2, Page 14] for the material and tools required for work. Please see chapter Drawing of screwing positions [►Section 2.3.1.6, Page 49] for instructions how to make the relevant bolt connections that are opened during the replacement of the vacuum interrupters with supporting structure. NOTICE Risk of personal damage or injury, damage to property. Transport and setup of the diverter switch insert by insufficiently qualified personnel may lead to personal damage or injury and damage to property. There is a risk of tilting due to high center of gravity. ► The diverter switch insert must be carefully transported. ► The diverter switch insert must be installed on a level surface. ► The diverter switch insert must be secured against tipping. 12 EN 2 Step-by-Step 6 cm Figure 10: Risk of tilting of diverter switch insert WARNING Danger of tipping! On the basis of its elevated center of gravity, the diverter switch insert can tilt during transport or in unstable position. This can lead to injuries and property damage. ► Transport the diverter switch insert carefully. ► Place the diverter switch insert on a level surface. ► Secure the diverter switch insert against tipping during transport and setup. 2.3.1.1 Material - IEM Material required for the modification: ▪ IEM (vacuum interrupters with supporting structure) with energy accumu- lator spring ▪ Bolts, nuts, washers, dowel pins, retaining rings, grooved ball bearings ▪ Roller pin replacement kit, part number 10019494XX will be provided to your place of work by the OPS. EN 13 2 Step-by-Step 2.3.1.2 Tools - IEM Qt Description Part num- Note y ber 1 Toolkit VM + VR TS 6524640001 Punch drift for dowel pins Bolt connection type C - Torx bit (Torx driver) Bolt connection type X - Pull-off tool for drive sleeve Bolt connection type K - Tx bolt M4x50 Bolt connection type C - Retaining ring pliers A11, bent 1 Mounting device MD-VM nut holder 6530240000 Bolt connection type F 1 Auxiliary device AD-tensioning guide 6530010000 Spring energy accumula- tube tor 3-sector diverter switch in- serts 1 Mounting device MD-diverter switch 65234900 For installation of grooved insert ball bearing 1 Mounting device MD-resistor pack 6531260000 Installing and removing VR2-DSI transition resistors 2 Ring-type lifting bolt M8 For installing and remov- ing spring energy accumu- lator Table 4: Tools - IEM 2.3.1.3 Bolt connection elements IEM Ty Qty Elements of the bolt Size Part no. No. in Torque pe. connection drawing A 1 Allen bolt OT30 M8 x 25 782131XX 0092 20 Nm C 1 Dowel pin 8 x 12 766465XX 0022 9.5 Nm 1 Set nut SM4 SM4 400662XX 0020 1 Hex. head bolt OT30-8 M6 x 25 718416XX 0110 1 Washer 6.4 785247XX 0072 1 Spring washer 6 400372XX 0074 E 1 Half-round head bolt M5 x 14 766327XX 0115 5 Nm 1 OT30-8 5 401757XX 0054 1 Spring washer 5.3 712298XX 0052 1 Washer M5 10012208 0064 Square nut XX F 1 Half-round head bolt M5 x 12 74157900 0060 5 Nm 1 OT30-8 5 40175700 0054 1 Spring washer 5.3 712298XX 0052 1 Washer M5 451237 0062 Nut 14 EN 2 Step-by-Step Ty Qty Elements of the bolt Size Part no. No. in Torque pe. connection drawing G 1 Allen bolt OT30-8 M6 x 20 10020219 0105 4.5 Nm 1 Washer 5.3 XX 0052 1 Square nut M6 712298XX 0082 10008066 XX I 1 Hex. head bolt OT30-8 M6 x 22 748419XX 0076 6.5 Nm 1 Spring washer 6 400372XX 0074 1 Washer 6.4 785247XX 0072 1 Square nut 6 10008066 0082 XX J 1 Half-round head bolt M5 x 12 741579XX 0060 5 Nm 1 OT30-8 5.3 420713 0066 1 Washer M5 743862XX 0145 Nut for T grooves K 1 Hex. head bolt OT30 M8 x 40 745006XX 0135 20 Nm 1 Spring washer 8 400373XX 0130 M 1 Dowel pin 2 x 12 451433 0180 X 1 Half-round head bolt M5 x 20 766470XX 0120 5 Nm 1 OT30-8 5.3 712298XX 0052 1 Washer 5 401757XX 0054 Spring washer Table 5: Bolt connection elements IEM 2.3.1.4 Removing vacuum interrupters 2.3.1.4.1 Preparing the diverter switch insert Before starting work, make sure that the removed diverter switch insert and the new IEM (vacuum interrupters with supporting structure(Interrupter ex- change module)) are in basic position. In basic position, diverter switch in- sert and IEM are in final end position on side B. The new IEM is shipped in basic position. EN 15 2 Step-by-Step 6 cm In final end position on side B, the main contact is visible in the hole of the right-hand supporting bar (see in the following figure), while the hole of the left-hand supporting bar is empty (see in the following figure). 2 1 Figure 11: Diverter switch insert in final end position on side B Use crane to lift the diverter switch insert. Then remove the following (Posi- tion numbers refer to the following figure): ▪ lower retaining ring ( ), ▪ selector coupling ( ) using pull-off tool ( 6 cm ), ▪ Feather key ( ) and ▪ top retaining ring ( ). 4 1 5 3 2 Figure 12: Removing selector coupling 16 EN 2 Step-by-Step 6 cm Removing supporting bar stabilizer: remove 4x bolt connection G (see following figure) and remove the support- ing bar stabilizer ( ). 1 G Figure 13: Removing stabilizer NOTICE Risk of personal damage or injury, damage to property. Removal of diverter switch insert with removed stabilizer by insufficiently qualified personnel may lead to personal damage or injury and damage to property. There is a risk of tilting due to overloading of supporting bars. ► The diverter switch insert must only be placed on the supporting bars when the stabilizer is firmly installed. ► When the stabilizer is not installed6orcmnot completely attached using the bolts, the diverter switch insert must remain hooked to the crane hook and the rope must be kept tight. Figure 14: Risk of tilting of diverter switch insert when stabilizer is removed EN 17 2 Step-by-Step 2.3.1.4.2 Removing transition resistors and resistor connecting leads Deposit diverter switch insert on work surface (on supporting bars), leaving the diverter switch insert hooked to crane hook and keeping the rope tight. Remove bolt connections E and J. Remove the resistor connecting leads connected to the lower end of the transition resistor. When clamps (see in the following figure) are installed 6 cm on the transition resistor variant, first unscrew relevant bolts on bolt connec- tion I (see in the following figure) until clamps ( ) release resistor con- necting lead. Remove resistor connecting leads and retighten the bolts ( ). E J I 2 1 Figure 15: Removing resistor connecting leads 18 EN 2 Step-by-Step 6 cm Remove bolt connections F (connecting leads on varistor). F Figure 16: Removing bolt connections F Set up MD-resistor pack: Mounting aid (or "mounting device") for resistor pack (see following figure): ▪ Adjust holders ( ), using extension ( ) where necessary, to height of transition resistors - 160 mm, 310 mm or 400 mm are possible. ▪ Set blocking nuts ( ) to measure Y (measure Y = measure X - 10 mm) ( ): – 60 mm – 10 mm = 50 mm or – 100 mm – 10 mm = 90 mm or – 130 mm – 10 mm = 120 mm. ▪ Adjust holder so that the blocking nuts ( ) are at a radius of approx. 90 mm. ▪ Adjust bolts ( ) in a way that holders ( ) on bearing block ( ) can be moved toward diverter switch shaft. 1 strip isolation to 10 mm strip isolation to 90 mm 2 Measure X Measure Y Measure Y 5 4 3 6 Figure 17: MD-resistor pack EN 19 2 Step-by-Step NOTICE Risk of damage to property! If depositing of diverter switch insert is performed by insufficiently qualified personnel and/or safety instructions are not observed, there is a risk of damage to property. There is a risk of damage to the transition resistors due to the set up MD-resistor pack. ► It is important to follow the procedure below. 6 cm Figure 18: Risk of damage to transition resistors. Use crane to lift the diverter switch insert. Install MD-resistor pack in transi- tion resistors as far as it will go (see following figure). Figure 19: Installing MD-resistor pack in the transition resistors Pay attention that installation will go smoothly and easily. If it does not, en- sure that the holders (see position in the figure before MD-resistor pack) can move as they should on the bearing block. 20 EN 2 Step-by-Step NOTICE Risk of personal damage or injury. If depositing of diverter switch insert is performed by insufficiently qualified personnel and/or safety instructions are not observed, there is a risk of per- sonal damage or injury and damage 6tocm property. Risk of crushing ► Pay attention that your fingers are not between MD-resistor pack and work surface when depositing the diverter switch insert. Figure 20: Risk of crushing when depositing the diverter switch insert 6 cm Proceed in 3 steps to put down diverter switch insert and MD-resistor pack: ▪ Lower diverter switch insert and MD-resistor pack to approx. 100-120 mm above work surface. 100 - 120 mm Figure 21: Proceed in 3 steps to put down diverter switch insert and MD-resistor pack ▪ Then first put down MD-resistor pack - not separating it from the diverter switch insert. ▪ Then deposit diverter switch insert with supporting bars on the work sur- face. EN 21 2 Step-by-Step 6 cm Prepare blocking nuts for installation of the transition resistors:. Turn nuts (see in the following figure) upward manually until they touch the transition resistors. 1 Figure 22: Prepare blocking nuts for installation of the transition resistors Remove bolt connections I: For the lower bolt connections, make sure to prevent dropping of washer and square nut M6 by removing them (see in the following figure). In some cases, when the transition resistors rest on supports located at the lower end of the supporting bars (see6 detail cm below), it is necessary to put the transition resistors down from their support. Put the transition resistors down on the MD-resistor pack. I 1 Figure 23: Removing bolt connections I: 22 EN 2 Step-by-Step 6 cm Push holders (see in the following figure) with transition resistors, moving them as far as they will go (approx. 15 mm) on the mounting fixture towards middle of diverter switch insert. 1 Figure 24: Preparing transition resistors for removal Use crane to lift the diverter switch insert carefully; pay special attention that the supports on the supporting bars do not collide with the transition resis- 6 cm tors. Use the old bolts to reinstall stabilizer of supporting bars to diverter switch in- sert. (see bolt connections G in following figure) 1 G Figure 25: Removing stabilizer EN 23 2 Step-by-Step Then deposit diverter switch insert with supporting bars on the work surface 6 cm (separate from transition resistors). Leave the removed transition resistors on the MD-resistor pack for later in- stallation to the new IEM. Figure 26: Removing transition resistors NOTICE Risk of personal damage or injury, damage to property. Removal of retaining ring below the grooved ball bearing by insufficiently qualified personnel may lead to personal damage or injury and damage to property. ► Removal of retaining ring (see in the following figure) below the grooved ball bearing is only allowed when the diverter switch insert is de- posited on the work surface (on the supporting bars). 6 cm ► A detailed depiction of retaining ring below the grooved ball bearing can be found in the figure after next ( ). 1 Figure 27: Risk of injury when removing the retaining ring below the grooved ball bearing 24 EN 2 Step-by-Step 6 cm 1 Figure 28: Removing retaining ring 6 cm Removing TTV resistor connecting leads (see following figure): Remove bolt connections X using torx bit from tool kit and then remove the TTV resistor connecting leads. X Figure 29: Remove bolt connection X 2.3.1.4.3 Removing coupling tube and selector drive shaft 6 cm Removing bolt connections K: Remove bolts of lower shielding ring using extension, ball joint and socket adapter size 13 mm. K Figure 30: Removing lower shielding ring Attach lower shielding ring with cable tie to top shielding ring: Use pull-off tool to remove drive sleeves from coupling tube and remove coupling tube from the top. EN 25 2 Step-by-Step 6 cm Clean coupling tube inside and outside, and check visually for mechanical or electrical damage. K Figure 31: Removing drive sleeves of coupling tube 6 cm Removing bolt connection A: Remove bolt in lower coupling flange, and remove lower coupling flange and cam disk (see detail below). A 6 cm Figure 32: Removing coupling flange and cam disk Remove retaining ring below grooved ball bearing (see following figure ). 1 6 cm Figure 33: Removing retaining ring Pull out selector drive shaft vertically. Figure 34: Upper base plate of energy accumulator 26 EN 2 Step-by-Step Check needle roller bearing visually. Figure 35: Check needle roller bearing visually. 6 cm 2.3.1.4.4 Removing spring energy accumulator Remove the top bolts of bolt connection C, leaving the lower bolts un- touched for the moment (see figure below). C Figure 36: Removing top bolts of spring energy accumulator Remove dowel pins and set nuts (see following figure): Install bolt M4x50 ( ) from tool kit in6 set cm nut and continue screwing down until set nut and dowel pin are removed. Pay attention that the supporting bar does not get bent outward more than 0.5 mm. Remove lower bolts of bolt connection C ( ). C 1 2 Figure 37: Removing set nuts, dowel pins and lower bolts EN 27 2 Step-by-Step 6 cm Install two ring-type lifting bolts M8 on top plate of spring energy accumula- tor. 6 cm Figure 38: Preparing removal of spring energy accumulator Use crane to lift spring energy accumulator from IEM. Figure 39: Removing spring energy accumulator 2.3.1.5 Installing new vacuum interrupters 2.3.1.5.1 Preparation of IEM Unpack new IEM. All parts supplied for transportation or modification pur- poses must be removed. (Energy accumulator spring: see in the following figure and transportation device: see in the following figure). 28 EN 2 Step-by-Step 6 cm When returning the old IEM, make sure to install the transport device to the removed IEM. 2 1 Figure 40: Preparing the IEM NOTICE Damage on on-load tap-changer Damage to on-load tap-changer if connections are performed incorrectly ► When using bolts and nuts with OT30 or OT80 coating, always make sure that the bolted connection elements are free of oil and grease. Re- move oil and grease from all connection surfaces as much as possible. ► Be sure to install bolted connections with OT30 or OT80 coating in a sin- gle step with the specified tightening torque, and do not release or re- tighten them later. ► If a bolted connection must be released again, use new bolts or nuts with intact OT coating. Adhesive residues escaped from the OT nut must be removed. 2.3.1.5.2 Preparation of energy accumulator 2.3.1.5.2.1 Replacing roller pin (cam roller) The criteria and replacement of the roller pin (cam roller) (see in the fol- lowing figure) are described in the maintenance manual. EN 29 2 Step-by-Step An axial support ring is part of the roller pin replacement kit (see in the following figure). When an axial support ring is installed (delivery dates from April 25, 2016, to 6 cm January 3, 2018), install a new axial support ring. When no axial support ring is installed (delivery date from January 3, 2018), do not install an axial support ring. 1 2 Figure 41: Cog segment with cam roller (roller pin) 2.3.1.5.2.2 Replacing energy accumulator spring Removing the support pin 6 cm Unscrew attachment bolt on lower side of lower gear plate of spring energy accumulator (see in the following figure ) and remove support pin (see in the following figure) from the top. 2 1 Figure 42: Removing the support pin Removing support ring and energy accumulator spring: For this purpose, remove the following parts (position numbers refer to the following figure): ▪ 2 sleeve bearings ( ) ▪ Dowel pin( ) ▪ 2 washers ( ) ▪ Pin ( ) for support ring ▪ Support ring ( ). 30 EN 2 Step-by-Step 6 cm Remove energy accumulator spring ( ) from spring guide, the spring guide itself remains in place. 4 2 3 1 6 5 Figure 43: Removing the energy accumulator spring Installing new energy accumulator spring Install the new energy accumulator spring 6 cm (see in the following figure) that was shipped with the new IEM. The spring inside the spring guide (see in the following figure) will not be replaced. 1 2 Figure 44: Installing new energy accumulator 6 spring cm Install support ring (see following figure): Install support ring ( ), pin ( ), 2 washers ( ) and a new dowel pin ( ). 2 4 3 1 Figure 45: Installing the support ring EN 31 2 Step-by-Step Temporarily install support pin (see following figure): 6 cm Install two new sleeve bearings ( ) in the spring guide. For subsequent measuring and adjustment of value "L", provisionally use old bolt ( ) to install the support pin. 1 2 Figure 46: Installing support pin temporarily Only concerning 3-sector diverter switch inserts: Since 15 March, 2018, a longer energy accumulator spring has been in- stalled on 3-sector diverter switch inserts. Use auxiliary device (AD) "AD-tensioning 6 cm guide tube" (see in the following figure ) to pretension the longer energy accumulator spring, and install support pin. Subsequently, remove the auxiliary device "AD-tensioning guide tube" to measure specified value "L". 1 Figure 47: Tensioning energy accumulator spring on 3-sector diverter switch inserts using aux- iliary device 32 EN 2 Step-by-Step If the auxiliary device "AD-tensioning guide tube" (see in the previous fig- ure) is not available, use 2 open-end6wrenches cm to pretension the energy ac- cumulator spring (see in the previous figure), install support pin and screw it in place. This step is much easier if someone can assist you, but can also be managed alone once you have gained some experience. 1 Figure 48: Tensioning energy accumulator spring on 3-sector diverter switch insert without auxiliary device When installing a new energy accumulator 6 cm spring, corresponding specified value "L" must be set. Specified value "L" corresponding to the energy accu- mulator spring that was part of the delivery is indicated on the information disk (on the new IEM) (see in the following figure). 1 Figure 49: Specified value "L" on new energy accumulator spring Check specified value "L" (see in the following figure) by measurement: Pay attention to the following when measuring: ▪ Support pin (see in the following figure) is installed and energy accu- mulator spring is relaxed. (On 3-sector diverter switch inserts, remove auxiliary device AD-tensioning guide tube (see in the figure after next) before the measurement.) ▪ Support ring must be tilted outward (to the left in picture) (see in the following figure). ▪ Place caliper between support ring and slide washers (see in the fol- lowing figure). EN 33 2 Step-by-Step 6 cm 4 3 1 6 cm 2 Figure 50: Measuring actual value of adjustment dimension "L": 1 Figure 51: Tensioning energy accumulator spring on 3-sector diverter switch inserts using auxil- iary device Adjusting specified value "L" If measured value from previous step is different from specified value "L", adjust specified value "L" as follows: ▪ Remove support pin (see in the following figure). ▪ Set required specified value "L" by turning the spring guide, please ob- serve in this context: – 1 clockwise turn reduces measured value "L" by - (minus) 1 mm – 1 counterclockwise turn increases measured value "L" by + (plus) +1 mm. – After installation, dowel pin of support pin (see in the following fig- ure) must be showing toward energy accumulator carrier center. This means that only full turns by 360° are possible. ▪ Install support pin (see in the following figure) ▪ Measure specified value "L" again (see step before). 34 EN 2 Step-by-Step 6 cm If specified value "L" is set, use new OT30 bolt to complete installation of support pin (tightening torque = 8 Nm). 1 2 Figure 52: Setting actual value of adjustment dimension "L" to default value 2.3.1.5.3 Installing spring energy accumulator and drive shaft Basically, installation must be done in reverse order of removal of vacuum interrupters. When installing spring energy accumulator to the IEM (vacuum interrupters with supporting structure (Interrupter exchange module)), make sure that IEM and all components of the energy accumulator are in basic position. Checking basic position of IEM: 6 cm The marks on drive hub (see in the following figure) and upper base plate of the IEM (see in the following figure) must match. 1 2 Figure 53: Basic position of IEM EN 35 2 Step-by-Step When installing spring energy accumulator to IEM, pay attention to the fol- lowing: ▪ Marks on spring energy accumulator (see in the following figure) and IEM (see in the following figure) must match. 6 cm ▪ spring energy accumulator is in basic position (on side B), crank points outward (see in the following figure) and marks (made by a counter- sink) match (see in the following figure). 3 1 3 4 2 Figure 54: Paying attention to marks and basic position on spring energy accumulator Attach the spring energy accumulator using bolt connection type C. 6 cm Install dowel pin and set nut using punch drift (see in the following figure) from tool kit, paying attention to correct seating of set nut (see in the fol- lowing figure) (see details below). 2 C 1 Figure 55: Installing dowel pin and set nut Install drive shaft from the top, and install grooved ball bearing: 36 EN 2 Step-by-Step 6 cm The IEM is delivered without grooved ball bearing. Install grooved ball bear- ing (see in the following figure) to lower side of IEM using mounting de- vice MD‑diverter switch insert (see in the following figure). 1 2 Figure 56: Install grooved ball bearing To set axial play of drive shaft: 6 cm Use fitting washers to set axial play of drive shaft to 0.1 - 0.3 mm (see in the following figure). 1 Figure 57: Setting axial clearance of drive shaft 6 cm Measure axial play (0.1 - 0.3 mm) between retaining ring and fitting washers using feeler gauge (see in the following figure). 1 Figure 58: Measuring axial play 2.3.1.5.4 Installation of coupling tube The coupling tube must be installed in reverse order of removal. EN 37 2 Step-by-Step NOTICE Risk of personal damage or injury. If depositing of diverter switch insert is performed by insufficiently qualified personnel and/or safety instructions are not observed, there is a risk of per- sonal damage or injury and damage to property. Risk of crushing ► Ensure that your fingers are not between cam disk and diverter switch in- sert when placing the cam disk on the diverter switch insert. ► Place the diverter switch insert carefully onto the cam disk. Install cam disk (using bolt connection type A): 6 cm Put cam disk (see in the following figure) down carefully, paying attention that feather key and cam roller are in correct position. Install cam disk to drive shaft using tightening torque 20 Nm. 1 A Figure 59: Installing coupling flange and cam disk Install coupling tube to diverter switch insert with adjustment position on side B (see attachment "Adjustment position"): 6 cm Install coupling tube to lower coupling flange, paying attention that mark on coupling tube (see following figure ) matches mark on cam disk (see in the following figure) (diverter switch insert is in final end position on side B). 1 2 Figure 60: Installing coupling tube to diverter switch insert with adjustment position on side B (in final end position on side B) 38 EN 2 Step-by-Step Install coupling tube to diverter switch insert with adjustment position on side A (see attachment "Installation instruction vacuum interrupters and sup- porting structure"): Install coupling tube to lower coupling flange, paying attention that mark on 6 cm coupling tube (see in the following figure) matches mark on cam disk (see in the following figure) (diverter switch insert is in final end position on side B). 1 2 Figure 61: Install coupling tube to diverter switch insert with adjustment position on side A (in fi- nal end position on side B). 6 cm Use pull-off tool to install drive sleeves in coupling tube, using new bolts and bolt connection type K (20 Nm, see following figure). K Installing drive sleeves EN 39 2 Step-by-Step 2.3.1.5.5 Installing transition resistors and resistor connecting leads NOTICE Risk of personal damage or injury, damage to property. Removal of diverter switch insert with removed stabilizer by insufficiently qualified personnel may lead to personal damage or injury and damage to property. There is a risk of tilting due to overloading of supporting bars. ► The diverter switch insert must only be placed on the supporting bars when the stabilizer is firmly installed. ► When the stabilizer is not installed or not completely attached using the bolts, the diverter switch insert must remain hooked to the crane hook and the rope must be kept tight. NOTICE Risk of damage to property! ► Always make sure not to damage OT30 or OT80 coatings during installa- tion. ► When the resistor pack is installed, complete all bolt connections of the resistor connecting leads. Install resistor connecting lead to 6TTV cm (bolt connection type X) Use torx bit from tool kit to install bolt connection type X (see following fig- ure). X Figure 62: Installing bolt connections type X 40 EN 2 Step-by-Step Replace 4 nuts per sector of bolt connection type J: Use screwdriver (see in the following figure) to press down holders (see 6 cm in the following figure) (left and right), releasing the retainer clip (see in the following figure) and remove the retainer clip. Replace retainer clip and 4 nuts for T grooves (see in the following figure). 1 J 2 4 3 Figure 63: Removing retainer clip and nuts for T grooves Make sure that the transition resistors are as close as possible to the central shaft. This is achieved by moving the holders (see in the following figure) as much as possible in direction of the shaft. Use crane to lower diverter switch insert carefully to the transition resistors. Pay attention to the following: ▪ The transition resistors must not collide with the supports on the support- ing bars of the diverter switch insert (see in the following figure) and ▪ The diverter switch shaft must not collide with the guide tube of MD-resis- tor pack (see in the following figure). EN 41 2 Step-by-Step 1 strip isolation to 10 mm strip isolation to 90 mm 2 Measure X Measure Y Measure Y 5 4 3 6 cm 6 Figure 64: MD-resistor pack 1 2 Figure 65: Lowering IEM to transition resistors Move holders on bearing block outward until transition resistors touch the supporting bars. 42 EN 2 Step-by-Step 6 cm Check installation height of transition resistors, using blocking nuts (see in the following figure) to adjust height where necessary, enabling you to in- stall the bolts type I later on. 1 Figure 66: Preparing transition resistors for installation If any spacer sleeves are installed, check their correct seat before installing transition resistor (see in the following figure). In those variants where the transition resistors are seated on a support on the supporting bar, put transition resistors 6 cm down on support (see in the following figure) and install middle bolts of connection type I (see in the following figure). Screw down the bolts only to an extent where the bolt lock glue will not yet be damaged. 1 3 I 2 Figure 67: Attaching transition resistors EN 43 2 Step-by-Step Preparing bolt connection type I The middle bolts were already installed in the previous step. Reinstall top bolts (see in the following figure). Reinstall lower bolts (see in the fol- lowing figure ). Proceed as follows for variants where the transition resistors are seated on the bottom end of the supporting bars ▪ on supports at lower end of supporting bars: – install washer (see in the following figure); the washer is kept in place by the support (see in the following figure). – Install square nut M6 (see in the following figure) – install lower bolts. ▪ not on supports: 6 cmstep. – install washer and nut in one work NOTICE! Screw down the bolts only to an extent where the bolt lock glue is not damaged. I 1 6 5 4 2 Figure 68: Preparing bolt connection type I Preparing bolt connection type E ▪ Place resistor connecting lead (see in the following figure) in desired position and hold it there using clamp (see in the following figure) and corresponding bolt of bolt connection type I (see in the following fig- ure). ▪ Position new square nut (see in the following figure) using punch drift (see in the following figure) and screwdriver (see in the following figure). 44 EN 2 Step-by-Step 6 cm E 1 4 5 6 2 3 Figure 69: Preparing bolt connection type E Installing bolt connection type E ▪ hold square nut (see in the following 6 cm figure ) in correct position using screwdriver ▪ install new bolt, tightening torque = 5 Nm; the nut cannot turn in this process. E 1 Figure 70: Installing bolt connection type E Finish bolt connection type I (6.5 Nm) EN 45 2 Step-by-Step 6 cm Paying attention to correct seat of clamps (see following figure). I Figure 71: Finish bolt connection type I: Installing bolt connection type F 6 cm Install connecting lead to varistor using mounting device MD-VM nut holder (see in the following figure) and tightening torque 5 Nm. F 1 Figure 72: Installing bolt connection type F using mounting device 46 EN 2 Step-by-Step 6 cm If mounting device MD-nut holder (see in the following figure) is not avail- able, use pliers or open-end wrench size 8 mm to install bolt connection type F. F Figure 73: Installing bolt connection type F without mounting device Installing bolt connection type J Please note that bolt connection type J: ▪ on 2-sector diverter switch insert delivered from October 31, 2019, and ▪ on 1- and 3-sector diverter switch inserts from production finish date April 14, 2020 onwards contains half-round head bolt OT 30‑8. Before the delivery dates specified above, a hex. head bolt OT 30-8 was used for connection type J. Please note that it is absolutely necessary to use 6 cm a half-round head bolt OT 30-8 in bolt connection type J. Use tightening torque 5 Nm to install transition resistor leads (see following figure). J Figure 74: Installing resistor connecting leads EN 47 2 Step-by-Step 6 cm Install stabilizer (see in the following figure) of supporting bars using 4 new bolts (bolt connection type G, tightening torque = 4.5 Nm). 1 G Figure 75: Installing stabilizer 6 cm Install selector coupling (see in the following figure), feather key (see in the following figure) and corresponding retaining rings (see and in the following figure). 4 1 5 3 2 Figure 76: Installing the selector coupling 48 EN 2 Step-by-Step 2.3.1.6 Drawing of screwing positions EN 49 2 Step-by-Step 2.3.1.7 Drawing spring energy accumulator as a whole EN 51 2 Step-by-Step 6 cm 2.3.1.8 Figure adjustment position Figure 77: Adjustment position 1 of 2 54 EN 2 Step-by-Step 6 cm Figure 78: Adjustment position 2 of 2 2.3.1.9 Change log - Vacuum interrupters - Replacement (600,000) 7 July 2022 TSC - Steindl 1. Attachment of transition resistor - bolt connection I: tightening torque decreased from 9.5 Nm to 6.5 Nm EN 55 2 Step-by-Step 2. Transfer of instructions to the CDS platform 17 March 2022 TSC Steindl 1. First publication 2.3.2 Replacement oil compartment contacts (1,200,000) Replacement of oil compartment contacts is due after every 1,200,000 oper- ations. 6 cm 2.3.2.1 Drawing Implementation VR® III C3 C1 Figure 79: VACUTAP® VR® (2016) 3-sector version 56 EN 2 Step-by-Step 6 cm 2.3.2.2 Drawing Implementation VR® II Use red labeling for VRSI2622, VRMI2622, VRLI2622, VRHI2622. C3 C1 C2 C1 Ua/S2 Ub/S3 Figure 80: VACUTAP® VR® (2016) 2-sector version EN 57 2 Step-by-Step 6 cm 2.3.2.3 Drawing Implementation VR® I C3 C2 C1 C2 Figure 81: VACUTAP® VR® (2016) 1-sector version 2.3.2.4 Bolt connection elements oil compartment contacts Figure Con- Qt Elements of the bolt Size Part no. Torque nect. y. connection C1 1 Allen bolt OT30 M10x2 1000718 35 Nm 1 Spring washer 5 500 (=5.56 V) 10 4003740 0 C2 1 Allen bolt OT30 M10x2 1000718 35 Nm 1 Spring washer 5 500 (=5.56 V) 1 Washer 10 4003740 10 0 7796090 1 C3 1 Allen bolt OT80 M10x2 0838780 35 Nm 1 Spring washer 0 0 (=5.56 V) 10 4003740 0 Table 6: Bolt connection elements of oil compartment contacts VACUTAP® VR® (2016) 58 EN 2 Step-by-Step 2.4 One-time retrofit and modifications EN 59 3 Assemblies 3 Assemblies 3.1 Introduction NOTICE Risk of personal damage or injury, damage to property or mal- function. If work is performed by insufficiently qualified personnel and/or safety in- structions are not observed, there is a risk of personal damage or injury, damage to property or malfunction. ► Safety, hazard and other information included in the MR operating in- structions for the relevant on-load tap-changer type must be observed! ► Please read the instructions carefully before starting work. ► The realization of the instructions below requires profound knowledge and experience that correspond to the knowledge acquired during a train- ing at MR about maintenance of the relevant on-load tap-changer type. ► It is absolutely necessary that the diverter switch insert (or selector switch insert, respectively) has been removed. 3.2 General 3.2.1 Replacement intervals diverter switch insert, selector switch insert, diverter switch oil compartment contacts and on-load tap- changer The tables in the instructions below show when to replace which subassem- bly groups of MR on-load tap-changers and when to perform tap selector maintenance. The relevant operating instructions or technical instructions for the respec- tive on-load tap-changer must be observed. 60 EN 3 Assemblies OILTAP® / VACUTAP® diverter switch insert and oil compartment On-load tap-chang- Replacement ers Oil compartment contact Diverter switch OLTC (1) insert OILTAP® M 2,000,000 – 2,400,000 800,000 4,000,000 OILTAP® MS Replacement only within 800,000 4,000,000 scope of selector mainte- nance. When retrofitting to VM®, no replacement necessary Please note for on-load tap-changer type OILTAP® M or OILTAP® MS: When the replacement interval for oil compartment contacts is reached, the diverter switch in- sert should be retrofitted with diverter switch insert type VACUTAP® VM®. In this case, the replacement of the oil compartment contacts is not necessary. If retrofitting to type VACUTAP® VM® is not possible, the oil compartment contacts must be replaced according to above-mention interval. OILTAP® R 800,000 800,000 4,000,000 OILTAP® RM 800,000 800,000 4,000,000 OILTAP® G ---- 800,000 4,000,000 (2) VACUTAP® VM® 2,000,000 – 2,400,000 1,200,000 3,600,000 VACUTAP® VMS® Replacement only within 600,000 3,600,000 scope of selector mainte- nance VACUTAP® VRC, 1,200,000 1,200,000 3,600,000 VRD, VRE, VRF, VRG (3) VACUTAP® VRF I 300,000 1,200,000 3,600,000 1601 VACUTAP® VRF I 1801 VACUTAP® VRS, Details - Checking contact 1,200,000 3,600,000 VRM, VRL®, VRH®, wear on main contact and VRX® replacement intervals of oil compartment contacts [►Section 3.3.1.1, Page 64]Details - Checking con- tact wear on main contact and replacement intervals of oil compartment contacts VACUTAP®VRL I 600,000 (4) 1,200,000 3,600,000 1801-2401 network operation EN 61 3 Assemblies On-load tap-chang- Replacement ers Oil compartment contact Diverter switch OLTC (1) insert VACUTAP®VRL I 300,000 (4) 1,200,000 3,600,000 2601-3201 network operation VACUTAP®VRL I 300,000 (4) 1,200,000 3,600,000 1801-2401 arc fur- nace operation Table 7: Overview OILTAP® / VACUTAP® on-load tap-changers (1) OLTC includes the following subassembly groups: oil compartment, tap selector, motor-drive unit, drive shafts (2) Measure diameter of worn shape on oil compartment contacts after every 600,000 operations (3) Without VACUTAP® VRF I 1601, 1801 (4) When replacing the vacuum interrupters with supporting structure or the diverter switch insert, the oil compartment contact must necessarily be re- placed. OILTAP® / VACUTAP® selector switch insert / ECOTAP® The following table shows replacement on the basis of number of opera- tions, of subassembly groups for on-load tap-changers type OILTAP®, VACUTAP® and ECOTAP®. On-load tap-chang- Replacement ers Oil compartment contact Selector switch OLTC (5) insert ECOTAP® VPD® ---- ---- 500,000 VACUTAP® VVS® ---- ---- 500,000 VACUTAP® VV® ---- 1,200,000 4,000,000 OILTAP® V (without Oil compartment contact V 800,000 4,000,000 V200) 350 / 500 / 700Oil compart- ment contact V 350 / 500 / 700 OILTAP® V200 Oil compartment contact V 800,000 4,000,000 200Oil compartment contact V 200 Table 8: Overview OILTAP® / VACUTAP® and ECOTAP® on-load tap-changers (5) OLTC includes the following subassembly groups: oil compartment, tap selector, motor-drive unit, drive shafts 62 EN 3 Assemblies Selector Selector Selector size On-load tap-changer type Selector mainte- type nance New selector RC, RD, RDE VACUTAP® VRF, VRS, 1,200,000 type R VRM, VRL®, VRH®, VM® OILTAP® M, R RE, RF VACUTAP® VRS, VRM, 1,200,000 VRL®, VRH®, VRX® OILTAP® R Old selector C, D VACUTAP® VRD, VRF 1,000,000 type R OILTAP® R E VACUTAP® VRG 1,000,000 OILTAP® R Selector type B, C, D, DE VACUTAP® VRC, VRE, Selector contact Ø M VRS®, VRM®, VM®, 22 mm: VMS® (6) 1,200,000 OILTAP® M, RM Selector contact Ø 14 mm: 1,200,000 Selector type B VACUTAP® VMS® 1,000,000 MS OILTAP® MS Selector type D, E OILTAP® G 1,000,000 G VV change- -- VACUTAP® VV 2,100,000 over selector Table 9: Overview selector (6) VMS® : selector size C only 3.2.1.1 Change log 2023-04-28 1. Adjustment replacement criterion of oil compartment contacts OILTAP® M, VACUTAP® VM, VACUTAP® VRL® I arc furnace operation 2. General re-working and adjustment of interval cycles, e.g. interval se- lector maintenance OILTAP® M 3. DS3200 added EN 63 3 Assemblies 3.3 Contact system, switching element 3.3.1 Checking contact wear on main contact and replacement intervals of oil compartment contacts In the following, the contact wear on the main contact, as well as the re- placement criteria of the oil compartment contacts on the on-load tap- changer type VRS, VRM, VRL, VRH, VRX (includes all OLTC VR2) is de- scribed. This check must be performed during every maintenance and documented accordingly in the service report. The oil compartment contacts are replaced depending on condition, but at the latest after 1,200,000 tap-change operations. 3.3.1.1 Details - Checking contact wear on main contact and replacement intervals of oil compartment contacts In the following, the contact wear on the main contact, as well as the re- placement criteria of the oil compartment contacts on the on-load tap- changer type VRS, VRM, VRL, VRH, VRX (includes all OLTC VR2) is de- scribed. This check must be performed during every maintenance and documented accordingly in the service report. The oil compartment contacts are replaced depending on condition, but at the latest after 1,200,000 tap-change operations. General To find out whether condition-based replacement must be carried out before the operations-dependent interval (1,200,000 operations) is reached, contact wear must be measured. There are generally two ways to measure contact wear: ▪ Measurement of wear width b on DSI ▪ Measurement of wear depth t on oil compartment contact NOTICE! Using measured value "Wear depth b on DSI" is only permitted if the number of DSI contact operations exceeds or is equal to the number of oil compartment contact operations. Otherwise, wear depth t on the oil com- partment contact must be measured and evaluated. 64 EN 3 Assemblies See the table below for examples. Specific situation Permissible way of determining wear Performing first maintenance Measurement of wear width b on DSI is per- mitted During last maintenance, IEM or DSI Measurement of wear width b on DSI is per- and oil compartment contacts were mitted replaced During last maintenance, IEM or DSI Measurement of wear width b on DSI is NOT were replaced, but not the oil com- permitted. Measurement of wear depth t on partment contacts. oil compartment contact must be performed. Table 10: Examples Measurement of contact wear on main contact Measurement of wear width b on diverter switch insert Measure width b of commutation marks on all moving DSI main contacts (side A and side B) using a caliper (see following figure). The decisive wear criterion as described in section 3 is the widest commutation mark on the complete DSI. Commutation mark Figure 82: Measuring width b of commutation marks on DSI Measurement of wear depth t on oil compartment contact Measure depth t of the commutation marks on all fixed main contacts in the oil compartment (side A and side B) using caliper or depth gauge (see fol- lowing figure). The deepest commutation mark in the complete oil compart- ment is the relevant value for the wear criteria specified in section 3. Commutation mark Figure 83: Measuring depth t of the commutation marks in the oil compartment EN 65 3 Assemblies Wear-dependent criteria The oil compartment contacts must always be replaced before reaching the following wear values (further operation is not allowed before the replace- ment): ▪ Width b of a commutation mark on a moving main contact of the DSI > 8.0 mm ▪ Depth t of a commutation mark on a fixed main contact in the oil compart- ment > 0.6 mm Consider the following basic points for your decision whether or not the wear limits will be exceeded before the next maintenance interval is reached: Number of tap-change operations of the oil compartment contacts: 300,000 300,000 operations correspond to the number of tap-change operations of the maintenance interval, up to 350,000 operations are tolerable. Type of measurement Measured value and action Example 1 Example 2 Wear width b DSI < 4.5 mm > 4.5 mm Wear depth t oil compartment con- Not measurable > 0.2 mm tact Contact replacement necessary at Not necessary Necessary next maintenance? Table 11: Number of tap-change operations of the oil compartment contacts: 300,000 Number of tap-change operations of the oil compartment contacts: 600,000 Type of measurement Measured value and action Example 3 Example 4 Wear width b DSI < 6.0 mm > 6.0 mm und < 8.0 mm Wear depth t oil compartment con- < 0.2 mm > 0.2 mm und < 0.3 mm tact Contact replacement during next Not necessary Necessary maintenance? Table 12: Number of tap-change operations of the oil compartment contacts: 600,000 Number of tap-change operations of the oil compartment contacts: 900,000 900,000 operations correspond to the number of tap-change operations of the maintenance interval, up to 950,000 operations are tolerable. 66 EN 3 Assemblies Number of tap-change operations of the oil compartment contacts: 900,000 Type of measurement Measured value and action Example 5 Wear depth t oil compart- must be < 0.4 mm ment contact Contact replacement dur- Contacts must be replaced during next maintenance ing next maintenance? because 1,200,000 operations will be reached. 3.3.2 Vacuum interrupters - Replacement (600,000) The instructions below describe how to replace the vacuum interrupters and supporting structure on a 3-sector diverter switch insert. The same proce- dure applies to diverter switch inserts with 1 or 2 sectors. Depending on on-load tap-changer type and its step capacity, replacement must be performed, as a general rule, after every 300,000 (A) or 600,000 (B) operations (see maintenance manual for specific replacement interval): ▪ After 290,000 (A) or 580,000 (B) operations at the earliest ▪ After 310,000 (A) or 620,000 (B) operations at the latest General Please see chapters Material - IEM [►Section 3.3.2.1, Page 68] and Tools - IEM [►Section 3.3.2.2, Page 69] for the material and tools required for work. Please see chapter Drawing of screwing positions [►Section 3.3.2.6, Page 104] for instructions how to make the relevant bolt connections that are opened during the replacement of the vacuum interrupters with supporting structure. NOTICE Risk of personal damage or injury, damage to property. Transport and setup of the diverter switch insert by insufficiently qualified personnel may lead to personal damage or injury and damage to property. There is a risk of tilting due to high center of gravity. ► The diverter switch insert must be carefully transported. ► The diverter switch insert must be installed on a level surface. ► The diverter switch insert must be secured against tipping. EN 67 3 Assemblies 6 cm Figure 84: Risk of tilting of diverter switch insert WARNING Danger of tipping! On the basis of its elevated center of gravity, the diverter switch insert can tilt during transport or in unstable position. This can lead to injuries and property damage. ► Transport the diverter switch insert carefully.