OILTAP V-CDS-Komplett Maintenance Instructions PDF
Document Details
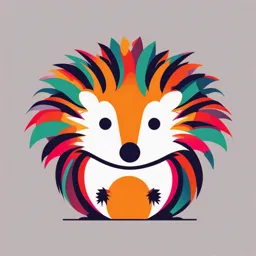
Uploaded by ValuableSugilite
Pink University
Tags
Related
- On-Load Tap Changer Type T Inspection Instructions PDF
- VACUTAP VR 2010 Spare Parts & Maintenance PDF
- On-load tap-changer VACUTAP® VV Maintenance Manual WA 241/05 PDF
- On-Load Tap Changer Type H Inspection Instructions PDF
- VACUTAP® VM® Maintenance Instructions PDF
- VACUTAP® VR I On-Load Tap-Changer Maintenance Manual PDF
Summary
This document is an instruction manual for maintaining OILTAP® V on-load tap-changers. It provides details on spare parts, step-by-step procedures for maintenance and replacements, and troubleshooting. Focused on technical maintenance and replacing parts.
Full Transcript
EN © All rights reserved by Maschinenfabrik Reinhausen Dissemination and reproduction of this document and use and disclosure of its content are strictly prohibited unless expressly permitted. Infringements will result in liability for compensation. All rights reserved in the event of the granting...
EN © All rights reserved by Maschinenfabrik Reinhausen Dissemination and reproduction of this document and use and disclosure of its content are strictly prohibited unless expressly permitted. Infringements will result in liability for compensation. All rights reserved in the event of the granting of patents, utility models or designs. The product may have been altered since this document was published. We reserve the right to change the technical data, design and scope of supply. Generally the information provided and agreements made when processing the individual quotations and orders are binding. The product is delivered in accordance with MR's technical specifications, which are based on information provided by the customer. The customer has a duty of care to ensure the compatibility of the specified product with the customer's planned scope of application. The original operating instructions were written in German. Table of contents Table of contents 1 Introduction......................................................................................................................... 5 2 Spare parts list.................................................................................................................... 6 2.1 Spare parts list - OILTAP® V.............................................................................................................. 7 2.1.1 Spare parts list - OILTAP® V ................................................................................................................................ 8 3 Step-by-Step ..................................................................................................................... 13 3.1 Note spare parts list.......................................................................................................................... 13 3.2 Tests and condition-based parts replacement at each maintenance ............................................... 13 3.2.1 Checking bearing block for cracks, V 200 / V 250 / V 500 .................................................................................. 13 3.2.2 Protrusion of hollow shaft in switching contacts V 200 /V 250 ............................................................................ 16 3.2.3 Permitted contact wear of oil compartment contact ............................................................................................ 17 3.2.4 Change-over selector contacts - Cleaning .......................................................................................................... 18 3.2.5 Max. permitted contact wear ............................................................................................................................... 19 3.3 Parts replacement after fixed number of tap-change operations intervals ....................................... 21 3.4 One-time retrofit and modifications................................................................................................... 21 3.4.1 Until 30 April, 1984 - Replacement of main contacts .......................................................................................... 21 3.4.2 Until 18 August, 1991 - Modification of inner screening rings ............................................................................. 24 3.4.3 Until 31 December 1992 - Installation of spring plates at the outer shielding rings of the switching column ...... 26 3.4.4 Until 31 October, 1995 - Additional securing of dowel pin .................................................................................. 32 3.4.5 Until 31 July, 1999 - Replacement of bearing block transition contacts and main switching contacts................ 33 3.4.6 Until 30 September, 2007 - Replacement of gear unit with tension springs ....................................................... 36 3.4.7 Until 31 July, 2009 - Modification tension-spring energy accumulator to tumble-riveted connection OILTAP® V ... 37 4 Assemblies........................................................................................................................ 44 4.1 General ............................................................................................................................................. 44 4.1.1 Replacement intervals diverter switch insert, selector switch insert, diverter switch oil compartment contacts and on-load tap-changer ............................................................................................................................................ 44 4.1.2 Location of pipes type V and G ........................................................................................................................... 48 4.2 Contact system, switching element .................................................................................................. 50 4.2.1 Checking bearing block for cracks, V 200 / V 250 / V 500 .................................................................................. 50 4.2.2 Protrusion of hollow shaft in switching contacts V 200 /V 250 ............................................................................ 53 4.2.3 Permitted contact wear of oil compartment contact ............................................................................................ 54 4.2.4 Change-over selector contacts - Cleaning .......................................................................................................... 55 4.2.5 Until 30 April, 1984 - Replacement of main contacts .......................................................................................... 55 EN 3 Table of contents 4.2.6 Until 31 October, 1995 - Additional securing of dowel pin .................................................................................. 58 4.2.7 Until 31 July, 1999 - Replacement of bearing block transition contacts and main switching contacts................ 59 4.2.8 Max. permitted contact wear ............................................................................................................................... 62 4.3 Energy accumulator, gearbox........................................................................................................... 64 4.3.1 Adjustment of energy accumulator...................................................................................................................... 64 4.3.2 Until 30 September, 2007 - Replacement of gear unit with tension springs ....................................................... 68 4.3.3 Until 31 July, 2009 - Modification tension-spring energy accumulator to tumble-riveted connection OILTAP® V ... 70 4.3.4 Switching time measurement type OILTAP® V .................................................................................................. 75 4.3.5 Preliminary information ....................................................................................................................................... 98 4.4 Supporting cylinder/supporting bars, coupling shaft, switching column.......................................... 121 4.4.1 Replacement of current ring connection ........................................................................................................... 121 4.4.2 Until 18 August, 1991 - Modification of inner screening rings ........................................................................... 122 4.4.3 Until 31 December 1992 - Installation of spring plates at the outer shielding rings of the switching column .... 124 4.5 Transition impedance and protective circuit ................................................................................... 131 4.6 Oil compartment ............................................................................................................................. 131 4.6.1 Replacement of fixed contacts on OLTC type V ............................................................................................... 131 4 EN 1 Introduction 1 Introduction NOTICE Risk of personal damage or injury, damage to property or malfunction. If work is performed by insufficiently qualified personnel and/or safety instructions are not observed, there is a risk of personal damage or injury, damage to property or malfunction. ► Safety, hazard and other information included in the MR operating instructions for the relevant on-load tap-changer type must be observed! ► Please read the instructions carefully before starting work. ► The realization of the instructions below requires profound knowledge and experience that correspond to the knowledge acquired during a training at MR about maintenance of the relevant on-load tap-changer type. ► It is absolutely necessary that the diverter switch insert (or selector switch insert, respectively) has been removed. EN 5 2 Spare parts list 2 Spare parts list 6 EN 2 Spare parts list 2.1 Spare parts list - OILTAP® V EN 7 Spare parts for on-load tap-changers Type V Designation Pictures of parts Pcs Part no. Date: 30.03.2017 Doc.: V97001.xls Remarks O ring 1 400308:00 red and green marking O ring for upper gear unit Pressure ring segment for upper gear unit Locking plate 2 860088 3 712045:00 3 057971:00 Notched nail Washer O ring - upper part/lower part of bell-type tank O ring head/oil compartment 18 18 1 1 until June 1980 (=130350) 453237 051331:00 400814:00 400816:00 Speedometer flexible shaft (only V200) up to 088980:07 OLTC no. 132012 086948:12 until approx. 31.02.82 V 200 - ten- and twelve-part : 1 set of movable contacts consisting of: Switching contacts Auxiliary contacts, right Auxiliary contacts, left with accessories 1 3 3 087094:08 3 087093:08 V 200 - 14-part: 1 set of movable contacts consisting of: Switching contact Auxiliary contacts, right Auxiliary contacts, left with accessories 1 3 3 3 V 350 - ten- and twelve-part : Movable switching auxiliary contact with accessor. V 350 - 14-part: 1 set of mov. spare contact consisting of: Switching contacts Auxiliary contacts, right Auxiliary contacts, left with accessories 088982:07 087252:12 087014:08 087013:08 1 088975:07 1 3 3 3 088978:07 086063:12 086064:11 086065:11 Spring system complete Spring plates for screening rings V__15001en V__05004en Bearing block Cyl. screw M 6x12 18 706646:00 18 707732:00 Operating key complete 1 099915:02 Mounting devices 1 631502:01 Special brushes for cleaning the on-load tap-changer d = 400 d = 140 d = 40 with mounting rod and extension, mounting rod 1 1 1 1 1 For this documentation we reserve all rights according to standard DIN 34, section 2.1. 090786:00 090782:00 090781:00 089274:01 067997:01 Page 1 of 5 Pictures of parts Spare parts for on-load tap-changers Type V Designation Pcs Part no. Date: 30.03.2017 Doc.: V97001.xls Remarks Lifting device for suction pipe 1 631187:00 Small parts (screws, nuts, lock tabs etc.) 1 089011:03 1 set of spare contacts V I 500, movable with accessories 10- and 12-part with movable main contact 1 092658:09 Y + D same design 1 set of spare contacts V I 500, fixed with accessories 10-part- horizontal + vertical 1 092668:01 horizontal - standard design 1 set of spare contacts V I 500, fixed with accessories 12-part - horizontal + vertical 1 092669:01 1 set of spare contacts V I 350, fixed with accessories 14-part - horizontal + vertical 1 092667:01 1 set of spare contacts V I 350, fixed with accessories 12-part - horizontal + vertical 1 092666:01 1 set of spare contacts V I 350, fixed with accessories 10-part - horizontal + vertical 1 092665:01 1 set of spare contacts V I 200, fixed with accessories 10-part, horizontal 10 V10259 up to 09.03.84 :0001 complete parts required (drill hole, screw horizontal) according list of components For this documentation we reserve all rights according to standard DIN 34, section 2.1. Page 2 of 5 Pictures of parts Spare parts for on-load tap-changers Type V Designation Pcs Part no. Date: 30.03.2017 Doc.: V97001.xls Remarks 1 set of spare contacts V I 200, fixed with accessories 10-part, horizontal 1 092653:01 from 09.03.84 on 1 set of spare contacts V I 200, fixed with accessories 10-part, vertical 10 V10259 up to 09.03.84 :0002 terminal contact turned by 90° complete parts required according list of components 1set of spare contacts V I 200, fixed with accessories 10-part, vertical 1 092655:01 from 09.03.84 on 1 set of spare contacts V I 200, fixed with accessories 12-part, vertical 12 V10259 up to 09.03.84 :0003 complete parts required terminal contact turned by 90° according list of components 1set of spare contacts V I 20, fixed with accessories 12-part, horizontal 1 092657:01 from 09.03.84 on 1 set of spare contacts V I 200, fixed with accessories 12-part, vertical 1 V10259 up to 09.03.84 :0003 complete parts according to list of components 1 set of spare contacts V I 200, fixed with accessories 12-part, vertical 1 092660:01 from 09.03.84 on 1 set of spare contacts V I 200, fixed with accessories 14-part, horizontal 14 V10259 up to 09.03.84 :0004 complete parts according to list of components 1 set of spare contacts V I 200, fixed with accessories 14-part, horizontal For this documentation we reserve all rights according to standard DIN 34, section 2.1. 1 092662:01 from 09.03.84 on Page 3 of 5 Pictures of parts Spare parts for on-load tap-changers Type V Designation 1 set of spare contacts V I 200, fixed with accessories 14-part, vertical Pcs Part no. Date: 30.03.2017 Doc.: V97001.xls Remarks 1 V10259 up to 09.03.84 :0005 complete parts according to list of components 1 set of spare contacts V I 200, fixed with accessories 14-part, vertical 1 092664:01 from 09.03.84 on 1 set of spare contacts V I 350, movable with accessories 10-part and 12-part 1 088973:07 1 set of spare contacts V I 700, movable with accessories 10-part and 12-part fixed - 10-part: fixed contact slotted socket screw fixed - 12-part: fixed contact slotted socket screw 1 088974:07 20 20 24 24 060854:02 401049:00 060894:02 401049:00 1 set of spare contacts V I 350, movable with accessories 14-part 1 088976:07 1 set of spare contacts V I 700, movable with accessories 14-part 1 088977:07 fixed - 14-part 28 061935:02 28 401049:00 1 set of spare contacts V I 200, movable with accessories 10-part and 12-part 1 088979:07 1 set of spare contacts V I 200, movable with accessories 14-part 1 088981:07 Rev. switch contact shell 30 - 60 kV - old type 1 200382:01 complete with contacts For this documentation we reserve all rights according to standard DIN 34, section 2.1. Page 4 of 5 Pictures of parts Spare parts for on-load tap-changers Type V Designation Cocking pin 10 x 50 Hex. head screw M 8 x 25 Lock tab For this documentation we reserve all rights according to standard DIN 34, section 2.1. Pcs Part no. Date: 30.03.2017 Doc.: V97001.xls Remarks 1 400425:00 2 400519:00 1 063481:00 Page 5 of 5 3 Step-by-Step 3 Step-by-Step 3.1 Note spare parts list NOTICE! The tests, parts replacements and one-time retrofittings described in the image list must be - especially in case of performance of maintenance - considered in addition to the intructions listed below. Link to spare parts list: Spare parts list [►Section 2, Page 6] 3.2 Tests and condition-based parts replacement at each maintenance 3.2.1 Checking bearing block for cracks, V 200 / V 250 / V 500 When performing work on on-load tap-changer type V 200 / V 250 / V 500, always check top and lower bearing blocks of switching contacts and transition contacts for cracks. Replace the bearing blocks if you detect any cracks. The two following figures show possible cracks. Figure 1: Bearing block, front view EN 13 3 Step-by-Step Figure 2: Bearing block, rear view 3.2.1.1 Checking bearing block for cracks, V 200 / V 250 / V 500 When performing work on on-load tap-changer type V 200 / V 250 / V 500, always check top and lower bearing blocks of switching contacts and transition contacts for cracks. Replace the bearing blocks if you detect any cracks. The two following figures show possible cracks. Figure 3: Bearing block, front view 14 EN 3 Step-by-Step Figure 4: Bearing block, rear view EN 15 3 Step-by-Step 3.2.2 Protrusion of hollow shaft in switching contacts V 200 /V 250 Ensure for on-load tap-changers type V 200/250, that protrusion of hollow shaft of switching contacts below the swing frame may not exceed 1.6 ± 0.5 mm. The hollow shaft must not be slack. If any of the two conditions is not fulfilled, replace the complete switching contact roller. Switching contact Swing frame 1.6 ± 0.5 mm Hollow shaft Figure 5: Protrusion of hollow shaft in switching contacts V 200 16 EN 3 Step-by-Step 3.2.3 Permitted contact wear of oil compartment contact 3.2.3.1 Oil compartment contact V 200 A drawing of a worn oil compartment contact is shown in the following figure. The contact must be replaced if one of the following criteria is fulfilled: ▪ d1 ≥ 4 mm ▪ d2 ≥ 4 mm Please note that d1 and d2 refer to wear depth measured from the interior side of the oil compartment contact (i.e., the side showing towards middle of oil compartment). Only contacts exceeding the wear limits need to be replaced. All other contacts can remain installed in the oil compartment. Wear recess Interior side of d2 oil compartment contact d1 Wear recess Figure 6: Drawing of worn arcing contact A photo of a worn oil compartment contact is shown in the following figure. d1 d2 Figure 7: Photo of worn arcing contact EN 17 3 Step-by-Step 3.2.3.2 Oil compartment contact V 350 / 500 / 700 The following figure shows a worn arcing contact V 350/500/700. The contact must be replaced if one of the following criteria is fulfilled: ▪ d1 < 1 mm ▪ d2 ≤ 0 mm Please note that d1 is min. distance from wear recess to iron base, and d2 is min. distance from wear recess to counterbore. Only contacts exceeding the wear limits need to be replaced. All other contacts can remain installed in the oil compartment. Counterbore d1 d2 Iron base Wear recess Figure 8: Arcing contact V 350/500/700 3.2.4 Change-over selector contacts - Cleaning Use Scotch Brite to clean fixed and moving change-over selector contacts thoroughly. 18 EN 3 Step-by-Step 3.2.5 Max. permitted contact wear EN 19 Maximum admissible contact wear (Summary) Replacement for document TCS06004en TCS06004 is replaced owing to the correction for V200 14pitches CST09001en.xls CST1 Suw 10.12.2009 Page 1/1 OLTC type Dimensions of the contacts in mm, Max. admissible or OLTC-dependent reference dimension in mm contact wear with diverter switch inserts type G 22000, R, T New condition movable SC minimum residual value fixed TC SC TC Additional wear criterions in mm movable fixed Entry in SAP documentation as (individual wear) SC TC SC TC A 25 Ø 25 Ø - - 23 Ø 23 Ø - - SC 2Ø RC TC 2Ø none diameter B 5-6 4,5-6 - - 2 1,5 - - 3 3 none individual wear C250 5-6 4,5-6 ∗ ∗ 2 1,5 - - 3 3 none individual wear C350 18,5 18 ∗ ∗ 10,5 10 - - 8 8 none individual wear bis bis none diameter 19,5 19,5 22 Ø 22Ø - - 16 Ø 16 Ø - - 6Ø 6Ø V200 14 pitches 22 Ø 20 Ø - - 16 Ø 16 Ø - - 6Ø 4Ø none diameter V350/500/ 22 Ø 22 Ø - - 17 Ø 17 Ø - - 5Ø 5Ø see V__09001.doc (TS Manual) diameter V350/700 14 pit. 22 Ø 20 Ø - - 17 Ø 17 Ø - - 5Ø 3Ø see V__09001.doc (TS Manual) diameter V200 - except with 14 pitches 700 - except with 14 pitches M 8 8 8 8 4 4 4 4 4 4 see TS284043.1 (TS Manual) SAP document.: individual wear addit. cont. sheet: indivi. wear D 20000 2 4 11 10 0,5 2 9,5 8 1,5 2 none individual wear oder 2,5 4 11,5 10 0,5 2 9,5 8 2 2,5 D 21000 8,5 8,5 11,5 11,5 3,5 3,5 6,5 6,5 5 5 see TS282034 (TS Manual) individual wear D 0466 6 6 6 6 1 1 1 1 5 5 see TCS05011.doc individual wear D 0444, 6 6 6 6 1 1 1 1 5 5 (TS Manual) E 6 6 6 6 1,5 4,5 4,5 see SI_E_2 (TS Manual) F 21000 8 8 8 8 1 1 1 1 7 7 F 23000 9,5 8 10 8 3 1 2,5 1 7 7 see TCS05010.doc (TS Manual) 1,5 1,5 1,5 F 24000 8 8 8 8 1 1 1 1 7 7 F 26000 9,5 8 10 8 3 1 2,5 1 7 7 T and R 34 34 34 34 22 22 6 6 22 22 if end inspection G 21000 sheet is not available 7 7 7 G 22000 entered into 7 1 1 1 1 if total wear = 13 mm 8,5 8,5 8,5 8,5 1,5 1,5 1,5 1,5 individual wear add. contact sheet F26000 SAP document.: total wear see inspection instructions type R additional contact sheet 6 6 see TCS05012.doc (TS Manual) SAP document.: total wear additional contact sheet 6,5 6,5 see inspection instructions - type G SAP document.: total wear TCS05012.doc (TS Manual) additional contact sheet none individual wear guide bridge K SAP document.: individual wear addit. contact sheet: individ. wear 7 7 SC = switching contact TC = transition contact * see document TS94N094 i. A. Uwe Seltsam Copies to: CTT, CST, TS Manual, CTE, CSxO, CST1, CST3 notice board, CS4T notice board, MR subsidiaries and representatives The copying, distribution and utilization of this document as well as the communication of its contents to others without expressed authorization is prohibited. Offenders will be held liable for the payment of damages. All rights reserved in the event of the grant of a patent, utility model or ornamental design registration F00788:01 CST09001en.XLS 11.12.2009 Seite 1/1 3 Step-by-Step 3.3 Parts replacement after fixed number of tap-change operations intervals 3.4 One-time retrofit and modifications 3.4.1 Until 30 April, 1984 - Replacement of main contacts The section below lists the conditions when main contacts without flexible shaft must be replaced with the version with flexible shaft. Replacement criterion and how to do the replacement For all OLTC type OILTAP® V 200 and OILTAP® V 350 versions listed in the following table, main contacts without flexible shaft must be replaced with main contacts with flexible shaft during next maintenance if the replacement has not been done yet. Please see section "Material for OILTAP® V 350 Y“ and "Material for OILTAP® V 350 D“ for the material required for the modification. In SAP, all relevant equipments are identified by corresponding service notifications. The replacement must be done as specified in Inspection Instructions IA113/01, section 6.1 or 6.2. OLTC type Criterion OILTAP® V 200 Up to delivery date 15 June, 1982 equipment MR132012 OILTAP® V 350 Up to delivery date 30 April, 1984 Table 1: Condition for replacement 3.4.1.1 Details - Replacement of main contacts The section below lists the conditions when main contacts without flexible shaft must be replaced with the version with flexible shaft. Replacement criterion and how to do the replacement For all OLTC type OILTAP® V 200 and OILTAP® V 350 versions listed in the following table, main contacts without flexible shaft must be replaced with main contacts with flexible shaft during next maintenance if the replacement has not been done yet. Please see section "Material for OILTAP® V 350 Y“ and "Material for OILTAP® V 350 D“ for the material required for the modification. In SAP, all relevant equipments are identified by corresponding service notifications. The replacement must be done as specified in Inspection Instructions IA113/01, section 6.1 or 6.2. EN 21 3 Step-by-Step OLTC type Criterion OILTAP® V 200 Up to delivery date 15 June, 1982 equipment MR132012 OILTAP® V 350 Up to delivery date 30 April, 1984 Table 2: Condition for replacement Distinctive feature OILTAP® V 350 is shown below to explain the differentiation between designs with or without flexible shaft. The same differentiation is valid for the OILTAP® V 200; it should be noted though, that the OILTAP® V 200 is not equipped with a separate main contact. On the main contact without flexible shaft (see following figure), there is a copper sleeve around the braided copper lead. Current take-off rollers Figure 9: Main contact without flexible shaft 22 EN Braided lead without flexible shaft with copper sleeve 3 Step-by-Step On the main contact with flexible shaft (see following figure), there is no copper sleeve. Current take-off rollers Braided lead with flexible shaft without copper sleeve Figure 10: Main contact with flexible shaft Quantity Description Part no. 3 Compression spring 500147XX 2 Compression spring 500564XX 2 Lock tab 060858XX 3 Hex head bolt Polyfleck 401255XX 3 Washer 451323 1 Main contact cpl. 085497XX 1 Main contact cpl. 085553XX Table 3: Material for OILTAP® V 350 Y Quantity Description Part no. 3 Compression spring 500147XX 3 Compression spring 500564XX 3 Lock tab 060858XX 3 Hex head bolt Polyfleck 401255XX 3 Washer 451323 3 Main contact cpl. 085497XX Table 4: Material for OILTAP® V 350 D Quantity Description Part no. 1 Set of moving contacts with accessories - 10 and 12 pitch design 088980XX Table 5: Material for OILTAP® V 200 10-pitch and 12-pitch design EN 23 3 Step-by-Step Quantity Description Part no. 1 Set of moving contacts 088982XX with accessories – 14 pitch design Table 6: OILTAP® V 200 14 pitch design 3.4.2 Until 18 August, 1991 - Modification of inner screening rings Up to delivery date 18 August, 1991, rivets were used to attach the inner screening rings to the switching tube of on-load tap-changers type OILTAP® V and OILTAP® H. The rivets must be replaced with bolts. The work must be performed at next maintenance. Overview Up to delivery date 18 August, 1991, rivets were used to attach the inner screening rings to the switching tube. The rivets must be replaced with bolts. This is necessary to be able to remove the inner screening rings during maintenance and clean the inner surface area of the switching tube. In contrast to Inspection Instructions No. 113_01en, On-load tap-changer Type V, section 4.3.2, also the inner screening rings of types V III 350 Y, V III 200 Y and V III 500 Y must be retrofitted to screwable design. 3.4.2.1 Details - Modification of inner screening rings Up to delivery date 18 August, 1991, rivets were used to attach the inner screening rings to the switching tube of on-load tap-changers type OILTAP® V and OILTAP® H. The rivets must be replaced with bolts. The work must be performed at next maintenance. Overview Up to delivery date 18 August, 1991, rivets were used to attach the inner screening rings to the switching tube. The rivets must be replaced with bolts. This is necessary to be able to remove the inner screening rings during maintenance and clean the inner surface area of the switching tube. In contrast to Inspection Instructions No. 113_01en, On-load tap-changer Type V, section 4.3.2, also the inner screening rings of types V III 350 Y, V III 200 Y and V III 500 Y must be retrofitted to screwable design. Retrofit to screwable design Perform retrofit in accordance with Inspection Instructions On-load Tapchanger type V Inspection Instructions On-load Tap-changer type V, No. 113_01en, On-load tap-changer Type V", section 4.3.2.5. or 4.3.2.6, respectively. 24 EN 3 Step-by-Step Quantity Part no. Description Torque 9 401045xx Hex head bolt Polyfleck M5 x 16 5 Nm 9 073284xx M5 washer 9 401809xx Hex head bolt Polyfleck M6 x 30 10 Nm 6 401832xx Hex head bolt Polyfleck M6 x 16 10 Nm Table 7: Material - Modification of inner screening rings All material is included in set of small parts V: 089011xx. Tools - Modification of inner screening rings ▪ Drill ø 4.2 mm ▪ Drill ø 5.5 mm ▪ Thread cutter M5 Torques - Modification of inner screening rings Ma (max. torque) = 10 Nm Ma (max. torque) = 19 Nm Ma (max. torque) = 5 Nm Figure 11: Torque OILTAP® V III 350 D Screw M6x30, self-locking, Ma (max. torque) = 10 Nm Figure 12: Torque OILTAP® V III 200D Ma (max. torque) = 9 Nm Ma (max. torque) = 19 Nm Ma (max. torque) = 19 Nm Figure 13: Torque OILTAP® V III 500D Figure 14: Torque OILTAP® V ... EN 25 3 Step-by-Step 3.4.3 Until 31 December 1992 - Installation of spring plates at the outer shielding rings of the switching column Delivery period Version Application to 92.12.31 Shielding ring Power station and coated or uncoated, grid mounting plates riveted Measures ▪ As soon as number of operations ≥ 70,000, install spring plates during inspection. ▪ Only install spring plates immediately, if mounting plates are torn. to 92.12.31 Shielding ring Electric furnace and Install spring plates coated or uncoated, electrolysis during next inspecmounting plates rivtion. eted From 93.01.01 Shielding ring coated, mounting plates welded together Power station, grid, electric furnace and electrolysis No actions required On the selector switches type V manufactured until 31 December 1992, the mounting plates of the outer shielding rings can tear or tear off. The spring plates are inserted into the shielding rings and together with the mounting plates they are screwed to the resistor tube. For the different selector switch versions type V 200/350/500, the following parts are required: 3.4.3.1 Details - Installation of spring plates at the outer shielding rings of the switching column Delivery period Version Application to 92.12.31 Shielding ring Power station and coated or uncoated, grid mounting plates riveted Measures ▪ As soon as number of operations ≥ 70,000, install spring plates during inspection. ▪ Only install spring plates immediately, if mounting plates are torn. 26 to 92.12.31 Shielding ring Electric furnace and Install spring plates coated or uncoated, electrolysis during next inspecmounting plates rivtion. eted From 93.01.01 Shielding ring coated, mounting plates welded together EN Power station, grid, electric furnace and electrolysis No actions required 3 Step-by-Step On the selector switches type V manufactured until 31 December 1992, the mounting plates of the outer shielding rings can tear or tear off. The spring plates are inserted into the shielding rings and together with the mounting plates they are screwed to the resistor tube. For the different selector switch versions type V 200/350/500, the following parts are required: Type/Quantity set Set1 Set 2 Set 3 Set 4 V 200 Δ 3 - 2 1* V 350 Δ - 3 2 1* V 500 Δ 3 - - 2 + 1* V 200 without change-over selector 1 - - 1* V 350 without change-over selector - 1 - 1* V 500 without change-over selector 1 - - 1* V I 200 1 - - 1* V I 350 - 1 - 1* V I 700 - 1 - 1* *Set 4 is additionally required for all OLTCs without change-over selector For inspections, generally carry the relevant sets. Set 1 part no. 084022:01 V200/500 installation of spring plates at the upper shielding ring of the switching element Spring plate, top 079732 : xx 3 items Lock tab 5.5x20 021986 : xx 3 items Washer 5.5 x 12 x 3 080186 : xx 6 items Hex head screw M5 x 12 Tuflok® 401255 : xx 6 items Set 2 part no. 084021:01 V350 installation of spring plates at the upper shielding ring of the switching element Spring plate, top 079733 : xx 3 items Lock tab 5.5x19 060860 : xx 3 items Hex head screw M5 x 8 Tuflok® 098389 : xx 6 items EN 27 3 Step-by-Step Set 3 part no. 084023:01 V200/350 installation of spring plates at the lower shielding ring of the switching element Spring plate, bottom 079341 : xx 3 items Lock tab 5.5x19 060860 : xx 3 items Hex head screw M5 x 8 Tuflok® 098389 : xx 6 items Set 4 part no. 084020:01 V500 installation of spring plates at the lower shielding ring of the switching element Installation of spring plates at the upper shielding ring at the switching column on OLTCs without change-over selector Spring plate, bottom 080185 : xx 3 items Lock tab 451427 3 items Distance tube 8.5 x 12 x 5.2* 047738 : xx 3 items Hex head screw M8 x 30 Tuflok® 401782 : xx 3 items Hex head screw M8 x 25 Tuflok® 401789 : xx 3 items *For installation of spring plates at the upper shielding ring at the switching column How to proceed 1. Selector switch with change-over selector The installation of the spring plates is shown on a selector switch type V III 350 ∆ as an example. The single-phase switches type V I 200/350/700 with and without changeover selector, as well as the OLTCs in neutral point connection type V III 200/350/500 without change-over selector, only have one shielding ring on the upper switching element. The OLTCs in neutral point connection type V III 200/350/500 with change-over selector are designed without shielding rings. 28 EN 3 Step-by-Step 1.1 Remove switching elements from the switching tube (see following figure). Figure 15: Selector switch insert 1 Fixing bolts of base bearing (max. torque = 19 Nm) 2 Fixing bolts of upper shielding ring 3 Fixing bolts of switching element 4 Fixing bolts of lower shielding ring How to proceed ▪ Unscrew fixing bolts [1] of the base bearing. ▪ Unscrew fixing bolts [2] of the upper shielding rings. For types V200 and V500, the lower shielding rings must also be unscrewed. ▪ Unscrew fixing bolts [3] of the switching elements. First, the bolts in the middle, then the outer ones. ▪ Remove switching elements and shielding rings from the switching tube. NOTICE! Remove switching elements and shielding rings carefully from the switching tube to prevent scratches on the insulating material. 1. 1.2.1 Unscrew lower shielding rings from the switching elements [4] (see previous figure Selector switch insert). 1.2.2 Insert spring plates into the unscrewed shielding rings. The cranked spring plates are inserted into the upper shielding rings, the non-cranked spring plates are inserted into the lower shielding rings (see following figure of different spring plates). If the boreholes of the spring plates are not exactly above the boreholes of the mounting plates after insertion, the spring plates must be inserted anew, as they cannot be moved while inside the shielding ring. Display of different spring plates Figure 16: V200/500 Spring plate, top part no. 079732:xx EN 29 3 Step-by-Step Figure 17: V350 Spring plate, top part no. 079733:xx Figure 18: V200/350 Spring plate, bottom part no. 079341:xx Figure 19: V500, V200/350/500 without change-over selector spring plate 1.2.3 The lower shielding rings are attached with the mounting plates and spring plates (part no. 079341:xx) from the inside at the resistor tube using M5 x 8 bolts (part no. 098389:xx) and lock tabs (part no. 060860:xx) and secured (max. torque = 5 Nm). For type V 200, the lower shielding rings are attached outside on the switching element with M8 x 8 bolts (part no. 098389:xx) and lock tabs (part no. 060860:xx) and secured (max torque: 5 Nm). For type V500, the lower shielding rings are directly attached to the switching tube using spring plates (part no. 080185:xx) and M8 x 30 bolts (part no. 401782:xx) and lock tabs (part no. 451427) and secured (max. torque = 19 Nm). On types V200 and V500, the lower shielding rings are only attached once the switching elements are already screwed to the switching tube and secured. 1.3.1 Insert spring plates into the unscrewed upper shielding rings, as described in section 1.2.2. 1.3.2 Place the upper shielding ring and the switching element of the upper phase back on the switching tube and screw down the switching element and secure it (max. torque = 10 Nm) (see figure "Attaching shielding rings"). 30 EN 3 Step-by-Step NOTICE! Place switching elements and shielding rings carefully onto the switching tube to prevent scratches on the insulating material. 1.3.3 Attach the upper shielding ring using M5 x 8 bolts (part no. 098389:xx) and lock tabs (part no. 021986:xx) (max. torque = 5 Nm, see following figure) and secure it. Figure 20: Attaching shielding rings 2 Max. torque 5 Nm 3 Max. torque 10 Nm 4 Max. torque 5 Nm For the types V200 and V500, spacers (part no. 080186:xx) are placed between the mounting plates of the upper shielding rings and the spring plates. The upper shielding rings are attached using M5 x 12 bolts (part no. 401255:xx) and lock tabs (part no. 021986:xx) and secured (max. torque = 5 Nm). 1.4 Installing the spring plates into the shielding rings of the middle and lower phase is performed as described in sections 1.1 to 1.3.3. 1.5 Check all fixing bolts for tight and secure seat. 2. Selector switch without change-over selector For selector switches type V without change-over selector, the spring plates with part no. 080185:xx are inserted into the shielding ring (part no. 061494) at the head of the switching column. For these selector switches, set 4 is additionally required once. The spring plates are installed at the attached at the shielding ring at the switching tube. 2.1 Remove one M8 x 20 bolt at the mounting plate (replaced by M8 x 25 bolt, part no. 401789:xx). EN 31 3 Step-by-Step 2.2 Insert spring plate (part no. 080185:xx) into shielding ring (see following figure). If the boreholes of the spring plate are not exactly above the boreholes of the mounting plate of the shielding ring after insertion, the spring plate must be inserted anew, as it cannot be moved while inside the shielding ring. Figure 21: Install spring plates in shielding ring 2.3 Place distance tube (part no. 047738:xx) between mounting plate and spring plate and attach shielding ring with lock tab (part no. 451427) and M8 x 25 bolt (part no. 401789:xx) and secure (max. torque = 19 Nm). 2.4 Install the other two spring plates into the shielding ring as described in sections 2.1 to 2.3. 2.5 Check all fixing bolts for tight and secure seat. 2.6 Install the spring plates at the upper and lower shielding rings of the switching elements as described in section 1. 3.4.4 Until 31 October, 1995 - Additional securing of dowel pin Since November, 1995, the dowel pins on the moving main contacts of (factory-fresh) tap-changers types V 350, V 500 and H 400 are additionally secured with a punch mark. During maintenance, these dowel pins must be additionally secured by means of a punch mark on all tap-changers types V 350, V 500 and H 400 in operation. How to proceed 1. Sink dowel pin a little deeper into the borehole. Apply punch mark at the edge of the borehole (in the copper area), (see figures "Dowel pin sunk" and "View of A"). 2. If sinking the dowel pin is not possible, apply punch mark at the edge (see figure "View of A"). 32 EN 3 Step-by-Step Figure 22: Main contact View A Punch drift Main contact roller Dowel pin 400411 Hollow shaft 062783 Figure 23: Dowel pin sunk Main contact roller (copper) Dowel pin Punch mark Figure 24: View of A 3.4.5 Until 31 July, 1999 - Replacement of bearing block transition contacts and main switching contacts For selector switches type OILTAP® V 200; V250 and V 500 until delivery date 31 July, 1999, the bearing blocks of transition contacts and main switching contacts must be replaced with the current version. The work must be performed at next maintenance. EN 33 3 Step-by-Step 6 cm Distinguishing features Old1variant Current2 variant Pay attention to the location of the chamfer Old part number: 20040103 Current part number: 706646xx Figure 25: Distinguishing features 1 Old variant, part number 20040103 2 Current variant, part number: 706646xx Delivery period and features Delivery period Measures Up to February, 1984 Modification to current design. Check if current variant of bearing blocks fits in the holes on the contact housing. If this is not possible, the bearing blocks must be reworked. From March, 1984 to July, 1999 Modification to current design. From August, 1999 onward No modification, as it already is the current version Table 8: Overview delivery periods 34 EN 3 Step-by-Step How to rework the bearing blocks If the bearing blocks do not fit in the holes of the contact housing, rework the hatched areas (see following figure) by approx. 0.1 mm on each side using sanding paper, scraper or knife. Figure 26: Areas to rework 3.4.5.1 Preliminary information section CAUTION! The following section is currently being updated. The following information is preliminary. 3.4.5.1.1 Material - Replacement of bearing block transition contacts and main switching contacts Material - Replacement of bearing block transition contacts and main switching contacts Material per selector switch insert type V III 200, V III 250 and V III 500 Ite m Quantity Description Part no. 141 18 Bearing block 706646xx 146 18 Allen bolt A M6 x 12 707732xx 148 1 RESISTANT GLUE DELOML-5327 900025xx 160 6 Allen bolt Polyfleck M6 x 10 099177xx 225 9 Pin-type cable terminal 581869xx 230 3 Cable terminal 715773xx 240 3 Washer DIN 125-1 form B 5.3 451323 250 3 Hex head bolt Polyfleck M5 x 12 401255xx Hex. head screw 450351 EN Torque 3 Nm, locked with item 148 10 Nm 6 Nm 35 3 Step-by-Step Ite m Quantity Description Part no. Torque 064273 063835 Table 9: Material - Replacement of bearing block transition contacts and main switching contacts 3.4.6 Until 30 September, 2007 - Replacement of gear unit with tension springs This section describes the criteria for the replacement of the gear unit with tension-spring energy accumulator with a gear unit with pressure-spring energy accumulator during maintenance of all on-load tap-changers type OILTAP® V with a delivery date up until 1 October, 2007. On all on-load tap-changers type OILTAP® V with a delivery date from 1 October, 2007 onward, a gear unit with pressure-spring energy accumulator is already installed. On-load tap-changers types OILTAP® V I 200, V III 500 Y, V III 500 D and V I 700 During next maintenance of types OILTAP® V I 200, V III 500 Y, V III 500 D and V I 700, the gear unit with tension-spring energy accumulator must be replaced with a gear unit with preadjusted pressure-spring energy accumulator. The required material for the respective on-load tap-changer must be provided by the responsible OPS before starting work. NOTICE Switching time measurement necessary Always perform a switching time measurement after installing a new gear unit with pressure-spring energy accumulator. ► Perform switching time measurement in accordance with chapter Performing switching time measurement. If an on-load tap-changer type OILTAP® V is already equipped with a gear unit with pressure-spring energy accumulator, it must be replaced after every 800,000 operations. Other on-load tap-changers type OILTAP® V During next maintenance of types OILTAP® V III 200 Y, V III 200 D, V III 350 Y, V III 350 D, V I 350, V III 400 Y and V III 400 D, the gear unit with tension-spring energy accumulator must be replaced with a gear unit with preadjusted pressure-spring energy accumulator. The required material must be provided by the responsible OPS before starting work. Switching time measurement is not necessary. 36 EN 3 Step-by-Step If an on-load tap-changer type OILTAP® V is already equipped with a gear unit with pressure-spring energy accumulator, it must be replaced after every 800,000 operations. Note for installing the pressure-spring energy accumulator For types OILTAP® V III 200 Y, V III 200 D, V III 350 Y, V III 350 D, V I 350, V III 400 Y, and V III 400 D up to delivery date 31 December, 1984 and with version type "without", make sure to reinstall the previously used suction pipe flange in the new gear unit with pressure-spring energy accumulator. Use Allen key size 14 mm to remove the suction pipe flanges of the old and new gear unit. Then install the old flange in the new gear unit with preadjusted pressure-spring energy accumulator (see following figure). The tightening torque is 20 Nm ± 2. 6 cm Figure 27: Removing / installing suction pipe flange Detail view removed flange (see following figure). Allen key size 14 Suction pipe flange Suction pipe Figure 28: Detail view removed flange 3.4.7 Until 31 July, 2009 - Modification tension-spring energy accumulator to tumble-riveted connection OILTAP® V Since 10 July, 2009, tumble-riveting is used to connect crank and connecting piece of pressure-spring energy accumulator (see section "Removed gear unit") for on-load tap-changer type OILTAP® V. EN 37 3 Step-by-Step This section describes how to perform the modification of the pressurespring energy accumulator to tumble-riveted version. The replacement must be performed once at next maintenance, in accordance with the table "Modification criteria". Type Delivery date How to proceed OILTAP® V From delivery date 1 October, 2007 Modification of pressure-spring energy accumulator at next maintenance to delivery date 31 July, 2009 Older OLTCs that were Up to delivery equipped with replacement date 31 July, gear unit with pressure2009 spring energy accumulator Table 10: Modification criteria 3.4.7.1 Details - Modification pressure-spring energy accumulator to tumbleriveted connection OILTAP® V Since 10 July, 2009, tumble-riveting is used to connect crank and connecting piece of pressure-spring energy accumulator (see section "Removed gear unit") for on-load tap-changer type OILTAP® V. This section describes how to perform the modification of the pressurespring energy accumulator to tumble-riveted version. The replacement must be performed once at next maintenance, in accordance with the table "Modification criteria". Type Delivery date How to proceed OILTAP® V From delivery date 1 October, 2007 Modification of pressure-spring energy accumulator at next maintenance to delivery date 31 July, 2009 Older OLTCs that were Up to delivery equipped with replacement date 31 July, gear unit with pressure2009 spring energy accumulator Table 11: Modification criteria Removed gear unit Overview of removed gear unit see following figure Refer to attachment "Overview gear unit VACUTAP® VV®" for designations of components. 38 EN 3 Step-by-Step Figure 29: Gear unit VACUTAP® VV® Overview of old and new connection between crank and connecting piece Connecting piece Figure 30: Pressure-spring energy accumulator with tumble-riveted connection (new), crank not removable Connecting piece Figure 31: Pressure-spring energy accumulator with retaining ring (old), crank can be removed Replacing the pressure-spring energy accumulator To be able to reinstall the pressure-spring energy accumulator correctly, mark position of crank in relation to drive shaft. EN 39 3 Step-by-Step Crank Drive shaft Figure 32: Drive shaft Use a caliper or a feeler gauge to measure the existing setting value "A" between bearing ring and mounting plate. Mounting tab A Support ring Figure 33: Setting value "A" Screw M5 bolt into tapped dowel pin of mounting plate and remove the tapped dowel pin, using pipe wrench if necessary, and reducing strain manually from the spring balancer, to the direction of the mounting plate. Next, remove pressure-spring energy accumulator from mounting plate. M5 screw Tapped dowel pin Mounting tab Figure 34: Removal from mounting tab Use appropriate retaining ring pliers to remove the retaining ring that attaches crank to drive shaft. 40 EN 3 Step-by-Step Figure 35: Removing retaining ring Make sure to use appropriate type and number of washers. Figure 36: Removing washers Remove crank with pressure-spring energy accumulator from drive shaft. Figure 37: Removing pressure-spring energy accumulator Mount crank to drive shaft, observing marks on drive shaft you made in step 1. Reinstall washers removed in step 4 and secure them with new retaining ring. EN 41 3 Step-by-Step Figure 38: Mounting drive shaft Check axial clearance between crank and circlip (desired measure = 0.2 ± 0.1 mm) and adjust it by removing or adding washers if necessary. Mount pressure-spring energy accumulator in bearing ring. For this purpose, install the tapped dowel pin that was removed in step 3. The springs are pretensioned by inserting the pressure-spring energy accumulator; installing the tapped dowel pin is easier if you reduce strain manually from the spring balancer to the direction of the mounting plate. Tapped dowel pin Mounting tab Figure 39: Installation in mounting tab Setting value "A" must correspond to the original value. If not, remove tapped dowel pin and turn pipe nut in appropriate direction. A Pipe nut Figure 40: Checking setting value "A" Checking position of crank on drive shaft Make sure to position the crank with rough teeth on the drive shaft in such a way that crank and catch on drive shaft point to the same direction. 42 EN 3 Step-by-Step Crank Catch on coupling shaft Figure 41: Reinstallation check-up After retrofitting, the following must be noted in the service report: "Correct position of crank and catch were checked when replacing pressure-spring energy accumulator." Material - Energy accumulator with tumble-riveted connection Quantity Description Part number 1 Pressure-spring energy accumulator complete SETERSATZ 5 Washers 454003 1 Retaining ring 452216 Table 12: Material - Energy accumulator with tumble-riveted connection EN 43 4 Assemblies 4 Assemblies 4.1 General 4.1.1 Replacement intervals diverter switch insert, selector switch insert, diverter switch oil compartment contacts and on-load tapchanger The tables in the instructions below show when to replace which subassembly groups of MR on-load tap-changers and when to perform tap selector maintenance. The relevant operating instructions or technical instructions for the respective on-load tap-changer must be observed. OILTAP® / VACUTAP® diverter switch insert and oil compartment On-load tap-chang- Replacement ers Oil compartment contact Diverter switch insert OLTC (1) OILTAP® M 2,000,000 – 2,400,000 800,000 4,000,000 OILTAP® MS Replacement only within scope of selector maintenance. 800,000 4,000,000 When retrofitting to VM®, no replacement necessary Please note for on-load tap-changer type OILTAP® M or OILTAP® MS: When the replacement interval for oil compartment contacts is reached, the diverter switch insert should be retrofitted with diverter switch insert type VACUTAP® VM®. In this case, the replacement of the oil compartment contacts is not necessary. If retrofitting to type VACUTAP® VM® is not possible, the oil compartment contacts must be replaced according to above-mention interval. OILTAP® R 800,000 800,000 4,000,000 OILTAP® RM 800,000 800,000 4,000,000 OILTAP® G ---- 800,000 4,000,000 VACUTAP® VM® 2,000,000 – 2,400,000(2) 1,200,000 3,600,000 VACUTAP® VMS® Replacement only within scope of selector maintenance 600,000 3,600,000 VACUTAP® VRC, VRD, VRE, VRF, VRG (3) 1,200,000 1,200,000 3,600,000 VACUTAP® VRF I 1601 300,000 1,200,000 3,600,000 VACUTAP® VRF I 1801 44 EN 4 Assemblies On-load tap-chang- Replacement ers Oil compartment contact Diverter switch insert VACUTAP® VRS, Details - Checking contact 1,200,000 VRM, VRL®, VRH®, wear on main contact and VRX® replacement intervals of oil compartment contactsDetails - Checking contact wear on main contact and replacement intervals of oil compartment contacts OLTC (1) 3,600,000 VACUTAP®VRL I 1801-2401 network operation 600,000 (4) 1,200,000 3,600,000 VACUTAP®VRL I 2601-3201 network operation 300,000 (4) 1,200,000 3,600,000 VACUTAP®VRL I 1801-2401 arc furnace operation 300,000 (4) 1,200,000 3,600,000 Table 13: Overview OILTAP® / VACUTAP® on-load tap-changers (1) OLTC includes the following subassembly groups: oil compartment, tap selector, motor-drive unit, drive shafts (2) Measure diameter of worn shape on oil compartment contacts after every 600,000 operations (3) Without VACUTAP® VRF I 1601, 1801 (4) When replacing the vacuum interrupters with supporting structure or the diverter switch insert, the oil compartment contact must necessarily be replaced. OILTAP® / VACUTAP® selector switch insert / ECOTAP® The following table shows replacement on the basis of number of operations, of subassembly groups for on-load tap-changers type OILTAP®, VACUTAP® and ECOTAP®. On-load tap-chang- Replacement ers Oil compartment contact Selector switch insert OLTC (5) ECOTAP® VPD® ---- ---- 500,000 VACUTAP® VVS® ---- ---- 500,000 VACUTAP® VV® ---- 1,200,000 4,000,000 EN 45 4 Assemblies On-load tap-chang- Replacement ers Oil compartment contact Selector switch insert OLTC (5) OILTAP® V (without V200) Oil compartment contact V 350 / 500 / 700 [►Section 4.2.3.2, Page 55]Oil compartment contact V 350 / 500 / 700 800,000 4,000,000 OILTAP® V200 Oil compartment contact V 800,000 200 [►Section 4.2.3.1, Page 54]Oil compartment contact V 200 4,000,000 Table 14: Overview OILTAP® / VACUTAP® and ECOTAP® on-load tap-changers (5) OLTC includes the following subassembly groups: oil compartment, tap selector, motor-drive unit, drive shafts Selector Selector type Selector size New selector RC, RD, RDE type R On-load tap-changer type Selector maintenance VACUTAP® VRF, VRS, VRM, VRL®, VRH®, VM® 1,200,000 OILTAP® M, R RE, RF VACUTAP® VRS, VRM, VRL®, VRH®, VRX® 1,200,000 OILTAP® R Old selector type R C, D VACUTAP® VRD, VRF 1,000,000 OILTAP® R E Selector type B, C, D, DE M VACUTAP® VRG OILTAP® R 1,000,000 VACUTAP® VRC, VRE, VRS®, VRM®, VM®, VMS® (6) Selector contact Ø 22 mm: OILTAP® M, RM Selector contact Ø 14 mm: 1,200,000 1,200,000 Selector type B MS VACUTAP® VMS® Selector type D, E G OILTAP® G 1,000,000 VV changeover selector VACUTAP® VV 2,100,000 OILTAP® MS -- Table 15: Overview selector (6) 46 1,000,000 VMS® : selector size C only EN 4 Assemblies 4.1.1.1 Change log 2023-04-28 1. Adjustment replacement criterion of oil compartment contacts OILTAP® M, VACUTAP® VM, VACUTAP® VRL® I arc furnace operation 2. General re-working and adjustment of interval cycles, e.g. interval selector maintenance OILTAP® M 3. DS3200 added EN 47 4 Assemblies 4.1.2 Location of pipes type V and G 48 EN 4 Assemblies 4.2 Contact system, switching element 4.2.1 Checking bearing block for cracks, V 200 / V 250 / V 500 When performing work on on-load tap-changer type V 200 / V 250 / V 500, always check top and lower bearing blocks of switching contacts and transition contacts for cracks. Replace the bearing blocks if you detect any cracks. The two following figures show possible cracks. Figure 42: Bearing block, front view Figure 43: Bearing block, rear view 4.2.1.1 Details - Checking bearing block for cracks, V 200 / V 250 / V 500 When performing work on on-load tap-changer type V 200 / V 250 / V 500, always check top and lower bearing blocks of switching contacts and transition contacts for cracks. Replace the bearing blocks if you detect any cracks. The two following figures show possible cracks. 50 EN 4 Assemblies Figure 44: Bearing block, front view Figure 45: Bearing block, rear view EN 51 4 Assemblies To perform the check, open the two Allen bolts Polyfleck M6 x 10 of the screening cap. Remove protection. Check top bearing blocks of switching contacts and transition contacts for cracks. Check lower bearing blocks of switching and transition contacts for cracks. Protection Cylinder head bolt Polyfleck M6 x 10 Bearing block Figure 46: Checking bearing block Material - Replacement of bearing block transition contacts and main switching contacts Ite m Quantity 160 6 Description Part no. Torque Allen bolt Polyfleck M6 x 10 099177xx 10 Nm Table 16: Material - Replacement of bearing block transition contacts and main switching contacts 52 EN 4 Assemblies 4.2.2 Protrusion of hollow shaft in switching contacts V 200 /V 250 Ensure for on-load tap-changers type V 200/250, that protrusion of hollow shaft of switching contacts below the swing frame may not exceed 1.6 ± 0.5 mm. The hollow shaft must not be slack. If any of the two conditions is not fulfilled, replace the complete switching contact roller. Switching contact Swing frame 1.6 ± 0.5 mm Hollow shaft Figure 47: Protrusion of hollow shaft in switching contacts V 200 EN 53 4 Assemblies 4.2.3 Permitted contact wear of oil compartment contact 4.2.3.1 Oil compartment contact V 200 A drawing of a worn oil compartment contact is shown in the following figure. The contact must be replaced if one of the following criteria is fulfilled: ▪ d1 ≥ 4 mm ▪ d2 ≥ 4 mm Please note that d1 and d2 refer to wear depth measured from the interior side of the oil compartment contact (i.e., the side showing towards middle of oil compartment). Only contacts exceeding the wear limits need to be replaced. All other contacts can remain installed in the oil compartment. Wear recess Interior side of d2 oil compartment contact d1 Wear recess Figure 48: Drawing of worn arcing contact A photo of a worn oil compartment contact is shown in the following figure. d1 d2 Figure 49: Photo of worn arcing contact 54 EN 4 Assemblies 4.2.3.2 Oil compartment contact V 350 / 500 / 700 The following figure shows a worn arcing contact V 350/500/700. The contact must be replaced if one of the following criteria is fulfilled: ▪ d1 < 1 mm ▪ d2 ≤ 0 mm Please note that d1 is min. distance from wear recess to iron base, and d2 is min. distance from wear recess to counterbore. Only contacts exceeding the wear limits need to be replaced. All other contacts can remain installed in the oil compartment. Counterbore d1 d2 Iron base Wear recess Figure 50: Arcing contact V 350/500/700 4.2.4 Change-over selector contacts - Cleaning Use Scotch Brite to clean fixed and moving change-over selector contacts thoroughly. 4.2.5 Until 30 April, 1984 - Replacement of main contacts The section below lists the conditions when main contacts without flexible shaft must be replaced with the version with flexible shaft. Replacement criterion and how to do the replacement For all OLTC type OILTAP® V 200 and OILTAP® V 350 versions listed in the following table, main contacts without flexible shaft must be replaced with main contacts with flexible shaft during next maintenance if the replacement has not been done yet. Please see section "Material for OILTAP® V 350 Y“ and "Material for OILTAP® V 350 D“ for the material required for the modification. In SAP, all relevant equipments are identified by corresponding service notifications. The replacement must be done as specified in Inspection Instructions IA113/01, section 6.1 or 6.2. EN 55 4 Assemblies OLTC type Criterion OILTAP® V 200 Up to delivery date 15 June, 1982 equipment MR132012 OILTAP® V 350 Up to delivery date 30 April, 1984 Table 17: Condition for replacement 4.2.5.1 Details - Replacement of main contacts The section below lists the conditions when main contacts without flexible shaft must be replaced with the version with flexible shaft. Replacement criterion and how to do the replacement For all OLTC type OILTAP® V 200 and OILTAP® V 350 versions listed in the following table, main contacts without flexible shaft must be replaced with main contacts with flexible shaft during next maintenance if the replacement has not been done yet. Please see section "Material for OILTAP® V 350 Y“ and "Material for OILTAP® V 350 D“ for the material required for the modification. In SAP, all relevant equipments are identified by corresponding service notifications. The replacement must be done as specified in Inspection Instructions IA113/01, section 6.1 or 6.2. OLTC type Criterion OILTAP® V 200 Up to delivery date 15 June, 1982 equipment MR132012