MR Replacement Intervals - PDF
Document Details
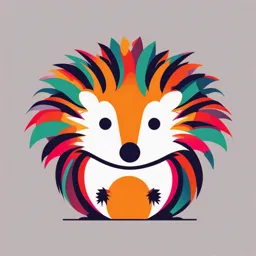
Uploaded by ValuableSugilite
Pink University
Tags
Summary
This document provides replacement intervals for various components of MR on-load tap-changers, including diverter switch inserts, selector switch inserts, and compartment contacts. Replacement intervals are presented in tables, categorized by component type.
Full Transcript
1 Replacement intervals diverter switch insert, selector switch insert, diverter switch oil compartment contacts and on-load tap-changer 1 Replacement intervals diverter switch insert, selector switch insert, diverter switch oil...
1 Replacement intervals diverter switch insert, selector switch insert, diverter switch oil compartment contacts and on-load tap-changer 1 Replacement intervals diverter switch insert, selector switch insert, diverter switch oil compartment contacts and on-load tap-changer The tables in the instructions below show when to replace which subassem- bly groups of MR on-load tap-changers and when to perform tap selector maintenance. The relevant operating instructions or technical instructions for the respec- tive on-load tap-changer must be observed. OILTAP® / VACUTAP® diverter switch insert and oil compartment On-load tap-chang- Replacement ers Oil compartment contact Diverter switch OLTC (1) insert OILTAP® M 2,000,000 – 2,400,000 800,000 4,000,000 OILTAP® MS Replacement only within 800,000 4,000,000 scope of selector mainte- nance. When retrofitting to VM®, no replacement necessary Please note for on-load tap-changer type OILTAP® M or OILTAP® MS: When the replacement interval for oil compartment contacts is reached, the diverter switch in- sert should be retrofitted with diverter switch insert type VACUTAP® VM®. In this case, the replacement of the oil compartment contacts is not necessary. If retrofitting to type VACUTAP® VM® is not possible, the oil compartment contacts must be replaced according to above-mention interval. OILTAP® R 800,000 800,000 4,000,000 OILTAP® RM 800,000 800,000 4,000,000 OILTAP® G ---- 800,000 4,000,000 VACUTAP® VM® 2,000,000 – 2,400,000(2) 1,200,000 3,600,000 VACUTAP® VMS® Replacement only within 600,000 3,600,000 scope of selector mainte- nance VACUTAP® VRC, 1,200,000 1,200,000 3,600,000 VRD, VRE, VRF, VRG (3) VACUTAP® VRF I 300,000 1,200,000 3,600,000 1601 VACUTAP® VRF I 1801 EN 1 1 Replacement intervals diverter switch insert, selector switch insert, diverter switch oil compartment contacts and on-load tap-changer On-load tap-chang- Replacement ers Oil compartment contact Diverter switch OLTC (1) insert VACUTAP® VRS, Details - Checking contact 1,200,000 3,600,000 VRM, VRL®, VRH®, wear on main contact and VRX® replacement intervals of oil compartment contactsDe- tails - Checking contact wear on main contact and re- placement intervals of oil compartment contacts VACUTAP®VRL I 600,000 (4) 1,200,000 3,600,000 1801-2401 network operation VACUTAP®VRL I 300,000 (4) 1,200,000 3,600,000 2601-3201 network operation VACUTAP®VRL I 300,000 (4) 1,200,000 3,600,000 1801-2401 arc fur- nace operation Table 1: Overview OILTAP® / VACUTAP® on-load tap-changers (1) OLTC includes the following subassembly groups: oil compartment, tap selector, motor-drive unit, drive shafts (2) Measure diameter of worn shape on oil compartment contacts after every 600,000 operations (3) Without VACUTAP® VRF I 1601, 1801 (4) When replacing the vacuum interrupters with supporting structure or the diverter switch insert, the oil compartment contact must necessarily be re- placed. OILTAP® / VACUTAP® selector switch insert / ECOTAP® The following table shows replacement on the basis of number of opera- tions, of subassembly groups for on-load tap-changers type OILTAP®, VACUTAP® and ECOTAP®. On-load tap-chang- Replacement ers Oil compartment contact Selector switch OLTC (5) insert ECOTAP® VPD® ---- ---- 500,000 VACUTAP® VVS® ---- ---- 500,000 VACUTAP® VV® ---- 1,200,000 4,000,000 2 EN 1 Replacement intervals diverter switch insert, selector switch insert, diverter switch oil compartment contacts and on-load tap-changer On-load tap-chang- Replacement ers Oil compartment contact Selector switch OLTC (5) insert OILTAP® V (without Oil compartment contact V 800,000 4,000,000 V200) 350 / 500 / 700Oil compart- ment contact V 350 / 500 / 700 OILTAP® V200 Oil compartment contact V 800,000 4,000,000 200Oil compartment contact V 200 Table 2: Overview OILTAP® / VACUTAP® and ECOTAP® on-load tap-changers (5) OLTC includes the following subassembly groups: oil compartment, tap selector, motor-drive unit, drive shafts Selector Selector Selector size On-load tap-changer type Selector mainte- type nance New selector RC, RD, RDE VACUTAP® VRF, VRS, 1,200,000 type R VRM, VRL®, VRH®, VM® OILTAP® M, R RE, RF VACUTAP® VRS, VRM, 1,200,000 VRL®, VRH®, VRX® OILTAP® R Old selector C, D VACUTAP® VRD, VRF 1,000,000 type R OILTAP® R E VACUTAP® VRG 1,000,000 OILTAP® R Selector type B, C, D, DE VACUTAP® VRC, VRE, Selector contact Ø M VRS®, VRM®, VM®, 22 mm: VMS® (6) 1,200,000 OILTAP® M, RM Selector contact Ø 14 mm: 1,200,000 Selector type B VACUTAP® VMS® 1,000,000 MS OILTAP® MS Selector type D, E OILTAP® G 1,000,000 G VV change- -- VACUTAP® VV 2,100,000 over selector Table 3: Overview selector (6) VMS® : selector size C only EN 3 1 Replacement intervals diverter switch insert, selector switch insert, diverter switch oil compartment contacts and on-load tap-changer 1.1 Change log 2023-04-28 1. Adjustment replacement criterion of oil compartment contacts OILTAP® M, VACUTAP® VM, VACUTAP® VRL® I arc furnace operation 2. General re-working and adjustment of interval cycles, e.g. interval se- lector maintenance OILTAP® M 3. DS3200 added 4 EN 2 Applying a service label to the motor-drive unit after maintenance 2 Applying a service label to the motor-drive unit after maintenance After each maintenance of an on-load tap-changer performed by a Premium Service Provider (PSP), a service label must be applied inside the relevant motor-drive unit. The label may only be applied if complete maintenance was performed. Service labels are available in the respective language with all required con- tact details for each subsidiary. The subsidiary is responsible for using the correct service label. ▪ Enter the date of the performed maintenance in the format DD / MM / YYYY: Example: May 2, 2013 ► 02 / 05 / 2013. ▪ Number of operations performed by motor-drive unit (operations counter reading on the MDU). Figure 1: Filled in service label The service technician attaches the filled in service label after the mainte- nance in the upper left corner on the inside of the motor-drive unit door (or right in case of door hinge on the right). EN 5 2 Applying a service label to the motor-drive unit after maintenance In case there is already a service label present, attach the new service label below the already present one (see following figure). Service label position Service label position if another label is already present Figure 2: Service label position MR subsidiaries should inform their MR contact person if they require new service labels or in case contact details must be changed. 6 EN 3 Check list incident report 3 Check list incident report EN 7 Check list incident report Replacing ALL99003.doc ALL13002en.docx CST1-Litzkendorf 13.06.2013 Page 1 of 4 General information Operator: Date: Contact: E-mail address: Phone number: Substation Operating site: Address: Transformer data Note: Please mark accordingly Manufacturer: serial number / designation: Application: Network power station furnace electrolysis rectifier Phase shifter HVDC other: Nominal power: [MVA] nominal voltage: [kV] nominal current: [A] Load: [%] Vector group: On-load tap-changer in intermediate circuit: yes no Neutral-point treatment: insulated direct resonant earthing Commissioning date: On-load tap-changer data Type: serial number: Current number of tap-change operations: Last on-load tap-changer maintenance date: _______________ No. of tap-change operations: Maintenance by MR: yes no ✔ Is an oil filter unit installed? yes no ✔ Unauthorized copying and distribution of this document and the utilization and communication of its contents are strictly prohibited unless expressly authorized. Offenders will be held liable for the payment of damages. All rights reserved in the event of the grant of a patent, utility model or ornamental design registration. F00788:01 Page 2 of 4 / 13.06.2013 ALL13002en.docx Incident description Date and time of incident: Did the incident occur during a tap change operation? yes no If yes, from operating position _________________ to operating position ______________ Last tap change operation before the incident was from operating position __________________ to operating position __________________ on ________________ at __________ o'clock. Current operating position indication on on-load tap-changer head: on motor-drive unit: Other information: Protective devices of the transformer Did protective devices of the transformer respond? yes no If yes, which? Buchholz protection: yes no If yes: warning tripping Differential protection distance protection pressure relief device (transformer) SERGI overcurrent protection (fuses, relays) Overvoltage protection (spark gaps, surge arresters; counter reading: ______________ ) Are recordings of a fault recorder available? yes no 1 If so, we kindly ask you to make the recordings available to MR. Protective devices of the on-load tap-changer Did protective devices of the on-load tap-changer respond? yes no If yes, which? DW 2000 protective relay RS1000 protective relay RS2001 ® pressure relief device (e.g. MPreC ) SERGI If RS1000 or RS2001 responded, which position was the flap valve in after the incident? tripped untripped Please specify the following information about the RS1000 or the RS2001: Tripping circuit design: open circuit principle closed circuit principle other: Is the transformer exposed to vibrations? yes no Continued on next page 1 MR: Maschinenfabrik Reinhausen GmbH Page 3 of 4 / 13.06.2013 ALL13002en.docx Protective devices of the on-load tap-changer – continued Indicate design of the oil systems of transformer and on-load tap-changer Combined separate How are the oil conservators (transformer tank / oil compartment of on-load tap-changer) connected to atmosphere? Hermetically sealed transformer ® Silicagel breather (e.g., maintenance-free dehydrating breather MTraB ) Network and substation data Network Primary voltage: cable overhead line other: Secondary voltage: cable overhead line other: 2 Switchgear Primary voltage: conventional GIS other: Secondary voltage: conventional GIS other: 3 Circuit breaker Primary voltage: SF6 vacuum compressed air other: Secondary voltage: SF6 vacuum compressed air other: 4 5 Surge arrester design: SiC ZnO response voltage: [kV] Surge arrester arrangement: Phase-ground phase-phase Other Were irregularities detected on on-load tap-changer or transformer before the incident occurred? Yes no If yes, which and when? Are further circumstances known such as switching operations in the network or in the substation at the time of the incident, or possibly lightning stroke, short circuit etc.? Yes no If yes, which and when? Which steps were taken after the incident (e.g., mechanical tap-change operations, replacement of diverter switch insert etc.)? Continued on next page 2 GIS means gas-insulated switchgear 3 SF6 means sulfur hexafluoride 4 SiC means silicon carbide 5 ZnO means zinc oxide Page 4 of 4 / 13.06.2013 ALL13002en.docx Other – continued Were oil sample tests carried out? yes no If yes, please provide the following information: 6 Oil sample 1 Oil sample taken from: OLTC OLTC oil conservator transformer Oil temperature when oil sample was taken: [°C] date: Test standard: IEC ASTM Dielectric strength IEC 156: [kV / 2.5 mm] water content: [ppm] Dielectric strength ASTM D877: [kV] Interpretation of oil sample 1: Oil sample 2 Oil sample taken from: OLTC OLTC oil conservator transformer Oil temperature when oil sample was taken: [°C] date: Test standard: IEC ASTM Dielectric strength IEC 156: [kV / 2.5 mm] water content: [ppm] Dielectric strength ASTM D877: [kV] Interpretation of oil sample 2: Documentation of incident Please take pictures of the damaged on-load tap-changer, and forward the pictures to MR. Additional notes / sketches: Please return the completed form to the following e-mail address [email protected] or to: Maschinenfabrik Reinhausen GmbH Phone +49 (0)941 4090-0 Falkensteinstraße 8 Fax +49 (0)941 4090-7001 93059 Regensburg Copies CTE, CTPS, CTT, CST, CST1-all, CST2-all, CST3-all, CST3 notice board, CS4T-all, CS4T notice to: board, CSTA-all, CSxO-all (except CSAO), OPS-Wiki, TS Manual, MR subsidiaries and representatives 6 OLTC means on-load tap-changer 4 Oil (oil sapmle, oil filter unit, sealing, tightnes, oil conservator) 4 Oil (oil sapmle, oil filter unit, sealing, tightnes, oil conservator) 12 EN 4 Oil (oil sapmle, oil filter unit, sealing, tightnes, oil conservator) 4.1 Instructions for oil draining and removal of switching gases EN 13 Instructions for draining oil and removing switching gases TCS06005en.docx TCS/Suw 15.10.2013 Page 1/5 1. Tap changers by Siemens, TU or AEG 1.1 On-load tap-changer is equipped with pipe or valve for oil draining Oil drain pipe 4 3 8 7 Vent screw Cover 1 Protective relay Return valve 9 Silicagel breather 5 Stop valve 2 10 6 Pump Sequence of work: (1) OPEN return valve (2) CLOSE stop valve (3) Open vent screw at intervals until oil comes out to allow switching gases to escape (4) CLOSE vent screw (5) OPEN stop valve (6) SWITCH ON pump until no more oil is pumped (7) Lift cover (pressure ring) slightly to allow residual gases to escape (8) Remove cover (pressure ring) (9) Wait 10 min. (to allow gas to escape); do not perform any cleaning work during that time. (10) Drain oil compartment; remove diverter switch insert (11) Pump off residual oil Unauthorized copying and distribution of this document and the utilization and communication of its contents are strictly prohibited unless expressly authorized. Offenders will be held liable for the payment of damages. All rights reserved in the event of the grant of a patent, utility model or ornamental design registration. F00788:01 Page 2 of 5 / TCS06005en.docx 1.2 On-load tap-changer is not equipped with pipe or valve for oil draining Drain hose d b 4 f 2 a 6 h Vent screw 1 c Cover Protective relay Return valve 9 l j 8 Silicagel breather 5 g 3 e Pump Sequence of work 1: Sequence of work 2: There is no gas cushion There is a gas cushion (1) CLOSE return valve a) OPEN return valve (2) Introduce pump suction pipe to vent screw b) Open vent screw at intervals until oil comes out to (3) Pump off oil allow switching gases to escape (4) OPEN return valve c) CLOSE vent screw (5) Continue to pump off oil until no more oil is pumped d) CLOSE return valve (6) Remove cover (pressure ring) e) Introduce pump suction pipe to vent screw (7) Wait about 10 min. (to allow gas to escape); do not f) Pump off oil perform any cleaning work during that time g) OPEN return valve (8) Drain oil compartment; remove diverter switch insert h) Continue to pump off oil until no more oil is pumped (9) Pump off residual oil i) Remove cover (pressure ring) j) Wait about 10 min. (to allow gas to escape); do not perform any cleaning work during that time k) Drain oil compartment; remove diverter switch insert l) Pump off residual oil Page 3 of 5 / TCS06005en.docx 2. MR tap changer 2.1 On-load tap-changer is equipped with pipe or valve for oil draining 11 7 Oil drain pipe Air-vent valve 5 9 4 Cover 2 Protective relay Return valve 10 Silicagel breather 6 Stop valve 3 13 8 Pump Sequence of work: (1) CLOSE 3-way valve of main oil conservator of transformer (2) OPEN return valve (3) CLOSE stop valve (4) Open air-vent valve of cover at intervals until oil comes out to allow switching gases to escape (5) CLOSE return valve (6) OPEN stop valve (7) OPEN air-vent valve of cover (8) Pump off oil to just below cover level (9) Remove cover (10) Remove diverter switch insert, drain oil compartment (11) OPEN return valve - let oil drain completely from oil conservator (only if oil conservator of tap changer and main oil conservator of transformer were separated before) (12) Wait 10 min. (to allow gas to escape); do not perform any cleaning work during that time (13) Pump off residual oil 1 Page 4 of 5 / TCS06005en.docx 2.2 Transformer or on-load tap-changer is not equipped with pipe or valve for oil draining Drain hose Rupture Rupture disk d c 7 e Air-vent valve 3 5 b 1 a Return valve Protective relay 9 Silicagel breather g 4 Pump Sequence of work 1: Sequence of work 2: There is no gas cushion There is a gas cushion (1) CLOSE return valve a) CLOSE return valve (2) CLOSE 3-way valve of main conservator of b) Lift cover slowly to allow switching gases to escape transformer c) Remove cover (3) Break the rupture disk (type D, E, F, G, K) and d) Remove diverter switch insert, and drain oil introduce the pump suction pipe compartment (4) Pump off oil to just below cover level e) OPEN return valve - let oil drain completely from oil (5) Remove cover conservator (6) Remove diverter switch insert, drain oil compartment f) Wait 10 min. (to allow gas to escape); do not perform (7) OPEN return valve - let oil drain completely from oil any cleaning work during that time conservator (only if conservator is separate, otherwise, g) Pump off residual oil rinse pipe) (8) Wait 10 min. (to allow gas to escape); do not perform any cleaning work during that time (9) Pump off residual oil Page 5 of 5 / TCS06005en.docx DANGER! Fire hazard! The switching oil of the on-load tap-changer should always be treated as an inflammable liquid. During operation, potentially explosive switching gases may accumulate under the on-load tap-changer cover, in the piping, in the oil conservator or at the dehydrating breather opening. Please ensure that there are no open fires, hot surfaces or sparks (e.g. through static charging) in the direct vicinity. Possible sources of ignition at the on-load tap- changer: Caution during draining of the diverter switch oil compartment and oil conservator: Use only conductive, grounded hoses, tubes and pumping equipment suitable for flammable liquids, in order to pre- vent ignition the switching gases. Caution when removing the on-load tap-changer cover: Before starting work on the on-load tap-changer cover, all auxiliary circuits must be de-energized (e.g. tap- change supervisory control, pressure relief valve, pressure monitoring device). No electrical devices may be used for the work (e.g. impact wrench - spark formation). Open the stop valve between the oil conservator and the diverter switch oil compartment, then open the bleeder valve in the on-load tap-changer cover. Vent the swit- ching gas from the space below the on-load tap-changer cover. Ensure adequate ventilation (e.g. in transformer cells and work tents). Once the switching gas has been vented and oil starts to enter through the bleeder valve, close the bleeder valve and then the stop valve between the oil conservator and the diverter switch oil compart- ment. Now open the bleeder valve again open and drain approx. 5-10 l of oil via the drain pipe (until the area below the on-load tap-changer cover is oil-free). The on-load tap-changer cover must be removed, if oil is to be drained from the oil conservator via the diverter switch oil compartment. Wait approx. 15 min in order to allow the switching gases to dissipate. Caution when working on the dehydrating breather: When removing the dehydrating breather, ensure that no explosive gases are present in the dehydrating breather and the piping. During normal operation small quantities of explosive gases may escape from the dehydrating breather. TCS Uwe Seltsam [valid with typewritten signature] Copies to: TS Manual, MR subsidiaries and representatives 4 Oil (oil sapmle, oil filter unit, sealing, tightnes, oil conservator) 4.2 Oil conservator for tap changers Tap changers with separate oil conservators are faced with frequent difficul- ties, as transformer manufacturers only take the thermal expansion of the oil inside the diverter switch oil compartment into consideration in regard to the dimensioning of the oil conservators, but not the oil displacement in the tap changer head due to switching gases. The table in attachment 1 shows oil contents of diverter switch oil compartments, the oil displacement due to switching gases, the thermal expansion of oil for T130°C and the resulting oil contents of the oil conservators for tap changer types C, D, E, F, G, K. Column 4 shows the change in oil volume in the oil conservator, in relation to the lowest and highest insulation level voltage of the tap changers. The rec- ommended oil content of the oil conservators is shown in column 5. The number relates to the highest insulation level voltage of the respective tap changer, while taking the safety margin of 50% into account. Type V_gas V_OLTC V_130°C V_delta V_min C I 200 20 kV 1 2 3 4 5 3 58 5.8 8.8 20 C III 200 ∆ 60 kV 105 10.5 13.5 D 30 kV 19 83 8.3 27.3 50 150 kV 136 13.6 32.6 E 60 kV 19 140 14 33 55 220 kV 175 17.5 36.5 F 30 kV 30 223 52.3 58.3 90 220 kV 311 61.1 61.1 G 60 kV 70 670 137 137 225 220 kV 800 158 150 K 60 kV 45 485 93.5 93.5 150 220 kV 575 102.5 102.5 Table 4: Minimum oil content in conservator Legend of table Type – On-load tap-changer type V_gas – oil displacement due to switching gases V_OLTC – oil content inside diverter switch oil compartment V_130°C - ∆T 130°C expansion -30°c to +100°C V_delta – Change of oil volume inside the conservator V_min – Minimum oil content in conservator All information given in [ l ]. EN 19 4 Oil (oil sapmle, oil filter unit, sealing, tightnes, oil conservator) 4.3 Mobile Oil Filter Unit OFP 010-SD Quick reference guide This quick reference guide describes the work steps with the mobile oil filter unit OFP 010-SD in detail. Basically, you always have to take the operating instructions with you. This quick reference guide is intended to simplify work. Preparations Preparations before the trip Check the mobile oil filter unit for completeness before the start of the trip. The mobile oil filter unit consists of the following components: ▪ 4 hoses. Increase number if more hoses are required ▪ 2 suction tubes ▪ Pipe adapter with sealing tape ▪ Operating instructions and quick reference guide ALL15002 In addition, you should have the following objects and material with you: ▪ New oil reserve of about 15 l per OLTC column ▪ Measuring device for dielectric strength of insulating oil (BAUR) ▪ Empty barrels (at least 2) ▪ Drip pan to be placed underneath ▪ Waste sacks ▪ Plastic tarp to be placed underneath ▪ Cloths ▪ Oil binding agent ▪ Oil sample bottle (if necessary) Take the following material with you for filtering the insulating oil: ▪ Fuller's earth – Type Microsorb 30/60 LVM, about 10 l per diverter switch insert ▪ Bag filter – Type FSI, 2 items per diverter switch insert ▪ Fine filter cartridges – Type AC-718 ½, 2 items per diverter switch insert ▪ Moisture filter cartridges – Type SD-718 P3, 1 item per 4 diverter switch inserts 20 EN 4 Oil (oil sapmle, oil filter unit, sealing, tightnes, oil conservator) Preparations on site When installing oil filter unit and corresponding components and during op- eration of the oil filter unit, take appropriate measures to make sure that leaking insulating oil does not pollute the environment (e.g., plastic tarp and / or drip pan). Check the oil filter unit for leaks, completeness, transport dam- age and sound condition of the electrical connections (see following figure). Clean the coarse filter as described in section 4. Figure 3: Mobile oil filter unit - overview Overview and connecting the oil filter unit When connecting the hoses to the mobile oil filter unit, always make sure to meet the following requirements (see following figure): Suction side --> inlet valve EN 21 Tex 8 M8 x 20 30 Nm 11 12 13 14 15 16 17 18 19 20 Text box Text box 4 Oil (oil sapmle, oil filter unit, sealing, tightnes, oil conservator) 6 cm Pressure side --> outlet valve Tank for bag filter with Fuller's earth Tank for fine particle filter and fine moisture filter Outlet valve / pressure side Inlet valve / suction side Figure 4: Overview front Valve configuration See attachment A.1 for an overview and designation of all valves of the mo- bile oil filter unit. Representation of the valves on the display Visual symbols are used to present the desired valve positions for the vari- ous operating modes. To set the oil flow as shown in figure 3 , set the corre- sponding valves manually to the position shown on the display. When you press the valves on the display, the valves change position on the display, and therefore change the oil flow on the display (brown in the follow- ing figure). Caution: 22 EN 4 Oil (oil sapmle, oil filter unit, sealing, tightnes, oil conservator) The valves must be set manually. The valves cannot be set electronically. The display is just intended to show the desired state! Figure 5: Representation on the display Setting the valves for the "Bypass" function Open inlet valve and outlet valve (see following figure). Close all drain valves. Drain valve Outlet valve Inlet valve Figure 6: Main valves "Bypass” function Put particle filter valve and moisture filter valve in the "Bypass" position (see following figure). Valve of the particle filter Valve of the moisture filter Figure 7: Fine filter function “Bypass” EN 23 4 Oil (oil sapmle, oil filter unit, sealing, tightnes, oil conservator) 10 11 20 21 1 30 4 2 3 22 Figure 8: Pipe diagram of “Bypass” function Valve in red Closed condition Valve in green Open condition Yellow line Oil flow 1 Inlet valve of the unit, suction side 2 Outlet valve of the unit, pressure side 3 Valve of the particle filter 4 Valve of the moisture filter 10 Air-vent valve of particle filter 11 Air-vent valve of moisture filter 20 Drain valve of particle filter 21 Drain valve of moisture filter 22 Drain valve of the unit 30 Valve of the coarse filter Setting the valves for "Filter particles" function Open inlet valve and outlet valve (see following figure). Close all drain valves (third drain valve is not shown). Drain valve Inlet valve Outlet valve Figure 9: Main valves “Filter particles" function 24 EN 4 Oil (oil sapmle, oil filter unit, sealing, tightnes, oil conservator) Put particle filter valve and moisture filter valve in the "Filter particles" posi- tion (see following figure). Valve of the particle filter Valve of the moisture filter Figure 10: Fine filter function “Filter particles" 10 11 20 21 1 30 4 2 3 22 Figure 11: Pipe diagram of “Filter particles” function Valve in red Closed condition Valve in green Open condition Yellow line Oil flow 1 Inlet valve of the unit, suction side 2 Outlet valve of the unit, pressure side 3 Valve of the particle filter 4 Valve of the moisture filter 10 Air-vent valve of particle filter 11 Air-vent valve of moisture filter 20 Drain valve of particle filter 21 Drain valve of moisture filter 22 Drain valve of the unit 30 Valve of the coarse filter Setting the valves for the "Filter particles and moisture" function Open inlet valve and outlet valve (see following figure). EN 25 4 Oil (oil sapmle, oil filter unit, sealing, tightnes, oil conservator) Close all drain valves (third drain valve is not shown). Drain valve Outlet valve Drain valve Inlet valve Figure 12: Main valves “Filter particles and moisture" function Put particle filter valve and moisture filter valve in the "Filter particles and moisture" position (see following figure). Valve of the particle filter Valve of the moisture filter Figure 13: Fine filter function “Filter particles and moisture“ 26 EN 4 Oil (oil sapmle, oil filter unit, sealing, tightnes, oil conservator) 10 11 20 21 1 4 30 2 3 22 Figure 14: Pipe diagram of “Filter particles and moisture” function Valve in red Closed condition Valve in green Open condition Yellow line Oil flow 1 Inlet valve of the unit, suction side 2 Outlet valve of the unit, pressure side 3 Valve of the particle filter 4 Valve of the moisture filter 10 Air-vent valve of particle filter 11 Air-vent valve of moisture filter 20 Drain valve of particle filter 21 Drain valve of moisture filter 22 Drain valve of the unit 30 Valve of the coarse filter Setting of valves for "Drain oil filter unit" Close inlet valve and outlet valve (see following figure). Open all drain valves. Inlet valve Drain valve Outlet valve Drain valve Figure 15: Main valves “Drain“ function EN 27 4 Oil (oil sapmle, oil filter unit, sealing, tightnes, oil conservator) Put particle filter valve and moisture filter valve in the "Bypass" position (see following figure). Valve of the particle filter Valve of the moisture filter Figure 16: Fine filter function “Drain“ 10 11 20 21 1 4 30 2 3 22 Figure 17: Pipe diagram of “Drain oil filter unit” function Valve in red Closed condition Valve in green Open condition Yellow line Oil flow 1 Inlet valve of the unit, suction side 2 Outlet valve of the unit, pressure side 3 Valve of the particle filter 4 Valve of the moisture filter 10 Air-vent valve of particle filter 11 Air-vent valve of moisture filter 20 Drain valve of particle filter 21 Drain valve of moisture filter 22 Drain valve of the unit 30 Valve of the coarse filter 28 EN 4 Oil (oil sapmle, oil filter unit, sealing, tightnes, oil conservator) Handling of filter cartridges Bag filter with Fuller's earth (Type – FSI) Always use a new filter before starting the filtering process (see following fig- ures). Fill bag filter type FSI with Fuller's earth type Microsorb 30/60 LVM and put it in the "particle" filter tank. This step can be skipped if it is an OLTC type VACUTAP® or an OLTC in a spare transformer. Figure 18: Empty bag filter Figure 19: Bag filter with Fuller's earth Fine particle filter (type – AC 718 ½) Always change this filter when a differential pressure of ≥1500 mbar at a flow volume of 500 l/h is reached, or not later than you notice that the insulating oil gets more and more black (see following figure). Use this filter in the "particle" or "moisture" fine filter tank. EN 29 4 Oil (oil sapmle, oil filter unit, sealing, tightnes, oil conservator) Protect the filters from humidity during storage. Used filters contain insulating oil residues, therefore make sure to use safe packaging. Figure 20: Fine particle filter Fine moisture filter (type – SD 718 P3) Change this filter every time when one of the following criteria is met (see figure 19): – After absorption of 300 ml water or when reaching a differential pres- sure of ≥1500 mbar at a flow volume of 500 l/h – Water content of 13 ppm at the exit of the oil filter unit is exceeded Use this filter in the "water" fine filter tank (see figure 2). Protect the filters from humidity during storage. Used filters contain insulating oil residues, therefore make sure to use safe packaging. Figure 21: Fine moisture filter 30 EN 4 Oil (oil sapmle, oil filter unit, sealing, tightnes, oil conservator) Cleaning the coarse filter The coarse filter must be cleaned in the following cases: ▪ Before every filtering process, ▪ if the flow rate drops considerably, ▪ before removing the oil filter unit. Open cover and remove filter (see following figures). Clean filter and then install it again and close the cover. Figure 22: Sieve Figure 23: Coarse filter and cleaning Filtering procedure Commissioning Switch on main switch and wait until initialization phase is over (about 1 minute) (see following figure). EN 31 4 Oil (oil sapmle, oil filter unit, sealing, tightnes, oil conservator) Determine operation mode (Bypass, filter particles, filter particles and mois- ture) and set valves in accordance with the respective sections above. Insert filter(s) as described. Confirm valve position on display. Press start button (green). Set speed controller. Figure 24: Overview rear of oil filter unit Before starting the pump, bleed the filters via the top air-vent valves (see fol- lowing figure). Air-vent valve Figure 25: Bleeding the filter cartridges Filtering steps Step 1: Drain oil, "Bypass" Use this valve position for the "Bypass" function to pump down the oil in the oil barrels. This function can also be used to pump oil in the oil compartment to rinse it - but be sure to observe the correct pumping direction of the oil. The flow volume can be freely selected (max. 1000 l/h). Step 2: Filter particles - circulation Start oil circulation immediately after draining the oil at a flow volume of 450 l/h for about 2 hours, setting the valves as specified in the "Filter particles" function (3.3). Use only the bag filter with Fuller's earth for this step. 32 EN 4 Oil (oil sapmle, oil filter unit, sealing, tightnes, oil conservator) Make sure that the barrel is large enough for the purpose of circulation. Place the suction side on the bottom of the barrel and the pressure side or return hose in the top part of the barrel, below the oil level. The oil must not sputter or blow bubbles during circulation. Step 3: Filter particles and fine particle filter - circulation Then circulate the oil at a flow volume of 450 l/h for about 2 hours, setting the valves as specified in the "Filter particles and moisture" function (3.4). In this step, insert and use fine filter type – AC-718 ½ in addition to the bag filter with Fuller's earth. Make sure that the barrel is large enough for the purpose of circulation. Place the suction side on the bottom of the barrel and the pressure side or return hose in the top part of the barrel, below the oil level. The oil must not sputter or blow bubbles during circulation. Skip this step if it is new oil or used oil of a tap changer type VACUTAP®. Step 4: Particle filter and moisture filter – circulation Then circulate the oil at a flow volume of 450 l/h for about 2 hours, setting the valves as specified in the "Filter particles and moisture" function (3.4). In this step, insert and use fine filter type – SD-718 P3 in addition to the bag filter with Fuller's earth. Make sure that the barrel is large enough for the purpose of circulation. Place the suction side on the bottom of the barrel and the pressure side or return hose in the top part of the barrel, below the oil level. The oil must not sputter or blow bubbles during circulation. Step 5: Fill with oil Next, pump the oil into the oil compartment, setting the valves as specified for the "Filter particles and moisture" function. In this step, insert and use fine filter type – SD-718 P3 in addition to the bag filter with Fuller's earth. Set the flow volume to a value between 300 l/h and 400 l/h for this step. Step 6: Drain the oil filter unit Set the valves as specified in "Drain oil filter unit" (3.5) and drain the oil filter unit independent of the mode of operation. Let the pump run at full speed until no more oil is pumped. Then switch off the pump and close all valves. Automatic shutdown of the oil filter unit Should the overall pressure of the unit exceed 3.5 bar, the unit will stop op- eration automatically to protect the pump. If this happens, you should find and eliminate the cause why the maximum pressure was reached. EN 33 4 Oil (oil sapmle, oil filter unit, sealing, tightnes, oil conservator) Possible causes are: ▪ Kinked or clogged hose ▪ Outlet valve of unit is closed ▪ Oil conservator of tap changer is mounted too high (static pressure) ▪ Inserted filter is already full ▪ Viscosity of oil at cold temperatures (< 5°C) is too high Tests after completion of filtering process Determination of dielectric strength The dielectric strength of the refilled oil must be tested. Observe the specifications or operating instructions for the used test device when determining the breakdown voltage (see following figure). The measured breakdown voltage must always be ≥ 50 kV / 2.5 mm. Write down the value in the service report. Figure 26: Dielectric strength Determination of water content After the filtering process, the refilled oil must be tested for its water content. The water content in "ppm" is indicated on the display of the oil filter unit (see following figure). It must always be ≤ 15 ppm. 34 EN 4 Oil (oil sapmle, oil filter unit, sealing, tightnes, oil conservator) Write down the value in the service report. Figure 27: Water content 4.4 Oil samples for determining dielectric strength and water content The section below explains how to take oil samples for determining dielectric strength and water content of the diverter switch insulating oil. This instruction applies also when oil samples are taken on the transformer tank. For oil sampling on Hermetic-Transformers the following instructions are to be followed also: See (depending on OEM): Hermetic transformer General information The oil sample is used to determine dielectric strength in accordance with IEC 60156 / VDE0370-5 and water content using the Karl Fischer moisture test. Usability and validity of the test depend very much on the method the sam- ple is taken (IEC 60475 / VDE0370-3). It must be done with greatest care to ensure that the oil being tested actually corresponds to the conditions at the sampling location. In cases where the oil falls below the relevant minimum requirements, a sec- ond oil sample must be taken to decide on further action. Taking the oil sample General information ▪ Use faultless, clean and dry sample bottles only. ▪ Make sure that the sample bottle is not significantly colder than ambient temperature. ▪ In the case of rain, mist or high humidity, take precautions to prevent moisture from getting into the oil. ▪ Always fill the sample bottle to 95 - 98 % of its cubic content. EN 35 4 Oil (oil sapmle, oil filter unit, sealing, tightnes, oil conservator) Sampling from oil drain pipe Preferably take the oil sample from the sampling valve of the oil drain pipe that is mounted to the transformer wall. Oil drain pipe Diverter switch oil compartment Transformer Sampling valve Figure 28: Oil drain pipe of on-load tap-changer ▪ Connect hose (2) to sampling valve (1). ▪ To rinse outlet pipe and hose, open sampling valve and let off approx. 3 liters of oil. Dispose of this oil. ▪ Insert hose (2) into sample bottle (3) and rinse the sample bottle at least twice with the oil being tested. Dispose of this oil. ▪ Place sample bottle (3) in overflow container (4). ▪ Insert hose (2) right down to the bottom of the sample bottle (3) and open sampling valve (1) slowly. Drain oil at low speed into sample bottle (3) un- til it escapes from the bottle top. ▪ Open sampling valve (1) further until approx. 0.5 liters of oil escaped. ▪ Lower sample bottle (3) together with overflow container (4) until hose (2) is out of sample bottle. ▪ Pour out very little oil by tilting the sample bottle (3) slightly (95 to 98 % of sample bottle must be filled) and close it with the appropriate closure. ▪ Fill in the supplement sheet of the sample bottle and hand both off, mak- ing sure they cannot be mixed up, for further use. ▪ Check oil level of oil conservator and refill if necessary. 36 EN 4 Oil (oil sapmle, oil filter unit, sealing, tightnes, oil conservator) Figure 29: Sketch of oil sampling Sampling with open on-load tap-changer oil compartment When sampling via oil drain pipe is not possible, the sample can be taken from the OLTC oil compartment directly. ▪ If possible, take the sample immediately after opening the cover. If this is not possible, remove diverter switch insert and then take the sample im- mediately. ▪ Rinse sample bottle at least twice with the oil being tested. Dispose of this oil. ▪ Immerse sample bottle into the oil being tested and let oil flow slowly in the sample bottle, avoiding oil flow currents. ▪ Pour out very little oil by tilting the sample bottle (95 to 98 % of sample bottle must be filled) and close it with the appropriate closure. ▪ Fill in the supplement sheet of the sample bottle and hand both off, mak- ing sure they cannot be mixed up, for further use. ▪ Check oil level of oil conservator and refill if necessary. Dielectric strength test on site If dielectric strength is evaluated on site, attach test printout with OLTC serial number and signature of person performing test to your service report. Use relevant oil testing equipment (e.g., Baur DPA 75 C) as indicated in the appropriate user guide. ▪ Based on valid standards, the test must be made at 20 °C ± 5 °C. ▪ The test vessel of the oil testing equipment must not be significantly colder than ambient temperature. ▪ Check gap between test electrodes and adjust if necessary. ▪ Clean test vessel and test vessel cover in accordance with user guide of oil testing equipment. EN 37 4 Oil (oil sapmle, oil filter unit, sealing, tightnes, oil conservator) ▪ Rinse test vessel at least twice with the oil being tested. Dispose of this oil. ▪ Drain oil being tested along internal side of test vessel slowly and free from bubbles until 95 to 98 % of the test vessel are filled. ▪ Be sure to wait at least 1 hour. ▪ Perform test as described in the user guide of the oil testing equipment. 4.4.1 Change log 05.05.2023 TSC-Schmitten 1. Additional information for Hermetic transformers 23.09.2020 TSC-Schmitten 1. First release 38 EN 5 GFRP, hard paper 5 GFRP, hard paper 5.1 "Brown stains" on the inside of Rotafil insulating cylinders Brown stains are thermically discolored fiber bundles within the polyester fleece that may occur during the manufacturing process of the fleece. These thermic discolorations are located under the surface of the insulating mate- rial, on the inside of the GFRP cylinders (see following figures). Figure 30: Brown stains in insulating material_1 Figure 31: Brown stains in insulating material_2 EN 39 5 GFRP, hard paper Features Measures ▪ Diameter approx. 1 to 3 mm ▪ Stains remain unchanged ▪ In some cases elongated shape, up to 20 mm long and 5 mm wide ▪ No damage to surface ▪ No perceptible ridges Table 5: Features and measures 5.2 Chipped resin layers on insulating material First, the features and the resulting measures are regarded, see example 1 i the following figure. Chipped resin layers Figure 32: Chipped resin layers on insulating material Example 1 (top figure) Features: ▪ Chipped resin layer in the area of bore holes or in the shielded area ▪ Insulating materials Vetrelam or Rotafil 40 EN 5 GFRP, hard paper Resulting in the following measures: ▪ Damaged areas remain unchanged Example 2 (without figure) Features: ▪ Chipped resin layers in the area of the earthing distance or phase dis- tance on single-phase and delta tap changers ▪ Insulating materials Vetrelam or Rotafil ▪ Size up to approx. 4 cm² Measures: ▪ Use sanding paper with gradual grit (100 to 400) and transformer oil to smoothen ▪ Keep abraded area as small as possible ▪ Transition area from abraded to non-abraded surface must be rounded and without edges ▪ The responsible OPS will decide about shortening the inspection intervals or potential replacement of insulating materials 5.3 Polishing and wipe-lacquering of damaged GFRP surfaces Damaged GFRP surfaces can be polished and wipe-lacquered. Whether such repair work should be performed on the relevant area, is a case-by- case decision of TSC. Sequence of work: The affected area is thoroughly polished. A hand grinder is most useful in this case, such a Dremel or a similar tool that has a diamond polisher. In the process, the damage is polished out so far that no residual impurities remain in the material. The transition areas to the undamaged material should be rounded as far as possible. The polished area must be cleaned thoroughly. As the area is to be lacquered later on, the cleaning must be performed us- ing alcohol or spiritus (see following figure). Figure 33: Damaged surface EN 41 5 GFRP, hard paper Figure 34: Damaged area after polishing Apply lacquer to the affected area. To do so, mix the lacquer (part no 900107:00) and the hardener (part no 900108:00) with the mixing ratio 50:50. The remaining lacquer on the surface is wiped off with a lint-free cloth. The drying process of the remaining lacquer inside the pores can be accelerated by means of a hair dryer. Take care not to burn the lacquer though. This procedure must be repeated several times to decrease the roughness of the surface (see following figure). Figure 35: cleaned surface Figure 36: wipe-lacquered surface 42 EN 5 GFRP, hard paper 5.4 Criteria for dielectric testing of insulating material deliveries If the transformer is not dielectrically tested before commissioning or re-com- missioning, all insulating parts to which voltage is applied during operation must be dried and dielectrically tested by CTTV. This applies to both the cur- rent portfolio of products and old tap changers. CTTV will decide on a case- by-case basis which criteria apply to Siemens, TU or AEG on-load tap- changers and their components. Components Delta tap OLTC in neu- Single-phase Single-phase changer tral-point de- tap changer tap changer in sign neutral point application Diverter Yes No Yes No switch / selec- tor switch in- sert incl. insu- lating parts, in- dicator drive shaft, centering tube, tap- change super- visory shaft, di- verter switch oil compartment incl. suction tube Selector (se- Yes lector bars, se- lector column parts, segment drive shafts, selector shells) selector switch oil compart- ment incl. change-over selector Table 6: Dielectric test of various components depending on the OLTC type Dielectric tests are performed by CTTV in accordance with TD with 100 % of the rated power-frequency withstand voltage. The required test instructions will be prepared and archived by CTTV. Drying must be done even if no dielectric test is done by MR. Insulating material deliveries do not have to be dielectrically tested if the in- sulating parts are not dried at MR. If the information is missing whether a di- electric test was carried out at the customer, the customer must be advised in writing that MR did not dielectrically test the insulating parts. EN 43 5 GFRP, hard paper The prices for the dielectric test have been specified in SAP for the most common components and will be extracted automatically. If no price is ex- tracted, it must be calculated separately. The criteria for the dielectric test stated above have been agreed upon on 10 September, 2013 by CTTV, TD (CSTA) and TSC (CST1). 5.5 Treeing on the insulating material surface Below, the features and the resulting measures of the following figure are re- garded. Features Measures ▪ Net-like treeings of small dimensions ▪ Abrade using sanding paper (grit 100 non-removable to 400) and transformer oil (start with grit 100 and polish with grit 400) ▪ Keep abraded area as small as possi- ble ▪ Glass fiber must not be abraded ▪ The responsible OPS will decide about shortening the inspection inter- vals or potential replacement of insu- lating materials Table 7: Net-like treeings inside switching tube (see following figure) Figure 37: Net-like treeings inside switching tube 44 EN 5 GFRP, hard paper Features Measures ▪ Net-like treeings of substantial dimen- ▪ Replace insulating material sions non-removable ▪ If shutdown of transformer is not pos- sible until replacement, perform mea- sures as shown above ▪ The responsible OPS must arrange for the replacement as soon as possi- ble Table 8: Net-like treeings outside of switching tube (see following figure) Figure 38: Net-like treeings outside of switching tube Feature Measures ▪ Carbon deposits non-removable using ▪ Remove using eraser type Edding transformer oil and cloth. Similar to R20 figures shown above ▪ If not possible, proceed according to the measures stated above Table 9: Another feature and measures EN 45 5 GFRP, hard paper Features Measures ▪ Creepage path in scratch with light ▪ Light brown areas remain unchanged brown discolorations ▪ Abrade shorter dark brown to black ▪ Shorter dark brown to black areas areas using sanding paper, grit 100 to 400, and transformer oil ▪ Keep abraded area as small as possi- ble ▪ Use appropriate sanding paper holder ▪ The responsible OPS will decide about shortening the inspection inter- vals or potential replacement of insu- lating materials Table 10: Scratch with creepage path in insulating material Vetrelam (see following figure) Figure 39: Scratch with creepage path in insulating material Vetrelam Features Measures ▪ Length of creepage path up to 50% of ▪ Light brown areas remain unchanged phase distance ▪ Abrade shorter dark brown to black ▪ Light brown discoloration with dark areas using sanding paper, grit 100 to brown to black areas 400, and transformer oil ▪ Keep abraded area as small as possi- ble ▪ Use appropriate sanding paper holder ▪ The responsible OPS will decide about shortening the inspection inter- vals or potential replacement of insu- lating materials Table 11: Creepage path with black burn marks (see following figure) 46 EN 5 GFRP, hard paper Figure 40: Creepage path with black burn marks in insulating material Vetrelam Note: According to present knowledge, the light brown discoloration is a heating occurrence of the insulating material caused by "surface currents". The light brown discoloration is the beginning of a decomposition process of the insulating material. The light brown discoloration is not critical, as the complete decomposition of the insulating material has not yet been com- pleted. Type A Features Measures ▪ Length of creepage path up to 50% of ▪ Light brown areas remain unchanged phase distance ▪ Abrade shorter dark brown to black ▪ Light brown discoloration with dark areas using sanding paper, grit 100 to brown to black areas 400, and transformer oil ▪ Keep abraded area as small as possi- ble ▪ Use appropriate sanding paper holder The responsible OPS will decide about shortening the inspection intervals or po- tential replacement of insulating materi- als Table 12: Creepage path inside switching column, type A (see following figure) EN 47 5 GFRP, hard paper Type B Features Measures ▪ Creepage paths with dark brown to ▪ Abrade using sanding paper, grit 100 black areas to 400, and transformer oil ▪ Length up to approx. 2 cm ▪ Keep abraded area as small as possi- ble ▪ Use appropriate sanding paper holder ▪ The responsible OPS will decide about shortening the inspection inter- vals or potential replacement of insu- lating materials Table 13: Creepage path inside switching column, type B (see following figure) Type C Features Measures ▪ Creepage paths bridge individually or ▪ Replace insulating material in total more than 50% of the phase ▪ If shutdown of transformer is not pos- distance sible until replacement, abrade creep- age paths using sanding paper, grit 100 to 400, and transformer oil ▪ Use appropriate sanding paper holder ▪ Keep abraded area as small as possi- ble ▪ The responsible OPS must arrange for the replacement of the insulating materials as soon as possible Table 14: Creepage path inside switching column, type C (see following figure) 48 EN 11 12 13 14 15 16 17 18 19 20 Text box Text box 5 GFRP, hard paper 6 cm Type A) Short light brown Type B) creepage path Type B) Short creepage path Type A) with dark brown to black Phase distance areas Type C) Creepage path bridges 50% Type C) of phase distance Type B) Figure 41: Creepage path inside switching column EN 49 5 GFRP, hard paper Features Measures ▪ Creepage paths bridge individually or ▪ Replace insulating material in total more than 50% of the phase ▪ If shutdown of transformer is not pos- distance sible until replacement, abrade creep- age paths using sanding paper, grit 100 to 400, and transformer oil ▪ Use appropriate sanding paper holder ▪ Keep abraded area as small as possi- ble ▪ The responsible OPS must arrange for the replacement of the insulating materials as soon as possible ▪ Shorter creepage paths up to a few ▪ Use scraper to scrape out cm of length ▪ Subsequently, use sanding paper, grit ▪ Dark brown to black discoloration 100 to 400, and transformer oil to ▪ Insulating material burned smoothen ▪ Creepage path burned deeply into the ▪ Keep abraded area as small as possi- insulating material ble ▪ Use appropriate sanding paper holder ▪ Transition area from abraded to non- abraded surface must be rounded and without edges ▪ The responsible OPS will decide about shortening the inspection inter- vals or potential replacement of insu- lating materials Table 15: Creepage path bridges phase distance 50 EN 5 GFRP, hard paper Phase distance Figure 42: Creepage path bridges phase distance Features Measures ▪ Extensive creepage path ▪ Replace insulating material ▪ Lots of treeings ▪ If shutdown of transformer is not pos- sible until replacement, abrade creep- age paths using sanding paper, grit 100 to 400, and transformer oil ▪ Use scraper to scrape out any deep creepage paths ▪ Avoid abrading undamaged areas be- tween creepage paths ▪ The responsible OPS must arrange for the replacement of the insulating materials as soon as possible Table 16: Extensive creepage path on outside of switching column EN 51 5 GFRP, hard paper Figure 43: Extensive creepage path on outside of switching column 52 EN 5 GFRP, hard paper Features Measures ▪ Distance a) ▪ Distance a) ▪ Shorter creepage paths up to a few ▪ Use scraper to scrape out cm of length ▪ Subsequently, use sanding paper, grit ▪ Dark brown to black discoloration 100 to 400, and transformer oil to ▪ Insulatin