Petroleum Refining Processes PDF
Document Details
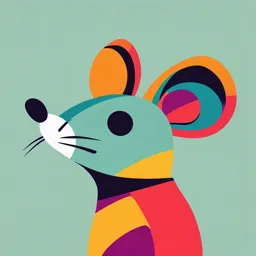
Uploaded by SwiftSugilite1509
Tags
Related
- Introduction to Petroleum Refining PDF
- Introduction To Petroleum Refining PDF
- Petrochemical & Petroleum Refining Technology - c5.pdf
- Petrochemicals & Petroleum Refining Technology PDF
- Petrochemical & Petroleum Refining Technology PDF
- Fundamentals of Refining and Petrochemical Engineering (RP 170) 2022 PDF
Summary
This document details the manufacturing process of petroleum, including raw materials like crude oil and natural gas, as well as unit operations like distillation and solvent extraction. It also covers unit processes such as hydrotreating and reforming, along with other aspects of petroleum refining.
Full Transcript
II. Manufacturing Process Petroleum A. Raw Materials Crude Oils Crude oils are the primary raw material utilized in production; they are complex combinations of hydrocarbons and saturated molecules, including paraffin, ethane, and...
II. Manufacturing Process Petroleum A. Raw Materials Crude Oils Crude oils are the primary raw material utilized in production; they are complex combinations of hydrocarbons and saturated molecules, including paraffin, ethane, and methane. Petroleum products like gasoline, diesel, jet fuel, and kerosene are made from crude oil. Natural Gas Natural gas undergoes treatments like hydrotreating and hydrocracking to eliminate sulfur content and generates hydrogen through steam reforming. Its role extends to being a heating fuel, which is crucial for maintaining elevated temperatures necessary for distillation and cracking processes. Hydrogen Hydrogen purifies crude oils by extracting sulfur and other impurities, in addition to facilitating the breakdown of large molecular structures into smaller constituents. Water Water is employed both as a cooling agent to remove hydrogen sulfide chemicals and as a critical component in hydrogen production and cracking, achieved through steam reforming. 18 Oxygen The application of oxygen is mainly in the conversion of hydrogen sulfide into elemental sulfur via the Claus process, and it plays a critical role in combustion processes to generate heat or power. Catalyst Catalysts play a crucial role in speeding up the rate of reactions without being used up. Platinum-based catalysts convert naphtha into high-octane gasoline compounds through catalytic reforming. Zeolite catalysts facilitate the cracking of gas oils into gasoline, while metal catalysts are needed in sulfur removal and hydrocarbon breakdown. Acid catalysts used in alkylation convert isobutane and olefin into high-octane alkylates. Other Chemicals and Additives Other chemicals and additives like sodium hydroxide are utilized to enhance product quality. Sodium hydroxide effectively eliminates excess sulfur from kerosene and gasoline, thereby improving the properties of the final products. B. Unit Operations Distillation Atmospheric distillation separates crude oil into fractions using heat to vaporize components based on their boiling points. After the crude oil undergoes atmospheric distillation, the heavy residues go through vacuum distillation under reduced pressure. Atmospheric distillation allows distilling components to decompose at high temperatures. 19 Separation Distillation separates gases from liquid streams to extract valuable gases such as LPG and butanes. Sour water stripping is an operation in which sour water, laden with hydrogen sulfide, undergoes the stripping process to remove gas. Gas-liquid separators are employed to separate gases from liquids to ensure the efficiency of the refining process. Solvent Extraction Merox treating represents a physical and chemical process aimed at purifying distillates, including but not limited to kerosene and gasoline. The process extracts sulfur components that are present in the distillates, which results in an acidic solvent. The removal of sulfur compounds is crucial for enhancing the quality of the fuel and meeting environmental standards. Through the application of this process, the treated distillates exhibit significantly lower levels of sulfur, thereby contributing to the production of cleaner and more efficient fuels. Blending The process of blending gasoline wherein gasoline components undergo a mixing process. Blending process ensures the gas complies with fuel standards and enhances its properties. Through the strategic selection and combination of different gasoline fractions, refiners can tailor the properties of the final gasoline product to meet specific criteria, such as octane rating and volatility, making blending an essential step in the production of gasoline that meets both industry standards and consumer expectations. 20 C. Unit Processes Hydrotreating The hydrotreating oil process removes impurities such as sulfur and nitrogen utilizing hydrogen methods. The hydrotreating process evaporates the oil, combines it with hydrogen, and runs it over a catalyst. These catalysts are essential because they quicken the chemical reactions that eliminate sulfur and nitrogen. Examples of these catalysts include tungsten, nickel, or a combination of cobalt and molybdenum oxides supported on an alumina basis. Operating temperatures typically fall between 260°C to 425°C with pressures ranging from 14 to 70 bars or 200 to 1,000 psi. Without compromising the oil's other qualities, these parameters are carefully regulated to remove sulfur to the right amount. The nitrogen in the oil is changed into ammonia and the sulfur into hydrogen sulfide throughout this process. Next, the hydrogen sulfide is absorbed in a solution like diethanolamine to be extracted from the hydrogen stream that is currently in circulation. To get rid of the sulfide, heat this solution and then use it again. High-purity elemental sulfur can be made with the recovered hydrogen sulfide. Reforming Reforming is a process that uses heat, pressure, and a catalyst (often containing platinum) to convert naphthas into high-octane gasoline and petrochemical feedstock. Naphthas are hydrocarbon mixtures containing paraffins and naphthenes. In Australia, naphtha feedstock comes from crude oil distillation or catalytic cracking processes, while overseas, it comes from thermal and hydrocracking processes. Reforming converts some of these compounds into iso paraffins and aromatics, which produce higher-octane 21 gasoline. For example, paraffins are converted to isoparaffins, paraffins are converted to naphthenes, and naphthenes are converted to aromatics. Figure 17. Reaction of Catalytic Cracking Process Isomerization The process of isobutane production involves the isomerization of regular butane. The catalyst utilized in this process is aluminum chloride, supported on alumina and improved by adding hydrogen chloride gas. Developments in commercial methods have made it possible to isomerize low-octane normal pentane and hexane into their higher-octane isoparaffin counterparts, in addition to isobutane. The process includes platinum-based catalysts similar to catalytic reforming, which occurs in the presence of hydrogen. The value of hydrogen is found in its capacity to reduce adverse side effects without being created or consumed. It is subjected to distillation and molecular extraction to desired compounds from the mixture are subjected to distillation. Most processes extract low-octane components from the gasoline mix, and it does not raise the octane level enough to make a considerable contribution to the manufacturing of unleaded gasoline. Alkylation The alkylation process synthesizes longer chain molecules by merging two smaller ones, specifically an olefin with an isoparaffin, typically isobutane, that makes 22 high-octane petrol. Two primary alkylation methods are utilized in the industry, each distinguished by the type of acid catalyst employed. The sulfuric acid alkylation method uses concentrated sulfuric acid with a purity of 98% to catalyze the reaction, which takes place at temperatures ranging from 2 to 7°C (35 to 45°F). High-quality gasoline components are indicated by the octane ratings of the alkylates produced using this process, which range from 85 to 95. Furthermore, hydrofluoric acid is used as the catalyst in the hydrofluoric acid alkylation process as an alternative. The use of hydrofluoric acid enables the reaction to take place at high temperatures ranging from 24 to 46°C (75 to 115°F). The chemical reactions stimulated by HF resemble those in the sulfuric acid process. Hydrofluoric acid recovery is accomplished through distillation. Cracking The Fluid Catalytic Cracking process uses a fine particle catalyst that acts as a fluid when mixed with vapor. The fresh feed is preheated in a process heater and then introduced into the bottom of a vertical transfer line or riser along with a hot regenerated catalyst. The hot catalyst vaporizes the feed, bringing both to the desired reaction temperature of 470 to 525°C (880 to 980°F). Most of the cracking reactions occur in the riser due to the high activity of modern catalysts as the catalyst and oil mixture flows upward into the reactor. Cyclones in the reactor separate the hydrocarbon vapors from the catalyst particles. The resulting reaction products are sent to a fractionator for separation. As the catalyst is used up, it settles at the bottom of the reactor. It undergoes steam stripping as it exits the reactor's base to eliminate absorbed hydrocarbons. The catalyst that has been spent is then transported to a regenerator. Any coke accumulated on 23 the catalyst due to the cracking reactions within the regenerator is burned away in a carefully controlled combustion process utilizing preheated air. The temperature in the regenerator is typically maintained between 590 to 675°C (1100 to 1250°F). Following this regeneration process, the catalyst is recycled and mixed with a fresh supply of hydrocarbon feed, ready to be used again in the reaction process. Hydrocracking is a process where the value of crude oil is greatly increased when large hydrocarbons are broken down into smaller, more valuable products like jet fuel, diesel, and gasoline. This conversion is accomplished by a process in which hydrogen is necessary. Hydrocarbon molecules are "cracked" into smaller ones through high-pressure reactions between hydrogen and a catalyst. FCC converts unsaturated hydrocarbons to saturated hydrocarbons and prevents the development of coke. Thus, the usefulness and economic worth of crude oil are maximized as a result of this process, which successfully raises the production of lighter, more valuable petroleum products from the heavier fractions. Delayed Coking In the delayed coking process, the heated feedstock is introduced at the bottom of a fractionator to remove light ends from the feed. The stripped feed is then mixed with recycled products from the coke drum and rapidly heated in the coking heater to a temperature range of 480 to 590°C (900 to 1100°F). Steam injection is utilized to regulate the residence time in the heater. The vapor-liquid feed exits the heater and moves to a coke drum where, under controlled residence time, pressure (1.8 to 2.1 kg/cm2 [25 to 30 psig]), and temperature (400°C [750°F]), it is cracked to produce coke and vapors. 24 Claus Process The Claus process involves the partial combustion of the H2S-rich gas stream using one-third of the stoichiometric quantity of air. The unburned H2S and resultant sulfur dioxide are combined with a bauxite catalyst to create elemental sulfur. In the Claus furnace, acid gas from the acid gas removal (AGR) process is burned with enough air or oxygen to produce a gas mixture that has the correct 2 to 1 stoichiometric ratio of H2S to sulfur dioxide (SO2) for conversion to sulfur and water. A small quantity of recycling from the tail gas treatment unit and overhead gases from sour water stripping are among the other fuels used in the furnace. The reactions primarily form the sulfur in the furnace. The hot furnace exhaust cools and condenses in the waste heat boiler, separating the gaseous sulfur from the gasses. To promote complete conversion to sulfur, the removal of sulfur catalyzes more conversion in the downstream catalytic reactor stages, which occur at progressively lower temperatures. The gases are reheated before entering the first catalytic reactor, where they undergo a 75% conversion process. Subsequently, the gases are cooled, the sulfur is condensed, and finally removed. Additional steps are taken to recover roughly 98% of the total sulfur. The integrated WHB recovers reaction heat from the burner by producing medium-pressure steam for reheating in catalytic stages and other applications. Hydrogen Synthesis Hydrogen synthesis uses hydrogen to decrease the amount of sulfur in fuels through hydrotreating and hydrocracking. For the production of ultra-low sulfur fuels—which are required by law in several countries related to environmental 25 concerns—hydrogen synthesis is particularly crucial. Sulfur compounds and hydrogen combine to form hydrogen sulfide, which may be separated out. D. Process Flow Diagrams Figure 18. Schematic Diagram of Petroleum Refinery 26 Petrochemicals A. Raw Materials Primary Raw Materials Primary raw materials typically refer to naturally occurring substances that have not undergone chemical changes after extraction. Petrochemical manufacturing relies on natural gas and crude oils as fundamental raw materials. Crude Oil The gases produced by various methods of processing crude oil are significant suppliers of olefins and LPG. Distillates and residues of crude oil are used as starting materials for olefins and aromatics through cracking and reforming procedures. Crude oil consists of a blend of hydrocarbons and the distillation process is designed to separate the crude oil into distinct categories of hydrocarbon components, known as "fractions." The crude oil is initially heated and then introduced into a distillation column also referred to as a still. In this column, different products vaporize and are collected at varying temperatures. Lighter products, such as butane, liquid petroleum gases (LPG), gasoline blending components, and naphtha, are collected at lower temperatures. Medium-range products, including jet fuel, kerosene, and distillates (diesel fuel), are recovered at moderate temperatures. Residual fuel oil is collected at temperatures that can exceed 1,000 degrees Fahrenheit. 27 Natural Gas Ethane and LPG are recovered from natural gas and utilized as intermediates in the production of olefins and diolefins. Methanol and ammonia are extracted from methane through synthesis gas. Secondary Raw Materials Secondary raw materials, or intermediates, are derived from natural gas and crude oil using various processing methods. The raw materials used in producing other chemicals from petroleum are known as feedstocks. These can be classified into three general groups: olefins, aromatics, and a third group that includes synthesis gas and inorganics. Olefins Olefins are unsaturated hydrocarbons with straight-chain molecules, including ethylene, propylene, and butadiene. Ethylene is the primary hydrocarbon feedstock utilized in the petrochemical industry with many different uses. It is used to manufacture ethylene glycol for polyester fibers and resins, as well as antifreeze, ethyl alcohol for solvents and chemical reagents, polyethylene for film and plastics, styrene for resins, synthetic rubber, plastics, and polyesters, and ethylene dichloride for vinyl chloride, which is used in plastics and fibers. Propylene is commonly used in the production of epoxy glue, rubbing alcohol, acrylics, and carpets, while butadiene is used for making synthetic rubber, carpet fibers, paper coatings, and plastic pipes. 28 Aromatics Aromatics are unsaturated hydrocarbon molecules that form rings. The primary aromatic feedstocks include benzene, toluene, xylene, and naphthalene. Benzene is utilized in the production of styrene, a key component of polystyrene plastics, as well as in the manufacturing of paints, epoxy resins, glues, and other adhesives. Toluene is predominantly employed in manufacturing solvents, gasoline additives, and explosives. Xylene has applications in producing plastics, synthetic fibers, and refining gasoline. Lastly, naphthalene is used in manufacturing pesticides. Synthesis Gas and Inorganics Synthesis gas is necessary for the production of methanol and ammonia. The Haber-Bosch process produces ammonia that is used to produce ammonium nitrate which is commonly used as a fertilizer. Meanwhile, formaldehyde is made from methanol, obtained by catalytically hydrogenated carbon monoxide. As formaldehyde is essential in creating resins and adhesives, a significant amount of methanol is needed to achieve this objective. In addition, methanol helps create silicone rubber, polyester fibers, and plastics—substances essential to the packaging, textile, and automobile sectors. B. Unit Operations Distillation The distillation column plays a crucial role in the refining of crude oil, functioning much like a still by separating the product into its various chemical 29 components based on differences in volatility. The process stream is heated before entering the column, leading to partial vaporization. As it ascends the tower, the vapor cools. Light components continue to rise, while heavier components condense and fall to the bottom as a liquid. The crude distillation unit separates crude oil into fractions such as light naphtha, heavy naphtha, jet fuel, diesel, and atmospheric gas oil (AGO) based on their boiling points. Additionally, the vacuum distillation unit further separates heavier residues from the crude distillation. Gas Processing Gas processing purifies raw natural gas to extract valuable components. The process begins with natural gas extraction which contains impurities like sulfur or carbon dioxide. The natural gas is then extracted into fractions: ethane, methane, propane, and butane. The purified gas is then fractionated into crucial components such as methane (used as fuel), ethane (for ethylene production), and propane and butane (used in fuels or further processed into petrochemicals). Heat Exchangers Preheating feedstocks such as crude oil, natural gas, or intermediate streams is a common practice before they enter reactors or cracking units. In the petrochemical sector, heat exchangers are required to operate at high pressure and high temperature, both onshore and offshore. Since crude fossil fuels contain significant amounts of water, a considerable part of the process is dedicated to removing it from the finished products. Heating, cooling, and distillation 30 operations are all crucial stages further along in the process, as is the recovery of energy to maximize product efficiency. Compression In the production of petrochemicals, compression is the process of increasing gas pressure for easier movement and processing. By decreasing the amount of gas, compressors produce denser gas and higher pressure. High pressure prepares gases like ethylene and methane for additional processing in reactors or distillation units and enables effective gas transportation via pipelines. Gases are made suitable for separation and conversion into valuable petrochemical materials through compression. Separation The process of separating a hydrocarbon mixture into its various components and using their unique physical properties such as density and boiling points. Fractional distillation is a common technique that entails heating the mixture and separating its parts as they evaporate at various temperatures. Aromatics Extraction One crucial process used in petrochemicals to separate aromatic hydrocarbons from petroleum and other hydrocarbon blends is aromatics extraction. Aromatic hydrocarbons, such as benzene, toluene, and xylene (referred to as BTX), are valuable raw materials used in the production of various chemicals and materials, such as synthetic fibers, resins, and plastics. 31 Polymerization In petrochemicals, polymerization is the process of forming polymers from petroleum-based monomers like ethylene and propylene. There are two main types of polymerizations: condensation (step-growth) polymerization, where monomers react and release a tiny molecule like water, and addition (chain-growth) polymerization, when unsaturated bond monomers connect together. Several significant polymers are produced as a result of this process, such as nylon for textiles, polyethylene for packaging, and polypropylene for auto parts. C. Unit Processes Steam Cracking The process of steam cracking is a petrochemical method that involves breaking down saturated hydrocarbons into smaller, often unsaturated hydrocarbons. This process is the main industrial technique for generating lighter alkenes, such as ethene (ethylene) and propene (propylene). Aromatization Aromatization refers to a chemical transformation in which specific hydrocarbons, such as those present in naphtha (a light segment of crude oil), undergo conversion into aromatic compounds such as benzene, toluene, and xylenes (known collectively as BTX). These aromatic substances are crucial foundational elements in manufacturing plastics, synthetic fibers, and other petrochemical goods. 32 Hydrogenation Hydrogenation involves the addition of hydrogen gas (H₂) to unsaturated hydrocarbons, such as ethylene and propylene, which contain double bonds. This chemical process disrupts the double bonds, enabling the carbon atoms to form bonds with hydrogen atoms, thereby transforming the unsaturated hydrocarbons into more stable saturated hydrocarbons with single bonds. The process enhances the material to be suitable into conversion of products like plastics. D. Process Flow Diagrams Figure 19. Schematic Diagram of Primary Raw Materials of Petrochemical Manufacturing Process Figure 20. Schematic Diagram of Natural Gas Processing 33 III. Common Manufacturing Problems and Proposed Solutions The petroleum and petrochemical industries form the backbone of the global economy, initiating energy production, manufacturing, and virtually any other industry. Nevertheless, the technical problems associated with the refining and processing petroleum create problems regarding lost operations, reduced efficiency, and environmental degradation. Common manufacturing issues such as corrosion, fouling, scaling, emissions, environmental contamination, and production bottlenecks are not only technical problems but cause economic and social concerns, which also incur expensive losses in terms of time, increased running costs, and damage to the environment, all of which have feedback effects across supply chains and communities. 1. Corrosion and Leaks Petroleum refineries face a significant challenge in the form of corrosion. Over the last few decades, there has been a growing focus on this issue because of the ongoing reliance of the global economy on oil and natural gas-based industries. It may lead to interference with refinery processes, which include without notice shut down, leaks, and loss of products. Corrosion is considered a great danger to refineries because it ensures metallic appliances are exposed to corroding agents. There have been other forms of corrosion caused by the interaction of the material with the environment in other parts of petroleum refineries, and as National Association of Corrosion Engineers (NACE) has estimated, the annual cost of corrosion in US refineries exceeds 3.7 billion dollars. 34 Figure 21. Oil and Gas Refinery Explosion Caused by Corrosion With increased demand for highly acidic crude to maximize profits, refineries would experience more corrosion. The overhead distillation unit tends to be very acid in nature and hence corrosive since it favors the occurrence of acid corrosion. Hydrotreaters are used in refinery areas for removing impurities such as sulfur and nitrogen and, hence are more susceptible to corrosive conditions. However, naphthenic acid (NA) corrosion can damage hydrotreaters and undermine the reliability of the unit. Therefore, the first measure of corrosion prevention will be to choose proper materials for the design plants by regulating the deteriorating agents applied in refineries. After that, it is also equally important to apply suitable coatings, inject corrosion inhibitors, remove corrosive elements from crude oil, and apply other techniques uniformly during the course of plant operation. 2. Fouling and Scaling Fouling and scaling occur when unwanted materials, such as minerals, biological organisms, or hydrocarbons, accumulate on the surfaces of heat exchangers, pipes, and reactors (Kazi, 2022). These phenomena commonly occur because of suspended particles in the fluid flow, high temperatures that cause chemical reactions, and biological growth 35 in cooling systems, which are all common in petrochemical industries, specifically crude oil processing plants, and are particularly prevalent in heat exchangers, pipes, and reactors. Particle buildup within crucial equipment such as heat exchangers, boilers, and reactors reduces heat transfer efficiency, increases energy consumption, and can lead to equipment failures and unscheduled shutdowns. Fouling can reduce plant efficiency by up to 30%, increasing energy consumption and operational costs. When left ignored, fouling can lead to intensive maintenance and cleaning operations, where maintenance costs for cleaning and replacing fouled equipment can run into millions (Kazi, 2022). Figure 22. Fouling in Heat Exchangers Common mitigations used to control fouling in petrochemical industries include scale inhibitors, chemical additives, and manual mechanical and chemical cleaning (Fryer, 2021). These solutions were proven to prevent mineral deposits and help remove fouling, but they have limitations. Mechanical and chemical cleaning is commonly reactive rather than preventive. Effective corrosion mitigation methods are required to reduce the asset failure of billions of dollars annually. The United States hosts the largest refining capacity worldwide, with well over 18 million barrels of refined petroleum products daily. This action also increases the risk of wear and tear on the equipment, 36 decreasing its life span. Moreover, although preventive, chemical additives are selectively effective, especially in extreme conditions. One of the critical proposed solutions for fouling and scaling is using hydrophobic or oleophobic coatings, which reduces the adhesion of suspended particles that may build to equipment surfaces. Zhang et al. (2021) discussed that surfaces coated with these coatings had a decreased surface energy of approximately 18.5% to 45.3%, which further shows that these coatings reduce fouling sites and increase the surface's hydrophobicity, which also gives the surface a repellent and self-cleaning effect, which may diminish the regular need for maintenance and mechanical cleaning. 3. Environmental Contamination and Emissions Control The petroleum and petrochemical industries contribute significantly to environmental pollution in the form of emissions of greenhouse gases, volatile organic compounds (VOCs), and accidental emissions of toxic substances. In refining, gases that are not easily captured or processed are flared or vented in the routine operations of the industry, which translates into high levels of CO₂ and other toxicant emissions from the atmosphere (David & Niculescu, 2021). Besides gas emissions, refineries are also known to have spillages of oil and gas that may occur due to old infrastructure and lack of proper maintenance, thus damaging the environment gravely. Indeed, the petrochemical industry has been one of the primary causes of pollution in the Philippines, which serves as one of the key reason that the recent Mindoro oil spill caused by an oil tanker from Petron brought about severe damage to marine ecosystems and was detrimental to biodiversity and the lifestyle of coastal dwellers. Based on reports, this incident caused at least 41.2 billion pesos worth of damage to the coastal communities and even in the marine 37 environment of Oriental Mindoro, which is 800% higher compared to the initial estimate of the Center for Energy, Ecology, and Development (CEED) (Abrina, 2024). Figure 23. Oil Spill in Mindoro (February 2024) Technologies like flue gas desulfurization (FGD) and selective catalytic reduction (SCR) are used to reduce emissions of sulfur and nitrogen compounds. In response to oil spills like the one in Mindoro, a combination of traditional methods, such as booms, skimmers, and dispersants, are typically deployed, which are the industry standards for containing and cleaning up oil spills. However, these traditional methods are highly dependent on the sea's condition and are effective if the conditions are calm, but they are less effective in rough waters. Also, the effectiveness of these methods decreases as oil spreads over a large area, specifically manual cleanup, which only recovers 10-15% of spilled oil even with extensive actions. To address these countless problems, petrochemical industries can adopt technologies and artificial intelligence using drones with infrared cameras, AI-driven algorithms, and remote sensing technologies, which may improve leak and oil spill early detection and monitoring. In gas emissions, Carbon capture and storage can be adopted, 38 which has been proven to capture up to 90% of CO₂ emissions from petrochemical plants, thus averting them from reaching the atmosphere. 4. Production Bottlenecks To define, bottlenecks are points in the production process where throughput can be improved, so they naturally slow these points down and reduce the plant's overall efficiency. It can happen in distillation columns, catalytic cracking units, or material handling systems in a refinery. In general, the two standard reasons are underperformance and supply chain disruptions. Cases of bottlenecks in catalytic cracking units-the beating hearts of refineries have reduced the capacity of the entire refinery by 15%, delayed shipments, and increased costs in a time when demand is high, which has caused considerable financial losses and a cascading effect on regional fuel prices, pointing out how inefficiencies in such production are critical. Bottlenecks are economically significant because, at times, they can halt or slow production and translate into huge losses in revenue. According to Barone (2023), bottlenecks would also mean erosion of 20% of the plant's overall efficiency, which meant millions of dollars that would have been accounted for in terms of profit. The need for mitigation, therefore, is enormous. The primary ways to mitigate bottlenecks are equipping process improvement, and scheduled maintenance. For instance, most refineries try to counter blockages by increasing the reactors or replacing the old distillation columns. In most cases, however, these countermeasures have to play catch-up because of the nature of interacting systems. According to TOC, removing a single bottleneck might increase production in the short term but only promise long-term success if the system is 39 optimized. In addition, upgrades can be overly expensive and take months or years to implement, thus causing a protracted disruption of operations. Advanced solutions grounded in technology and data analytics are becoming essential to tackle production bottlenecks more effectively. One such approach is Advanced Process Control (APC), which uses real-time data and algorithms to optimize process variables such as temperature, pressure, and flow rates (Heinrich & Abernethy, 2018). According to studies in Industrial & Engineering Chemistry Research, the refineries using APC have experienced up to 25% increase in throughput while at the same time dramatically minimizing process variability, ensuring smooth operations and conditions (Symestic, 2022). It works on the real-time adjustment of system performance, keeping a close watch on its performance and instantly correcting small inefficiencies before they develop into significant bottlenecks. Supply chain optimization is another critical area in mitigating production bottlenecks, which is less technical than the other solutions (Katsaliaki & Kumar, 2021). Further improvement in the availability of material and avoidance of associated bottlenecks can be contributed by the application of predictive analytics in predicting demand and by understanding logistics in the supply chain. According to Accenture, a 20% rise in operational efficiency and reduction of lead time can be achieved through predictive analytics supply chains where raw materials arrive in time for production without any delay or excess inventory. 40 IV. Product and/or Process Innovations Indeed, innovation is one of the predominant advancements that a company can achieve as a gateway to the growth of the business. In the process of innovating a business, there can be challenges involved, however the payoffs are high for those companies that make this as their core priority. As a matter of fact, petroleum and petrochemical companies have always been at the forefront of technological innovations, pursuing for more ways to improve efficiency, safety, and sustainability. Hence, listed here are the top process innovations that the petroleum and petrochemical industries implemented: Petroleum Advance Seismic Imaging For the past decades, seismic imaging has been utilized in the petroleum industry. Its purpose is to characterize subsurface properties and structures of geological formations, which helps in identifying Dense Nonaqueous Phase Liquids (DNALPs). Although, the recent advancement of it has revolutionized the industry in properly locating and extracting hydrocarbon supplies. As a result, high-resolution 3D seismic imaging techniques integrated into artificial intelligence algorithms were discovered to contribute to more precise imaging of subsurface structures and properties. Furthermore, this also diminishes the risk exploration dangers that may be faced by the employees, which leads to the increasing success rate of drilling operations. According to Prismecs (2024), the demand for seismic services is expected to increase by 14% or 1.1 billion dollars for almost 9.3 billion dollars as exploration activities also increase. 41 Digital Oilfield Solutions Similar to advanced seismic imaging, digital oilfield solutions also incorporate technologies, including the Artificial Intelligence (AI) and the Internet of Things (IoT) to evaluate and optimize real-time production-related information in the field (Prismecs, 2024). This idea may aid in the monitoring of inaccessible regions, promote production efficiency, and fine-tune equipment performance. This offers a wide array of advantageous commercial significance, like cost reduction and operational efficiency gains. Enhanced Oil Recovery (EOR) Techniques Since the world is now experiencing climate change, oil reserves are also at risk, making the petroleum industry to shift in the enhanced oil recovery (EOR) techniques. With this, different innovations were discovered, such as steam injection, which was proven to be the foremost enhanced oil recovery method, polymer flooding, and microbial enhanced oil recovery, which provided outstanding results in extending the economic life of mature reservoirs and improving production rates. In line with this, EOR can not only aid in improving production rates but can also aid businesses wanting to optimize the return on their current investments by creating attractive commercial prospects. Renewable Energy Integration Since petroleum industries promote innovations, it is also essential to encourage them while increasingly integrating renewable energy resources to respond to growing environmental issues, such as reducing carbon footprint and enhancing sustainability. One innovation that has impacted the environment was the alteration of solar-powered 42 wellheads to wind-driven offshore platforms. According to Prismecs (2024), inaugurating the hybrid energy systems (HES) can play a vital role in the innovation of the petroleum industry. This idea can not only reduce in the release of greenhouse gas emissions but also can generate new revenue streams (Prismecs, 2024). Petrochemical Circular Economy and Resource Recovery As the world progresses, embracing innovations in various companies would be beneficial in remaining sustainable and competitive in the industry. Therefore, transitioning into a circular economy would be one of the ways a company must implement this since it will aid in maximizing resource efficiency while minimizing waste and promoting the reuse, recycling, and recovery of materials. In this instance, the petrochemical industry may help create closed-loop systems that recycle plastics, extract valuable chemicals from waste streams, and use byproducts for further uses. Hence, this will greatly reduce cost production as it will promote in recycling materials that will also be beneficial in protecting the environment. Figure 24. Circular Economy Model 43 Green Chemistry and Sustainable Manufacturing To continue about protecting the environment, green chemistry is one of the innovations that can be implemented by the companies as this will center on developing chemical processes and products that conserve resources and minimize environmental impact. If this innovation will be implemented in the industry, it will lead to an eco-friendly products, renewable feedstocks, and energy-efficient manufacturing processes. Biobased Chemicals and Renewable Feedstocks As it has been evidently known, petrochemical companies rely on fossil fuels as their main source of feedstock. Since fossil fuels have been continually depleted throughout the years, which must be faster than the new ones being made available, it is acceptable to shift to biobased chemicals and renewable feedstocks because these serve as alternatives to fossil fuels-derived raw materials in the industries. Furthermore, the industry should also focus on recognizing biorefinery platforms and biotechnologies enabling the production processes to greener, more sustainable products. Digital Transformation and Industry Entering into a generation of technology, it is advantageous if the innovation of a company is also integrated into the world of technology, involving Artificial Intelligence (AI), Internet of Things (IoT), big data analytics, and advanced automation (Prismecs, 2024). By using these technologies, companies can enhance efficiency, productivity, and safety inside the manufactory. Considering this, digital simulations will play an important role in enabling companies in optimizing their chemical processes, that will lead to a faster and easier innovation process. 55