Petrochemicals & Petroleum Refining Technology PDF
Document Details
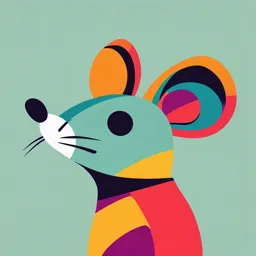
Uploaded by SubstantiveAutoharp
Tags
Related
- Introduction to Petroleum Refining PDF
- Introduction To Petroleum Refining PDF
- Petrochemical & Petroleum Refining Technology - c5.pdf
- Petrochemical & Petroleum Refining Technology PDF
- Fundamentals of Refining and Petrochemical Engineering (RP 170) 2022 PDF
- Fundamentals of Refining and Petrochemical Engineering (RP 170) 2022 PDF
Summary
This document discusses petrochemical and petroleum refining processes, focusing on refining technology and conversion methods. It details the process of changing the size and structure of hydrocarbon molecules through decomposition, unification, and alteration. The document also explains catalytic reforming, highlighting its role in increasing gasoline octane ratings.
Full Transcript
Petrochemicals & Petroleum Refining Technology The Refining Process (Conversion : Alteration-Catalytic Reforming) THE REFINING PROCESS Change the size and/or structure of hydrocarbon molecules 1. Decomposition (dividing) - thermal & catalytic cracking 2. Unificati...
Petrochemicals & Petroleum Refining Technology The Refining Process (Conversion : Alteration-Catalytic Reforming) THE REFINING PROCESS Change the size and/or structure of hydrocarbon molecules 1. Decomposition (dividing) - thermal & catalytic cracking 2. Unification (combining) - alkylation & polymerization 3. Alteration (rearranging) - isomerization & catalytic reforming CATALYTIC REFORMING Introduction Demand for high octane gasolines for today’s automobiles Catalytic Reforming Catalytic reformate furnishes approximately 30-40% of the US gasoline requirements Catalytic reforming primarily increases the octane number rather than increasing the yield Decreases in yield may occur because hydrocracking reactions may involved Feedstocks: - Heavy straight run (HSR) gasoline and naphtha (82- 190oC) - Heavy hydrocracker naphthas In catalytic reforming, HC molecular structures are rearranged to form higher octane aromatics Typical feedstocks & reformer products have the following PONA analysis (vol %) Paraffins & naphthenes undergone: - Cyclization Convert into higher octane - Isomerization components CATALYTIC REFORMING Catalytic reforming is an important process used to convert low-octane naphthas into high-octane gasoline blending components called reformates CATALYTIC REFORMING Reformate is a high octane, low sulfur, blending component used in the production of gasoline. Reformates Reformate has a high aromatic content and is commonly used as a feedstock to an aromatics complex producing benzene, toluene and xylene. Steam Cracking & Catalytic Reforming THE REFINING PROCESS CONVERSION CATALYTIC REFORMING Light Naphtha to Gasoline Blending Pool Naphtha Crude Oil Naphtha Splitter Hydrogen Catalytic Atmospheric Reformer Distillation High Octane Reformate, to Gasoline Blending Pool CATALYTIC REFORMING Purpose To enhance aromatic content of naphtha Feed stocks to aromatics complex Improve the octane rating for gasoline Produces H2 (dehydrogenation) use as cooling gas in Alkylation unit CATALYTIC REFORMING Reactions Dehydrogenation — removal of hydrogen from cycloparaffins (naphthenes) to form aromatics » Aromatics provide octane enhancement of gasoline feedstocks Reactions Paraffins are converted to branched isoparaffins Isoparaffins Paraffins (branched) Cycloparaffins AROMATICS Some of these isoparaffins are reacted to cycloparaffins that are subsequently reacted to aromatics THE REFINING PROCESS CONVERSION 4 major reactions during reforming: 1. Dehydrogenation of Naphthenes to Aromatics 2. Dehydrocyclization of Paraffins to Aromatics 3. Isomerization 4. Hydrocracking Dehydrogenation Reactions Dehydrogenation of alkylcyclohexanes to Dehydrocyclization of paraffins to aromatics (highest reaction rates aromatics compared to others) 1. Endothermic reaction 2. Need heat, decrease in T as the reaction Dehydroisomerization of alkylcyclopentanes progressed to aromatics Conversion of aromatics increases the gasoline end point because the boiling points of aromatics are higher than the boiling pt of paraffins & naphthenes The yield of aromatics is increased by: - High T ( kinetic rate) - Low P - Low space velocity (promote the approach of equilibrium) - Low hydrogen/HC mole ratios (sufficient H2 partial pressure must be maintained to avoid coke formation) Isomerization Reactions n-hexane isohexane Isomerization of normal paraffins to isoparaffins Isomerization of alkylcyclopentanes to cyclohexanes plus subsequent conversion to benzene Isomerization yield is increased by: 1. High T (increases reaction rate) 2. Low space velocity 3. Low pressure Hydrocracking Reactions The major hydrocracking reactions involve the cracking & saturation of paraffins Hydrocracking yields are increased by: 1. High T 2. High P 3. Low space velocity Reforming processes are classified as - Continuous - Cyclic - Semiregenerative Depending upon the frequency of catalyst regeneration The equipment for the continuous process is designed to permit the removal & replacement of catalyst during normal operation. As a result, the catalyst can be regenerated continuously & maintained at high activity The semiregenerative unit has the advantage minimize capital cost catalyst can be replaced when the unit is still on-stream Continuous Catalyst Regeneration (CCR Platforming) EXPENSIVE -catalyst regenerated continuously Continuous Catalyst Aged catalyst in the reactors is continuously replaced with Regeneration (CCR catalyst that has been freshly Platforming) regenerated in an external regenerator (CCR regenerator) to maintain fresh catalyst performance. Semiregenerative Process -LOW COST -high H2 recycle rate & high operating P (1.3 to 3.0 MPa) to minimize coke lay down to minimize consequent loss catalytic activity Semiregenerative Process The semiregenerative has the advantage of minimum capital costs Regeneration requires the unit to be taken off-stream Depending upon severity of operation, regeneration is required at intervals of 3 to 24 months High hydrogen recycle rates and operating pressures are utilized to minimize coke laydown and consequent loss of catalyst activity Semiregenerative Fixed Bed Process Cyclic Process Catalyst can be regenerated without shutting down the unit Having a swing reactor along with other reactors When the activity of the catalyst in one of the on-stream reactors drop below the desired level, this reactor is isolated from the system and replaced by the swing reactor containing freshly regenerated catalyst The catalyst is regenerated by admitting hot gas containing 0.5% oxygen into the reactor to burn the carbon off the catalyst Reforming Catalyst Bifunctional catalyst that is capable of rearranging and breaking long chain HCs as well as removing hydrogen from naphthenes to produce aromatics Catalyst activity is reduced during operation by coke deposition & chloride loss Activity of catalyst can be replaced by high-T oxidation of carbon followed by chlorination or referred as semi-regenerative Semiregenerative is able to operate for 6 to 24 months between regenerations THANK YOU CATALYTIC ISOMERIZATION ISOMERIZATION Transformation of one molecular structure into another (isomer) whose component atoms are the same but arranged in a different geometrical structure Pt catalyst ISOMERIZATION N-hexane 2,2-dimethylbutane RON =25 RON =92 ISOMERIZATION Isomerisation offers the possibility of converting less desirable compounds into isomers with desirable properties, in particular to convert n- paraffins into iso-paraffins, thereby increasing the octane of the hydrocarbon stream. ISOMERIZATION Isomerization of n-butane to i-butane Additional feedstock for alkylation unit ISOMERIZATION Isomerization of pentane/hexane into its isomers N-pentane N-hexane RON = 62 RON =25 2-methylbutane 2,2-dimethylbutane RON = 92 RON =92 ISOMERIZATION Isomerization Catalyst Low T process: Aluminium chloride + hydrogen chloride High T process: Platinum or other metal Dual function catalyst Isomerization Reactors ISOMERIZATION Feed is dried, desulfurized, add chloride and H2 benzene and olefins are paraffins are hydrogenated catalytically isomerized to isoparaffins Neutralized/ acid stripped Recycle gas stream Liquid stream (isomerate) Schematic of C5 and C6 isomerization THANK YOU Thermal and Catalytic Cracking (Conversion : Decomposition) Catalytic Hydrocracking Unit Change the size and/or structure of hydrocarbon molecules 1. Decomposition (dividing) - thermal & catalytic cracking 2. Unification (combining) - alkylation & polymerization 3. Alteration (rearranging) - isomerization & catalytic reforming Decomposition (Dividing) Cracking processes: Break down heavier hydrocarbon molecules (high boiling point oils) into lighter products such as petrol and diesel. CRACKING CRACKING Notice the double bonds formed CRACKING Thermal cracking Free radicals formed CRACKING CRACKING An initiation reaction - homolysis of a carbon-carbon bond (only spontaneous at high temperatures). Homolysis is where the bond breaks so that each fragment has one electron CRACKING THERMAL CATALYTIC - High T,P -Low T,P +catalyst Thermal Cracking Steam Coking Visbreaking Steam High temperature steam (1500°F/816° C) is used to break ethane, butane and naptha into ethylene and benzene, which are used to manufacture chemicals. Coking is a severe thermal cracking. Residual from the distillation tower is heated about 475°C to 520°C. It is then charged to the product fractionator for separation into naphtha, diesel oils, and heavy gas oils for further processing in the catalytic cracking unit When the process is done, a heavy, almost pure carbon residue is left (coke); the coke is cleaned from the cokers and sold. Visbreaking Residual from the distillation tower is heated (900 ° F / 482 ° C), cooled with gas oil and rapidly burned (flashed) in a distillation tower. This process reduces the viscosity of heavy weight oils and produces tar. Typically convert about 15 percent of the feedstock to naphtha and diesel oils and produce a lower-viscosity residual fuel. 1. STEAM CRACKING Petrochemical process Produce olefinic raw materials (ethylene,benzene) Feed – ethane, butane,naphta Process: High T : 1500°F/816°C (steam) Pressure: slightly higher than atmospheric pressure The market demand for heavy residual fuel oils has been decreasing Coking units convert heavy feed stocks to other refinery units for conversion into higher value products To eliminate essential volatile matter, coke calcined at 2000-2300oF (900-1300° C) Pressure: slightly higher than atmospheric pressure Convert heavy feed stocks into solid coke & lower boiling point HC products Feed stocks to other refinery units –convert higher value fuels Coke formed : 1) contained some volatile matter/ higher boiling pt HC (incomplete carbonization reaction) 2) contained sulfur content 0.3-1.5 wt % 3) in vessel--easily removed Advantages: 1) Reduced coke formation on cracker catalyst and increase the cracking process 2) Reduced yield of low price residual fuel 3) Reduced metal content of the catalytic feedstocks Undesirable Fuel Manufacture of anodes for electrolytic cell reduction of alumina Direct use as chemical carbon source for manufacture of elemental phosphorus, calcium carbide and silicon carbide Manufacture of electrodes for usage in electric furnace production of elemental phosphorus, titanium dioxide, calcium carbide and silicon carbide 3 Types of Coking Process: i) Delayed Coking ii) FlexiCoking iii) Continuous Coking/ Delayed Coking Unit Fluid coking Delayed Coking Developed to minimize refinery yields of residual fuel oil by severe thermal cracking of stocks. Feed: VDU/ADU Residue Operating conditions: Furnace: 900°-950°F (480 – 510°C) , 25-30 psi (1.7 to 2 atm) Delayed: 24 hours Coke drums: 25-75 psi Hydraulic System Delayed coking is a semi-continuous operation - feed is introduced continuously, but coke is recovered intermittently (~24 hours to fill one drum, then switch the feed to fill the other drum) Schematic Diagram of Delayed Coking ARCO/LA Refinery Coker Unit A 4-drum delayed coking unit in a petroleum refinery Delayed coking, two or more large reactors, called coke drums, are used to hold, or delay, the heated feedstock while the cracking takes place. Coke is deposited in the coke drum as a solid. This solid coke builds up in the coke drum and is removed by hydraulically cutting the coke using water. In order to facilitate the removal of the coke, the hot feed is diverted from one coke drum to another, alternating the drums between coke removal and the cracking part of the process FlexiCoking Thermally converts heavy oils (such as vacuum resid, atmospheric resid, oil sands bitumen, heavy whole crudes, deasphalter bottoms, or FCC bottoms) to lighter more valuable products. Coking and gasification process fully integrated Reactor Coker heater Fluidized bed reactor Gasifier Schematic Diagram of FlexiCoking Flexi-coking, as a variation of fluid coking, provides the options of partial or complete gasification of the coke product to produce a fuel gas with some or no coke in the product slate. Different from the bulk liquid-phase coking in delayed coking, flexicoking takes place on the surface of circulating coke particles of coke heated by burning the surface layers of accumulated coke in a separate burner. 1) Feed (565°C-plus vacuum resid) enters the scrubber for integrated direct contact heat exchange with reactor overhead effluent vapors. 2) The scrubber condenses higher boiling hydrocarbons in the reactor effluent (525°C) and recycles these along with the fresh feed to the reactor. 3) Lighter overhead vapors are sent to conventional fractionation and light ends recovery. 4) In the reactor, feed is thermally cracked to a full range of liquid products and coke. 5) Coke inventory is maintained by transferring bed coke from the reactor to the heater via a transfer line. 6) Hot coke from the heater is circulated back to the reactor (through coke transfer line), supplying the heat necessary to maintain reactor temperature and to sustain thermal cracking reactions. Excess coke is sent to the gasifier where the coke reacts with air and steam to produce a clean fuel gas (Flexigas) boilers and furnaces, backing out purchased fuel gas. 7) Approximately 97% of the coke generated in the reactor is consumed in the process, with a small amount of product coke recovered from the fines system Continuous Coking/Fluid Coking Converts heavy residual crude into lighter products such as naphtha, kerosene, heating oil, and hydrocarbon gases. The "fluid" term refers to the fact that coke particles are in a continuous system versus older batch-coking technology. Simplified version of Flexicoking - Reactor - Burner Schematic Diagram of Continuous Coking Fluid coking, the feed is charged to a heated reactor The cracking takes place, and the formed coke is transferred to a heater as a fluidized solid where some of it is burned to provide the heat necessary for the cracking process. The remaining coke is collected to be sold. 1. Only enough coke is burned to satisfy the heat requirements of the reactor and the feed preheat. 2. 20-25% of coke produced in the reactor. 3. Balance of the coke is withdrawn from the burner vessel & is not gasified as it is in flexicoker. Temperature higher than delayed coking Feedstock + hot coke particles Reactor : 50 psi Gases + vapors-quenched-fractionated Coke : removed, recycled Decoking Operation 1. Mechanical Drill 2. Hydraulic System - Uses high pressure water jet (2000 psig) - High Pressure cuts the coke into lumps, drop into bottom of drum, collected 3. Chipping - cutting bit repeatedly transferred back and forth from top to bottom as the hydraulic bit rotates Chipping https://www.youtube.com/watch?v=fpyTdlziAZs 3. Visbreaking Non-catalytic process Mild thermal cracking operation (heating in furnace) Objectives: Lowers viscosity of heavy residueproduce light HC (LPG, gasoline) Reduce pour point of waxy residues Reduce production of heavy fuel oils from 20-35% Gas oil produced: Used to increase catalytic cracker feed Used to increase gasoline yields Visbreaking Feed: ADU/VDU Residue Operating conditions: Furnace: 800-950 F (400-500°C) - Mild conditions Visbreaking is a mild form of thermal cracking, with primarily aim to lower the viscosity of vacuum residues. Two visbreaking processes are available: the coil or furnace type and the soaker type. Visbreaking Process Visbreaker Tarfurther refined by feeding it to a vacuum fractionator Additional heavy gas oil may be recovered and routed either to catalytic cracking, hydrocracking or thermal cracking units on the refinery. The vacuum-flashed tar (pitch) is then routed to fuel oil blending. Visbreaker tar routed to a delayed coker for the production of certain specialist cokes such as Schematic Diagram of Visbreaker anode coke or needle coke. Visbreaker operations Coil & Furnace Soaker cracking cracking Coil/ Furnace Cracking Soaker Cracking Reaction 473-500°C 427-443°C Temperature lower energy consumption Reaction times 1-3 minutes Longer reaction times Soaking drum Running time 3-6 months 6-18 months Pressure Up to 5200 kPa Fuel consumption 80% of the operating cost 30-35% lower than furnace Objectives: To convert heavy oils into more valuable gasoline and lighter products of higher octane number along with the production of coke deposited over the catalyst particles. Most important & widely used refinery process Heavy Oils Heat ,Pressure, Catalyst Valuable products (higher octane & light gases) + Coke on catalyst surface (lower its activity) To maintain the catalyst activity : Regenerate the Catalyst ( burning off the coke with air) Reactor Regenerator Fluidized Catalytic Cracker Catalytic cracking in use today can be classified as: a) Moving bed (Thermafor Catalytic Cracking process) b) Fluidized bed (Fluid Catalytic Cracker) The hot oil feed is contacted with the catalyst in either the feed riser line or the reactor. Cracking reaction progresses, the catalyst is progressively deactivated by the formation of coke. The catalyst & HC vapors are separated mechanically & oil remaining on the catalyst is removed by steam stripping before the catalyst enters the regenerator. The oil vapors are taken overhead to a fractionation tower for separation into streams having the desired boiling ranges. The spent catalyst flows into the regenerator and is reactivated by burning off the coke deposit. Regenerator temperatures are controlled by CO2/CO ratio. The flue gas and catalyst are separated by cyclone separator & ESP. The catalyst is stripped as it leaves the regenerator to remove adsorbed O2 before the catalyst is contacted with the oil feed. Feedstocks: straight – run gas oil vacuum gas oil atmospheric residue heavy ends (coker gas oil, DAO) vacuum residue Pretreatment: 1. Reduced sulfur & nitrogen 2. Increased production of naphtha & LCO yield Types of pretreatment: Deasphalting – to prevent excessive coking on catalyst surfaces Demetallation (Ni, V) – prevent catalyst deactivation Hydrocracking – to prevent excessive coking FCC employs a catalyst in the form of very fine particles (~70 microns) which behave as fluid when aerated with a vapor. The fluidized catalyst circulated continuously between the reaction zone (reactor) and the regeneration zone (regenerator). 2 basic types of FCC units: a) “Side by side” : reactor & regenerator are separate vessels adjacent to each other b) “Orthoflow” (Stacked type) : reactor is mounted on top of the regenerator Side by side Orthoflow Side by side Side by side Orthoflow Reactions: Products in catalytic cracking are the results of 1. Primary reaction 2. Secondary reaction Primary reaction: Carbon-carbon bond scission & neutralization of the carbonium ion Paraffin paraffin + olefin Alkyl naphtene naphtene + olefin Alkyl aromatic aromatic + olefin Reactions: Catalyst: A substance added to a chemical reaction that facilitates or causes the reaction but when the reaction is complete the catalyst comes out just like it went in. In other words, the catalyst does not change chemically. It causes reactions between other chemicals Catalyst : i) Acid-treated natural aluminosilicate ii) Amorphous synthetic silica alumina combinations iii) Crystalline zeolites @ molecular sieves Zeolite Hydrorefining Catalyst Higher activity Higher gasoline yields Gasoline production contained larger % of paraffinic and aromatic content Lower coke yield Increased isobutane production Higher conversions Catalyst: Commercial :Zeolite (USY zeolite) - higher activity - higher gasoline - lower coke yield - lower costs & make up rates compared amorphous Zeolite Fluidized Catalytic Cracker Fluidized Catalytic Cracker (FCC) FCC Cyclone FCC Regenerator (located in the reactor) Catalytic Cracker at ExxonMobil's Oil Refinery Cracking Phenomena: Formation of coke Formation of smaller molecules Smaller naphtenic+aromatic+olefins formed Cracking of large molecules Producing full range of HC Fluidized Catalytic Cracker (FCC): - Reactor/Riser - Catalyst - Regenerator - Fractionator Regenerator Materials and energy balances are required for both the fluid, which occupies the interstitial region between catalyst particles, and the catalyst particles, in which the reactions occur Fractionator Yield 4 11 5 6 3 10 8 2 1 7 9 Catalytic cracker. The feedstock of long-chain hydrocarbons (1) is mixed with hot catalyst (2) and vaporized. The vapor/powder mixture is carried to the reactor where the cracking reactions occur. Cyclones (3) extract the cracked hydrocarbon vapor and pass it to the fractionating column where it is fractionated, yielding petroleum gases and gasoline (4), light gas oil (5), medium gas oil (6), and heavy gas oil (7). Spent catalyst meanwhile is mixed with steam (8) and carried in a current of hot air (9) to the catalyst regenerator where it is cleaned and recycled (10. Waste gases are drawn off (11) and vented THANK YOU Objective: To convert heavy oil feedstock into high quality, lighter fuel products (gasoline, naphtha, kerosene, diesel, hydrowax) which can be used as petrochemical plant feedstock @ lube basestock Reasons 1. Demand for petroleum products has shifted to high ratios of gasoline and jet fuel compared usage of diesel fuel and home heating oils 2. By product hydrogen at low cost and large amounts 3. Limiting sulfur & aromatic compound in motor fuels have increased 1. Better balance of gasoline & distillate production 2. Greater gasoline yield 3. Improved gasoline octane quality & sensitivity 4. Production of relatively high amounts of isobutane in the butane fraction Mechanism of hydrocracking is superimposed of catalytic cracking & hydrogenation Catalytic cracking is the scission of a carbon-carbon single bond Hydrogenation is the addition of hydrogen to a carbon-carbon double bond endothermic exothermic Cracking & Hydrogenation are complementary Cracking provides olefins for hydrogenation Hydrogenation provides heat for cracking Overall reaction provides excess heat quenching unit Two-stage Hydrocracker All hydrocracking & hydroprocessing processes in used today are fixed bed catalytic processes with liquid downflow. Hydrocracking process may require either one or two stages depending upon the process and the feed stocks used. Petrochemical & Petroleum Refining Technology The Refining Process (Conversion : Unification-Alkylation) THE REFINING PROCESS Change the size and/or structure of hydrocarbon molecules 1. Decomposition (dividing) - thermal & catalytic cracking 2. Unification (combining) - alkylation & polymerization 3. Alteration (rearranging) - isomerization & catalytic reforming THE REFINING PROCESS UNIFICATION Processes to make gasoline components from materials that are too light to otherwise be in gasoline Alkylation Polymerization Cracking + Polymerization + Alkylation = Gasoline yield representing 70 percent of the starting crude oil. Alkylation In alkylation, small molecules produced from other processes are recombined in the presence of a catalyst. Chief sources of olefins are catalytic cracking and coking operations Most common olefins used: butene and propene, sometimes pentene included The product can be made to fall within the gasoline boiling range with MON from 88-94 & RON from 94-99 Alkylation Combination of low molecular weight olefins (propylene and butylene) with an isoparaffin (isobutane) in the presence of a catalyst (sulfuric acid or hydrofluoric acid) to form higher molecular weight isoparaffins. Isoparaffin Olefins HF /H2SO4 Isoparaffins (Isobutane) (Propylene/Butylene) (ALKYLATE) By products: 1. Polypropylene (polymerization of propylene) – lower product octane & increase acid consumption 2. Ester (reaction with H2SO4 ) – very corrosive, require treatment ALKYLATE Excellent blending MON 90-95 component for gasoline RON 93-98 Alkylation Reaction Isobutane is normally used in Alkylation process…WHY? Isobutane has a sufficiently high octane number and low vapor pressure to allow it to be effectively blended directly into finished gasoline. Process using sulfuric acid as a catalyst is much more sensitive to T than hydrofluoric acid process. With Sulfuric Acid it is necessary to carry out the reactions at 40-70oF (5-21oC) or lower minimize oxidation reduction reactions… Hence, will result in the formation of tars, sulfur dioxide, ester When anhydrous hydrofluoric acid is the catalyst, the temperature usually limited to 100oF (38oC) or below. The volume of acid employed is about equal to that of the liquid HC charge & sufficient P is maintained on the system to keep the HC & acid in the liquid state. High isoparaffin/olefin ratios (4:1 to 15:1) are used to : minimize side reaction polymerization (reduce by product) to increase product octane number. Efficient agitation: to promote contact between the acid and HC phases is to obtain high product quality & yields. The yield, volatility & octane no. of the product is regulated by adjusting the temperature, acid/HC ratio & isoparaffin/olefin ratio. In practice however, the plants are operated at different conditions & the products will be different Important variables in alkylation unit: Reaction temperature Acid strength & Composition Isobutane concentration Olefin type (ratio of butylene/propylene) Olefin space velocity Alkylation Reaction Reaction of isobutane with an olefin to form a high molecular weight isoparaffin Alkylate The olefin used is butylene and propylene, which combines with isobutane to yield iso-octane and isoheptane. Alkylation Reaction Another significant reaction of propylene alkylation is: Propylene + Isobutane Propane + Isobutylene Isobutylene + Isobutane 2,2,4-trimethylpentane (isooctane) HF /H2SO4 HF /H2SO4 Alkylation Chemistry Alkylation Chemistry Alkylation Sulfuric Acid Alkylation Unit Reaction Variables 1. Reaction Temperature Greater effect in Sulfuric Acid processes than Hydrofluoric Acid Low T (-4 to 20oC) for Sulfuric Acid: higher quality where the octane number may increase from one to three (depending on efficiency of mixing in reactor) Higher T for Sulfuric Acid may affect the decreased of octane number In Hydrofluoric acid alkylation, T range is 21-38oC Higher T for Hydrofluoric acid may degrades the quality about three octane number Sulfuric acid alkylation : low T caused the acid viscosity to increase, uniform mixing & separation of emulsion will be difficult. T>21oC : polymerization of the olefins is increased, yields are decreased. Normal sulfuric acid reactor T is from 5oC to 10oC Max T: 21oC Min T: -1oC Reaction Variables 2. Acid Strength & Composition Alkylate quality depends on the effectiveness: a) reactor mixing b) water content of the acid In Sulfuric Acid Alkylation: the best quality & highest yields are obtained with acid strengths:93-95% 1-2% water (remainder HC diluents) In hydrofluoric acid alkylation, acid strength of 86-90% with less than 1% water to get the highest octane number Acid Strength & Composition The water concentration and HC diluents in the acid lowers its catalytic activity thus an 88% acid containing 5% water is less effective than 88% acid containing 2% water. Poor mixing efficiency, higher acid strength is required Increase acid strength 89-93% by weight increases alkylate quality by 1-2 octane numbers. Reaction Variables 3. Isobutane Concentration Expressed in terms of isobutane/olefin ratio High isobutane/olefin ratios: increase octane number & yield reduce side reactions & acid consumption In industrial practice the isobutane/olefin ratio on reactor charge varies from 5:1 to 15:1 Reaction Variables 4. Olefin Space Velocity (SV) Defined as volume of charged per hour divided by the volume of acid in the reactor SV = Olefin in Reactor (bbl/hour) Acid in Reactor (bbl) Schematic Diagram of Sulfuric Acid Alkylation Process Olefin Space Velocity Lowering the olefin space velocity : reduces the amount of high boiling HC produced increases the product octane number lowers acid consumption Olefin space velocity is one way of expressing reaction time Contact time : Residence time of the fresh feed & externally recycled isobutane in the reactor. HF acid alkylation : 5-25 minutes Sulfuric acid alkylation : 5-40 minutes Correlating factor, F The relationship is predicted based on a formula of a correlating factor, F: This formula is useful in predicting trends in alkylate quality The higher the value of F better the alkylate quality Normal values of F: 10 99.3% not generally used Catalyst ~ Sulfuric acid : Sulfuric Plants for Butylene ~ Hydrofluoric acid : Hydrofluoric Plant for Propylene High octane alkylate gasoline Catalyst Alkylation Sulfuric (catalyst) plant is more favorable: ~ Butylene preferred Produces the highest iso-octane levels Resulting Research Octane Numbers of 93-95 (with isobutane) RON and MON are about equal for alkylation Amounts of butylene consumed per alkylate produced is the lowest Side reactions are limited ~ Propylene less preferred » Octane numbers are low (89-92 RON) » Propylene & acid consumption are high Alkylation Reactor Alkylation ~ Acid settler - separator - acid drawn off bottom – recycled ~ Caustic Scrubber - neutralizes Hydrocarbon - using caustic solution (NaOH) HF Alkylation Unit 2.0 THE At the end of this chapter, you should be REFINING able to: 1. Justify the importance of major steps involved in refining process PROCESS 2. Explain the basic refining process ExxonMobil oil refinery in Baton Rouge (the second-largest in the United States) Anacortes Refinery (Tesoro), on the north Fire-extinguishing operations after end of March Point southeast of Anacortes, the Texas City refinery explosion. Washington Exxonmobil explosion at Refinery Plant, Torrance USA (18 Feb 2015) Electrostatic precipitator (ESP) which reduces fluid catalytic cracker (FCC) particulates, exploded as contract workers were doing maintenance on the nearby FCC REFINERY Refining Processing of one complex mixture of hydrocarbons into products that have consumers value It relies on a basic difference between chemicals - boiling points Crude Oil Tank Farm THE REFINING PROCESS PRE-TREATMENT THROUGH DESALTING TREATMENT BLENDING REFINING CONVERSION SEPARATION CRUDE OIL PRE-TREATMENT PROCESS & SEPARATION PROCESS The Refining Process (Pre-Treatment & Separation) THE REFINING PROCESS Desalter Crude preheat Train ADU &VDU CRUDE OIL PRE-TREATMENT THE REFINING PROCESS TREATMENT Prepare hydrocarbon streams for additional processing and to prepare finished products. Treatment may include the removal or separation of aromatics and naphthenes as well as impurities and undesirable contaminants THE REFINING PROCESS TREATMENT PROCESS Desalting (pre-treatment) Drying Hydrodesulfurizing Solvent refining Sweetening Solvent extraction Solvent dewaxing. Desalter Hydrodesulfurization Unit Solvent Dewaxing Unit CRUDE OIL PRETREATMENT Crude Oil often contains : Water Inorganic salts Suspended solids Water-soluble trace metals CRUDE OIL PRETREATMENT Desalting (dehydration) to remove salts, solids & formation of water from unrefined crude oil to reduce corrosion, plugging, and fouling of equipment to prevent poisoning the catalysts in processing units Desalter CRUDE OIL PRETREATMENT Crude Oil Desalting : 1. Chemical 2. Electrostatic 3. Filtering *Use hot water as the extraction agent CRUDE OIL PRETREATMENT Chemical Desalting Water and chemical surfactant (demulsifiers) are added to the crude, heated so that salts and other impurities dissolve into the water or attach to the water, and then held in a tank where they settled out CRUDE OIL PRETREATMENT Electrostatic Desalting Emulsified Oil & water being introduced to high voltage AC electrical field Action of electrical field causes the emulsified droplets suspended in the oil become polarized, coalesce into larger droplets & separated by gravity settler Surfactants are added only when the crude has a large amount of suspended solids. CRUDE OIL PRETREATMENT Electrostatic Desalting CRUDE OIL PRETREATMENT Filtering Filtering heated crude using diatomaceous earth as a filtration medium CRUDE OIL PRETREATMENT Preheating The feedstock crude oil is heated to between 150° and 350°F - reduce viscosity and surface tension for easier mixing and separation of the water CRUDE OIL PRETREATMENT Ammonia - to reduce corrosion. Caustic or acid - to adjust the pH of the water wash THE REFINING PROCESS BLENDING Mixing and combining hydrocarbon fractions, additives, and other components to produce finished products with specific performance properties. THE REFINING PROCESS Atmospheric Distillation Unit (ADU) Vacuum Distillation Unit (VDU) THE REFINING PROCESS CONVERSION Change the size and/or structure of hydrocarbon molecules 1. Decomposition (dividing) - thermal & catalytic cracking 2. Unification (combining) - alkylation & polymerization 3. Alteration (rearranging) - isomerization & catalytic reforming Catalytic Hydrocracking Unit Fluidized Catalytic Cracker Hydrocracker Reactors THE REFINING PROCESS SEPARATION Separates the various fractions of crude oil Fractional distillation Separation of crude oil in atmospheric and vacuum distillation towers into groups of hydrocarbon compounds of differing boiling- point ranges called "fractions" or "cuts." SEPARATION Crude oil is a mixture of hydrocarbons with different boiling temperatures, thus it can be separated by distillation into groups of hydrocarbons that boil between two specified boiling points. SEPARATION Boiling ranges of typical crude oil fractions b.p = Boiling point (oC) THE REFINING PROCESS SEPARATION A perforated tray THE REFINING PROCESS SEPARATION Atmospheric Distillation Unit (ADU) SEPARATION Vacuum Distillation Unit (VDU) ATMOSPHERIC DISTILLATION UNIT (ADU) - Operates at atmospheric pressure (760 mmHg) - 30-50 trays - Residuum : heaviest fractions of the crude oil leaving the bottom of the atmospheric distillation column fractions that boil in excess of 426oC ATMOSPHERIC DISTILLATION UNIT (ADU) ADU Process Crude Oil Desalter Pump to Heat Exchanger -temperature raised to 288oC Further heated in Furnace -temperature raised to 399oC Products -vaporization -Heavy naphtha -Kerosene Send to Atmospheric -Light gas oil Fractionator (ADU) -Heavy gas oil ADU Process After desalting, the crude oil is pumped through a series of heat exchangers and its temperature raised to about 550°F (288°C) by heat exchange with product and reflux streams. It is then further heated to about 750°F (399°C) in a furnace (i.e., direct-fired heater or “pipe still”) and charged to the flash zone of the atmospheric fractionator. The furnace discharge temperature is sufficiently high [650 to 750°F (343 to 399°C)] to cause vaporization of all products withdrawn above the flash zone plus about 10 to 20% of the bottoms product. Reflux is provided by condensing the tower overhead vapors and returning a portion of the liquid to the top of the tower. If sufficient reflux was produced in the overhead condenser to provide for all sidestream drawoffs as well as the required reflux, all of the heat energy would be exchanged at the bubble-point temperature of the overhead stream. ADU Process The atmospheric fractionator normally contains 30 to 50 fractionation trays. Separation of the complex mixture in crude oils is relatively easy, and generally five to eight trays are needed for each sidestream product. The liquid sidestream withdrawn from the tower will contain lower-boiling components that lower the flash point, because the lighter products pass through the heavier products and are in equilibrium with them on every tray. These “light ends” are stripped from each sidestream in a separate small stripping tower containing four to ten trays with steam introduced under the bottom tray. The steam and stripped light ends are vented back into the vapor zone of the atmospheric fractionator above the corresponding side-draw tray. The ADU (Atmospheric Distillation Unit) separates most of the lighter end products such as gas, gasoline, naphtha, kerosene, and gas oil from the crude oil. The bottoms of the ADU is then sent to the VDU (Vacuum Distillation Unit). VACUUM DISTILLATION UNIT (VDU) Taking the heavy residue in the ADU and further separating this fraction into lighter fractions or cuts. Heavy residue from ADU normally require more energy and higher temperatures for cracking to occur ~ under VACUUM (less than atmospheric pressure). Vacuum acts so as to reduce the boiling point of the various fractions. The lower operating pressure causing high volume of vapor per barrel vaporized (VD column > diameter than AD tower) VACUUM DISTILLATION UNIT (VDU) - Operates at reduced pressure (25 - 40 mmHg) - To improve vaporization, the effective pressure is lowered even further (to 10 mmHg or less) by the addition of steam - Addition pf steam, increases the furnace tube velocity and minimizes coke formation, decrease the total hydrocarbon partial pressure in the vacuum tower -The lower operating pressures cause significant increases in the volume of vapor per barrel vaporized and, as a result, the vacuum distillation columns are much larger in diameter than the atmospheric towers. It is not unusual to have vacuum towers up to 40 ft (12.5 m) in diameter. - Operates at reduced pressure (25 - 40 mmHg) - To improve vaporization, the effective pressure is lowered even further (to 10 mmHg or less) by the addition of steam - Addition pf steam, increases the furnace tube velocity and minimizes coke formation, decrease the total hydrocarbon partial pressure in the vacuum tower -The lower operating pressures cause significant increases in the volume of vapor per barrel vaporized and, as a result, the vacuum distillation columns are much larger in diameter than the atmospheric towers. It is not unusual to have vacuum towers up to 40 ft (12.5 m) in diameter. Crude Distillation Unit Products Fuel gas The fuel gas consists mainly of methane and ethane. In some refineries, propane in excess of LPG requirements is also included in the fuel gas stream. This stream is also referred to as “dry gas.” Wet gas The wet gas stream contains propane and butanes as well as methane and ethane. The propane and butanes are separated to be used for LPG and, in the case of butanes, for gasoline blending and alkylation unit feed LSR naphtha The stabilized LSR naphtha (or LSR gasoline) stream is desulfurized and used in gasoline blending or processed in an isomerization unit to improve octane before blending into gasoline. HSR naphtha The naphtha cuts are generally used as catalytic or reformer feed to produce high-octane reformate for gasoline blending HSR gasoline and aromatics Gas oils The light, atmospheric, and vacuum gas oils are processed in a hydrocracker or catalytic cracker to produce gasoline, jet, and diesel fuels. The heavier vacuum gas oils can also be used as feedstocks for lubricating oil processing units Residuum The vacuum still bottoms can be processed in a visbreaker, coker, or deasphalting unit to produce heavy fuel oil or cracking or lube base stocks. For asphalt crudes, the residuum can be processed further to produce road or roofing asphalts Vacuum Distillation Unit : Santa Fe Springs, California Thank You Petrochemical & Petroleum Refining Technology The Refining Process (Conversion : Unification) THE REFINING PROCESS Change the size and/or structure of hydrocarbon molecules 1. Decomposition (dividing) - thermal & catalytic cracking 2. Unification (combining) - alkylation & polymerization 3. Alteration (rearranging) - isomerization & catalytic reforming THE REFINING PROCESS UNIFICATION Processes to make gasoline components from materials that are too light to otherwise be in gasoline Alkylation Polymerization Cracking + Polymerization + Alkylation = Gasoline yield representing 70 percent of the starting crude oil. Polymerization Convert light olefin gases including ethylene, for example, propylene and butylene into hydrocarbons of higher molecular weight and higher octane number that can be used as gasoline blending stocks. Polymerization Combines two or more identical olefin molecules to form a single molecule with the same elements in the same proportions as the original molecules. Product : Polymer gasoline Introduction 1930s & 1940s, polymerization was widely used produced leaded gasoline Replaced by alkylation process. Why? market demand for unleaded gasoline Low cost processes still required to produce high octane gasoline blending components polymerization still added to some refineries Chemist Thomas Midgley insisted that tetraethyl lead was safe Important facts of Polymerization Propene & butene can be polymerized to form a high octane product boiling in the gasoline boiling range. The product is an olefin having unleaded octane numbers of RON 97 and MON 83. This process produces ~0.7 barrels of polymer gasoline per barrel of olefin feed as compared with ~1.5 barrels of alkylate by alkylation But the product has high octane sensitivity, low capital & operating cost compared to alkylation – polymerization are being added to some refineries Polymerization Catalyst: Phosphoric Acid on an inert support Example : Phosphoric acid + natural clay @ Film of liquid phosphoric acid on crushed quartz Normal catalyst consumption rates are in the range of 1 lb catalyst per 100-200 gallons of polymer produced (830- 1660L/kg) Polymerization * Sulfur in the feed poisons the catalyst and basic compounds neutralize the acid increase acid consumption * Oxygen dissolved in the feed strongly affects the reactions and must be removed Temperature - 300-425˚F Pressure - 400-1500 psi Space Velocity - 0.3 gal/lb Polymerization Schematic Diagram of Polymerization Unit Process description The feed, consisting of propane and butane as well as propene & butene is contacted with amine solution to remove hydrogen sulfide & caustic washed remove mercaptans It is then scrubbed with H2O to remove any caustic @ amines & then dried by passing through a silica gel @ molecular sieve bed Finally a small amount of H2O (350-400 ppm) is added to promote ionization of the acid before the olefin feed steam is heated to 204oC & passed over catalyst bed. Reactor pressures are about 3450 kPa (500 psi or 34 atm). The polymerization reaction is highly exothermic, and temperature is controlled either by injecting a cold propane quench or by generating steam. The propane and butane in the feed act as diluents and a heat sink to help control the rate of reaction and the rate of heat release. Propane is also recycled to help control the temperature After leaving the reactor, the product is fractionated to separate the butane & lighter material from the polymer gasoline Gasoline boiling range polymer production is normally 90-97 wt% on olefin feed @ about 0.7 barrel of polymer per barrel of olefin feed. Cont… Polymerization reaction is highly exothermic Temperature controlled by: - Injecting cold propane quench - Generating steam - Propane being recycled Pre-polymerization Kettle Thank You