PC Unit 3 PDF
Document Details
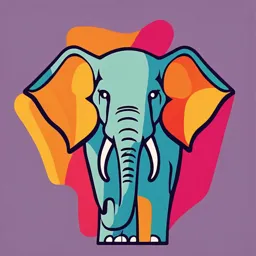
Uploaded by UnparalleledZombie4881
Tags
Summary
This document discusses various types of temperature measurement methods, including flow, level, temperature, and pressure. It also looks at the use of instruments for these measurements, focusing on process control and optimization. Additional topics include thermocouples, bimetallic strips, and other temperature measurement devices.
Full Transcript
## Unit 3 ### Types of Measurement 1. Flow measurement (liquid, gases) 2. Level Measurement (liquid) 3. Temperature Measurment (Solid, liquid, gases) 4. Pressure Measurment (solid, liquid, gases) ### Uses Instrument to Measure: - Pressure, flow, level, Temp ### Control the parameters: - to co...
## Unit 3 ### Types of Measurement 1. Flow measurement (liquid, gases) 2. Level Measurement (liquid) 3. Temperature Measurment (Solid, liquid, gases) 4. Pressure Measurment (solid, liquid, gases) ### Uses Instrument to Measure: - Pressure, flow, level, Temp ### Control the parameters: - to control process - optimised product - max.yield ### Raw Material - Process - Finished Product - Series of Unit Operations - Single operation performed on raw material - Unit operation: - Crashing - Grinding - Filtration ### Process - Integration of Unit Operation - Vacuum: Negative pressure or absence of pressure - Consider distillation: - Atmospheric Distillation - Vacuum Distillation - High Temp Distillation ### Process Instrumentation Diagram - Temp Difference - Temp Gradient - Feedpoint plate - Reboiler coil - Product - Control Panel - Level Indicator - Pressure Indicator - Temp Indicator - Composition Indicator ### Control Panel - Control these Parameters - Control Product/Process - Optimised Product (Max Yield) ### Redwood Viscometer - Determine viscosity of oil - Uniform temperature: Single Unit input ### Fermentor - Drive PPM - PH Sensor (Controller) - O2 Supply - Aeration Device - Temp Sensor - Impeller shaft/RPM - Impeller - Head ### Temperature Measuring Devices - The Temp can be measured using different sensors for measurment of Temp. - There four basic types of temperature measuring devices. Each of these uses a diff principle. They are given Below: - Mechanical Temp measuring devices (liquid in gases - glass thermometers, bimetallic strips, bulb and capillary, pressure type devices, etc) - Thermo Conjuctive Devices (thermocouples) - Thermo resistive devices (RTD's and thermistors) - Radiative (Cinfrared and optical pyrometers) ### Mechanical Temperature Measuring Devices - Thermometer - Graduations of 10 units - Thermometer Bulb - Principal of Operation (Working): Thermal measurement (use) - Expansion of mercury in thermometer. Mercury thermometer works on the principal of Expansion of Mercury due to the heat applied to the Mercury bulb. Now a days, we get. mercury thermometer which measure the temp digitally. In such thermometer, there is no such graduation or marking on the thermom- -eter. The thermometer reading is Directly digitally displayed. We have other types of thermometers also like a thermometer with a prope and the temperature can be measured on different scales & the scales are inter convertable i.e. the temp from one scale can be converted to another scale. - Bimetallic Thermometer - A bimetallic stripe works on the principal of thermal expansion of the metal on obligation of heat. - Different metals have different coefficient of thermal expansion & they expand differently on application of heat - Generally, the metals having greater conductance or good conducting metals expand more than bad conducting or less conducting metals. - A bimetal consist of two different metals, one of them is a good conductor whereas the second one is less conducting. - When Heat is applied the good conductor bends first and then the less conducting will bend along with the good conducting metal. - The principle of bimetallic expansion is used for making & breaking of the contact in the thermostat devices. - The thermostat devices are those devices which require controlled heating for some purpose. The bimetal incorporated in the thermostatic devices makes and breaks the circuit on achieving the set point. The setpoint in a device & is the temp. or pressure which is setup in the device & which is to be achieved by the device. On reaching the set point, the device automatically breaks the circuit. - Bulb & Capillary Sensor - Capillary to remote sensing bulb - Sealed bellows & seed silloide temperature sensor - This is filled with a gas, vapour or liquid. It responds to change in temperature by variation in volume and pressure causing expansion or contraction - Bulb and Capillary Sensor Thermometer. bulb and capillary elements are used where temperatures are to be measured in ducts, pipes, tanks, or similar locations remote from the controller. The bulb is filled with liquid from a gas or rerigerent depending on the temp range required. Expansion of Fluid in the heated bulb exerts a pressure which is transmitted by the capillary to the diphorgram & there it is transmitted into the moment. - Pressure Thermometer - Bulb Tube Pressure Gauge pressure thermometer while still considered mechanical opearates by the expansion of agas instead of liquid or solid. Suppose the gas inside from the thermometer is anideal gas then the ideal gas will follow ideal gas law that is PV=nRT where Pis pressure, Vis volume, nis no. of mass ofgas, R is gas constant forfor specificgas, T is the absolute temperature. The bulb and tube are of constant volume so Vis constant. also the mass (n) of the gas in the sealed bulb is also constant. Hence the above eg" reduces to P=KT where Kis constant. A pressure thermometer therefore measures temp indirectly by measuring pressure. The gauge pressure is cablirated in terms of temp. Hence the device canbe used for measurment of Temp. ### Sample Question 1. What are the different parameters that are measured in a chemical industry? How these parameters affect the processing in a chemical industry. Explain in Brief. 2. What are the different devices for measurment of temp. Discuss them in brief. 3. What is a bimetallic strip? What are the different application of a bimetallic strip in industry? 4. With a neat sketch explain the temp. measurement with a bourdon tube. ### Characteristics of Instruments - The characteristics of instruments are divided into two types. The static characteristics and the dynamic characteristics - The static characteristic of an instrument are as follows: | Sr.no. | Desired Characteristic | Opposite Characteristic | |---|---|---| | 1 | Accuracy | Static error | | 2 | Reproducibility | Drift | | 3 | Sensitivity | Dead zone | 4. * Accuracy - The accuracy of an instrument is defined in percent as ± x% accurate. Generally the accuracy of the instrument varies in between 5-10%. The decuracy of an instrument is an important characteristic of an instrument * Static rerror - The static error may be defined as the difference between the true value & the actual reading of the instrument. The true value + static error = actual reading of the instrument. * Reproducibility - The reproducibility of an instrument may be defined as the accuracy with which the instrument produces the same reading * Drift - The drift in an instrument is defined as the shift in the instrument calibration over period of time. In some instruments the calibration may not shift for days & months whereas in some cases the calibration may shift immediately within a day. There are different types of drifts in instruments. * Sensitivity - The sensitivity of an instrument may be defined as the immediate response given by the instrument to the input. A sensitive instrument reacts immediately to the smallest input given to it. A non sensitive instrument will not react to the input given to it. * Dead Zone - It may be defined as the zone in which no response is observed through the input. i.e. the dead zone is a zone in which the instrument fails to respond. ### Dynamic Characteristics - These are those characteristics which Vary with the real time. | Desired Characteristics | Undesired Characteri-istics | |---|---| | Speed of Response | Lag | | Fidelity | Dynamic Error | - Speed of Response - It may be defined as the immediate response or the rate of response given by an instrument to the input provided to the instrument. - Lag. - It may be defined as the time taken by the instrument to respond to the given input. The Lag in an instrument may be calculated in seconds. - Fidelity - The Fidelity of an instrument may be defined as the degree to which an instrument indicates the changes in measured variable without dynamic error. Dynamic error is defined as the difference between the true value and the quantity changing with time. and the value indicated by the instrument if no static error is assumed. ### Thermocouples, Thermocouples - These are the instruments used in the industry for high temperature measurment. Thermocouples measure the temperature between 2000 °F to 3000°F. Initially, the thermocouples were used to measure the temperatures between the range 2000°F to 3000°F but nowdays. the thermocouples are also able to measure lower temp also. Thermocouple can measure temp as low as 200°F. They are generally used in industries like Metal industry, glass, molten salt industry & with the reactors & furnaces - There are diff. combinations of thermocoupl along with the thermocouple lead wires - The diff combinations of thermocouple are given in the table below. | Sr.no. | Metal 1 | Metal 2 | Leadwire Metal 1 | Leadwire Metal 2 | |---|---|---|---|---| | 1 | Copper | Constantan | Copper | Constantan | | 2 | Iron | Constantan | Iron | Constantan | | 3 | Chromel | Alumel | Chromel | Alumel | | 4 | Iron | Constantan | Iron | Copper-Nickel Alloy | | 5 | Chromed | Alumel | Copper | Constantan | | 6 | Platinum- Rhodium | Platinum | Copper | Copper-Nickel Alloy | ### Desirable Properties in a Thermocouple for Industrial Use: 1. Thermocouples should have a large thermal EMF for a given temperature range so that a Simple & durable measuring instrument can be coupled with the thermocouple. Generally, instruments measuring Voltage are connected with the thermocouple 2. The thermocouple must have a precised calibration. The thermocouples are used in high temp operation hence the thermocouple should have aprecised measurment so that they do not have any kind of drift in their output or reading. 3. Resistance to corrosion and oxidation. The thermocouple is used for measurment of high temp. A metal during operation at high temp is subjected to diff thermal stresses. These stresses are responsible for thermal corrosión in the metal. Hence while selecting the material for thermocouple proper oper material. which can handle the operating conditions should be selected. Such a material will resist both corrosion and oxidation, Both point 4. Linear relationship with the temp. The thermocouple should have linear relationship with the temp. that means as the temp increas -es the thermocouple output in whatever unit) it is should increase linearly i.e. if weplot temp against outpat (milliNoHS) we mustget a straight line in the graph. Only then the relationship will be a linear relationship. ### The preinciple and working of a Thermocouple - The principle of working of a thermocouple can be understood from the following:- - When two dissimilar metals are connected together. a small voltage called as the thermojunction voltage is generated at the junction this is called as peltier effect. - If the temperature of the junction changes, it causes the voltage to change. This voltage can be measured by means of and electric circuit connected to a voltmeter or millivoltmeter. The output voltmeter voltage is proportional to the temperature difference between the free ends, this is called as thomson effect. - Both this effects can be combined to measure temp By holding one junction at a known temperature (reference junction & measuring the voltage). The temp at the sensing junction can be calculated or known. The voltage generated is directly proportional to the temp difference. The combined effect at the thermo junction is known as thermojunction effect or the Seebeck effect. ### The thermocouple can be represented by a diagram given below: - Figure representing a thermocouple okt along with thermocouple probe and a measuring device. The thermocouple probe and a measuring device produces temp difference which is directly proportional to the EMF generated. Hence we can use the thermocouple for measurment of temperature. after callibration of temperature in either volts or millivolts. Based on the sensing position of the thermocouple measuring junction the thermocouple are divided into three types. 1. The grounded junction thermocouple the measuring junction directly touches the probe wall. Such type of arrangement gives good heat transfer from the outside through the probe wall to the thermocouple junction 2. Underground junction thermocouple -> The thermocouple Junction is not touching the wall of the probe instead it is far away from the wall of the probe. Such a thermocouple offers electrical isolation. Hence the underground thermocouple is recommended for corrosive environments where electrical isolation is required. 3. The exposed junction thermocouple has the electrical circuit 1.e. the measuring junction coming out of the probe, such type of thermocouple offers best response time but it is limited to the use in non pressurised application.