Heat Transfer Equipment Standards Committee PDF
Document Details
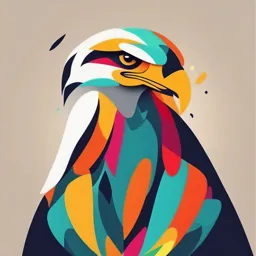
Uploaded by NonViolentWisdom1977
2020
Tags
Summary
This document provides detailed information about heat exchanger manufacturing, including specifications for reinforcing pads, welding procedures, and related standards. It describes various types of welds and considerations for different materials and applications.
Full Transcript
Document Responsibility: Heat Transfer Equipment Standards Committee 32-SAMSS-007 Issue Date: 26 June 2017 Next Planned Update: 26 June 2020 Manufacture of Shell and Tube Heat Exchangers 9.1.9 Telltale Holes in Reinforcing Pads...
Document Responsibility: Heat Transfer Equipment Standards Committee 32-SAMSS-007 Issue Date: 26 June 2017 Next Planned Update: 26 June 2020 Manufacture of Shell and Tube Heat Exchangers 9.1.9 Telltale Holes in Reinforcing Pads 9.1.9.1 ¼ - inch telltale vent holes drilled and tapped for ⅛ -inch NPT shall be provided in reinforcing pads for welded attachments, including nozzles and manways, per the following: 1) One hole in single piece reinforcing pad. 2) Where a pad is split, each segment shall have at least one hole. 9.1.9.2 Telltale holes shall be located at the lowest position accessible for inspection with center of the hole 25 mm from edge of the pad. This is also applicable to each segment of a split-reinforcing pad. Commentary Note: In case of reinforcing pads for attachments, other than nozzles and manways, center of telltale hole shall be 25 mm from the closest edge of the pad. 9.1.9.3 Telltale holes in reinforcing pads for external welded attachments shall be plugged with grease or other materials adequate for the operating temperature but not capable of retaining pressure. Telltale holes in internal attachment pads shall be seal welded. 9.1.10 Segments of split reinforcing pad shall be welded together without using a backing strip. 9.2 Pass Partition Plates Pass partition plate shall be provided with a 6 mm (¼") drain hole. 9.3 Connection Junctions (Exception) All nozzles shall be ground flush to the inside curvature of the exchanger inside diameters with smooth inside corner radius equal to the nozzle wall thickness. 9.5 Welding 9.5.1 (Exception) All welding shall be in accordance with the requirements of SAES-W-010 and SAES-W-016. 9.5.2 (Exception) All welded joints of category A, B, C, and D shall be complete fusion full penetration welds, except for joint welds of slip-on flanges specified per paragraph 7.6.5 of this specification. 9.5.13 Where a split-reinforcing pad is required, the weld joining the pad sections shall be oriented with the circumferential direction of the shell. Welding the Page 36 of 59 Document Responsibility: Heat Transfer Equipment Standards Committee 32-SAMSS-007 Issue Date: 26 June 2017 Next Planned Update: 26 June 2020 Manufacture of Shell and Tube Heat Exchangers pad sections together shall be done without using a backing strip. 9.5.14 Dissimilar metal welds (DMW) are not permitted in sulfide stress cracking environment as defined in this specification. 9.5.15 Following maximum allowable carbon equivalent, based on thickness before forming (t) shall be met for exchangers intended for sulfide stress cracking environment. Thickness (mm) Carbon Equivalent (%) 6 < t ≤ 60 0.43 60 < t ≤ 100 (0.00125*t – 0.075) + 0.43 t > 100 0.48 9.5.16 The method of weld overlay shall be such as to produce a minimum of 3.2 mm thickness meeting the specified chemical composition of the specified weld overlay material. 9.5.17 Intermediate stress relief (ISR) shall performed on all highly restrained joints in exchangers under the scope of API RP 934-A, such as nozzle/ manway welds in shells or heads and for other joints which are highly stressed during fabrication (e.g., grooves in RTJ). Dehydrogenation Heat Treatment (DHT) shall not be used as an alternative to ISR for the aforementioned joints. 9.5.18 Welding procedures shall be qualified considering all of the thermal treatments that could affect the material plus two additional cycles to account for future repairs and/or alterations (refer to paragraph 8.1.15 of this specification). 9.5.19 Exchangers constructed of 1 Cr- ½ Mo, 1 ¼ Cr- ½ Mo, 2 ¼ Cr-1 Mo, 2 ¼ Cr-1 Mo- ¼ V, 3 Cr-1 Mo and 3 Cr-1 Mo- ¼ V steels with internal weld overlay shall have two-layer (ER309L/ER347) overlay. 9.5.20 Weld overlay per paragraph 9.5.19 shall have smooth contour finished surfaces where there is change in geometry for highly stressed areas (such as nozzle/manway welds in shells or heads and RTJ grooves). 9.5.21 Necessary logistic fabrication steps shall be taken to ensure that highly restrained joints, such as nozzle/manway welds in shells or heads and RTJ grooves, in exchangers constructed of 2 ¼ Cr-1 Mo- ¼ V and 3 Cr-1 Mo- ¼ V steels are welded continuously throughout the welding process without any stop, i.e., from start of the first welding pass to completion of welding the joint. Page 37 of 59 Document Responsibility: Heat Transfer Equipment Standards Committee 32-SAMSS-007 Issue Date: 26 June 2017 Next Planned Update: 26 June 2020 Manufacture of Shell and Tube Heat Exchangers 9.5.22 No dissimilar metal weld is allowed for A, B, C, and D weld joint categories in exchangers fabricated according to API RP 934-A, API RP 934-C or API RP 934-E, regardless of the presence of stainless steel weld overlay. 9.5.23 For services requiring impact test, welding procedures shall be qualified for at least 80% of the time for any heat treatment after welding required per paragraphs 8.1.15 (a) and 8.1.15 (b) of this specification. 9.5.24 Production Test Coupons, if required as per Code, shall be subject after welding to the production heat treatment time per paragraphs 8.1.15 (a) and 8.1.15 (b) of this specification. 9.5.25 Production test coupons are required for hot forming. The coupons shall simulate all heat treatment cycles expected during and after forming, and any post weld heat treatment cycles by exchanger manufacturer specified per paragraph 8.1.15 of this specification. The tests to be performed shall include, but not limited to, all of the mechanical tests required by the original material specification. 9.5.26 In addition to the requirement of paragraph 9.5.23 of this specification, welding procedures and production test coupons (if required by code) for exchangers in sour service shall be subject to additional supplementary impact and hardness tests with one PWHT cycle. Hardness testing shall comply with NACE MR0175/ISO 15156. 9.5.27 When production test coupons require multiple thermal heat treatment cycles to be simulated, the multiple cycles shall not be combined into one cycle. 9.6 Heat Treatment 9.6.3 (Exception) 1) The following tubes shall be stress relief heat treated after cold forming and bending: a) U bends, including 150 mm of straight portions measured from the tangent line of all carbon steel tubes for exchangers in caustic, wet sour and amine services. b) Monel, brass and all chrome alloy tubes in all services. 2) The following tubes shall be solution annealed: a) Entire tubes manufactured of un-stabilized or non-low carbon stainless steels or Nickel base alloys in accordance with ASME SA-688. Page 38 of 59 Document Responsibility: Heat Transfer Equipment Standards Committee 32-SAMSS-007 Issue Date: 26 June 2017 Next Planned Update: 26 June 2020 Manufacture of Shell and Tube Heat Exchangers b) U bends, including 150 mm of straight portions measured from the tangent lines of all stabilized or low carbon stainless steels or Nickel base alloys. 9.6.12 Postweld heat treatment (PWHT) shall be done when required by the applicable Code or when specified on the data sheet. 9.6.14 Code exemptions for postweld heat treatment (PWHT) of ferritic materials based on the use of austenitic or nickel-based electrodes are not permitted for exchangers in sulfide stress cracking environments as defined in this specification. 9.6.15 Code exemptions for postweld heat treatment of P4 and P5 materials are not permitted for applications involving the following: a) Environments containing wet H2S b) Hydrogen services c) Materials exceeding 2.5% nominal chromium content 9.6.16 The maximum post weld heat treating soaking temperature for quenched and tempered carbon and low alloy steel materials shall not exceed either the tempering temperature shown on the Mill Test Reports or the following: 650°C maximum for carbon steel 700°C maximum for low alloy steels. For Cr-Mo materials covered by API RP 934-A, alternative tempering and PWHT temperatures are acceptable if qualified in accordance with this specification. 9.6.17 Final postweld heat treatment (PWHT) shall follow all welding and repairs but shall be performed prior to any hydrotest or other load test. 9.6.18 A sign shall be painted on a postweld heat treated exchanger and located such that it is clearly visible from grade: "Caution – Exchanger Has Been Postweld Heat Treated – Do Not Weld" 9.6.19 Postweld heat treatment (PWHT) shall be in accordance with the requirements of SAES-W-010 and this specification. 9.6.20 The holding temperature for post weld heat treatment for carbon steel exchangers shall be 620°C – 650°C (1,150°F – 1,200°F). 9.6.21 It is the responsibility of the Exchanger Manufacturer to ensure structural stability of the exchanger that will undergo PWHT, considering but not Page 39 of 59 Document Responsibility: Heat Transfer Equipment Standards Committee 32-SAMSS-007 Issue Date: 26 June 2017 Next Planned Update: 26 June 2020 Manufacture of Shell and Tube Heat Exchangers limited to the following: a) Dead weight at intended PWHT soaking temperature. b) Temperature gradients in equipment wall due to the intended PWHT procedure. c) Mechanical restraints that may prevent the equipment from free movement (expansion/ contraction) during PWHT. 9.7 Dimensional Tolerances 9.7.5 Fabrication tolerances shall be in accordance with the more stringent of the applicable Code, TEMA, and PIP document VEFV1100. 9.7.6 Use of fitness-for-service assessment methodology to qualify the design of components that do not satisfy the fabrication tolerances according to this specification is prohibited. 9.8 Gasket Contact Surfaces other than Nozzle Flange Facings 9.8.1 (Exception) Gasket seating surfaces shall comply with the following: 1) For spiral wound gaskets, 125 to 250 AARH, in all services, except hydrogen. 2) For spiral wound gaskets in hydrogen service, 125 to 150 AARH. 3) The side-walls of ring joint flanges in all services, 63 AARH. 4) For non-metallic gaskets, 250 to 500 AARH. The surface roughness of machined surfaces, other than gasket contact faces, shall not exceed 500 AARH. 9.9 Tube Holes 9.9.3 Tubesheet tube hole diameters and tolerances shall be special close fit when tube bundle vibration is suspected or when exchanger is in cyclic service. 9.9.4 Tube expanding procedures shall incorporate stops to prevent tube expansion past tubesheet faces. 9.9.5 Tube expansion and tube-end welding (where specified) procedures shall be submitted to the Saudi Aramco Inspector for review and approval before start of fabrication. 9.9.6 The Exchanger Manufacturer shall submit a mock-up sample of the tube to tubesheet weld when tubes are strength welded to the tubesheet. This sample Page 40 of 59