Sheet and Panel Products PDF
Document Details
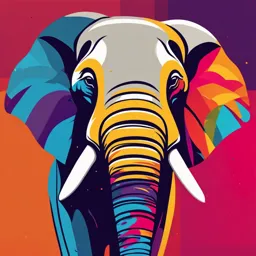
Uploaded by AttractiveJaguar
Tags
Summary
This document provides an overview of manufactured sheet and panel products, including composite panels, plywood, and different types of particleboard. It details the manufacturing processes and terminology related to these materials, along with their properties and applications. The information also includes details about handling and storage.
Full Transcript
Manufactured Sheet and Panel Products 1 Topics 1. Composite Panels 2. Plywood 3. Handling and Storage of Panel Products 2 1 Terminology The terms Sheet Product and Panel Product are often used interchangeably 3 Composite Panel Products • Made from small wood pieces / wood fibers and adhesive...
Manufactured Sheet and Panel Products 1 Topics 1. Composite Panels 2. Plywood 3. Handling and Storage of Panel Products 2 1 Terminology The terms Sheet Product and Panel Product are often used interchangeably 3 Composite Panel Products • Made from small wood pieces / wood fibers and adhesives • • • • • Particleboard Low Density Fibreboard Medium Density Fibreboard High Density Fibreboard Oriented Strand Board • Panels are produced to specific densities, thickness tolerances, and surface finishes • Free of knots and voids • Often used as a core/substrate for overlays such as wood veneer, laminates, etc 4 2 Particleboard 5 Particleboard • Engineered wood product • Made of wood particles such as chips, splinters, shavings and flakes • Particles mixed with a bonding agent (glue) • Mixture formed into sheets • Two manufacturing methods • Extrusion method • Mat formed method 6 3 Extrusion Method • Board formed by forcing particles/bonding agent mixture through a small heated opening (extrusion die) • Boards are not pressed flat after extrusion • Process results in random orientation of particles • Minor thickness variations throughout board • Least common method of particleboard production 7 Mat Formed Method • Most common method of particleboard production • Particles and binder are formed into mats • Mats are pressed into sheets • Results in a product with a hard dense smooth surface with uniform thickness • 2 types of Mat Formed Particleboard 8 4 Types of Mat Formed Particleboard 1. Mat Formed - Single layer • Same size particles throughout the sheet 2. Mat formed - Multilayer • Layers on outside of sheet have fine particles • Layer on inside of sheet have coarser particles • Results in a sheet with fine particles on surface and coarser interior • Reduces weight while still providing a hard dense smooth surface 9 A close up of particle board with the core/edge visible. 10 5 Particleboard Manufacturing Steps 1.Chipping and Flaking 2.Drying 3.Screening 4.Blending with Adhesive 5.Forming 6.Pressing 7.Cooling & Curing 8.Sizing 9.Sanding 11 The end of the production line. 12 6 Specialty Particleboard • Fire Resistant • Include additives that retard the spread of fire • Intended for use in commercial buildings where building code limits flame spread and smoke generation • Moisture Resistant • Sheltered exterior applications • Waterproof glue • Anti-Static • Will not generate static electricity • For use in areas with sensitive electronic equipment 13 Particleboard Grades High Density Medium Density Low Density 14 7 Particleboard Bonding Systems • Type 1 • Urea Formaldehyde Resin • Interior use only • Type 2 • Phenol Formaldehyde Resin • Greater Heat / Moisture Resistance • No Added Formaldehyde (NAF) • In response to consumer demand “No Added Formaldehyde” products are now also available Sizes • Thickness: ¼” – 2 ¼” • Sheet sizes: 49” x 97”, 61” x 145” (oversized by 1 inch) 15 Particleboard & Moisture With standard particleboard (Type 1 bonding system), unprotected edges will wick water from any source, causing the individual particles to expand To reduce risk of moisture damage, edges should be sealed or protected in some way 16 8 Face Ply Particleboard Core Back Ply Particleboard makes an ideal substrate for veneering projects. It’s surface is very flat with just the right porosity/texture to ensure a good adhesive bond. 17 Particleboard Videos • https://www.youtube.com/watch?v=y1PWusUN9N4 • https://www.youtube.com/watch?v=4SkseNnbuEo • https://www.youtube.com/watch?v=1Fjn1FYCQ0I 18 9 Fibreboard 19 Fibreboard - General • Engineered wood product • Wood (poplar and softwoods) broken down into wood fibres using pressure and steam • Fibres formed into a continuous interfelted mat and compressed with rollers à wetlaps • Continuous sheet cut into panels and then pressed • Different amount of pressure, heat, and additives for different products Low Density Fibreboard Medium Density Fibreboard High Density Fibreboard 20 10 Low Density Fibreboard (LDF) • Manufactured by cold pressing wetlaps in felted sheets • Held together by interlocking fibres rather than adhesive • Can contain additives such as fire retardant • Good sound absorption qualities • Standard Thicknesses: ½” – 1” • Special Order: 2” – 3” • Applications • Ceiling tiles • Wall soundboards • Notice boards 21 Medium Density Fibreboard (MDF) • Wetlaps include a binder • Wetlaps formed into panels under high temperature and pressure • MDF is homogenous, flat, and smooth with a tempered surface • Specialty MDF available – Fire retardant – Moisture Resistant – NAF • Applications – Kitchen cabinet doors – Millwork/Mouldings – Core material for plywood • ASTM D 1037-06a defines MDF grades as 115, 130 and 155 based on strength • Grade names vary by supplier • www.pbmdf.com 22 11 23 24 12 Medium Density Fibreboard Advantages Disadvantages • Can be shaped due to uniform surface to core consistency • Edges can be problematic for finishing due to their porous nature • Prone to splitting when driving screws • Used often for thermal foil doors or one piece CNC doors • Very smooth surface • Excellent for painted or coloured lacquer finish 25 The homogenous core of MDF allows for edge treatments and clean internal routings. Mouldings are frequently manufactured using MDF. 26 13 5 Piece Shaker-Style Door in Solid Wood http://burrowscabinets.com/wp-content/uploads/5-pc-shaker-alder-bali-495x495.jpg 27 “Mock” 5 Piece Shaker-Style Door in MDF http://cdn3.volusion.com/ufddy.cnppv/v/vspfiles/photos/MDF-SHAKER-DOOR-2.jpg?1431008784 http://cdn3.volusion.com/ufddy.cnppv/v/vspfiles/photos/MDF-SHAKER-DOOR-3.jpg?1431008784 28 14 • Joining MDF requires the same care as particleboard • Edge screws must be countersunk and have pilot holes drilled to prevent splitting • MDF will dull normal tools à Carbide cutters and tooling should be used 29 Slatwall MDF product in common use for display purposes. 30 15 High Density Fibreboard (HDF) • Also known as “Hardboard” and “Masonite” • Very durable thin sheet • Typically has a very smooth tempered surface • Available smooth back or textured back • Numerous surface finishes and textures also available • Common thicknesses: 1/8”, 3/16”, 1/4” http://www.hyatts.com/eCom/images/K/K21346.jpg • 1/8” is commonly used for backs with “inset back construction” cabinets 31 http://www.rona.ca/images/5120017_L.jpg http://g03.s.alicdn.com/kf/HTB1wx.fFFXXXXavaXXXq6xXFXXXe/685729/HTB1wx.fFFXXXXavaXXXq6xXFXXXe.jpg HDF is also available perforated (pegboard) and embossed (patterned) 32 16 High Density Fibreboard - Grades • Tempered Grade • Impregnated with resin and heat cured to improve • Water resistance • Hardness • Strength • Finishing properties • Suitable for exterior applications as long as cut edges are sealed • Standard Grade • No special treatment after manufacturing • Used for cabinet backs and drawer bottoms • Service Grade • Lower strength • Rougher face • Used when lower quality is acceptable 33 Oriented Strand Board 34 17 Oriented Strand Board (OSB) • Manufactured by layering oriented wood strands and adhesive into mats • Mats compressed into panels under heat • Applications: • Plywood substitute for subfloors and sheathing • Core material for plywood 35 36 18 Wood chip mat before pressing into sheets Sections of OSB after pressing to various thicknesses 37 Plywood 38 19 Plywood • Any sheet product with outer plies made from wood veneer • Engineered sheet • 3 or more layers called plies • At a minimum http://formationswood.com/hardwood-plywood/ Veneer Core • 2 outside plies of hardwood or softwood veneer • at least one core ply • Each core ply can be a sheet of veneer or layer of composite panel • Always odd number of plies • Face plies and core plies bonded together under high temp and pressure to form a plywood sheet MDF Core PB Core 39 Veneer Core Plywood • Core comprised of layers of veneer • Core veneer is typically rotary sliced • Orientation of veneer plies is key to stability and strength • Crossbanding Process of alternating the grain direction of plies 90 degrees to adjacent plies • Any dimensional changes in plywood are equal in both directions due to crossbanding http://www.hobbithouseinc.com/personal/woodpics/images/veneercore.jpg Equal Expansion http://static.nordcompensati.com/immagini-prodotti/Compensati/okoumè%20rina/Pagina%20prodotto/okoumè-rina.png 40 20 Rotary Slicing • Uses a massive lathe • Logs used for rotary slicing are called peelers or bolts • Peelers rotated downward against pressure bar and knife • Pressure bar and knife mounted at centreline of peeler • Pressure bar pressed against peeler ahead of knife to prevent splitting • Can produce 200-400 ft of veneer per minute • Grain pattern is very erratic • Guillotine cuts sheets to length 41 Veneer Core Plywood • VC Plywood performance affected by • Thickness of each ply • Total number of plies Plywood 1 Plywood 2 Thickness 19 mm 19 mm # of plies 5 11 Strength ↓ ↑ Stiffness ↓ ↑ Weight ↓ ↑ Cost ↓ ↑ • Adhesives • selected for intended environment – interior or exterior 42 21 Plywood Core Types 1. Veneer Core • Core made up of rotary cut veneer layers • Crossbanded https://yomega.co/best-veneer-core-plywood-inspirations/ 2. Particleboard Core • Particleboard core • Veneer on each side https://images.lowes.ca/img/p400/20312/772851214805_ca.jpg 43 Plywood Core Types 3. MDF Core • MDF core • Veneer on each side http://walzcraft.com/wp-content/uploads/2011/06/1-1.4-Plywood-MDF-Core-Angle.jpg 4. Combination Core / Multi-core • Combination of composites and veneer for plies • Veneer in each side Why has MDF been placed next to the face and back plies in this combination core plywood? 44 22 Face and Back Plies Face Ply Back Ply • Outside faces of a sheet • Face and back plies may or may not be the same species • Dependent on what will be visible in the application • Face ply often higher grade than back ply 45 Hardwood Veneer Plywood Grades • Grading defined by the Canadian Hardwood Plywood and Veneer Association • Face Veneer - Letter Grade A, B, C • Back Veneer – Number Grade 1, 2, 3 • End users must specify • core type • cut of veneer • veneer match Note: Grading practices for Hardwood Veneer Plywood are very inconsistent. Face, back and core requirements must be clearly specified. 46 23 Baltic Birch Plywood http://www.appleply.com/about.php • Made from thin plies of birch • More plies than “normal” plywood • Very strong and dense • Available in many thicknesses (3, 6, 9, 12, 18, 24 mm) • Sheets are typically 60” x 60” but some thicknesses also available in 4’ x 8’ • Edges often left untaped for an industrial look http://www.woodworkerssource.com/blog/wp-content/uploads/2013/10/baltic-birch-dovetail1.jpg http://i184.photobucket.com/albums/x295/kach22i/MISC/kach22i-tabledetail-2000B.jpg 47 “Construction” Softwood Plywood Grades www.canply.org 48 24 Canadian Softwood Plywood Sizes • 48” x 96” (4’ x 8’ ) • Thicknesses are Metric • Available thicknesses differ between sanded and unsanded products • Example: • Unsanded: 12.5 mm • Sanded G2S: 11 mm 49 Plywood Videos https://www.youtube.com/watch?v=AmPkAuQc4-E https://www.youtube.com/watch?v=qA9XmJfh_RE 50 25 Handling and Storage of Sheet/Panel Products 51 Handling and Storage of Panel Products 1. 2. 3. 4. 5. 6. 7. Store sheets flat and level Do not store directly on concrete floors Protect panel edges and corners Carry panels on edge Do not slide sheets off a stack Ensure panels have acclimatized prior to use Protect from sunlight, water, and excessive humidity 52 26 Questions? 53 27