Operational Planning and Service Delivery PDF
Document Details
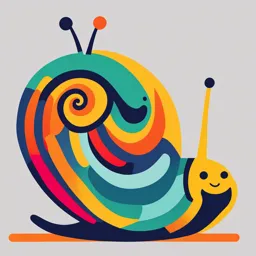
Uploaded by BuoyantCliché
Tags
Summary
This document discusses operational planning and service delivery in vehicle maintenance and repair, focusing on aspects such as customer satisfaction and efficiency. It also highlights several services offered by Abou Ghaly Motors in Egypt.
Full Transcript
**Operational planning** and **service delivery** ================================================= **Operational planning** and **service delivery** are two crucial components in the efficient management of services like vehicle repairs and maintenance. 1. **Operational Planning**: This involves...
**Operational planning** and **service delivery** ================================================= **Operational planning** and **service delivery** are two crucial components in the efficient management of services like vehicle repairs and maintenance. 1. **Operational Planning**: This involves the advanced organisation of resources, processes and schedules needed to ensure smooth service delivery. In a vehicle service centre, operational planning covers scheduling appointments, ordering parts, allocating technicians and preparing for anticipated demand. Effective planning helps ensure that resources are available when needed, reducing wait times and improving overall efficiency. 2. **Service Delivery**: This is the execution phase where planned services are provided to meet customer needs. In the context of vehicle servicing, it includes the actual repair or maintenance work, quality checks and the final handover of the vehicle. The goal of service delivery is to meet or exceed customer expectations, ensuring services are performed accurately, promptly and professionally. Together, operational planning and service delivery create a cohesive process that ensures customer satisfaction through organised, timely and high quality service. Operational planning and service delivery directly impact a business\'s success by shaping customer satisfaction, operational efficiency and profitability. Here's how: 1. Customer satisfaction and loyalty: Effective operational planning ensures that services are available when customers need them, reducing wait times and enhancing convenience. Efficient service delivery builds trust by meeting or exceeding customer expectations. Satisfied customers are more likely to return and recommend the business to others, driving long term growth. 2. 3. Employee productivity and morale: When operations are well planned, technicians have clear schedules, tasks and resources, which reduces delays and stress. This boosts morale and job satisfaction, leading to better performance and lower staff turnover. 4. Financial performance: Streamlined operations mean more services can be completed within a given timeframe, increasing revenue potential. Reducing operational errors and minimising delays also cuts costs, which in turn improves overall profitability. 5. Competitive advantage: Businesses that consistently provide timely, high quality services build a strong reputation, which distinguishes them from their competitors. A positive reputation helps to attract new customers and strengthens the business's position in the market. Abou Ghaly Motors offers a comprehensive range of vehicle maintenance and after-sales services designed to cover both routine and specialised automotive needs. These services include: - **Routine maintenance and repair**: This covers standard maintenance procedures such as oil changes, brake checks, fluid refills and routine engine inspections. These are typically performed as part of periodic servicing to ensure vehicle longevity and performance. - **Body and paint services**: Abou Ghaly Motors provides full body and paint repair services to address aesthetic and structural damage. These services include dent repair, repainting and body panel replacements, helping maintain the car's appearance and value. - **Roadside assistance**: For emergencies, Abou Ghaly offers roadside support, allowing customers to access help for on-the-go issues, such as breakdowns or lockouts, as part of their extended service package. - **Protection and wrapping**: This service includes options like protective coatings and vehicle wraps, which safeguard the car\'s exterior from environmental damage and improve its aesthetics. - **Door-to-door service**: To enhance convenience, Abou Ghaly Motors provides a pickup and delivery service for vehicles in need of maintenance, which helps busy clients maintain their vehicles without disrupting their schedules. - **Extended warranty and insurance options**: The company also offers extended warranty services and flexible insurance plans, providing financial protection for repairs and minimising unexpected maintenance costs over the vehicle's life. Abou Ghaly Motors emphasises convenience and flexibility, making it a top choice for comprehensive vehicle maintenance and service support in Egypt. These services are accessible through their multiple service centres and their customer service app, allowing users to manage appointments, track services and stay informed about their vehicle's maintenance status. For more details, visit their official website. Describe methods that clients can use to book a car in for service, maintenance or repair ========================================================================================= Clients have several convenient options for booking a car for service, maintenance, or repair, catering to different preferences and needs. Here are some common methods: ### 1. Online booking via website - Many service centres offer an online booking portal where clients can schedule service appointments. The process typically involves: - Selecting the type of service required (service, maintenance, repair, diagnostics etc.). - Choosing a preferred date and time from available slots. - Adding specific details about the vehicle (make, model, mileage and any known issues). - Some platforms also offer options to create a customer account for tracking service history, getting reminders and accessing promotions. ### 2. Mobile app booking - Some automotive brands or service centres have dedicated mobile apps, allowing users to schedule service on the go. - Apps may offer additional features like appointment reminders, service updates and real-time tracking of the vehicle\'s status during servicing. - Some apps also allow users to pay through the app, view past service history and even request roadside assistance. ### 3. Phone call - Calling the service centre directly is a traditional but effective way for clients to book service appointments. - This method allows for immediate, personalised interaction where the client can ask questions, get advice on necessary services and clarify any concerns about their vehicle. ### 4. Email booking - Many service centres accept booking requests via email, which is useful for clients who prefer a more asynchronous communication style. - In the email, clients can specify the desired service type, date and time, as well as any specific issues or requests. - Service centres generally respond within 24 hours to confirm the appointment or offer alternative options if slots are unavailable. ### 5. SMS Booking - Some service centres use SMS-based systems for booking. Clients can text a specific number to request an appointment, often using a preset format (e.g., \"BOOK + \[Date\] + \[Service Type\]\"). - The centre then sends a confirmation text with the appointment details. ### 6. Drop-in scheduling - Some clients prefer to drive directly to the service centre and book an appointment in person. - While this might work well for non-urgent needs or if the centre has available slots, it may be less convenient during peak times when appointments fill up quickly. - Drop-in visits often work best at smaller or local garages where appointment systems are more flexible. ### 7. Social Media or Chatbots - Many automotive brands and service centres now have booking options through social media channels (like Facebook Messenger) or integrated website chatbots. - These options allow clients to interact with automated systems or live agents who guide them through the booking process and answer general inquiries. ### 8. Third-party service platforms - Third-party automotive service platforms or aggregators (like Openbay or YourMechanic) allow clients to find local service providers, compare prices, read reviews and schedule appointments directly through the platform. - These platforms are especially useful for clients looking for specific services or those comparing prices across various providers. Each of these booking methods offers flexibility for different client preferences, helping ensure that scheduling a car service is as convenient and efficient as possible. Can drivers just turn up with their vehicle and get it serviced or repaired? ============================================================================ Yes, drivers can sometimes turn up without an appointment to have their vehicle serviced or repaired, but there are several factors to consider: ### 1. Availability of service technicians - For smaller, local garages, walk-ins may be more feasible, especially during non-peak times when technicians may have open time slots. However, at larger or busier service centres, technicians are often fully booked, so wait times could be long or they may not be able to take the vehicle on the same day. ### 2. Type of service needed - Simple services, such as oil changes or tyre rotations, may be easier to accommodate on a walk-in basis since they typically require less time and fewer parts. - For more complex repairs or diagnostics, however, a walk-in service may be harder to accommodate, as these often require specific parts or tools that may need to be pre-ordered based on the appointment. ### 3. Time of day and day of the week - Early in the day or during weekdays, especially early in the week, may provide better chances of getting a walk-in appointment, as weekends and end-of-week days tend to be busiest. ### 4. Waiting time - Walk-in customers may face extended wait times or have to leave their vehicle at the shop if technicians are currently working on other vehicles with scheduled appointments. Some service centres might offer a \"first-come, first-served\" policy for walk-ins, but there's usually no guarantee of an immediate service. ### 5. Service centre policies - Many larger dealerships and service centres require appointments, particularly for warranty-related or brand-specific maintenance. Independent garages may be more flexible but will still prioritise scheduled appointments over walk-ins. ### 6. Emergency and express services - Some centres offer express or emergency repair services for urgent needs, such as flat tyres, battery replacements or quick diagnostics and might accommodate these needs without an appointment. It's advisable to call ahead to confirm whether the shop can accommodate the vehicle that day. ### Summary While many service centres will accept walk-ins if they have availability, it's often best to call ahead and check. This can save time, ensure the needed parts are available and avoid unnecessary waiting. How is work scheduled, planned and allocated in the vehicle service centre ========================================================================== Work scheduling, planning and allocation in a vehicle service centre is a well-structured process that involves managing resources, technicians, tools and parts to ensure efficient workflow and timely delivery of services. Here's an overview of how this process typically unfolds: **1. Service appointment scheduling** - **Customer booking**: Appointments are scheduled based on customer bookings via online systems, phone calls, or in-person requests. - **Service Type and Complexity**: The type of service (routine maintenance, repairs, diagnostics) is noted at the time of booking to allocate the appropriate technician and time. Routine services (e.g., oil changes) are usually quicker, while complex repairs are scheduled for longer time blocks. - **Time allocation**: Estimated time for each service type is assigned based on standardised guidelines, helping manage technician workloads and minimise wait times. **2. Work planning and pre-service preparation** - **Service order creation**: A service order is created with the customer's details, vehicle information, requested services and any additional notes. This helps streamline the en tyre process by having all necessary details pre-prepared. - **Parts and tool availability check**: For each job, service planners check if the required parts and tools are available or if they need to be ordered. This minimises delays once the car is in the workshop. - **Preliminary vehicle inspection**: Some centres conduct a brief inspection when the vehicle arrives to confirm the issue or identify additional needs that might impact the estimated completion time. **3. Work allocation to technicians** - **Assigning technicians by skill level**: Jobs are allocated based on the expertise required and the technician\'s specialisation. For example, complex engine diagnostics are assigned to senior technicians, while standard maintenance may be handled by junior technicians or apprentices. - **Job prioritisation**: Based on urgency, complexity and customer requirements, jobs are prioritised. For example, urgent repairs for fleet vehicles may take precedence over routine maintenance for private vehicles. - **Workflow balancing**: Service managers balance technician workloads to optimise efficiency, often using a centralised scheduling system that shows each technician's current assignments, availability and skill sets. **4. Workflow monitoring and adjustment** - **Tracking and adjusting schedules**: Service centres use software to track job progress in real-time, allowing managers to monitor completion rates, technician performance and any unexpected delays. - **Dynamic rescheduling**: If a job takes longer than expected or a technician becomes unavailable, managers may need to reallocate the job to another technician or adjust other appointments. This flexibility helps keep the workflow smooth despite potential disruptions. - **Break and downtime management**: Schedules include breaks to avoid technician fatigue, which is especially important for maintaining quality on intensive repairs. **5. Quality control and final checks** - **Inspection and testing**: After work completion, a quality control technician or the senior technician inspects the vehicle to verify that all work is done correctly and meets safety standards. - **Customer notification**: Once the service is complete, the customer is notified that their vehicle is ready for pick-up, or the service advisor may go over any additional findings or maintenance suggestions. **6. Documentation and record keeping** - **Service documentation**: Detailed service records are updated in the system, including parts used, labour hours and specific tasks completed. This is critical for maintaining an accurate history for the customer and for any future reference. - **Billing and invoicing**: Once the service is complete and inspected, the billing department prepares the invoice based on the labour and parts used, which is then presented to the customer upon pick-up. **Key tools for scheduling and allocation** - **Service management software**: This software aids in managing schedules, monitoring job progress and allocating resources effectively. Common features include calendar views, job tracking and real-time updates. - **Technician boards**: Some centres use visual boards to display technician assignments, progress on each vehicle and priority tasks, providing a quick, at-a-glance overview. - **Communication systems**: Effective communication tools (such as radios or intercoms) help service advisors, technicians and managers coordinate on urgent tasks, part needs and any unexpected issues. Overall, this structured approach ensures that work is systematically scheduled, efficiently allocated and carefully monitored, which helps maintain quality and optimise the customer experience at the service centre. In a vehicle service centre, work is scheduled, planned and allocated through a well-organised process to ensure efficiency, customer satisfaction and optimal resource utilization. Here's an overview of how it's typically done: ### 1. Appointment scheduling - **Booking and appointments**: Appointments are scheduled based on customer requests, often through multiple channels (online, phone, in-person). The service advisor or booking team reviews the customer's requirements, including the type of service or repair, urgency and availability of technicians and resources. - **Time estimation and slot allocation**: Different services have standardised time estimates (e.g., oil change = 30 minutes, brake repair = 1 hour). Using these estimates, the booking team assigns time slots that fit within the centre's daily or weekly schedule. ### 2. Work planning - **Job cards creation**: A job card is created for each scheduled service, detailing the work to be performed, vehicle details, customer notes and any specific requests. Job cards serve as a roadmap for technicians and ensure that all tasks and customer concerns are addressed. - **Resource and parts planning**: For each job, the required parts, tools and equipment are identified in advance. The parts department checks inventory and pre-orders any out-of-stock parts to avoid delays. This proactive planning ensures all resources are available on the day of service. - **Diagnostic and pre-service checklists**: For some jobs, a preliminary checklist may be completed to verify any issues reported by the customer. This could include a quick diagnostic or visual inspection to confirm the necessary repairs. ### 3. Work allocation - **Technician assignment**: Technicians are assigned tasks based on their expertise (e.g., electrical, transmission, engine repair), certification levels and current workload. Advanced service centres use scheduling software that automatically assigns jobs to the most suitable technician available at the time. - **Team-based allocation**: In larger centres, work might be divided among specialised teams, each handling specific types of repairs or maintenance (e.g., a diagnostics team, a repair team and a maintenance team). This specialization helps speed up service and improve quality. - **Priority and emergency job management**: Urgent or emergency jobs, such as breakdowns or vehicles with safety issues, are flagged as high priority and often assigned to technicians on standby. For urgent cases, non-priority scheduled jobs may be shifted to accommodate immediate needs. ### 4. Workflow monitoring and coordination - **Service advisors and workflow coordinators**: Service advisors or coordinators oversee job progress, track estimated completion times and communicate any delays or issues to customers. They adjust schedules as needed if unexpected repairs are identified or if technicians complete work faster than planned. - **Real-time updates and communication**: Some centres use software that tracks each job's status (e.g., "in progress," "awaiting parts," "ready for pickup"), allowing coordinators and advisors to provide real-time updates to customers. This software also helps manage technician workloads and highlights any delays. ### 5. Quality control and post-service checklist - **Final inspection**: Once the service or repair is completed, a senior technician or quality control team inspects the work to ensure it meets standards. They use a checklist to verify that all requested services were performed and that the vehicle is safe to return to the customer. - **Customer feedback and documentation**: After the service, the advisor reviews the completed job card with the customer, explaining the work done and any additional findings or future maintenance recommendations. Customer feedback may be gathered to help improve service quality. ### 6. Continuous improvement and follow-up - **Post-service follow-up**: Some centres follow up with customers a few days after service to check satisfaction, answer questions and schedule future maintenance if needed. - **Data analysis for process improvement**: Service centres often analyse scheduling and workload data to identify bottlenecks, optimise technician allocation and refine appointment scheduling for future efficiency. These steps ensure that work at a vehicle service centre is carefully scheduled, planned and allocated, leading to a smooth workflow, reduced wait times and high-quality service for customers. Why do garages inspect a vehicles? and what types of fault are they trying to identify ====================================================================================== Garages inspect vehicles to ensure safety, maintain performance and prevent potential breakdowns or costly repairs. Inspections help to identify both immediate issues and emerging problems that, if left unaddressed, could lead to safety hazards or expensive repairs further down the line. ### Reasons for vehicle inspections 1. **Safety**: Ensuring that essential systems like brakes, steering and lights are functioning correctly helps keep drivers, passengers and other road users safe. 2. **Compliance**: Many regions require vehicles to pass periodic inspections to meet safety and emissions standards. 3. **Preventative maintenance**: Inspections help with early detection of wear and tear issues, allowing for timely maintenance that can prevent more severe and costly problems in the future. 4. **Performance optimisation**: A well maintained vehicle performs better in terms of fuel efficiency, handling and overall reliability. ### Types of faults identified during inspections Garages look for a wide range of issues, generally focusing on key areas that affect safety, performance and legal compliance: 1. **Mechanical faults**: - **Engine issues**: These include misfires, low compression, oil leaks, or worn timing belts, which can lead to poor performance or engine failure. - **Transmission problems**: Gear slippage, delayed shifting, or fluid leaks may indicate transmission wear that can worsen if unaddressed. - **Suspension and steering**: Worn shock absorbers, struts, or steering components can compromise handling and safety, especially during manoeuvres or on rough roads. 2. **Electrical and battery faults**: - **Battery health**: Garages check the battery's ability to hold a charge and assess its overall condition, as weak batteries are a common cause of breakdowns. - **Lighting and signals**: Faulty headlights, brake lights and turn signals are both safety hazards and legal violations. - **Electrical systems**: Problems with sensors, wiring or the alternator can disrupt vehicle performance or cause warning lights to appear. 3. **Braking system faults**: - **Brake pads and rotors**: These are checked for wear and tear as worn brake components reduce stopping power and can lead to accidents. - **Brake Fluid**: Low or contaminated brake fluid can impact brake performance, so fluid levels and quality are inspected. 4. **Tyre and wheel issues**: - **Tyre tread and pressure**: Tyres are inspected for proper tread depth, wear patterns, and inflation, as worn or underinflated tyres affect traction and increase the risk of blowouts. - **Alignment**: Misalignment causes uneven tyre wear and handling issues, which can lead to safety concerns and increased tyre costs. 5. **Exhaust and emissions faults**: - **Exhaust leaks**: These can lead to harmful gases entering the vehicle's cabin, which is a serious health hazard. - **Emissions compliance**: Garages check the catalytic converter and emissions levels to ensure the vehicle meets environmental standards, which is often a legal requirement. 6. **Fluid levels and leaks**: - **Oil, coolant, transmission fluid, brake fluid**: Low or contaminated fluids can cause engine overheating, transmission issues or brake failure. Inspecting and replenishing these fluids prevent wear and protect critical components. By regularly inspecting these areas, garages help ensure vehicles are safe, efficient and legally compliant, while also helping drivers avoid more severe issues through proactive maintenance. What is the process for inspecting a car and identifying faults =============================================================== The process of inspecting a car and identifying faults involves a structured series of steps to ensure a thorough check of all major systems and components. Here's a breakdown of this multi-step inspection process: **1. Initial consultation and symptom inquiry** - **Customer interview**: The service advisor or technician talks with the customer to understand specific concerns, symptoms, or performance issues they have noticed, such as unusual noises, warning lights or handling problems. This input helps guide the inspection. - **Review vehicle history**: If available, the vehicle's maintenance history is reviewed to check for recurring issues or any recently completed work that might be relevant. **2. Visual inspection** - **Exterior check**: The technician inspects the vehicle's exterior for any visible damage (dents, scratches, rust) and checks the condition of components like lights, mirrors and wipers. - **Under the hood**: A preliminary look under the hood assesses the engine bay for signs of leaks (oil, coolant), corrosion, damaged belts and fluid levels (oil, brake fluid, coolant, windshield washer fluid). The technician checks for loose or damaged components that could indicate underlying issues. - **Undercarriage inspection**: If the vehicle is lifted, the technician checks the undercarriage for leaks, worn or damaged suspension parts and exhaust system integrity. **3. Diagnostic scanning** - **Onboard diagnostics (OBD-II) scan**: For vehicles with onboard diagnostics, a technician connects an OBD-II scanner to retrieve error codes from the car's computer. These codes indicate issues with specific systems, such as the engine, transmission or emission controls. - **Advanced diagnostic tools**: Some centres use specialised diagnostic software and tools that can give deeper insights, testing sensors, actuators and individual components within complex systems (like ABS, airbag and stability control systems). **4. Mechanical and functional inspection** - **Engine performance and components**: The technician starts the engine to listen for unusual noises and tests the throttle response. Components like the air filter, spark plugs, fuel injectors and timing belt are checked as needed. - **Battery and electrical system**: A battery test checks voltage, charging capacity and alternator function. Electrical connections are inspected and major components (like lights, windscreen wipers and horn) are tested. - **Fluid checks**: In addition to fluid levels, the technician inspects the condition and quality of each fluid (e.g. colour, presence of debris in oil or coolant), as contamination can signal internal issues. **5. Brake and suspension inspection** - **Brake system**: The technician examines the brake pads, rotors, callipers, brake lines and brake fluid. Brake wear is measured to determine if replacement is necessary and any signs of vibration, squeaking or uneven wear are noted. - **Suspension and steering**: Shock absorbers, struts, control arms and bushings are visually and physically inspected for wear, leaks or damage. Steering components, including the power steering fluid level and joints, are checked to ensure safe handling and stability. **6. Tyre and wheel inspection** - **Tread depth and condition**: Tyre tread depth and overall condition are checked, along with any signs of uneven wear, cracks or bulges. Uneven wear patterns can indicate alignment or suspension issues. - **Alignment and balance**: If necessary, the wheels are checked for alignment and balanced to prevent uneven tyre wear, vibration and handling issues. **7. Road test** - **Test drive**: A road test allows the technician to assess real world performance, testing for issues like abnormal noises, vibrations, braking efficiency, acceleration and transmission shifting. - **Evaluating specific symptoms**: During the drive, the technician replicates any customer reported issues (e.g. steering drift, transmission slip) to confirm and diagnose them accurately. **8. Analysis and fault identification** - **Cross referencing findings**: The technician analyses all gathered data, error codes and inspection notes to determine the root causes of any detected issues. - **Comprehensive inspection report**: A report is generated, listing each identified issue, the severity of the fault and recommended actions. The report may include photos or descriptions of parts that need replacement. **9. Consultation with customer** - **Report explanation**: The technician or service advisor explains the findings to the customer, prioritising critical safety repairs and discussing preventative maintenance items. - **Estimate for repairs**: A cost estimate is provided, detailing parts, labour and any additional recommendations for optimal vehicle performance. **Summary of key tools and techniques** - **Diagnostic scanners** for retrieving error codes. - **Multimeters** and **battery testers** for electrical inspections. - **Fluid testers** to assess quality and contamination. - **Tyre tread gauges** and **brake callipers** for measuring wear. - **Visual and physical inspection tools** (flashlights, creepers, lifts). This comprehensive process helps ensure a thorough and accurate diagnosis, allowing for efficient and targeted repairs, ultimately enhancing vehicle reliability and safety. What tools and equipment are required when inspecting a vehicle =============================================================== When inspecting a vehicle, mechanics and technicians use various tools and equipment to diagnose and assess its condition accurately. These tools help identify mechanical, electrical and safety issues to ensure the vehicle is roadworthy. Here are some essential tools and equipment commonly used in vehicle inspections: ### 1. Diagnostic tools - **OBD-II Scanner**: Connects to the vehicle's onboard diagnostics system to read error codes from the engine, transmission and other electronic systems. - **Multimeter**: Measures voltage, current and resistance, essential for diagnosing electrical issues such as battery and alternator health, wiring problems, and sensor issues. - **Battery tester**: Checks the battery's voltage and load capacity to determine if it needs to be replaced. ### 2. Mechanical inspection tools - **Torque wrench**: Ensures bolts on critical parts like brakes and suspension are tightened to manufacturer specifications. - **Compression tester**: Measures the compression levels in each engine cylinder to assess the engine's health. - **Stethoscope**: Allows mechanics to listen for unusual noises in areas like the engine, transmission and other moving parts, helping to identify potential issues. - **Brake fluid tester**: Determines if brake fluid has absorbed moisture, which can reduce braking efficiency and lead to corrosion in the brake system. ### 3. Visual inspection equipment - **Inspection mirror**: Helps view hard-to-see areas, such as behind engine components or under the chassis. - **Flashlight/LED Light**: Essential for checking dark or enclosed areas, like inside the engine bay or under the vehicle. - **Creeper**: A low, wheeled platform that allows mechanics to slide under vehicles easily for inspecting the undercarriage. ### 4. Lifting equipment - **Hydraulic lift or jack**: Used to elevate the vehicle, providing access to the undercarriage, suspension, exhaust and other components. - **Jack stands**: Provide stable support for a vehicle when it is lifted, ensuring safety during inspection and repair. ### 5. Tyre and alignment tools - **Tread depth gauge**: Measures tyre tread depth to determine if tyres need replacement. - **Tyre pressure gauge**: Checks for proper tyre inflation, as under or over inflated tyres can lead to handling issues and uneven tyre wear. - **Wheel alignment machine**: Measures and adjusts the vehicle's alignment angles, including camber, caster and toe, to ensure proper handling and tyre wear. ### 6. Fluid inspection tools - **Fluid extractor**: Removes fluid samples from reservoirs for testing, particularly useful for oil, coolant and transmission fluid. - **Coolant hydrometer**: Checks the coolant's freeze point and concentration, ensuring the cooling system is protected in all weather conditions. ### 7. Emissions testing equipment - **Gas analyser**: Tests exhaust gases for pollutants like carbon monoxide (CO), hydrocarbons (HC) and nitrogen oxides (NOx) to ensure compliance with emissions standards. - **Smoke machine**: Introduces smoke into the vehicle's intake system to detect leaks in hoses, manifolds and other vacuum-related parts. ### 8. Additional inspection tools - **Paint thickness gauge**: Measures the thickness of paint, which can indicate whether a car has been repainted after an accident. - **Infrared thermometer**: Used to check temperatures in various components, such as the radiator and brake system, to ensure they're operating within a safe range. By using these tools, mechanics can conduct a thorough inspection, covering mechanical, electrical, safety and emissions-related components. This comprehensive approach allows for early detection of issues, ultimately improving vehicle safety and performance. What is the impact of delays when completing servicing, maintenance or repair of vehicles ========================================================================================= Delays in completing servicing, maintenance or repairs can have significant impacts on both customers and the vehicle service centre. These impacts affect customer satisfaction, operational efficiency, financial outcomes and even safety. Here's a closer look at the key impacts: **1. Customer dissatisfaction and trust issues** - **Inconvenience for the customer**: Delays disrupt customers' schedules and may force them to seek alternative transportation, which can be costly and inconvenient. - **Decreased trust in the service centre**: Repeated or unexplained delays can erode customer trust, making them less likely to return and more likely to leave negative reviews, which affects the service centre\'s reputation. - **Reduced customer loyalty**: Dissatisfied customers may seek out other service providers who can offer faster or more reliable turnaround times. **2. Financial losses** - **Reduced revenue**: Delays can decrease the number of vehicles a service centre can handle, leading to missed opportunities to service additional clients and impacting overall revenue. - **Additional labour costs**: If technicians have to work overtime to compensate for delays, labour costs increase. Additionally, if delays result from misdiagnosed issues, the time spent correcting these may not be billable, leading to absorbed costs. - **Potential for discounts or compensation**: Some service centres may offer discounts or complimentary services to compensate for delays, which also impacts profitability. **3. Operational backlog and resource mismanagement** - **Overcrowded service bay**: Prolonged repair times can cause bottlenecks, creating a backlog of vehicles awaiting service and increasing wait times for new clients. - **Inefficient use of resources**: Delays in parts procurement, diagnostics, or technician availability can disrupt the workflow, leading to underutilized or idle technicians and equipment, ultimately reducing productivity. - **Impact on scheduling**: Scheduling becomes more challenging, as delayed vehicles need to be rebooked, pushing back appointments for other customers and creating a chain reaction of delays. **4. Negative impact on employee morale and productivity** - **Increased workload and stress**: Delays add pressure on technicians and service advisors to work faster, which can lead to errors and reduce job satisfaction. - **Lowered morale**: Frequent delays may frustrate technicians and staff, as they deal with dissatisfied customers, tight deadlines and potential overtime. This can contribute to burnout and reduced productivity over time. - **Decreased quality of work**: Rushed jobs due to backlog or re-prioritising urgent work can reduce attention to detail, leading to potential errors, safety issues, or future breakdowns. **5. Risk of compounded vehicle issues and safety concerns** - **Worsening of existing issues**: Delays can lead to minor problems worsening over time, causing more extensive (and costly) damage. For instance, a delayed oil change can lead to engine wear, or postponed brake repairs may result in total brake failure. - **Increased accident risk**: Safety issues, such as brake problems or tyre wear, can compromise vehicle safety if left unaddressed. Delays in repairs may increase the likelihood of accidents, endangering drivers and other road users. - **Higher repair costs**: Delayed maintenance often results in more extensive repairs, which can significantly increase the final bill for the customer. **6. Inventory and supply chain management issues** - **Parts shortages**: Delays may lead to part orders being deferred or mismanaged, affecting stock levels and creating longer wait times for parts in future repairs. - **Supplier relationship strain**: Frequent last-minute requests or adjustments can strain relationships with suppliers, potentially affecting future availability or pricing. **7. Reputational damage and competitive disadvantage** - **Negative reviews and word of mouth**: Dissatisfied customers may share their experiences through reviews and social media, which can harm the centre's reputation and deter potential new clients. - **Competitive disadvantage**: In an industry where convenience and reliability are highly valued, service centres with delays risk losing customers to competitors with faster and more reliable turnaround times. **8. Insurance and fleet management complications** - **Increased insurance premiums for fleet owners**: Fleet owners who experience delays in maintenance may face higher insurance premiums due to the increased risk of breakdowns or accidents. - **Missed fleet service agreements**: Fleet managers often have service agreements requiring a minimum uptime. Delays in service centres can result in penalties, loss of contracts, or added costs for fleet companies. **Summary** Delays when completing vehicle servicing or repairs can have a knock on effect to customer satisfaction and the financial health and operational efficiency for the service centre. To mitigate these impacts, service centres should focus on efficient scheduling, proactive parts management and clear communication with customers detailing realistic timelines for completion of services or repairs. What causes delays to the completion of vehicle servicing, maintenance or repair? ================================================================================= Several common factors can cause delays in completing vehicle servicing, maintenance, or repairs. These delays can stem from issues related to parts availability, diagnostic challenges, unexpected repair needs, or operational inefficiencies. Here's a breakdown of the primary causes: **1. Parts availability issues** - **Shortage or lack of parts**: Specific or uncommon parts may not be in stock, requiring orders from suppliers, which might take days or even weeks depending on the source. - **Shipping delays**: Parts ordered from remote locations or international suppliers may face shipping delays due to logistical issues, weather conditions, or customs processing. - **Wrong parts or quality issues**: Sometimes, the wrong part is delivered or the part doesn't meet quality standards, necessitating reorders and further delaying the repair process. **2. Unexpected or complex diagnoses** - **Hidden or complicated faults**: Initial assessments might not uncover the full extent of a vehicle's issues, leading to additional diagnostic time or the discovery of secondary issues that require further inspection. - **Electrical and computer diagnostic challenges**: Modern vehicles often require advanced diagnostics, particularly for issues related to computer systems, sensors and electronic components. These can be time-intensive and may need specialist equipment or software updates. - **Multiple issues in one vehicle**: If a vehicle has multiple problems (e.g., transmission issues along with engine troubles), diagnosing and addressing each problem can significantly extend service time. **3. Availability of suitably skilled employees** - **Shortage of skilled technicians**: Complex issues may require specialised technicians who may be unavailable due to high demand or staffing shortages. - **High technician workload**: If technicians are overloaded with other jobs, scheduling becomes tight and the availability of qualified technicians for specific repairs may be limited. - **Training needs for new models**: Some vehicle models or new technologies may require additional training or certifications, limiting the number of qualified technicians who can work on certain vehicles or systems. **4. Additional or unforeseen repairs** - **Secondary repairs discovered during service**: Routine maintenance can uncover other issues, such as worn brake pads, fluid leaks, or faulty suspension components. Addressing these additional repairs requires more time, parts and technician availability. - **Customer authorisation delays**: For unexpected repairs, customers may need to be contacted for authorisation and delays in reaching them or obtaining their approval can hold up the work. **5. Operational and workflow inefficiencies** - **Scheduling conflicts and overbookings**: Poor scheduling practices, such as overbooking or underestimating service times, can lead to a backlog of vehicles awaiting service. - **Lack of organised workflow**: Disorganised workflows, ineffective communication between service advisors and technicians, or inefficient workspace setups can slow down progress on each job. - **Inadequate tools or equipment**: Certain repairs require specific tools or diagnostic equipment. If these are unavailable or need repairs, it can delay the job until the tools are accessible. **6. External factors and supply chain disruptions** - **Weather conditions**: Severe weather can impact both customer drop-offs and parts shipments, particularly if there are road closures or restricted access to service centres. - **Supply chain disruptions**: Industry wide issues like factory shutdowns, labour strikes, or shortages in materials can affect the availability of parts and supplies, leading to widespread delays in vehicle repair timelines. **7. Customer related delays** - **Late drop-offs or pick-ups**: Customers may not drop off their vehicles on time, pushing back the start time of their service. Additionally, if they are late for pick-up, it can delay the release of the service bay or parking space for the next job. - **Changes to service requests**: Customers may add new service requests after the initial booking, which can extend the time needed to complete the work. - **Inaccurate information from customers**: Misreporting symptoms or omitting important information can lead to incorrect initial diagnoses, requiring additional time to identify the real problem. **8. Quality control and testing delays** - **Additional testing and quality control**: Some repairs or complex diagnostics require road testing or multiple checks to ensure the issue is fully resolved, which can add time to the overall service duration. - **Recurrence of faults during testing**: If a problem persists after the repair, technicians may need to revisit the work, perform additional diagnostics, or test new solutions, adding more time. **9. Warranty and insurance related delays** - **Approval delays from warranty or insurance providers**: When repairs are covered by warranties or insurance, the service centre may need prior approval, which can take time, particularly if the provider requires detailed assessments. - **Paperwork requirements**: Extended paperwork processes, such as submitting diagnostic reports, cost estimates and repair summaries, can delay the start or completion of repairs covered by third-party providers. **10. Unanticipated equipment or facility downtime** - **Equipment malfunctions**: Essential equipment (like lifts, diagnostic machines, or alignment tools) may require maintenance or repair, slowing down work on vehicles that need those tools. - **Power or internet outages**: In cases where diagnostic or communication systems are internet-dependent, outages can prevent diagnostics, order placements, or customer communication, adding time to the process. Delays to completion of vehicle servicing, maintenance or repairs are often caused by a combination of issues relayed to parts, unexpected repairs, diagnostic complexity and operational factors. Many vehicle service centres address these challenges by optimising scheduling, maintaining open communication with customers and by investing in skilled staff, digital tools and up to date equipment to minimise these delays. What is the impact of not having required parts in stock? ========================================================= Not having required parts in stock can significantly impact service centres, leading to delays, increased costs, and customer dissatisfaction. Here's how these factors play out: ### 1. Customer dissatisfaction and loss of trust - When parts are not immediately available, repair times increase, often leading to delays in returning vehicles to customers. This can create frustration, as customers may have to arrange alternative transportation for a longer period. Prolonged wait times can erode customer trust and satisfaction, impacting their likelihood of returning for future service or recommending the centre to others. ### 2. Operational inefficiency - Technicians often need to stop working on a vehicle if they encounter missing parts, leading to workflow disruptions and scheduling inefficiencies. Technicians may be forced to move on to other jobs or wait idly, which can reduce overall productivity and lead to costly labour inefficiencies within the service centre. ### 3. Increased costs and lost revenue - Service centres may face increased costs when expedited shipping is needed for essential parts to reduce customer wait times. This additional cost can cut into profit margins or lead to higher prices for customers, depending on the policy of the service centre. Additionally, vehicles taking up repair bays while waiting for parts reduce the capacity to serve other clients, limiting revenue potential. ### 4. Negative impact on business reputation - Consistent delays due to unavailable parts can lead to a negative reputation, particularly in today's review-driven market. Dissatisfied customers are more likely to leave negative reviews or discourage others from using the service, which can impact the service centre's ability to attract new business. ### 5. Supply chain challenges - Relying on just-in-time (JIT) ordering without maintaining a base inventory of commonly used parts can backfire if there are supply chain issues. Delays from suppliers, especially with complex or specialised parts, can extend repair times significantly. This has been particularly challenging in recent years, where global supply chain disruptions have impacted parts availability in various industries. ### Managing inventory strategically To mitigate these impacts, service centres often use historical data to keep frequently used parts in stock, which can balance inventory costs with service efficiency. Additionally, strong supplier relationships and flexible stocking policies can help prevent or reduce delays. In summary, while it can be costly to maintain a large inventory, having essential parts in stock supports operational efficiency, customer satisfaction and overall business success. When might additional parts need to be ordered to complete a service or repair? =============================================================================== Additional parts might need to be ordered during a vehicle service or repair in a variety of situations, typically when unexpected issues are identified, or the service requires unique parts. Here are some common instances where ordering additional parts becomes necessary: **1. Discovery of additional faults during service** - **Hidden or secondary issues**: During routine maintenance or repair, a technician may discover unexpected issues that need immediate attention. For example, while replacing brake pads, they might find worn brake rotors that also require replacement. - **Wear and tear components**: During inspections, certain parts might show signs of advanced wear (e.g., belts, hoses, or gaskets), which, while not initially reported, should be replaced to avoid future breakdowns. **2. Diagnosing complex problems** - **Further diagnostic requirements**: For complex systems, especially electrical or computerised components, diagnosing one issue may reveal other parts in the system that need replacement. For example, if an alternator issue is discovered, there might also be damaged wiring or connectors requiring replacement. - **Interdependent components**: In cases where multiple components work together, one failure may have led to wear or damage on another. For example, a failing water pump might also mean a worn timing belt, necessitating both parts for a reliable fix. **3. Customer requested additions** - **Changes in service scope**: Customers may request additional services or upgrades after the vehicle is already being serviced. If they decide to replace a set of worn tyres, upgrade headlights, or add a new battery, additional parts will need to be ordered if they aren't readily available. - **Upgrades and customisations**: Some customers may request upgraded parts or custom components (like performance brakes or specialty exhaust systems), which generally require special ordering. **4. Unexpected part defects or damage** - **Damaged parts on arrival**: Sometimes, ordered parts arrive damaged or are of unsatisfactory quality, requiring a re-order. This could be due to poor packaging, handling during transit, or manufacturing issues. - **Incorrect part shipment**: Occasionally, the wrong part might be shipped due to a catalogue error or miscommunication with the supplier, leading to delays while waiting for the correct part. **5. Manufacturer or model specific parts** - **Specialised or uncommon parts**: Certain makes and models, particularly luxury or rare vehicles, may require parts that aren't commonly stocked and need to be ordered from specialised suppliers or directly from the manufacturer. - **Older or classic vehicles**: Parts for older models, vintage, or classic cars often need to be ordered from specialty suppliers and sometimes may even need to be custom made due to limited availability. **6. Parts not commonly stocked** - **Low demand parts**: Some parts that are only occasionally needed, such as specific sensors or specialised bolts, may not be kept in regular inventory due to low demand and must be ordered as needed. - **Non-standard components**: Non-standard parts or modifications, such as oversized tyres, custom suspension components or aftermarket upgrades, often require ordering because they don't align with the typical service parts inventory. **7. Warranty and recall related parts** - **Manufacturer recalls**: During a service, a vehicle might be identified as subject to a recall, in which case the centre may need to order specific parts provided by the manufacturer to address the recall. - **Warranty claims**: When repairs are covered under warranty, specific parts may need to be sourced from the manufacturer to ensure they meet warranty requirements, even if alternatives are available. **8. Additional parts for extensive repairs** - **Structural or safety components**: For major repairs following accidents or extensive wear, additional structural parts (e.g., body panels, frames, or reinforcements) might need to be ordered to complete the repair fully and safely. - **Seals, gaskets and hardware**: Complex repairs, such as those involving engine or transmission disassembly, often require new seals, gaskets, or specific hardware that might not be anticipated until the unit is fully opened and inspected. **9. Parts needed for quality control or compliance** - **Safety compliance parts**: If a part required to pass a safety or emissions inspection is missing or fails to meet standards, it will need to be replaced to make the vehicle compliant, prompting an order if not readily available. - **Quality control findings**: After the initial repair or service, quality control checks may reveal that certain parts, such as sensors or fasteners, need replacement for optimal performance, resulting in a parts order to complete the job thoroughly. **Summary** Service centres often encounter the need for additional parts when unexpected issues arise or when specific, hard-to-find parts are required. Efficient parts ordering processes, combined with clear communication with customers, help to minimise the impact of these additional requirements on service timelines. How does a vehicle warranty work? ================================= A vehicle warranty is a type of guarantee provided by a manufacturer or dealer, covering the cost of certain repairs or replacements if the vehicle experiences specific issues within a set period or mileage limit. Warranties offer peace of mind to buyers by ensuring that defects or malfunctions due to manufacturing faults are addressed without additional cost. Here's a breakdown of how warranties typically work: ### 1. Types of vehicle warranties - **Basic or bumper-to-bumper warranty**: Covers most parts of the vehicle (excluding regular wear and tear items) for a specific period of time or specified mileage, for example, 3 years or 36,000 miles. It's the most comprehensive warranty, covering issues with electronics, suspension and more. - **Powertrain warranty**: Covers the engine, transmission, and drivetrain, which are costly to repair if they fail. Powertrain warranties usually last longer than bumper-to-bumper warranties. - **Corrosion/rust warranty**: Protects against rusting and corrosion of the vehicle's body panels. Coverage duration varies, but rust protection can sometimes extend up to 10-12 years. - **Emissions warranty**: Covers repairs related to the emissions system, mandated by the government to ensure compliance with environmental standards. Coverage is usually separate and can last longer in some regions due to legal requirements. ### 2. Warranty coverage and exclusions - **What's covered**: Warranties typically cover repairs and replacements due to manufacturing defects, such as issues with the engine, electrical components, or transmission. - **Exclusions**: Wear and tear items like tires, brake pads, filters and fluids are generally not covered. Damage from misuse, accidents, or modifications (like aftermarket parts) can also void warranty coverage. Routine maintenance, such as oil changes are not covered by warranties. ### 3. Duration and limits - Warranties have both a time and mileage limit, whichever comes first. For example, a 3-year/36,000-mile warranty ends after three years or 36,000 miles, whichever the vehicle reaches first. - Some components, like powertrain parts, may have extended warranties, potentially up to 5-10 years or 100,000 miles. ### 4. How claims are handled - **Authorised repair**: To make a claim, the owner typically brings the vehicle to an authorised dealership or service centre. Only these locations can perform repairs under warranty to ensure compliance with the manufacturer's standards. - **Verification**: The service team assesses if the issue is covered under warranty. If it's a manufacturing defect, they proceed with the repair or replacement. - **No cost repairs**: If covered, the repair or replacement is completed at no cost to the owner, except for possible small fees or deductibles associated with some extended warranties. ### 5. Extended and third party warranties - **Extended warranties**: Many manufacturers or dealerships offer extended warranties for purchase, which extend coverage beyond the original warranty period. These may cover major systems like the powertrain or bumper-to-bumper items. - **Third party warranties**: These are provided by companies other than the manufacturer, offering customised coverage plans. Third party warranties can sometimes be more flexible but may have specific repair location requirements. Vehicle warranties help manage repair costs and keep vehicles in good condition, especially for major mechanical issues. They also encourage regular maintenance, as staying within service requirements can prevent the warranty from becoming void. Do EVs have a specific warranty =============================== Yes, electric vehicles (EVs) come with specific warranties that cover unique components essential to their operation, particularly the battery and electrical drivetrain. These warranties are designed to address the different needs and wear patterns of EVs compared to traditional gas-powered vehicles. Here's a breakdown of the typical warranty coverage for EVs: ### 1. Battery warranty - **Battery and battery components**: Most EV manufacturers offer warranties specifically for the battery pack, which is often the costliest part of an EV. These warranties generally cover battery failure, significant degradation and manufacturing defects. - **Duration**: Battery warranties typically last 8 years or 100,000 miles, though some brands may extend this further. For instance, Tesla and Hyundai offer 8-year warranties, while Nissan's warranty extends to 150,000 miles in some regions - **Degradation coverage**: Some warranties cover a minimum retention rate for battery capacity, often around 70% of the original capacity within the warranty period. This ensures that the battery should not degrade beyond a certain level during normal use. ### 2. Powertrain and drivetrain warranty - EVs usually have warranties for the electric motor, transmission (if applicable) and drivetrain components. These warranties are often the same duration as the battery warranty, covering components like the motor and other key electric drivetrain parts. - **Coverage Period**: Many manufacturers offer 8-year/100,000-mile warranties for these components, but the specific terms can vary. ### 3. Basic/bumper-to-bumper warranty - Similar to warranties for traditional vehicles, EVs come with a basic or bumper-to-bumper warranty, typically covering everything from the car's electrical systems and entertainment features to cosmetic issues and other manufacturing defects. This warranty generally lasts around 3--5 years or 36,000--60,000 miles. ### 4. Corrosion and rust warranty - EV warranties often include coverage for body rust and corrosion, which is comparable to that offered for gasoline vehicles. This coverage typically extends to 5--12 years, depending on the manufacturer. ### 5. Extended and optional warranties - Some EV manufacturers offer extended warranties that cover the battery and other EV-specific components for a longer period. These can be useful for buyers who plan to keep the vehicle for many years and want peace of mind about battery longevity. Overall, the warranties provided for EVs are designed to instil confidence in EV technology, especially given concerns over battery degradation and the unique structure of electric drivetrains. This specialised warranty coverage helps to make EV ownership more affordable and secure by addressing both high cost components and any expected degradation. Describe parts that are eligible to be changed under the terms of a warranty and what parts are not covered by the warranty =========================================================================================================================== Warranties on vehicles usually cover defects in materials or workmanship in specific parts, particularly those integral to the vehicle's functionality, while excluding parts that wear out through regular use or that require replacement as part of routine maintenance. Here's a detailed look at which parts are typically eligible for replacement under warranty and which are not: **Parts typically covered by warranty** 1. **Engine components** - **Cylinder block and heads**: Includes the actual metal components of the engine's main structure. - **Internal engine parts**: Camshaft, crankshaft, pistons, timing gears and other moving parts are covered if they fail due to a manufacturing defect. - **Turbocharger/supercharger**: If the vehicle includes a factory-installed turbo or supercharger, these are often covered as part of the powertrain warranty. 2. **Transmission and drivetrain components** - **Transmission**: The en tyre transmission system, including internal parts like gears, bearings and clutch plates, is covered if defects are found. - **Drive shafts and axles**: This includes components that transfer power from the engine to the wheels, like drive shafts and CV joints. - **Differentials and transfer case**: The transfer case and differentials in 4WD or AWD vehicles are typically included in powertrain warranties. 3. **Electrical system components** - **Alternator and starter motor**: These parts are covered if there's a defect in manufacturing that causes premature failure. - **Electrical wiring and computer modules**: Major electronic systems, including the vehicle's main computer, wiring and control modules, are usually covered. - **Factory installed audio and navigation systems**: Defects in these systems, including infotainment or navigation screens, are typically covered under a new vehicle warranty. 4. **Air conditioning and heating system** - **Compressor and condenser**: Factory-installed air conditioning systems and key components like the compressor, condenser and evaporator are covered. - **Blower motor and HVAC controls**: Faults in the HVAC system's blower motor or control panel are usually included. 5. **Fuel system** - **Fuel pump and injectors**: These components are covered if they fail due to defects. - **Fuel delivery lines**: Fuel lines that transfer fuel from the tank to the engine are covered if they corrode or break due to manufacturing issues. 6. **Suspension components** - **Struts, shock absorbers and springs**: Suspension parts are usually covered if they fail prematurely, though wear from normal use may sometimes be excluded. - **Control arms and bushings**: Defects in control arms, ball joints and bushings that affect vehicle handling are covered. 7. **Emissions and exhaust system** - **Catalytic converter**: This part, vital to emissions control, is often covered under both general and extended emissions warranties. - **Oxygen sensors**: These are covered as they play a critical role in emissions control. - **Exhaust manifold**: The manifold, along with some parts of the exhaust system, may be included if it fails due to manufacturing issues. **Parts not typically covered by warranty** 1. **Wear and tear items** - **Brakes**: Brake pads, rotors and drums are typically excluded, as they wear out through normal use. Callipers may sometimes be covered under specific conditions. - **Tyres**: Tyres are not usually covered by vehicle warranties; instead, they are covered by a separate tyre manufacturer warranty. - **Wiper blades**: As parts that wear out regularly, wiper blades are not covered. 2. **Fluids and filters** - **Engine oil and coolant**: Oil changes, coolant refills and related fluids are considered regular maintenance items and are not covered. - **Air, oil and fuel filters**: Filters require regular replacement as part of maintenance and are generally not covered. 3. **Battery** - **Hybrid or electric vehicle batteries**: High voltage batteries in hybrid or electric vehicles often have separate, extended warranties but are not covered under standard vehicle warranties. - **Regular 12-Volt Battery**: Traditional batteries usually have shorter, separate warranties (e.g., two years) and are not covered by the standard vehicle warranty. 4. **Exterior and interior parts subject to wear** - **Paint and bodywork**: Most warranties cover rust-through but not surface rust, fading, or scratches from wear. - **Upholstery and interior trim**: Seats, carpets and interior panels are not covered for general wear, stains, or damage from usage. - **Glass components**: Windshields and windows are generally excluded from warranty coverage unless the damage is due to a manufacturer defect. 5. **Alignment and tyres** - **Wheel alignment and balancing**: Regular alignment and balancing are part of maintenance, though alignment may be covered within a certain timeframe if it was incorrect from the factory. - **Tyre wear**: Covered by a separate warranty through the tyre manufacturer rather than the vehicle warranty. 6. **Light bulbs and fuses** - **Standard bulbs and fuses**: Headlights, taillights and interior bulbs are not covered, as they are expected to require periodic replacement. - **LED and HID systems**: Although standard bulbs are excluded, some manufacturers cover LED and HID systems under specific terms due to their longevity. 7. **Damage from improper use or lack of maintenance** - **Neglect or improper maintenance**: Parts that fail due to a lack of maintenance or misuse, such as missed oil changes or overloading the vehicle, are not covered. - **Aftermarket modifications**: Parts damaged as a result of aftermarket modifications (e.g., performance enhancements or lift kits) are excluded from warranty coverage. - **Accidental or environmental damage**: Damage from accidents, weather, or environmental factors (like corrosion from road salt) is also excluded. ### Summary Vehicle warranties are designed to cover components that may fail due to manufacturing or material defects, especially those related to critical systems like the engine, transmission and electronics. Items subject to routine wear, or those requiring regular maintenance, are generally excluded, as are components that degrade due to normal usage or external factors. Why do we need to invoice clients? ================================== Invoicing clients is essential for businesses to maintain accurate financial records, ensure timely payment, and provide clients with clear documentation of services or products provided. Here are the key reasons why invoicing is important: ### 1. Financial record keeping - Invoices serve as official records of sales or services rendered, helping businesses track revenue, manage cash flow and prepare for tax filings. Proper invoicing ensures there is a documented trail of income, which is necessary for auditing and accounting. ### 2. Legal documentation - An invoice is a legally binding document that details the agreement between the business and the client regarding payment. It specifies the service or product provided, amount due and payment terms, which can protect both parties in case of disputes. ### 3. Payment tracking and timely collection - Invoicing clarifies payment expectations, helping ensure clients understand the amount due and the due date. Clear invoicing also assists businesses in tracking outstanding payments and sending reminders, which is crucial for maintaining steady cash flow. ### 4. Transparency and client trust - Providing an itemised invoice helps clients understand exactly what they're paying for, promoting transparency and fostering trust. This transparency can improve customer satisfaction by giving clients confidence in the pricing and services received. ### 5. Professionalism and branding - Invoices offer an opportunity to present a professional image through consistent branding, including logos and company details. A well organised invoice reflects the business\'s professionalism and attention to detail, which can positively impact the client relationship. In summary, invoicing is a critical tool that supports financial management, legal protection, customer relations and business professionalism, all of which contribute to the overall success and reliability of a business. What is the process for invoicing and taking payment after a service or repair has been completed ================================================================================================= The invoicing and payment process after a vehicle service or repair typically involves several steps, from preparing a detailed invoice to collecting payment from the customer. Here's a breakdown of the process: **1. Finalise the job and confirm completion** - **Verify work completion**: The service advisor or technician ensures that all requested repairs or services are complete, including any additional work that was authorised during the process. - **Quality check**: Some service centres perform a final quality check or test drive (if necessary) to confirm the repairs are successful and the vehicle is functioning properly. **2. Prepare the invoice** - **Compile service and parts details**: The service advisor reviews the work order and compiles all parts used, labour hours and any additional fees or costs, including shop supplies or environmental fees. - **Itemise costs**: The invoice typically lists parts, labour charges, taxes and any discounts or warranties applicable to the work performed. This level of detail helps clarify costs for the customer and makes it easier to answer any questions about the charges. - **Apply discounts or promotions**: If any discounts (e.g., loyalty discounts, coupons) are applicable, these are deducted before finalising the invoice total. **3. Review the invoice with the customer** - **Explain the charges**: The service advisor goes over the invoice with the customer, explaining the work performed, the parts replaced and the total cost. This is an opportunity to answer any questions or concerns the customer may have. - **Present warranty information**: For parts and labour that come with warranties, the service advisor should inform the customer of these details, including warranty terms and duration. **4. Take payment** - **Present payment options**: The customer is informed of the accepted payment methods, which might include cash, credit/debit cards, bank transfers, or financing options. In some cases, fleet customers may have separate billing arrangements. - **Process payment**: - **In-person payment**: If the customer is paying in person, the payment is processed through a point-of-sale system for immediate authorisation. - **Online or remote payment**: Many service centres offer online or electronic payment options through email or SMS links, which allows the customer to pay before picking up the vehicle. - **Offer financing options**: For high cost repairs, financing options or instalment payment plans may be available, allowing customers to spread the payment over time. **5. Issue receipt and document payment** - **Generate and provide receipt**: Once payment is confirmed, the customer receives a receipt for the transaction, either as a printed copy or digitally via email or SMS. - **Update payment records**: The service centre updates its records to reflect that the job has been completed and paid for. This may also include updating the vehicle's service history for future reference. **6. Release the vehicle to the customer** - **Coordinate pickup**: The customer is notified that the vehicle is ready for pickup once payment is complete. This can be done via call, SMS, or email, depending on the customer's preference. - **Key handoff and final confirmation**: When the customer arrives, the service advisor or cashier confirms their identity, hands over the keys and provides any final instructions or recommendations for ongoing vehicle maintenance. **7. Follow up and record keeping** - **Maintain service records**: A record of the completed work and payment is stored in the service centre's database for future reference, aiding in warranty claims, future services, or customer inquiries. - **Follow up communication**: Some centres may follow up with the customer within a few days to ensure satisfaction with the service and offer a chance for feedback. This helps build customer loyalty and improve service quality. **Additional considerations** - **Insurance or warranty billing**: If the repair is covered by insurance or a third-party warranty provider, the service centre may directly bill the provider, requiring additional paperwork and authorisation from the insurer. - **Fleet or account billing**: For corporate clients or fleet accounts, the service centre may use monthly billing rather than immediate payment, invoicing the client for multiple services at once. Why is it important to have a smooth process for customers collecting their vehicle or having it returned to them? ================================================================================================================== Having a smooth, efficient process for customers to collect or have their vehicle returned after service or repair is important because it enhances customer satisfaction, builds trust, and ensures operational efficiency. Here's why these factors matter: ### 1. Customer satisfaction and convenience - A seamless process helps clients feel valued and reduces any frustration or inconvenience. When customers can quickly and efficiently pick up or receive their vehicle, it minimises disruption to their day and reinforces a positive experience with the service provider. ### 2. Builds trust and professionalism - A well organised return or pickup process demonstrates the business's professionalism and reliability, making customers more likely to return for future services. For example, if customers are promptly informed when their car is ready and provided with clear instructions, it shows attention to detail and respect for the customer\'s time, both of which are key to building trust. ### Streamlines operations and reduces bottlenecks - A smooth process also benefits the service centre's internal operations. When vehicle pickups and returns are handled efficiently, it allows the business to maintain workflow continuity without unnecessary delays. This reduces congestion in the service area and helps the business serve more customers, increasing overall capacity and revenue potential. ### 4. Promotes customer retention and 'word of mouth' referrals - An easy, customer friendly collection or return process can improve retention rates and encourage 'word of mouth' recommendations. Satisfied customers are more likely to share positive experiences with others, which can attract new clients and positively enhance the business's reputation. In summary, vehicle return or collection process is essential for enhancing customer experience, building trust, and maintaining operational efficiency, all of which contribute to long term business success. What is the process for a customer collecting their vehicle or having their vehicle returned to them? ===================================================================================================== The process for a customer collecting their vehicle or having it returned after service or repair generally involves steps to ensure that the work has been completed satisfactorily, payment has been processed and the customer receives any necessary information about their service. Here's a summary of the collection and return process: **1. Notification of completion** - **Contact the customer**: Once the service or repair is complete, the service centre contacts the customer (via phone, SMS, or email) to inform them that their vehicle is ready for collection or delivery. - **Provide essential details**: The customer is informed of any final charges, payment options and necessary paperwork they should bring (e.g., ID, insurance or authorisation forms if another person is picking up the vehicle). **2. Arrange payment if not already settled** - **Review invoice and payment options**: If payment has not been settled, the customer is informed of the total cost and the available payment options, such as credit/debit cards, cash or financing if applicable. - **Payment processing**: The payment can be handled either online (if the customer prefers remote payment) or in person at the service centre. Once payment is confirmed, a receipt is provided. **3. Customer collection process** - **Customer identity verification**: Upon arrival, the customer may need to provide identification to verify that they are the authorised person collecting the vehicle. - **Final review of work done**: The service advisor briefly reviews the service or repair details with the customer, explaining the work done, any replaced parts and any additional findings. They also go over any maintenance or warranty information. - **Provide documentation**: The customer receives a copy of the service invoice, receipts and any warranty information on the parts or services provided. **4. Vehicle handover** - **Inspect the vehicle with the customer**: In some cases, the service advisor might walk the customer to the vehicle, allowing them to inspect the work or the vehicle's overall condition. This is also an opportunity for the advisor to point out any future maintenance needs. - **Handover of keys and documentation**: The keys are handed to the customer and any additional instructions are provided, such as reminders for follow up maintenance or information on what to do in case of a warranty claim. **5. Vehicle return for remote delivery (if applicable)** - **Arrange delivery service**: If the customer opts for vehicle return, the service centre arranges for a staff member, third-party service or flatbed service (for long distances) to deliver the vehicle. - **Coordinate delivery time**: The customer is notified of the delivery time and any special instructions, such as where to meet or sign for the vehicle. - **Confirmation on delivery**: Upon arrival, the driver may request ID and confirm payment if not settled. The customer can inspect the vehicle before signing off on the receipt of delivery. **6. Post collection follow up** - **Service follow up**: Some service centres reach out a few days after the collection to ensure that the customer is satisfied and to address any questions or concerns they may have. - **Documentation and record keeping**: The completed service, payment details and any warranties are recorded in the customer's file for future reference, ensuring easy access to service history. By following these steps, the service centre ensures the customer has a smooth experience collecting or receiving their vehicle after maintenance or repair, reinforcing customer satisfaction and trust.