Operations Management (OPTS2001) PDF
Document Details
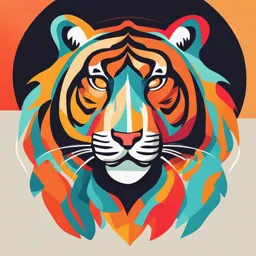
Uploaded by BlissfulFern3567
GITAM School of Business
Tags
Summary
This document provides an overview of Operations Management (OPTS2001) at GITAM School of Business, focusing on topics like productivity, job design, work study, and different techniques like operation process charts, flow process charts.
Full Transcript
Operations Management (OPTS2001) GITAM School of Business, Visakhapatnam Unit IV: Productivity Introduction Productivity is crucial to the welfare of industrial firm as well as for the economic progress of the country. High productivity refers to doing the...
Operations Management (OPTS2001) GITAM School of Business, Visakhapatnam Unit IV: Productivity Introduction Productivity is crucial to the welfare of industrial firm as well as for the economic progress of the country. High productivity refers to doing the work in a shortest possible time with least expenditure on inputs without sacrificing quality and with minimum wastage of resources. Introduction (cont’d) Work-study forms the basis for work system design. The purpose of work design is to identify the most effective means of achieving necessary functions. Work-study aims at improving the existing and proposed ways of doing work and establishing standard times for work performance. Work-study is encompassed by two techniques, i.e., method study and work measurement. Introduction (cont’d) “Method study is the systematic recording and critical examination of existing and proposed ways of doing work, as a means of developing and applying easier and more effective methods and reducing costs.” “Work measurement is the application or techniques designed to establish the time for a qualified worker to carry out a specified job at a defined level or performance.” Introduction (cont’d) Method study is concerned with the reduction of the work content and establishing the one best way of doing the job whereas work measurement is concerned with investigation and reduction of any ineffective time associated with the job and establishing time standards for an operation carried out as per the standard method. Productivity Productivity is the quantitative relation between what we produce and we use as a resource to produce them, i.e., arithmetic ratio of amount produced (output) to the amount of resources (input). Productivity can be expressed as: Productivity =Output ÷ Input Productivity (cont’d) Productivity refers to the efficiency of the production system. It is the concept that guides the management of production system. It is an indicator to how well the factors of production (land, capital, labour and energy) are utilized. Factors Influencing Productivity Factors influencing productivity can be classified broadly into two categories: (A) controllable (or internal) factors. (B) un-controllable (or external) factors. Controllable or Internal factors Product – extent to which it meets requirements. Plant and equipment – availability and reduction of idle time. Technology – automation. Material and Energy - reduce material and energy consumption. Human factors – motivation and training. Work methods – improvement in the way of doing things. Management style – communication, policy and procedures. Un-controllable or external factors Structural adjustments- include both economic and social changes. Economic changes that influence significantly are: (a) Shift in employment from agriculture to manufacturing industry, (b) Import of technology, and (c) Industrial competitiveness. Social changes such as women’s participation in the labour force, education, cultural values, attitudes are some of the factors that play a significant role in the improvement of productivity. Natural resources – manpower, land and raw materials Government and infrastructure – government policies ,transport, power, fiscal policies Total Productivity Measure (TPM) It is based on all the inputs. The model can be applied to any manufacturing organization or service company. Total productivity =Total tangible output ÷ Total tangible input Total tangible output = Value of finished goods produced + Value of partial units produced + Dividends from securities + Interest + Other income Total tangible input = Value of (human + material + capital + energy + other inputs) used. The word tangible here refers to measurable. The output of the firm as well as the inputs must be expressed in a common measurement unit. The best way is to express them in rupee value. Partial Productivity Measures (PPM) Depending upon the individual input partial productivity measures are expressed as: Partial productivity = Total output ÷ Individual input 1. Labour productivity = Total output ÷ Labour input Labour input is measured in terms of man-hours 2. Capital productivity = Total output ÷ Capital input 3. Material productivity = Total output ÷ Material input 4. Energy productivity = Total output ÷ Energy input One of the major disadvantage of partial productivity measures is that there is an over emphasis on one input factor to the extent that other input are underestimated or even ignored. Example 1 Example 2 Example 2 (cont’d) Example 2 (cont’d) JOB Design According to Michael Armstrong, "Job Design is the process of deciding on the contents of a job in terms of its duties and responsibilities, on the methods to be used in carrying out the job, in terms of techniques, systems and procedures, and on the relationships that should exist between the job holder and his superior subordinates and colleagues." JOB Design (cont’d) Job design is the process of a) Deciding the contents of the job. b) Deciding methods & processes to carry out the job. c) Making optimize use of job/work-time so that job/work- time should not be wasted as time is money and time cannot be earned, but can be saved by making efficient use of it. d) Avoiding manual task if can be handled by machines or automated. e) Synchronization of work, and no conflict with other jobs f) Deciding the relationship which exists in the organization. Job design gives framework to job analysis as it tries to figure out what qualities, skills and other requirements are needed to perform the given job by a job holder. JOB Design (cont’d) Job design gives framework to job analysis as it tries to figure out what qualities, skills and other requirements are needed to perform the given job by a job holder. Job Rotation A job rotation is a technique in which employees are moved between two or more jobs in a planned manner. The objective is to expose the employees to different experiences and wider variety of skills to enhance job satisfaction and to cross-train them. Job Enlargement Job Enlargement, a job design technique in which the number of tasks associated with a job is increased (and appropriate training provided) to add greater variety to activities, thus reducing monotony. Job enlargement is considered a horizontal restructuring method in that the job is enlarged by adding related tasks. Job Enrichment Job enrichment adds new sources of job satisfaction by increasing the level of responsibility of the employee in organization. While job enlargement is considered as horizontal restructuring method, job enrichment is considered as vertical restructuring method of moral excellence of giving the employee additional authority, autonomy, and control over the way the job is accomplished. Also called job enhancement or vertical job expansion. Work Study “Work study is a generic term for those techniques, method study and work measurement which are used in the examination of human work in all its contexts and which lead systematically to the investigation of all the factors which affect the efficiency and economy of the situation being reviewed, in order to effect improvement.” Work Study (cont’d) Work study is a means of enhancing the productivity of the firm by elimination of waste and unnecessary operations. It is a technique to identify non-value adding operations by investigation of all the factors affecting the job. It is the only accurate and systematic procedure oriented technique to establish time standards. Method study and work measurement is part of work study. Part of method study is motion study, work measurement is also called by the name ‘Time study’. Work Study (cont’d) Advantages of Work Study 1. It helps to achieve the smooth production flow with minimum interruptions. 2. It helps to reduce the cost of the product by eliminating waste and unnecessary operations. 3. Better worker-management relations. 4. Meets the delivery commitment. 5. Reduction in rejections and scrap and higher utilization of resources of the organization. 6. Helps to achieve better working conditions. 7. Better workplace layout. 8. Improves upon the existing process or methods and helps in standardization and simplification. 9. Helps to establish the standard time for an operation or job which has got application in manpower planning, production planning. Method Study Method study enables the industrial engineer to subject each operation to systematic analysis. The main purpose of method study is to eliminate the unnecessary operations and to achieve the best method of performing the operation. According to British Standards Institution (BS 3138): “Method study is the systematic recording and critical examination or existing and proposed ways or doing work as a means or developing and applying easier and more effective methods and reducing cost.” Fundamentally method study involves the breakdown of an operation or procedure into its component elements and their systematic analysis. Objectives of Method Study Method study is essentially concerned with finding better ways of doing things. It adds value and increases the efficiency by eliminating unnecessary operations, avoidable delays and other forms of waste. The improvement in efficiency is achieved through: 1. Improved layout and design of workplace. 2. Improved and efficient work procedures. 3. Effective utilization of men, machines and materials. 4. Improved design or specification of the final product. Objectives of Method Study (cont’d) The objectives of method study techniques are: 1. Present and analyze true facts concerning the situation. 2. To examine those facts critically. 3. To develop the best answer possible under given circumstances based on critical examination of facts Scope of Method Study The scope of method study is not restricted to only manufacturing industries. Method study techniques can be applied effectively in service sector as well. It can be applied in offices, hospitals, banks and other service organizations. The areas to which method study can be applied successfully in manufacturing are: 1. To improve work methods and procedures. 2. To determine the best sequence of doing work. 3. To smoothen material flow with minimum of back tracking and to improve layout. 4. To improve the working conditions and hence to improve labour efficiency. 5. To reduce monotony in the work. 6. To improve plant utilization and material utilization. 7. Elimination of waste and unproductive operations. 8. To reduce the manufacturing costs through reducing cycle time of operations. Steps or Procedure Involved in Methods Study 1. SELECT the work to be studied and define its boundaries. 2. RECORD the relevant facts about the job by direct observation and collect such additional data as may be needed from appropriate sources. 3. EXAMINE the way the job is being performed and challenge its purpose, place sequence and method of performance. 4. DEVELOP the most practical, economic and effective method, drawing on the contributions of those concerned. Steps or Procedure Involved in Methods Study (cont’d) 5. EVALUATE different alternatives to developing a new improved method comparing the cost-effectiveness of the selected new method with the current method with the current method of performance. 6. DEFINE the new method, as a result, in a clear manner and present it to those concerned, i.e., management, supervisors and workers. 7. INSTALL the new method as a standard practice and train the persons involved in applying it. 8. MAINTAIN the new method and introduce control procedures to prevent a drifting back to the previous method of work. Selection of the Job for Method Study The job should be selected for the method study based upon the following considerations: A. Economic aspect B. Technical aspect C. Human aspect A. Economic Aspects (a) Bottleneck operations which are holding up other production operations. (b) Operations involving excessive labour. (c) Operations producing lot of scrap or defectives. (d) Operations having poor utilization of resources. (e) Backtracking of materials and excessive movement of materials. B. Technical Aspects The method study man should be careful enough to select a job in which he has the technical knowledge and expertise. Other factors which favour selection in technical aspect are: 1. Job having inconsistent quality. 2. Operations generating lot of scraps. 3. Frequent complaints from workers regarding the job. C. Human Considerations 1. Workers complaining about unnecessary and tiring work. 2. More frequency of accidents. 3. Inconsistent earning Recording Techniques for Method Study Recording Techniques for Method Study Charts Macro-Motion Charts Micro-motion chart Diagrams 1. Operations Process chart 1. SIMO Chart 1. Flow Diagram 2. Flow Process chart 3. Two handed process chart 2. String diagram 4. Multiple activity chart Method Study Symbols 1. Operation Process Chart The manufacturing process is divided into separate operations with the help of the operation process chart. It is also called outline process chart. It shows -The points at which materials are introduced into the process -The sequence of various operations and -Inspections This chart represents the basic activities required for producing a product. Since it presents the overall visualization of the process, basis for studying possibilities for the improvement of operations by elimination, combination, rearrangement or simplification is available. Operation Process Chart (cont’d) 2. Flow process Chart Graphic representation of all the production activities occurring on the shop floor. It may be considered as an elaboration of the operation process chart which includes transportation, storage and delay. Process charts are of three types: (a) Material type—Which shows the events that occur to the materials. b) Man type—Activities performed by the man. (c) Equipment type—How equipment is used. Flow process Chart (cont’d) 3. Two Handed Process Chart A two handed (operator process chart) is the most detailed type of flow chart in which the activities of the workers hands are recorded in relation to one another. The two handed process chart is normally confined to work carried out at a single workplace. The application of this charts are: (a) To visualize the complete sequence of activities in a repetitive task. (b) To study the work station layout Two Handed Process Chart (cont’d) 4. Multiple Activity Chart It is a chart where activities of more than subject (worker or equipment) are each recorded on a common time scale to show their inter- relationship. Multiple activity chart is made: a) to study idle time of the man and machines, b) to determine number of machines handled by one operator, and c) to determine number of operators required in teamwork to perform the given job. Multiple Activity Chart (cont’d) 1. Flow Diagram Flow diagram used to supplement the flow process chart. It is the diagram of building plan representing graphically the relative position of productive machinery storage space, gangways etc. and path followed by men or materials. All routes followed by different items are shown by joining symbols with straight lines. Flow Diagram (cont’d) 2.String Diagram The string diagram is a scale layout drawing on which, length of a string is used to record the extent as well as the pattern of movement of a worker working within a limited area during a certain period of time. Produce a record of a existing set of conditions so that the job of seeing what is actually taking place is made as simple as possible. Actual distance travelled during the period of study to be calculated by relating the length of the thread used to the scale of drawing. Movements between work stations which are difficult to be traced on the flow diagram can be conveniently shown on string diagram. String Diagram (cont’d) Micro-Motion Study Chart Micro-motion study provides a technique intended to divide the human activities in a groups of movements or micro-motions called Therbligs. It helps to find for an operator one best pattern of movements that consumes less time and requires less effort to accomplish the task. Therbligs were suggested by Frank O. Gilbreth, the founder of motion study. 1. SIMO Chart Simultaneous motion cycle chart (SIMO chart) is a recording technique for micro-motion study. A SIMO chart is a chart based on the film analysis, used to record simultaneously on a common time scale the Therbligs or a group of Therbligs performed by different parts of the body of one or more operators. It is the micro-motion form of the man type flow process chart. SIMO Chart (cont’d) Work Measurement “Work measurement is the application or techniques designed to establish the time for a qualified worker to carry out a specified job at a defined level or performance.” Work measurement is also called by the name ‘time study’. Work measurement is concerned with investigation and reduction of any ineffective time associated with the job and establishing time standards for an operation carried out as per the standard method. Objectives of Work Measurement 1. Comparing alternative methods. 2. Assessing the correct initial manpower requirement 3. Planning and control. 4. Realistic costing. 5. Financial incentive schemes. 6. Delivery date of goods. 7. Cost reduction and cost control. 8. Identifying substandard workers. 9. Training new employees. Techniques of Work Measurement 1. Time study (stop watch technique), 2. Synthesis, 3. Work sampling, 4. Predetermined motion and time study, 5. Analytical estimating Time study and work sampling involve direct observation and the remaining are data based and analytical in nature. Techniques of Work Measurement (cont’d) 1. Time study: A work measurement technique for recording the times and rates of working for the elements of a specified job carried out under specified conditions and for analyzing the data so as to determine the time necessary for carrying out the job at the defined level of performance. In other words measuring the time through stop watch is called time study. Techniques of Work Measurement (cont’d) 2. Synthetic data: A work measurement technique for building up the time for a job at a defined level of performance by totaling element times obtained previously from time studies on other jobs containing the elements concerned or from synthetic data. Techniques of Work Measurement (cont’d) 3. Work sampling: A technique in which a large number of observations are made over a period of time of one or group of machines, processes or workers. Each observation records what is happening at that instant and the percentage of observations recorded for a particular activity, or delay, is a measure of the percentage of time during which that activities delay occurs. Techniques of Work Measurement (cont’d) 4. Predetermined motion time study (PMTS): A work measurement technique whereby times established for basic human motions (classified according to the nature of the motion and conditions under which it is made) are used to build up the time for a job at the defined level of performance. The most commonly used PMTS is known as Methods Time Measurement (MTM). Techniques of Work Measurement (cont’d) 5. Analytical estimating: A work measurement technique, being a development of estimating, whereby the time required to carry out elements of a job at a defined level of performance is estimated partly from knowledge and practical experience of the elements concerned and partly from synthetic data. Time Study Time study is also called work measurement. It is essential for both planning and control of operations. According to British Standard Institute time study has been defined as “The application of techniques designed to establish the time for a qualified worker to carry out a specified job at a defined level of performance.” Steps in Making Time Study 1. Select the work to be studied. 2. Obtain and record all the information available about the job, the operator and the working conditions likely to affect the time study work. 3. Breakdown the operation into elements. An element is a instinct part of a specified activity composed of one or more fundamental motions selected for convenience of observation and timing. 4. Measure the time by means of a stop watch taken by the operator to perform each element of the operation. Either continuous method or snap back method of timing could be used. 5. At the same time, assess the operators effective speed of work relative to the observer’s concept of ‘normal’ speed. This is called performance rating. Steps in Making Time Study (cont’d) 6. Adjust the observed time by rating factor to obtain normal time for each element Normal = (Observed time * Rating ) ÷ 100 7. Add the suitable allowances to compensate for fatigue, personal needs, contingencies. etc. to give standard time for each element. 8. Compute allowed time for the entire job by adding elemental standard times considering frequency of occurrence of each element. 9. Make a detailed job description describing the method for which the standard time is established. 10. Test and review standards wherever necessary. Computation of Standard Time Standard time is the time allowed to an operator to carry out the specified task under specified conditions and defined level of performance. Standard time may be defined as the, amount of time required to complete a unit of work: (a) under existing working conditions, (b) using the specified method and machinery, (c) by an operator, able to the work in a proper manner, and (d) at a standard pace. Computation of Standard Time (cont’d) The basic constituents of standard time are: 1. Elemental (observed time). 2. Performance rating to compensate for difference in pace of working. 3. Relaxation allowance. 4. Interference and contingency allowance. 5. Policy allowance. Computation of Standard Time (cont’d) OT – Observed Time PRF – Performance Rating Factor NT – Normal Time PA – Process Allowances RPA – Rest and Personal Allowances SA – Special Allowances PoA – Policy Allowances Computation of Standard Time (cont’d) Computation of Standard Time (cont’d) Computation of Standard Time (cont’d) Any Questions