Temperature Control System Instrumentation PDF
Document Details
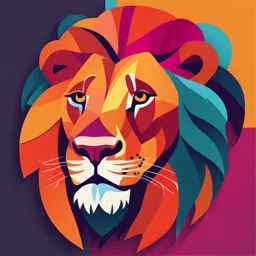
Uploaded by HardierLeaningTowerOfPisa6051
Tags
Summary
This document provides an overview of temperature control systems, focusing on thermocouples and resistance temperature detectors (RTDs). It compares their advantages and disadvantages, including factors like accuracy, cost, and response time. The document also explains their working principles and component parts.
Full Transcript
TEMPERATURE Control System Instrumentation (Temperature) ADVANTAGES OF USING THERMOCOUPLE I. THERMOCOUPLE Wide temperature range They can handle a vast temperature...
TEMPERATURE Control System Instrumentation (Temperature) ADVANTAGES OF USING THERMOCOUPLE I. THERMOCOUPLE Wide temperature range They can handle a vast temperature spectrum, from very low to extremely high. Relatively low cost Compared to other temperature sensors, thermocouples are generally affordable. response time Some types of thermocouples can react to temperature changes quickly. Figure 1: Types of thermocouples Durable A thermocouple is a thermoelectric device that They can withstand harsh environments can continuously measure temperature changes through and vibrations. a temperature sensor. It comprises two dissimilar metallic wires joined together to form a junction. When the junction is heated or cooled, a small voltage is DISADVANTAGES OF USING THERMOCOUPLE generated in the electrical circuit of the thermocouple which can be measured, and this corresponds to Accuracy temperature. (Hu et al., 2006; Process Parameters Ltd, While they’re good for most 2024) applications, they might not be the most precise option for situations requiring super high Some examples (types): accuracy. For those cases, other sensors like RTDs (Resistance Temperature Detectors) might be better suited. Calibration Thermocouples need regular calibration to ensure they’re measuring temperatures accurately. Cold junction temperature The temperature at the unconnected ends of the wires (cold junction) needs to be stable for accurate readings. II. RESISTANCE-TEMPERATURE DETECTOR (RTD) Figure 2:: Type-K, Type-J, Type-N, Type-T (RS Online, 2023) A Resistance Temperature Detector is an electrical PARTS OF A THERMOCOUPLE sensor used to measure the environment's temperature by measuring a metallic wire's change in electrical resistance. It can be described as a temperature transducer that converts heat energy into some other form of energy. The metals that are best convenient for use as RTD sensors are pure of uniform quality and stable within a given range of temperature and able to give reliable resistance- temperature readings. These are Figure 3: Parts of a Thermocouple (Ueidaq, 2022) commonly platinum, nickel, and other resistance wire elements. HOW IT WORKS For a visual representation of how a thermocouple works, attached here is a demo youtube video that you can visit and watch: Video Link: Thermocouple Explained | Working Principles PARTS OF A RESISTANCE-TEMPERATURE possesses durability as they are made from DETECTOR (RTD) platinum material which is resistant to corrosion. This makes them reliable for accurate temperature measurements in harsh environments Stable and has a longer life span at high temperature measurement RTDs maintain consistent performance over time and are less prone to degradation even when exposed to high temperatures. This ensures its reliability thus extending its service Figure 4: Parts of an RTD life. Easy to construct, install, and replace 1. Resistance Element - it is the portion of the RTDs can be created in any sensor that senses the actual process temperature configuration which makes it easy to design. 2. Internal Conductors - it is the wires that There is no rule in the shape and the way it is transmit resistance signal to the control system constructed. 3. Protection Tube - it shields the resistance element from environmental factors 4. Insulated Tube - it gives insulation to the DISADVANTAGES OF USING internal conductors to prevent electrical RESISTANCE-TEMPERATURE DETECTOR disruption (RTD) 5. Terminated Head - it provides a secure connection point for the wires and external Requires a current source control system The change in resistance is measured by 6. Conduit - it protects the electrical wiring cable the sensing element of the RTD. In this case, an external current source must be employed for the RTDs to perform its function. HOW IT WORKS Accuracy depends on the battery’s health The accuracy of RTDs can be affected For a visual representation of how a by the battery’s health. An unstable battery may resistance-temperature detector works, attached here is a result in inconsistent current flow. demo youtube video that you can visit and watch: Can cause self-heating in-case current value Video Link: Understanding Temperature Sensor Technology: exceeds slightly than the limit RTDs, Thermocouples, and Thermistors If current values exceed the limit, self heating will occur. The resistance is measured by the current passing through the wire, ADVANTAGES OF USING resulting in heating in the wire. RESISTANCE-TEMPERATURE DETECTOR Has a higher initial cost (RTD) Resistance-Temperature Detectors have a higher initial cost compared to other Can operate at a wide range of temperatures temperature sensors because it is made from A Resistance-Temperature Detector can high quality platinum materials. operate at a temperature range between -200°C Has complex operating circuitry or signal to 850°C. conditioning unit Has excellent accuracy and precise It requires complex operating circuitry measurements or signal processing given that the measured The electrical resistance of RTD varies change in resistance by the sensing element must reliably in a range of temperatures thus be converted into a readable temperature data. eliminating any cause of error. Has low sensitivity and slower response time Has linear characteristics RTDs cannot detect small changes The metals used in RTD exhibit linear tremendously. With that, they take longer to nature. The variation in their resistance values is measure rapid temperature changes. useful in predicting future values given that it follows a linear curve with respect to temperature. III. BI-METAL THERMOMETER Resistant to corrosion and ideal for use in extreme environment This thermometer operates based on the The Resistance-Temperature Detector functional principle that metals expand differently depending on the change in temperature. It always ADVANTAGES OF USING BI-METAL consists of two different metal strips that have a different THERMOMETER thermal expansion coefficient. These two strips are joined together inseparably and thus form the bimetal Simple and robust design strip. The strip is in the form of a helical shape in which Due to the simplicity in the design of the this will create a motion for the temperature reading to measuring device, it is considered as a durable be done. When the temperature changes, the different and reliable instrument for temperature reading metals expand to different degrees, which leads to a as its mechanical nature means that failure in the mechanical deformation of the bimetal strip. components and mechanism is less likely to occur. PARTS OF A BI-METAL THERMOMETER Cheaper than other thermometers This device is lesser in cost than others since it has a simpler design which does not require electronic sensors and the manufacturing process of this device is simpler than others. Mechanical Along with the simplicity of the design of this device, operating this does not require any power since electronic sensors and devices are not incorporated which makes this completely mechanical. Easy to install and maintain Figure 5: Parts of a Bi-metal thermometer As this device does not require any complex wiring and power sources, calibrating 1. Pointer - this is in needle form that is attached this to accurately measure temperature is just to the rod in which through the mechanical straightforward which allows for zero-point movement of the strip the temperature reading is resetting on-site. For installation of this device, generated. it only requires physical contact with the fluid in 2. Sliding bearing - a part of the measuring device order to measure the temperature. which is used to ensure that the rotation of the Suitable for a wide temperature range gear or pointer moves smoothly along with the It is suitable for wide-range of strip to give accurate measurement. temperatures as this device can measure the 3. Rotatable rod - this is connected to the pointer temperature of liquid, steam and gas medium in and this generates a rotational movement which the range of -80℃ up to +500℃ in various is the indicator of the temperature change or production processes. reading. 4. Cylindrical pin - this serves as the connector between the pointer and the strip and this DISADVANTAGES OF OF USING BI-METAL contributes to the overall precision of the THERMOMETER thermometer. 5. Helical bimetal Strip - a bi-metal strip that is Not recommended for very high temperatures transformed into the helical shape so that Despite the device being suitable for rotational movement will be enough to reach the wide-range of temperature, it is important to pointer that will give an accurate reading of the take into account the optimum temperature as temperature. this type of thermometer may not give an 6. Stem - the long tube that serves as the housing accurate measurement of the temperature which for the bimetallic strip and this comes into is why it is not recommended for temperatures contact to the fluid or process that is being lower than -80 oC and higher than +500oC. measured. It may require frequent calibration. The device's straightforward design and ease of installation require regular calibration, HOW IT WORKS particularly if the thermometer is handled roughly or is exposed to extreme conditions. For a visual representation of how a Bi-metal May not give accurate low temperature Thermometer works, attached here is a demo youtube readings. video that you can visit and watch: As the use of this device is simple and Video Link: How does a bimetallic strip thermometer work? reliable, this can still result in the low accuracy of the measurement especially for temperatures lower than the -80oC which is said to be the HOW IT WORKS minimum temperature for this device. Rough handling can interfere with calibration For a visual representation of how a total radiation The use of this device for rough pyrometer works, attached here is a demo youtube video conditions may cause damage to the device and that you can visit and watch: to the results that it may generate as those can Video Link: Radiation Pyrometer: Working Principle, cause a possible disruption to the simple Diagram, Temperature Measurement Sensor [Animation mechanism of the device which will lead to Video] inaccurate results, frequent calibration or replacement of the device. ADVANTAGES OF A TOTAL RADIATION PYROMETER IV. TOTAL RADIATION PYROMETER Measures temperature with non-contact Total radiation pyrometer is a type of pyrometer objects. which is used to measure high temperature objects Unlike other temperature measuring without the need of being in contact with it. This remote instruments, a total radiation pyrometer does not temperature sensor device measures the total radiation require direct contact with the body being emitted by the body, including visible and invisible measured. This is due to the fact that this radiations. These radiations are then calibrated for black instrument utilizes radiation to measure the body conditions using a radiation sensing element and temperature of a hot body. measuring device inside the instrument (What is Can measure high temperature objects. Radiation Pyrometer? Working Principle, Construction, Being able to measure the temperature Diagram & Advantages, 2023) of bodies at a distance, this instrument can be PARTS OF A TOTAL RADIATION PYROMETER used to measure very hot objects. This allows a safer method of measuring high temperature objects and saves the device from melting. Provides response with fast speed. Since radiation is being measured in a total radiation pyrometer, it can provide a fast speed response as it travels at approximately as fast as the speed of light. Produces output of high accuracy. With the help of the instrument’s design, a total radiation pyrometer is able to provide Figure 6: Parts of a total radiation pyrometer highly accurate outputs. Utilizing an adjustable eyepiece, mirror, and a black body or the 1. Sighting hole - this is where the hot object may temperature detector, total radiations emitted by be viewed from. It contains an adjustable the object are absorbed and measured. eyepiece which helps make the total radiation to Is less affected by the corrosive atmosphere. fall on the radiation receiving element or This happens because of the mechanism transducer. of the total radiation pyrometer which only uses 2. Housing - contains and houses the content of the total radiation in measuring the temperature of a total radiation pyrometer. body and does not require contact with it. With 3. Window - protects the thermocouple from direct this, it can be used in measuring temperature in radiation. corrosive environments. 4. Diaphragm - is used to focus the radiation emitted by the hot body on the radiation sensing transducer, along with the mirror. DISADVANTAGES OF A TOTAL RADIATION 5. Mirror - also called lens, is responsible for PYROMETER adjusting the focus of the radiation accordingly. Using this is an advantage since no reflection Has a non-linear scale and absorption of radiation will happen. Having a non-linear scale, the results 6. Thermocouple/thermopile - receives the total that may be given by the device are susceptible radiation This serves as the transducer, which to deviations. This may happen especially when may also vary in forms of resistance there is the occurrence of errors in the process or thermometer or thermocouple. within the instrument itself, due to some factors. Is not suitable for objects with low temperature. Total radiation pyrometer is typically 2. Objective lens - focuses the thermal radiation designed to measure high temperature objects. emitted by the target onto the detector. Due to poor sensitivity, it is not suitable with 3. Field stop - limits the field of view of the low temperatures. Measuring an object with less pyrometer, ensuring that only the radiation from than 600 °C may affect the accuracy of the a specific area of the target is measured. results. 4. Mirror - redirect thermal radiation towards the Sometimes requires cooling arrangements to detector. remove the instrument's overheating. 5. Target Objective - additional lens system that Due to the same feature of being able to helps to focus on a specific part of the target measure very high temperatures using 6. Diffuser - it can relate to how thermal radiation radiations, the instrument is subjected to from the target is diffused before reaching the overheating. Thus, it sometimes requires cooling detector arrangements to overcome it. 7. Eyepiece - allows the operator to visually align It is possible for errors to occur. and focus on the target object Like other instruments, errors may occur 8. Collimator - ensures that incoming rays of light in a total radiation pyrometer. This may happen are parallel before they reach the detector due to the presence of dirt or dust in the mirror 9. Interference filter - selectively allows certain or through the intervention of pressure in the wavelengths of thermal radiation to pass while radiation which is the one being measured in the blocking others process. 10. Weakened filter - reduces the intensity of It is expensive. incoming radiation to prevent saturation of the Its ability to measure high temperature detector objects and its requirement for cooling 11. Photo-detector - converts thermal radiation into arrangement are also the reason for the an electrical signal for processing instrument’s high cost. This may become a disadvantage in terms of considering a temperature measuring device to be used. HOW IT WORKS For a visual representation of how a photoelectric V. PHOTOELECTRIC PYROMETER pyrometer works, attached here is a demo youtube video that you can visit and watch: Photoelectric pyrometers are advanced Video Link: Photoelectric Effect non-contact temperature measurement devices that ADVANTAGES OF USING PHOTOELECTRIC utilize a detection optical system to measure PYROMETERS temperature. The optical system focuses visible and infrared energy from an object onto a detector, which Prevents contamination and damage. converts the energy into an electric signal. The detector's They measure temperature without output is proportional to the amount of energy radiated physical contact, preventing contamination and by the object. Uses photoelectric cells to measure the damage to both the sensor and the target object, intensity of light emitted by a source. Photoelectric which is especially useful for high-temperature pyrometers are accurate to within 0.5% and can be used or hazardous materials to measure temperatures in the range of 900–2500 °C. Provides quick temperature readings. Photoelectric pyrometers provide rapid temperature readings, making them suitable for dynamic environments where objects are PARTS OF A PHOTOELECTRIC PYROMETER moving or rotating, such as in manufacturing processes Suitable for high and low temperatures. These devices can measure a broad range of temperatures, often from several hundred to several thousand degrees Celsius, accommodating various industrial applications Can achieve high accuracy in temperature Figure 7: Parts of a photoelectric pyrometer readings. With advanced optical systems and 1. Substance - this refers to the material being sensitive detectors, photoelectric pyrometers can measured, which emits thermal radiation based achieve high accuracy in temperature readings, on its temperature. even in challenging conditions 3. Heat Sink (for Passive Cooling) - Conducts DISADVANTAGES OF USING PHOTOELECTRIC heat away from the laser, dissipating it into the PYROMETERS surrounding air. 4. Peltier Device (TEC - Thermoelectric Cooler) More expensive than contact thermometers. - Actively cools or heats surfaces by transferring The initial investment for photoelectric heat across its two sides. pyrometers is generally higher compared to 5. Cold Plate - Made of aluminum or copper, it traditional contact thermometers, which may makes direct contact with the laser to aid in heat deter some users from adopting this technology transfer. Accuracy can be affected by dust or smoke. 6. Fan - Used to enhance the cooling efficiency of Their accuracy can be compromised by both passive and active systems. environmental factors such as dust, smoke, or 7. Temperature Sensor - Provides real-time ambient radiation. These elements can scatter or feedback to the controller to maintain optimal absorb the infrared radiation necessary for laser temperature. accurate measurements Needs regular calibration for precision. Regular calibration and adjustments HOW IT WORKS may be required to maintain accuracy, especially in fluctuating environmental conditions. This For a visual representation of how a laser works, can add to operational complexity attached here is a demo youtube video that you can visit Alignment is crucial for accurate readings. and watch: If the pyrometer's field of view does not Video Link: LASER BEAM MACHINING PROCESS align properly with the target size, measurement (Animation): Working of LASER beam machining process. accuracy may be affected. Careful alignment is crucial for reliable readings ADVANTAGES OF USING A LASER VI. LASER High Precision and Accuracy Lasers can operate with highly A laser control system temperature is essential controlled and stable outputs, enabling precise for managing the heat generated during laser operation. temperature control for applications that demand As lasers convert only a fraction of electrical energy into tight tolerances, such as in medical devices and light, the remaining energy turns into heat. If not semiconductor manufacturing. controlled, this excess heat can impact laser Fast Response Time performance, affecting light quality and wavelength, and Lasers can rapidly adjust their output in potentially damaging laser components. The system's response to changes in system conditions, goal is to dissipate heat effectively, ensuring stable laser allowing for quick stabilization of temperature. output and longevity. This can be achieved using either This makes them suitable for environments passive or active cooling methods, along with careful where temperature fluctuations must be selection of a suitable laser mount. minimized. Non-Contact Measurement Reduces the risk of contamination or PARTS OF A LASER interference with sensitive materials, beneficial in applications like clean rooms and bio-labs. Energy Efficiency Compared to traditional heating methods, lasers can be more energy-efficient by focusing heat directly on the target area, minimizing waste and reducing overall power Figure 9: Temperature consumption. Figure 8: Anatomy and heat control loop response in a Versatility in Different Applications flow of a passively cooled actively cooled laser moun Lasers can be used in various laser mount. applications, from cooling in laser mounts (like 1. Temperature Controller - Manages the power Peltier devices) to heating processes that require supply to cooling devices, ensuring stable laser controlled temperature exposure. temperature. 2. Laser Mount - Provides a stable platform for the laser, equipped with thermal management DISADVANTAGES OF USING A LASER features. High Initial Cost in pressure of the flow before and after the Laser systems with precise temperature orifice. control capabilities are expensive to set up. The The flow rate is measured using the measured initial investment may not be feasible for pressure difference using Bernoulli’s small-scale operations or budget-sensitive equation. projects. Complex Setup and Maintenance Industrial Applications The integration of lasers into Oil and Gas Industry - Used for measuring temperature control systems often requires natural gas or other gas flow. Also used for specialized knowledge and equipment which can measuring the flow of oil in pipelines. lead to higher maintenance costs and the need Chemical Industry and Water Treatment - for skilled technicians. orifice meter is used to measure the flow Heat Generation rates of various fluids to control and optimize Lasers themselves generate heat, which processes. can sometimes require additional cooling Power Generation - used for the measurement systems to prevent overheating. This can of steam and cooling water or other process complicate the setup and reduce the overall fluids used. efficiency of the system. HVAC Systems - it can be used to measure Sensitivity to Environmental Factors the flow of gasses to monitor airflow and Factors like dust, vibration, and ventilation rates. alignment can affect the laser's performance, potentially leading to inconsistent temperature Parts control. Limited Temperature Range While lasers are effective for precise temperature control, they may not be suitable for h extremely high-temperature applications where ttps://c traditional heating methods like resistive heaters analtafl or induction heating are more efficient. ow.com /flow-c onditio FLOW MEASUREMENT ners/ A. ORIFICE An orifice meter is a type of flow meter that is used to measure the flow of fluid inside a pipe. An orifice meter works based on the principle of differential pressure measurement which means that the fluid flow rate is measured using the differential pressure. The orifice meter consists of a thin plate with a hole (orifice) in the center, which is installed in the pipeline. The orifice plate is typically made of stainless steel. When the fluid flows through the plate, the flow is restricted, creating a pressure drop. The pressure of the fluid decreases until it reaches the vena contracta. The vena contracta is the smallest-cross sectional area developed along the downstream of the orifice. After the fluid reaches this point, the pressure gradually increases until it reaches the maximum pressure. The pressure drop is then used to calculate the flow rate of the fluid https://theinstrumentguru.com/orifice-meter-orif using Bernoulli’s equation. The Orifice meter is ice-meter-is-used-to-measure/ considered as one of the simplest types of flowmeter devices. Inlet - The part where the fluid enters the orifice. Operation Fluid flows through the orifice plate causing Orifice Plate - A thin, flat plate typically with a a pressure drop. single hole that is placed in between the inlet A manometer or a differential pressure (DP) and outlet sections. This is the primary part of transmitter is used to measure the difference the orifice that creates a pressure drop to compact plate size provides versatility in measure the flow rate. various arrangements and tight areas. Flow Conditioner - located near the inlet Conveniently fitted. section that enables uniform and linear flow of Systems are created to easily fit between the fluid. This ensures a more accurate flanges, making installation straightforward measurement and guaranteeing secure connections. As there Outlet - The part where the fluid goes out of the are no moving components in the flow stream, orifice. the possibility of wear and tear is lowered, resulting in enhanced durability and less maintenance. Demo Video Calibration is minimal. Link: Orifice Meter Calibration needs are limited, mainly consisting of confirming mechanical Differential pressure flow meters have an artificial tolerances upon purchase and periodically restriction integrated into the measuring tube, illustrated throughout use. This minimal upkeep feature here by the example of an orifice plate. Two holes are lessens the necessity for regular modifications, located in the pipe wall, one before and one after the enhancing the system's ease of use and orifice plate. affordability. Two separate tubes connect these holes to a differential Disadvantages pressure sensor. As soon as the fluid starts to flow, its velocity around the orifice plate increases significantly Requires homogeneous. because of the restriction in the cross-section. Different values are detected in the pressure chambers of the The system needs a homogenous, sensor, a higher pressure before and a lower pressure single-phase liquid to guarantee consistent flow after the orifice plate. This pressure difference is a direct traits, aiding in the preservation of precise measure for the flow velocity, and thus the mass and measurements. Furthermore, the flow must volume flow in the pipe. display axial velocity vectors, indicating that the fluid travels mainly in a straight path along the system's axis. Advantages Accuracy is influenced by fluid's density, Simple and precise. pressure, and viscosity. Its approach is simple and provides The precision of an orifice meter is precise measurements, making it suitable for influenced by the fluid's density, pressure, and different types of fluids, such as liquids, viscosity, since these elements affect the fluid's gasses, and steam. Its straightforward design flow characteristics and the pressure loss across guarantees dependable results without the orifice. Fluids with high viscosity can result complicated configurations or lengthy in greater pressure losses, possibly decreasing calibrations. measurement precision, whereas fluids that vary Cost-effective. in density or pressure might produce unreliable readings. It is cost-effective, since price increases only slightly with larger sizes. Straight conduits are necessary. Cost-effectiveness renders it a suitable option for uses needing various capacities. Its Straight conduits are vital for orifice scalability enables users to control expenses meters to guarantee a stable and consistent flow efficiently while addressing different size through the meter, which is important for precise requirements. pressure readings. Any curves or interruptions in the pipes can create turbulence, potentially Easy to install, remove, and maintain. resulting in measurement inaccuracies. For accuracy to be maintained, the fluid flow needs Its designs feature compact plates that to be laminar and unobstructed as it moves make installation, removal, and maintenance through the orifice. easier. This simplifies management and decreases downtime during maintenance. The The pipeline must be specifically designed with limited range capacity. The pipeline employed with an orifice measure the difference in pressure of the flow meter needs to be specially constructed for before and after the orifice. measuring liquid flow, guaranteeing the The flow rate is determined from the pressure appropriate size and circumstances for precise differential using Bernoulli’s equation, the measurements. It generally must be clear of pipe diameter, and the meter’s discharge blockages or anomalies that could influence coefficient. flow uniformity. Industrial Applications Unable for self-cleaning. Oil and Gas Industry - used for measuring The flow characteristics in an orifice natural gas or other gas flow. Also used for meter do not promote self-cleaning, which measuring the flow of oil in pipelines. They means that particles or debris in the fluid may provide accurate flow measurements which gather and block the orifice. This may result in helps in detecting leaks or irregularities in the incorrect measurements or potentially harm the pipelines. meter as time passes. Routine upkeep and Water Treatment Industry - venturi meters are sanitation are necessary to guarantee the meter also utilized in water treatment industries. It functions properly and delivers accurate is used to measure the flow of water through measurements. different stages of treatment. Its accurate flow measurement and low-pressure loss made it idea for monitoring water flow in pipelines Chemical Industry - venturi meters are used to measure flow in chemical production B. Venturi processes where accurate control of liquids or gasses is essential for maintaining reaction A venturi meter is a type of flow meter that rates and yields. operates on the same principle as with an orifice meter, Automotive Industry - used for the relying on the measurement of pressure differences to measurement and monitoring of airflow in determine the flow rate of a fluid. However a venturi engine carburetors. meter features a different way of creating a pressure drop for the fluid. It consists of a pipe with three sections: a Parts converging section, a throat (the narrowest part), and a diverging section. As the fluid flows through the pipe, its velocity increases within the converging section causing a pressure drop at the throat section. This differential pressure is then measured using various pressure measuring devices and is then used to calculate for the flow rate of the fluid. The converging-diverging configuration of the pipe of a venturi meter helps minimize the energy losses https://engineerexcel.com/venturi-meter-and-orif compared to other flow measurement devices like orifice ice-meter-difference/ meters. This ensures that the fluid’s flow is relatively stable and less turbulent allowing for a more accurate Converging Section - The section where the measurement of the pressure drop. Venturi meters are area is decreasing, causing the velocity to commonly used for systems that require low pressure increase and the pressure to decrease. loss and high accuracy such as in water treatment Throat - The narrowest part of the tube that industries. connects the converging and diverging sections. This is where the maximum velocity and the minimum pressure is found. The pressure is usually measured here where the change in pressure is the most significant. Operation Diverging Section - The section where the area When the fluid flows through a venturi meter, is increasing in diameter. At this point, the its velocity increases as it passes through the velocity decreases and the pressure increases. throat section which causes a pressure drop. Similar to orifice meters, a manometer, differential pressure (DP) transmitter or other Demo Video pressure measuring equipment is used to The design of the venturi meter Link: Venturi Meter facilitates versatile installation, enabling it to be placed vertically, horizontally, or at an angle, A Venturi meter, also known as a Venturi tube, is a flow based on the system's requirements. This measurement device used to determine the flow rate of flexibility allows it to fit into different piping fluid in a pipe. It consists of a tapered tube with a layouts and accommodate space limitations. No constriction in the middle, creating a region of reduced matter the orientation, as long as the meter is cross-sectional area. By measuring the pressure properly installed, it can provide precise flow difference between the narrowest section, throat, and the measurements. upstream section, the flow rate can be determined. High precision across a broad range of flows. The purpose of the divergent cone is to recover some of the pressure that was lost in the convergent section, The venturi meter is recognized for its resulting in a higher pressure at the exit compared to the excellent accuracy and consistency in convergent venturi meter. The longer length of the exit differential pressure measurements, ensuring its cone allows for a more gradual pressure recovery dependability across various flow rates. Its process, reducing the intensity of the pressure recovery design reduces energy loss, facilitating shock and minimizing disturbances in the flow. They remarkable pressure recovery, generally about offer several advantages such as low pressure drop, high 90%. This elevated pressure recovery guarantees accuracy, and minimal maintenance requirements. that flow measurements stay reliable and precise, even under fluctuating flow conditions that make more accurate measures than flow Advantages nozzles and orifice plates Suitable for dirty fluids and higher flow rates. Disadvantages The narrower cone angle of a venturi Prone to cavitation of fluid in the throat. meter aids in reducing sediment accumulation by permitting solids to pass through with greater The Venturi meter is inappropriate for ease. This function is particularly advantageous pipes with narrow diameters, usually under 7.5 for applications that deal with contaminated cm, since the fluid speed notably rises when it fluids, where particles could otherwise lead to moves through the narrowed section, potentially obstructions or errors. Moreover, the design causing cavitation. Cavitation takes place when accommodates greater flow rates, guaranteeing the pressure falls beneath the vapor pressure of that the meter stays efficient. the liquid, leading to the creation of gas bubbles that may harm the meter and diminish High discharge coefficient. measurement precision. A venturi meter possesses a high Unsuitable for areas with limited space. discharge coefficient, signifying its capacity to accurately measure flow with reduced energy Venturi meters can be excessively large loss. The discharge coefficient is affected by for situations with restricted space because their factors like the number of flow lines and the construction needs a specific length of pipe to dimensions of the meter's throat, as these aspects generate the required flow restriction. Their directly influence the flow behavior and pressure dimensions render them less suitable for reduction across the meter. compact systems or setups with limited space. This can restrict their application in smaller or Behavior is highly predictable. tighter spaces where a more compact flow measurement instrument would be better suited. The operation of a venturi meter is very predictable because of its proven design and High initial costs, costly installation, and flow properties. The connection between flow maintenance rate and pressure drop is stable, enabling precise and dependable measurements for different fluid Venturi meters have significant upfront types, provided the fluid characteristics stay costs because of their unique design and within defined boundaries. This reliability materials, which add to their overall price. renders the venturi meter a dependable and Setting up can also be expensive since it efficient instrument for measuring flow in demands accurate alignment and might numerous industrial applications. necessitate extra infrastructure to support their dimensions. Additionally, their intricate design Vertical, horizontal, or inclined installations. complicates maintenance and inspection, as opposed to simpler flow meters, necessitating Industrial Applications increased time. Chemical and Pharmaceutical Industry - it Cannot measure pressures beyond a certain accurately measures the flow of chemicals, maximum. solvents, and reagents which are crucial for chemical and pharmaceutical processes. Venturi meters are engineered to function efficiently within a designated range of Petrochemical Industry - rotameters are flow rates, and they are unable to measure utilized for the measurement of flow rates of pressures at velocities that surpass a certain fuels, lubricant, and other hydrocarbon-based upper limit. If the flow rate or pressure exceeds fluids. this threshold, the meter might not deliver precise measurements, and the likelihood of Water & Wastewater Treatment - metal damage, including cavitation, rises. rotameters can also be used to measure the flow of water, wastewater, and the chemical reagents used for their treatment. In addition, rotameters are also used for the C. Rotameter purging of corrosive substances. They are also used for monitoring industrial gas A rotameter is another type of flow meter that is burners and furnaces to prevent equipment used to measure the flow rate of liquids and gasses. It harm. Rotameters are also used to control consists of a transparent, tapered vertical tube that has a refrigeration flow in industrial settings. float inside that moves up and down according to the flow of the fluid that enters. The tapered vertical tube is Parts marked with a scale, which allows for the direct reading of the flow rate based on the position of the float. A rotameter is also called a “variable area flow meter" because of the tapered shape of the tube, which creates a varying cross-sectional area as the fluid flows through it. The position of the float inside the tube at a certain time corresponds to the fluid’s flow rate at that specific time. The main principle behind a rotameter is that as the flow rate increases, the float rises, expanding https://www.solnpharma.com/2021/11/rotameter the annular gap between the float and the tube allowing -construction-working.html for more fluid to flow. On the other hand, when the flow rate is decreased, the float moves downward and the Metering Tube - It is usually a tapered, annular space between the float and the tube decreases transparent, and cylindrical tube that pushes the which limits the flow of fluid. The position of the float is float upward. This tube includes glass or metal determined by the balance between the upward force type where the fluid flows. brought by the flowing fluid from the bottom, the buoyant force acting on the float caused by the dispersed Float - It is a cylindrical or spherical object that fluid and the downward drag force created by the is inside the tube and moves up and down in velocity of the fluid as it passes through the annular response to the fluid flow. With the increase in space. Rotameters are commonly used for processes flow rate, the float rises and vice versa. The float where continuous flow monitoring is required. is used to measure the flow rate by referencing its position to a scale on the flow tube. The Operation shape of the float is crucial in the rotameter’s sensitivity to fluid viscosity, with sharp-edged When the fluid enters from the bottom of the floats being less affected by viscosity. tapered tube, it causes the float to move upward. Demo Video As the flow of the fluid increases, the float moves further rises due to an increase in the Link: Rotameter flow velocity of the fluid. Rotameter is a type of flowmeter that is used to measure The position of the float determines the the flow rate of fluids, typically gases or liquids. It current flow rate of the fluid at a specific time consists of a tapered tube with a float inside that moves using the scale printed on the tube. up and down as the fluid flows through the tube. When fluid flows through the rotameter, it enters the tapered adaptable for different applications. This tube at the bottom and the float rises upwards with the flexibility is particularly crucial when handling increasing flow rate. aggressive or hazardous fluids in compact systems. The float reaches a height where the buoyancy force equals the gravitational force and it remains in Easily fitted with alarms, switches, or equilibrium. The height of the float is directly transmitting devices. proportional to the flow rate of the fluid and the flow rate is measured by reading the height of the float Rotameters can be readily combined against the calibrated scale. The scale is usually marked with alarms, switches, or transmission devices, in units of volume per unit time such as lighters per improving their capabilities and allowing for minute or gallons per hour. remote flow rate monitoring. These extra functions enable automatic notifications when flow rates hit predetermined thresholds, Advantages enhancing process management and safety. This Affordable and widely accessible. feature renders rotameters especially valuable in automated systems where constant flow Rotameters are fairly affordable in observation is essential. comparison to other flow measurement instruments, which makes them a Disadvantages budget-friendly choice for numerous uses. Their Measuring with non-transparent fluids is ease of use and accessibility in multiple sizes challenging and configurations lead to their extensive application across various industries. Their Measuring opaque fluids with a affordability makes them a favored option for rotameter can be challenging because the circumstances where budget limitations are a metering float, which shows the flow rate, factor, without sacrificing essential flow becomes difficult to observe through measurement capabilities. non-transparent or dark liquids. This may result in difficulties in precisely measuring the flow Perform well with low to medium flow rate, particularly if the float is hidden. In these velocities. situations, extra elements such as electronic sensors or outside indicators might be required Rotameters are best suited for measuring to guarantee precise measurements. low to medium flow rates and velocities, generally falling between 1 LPM and 10 LPM. They are especially beneficial in situations that Not ideal for pulsating flow conditions, and require accurate measurements at these flow prone to breakage rates, providing dependable and uniform performance. Rotameters are not ideal for pulsating flow conditions since the variations can result in Pressure loss remains consistently low. instability of the float's position, causing incorrect measurements. Moreover, the glass Rotameters are designed to create tubes typically found in rotameters are delicate minimal pressure drop as the fluid passes and may shatter or develop cracks when through, ensuring that flow remains largely subjected to high pressure or prolonged use, unobstructed. This minimal pressure drop particularly if the fluid pressure rises. These enhances the efficiency of rotameters, as it constraints render rotameters less dependable in reduces unnecessary stress on the system and systems with fluctuating or elevated pressure decreases energy loss. The continuous pressure flows. drop, no matter the flow changes, supports stable performance over various flow rates. Limited to small pipes, low temperatures, Suitable for use with corrosive fluids varying flow rates, and high-pressure Rotameters are ideal for measuring Rotameters should be positioned corrosive liquids as they can be constructed from vertically to guarantee that the float can move materials that withstand chemical deterioration, freely along the scale, resulting in precise like stainless steel or specific plastics. Their measurements. They are generally most compact design enhances rangeability, enabling appropriate for smaller pipes since their design them to measure an extensive range of flow rates is tailored for low to medium flow rates and within a specific size, which makes them temperatures. Moreover, rotameters are Chemical Processing - Fluid handling unsuitable for high-pressure uses since the glass including corrosive, volatile fluids, minimize tubes can shatter under intense conditions, and contact, for safety considerations. the float may not adequately react to varying or HVAC Systems - Measure chilled water and high-pressure flows. other fluids for energy saving. Food and Beverage - Measuring syrups, Parallax errors can affect readings juices, and others where contamination must be avoided. Parallax errors arise in rotameters when Parts the user's viewpoint is misaligned with the float, resulting in an inaccurate reading because of the An ultrasonic flowmeter is made up of various angle from which it is observed. This important components that work together to precisely misalignment may result in lower resolution and gauge fluid flow. less accurate flow measurements. D. Ultrasonic An ultrasonic flow meter is a device that Image from: https://www.bellflowsystems.co.uk/images/filemanage measures the flow rate of a liquid or gas by emitting r/uploads/Product%20Images%204/energy%20meas ultrasonic waves across a pipe in both the flow direction urement%20ultrasonic%20flow%20meters.jpg and the opposite direction. It works by sending high-frequency sound waves into a fluid and measuring Transducers - These are the primary the time it takes for the waves to travel through the fluid components that emit and receive ultrasonic and back to a receiver. Ultrasonic flow meters are signals. They are typically made of piezoelectric affected by the acoustic properties of the fluid and can be materials that generate ultrasonic waves when an impacted by temperature, density, viscosity and electrical signal is applied. suspended particulates depending on the exact flow Piezoelectric Crystals - These crystals are used meter. They vary greatly in purchase price but are often within the transducers to create and detect inexpensive to use and maintain because they do not use ultrasonic waves. They vibrate when an moving parts, unlike mechanical flow meters. electrical current is applied, producing ultrasonic pulses. Operation Reflectors - These components direct the The ultrasonic flow meter sends sound waves ultrasonic waves through the fluid, ensuring in the forward and backward directions accurate measurement by reflecting the waves through the fluid, downstream and upstream. back to the receiving transducer. The time elapsed between the two pulse paths is measured. When the fluid is moving, the Signal Processor - This unit analyzes the time it speed of the sound waves upstream is higher takes for the ultrasonic waves to travel through than those downstream. the fluid. It calculates the flow rate based on the The device takes advantage of this time difference in transit times of the ultrasonic difference to measure the velocity of flow pulses moving with and against the flow hence the rate of flow without affecting or direction. causing pressure loss. Flow Tube - The section of the pipe where the fluid flows and the ultrasonic measurements are Industrial Applications taken. It houses the transducers and ensures the proper alignment of the ultrasonic path. Water and Wastewater Treatment - Measure to improve the management of water; finding leaks. Demo Video Oil and Gas - Measuring flow in pipelines for maximizing production and transporting. Link: Ultrasonic Flow Meter Ultrasonic flow meters can usually be clamped onto an ultrasonic flowmeters is not influenced by existing pipe to measure the flow rate. Two ultrasonic pressure, temperature or density of fluids and signals are emitted into the pipe. One travels thus they are used in a variety of applications in downstream with the water, the other travels upstream different industries. against the water. When no water is flowing, the upstream and downstream signals take the same amount Convenient Installation and Maintenance of time to send and receive. But when water is flowing, the downstream signal is faster than the upstream signal. Another advantage that could be attributed to ultrasonic flowmeters is that they It's very similar to a boat crossing a river. It is much are easy to install, and require minimal easier and faster for a boat to travel with the current of maintenance once installed. Since they do not water than against it. With an ultrasonic flow meter, we involve shutting down fluid flow during measure these signal times and compare them to establishment or management exercises, they determine the velocity of the water. The velocity and the eliminate or reduce losses in productivity. This cross-sectional area of the pipe are then used to feature is especially suitable for the processes calculate the volume flow rate. that run constantly because keeping operational performance is essential. In addition, it eliminates the need for valves and flanges, Advantage and Disadvantage which are considered complicated components in instrumentation pipes and contribute to Energy Conservation simplification during the installation and maintenance processes. As for the construction of ultrasonic flowmeters, these devices are designed to be Advanced Signal Processing Technology fitted round the measuring pipeline externally, so in fact they do not come into contact with the Today’s most commonly used ultrasonic pipe at all. This design fully avoids contact with flowmeters employ complex signal processing the fluid, eliminating interference with the flow that improves accuracy and stability of the field and no pressure loss occurs. This makes measurement. These technologies can also block these meters very energy efficient especially in interferences from other sources and provide large usage applications where even small increased performance in application conditions amounts of energy can translate to big money like dynamic flow or changing fluid content. saving over time. These characteristics make them suitable for industries that embrace environmental governance and efficiency when it comes to energy consumption. Disadvantages Suitability for Large-Diameter Pipes Temperature Measurement Limitations Ultrasonic flowmeters prove themselves Temperature measurements of ultrasonic in measuring large-caliber flows. Compared to flowmeters generally do not go over the range of other flowmeter types where total cost increases 200°C (392°F). This limitation makes it as pipe diameter rises, the cost of ultrasonic unsuitable where the system operates at high flowmeters remains constant regardless of pipe temperature such as in petrochemical refining diameter. This economic advantage is especially industries or power generation industries etc. relevant in the water treatment and oil and gas industries that are characterized by use of extra Poor Anti-Interference Ability large pipes. How they manage to keep their prices relatively low especially as they scale up These flowmeters are sensitive to noise makes them a go to solution for many use cases. from bubbles, fouling, pumps, and other such external sources which impose ultrasonic Versatile Flow Measurement Capability frequencies into the metering system. Such interferences can cause inaccuracies to appear in They are far more suited to address a the readings and require close attention to the number of flow metering problems because of operating conditions to obtain accurate their non-intrusive nature. They can measure measurements. almost all types of media, corrosive liquids, non-conductive liquids, and even explosive or Strict Installation Requirements radioactive fluids. Moreover, the application of For measurement accuracy, straight pipe Chemical Industries - Ideal for handling lengths are needed—20 diameters (20D) before aggressive and corrosive chemicals as they the meter and 5 diameters (5D) after the meter. do not interfere with the measurement. If these installation requirements are not met, the Pharmaceutical Industry - Accurate flow dispersion capability is expected to be poor measurements of conductive fluids in aseptic together with low measurement accuracy, and environments. further, piping adjustments might be required. Food and Beverage - To measure liquids such as milk, juices, and syrups for quality Installation Uncertainty measurement. Pulp and Paper Industry - Measuring pulp Certain errors can easily creep in during slurry and other thick liquids that traditional the installation process thus requiring competent meters cannot measure. personnel to undertake the installation process. Parts While the components do require the need for Several important components make up a very accurate alignment and positioning, this magnetic flowmeter, which monitors conductive fluid may complicate their eventual installation. flow. Impact of Pipeline Fouling One of the most detrimental impacts of deposits is the threshold effect in the measuring pipeline, which gradually degrades the accuracy of measurement. When the fouling is quite severe, the flow meter can read zero, thus causing working interruptions and possibly time-consuming exercises such as cleaning the Image from: system or re-calibrating the flow meter. https://sino-inst.com/wp-content/uploads/2019/11/Magnetic-Fl ow-Meter-Construction.png Electrodes - These are placed inside the flow tube and are responsible for detecting the E. MAGNETIC voltage generated by the fluid as it flows A magnetic flow meter is a device that measures through the magnetic field. the velocity of a fluid and converts it into an electrical signal. The unique design of magnetic flow meters Magnetic Coils - These coils create a magnetic allows them to take their readings without the need for field across the flow tube. The fluid flowing any moving parts. This particular feature gives them the through this magnetic field induces a voltage ability to measure high pressure applications without any proportional to its velocity. fear of leakage. Flow Tube - This is the section of the pipe Operation where the fluid flows and the magnetic field is applied. It houses the electrodes and ensures The magnetic flowmeter generates a proper alignment for accurate measurement. magnetic field across the pipe. Voltage is Lining - The inner lining of the flow tube induced in a conductive fluid while moving prevents the conductive fluid from coming into with that field. direct contact with the metal body of the Electrodes located on the inner sides of the flowmeter, avoiding electrical short circuits. meter detect the induced voltage, which is proportional to flow velocity. Transmitter - This component converts the The device uses the voltage measured in voltage signal detected by the electrodes into a order to measure the flow rate accurately, flow rate reading. It processes the signal and even in challenging environments involving displays the flow rate. slurries or corrosive fluids. Industrial Applications Demo Video Water and WasteWater Treatment - Sewage, Link: Magnetic Flow Meter sludge as well as raw water measurement for efficient treatment processes. There are two coils that create a magnetic field. When because it decreases the number of types of the fluid is sitting still, positive and negative particles meters needed to be stored on site. are evenly distributed. Bidirectional Flow Measurement When the fluid starts to move, the magnetic field forces the particles to separate. Faster the flow, more the These flowmeters can also determine the particles separate. The more the particles separate, more real fluid rates in both the forward and back the voltage differential. These electrodes embedded in directions, which is essential for applications the side walls are then used to measure the voltage where direction may switch or backflow may created by the separated particles. happen through maintenance work or process modifications. And since that voltage is directly proportional to the rate of flow and the cross-sectional area is known, the meter Disadvantages can calculate the total flow. Inapplicability for Gases Advantages Magnetic flowmeters cannot measure Simple Sensor Structure gasses or vapors since they require conductive liquids and this limits them in operations The magnetic flowmeter contains the involving gaseous phase or liquid-gas mixture. simple body of the sensor, no moving part, low power consumptions and low maintenance. This Low Conductivity Limitations makes its usage to cause less wear and tear on its different parts in the long run thus it has lower They are ill-suited for measuring low operational cost than the electronic meter, which conductivity fluids (below 5 µS/cm), like refined usually has to be fixed or replaced within several oil or organic solvents, hence, this limitation years for efficient usage. narrows applications in processes involving these media. Capability to Measure Corrosive Media Temperature Measurement Limitations Magnetic flowmeters are also ideal for measuring highly corrosive fluids since the Like with ultrasonic meters, magnetic metering tube is open, however, only the lining flowmeters are used to assess fluids that are not and electrodes come into contact with the fluid. hot, normally the maximum temperature should This design choice allows users to choose not exceed 200°C (392°F), which means they materials in relation to fluidity (for example, are not suitable for high temperature processes rubber interiors for aggressive agents) which such as steam generation or hot oil makes it possible to use them in chemical transportation. production, food industry, and water treatment field. Electromagnetic Interference Sensitivity Independence from Fluid Properties These meters should be protected from outside electromagnetic influence which may These flowmeters determine volume impact the accuracy of measurement, thus, it is flow without influence of temperature, viscosity important to avoid placing these meters close to or density changes provided that the motors or transformers during installation. conductivity of the fluid is above 5 µS/cm. It guarantees accurate reading irrespective of the Initial Calibration Requirements prevailing conditions and the type of the fluid being measured–which makes it very useful in Despite the fact that magnetic processes that need to be tightly controlled. flowmeters are quite stable once installed, an initial calibration often has to be done with a Wide Measurement Range Flexibility standard liquid, usually water, thereby increasing start-up time in new systems. Magnetic flowmeters boast an impressive range capability—often up to 100:1—enabling them to work efficiently at both low and high flow rates without the need for F. CORIOLIS purchasing different kinds of equipment. This flexibility has beneficial effects on operators A Coriolis flow meter measures the mass flow Image from: rate of liquids and gasses by utilizing the Coriolis effect. https://th.bing.com/th/id/OIP.116Sm5X04gsNrac_2Ln It does this by vibrating tubes through which the fluid 4qQHaH9?rs=1&pid=ImgDetMain passes. The fluid flow causes a deflection in the Flow Tubes - These tubes vibrate to create vibration pattern, which is detected by sensors. The Coriolis forces as the fluid flows through them. degree of this deflection is directly related to the mass The most common designs include U-shaped or flow rate, allowing for highly accurate and direct straight tubes. measurements. Drive Coils - These coils induce vibration in the Operation flow tubes. The vibration is essential for creating the Coriolis effect, which is used to measure the Coriolis flow meters vibrate their tubes at a mass flow rate. known frequency. The fluid passing through these tubes produces a Coriolis force, causing Sensors - These detect the phase shift caused by the tubes to twist. the Coriolis effect. The sensors measure the time Sensors mounted on the tubes measure the delay between the vibrations of the inlet and phase shift that occurs because of this outlet sections of the flow tubes. deflection. The more mass flow rate, the Transmitter - This component processes the greater the twisting. signals from the sensors to calculate the mass It calculates mass flow rate and even density flow rate and density of the fluid. It also displays of the fluid based on phase shift and the flow rate and other relevant data. frequency modification. Mounting Frame - This frame holds the flow Industrial Applications tubes and other components in place, ensuring stability and accurate measurements. Oil and Gas - Applicable in the measurement of oil, natural gas, and refined products with high accuracy to support transfer or inventory control. Chemical Processing - Suitable chemical measurement to aggressive or highly viscous chemicals to ensure the accuracy with Demo Video security in a process. Food and Beverage -This follows the large Link: Coriolis Flow Meter size of syrups, oils, and dairy to ensure uniform quality in the final product. Shown in exaggerated detail, the measuring tube is Pharmaceutical - Assures dosing and flow oscillated and by using the Coriolis principle and with a clean environment that demands frequency of vibration, it can measure fluid mass flow accuracy. and density. Petrochemical and Refining - Measures With zero flow, oscillation is symmetrical and there is no hydrocarbons and heavy fluids up to extreme phase difference. As flow starts, the Coriolis effect pressures and temperatures. causes the relative phase of the measuring tube to change over its length. This phase difference is directly Parts proportional to the fluid mass flow rate. A Coriolis flowmeter employs a number of important components to determine mass flow rate and Advantages density. Highly Accurate Mass Flow Measurements The coriolis flowmeters are excellent in measuring mass flows because of their direct measurement principle using the Coriolis effect and not volume calculation, which makes them suitable for quality conscious industries such as pharmaceuticals and food processing. High Precision Density Measurement Besides providing superior mass flow accuracy, such flow meters also provide accurate The choice of materials for coriolis density measurements f