Industrial Pharmacy صيدلة صناعية PDF
Document Details
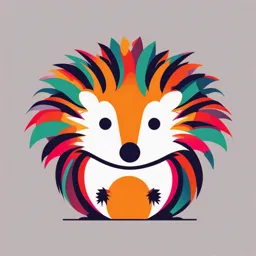
Uploaded by DashingDiscernment2526
Dr Ahmad Eid
Tags
Related
- Laporan PKPA Industri Periode Juli-Agustus (PDF)
- Laporan PKPA Industri Periode Juli-Agustus (Fixx) PDF
- M1 Intro to Manuf Pharmacy PDF
- Lecture 1: Overview of Pharmaceutical and Industrial Pharmacy Regulation PDF
- Pharmacy Careers Lecture 2 PDF
- Farmacotecnia II 2024 Module - Generalidades & Industrial Pharmacy
Summary
This document provides an overview of industrial pharmacy, covering topics such as job opportunities, types of pharmaceuticals, a history of Palestinian pharmaceutical industries, and various departments within the industry like Production, Quality Assurance, and Quality Control. It also discusses GMP (Good Manufacturing Practice) considerations.
Full Transcript
INDUSTRIAL PHARMACY صيدلة صناعية Dr Ahmad Eid “We are all members of the pharmaceutical industry – we either prescribe drugs, prepare drug or take them ourselves. We need to learn to work together.” IT INCLUDES MANY JOB OPPORTUNITIES: ...
INDUSTRIAL PHARMACY صيدلة صناعية Dr Ahmad Eid “We are all members of the pharmaceutical industry – we either prescribe drugs, prepare drug or take them ourselves. We need to learn to work together.” IT INCLUDES MANY JOB OPPORTUNITIES: Drug discovery Quality assurance Manufacturing Quality control Marketing Training & development Medical information Sales Product development Information technology The pharmaceutical industry develops, produces, & markets medicinal drugs. Pharmaceutical companies can deal in generic &/or brand medications. They are subject to a variety of laws & regulations regarding the patenting, testing & marketing of drugs. Brand Name: Marketed under a specific trade name by a pharmaceutical manufacturer and are still under patent protection. Generic Name: Made with the same active ingredients in the same dosage form as a brand name drug, but are sold to customer under the their chemical name. The industry was born just after the 1967 War as a result of the isolation of the West Bank from the rest of the Arab World. Before the 1967 War, all pharmaceutical products were imported from foreign companies via importers in Amman, Jordan. After the war, the borders were closed, thus preventing the import of any products from Jordan. The only products available were either produced in Israel or imported through Israeli agents. This difficult situation led nine pharmacists in the West Bank to establish small laboratories. They manufactured simple syrups and anti-diarrhoeal products in 1969. In 1970 these nine small laboratories merged to become three larger companies: Jordan Chemicals in Beit Jala; Palestine Medical Company in Ramallah; and Jerusalem Pharmaceuticals in El-Bireh. After 1970 the pharmaceutical industry started to grow and new companies entered the field: Balsam Company (El-Bireh, 1972); Birzeit Company (Birzeit, 1973); Eastern Medical Company and Gama (Ramallah, 1978); Pharmacare (Beitunia, 1985); and MASCO (Gaza, 1984). Currently we have five major Palestinian pharmaceutical companies: Quds Pharmaceuticals (Jepharm); Birzeit Pharmaceuticals (BPC); Beit Jala Pharmaceuticals; Pharmacare Pharmaceuticals; and Megapharm Pharmaceuticals. التوزيع الجغرافي لمصانع اﻷدوية وتاريخ تأسيسها ﺳﻨة الموقع الشركة التأﺳيس 1969 بيت جاﻻ شركة بيت جاﻻ لﻸدوية 1969 رام ﷲ-البيرة شركة القدس لﻸدوية 1970 رام ﷲ-الشرقية )قامت شركة بيزيت بشرائها( البيرة 1973 رام ﷲ-البيرة فلسطين-شركة بيرزيت لﻸدوية 2009 ﻧابلﺲ شركة سما لﻼدوية 1973 ( رام ﷲ )أغلقت-بيتوﻧيا جاما 1986 رام ﷲ-بيتوﻧيا دار الشفاء 1988 (الخليل )أغلقت الرازي 1981 (غزة )أغلقت الشركة العربية 1998 غزة الشرق اﻷوسط How the medicine ultimately reaches the patient Departments in Pharmaceutical Industry Production Finance department Quality Assurance(QA) Sales department Quality control(QC) Marketing Research & Technical department development(R&D) Human resources Regulatory affairs (RA) Information technology Industrial Pharmacy - Drs Ahmad Eid and Saed Khammash Departments in Pharmaceutical Industry Production This is the main department where manufacturing of API and / or Drug products take place. This contains various modules depending on the nature of the product (dosage form). Production of different dosage forms such as: tablets, capsules, creams, solutions …….. Departments in Pharmaceutical Industry…..Cont. Quality assurance It is the part of the Quality Management focused on providing confidence that quality requirements will be fulfilled. Multiple roles/functions within QA: Office based Review and control of documents, Checking & review of batch documents and test results versus specification, Documenting deviations from procedures. They will give the assurance to the product based on the analyzing data from quality control. Departments in Pharmaceutical Industry…..Cont. Quality control In this department they will analysis the drug, whether the drug is qualified to manufacture or not. Also after manufacturing they will determine the quality of product to release into market as per the specification. Lab based role. This includes quantification and qualification of the following, 1. Routine testing of raw materials, (Efficacy, Safety, Quality, Compliance with the international regulations) 2. In-process, 3. Finished product, packaging, 4. Stability testing, Departments in Pharmaceutical Industry…..Cont. Research & Development R & D is the heart of Pharmaceutical industry, as it is the key to growth and sustenance of the industry. Role of R & D: - New Drug Discovery Research. - Development of viable processes for the manufacture of drugs & intermediates for their commercial production. - Formulation & Development of Conventional and Novel Drug Delivery Systems. Departments in Pharmaceutical Industry…..Cont. Regulatory affairs Every Pharmaceutical Industry has now set up Regulatory Affairs Department. This mainly concern with legal documentation like, 1. Drug licensees from Drug Controller. 2. Drug and drug product registration 3. Various Drug Approval for marketing in various countries. 4. Internal Audit and Compliance. Departments in Pharmaceutical Industry…..Cont. Information Technology The Information Technology (IT) Department aims: - To conduct the establishment’s information management in the best possible manner by utilizing advanced data processing technologies. - To meet the information technology needs of all other departments. The goal is to use technology correctly and efficiently and to gain a competitive advantage in accord with company strategies. Departments in Pharmaceutical Industry…..Cont. Finance Department Finance Department, which play a vitally important role in the growth of all establishments. Achievement of business goals. Generally consists of: Payments, Accounting, Production Costs, Financial Process Development, Reporting and Budgeting. Departments in Pharmaceutical Industry…..Cont. Sales Department The goal of sales departments: - To provide information to physicians and pharmacists who inform and guide patients and families of patients with regard to drugs and patients in an accurate and scientifically-based manner. - To share information regarding drugs and treatments based upon scientific research with physicians and pharmacists. Departments in Pharmaceutical Industry…..Cont. Marketing The goal of marketing departments is: - To promote new products and treatments. - To present updated information in these areas to the medical world. - To raise public awareness regarding health issues. Departments in Pharmaceutical Industry…..Cont. Technical Department The Technical Department is responsible for ensuring that all equipments, tools and machinery within the establishment function accurately and efficiently. Departments in Pharmaceutical Industry…..Cont. Human Resource Provide training to the employee. Develop a training program. Training will : ensure dependability and reliability of staff, improve skill and GMP compliance, reduce error and mistakes. Provide quality employee. 9/7/2023 Pharmaceutical Plant Design Dr Ahmad Eid Introduction Plant Layout: Arrangement of physical facilities such as Machinery Equipment furniture etc. within the factory building in such a manner so as to have quickest flow of material at lowest cost & with the least amount of handling in processing the product from the receipt of material to the shipment of finished product. Pilot Plant: It is the part of the pharmaceutical industry where a lab scale formula is transformed into a viable product by development of practical procedure of manufacture. 1 9/7/2023 Importance An ideal plant layout should provide the optimum relationship among output, floor area & manufacturing process. Flexibility of operation. Easy production flow. Make economic use of building. Promotes effective utilization of manpower. Employee’s convenience. Safety. Comfort at work. Maximum exposure to natural light & ventilation. Pharmaceutical plant design 2 9/7/2023 Aims of manufacturing facility design 1. Designed to maximize protection against the entry of insects/ animals. 2. Microbiological contamination must be acceptably low. 3. Ensure that no unauthorized personnel gain entry to processing or storage areas. 4. Manufacturing efficiency: Correctly designed and located facilities within the manufacturing area will improve the efficiency of the manufacturing process and to optimize the production facility layout. Aims of manufacturing facility design 5. An acceptable working environment. - To ensure that the manufacturing area is designed and operated so that the exposure of personnel to drugs, solvents etc. is at an acceptably low level. - And by controlling the air flow and quality in the area with more toxic materials. Special breathing apparatus with appropriate filters may be necessary. - Comfortable working conditions should be provided for process operators. 3 9/7/2023 Achievement of manufacturing aims Environmental condition Control of the air temperature, relative humidity and particulate and microbial content is important. The specific conditions required depend on the product being manufactured. 99 Achievement of manufacturing aims For a tableting operation: temperature of 21 °C, a relative humidity of 35-40% and an air filtration target of 95% removal of particles less than 5 /µm. Hard gelatin capsule filling processes: temperature of 24°C and a relative humidity of approximately 30%. Air relative humidity is also vital when manufacturing deliquescent products, where levels as low as 20% may be required. 100 4 9/7/2023 Achievement of manufacturing aims With clean preparation areas the air particulate level is very important and the filtration target may be for more than 99% removal of particles of 1 µm or less. Typical 'comfortable' working conditions for operators are 18-24°C and 30-60% relative humidity. In manufacturing area, the stale air must be frequently 'replaced' with 'conditioned' air. 101 Achievement of manufacturing aims Architectural considerations Manufacturing areas should be of a suitable size, construction and location to facilitate proper operation, cleaning and maintenance. Pipework, light fittings or ventilation points: avoid the creation of recesses which might collect 'dust' and are difficult to clean and be accessible from outside the manufacturing area for maintenance. Interiorsurfaces should be smooth, free from cracks and open joints and permit easy and effective cleaning or disinfection. 102 5 9/7/2023 Classified and Non-Classified Areas in Pharmaceuticals Pharmaceutical industries classified areas based on activities. Classified Areas in Pharmaceuticals A classified Areas have control of airborne particle amount. These areas are constructed to minimize the generation introduction and retention of airborne particles in the area. An example of a classified area is Dispensing, Granulation, Compression, Coating, and primary Packing. Air comes into direct contact with the materials and product. 6 9/7/2023 Non-Classified Areas in Pharmaceuticals Non- classified areas have uncontrolled airborne particle amounts, but temperature and humidity are still maintained. Example of Non-classified area is RM store, Packing material store, change room, secondary packing hall, and quality control area. Non- classifies area design as the non-process area or area in which the product does not comes in direct contact with air. Sterile and Non-Sterile Pharmaceuticals Sterile Non-Sterile 7 9/7/2023 Sterile Pharmaceutical Products List Of Common Sterile Pharmaceutical Products: Ophthalmic preparations. Pulmonary or inhalational preparations. Parenteral drugs: Non-Sterile Pharmaceutical Products List Of Common Non-Sterile Pharmaceutical Products: Nasal sprays Vaginal suppositories Topicals Rectal suppositories Oral liquids (aqueous) Liquid-filled capsules, Oral tablets and powder-filled capsules. 8 9/7/2023 Sterile Pharmaceutical Products Grade A zone: The critical zone for high risk operations or for making aseptic connections by ensuring protection by first air (e.g. aseptic processing line, filling zone, stopper bowl, open ampoules and vials) Grade B area: For aseptic preparation and filling, this is the background cleanroom for the Grade A zone (where it is not an isolator) Grade C and D area: These are cleanrooms used for carrying out less critical stages in the manufacture of aseptically filled sterile products but can be used for the preparation /filling of terminally sterilized products Sterile Pharmaceutical Products Clean room and clean air device classification, in relation to GMP Annex 1 (2015). Maximum limits for total Maximum limits for total particle particle ≥0.5µm/m³ ≥5.0µm/m³ Grade At rest In operation At rest In operation A 3,520 3,520 Not applicable Not applicable B 3,520 352,000 Not applicable 2,930 C 352,000 3,520,000 2,930 29,300 D 3,520,000 Not defineda 29,300 Not defineda For Grade D, in operation limits are not defined. The company should establish in operation limits based on a risk assessment and historical 9 9/7/2023 Non-Sterile Pharmaceutical Products Environmental conditions EU regulations related to temperature and humidity controls Lighting, temperature, humidity and ventilation should be appropriate and such that they do not adversely affect, directly or indirectly, either the medicinal products during their manufacture and storage, or the accurate functioning of equipment Storage areas should be designed or adapted to ensure good storage conditions. In particular, they should be clean and dry and maintained within acceptable temperature limits. Where special storage conditions are required (e.g. temperature, humidity) these should be provided, checked and monitored. Other characteristics such as temperature and relative humidity depend on the product and nature of the operations carried out. Non-Sterile Pharmaceutical Products-Temperature Table 3: Suggested temperature ranges for facility space design conditions.a Space Lower Limit, °C Operating Range, °C Upper Limit, °C Raw materials warehouse 10 15–30 35 (ambient) Raw materials warehouse 15 20–25 30 Grade D 15 18–22 30 Grade C 15 18–22 30 Grade B 14 17–20 30 Grade A 14 17–20 30 Finished goods (refrigerated) 2 3–7 8 Finished goods (CRT) 15 20–25 30 Manufacturing Areas Temperature is generally controlled in the range of 15°C–25°C for manufacturing and storage facilities, except where a process or product requires more stringent control. 10 9/7/2023 Non-Sterile Pharmaceutical Products- Humidity As with temperature, regulatory guidance suggests that humidity levels should be appropriate for the product and process as well as for operator comfort and to limit shedding and sweating. Therefore, if humidity does not affect product and process, RH is commonly maintained within a band, at levels less than 60%, with the lower RH limit defined by local custom and practice. Non-Sterile Pharmaceutical Products- Humidity Table 4: Suggested RH ranges for facility space design conditions Lower Limit, % Operating Range, % Upper Limit, % Space RH RH RH Raw materials warehouse N/A 20–80 90 (ambient) Raw materials warehouse N/A 30–60 65b (controlled) Grade D 25 30–60 65b Grade C 25 30–60 65b Grade B 25 30–60 65b Grade A 25 30–60 65b Finished goods (refrigerated) N/A 20–80 90 Finished goods N/A 20–75 80 Dry storage N/A 30–40 45 11 9/7/2023 The pharmaceutical facility must be adequately designed to satisfy the following 1. Process requirements 2. Personnel flows 3. Material flows (product, component and raw material movements) 4. Equipment layout requirements 5. Operational access requirements 6. Maintenance access requirements Material and Personnel Flows 1. One-way flow is always preferred 2. Avoid simultaneous two-way flow through a common area 3. Gowning areas separated entry from exit 4. Airlocks should be used between areas of different classifications 12 9/7/2023 Material & Personnel Flow Example What are personnel flows, exactly? 1. Manufacturing personnel 2. Maintenance personnel 3. Quality control personnel 13 9/7/2023 What are material flows, exactly? 1. Raw materials 2. Finished goods 3. Waste 4. Product (In-process, Intermediate & Final) 5. Equipment: Clean and dirty components Portable equipment Product containers Manufacturing Units It divides in to four types: Product or line layout. Process or functional layout. Fixed position or location layout. Combined or group layout. 28 14 9/7/2023 Product layout Layout that uses standardized processing operations to achieve smooth, rapid, high-volume flow. Process layout Layout that can handle varied processing requirements. Fixed Position layout Layout in which the product or project remains stationary, and workers, materials, and equipment are moved as needed PRODUCT CELLULAR (Group Technology) PROCESS 30 FIXED POSITION 15 9/7/2023 Product or Line Layout Principles: All the machine tools or other items of equipment must be placed at the point demanded by the sequence of operations. There should no points where one line crossed another line. Materials may be fed where they are required for assembly but not necessarily at one point. All the operations including assembly, testing packing must be included in the Line. 31 Process Layout Principle The distance between departments should be as short as possible for avoiding long distance movement of materials. The departments should be in sequence of operations. The arrangement should be convenient for inspection and supervision. 32 16 9/7/2023 Fixed Position or Location Layout Principle: In this type of layout, the major product being produced is fixed at one location. Equipment, labour and components are moved to that location. All facilities are brought and arranged around one work centre. 33 Combined Layout Principle: In most of industries, only a product layout or process layout or fixed location layout does not exist. Generally, a combination of the product and process layout or other combinations are found, in practice. 34 17 9/7/2023 Materials of fabrication: Desirable properties and selection Factors affecting the selection materials for the construction of satisfactory plant include: Chemical Factors Physical Factors Economic Factors 107 18 9/7/2023 Chemical Factors Two aspects of chemical action must be considered: 1. Thepossible contamination of the product by the material of the plant, 2. Theeffect on the material of the plant by the drugs and chemicals being processed. The impurities have considerable toxicological effects, and even trace amounts of impurity may initiate decomposition mechanisms in the product. 108 Physical factors An ideal construction material would satisfy all the following criteria: Strength Weight Wearing qualities Ease of fabrication Thermal expansion Thermal conductivity Cleaning Sterilization Transparency 109 19 9/7/2023 Economic factors Cost and maintenance of plant must be economic. The main concern is not simply to obtain the least costly material: better wearing qualities and lower maintenance may well mean that a higher initial cost is more economical in the long run. 110 Building & Facilities (Premises) Important aspects to ensure the suitability of the operations to be carried out for different dosage forms and product range: Location. Design. Construction. Adaptation. Maintenance. 20 9/7/2023 Building & Facilities (Premises)…..Cont. Location Geography, climate, noise and economic factors. Neighbours What do they do? What impact can they have on the business? Pollution/effluent control. Minimum risk for contamination of products and materials. Building & Facilities (Premises)…..Cont. Design Suitable design and construction to facilitate good sanitation Cleaning and disinfecting according to detailed written procedures – records maintained Maximum protection against entry of insects, birds and animals Procedure for rodent and pest control 21 9/7/2023 Building & Facilities (Premises)…..Cont. Construction Suitable materials. Electrical supply. Suitable lighting (especially for visual on-line checks). Temperature and relative humidity control. Appropriate and effective ventilation. These may affect products during manufacture or storage as well as functioning of equipment. Building & Facilities (Premises)…..Cont. Construction Dust generating operations. e.g. during sampling, weighing, mixing, packing of powders, etc.) Measures should be taken to prevent cross-contamination. Measures to facilitate cleaning. 22 9/7/2023 Not present any hazard to the product. Part of prod equipment which have direct contact with product MUST NOT BE reactive, additive or adsorptive, e.g: Stainless steel, Teflon. Production & Process Control Minimize risk of cross-contamination: Dedicated and self-contained facilities for some products such as highly sensitizing materials (e.g. penicillin) or biological preparations (e.g. live microorganisms). Separate facilities for other products such as some antibiotics, hormones, cytotoxic substances. Non-pharmaceuticals normally not in the same facility, e.g. pesticides, herbicides 23 9/7/2023 Production & Process Control…..Cont. Layout in accordance with sequence of production. Appropriate cleanliness level. Adequate work and in-process storage space. Orderly and logical positioning of equipment, minimizes risk of contamination, mix-ups and missing production steps. Specially designed areas for packaging. Production & Process Control…..Cont. 24 9/7/2023 Weighing areas Weighing operations – in separated areas. Appropriate design (see also training material on HVAC). Provision for dust control. Smooth, impervious, durable, easy-to-clean finishes. Cleaning procedures and records. Documentation. Storage areas Storage areas of sufficient capacity. Orderly storage of categories of materials and products Separate and segregated areas: starting materials, packaging materials, intermediates, bulk, finished products, quarantined, released, rejected, returned and recalled products and materials. Appropriate temperature and relative humidity conditions within defined limits. Provided, controlled, monitored and recorded Good storage conditions: clean, dry and appropriate light. 25 9/7/2023 Storage areas…..Cont. Laboratory Control QC laboratories should be separate from production areas. Separate areas for biological, microbiological and radioisotope methods. Suitable design with sufficient space to avoid mix-ups and cross-contamination. Suitable space for storage samples, reference standards, solvents, reagents and records. 26 9/7/2023 Laboratory Control…..Cont. Suitable construction materials. Prevention of fumes. Ventilation. Separate air supply (production and QC). Separate rooms for some instruments to protect them from interference (e.g. electrical, vibration, moisture, etc.). 27 9/7/2023 GMP CONSIDERATIONS Dr Ahmad Eid What is GMP ? That part of Quality assurance. The procedures employed to ensure that the drug product or substance is manufactured under a quality management system and meets the claimed requirements for purity, identity, safety and quality. "GMP" - A set of principles and procedures which, when followed by manufacturers for therapeutic goods, helps ensure that the products manufactured will have the required quality. 1 9/7/2023 What is cGMP ? Usually “cGMP” – where c = current, to emphasize that the expectations are dynamic. Reminding manufacturers that they must employ technologies and systems that are up-to-date in order to comply with the regulation. Why GMP is important – A poor quality medicine may contain toxic substances that have been unintentionally added. – A medicine that contains little or none of the claimed ingredient will not have the intended therapeutic effect. 2 9/7/2023 GMP Covers… ALL aspects of production; from the starting materials, premises and equipment to the training and personal hygiene of staff. Detailed, written procedures are essential for each process that could affect the quality of the finished product. There must be systems to provide documented proof that correct procedures are consistently followed at each step in the manufacturing process - every time a product is made. QUALITY RELATIONSHIP Quality Management QA GMP Quality Assurance QC G.M.P. Quality Control 3 9/7/2023 QA, GMP & QC inter-relationship…..Cont. QA It is the sum total of the organized arrangements with the objective of ensuring that products will be of the quality required for their intended use QA, GMP & QC inter-relationship…..Cont. GMP Is that part of Quality Assurance aimed at ensuring that products are consistently manufactured to a quality appropriate to their intended use 4 9/7/2023 QA, GMP & QC inter-relationship…..Cont. QC Is that part of GMP concerned with sampling, specification & testing, documentation & release procedures which ensure that the necessary & relevant tests are performed & the product is released for use only after ascertaining it’s quality GMP 5 9/7/2023 GMP Beyond GMP Reduce pollution - Zero discharge. Adaptation of environment friendly methods. Consideration for better and healthier life tomorrow. Consideration of ethics in life. One should begin with end in mind otherwise it will be the beginning of the end. 6 9/7/2023 GMP 9/7/2023 Dr. Hani Shtaya, Dr Ahmed Eid 13 What are the objectives of GMP ? a) Provide consistent quality product. b) Maintain consistent reproducible processes. c) Reduce the need of extensive testing of each batch through quality assurance. d) Maintain the ability to reconstruct past production through accurate records. e) Develop the ability to predict future process performance based on past results. 7 9/7/2023 The GMP Institute was established Ten Principles of cGMP Principle1: Writing detailed step-by-step procedures that provide a roadmap for controlled and consistent performance. Principle2: Carefully following written procedures to prevent contamination, mix-ups and errors Importance of Written Procedures Importance of Written Taking shortcuts may save Procedures time or make the task easier, but you should never deviate Procedures should be from a written procedure Clear , Concise and without the approval of a Logical supervisor or Quality Department The GMP Institute has established Ten Principles of cGMP Principle3: Promptly and accurately documenting work for compliance and traceability. Principle 4: Proving that systems do what they are designed to do by validating Validate and Document Work To prove that our equipment and process consistently do what they are supposed to do 8 9/7/2023 The GMP Institute has established Ten Principles of cGMP Principle 5: Develop a good design for the facility and the equipment from the beginning. Principle 6: Properly maintaining facilities and equipment. Design , construction and maintenance of the facility and equipment A Logical and well planning layout will improve productivity. Remove unnecessary traffic in the production area Segregate materials , products, and their components to minimize the confusion and potential mix-ups and errors It is important to control : 9/7/2023 Dr. Hani Shtaya, Dr Ahmed Eid 17 Air, Water, Lighting, Ventilation, Temperature and RH The GMP Institute has established Ten Principles of cGMP Principle7: Clearly defining, developing and demonstrating job competence. GMP makes for Competent Employees Training: include basic training on the theory and practice of GMP as well as specific training relative to their role Companies need people who know to do the job right the first time , every time 9/7/2023 Dr. Hani Shtaya, Dr Ahmed Eid 18 9 9/7/2023 The GMP Institute has established Ten Principles of cGMP Principle 8 : Protecting products against contamination by making cleanliness a continual habit. Practice good Hygiene Health examinations Written procedures and instructions - to wash hands before entering production areas. Direct contact between product, raw materials and operator Should be avoided Protection of product from contamination: Clean clothes appropriate to personnel activities Including hair covering (e.g. caps) Check change rooms/changing facilities Smoking, eating and drinking not allowed in production areas, laboratories and storage areas No chewing (e.g. gum), or keeping food or drinks allowed No plants kept inside these areas Rest and refreshment areas 9/7/2023 Dr. should beDrseparate Hani Shtaya, Ahmed Eid from manufacturing and 19 control areas The GMP Institute has established Ten Principles of cGMP Principle 9: Building quality into products by.. Systematically Systematically controlling our packaging and controlling components labeling manufacturing and products control processes Holding and distribution control 10 9/7/2023 The GMP Institute has established Ten Principles of cGMP Principle 10 : Conducting planned and periodic audits for compliance and performance. CURRENT GOOD MANUFACTURING PRACTICE FOR FINISHED PHARMACEUTICALS Subpart A--General Provisions Subpart B--Organization and Personnel Subpart C--Buildings and Facilities Subpart D—Equipment Subpart E--Control of Components and Drug Product Containers and Closures Subpart F--Production and Process Controls 11 9/7/2023 CURRENT GOOD MANUFACTURING PRACTICE FOR FINISHED PHARMACEUTICALS Subpart G--Packaging and Labeling Control Subpart H--Holding and Distribution Subpart I--Laboratory Controls Subpart J--Records and Reports Subpart K--Returned and Salvaged Drug Products CURRENT GOOD MANUFACTURING PRACTICE FOR FINISHED PHARMACEUTICALS Active ingredient or active pharmaceutical ingredient (API) Active pharmaceutical ingredient means any substance that is intended for incorporation into a finished drug product and is intended to provide pharmacological activity or other direct effect: Diagnosis, cure, mitigation, treatment, or prevention of disease, or to affect the structure or any function of the body. 12 9/7/2023 CURRENT GOOD MANUFACTURING PRACTICE FOR FINISHED PHARMACEUTICALS Batch A specific quantity of a drug of uniform specified quality produced according to a single manufacturing order during the same cycle of manufacture CURRENT GOOD MANUFACTURING PRACTICE FOR FINISHED PHARMACEUTICALS Lot: A batch or any portion of a batch having uniform specified quality and a distinctive identifying lot number. Lot number, control number, or batch number: Any distinctive combination of letters, numbers, or symbols from which the complete history of the manufacture, processing, packaging, holding, and distribution of a batch or lot of a drug product may be determined. 13 9/7/2023 CURRENT GOOD MANUFACTURING PRACTICE FOR FINISHED PHARMACEUTICALS Certification: Documented testimony by qualified authorities that a system qualification, calibration, validation, or revalidation has been performed appropriately and that the results are acceptable. Compliance: Determination through inspection of the extent to which a manufacturer is acting in accordance with prescribed regulations, standards, and practices. CURRENT GOOD MANUFACTURING PRACTICE FOR FINISHED PHARMACEUTICALS Component: Any ingredient used in the manufacture of a drug product, including those that may not be present in the finished product. Inactive ingredient: Any component other than the active ingredients in a drug product. Drug product: A finished form that contains an active drug and inactive ingredients. The term may also include a form that does not contain an active ingredient, such as a placebo. 14 9/7/2023 CURRENT GOOD MANUFACTURING PRACTICE FOR FINISHED PHARMACEUTICALS Master record: Record containing the formulation, specifications, manufacturing procedures, quality assurance requirements, and labeling of a finished product CURRENT GOOD MANUFACTURING PRACTICE FOR FINISHED PHARMACEUTICALS Quality audit: A documented activity performed in accordance with established procedures on a planned and periodic basis to verify compliance with the procedures to ensure quality. 15 9/7/2023 CURRENT GOOD MANUFACTURING PRACTICE FOR FINISHED PHARMACEUTICALS Quarantine: An area that is marked, designated, or set aside for the holding of incoming components prior to acceptance testing and qualification for use. CURRENT GOOD MANUFACTURING PRACTICE FOR FINISHED PHARMACEUTICALS Reprocessing: The activity whereby the finished product or any of its components is recycled through all or part of the manufacturing process. Strength: The concentration of the drug substance per unit dose or volume 16 9/7/2023 CURRENT GOOD MANUFACTURING PRACTICE FOR FINISHED PHARMACEUTICALS Documentation Good documentation is an essential part of the quality assurance system and, as such, should exist for all aspects of GMP. Aims are to: 1. Define the specifications and procedures for all materials and methods of manufacture and control. 2. Ensures that all personnel concerned with manufacture know what to do and when to do it. 3. Ensures the existence of documented evidence and to provide records that will permit investigation. 4. Ensures the availability of the data needed for validation, review and statistical analysis. 17 9/7/2023 Documents required Labels: Labels applied to containers, equipment or premises should be clear. Validation of manufacturing facilities is a component of cGMP. Defined as 'establishing documented evidence which provides a high degree of assurance that a specific process will consistently produce a product meeting its predetermined specifications and quality characteristics'. In other words, validation is proving that a process works. 18 9/7/2023 Validation of manufacturing facilities Validation of all aspects of manufacturing a process. This includes bulk drugs, excipients, suppliers, analytical methods, computer systems and personnel, equipments and processes. It must be ensured that the manufacturing equipment complies with the intended specification and that all services and recording equipment function correctly. Types of Validations 1. Prospective validation This is where the validation programme is designed before the equipment or facility is used, or before the product manufactured by the process being validated is distributed. This type of validation is employed when producing the data on initial full-scale production batches required to obtain a regulatory authorization for marketing and manufacture of that product. 19 9/7/2023 Types of Validations 2. Retrospective validation This is achieved by reviewing historical manufacturing and testing data of products or processes which are already in operation and working well. 3. Concurrent validation This is ongoing prospective validation or ongoing review and evaluation of historical data. 4. Revalidation Involves repeating all or part of the validation if, for example, a process or facility is modified. 106 20 9/30/2023 New Drug Product Development Dr Ahmad Eid Introduction The success of pharmaceutical companies is completely depends on drug discovery. It involved great amount of time and money. The highly successful companies have a great teams dedicated for R&D, who are continuously keeping their efforts to build and develop new molecules or medicines. 1 9/30/2023 Introduction…..Cont. Drug: Any chemical compound which produces a change in the body. Active Pharmaceutical Ingredient (API) Active pharmaceutical ingredient means any substance that is intended for incorporation into a finished drug product and is intended to provide pharmacological activity or other direct effect in the diagnosis, cure, mitigation, treatment, or prevention of disease, or to affect the structure or any function of the body. Introduction…..Cont. A New Chemical Entity (NCE): According to the FDA, NCE is a drug that contains no active moiety that has ever been approved by the FDA. That means; the drugs in this class does not have a single approved moiety that is active. A New Molecular Entity (NME): The term describes any drug that contains an active moiety which has never been approved by the FDA. 2 9/30/2023 What is the Difference Between NCE and NME? The terms NCE and NME are used to categorize drugs according to the presence or absence of active moieties. Moreover, there is another difference between NCE and NME in the time period given for market data exclusivity; for NCE, the time period for market data exclusivity is five years, and for NME, it is three years. Introduction…..Cont. 3 9/30/2023 The new drug development process of a new chemical entity from discovery through preclinical and clinical studies, FDA review of the NDA, and post-marketing activities. Sources of New Drugs New drugs may be discovered from a variety of natural sources (e.g., plants), synthesized in the laboratory, or created through processes of biotechnology. 1. Plant materials: have provided drugs that are mannered from their tissues or through their biologic processes. 2. Animals: Hormonal substances, such as thyroid extract, insulin, and pituitary hormone obtained from the endocrine glands of cattle, sheep, and swine, are lifesaving drugs used daily as replacement therapy in the human body. 4 9/30/2023 3. A new era in the development of pharmaceutical products- genetic engineering The two basic technologies that drive the genetic field of drug development are Recombinant DNA and Monoclonal antibody (mAb) production Human gene therapy, used to prevent, treat, cure, diagnose, or mitigate human diseases caused by genetic disorders, is another promising new technology. How are drugs discovered and developed? Choose a disease Choose a drug target Identify a “bioassay” bioassay = A test used to determine biological activity. 5 9/30/2023 How are drugs discovered and developed?.....Cont. Find a “lead compound” “lead compound” = structure that has some activity against the chosen target, but not yet good enough to be the drug itself. If not known, determine the structure of the “lead compound” How are drugs discovered and developed?.....Cont. Identify the “pharmacophore” pharmacophore = The structural features directly responsible for activity. Optimize structure to improve interactions with target. 6 9/30/2023 How are drugs discovered and developed?.....Cont. Determine toxicity and efficacy in animal models. This process Called Preclinical Phase. How are drugs discovered and developed?.....Cont. Patent the drug Continue to study drug metabolism Continue to test for toxicity 7 9/30/2023 How are drugs discovered and developed?.....Cont. Design a manufacturing process to carry out clinical trials. Investigational New Drug (IND) IND Application is submitted to FDA (Food and Drug Administration). Application includes: The results of the preclinical work. The drugs chemical structure and how it is thought to work in the body. A list of any side effects and manufacturing information. A detailed clinical trial plan, that outlines how, where and by whom the studies will be performed. 8 9/30/2023 Clinical Test This phase is the longest one in drug development ranging from 2-10 years. A suitable clinical trial design is developed. Clinical trials comprise of three phases: Phase 1. Phase 2. Phase3. 9 9/30/2023 Clinical Trials…..Phase I: Drug is tested on healthy volunteers (20-100).(unless the drug is prepared for serious indications for example cytotoxic drugs for cancer). Phase I trials are designed to test, study a new drug or combination, on the human body, and to ensure the maximum dose humans can take in the absence of serious adverse effects or toxicities. Used to determine toxicity relative to dose and to screen for unexpected side effects. How the drug is absorbed, metabolized and excreted. Phase I trials involve mainly three particular types of studies: single ascending dose (SAD) at first, after that multiple ascending dose (MAD), and then examination of the effect of food on the drug. Usually last 6 months to 1 year. (30% of drugs fail phase 1). Difference between a Multiple Ascending Dose (MAD) study and a Single Ascending Dose (SAD) study The main difference is the number of doses given to individual study subjects. Subjects in a MAD study receive multiple doses of the study drug, whereas subjects in a SAD study receive only one dose of the study drug. SAD studies are almost always performed first in order to obtain a rough understanding of a drug’s single dose pharmacokinetics. The repetitive dosing in a MAD study allows steady state to be reached, which is when the rate of drug absorption is equal to the rate of drug elimination. When this occurs, the concentration of drug in the body is in equilibrium. Although steady state concentrations can be predicted from a single-dose study, a multiple-dose study provides empirical confirmation. 10 9/30/2023 Clinical Trials…..Phase 2: 100 to 500 patients with the disease or condition under study. To check the efficacy and the impact of the drug on the body, and to carry on with the Phase I safety estimation and assessment and adverse effects. Some of patients are given placebo- not a real drug it has no efficacy. This is depleted to understand and determine if the drug is really helping the patient to stop or reduce suffering from the condition or not Upon passing this Phase, chances of the product reaching to the market will be 60%. Last for 2 years. (37% of drug fail phase 2 testing). Clinical Trials…..Phase 3: Drug is tested on much larger group of patients (1000-5000). Compared with existing treatments and with a placebo. Purpose is to: Confirms earlier efficacy results Identify adverse events which when drug is given to a larger population over a longer period of time If passed this phase, chances of the product reaching to the market will be 70%. Verifies the drug’s effectiveness in its intended use. Usually Last 3 years (6% fail phase 3 testing). 11 9/30/2023 NDA Filing Upon desirable results from Phase III, New Drug Application (NDA) will be submitted. NDA contains all data supporting the efficacy and safety of the drug from the pre-clinical and clinical studies. Approval can take 2 month to several years, but on average, it takes around 18 to 24 months. Drugs are subject to ongoing review, making sure no adverse side effects appear from the drug. After FDA’s approval, the drug can be marketed and distributed Product Development Pre Formulation: Characterization of the physical and chemical properties of the active ingredient. The therapeutic indication of the drug and the route of administration. (Performed during the preclinical stage). Selection and characterization of dosage form. 12 9/30/2023 Product Development……Cont. Pre Formulation………….cont Formulation Development: Initial drug formulations are developed for early clinical studies. The dose of the drug and the route of administration are important. Product Development……Cont. Marketed Product: Considerations: Colour, Size, Shape, Viscosity, Skin feel……. Size and Shape of the container. Production Size. Country of origin in which the drug is to be manufactured and marketed. 13 9/30/2023 Clinical Trials…..Cont. Drug is placed on the market and patients are monitored for side effects. Clinical Trials…..Cont. Post-marketing surveillance Post-marketing surveillance refers to the ongoing monitoring of a product's safety and efficacy after it has been approved and made available on the market. Pharmacovigilance Pharmacovigilance (PV) is defined as the science and activities relating to the detection, assessment, understanding and prevention of adverse effects or any other drug-related problem. The prompt reporting of adverse reactions can lead to the early identification of Falsified (SF) medical products. 14 9/30/2023 15 9/7/2023 CLARIFICATION UNIT OPERATION Dr Ahmad Eid CLARIFICATION A process that involve the removal or separation of a solid from a fluid, or a fluid from another fluid. The term ‘fluid’ encompasses both liquids and gases. Clarification can be achieved using either filtration or centrifugation techniques. 1 9/7/2023 FILTRATION The separation of solid from a fluid by means of a porous medium that retains the solid but allows the fluid to pass. Slurry: The suspension of solid and liquid to be filtered. Filter Medium: The porous medium used to retain the solids. Filter Cake: The accumulation of solids on the filter. Filtrate: The clear liquid passing through the filter. TYPES OF FILTRATIONS: 1. Solid/Fluid filtration. Solid/Liquid filtration. Solid/Gas filtration. 2. Fluid/Fluid filtration. 2 9/7/2023 SOLID/FLUID FILTRATION Some application of solid/liquid filtration in pharmaceutical processes. Improve of appearance of solutions to give them sparkle or brightness. This is often referred to as ‘clarifying a product’. e.g. Mouthwashes. Removal of potential irritant. e.g. Eye drop preparations or solutions applied to mucous membranes. Recovery of desired solid material from a suspension or slurry. e.g. To obtain drug or excipient after a crystallization process. SOLID/FLUID FILTRATION Certain operations may yield a turbid product with a small quantity of fine suspended in it. This can be removed by filtration. e.g. The extraction of vegetable drugs with a solvent. Sterilization of liquid or semisolid product, Where heat process is not appropriate. Detection of microorganisms present in liquids. e.g. Checking the availability of microorganisms in sterile product. 3 9/7/2023 SOLID/GAS FILTRATION There are two main applications of solid/gas filtration in pharmaceutical processing: 1. The removal of suspended solid material from air in order to supply air of the required standard for processing equipment. e.g. Fluidized-bed processors, film-coating machinery. 2. The removal of suspended solid material from air in order to supply air of the required standard for manufacturing areas. e.g. Filter the air which inter the production area, also to remove particulate matter (dust) generated during a manufacturing operation. FLUID/FLUID FILTRATION Flavouring oils are sometimes added to liquid preparations in the form of a spirit, (i.e. dissolved in alcohol). When these spirits are added to aqueous-based formulations some of the oil may come out of solution, giving the product a degree of turbidity. Removal of the oil droplets by passing them through an appropriate filter (a liquid/liquid filtration process) is used to produce the desired product appearance. 4 9/7/2023 DARCY'S LAW Filtration rate: V/dt = KA ∆p/ƞL Where, V = volume of filtrate t =time of filtration K= constant for the filter medium and filter cake. A= area of filter medium ΔP = pressure difference above the filter medium and below the filter medium i.e. on the filtrate. Ƞ = viscosity of the filtrate. L = thickness of the filter bed i.e. thickness of the filter cake and filter medium. FACTORS AFFECTING RATE OF FILTRATION 1. Area of filter surface. 2. Particle size of cake solids. 3. Pore size of filter media. 4. The resistant of the filter cake. 5. The resistant of the filter media. 6. Viscosity of liquid to be filter. 7. Temperature. 8. Pressure difference across the filter. 5 9/7/2023 METHODS USED TO INCREASE FILTRATION RATE Increase the area available for filtration. Increase the pressure difference across the filter cake. Decrease the viscosity of liquid to be filter (Slurry). Decrease the thickness of the filter cake. Increase the permeability of the cake. INDUSTRIAL FILTRATION EQUIPMENT Filters for liquid products may be classified by the method used to drive the filtrate through the filter medium. Filters can be organized into three classes, Gravity filters. Vacuum filters. Pressure filters. 6 9/7/2023 GRAVITY FILTERS Filters that rely solely on gravity generate only low operating pressures and therefore use on a large scale is limited. Gravity filters are, simple and cheap, and are frequently used in laboratory filtration where volumes are small and a low filtration rate is relatively unimportant. BUCHNER FUNNEL An import component of vacuum filtration procedures. It is a piece of laboratory equipment 7 9/7/2023 PRESSURE FILTERS Pressure filters feed the product to the filter at a pressure greater than that which would arise from gravity alone. This is the most common type of filter used in the processing of pharmaceutical products. THE METAFILTER. The metafilter consists of a grooved drainage rod on which is packed a series of metal rings. These rings, usually made of stainless steel, are about 15 mm inside diameter, 22 mm outside diameter and 0.8 mm in thickness, with a number of semicircular projections on one surface. The height of the projections and the shape of the section of the ring are such that when the rings are packed together and tightened on the drainage rod, channels are formed that taper from about 250 µm down to 25 µm. 8 9/7/2023 9 9/7/2023 CARTRIDGE FILTERS Cartridge filters are now commonly used in the preparation of pharmaceutical products. They possess a very large filtration area in a small unit and are easy and relatively cheap to operate. They consist of a cylindrical cartridge containing highly pleated material (e.g. Polytetrafluorethylene (PTFE) or nylon). This cartridge can fits in a metal supporting cylinder and the product is pumped under pressure into one end of the cylinder surrounding the filter cartridge. 10 9/7/2023 CARTRIDGE FILTERS The filtrate is forced through the filter cartridge from the periphery to the inner hollow core, from where it exits through the other end of the support cylinder. The filter cartridges are often disposable and are good for applications where there is a low contaminant level, e.g. during the filtration of liquid products as they are filled into bottles. 11 9/7/2023 CROSS-FLOW MICROFILTRATION It is possible to form membrane filters within ‘hollow fibres’. The membrane, which may consist of polysulfone, acrylonitrile or polyamide (Nylon), is laid down within a fibre which forms a rigid porous outer support. The lumen of each fibre is small, typically 1–2 µm. However, a large number of fibres can be contained in a surrounding shell to form a cartridge which may have an effective filtration area of over 2 m2. In use, the liquid to be treated is pumped through the cartridge in a circulatory system, so that it passes through many times. The filtrate, which in this technique is often called the ‘permeate’, flows radially through the membrane and porous support. 12 9/7/2023 13 9/7/2023 FILTRATION OF AIR FOR ALL CLASSIFIED AREAS IN THE PRODUCTION SIDES Cleanrooms and Air Filtration Ultra low particulate air (ULPA) filters High Efficiency Particulate Air (HEPA) filters ULPA filters trap more and smaller particulate matter than HEPA filters. ULPA filters are 99.999% effective at removing submicron particulate matter of 0.12-micron diameter or larger, While HEPA filters are 99.97% effective for eliminating particulate matter of 0.3-micron diameter or larger. FILTRATIONOF AIR FOR ALL CLASSIFIED AREAS IN THE PRODUCTION SIDES Ultra low particulate air (ULPA) filters High Efficiency Particulate Air (HEPA) filters 14 9/7/2023 CENTRIFUGATION Centrifuges are often used in the laboratory to separate solid material from a liquid, the solid typically forming a ‘plug’ at the bottom of the test tube at the end of the process. Centrifugal force can be used either to provide the driving force (ΔP) for the filtration process (refer to Darcy’s equation) or to replace the gravitational force in sedimentation processes (refer to Stokes’ Law). PRINCIPLES OF CENTRIFUGATION If a particle (mass = m, kg) spins in a centrifuge (radius r, m) at a velocity (v, m s−1) Then the centrifugal force (F, N) acting on the particle = mv2/r. The same particle experiences gravitational force. (G, N) = m × g (where g = the gravitational constant). 15 9/7/2023 PRINCIPLES OF CENTRIFUGATION…..CONT. The centrifugal effect (C) is the ratio of these two forces, so C = F/G, i.e. C indicates how many times greater F is than G. If the rotational velocity is taken to be π d n, where n is rotation speed (s−1) and d is the diameter of rotation (m), Then C = 2.01 d n2. To increase the centrifugal effect, it is more efficient to increase the centrifuge speed than use a larger diameter at the same speed. PERFORATED-BASKET CENTRIFUGES (CENTRIFUGAL FILTERS) It consists of a stainless steel perforated basket (typically 1–2 m in diameter) lined with a filter cloth. The basket rotates at a speed which is typically