EASA Part 66 Module 15 Gas Turbine Engines PDF
Document Details
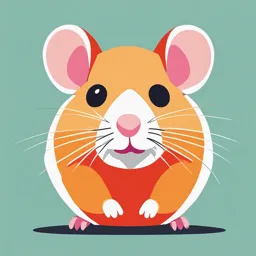
Uploaded by LowCostNeumann3181
IKAROS Aviation Training Center
2020
EASA
Alan Broadfoot
Tags
Summary
This document is a training manual for EASA Part 66 Module 15 on gas turbine engines. It details various components, sections, and principles of operation of gas turbine engines. It includes a table of contents and index.
Full Transcript
EASA Part 66 Module 15 - B1 GAS TURBINE ENGINES Issued Oct 2012/Reviewed. January 2020 PDF Pro Trial Part 66 Module 15 (Gas Turbine Engines) B1 This publication is issued to trainees of IKAROS Aviation Training...
EASA Part 66 Module 15 - B1 GAS TURBINE ENGINES Issued Oct 2012/Reviewed. January 2020 PDF Pro Trial Part 66 Module 15 (Gas Turbine Engines) B1 This publication is issued to trainees of IKAROS Aviation Training Center and is classified as ‘FOR TRAINING USE ONLY’ The information contained in this publication is not intended to substitute or replace any relevant technical publication issued by the aircraft competent design authority. The trainees shall always refer to the official documents issued to the aircraft user while performing activities on the aircraft. The information herein is updated at the date of release of this training publication and IKAROS does not take any commitment to update this material unless specifically requested. Issued Oct 2012/Reviewed. January 2020 PDF Pro Trial Part 66 Module 15 (Gas Turbine Engines) B1 INDEX OF SECTIONS 15.1 FUNDAMENTALS 15.2 ENGINE PERFORMANCE 15.3 INLET SECTION 15.4 COMPRESSORS SECTION 15.5 COMBUSTION SECTION 15.6 TURBINE SECTION 15.7 EXHAUST SECTION 15.8 BEARINGS and SEALS 15.9 LUBRICANTS and FLUIDS 15.10 LUBRICATION SYSTEMS 15.11 FUEL SYSTEMS 15.12 AIR SYSTEMS 15.13 STARTING and IGNITION SYSTEMS 15.14 ENGINE INDICATION SYSTEMS 15.15 POWER AUGMENTATION SYSTEMS 15.16 TURBO-PROP ENGINES 15.17 TURBO-SHAFT ENGINES 15.18 AUXILIARY POWER UNITS (APUs) 15.19 POWERPLANT INSTALLATION 15.20 FIRE PROTECTION SYSTEMS 15.21 ENGINE MONITORING and GROUND OPERATIONS 15.22 ENGINE STORAGE and PRESERVATION Issued Oct 2012/Reviewed. January 2020 PDF Pro Trial Part 66 Module 15 (Gas Turbine Engines) B1 INTENTIONALLY LEFT BLANK Issued Oct 2012/Reviewed. January 2020 PDF Pro Trial Part 66 Module 15 (Gas Turbine Engines) B1 Amendment Record INCORPORATED AL No. AL DATE SUBJECT BY: (a) (b) (d) (c) Alan Broadfoot Reviewed Jan 2020 Full reformat with all new pictures MISTC Alan Broadfoot Addition of Triple Spool engine 1 Feb 2020 MISTC description Addition of pic and small text free Alan Broadfoot 2 Feb 2020 power turboprops section 1 and new MISTC pic in section 16 Alan Broadfoot 3 March 2020 Small changes to header and footer MISTC 4 5 6 7 8 9 10 11 12 13 Issued Oct 2012/Reviewed. January 2020 PDF Pro Trial Part 66 Module 15 (Gas Turbine Engines) B1 Amendment Record AL No. AL DATE INCORPORATED BY: SUBJECT (a) (b) (c) (d) 14 15 16 17 18 19 20 21 22 23 24 25 26 27 28 Issued Oct 2012/Reviewed. January 2020 PDF Pro Trial Part 66 Module 15 (Gas Turbine Engines) B1 MODULE 15 – GAS TURBINE ENGINES Part 66 Ref 15.1 FUNDAMENTALS Potential energy, kinetic energy, Newton’s laws of motion, Brayton cycle. The relationship between force, work, power, energy, velocity, acceleration. Constructional arrangement and operation of turbo-jet, turbo-fan, turbo-shaft and turbo-prop engines. 15.2 ENGINE PERFORMANCE Gross thrust, net thrust, choked nozzle thrust, thrust distribution, resultant thrust, thrust horsepower, equivalent shaft horsepower and specific fuel consumption. Engine efficiencies. By-pass ratio and engine pressure ratio. Pressure, temperature and velocity of the gas flow. Engine ratings; static thrust, influence of speed, altitude and hot climate, flat rating and limitations. 15.3 INLET SECTION Compressor inlet ducts. Effects of various inlet configurations. Ice protection. 15.4 COMPRESSORS SECTION Axial and centrifugal types. Constructional features and operating principles and applications. Fan balancing. Operation. Causes and effects of compressor stall and surge. Methods of air flow control; bleed air valves, variable intake guide vanes, variable stator vanes and rotating stator vanes. 15.5 COMBUSTION SECTION Constructional features and principles of operation. Issued Oct 2012/Reviewed. January 2020 PDF Pro Trial Part 66 Module 15 (Gas Turbine Engines) B1 15.6 TURBINE SECTION Operation and characteristics of different turbine blade types. Blade to disk attachment. Nozzle guide vanes. Causes and effects of turbine blade stress and creep. 15.7 EXHAUST SECTION Constructional features and principles of operation. Convergent, divergent and variable area nozzles. Engine noise reduction. Thrust reverse systems. 15.8 BEARINGS and SEALS Constructional features and principles of operation. 15.9 LUBRICATION and FLUIDS Properties and specifications. Fuel additives. Safety precautions. 15.10 LUBRICATION SYSTEMS System operation / layout and operation. 15.11 FUEL SYSTEMS Operation of engine control and fuel metering systems including electronic engine control (FADEC). System layout and components. 15.12 AIR SYSTEMS Operation of engine air distribution and anti-ice control systems, including cooling, sealing and external air services 15.13 STARTING and IGNITION SYSTEMS Operation of engine start system and components. Ignition system and components. Maintenance Safety requirements. Issued Oct 2012/Reviewed. January 2020 PDF Pro Trial Part 66 Module 15 (Gas Turbine Engines) B1 15.14 ENGINE INDICATION SYSTEMS Exhaust gas temperature / inter-stage turbine temperature, engine thrust indication, engine power ratio, engine turbine discharge pressure or jet-pipe pressure systems. Oil pressure and temperature. Fuel pressure and flow. Vibration measurement and indication. torque. Power. 15.15 POWER AUGMENTATION SYSTEMS Operation and applications. Water injection / water methanol. Afterburner systems. 15.16 TURBO-PROP ENGINES Gas coupled / free turbine and gear coupled turbines. Reduction gears. Integrated engine and propeller controls. Over-speed safety devices. 15.17 TURBO-SHAFT ENGINES Arrangements, drive systems, reduction gearing, couplings and control systems. 15.18 AUXILIARY POWER UNITS (APUs) Purpose, operation and protective systems. 15.19 POWERPLANT INSTALLATION Configuration of firewalls, cowlings, acoustic panels, engine mounts, anti-vibration mounts, hoses, pipes, feeders, connectors, wiring looms, control cables and rods, lifting points and drains 15.20 FIRE PROTECTION SYSTEMS Operation of detection and extinguishing systems. Issued Oct 2012/Reviewed. January 2020 PDF Pro Trial Part 66 Module 15 (Gas Turbine Engines) B1 15.21 ENGINE MONITORING and GROUND OPERATIONS Procedures for starting and ground run-ups. Interpretations of engine power output and parameters. Trend monitoring (including oil analysis, vibration and boroscope). Inspection of engine and components to criteria, tolerances and data specified by engine manufacturer. Compressor washing and balancing. Foreign Object Damage (FOD). 15.22 ENGINE STORAGE and PRESERVATION Preservation and de-preservation for the engine and accessories/ systems. Extra Reading References Rolls Royce: The jet Engine Jeppeson: A & P Powerplant textbook Jeppeson: Gas Turbine Powerplant textbook Jeppeson A & P Airframe textbook AMT Mechanical Technicians Handbook Sherwin & Horsely - Thermodynamics Dale Clark - Dictionary of Aircraft Terms Issued Oct 2012/Reviewed. January 2020 PDF Pro Trial SECTION 15.1 FUNDAMENTALS Issued Oct 2012/Reviewed. January 2020 PDF Pro Trial Part 66 Module 15 (Gas Turbine Engines) B1 INTENTIONALLY LEFT BLANK Issued Oct 2012/Reviewed. January 2020 PDF Pro Trial Part 66 Module 15 (Gas Turbine Engines) B1 TABLE OF CONTENTS BASIC THEORIES.................................................................................................... 1 General............................................................................................................................ 1 Newton's Laws of Motion................................................................................................. 1 The Rocket Engine.......................................................................................................... 4 The Ram Jet.................................................................................................................... 6 THE TURBOJET ENGINE........................................................................................ 8 Introduction...................................................................................................................... 8 The Constant Pressure Cycle........................................................................................ 11 Constructional Arrangements........................................................................................ 11 Single Spool Axial Flow Engine..................................................................................... 12 Multi-Spool Design........................................................................................................ 13 BY-PASS ENGINES................................................................................................ 14 Twin Spool Low By-Pass Turbo Fan............................................................................. 14 High By-Pass Turbo Fan............................................................................................... 15 Twin Spool High Bypass................................................................................................ 16 Two-Spool vs Tree-Spool Turbofan Engines................................................................. 17 TURBO PROP ENGINES....................................................................................... 22 Introduction.................................................................................................................... 22 TURBO-SHAFT ENGINES...................................................................................... 25 Introduction.................................................................................................................... 25 EXAMPLES OF ENGINE ARRANGEMENTS......................................................... 26 LIST OF ILLUSTRATIONS...................................................................................... 28 Issued Oct 2012/Reviewed. January 2020 Page i PDF Pro Trial Part 66 Module 15 (Gas Turbine Engines) B1 INTENTIONALLY LEFT BLANK Issued Oct 2012/Reviewed. January 2020 Page ii PDF Pro Trial Part 66 Module 15 (Gas Turbine Engines) B1 BASIC THEORIES General To understand the working principle of the gas turbine engine, the following facts about physics must be studied. These are; Newton's Laws of Motion Behaviour of a gas as it flows through ducts of non-constant cross section. Newton's Laws of Motion First Law A body at rest tends to stay at rest and a body in motion tends to stay in motion in a straight line unless caused to change its state by an external force. This first law is of little importance to the function of the gas turbine engine. Second Law The acceleration of a body is directly proportional to the force causing it and inversely proportional to the mass of the body. The second law is the law which is used to determine exactly the amount of thrust achieved by the gas turbine engine. The second law can be written as a formula: Force = Thrust = Mass x Acceleration Issued Oct 2012/Reviewed. January 2020 Page 1 PDF Pro Trial Part 66 Module 15 (Gas Turbine Engines) B1 Third Law For every action there is an equal and opposite reaction. The third law is of most importance to us in understanding the gas turbine engine. What it is saying is that if a mass of air is propelled backwards, the object which propelled it will be propelled forwards at an equal rate. It follows then that the more air that the gas turbine engine can propel backwards, the greater will be the forward thrust of the engine. The second law also tells us that the greater the mass propelled backwards (m), the greater is the forward force (F). Fig 01. 01 - Gas Flowing through a Convergent Duct - Subsonic airflow Fig 01. 02 - Gas Flowing through a Divergent Duct - Subsonic airflow Issued Oct 2012/Reviewed. January 2020 Page 2 PDF Pro Trial Part 66 Module 15 (Gas Turbine Engines) B1 The ‘Choked’ Nozzle There is one, exception to the above rule, and that is when the gas is at the speed of sound (sonic velocity) just before it enters the divergent part of the duct. It is extremely difficult to accelerate a gas to supersonic speed - the only way to do it is to have a very high pressure to begin with and increase its speed in a ‘Convergent’ duct. Once it has reached sonic speed, it is impossible to increase its speed any further -the duct (or nozzle) is then said to be ‘CHOKED’. If this procedure is carried out in a Convergent-Divergent duct, an additional form of thrust (additional to Newton's Third Law) can be achieved. This can be visualised more easily if you think of a beach-ball being forced and compressed through a convergent-divergent duct. As it expands through the divergent duct, it will cause a forward reaction on the wall of the duct. Fig 01. 03 - Convergent/Divergent Duct - Sonic Airflow The application of the CHOKED CONVERGENT-DIVERGENT nozzle can be seen in supersonic military aircraft and rockets. Issued Oct 2012/Reviewed. January 2020 Page 3 PDF Pro Trial Part 66 Module 15 (Gas Turbine Engines) B1 The Rocket Engine Although the rocket engine is a jet engine, it has one major difference in that it does not use atmospheric air as the propulsive fluid stream. Instead, it produces its own propelling fluid by the combustion of liquid or chemically decomposed fuel with oxygen, which it carries, thus enabling it to operate outside the earth’s atmosphere. It is therefore, only suitable for operating over short periods. The fuel or propellant is carried in one tank and an oxidizer in another tank. These are typically pumped to and mixed in the combustion chamber where the fuel is burned. As the gases rush out of the nozzle at the back of the engine, thrust is produced. This nozzle has a definite shape and is known as a converging-diverging nozzle. This type of nozzle is required in rockets because of the desire for extremely high velocity (highly accelerated) exhaust gases. Issued Oct 2012/Reviewed. January 2020 Page 4 PDF Pro Trial Part 66 Module 15 (Gas Turbine Engines) B1 Fig 01. 04 - The Rocket Engine Issued Oct 2012/Reviewed. January 2020 Page 5 PDF Pro Trial Part 66 Module 15 (Gas Turbine Engines) B1 The Ram Jet The Ram Jet requires initial forward motion to get it started. It's operation is then as follows: Fig 01. 05 - The Ram Jet Intake The intake is convergent/divergent in shape and therefore the air flowing through it will decrease/ increase in pressure. Combustion At a certain pressure, the air is mixed with fuel and ignited. Its temperature will increase and it will expand. This expansion takes the form of an increase in velocity. If the gas increases in velocity inside the jet, it will obey Newton's 2nd Law, which is that: Force = Mass x Change in Velocity through the duct Issued Oct 2012/Reviewed. January 2020 Page 6 PDF Pro Trial Part 66 Module 15 (Gas Turbine Engines) B1 Exhaust Before entering the exhaust nozzle, the gas may be of high enough pressure to be accelerated to supersonic speed. The exhaust nozzle would then be choked. The force produced as a result of the acceleration is known as momentum or kinetic thrust. A second type of thrust is produced in the divergent part of the exhaust nozzle and is called pressure thrust. The total force produced will, according to Newton’s 3rd Law, produce an equal and opposite reaction on the inner workings of the engine. This is known as Thrust Issued Oct 2012/Reviewed. January 2020 Page 7 PDF Pro Trial Part 66 Module 15 (Gas Turbine Engines) B1 THE TURBOJET ENGINE Introduction In 1931 Sir Frank Whittle patented the self-sustaining Gas Turbine Engine. It consists of a single rotating spool comprising of a compressor and turbine. The advantage of this engine over the ram jet is that it is self-sustaining without the need for forward speed. In other words it can be started whilst stationary on the ground The engine is started by spinning the compressor. This establishes a rearward flow of air into the combustion zone where fuel is added and ignited. The gasses increase in temperature and therefore expand rearwards. Before the gasses reach the exhaust nozzle, some of its energy is extracted by rotating the turbine, which in turn drives the compressor. To increase the thrust of the gas turbine engine, more fuel is added which raises the energy level of the gas stream. The turbine will therefore be turned at a greater speed which will turn the compressor at a greater speed. The compressor will therefore deliver a greater mass of air, and the thrust force of the gas turbine engine is therefore increased according to Newton's 2nd Law. The thrust produced by the turbojet is proportional to the change in momentum of the gas stream. To increase the thrust, more fuel is introduced which raises the energy level of the gas stream and the turbine and compressor rotate at a higher speed. The compressor delivers a larger mass of air to the combustion zone and there is a corresponding increase in the thrust produced by the engine. The gas turbine can also be compared with the piston engine where fuel and air are burned inside a cylinder to cause a piston to move and turn a crankshaft. The working cycle of the gas turbine engine is indeed similar to that of the 4-stroke piston engine as in each gas turbine engine there is induction, compression, combustion and exhaust. Issued Oct 2012/Reviewed. January 2020 Page 8 PDF Pro Trial Part 66 Module 15 (Gas Turbine Engines) B1 In the piston engine cycle the combustion cycle is intermittent where as in the gas turbine engine it is continuous. The gas turbine engine has a separate compressor, combustion chamber, turbine wheel, and exhaust system with each part concerned only with its function. Thus the combustion in a gas turbine engine takes place as a continuous process at a constant pressure. This, combined with the absence of reciprocating parts, provides a much smoother running engine that can be of a lighter structure, enabling more energy to be released for useful propulsive work. Fig 01. 06 - The Pure Turbo-Jet The modern gas turbine engine is basically cylindrical in shape because it is essentially a duct in which a mass airflow is the same from the intake to the exhaust nozzle. Into this duct the necessary parts are fitted. The parts from front to rear are an air compressor, a combustion chamber, a turbine wheel, and an exhaust duct. A shaft connects the turbine wheel to the compressor, so that turning the turbine will also turn the compressor. Inside the combustion chambers are fuel burners and the means of igniting the fuel. Because the jet engine is basically an open ended duct it is not satisfactory to ignite the fuel in static air, because this would allow the gas to expand equally forwards and backwards without doing any useful work; when the air was used up the flame would die out. Issued Oct 2012/Reviewed. January 2020 Page 9 PDF Pro Trial Part 66 Module 15 (Gas Turbine Engines) B1 Before lighting the fuel it is, therefore, essential that the air is moving, and the moving columns of air must be moving through the engine from the front towards the rear. This movement is brought about by using a starter motor to spin the compressor and the turbine wheel in excess of 1500rpm; this drives a large volume of air through the combustion chamber. When the airflow is sufficient, fuel is injected into the chambers through spray nozzles, and is ignited by means of ignitor plugs. (Note that the gas turbine engine is not an alternate firing engine. The spark ignitors are only used for the initial firing, and the fuel in all the combustion chambers burns continuously like a blowtorch). This burning will cause the airflow towards the rear to increase in velocity and drive the turbine wheel as it flows over the turbine blades in its headlong rush through the exhaust system out to atmosphere. The spinning turbine wheel turns the compressor through the drive shaft, and the compressor feeds more air into the combustion chamber to complete a cycle of operations that continues as long as fuel is fed to the burners. The turbine wheel also originates a drive to a gearbox that provides external drives for items such as: Fuel Pumps Hydraulic Pumps Electrical Generators Other engine accessories Issued Oct 2012/Reviewed. January 2020 Page 10 PDF Pro Trial Part 66 Module 15 (Gas Turbine Engines) B1 The Constant Pressure Cycle The Constant Pressure Cycle or Brayton Cycle is so called because the heat is added within the combustion chamber where a theoretical constant pressure is maintained. (In fact there is always a very slight – less than 3% -pressure drop due to friction between the gases and the combustion liner. Fig 01. 07 - The Constant Pressure Cycle Constructional Arrangements The basic design of Whittles gas turbine engine exists in all gas turbine engines. However various applications have been derived over the past 60 years to suit the airframe and industrial requirements. Issued Oct 2012/Reviewed. January 2020 Page 11 PDF Pro Trial Part 66 Module 15 (Gas Turbine Engines) B1 Single Spool Axial Flow Engine A modern single spool axial flow turbojet engine produces its thrust from the acceleration of the flow of the hot gases. Air enters the engine inlet and flows into the compressor where its pressure is increased. Fuel is added in the combustor where it is ignited and burns The expanding of the gases as they leave the tail pipe produces the reaction we know as thrust. Fig 01. 08 - The Single Spool Axial Flow Engine The use of a multi stage axial flow compressor enabled higher compression ratios to be obtained and hence more thrust. The single spool turbo jet has very low propulsive efficiency, high specific fuel consumption (SFC) and an undesirable noise level. Issued Oct 2012/Reviewed. January 2020 Page 12 PDF Pro Trial Part 66 Module 15 (Gas Turbine Engines) B1 Multi-Spool Design Dual and triple spool axial compressors were developed for the operational flexibility they provide to the engine in the form of high compression ratios, quick acceleration, and better control of stall characteristics. This operational flexibility is not possible with single spool axial flow engines. For any given power lever setting, the high pressure (HP) compressor speed is held fairly constant by a fuel control governor. Assuming that a fairly constant energy level is available at the turbine, the low pressure (LP) compressor will speed up and slow down with changes in aircraft inlet conditions resulting in changes in atmospheric changes or manoeuvres in flight. The varying LP compressor output therefore, provides the HP compressor with the best inlet condition within the limits of the design. That is, the LP compressor tries to supply the HP compressor with a fairly constant air pressure for a particular air pressure for a particular power setting. To better understand when the low pressure compressor speed up and slow down, consider that when ambient temperature increases, the air's molecular motion increases. In order to collect air molecules at the same rate as temperature increases, the compressor would have to change either its blade angles, which it cannot do, or its speed, which it in fact does. Fig 01. 09 - A Twin Spool Axial Flow Engine Issued Oct 2012/Reviewed. January 2020 Page 13 PDF Pro Trial Part 66 Module 15 (Gas Turbine Engines) B1 BY-PASS ENGINES Twin Spool Low By-Pass Turbo Fan This type of engine has a twin spool layout with the addition that the L.P. compressor is of larger diameter than before and thus handles a greater mass of air than is required by the H.P. compressor. The airflow which is not required by the H.P. compressor is fed into the by-pass duct and it re-joins the normal gas flow behind the turbines. The airflow is split approximately 50 % each way. The mixing of the "hot" and "cold" gas streams promotes very rapid expansion of the gasses, which gives good power output with a low fuel consumption. Low bypass engines are defined as having a bypass ratio of 3:1 or less. Fig 01. 10 - A Adour Twin-Spool By-Pass Turbo-Jet Issued Oct 2012/Reviewed. January 2020 Page 14 PDF Pro Trial Part 66 Module 15 (Gas Turbine Engines) B1 High By-Pass Turbo Fan The difference in operation between a propeller and a pure jet engine can be summarised as follows; A propeller accelerates a large quantity of air rearwards at a low rate. A pure jet engine accelerates a small quantity of air rearwards at a high rate. The net result is the same, but the efficiency of each depends on the required speed of the aircraft. For medium speed aircraft, a combination of the two has been developed. On the following pages are two examples of high bypass multi-spool engines. High Bypass is defined as a bypass ratio of 4:1 up to 8: 1 Ultra high bypass engines are being researched with a bypass ratio of 10: 1 and above. A high bypass engine is more efficient than a pure turbo jet because its principle of operation is more akin to that of a propeller, in that it accelerates a relatively large mass of air at a low rate. Fig 01. 11 - International Aero Engines V2500 Issued Oct 2012/Reviewed. January 2020 Page 15 PDF Pro Trial Part 66 Module 15 (Gas Turbine Engines) B1 Twin Spool High Bypass The amount of air going through the by-pass section (or "fan") is typically 5 or 6 times that going through the combustion section. Approximately 80 % of the thrust produced is from the by-pass air ducting. Fig 01. 12 - Twin Spool Turbo Fan Fig 01. 13 - Pratt and Whitney GP7000 Issued Oct 2012/Reviewed. January 2020 Page 16 PDF Pro Trial Part 66 Module 15 (Gas Turbine Engines) B1 Two-Spool vs Three-Spool Turbofan Engines When it comes to jet engine design for commercial airliners, there are two typical designs that are similar in concept, but radically different in terms of its working mechanics. Both have a fan in front with a core behind it, but there are two different approaches to making all the components rotate concentrically. Most engine manufacturers employ a 2-spool design, as shown in Fig 01.12, where a fan and low-pressure compressor are driven by a low-pressure turbine, with a high-pressure compressor driven by a high-pressure turbine. While there are no fundamental problems with this design, the fact that the fan is much larger in diameter to the low-pressure compressors and turbines means that either the fan needs to be rotating much faster than optimal, or the low-pressure compressor and turbine needs to be rotating much slower than optimal. This is because maximum efficiency point of the fan, compressor, and turbines is dictated by blade tip speed relative to the speed of sound. Fig 01. 14 - Triple Spool Engine Issued Oct 2012/Reviewed. January 2020 Page 17 PDF Pro Trial Part 66 Module 15 (Gas Turbine Engines) B1 Not only does a larger diameter rotor mean the blade tip reaches optimal speed sooner in terms of shaft RPM, but as air is compressed and combusted, air temperature and pressure increase, both of which raise the speed of sound, allowing blades to spin faster than they could at atmospheric pressures and temperatures. This further exaggerates the rotation speed mismatch between the fan and core components. Engine manufacturers typically limit the rotation speed of the shaft powering the fan to the optimal fan blade tip speed, which causes the low-pressure compressor and turbine to rotate much slower than optimal. Rolls Royce has relieved this problem by separating the fan from the low-pressure compressor and turbine, thus creating 3 spools. In this design, what used to be the low-pressure compressor and turbine is now designated as the intermediate-pressure compressor and turbine, and the fan the driven by a low-pressure turbine. This way, both the fan and the intermediate-pressure compressor and turbine can rotate at their optimal speeds. However, the drawback to this solution is increased mechanical complexity and weight, in addition to the remaining problem that the low-pressure turbine driving the fan is still rotating much slower than optimal. The only way to make all the components rotating at optimal speeds is to use a reduction gearbox for the fan, since no component in the core can match the fan’s diameter and the resulting efficiency at low RPM’s. This is what is commonly referred to as a geared turbofan. The geared turbofan operates the same way a 2 Spool engine would, with the addition of a gearbox between the fan and the low-pressure compressor. Part of the reason is that the technological advances which have been made in the past 30 years now allow a reliable planetary gearbox to be made. But perhaps more importantly is the fact the bypass ratios of engines continue to increase. Issued Oct 2012/Reviewed. January 2020 Page 18 PDF Pro Trial Part 66 Module 15 (Gas Turbine Engines) B1 Back in 1975 when the BAe-146 was being designed, bypass ratios were around 5:1, which means that 5 times the air bypasses the core than the amount of air that travels through the core and is combusted. Today, we are generally designing engines with bypass ratios of at least 10:1, and the higher the bypass ratio, the greater the difference in diameter between the fan and the compressors and turbines in the core, which results in a greater mismatch in RPM’s between fan and core components that are attached to the same shaft. At these higher bypass ratio’s, it could be that the efficiencies gained from decoupling the fan’s rotation speed from core components are worth the development costs of designing and building a reliable gearbox. What are the advantages of 3 spool over 2 spool turbofan engines? There are two; It's easier to match the compressor rotational speed with the turbine. A greater pressure rise per stage can be achieved. Typically, the first stages of the compressor want to rotate slower than the turbine is required to rotate. The turbine needs to spin faster to help obtain as much energy from the airstream as possible, but initial stages of compression prefer to spin slower. With 3 spools instead of 2, less compromise is required. A greater pressure rise per stage occurs because each compressor in a 3-spool engine (fan, LPC, HPC) will have fewer stages than each compressor in a 2-spool engine (for the same overall pressure ratio). A 5-Stage compressor requires less compromise than an 8-Stage compressor. The front stages prefer a high airflow to avoid stall, but the back stages can't always swallow the same mass flow, and can cause a backpressure which can lead to stall. Hence, air flow is often bled off in the middle of the compressor, to avoid stall. This is Issued Oct 2012/Reviewed. January 2020 Page 19 PDF Pro Trial Part 66 Module 15 (Gas Turbine Engines) B1 air that has been partly compressed, absorbing work, but isn't available to generate thrust. Hence, it's a parasitic load. So, the compressors in a 3-spool engine are better optimised than in a 2-spool engine, because this situation isn't as severe. Hence, the designer can be a little more aggressive in the pressure rise per stage the compressor achieves, because the compressor is less prone to stall. Thus, a 3-spool engine, in theory, can achieve the same overall pressure ratio, as a 2 spool, with fewer stages. This means, a lighter weight engine. Issued Oct 2012/Reviewed. January 2020 Page 20 PDF Pro Trial Part 66 Module 15 (Gas Turbine Engines) B1 INTENTIONALLY LEFT BLANK Issued Oct 2012/Reviewed. January 2020 Page 21 PDF Pro Trial Part 66 Module 15 (Gas Turbine Engines) B1 TURBO PROP ENGINES Introduction The advent of the twin spool engine enabled easier starting (only the small HP compressor needs to be rotated by the starter) and better surge resistance as the two spools run at their own optimum speeds. This type was used as a pure thrust engine, but the example shown below drove a propeller on the end of the LP compressor shaft via a reduction gear Fig 01. 15 - Inside Turbo Prop Engines Issued Oct 2012/Reviewed. January 2020 Page 22 PDF Pro Trial Part 66 Module 15 (Gas Turbine Engines) B1 Fig 01. 16 - Bombardier Q400 Turbo Prop Fig 01. 17 - Free (Power) Turbine Engine Issued Oct 2012/Reviewed. January 2020 Page 23 PDF Pro Trial Part 66 Module 15 (Gas Turbine Engines) B1 All types invariably use a multi-stage turbine and an epicyclic reduction gear. Multi-stage turbines with small diameter discs can run at higher rev/min and thus absorb more energy from the gas stream than a single large disc that must necessarily be restricted in rev/min because of high centrifugal loading. Epicyclic gearing is selected for the reduction gear because: A high degree of speed reduction can be obtained. The propeller shaft and thrust lines remain on the same centre line as the compressor and turbine shafts, thus causing little interference with the entry of air into the air intake. Streamlining of the whole unit is, therefore, an easier task. This type of gas turbine engine is used wherever the direct thrust from the engine is not required. All the energy in the gasses is absorbed by the turbines and transformed into a rotational force - or TORQUE. There is usually little or no thrust produced in the exhaust. The reduction gearbox is required because the gas turbine engine is most efficient at high RPM, but the device which it drives (propeller, helicopter rotor etc.) becomes inefficient at such high speed. A free-turbine turboshaft is a form of turboshaft or turboprop gas turbine engine where the power is extracted from the exhaust stream of a gas turbine by a separate turbine, downstream of the gas turbine and is not connected to the gas turbine (the exhaust airflow is what spins the turbine that is connected to the shaft hence the term "free"). This is opposed to the power being extracted from the power spool via a gear box. Issued Oct 2012/Reviewed. January 2020 Page 24 PDF Pro Trial Part 66 Module 15 (Gas Turbine Engines) B1 TURBO-SHAFT ENGINES Introduction A turbo-shaft engine is used to drive any industrial application that requires high torque output. For example: Helicopter Rotors Ship Drive Shafts Hovercraft Engines Oil Pumps Generator Sets This example uses a free or power turbine. All the energy not required to drive the gas generator compressor is used to drive the free turbine which drives the output shaft. The output shaft is shown coming out of the front of the engine but it can be geared to come out at any angle, even though the exhaust is directly connected to the rear of the turbine. Fig 01. 18 - Twin Spool Turbo-Shaft Engine Issued Oct 2012/Reviewed. January 2020 Page 25 PDF Pro Trial Part 66 Module 15 (Gas Turbine Engines) B1 EXAMPLES OF ENGINE ARRANGEMENTS Fig 01. 19 - Two Stage Centrifugal Turbo-Prop Engine Fig 01. 20 - Twin Spool Axial Flow Turbo Prop Engine Fig 01. 21 - Twin Spool Turbo-Shaft Engine Issued Oct 2012/Reviewed. January 2020 Page 26 PDF Pro Trial Part 66 Module 15 (Gas Turbine Engines) B1 Fig 01. 22 - Twin Spool Axial Flow By-pass turbo Jet Fig 01. 23 - Axial Flow Contra-Rotating Prop Fan Fig 01. 24 - Axial Flow Contra-Rotating Rear Fan Issued Oct 2012/Reviewed. January 2020 Page 27 PDF Pro Trial Part 66 Module 15 (Gas Turbine Engines) B1 LIST OF ILLUSTRATIONS Fig 01. 01 - Gas Flowing through a Convergent Duct - Subsonic airflow............. 2 Fig 01. 02 - Gas Flowing through a Divergent Duct - Subsonic airflow................ 2 Fig 01. 03 - Convergent/Divergent Duct - Sonic Airflow....................................... 3 Fig 01. 04 - The Rocket Engine............................................................................ 5 Fig 01. 05 - The Ram Jet...................................................................................... 6 Fig 01. 06 - The Pure Turbo-Jet............................................................................ 9 Fig 01. 07 - The Constant Pressure Cycle.......................................................... 11 Fig 01. 08 - The Single Spool Axial Flow Engine................................................ 12 Fig 01. 09 - A Twin Spool Axial Flow Engine...................................................... 13 Fig 01. 10 - A Adour Twin-Spool By-Pass Turbo-Jet.......................................... 14 Fig 01. 11 - International Aero Engines V2500................................................... 15 Fig 01. 12 - Twin Spool Turbo Fan..................................................................... 16 Fig 01. 13 - Pratt and Whitney GP7000.............................................................. 16 Fig 01. 14 - Triple Spool Engine......................................................................... 17 Fig 01. 15 - Inside Turbo Prop Engines.............................................................. 22 Fig 01. 16 - Bombardier Q400 Turbo Prop......................................................... 23 Fig 01. 17 - Free (Power) Turbine Engine.......................................................... 23 Fig 01. 18 - Twin Spool Turbo-Shaft Engine....................................................... 25 Fig 01. 19 - Two Stage Centrifugal Turbo-Prop Engine...................................... 26 Fig 01. 20 - Twin Spool Axial Flow Turbo Prop Engine...................................... 26 Fig 01. 21 - Twin Spool Turbo-Shaft Engine....................................................... 26 Fig 01. 22 - Twin Spool Axial Flow By-pass turbo Jet........................................ 27 Fig 01. 23 - Axial Flow Contra-Rotating Prop Fan.............................................. 27 Fig 01. 24 - Axial Flow Contra-Rotating Rear Fan.............................................. 27 Issued Oct 2012/Reviewed. January 2020 Page 28 PDF Pro Trial SECTION 15.2 PERFORMANCE Issued Oct 2012/Reviewed. January 2020 PDF Pro Trial Part 66 Module 15 (Gas Turbine Engines) B1 INTENTIONALLY LEFT BLANK Issued Oct 2012/Reviewed. January 2020 PDF Pro Trial Part 66 Module 15 (Gas Turbine Engines) B1 TABLE OF CONTENTS PERFORMANCE...................................................................................................... 1 Thrust...................................................................................................................... 1 Momentum Thrust.................................................................................................. 1 Choked Nozzle Thrust or Pressure Thrust............................................................. 2 Net Thrust............................................................................................................... 2 Gross Thrust........................................................................................................... 2 Thrust Distribution.................................................................................................. 4 POWER MEASUREMENT IN TURBOPROP AIRCRAFT........................................ 6 Shaft Horsepower................................................................................................... 6 Brake Horsepower.................................................................................................. 6 Equivalent Shaft Horsepower................................................................................. 7 EFFICIENCY............................................................................................................. 8 Propulsive Efficiency.............................................................................................. 8 Propulsive Efficiency Graphs................................................................................ 10 Thermal Efficiency................................................................................................ 11 Overall Efficiency.................................................................................................. 12 Thermal Efficiency Curves.................................................................................... 12 Engine Compression Ratio................................................................................... 13 Specific Fuel Consumption................................................................................... 14 THRUST FACTORS................................................................................................ 15 The International Standard Atmosphere............................................................... 15 Variation of Thrust with Altitude, Temperature and Airspeed............................... 16 RAM Effect........................................................................................................... 18 ENGINE RATINGS.................................................................................................. 19 Flat Rating............................................................................................................ 19 Engine Power Ratings.......................................................................................... 20 LIST OF ILLUSTRATIONS...................................................................................... 22 Issued Oct 2012/Reviewed. January 2020 Page i PDF Pro Trial Part 66 Module 15 (Gas Turbine Engines) B1 INTENTIONALLY LEFT BLANK Issued Oct 2012/Reviewed. January 2020 Page ii PDF Pro Trial Part 66 Module 15 (Gas Turbine Engines) B1 PERFORMANCE Thrust Consider a basic gas turbine moving through the atmosphere with an inlet velocity of ‘Va’ and an exit velocity of Vj. Mass flow of air through the engine is m. Fig 02. 01 - Thrust = Mass x Acceleration Momentum Thrust From Newton’s Second Law Force = Mass x Acceleration But Thrust is a Force Therefore Thrust = Mass x Acceleration (𝑽𝒋 − 𝑽𝒂) 𝒎𝒂𝒔𝒔 = 𝒕 𝒎𝒂𝒔𝒔 (𝑽𝒋 − 𝑽𝒂) 𝒕 = mass flow ( m) x (Vj- Va) Units are Newtons or lbf This type of thrust is known as Momentum Thrust Momentum Thrust = ( m) x (Vj- Va) Issued Oct 2012/Reviewed. January 2020 Page 1 PDF Pro Trial Part 66 Module 15 (Gas Turbine Engines) B1 Choked Nozzle Thrust or Pressure Thrust If the air speed at the exit nozzle reaches Mach 1( the speed of sound) a shock wave will form and the nozzle is said to be ‘Choked’. As a result the pressure in the jet pipe (Pj) will increase. When it gets above 1.4:1 compared to ambient pressure (Pa) then significant pressure thrust begins to be produced. Engines designed for commercial passenger aircraft have the exit nozzle designed so that the nozzle is only just at Mach 1 hence pressure thrust is negligible for these types. To fully exploit pressure thrust and the choked nozzle concept a convergent /divergent nozzle is required. For military applications and rockets with convergent/divergent exit nozzles pressure thrust becomes more significant 𝑷𝒓𝒆𝒔𝒔𝒖𝒓𝒆 𝑻𝒉𝒓𝒖𝒔𝒕 = 𝑨𝒋 (𝑷𝒋 − 𝑷𝒂) Total Thrust = Momentum Thrust + Pressure Thrust Net Thrust Net thrust takes into account the term Va in the momentum thrust formula therefore net thrust varies with airspeed. Gross Thrust When the aircraft is stationary on the ground the value of Va is zero Therefore Gross thrust = mVj + pressure thrust Gross thrust is that thrust developed when the engine is stationary on the ground or on the test bed. Gross Thrust is sometimes known as Static Thrust. Issued Oct 2012/Reviewed. January 2020 Page 2 PDF Pro Trial Part 66 Module 15 (Gas Turbine Engines) B1 Gas Turbine Working Cycle and Airflow As the air is induced into the compressor the pressure and temperature rise. Note that velocity which you would expect to decrease remains almost constant due to the convergent annulus formed by the compressor casing and the compressor rotor. Fuel is added to the combustion chamber and ignited. Flame temperature rapidly increases to a level far greater than the melting point of the turbines, so the remainder of the air is added to the combustor and the temperature reduces as the air reaches the turbines. Fig 02. 02 - Pressure, Temperature and Velocity Distributions Note that the pressure through the combustor remains almost constant. Velocity of the gases increases as the gases pass through the convergent nozzles of the turbine and pressure decreases. As the pressure is above atmospheric as it leaves the jet pipe then pressure thrust will be generated in addition to the momentum thrust. Issued Oct 2012/Reviewed. January 2020 Page 3 PDF Pro Trial Part 66 Module 15 (Gas Turbine Engines) B1 It is worth noting at this point that the Speed of Sound (and its associated shock waves) rises as temperature rises. At ISA conditions Speed of Sound = 315 m/s. Due to the high temperatures the hot section of the engine will not suffer shock effects until the exit nozzle is reached. The nozzle being sized to just choke the nozzle to enable maximum momentum thrust to be obtained with little or no pressure thrust. Thrust Distribution At the start of the cycle, air is induced into the engine and is compressed. The rearward accelerations through the compressor stages and the resultant pressure rise produce a large reactive force in a forward direction. On the next stage of its journey the air passes through the diffuser where it exerts a small reactive force, also in a forward direction. From the diffuser the air passes into the combustion chamber where it is heated, and in the consequent expansion and acceleration of the gas large forward forces are exerted on the chamber walls. When the expanding gases leave the combustion chambers and flow through the nozzle guide vanes they are accelerated and deflected on to the blades of the turbine. Due to the acceleration and deflection, together with the subsequent straightening of the gas flow as it enters the jet pipe, considerable ‘drag’ results; thus the vanes and blades are subjected to large rearward forces, the magnitude of which may be seen on the diagram. As the gas flow passes through the exhaust system, small forward forces may act on the inner cone or bullet, but generally only rearward forces are produced and these are due to the ‘drag’ of the gas flow at the propelling nozzle. Issued Oct 2012/Reviewed. January 2020 Page 4 PDF Pro Trial Part 66 Module 15 (Gas Turbine Engines) B1 It will be seen that during the passage of the air through the engine, changes in its velocity and pressure occur. Where the conversion is to velocity energy, ‘drag’ loads or rearward forces are produced. Where the conversion is to pressure energy, forward forces are produced. Fig 02. 03 - Forward Loads and Rearward Loads on a Turbo-Jet Engine Issued Oct 2012/Reviewed. January 2020 Page 5 PDF Pro Trial Part 66 Module 15 (Gas Turbine Engines) B1 POWER MEASUREMENT IN TURBOPROP AIRCRAFT Shaft Horsepower As in reciprocating engines the gas generator of a turbo-prop engine is used to drive a propeller. It is the propeller that develops the thrust that drives the airframe. To measure the power that is developed one needs to devise a system that can monitor the turning force on the propeller shaft. If an engine produces torque (T) at N revs/min Power = 2 πNT The Imperial Unit of Power is Horsepower. 𝟐𝝅𝑵𝑻 𝑯𝒐𝒓𝒔𝒆𝒑𝒐𝒘𝒆𝒓 = 𝟑𝟎𝟎𝟎 Horsepower developed by an engine output shaft is known as shaft horsepower. Brake Horsepower To measure shaft horsepower it is usual to use a brake dynamometer. Hence, Shaft Horsepower is sometimes known as Brake Horsepower. Numerically it is the same. Issued Oct 2012/Reviewed. January 2020 Page 6 PDF Pro Trial Part 66 Module 15 (Gas Turbine Engines) B1 Equivalent Shaft Horsepower The turboprop engine uses the majority of gas power to drive the turbines, with the free or power turbine driving the propeller shaft. There is always a residue of gas power exiting the exhaust however. As long as the exhaust is directed parallel to the thrust line of the engine then this exhaust will add to the thrust the propeller is producing. The total thrust production of the engine is therefore the Shaft Horsepower plus exhaust or jet thrust. It is called equivalent shaft horsepower. ESHP = SHP + Jet Thrust If the aircraft is in flight then the efficiency of the propeller must be taken into account. ESHP = SHP x prop-eff. + Jet Thrust Issued Oct 2012/Reviewed. January 2020 Page 7 PDF Pro Trial Part 66 Module 15 (Gas Turbine Engines) B1 EFFICIENCY Propulsive Efficiency Propulsive efficiency is concerned with the efficiency of the engine to drive the aircraft in flight. If Peπ = Propulsive Efficiency Va = Aircraft Speed Vj = Exhaust Velocity Then 𝟐𝑽𝒂 𝑷𝒆𝝅 = 𝑽𝒋 + 𝑽𝒂 Consideration of the formula reveals that: If Va = Vj then the efficiency will be 100%. But if Va = Vj there is no difference in velocity through the engine and hence there can be no thrust. Therefore 100% efficiency is impossible. Also note there would be no energy used to drive the compressors if 100% of energy was used for propelling the aircraft. If the aircraft is stationary on the ground then Va = 0. In this case efficiency would be 0. This shows that propulsive efficiency is concerned with propelling the aircraft through the sky, not just producing thrust. Issued Oct 2012/Reviewed. January 2020 Page 8 PDF Pro Trial Part 66 Module 15 (Gas Turbine Engines) B1 INTENTIONALLY LEFT BLANK Issued Oct 2012/Reviewed. January 2020 Page 9 PDF Pro Trial Part 66 Module 15 (Gas Turbine Engines) B1 Propulsive Efficiency Graphs The graph reveals how propeller-driven aircraft gain their efficiency first at low airspeeds because the controllable pitch propeller is capable of moving large mass airflows. The curves all peak out as soon as more fuel energy is introduced to create an exhaust velocity increase. Work then comes out in the form of increase aircraft speed. Fig 02. 04 - Propulsive Efficiency Graphs The propeller aircraft (either piston or turbine driver peaks out slightly above 85%, after which the propeller loses efficiency. That is, its exhaust wake velocity continues to increase from added fuel energy, but aircraft speed does not increase proportionally. Issued Oct 2012/Reviewed. January 2020 Page 10 PDF Pro Trial Part 66 Module 15 (Gas Turbine Engines) B1 Note that after reaching approximately 375 mph (Mach 0.57 or 325kn), propulsive efficiency starts to decrease. Aerodynamic drag and tip shock stall are involved here and by 500 mph efficiency decreases to 65%. The ultra-high bypass turbofan curve peaks at approximately 560 mph (Mach 0.85, or 486kn), after which the fan suffers the same losses in drag and tip speed as the propeller. In order to go to 700 mph (aircraft speed), the exhaust velocity will have to be increased to an uneconomical level. The high bypass turbofan is the most widely use engine today in both large and small aircraft. Its propulsive efficiency curve peaks out slightly lower than the UHB engine but at approximately the same airspeed. Subsonic aircraft with low and medium bypass turbofans all operate in the 500 to 600 mph range. Note that the curve shows a lower efficiency value than a high bypass engine in that range. Because of this, high bypass engines are rapidly replacing low and medium bypass engines in many aircraft. The supersonic low bypass turbofan and turbojet have a theoretical propulsive efficiency peak limit in the 2,000 to 3,000 mph range. Their narrow, low-drag profile allows this range. Any additional energy added (in the form of fuel) to increase speed further would raise the internal engine temperatures to unacceptable levels. Thermal Efficiency Thermal efficiency is the ratio of ‘Net Work’ produced by the engine to the ‘Fuel Energy Input’. As with propulsive efficiency it cannot be measured in the cockpit but can be calculated by utilising a fuel flow indication. 𝑵𝒆𝒕 𝒑𝒐𝒘𝒆𝒓 𝒐𝒖𝒕𝒑𝒖𝒕 𝒐𝒇 𝒕𝒉𝒆 𝒆𝒏𝒈𝒊𝒏𝒆 𝑻𝒉𝒆𝒓𝒎𝒂𝒍 𝑬𝒇𝒇𝒊𝒄𝒊𝒆𝒏𝒄𝒚 = 𝑬𝒏𝒆𝒓𝒈𝒚 𝒗𝒂𝒍𝒖𝒆 𝒐𝒇 𝑭𝒖𝒆𝒍 𝒄𝒐𝒏𝒔𝒖𝒎𝒆𝒅 Issued Oct 2012/Reviewed. January 2020 Page 11 PDF Pro Trial Part 66 Module 15 (Gas Turbine Engines) B1 Overall Efficiency It is necessary to combine both of the above efficiencies when looking for a powerplant to suit a particular application. Overall Efficiency = Propulsive Efficiency x Thermal Efficiency For example if Peff = 70% and Thermal Eff. = 40% then Overall efficiency = 70% x 40% = 28%. Thermal Efficiency Curves Propulsive, thermal and overall efficiencies, variation with speed Propulsive efficiency increases as airspeed approaches exhaust velocity values. Thermal efficiency decreases due to added fuel needs at higher airspeeds. Overall efficiency increases as airspeed increases because propulsive efficiency increases more than thermal efficiency decreases. Fig 02. 05 - Efficiency Curves Issued Oct 2012/Reviewed. January 2020 Page 12 PDF Pro Trial Part 66 Module 15 (Gas Turbine Engines) B1 Engine Compression Ratio Engine Compression Ratio in a gas turbine is defined as the ratio between Compressor Outlet Pressure to Compressor Inlet Pressure. The Higher the compression ratio of the engine the greater the power that can be produced. Fig 02. 06 - Thermal Efficiency Variation with CPR Most modern Compressor and Turbine efficiencies are in the high 80% range. It can be seen from the above that a high compression ratio will produce an increased thermal efficiency. In other words the ideal compressor efficiency (adiabatic compression) occurs when the compressor produces the maximum pressure with the least temperature rise and the ideal turbine extracts most work for the minimum fuel addition. Degraded efficiency of the compressor and turbine as shown above at 60 & 70% is due to wear in service, damage or just contamination by dirt etc. Issued Oct 2012/Reviewed. January 2020 Page 13 PDF Pro Trial Part 66 Module 15 (Gas Turbine Engines) B1 Specific Fuel Consumption Specific Fuel Consumption (SFC) is sometimes called ‘the engine man’s efficiency’. SFC is defined as the ratio of fuel consumed per pound of thrust produced. SFC is inversely proportional to efficiency. In other words the lower the SFC the higher the efficiency. Units of SFC in a pure Jet engine are - lb/hr/lb thrust In a turbo Jet Engine -lb/hr/SHP Fig 02. 07 - SFC and Efficiency, Variation with Forward Speed Note that the SFC starts to increase after falling to a minimum as the aircraft goes faster. This is due to ram effect causing an increase in mass airflow and hence an increase in fuel flow. The engine power limiter will control the maximum fuel flow to prevent over speeding or flat rated power limits. Ram effect is discussed in Chapter 3 - Intakes Issued Oct 2012/Reviewed. January 2020 Page 14 PDF Pro Trial Part 66 Module 15 (Gas Turbine Engines) B1 THRUST FACTORS The International Standard Atmosphere Fig 02. 08 - The International Standard Atmosphere Issued Oct 2012/Reviewed. January 2020 Page 15 PDF Pro Trial Part 66 Module 15 (Gas Turbine Engines) B1 Variation of Thrust with Altitude, Temperature and Airspeed The figure below shows that thrust improves rapidly with decreasing temperature, given constant altitude, RPM and airspeed. This is because with decreased temperature one gets increased density, hence the air has greater mass and from the momentum thrust formula thrust will increase. Fig 02. 09 - Net Thrust Variation with Outside Air Temperature (OAT) Issued Oct 2012/Reviewed. January 2020 Page 16 PDF Pro Trial Part 66 Module 15 (Gas Turbine Engines) B1 The altitude effect on thrust is shown below. Thrust decreases with altitude, given constant airspeed and RPM. Whilst temperature is decreasing with altitude so is pressure. Since the temperature lapse rate is less than the pressure lapse rate as altitude is decreased, the density is decreased and as a result thrust will decrease. Fig 02. 10 - Thrust Decreases with Altitude Issued Oct 2012/Reviewed. January 2020 Page 17 PDF Pro Trial Part 66 Module 15 (Gas Turbine Engines) B1 RAM Effect The effect of airspeed on thrust depends upon Ram Effect being present. Without ram effect thrust will decrease. With ram effect thrust will start to recover then increase as the speed increases above about 200kts Increase in forward speed without ram effect will cause the momentum drag term (mVa) in the thrust formula m(Vj - Va) to increase thus reducing thrust. In an intake designed to promote ram recovery, that is to increase pressure above existing atmospheric pressure at the engine inlet, ram effect will provide extra compression without further work being needed at the turbine. In reality there is always some ram effect as the aircraft increases speed so the actual result is a compromise between the two conditions shown above. Fig 02. 11 - Thrust Variation with True Airspeed (TAS) Issued Oct 2012/Reviewed. January 2020 Page 18 PDF Pro Trial Part 66 Module 15 (Gas Turbine Engines) B1 ENGINE RATINGS Flat Rating As OAT increases for a given maximum throttle setting the engine thrust increases to a thrust limit. This is known as the flat rated thrust and is usually quoted at the maximum ambient temperature allowed (i.e. 42,000 lb thrust at 59°F). Above this temperature, sometimes known as the ‘Kink Point’ or ‘Corner Point’ the engine will exceed the maximum exhaust gas temperature limit and will become temperature limited. Fig 02. 12 - Flat Rating Issued Oct 2012/Reviewed. January 2020 Page 19 PDF Pro Trial Part 66 Module 15 (Gas Turbine Engines) B1 Engine Power Ratings Turbine engines, both turbojet and turbofan, are thrust rated in terms of either: Engine Pressure Ratio Fan Speed Turboshaft/turboprop engines are SHP rated in the following categories: Take-Off Maximum Continuous Maximum Climb Maximum Cruise Idle For certification purposes, the manufacturer demonstrates to the FAA or CAA that the engine will perform at certain thrust or shaft horsepower levels for specified time intervals and still maintain its airworthiness and service life for the user. These ratings can usually be found on the engine Type Certificate Data Sheets. The ratings are classified as follows: Take-Off Wet Thrust/SHP This rating represents the maximum power available while in water injection and is time limited. It is used only during take-off operation. Engines are trimmed to this rating. Take-Off Dry Thrust/SHP Limits on this rating are the same as take-off wet but without water injection. Engines are trimmed to this rating. Issued Oct 2012/Reviewed. January 2020 Page 20 PDF Pro Trial Part 66 Module 15 (Gas Turbine Engines) B1 Maximum Continuous Thrust/SHP This rating has no time limit but is to be used only during emergency situations at the discretion of the pilot, for example, during one engine-out cruise operation. Maximum Climb Thrust/SHP Maximum climb power settings are not time limited and are to be used for normal climb, to cruising altitude, or when changing altitudes. This rating is sometimes the same as maximum continuous. Maximum Cruise Thrust/SHP This rating is designed to be used for any time period during normal cruise at the discretion of the pilot. Idle Speed This power setting is not actually a power rating but, rather, the lowest usable thrust setting for either ground or flight operation. Issued Oct 2012/Reviewed. January 2020 Page 21 PDF Pro Trial Part 66 Module 15 (Gas Turbine Engines) B1 LIST OF ILLUSTRATIONS Fig 02. 01 - Thrust = Mass x Acceleration............................................................ 1 Fig 02. 02 - Pressure, Temperature and Velocity Distributions............................ 3 Fig 02. 03 - Forward Loads and Rearward Loads on a Turbo-Jet Engine............ 5 Fig 02. 04 - Propulsive Efficiency Graphs........................................................... 10 Fig 02. 05 - Efficiency Curves............................................................................. 12 Fig 02. 06 - Thermal Efficiency Variation with CPR............................................ 13 Fig 02. 07 - SFC and Efficiency, Variation with Forward Speed......................... 14 Fig 02. 08 - The International Standard Atmosphere.......................................... 15 Fig 02. 09 - Net Thrust Variation with Outside Air Temperature (OAT).............. 16 Fig 02. 10 - Thrust Decreases with Altitude........................................................ 17 Fig 02. 11 - Thrust Variation with True Airspeed (TAS)...................................... 18 Fig 02. 12 - Flat Rating....................................................................................... 19 Issued Oct 2012/Reviewed. January 2020 Page 22 PDF Pro Trial SECTION 15.3 INLET SECTION Issued Oct 2012/Reviewed. January 2020 PDF Pro Trial Part 66 Module 15 (Gas Turbine Engines) B1 INTENTIONALLY LEFT BLANK Issued Oct 2012/Reviewed. January 2020 PDF Pro Trial Part 66 Module 15 (Gas Turbine Engines) B1 TABLE OF CONTENTS INLET........................................................................................................................ 1 General Description................................................................................................ 1 Purpose.................................................................................................................. 1 RAM.......................................................................................................................... 2 Definitions............................................................................................................... 2 Ram Compression.................................................................................................. 2 Intake Momentum Drag.......................................................................................... 3 INTAKE DESIGN....................................................................................................... 4 Pitot Intakes............................................................................................................ 4 The Nacelle or Pod Intake...................................................................................... 8 Auxiliary Air Doors.................................................................................................. 9 Auxiliary Air Door Operation................................................................................... 9 Supersonic Flight.................................................................................................. 10 Fixed Geometry Operation................................................................................... 12 Variable Geometry................................................................................................ 13 Operation.............................................................................................................. 14 Above Mach 1....................................................................................................... 15 External / Internal Intake....................................................................................... 17 INTAKE DANGER AREAS...................................................................................... 18 INTAKE GUARDS................................................................................................... 19 INTAKE ICE PROTECTION.................................................................................... 20 Hot Air Anti Icing................................................................................................... 20 Electrical Intake De-icing / Anti-icing systems...................................................... 22 LIST OF ILLUSTRATIONS...................................................................................... 26 Issued Oct 2012/Reviewed. January 2020 Page i PDF Pro Trial Part 66 Module 15 (Gas Turbine Engines) B1 INTENTIONALLY LEFT BLANK Issued Oct 2012/Reviewed. January 2020 Page ii PDF Pro Trial Part 66 Module 15 (Gas Turbine Engines) B1 INLET General Description The main air intake is often part of the airframe structure, delivering the air to the engine air intake casing. The intake is designed to convert kinetic energy into pressure energy and reduce the velocity at the compressor inlet to no more than between 0.4 and 0.5 Mach. Any inefficiency in the intake results in a pressure loss at the compressor inlet and reduced compressor outlet pressure. Purpose The purpose of the intake system is to deliver the air to the compressor with the minimum loss of energy. The intake system should meet the following requirements: Deliver to the engine an adequate mass flow of air under any engine operating condition. The air must be delivered evenly across the face of the compressor, free from turbulence at approximately M = 0.4. Must make maximum use of RAM pressure. Produce minimum airframe drag. Issued Oct 2012/Reviewed. January 2020 Page 1 PDF Pro Trial Part 66 Module 15 (Gas Turbine Engines) B1 RAM Definitions Total Head Pressure The pressure of the air when brought to rest in front of the intakes. Ram Ratio The ratio of the total pressure (Pt) at the compressor entry to static pressure (Ps) at the intake entry i.e. Pt/Ps (See figure 3.1) Ram Recovery. To convert as much of the intake air velocity as possible to pressure at the face of the engine. If all available ram pressure is converted, it is known as “TOTAL PRESSURE RECOVERY”. Ram Compression Ram Compression increases in pressure within the intake at substantial forward speeds. When an aircraft is stationary, the engine intake is of little interest, in fact, a slight depression exists within it. Ram compression causes redistribution of the energy existing in the air stream. As the air in the intake slows in endeavouring to pass into and through the compressor element against the air, increasing pressure and density exists therein, so the kinetic energy of the air in the intake decreases. This is accompanied by a corresponding increase in its pressure and internal energies and consequently compression of the air stream is achieved within the Issued Oct 2012/Reviewed. January 2020 Page 2 PDF Pro Trial Part 66 Module 15 (Gas Turbine Engines) B1 intake, thus converting the unfavourable intake lip conditions into the compressor inlet requirements. Although ram compression improves the performance of the engine, it must be realised that during the process there is a drag force on the engine and hence the aircraft. This drag must be accepted, since it is a penalty inherent in a ram compression process. The added thrust more than makes up for the increase in drag. The degree of ram compression depends on the following: The frictional losses at those surfaces ahead of the intake which are "wetted" by the intake airflow. Frictional losses at the intake duct walls. Turbulence losses due to accessories or structural members located in the intake. Aircraft speed. In a turbo-prop engine, drag and turbulence losses due to the propeller, blades and spinner. Intake Momentum Drag As forward speed increases, thrust decreases, this is due to the momentum of the air passing into the engine in relation to the aircraft’s forward speed. Issued Oct 2012/Reviewed. January 2020 Page 3 PDF Pro Trial Part 66 Module 15 (Gas Turbine Engines) B1 INTAKE DESIGN The following types of intake can be seen on modern aircraft: Pitot Divided Entrance Nacelle or Pod Intake Variable Geometry External/Internal Compression Pitot Intakes This intake is suitable for subsonic or low supersonic speeds. The intake is usually short and is very efficient because the duct inlet is located directly ahead of the compressor. The duct is divergent from front to rear with smooth gradual changes in shape Efficiency will fall rapidly at sonic speeds due to shock wave formation at the lip. With increased speeds above sonic, this shock wave will move backwards towards the compressor face. If the shock wave enters the compressor, damage may occur and there is a high risk of compressor surge. Issued Oct 2012/Reviewed. January 2020 Page 4 PDF Pro Trial Part 66 Module 15 (Gas Turbine Engines) B1 Fig 03. 01 - Pressure in a Pitot Intake Fig 03. 02 - A Pitot Intake Issued Oct 2012/Reviewed. January 2020 Page 5 PDF Pro Trial Part 66 Module 15 (Gas Turbine Engines) B1 Divided Entrance Intakes This type is used on some single engined aircraft with a fuselage mounted engine and can be either side scoop or wing root mounted. The side scoop inlet is placed as far forward of the compressor as possible to approach the straight line effect of the single inlet. The wing root inlet presents problems to the designer in the forming of the curvature necessary to deliver the air to the engine compressor. One major problem with both of these inlet types is a loss of ram pressure occurs on one side of the intake and as a result separated turbulent air is fed to the compressor. Fig 03. 03 - Side Scoop Divided Intakes Issued Oct 2012/Reviewed. January 2020 Page 6 PDF Pro Trial Part 66 Module 15 (Gas Turbine Engines) B1 Fig 03. 04 - Divided Intake Loss of RAM Pressure To prevent this uneven airflow and loss of ram pressure, aircraft with a divided air intake: Must be operated very carefully during flight Must always be pointed nose into the wind when ground running, especially at high power settings. Issued Oct 2012/Reviewed. January 2020 Page 7 PDF Pro Trial Part 66 Module 15 (Gas Turbine Engines) B1 The Nacelle or Pod Intake The Nacelle intake or Pod intake is a variation of the pitot type. They are used when the engine is carried in an external pod outside the fuselage or under the wings. The pod is called a Nacelle. This type allows more fuel / cargo or passengers to be carried internally. Fig 03. 05 - The Nacelle or Pod Type Intake Note This type of intake is used on larger aircraft, where ease of access and speed of removal and refitting is of greater importance than reduction of drag. Issued Oct 2012/Reviewed. January 2020 Page 8 PDF Pro Trial Part 66 Module 15 (Gas Turbine Engines) B1 Auxiliary Air Doors Some aircraft designs require very high angles of attack during landing and take-off, which can cause the intake to become masked. Other aircraft may operate at high thrust with a low forward aircraft speed, and the air intake may be unable to pass enough air to the compressor. (Harrier loses ram effect when hovering) To allow for the extra air needed for the engine to operate under such conditions, the air intakes of these aircraft may be fitted with auxiliary air doors. Auxiliary Air Door Operation The auxiliary air doors are held closed with a very light spring. At high angles of attack, or at low forward speed and high engine rpm, the engine needs sufficient air to maintain thrust. As the engine takes in this air, the air intake cannot draw in sufficient air to replace it and intake pressure will reduce causing thrust to reduce. The auxiliary air doors are automatically sucked open against spring pressure and extra air is now available to maintain the engine thrust. Fig 03. 06 - Auxiliary Air Doors Auxiliary air doors may open during start-up and while the aircraft is taxiing. This is because intake or ram pressure is lower than ambient pressure. Issued Oct 2012/Reviewed. January 2020 Page 9 PDF Pro Trial Part 66 Module 15 (Gas Turbine Engines) B1 Supersonic Flight For a Gas Turbine engine to operate correctly, the speed of the air passing through the engine must always be kept below the speed of sound, (Mach 1) even when the aircraft is flying at Supersonic speeds. To make sure that the airflow through the engine is always below Mach 1, the air intake must smoothly decrease the air speed at the entrance to the compressor. At Mach 1, shock waves will begin to form in the narrowest part of the intake, and these waves will choke or restrict the airflow. As speeds increase above Mach 1, the shockwave will cause the properties of convergent and divergent ducts to reverse: A convergent duct will now decrease velocity and increase pressure A divergent duct will now increase velocity and decrease pressure At supersonic speed, the pitot type of air intake with its divergent entry is unsuitable, so a different shape of intake is used. The intake forms a convergent / divergent duct. There are two types of supersonic air intake: Fixed geometry (transonic up to around Mach 2 e.g. F 16) - with this type the shape of the duct is fixed during manufacture. Variable geometry (higher supersonic > Mach 2 e.g. Typhoon) - with this type the shape of the ducts is changed as speed changes. Issued Oct 2012/Reviewed. January 2020 Page 10 PDF Pro Trial Part 66 Module 15 (Gas Turbine Engines) B1 Fig 03. 07 - Fixed Geometry Intake Fig 03. 08 - Variable Geometry Intake Issued Oct 2012/Reviewed. January 2020 Page 11 PDF Pro Trial Part 66 Module 15 (Gas Turbine Engines) B1 Fixed Geometry Operation The supersonic airflow meets the sharp edges of the intake entrance. This creates a shock wave to slow the air. The supersonic air then enters the convergent entry duct The duct slows down the air and increases the pressure. The air reaches the narrowest part of the duct. The flow is choked and another very large shock wave is created. The air flow slows down to subsonic speeds. The subsonic airflow then enters the divergent section of the duct. Its velocity reduces and pressure increases. Fig 03. 09 - Transonic Air Intake The transonic intake works best at approximately Mach 1.0. (The speed of sound, or 1250kph at sea level). Issued Oct 2012/Reviewed. January 2020 Page 12 PDF Pro Trial Part 66 Module 15 (Gas Turbine Engines) B1 At low forward speeds, it will accelerate the incoming air, and will cause airflow instability in the compressor. Additional devices must be fitted to the engine to overcome this problem. At higher speeds (above about Mach 1.2) the increase in ram air volume will choke the intake, again causing airflow instability in the compressor. This gives a limitation of aircraft maximum speed. Variable Geometry The Transonic intake is inefficient at both very low and very high speeds. Because of this a modified type is often fitted where the shape of the duct can automatically be changed as speed changes. A set of moveable surfaces called ‘Shock Ramps’ can be pushed out into the airflow to change the intake shape. Fig 03. 10 - Variable Geometry Intakes Issued Oct 2012/Reviewed. January 2020 Page 13 PDF Pro Trial Part 66 Module 15 (Gas Turbine Engines) B1 Operation At low forward speed, the intake works in a similar way to the ‘Pitot’ type. The Shock Ramps are withdrawn (pulled inwards). The first part of the intake forms a parallel duct. The second part is divergent, slowing down the air and increasing its pressure. The secondary air doors are closed and the Engine Bay Vent Doors are open. This allows atmospheric cooling air into the engine spaces. The Spill Doors operate as Auxiliary Air doors. This allows in extra air at high angles of attack. Fig 03. 11 - High Supersonic Air Intake – below Mach 1 Issued Oct 2012/Reviewed. January 2020 Page 14 PDF Pro Trial Part 66 Module 15 (Gas Turbine Engines) B1 Above Mach 1 At high forward speed the intake works in a similar way to the transonic type intake. As speed increases the Variable Shock Ramps are deployed (pushed out). The ramps progressively narrow the air intake. This makes the entrance increasingly convergent. The convergent inlet develops multiple shock waves. The shockwaves progressively slow the airflow and increase its pressure. The air reaches the narrowest part of the duct. The flow is choked and another very large shock wave is created. The subsonic airflow then enters the divergent section of the duct. Its velocity reduces and its pressure increases. The engine bay vent doors are closed and the secondary air doors are open. Excessive ram pressures are diverted around the outside of the engine. This air provides ram air cooling for the hotter engine. Issued Oct 2012/Reviewed. January 2020 Page 15 PDF Pro Trial Part 66 Module 15 (Gas Turbine Engines) B1 The cooling air joins the main flow in the exhaust. Extreme increase in intake ram pressure cause the spill doors to open outwards. This dumps the excess air volume to atmosphere. Fig 03. 12 - High Supersonic Air Intake – above Mach 1 Issued Oct 2012/Reviewed. January 2020 Page 16 PDF Pro Trial Part 66 Module 15 (Gas Turbine Engines) B1 External / Internal Intake At higher supersonic speeds, a more suitable type of intake is the one shown below. This type of intake produces a series of mild shock waves without excessively reducing the intake efficiency. Fig 03. 13 - External / Internal Intake This intake is sometimes known as a plug intake. In some applications the plug position is variable dependent upon Mach number. Issued Oct 2012/Reviewed. January 2020 Page 17 PDF Pro Trial Part 66 Module 15 (Gas Turbine Engines) B1 INTAKE DANGER AREAS WARNING AIRCRAFT AIR INTAKES CAN BE DANGEROUS. MAKE SURE PEOPLE ARE AWARE WHEN YOU ARE INSIDE ONE. ALWAYS USE A SAFETY MAN OR SAFETY SIGN. LOOSE ARTICLES, CLOTHING, EQUIPMENT AND EVEN PEOPLE CAN BE SUCKED INTO THE INTAKES OF A RUNNING ENGINE. THE AIRCRAFT SAFETY & SERVICING NOTES SHOW THE SAFE DISTANCES IN FRONT OF AN AIRCRAFT WITH RUNNING ENGINES. LEARN THE SAFETY DISTANCES FOR YOUR AIRCRAFT AND OBSERVE THEM AT ALL TIMES. Fig 03. 14 - Air Intake Danger Areas Issued Oct 2012/Reviewed. January 2020 Page 18 PDF Pro Trial Part 66 Module 15 (Gas Turbine Engines) B1 INTAKE GUARDS WARNING IF THE AIRCRAFT IS GOING TO BE GROUND RUN, AIR INTAKE DEBRIS GUARDS MUST BE FITTED. CHECK THE INSIDE OF THE GUARDS FOR FOD BEFORE FITTING. Fig 03. 15 - Air Intake Debris Guards WARNING TO PREVENT FOD FROM ENTERING THE INTAKE WHEN THE AIRCRAFT IS NOT BEING FLOWN, THE ENGINE AIR INTAKE BLANKS MUST ALWAYS BE FITTED Fig 03. 16 - Air Intake Blanks WARNING MAKE SURE YOU REMOVE THE INTAKE BLANKS BEFORE ENGINE STARTING AND GROUND RUNNING. Issued Oct 2012/Reviewed. January 2020 Page 19 PDF Pro Trial Part 66 Module 15 (Gas Turbine Engines) B1 INTAKE ICE PROTECTION Hot Air Anti Icing Large commercial passenger aircraft use podded engines with pitot intake nacelles. It is normal for this configuration to ensure no ice accretion can occur at the leading edge of the intake. Normally in this configuration the intake lip is prevented from icing by blowing hot air, normally from the HP compressor, through a TAI Manifold also known as a piccolo tube that runs inside the leading edge of the duct. The air exits the duct, either from a dedicated exit port on the side of the intake (GE CF6-80) or into the intake itself through a joggled lip on the inside of the intake. The example shown below is a Rolls Royce 535-E4 as fitted to a Boeing 757. The air supply is usually taken immediately at the HP air outlet. In this way air for anti-icing is always available if the engine is running. On some engines this air is also routed through inlet guide vanes and into the LP fan spinner. The system is activated manually from within the cockpit. An anti-ice pressurisation and control valve is activated and allows HP air to pass to the anti-ice manifold. The valve regulates the pressure, to a figure of about 40 psi or below. Anti-icing conditions are deemed to exist at below +100C with visible moisture, that is rain, hail, snow or fog. In the event of valve failure it may be manually locked in the open position prior to take-off. Issued Oct 2012/Reviewed. January 2020 Page 20 PDF Pro Trial Part 66 Module 15 (Gas Turbine Engines) B1