Supply Chain Management PDF
Document Details
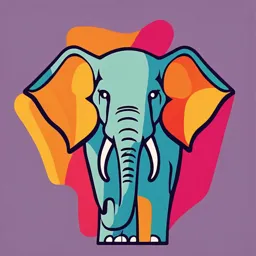
Uploaded by ObservantLeaningTowerOfPisa
University of the Free State
C Hendricks
Tags
Summary
This document provides an overview of supply chain management, focusing on inventory management. It details different types of inventory and their purposes, including the concepts of cycle stock, safety stock, and transit inventory, as well as ordering costs and carrying costs.
Full Transcript
ESCM 2724 SUPPLY CHAIN MANAGEMENT PROF C HENDRIKS LEARNING UNIT 3: INVENTORY MANAGEMENT (CH 10) After you have studied this chapter, you should be able to: provide reasons why it is necessary to hold inventory; differentiate between the various types of inventory; explain...
ESCM 2724 SUPPLY CHAIN MANAGEMENT PROF C HENDRIKS LEARNING UNIT 3: INVENTORY MANAGEMENT (CH 10) After you have studied this chapter, you should be able to: provide reasons why it is necessary to hold inventory; differentiate between the various types of inventory; explain some basic inventory concepts; identify inventory-ordering costs and inventory-carrying costs; LEARNING UNIT 3: INVENTORY MANAGEMENT What is inventory: Inventory refers to material resources that are stored for usage at a later stage, either through transformation from a raw to a finished state, or through use in the current state. Inventory can be seen in different categories, such as raw materials inventory, work-in-process inventory and finished goods inventory. LEARNING UNIT 3: INVENTORY MANAGEMENT 10.2 The purpose of inventory There are various reasons why businesses on different levels in the supply chain hold inventory. The functions of inventories can be classified into the following broad categories: Decoupling Balancing supply and demand Buffering against uncertainties in supply and demand Geographical specialization Preventing the cost of a stockout. LEARNING UNIT 3: INVENTORY MANAGEMENT The purpose of inventory Decoupling Decoupling provides maximum operating efficiency in a logistics environment by keeping inventories at different stages or different locations in the supply chain. Holding inventory at different stages may lead to economies of scale. LEARNING UNIT 3: INVENTORY MANAGEMENT The purpose of inventory Balancing supply and demand To reconcile supply with the demand for a product. Balancing is concerned with the elapsed time between consumption and manufacturing and links the economies of manufacturing with variations in consumption. The balancing function of inventory is most prominent in seasonal supply and/or demand. This seasonality can take two forms: Seasonal production, but year-round consumption Seasonal consumption, where supply must meet peak demand. LEARNING UNIT 3: INVENTORY MANAGEMENT The purpose of inventory Buffering against uncertainties in supply and demand. Protect the supply chain against three types of uncertainty: Uncertainty of future demand Lead-time uncertainty Uncertainty in supply LEARNING UNIT 3: INVENTORY MANAGEMENT The purpose of inventory Geographical specialization The economic location of factories is often based mostly on the availability and cost of the factors of production, such as land, power, materials, water and human resources. The factors of production are not necessarily close to the markets where the final product is consumed. Example: Factory in Italy and factory in Portugal needs different inventor. LEARNING UNIT 3: INVENTORY MANAGEMENT The purpose of inventory Preventing the cost of a stockout. The most important function of inventories is to ensure the availability of products – either raw materials, semi-finished goods or final products. If these are not available, the result is the cost of a stockout. There are three possible costs attached to a stockout. In order of severity, these are: The cost of a backorder The cost of a lost sale The cost of a lost customer. LEARNING UNIT 3: INVENTORY MANAGEMENT 10.3 Types of Inventory 10.3.1 Inventory based on its position in the supply chain Raw material Work-in-process Packaging material Finished goods inventory LEARNING UNIT 3: INVENTORY MANAGEMENT 10.3 Types of Inventory 10.3.2 Classification of inventory based on its purpose Cycle stock From a manufacturing perspective, cycle stock is the amount of stock produced in an average production run. From a distribution perspective, cycle stock is the inventory required to meet normal or average demand for the product. LEARNING UNIT 3: INVENTORY MANAGEMENT 10.3 Types of Inventory 10.3.2 Classification of inventory based on its purpose Transit inventory- stock that is enroute Safety (buffer) stock – Demand uncertainty – Lead-time uncertainty – Duration of the lead time – Service level policy of the business – Order quantity. LEARNING UNIT 3: INVENTORY MANAGEMENT 10.3 Types of Inventory 10.3.2 Classification of inventory based on its purpose Speculative stock To qualify for quantity discounts When a price increase in goods is expected When a shortage of the goods is expected To protect against a strike To provide for the promotion (marketing campaign) of a certain item To provide for seasonal sales. LEARNING UNIT 3: INVENTORY MANAGEMENT 10.3 Types of Inventory 10.3.2 Classification of inventory based on its purpose Dead stock Dead stock is the term used for items for which there has been no demand for a specified period of time. Such stock is normally obsolete and should be disposed of, since it occupies space that could be put to better use. LEARNING UNIT 3: INVENTORY MANAGEMENT 10.4. Inventory Concepts 10.4.1 Availability 10.4.2 Average inventory Average inventories include cycle stock, safety stock and transit inventory. Average inventory for a specific item is calculated as half-order quantity plus safety stock. Where applicable, transit inventory must also be added. LEARNING UNIT 3: INVENTORY MANAGEMENT 10.4.2 Average inventory Order quantity = 500, then ½ order quantity is 250 Assume that safety stock is 50 then average inventory = 250 + 50 = 300 LEARNING UNIT 3: INVENTORY MANAGEMENT LEARNING UNIT 3: INVENTORY MANAGEMENT 10.4.3 Inventory turnover Inventory turnover (or stock turnover) is a measure of how well stock is managed. It gives an indication of how many times during a year the average stock is used up and can be expressed as follows: Inventory turnover = total annual sales ÷ average inventory. If you only sell 600 ÷ 300 = turnover = 2 But if sell 2400 ÷ 300 = turnover = 8 LEARNING UNIT 3: INVENTORY MANAGEMENT 10.5.1Ordering costs Ordering costs consist typically of administration, communication and handling costs, associated with order placement, processing and receiving. LEARNING UNIT 3: INVENTORY MANAGEMENT 10.5.2 Carrying costs Costs associated with holding products in stock. Together with transport costs, these are regarded as one of the major components of logistics costs. Assuming a carrying cost of 25 per cent, the annual inventory cost for a business with R1 million in average inventory is calculated as follows: Inventory-carrying costs= value of average inventory × carrying cost % = R1 000 000 × 25% = R250 000 LEARNING UNIT 3: INVENTORY MANAGEMENT Inventory-carrying costs can be broadly categorised as follows: Capital costs on inventory investment Insurance Inventory risk costs – Obsolescence – Damage – Shrinkage Storage costs. Leave out 10.5.3 and 10.5.4