LU-1-INTRODUCTION-AND-OVERVIEW-OF-SUPPLY-CHAIN-MANAGEMENT PDF
Document Details
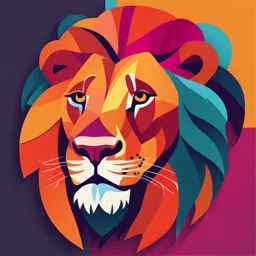
Uploaded by PhenomenalVitality
NEUST
CLD
Tags
Summary
This document is a module on supply chain management. It provides a comprehensive understanding of the key concepts and is designed for BS Entrepreneurship students. The document covers topics such as supply chain planning, sourcing, manufacturing, delivery, and returning.
Full Transcript
Title Page i Preface What Will You Learn? By the end of this module, you will have a comprehensive understanding of the key principles and practices of Suppl...
Title Page i Preface What Will You Learn? By the end of this module, you will have a comprehensive understanding of the key principles and practices of Supply Chain Management. You will be equipped with the knowledge and skills necessary to navigate the complexities of supply chain operations and apply effective strategies to optimize performance and achieve business success. Specifically, you should be able to: § develop a mature and critical understanding of the concepts, theories, and evidence related to supply chain management; § understand how the mathematical foundations of supply chain solutions can be applied; § comprehend the factors underlying vendor selection; § be able to desc ribe and present logistics management effectively; § be able to analyze and present supply chain inventory management insights; and § explore the importance of information, its uses, and the technologies that facilitate better decision-making. What are the general contents of this module? This module is composed of six (6) units. Each section has the following major parts: § Overview. This offers a one-paragraph overview of the entire unit. § Learning Objectives. These describe the measurable skills, abilities, knowledge or values that you are expected to demonstrate as a result of completing the unit. § Setting Up Activity. This part stimulates interests to participate and to engage yourself in the lessons. § Lesson Proper. This includes discussions of the topics/lessons covered in each unit. § Assessing Learning Activities. This part measures and helps you to test your learning in every unit. § References. This part collates the various sources used in the module. What is the significance of this course? This course in Supply Chain Management (SCM) is highly significant for BS Entrepreneurship students, providing essential insights and skills that are crucial for the success of any entrepreneurial venture. By the end of this module, you will gain a comprehensive understanding of key principles and practices that will empower you to manage and optimize supply chain operations effectively. This module in Opportunity Seeking was prepared to serve as reference material for BS Entrepreneurship students which provided essential knowledge in managing a business. The author also welcomes any suggestions or comments to improve or make this module more useful. - CLD ii Table of Contents of Contents able Title Page........................................................................................................................................................................................ i Preface............................................................................................................................................................................................ ii Table of Contents......................................................................................................................................................................iii UNIT I: INTRODUCTION AND OVERVIEW OF SUPPLY CHAIN MANAGEMENT.................................. 1 The Concept of Supply Chain Management............................................................................................................... 2 The Importance of Supply Chain Management........................................................................................................ 4 Societal Role of Supply Chain Management.............................................................................................................. 4 Supply Chain Activities / Functions.............................................................................................................................. 5 Make or Buy Decisions and Considerations.............................................................................................................. 6 Supply Chain Strategies and Managing Supply Chain........................................................................................... 7 Supply Chain Integration: Issues and Opportunities............................................................................................. 8 The Concept of Vendor Managed Inventory (VMI) and Its Benefits............................................................... 8 Types of Purchase Orders................................................................................................................................................. 9 Assessing Learning............................................................................................................................................................ 10 Activity 1-1....................................................................................................................................................................... 10 Activity 1-2....................................................................................................................................................................... 12 Activity 1-3....................................................................................................................................................................... 13 UNIT II: MATHEMATICAL FOUNDATIONS OF SUPPLY CHAIN SOLUTIONS..................................... 14 Supply Chain Planning..................................................................................................................................................... 15 Key Supply Chain Planning Elements....................................................................................................................... 15 Supply Chain Planning Software................................................................................................................................. 16 Supply Chain Planning Strategies............................................................................................................................... 16 Capacity Planning.............................................................................................................................................................. 17 Capacity Strategies............................................................................................................................................................ 17 Strategic Capacity Planning for Products and Services..................................................................................... 17 Defining and Measuring Capacity and the Determinants of Effective Capacity...................................... 18 Steps in the Capacity Planning Process.................................................................................................................... 18 Inventory Optimization................................................................................................................................................... 19 Dynamic Routing and Scheduling............................................................................................................................... 19 Assessing Learning............................................................................................................................................................ 20 Activity 2-1....................................................................................................................................................................... 20 Activity 2-2....................................................................................................................................................................... 23 Activity 2-3....................................................................................................................................................................... 24 UNIT III: VENDOR SELECTION....................................................................................................................... 25 Vendor Selection................................................................................................................................................................ 26 Vendor Evaluation............................................................................................................................................................. 26 Vendor Development....................................................................................................................................................... 27 Negotiations......................................................................................................................................................................... 27 Tools for Vendor Selection............................................................................................................................................. 27 Assessing Learning............................................................................................................................................................ 30 Activity 3-1....................................................................................................................................................................... 30 Activity 3-2....................................................................................................................................................................... 32 Activity 3-3....................................................................................................................................................................... 33 iii UNIT IV: LOGISTICS MANAGEMENT............................................................................................................. 34 Definition of Logistics...................................................................................................................................................... 35 Supply Chain Management and Logistics................................................................................................................ 35 Role of Logistics in Supply Chain Management.................................................................................................... 35 Logistics Management..................................................................................................................................................... 36 7 R’s of Logistics Management..................................................................................................................................... 36 Importance of Logistics Management in Modern Business Operations..................................................... 37 Distribution Management.............................................................................................................................................. 37 Four (4) Channels of Distribution............................................................................................................................... 38 A Systems Approach to Logistics Management.................................................................................................... 38 Assessing Learning............................................................................................................................................................ 40 Activity 4-1....................................................................................................................................................................... 40 Activity 4-2....................................................................................................................................................................... 42 Activity 4-3....................................................................................................................................................................... 43 UNIT V: SUPPLY CHAIN INVENTORY MANAGEMENT............................................................................. 44 The Role of Inventory in the Supply Chain............................................................................................................. 45 Inventory Management Process.................................................................................................................................. 45 Inventory Management Techniques.......................................................................................................................... 45 Inventory Management Strategies............................................................................................................................. 46 Useful Inventory Management Formulas................................................................................................................ 47 Economic Order Quantity (EOQ)............................................................................................................................ 47 Safety Stock...................................................................................................................................................................... 48 Reorder Point.................................................................................................................................................................. 48 Assessing Learning............................................................................................................................................................ 50 Activity 5-1....................................................................................................................................................................... 50 Activity 5-2....................................................................................................................................................................... 52 Activity 5-3....................................................................................................................................................................... 53 UNIT VI: INFORMATION TECHNOLOGY IN A SUPPLY CHAIN............................................................... 54 The Role of Information Technology (IT) in a Supply Chain........................................................................... 55 The Supply Chain IT Framework................................................................................................................................ 55 Transaction Management Foundation...................................................................................................................... 58 Assessing Learning............................................................................................................................................................ 59 Activity 6-1....................................................................................................................................................................... 59 Activity 6-2....................................................................................................................................................................... 61 Activity 6-3....................................................................................................................................................................... 62 References........................................................................................................................................................... 63 iv UNIT I: INTRODUCTION AND OVERVIEW OF SUPPLY CHAIN MANAGEMENT MANAGEMENT Overview This module introduces you to the fundamental concepts and significance of supply chain management (SCM). You will explore the roles and activities involved in SCM and gain a comprehensive overview of its importance in today's business environment. Learning Objectives At the end of the unit, I am able to: 1. describe the concept and significance of supply chain management; 2. determine the roles and activities performed in supply chain management; and 3. summarize the overview of supply chain management. Setting Up Name: _____________________________________________ Date: __________________ Course/Year/Section: ___________________________ Tell Me Game! Direction: This game will help you relate your personal experience of the topics to be discuss in this chapter. It will boost your prior knowledge on the topic for you to easily cope up with the topics in this module. Here are the mechanics: 1. Try to ask a seller of a retail product and a seller of a wholesale or bulk products. Compare their price. Based on your comparison try to figure out why are they different and what made it different price in buying a wholesale or bulk compared to retail. 2. After doing so, try to relate each of your answers on the subtopics to be discuss in this module and answer the remain question you might be thinking. 1 Lesson Proper The Concept of Supply Chain Management The scent of your favorite coffee fills the air soon after your alarm clock leaves and the coffeemaker begins. The supply chain will deliver coffee beans to your kitchen and the world over. Every household has something so common: preparing, requirement forecasting, sourcing and logistical skills in order to transfer the beans to local sellers while they are still young. Your caffeine fix options would be severely limited without a strong supply chain in place. According to Fernando (2022), a supply chain is the network of individuals, companies, resources, activities, and technologies used to make and sell a product or service. A supply chain starts with the delivery of raw materials from a supplier to a manufacturer and ends with the delivery of the finished product or service to the end consumer. Meanwhile, supply chain management (SCM) is the management of the flow of goods and services and includes all processes that transform raw materials into final products. It involves the active streamlining of a business's supply-side activities to maximize customer value and gain a competitive advantage in the marketplace. Supply chain management can be broadly categorized into five steps or areas: 1. Planning. To get the best results from SCM, the process usually begins with planning to match supply with customer and manufacturing demands. Firms must predict what their future needs will be and act accordingly. This relates to raw materials needed during each stage of manufacturing, equipment capacity and limitations, and staffing needs along the SCM process. 2. Sourcing. Efficient SCM processes rely very heavily on strong relationships with suppliers. Sourcing entails working with vendors to supply the raw materials needed throughout the manufacturing process. A company may be able to plan and work with a supplier to source goods in advance. However, different industries will have different sourcing requirements. In general, SCM sourcing includes ensuring: o the raw materials meet the manufacturing specification needed for the production of goods. o the prices paid for the goods are in line with market expectations. o the vendor has the flexibility to deliver emergency materials due to unforeseen events. o the vendor has a proven record of delivering goods on time and in good quality. 3. Manufacturing. At the heart of the supply chain management process, the company transforms raw materials by using machinery, labor, or other external forces to make something new. This final product is the ultimate goal of the manufacturing process, though it is not the final stage of supply chain management. 4. Delivering. Once products are made and sales are finalized, a company must get the products into the hands of its customers. The distribution process is often seen as a brand image contributor, as up until this point, the customer has not yet interacted with the product. In strong SCM processes, a company has robust logistic capabilities and delivery channels to ensure timely, safe, and inexpensive delivery of products. 5. Returning. The supply chain management process concludes with support for the product and customer returns. Its bad enough that a customer needs to return a product, and its even worse if its due to an error on the company's part. This return process is often called reverse logistics, and the company must ensure it has the capabilities to receive returned products and correctly assign refunds for returns received. 2 It is expected that all the things should be handled in the supply chain correctly to satisfy consumer expectations in anything. And it means getting things correctly for the first time – there are no mulligans, no errors. The Seven Rights of Fulfillment guided world-class enterprises throughout the supply chain to deliver quality service and satisfy customers. APICS Dictionary, 15th edition, defines Perfect Order Fulfillment as a measure of an organization’s ability to deliver a perfect order. Perfect Order is defined as an order which the “seven R’s” are satisfied: the right product, the right quantities, the right condition, the right place, the right time, the right customer, the right cost.’ In short, Perfect Order Fulfillment is the percentage of orders meeting delivery performance with complete and accurate documentation and no delivery damage or defects. A research study of more than 100 producers, distributors and retailers over ten years ago has revealed certain widely used supply chain strategies and initiatives. These ideas and practices have been broken down to seven principles and have been presented by SCM professionals in an article from the Supply Chain Management Review. Principle 1: Customer segments based on the different groups' service needs, and adjust the supply chain to provide a profitable service for these segments. Principle 2: Adapting the logistics network to the customer segments' service needs and profitability. Principle 3: Listen to market signals and coordinate demand forecasting across the supply chain to ensure accurate forecasts and optimum allocation of resources. Principle 4: Differentiate between the product and the customer and speed throughout the supply chain. Principle 5: Strategically controlling supply sources in order to reduce the total ownership and service costs. Principle 6: Build an IT supply chain strategy that supports multiple decision-making levels and offers a clear picture of the flow of goods, resources and knowledge. Principle 7: To follow a performance-crossing networks in order to measure mutual progress in effectively and efficiently reaching end users. Even though these timeless concepts are over ten years old, they emphasize the need for supply chain management to concentrate on the company. They stress the importance of organized activities inside and through organizations (demand planning, procurement, assembly, distribution and knowledge sharing). An excerpt from the article is provided here: "Managers are being more and more assigned a role in a very real battle – one direction motivated by the increased demands of consumers and the other by the desire for growth and propitiation of the business. Many have discovered that they can prevent the cable from snapping and indeed achieve profitable growth through strategic variable management of the supply chain.” Two important things these experienced managers recognize: 1. They think of all the links involved in the flow of products, services and information from their suppliers to their customers (i.e. canal customers, such as distributors and retailers) in the entire supply chain. 2. They are striving for tangible results — concentration on revenue growth, asset use and costs. 3 The Importance of Supply Chain Management It is well known that supply chain management is an integral part of most businesses and is essential to company success and customer satisfaction. 1. Boost Customer Service Customers expect the correct product assortment and quantity to be delivered. Customers expect products to be available at the right location. Customers expect products to be delivered on time. Customers expect products to be serviced quickly. 2. Reduce Operating Costs o Decreases purchasing cost. Retailers depend on supply chains to quickly deliver expensive products to avoid holding costly inventories in stores any longer than necessary. o Decreases production cost. Manufacturers depend on supply chains to reliably deliver materials to assembly plants to avoid material shortages that would shutdown production. o Decreases total supply chain cost. Manufacturers and retailers depend on supply chain managers to design networks that meet customer service goals at the least total cost. 3. Improve Financial Position o Increases profit leverage. Firms value supply chain managers because they help control and reduce supply chain costs. This can result in dramatic increases in firm profits. o Decreases fixed assets. Firms value supply chain managers because they decrease the use of large fixed assets such as plants, warehouses and transportation vehicles in the supply chain. o Increases cash flow. Firms value supply chain managers because they speed up product flows to customers. Societal Role of Supply Chain Management 1. Ensuring Survival of Humans o SCM helps sustain human life. Human beings rely on supply chains to provide basic food and water resources. o SCM enhances human health. Human beings rely on supply chains for drug and health care delivery. The difference between life and death may be the supply chain output during a medical emergency. o SCM protects people against extreme climatic conditions. Humans are dependent on the energy supply chain to supply the energy for lighting, heat, cooling and air conditioning for homes and businesses. Logistic failure (a power blackout) could soon lead to a danger to people's lives. 2. Improving Life Value o Economic growth base. Companies with highly established supply chain infrastructure (modern interstate highways, a massive rail network and numerous modern ports and airports) can trade many goods quickly and efficiently between businesses and consumers. Therefore, the economy is expanding. Ironically, the one thing most poor countries have in common is neither a very poorly developed infrastructure for the supply chain. o Improves living standard. Companies with a highly developed supply chain infrastructure (modern interstate highway system, extensive rail network, numerous modern ports and airports) are able to exchange goods quickly and cheaply between 4 businesses and consumers. As a result, consumers can afford to buy a higher level of living in society with their income thereby. o Employment development. Professionals in the supply chain design and operate the supply chain in the business, overseeing transport, storage, inventory management, packaging and logistics details. As a result, there are many jobs in the supply chain sector. o Opportunity for pollution reduction. Packaging and transportation are central to supply chain activities. Some unwanted environmental pollutants, like cardboard waste and carbon dioxide gas fuel emissions, are produced as a by-product of these activities. o The opportunity for energy use reduction. Supply chain activities involve transportation of both human and product. Scarce energy is being exhausted as a by- product of these practices. Transportation actually accounts for 30% of world energy usage and 95% of global oil production. As network designers, supply chain experts play their part in developing less resourceful, energy-efficient supply chains. Supply Chain Activities / Functions Supply chain strategy must be consistent with both the overall business strategy and efforts within such areas as purchasing, logistics, manufacturing and marketing. The Supply Chain activities have to be clearly spelled out for the given business. 1. Strategic Activities o Strategic network optimization, including the number, location, and size of warehouses, distribution centers and facilities. o Strategic partnership with suppliers, distributors, and customers, creating communication channels for critical information and operational improvements such as cross docking, direct shipping, and third-party logistics. o Product design coordination, so that new and existing products can be optimally integrated into the supply chain, load management o Information Technology infrastructure, to support supply chain operations. o Where to make and what to make or buy decisions o Align overall organizational strategy with supply strategy 2. Tactical Activities o Sourcing contracts and other purchasing decisions. o Production decisions, including contracting, locations, scheduling, and planning process definition. o Inventory decisions, including quantity, location, and quality of inventory. o Transportation strategy, including frequency, routes, and contracting. o Benchmarking of all operations against competitors and implementation of best practices throughout the enterprise. o Milestone payments 3. Operational Activities o Daily production and distribution planning, including all nodes in the supply chain. o Production scheduling for each manufacturing facility in the supply chain (minute by minute). o Demand planning and forecasting, coordinating the demand forecast of all customers and sharing the forecast with all suppliers. o Sourcing planning, including current inventory and forecast demand, in collaboration with all suppliers. o Inbound operations, including transportation from suppliers and receiving inventory. 5 o Production operations, including the consumption of materials and flow of finished goods. o Outbound operations, including all fulfillment activities and transportation to customers. o Order promising, accounting for all constraints in the supply chain, including all suppliers, manufacturing facilities. distribution centers, and other customers. o Performance tracking of all activities. Make or Buy Decisions and Considerations The decision to make or buy is to make a business decision to either make an object internally (in-house) or purchase it externally (from an external supplier). Often known as outsourcing, the purchase side of the decision. Decisions are typically made when a business which has created or partially changed a component or part significantly — is having difficulties with existing suppliers or is declining capability or increasing demand. Analysis of performance or purchase is carried out on a strategic and operational level. Obviously, the long range of the two is the strategic level. At the strategic level the factors considered include prospective prediction and the existing climate. Things such as government policy, competitive companies and consumer dynamics all influence making or buying decisions strategically. Naturally, businesses should create products that reinforce their core competencies, or are in line with them. These are areas in which the company is strongest and give the company a competitive edge. Decisions on making or purchasing are often taken into service. Review by Burt, Dobler, and Starling, and Joel Wisner, G. Keong Leong, and Keah-Choon Tan in separate texts suggests these things which favor a path within the company: o Performance considerations (less costly to do the job) o Want to combine farm activities o The successful usage, using established idle power, of excess plant capability to assist fixed overhead absorption. o Want to monitor output and/or quality directly o Improved regulation of quality o Proprietary technologies must be secured by design secrecy o Untrustworthy networks o No eligible suppliers o Want to retain stable workers (during rising sales periods) Companies can be affected by factors which include externally: o Lack of expertise-how o The work and know-how of suppliers goes beyond that of the consumer o Price (less costly to buy) cost considerations o Specifications for limited volume o Limited or insufficient production facilities o Want to maintain a policy on multiple sources o Considerations of indirect management power o Considerations of sourcing and inventory o Preference for brand o Not applicable to the strategy of the company The cost and the availability of productive resources are the two main factors to consider in making or purchasing decisions. The consequences of these factors would cover all costs and be of long-term significance. Burt, Dobler and Starling note that "no other element is more common in perception or confusion." The buying company would naturally compare costs of production and 6 acquisition. The main elements included in this comparison are Burt, Dobler and Starling. The "make" analytical elements include: o Incremental carrying costs for inventories o Labor related costs o Overhead costs for marginal factories o The purchased content has been shipped o Incremental cost of production o Any costs associated with consistency and related issues o Incremental costs of procurement o Incremental cost of debt For the "buy" study cost considerations include: o The part purchase price o Costs of shipping o Costs of receipt and monitoring o Incremental cost of production o All quality or service follow-up costs Six of the costs to be taken into account are incremental. An additional expense should not be borne by definition if the component was imported from an external supplier. Incremental costs include the variable cost plus the cumulative portion of the fixed overhead allocated to the component production, when a business is not able to manufacture the product at the present time.. If the company has a surplus capacity of the output of the element in question, only the overhead variances arising from the manufacture of the components is considered in progress. This implies that fixed costs are not incremental and should not be considered part of the cost of making the part under circumstances with a reasonable idle power. Supply Chain Strategies and Managing Supply Chain A supply chain strategy is the overarching plan that an organization uses to manage the flow of goods and services, from sourcing raw materials to delivering products to customers. It outlines the key processes, technologies, and partnerships that the organization will use to optimize the efficiency and effectiveness of its supply chain. There are several different components that make up a supply chain strategy, including: 1. Sourcing. This involves identifying and selecting suppliers, as well as managing the relationships with those suppliers to ensure that they can meet the organization’s needs in terms of quality, cost, and delivery. 2. Logistics. This includes managing the movement of goods and materials through the supply chain, from the point of origin to the point of consumption. This can include transportation, warehousing, and inventory management. 3. Production. This includes the processes and technologies that are used to turn raw materials into finished goods. It can also include managing the flow of goods through the organization’s own production facilities. 4. Distribution. This involves getting the finished goods to the customers. It can include managing the organization’s own distribution centers, as well as working with third-party logistics providers (3PLs) and other partners to deliver products to customers. 5. Customer Service. This includes managing the relationship with customers, including taking orders, providing after-sales service, and handling returns and complaints. 7 Creating a supply chain strategy There are three phases to creating a supply chain strategy: 1. Supply chain strategy design. At this stage, you will decide the company’s strategic objectives and KPIs. You should also review and choose suppliers, decide where to locate warehouses and whether to implement software throughout the supply chain. 2. Supply chain strategy planning. If you understand your strategic objectives, you will be able to plan how to balance supply and demand. This will ensure that you have the right goods, at the right time, and in the right place to meet customer demand. 3. Supply chain strategy execution. This is where inventory teams will manage warehouses and inventory levels to ensure the company can meet customer demand. Supply Chain Integration: Issues and Opportunities Supply chain integration is a strategy that establishes a single system that can bring together multiple stakeholders involved in the process for greater efficiency, both in terms of productivity and cost savings. Supply chain integration is done to create an efficient system that starts from raw materials from the supplier to the end product going to the consumer without delays, increases in cost, or poor customer experience. An organization strives to build a superior supply chain with the help of integration. It involves complete system transparency, from the supplier to the customer. Multiple elements at multiple levels in an enterprise must work together to achieve integration in the supply chain. As the supply chain integration benefits far outweigh the efforts in establishing the processes, it is essential to understand the key elements to achieve supply chain integration. 1. Choosing the right vendors. A business needs to choose the right vendors who are willing to meet the standard requirements at the right price and at the right time. 2. Working with internal teams. A business needs to work closely with internal teams in the supply chain and across the organization. Therefore, you can expect efficient supply chain processes with the internal team onboard for supply chain integration. 3. Waste elimination. A business needs to focus on eliminating wastage from supply chain processes. It can be done via manual changes or with gaps identified with the procurement software. Aside from that, there are several barriers to the supply chain integration process. Some of the critical barriers to supply chain integration are: o Lack of IT solutions o Lack of knowledge o Poor working relationship o Lack of communication o Cost of integration o Conflicting goals The Concept of Vendor Managed Inventory (VMI) and Its Benefits The Vendor Managed Inventory (VMI) is used to manage the inventory of their customers by manufacturers. It happens with physical counts or the use of customer info. When inventory rates exceed their reorder points, vendors must refill their inventory. There following are the benefits using Vendor Managed Inventory: 1. More tracking. In order to forecast demand accurately, VMI gives sellers more leverage. This can lead to more productive production. They will produce clean and deliver frequently. In addition, VMI reduces inventory and inventory shortages. In addition, VMI providers have 8 full visibility into inventory levels of their customers. They can satisfy demand better and that inventory and expense. 2. Strengthen the relationship between consumers and suppliers. Superior service providers are able to establish better relations with their customers. VMI vendors should grow into more valuable vendors. In addition, the strategic coordination will be improved. VMI will give both parties substantial benefits. 3. Price management of production. When VMI regulates suppliers, waste, value-added factors and other costs can be minimized. Precise preparation decreases storage costs and reduces unused inventory. In particular, sellers should reduce inventory shortfalls and high shipping distribution costs. Types of Purchase Orders In essence, a purchase order is a request from the buyer to the vendor, which provides information on what they want in their order: object, quantity, delivery time, etc. If the order is approved, it is a contract which is binding on any conditions stated in the order. There are four major types of buying orders, which vary basically based on the amount of details that you know when the order is put. 1. Standard Purchase Order. The most common form of purchasing order is where every aspect of the goods to be purchased is known, i.e. the amount, the size, the delivery time and the payment terms is known at the time of the purchase. Standard buying orders are used for sporadically ordered products, one-off shipments or shopping, where there is a lot of clarity about exactly what is required. 2. Plan Purchase Order. The majority of the information for this purchase order are known: products, number, price and payment terms. You agree to price and quantity and so on by using this order, but you just make a timely delivery schedule. Then you can build releases against the PPO with a comprehensive delivery schedule when you decide those dates that you want your goods shipped. You commit to the delivery when you release it. 3. Contract Purchase Order. Even the particular item needed is not known, or this final purchase order form. In that case, you can negotiate with your supplier on terms and conditions, but only until the products and quantities you want are determined. Standard Purchase Orders are defined by referring to the CPO when something from that supplier is purchased from the CPO. 4. Blanket Purchase Order. The situation with a BPO is the same as that of a PPO, unless prices and quantities are also unknown. In some delivery conditions you will still specify the item you want, but nothing until you release it against the BPO. Typically for the specified period, you agree on a maximum quantity and then order a quantity below it. The price breaks depending on the quantity you bought may be agreed upon. 9