Green Operations and Supply Chain Flexibility in Automotive (PDF)
Document Details
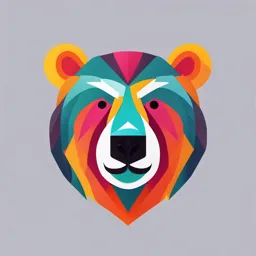
Uploaded by InnocuousShark3994
University of Birmingham
2019
Yang Liu, Yufeng Zhang, Luciano Batista, Ke Rong
Tags
Summary
This paper, published in the International Journal of Production Economics in 2019, explores the relationship between supply chain flexibility and green operations strategies, focusing on the automotive sector. The authors use a case study approach to analyze how different flexibility dimensions support various green initiatives within three automakers. Their findings contribute to the theoretical understanding of this complex relationship and provide practical implications for managers seeking to integrate green efforts into their supply chains.
Full Transcript
International Journal of Production Economics 214 (2019) 30–43 Contents lists available at ScienceDirect International Journal of Production Economics...
International Journal of Production Economics 214 (2019) 30–43 Contents lists available at ScienceDirect International Journal of Production Economics journal homepage: www.elsevier.com/locate/ijpe Green operations: What's the role of supply chain flexibility? T a,∗ a b c Yang Liu , Yufeng Zhang , Luciano Batista , Ke Rong a Birmingham Business School, University of Birmingham, Birmingham, United Kingdom b Aston Business School, Aston University, Birmingham, United Kingdom c Institute of Economics, School of Social Science, Tsinghua University, Beijing, China A R T I C LE I N FO A B S T R A C T Keywords: This paper aims to understand the specific role that supply chain flexibility (SCF) can play in the successful Green operations adoption of green operations (GO) strategies based on evidence from the automotive industry. By conducting an Supply chain flexibility exploratory case study with three automakers, it is found that different GO strategies require the support of Case study different SCF dimensions. More importantly, the magnitude of the role played by each flexibility dimension Automotive varies depending on the degree of innovativeness in the green design initiatives, the types of green purchasing Sustainability initiatives, and the strategic orientation of green manufacturing initiatives being adopted. Our case studies con- tribute to the theoretical understanding of the complex SCF-GO relationship by identifying the essential theo- retical constructs and indicating their lower layer interactions in a systematic way. In practice, our findings may help managers assess which SCF dimensions can contribute more significantly to their specific GO efforts, and then strategically plan, develop, and deploy relevant flexibility to support beneficial outcomes. Our study contributes to the OM literature by clarifying the multidimensional effects of SCF on GO. 1. Introduction eco-design initiatives and VW's green purchasing programs (Nunes and Bennett, 2010). In recent years, extensive research has been conducted Dynamic consumer demands and market competition have caused to explore effective ways to tackle environmental problems, many of pressure for rapid response for customized products and services. For which have focused on examining the association between lean man- instance, Volkswagen (VW) could potentially offer over a billion of ufacturing and sustainability (Cherrafi et al., 2016, 2018; Das, 2018; different variations of VW Golf to its customers (Scavarda et al., 2010). Zhu et al., 2018). However, the contribution of an optional approach However, a mass customization strategy can place significant burden on focusing on SCF has been overlooked in the context of GO. Whether the focal firm and its supply chain with respect to managing cost, there is an association (directly or indirectly) between SCF and GO is quality, and responsiveness (Malhotra and Mackelprang, 2012). De- still under discovered. Can SCF possibly make positive contributions veloping supply chain flexibility (SCF) is a common approach adopted towards GO? Answering this critical question has significant implica- by organizations to meet these challenges (Christopher and Towill, tions for the OM literature due to a widely spread concern that firms 2000). SCF represents the ability of a firm's supply chain to make agile, operating in rapidly changing contexts prefer a flexible working ap- adaptive, and responsive changes to meet market requirements by proach instead of the efficiency-focused lean approach (Fisher, 1997; coping with uncertainty and ensuring the smooth flow of products and Christopher and Towill, 2000). For instance, if a firm possesses strong services through the supply chain (Blome et al., 2014). Empirical stu- volume flexibility supported by its external suppliers and logistics dies confirm that organizations can enjoy superior performance by partners, it may be able to quickly scale up production for its newly fostering high-level SCF capability (Thomé et al., 2014; Sánchez and developed green products to satisfy customers and gain competitive Pérez, 2005). advantages. The firm may enjoy more revenue by rapidly offering the In addition to responding to product and service customization necessary quantity of green products to the market. Tesla Motors suffers pressures, organizations are also facing environmental sustainability a bottleneck of scaling up its production for new models with green concerns. There is a growing emphasis for manufacturing firms to adopt value propositions, providing a testifying example on the negative im- green operations (GO) strategies to reduce their negative environmental pact of not having necessary SCF (Vengattil and Chatterjee, 2018). impacts (Zhu et al., 2007; Liu et al., 2017). Examples include Toyota's According to the resource-based view (RBV) (Barney, 1991; Hitt ∗ Corresponding author. E-mail addresses: [email protected] (Y. Liu), [email protected] (Y. Zhang), [email protected] (L. Batista), [email protected] (K. Rong). https://doi.org/10.1016/j.ijpe.2019.03.026 Received 4 July 2018; Received in revised form 4 March 2019; Accepted 28 March 2019 Available online 01 April 2019 0925-5273/ © 2019 Elsevier B.V. All rights reserved. Y. Liu, et al. International Journal of Production Economics 214 (2019) 30–43 et al., 2016), the adoption of strategies requires the support of firm- example pollution prevention and control in factories, reduction of specific resources and capabilities. It has been further pointed out that energy consumption and emissions, and enhancement of operational firms need to possess and deploy specific capabilities in the pursuit of efficiency at plants (Deif, 2011; Liu et al., 2017). green strategies (Christmann, 2000; Gold, 2010; Liu et al., 2016). As Adopting GO strategies creates many benefits not only to the focal Duclos et al. (2003) noted, the benefit of SCF lies in the ability to fa- firm but also to its supply chain partners (Handfield et al., 2005). For cilitate the adoption of meaningful organizational strategies that satisfy example, a green design strategy can be adopted by a firm to differ- customer demands and improve overall firm performance. We would entiate itself from its rivals by offering eco-friendly products and ser- like to posit that SCF as a key organizational capability will also support vices. Customers may be willing to pay premium prices for these pro- the adoption of GO strategies. However, existing literature offers lim- ducts, thus representing a clear economic advantage both for the focal ited insights into this SCF – GO relationship. For example, an early firm and for its suppliers that manufacture products with less harmful attempt was made by Klassen and Angell (1998) to examine the re- raw materials or in a more environmentally sound manner (Marchi lationship between manufacturing flexibility and environmental man- et al., 2013). agement, but they treated flexibility as an amalgamated construct. Si- Given highly fragmented production networks and increasing glo- milarly, Liu et al. (2016) explored the association between SCF and GO balization, firms are confronted with the complexity of coordination on in the automotive sector, but also treated SCF as a single integrated GO matters because of enlarged distances, and differences in business construct. Prior research has confirmed that SCF is rather a multi- culture and environmental legislation. The more complex a firm's dimensional construct (Vickery et al., 1999; Duclos et al., 2003; supply chain, the more the firm is compelled to shape its green stra- Stevenson and Spring 2007; Malhotra and Mackelprang, 2012), with tegies to reduce environmental problems (Marchi et al., 2013). There- each dimension contributing differently to a firms' performance fore, strategic decision-making in GO becomes critically important and (Sánchez and Pérez, 2005; Malhotra and Mackelprang's, 2012). That challenging, especially when firms are constrained by their limited re- means different dimensions of SCF may play dissimilar roles in the sources and capabilities (Wu and Pagell, 2011). adoption of a specific GO strategy. Hence, there is still a need to un- derstand in what way SCF will contribute to GO, especially considering 2.2. The concept of flexibility the multidimensional nature of SCF. In this study, we will address these knowledge gaps through in- Flexibility is often recognized as a key capability for achieving a vestigations guided by the primary research question: what is the role of competitive advantage (D'Souza and Williams, 2000). Teece and Pisano SCF in the successful adoption of GO strategies? To answer the question, (1994) thus characterized firms that have honed such a capability as we conducted an exploratory case study involving three automakers. ‘high flex’. Research on flexibility has traditionally focused on internal We focused on the automotive industry because the sector's reputation manufacturing flexibility (Duclos et al., 2003). D'Souza and Williams has often been associated with issues concerning environmental man- (2000) noted that manufacturing flexibility represents the capability of agement (Gonzalez et al., 2008; Liu et al., 2016). Flexibility is also one the manufacturing function to make necessary adjustments to respond of the key factors underpinning the success in this industry (Sánchez to environmental changes without a significant sacrifice to firm per- and Pérez, 2005). Studying this sector can therefore produce valuable formance. Despite dissimilar definitions existed the literature, it is insights for academics and practitioners. This focus will also allow us to generally agreed that manufacturing flexibility is a multi-dimensional possibly compare and contrast our observations with the well reported construct (D'Souza and Williams, 2000; Duclos et al., 2003; Koste et al., lean practices in this industry. 2004; Malhotra and Mackelprang, 2012; Merschmann and Thonemann, After this introduction, we will review the relevant literature and 2011). However, some of the proposed dimensions are “primary” (e.g., establish the theoretical background for our case studies in section 2. volume flexibility, modification flexibility, and mix flexibility), whereas The research methodology will then be introduced in section 3 followed others are “secondary” (e.g., machine flexibility, labor flexibility, and by section 4 to outline our analysis process and highlight the key re- material handling flexibility) and the secondary dimensions may be search findings. Section 5 will discuss the wider implications of the components subsumed under the primary ones (Watts et al., 1993), research findings. Finally, in section 6, we draw our conclusions, and suggesting a hierarchical nature to manufacturing flexibility (Koste and offer directions for future research. Malhotra, 1999; Thomé et al., 2014). The various dimensions of manufacturing flexibility proposed in the 2. Literature review and theoretical foundation literature and the hierarchical nature of flexibility dimensions con- centrate on flexibility within a single plant or organization. As noted by 2.1. Green operations (GO) Koste and Malhotra (1999), the tiered perspective of flexibility starts at the top with strategic flexibility and moves down through functional, Due to an increasing need to address environmental issues, GO has plant, and shop floor flexibility and, finally to individual resource attracted considerable attention in recent years (Liu et al., 2016, 2017; flexibility. However, for a firm to bring a new product or a modified Beske and Seuring, 2014; Cherrafi et al., 2018). GO concerns the in- product to market more parts of the “system” must be considered than tegration and alignment of environmental management strategies into only the internal plant (Duclos et al., 2003). Studies have thus shifted production and operations to improve environmental performance focus away from manufacturing flexibility to the linkages between (Marchi et al., 2013; Beske and Seuring, 2014; Liu et al., 2017). The key manufacturing units and suppliers and customers, i.e., supply chain elements of GO include green design (GD), green purchasing (GP), and flexibility. green manufacturing (GM) (Liu et al., 2016, 2017; Wong et al., 2012; Nunes and Bennett, 2010; Cherrafi et al., 2018). GD refers to the sys- 2.3. Supply chain flexibility (SCF) tematic consideration of design performance with respect to environ- mental improvement over the full product life cycle (Liu et al., 2017; An early study on SCF can be found in Vickery et al. (1999), in Nunes and Bennett, 2010). Examples include design for resource con- which they argued that SCF should be examined from an integrative, servation, using recycled materials in product, and design of product for customer-oriented perspective. Their definition encompasses the flex- reduced consumption of energy. GP considers environmental perfor- ibility dimensions that directly impact a firm's customers and the re- mance improvement in the procurement process (Zhu et al., 2007; Seles sponsibility of two or more functions, whether internal or external to et al., 2016). Exemplar practices include environmental audit of sup- the firm. Duclos et al. (2003) contended that a complete definition of pliers and supplier environmental certification. GM is about reducing SCF would include the flexibility dimensions required by all the parti- harmful environmental impacts during the production stage, for cipants in the supply chain to successfully meet customer demand. They 31 Y. Liu, et al. International Journal of Production Economics 214 (2019) 30–43 proposed a conceptual model of SCF consisting of six dimensions, re- firms. In order to address our research question, we aim to explore the fined to five by Lummus et al. (2003). These include operations systems key SCF dimensions and the current GO strategies (exemplified by GO flexibility, logistics processes flexibility, supply network flexibility, organi- initiatives/practices being adopted) in the automotive industry, and to zational design flexibility, and information systems flexibility. examine whether there are relationships between each key SCF di- Although different conceptualizations exist in the literature, it is mension and the respective GO strategy. commonly accepted that SCF has both internal and external dimensions For example, in the event of designing and launching new greener (Vickery et al., 1999; Duclos et al., 2003; Stevenson and Spring 2007; products, firms would possibly need to possess strong new product Malhotra and Mackelprang, 2012; Thomé et al., 2014; Seebacher and flexibility (NPF) as it can help the firms to quickly generate ideas and Winkler, 2015). Internal SCF mainly concerns a focal firm's manu- effectively introduce new products (Zhang et al., 2002). NPF thus can facturing flexibility. Four key dimensions have been discussed in the enable firms to respond quickly to changing customer needs with re- literature, including (1) modification flexibility (MOD), describes how spect to sustainability with new innovative products offerings. More- quickly and efficiently a product alternation can be made to meet more over, incorporating new greener products into existing product port- specific customer demands; (2) mix flexibility (MIX), the ability of the folios may also require a strong mix flexibility (MIX) as it can enable the system to produce a range of different products during the same plan- firms to economically and effectively produce different combinations of ning period; (3) new product flexibility (NEW), the plant's ability to products given certain capacity (Zhang et al., 2003). Green strategies introduce substantially new discrete products into production; (4) vo- also necessitate the use of sustainable materials in production, which lume flexibility (VOL), the ability to change the volume of output of a can be facilitated by firms having strong modification flexibility (MOD) manufacturing process (D'Souza and Williams, 2000; Koste et al., 2004; as it can quickly and efficiently support product modification. There- Malhotra and Mackelprang, 2012; Thomé et al., 2014; Blome et al., fore, it is believed the successful adoption of certain GO strategies may 2014). require the support of certain SCF, both internally and externally, as By synthesizing the dimensions from previous studies and empha- depicted in Fig. 1. We will explain our research method to investigating sizing an integrative view, these external SCF include supplier, logistics, this relationship in the next section. and supply (network) flexibilities. Specifically, supplier flexibility (SUP) refers to the supplier's ability to consistently accommodate various 3. Methods customer requests (Malhotra and Mackelprang, 2012). Logistics flex- ibility (LOG) is the ability to efficiently and cost effectively receive and A multiple case study methodology (Stake, 2006) was used to ex- deliver products as sources of supply and customers change (Duclos plore this SCF – GO relationship in a view to identifying key variables et al., 2003; Thomé et al., 2014), whereas supply network flexibility and linkages between the variables that are not clearly envisaged in the (NET) refers to the ease of changing supply chain partners in response existing literature (Voss et al., 2002; Yin, 2018). This research design to business environment changes (Lummus et al., 2003; Jin et al., allows us to gain in-depth understanding of new or complex phenomena 2014). by yielding a high level of details around SCF and GO. In addition, Not all firms can achieve the same level of flexibility in their supply because of the explorative nature of this research due to the lack of an chains as SCF is a specific organizational capability (Malhotra and established theoretical model in the literature, the primary focus of our Mackelprang, 2012; Merschmann and Thonemann, 2011; Sánchez and case analysis is to gain an overall understanding rather than a complete Pérez, 2005; Vickery et al., 1999). Firms that have strong SCF can test of the causal effect between SCF and GO (Yin, 2018). achieve superior performance (Thomé et al., 2014; Sánchez and Pérez, Although a study on SCF and GO may suggest a firm's supply chain 2005). Despite much has been done to decipher the SCF – performance should be the unit of analysis or the “object of study”, in this research linkage in the existing literature, limited research has explored how SCF we consider a focal firm perspective. This is because SCF should be might influence company's strategic efforts towards environmental treated as the focal firm's strategic capability and should be viewed management, especially considering the multi-dimensional nature of from the integrative perspective, which supports the focal firm's per- SCF. formance outcomes (Vickery et al., 1999; Malhotra and Mackelprang, 2012). We also take on board of Yin's (2018) suggestion that one must 2.4. The conceptual framework focus the case on the perspectives of analysis that will most likely il- luminate the research question. Based on the review and synthesis of literature on SCF and GO, we We select automakers for our exploration to possibly contrast our construct our conceptual model to guide our research (see Fig. 1). From observations with the widely reported practices on lean and green op- a resource-based view (RBV) perspective (Barney, 1991), the successful erations in the automotive industry. Potential candidates were identi- adoption of green strategies requires the support of specific resources fied from the Dow Jones Sustainability Index that contains both social and capabilities (Morash, 2001; Liu et al., 2016). In particular, SCF is a and environmental criteria. These industry leaders are considered more key firm-specific capability (Seebacher and Winkler, 2015), which may active in pursuing environmental management. Annual corporate sus- enable the successful adoption of green strategies in the automotive tainability reports of identified organizations were evaluated to Fig. 1. The conceptual framework. 32 Y. Liu, et al. International Journal of Production Economics 214 (2019) 30–43 determine whether any initiatives to improve environmental perfor- No. of interviews mance existed. We identified 28 potential car manufacturers and over a half of them expressed little interest in supporting our research at the initial contact. Among the firms that were happy to continue the dis- cussion, 6 of them were prepared to provide necessary access to their 13 14 12 entire supply networks as well as offering senior support on strategic environment department managers, production managers managers, environment control managers, plant managers Vice-president, Chief logistics manager, supply managers, managers, environment department managers, production matters. We finally picked 3 firms that would likely lead to distinctive Chief logistics manager, purchasing managers, R&D situations to analyze thematic patterns around the SCF and GO re- SCM managers, CFO, R&D managers, purchasing lationship (Eisenhardt, 1989). Selecting an appropriate number of cases is important in ensuring research quality, validity, and generalizability (Voss et al., 2002). The 3 case firms revealed similar multi-tiered supply networks and each adopted some level of GO initiatives. Most importantly, a high level of access was afforded by top executives of the 3 case firms. This access enabled us to gain deeper insights into their respective SCF and GO. We visited their main manufacturing hubs where they produce their most passenger vehicles. Table 1 provides the characteristics of the 3 case firms. For confidentiality reasons, the names of the case firms remain anonymous. Informants managers Data collection started in August 2016 with the support of a semi- structured interview protocol with open-ended questions (see Appendix). The questions worked as an initial guide to conduct the case 400 1st tier suppliers, approx. 73% of which were located interviews. Necessary adjustments and alterations were made locally, and requiring its suppliers to be located within 555 1st tier suppliers, over 90% of which were located 600 1st tier suppliers, over 80% of which were located throughout and after each interview in order to better capture parti- cular aspects of the subject being investigated (Yin, 2018). The protocol called for multiple respondents from multiple functional areas, in- cluding members of the top management team, R&D, operations/pro- duction, environmental management, purchasing, and logistics/SCM managers (see Table 1). Interviewing multiple respondents allowed us to examine different aspects of internal and external SCF of a case firm and their GO initiatives. In general, each face-to-face interview lasted between 60 and 120 min, with 8 interviews lasting more than 120 min within 300 km radius. because the respondents were more knowledgeable in answering our within 400 km radius questions due to their roles in relevant departments (e.g., SCM). The 200 km radius interviews were recorded under formal consent of the respondents and later transcribed. We made follow-up telephone/Skype interviews to Suppliers further investigate and clarify unclear issues. We also collected data from direct observations within the case firms, presentations, company websites, reports, and newsletters. Data collection was stopped in Size (no. of employees) Approx.30,000 in total Approx.24,000 in total Approx. 6,000 in total March 2017 when a saturation point was reached, where additional data would not add new information to support understanding of the research question (Eisenhardt, 1989). Data analysis comprised both within and across case analysis. The process as outlined in Yin (2018) and Voss et al. (2002) was followed. Accordingly, we have initially written up case overview for each firm (Eisenhardt, 1989) in order to generate internally consistent descrip- tions of each case's SCF and GO initiatives (a total of 165 pages). The Approx. 0.70 m units (of Approx. 0.32 m units (of Approx.1.67 m units (of next stage began with the open coding of the interviews by grouping phrases, sentences, or paragraphs into codes and categories in an in- ductive fashion. Each researcher individually coded the data and then Annual sales we compared the individually coded data to assure consistency. In particular, the coding categories for GO were relatively straightforward 2016) 2016) 2016) and agreement was reached on GD, GP, and GM respectively. Indicative analysis for these categories is presented in Table 2. Passenger vehicle Passenger vehicle Passenger vehicle The coding categories for SCF are depicted in Table 3. The level of SCF in each firm was evaluated using the capability maturity model Main market (Srai and Gregory, 2008), ranging from 1: Initial to 5: Optimizing. The segments results are presented in Table 4 in radar diagram for review and com- ments within the research team and with senior managers from the case firms. Disagreements were resolved through further analysis and up- Joint venture Case characteristics. State owned dates till a high degree of consensus was reached on all constructs be- Ownership fore combining the data into a consensus document. Triangulation in- Private volved combining the findings from multiple interviews, as well as observations and data from multiple sources to mitigate biases and to Table 1 Case enhance reliability and validity (Yin, 2018). A C B Cross-case analysis helped to identify common themes and 33 Y. Liu, et al. International Journal of Production Economics 214 (2019) 30–43 Table 2 GO examples in three case firms. Case Green design (GD) Green purchasing (GP) Green manufacturing (GM) A Energy-efficient vehicles; electric vehicles (EVs); plug- Purchasing more sustainable materials; environmental Environmental management systems; environmental in hybrid vehicles (PHEV); green technologies in design certification of suppliers; strong environmental criteria certifications (ISO14000 series; ISO50001), pollution (e.g. energy-efficient powertrain/engine/ on suppliers; environmental training and support for prevention technologies, emission monitoring and transmission); lightweight design (e.g. intelligent suppliers; environmental assessment and monitoring of control; green factories; new painting shop (e.g. 75% multi-material design in body and engine); use of suppliers. VOCs reduction); use more sustainable energy source sustainable materials (e.g. natural fibers, high/ultra- (e.g. solar power); waste management and recycling high-tensile steels, and recycled parts). (e.g. waste water recycling, heavy metal and mechanic oil recycling); 91% waste recycling rate; noise reduction; Productivity and process optimization (e.g. resource efficiency platform); lean production. B Energy-efficient vehicles, EVs, new green technologies Purchasing more sustainable materials; environmental Quality improvement (e.g. ISO/TS16949); ISO14000 in engine and transmission design (e.g. direct certification of suppliers; research and design series certification; environmental management injection); new body shape design; sustainable collaboration with suppliers; Environmental criteria on systems; green factories (e.g. use LED lights, energy- materials (e.g. avoid the use of hazardous and non- suppliers (e.g. reduce hazardous materials usage, use saving air conditioning and water conservation); new biodegradable materials, use high-strength and lighter more bio-degradable materials) painting shop; energy savings in production; material in body structure) Productivity and process improvement; pollution prevention technologies; emission monitoring and control; lean production C Energy-efficient vehicles; PHEV, EVs, fuel cell vehicles; Purchasing more sustainable materials; suppliers Production process improvement and optimization; lightweight design; green technologies in design. environmental performance assessment and pollution prevention and control (e.g. hazardous waste, monitoring waste water and solid waste); noise reduction; new painting shop and process; environmental certifications; green factories; lean production differences on how different dimensions of internal and external SCF 4. Case analysis towards an integrating framework could impact GO. The within case analysis helped us to examine SCF and GO within a coherent context, while the cross-case analysis served 4.1. GD and SCF as a form of replication where the constructs of interest in one setting could be refined and enriched in other settings (Yin, 2018). Table 4 All three case firms have implemented GD initiatives (see Table 2). illustrates the overall process of our cross-case analysis. These initiatives can be further categorized into three types, based on the degree of innovativeness in GD, i.e., 1) small/minor and frequent modification of existing models for environmental improvement, 2) substantial changes, including for example, lightweighting structural design, and energy-efficient engine/powertrain systems, and 3) radical Table 3 Description of coding categories for SCF. Coding Category Description Example codes Examples Modification Instances in which the interviewees discussed how “Modify”, “modification”, “quickly alter “… we can quickly modify our product features to flexibility quickly and efficiently they can alter their car models product features”, “frequent satisfy different customers' demands.” or their ability to make frequent modification of modification”, product features for a large number of existing models to meet more specific market demands. Mix flexibility Instances in which the interviewees described their “mix”, “make different styles”, “… we have a large product range -producing over a ability to produce many different types of vehicles “different models”, “large product hundred different models in our factories, [with] an during the same planning period or to make quick and ranges”, “product portfolios”, annual production capacity of 900,000 units …” significant alternations to their product portfolios to compete in the market. New product Instances in which the interviewees discussed their “quickly make electric vehicles”, “… the design capability we have enable us to quickly flexibility ability to introduce substantially new discrete vehicles “hybrid vehicles”, “green models”, introduce new models to the market”; into production or to quickly and effectively design and “sustainable cars”, “quickly launch launch these innovative new models on the market. new”, Volume flexibility Instances in which the interviewees discussed how “output flexibility”, “volume “… our factories can produce different models, quickly and efficiently they can change the volume of flexibility”, “volume change”, “volume colours, and configurations [cars] at the same time … output of a manufacturing process to meet specific variation” we can effectively adjust production volume [for each market conditions. model] according to demands.” Supplier flexibility Instances in which the interviewees assessed their “flexible supplier”, “quick response”, “… 90% of our tier-1 suppliers are located within suppliers' ability to consistently and efficiently “flexible supply” 300 km range, which enables fast response and JIT accommodate their various requests and changes. supplies … they can quickly change their production according to our requests” Logistics flexibility Instances in which the interviewees discussed their “flexible delivery”, “logistics “… they[suppliers] locate very closely to our factories logistics operation's ability to efficiently and cost- flexibility”, “efficient logistics”, “quick to realize quick delivery to us.”; “… the milk-run effectively receive and deliver products to meet delivery” model we use can effectively facilitate flexible and production/market needs. quick delivery …” Supply network Instances in which the interviewees discussed how easy “quickly change suppliers”, “select new “… we keep an average 2-3 suppliers per component to flexibility it was for them to change/select supply chain partners suppliers”, “new partners”, “re-design main flexible supply” “for majority of the parts we can in response to changes in sourcing/production network” quickly find and change our suppliers …” requirements. 34 Table 4 Cross-case analysis. Y. Liu, et al. Flexibility Maturity Level Green design (GD) Green purchasing (GP) Green manufacturing (GM) Case A GD-A1: Case A was able to quickly launch a series GP-A1: Case A's sustainable material purchasing was GM-A1: No significant relationship was detected of new hybrid and electric models on the market to related to its green design. Its strong MOD ensured between case A's green factory initiatives and its compete due to its high NEW in place (++). the use of more sustainable materials/parts in its supply chain flexibility (∅). Internal MOD and MIX, SUP mainly played a existing models was performed quickly and GM-A2: Case A had successfully installed new supporting role (+). But, it also required strong effectively (++). Its strong MIX also ensured the technologies in its stamp shop and paint shop for NET (++) to quickly find/switch to competent efficient substitution with recycled bumpers across production process improvement. Its strong MOD suppliers for the new models. several models (++). Case A's strong SUP (++) ensured efficient and smooth adoption without GD-A2: Minor, frequent, ongoing modification of facilitated the smooth procurement of sustainable major interruption for its normal operations (++). existing models for energy efficiency & materials/parts, without disruptions/major It also had successful ongoing small incremental environmental improvement was successful in case problems, despite having the strongest standards of process improvement at plants, requiring the strong A, because it has strong MOD (++). This type of the three case firms. Its NET (+) also provided support from its MOD (++), as well as its SUP to modification also needed the support of internal necessary support if the existing suppliers failed to cope with any changes (+) (e.g. JIT/JIS supplies). MIX (+) if shared across different models and comply with/meet its standards, whilst this was not GM-A3: Case A had strong MIX, which was further Level defined: external SUP to cope with various changes (+). often the case. enhanced by its modular transverse matrix system. 1. Initial (ad hoc) GD-A3: Substantial changes (e.g. lightweighting GP-A2: Case A provided strong support and training This had in turn led to improved production 2. Repeatable (disciplined, under effective control) design) in case A for different models are enabled for all its tier-1 suppliers' environmental certification efficiency (++). 3. Defined (standard, consistent process) by its strong MOD and MIX (++), without and legal obligation. The firm had the most stringent GM-A4: Case A had relatively stronger VOL, and a 4. Managed (predictable process, with detailed measures and affecting its normal production and incurring standards and monitoring of its suppliers' high capacity utilization rate (Cu), enabled by its controls) additional cost. Also, these changes were supported environmental performance. But, its suppliers had strong MIX. When reaching a high Cu, high 5. Optimizing (continuous process improvement is enabled, by case A's external NET and SUP (+) to maintain the highest compliance rate due to the firm's strong productivity and economies of scale can be piloting innovative ideas and technologies) smooth and efficient supplies. SUP (++), and some fear of losing businesses with achieved. case A, enabled by its NET (+). GM-A5: Case A's recycling and reuse efforts (e.g. GP-A3: Compared with other two cases, case A could water pump) were relatively better than the other more easily evaluate and select new environmentally case firms. Its strong MOD provided strong support qualified suppliers who can meet its standards, which for effective modification and production (++), 35 was supported by its relatively stronger NET (++). and its MIX ensured different product models can GP-A4: Large purchasing volume supported all case accommodate these changes (+). These initiatives A's green purchasing, as it provided strong in case A required also strong external support from bargaining power over suppliers (+). suppliers, 3 PL and recyclers due to the complexity and uncertainty in product returns, necessitating both strong SUP and LOG (++). Case B GD-B1: Case B was also able to launch a series of GP-B1: Likewise, Case B's sustainable material GM-B1: Similarly, no significant relationship was EV models on the market with the support of its purchasing was also related to its green design detected between case B's green factory initiatives NEW (++). Its existing suppliers SUP provide initiatives (e.g. using carbon fibre). Though it was and its supply chain flexibility (∅). supporting role in this initiative (+). It however, not on a large scale, its internal MOD and MIX GM-B2: Case B had also successfully installed had some troubles finding competent new suppliers facilitated the modification and substitution of several new technologies (incl. paint shop) for for certain key components, resulting delays. sustainable materials/parts across different product process improvement, which was ensured by its GD-B2: Case B also have minor, frequent, ongoing range without affecting productivity (++). Case B's strong MOD for efficient and smooth transition modification of existing models for energy suppliers most of the time can satisfy its green without major interruption (++). Besides, it also efficiency & environmental improvement purchasing requirements, enabled by its SUP (++). had small and gradual process improvement. Case supported by its strong MOD (++), and the In some cases, however, the firm would need to find B's strong MOD ensured their success. Externally, support of internal MIX (+). Externally, this has alternative suppliers, which required its NET support the suppliers could cope with the changes, been supported by its external SUP to cope with (+). supported by the SUP. The case firm also adopted various changes (+). GP-B2: By contrast, case B had less stringent lean, external SUP provided support for efficient GD-B3: Case B's substantial changes in different standards and monitoring of its suppliers' supplies, especially for JIT delivery (+). models for sustainability considerations are environmental performance. But its suppliers must GM-B3: Case B's platform technologies and some enabled by strong MOD and MIX (++). But, case B comply with the requirements, or they can be key components supplier's modular supplies had experienced difficulties in finding competent penalized or even lose the business with the case improved its MIX, which had in turn led to external suppliers who can meet its requirements firm. This required the firm to have strong SUP improved production efficiency (++). due to its relatively weaker NET. (++). When it had to look for alternative sourcing, GM-B4: Case B had relatively weaker VOL, and a case B required the support of NET (+) to quickly lower Cu and a larger slack capacity, which led to identify competent suppliers. certain waste and affected productivity. GP-B3: For new green supplier selection, case B was GM-B5: Case B's MOD provided strong support for not as efficient as case A as it sometimes experienced its recycling and reuse efforts (e.g. using recycled (continued on next page) International Journal of Production Economics 214 (2019) 30–43 Table 4 (continued) Flexibility Maturity Level Green design (GD) Green purchasing (GP) Green manufacturing (GM) Y. Liu, et al. difficulties, due to relatively weaker NET (++). aluminum and plastics), ensuring the recycled parts GP-B4: Similarly, when there was a large purchasing can be efficiently accommodated by current volume, case B could have greater power influence assembly (++). Despite not being rolled out on a over its suppliers and more easily urge them to meet large scale, this initiative had been used across standards (+) different models, supported by its MIX (+). External suppliers and 3 PL played important role in such initiatives due to uncertainties in returns, requiring strong SUP (++) and LOG (++). Case C GD-C1: Case C had also introduced a series of new- GP-C1: Case C's sustainable material purchasing is GM-C1: Likewise, no obvious relationship was energy models on the market; despite not being the also related to its green design initiatives. Similarly, detected between case C's green factory initiatives quickest of the three, the firm has used all three key its internal MOD and MIX facilitated quick and its supply chain flexibility (∅). technologies (EVs, fuel cell & PHEV), which was modification and efficient substitution with GM-C2: Case C had also successfully installed new enabled by its NEW (++). It also required strong sustainable materials/parts across different product technologies (e.g. new platforms) for process NET (++) to quickly find/switch to competent range (++). Case C's suppliers can largely satisfy its improvement. Its strong MOD facilitated smooth suppliers for the new models, which created some green purchasing requirements, enabled by its SUP and effective transitions (++). There were also challenges for the case firm. Existing suppliers (++). However, the firm in some cases needed to frequent small improvement initiatives, requiring provided necessary support, with SUP (+). find alternative suppliers, which requires its NET strong MOD for effective modification. Its suppliers GD-C2: Likewise, those simple, frequent, ongoing (+). could promptly cope with the changes, supported modification of existing models for environmental GP-C2: By contrast, case C had also set strong by its SUP (+). Lean practices were evident in the improvement in case C also required strong MOD standards and monitoring of its suppliers' firm, which required the support of flexible (++) and the support of internal MIX (+). The environmental performance. Its suppliers also had suppliers, i.e. SUP, especially for JIT/JIS supplies external SUP was also needed to cope with various high compliance rate, which was enabled by case C's (+). changes (+). strong SUP (++) and certain degree of fear of losing GM-C3: Case C's platform technologies and GD-C3: Any substantial changes for sustainability business with case C, supported by NET (+). modular strategy had improved its MIX, which had considerations also required case C to have strong GP-C3: Likewise, case C's new green supplier in turn led to improved production efficiency MOD and MIX (++). Case C sometimes also selection can be successfully done with the strong (++). 36 experienced difficulties in finding competent support of its NET (++), but was not as efficient as GM-C4: Case C strived to achieve high Cu and could external suppliers who can meet its requirements, Case A. largely achieve economies of scales in production, but with less extent compared to case B. GP-C4: It is also discovered that when case C had thereby reducing waste and improving large purchasing volumes, its green purchasing productivity. initiatives can be supported, either for the green GM-C5: Case C had also started recycling and reuse materials purchased or the environmental standards (e.g. refurbished engines). Despite only being on imposed onto the suppliers. The case firm could have trial stage, strong MOD were required to ensure greater influence onto its suppliers and easily request smooth adoption of these recycled parts in existing them to comply with their environmental production line (++). Besides, its MIX ensured that substandard (+) the refurbished engines can be installed in different models (+). External suppliers and logistics were also the key plays for the successful recycling and reuse effort, requiring strong SUP (++) and LOG (++). Note: ++ Strong Positive relationship: The studied flexibility reveals a very clear and direct positive effect on the success of the GO strategies adopted by the case firm. In other words, this flexibility is a critical enabler, without which the case firm cannot successfully adopt its GO strategies; + Positive relationship: The studied flexibility can positively support the GO strategies adopted by the case firm. However, it is not a critical enabler that the case firm must have in order to achieve the successful adoption of its GO strategies; ∅Unclear relationship: There is no obvious effect on between the studied flexibility and the GO strategies adopted by the case firm. International Journal of Production Economics 214 (2019) 30–43 Y. Liu, et al. International Journal of Production Economics 214 (2019) 30–43 Fig. 2. Effects of flexibility on green design. changes, in this case, electric vehicle (EV), plug-in hybrid vehicle changes and launch these models on the market. According to the plant (PHEV), etc. Through our cross-case analysis, we found that all three managers, without strong MOD, they cannot make efficient changes case firms’ GD efforts require the support of certain internal and ex- and modifications, and without strong MIX, they cannot produce these ternal SCF. For example, when substituting certain car parts with more mixed models with changes in a timely and efficiently manner. Case sustainable or recycled materials, all the case firms need strong MOD in company A for example, has created a system that allows any volume- place to quickly perform the changes without affecting production time production model to be equipped with any type of powertrains with no and incurring additional cost. The mix flexible manufacturers (case A additional engineering effort. Its MOD has since been greatly enhanced, and case C) can proactively make quick and significant alterations to as they can easily modify their existing models to equip various types of their product portfolios to launch different types of energy-efficient powertrains. Also, they have improved their MIX, as the new system can vehicles on the market without significant plant alternations or ex- enable the firm to efficiently share the same powertrain system in wider pansions. We analyze the case findings (see Table 4) and depict them in ranges. As such, case A has successfully developed a series of green Fig. 2 below. models ranging from conventional to EVs. Externally, although the As revealed in Fig. 2, when the three case firms only modify minor substantial changes do not occur as often as those minor ones, all the features of their existing models to improve energy efficiency and re- case firms need to maintain an adequate level of external SUP and NET. duce environmental impact in their GD projects, MOD plays a more This is because the suppliers still need to make flexible and fast re- important role than other flexibility dimensions. For example, company sponse to the buying firms’ requests, and if the existing suppliers cannot C made over 20 small modifications (e.g., aerodynamic body shapes, satisfy their requirements, alternative suppliers will be quickly sought side mirrors, and door handles) on one of its better selling models to after. lower fuel consumption. Because of case C's strong MOD, it ensured the Finally, our observation suggests that when the case firms make modifications were quickly and efficiently performed without affecting completely new offerings (e.g., EVs, PHEVs, etc.) on the market to its normal production. MIX is not strongly needed in this case, but if compete, NEW appears to play a more important role than other flex- these modifications are shared across different models, the case firms ibility dimensions, as is evidenced in all the projects (12 projects fo- will need the support of MIX as it can ensure compatibility and pro- cusing on green new designs were observed in our case studies). This is duction efficiency. Externally, the suppliers are constantly informed because, for instance, case A has a strong NEW (see Table 4), and when and communicated with any small changes. Although all the three case the firm focused on developing EVs to complement its combustion-en- firms have similar level of SUP (see Table 4), case A and C that have gine offerings, its strong NEW ensured a quick and effective design and relatively stronger SUP have experienced fewer problems when making launch. As note by one chief manager, “… we have a stronger design frequent and small modifications as their suppliers are more responsive team and the capability we have today has enabled us to come up new and capable to meet their various requirements. better designs at a much faster pace in order to occupy the market.” However, when the case firms make substantial changes in their However, in this particular industry, the design and launch of new products for environmental improvement, then both strong modifica- vehicles also requires the modification of vehicle structure and shapes, tion and mix flexibility are required in order to quickly perform the as well as creating an EV/PHEV product portfolio. Thus, both MOD and 37 Y. Liu, et al. International Journal of Production Economics 214 (2019) 30–43 MIX are also required to ensure a smooth introduction of the new series, firms was facilitated as they have strong MOD at their plants. Besides, it as explored in all three cases’ projects. Externally, existing suppliers was found that in all our case firms’ green material purchasing in- must provide necessary support for this initiative by making flexible itiatives, the stronger MIX the plants have, the wider product mix can adjustment according to the new requirements. However, as discovered be manufactured with more environmentally-friendly parts and mate- in the case firms, approximately over 90% of the time, these radical rials without affecting productivity and cost. In most cases, as the de- changes in design can lead to the selection of new suppliers for new gree of green product mix increases, the demand for sustainable ma- components. Case A that had a relative stronger NET than case B and C terials and components also surges. Therefore, MIX can also play a did not reveal any substantial problems in new supplier selection for significant role in green materials purchasing. However, MOD and MIX their new designs; whilst in the latter cases, especially case B did ex- did not present strong impacts on the other two types of GP initiatives, perience some delays and challenges in seeking new competent sup- i.e., supplier certification & monitoring, and green supplier selection. pliers. Unlike making modifications and altering the mix of existing product sets, the introduction of new green products encompasses intensive 4.2. GP and SCF changes to product configurations and characteristics. Yet, due to the current mark share and the production volumes of these new types of The GP initiatives adopted by the three case firms can be sum- vehicles, NEW did not reveal a clear association with any types of GP marized into three types, i.e., 1) purchasing sustainable materials and initiatives in our case firms. components, which is associated with the design of green products, 2) Turning to external SCF, as case firm A had a stronger SUP, it could supplier certification and monitoring, including setting environmental more easily request their suppliers to supply sustainable materials and requirements on existing suppliers (e.g., ISO14000 series certifications parts, and/or meet their environmental requirements than case B and C. and the case firms' own standards), as well as the associated training, The suppliers of case A could efficiently accommodate these specific auditing, and monitoring, and 3) green suppliers selection, i.e., evalu- requests and provide timely supplies to case A's plants. By contrast, ating and establishing new partnerships with potential suppliers who Case B and C's GP initiatives was not as successful as case A's. They can meet the case firm's green requirements. According to these three could also request their suppliers to meet their environmental standards types of GP initiatives, we summarize our cross-case findings in Fig. 3 (type 2) and supply green materials (type 1), but it was less efficient below. than case A due to their relatively weaker SUP. Therefore, our ob- Regarding type 1 green purchasing, all the projects (15 observed in servations suggest that a strong SUP can facilitate both type 1 and type our case studies) required strong MOD at their plants to modify their 2 GP initiatives. existing products with more sustainable materials and components in In addition, as noted by one purchasing manager, “[the existing an efficient and cost-effective manner. For instance, case A had suc- suppliers] they can satisfy our changing requests, because either they cessfully substituted the bumpers across many existing models with have strong ties with us or they do not want to lose the businesses with 100% recycled plastics, which was supported by its strong MOD. us”. His point offers useful insights and coincides with our findings that, Similar associations were discovered in case B and case C, for example GP can also be facilitated by NET. When it comes to type 1 and type when they tried to adopt carbon fiber materials, recycled metal and 2 GP, a lot of the existing tier-1 suppliers could sense the pressure of plastics. As a result, type 1 green purchasing initiative in the three case potentially losing their contracts with the case firms and thus strived to Fig. 3. Effects of flexibility on green purchasing. 38 Y. Liu, et al. International Journal of Production Economics 214 (2019) 30–43 Fig. 4. Effects of flexibility on green manufacturing. follow the various environmental standards imposed by the buying On the other hand, large purchasing volume also means greater bar- firms. Although the case firms do not usually use their NET as a weapon gaining power and influence over suppliers. Therefore, the case firms to ‘threat’ their suppliers, a stronger NET signifies a greater choice of can impose stronger environmental requirements on their suppliers available suppliers for the buying firms. Therefore, a strong NET, to (regardless of new or existing ones) to meet their sustainable objectives, certain extent, can also contribute to type 1 and type 2 GP. facilitating both type 2 and 3 GP initiatives. Our observations also reveal that, in our case firms however, if the existing suppliers could not supply the requested green parts/compo- 4.3. GM and SCF nents or failed to comply with the environmental requirements, the automakers had to look for alternative new suppliers, i.e., type 3 GP. It The three case firms have implemented a variety of GM initiatives to subsequently required the case firms to have strong NET in place, with target their environmental problems at plants. These initiatives can be which they can deal with the inflexible suppliers or swiftly change to broadly classified into three major categories based on their strategic alternative suppliers without incurring extra cost and delays. Case A orientations (Hsu et al., 2016), i.e., 1) building green factories, in- and C for example, encountered no major problems for their green cluding for example using renewable energies and LED lighting, col- supplier selection, as they were located in highly-clustered industrial lecting rain water, and isolating factory noise, 2) production process zones where there were many available environmentally-qualified improvement, including for example process optimization for quality, suppliers. However, case B was located relatively far away from these productivity, and efficiency improvement as well as pollution preven- industrial clusters, bestowing it with less NET. The firm had thus en- tion and control technologies for hazardous waste, water pollution and countered some delays in sourcing some key components for its newly greenhouse gas emission reduction and elimination, and 3) resource developed hybrid models, as they could not find competent suppliers conversation through reuse, recycling, refurbishing and re- locally who can make the requested components. “… it is really painful manufacturing initiatives. The managers often described these in- when you don't have many choices [enough NET] … and it costs!”, said itiatives as “reverse logistics” or “closed-loop” supply chains, in which one purchasing manager. the end-of-life products/parts are taken back to the production system. Worth mentioning, with regard to volume flexibility (VOL), we in- When the case firms’ GM orientation is towards building green itially anticipated that frequent volume variations in production may factories, we found no obvious links between SCF and their green fac- affect supply stability and thus, affecting the efficiency of GP and tory initiatives (22 such initiatives have been identified in our case partnership with external suppliers and logistics providers (Sezen, studies). These initiatives are typically one-off projects and focus 2008). Nevertheless, we did not find strong evidence on frequent large mainly on factory buildings and facilities, which do not directly relate volume changes for the models produced in our case firms. Although to production activities. For example, replacing with LED lights and there were monthly, weekly, and daily volume variations, as one installing solar panels to save energy did not reveal a clear association manager put it, “the flexibility we have can enable us to cope with these with either internal flexibility or any external ones. However, if the changes”. As revealed in the cases, the only possible association be- orientation is towards production process improvement or resource tween VOL and GP was when the case firms had significantly increased conversation, possible associations are revealed as depicted in Fig. 4. their production volume with sustainable parts and components, First, with regard to production process improvement, our ob- reaching economies of scale in production. As a result, the case firms servations suggest that strong MOD is required to cope with the changes had to buy more sustainable materials and parts, facilitating type 1 GP. in production process and new technologies. This association was 39 Y. Liu, et al. International Journal of Production Economics 214 (2019) 30–43 detected in all the process improvement projects discovered in our case production efficiency and minimizing waste for example, external firms. For example, case A had successfully installed an automatic serial suppliers would need to make prompt and flexible production and de- production line in its stamp shop to improve production efficiency, liveries to support the buying plants' operations. As one manager said, reduce energy consumption, and insulate noise. The firm's strong MOD “… we certainly need their support to achieve our goals [process im- ensured that the product models were fully integrated and compatible provement]”, “… if they are not as flexible as we are; it will be very with the new production line, and the transition did not result in major difficult [towards process improvement]”. Thus, SUP can also provide interruptions to its production. Similarly, in cases B and C, the newly support for certain production process improvement at our case firm's upgraded paint shop had significantly reduced water consumption and plants. VOCs as well as chemical and energy usage. The modification and Next, when a firm's GM effort is orientated towards resource con- changes in the whole painting process were also facilitated by internal servation, the story is a little different. Similar to process improvement, MOD in these factories to ensure a smooth transition. findings in all our case firms suggest that strong MOD are required at In addition to the “big-step” process improvement, the continuous, the plants in order to effectively modify the existing product features to small, and gradual improvement, and especially the lean paradigm equip with the refurbished and remanufactured parts/components (e.g., advocated in the automotive industry also require the case firms to have engines and water pumps). Over 90 percent of these resource con- strong MOD to make frequent and swift modifications/changes at servation efforts in our case firms were not for a single model but were plants. As quoted from one production manager, “no matter big or small shared across different product ranges, supported by the case firms' [process improvement], we got to have the flexibility in place to make MIX. Besides, in the three case firms' recycling and reuse initiatives, the quick changes without affecting our daily production”, and “it's a very recycled parts/materials would go to their suppliers first, where they important factor for making successful improvement in our factory”, got recovered before being reused in car assembly. Our observations said another. reveal that these initiatives in all our case firms would require strong The advantage of MIX is its capability to create a wide range of support from the suppliers and the logistics providers as there are high product choices to satisfy various customer demands. Intuitively, we complexity and uncertainty in product returns. The case firms, their anticipated that a wider product mix would tend to lower the efficiency suppliers, and logistics providers had to work very closely to deal with of production, especially when a large number of discrete products are the recycling initiatives more effectively. For example, case A's recycled manufactured. Yet, the findings in the three case firms suggest the bumper plastics program required not only strong internal MOD, but opposite. The prevalence of platform technology and modularization also the effective coordination from external suppliers, recyclers, and strategies in this specific sector bestows the automakers strong MIX. All logistics providers. These external partners need to be flexible enough the three case firms were able to flexibly produce a number of different to cope with these uncertainties in recycling and make timely produc- models using the same platforms at their plants. As a result, greater tion and delivery to the case firm. “Recycling, remanufacturing, and production efficiency can be achieved. It was found in our case ob- refurbishing are getting more and more important in this sector, but servations that the more MIX the case firms had the more production would require strong collaboration both internally and externally, efficiency and lowered unit cost can be achieved when producing a especially with industrial partners …” said one plant manager. “… you large mix of models within their factories. Case A for instance, has tried can't do much without the support of our suppliers and logistics part- to improve its production process by adopting a modular transverse ners; it's not just about yourself being flexible, it is about the whole matrix, which has enabled the company to integrate all the relevant network that functions together …” said another logistics manager. drive systems to one model series – from conventional to EVs, thus Lastly, we found no str