Lesson 4 PDF - Print Finishing, Folding & Cutting
Document Details
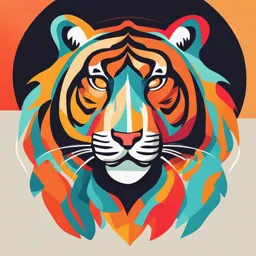
Uploaded by EyeCatchingCynicalRealism8205
Imam Abdulrahman Bin Faisal University
Tags
Summary
This document details different print finishing techniques, including lamination, varnishing, foil stamping, embossing, and metallic inks, along with explanations and examples of their usage in printing. The document also touches on different ways to add additional effects to printed material, such as pasting and drilling.
Full Transcript
FINISHING, FOLDING, AND CUTTING. 1.0 Finishing Production Finishing 1.1 Finishing Production About print finishing Print finishing, as its name suggests, is th...
FINISHING, FOLDING, AND CUTTING. 1.0 Finishing Production Finishing 1.1 Finishing Production About print finishing Print finishing, as its name suggests, is the process that occurs after printing to finish the production of the graphic print product. It includes the finalization, fastening and/or decoration of the printed material. Although it is the last phase in graphic production, finishing should be taken into account from the very beginning of the design process. The budget and timeline are key factors that may lead to one finish being chosen over another. 1.2 Finishing Production Lamination A plastic coating can provide printed material with good protection from friction, dirt and moisture, but it can also be applied for aesthetic reasons. Mostly used on covers, folders and restaurant menus. 1.3 Finishing Production Varnish A varnish is a colorless ink applied to printed material to provide mild protection (smudging, finger marks) or a particular aesthetic effect. Varnish can be applied to the whole document, or just to a specific area, in which case it is known as ‘spot varnishing’. The varnish is applied after the printing process, but before the cutting and binding of sheets (so production and drying times can be increased). Common types of varnish include; Machine: used to coat or seal the ink Gloss: gives the document a shiny coating Matt: gives a smooth quality finish and has the benefit of not reflecting the light Stain/Silk: somewhere in between gloss and matt UV (Next slide) 1.4 Finishing Production Spot UV Varnish Lamination involves covering the paper with a thin plastic protective layer, and UV varnish achieves a similar result. Unlike lamination, UV varnish breaks or cracks when it is cut with a guillotine cutter, folded, scored or die-cut. However, UV varnish can be printed onto specific sections of the page to enhance an image, photograph, text, or logo. UV varnishes come in gloss, matt, glitter, tints, and an array of other finishes. 1.5 Finishing Production Foil Stamping Foiling is one of the most popular finishing techniques, where a metallic foil is applied with pressure to the stock using heated metal die and a hot foiling stamping machine. The finished effect creates a smooth and highly reflective surface, although matt foils are available as well. Foil stamping works brilliantly in combination with embossing, creating a three-dimensional, gleaming piece of print. Foil blocking can also be used add an extra layer of security to documents, for example, to guarantee authenticity on tickets or certificates. 1.6 Finishing Production Embossing & Debossing Embossing and debossing are similar finishes, where the surface is either raised or pressed into the page. This process brings a three-dimensional appeal to printed items, and works really well on business cards and cover pages. This process works very well in combination with another finish, such as foil stamping. Blind Embossing 1.8 Finishing Production Metallic Inks These inks contain metallic components that give them a reflective quality and bright finish. Metallic inks are less lustrous than foil stamping, so if you’re looking for a highly reflective and striking finish, foils are more appropriate, whereas metallic inks provide a more subtle finish. 1.9 Finishing Production Pasting Two or more substrates can be pasted together and used as a single substrate. The resulting substrate is heavier (its weight is the sum of the weights of the pasted substrates) and may have different properties on each side if composed of two substrates with different characteristics. Not all substrates can he pasted together. Depending on a substrate's characteristics, it may reject the paste, leading to a bad result. The designer should ask the printer whether the desired materials are suitable for pasting to each other. 1.10 Finishing Production Thermography In thermography (sometimes called poor man's engraving), raised images are created by applying thermograph's powders over a special type of screen-printing ink while the ink is still wet. After the excess powder is removed by a vacuum unit, the substrate is heated and the powder-and-ink mixture rises and solidifies. Thermography cannot be applied to both side of the page and materials featuring this effect cannot be folded. If it is applied uniformly over a large, smooth surface, hickeys and bubbles usually appear. Thermography is a printing special effect that raises the ink in a ‘brail like’ effect and is used for a high quality and creative finish. Typically thermographic printing is used for printing high quality formal invitations and business cards. 1.11 Finishing Production How should The finish should be properly specified in the quote. a special The printer should specify how the finish should be indicated in the original file (this is generally done using a finish be separate layer or color). requested? The desired finish should be clearly indicated in the purchase order and, following the printer's instructions, this information should be reiterated when the prepared file is submitted. 2.0 Folding Production Folding 2.1 Folding Production About folding Folding is one of the most frequent finishing operations. A product printed on a machine that includes a folding unit (a web-fed offset press, certain digital printing machines, etc.) is already folded when it comes off the press. However, a product printed on a flatbed sheet-fed machine or a web-fed system that does not have a folding or binding unit must be folded by a folding machine. Some products simply need to be folded, whereas others are folded in preparation for binding. In either case, it is important to take the grain direction into account, especially if the substrate is paper. It is easier to fold paper along the grain than against it, although it is some-times better to fold against the grain in order to avoid excessive elasticity. 2.2 Folding Production Gatefold Double Gatefold Most Common Types of Fold Accordion or Z-folds Cross Fold or French Fold 2.3 Folding Production Folding Machines Folding is done on machines that work at very high speeds (up to 10,000 sheets per hour) and have numerous features and possibilities, as well as certain limitations. Not all types of fold are possible. The designer should always ask the printer about the feasibility of any unusual type of fold. The two basic types of folding machine are Buckle folder Knife folder The sheet is guided between two metal A knife presses the paper into the slot plates. When it hits the stop gauge, it between the two revolving rollers that rebounds, buckling slightly; two revolving complete the operation rollers grab the buckle and pull it downwards, creating a fold. In general knife folders are used for heavier stocks, while buckle folders are used for lighter paper types. 2.3 Folding Production Folding Machines Buckle folder Knife folder 2.4 Folding Production Bi-fold brochure. Contrary to what the name Most Common suggests, this type of publication is folded just once, creating two panels. It is a very common brochure format. Fold-out Tri-fold brochure. These products are actually folded just twice (either letter fold or accordion fold), creating three panels. This format is also very common for brochures. For the brochure to close properly, the end panel that will be folded inside must be slightly narrower than the cover panel (by about 2 mm). 2.4 Folding Production Most Common Quad-fold brochure. This type of publication is folded three times (letter, accordion or gatefold), creating four panels. As with the tri-fold brochure, Fold-out not all of the panels have the same width; the ones folded inside are usually about 2 mm narrower than the outside ones. Roll-fold brochure. Products that have more than four panels are called fold-outs or roll-fold brochures. It is very important to ask the printer about the feasibility of this type of product. 2.5 Folding Production Alignment When a graphic element spans both pages in a two-page spread, it may not match up properly where the two pages - each printed separately - meet at the gutter. In such cases, perfect registration cannot be guaranteed in terms of either alignment or color. In any given signature, only the center spread is free of this problem and can achieve exact registration. The designers should take this phenomenon into account and avoid placing elements requiring perfect alignment on two-page spreads other than the center spread. 2.6 Folding Production Creep Creep When a signature is cross-folded, the middle pages, protrude outward slightly farther than the outer pages. This results in smaller margins on the middle pages after trimming. The number of folds and the thickness and weight of the paper determine how noticeable the creeping will be. Designers should take creep into account and avoid placing elements too close to the trimming margin. 2.7 Folding Production Scoring A score is a crease applied to a sheet of paper using a bone folder to make it easier to fold and protect the paper from inadvertent creasing, tearing or stretching. Scoring is necessary for paper with a weight greater than 150-170 g, especially if it has to be folded against the grain. 3.0 Cutting Production Cutting 3.1 Cutting Production About Cutting During finishing, most printed products are cut in some way to ensure that all the printed sheets have regular edges and that all the items are the same size. Some products are cut several times. For example, paper may first be cut to the size of the printing machine, be cut again after Printing to the size of the finishing machines and be cut once more as a finished product. Due to possible misalignments in the cutting process, a bleed and safety margin should always be left during the design and prepress processes. The designer should take these misalignments into account when designing a product that requires some sort of cutting (die-cutting, perforation, drilling, etc.) and avoid graphics that need to be perfectly aligned with a cut made during finishing. 3.2 Cutting Production Guillotine cutter The guillotine cutter is a device used to cut paper. It consists of a bed where the paper to be cut is piled, movable gauges that hold the back of the pile in the correct position, a clamp that exerts pressure and immobilizes the pile before cutting it with a sharp knife. Today's guillotine cutters have sophisticated photoelectric safety systems designed to prevent accidents in the workplace. The most modern models can be connected to a computer and receive instructions from workflow software. Three-knife trimmers, which cut the head, fore edge and tail of a book simultaneously, are used in bookbinding 3.3 Cutting Production Die-cutting This technique can be used to cut an irregular shape or to create an opening, perforation, score, etc. When designing a die-cut product, it is important not to place openings too close to the edges or to create very thin fragments that can tear easily. There are various die-cutting techniques, as well as techniques that achieve the same effects without a die: 1. With a die Die-cutting usually involves using steel blades mounted on a die in a particular pattern to cut an irregular shape. In addition to cutting blades, the die can also have perforation and scoring blades. Die-cutting can also be done using acid-etched plates. Because an acid-etched die is based on a photographic image, it can reproduce the original design with great precision. 3.4 Cutting Production Die-cutting 2. Without a die Another system is laser cutting, which does not require a steel or acid-etched die. Laser cutting can be used on almost any type of substrate (paper, plastic, leather, metal, fiberglass, etc.), but when used with certain materials it can cause burns, leading to an undesirable result. This technique is usually re-served for jobs that require a high degree of precision. A cutting plotter uses its blade to create die-cutting effects by following lines drawn with vector-graphics software. 3.5 Cutting Production Perforation Perforation is a cutting operation that creates a series of slits or holes in a substrate to weaken it and allow it to be cut more easily. Perforation blades are usually used to cut straight lines, but if they are coupled to a steel die, they can also be used to create irregular shapes. A perforation consists of two elements: ties (the uncut parts of the material that remain intact) and cuts. Depending on the intended use and the type of material, the size of the ties and cuts can be adjusted in order to increase or decrease the strength of the perforation. Perforation with less than 1 mm between cuts is called microperforation. Cut Tie 3.6 Cutting Production Drilling This operation is used to make one or more holes in the substrate. Drilling is usually done to allow sheets of paper to be inserted in a ring binder. In addition to making holes for ring binders, drilling can also be used to make holes in any location and of any size (minimum diameter 2 mm) in labels, sample books or other products. Holes can be made using paper drilling machines or steel dies. 3.7 Cutting Production Incisions Incisions or half cuts tend to be used on adhesive papers, With the cutting blade cutting the adhesive but not the protective base. A cutting plotter can also be used to make incisions by adjusting the pressure and blade height so that it Cuts the vinyl decal, for example, but not the plastic sheet beneath it. 1.11 Finishing Production How should The operation should be properly specified in the quote. a die-cutting, The print technician should specify how the operation perforation, should be indicated in the original file (this is generally drilling or done using a separate layer or color). incision The desired operation should be clearly indicated in the purchase order and, following the printer's instructions, operation be this information should be reiterated when the prepared file is submitted. requested?