Engineering Design and Material Selection Lecture 10 PDF
Document Details
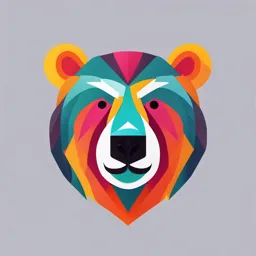
Uploaded by FervidDune
ETH Zurich
Prof. Dr. Kristina Shea, Dr. Tino Stankovic
Tags
Summary
This lecture covers materials and their properties in engineering design. It discusses material categorization, mechanical behavior, stress and strain, and material deformation. A case study on ski design is included to illustrate the concepts.
Full Transcript
ENGINEERING DESIGN AND COMPUTING Engineering Design and Material Selection Lecture 10 — Materials and their Properties Prof. Dr. Kristina Shea Dr. Tino S...
ENGINEERING DESIGN AND COMPUTING Engineering Design and Material Selection Lecture 10 — Materials and their Properties Prof. Dr. Kristina Shea Dr. Tino Stankovic Prof. Kristina Shea 1 ENGINEERING DESIGN AND COMPUTING Course Schedule Week/ Topic Case study Quiz Lecturer Dates 1 Introduction and Sketching 2 Introducing Engineering Design Health Prof. Dr. Kristina Shea 3 Technical Drawing: Projections and Cuts 4 CAD: Introduction and Modeling Operations 5 CAD: Features and Parametric Modeling Future Mobility 6 CAD: Freeform Modeling Dr. Tino Stankovic 7 CAD: Assemblies and Standard Mechanical Parts X (45 min) 8 Technical Drawing: Dimensioning Health 9 Sustainability in Engineering Design 10 Materials and their Properties 11 Manufacturing Processes with Focus on Additive Manufacturing Sustainable Materials Prof. Dr. Kristina Shea 12 Material Selection 13 Review and Q+A X (75 min) Prof. Kristina Shea Engineering Design + Computing Laboratory 2 ENGINEERING DESIGN AND COMPUTING Learning Objectives § Learn a categorization of materials into material families and understand their general mechanical behavior § Learn the definition of stress and strain and express their relation via simple material laws § Learn different material deformation behavior focusing on bending and how to express it mathematically Prof. Kristina Shea Engineering Design + Computing Laboratory 3 ENGINEERING DESIGN AND COMPUTING Case Study: Ski Design Function: Force transmission from the human body to the ski for controlling the ski motion. Requirements : § Withstand environment forces § Bend at level desired by skier § Provide torsional resistance § Reduce vibration § Turn easily § Resist environment temperatures and wear Ski design is a compromise of design variables to match the skiers' weight, technique and use. Prof. Kristina Shea Engineering Design + Computing Laboratory 4 ENGINEERING DESIGN AND COMPUTING Case Study: Ski Design Source: https://www.jans.com/alpine-ski-anatomy (20.06.2022) Prof. Kristina Shea Engineering Design + Computing Laboratory 5 ENGINEERING DESIGN AND COMPUTING Overview – Design Dependencies Function: A task of a product or system independent of solutions. Shape Dependencies: Fulfilling a function requires a certain shape (part size, features, …) Function Prof. Kristina Shea Engineering Design + Computing Laboratory 6 ENGINEERING DESIGN AND COMPUTING Overview – Design Dependencies Function: A task of a product or system independent of solutions. Dependencies: Shape Fulfilling a function requires a certain shape (part size, features, …) Functions require specific material properties (e.g., material elasticity and thermal properties) The material choice and the target shape interact with Function manufacturing process since each process has a range of manufacturable geometries and processable materials. Material Process The manufacturing process influences the designs' function by changing the part properties Prof. Kristina Shea Engineering Design + Computing Laboratory 7 ENGINEERING DESIGN AND COMPUTING History: Material shapes technology Ashby, 2011 Prof. Kristina Shea Engineering Design + Computing Laboratory 8 ENGINEERING DESIGN AND COMPUTING History: Material technology What will come next? Trend: § Closer interaction of shape, material, process and function in engineering design § Multi-material, integrated designs § Highly complex design “Floating Steel” “Artificial Tree” “Multi-Material Designs” spaces and computational Tuning material Active material 3D printing varying material design approaches needed properties by turning CO2 and properties to tune mechanical including AI shape, e.g. steel water into energy strength foam Left and Middle Source: Milano Design Week – Material Shapes the Ages (https://ethz.ch/en/the-eth-zurich/global/events/2022/eth-zurich-material-shaps-the-ages-media-kit.html) Prof. Kristina Shea Engineering Design + Computing Laboratory 9 ENGINEERING DESIGN AND COMPUTING Vast choice of material Prof. Kristina Shea Engineering Design + Computing Laboratory 10 ENGINEERING DESIGN AND COMPUTING Material Families § ABS (Acrylonitrile- Butadiene-Styrene) § Steel § Polyesters (e.g. PET) § Aluminum Metal Polymer § Silicone § Cast iron § Alloys, e.g. aluminum and § Carbon fiber titanium Hybrid § Fiberglass § Natural materials, e.g. wood, flax, and basalt § Soda-lime glass Glass Ceramic § Alumina § Borosilicate glass (Pyrex) § Silicon carbide § Silica glass § Boron carbide Prof. Kristina Shea Engineering Design + Computing Laboratory 11 ENGINEERING DESIGN AND COMPUTING Material Families Ceramics and glass are brittle. Metals can bend. Polymers are lightweight. Metal Polymer Hybrid Engineers need a common language to select materials! Glass Ceramic Prof. Kristina Shea Engineering Design + Computing Laboratory 12 ENGINEERING DESIGN AND COMPUTING Material Families Polymers: Low stiffness, Metals : Stiff and but strong strong, but can be Metal Polymer heavy and inexpensive (steel) or light but expensive (titanium) Hybrid: Combine the attractive properties of Hybrid other material families while avoiding drawbacks Glasses: Hard and brittle Glass Ceramic Ceramics: High stiffness, but brittle Prof. Kristina Shea Engineering Design + Computing Laboratory 13 ENGINEERING Post-industrial DESIGN Non- renewable AND Recycling COMPUTING resources Life Cycles and Renewable Materials Manufacturing Resources Resources Remanufacturing Materials Post- consumer Natural Recycling Industrial “Biological” “Product” Natural Life Cycle Life Cycle Transport Decay Toxics Recovery Reuse Organics Inorganics Deposit Use § Organic materials – renewable, biodegradable substances originating from living organisms, capable of reintegration into the biological life cycle through natural decay, e.g., wood, cellulose, and cork. § Inorganic materials – non-renewable, non-biodegradable substances derived primarily from geological sources, often requiring recycling, remanufacturing, reuse, e.g., metals, glass, and ceramic § Toxics - harmful substances that pose risks to living organisms or ecosystems and require specialized handling, containment, or detoxification to prevent contamination and harm during recovery or disposal, e.g., asbestos, heavy metals, and hazardous chemicals. Prof. Kristina Shea Engineering Design + Computing Laboratory 14 ENGINEERING DESIGN AND COMPUTING Question: You are designing a diving board for a swimming pool. Which material would you select? § A. Wood § B. Steel § C. Fiberglass § D. Glass Prof. Kristina Shea Engineering Design + Computing Laboratory 15 ENGINEERING DESIGN AND COMPUTING Material Data Sheet: Stainless Steel Data taken from CES EduPack Prof. Kristina Shea Engineering Design + Computing Laboratory 16 ENGINEERING DESIGN AND COMPUTING Categories of Material Properties Mechanical Thermal Electrical Optical Magnetic Chemical Economical Ecological Material properties are attributes given to a material and are evaluated by measurements or calculations. They are ONLY a guideline and a snapshot in time. This means that… … the material properties can vary inside a range due to variations in the material structure. … the material properties can change due to novel technology. Prof. Kristina Shea Engineering Design + Computing Laboratory 17 ENGINEERING DESIGN AND COMPUTING Categories of Material Properties Material resistant to wear è Longer lifetime è Potentially more expensive Sustainable Design Mechanical Thermal Electrical Optical Magnetic Chemical Economical Ecological Not conductive Material recyclable è no need for insulation è Less material waste è less material è Potentially lower cost Prof. Kristina Shea Engineering Design + Computing Laboratory 18 ENGINEERING DESIGN AND COMPUTING Sustainability properties (Granta EduPack Eco-Audit) Factors to Consider: Material: Stainless Steel Data taken from CES EduPack § Recyclability § Biodegradability § CO2 footprint (processing and recycling) § Water Usage § Energy Consumption § … Prof. Kristina Shea Engineering Design + Computing Laboratory 19 ENGINEERING DESIGN AND COMPUTING Mechanical Properties Mechanical Thermal Electrical Optical Magnetic Chemical Economical Ecological § Mechanical integrity is the basis for designing a product § No design can be successful if the structure fails § Mechanical properties quantify the mechanical behavior of the material è Design target mechanical behavior è Calculate safety against failure Prof. Kristina Shea Engineering Design + Computing Laboratory 20 ENGINEERING DESIGN AND COMPUTING Mechanical Properties The link between forces and deformation in a body Geometry Behavior Forces acting on the design Induced deformations Material Prof. Kristina Shea Engineering Design + Computing Laboratory 21 ENGINEERING DESIGN AND COMPUTING Material Properties Must be independent of geometry For example, the same forces result in different behavior of two different shapes: è A ski (shape 1) deforms more than a snowboard (shape 2) è Material properties need to be defined to be universally applicable to different shapes Prof. Kristina Shea Engineering Design + Computing Laboratory 22 ENGINEERING DESIGN AND COMPUTING Stress and Strain Stress Strain Force [N] 𝜎# Area [m2] ΔL [m] L0 [m] 𝜎" 𝜎! 𝐹 𝜎= ∆𝐿 𝐴 𝜀= Typically expressed at each “material point”. 𝐿! Unit [SI]: N/m2 Unit [SI]: m/m or % Often expressed in MPa (=1 N/mm2) Stress is the force per unit area. Strain is the deformation of a material relative to the initial configuration. Prof. Kristina Shea Engineering Design + Computing Laboratory 23 ENGINEERING DESIGN AND COMPUTING Key formulas On Moodle Stress Strain Force [N] 𝜎# Area [m2] ΔL [m] L0 [m] 𝜎" 𝜎! 𝐹 𝜎= ∆𝐿 𝐴 𝜀= Typically expressed at each “material point”. 𝐿! Unit [SI]: N/m2 Unit [SI]: m/m or % Often expressed in MPa (=1 N/mm2) Stress is the force per unit area. Strain is the deformation of a material relative to the initial configuration. Prof. Kristina Shea Engineering Design + Computing Laboratory 24 ENGINEERING DESIGN AND COMPUTING Material Testing: Determine the Stress-Strain Curves Sample Test Material Measurement Preparation Setup Model Plastic region Stress [MPa] Linear, elastic region Test sample with Sample is clamped in Stress and strain are calculated Complex curve is standard dimensions a testing machine and from force and displacement approximated by a (‘dogbone’) is 3D- pulled with a constant measurements and the sample material model printed rate. geometry. Prof. Kristina Shea Engineering Design + Computing Laboratory 25 ENGINEERING DESIGN AND COMPUTING Hooke’s Law: Linear elastic material The simplest material model is a constant relation between stress and strain, this is called the Hooke’s law. Stress [MPa] 𝐸 𝜎=𝐸𝜀 The Young’s Modulus or Elastic Modulus 𝐸 is a constant proportional 𝜎 Linear, elastic region factor relating the stress and strain. It is (approximated) typically given in GPa. è Pay attention to the unit conversion! 𝜀 Robert Hooke (1635-1702) The magnitude of 𝐸 provides the material stiffness. The higher 𝐸 , the Wikipedia: 22.06.2022 stiffer the material. Prof. Kristina Shea Engineering Design + Computing Laboratory 26 ENGINEERING DESIGN AND COMPUTING Hooke’s Law: Spring Analogy 1D - Spring 3D - Solid Equivalence: 𝐹: Force [N] 𝐹 Formula: 𝜎 = 𝐸𝜀 =𝜎 𝐿: Total Length [mm] 𝐴 𝐿 0: Initial Length [mm] 𝐹 Δ𝐿 Δ𝐿 Substitute: =𝐸 Δ𝐿: Elongation [mm] =𝜀 𝐴 𝐿+ 𝑘: Spring constant [N/mm] 𝐿! 𝐸𝐴 𝐹 = 𝑘Δ𝐿 Reformulate: 𝐹= Δ𝐿 𝐿+ Prof. Kristina Shea Engineering Design + Computing Laboratory 27 ENGINEERING DESIGN AND COMPUTING Hooke’s Law: Spring Analogy Spring ó Solid 1D - Spring 𝐹 , 𝜎 (Force [N]) 𝜎= (Stress [MPa]) 3D - Solid - Δ𝐿./ 𝜀 (Elongation [mm]) 𝜀= (Strain [mm/mm]) /" 𝐹 = 𝑘Δ𝐿 - 𝜎 = 𝐸𝜀 𝑘 𝐸 2- (Young’s modulus (Spring constant 𝑘01 = [N/mm]) /" [MPa]) Prof. Kristina Shea Engineering Design + Computing Laboratory 28 ENGINEERING DESIGN AND COMPUTING Question: A material test sample is pulled with an axial force (F ) and results in the stress-strain curve shown. Which statement is FALSE? § A. The deformation between (1) and (2) can be approximated as linear elastic. 3 § B. The Young’s modulus, E, can be approximated from the slope of the curve between (1) and (2). 2 § C. The Young’s modulus, E, can be 1 approximated from the slope of the curve between (1) and (3). Prof. Kristina Shea Engineering Design + Computing Laboratory 30 ENGINEERING DESIGN AND COMPUTING Bending and Torsion: Concepts Bending Simultaneous compression and tension of material Torsion Relative motion of «material layers» Prof. Kristina Shea Engineering Design + Computing Laboratory 31 ENGINEERING DESIGN AND COMPUTING 3-Point Bending Test The flexural rigidity of a beam depends on the cross- section and Young’s modulus of the material. The 3- point bending test, also know as the flexural test, measures a test that combines both: the bending stiffness: 𝐸×𝐼 Bending is a deformation of a slender beam, where the material experiences a compressive load on the concave side and tensile loads on the convex side. + ,! Formula: 𝛿= -. / 0 Bending Stiffness / Flexural rigidity Prof. Kristina Shea Engineering Design + Computing Laboratory 32 ENGINEERING DESIGN AND COMPUTING Bending: Second moment of area The second moment of area , noted 𝐼, is a geometrical property that reflects the material distribution in the cross-section. This parameter is needed for bending calculations. Cross-section Rectangular Circular F Neutral axis 𝑤ℎ " 𝜋𝑅 # 𝐼: Second moment of area [mm ]4 𝐼= 𝐼= 12 4 Prof. Kristina Shea Engineering Design + Computing Laboratory 34 ENGINEERING DESIGN AND COMPUTING Bending Stiffness Distribution Along a Ski Race / Carving Skis Touring Skis Bending stiffness = EI Source: https://soothski.com/technology-measure-ski-properties/ Prof. Kristina Shea 35 ENGINEERING DESIGN AND COMPUTING Case Study: Ski Bending Assumption 1: Problem A ski can be modelled as a beam with a To design a ski, the skis bending constant cross-section along its length. deformation is the first main design parameter to consider. L = 1600mm Goal: Find the center deflection of the ski. w Given: h Load case (center load) w = 110mm Supports at contact points of ski h = 12.5mm Ski geometry Material properties Assumption 2: The material is uniform along the length with a Young’s Modulus of 30 GPa. Prof. Kristina Shea Engineering Design + Computing Laboratory 36 ENGINEERING DESIGN AND COMPUTING Case Study: Ski Bending Load Case Load Case: 800N -Bending -Load: Body weight è ~800N -Load Location: Midpoint Contact Contact Deflection at midpoint: Point Point $ &! 𝛿= #' ( ) Free-body Diagram: 𝛿: Deflection at midpoint (mm) 800N 𝐹: Force at midpoint (N) 𝐿: Length (mm) 𝐸: Young’ Modulus (MPa) 1600mm 𝐼: 2nd moment of area (mm4) 400N 400N Prof. Kristina Shea Engineering Design + Computing Laboratory 37 ENGINEERING DESIGN AND COMPUTING Case Study: Ski Bending Step 1 Step 2 Calculate 𝐼 (for a rectangular cross-section) Calculate 𝛿 𝑤ℎ " 𝐹 𝐿" 𝐼= 𝛿= 12 48 𝐸 𝐼 110mm ? (12.5mm)" 800𝑁 ? (1600mm)" 𝐼= 𝛿= 12 48 ? 30 ? 10" MPa ? 1.79 ? 10# mm# 𝐼 = 1.79 ? 10# mm# 𝛿 = 127mm è Pay attention to the unit conversion! (GPa / MPa here) Solution: 𝛿 Ski center deflects by 127mm relative to the two contact points (supports). Prof. Kristina Shea Engineering Design + Computing Laboratory 38 ENGINEERING DESIGN AND COMPUTING Material and their Properties – Wrap Up Materials are categorized into material families Material properties quantify the behavior and attributes of a material independent of shape Material properties also relate to sustainable design Stress and strain describe the loads and deformations in a material at every material point Stress and strain are related by the material property Young’s modulus, through a simplified material law, Hooke’s law Bending is a combination of tensile and compressive stresses in a beam Prof. Kristina Shea Engineering Design + Computing Laboratory 40 ENGINEERING DESIGN AND COMPUTING Reference For Block 3 the following book may be consulted for further information and explanation. It is free to download within the ETH domain. M.F. Ashby, Materials Selection in Mechanical Design, Elsevier, Fourth Edition, 2011. https://www.sciencedirect.com/book/9781856176637/materials-selection-in-mechanical-design Supplementary reading for Lecture 10: Chapters 1-3 Prof. Kristina Shea Engineering Design + Computing Laboratory 41 ENGINEERING DESIGN AND COMPUTING Exercise 9: Materials and their properties Can you find the Young’s modulus of a sample using a flexural tester? Samples to measure Screw gauge Prof. Kristina Shea Engineering Design + Computing Laboratory 42