LEEA – Lifting Accessories Diploma (LAC) Global - Workbook PDF
Document Details
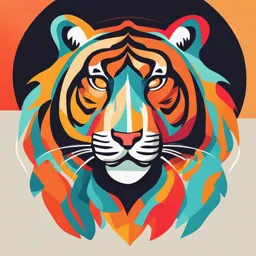
Uploaded by DazzlingIndigo
null
2022
LEEA
Tags
Summary
This workbook provides a practical guide for lifting equipment professionals. It covers areas such as working on-site, examiners' tools and equipment, and types of examinations. It also outlines learning outcomes and the importance of raising standards within the lifting equipment industry.
Full Transcript
LEEA – Lifting Accessories Diploma (LAC) Global - Workbook Lifting Accessories Diploma (LAC) Global Workbook Lifting Equipment Engineers Association...
LEEA – Lifting Accessories Diploma (LAC) Global - Workbook Lifting Accessories Diploma (LAC) Global Workbook Lifting Equipment Engineers Association Lifting Standards Worldwide © LEEA Academy – LAC (Global) v2 2022 AW 1 LEEA – Lifting Accessories Diploma (LAC) Global - Workbook Welcome to the Lifting Accessories Diploma The Diploma is LEEA's globally recognised, industry-standard qualification for lifting equipment testers, inspectors, examiners, repairers and maintainers. The Diploma qualification is essential for anyone engaged in the testing, inspection, examination and repair/maintenance of lifting equipment and responsible for assessing equipment’s suitability to return to service following statutory examination. The core areas covered in Unit 1 are: ▪ Working on-site ▪ Examiners' tools and equipment ▪ Types of examinations ▪ Slinging Accessories LAC Diploma Unit 2 topics are: ▪ Non-fixed load attachments ▪ Recommended further reading and other resources Learning Outcomes Upon successful completion of this Diploma course, students will acquire the knowledge that will assist them to perform the 'thorough examination' of specific lifting accessories in service and validate or otherwise assess their fitness for a further period of service, applying conditions as may be necessary. Students will be able to refer to and extrapolate information from sources to support their analysis of lifting equipment suitability for continued service. © LEEA Academy – LAC (Global) v2 2022 AW 2 LEEA – Lifting Accessories Diploma (LAC) Global - Workbook Working on-site As a professional in the lifting equipment industry, there are high expectations of you to perform your role to mitigate risk and keep people safe. This is of paramount importance and should always be the priority focus of your work. Secondly, our stakeholders, customers and employers rightly expect the highest professional standards from all those working in such a high-risk industry. So you are expected to be competent in your technical abilities, but moreover, as a professional, you must also manage your standards of service, both internally to your employer, and externally to your customers and other stakeholders. “Lifting and height safety industries which have eliminated accidents, injuries and fatalities.” LEEA’s Vision Statement TEAM Card On successful completion of this training course and the associated end-point assessment, you will be awarded the LEEA Diploma in Lifting Accessories (Global), and where applicable, the LEEA TEAM Card. As a TEAM Card holder, there is an expectation that you will perform your role to the very best of your ability, meeting the requirements of a ‘competent person’ as defined by LEEA in its COPSULE. Our industry ‘end-users’ are actively encouraged to use LEEA member companies that employ qualified and competent individuals. They are assured that by using LEEA TEAM Card holders, they are putting their lifting equipment into safe hands and minimising their risks as duty holders and owners of such equipment. © LEEA Academy – LAC (Global) v2 2022 AW 3 LEEA – Lifting Accessories Diploma (LAC) Global - Workbook In order that we continue ‘raising standards in the lifting equipment industry’, each of us has our own part to play. As lifting equipment examiner/inspector/tester, employed by a LEEA member company, you share this responsibility and have a very important role! NOTES: Pre-Job Information Before we consider travelling to the customer’s site, we should pause to think about the following: Representing Your Employer To ensure you provide a professional representation of your employer, answer the following questions: 1. 2. 3. 4. 5. 6. © LEEA Academy – LAC (Global) v2 2022 AW 4 LEEA – Lifting Accessories Diploma (LAC) Global - Workbook Pre-Job Information, Representing your Employer and Signing In © LEEA Academy – LAC (Global) v2 2022 AW 5 LEEA – Lifting Accessories Diploma (LAC) Global - Workbook Reporting and Signing In ▪ Signing In – ▪ Meet – ▪ Exchange of Information – ▪ Agree – ▪ Communication – IMPORTANT! LEEA Members represent the highest standards within our industry. You are an Ambassador for your company and your profession; it is essential that your personal behaviours are exemplary, and your competencies are consistently maintained through your active participation in continuous professional development (CPD). Firstly, you must consider the basic requirements for the examination to be effective: The area should be clean and clear of contaminants which may harm the examiner or the equipment Adequate access to the equipment shall be provided The equipment should be reasonably clean, and the examiner should have the means to clean local areas The examiner should have visual aids and tools required for the examination, including adequate natural or artificial lighting © LEEA Academy – LAC (Global) v2 2022 AW 6 LEEA – Lifting Accessories Diploma (LAC) Global - Workbook During the Job Conduct your job safety analysis/risk assessment review before starting work – make sure any changes are recorded as they arise Is a permit to work required? Confirm the identity of the equipment against the worksheet instruction or users record of the lifting equipment Isolation (lock-out/tag-out) and cordoning off the work area as necessary Toolbox talk with colleagues if applicable before starting the job Talk to equipment operators/user. Are there any issues they may have noticed with the equipment? o This is particularly important for lifting machines as the operator is usually the first to recognise intermittent faults or other issues arising) Make sure all information is recorded regarding the equipment (e.g. location, serial numbers, ID numbers and safety marking) Detail your findings for the report together with any defects found Maintain the safety of the area you are working in through awareness of your surroundings and what is happening. You may need to change the JSA/risk assessment if new control measures are needed due to changing hazards © LEEA Academy – LAC (Global) v2 2022 AW 7 LEEA – Lifting Accessories Diploma (LAC) Global - Workbook Why is it important to pre-arrange a sign off meeting with your customer prior to starting work on site? To ensure that checks can be made of the work area and customer is happy To ensure customer is available for you to present your report summary To ensure that work permits and control measures are removed To ensure that the customer can carry out operational checks of the equipment Completing the Job Returning 1. Have you ensured any isolated equipment has been put back into service? equipment back 2. Have all machinery guards been replaced? to service 3. Did you carry out post-examination running checks on equipment, where necessary? Operational checks? 4. Do you need to colour-code equipment? What colour is needed? 5. Has equipment been stowed in designated storage areas or parked in a safe area? 6. Have all barriers and signs been removed from cordoned areas? Communication 1. Let equipment users know that you have finished your work and that the equipment has been returned to service 2. Complete your reports, identifying any issues and your recommendations; safety- critical issues are your priority, and the owner of the equipment must be notified of these immediately. If the equipment is to be removed from service, ensure it is suitably quarantined and marked, “DO NOT USE”. 3. Identify and detail any repairs that may need carrying out and a timescale in which this should be completed Leaving the site 1. Have your debrief meeting with the site contact to present your report summary 2. Ensure your customer is completely satisfied before you leave the site © LEEA Academy – LAC (Global) v2 2022 AW 8 LEEA – Lifting Accessories Diploma (LAC) Global - Workbook NOTES: © LEEA Academy – LAC (Global) v2 2022 AW 9 LEEA – Lifting Accessories Diploma (LAC) Global - Workbook Equipment for Carrying Out On-Site Thorough Examinations Tools For the lifting equipment examiner/inspector/tester, a selection of hand tools will be required at work, which may be for a thorough visual examination of lifting accessories such as shackles and chain slings, or perhaps lifting appliances such as gantry cranes or electrically operated chain hoists fitted to slewing jib cranes. The selection of tools will therefore depend on the nature of the job. A broader perspective on tools required may include access equipment (MEWP, scaffolding etc.) You may also need to consider the types of lifting equipment you need to hoist/lower spares, lubricants, and cleaning or test equipment. You should be appropriately trained to use all equipment you are supplied with and have the appropriate PPE. Both hand and power tools should be maintained in a safe and operable condition. Measuring Equipment: Calibration of measuring equipment should be carried out in accordance with relevant standards, and this is verified by LEEA during compliance audits. © LEEA Academy – LAC (Global) v2 2022 AW 10 LEEA – Lifting Accessories Diploma (LAC) Global - Workbook Lighting It is very important that the area of inspection is well lit with natural or artificial light so that defects can be identified. Torches or portable lighting stations may be required to help you. Cleaning The area where you are carrying out the inspection should be reasonably clean and free of contaminants that may affect the equipment you are inspecting. It is recommended that you carry basic cleaning materials such as rags, dustpan and brush, a wire brush and PH neutral cleaning fluids in the event that you have to clean the item(s) being inspected. Ensure any data sheets and chemical warnings are adhered to for the use of such products and your JSA/risk assessment reflects this. © LEEA Academy – LAC (Global) v2 2022 AW 11 LEEA – Lifting Accessories Diploma (LAC) Global - Workbook Types of Examination There are 3 levels of inspection: Pre-Use The pre-use inspection is normally carried out by the operator before operating the Inspection equipment. The operator will visually check for any signs of obvious defect or damage that give cause for concern. If such an issue is found, the operator must report their findings to the appropriate maintenance/inspection personnel for further investigation before operating the equipment. Interim The interim inspection (sometimes referred to as the ‘frequent inspection’) is determined Inspection by risk assessment as to how often, and to what extent the inspection is performed. This level of inspection normally focuses on critical components that may become problematic prior to the next periodic thorough examination. The number and frequency of these inspections are also determined by the risk assessment and the manufacturers' literature. Interim Inspections are often done at the same time as planned maintenance or following a repair. Thorough A thorough examination (sometimes referred to as the periodic, or thorough inspection) Examination is a visual examination of lifting equipment that is carried out by a competent person. The examination should be performed carefully and critically, supplemented by testing and measurements required by the competent person to ascertain the equipment’s fitness for a further period of service. It is also used as a check of the suitability of the equipment and the inspection/maintenance regime. This means that the thorough examination should not find any defect affecting the safety of the equipment, if it does, this may suggest that there is an issue with the inspection/maintenance regime, the competency of the inspectors or maintainers or the product’s fitness for purpose, etc. In essence, it is a safety net, used to identify inadequacies in the inspection/maintenance regime and thereby provide a means of improvement and prevent a recurrence. This means that the root cause of any defect found following a thorough examination should be investigated and rectified with appropriate measures to prevent reoccurrence. Note 1: the term ‘testing’ includes, for example, proof load testing, operational testing at lower loads and non- destructive testing. Note 2: the period between thorough examinations must be established by the competent person on the basis of statutory requirements for the equipment. © LEEA Academy – LAC (Global) v2 2022 AW 12 LEEA – Lifting Accessories Diploma (LAC) Global - Workbook LEEA recommends that the following maximum intervals between thorough examinations are used as best practice: 12 Months for?________________________________________________________________________________ 6 Months for? _________________________________________________________________________________ Note 3: thorough examination shall be carried out following installation and after exceptional circumstances, i.e. substantial repair or modification, following a collision, etc. Note 4: the examination should identify issues that could become a danger in the period before the next thorough examination and the subsequent report should advise the appropriate action to be taken. Defined Scope of Examination Irrespective of the type of examination the competent person should always be working to a predefined scope of examination or inspection. A predefined scope of the examination should be established with a clearly documented list, of everything that needs to be checked, complete with acceptance/rejection criteria, which should be considered as the maximum permitted and used as a means of reaching a conclusion as to the fitness for service of the equipment. The examiner should take into account: 1 ____________________________________________________________________________________________ 2 ____________________________________________________________________________________________ 3 ____________________________________________________________________________________________ 4 ____________________________________________________________________________________________ 5 ____________________________________________________________________________________________ © LEEA Academy – LAC (Global) v2 2022 AW 13 LEEA – Lifting Accessories Diploma (LAC) Global - Workbook It should also specify the intervals at which the equipment, or its individual parts, should be thoroughly examined in accordance with the legislative requirements and, where appropriate, intervals for specific supporting reports and tests. These intervals should reflect the anticipated rate of deterioration and the likelihood and potential consequences of failure. In all cases it is recommended that the scope of examination is drawn up specifically for the particular item of lifting equipment, however, generic scopes of a thorough examination can be written for specific models and make of lifting equipment. Either way, the scope should also include any dedicated ancillary equipment, such as wire ropes. Further reading: LEEA Lifting Equipment Examiners Handbook NOTES: © LEEA Academy – LAC (Global) v2 2022 AW 14 LEEA – Lifting Accessories Diploma (LAC) Global - Workbook Supplementary Testing and Documentation Supplementary testing is carried out in support of a thorough examination and the extent and nature of any testing are specified by the competent person carrying out the thorough examination. These tests should be carried out in accordance with the manufacturer's instructions, the relevant standards and statutory requirements. Test areas should be carefully selected and steps are taken to protect personnel and property. In particular when load testing, ensure a clear area to facilitate the lifting and movement of test weights with a minimum of ground clearance. Common tests used to supplement a ▪ Operation testing thorough examination include: ▪ SWL and deflection tests ▪ Proof load testing ▪ Light load testing ▪ Calibration checks ▪ Insulation and continuity testing ▪ Pressure tests ▪ Non-destructive testing © LEEA Academy – LAC (Global) v2 2022 AW 15 LEEA – Lifting Accessories Diploma (LAC) Global - Workbook Documentation and records Following every examination, a formal report is drawn up. However, the examiner should always make a record at the time of the examination on the job paperwork or in a notebook etc. This contemporary record should always be authenticated and dated by the examiner and retained for reference purposes. If the formal report is authenticated by someone on the examiner's behalf, the contemporary record should be available to the authenticator so that the accuracy of the formal report can be checked. When an examination reveals a defect, the user should be notified promptly so that appropriate action can be taken and, if the defect is of immediate or imminent danger, further use is prevented. In some countries, it is also necessary to inform the enforcing authorities of certain defects. Textile Slings Fibre slings (including additional information for HMPE slings) The popularity of fibre rope slings has declined greatly in modern times, in favour of more convenient forms of sling such as webbing and roundslings. However, a few remain in general service but in the maritime industry they are still widely used. The slings are produced from cut lengths of 3, 4 or 8 strand rope which is then hand spliced. They are bulky to handle and natural fibres, in particular, are rough to the touch. Rope slings are less pliable than other types of textile slings and, unlike other textile slings, they present a hard point contact with the load. However, this is still less severe than with chain or wire rope. Identification Visually, the various fibres appear much the same. This makes identification extremely difficult. An international system of colour-coded labels, which carry the information necessary to be marked on a sling (see marking), has therefore been adopted in standards as follows: WHITE: BLUE: GREEN: BROWN: YELLOW: ORANGE: © LEEA Academy – LAC (Global) v2 2022 AW 16 LEEA – Lifting Accessories Diploma (LAC) Global - Workbook 3 strand ‘hawser’ laid rope: constructed from three strands of yarns spun from fibres. The strands are twisted together (laid) in right hand lay; this is known as a ‘Z’ direction of lay. 8 strand ‘plaited’ rope: constructed from eight strands of yarns spun from fibres. The strands are laid together in pairs, each alternative pair consisting of two left hand (‘S’ twist) strands and two right hand (‘Z’ twist) strands respectively. The eight strands contain the same number of yarns as the three strand rope of equivalent size. So, the weights and breaking strengths of both constructions are the same size for size. Fibre rope sling: a flexible sling, comprising one or more parts of identical fibre rope, terminating in spliced eyes with or without thimbles and fittings, or in the case of an endless sling, joined to itself with a splice. © LEEA Academy – LAC (Global) v2 2022 AW 17 LEEA – Lifting Accessories Diploma (LAC) Global - Workbook Multi-leg sling: Fibre rope sling assembly, consisting of two, three or four identical legs attached to a master link. Splicing What is Splicing? This is a method of laying the tail end strands of the rope into the strands of the standing part of the rope to form an eye or join the ends of the rope together. All splicing shall be carried out by a trained and competent splicer. Where 3 and 4 strands laid ropes are spliced by short splices, the splice shall comply with the following requirements: ▪ All the tucks of the splice shall be against the lay of the rope ▪ For polyamide, polyester multifilament ropes and polypropylene monofilament ropes, either five full tucks shall be made; alternatively, four full tucks with all of the yarns in the strands shall be made, followed by a further tuck with not more than half of the material cut out of each strand and a final tuck with not less than a quarter of the original strand material ▪ For polypropylene fibrillated film and staple ropes and for natural fibre ropes, not less than four full tucks shall be made, each with all of the yarns in the strands © LEEA Academy – LAC (Global) v2 2022 AW 18 LEEA – Lifting Accessories Diploma (LAC) Global - Workbook The Liverpool Splice A method of splicing known as the 'Liverpool splice' where the tucks are made in the same direction of the lay of the rope should not be used as this is unsafe and can easily come apart under load, with possible severe consequences. Length between splices For single leg slings and the individual legs of multi-leg slings, there shall be a minimum length of rope between the emergence of the final tucks of the splice of 20 times the nominal diameter of the rope. © LEEA Academy – LAC (Global) v2 2022 AW 19 LEEA – Lifting Accessories Diploma (LAC) Global - Workbook Thimbles and Fittings What are Thimbles? Thimbles are rigid-shaped components which are inserted into an eye termination for the purpose of protecting the eye from contact damage, abrasion and deformation. The thimbles used to form thimble, or hard, eyes shall comply with the relevant national standard and have a corrosion-resistant finish. Steel thimbles should not be a black finish but should be suitably plated or galvanised to resist corrosion. The use of thimble (hard) eyes is recommended when fittings form part of the fibre rope sling. The fitting of heart-shaped thimbles will prevent the sling from being used in the choke hitch. In such cases, either a soft eye or thimbles of a shape and size suitable for reeving may be used. NOTES: © LEEA Academy – LAC (Global) v2 2022 AW 20 LEEA – Lifting Accessories Diploma (LAC) Global - Workbook Fittings Loadbearing metal components are designed to be fitted and supplied as part of a sling, so as to permit the sling to be attached to other lifting accessories or connected to the load. Master link A link, or link assembly, forms the upper terminal fitting of a multi-leg sling assembly by means of which the sling assembly is attached to the hook of a crane, other lifting machine or accessory. Nominal diameter The specified diameter of the rope, which is usually used as the reference value for a given product. Nominal length The specified length of the sling, inclusive of fittings, from bearing point to bearing point. Thimbles are not included within the term ‘fitting’ Effective Working Length (EWL): the actual finished length of the fibre rope sling, inclusive of fittings, from bearing point to bearing point. The effective working length of a fibre rope sling shall not differ from the nominal length by more than 3% when laid flat underhand tension and measured with a steel tape or rule graduated in increments of 1 mm. The length of each leg of a multi-leg sling shall not differ from the lengths of the other legs by more than 2.5%. Fibres Natural fibres - Manila (Ma), Hemp (Ha), Sisal (Si) and man-made fibres Polyamide (PA), Polyester (PES) and Polypropylene (PP) fibres are used to manufacture fibre rope slings, including High Modulus Polyethylene for which ISO2076 is the standard for HMPE fibres) Sling construction Splicing is the only method to be used for joining or producing eyes. Endless slings shall have only a single splice. Other sling legs shall be spliced at each end to produce an eye and no other splices shall be permitted. Multi-leg slings shall be constructed so that all corresponding items are identical in respect of rope construction, size, material and fittings. © LEEA Academy – LAC (Global) v2 2022 AW 21 LEEA – Lifting Accessories Diploma (LAC) Global - Workbook Safety Requirements Manufacturer’s certification, statement of conformity / test certificate Fibre rope slings are not subject to proof load testing, as this could be detrimental to the sling and will not reveal any additional information. The standard requires the sling manufacturer to perform type tests and manufacturing tests at certain intervals to ensure that the performance requirements are met and maintained. It also requires the manufacturer to issue a manufacturer’s certificate with each batch of slings which states the WLL and, in the case of slings with integral fittings, this will also contain details of the fittings. Natural fibre rope slings offer little or no resistance to chemicals, their fumes or to certain gases. Chemical resistance Natural fibre rope slings offer little or no resistance to chemicals, their fumes or to certain gases. Man-made fibre rope slings however offer selective resistance to chemicals as follows: ▪ Polyamide [nylon] is virtually immune to the effects of alkalis. It is attacked by moderate strength acids. It also suffers the loss of strength on wetting which can be as much as 15% ▪ Polyester is resistant to moderate strength acids but is damaged by alkalis ▪ Polypropylene is little affected by acids and alkalis but is damaged by solvents, tars and paints ▪ HMPE fibres have good resistance to contact with chemicals, however, the sling manufacturer should be consulted if exposure has taken place and care should be taken to assess any contaminated sling for continuing service © LEEA Academy – LAC (Global) v2 2022 AW 22 LEEA – Lifting Accessories Diploma (LAC) Global - Workbook ▪ Aramid Polyamide is resistant to most chemicals Natural fibre ropes deteriorate with age and as natural lubricants dry out; the fibres become brittle. Mould and fungi, e.g. mildew, will readily grow on damp natural fibre ropes living on the cellulose and greatly weakening the rope. Man-made fibre ropes do not suffer in the same way, mould only being able to live on surface contamination, but they can be affected by ultra-violet light and therefore may suffer solar degradation if exposed to strong sunlight or other sources of ultra-violet radiation. Mildew does not attach HMPE ropes, but surface contaminants may provide a nutrient for its growth. Temperature Fibre rope slings are suitable for use within the following temperature ranges: Manila, Sisal, Hemp and Polypropylene -40°C to 80°C Polyester and Polyamide [nylon] -40°C to 100°C HMPE -40°C to 70°C Aramid Polyamide -50°C to 130° Critical components The critical components of textile slings are: ▪ The rope ▪ Terminal fittings such as master links, intermediate links and hook terminations ▪ Thimble eye protection ▪ The splicing of the rope terminations ▪ Identification labels/tags NOTE: Unless a mandatory requirement of the applicable national legislation or manufacturer dictates, LEEA does not recommend the routine overload testing of slings. Marking requirements The necessary marking should be made in such a way that it is not harmful to the sling. One suitable method is to apply the marking to a plastic sleeve which may be fitted over the rope during the sling manufacture and then shrunk to it. A further, clear plastic, a sleeve may also be fitted over the marked sleeve protecting it from soiling. © LEEA Academy – LAC (Global) v2 2022 AW 23 LEEA – Lifting Accessories Diploma (LAC) Global - Workbook Slings which incorporate links should be marked on a suitable tag permanently attached to the master link or one leg of the sling. If the latter option is adopted, care must be taken to ensure the tag is such that it cannot become trapped by the sling thereby damaging the sling. In addition to the information required by the national legislation and the standard being worked to, the marking should indicate the following minimum information: ▪ ▪ ▪ ▪ ▪ NOTES: © LEEA Academy – LAC (Global) v2 2022 AW 24 LEEA – Lifting Accessories Diploma (LAC) Global - Workbook Defined Scope of Examination The following is a list of defects that should be assessed with respect to the continued safety of the equipment: Thimbles should not be collapsed, cracked deformed or twisted There should be no damage to areas of the fibre ropes in contact with fittings It is necessary to evaluate the extent of soiling to a fibre sling as this can conceal damage which is very difficult for the examiner to see. Where necessary they should be washed in clean water or in accordance with the manufacturer’s instructions Grit and dirt will pick up on the rope fibres and can cause rapid wear and abrasion Terminal fittings should be examined carefully. Particular attention should be paid to any twisting, permanent deformation and signs of overloading The maximum wear for metal terminal components is stated by LEEA as 8% Cuts, nicks and cracks to any materials should be assessed for their likely impact as a stress raiser and whether they will affect the slings continued service Wear and chafing: this indicates that the filaments and fibres are breaking down. In ordinary use, some disarrangement or breaking of the fibres is to be expected. This is harmless if not excessive. It is natural for man-made fibre ropes, especially those of multifilament construction, to raise a pile or fur on their surface as the result of use. This is not cause for concern unless it becomes excessive Localised areas of abrasion, as distinct from general wear, are caused by mishandling such as the passage of the sling over a sharp edge whilst under tension Fraying of the yarns or strands is often an indication of cutting In the case of natural fibre rope slings, the growth of mildew will cause a serious loss of strength as the mould will live on the cellulose of the rope. It is caused by dampness, storage of wet slings or storage in stagnant air. In the case of man-made fibre rope slings, mildew will only grow on surface contamination, it does not affect the rope and may be removed by washing in clean water only. Detergents or other cleaning agents must not be used In the case of natural fibre rope slings, any known contact with chemicals or their fumes. In the case of man- made fibre rope slings, selective resistance permits some contact with chemicals however attack by strong solutions or by other chemical contaminants will result in loss of strength. Chemical attack may be recognised by embrittlement and flaking of the fibres or by a softening of the fibres, which may be rubbed or plucked from the rope Charring of natural fibres, fusing of fibres and glazed appearance of man-made fibres indicate the sling has been subjected to excessive heat, often as the result of friction. This can occur in use, e.g. by careless handling when the sling is used in choke hitch. It is difficult to observe unless severe. Other forms of heat damage, such as burning caused by weld splatter, are more easily identified Solar degradation. The outer fibres become brittle as the result of exposure to sunlight or other sources of ultra-violet radiation Localised flat areas of the rope where it has been suspended and loaded in one point (e.g. over a shackle) © LEEA Academy – LAC (Global) v2 2022 AW 25 LEEA – Lifting Accessories Diploma (LAC) Global - Workbook Keynote: Great care must be taken when inspecting slings as the vulnerability of fibre rope slings to the effects of wear, abrasion and mechanical damage increases inversely with the size of the rope. The smaller the rope diameter, the more of the yarns are exposed on the surface, hence the effects of wear and damage are more severe. Unless a mandatory requirement of the applicable national legislation or manufacturer, LEEA does not recommend the routine overload testing of fibre rope slings. - LEEA NOTES: LEEA’s Vision Statement © LEEA Academy – LAC (Global) v2 2022 AW 26 LEEA – Lifting Accessories Diploma (LAC) Global - Workbook Webbing Slings These may be endless or in the form of single or multi-leg slings which can terminate with soft eyes or metal terminal fittings. This section covers flat woven webbing slings for multi-purposes, made of Polyamide (Nylon), Polyester, Polypropylene or Aramid Polyamide, but excludes special slings or slings used for certain applications as follows: Excluded Bag slings or the lifting straps which form part of flexible intermediate bulk containers Nets, i.e. consisting of several crossed webbings stitched together, or fibre rope cargo nets Webbings used for the securing or lashing of cargoes to each other on pallets and platforms or in vehicles Adjustable slings, e.g. with intermediate buckles stitched along the webbing Slings consisting of webbing with a nominal width of less than 25mm or more than 450mm, or with a nominal thickness of less than 1.2mm Slings made from webbing woven from mono-filament yarns Slings of tubular webbing Slings formed from strips of cut fabric Disposable or ‘one trip’ slings used for pre-slung cargo and not reused o This is an example of a one-trip sling made to German DIN standards. These slings shall only be used in accordance with the specified limitations of use supplied by the manufacturer NOTES: © LEEA Academy – LAC (Global) v2 2022 AW 27 LEEA – Lifting Accessories Diploma (LAC) Global - Workbook Flat-woven webbing slings, also commonly known as belt slings, are used for a variety of lifting purposes. They are a form of textile sling which is soft and easy to handle whilst offering rigidity across their width. They are available as single-leg, endless or multiple leg slings with a choice of terminations. These qualities make them ideal for handling loads which require some support when being lifted as the load is spread across the full width of the webbing, thus avoiding point contact as is the case with chains or ropes. They are therefore less liable to damage finished surfaces than rope, wire rope or chain slings. However, they are less robust and more easily damaged than equivalent capacity wire rope and chain slings. Sewn Webbing Component The sewn webbing component is that part of the sling comprising woven webbing only including the stitching, i.e. an endless sling, a single sling with soft eyes or a single sling excluding its terminal fittings if any. © LEEA Academy – LAC (Global) v2 2022 AW 28 LEEA – Lifting Accessories Diploma (LAC) Global - Workbook All stitching used to make the sling is made from the same thread material as the webbing itself (so all properties are the same) and a locking stitch machine is used for the process. The lockstitch uses two threads: ‘upper’ and a ‘lower’. The two threads lock together in the fabric which they pass through, hence the name ‘lockstitch’. The stitches of the seam run across the sections of the webbing to be sewn together; the stitching must lay flat and not have loops above the surface of the webbing which could be caught and damaged whilst in use. The ends of cut webbing are treated to prevent them from fraying and coming apart. Treatment of cut ends by heating is normally used which melts the material and seals the fibres. As this process can produce a sharp edge, the stitching of the sling avoids running across it. Did you know? Some webbing material is pre-treated which avoids the need to heat seal the edge of the webbing. In this case, the stitching can run over the cut edge. © LEEA Academy – LAC (Global) v2 2022 AW 29 LEEA – Lifting Accessories Diploma (LAC) Global - Workbook Working load limit Marked on the sewn webbing component and indicated by any colour codes or stripe markings. It is the maximum load that the sewn webbing component may sustain when it is in straight pull. Note: For use in normal conditions, the SWL of a single leg sling in a straight pull, or an endless sling in a straight pull, will be equal to the WLL. Capacity The capacity of the sling is related to the width and thickness of the webbing. Slings are available as ‘Simplex’ (a single length of webbing), or, in order to provide a fuller range of capacities or allow a narrower sling, ‘Duplex’ or multi-layer slings are available, although it must be realised that this results in some loss of flexibility. Sling width There is a wide range of flat woven webbing slings in a range of widths from 25mm to 450mm. Mode factor This is a numerical value which is applied to the marked working load limit of a sewn webbing component to determine the maximum load which the sling may lift according to the mode of use and assembly, e.g. choke hitch, basket hitch, single or multiple slinging. Protective sleeve: a tubular sleeve, either fixed or movable, which may be of leather, woven fabric or other material placed over the webbing to provide extra protection to the webbing. It has no effect on the strength of the sling. Similar protection may also be given to soft eyes. © LEEA Academy – LAC (Global) v2 2022 AW 30 LEEA – Lifting Accessories Diploma (LAC) Global - Workbook Soft eye: this may be used to terminate a sling leg. It is formed by folding the webbing back on itself in the form of a loop, the free end of which is then sewn back to the body of the webbing so forming an eye. There are many variations of the soft eye which are available to suit the mode and method of use. The three main variations are the flat eye, reversed eye and folded eye. Metal fittings: Terminal fittings must be compatible with the other items to which they may be attached. The use of metal terminal fittings allows for more arduous conditions of wear on the sling eye and permits wide webbings to be readily attached directly onto the hooks of lifting appliances without the need for other fittings, e.g. shackles. They help to ensure that the load is taken evenly across the width of the webbing. If the sling is always to be used in straight pull or in basket hitch, metal ‘D’ links or eye plates may be used. If the sling is to be reeved into choke hitch, choker ‘D’ links or eye-plates may be used. These allow one plate to pass through the other and also enable the sling to be used in straight pull or in basket hitch. © LEEA Academy – LAC (Global) v2 2022 AW 31 LEEA – Lifting Accessories Diploma (LAC) Global - Workbook Selvedge: the natural woven edge of the material produced by the weaving process and which therefore is free of cutting, folding and stitching. Effective Working Length (EWL): the actual finished length of the flat woven webbing sling, inclusive of fittings, from bearing point to bearing point. NOTES: Identification: an international system of colour-coded labels, which carry the information necessary to be marked on a sling (see marking), has therefore been adopted in standards as follows: © LEEA Academy – LAC (Global) v2 2022 AW 32 LEEA – Lifting Accessories Diploma (LAC) Global - Workbook ▪ Polyester- blue ▪ Polyamide - green ▪ Polypropylene - brown ▪ Aramid Polyamide - yellow (where used regionally) Flat-woven webbing slings and roundslings are colour coded to signify the WLL of the sewn webbing component in straight pull. This must not be confused with the WLL of the completed sling assembly, which may be different. The marking information must always be read to establish the WLL of the sling assembly. It is however usual to find black coloured slings in the entertainment and events industry. This is so that their visual impact in stage and theatre rigging is minimised. Therefore the colour alone should never be assumed as the WLL and reference should always be made to the label. This is an equally true statement for roundslings (as the following pictures show) which will be covered in our next section. © LEEA Academy – LAC (Global) v2 2022 AW 33 LEEA – Lifting Accessories Diploma (LAC) Global - Workbook Traceability code: the traceability code, which is to be included in the marking, should provide the following basic elements of the manufacturing record for traceability purposes: ▪ Identification of webbing ▪ Identification of manufacturer's control ▪ Identification and grade of fittings ▪ This information is marked in the sling identification label and is sewn into the eye or the joining stitches of the sling Manufacturer’s Certification, Statement of Conformity / Test Record Flat woven webbing slings are not subject to proof load testing, as this could be detrimental to the sling and will not reveal any additional information. They are however subject to strength tests made on a number of representative slings during manufacture. Depending on the standard being worked to, a manufacturer’s certificate or statement of conformity is supplied with each sling. Note: A statement of conformity is not the same as a Declaration of Conformity which is a document required by some national legislation. NOTES: © LEEA Academy – LAC (Global) v2 2022 AW 34 LEEA – Lifting Accessories Diploma (LAC) Global - Workbook This confirms compliance with the manufacturing standard and certifies that such manufacturing and sampling tests as required have been completed. In the case of slings with integral fittings, this will also contain details of the verification of the fittings. NOTES: © LEEA Academy – LAC (Global) v2 2022 AW 35 LEEA – Lifting Accessories Diploma (LAC) Global - Workbook Chemical resistance If the webbing sling is to be used in a chemical environment, the supplier/manufacturer should always be consulted for advice. Man-made fibres offer high resistance to chemicals and can, subject to correct material selection, be used in certain chemical environments without detriment. Polyamide [nylon] is virtually immune to the effects of alkalis. It is attacked by moderate strength acids, but it is attacked by moderate strength acids Polyester is resistant to moderate strength acids but is damaged by alkalis Polypropylene is little affected by acids and alkalis but is damaged by solvents, tars and paints Aramid Polyamide is resistant to weak acids and alkalis Terminal fittings: Certain grades of steel are susceptible to hydrogen embrittlement as the result of contact with acids. This can seriously reduce the ductility and load-bearing capacity, and cause cracking and catastrophic brittle failures at stresses below the yield stress of the material. Other metals may be subject to corrosion. The advice of the supplier should always be sought when selecting flat woven webbing slings and/or fittings for use in chemical environments Temperature Webbing slings are suitable for use within the following temperature ranges: Polypropylene - 40°C to 80°C Polyester and polyamide [nylon] - 40°C to 100°C Aramid Polyamide -50°C to 130°C Care must be taken when selecting slings for use at low temperatures. Although the qualities of the materials used for flat woven webbing slings makes them suitable for use at temperatures as low as -40°C, if moisture is present, ice will be formed. Ice will both act as an abrasive and cutting agent and will damage the sling. Slings selected for use at low temperatures should be dry and steps must be taken to prevent ice forming on or, more importantly, between the woven strands of the webbing Ultraviolet radiation All textile fibres become brittle as the result of exposure to sunlight or other sources of ultra-violet radiation. This is known as solar degradation. Its effect is more pronounced in man-made fibres, but it is hard to detect until at an advanced stage. Then, very quickly, they will become brittle, turn to powder and crumble away. During the manufacturing stage man-made fibres, intended for use in sling manufacture, are subject to a process known as stabilising. Whilst this does not prevent solar degradation it does slow down the rate of this effect. © LEEA Academy – LAC (Global) v2 2022 AW 36 LEEA – Lifting Accessories Diploma (LAC) Global - Workbook Effects of water (wetting) Polyamide loses up to 15% of its strength when wet Polyester and Polypropylene are unaffected by water and therefore the strength remains unchanged when wet Critical Components Webbing material Stitching Soft eye protection Metal fittings Identification labels/tags Marking Requirements The marking may be directed onto the sling or on a sewn-on label. This marking must be such that it will not affect the safety of the sling when in use. Depending on the standard being worked to, for some slings the material of the webbing will be identified by the colour of the label: for polyamide (nylon) this will be green, polyester blue, polypropylene brown and Aramid Polyamide yellow. Terminal fittings should be individually marked to identify them with the appropriate record. In addition to the marking required by the applicable standard and legislation the marking on the label should indicate the following minimum information: SWL: Marks: Length: Material: Manufacturer: Year: Mode Factor: © LEEA Academy – LAC (Global) v2 2022 AW 37 LEEA – Lifting Accessories Diploma (LAC) Global - Workbook Some slings are dyed with a colour code to indicate the working load limit of the sewn webbing component. The WLL may also be indicated by stripes or lines running along the length of the sling, i.e. 1 stripe = 1 tonne, 2 stripes = 2 tonnes and so on. These colours and markings relate to the WLL of the sewn webbing component only and older slings may be marked with alternative colours or no specific colouring. For these reasons and due to the fact that a large proportion of the working population are colour blind to some degree, the user should always check the label to confirm the WLL of the sling. NOTES: © LEEA Academy – LAC (Global) v2 2022 AW 38 LEEA – Lifting Accessories Diploma (LAC) Global - Workbook Defined Scope of Examination Did you know? The webbing sling must regularly be thoroughly examined by a competent person to check whether it is safe to use. LEEA recommends that this is to be done within a maximum period of 6 months unless a written scheme of examination (for guidance refer to LEEA 032 Guidance to Written Schemes of Examination), drawn up by a competent person is in place and operating. Reports of thorough examination should be compliant with the legal requirements or the LEEA template report documents, retained and cross-referenced to the sling’s historical records for inspection by the Competent Person or the enforcement authority. Overload testing is not recommended! Any defects found by the examination should be reported to the owner of the equipment, who must assess the root cause of the defect and implement procedures to prevent reoccurrence, e.g. training of operators, increased inspections, etc., before remedying the equipment and returning it to service. Question: “…unless a mandatory requirement of the applicable national legislation or manufacturer, LEEA does not recommend the routine overload testing of slings”. True False NOTES: © LEEA Academy – LAC (Global) v2 2022 AW 39 LEEA – Lifting Accessories Diploma (LAC) Global - Workbook Surface chafing: some chafing will occur and is unavoidable. If this is confined to the surface fibres as opposed to the yarns, it has no effect on the safe use. However, in extreme cases, the faces of the webbing become so worn that the outer yarns are severed Localised abrasion: if the webbing shows signs of local abrasion, as opposed to general wear, serious loss of strength may occur Sling eyes and the eye protection: paying particular attention to the point where the eye passes around other lifting accessories or fittings as this is likely to be the point of the highest wear Cuts: longitudinal and across the webbing, paying particular attention to the selvedges (edges) of the sling as even a small nick in the selvedge of the webbing can seriously weaken the strength of the sling Soiling: this can conceal damage which is very difficult for the examiner to see. Where necessary they should be washed in clean water or in accordance with the manufacturer’s instructions. Grit and dirt will pick up on the rope fibres and can cause rapid wear and abrasion Chemical attack: which may be indicated by the flaking of the surface fibres which will then be able to be picked or rubbed off Heat and friction damage: this can be seen by the surface taking on a glazed appearance and signs of the fibres fusing together © LEEA Academy – LAC (Global) v2 2022 AW 40 LEEA – Lifting Accessories Diploma (LAC) Global - Workbook Weld splatter: textile slings are often used in welding processes as they insulate the workpiece from the lifting appliance. Weld splatter will cause localised burning and will be embedded in the webbing, causing internal abrasion Damaged stitching or loosening of the threads If the textile webbing sling has terminal fittings like master links and hooks fitted, then these should always be examined paying particular attention to permanent deformation, cracks or cuts, wear (maximum 8%), corrosion, stretched or twisted hooks, inoperative or missing safety catches Check tolerances of manufacturing length are correct, especially where slings are used in pairs which could be dangerous The webbing of a duplex sling that has come loose and the layers of the sling webbing are parting: Damaged web sling which has been cut over a period of time by localised abrasion: © LEEA Academy – LAC (Global) v2 2022 AW 41 LEEA – Lifting Accessories Diploma (LAC) Global - Workbook A cut in the selvedge of a webbing sling: Illegible markings: NOTES: © LEEA Academy – LAC (Global) v2 2022 AW 42 LEEA – Lifting Accessories Diploma (LAC) Global - Workbook Roundslings This section covers man-made fibre roundslings for multi-purpose use made of Polyamide (Nylon), Polyester, Polypropylene and Aramid Polyamide.It should be noted that anything other than a roundsling as defined in this section is excluded (e.g. an endless rope sling). The most popular roundslings are usually supplied as single endless slings, manufactured in polyester in a range of working load limits up to 12 tonnes, although there is no restriction and higher capacities are becoming more commonly available. Roundslings of 1 metre to 6-metre effective working length are readily available but other lengths can be readily manufactured to order and again there is no restriction other than that imposed by the capacity of the manufacturing equipment. Similarly, slings in polyamide and polypropylene can be supplied to order. A man-made roundsling is soft and pliable to use. It is easy and light to handle and is particularly useful when lifting loads with delicate surfaces. They are however less robust that chain and wire rope slings and can b be easily damaged if used, transported or stored incorrectly. A roundsling is a sling comprising a core enclosed in a protective cover. © LEEA Academy – LAC (Global) v2 2022 AW 43 LEEA – Lifting Accessories Diploma (LAC) Global - Workbook Core This is a hank of yarn, made up of one or more strands of the parent material which are wound together in a continuous loop and joined to make an endless sling. This core is the load-bearing part of the sling. An outer sleeve made of the same material as the core yarns, contains the inner core and protects it from wear, damage and contamination. Core termination join Yarn join Cover: the cover is made from webbing which is woven from identical parent material to the core, and it is made with the ends overlapped and sewn. The edges of the woven cover material are finished in such a way that they cannot unravel. If the cover is hot-welded, care must be taken to ensure that the welding does not affect the core. Note: the cover is designed to be non-load bearing; its sole purpose is to contain the core and protect it from contamination. © LEEA Academy – LAC (Global) v2 2022 AW 44 LEEA – Lifting Accessories Diploma (LAC) Global - Workbook ▪ Protective sleeve: not to be confused with the roundsling cover. This is a sleeve which is fitted to the roundsling on top of the cover, protecting part of the overall sling length. It is a loose sleeve that slides around the sling circumference. The protective sleeve does not affect the strength of the sling in any way ▪ Effective Working Length (EWL): the effective working length of a roundsling is equal to half its circumference ▪ Terminal and connection fittings: these are loadbearing metal components, supplied as part of a roundsling which allows it to be attached to other lifting accessories, connected to other roundslings to form a multi- leg sling assembly or connected to the hook of a crane or other lifting machine. They may be permanently attached to the roundsling in the course of manufacture or, more commonly, fitted by the means of metal connecting fitting, otherwise known as a coupling component Working Load Limit: the working load limit marked on the roundsling label and indicated by any colour codes or stripe markings is the maximum load that the sling may sustain when it is in a straight pull condition of loading NOTE: The covers of slings to BS EN 1492-2 and the latest version of BS 6668: Part 2 are dyed with a colour code to indicate the working load limit of the roundsling in straight pull. The WLL may also be indicated by stripes or lines running along the length of the sling: i.e. 1 stripe = 1 tonne, 2 stripes = 2 tonnes, etc. Older slings may be marked with alternative colours or no specific colouring. For these reasons and due to the fact that a proportion of the working population are colour blind to some degree, the user should always check the label to confirm the WLL of the sling. © LEEA Academy – LAC (Global) v2 2022 AW 45 LEEA – Lifting Accessories Diploma (LAC) Global - Workbook Mode Factor This is a numerical value which is applied to the marked working load limit of a sewn webbing component to determine the maximum load which the sling may lift according to the mode of use and assembly, e.g. choke hitch, basket hitch, single or multiple slinging. Identification An international system of colour-coded labels, which carry the information necessary to be marked on a sling (see marking), has therefore been adopted in standards as follows: Polyester- blue Polyamide - green Polypropylene - brown Aramid Polyamide - yellow (where used regionally) NOTES: © LEEA Academy – LAC (Global) v2 2022 AW 46 LEEA – Lifting Accessories Diploma (LAC) Global - Workbook Safety Requirements Manufacturer’s Certification, Statement of Conformity / Test Certificate Roundslings are not subject to proof load testing, as this could be detrimental to the sling and will not reveal any additional information. They are however subject to strength tests made on representative slings during manufacture. Depending on the standard being worked to, a manufacturer’s certificate or statement of conformity is supplied with each roundsling. This confirms compliance with the manufacturing standard and certifies that such manufacturing and sampling tests as required have been completed. In the case of slings with integral fittings, this will also contain details of the verification of the fittings. Note: A statement of conformity is not the same as a Declaration of Conformity which is a document required by some national legislation. Chemical Resistance If the roundsling is to be used in a chemical environment, consult the supplier for advice. Man-made fibres offer high resistance to chemicals and can, subject to correct material selection, be used in certain chemical environments without detriment. Polyester is resistant to moderate strength acids but is damaged by alkalis Polyamide (nylon) is virtually immune to the effect of alkalis but is attacked by moderate strength acids Polypropylene is little affected by either acids or alkalis but is damaged by some solvents, tars, paints etc. It is suitable for applications where the highest resistance to chemicals, other than solvents, is required Aramid Polyamide is resistant to weak acids and alkalis Terminal fittings: Certain grades of steel are susceptible to hydrogen embrittlement as the result of contact with acids. This can seriously reduce the ductility and load-bearing capacity, and cause cracking and catastrophic brittle failures at stresses below the yield stress of the material. Other metals may be subject to corrosion. The advice of the supplier should always be sought when selecting flat woven webbing slings and/or fittings for use in chemical environments Temperature Roundslings are suitable for use within the following temperature ranges: Polypropylene - 40°C to 80°C Polyester and polyamide [nylon] - 40°C to 100°C Aramid Polyamide -50°C to 130°C Care must be taken when selecting slings for use at low temperatures. Although the qualities of the materials used for roundslings makes them suitable for use at temperatures as low as -40°C, if moisture is present, ice will be formed. Ice will both act as an abrasive and cutting agent and will damage the sling. Slings selected for use at low © LEEA Academy – LAC (Global) v2 2022 AW 47 LEEA – Lifting Accessories Diploma (LAC) Global - Workbook temperatures should be dry and steps must be taken to prevent ice forming on or, more importantly, between the strands of the sling core or the cover. Ultraviolent radiation All textile fibres become brittle as the result of exposure to sunlight or other sources of ultra-violet radiation. This is known as solar degradation. Its effect is more pronounced in man-made fibres, but it is hard to detect until at an advanced stage. Then, very quickly, they will become brittle, turn to powder and crumble away. During the manufacturing stage man-made fibres, intended for use in sling manufacture, are subject to a process known as stabilising. Whilst this does not prevent solar degradation it does slow down the rate of this effect. Effects of water (wetting) Polyamide loses up to 15% of its strength when wet Polyester and Polypropylene are unaffected by water and therefore strength remains unchanged when wet Summary: Critical Components: Cover, Stitching, Metal fittings (coupling components), Identification labels/tags Marking Requirements Marking should be directed onto the outer cover or on a label attached to the outer cover of the roundsling. This marking must be such that it will not affect the safety of the sling when in use. Depending on the standard being worked to for some slings the material from which the sling is constructed will be identified by the colour of the label: Polyester slings will be blue Polyamide (nylon) green Polypropylene brown Aramid Polyamide yellow © LEEA Academy – LAC (Global) v2 2022 AW 48 LEEA – Lifting Accessories Diploma (LAC) Global - Workbook The information required by the applicable legislation and standard the markings on the label should indicate the following minimum information: (Select ALL that apply) Self-weight of the sling SWL in straight pull for single or endless slings, or for the appropriate range of angles in the case of multileg slings Distinguishing mark(s) Date of last thorough examination Nominal length The material the roundsling is made from Manufacturer’s name or identification Name of last examiner Year of manufacture Mode factors or SWLs for various modes of use and the grade of fitting (if applicable) NOTES: © LEEA Academy – LAC (Global) v2 2022 AW 49 LEEA – Lifting Accessories Diploma (LAC) Global - Workbook Did you know? Some slings are dyed with a colour code to indicate the working load limit of the roundsling in straight pull. The WLL may also be indicated by stripes or lines running along the length of the sling, i.e. 1 stripe = 1 tonne, 2 stripes = 2 tonnes and so on. Older slings may be marked with alternative colours or no specific colouring. For these reasons and due to the fact that a large proportion of the working population are colour blind to some degree, the user should always check the label to confirm the WLL of the sling. Defined Scope of Examination The roundsling must regularly be thoroughly examined by a Competent Person to check whether it remains safe to use. This is to be done within a maximum period of 6 months unless a written scheme of examination (for guidance refer to LEEA 032 Guidance to Written Schemes of Examination), drawn up by a competent person is in place and operating. Reports of thorough examination should be compliant with the legal requirements or the LEEA template report documents, retained and cross-referenced to the sling’s historical records for inspection by the Competent Person or the enforcement authority. Any defects found by the examination should be reported to the owner of the equipment who must assess the root cause of the defect and implement procedures to prevent reoccurrence, e.g. training of operators, increased inspections, etc., before remedying the equipment and returning it to service. The competent person may deem it necessary to supplement their examination with testing. Such testing could be NDT, overload testing, etc. The nature and extent of testing is always at the discretion of the competent person in support of their thorough examination. Note: unless a mandatory requirement of the applicable national legislation or manufacturer, LEEA does not recommend the routine overload testing of slings. Chemical attack. Normally difficult to detect until advanced deterioration has occurred. In an advanced state, surface powdering occurs. Possible loss of colouring of the sleeve. Unless the manufacturer has agreed to such usage and a safe system of work has been agreed, slings exposed to chemicals (e.g. acids, alkalis, solvents) should be washed and cleaned in water and withdrawn from service for examination by a Competent Person Illegible marking or missing label, i.e. the sling identification mark and safe working loads Soiling. Heavy soiling can obscure damage, making detection during inspection difficult. It can also make identification difficult by obscuring any marking or colour coding. Grit and dirt will pick up on the face of the cover and can cause rapid wear and abrasion. Clean the sling in an approved manner but if the soiling is such that cleaning has little or no effect, withdraw from service and refer to a Competent Person Check tolerances of manufacturing length are correct, especially where slings are used in pairs which could be dangerous Knotted slings or those that have been tied together for shortening purposes should be removed from service © LEEA Academy – LAC (Global) v2 2022 AW 50 LEEA – Lifting Accessories Diploma (LAC) Global - Workbook Only use cleaning agents approved by the manufacturer, whose instructions on its use must be sought and followed. Clean water may however be freely used. An international system of colour-coded labels, which carry the information necessary to be marked on a sling - from the options below - select the CORRECT label and colour. (Select one answer) Polyamide - Brown Polyamide - Yellow Polyamide - Green Polyamide - Blue © LEEA Academy – LAC (Global) v2 2022 AW 51 LEEA – Lifting Accessories Diploma (LAC) Global - Workbook Chain Slings Types of load chain Chain is the most basic of lifting media, and although it is far heavier than rope it has a far longer life and is far more robust. It can better withstand rough usage, is less likely to damage, is almost perfectly flexible and can be stored for long periods without serious deterioration. In use it tends to show evidence of damage better than wire rope or textiles, consequently examination is more reliable. Therefore, it remains the principal component of much lifting equipment. In this unit we will consider the various grades of chain in use in our industry today. Chain slings manufactured from wrought iron are obsolete and no longer available. Similarly, mild steel chain slings were rendered obsolete in the early 1980’s following the publication of newer standards which specifically exclude the use of this grade of chain for lifting applications. However, it is possible that examples of wrought iron and mild steel chain slings may occasionally be found in service, but their continued use is not recommended by LEEA and they are therefore outside the scope of this course. At the present time, the majority of chain slings in service are grade 8 or grade 80 (or T – See note below about the use of letter grades in older standards). Other grades, notably 40, M, 4 and, to a lesser degree, 60, S, 6, of welded construction may also be found in service and are therefore covered by this code of practice. Grades 8, 80 and T have a breaking load twice that of grades 40, M, 4 and are therefore lighter for the same strength. Keynote Older national and international standards permitted the use of either letters or numbers to indicate the grade of the chain irrespective of its intended use. However, most modern standards now reserve the use of numbers to indicate the grade of medium tolerance chain for chain slings and the use of letters to indicate the grade of fine tolerance chain for lifting appliances. Although not yet standardised in many parts of the world, grade 10, or higher, chain slings are available and gaining in popularity. © LEEA Academy – LAC (Global) v2 2022 AW 52 LEEA – Lifting Accessories Diploma (LAC) Global - Workbook Short link chain A short link chain only short link chain is allowed for lifting purposes. ‘Fine tolerance’ chain is used in lifting machines o Usually grade T, DT or DAT ▪ Each link must fit precisely into the load pocket wheel of the hoist! ‘Medium tolerance’ chain is used generally in the manufacture of lifting slings o Usually, grade 8 o Can be found marked T(8) Grade T chain slings Chain slings made in the UK between 1981 and 1997 may show the letter ‘T’ or as a grade mark. Students should therefore make themselves familiar in the recognition of fine tolerance and medium tolerance chains by looking at as many examples as possible and referring to the chain manufacturer if in doubt. Long Link Chain In the past, certain types of chain sling were made from or included, ‘long link’ chain. It should be noted that the European Machinery Directive only permits the use of a short link chain for lifting purposes and therefore the use of a long link chain is prohibited. This is generally the case for all known standards. Grading of Chain Slings Recognising Different Chain Grades A fine tolerance chain may be recognised in two ways. The calibrating process has the effect of removing all of the residual scales from the heat treatment process and many of the finish treatments include corrosion-resistant finishes. As a result, it has a bright finish and of course, there is also the grade mark. Fine tolerance chains to EN 818 use the letters ‘T’, ‘DAT’ and ‘DT’ to indicate the type of treatment given to the chain and its intended application. © LEEA Academy – LAC (Global) v2 2022 AW 53 LEEA – Lifting Accessories Diploma (LAC) Global - Workbook Chains in all of these grades may not be covered by European Standards. Grade T (Fine Tolerance) and 8 (Medium Tolerance) is currently the highest standardised grade of chain. This grading system has also been applied to hooks, links, shackles and other accessories, indicating their strength compatibility with the appropriate grade of chain. Should a sling be found in use manufactured from fine tolerance chain grades, it should be removed from service immediately. However, there is a slight problem here, which may apply to some older chain slings that can still be found in use. A fine tolerance chain is a chain which has been manufactured to precise dimensions for use as a load chain in lifting appliances - it is outside of the scope of this course, however it is important that we know a little about it. Medium tolerance chain is used to manufacture chain slings. It has to be more ductile in order to withstand shock loading in use, however, in use it is not subject to wear and can therefore have a softer outer surface. As it does not mate with other moving parts it does not need to have such a precise pitch. © LEEA Academy – LAC (Global) v2 2022 AW 54 LEEA – Lifting Accessories Diploma (LAC) Global - Workbook Note: This grading system has also been applied to chain sling components to indicate their strength compatibility with the appropriate grade of a chain. Nominal size: the nominated size of the round section of steel wire or bar from which the chain is made. That is, for example, a nominal 7mm chain has a link diameter of 7mm. Material diameter: this is the measured diameter of the chain link or its actual diameter. Pitch: this is the internal length of a chain link as measured. Heat treatment: all load chain is subjected to the appropriate heat treatment specified in the standard to which it is manufactured, for the particular type and grade of a chain. This is carried out before the application of the manufacturing proof force. Surface finish: the `finished' condition for load chain can be of different types depending on the standard to which it is manufactured. For example, chains are supplied with various surface finishes including natural black (i.e. furnace scaled), de-scaled, electroplated or painted. Grade marks: the chain grade mark should appear at regular intervals throughout the entire length of the load chain. By way of example, British standards call for the grade mark of the chain to appear at every 20th link or, at intervals of 1 metre, whichever is the least distance. The links must be stamped or embossed on the least stressed part of the chain, i.e. on the side of the link opposite the weld. © LEEA Academy – LAC (Global) v2 2022 AW 55 LEEA – Lifting Accessories Diploma (LAC) Global - Workbook Short link chain used in lifting machines is: Fine tolerance Medium tolerance © LEEA Academy – LAC (Global) v2 2022 AW 56 LEEA – Lifting Accessories Diploma (LAC) Global - Workbook Manufacturer’s Certificate A certificate of test and examination stating the load chain conformance to the relevant standard supplied to the purchaser. Typically, the information on the certificate will include: ▪ The name and address of the manufacturer or his authorized representative, including the date of issue of the certificate and authentication ▪ Number and Part(s) of the relevant standard ▪ Quantity and description of the chain of which the test sample is representative ▪ Identification of the chain of which the test sample is representative ▪ Nominal size of chain ▪ Manufacturing proof force ▪ Breaking force, in kilonewtons (i.e. confirmation that the specified minimum breaking force was met or exceeded) ▪ Total ultimate elongation at fracture, as a percentage (i.e. confirmation that the specified Minimum total ultimate elongation has been met or exceeded) NOTES: © LEEA Academy – LAC (Global) v2 2022 AW 57 LEEA – Lifting Accessories Diploma (LAC) Global - Workbook Components and Assembly Methods Chain sling assemblies are manufactured in various material and heat-treatment combinations to produce the different grades and to suit differing service conditions. The end fittings are attached to the chain by means of one or more welded links, or by mechanical joining devices. All grades are available in welded construction but only grades 8 (or 80), 10 (or 100) and 12 (or 120) are available constructed with mechanical joining devices. Chain connector pins: these pins are common for connecting components to the load chain. Manufacturers use their own patented pins of different shapes and sizes, usually oval or round in shape. They are held securely in place using roll pins. Some connectors use 1, others have two roll pins. Chain coupling component: some systems employ fittings with large eyes through which half a coupler is passed; the other half of the coupler is passed through the end link of the chain. Couplers are available for a chain to chain, chain to eye type fitting and chain to master link attachment. The two halves of the coupler fit together and a © LEEA Academy – LAC (Global) v2 2022 AW 58 LEEA – Lifting Accessories Diploma (LAC) Global - Workbook locking/load pin passes through the centre to hold them together. The locking pin is kept in position by a central retaining collar, spring clips or circlip type fixings. Adjustable slings: Most manufacturers can incorporate shortening devices into all sling assemblies rendering them adjustable. Shortening clutches are the preferred devices for adjusting leg length as they maintain the correct ‘in line loading’ of the chain so that the rating is not affected. The use of hooks that lock onto a link of the chain, commonly known as grab hooks, is not recommended for this purpose as they involve a transverse or oblique loading on the chain. If a manufacturer provides grab hooks for shortening purposes, their recommendations on de-rating must be sought and followed. Another, more appropriate, type of grab hook that is sometimes used is the cradle type and again if using these the manufacturer’s instructions must be strictly adhered to. Shortening devices in multi-leg slings will adjust the leg length, but care must be taken to ensure that no one leg is overloaded as a result. Bear in mind that if the legs are not equally disposed about the vertical, the leg making the smaller angle to the vertical will carry a larger share of the load. Such shortening devices MUST be used correctly with the load-bearing chain always leading out from the bottom of the device. © LEEA Academy – LAC (Global) v2 2022 AW 59 LEEA – Lifting Accessories Diploma (LAC) Global - Workbook General precautions Mechanically assembled chain system components are supplied by the system manufacturer in hardened and tempered conditions. As the assembly of the sling does not affect the material condition no further heat treatment is necessary, indeed it would be positively dangerous. This is particularly important when chain slings are used around heat, such as welding, or in a galvanising plant process area. Common chain sling assemblies The most commonly used chain sling assemblies are referred to in this course. Other special assemblies may be devised for lifting specific unusually shaped loads. Although the upper terminal fittings are usually links, rings were also permitted in some standards, but LEEA does not recommend their use. © LEEA Academy – LAC (Global) v2 2022 AW 60 LEEA – Lifting Accessories Diploma (LAC) Global - Workbook Rating chain slings When a multi-leg sling is used with the sling legs at an angle, the load in the individual sling legs will increase as the angle to the vertical (included angle between the legs) becomes greater. Traditionally, the angle has been measured as the included angle α (alpha) between the legs of a two-leg sling and between the diagonally opposite legs of a four-leg sling. As three-leg slings do not have an ‘opposite’ leg it was taken for these as twice the angle to the vertical. This assumed that the legs would be symmetrically disposed of in the plan. In order to emphasise that the angle of each leg to the vertical affects the share of the load, it will carry and to remove the anomaly with three leg slings. It should therefore be noted that the traditional method of measuring the included angle α (alpha) between the legs of a two-leg sling and between the diagonally opposite legs of a four-leg sling is no longer recommended by LEEA, and the angle between the leg and the vertical β (beta) should be used instead. It is possible that some multi-leg slings in service will be marked with the rating expressed at the included angle or range of angles, e.g. 0-90°. However, based on the above for this course, the rating is expressed at the range of angles of a leg to the vertical, e.g. 0-45°. This is based on new methods that have been used in previous LEEA training courses, however, as the courses have now been written to reflect equipment that will be found in service and the acceptance that some geographical regions have not yet adopted the new approach, reference is also made to the included angle. © LEEA Academy – LAC (Global) v2 2022 AW 61 LEEA – Lifting Accessories Diploma (LAC) Global - Workbook Method of Rating If a sling is to be used safely, allowance must be made for this angle and this is achieved by rating the sling in one of two ways. The two methods of rating are often known as the ‘uniform load method’ and the ‘trigonometric method’ It should be noted that the uniform load method is the only method of rating multipurpose slings used in harmonised European standards. The uniform load method must be used for general purpose lifting. The trigonometric rating is more suited to engineered lifts or where fitted to a fixed lifting frame or beam. Uniform Load Permits only one working load limit up to an angle of 45° to the vertical (90° included angle) Method and a reduced working load limit at angles between 45° and 60° to the vertical (90° and 120° included angle). This is the recommended method which should be used for all multipurpose slings Working load limits are derived from the following: Single leg sling = 1.0 x WLL of a single leg Two leg sling 0-45° (included angle 0-90°) = 1.4 x WLL of a single leg Two leg sling 45°-60° (included angle 90° -120°) = 1.0 x WLL of a single leg Three and four leg sling 0-45° (included angle 0-90°) = 2.1 x WLL of a single leg Three and four leg sling 45°-60° (included angle 90° -120°) = 1.5 x WLL of a single leg The uniform load method simplifies matters by removing the need for calculations and reducing the need for the operative to determine angles. Whilst the uniform load method of rating is most easily applied to equipment such as multi-leg slings, it may, with advantage, also be applied to such items as, for example, eyebolts when used in pairs. Standards where the uniform load method has been used, rate a multipurpose four-leg sling at the same working load limit as a three-leg sling of the same size and grade. This assumes that the load may only be taken by only three of the four legs. However, some national standards have now been amended such that they work on the assumption that the load may be carried by two of the legs. Trigonometric This method provides for a variation in the working load limit as the angle to the vertical (or Method the angle between the sling legs) varies. It was traditionally used in the UK, but in order to use it for multipurpose applications, the operative must be provided with tables showing the safe working loads at various angles for each size of chain, rope, etc. It also requires the operative to be trained in judging a range of angles and has the inherent danger that if he should misjudge these, the sling may well be overloaded. Although the uniform load method was introduced several years ago, some manufacturers continued to rate and mark multipurpose slings by the trigonometric method. Slings intended for multipurpose use marked this way will not comply with the requirements of harmonised standards and it is strongly recommended that this method should be used only for slings designed for a single purpose, as specified in the withdrawn standard, BS 6166 Part 1. Working load limits are derived from the following: Single leg sling = 1 x WLL of a single leg Two leg sling = 2 x WLL of a single leg x cos β Three leg sling = 3 x WLL of a single leg x cos β Four leg sling = 4 x WLL of a single leg x cos β © LEEA Academy – LAC (Global) v2 2022 AW 62 LEEA – Lifting Accessories Diploma (LAC) Global - Workbook Where β is equal to the angle between the sling leg and the vertical (i.e. half the included angle α). In the case of a single purpose four-leg sling designed for exclusive use in an application where the load will clearly be shared by the four legs, it is permissible to calculate the working load limit on that basis. NOTE Some standards do not recommend the rating of three leg slings at included angles greater than 90°. This is due to the possible hazard of a user assuming that the ‘included angle’ referred to the angle between the legs of the sling instead of twice the angle of a leg to the vertical. Where slings are rated and marked on the basis of the angle to the vertical, this hazard does not exist. Many national and international standards are now in favour of the uniform load method, largely on the grounds of safety and simplicity. However, this does not exclude the trigonometric method when working to national standards that allow it within their scope or with justified reason to deviate from the uniform load method. This code recommends that the uniform load method is used for all multipurpose applications and that the trigonometric method should be restricted to slings designed and used for a single purpose. Uniform v. Trigonometric Rating example: Uniform load method sling: 7mm (1.5t) 2-legged chain sling 0-45° 2 x Cos β x WLL of single leg 2 x 0.7 x 1.5t = WLL 2.1t Trigonometric load method sling: 7mm (1.5t) 2-legged chain sling @ 40° 2 x Cos β x WLL of single leg 2 x 0.766 x 1.5t = WLL 2.3t (2.298t) © LEEA Academy – LAC (Global) v2 2022 AW 63 LEEA – Lifting Accessories Diploma (LAC) Global - Workbook Re-marking of chain sling rating method: It should be clearly understood by the lifting equipment examiner that whilst equipment designed to be used under the trigonometric method may be re-rated and marked according to the uniform load method, the reverse is NOT always possible and may be dangerous. It is therefore recommended that to avoid confusion, all items of a given type (e.g. all chain slings) at the location should be rated and marked by the same method. The method of expressing and marking the rating at the angle to the vertical also raises the question of how a user, with existing slings rated by the uniform load method but marked with the ‘included angle’, will avoid confusion when introducing new slings marked with the ‘angle of inclination’. It is LEEA’s recommendation that the user should consider whether a programme of re-marking is worthwhile, bearing in mind the expected life of the slings. Irrespective of whether existing slings are re-marked, there will inevitably be a period when both systems are in use. We therefore further recommend that all operatives are made aware and trained to recognise the differences. Rating assumptions We have looked at both the uniform load and trigonometric methods of rating chain slings, we need to be mindful that both methods assume certain conditions of use which are imposed to ensure that no part of the sling can become overloaded. It is important to understand that although the weight to be lifted may be within the maximum lifting capacity of the sling, lifting it in the wrong way can place an excess of the load onto one part of the sling. Although deviations from the assumed conditions have the same effect whichever method of rating is used, it varies in degree and it is with the multipurpose slings where the designer has the least information about possible applications and where the responsibility to make allowance for the actual method of slinging employed therefore lies with the user. The first of the assumptions is that the sling legs are symmetrically disposed of in a plan, i.e. for three leg slings, all included angles between the legs in the plan are equal; for four leg slings, opposite included angles between adjacent legs, in a plan, are equal. The effect of tilt of the load during the lifting operation is also significant and becomes increasingly more so as the included angle between the legs decreases. As tilt increases, the loading in the leg on the ‘downhill’ side (i.e. the leg with the smaller angle to the vertical) increases. The second assumption, particularly applicable to multi-leg slings but also applicable to single leg and endless slings where more than one is used, is that all legs are of identical materials and load-bearing capacity. Assumptions are also made with regard to the method of attachment. Single leg and multi-leg slings are rated for use with the leg or legs in a ‘straight pull’, i.e. the legs are not bent around the load, choked, back hooked or otherwise prevented from taking up a straight line under load. There may be some variation from these assumptions, and this may in fact be desirable offering a more secure way of attaching to certain loads. Endless slings have fewer variations of use, but it should be remembered that the slinging factor for endless chain and wire rope slings assumes choke hitch, whereas the standard rating for textile slings assumes a straight pull. In all cases, it is also assumed that, at the points of attachment to both the lifting appliance and the load, the radii around which the sling passes are large enough to avoid damage to the sling. In the case of chain and wire rope endless slings, the rating takes account of the chain and wire rope being bent around itself on the bight. © LEEA Academy – LAC (Global) v2 2022 AW 64 LEEA – Lifting Accessories Diploma (LAC) Global - Workbook Adverse Conditions In adverse environments, the SWL must be reduced from a value equal to the working load limit, in accordance with the following recommendations. High-temperature conditions: As the temperature which a sling attains in service increases, its strength decreases. Care must be taken to account for the maximum temperature which can be reached by the sling in service. This may be difficult to determine in practice, but under-estimation of the temperature involved must be avoided. © LEEA Academy – LAC (Global) v2 2022 AW