IMS-PRO-115 Undercarriage Measurement Procedure PDF
Document Details
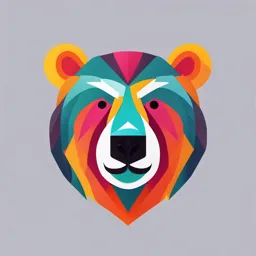
Uploaded by SportyLongBeach
Nicolette van Vreden, Nico Marx
Tags
Related
- A Concise History of the World: A New World of Connections (1500-1800)
- Lg 5 International Environmental Laws, Treaties, Protocols, and Conventions
- Ziraat Finans Grubu Uygulamaları
- Psychoanalytic Diagnosis: Understanding Personality Structure
- Dynamics of the Cell Membrane PDF - Istanbul Atlas University
- Mantenimiento Preventivo R1 Bajo Bastidor - Tren Alstom Ver00 PDF
Summary
This document outlines a procedure for undercarriage measurement in heavy machinery, emphasizing safety and accuracy. It covers scope, responsibilities for technicians and managers, and health and safety considerations. Designed for practical application, especially in an industrial setting.
Full Transcript
**AMENDMENT HISTORY** **Revision** **Date** **Amendments** **Initiator** -------------- ------------- ------------------ ---------------------- 0 1 June 2024 Original Release Nicolette van Vreden **ACCEPTANCE & UNDERSTANDING** **ORIGINATOR**...
**AMENDMENT HISTORY** **Revision** **Date** **Amendments** **Initiator** -------------- ------------- ------------------ ---------------------- 0 1 June 2024 Original Release Nicolette van Vreden **ACCEPTANCE & UNDERSTANDING** **ORIGINATOR** ----------------------------------- ------------------------------------------------ -------------- --------------- **Name** **Designation** **Date** **Signature** Nicolette van Vreden Field Services Coordinator 1 June 2024 **APPROVED BY** Nico Marx Group Operations Manager -- Systems / Workshop 11 June 2024 **ACCEPTANCE FOR IMPLEMENTATION** SHEQ Department **11 June 2024** **TABLE OF CONTENTS** {#section.TOCHeading} [1 Undercarriage Measurement Procedure 3](#undercarriage-measurement-procedure) [1.1 Introduction & Purpose 3](#introduction-purpose) [1.2 Scope 3](#scope) [1.3 Objective 3](#objective) [1.4 Responsibilities 3](#responsibilities) [1.4.1 Field Service Technician: 3](#field-service-technician) [1.4.2 Workshop Manager: 3](#workshop-manager) [1.4.3 Health and Safety Officer/Coordinator: 4](#health-and-safety-officercoordinator) [1.5 Procedure 4](#procedure) [1.5.1 Undercarriage Measuring 4](#undercarriage-measuring) [1.5.2 Documentation and Filing Procedure: 6](#documentation-and-filing-procedure) [1.6 Compliance, Review and Continuous Improvement 6](#compliance-review-and-continuous-improvement) [1.6.1 Periodic Review and Compliance: 6](#periodic-review-and-compliance) Undercarriage Measurement Procedure =================================== Introduction & Purpose ---------------------- This Standard Operating Procedure (SOP) serves to elucidate the process of measuring undercarriage wear in a safe and responsible manner. The primary objective is to establish clear guidelines for assessing the wear and tear of undercarriage components in heavy machinery. By adhering to this procedure, personnel will be equipped with the knowledge and tools necessary to conduct accurate measurements while prioritising safety and environmental responsibility. Scope ----- The scope of this procedure encompasses the safe and precise measurement of undercarriage wear, ensuring full compliance with both customer-specific and industry-standard health and safety regulations. Objective --------- The objective of this Standard Operating Procedure (SOP) is to establish a systematic process for measuring undercarriage wear in heavy machinery, ensuring safety and accuracy while adhering to customer-specific and industry-standard health and safety regulations. This SOP aims to provide clear guidance for measuring technicians on conducting undercarriage wear measurements in a safe, responsible, and efficient manner, particularly within the context of opencast mining sites. By following this procedure, personnel will be equipped to accurately assess undercarriage wear while prioritising safety and environmental responsibility, thereby contributing to the longevity and efficiency of heavy machinery operations. Responsibilities ---------------- ### Field Service Technician: - Perform undercarriage wear measurements in accordance with this SOP. - Adhere to all health and safety regulations mandated by the customer or mining site. - Ensure the accuracy and reliability of measurements through proper calibration and technique. - Report any safety concerns or deviations from protocol to the appropriate personnel immediately. ### Workshop Manager: - Provide necessary training and guidance to measuring technicians on the proper execution of undercarriage wear measurements. - Ensure that measuring technicians are equipped with the required tools and resources to perform their duties safely and effectively. - Oversee compliance with customer-specific and industry-standard health and safety regulations during undercarriage wear measurement activities. - Address any issues or discrepancies identified during measurement procedures and take corrective action as needed. ### Health and Safety Officer/Coordinator: - Collaborate with the supervisor to ensure that all health and safety regulations are followed during undercarriage wear measurement activities. - Conduct regular inspections and audits to assess compliance with safety protocols and identify areas for improvement. - Provide ongoing training and support to measuring technicians on safety best practices and hazard awareness. - Investigate and document any safety incidents or near-misses related to undercarriage wear measurement procedures and recommend preventive measures. Procedure --------- ### Undercarriage Measuring ### The following steps are taken: {#the-following-steps-are-taken.heading04} ### {#section-1.ListParagraph.heading04} +-----------------------------------+-----------------------------------+ | **Responsible Party** | **Action Step** | +===================================+===================================+ | **HR and ITR Safety Department** | 1. Medical fitness and induction | | | up to date where required. | +-----------------------------------+-----------------------------------+ | **Field Service | 2. Ensure Id document and | | Technician(employee)** | driver's license is available | | | for access on site. | +-----------------------------------+-----------------------------------+ | | 3. Measuring kit is complete and | | | in good working condition | | | along with tool list and | | | Undercarriage report book. | +-----------------------------------+-----------------------------------+ | **Field Service Co-ordinator** | 4. Appointment Confirmation with | | | Customer is in place. | +-----------------------------------+-----------------------------------+ | **Field Service | 5. Continue to machine and carry | | Technician(employee)** | out a visible inspection | | | around the machine to ensure | | | that it is safe to proceed. | | | Report any visible dangers to | | | site engineer and safety | | | department. | +-----------------------------------+-----------------------------------+ | | 6. When it is safe to continue, | | | complete the information on | | | undercarriage report book | | | pertaining the customer and | | | machine details. Be thorough | | | with details. | +-----------------------------------+-----------------------------------+ | | 7. Look for any structural | | | damage or any parts that | | | appear loose. | +-----------------------------------+-----------------------------------+ | | 8. Check the tracks for cuts or | | | bends in the metal. | +-----------------------------------+-----------------------------------+ | | 9. See if there is enough | | | tension in the tracks. | | | | | | 10. Measure 5 box sections centre | | | to centre of pins to | | | establish pitch. | +-----------------------------------+-----------------------------------+ | | 11. Make sure the track chain is | | | in its place with no signs of | | | disengaging. | +-----------------------------------+-----------------------------------+ | | 12. Check at the pins and | | | bushings to see if they need | | | to be turned. If the bottom | | | half of the bushing appears | | | worn, it is time to turn them | +-----------------------------------+-----------------------------------+ | | 13. Check rollers for damage and | | | flat spots. Check for wetness | | | at end collars of the | | | rollers, as well as the front | | | idler. Wetness at any of | | | these locations could mean | | | leakage from a roller or | | | idler. | +-----------------------------------+-----------------------------------+ | | 14. Sprockets are often seen as | | | being strongly correlated | | | with overall undercarriage | | | health. If the sprockets are | | | sharp and look show signs of | | | wear, then more components in | | | the undercarriage probably | | | need attention. | +-----------------------------------+-----------------------------------+ | | 15. Use the calliper for | | | measuring the top and bottom | | | rollers. Twist the adjustment | | | screw until the tongs touch | | | the sides of the roller at | | | its diameter. Record the | | | measurement. | +-----------------------------------+-----------------------------------+ | | 16. Pins and bushings are | | | measured in a similar | | | fashion. Slide the tongs of | | | the pin-and-bushing calliper | | | to determine their width. | | | Make note of the measurement. | | | Measure at least 5 pins each | | | side. | +-----------------------------------+-----------------------------------+ | | 17. Measure the width of your | | | track's shoes with a tape | | | measure and their depth with | | | a depth gauge. Push the gauge | | | down until it reaches the | | | bottom of the tracks. Rail | | | height is also checked using | | | a depth gauge. Place it | | | across the bottom of the | | | rails and push the gauge up | | | until it touches the bottom | | | of the shoe. Record these | | | measurements. | +-----------------------------------+-----------------------------------+ | | 18. A smaller depth gauge is | | | required to measure the | | | idler. Place it on the idler | | | and move the gauge until it | | | reaches the outer flange, and | | | then record that measurement. | +-----------------------------------+-----------------------------------+ | | 19. All these measurements are an | | | indication of wear. By | | | checking the wear percentage | | | chart, you can see how worn | | | (as a percent) the components | | | are. Make suggestion or | | | remarks in the section | | | provided | +-----------------------------------+-----------------------------------+ | | 20. Place the values that you | | | recorded for each component | | | to determine the percentage | | | of wear. | +-----------------------------------+-----------------------------------+ | | 21. Use a heat gun to take | | | readings on the end of the | | | track pins and on the end of | | | every roller and idler shaft. | | | If one or more of the track | | | pins or roller/idler shafts | | | are over 10 degrees | | | Celsius warmer than the rest | | | then you are starting to | | | identify parts of your | | | undercarriage that are | | | potentially under excessive | | | stress which could point to | | | an alignment, tension, load | | | or pre-failure issue. The | | | temperatures should be around | | | 8-10 degrees warmer than the | | | ambient temperature bearing | | | in mind that the sun shining | | | on one side of the machine | | | versus the other can cause | | | temps to be higher on that | | | side. | +-----------------------------------+-----------------------------------+ | | 22. Upon completion of | | | measurements, report need to | | | be completed in full and | | | returned to the salesperson | | | in question for quoting. | +-----------------------------------+-----------------------------------+ | Sales representative | 23. A Quotation with the full | | | report to be submitted to | | | customer. | +-----------------------------------+-----------------------------------+ | | 24. Sales to follow-up with | | | customer | +-----------------------------------+-----------------------------------+ ### {#section-2.ListParagraph.heading04} ### {#section-3.ListParagraph.heading04} ### Documentation and Filing Procedure: ### Documentation and Filing {#documentation-and-filing.heading04} ### All activities related to undercarriage wear measurement must be documented and filed to ensure compliance with regulatory requirements and to facilitate traceability and accountability. Documentation shall include records of measurement results, calibration logs, and any deviations from standard procedures. These records shall be maintained in a designated filing system, either electronically or in hard copy, and organised in a systematic manner for easy retrieval and review. Additionally, any correspondence with customers or mining sites regarding health and safety regulations shall be documented and filed accordingly. Regular reviews of documentation shall be conducted to verify completeness and accuracy, with any discrepancies addressed promptly to maintain the integrity of the measurement process. {#all-activities-related-to-undercarriage-wear-measurement-must-be-documented-and-filed-to-ensure-compliance-with-regulatory-requirements-and-to-facilitate-traceability-and-accountability.-documentation-shall-include-records-of-measurement-results-calibration-logs-and-any-deviations-from-standard-procedures.-these-records-shall-be-maintained-in-a-designated-filing-system-either-electronically-or-in-hard-copy-and-organised-in-a-systematic-manner-for-easy-retrieval-and-review.-additionally-any-correspondence-with-customers-or-mining-sites-regarding-health-and-safety-regulations-shall-be-documented-and-filed-accordingly.-regular-reviews-of-documentation-shall-be-conducted-to-verify-completeness-and-accuracy-with-any-discrepancies-addressed-promptly-to-maintain-the-integrity-of-the-measurement-process..ListParagraph.heading04} ### {#section-4.ListParagraph.heading04} Compliance, Review and Continuous Improvement --------------------------------------------- ### Periodic Review and Compliance: ### Compliance with this Standard Operating Procedure (SOP) will be regularly reviewed to ensure alignment with ISO 9001:2015 and ISO 45001:2018 standards. {#compliance-with-this-standard-operating-procedure-sop-will-be-regularly-reviewed-to-ensure-alignment-with-iso-90012015-and-iso-450012018-standards..heading04} ### Continuous improvement efforts will be implemented to enhance the effectiveness and efficiency of track press operations, ensuring ongoing compliance with ISO 9001:2015 and ISO 45001:2018 standards and optimal performance of heavy machinery maintenance processes. {#continuous-improvement-efforts-will-be-implemented-to-enhance-the-effectiveness-and-efficiency-of-track-press-operations-ensuring-ongoing-compliance-with-iso-90012015-and-iso-450012018-standards-and-optimal-performance-of-heavy-machinery-maintenance-processes..heading04} ### {#section-5.ListParagraph.heading04}