iMBA SEM 3 Process Costing PDF
Document Details
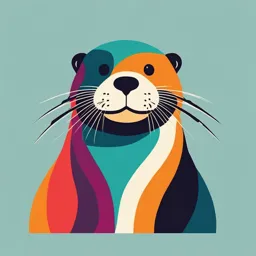
Uploaded by TriumphalDandelion9002
JG University
Prof. Pavan Dhodia
Tags
Summary
This document outlines the principles of process costing, a method used in manufacturing industries. It details the steps involved, features of process costing, and a procedure for determining process cost. The document appears to be part of an MBA program.
Full Transcript
SCHOOL OF MANAGEMENT BBA(Hons.)/iMBA Semester: III SUBJECT: METHODS & TECHNIQUES OF COSTING UNIT 1: PROCESS COSTING Compiled By: Prof. PAVAN DHODIA Definition: Process Costing is a method of costing used in industries where the material has to pass th...
SCHOOL OF MANAGEMENT BBA(Hons.)/iMBA Semester: III SUBJECT: METHODS & TECHNIQUES OF COSTING UNIT 1: PROCESS COSTING Compiled By: Prof. PAVAN DHODIA Definition: Process Costing is a method of costing used in industries where the material has to pass through two or more processes for being converted into a final product. It is defined as “a method of Cost Accounting whereby costs are charged to processes or operations and averaged over units produced”. A separate account for each process is opened and all expenditure pertaining to a process is charged to that process account. Such type of costing method is useful in the manufacturing of products like steel, paper, medicines, soaps, chemicals, rubber, vegetable oil, paints, varnish etc. where the production process is continuous and the output of one process becomes the input of the following process till completion. This can be understood with the help of the following diagram: Raw Finished Material Process-I Process-II Process-III Goods Basic Features: Industries, where process costing can be applied, have normally one or more of the following features: 1. Each plant or factory is divided into a number of processes, cost centres or departments, and each such division is a stage of production or a process. 2. Manufacturing activity is carried on continuously by means of one or more process run sequentially, selectively or simultaneously. 3. The output of one process becomes the input of another process. 4. The end product usually is of like units not distinguishable from one another. 5. It is not possible to trace the identity of any particular lot of output to any lot of input materials. For example, in the sugar industry, it is impossible to trace any lot of sugar bags to a particular lot of sugarcane fed or vice versa. 6. Production of a product may give rise to Joint and/or By-Products. ELEMENTS OF PROCESS COSTING The Cost of each process comprises the cost of: (i) Materials (ii) Employee Cost (Labour) (iii) Direct expenses, and (iv) Overheads of production. Materials - Materials and supplies which are required for each process are drawn against Material Requisitions Notes from the stores. Each process for which the materials are used, are debited with the cost of materials consumed on the basis of the information received from the Cost Accounting department. The finished product of first process generally become the raw materials of second process; under such a situation the account of second process is debited with the cost of transfer from the first process and also with the cost of any additional material used in process. Employee Cost (Labour) - Each process account should be debited with the labour cost or wages paid to labour for carrying out the processing activities. Sometimes the wages paid are apportioned over the different processes after selecting appropriate basis. Direct expenses - Each process account should be debited with direct expenses like depreciation, repairs, maintenance, insurance etc. associated with it. Production Overheads - Expenses like rent, power expenses, lighting bills, gas and water bills etc. are known as production overheads. These expenses cannot be allocated to a process. The suitable way out to recover them is to apportion them over different processes by using suitable basis. Usually, these expenses are estimated in advance and the processes debited with these expenses on a pre- determined basis. PROCEDURE OF ASCERTAINING PROCESS COST: In order to facilitate ascertaining separate cost for each process or operation, the following procedure may be followed: (1) The total production is divided into separate processes or operations under which the cost can be conveniently collected. (2) A separate account is opened for each process and each process account is charged with the material, labour and other expenses incurred directly for the process concerned as well as with its share of overhead charges. (3) The total cost of each process is ascertained and it is divided by the total number of units produced during the specified period and the cost per unit of each process is thus ascertained. (4) The finished product of the first process is transferred to the second process; from second process to third process and so on. The finished product of the last process is transferred to finished stock account. (5) Usually, the finished product of one process is transferred to the next process at cost so that the last process account gives the actual cost of finished products. At times, the finished product of one process is transferred to the next process at cost plus a certain percentage of profit. In such case, the closing stock contains loading for profit charged by previous processes. Hence, reserve for unrealised profit has to be created at the end of financial year and the stock is reduced to its cost price. The calculation of a reserve for unrealised profit involves a few difficult arithmetical calculations. FEATURES OF PROCESS COSTING: Some of the features of process costing may be stated as follows: (1) Transfer of Production to Another Process: The finished product of one process becomes the raw-material of another process. e.g. in cotton textile industry, the first process is spinning. Raw cotton is converted into yarn. The finished product of spinning process viz. yarn becomes the raw material for the next weaving process. (2) Wastage or Loss Ordinarily there is some wastage or loss in weight during various stages of production. e.g. in chemical or petroleum industry, some part of the raw material evaporates and some of it is thrown away as wastage. Thus finished goods obtained from the process is generally less than the quantity of raw materials introduced. (3) By-product: By-products are frequently obtained during the production of main product e.g. in petroleum industry, while refining crude oil, various products of small value are obtained at various stages. (5) Allocation of Joint Costs: At times, joint products are obtained during the same process of production and the problem of separating the joint costs arises. Various methods are used for separating the joint costs. (6) Inter-Process Profit: There is practice in some firms to charge certain percentage of profit while transferring finished goods of one process to the next process. At the close of the year, there will be some stock of finished goods in each process, the value of which will contain the profit charged by the previous process. This profit is unrealised profit. A reserve has to be created for such unrealised profit. Basis of Job order costing Process costing Distinction Performed against specific Production is 1. Specific order orders continuous. Product is homogeneous and 2. Nature Each job many be different. standardized. Costs are compiled for each Cost is determined for each process for department on time 3. Cost determination job separately. basis i.e. for a given accounting period. Cost is compiled when a job Cost is calculated at the end of 4. Cost calculations is completed. the cost period. Proper control is Proper control is comparatively comparatively difficult as easier as the production is 5. Control each product unit is different standardized and is more and the production is not suitable. continuous. There is usually not transfer The output of one process is from one job to another 6. Transfer transferred to another process unless there is some surplus as input. work. There is always some work-in- There may or may not be 7. Work-in-Progress progress because of continuous work-in-progress. production. Suitable to industries where production is intermittent and Suitable, where goods are made 8. Suitability customer orders can be for stock and productions is identified in the value of continuous. production. Process Losses: In many process, some loss is inevitable. Certain production techniques are of such a nature that some loss is inherent to the production. Wastages of material, evaporation of material is un avoidable in some process. But sometimes the Losses are also occurring due to negligence of Labourer, poor quality raw material, poor technology etc. These are normally called as avoidable losses. Basically process losses are classified into two categories: (a) Normal Loss (b) Abnormal Loss Normal Loss: Normal loss is an unavoidable loss which occurs due to the inherent nature of the materials and production process under normal conditions. It is normally estimated on the basis of past experience of the industry. It may be in the form of normal wastage, normal scrap, normal spoilage, and normal defectiveness. It may occur at any time of the process. No of units of normal loss: Input x Expected percentage of Normal Loss. The cost of normal loss is a process. If the normal loss units can be sold as a crap then the sale value is credited with process account. If some rectification is required before the sale of the normal loss, then debit that cost in the process account. After adjusting the normal loss the cost per unit is calculates with the help of the following formula: Cost of good unit: Total cost increased – Sale Value of Scrap Input – Normal Loss units Abnormal Loss: Any loss caused by unexpected abnormal conditions such as plant breakdown, substandard material, carelessness, accident etc. such losses are in excess of pre-determined normal losses. This loss is basically avoidable. Thus abnormal losses arrive when actual losses are more than expected losses. The units of abnormal losses in calculated as under: Abnormal Losses = Actual Loss – Normal Loss The value of abnormal loss is done with the help of following formula: Value of Abnormal Loss: Total Cost increase – Scrap Value of normal Loss x Units of abnormal loss Input units – Normal Loss Units Abnormal Process loss should not be allowed to affect the cost of production as it is caused by abnormal (or) unexpected conditions. Such loss representing the cost of materials, labour and overhead charges called abnormal loss account. The sales value of the abnormal loss is credited to Abnormal Loss Account and the balance is written off to costing P & L A/c. Abnormal Gains: The margin allowed for normal loss is an estimate (i.e. on the basis of expectation in process industries in normal conditions) and slight differences are bound to occur between the actual output of a process and that anticipates. This difference may be positive or negative. If it is negative it is called ad abnormal Loss and if it is positive it is Abnormal gain i.e. if the actual loss is less than the normal loss then it is called as abnormal gain. The value of the abnormal gain calculated in the similar manner of abnormal loss. The formula used for abnormal gain is: Abnormal Gain: Total Cost incurred – Scrap Value of Normal Loss x Abnormal Gain Unites Input units – Normal Loss Units The sales values of abnormal gain units are transferred to Normal Loss Account since it arrive out of the savings of Normal Loss. The difference is transferred to Costing P & L A/c. as a Real Gain. Q1) A product passes through three distinct processes to completion. These processes are numbered respectively 1, 2 and 3. During the first week of March, 500 units are produced. The following information is obtained: I II III Process Rs. Rs. Rs. Materials 30,000 15,000 10,000 Labour 25,000 20,000 25,000 Direct Expenses 5,000 1,000 5,000 The indirect expenses for the period were Rs. 14,000 apportioned to the processes on the basis of wages. No work-in-progress or process stocks existed at the close of the work. You are required to prepare Process Accounts showing total cost per unit in each process. [Ans. Total Cost: Process I Rs. 65,000; Process II Rs. 1,05,000 and Process III Rs. 1,50,000.] Q2) The production of Varda Manufacturing Company Ltd. Passes through 3 processes, before it is transferred to finished stock. The following information is obtained for the month of March: Particulars Process I Process II Process III Raw materials used- in tonnes 1100 65 75 Cost of Raw materials per tonne- Rs 180 120 350 Direct Wages 46,000 53,100 18,050 Manufacturing Overheads 12,300 20,000 7,000 Weight lost in process ( % of input) 5% 5% 5% Scrap in process ( % of input) 10% 10% 10% Sale value of wastage – per tonne Rs. 120 180 300 Actual output in tonnes 935 825 780 Finished product of each process is transferred to other process as raw material and that of process III to warehouse. There was no stock of material or work-in-progress in any process. From the above information, you are required to prepare process accounts and find out cost per unit of each process. Also give the Abnormal Wastage or Effectives (Gain) Accounts. [Ans: Process 1: Cost per unit Rs. 260; (Cost Rs. 2,43,100 / 935) Normal loss in weight 55 tons: Normal wastage 110 tons & its sale value. 13.200, Transfer to Process 2-935 tons costing Rs. 2,43,100, Process 2: Cost per ton Rs. 360, (Cost Rs. 3,06,000 / 850); Normal loss 50 tons, Normal Wastage 100 tons & its sale value Rs. 18,000; Abnormal Wastage 25 tons costing Rs. 9000, Transfer to Process 3: 825 tons costing Rs. 2,97,000; Loss on Abnormal wastage Rs. 4,500. Process 3: Cost per ton Rs. 420 (cost Rs. 3,21,300 / 765); Normal loss 45 tons; Normal wastage 90 tons and its value Rs. 27,000; Abnormal Gain 15 tons costing Rs. 6.300; Transfer to Finished Stock 780 tons at cost of Rs. 3,27,600; Profit on Abnormal gain Rs. 1,800.] Q3) A product passes through three different processes A, B and C and thereafter it is tansferred to finished stock. The information is as under: Particulars Process A Process B Process C Unit introduced ? - - (at Rs. 250 per 10 Units) Normal Wastage ( % of inputs) 1.5% 8% 10% Sales value of Wastage ( Per 10 Units) Rs. 100 Rs. 150 Rs. 500 Abnormal Wastage (units) 100 Nil - (Cost Rs. 50 per unit) Abnormal Gain (Cost Rs. 100 per unit) - Nil 60 Normal Cost of normal output ( per unit) - Rs. 75 - Actual Production ( % of inputs) 97.5% ? ? Other Information: (1) The abnormal wastage was 66 2/3% of the normal wastage in process A. (2) Factory overheads to be considered as 33 1/3% of direct wages in all three processes. From the above information, prepare Process Accounts. [Ans.: Process A: Cost per unit Rs. 50. (Total production 9,750. Units and cost Rs. 4,87,500), Abnormal loss 100 units and its cost Rs. 5,000, Net loss (of Abnormal Wastage) Rs. 4,000, Units introduced in process A 10,000 units (100 x 150/1.5). Process B: Cost per unit Rs. 75, Total production 8,970 units and its cost Rs. 6,72,750, No Abnormal loss or gain. Process C: Cost per unit Rs. 100, Total production 8,133 units and its cost Rs. 8,13,300, Abnormal Gain 60 units and its cost Rs. 6,000, Profit of Abnormal Gain Rs. 3,000.] Q4) 30. Production of Cotton passes through three processes. Finally, the product is transferred to finished stock. Particulars Dying Printing Finishing Unit introduced at Rs.20 per unit ? - - Actual output (units) ? ? ? Normal Loss (% of unit introduced) 3 5 10 Value of normal loss (Rs. Per 10 units) 30 60 80 Abnormal loss (units) (Cost per unit Rs.30) 300 - - Abnormal gain (units) (Cost per unit Rs.50) - - 300 Cost per unit of normal production (Rs.) - 40 - Other information of processes: (1) Factory overhead is estimated at 100% of direct wages. (2) Abnormal loss is 1/3 part of normal loss in dying process. Prepare Process Accounts of each process and Abnormal Loss and Abnormal Gain Accounts. [Ans.: Dying Process: Cost per unit Rs. 30, Normal wastage 900 units and sales Rs. 2,700, Abnormal loss 300 units and cost Rs. 9,000, Transferred to printing process 28,800 units and cost Rs. 8,64,000, Net loss of abnormal wastage Rs. 8,100, Units introduced in Dying process 30,000 units. Printing Process: Cost per unit Rs. 40, Normal wastage 1,440 units and sales Rs. 8,640, No abnormal loss or gain. Transferred to Finishing process 27,360 units and cost Rs. 10,94,400. Finishing Process: Cost per unit Rs. 50, Normal wastage 2,736 units and sale Rs. 21,888. Abnormal gain 300 units and cost Rs. 15,000. Transferred to Finished goods A/c 24,924 units and cost Rs. 12,46,200, Profit of abnormal gain Rs. 12,600] Q5) A Product passes through three processes X Y and from the following information prepare Process accounts and abnormal wastage or abnormal gain accounts: Production overheads were Rs.320000, which are distributed among all three processes in the ratio of direct labour.