Lubrication Principles PDF
Document Details
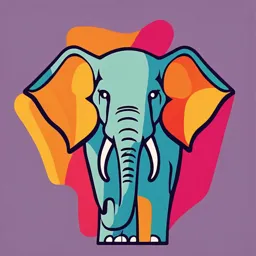
Uploaded by AdmiringSeries4959
Tags
Related
- Principles Of Industrial Maintenance PDF
- SWEP Programme 2022/2023 Petroleum Engineering - Recycling Used Engine Oil PDF
- Corrosion and Wear PDF
- The Effects of Minimum Quantity Lubrication (MQL) on Machining Force, Temperature, and Residual Stress PDF
- Engineering Tribology PDF
- Tribology Lecture Notes PDF
Summary
This document provides a detailed overview of lubrication principles including various types and properties of lubricants, and properties of lubricating oil additives. It also touches upon different methods of lubrication, suitable for use in specific applications such as bearings. It's geared towards engineering students.
Full Transcript
Lubrication Principles PanGlobal Power Engineering Fourth Class, Version 3.0 – Part B, Unit 1, Chapters 1 & 2 At the completion of this lesson, you will be able to: 1. Discuss the concept of lubrication and list the purpose of a lubricant 2. List the various cla...
Lubrication Principles PanGlobal Power Engineering Fourth Class, Version 3.0 – Part B, Unit 1, Chapters 1 & 2 At the completion of this lesson, you will be able to: 1. Discuss the concept of lubrication and list the purpose of a lubricant 2. List the various classes and types of lubricants and describe their respective properties and applications 3. List the properties of lubrication oils, the additives used, and their selection criteria Resistance to motion (or attempted motion). (Courtesy of http://johnarner.com/images/l1friction.jpg) (Courtesy of miniphysics.com) Lubrication separates surfaces with interlocking surface irregularities This allows the surfaces to move freely in relation to each other Separation of these contacting surfaces happens by adding a lubricant between the two surfaces LUBRICATION PRINCIPLES Primary purpose is to prevent two (bearing) surfaces from coming into direct contact When one lubricated surface slides or rolls over another, the lubricant adheres to each surface and the motion takes place within the lubricant The two metallic surfaces do not come into contact with each other, and wear is therefore reduced Fluid friction occurs as one film of the lubricant moves over another LUBRICANT PURPOSES Several reasons for using lubricants: 1. Friction Reduction Most Important 2. Wear Reduction 3. Corrosion Reduction 4. Temperature Control 5. Shock Absorption 6. Sealing MOST IMPORTANT ▪ Finely machined surfaces are not completely smooth ▪ Hills and valleys interlock and extra force is required to move the surfaces ▪ Where the materials touch, they cling or weld together (causes extra force to be required to move the surfaces) ▪ This extra force is known as the force of friction ▪ Using a lubricant to separate moving surfaces can considerably reduce friction Metal Surface Lubrication for Bearings 2. Wear Reduction ▪ When two surfaces are rubbing together, the “hills” and high spots break away due to striking other high spots; Sometimes results in a smooth wearing and is beneficial ▪ Usually continuous wearing causes larger chunks to break apart, which causes an even rougher surface, increasing friction and rate of wear. ▪ Lubrication keeps the high spots from contacting each other, thus reducing or elimination friction. 3. Corrosion Reduction ▪ Lubricant forms a film on the surface protecting them from corrosion (corrosion barrier film) ▪ Metal surfaces are susceptible to acid attacks, resulting in corrosion ▪ Often chemicals are added to lubricants to prevent the formation of acids, due to oxidation of the oil 4. Temperature control ▪ The force used to overcome friction is converted into heat ▪ If not controlled, heat will cause high bearing temperatures; will lose strength, hardness and ability to support load ▪ Lubricant reduces heat by reducing friction and also may be used to carry heat away from the bearings. ▪ Circulate generous quantities of lubricant over a bearing where it picks up heat then cool it in a heat exchanger before returning to the bearing 5. Shock Absorption ▪ Gear teeth meshing, lubricant serves to absorb shock or “cushion” the impact 6. Sealing ▪ Provide sealing, between pistons and cylinder walls, or rotating shaft seals CLASSES OF LUBRICANTS Dependant on: ▪ Nature of surfaces to be lubricated ▪ Load carried ▪ Speed of rubbing ▪ Operating temperature CLASSES OF LUBRICANTS In general lubricants must provide the following services: ▪ Minimum coefficient of friction: (A coefficient of friction is a value that shows the relationship between the force of friction between two objects and the normal reaction between the objects that are involved) ▪ Maximum adhesion to surfaces being lubricated ▪ Physical stability under various temperatures and pressures ▪ Resistant to oxidation ▪ Resistant to emulsion (an emulsion is a liquid dispersed in a different liquid) ▪ Fluidity at low temperatures Three general classes: 1. Solids 2. Semi-solids 3. Liquid Solid Lubricants ▪ Eg. Graphite, soapstone, molybdenum disulphide, mica, and polymer films ▪ Suitable for heavy load and/or extreme temperatures or BOTH ▪ Used when the bearing is subject to contact with materials, such as chemicals, which would deteriorate other classes of lubricants ▪ Lubrication of idle equipment in storage, and bearings difficult to service due to location ▪ Also used to lubricate electrical equipment and instruments, where others classes would collect dirt and become gummy (Courtesy of instructables.com) Semi-solid lubricants Greases, produced by combining a liquid lubricant, petroleum oil, with a thickening agent. Ball bearings, roller bearings, single application is good for a long period of time Good under conditions where an oil would leak away and leave the bearing dry, also less likely to drip or splash, good for textile and food industries Seals out dirt and water from bearings under idle conditions Not suitable for removing heat Types of Grease: Calcium (lime) base grease: ▪ Cheapest and most common, axle grease, water pump grease, pressure gun grease ▪ Not suitable for temperatures above 70℃, soap and oil will lose moisture and separate ▪ Insoluble in water - good for damp conditions Sodium (soda) base greases: ▪ More adhesive than Lime base ▪ Soluble in water – so not suitable for water service ▪ Good for temperatures up to 120℃ ▪ Used for high speed ball and roller bearings Mixed base greases: ▪ Mixture of Sodium and Calcium. ▪ Water resistant to a certain degree and can withstand higher temperatures than calcium base types Barium and Lithium base grease: ▪ Water resistant and suitable for high temperatures ▪ Extreme low temperatures of -50C ▪ Used in anti-friction bearings (roller or ball bearings) Aluminum base grease: ▪ Very sticky , stick well to metal therefore rust protection ▪ Unsuitable for high speed applications due to stickiness ▪ Good water resistance, good for temperatures up to 80°C Specialty Greases: ▪ Made of mineral oils thickened with solid lubricants such as graphite, mica, and talc ▪ Good for tractor rollers, cement mixers and excavating equipment (Heavy load) Liquid Lubricants Three general classes: 1. Mineral oils: ▪ From crude petroleum and most common 2. Fixed oils: ▪ Fatty oils, are animal or vegetable origin ▪ Include lard, whale oil, castor oil, cottonseed oil. ▪ Rarely used as lubricants but incorporated into greases or mineral oils for special applications 3. Synthetic oils: ▪ Polyglycols and silicones ▪ Suitable for high temperature applications ▪ Used as fire resistant turbine lubricants Properties of Lubricating Oils 1. Viscosity 2. Viscosity Index 3. Pour Point 4. Flash and Fire Points 5. Neutralization Points 6. Neutralization Number 7. Carbon Residue 8. Floc Point Viscosity: ▪ measure of the resistance of a liquid to internal deformation or shear; Liquids ability to flow ▪ Viscosity also indicates: a. Ability of an oil to support a load b. Power requirements to overcome internal friction c. Amount of heat produced due to internal friction ▪ Greatly affected by the temperature of the oil; As the temperature increases, the oil becomes less viscous and vice-versa ▪ Measured with a saybolt viscosimeter, units SSU (saybolt seconds universal) Viscosity Index: ▪ Measurement of how much viscosity of a certain oil changes with temperature changes ▪ High viscosity index means little change ▪ EG. High index wanted in automatic transmissions, good viscosity at operating temperatures as well as cold start-up (or lower temperatures) Pour Point: ▪ Lowest temperature at which the oil will flow ▪ Cold climates and refrigeration compressor oils need low pour points; otherwise oil will congeal Flash and Fire Points ▪ Flash point is the temperature at which the oil will give off sufficient vapour to ignite momentarily when mixed with air and exposed to an ignition source ▪ Fire point of an oil is the temperature when enough vapour is given off to burn continuously Neutralization Number: ▪ Indicate the acidity of the oil. ▪ When lubricating oils are in service they tend to oxidize and form acids Carbon Residue: ▪ Used to determine the amount of carbon which an oil will form when subjected to high temperatures ▪ Carbon will interfere with the functioning of the engine and compressor rings and valves Floc Point: ▪ Temperature at which the wax or other suspended particles in the oil will separate out of the oil Lubricant Additives Improve the characteristics by using additives: ▪ Anti-oxidants: decrease amount of oxygen combining with the oil, preventing corrosion of bearings, and sludge ▪ Detergent-dispersants: keep deposit forming substances in suspension ▪ Viscosity index improvers: reduce amount of viscosity change in an oil with temperature ▪ Antifoam agents: collapse air or vapour bubbles that form in oil ▪ Pour point depressants: lower the pouring point of oil ▪ Corrosion inhibitors: will form a protective film on metal surfaces and so reduce corrosion Selecting Lubricating Oils Turbine oils: ▪ Need to function as both a lubricant and cooling medium for the bearings ▪ Could also be used as a sealing medium ▪ Readily separated from water which might contaminate it, and should have corrosion inhibitors, antifoam and anti-oxidant additives Air Compressor Cylinder Oils: ▪ Suitable viscosity, if too high will not spread over cylinder walls, will cause drag on piston, if too low will not properly seal piston rings. ▪ Should have a low carbon residue Internal combustion engine oils: ▪ Withstand high temperatures in the cylinder walls, will evaporate and thicken and form carbon. ▪ Also lubricate crankshaft and bearings at low start up temperatures ▪ High viscosity index, anti-oxidants, detergent dispersants Refrigeration compressor oil: ▪ Low pour point so oil wont congeal at evaporating temperatures and will not react chemically with the refrigerant ▪ Some refrigerants are miscible with oil and reduce the viscosity Gear oils ▪ Low viscosity oil to prevent ‘dragging’ and excessive heating due to fluid frictions Please log into https://kahoot.it For additional practice, look for “Lubrication principles” under c0170874 Bearings Chapter 2 Objectives At the completion of this lesson, you will be able to: 1. Define boundary and fluid film lubrication 2. Describe shell (sleeve) bearings 3. Describe the construction and operations of antifriction and thrust bearings 4. Describe how to clean and replace roller and ball type bearings 5. Explain the causes of bearing failure Bearings The main function of a rotating shaft is to transmit power from one end of the line to the other It needs a good support to ensure stability and frictionless rotation The support for the shaft is known as a bearing Bearing Lubrication Many different bearing arrangements, each unique; it is necessary to provide lubricants which match the operating principles of the bearings and the conditions such as: Temperature Humidity Speed Two Types of bearing lubrication: 1. Boundary Lubrication 2. Fluid Film Lubrication Boundary lubrication: Fluid film lubrication: Surfaces are separated by only a Also called: Flood lubrication, amount of microscopic film lubrication between surfaces allows complete separation Certain amount of metal to metal contact exists, but friction and Only occurs if the bearing surface is flooded wear are reduced with oil and if the bearing is in continual motion Film strength is most important Rapidly rotating turbine shaft will force oil factor – grease or solid lubricant underneath it Bearings are classified under TWO main categories: FLUID FILM LUBRICATION : “Journal” (sleeve) Bearings – In which the rotating shaft has a sliding contact with the bearing which is held stationary. Load is transferred through a thin film of lubricant (oil) BOUNDRY LUBRICATION: “Rolling” (anti-friction) bearing- Due to less contact area, friction is much less than the sliding friction, hence these bearings are also known as antifriction bearing Shell or Sleeve (Journal) Bearings Usually constructed with a white-metal alloy (babbitt) lining carried on a cast iron or steel house Soft white-metal alloy is suitable for lining as it will yield or deform slightly to conform to load conditions Foreign particles can become embedded in the soft material, rather than scoring the shaft Shell or Sleeve (Journal) Bearings Bearing must provide sufficient clearance around the shaft Oil must be supplied in the LOW PRESSURE area of the bearing Low pressure side is located at the top of the bearing Methods of Oil Supply a) Intermittent lubricant supply; only suitable for small bearings that require only a few drops every few weeks or months b) Automatic oiler: wick-feed or gravity feed); must be refilled at regular intervals; otherwise bearings will run short of oil c) Oil ring (slinger ring): quite common on pump and motor bearings – lower part of the bearing house is filled with oil, oil ring rides on the shaft through a slot in the centre of the upper part Intermittent: Hand-operated oil can – Simplest and oldest method – Small bearings - require only a few drops a weeks Automatic oiler – Large equipment require a steady oil supply – Gravity feed, wick feed, etc – Has to be replenished at regular intervals Methods of Oil Supply Oil Ring Grooves are frequently used in the top half of the bearing, or non-pressure area, to distribute the lubricant evenly ahead of the pressure area Ring Oiled Bearings: Common on pump and motor bearings Lower part of bearing housing filled with oil Ring rides on the shaft through a slot in the centre of the upper bearing As shaft rotates, the ring picks up oil from the reservoir and drags it up through the bearing slot wear it is distributed Oil grooves in bearings Grooves are placed in the top half of the bearing to provide distribution of oil evenly ahead of the pressure area The ability of oil to lift and support heavy loads is dependant on hydraulic pressure which is brought about by the pumping action of the rotating journal or shaft; Grooves in the pressure area (bottom) will allow oil to escape and encourage metal to metal contact Corners of joints scrape oil from the shaft, therefore need to be rounded or chamfered Bearing Failure ▪ One of the first signs of bearing failure is a rise in temperature! ▪ Other signs are “Knocking” or other unusual noises (excessive wear) Caused by : 1. Improper viscosity in oil 2. Improper bearing design, oil groove, chamfer, clearance 3. Misalignment of shaft and bearing 4. Loss of bearing metal, corrosion or metal fatigue 5. Loss of oil supply 6. Oil temperature too high Bearing Failure Three ways to prevent bearing over heating: a) Special cooling water channel is cast in the bearing house through which the water flows; used for oil & greased bearings b) Special water coil is immersed in the oil basin of the bearing; oil picks up the heat when it passes through the bearing and transfers it to the water passing through the coil c) Oil circulates through an oil cooler, away from the bearing assembly; oil is then recycled through the bearing for further lubrication and heat removal Emergency Cooling of a Hot Sleeve Bearing Small bearings – sufficient to increase supply of oil Large bearings are more difficult to cool; heat produced can expand shaft and reduces the clearance in the bearing Large bearings in critical pieces of machinery have their temperatures monitored continually In case of a water-cooled bearing lubrication systems: a) Increase water flow to oil cooler b) If experiencing water or oil flow restriction, change to a standby lube oil cooler c) Additional lube oil coolers can be put in service Non-water-cooled bearings may use fans or air eductor horns to direct air on the bearing NEVER apply water to an overheated bearing; shrinkage or distortion of bearing cap my happen Forces on Bearings Shaft exert forces on bearings in two main directions: Radial direction: perpendicular to the axis; loads due to the weight of shaft (bearings designed for this movement are called radial bearings) Axial direction: “thrust” forces; force is parallel to the axis of the shaft (beatings designed for this movement are called thrust bearings) Bearing Designs Thrust and Radial Bearings come in a wide variety of designs: Plain sleeve (or shell) bearings Antifriction bearings Tilting pad bearings Bearing Designs Axial Thrust Bearings (Collar Thrust): Purpose is to prevent a rotating shaft from moving in an axial direction Machinery housing has cast-in bearing material (babbit) in locations where the thrust collars intersect Entire collar surfaces press against the bearing surfaces; no room for oil wedge to be formed Lubrication is of boundary type: load this type can carry is limited Bearing Designs Tilting Pad Bearings: Capable of handling extreme axial and radial loads Bearings no NOT permit metal-to-metal contact; establish oil wedges that carry entire load Bearing surface is in the form of pads which are free to tilt Permits oil wedges to separate pads from shaft collar Used with large steam turbines, where shaft position is critical and axial thrusts are great Tilt Pad Bearing Assembly Tilting Pad Thrust Bearing Kingsbury Thrust Bearing Bearing Designs Antifriction Bearings: Replace sliding friction with rolling friction Results in far less friction force than sliding, for a given load Because friction is nearly eliminated, the name “antifriction bearing” applies Ball bearings Roller bearings Needle bearings Tapered roller bearings Bearing Designs The rolling elements travel between two circular metal rings, known as “races” Rolling elements are uniform in shape, and have hard & highly polished surfaces Races also have hard and highly polished surfaces Ball Bearings Roller Bearings Bearing Seals To prevent foreign matter (dust, grit, water) from entering the bearing housing and the lubricant form leaving the housing seals are installed on the shaft where it enters the bearing housing Consist of felt, synthetic rubber, or leather rings, enclosed by their own steel casing and often fitted with a light spring to force the seal against the shaft Lubricating Antifriction Bearings The purpose of lubrication in each of the following bearing types is: Plain or Shell bearings: to separate the surfaces by means of a lubricating film; may be microscopic in thickness or thick enough to float the shaft Antifriction bearings: a. Protect balls, rollers, and raceways from corrosion b. Provide a seal to prevent dirt from getting into hearing housing c. Heat transfer medium to conduct away heat d. Provide lubrication to reduce small amount of friction, which is present even in the antifriction bearings Cleaning Antifriction Bearings (Ball & Roller) Cleaning without dismantling: 1. Remove all dirt from the outside of the bearing 2. Remove the end covers, spray solvent into the bearing to flush out old lubricant and sludge 3. Spray light lubricating oil into the bearing 4. Replace end covers and refill the beearing with the normal lubricant (oil or grease) Cleaning Antifriction Bearings (Ball & Roller) Cleaning without dismantling (if not possible to remove end covers): 1. Remove drain plugs and drain the old lubricant 2. Replace the plugs and fill the bearing with solvent 3. Run the machine without load for a short period 4. Stop, remove plugs, drain solvent/impurities (repeat 1-4 until clean) 5. Fill bearing with light oil, run machine for short period to remove solvent traces 6. Drain off light oil, and fill the bearing with normal lubricant Causes of Antifriction Bearing Failure 1. Poor quality, incorrect, or old lubricant: hard masses 1. Improper fitting: if force is applied through the balls or rollers, surface under the balls/rollers will be indented or nicked (brinelling or “true brinelling”) 1. Misalignment: uneven loading of the bearing, results in flaking of surfaces and excessive wear 1. False brinelling: occurs in stationary bearings subjected to vibration; produces indentation resembling brinelling in the race surfaces 1. High operating temperatures: metal tends to soften and excessive wear will result