ICA 2024 Steel Industry Analysis PDF
Document Details
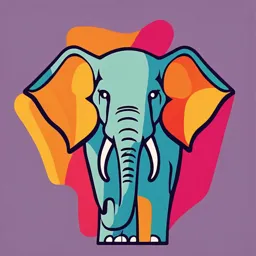
Uploaded by PraisingCerium
Tags
Summary
This document provides an overview of the steel industry, examining both the global and Indian steel sectors. The analysis includes historical context, current production figures, and an outlook for future trends. It also details relevant policies and initiatives. Key factors such as consumption, investment and raw materials are discussed.
Full Transcript
INDUSTRY AND COMPANY AWARENESS 1 INDEX SL NO 1.0 1.1 1.2 1.3 1.4 1.5 2.0 2.1 2.2 2.3 3.0 3.1 3.2 3.3 3.4 3.5 4.0 4.1 4.2 4.3 4.4 5.0 5.1 5.2 5.3 5.4 6.0 6.1 6.2 7.0 7.1 7.2 7.3 CONTENT PAGE NO GLOBAL STEEL SCENARIO & INDIAN STEEL INDUSTRY INTRODUCTION 4 GLOBAL SCENARIO 5 GROWTH OF INDIAN STEEL SECTO...
INDUSTRY AND COMPANY AWARENESS 1 INDEX SL NO 1.0 1.1 1.2 1.3 1.4 1.5 2.0 2.1 2.2 2.3 3.0 3.1 3.2 3.3 3.4 3.5 4.0 4.1 4.2 4.3 4.4 5.0 5.1 5.2 5.3 5.4 6.0 6.1 6.2 7.0 7.1 7.2 7.3 CONTENT PAGE NO GLOBAL STEEL SCENARIO & INDIAN STEEL INDUSTRY INTRODUCTION 4 GLOBAL SCENARIO 5 GROWTH OF INDIAN STEEL SECTOR 7 OUTLOOK FOR INDIAN ECONOMY 10 STEEL POLICIES AND RECENT INITIATIVES OF MOS 12 VISION, CULTURE AND CORE VALUES INTRODUCTION 21 CULTURE 22 CORE VALUES 22 SAIL – AN OVERVIEW FORMATION AND GROWTH : HINDUSTAN STEEL LIMITED 24 FORMATION OF SAIL 24 PRESENT STATUS OF SAIL 26 EXPANSION AND MODERNISATION IN SAIL 26 DIFFERENT PLANTS / UNITS OF SAIL 27 IMPORTANCE OF MOU FOR SAIL CONCEPT OF MEMORANDUM OF UNDERSTANDING 46 (MOU) THE MOU FRAMEWORK 46 DIGITAL DASHBOARD 47 MOU EVALUATION AND RATING 47 COMPANY STRATEGIES INTRODUCION 48 STRATEGY FORMULATION 49 SAIL’S TRYST WITH CORPORATE PLANS 50 SAIL VISION 2030 52 RAW MATERIALS FOR STEEL PLANTS MINES OF SAIL 54 SAIL MINES 56 TRANSPORTATION IN STEEL INDUSTRY INTRODUCTION 58 LAYOUT OF INTERNAL TRANSPORTATION SYSTEM IN 58 ISPS ROLE OF SUPERVISORS IN CONTROLLING COST 60 RELATED TO TRANSPORTATION 2 8.0 8.1 8.2 8.3 8.4 8.5 8.6 9.0 9.1 9.2 9.3 9.4 10.0 10.1 10.2 10.3 10.4 10.5 10.6 11.0 11.1 11.2 11.3 11.4 12.0 12.1 12.2 13.0 13.1 13.2 13.3 14.0 14.1 14.2 14.3 RELATIONS WITH EXTERNAL AGENCIES INTRODUCTION AREAS OF INTERACTION ORGANIZING PRODUCTION MARKETING OF PRODUCTS INTERFACE WITH GOVERNMENT AND MINISTRY IMPORTANT STAKE HOLDERS ENVIRONMENT MANAGEMENT IN SAIL INTRODUCTION ENVIRONMENT MANAGEMENT POLLUTION IN STEEL PLANT ESG CONCERNS AND GREEN STEEL MAJOR SERVICES IN STEEL PLANTS & THEIR ROLES FOUNDRY REPAIR SHOPS GAS UTILITIES & WATER MANAGEMENT RESEARCH AND CONTROL LABORATORY (RCL) REFRACTORY ENGINEERING CAPITAL REPAIR GROUP MAJOR FUNCTIONS IN STEEL PLANTS AND THEIR ROLES PRODUCTION PLANNING & CONTROL MANAGEMENT SERVICES DEPARTMENT (INDUSTRIAL ENGINEERING DEPT) MEDICAL & HEALTH SERVICES TOWN ADMINISTRATION SAIL SAFETY ORGANISATION INTRODUCTION ROLES & RESPONSIBILITIES TOTAL QUALITY PROCESS INTRODUCTION TOTAL QUALITY MANAGEMENT (TQM) AWARENESS OF ISO STANDARDS SUGGESTION SCHEME / QUALITY CIRCLES SUGGESTION SCHEME BUSINESS EXCELLENCE QUALITY CIRCLE 3 61 61 62 62 63 63 66 69 71 75 78 78 81 82 84 84 85 86 87 87 88 92 99 100 101 103 104 106 Chapter -1 Global Steel Scenario & Indian Steel Industry 1.1 Introduction Though Iron and steel have been used by men for almost 6000 years, yet the modern form of iron and steel industry came into being only during the 19th century. The growth and development of iron and steel industry in the world until the Second World War was comparatively slower. But the industry has grown very rapidly after the Second World War. By 1970, world steel production had reached 595 MT from 189 MT in 1950. However during 1970-2000, rate of growth of steel production somewhat slowed down due to static steel demand in the developed economies of USA, Europe, Japan and USSR and various geo-political crises such as the oil crisis of 1970s, Afghansitan war 0f 1980s and Asian currency crisis of 1997. World Steel production gained further momentum due to rise in production and demand in Asia particularly in China. In 1993, China overtook US and in 1996, it overtook Japan, as the top producer of steel. Since 2000, world steel production has grown rapidly on account of explosive growth of steel production in China. From a production figure of just 131 MT in 2000, China’s crude steel production rose to 1,013 MT in 2022 which was 54% of total world steel production. Steel production temporarily dipped in 2008 due to global financial crisis and in 2016 due to production clampdown by China. But otherwise Chinese steel production since 2000s have seen a steady growth rate. As per OECD (Organisation for Economic Co-operation and Development), following several years of decline until 2018, global steelmaking capacity has posted four consecutive years of growth in the period 2019-2022. The latest available information (as of December 2022) suggests that global steelmaking capacity grew to 2,459.1 MT by the end of 2022, an increase of 1.3% over 2021. Historical Background There are evidences that man knew the use of iron since the ancient civilization of Babylon, Mexico, Egypt, China, India, Greece and Rome. Archeological findings in Mesopotamia and Egypt have proved that iron or steel has been in the service of mankind for nearly 6000 years. The origin of the methods used by early man for extracting iron from its ores is unknown. In early days the iron produced probably was so relatively soft and unpredictable, that bronze continued to be preferred for many tools and weapons. Eventually iron replaced the non-ferrous metal for these purposes when man learned how to master the difficult arts of smelting, forging, hardening and tempering iron. 4 In the beginning, iron was smelted by charcoal made from wood. Later coal was discovered as a great source of heat. Subsequently, it was converted into coke, which was found to be ideal for smelting of iron. Iron kept its dominant place for 200 or more years after the Saugas works the first successful Iron Works in America, was founded in 1646. About the mid-19th century the new age of steel began with the invention of Bessemer process (1856) making steel available in large quantities at reasonable cost. Indian History Indian history is also replete with references to the usage of iron and steel. Some of the ancient monuments like the famous iron pillar near New Delhi or the massive beams used in the Sun Temple at Konark bear ample testimony to the technological excellence of the Indian metallurgists. The history of iron in India goes back to the ancient era. Our ancient literary sources like Rig Veda, the Atharva Veda, the Puranas and other Epics are full of references to iron and to its uses in peace and war. According to one of the studies, iron has been produced in India for over 3000 years, in primitive, small scale facilities. 1.2 Global Scenario Crude steel production 2022 (WSA) Total world crude steel production was 1,878.5 MT in 2022, down by 4.2% over 2021. India was the second largest producer of steel in the world in 2022. List of top ten producers of steel in the year 2022 is given below: Rank 2022 2021 %2022/21 1 013.0 1034.7 -2.1% 1 China 2 India 124.7 118.2 5.5% 3 Japan 89.2 96.3 -7.4% 4 United States 80.7 85.8 -5.9% 5 Russia (e) 71.5 77 -7.2% 6 South Korea 65.9 70.4 -6.5% 7 Germany 36.8 40.2 -8.4% 8 Turkey 35.1 40.4 -12.9% 5 Rank 2022 2021 %2022/21 9 Brazil 34.0 36 -5.8% 10 Iran (e) 30.6 28.6 8% Total Production of Crude steel; from 2017 to 2022-World, China, RoW World Steel Demand (WSA) The World Steel Association forecasts that the world steel demand will grow by 1.8% in 2023 and reach 1,814.5 Million T after contracting by 3.3% in 2022. In 2024, world steel demand will see a further increase of 1.9% to 1,849.1 Million T. China’s finished steel consumption in 2023 is expected to grow by 2.0% to 939.3 MT. Finished steel consumption in developed economies is likely to come down by 1.8% to 1814.5 MT in 2023 while the same in India is likely to shoot upto 126.1 MT, up by 8.6%. As per WSA, world steel demand has been feeling the impact of the high inflation and interest rate environment. Since the second half of 2022, the activities of steel using sectors have been cooling sharply both for most sectors and regions as both investment and consumption weakened. The situation continued into 2023, particularly affecting the EU and the US. Considering the delayed effect of the tightening monetary policy, WSA expects steel demand recovery in 2024 to be slow in the advanced economies. Emerging economies are expected to grow faster than developed economies. 6 1.3 Growth of Indian Steel Sector Steelmaking capacity in India has been expanding rapidly in recent years, and the country is now ranked second after China in terms of crude steel production. Further growth is expected in the medium to long term. The growth in the Indian steel sector has been driven by rising domestic demand for steel, low per capita steel consumption, domestic availability of raw materials such as iron ore and cost-effective labour. Consequently, the steel sector has been a major contributor to India’s manufacturing output. India was the world’s second largest steel producer in CY’2022 with a production figure of 124.7 MT, up by 5.5% y-on-y. In CY’2023, India is likely to produce 145 MT of crude steel. 7 Period Production for sale (MT) Import (MT) Export (MT) Consumption (MT) 2017-18 104.9 7.5 9.6 90.7 2018-19 101.2 7.8 6.3 98.7 2019-20 102 6.7 8.3 100.0 2020-21 95.1 4.7 10.7 94.1 2021-22 113.5 4.6 13.5 105.7 2022-23 121.3 6.02 6.71 119.7 Market Size India’s current crude steel production capacity stands at 161 MTpa. Unlike other large steel producers, the Indian steel industry is also characterized by the presence of a large number of small steel producers who utilize sponge iron, melting scrap and non-coking coal (EAF/IF route) for steelmaking. 8 Outlook for Indian Steel industry Following the initial spurt in domestic steel prices, due to onset of Russia-Ukraine war in February, 2022, prices started coming down from April, 2022 onwards, to mirror the falling international prices and weakening raw material prices. Imposition of Export Duties on Finished Steel by the Government of India in May, 2022, further accelerated the price decline.Consequently, in November, 2022, India’s Finished Steel Exports were only 0.34 MT, down by 53.1% over the previous year. As a result, many Indian mills opted for maintenance shutdowns due to non-remunerative steel prices. Such curtailed exports and falling steel prices, led to the domestic steel majors recording huge financial losses in Q3 of FY 2022-23. However, domestic steel prices started rising from December onwards supported by rising international steel prices and better performance by domestic end-user industries. While Indian Finished Steel Exports during the Financial Year 2022-23 were 6.71 MT, down by 50.2% as compared to previous financial year, imports were up by 29.0% to 6.02 MT. India’s Finished Steel Consumption during the year was 119.17 MT, up by 12.7% as compared to CPLY.Meanwhile domestic steel producers stayed on course to expand their production capacities. To promote production of Specialty Steel in India, the Ministry of Steel signed 57 MoUs with 27 companies under the Production Linked Incentive (PLI) scheme, which is expected to generate investment of about Rs.30,000 crore and create additional capacity of about 25 MT of specialty steel in next five years. In view of the rising concerns worldwide, the GoI has also started promoting Green Steel. The Centre plans to support Green Hydrogen based DRI projects as well as push primary steel producers to increase the usage of scrap in steel production. As per World Steel Association’s April, 2023 Short Range Outlook, after growth of 8.2% in 2022, India’s Finished Steel Consumption is expected to show healthy growth of 7.3% in 2023. India remained a bright spot in the Global Steel Industry in 2022. Having managed inflation well, the Indian economy is on a healthy growth track, with a rising share of investment in GDP, thanks to strong Government spending on infrastructure. The Real Estate sector is also expected to grow, backed by affordable 9 housing projects and urban demand. Private investment is improving on the back of the Production Linked Investment (PLI) Schemes. Steel Prices : Price regulation of iron & steel was abolished on 16.1.1992. Since then, domestic steel prices are determined by the interplay of market forces. Domestic steel prices are influenced by trends in raw material prices, demand – supply conditions in the market, international price trends among others. As a facilitator, the Government monitors the steel market conditions and adopts fiscal and other policy measures based on its assessment. The fluctuations in retail prices of steel (TMT, HRC and CRC) may be seen from the following graph: Road ahead India is the world's second largest producer of crude steel and its steel making capacity is projected to increase to about 300 MT by 2025. Huge scope for growth is offered by strong economy, India’s comparatively low per capita steel consumption and the expected rise in consumption due to increased infrastructure construction and the thriving automobile and railways sectors. Major threats include import dependency of coking coal, rising Chinese exports, overcapacity, worldwide focus towards Green Steel and high dependency on imports of steel making equipment 1.4 Outlook for Indian Economy India’s GDP grew by 7.2% in FY’22-23 as against 9.1% expansion in the previous fiscal. Despite the rate of GDP growth, coming at a slightly lower rate than the previous year, India remained one of the fastest growing economies among major global players. 10 The GDP growth of 7.2% was higher than the 7% median estimate in a Bloomberg survey as well as the Govt. forecast made three months ago. RBI successively raised Repo rates from a level of 4.0% in April’22 to a level of 6.5% in April’23 to contain the shooting inflation rate (CPI) which had reached eight year high of 7.8% in April’22. However, inflation has come down subsequently to 4.8% in June’23. Growth in Index of Industrial Production in the FY’22-23 was 5.1% as compared to 11.4% in the previous year. Growth in Manufacturing, Capital Goods and Consumer Durables sectors in FY’22-23 was 4.5%, 12.9% and 0.5% respectively as compared to 11.8%, 16.9% and 12.5% in the preceding year. India's merchandise exports faced tough conditions in FY’22-23, due to strong global headwinds and slowdown in major advanced economies. The merchandise exports in FY’22-23 rose to US$ 447.46 bn., up by just 6.0% over last year. Merchandise trade deficit during the year was US$ 266.78 bn. due to rising imports especially of coal, oil and gas. However, due to good performance of Services sector, overall trade deficit during FY’22-23 was US$ 122 bn. Government of India is giving strong impetus on infrastructure development and increased the outlay for capital investment in the Union Budget for the financial year 2023-24 by whopping 33% to Rs.10 lakh crore, which would be around 3.3% of GDP. Industry leaders have expressed confidence in the resilience of Indian economy. Amidst all the gloom enveloping the advanced economies, India has emerged as an island of hope for global investors, as its strong domestic demand rebounds after a pandemic-induced slowdown. 11 The automobile sector is considered to be a strong indicator of the prevailing economic scenario. India’s total automobile sales in the Financial Year 2022-23, as per Federation of Automobile Dealers Associations (FADA), witnessed a double-digit growth of 21%, at 2.21 crore nos. (approx.), wherein, all categories, except tractors saw a double-digit growth. Tractors sales, meanwhile, grew by only 8%. Forecasts for India GDP growth for FY’23-24 RBI 6.5% IMF 6.1% Fitch 6.3% ADB 6.4% Deloitte India S&P 6 – 6.3% 6% 1.5 Steel Policies and Recent Initiatives of Ministry of Steel A. NSP 2017 – Vision, Mission & Objectives Steel is a product of large and technologically complex industry having strong forward and backward linkages in terms of material flows and income generation. It is also one of the most important products of the modern world and of strategic importance to any industrial nation. From construction, industrial machinery to consumer products, steel finds its way into a wide variety of applications. It is also an industry with diverse technologies based on the nature and extent of raw materials used. In India, steel has an output multiplier effect of nearly 1.4 on GDP and employment multiplier factor of 6.8. 12 Today, the Indian steel industry contributes approximately 2% to the country’s GDP and employs about 5 lakh people directly and about 20 lakh people indirectly. The National Steel Policy 2017 (NSP 2017) is an effort to steer the industry to achieve its full potential, enhance steel production with focus on high end value added steel while being globally competitive. India’s competitive advantage in steel production is driven, to a large extent, from the indigenous availability of high grade iron ore and non-coking coal – the two critical inputs of steel production. In addition, it also has a vast and rapidly growing market for steel, strong MSME sector and a relatively young work force with competitive labour costs. Driven by the positive demand outlook and prevailing high prices of steel in the period post 2004, the Indian steel sector witnessed a wave of investments in the states of Odisha, Jharkhand, Karnataka and Chhattisgarh. Substantial new capacity was created and existing plants were modernized. A significant portion of these investments were funded by banks and other forms of borrowings. India today is 2nd largest steel producer in the world. There is significant potential for growth given the low per capita finished steel consumption of 82 Kg in India, as compared to world average of 224 Kg. Indian economy is rapidly growing with enormous focus on infrastructure and construction sector. Several initiatives mainly, affordable housing, expansion of railway networks, development of domestic shipbuilding industry, opening up of defence sector for private participation, and the anticipated growth in the automobile sector, are expected to create significant demand for steel in the country. Further, while the main focus of the industry is on the domestic market, being in close vicinity of the developed west and developing east, provides it a strategic location that augurs well for the industry seeking opportunities for exports of finished goods and imports of some scarcely available raw materials. Over the past two decades, the Indian steel industry has developed capabilities of producing a wide range of value added steel at par with global best practices addressing diverse needs of the end user industries. However, India still needs to make a special effort to domestically produce number of value added products like automotive steel for high end applications, electrical steel (CRGO), special steel and alloys for Power equipment, Aerospace, Defense and Nuclear applications. The Indian steel sector is disadvantaged due to limited availability of some of the essential raw material such as high grade lumpy Manganese ore & Chromite, coking coal, steel grade limestone, refractory raw material, Nickel, Ferrous Scrap etc. Due to shortage of domestic coking coal, both in terms of quantity and quality, pig iron producers/ BF operators in India have to significantly depend on import of coking coal. In the recent past, multiple issues have also adversely impacted the steel sector, viz. cancellations of iron ore and coal mine allocations, delays in land acquisition, environmental clearances, which led to many of the projects facing significant cost and time overruns. Additionally, companies also faced substantially increased operating costs on account of increased logistics & raw material costs and other charges. 13 Vision: To create a technologically advanced and globally competitive steel industry that promotes economic growth. Mission: Provide environment for attaining – i. Self-sufficiency in steel production by providing policy support & guidance to private manufacturers, MSME steel producers, CPSEs & encourage adequate capacity additions. ii. Development of globally competitive steel manufacturing capabilities iii. Cost-efficient production and domestic availability of iron ore, coking coal and natural gas iv. Facilitate investment in overseas asset acquisitions of raw materials. v. Enhance domestic steel demand. Objectives: The National Steel Policy aims at achieving the following objectives – i. Build a globally competitive industry ii. Increase per Capita Steel Consumption to 160 Kgs by 2030-31 iii. To domestically meet entire demand of high grade automotive steel, electrical steel, special steels and alloys for strategic applications by 2030-31 iv. Increase domestic availability of washed coking coal so as to reduce import dependence on coking coal from ~85% to ~65% by 2030-31 v. To have a wider presence globally in value added/ high grade steel vi. Encourage industry to be a world leader in energy efficient steel production in an environmentally sustainable manner. vii. Establish domestic industry as a cost-effective and quality steel producer viii. Attain global standards in Industrial Safety and Health ix. To substantially reduce the carbon foot-print of the steel industry NSP 2017 aims to increase focus on expansion of MSME sector, improve raw material security, enhance R&D activities, reduce import dependency and cost of production, and thus develop a “technologically advanced and globally competitive steel industry that promotes economic growth” eyeing self-sufficiency in production, developing globally economical steel manufacturing capabilities by facilitating investments and cost-efficient productions with adequate availability of raw materials. With focus on R&D, the technology would be of utmost focus over the next decade and MSME steel plants would be the key drivers to achieve the additional capacity required for India’s consumption led growth and improvement in the overall productivity and quality. Expected impact / outcome of NSP 2017 The following targets have been set in the NSP 2017: 14 The other expected impacts are as under: a) India to be world leader in energy efficiency and sustainability, in association with suitable agency, will constantly monitor techno-economic performance of all the steel plants within the country vis-a-vis the global best practices. Transfer of technology for production of automotive steel and other special steels will be facilitated by JVs with global leaders. b) 145 Indian Standards for steel and steel products have already been notified under the mandatory quality certification mark scheme of BIS. Efforts will be made to bring in additional steel products, which are used in critical end-use applications, under the mandatory scheme to ensure protection of human health, environment and safety. c) Attain global standards in Industrial Safety and Health The Ministry is coordinating with steel companies to ensure that on the job trainings on maintaining a safe workplace are provided to employees of the steel companies. d) Substantially reduce the Carbon footprint of the industry In order to address the environment related issues, the Ministry is facilitating the formation of a forum to chalk out best practices and is also focusing on development of a Waste Management Plan for the industry. e) Domestically meet the entire demand of high grade automotive steel, electrical steel, special steel and alloys. 15 Segment wise demand projections : Segments Demand (15-16) Infrastructure (oil refinery, highway, bridges, port, air-port, transportation, urban infrastructure, industrial sheds, pre-fab buildings) Construction (Real Estate) Demand (30-31) 9.5 90 23.5 45 Engineering & Fabrication (Capital Goods, Consumer Durables, boilers, General engineering) 35 43 Automotive 2.5 10 Railways 2 5 Packaging (LPG cylinders, grain bins, GI boxes) 2 6 Energy (power projects, transmission) Ship Building Oil & gas pipeline Defence, space, nuclear Others Total 3 11 4 3 4 2 11 230 wind mills, power 81.5 B. Policy for providing preference to Domestically Manufactured Iron and Steel Products (DMI&SP) Policy in Government Procurement The Government had introduced DMI&SP Policy on 8th May, 2017 to provide preference to domestically produced iron and steel material in Government tenders. Further, to fine tune this objective, the Policy was revised on 29th May, 2019 and on 31st December, 2020. The salient features of the Policy are as under: This policy provides preference to Domestically Manufactured Iron and Steel Products (DMI&SP) in Government procurement. The policy covers a list of 49 manufactured products of iron and steel. The policy also covers capitals goods for manufacturing iron and steel products. While earlier the domestic content was specified as 15-50% on the 49 products of iron and steel, the new list of 49 products have minimum prescribed value addition 16 ranging between 20-50%making it difficult for imported steel to compete with domestic bidders for government contracts. Each Ministry or Department of Government and all agencies/entities under their administrative control is under the purview of the DMI&SP policy as notified by the Ministry of Steel. All Central Sector Schemes (CS)/Centrally Sponsored Schemes (CSS) for which procurement is made by States and Local Bodies come within the purview of this Policy, if that project / scheme is fully / partly funded by Government of India. The policy is applicable to projects where the procurement value of iron and steel products is greater than Rs.5 lakh. The policy is also applicable for other procurements (non-project), where annual procurement value of iron and steel products for that Government organization is greater than Rs. 5 lakh. However, it shall be ensured by procuring entities that procurement is not split for the purpose of avoiding the provisions of this policy. The policy is applicable to purchase of iron and steel products by private agencies for fulfilling an EPC contract and/or any other requirement of Ministry or Department of Government or their CPSEs and also to capital goods for manufacturing iron and steel products in compliance to prescribed quality standards, as applicable. No Global Tender Enquiry (GTE) shall be invited for tenders related to procurement of iron and steel products. No Global Tender Enquiry (GTE) shall be invited for tenders related to procurement of Capital Goods for manufacturing iron and steel products having estimated value upto Rs. 200 Crore except with the approval of competent authority as designated by Department of Expenditure. The policy has provisions for waivers to all such procurements, where specific grades of steel are not manufactured in the country, or the quantities as per the demand of the project cannot be met through domestic sources. The policy is envisaged to promote growth and development of domestic steel Industry and reduce the inclination to use low quality and low cost (unfairly traded) imported steel in Government funded projects. Impact of the DMI & SP Policy The increased domestic value addition is expected to contribute to the vibrant steel sector and the associated industries by generating employment and domestic market for their products. This policy has provided and expected to provide significant savings to the Indian Economy and restrict the use of low quality and cheap imported steel in Government funded projects, alongside developing domestic capability for import substitution. DMI&SP Policy has so far resulted in import substitution of Rs. 26,600 Crore approximately. C. Steel Import Monitoring System (SIMS) for import data dissemination 17 Steel Import Monitoring System (SIMS) has been institutionalized which is an online platform for advance registration of intended imports of steel in order to provide granular data on steel imports, 0-60 days in advance to help the Ministry and the industry identify the exact grade being imported into the country in order to plan domestic manufacturing, besides giving advance warning about any surge in imports. SIMS platform was launched on 16th September 2019 for import consignments started at the Port of Entry w.e.f. 1st November 2019. SIMS has enabled the domestic industry to plan their pricing and production strategy and helped the country move towards Aatmanirbhar Bharat in steel making. D. Quality Control Orders/BIS Government has been facilitating supply of quality steel for critical end-use applications such as infrastructure, construction, housing and engineering sector. Ministry of Steel is the leading Ministry with maximum coverage of products under the BIS certifications marks scheme. A total of 145 Indian Standards on Steel and Steel products have been covered under Mandatory Quality Control Orders. These orders prohibit, import, sale and distribution of substandard steel products. The imposition of QCO is in the public interest or for the protection of human, animal or plant health, safety of the environment, or prevention of unfair trade practices, or national security as stated in the BIS Act, 2016. Through the aforementioned orders, Ministry of Steel has so far covered 99 Carbon Steel, 44 Stainless Steel and Alloy Steel products standards and 2 Ferro Alloys under the mandatory BIS Certification Scheme. In addition, as per the data of imported steel grades shared with BIS, more than 250 new steel grades have been included in the existing standards and 5 new standards are under preparation. This exercise is facilitating the upgradation of the Indian Steel Standards at par with Global Standards. This exercise is also facilitating indigenization of many of the imported steel grades for import substitution and “Make in India” initiative. QCO notified by Ministry of Steel and also the experience gained from the discussions held with the stakeholders have resulted in several benefits which are highlighted below: Strengthening of the Indian Standards and also formulation of new standards by BIS based on the information provided by Ministry of Steel. Promote indigenisation of the imported steel grades by bringing in the importers and the domestic steel producers together. Preventing unfair trade practices such as misdeclaration and under-invoicing of the imported steel consignments. Based on the information shared by Ministry of Steel, the relevant authorities have imposed measures such as ADD, penalties for misdeclaration, etc. E. other Key Initiatives : E.1 Production Linked Incentive (PLI) Scheme: PLI Scheme for domestic production of specialty steel has been approved with an outlay of Rs. 6322 crore by the Cabinet. The five broad categories of Specialty steel, identified under the scheme, are used in a variety of applications including white goods, automobile body and components, pipes 18 for transportation of oil and gas, boilers, ballistic and armour sheets, high-speed railway lines, turbine components, distribution and power transformers. The Scheme has been notified on 29.07.2021 and detailed Scheme Guidelines were published on 20.10.2021. The application process through online system was available from 29.12.2021 till 15.09.2022. The scheme is set to commence from FY:2023-24 (PLI to be released in FY:2024-25). 57 MoUs have been finalized out of 67 applications from 30 companies which were selected under the Production Linked Incentive (PLI) Scheme for Specialty Steel. This will attract committed investment of Rs. 29530 crore with a downstream capacity addition of 25 million tonne and employment generation potential of 70000. E.2 Decarbonization in Steel Sector: Ministry of Steel is continuously engaging with the stakeholders from the steel industry and the concerned stakeholder Ministries/ Departments such as Ministry of Environment, Forests and Climate Change (MoEF&CC), Ministry of Power, Bureau of Energy Efficiency (BEE), Ministry of New and Renewable Energy (MNRE), NITI Aayog etc to achieve net zero emissions by 2070. Detailed discussions on decarbonization and improvement of resource efficiency in Steel Sector were also held in meetings of Consultative Committees of Parliament on “Transition towards Low Carbon Steel-Green Steel on 6th May, 2022” and “Roadmap for Circular Economy in Steel Sector” on 1st July, 2022”. Further, Ministry of Steel hosted a session on the 6th Day of COP 27 event in Sharm-ElSheikh, Egypt on 11th November, 2022 wherein discussion was held on the issues of reducing carbon emissions hinging on technologies such as Green Hydrogen in steel making, Carbon Capture, Storage and Utilization (CCUS), Best Available Technologies on Energy Efficiency as well as transition to Renewable Energy. E.3 PM GatiShakti National Master Plan: With the help of Bhaskaracharya Institute for SpaceApplications and Geoinformatics (BiSAG-N) the infrastructure Ministries have uploaded their rail, road, port networks, etc. on PM GatiShatkti National Portal. Ministry of Steel has onboarded itself on PM GatiShakti Portal (National Master Plan portal) with the help of a mobile application created by BiSAG-N, by uploading the Geo locations of more than 2100 (Twenty one hundred) steel units (including big players) functioning in the country. The Geo location of all the Iron ore Mines and Manganese ore mines has also been uploaded. Ministry of Steel is in the process of uploading the geo locations of the existing slurry pipelines and the laboratories functioning in the steel sector. In addition, Ministry of Steel, in line with the goal of PM GatiShakti Master Plan, has identified 22 high impact projects to develop multimodal connectivity and bridge the missing infrastructure gaps. Planned expansion of railway lines, creation of new inland waterways, roads, ports, gas pipeline connectivity will result in creating much needed logistics solution which will drive the steel sector towards achieving its targeted goals by 2030-31, as delineated in NSP 2017. E.4 Engagement with Secondary Steel Sector: A major segment of iron and steel industry is the segment of secondary producers which contributes more than 40% to 19 the production of crude steel. The role of secondary steel sector in infrastructure development is immense. Not only does infrastructure development provide a stimulus to steel demand but steel intensive construction also leads to rapid building up of infrastructure. Considering the importance of this sector, which mostly consists of MSMEs, Ministry of Steel has organised a seminar under the chairmanship of Hon’ble Steel Minister with the aim of providing a platform to players in the Secondary Steel sector to share their views on the challenges faced by the sector and ways in which the Ministry can create an ecosystem in which the industry can thrive. The issues raised during the discussion were taken up with concerned Ministries such as Ministry of Finance, Ministry of Port, Shipping and Waterways, Ministry of Coal, Ministry of MSMEs and Ministry of PNG. Ministry of Steel also organized seminars at Bhuvneshwar, Indore, Roorkee and Surat to interact with secondary steel producers and consumers to enhance steel demand in the country. E.5 Steel Prices: Certain measures were taken by the Government to provide relief from high prices of crucial raw materials and intermediates, which included iron and steel. Accordingly, modifications were made in tariffs on raw materials of steel and other steel products vide notification dated 21.05.2022 whereby Import duty on Anthracite/Pulverized Coal Injection (PCI) coal, Coke and Semi-coke and Ferro-Nickel were reduced to zero. Export duty on Iron ores/ concentrates and iron ore pellets was raised to 50% and 45% respectively. In addition, 15% export duty was imposed on pig iron and several steel products. 20 Chapter – 2 Vision, Culture and Core Values 2.1 Introduction In an organization Mission/Vision leads to strategies. The long-term strategy leads to systems and structures. The right system and structure is driven by culture. For work culture to be conducive each member in the organization should have similar values and exhibit norms of behaviour in line with culture and values. Mission / Vision Strategies / Goals Systems Structure Culture Core Values SAIL Vision To be a respected world-class Corporation and the leader in Indian steel business in quality, productivity, profitability and customer satisfaction. Vision depicts the aspirations of an organization and gives substance to its existence. It defines boundaries for action and sets strategic direction for the organization. It can be compared to a beacon, functioning like a lighthouse for a ship. It is a distant goal that is always a challenge as the marketplace place throws up new and tougher challenges in the form of better technology, products and increased competition. The vision is never static and continuous focus on this long term aspect should be the focus of any organization that desires to excel. The Customer is seen to provide context for all our endeavors. The vision of SAIL has been evolved with this reality in mind. SAIL Vision was articulated in the Directors’ Workshop at Jodhpur. The SAIL Vision takes into account the realities of the environment and the core concern of the organization. Vision 2030: Long term strategic plan to steer the company towards a target of 50 million tonnes of hot metal production, thereby meeting the strategic objectives of 21 maintaining leadership position in Indian steel sector and a position amongst the top steel companies globally. 2.2 Culture In the most general sense, “Culture” could mean a ‘way of life’. Organization culture refers to the traditions, attitudes, beliefs and practices followed in an organization by the constituent members as an acquired habit. However, culture by itself cannot be observed. It can only be reflected in the observed behaviour of the employees : behaviour towards co-workers, towards customers, towards outsiders and most importantly towards ones’ job. For an organization to have a distinct culture, it is necessary that members of the organization behave in a given way in response to various stimuli every time. Culture of an organization is a consistent behaviour pattern that the employees imbibe as a part of their routine and which is consistent with a majority of the people at all times. Organization culture develops over a period of time and does not change overnight. It is a reflection of the observed attitude, values, norms, beliefs and responses by influential levels of the organization. SAIL is committed to inculcate and sustain a culture of creativity, involvement and innovativeness among employees to tap their creative potential. SAIL is also committed to building lasting relationships not only with employees but with all stakeholders for maximizing mutual benefit for sustained business while upholding the highest ethical standards. SAIL is committed to making a meaningful difference in the peoples’ lives. One should remember that in the final reckoning, it is the customer and not the employee alone who will measure customer satisfaction. It is important to undertake periodic reviews of the prevailing culture to ensure congruence between the existing culture and the requirements of the business environment. It may, therefore, be necessary to define and then cultivate a desired culture. 2.3 Core Values Consistent with Company’s vision, goals and strategies, SAIL adopted the following four Core Values in 1995: 1. Customer Satisfaction 2. Concern for People 3. Consistent Profitability 4. Commitment to excellence The meaning, rational and thrust of each of these Core Values is presented here. Customer Satisfaction: Customer comes first every time. Customer satisfaction is the first priority of every employee and the purpose of every job. We do not compromise this value because we believe that this alone can enable us to achieve the vision of attaining market leadership. 22 Concern for People: Talent of our people is our greatest asset. We believe that developing competence and commitment of our people for enhancing their contribution, is important for achieving customer satisfaction, and thereby the prosperity of the company and of the employees. Consistent Profitability: Consistent profitability is essential for growth. We believe that consistent and significant profitability must be essential outcome of all our activities. This is necessary for modernization, growth and market leadership. Commitment to Excellence: SAIL does it better. We are committed to harnessing the full potential of all our resources, through creativity, continuous improvements and teamwork. We believe that this is important for making SAIL the best organization so that our customers, employees and shareholders have a sense of pride. Norms of Behaviour The behaviour of everyone should reflect priority to the Core Value of customer satisfaction in relation to all other Core Values. Since our vision is to achieve market leadership through customer satisfaction, it is critical to establish and nourish all those behaviour, which we directly or indirectly contribute towards enhancing level of satisfaction of our customers on a continuing basis. Some examples of core values are given below: (a) Customer Satisfaction (i) Order booking should be communicated to Production Planning and Control (PPC) on the same day by the marketing branches. (ii) The PPC should start with quality and delivery commitment to customer. (b) Concern for People (i) Concern for safety and health of our employees and quality of their worklife should always guide all our decisions and actions. (ii) Every manager must communicate core-values both by words and actions behavioral deviations reflecting non-adherence to Core Values must be discouraged. (c) Consistent Profitability (i) We must continuously innovate methods to reduce costs in order to attain higher profitability. (ii) We must use all resources optimally and avoid the tendency of asking and giving more resources. (d) Commitment to Excellence (i) Rated capacity should be considered the minimum benchmark rather than the maximum limit. Besides measuring performance against past performance level and the target, Performance should also be evaluated against the potential to ensure 100 % achievement of potential in due courses. --- 23 Chapter – 3 SAIL: An Overview 3.1 Formation and Growth of Hindustan Steel Limited (1959-1973) When the Government of India decided to enter into the field of Iron and Steel production, it broadly envisaged not to run the firm as a departmental undertaking. Although initially steel project administration was directly under a Ministry of the Central Government, Hindustan Steel was formed as a Limited Company, with President of India owning the shares on behalf of the people of India. Thus Hindustan Steel Limited was set up on January 19, 1954. To start with, Hindustan Steel was designed to manage with only one plant that was coming up at Rourkela. For Bhilai & Durgapur plants, the preliminary work was done by officials in Iron & Steel Ministry. From April 1957, the supervision and control of the Bhilai & Durgapur Plants were also transferred to Hindustan Steel. The registered office was originally in New Delhi, moved to Calcutta in July 1956 and ultimately shifted to Ranchi in December 1959. Initially Bokaro Project was also under HSL. A new steel company Bokaro Steel Limited was incorporated in January 1964 to construct and operate the steel plant at Bokaro. The 1 MT phase of Bhilai & Rourkela Steel Plants were completed by end of December 1961. The 1 MT phase of Durgapur was completed in January 1962 after commissioning of wheel and axle plant. As a result, the crude steel production of HSL went up form 158 thousand tonnes (in 195960) to 1.6 MT (in 1961-62). 2.5 MT phase of Bhilai was completed on 2nd September, 1967 after commissioning of Wire Rod Mill. The last unit of 1.8 MT phase of Rourkela was Tandem Mill commissioned on 17th February, 1968 and 1.6 MT phase of Durgapur was completed on 6th August 1969 after commissioning of furnace in SMS. Thus, with the completion of 2.5 MT stage in Bhilai, 1.8 MT in Rourkela and 1.6 MT phase of Durgapur, the total Crude Steel output from HSL was raised to 3.7 MT in 1968-69 and 4 MT in 1972-73. 3.2 Formation of Steel Authority of India Limited (SAIL) The Committee of Public Undertaking of the Fifth Lok Sabha was the first Parliamentary Committee to undertake a significant review of the question of setting up a Holding Company for steel. It was first considered in the Department of Steel in 1971 with the following two objectives: Rapid growth of the industrial sector, of the economy, of the state as a leading agent of the growth process; and Ability of the Government to divert investment into areas which are strategic from the point of view of future development. 24 In this context, it was recognized that the Public Sector had to be made more efficient in order that it might be able to contribute far more than it had to the common pool of investible surplus in the economy. Further, such a holding company could perform a number of other important functions like coordination and control of constituent units, planning long term programmes, introduction of necessary technological changes, setting up of an R & D organisation and training of managerial personnel for the Public Sector as a whole. Based on the above considerations, the proposal to set up a holding company for Steel and associated input industries was approved by the Government in January 1972. Accordingly, the formation of Steel Authority of India Limited was approved by the Government in December, 1972. The company was incorporated on January 24, 1973 with an authorised capital of Rs.2,000 crores. SAIL formed in 1973, as a holding company, for : Hindustan Steel Ltd. (HSL) Bokaro Steel Limited (BSL) Salem Steel Limited (SSL) Hindustan Steel Construction Ltd. (HSCL) Bharat Coking Coal Ltd. (BCCL) National Mineral Development Corporation (NMDC) In 1978 SAIL was restructured as an operating company : Steel making subsidiaries of HSL, BSL and SSL were dissolved and merged HSCL, BCCL and NMDC were spun off as independent companies RINL set up in 1977 continued to be part of SAIL till it became a separate company in February’1982. Subsequently, companies taken over as subsidiaries : Indian Iron & Steel Company (“IISCO”) in 1979, (merged with SAIL in Feb.2006) Maharashtra Elektrosmelt Limited (“MEL”) in 1986 (merged in July’2011) Visvesvaraya Iron & Steel Limited in 1989 (merged with SAIL in 1998) Erstwhile Bharat Refractories Limited (BRL) merged with SAIL on 28th July’2009 and is known as SAIL Refractory Unit. SAIL Refractory Company Ltd. (SRCL), became SAIL’s subsidiary in December’2011 25 3.3 Present Status of SAIL Steel Authority of India Limited (SAIL) through its five integrated steel plants at Bhilai, Bokaro, Burnpur, Durgapur and Rourkela accounts for major steel production capacity of India. Three special steel plants at Bhadravati, Durgapur and Salem produce a wide range of special steels, special alloy steels and stainless steel. Chandrapur Ferro Alloy Plant is the only Public Sector Unit engaged in production of Manganese based Ferro Alloys in the Country Today, SAIL is one of the largest corporate entities. Its innate strength lies in its technologists and professionals and a trained manpower of over 57,000 as on 1.12.2023. During FY22-23, the company has clocked its best-ever production while achieving an all-time high revenue from operation of Rs.1,03,768 Cr. and EBITDA of Rs. 9,379 cr. 3.4 Expansion & Modernisation of SAIL: Steel Authority of India Limited (SAIL) has completed Modernisation & Expansion of its integrated steel plants at Bhilai, Bokaro, Rourkela, Durgapur &Burnpur and special steel plant at Salem including raw material resources and other related facilities. The Expansion Plan of SAIL, besides capacity enhancement, adequately addresses the need of SAIL Plants towards eliminating technological obsolescence, energy savings, enriching product mix, pollution control, and to introduce customer centric processes and have matching infrastructure facilities in the Plant to support higher production volumes. Items Hot Metal Crude Steel Saleable Steel Capacity Before Expansion 16.58 15.22 14.60 (Million Tonnes) Current capacity 21.79 19.15 18.00 Under the Modernisation & Expansion Plan of SAIL, new large size Blast Furnaces (>4000 m3 ), new state-of-the-art Rolling Mills such as Universal Rail Mill and Bar & Rod Mill at Bhilai Steel Plant, 4.3m wide Plate Mill at Rourkela, Universal Section Mill and Wire Rod & Bar Mill at IISCO Steel Plant, Medium Structural Millat Durgapur and Cold Rolling Mill with coupled pickling line & tandem cold Mill at Bokaro Steel Plant, have been installed. 26 3.5 Different Plants & Units of SAIL Bhilai Steel Plant (BSP) An agreement was signed in New Delhi on February 2, 1955 between the Government of India and Soviet Union to set up an integrated steel plant at Bhilai with a capacity of 1 MT of ingot steel. The plant began its operation on January 31, 1959 when Coke Battery No. 1 was commissioned. Production of Pig Iron at Bhilai began on February 4, 1959 when Blast Furnace No. 1 was commissioned. Situated in Chhattisgarh, this was one of the three 1 MTpa capacity crude steel plants set up in the Public Sector in the late fifties. Subsequently it was expanded to 2.5 MT ingot capacity. The plant was the first in India to produce wide (3600 mm wide) heavy plates. A major exporter of steel products, Bhilai specialises in shaped products, such as heavy rails, heavy structurals, merchant products and wire rods. Eleven times winner of Prime Minister's Trophy for Best Integrated Steel Plant in the country, Bhilai Steel Plant (BSP) is India's largest producer & supplier of world class rails for Indian Railways including world’s longest 130 metre rails in single piece and 260 metre long rail welded panels, and a major producer of large variety of wide and heavy steel plates and structural steel. The plant also specializes in other products such as wire rods and merchant products. The entire range of TMT products (Bars & Rods) produced by the Plant is of earthquake-resistant grade and superior quality. The plant also produces heavy structurals including channels and beams. Current production capacity of the plant is as under : Hot Metal – 6.28 MT (Million Tonnes) Crude Steel – 5.95 MT Saleable Steel – 5.55 MT Product Mix: Flat Long Product Mix Semis Rails & Structural Merchant products Wire & Bar rods Plates 27 Semis Rourkela Steel Plant (RSP) RSP was the first of the three steel plants taken up in the Public Sector. On December 31, 1953, an agreement was made between the Government of India and a Consortium consisting of Thyssen & Demag, Aktiengeselischaft, Duisburg, Germany to set up a steel plant of initial capacity of 0.5 MT subsequently a supplementary agreement was signed in July 1955 to set up a 1 MT plant. The Coke Oven Battery No.1 was commissioned on 3rd December, 1958 and the first of the three Blast Furnaces was commissioned on 3rd February, 1959. A major producer of diversified range of sophisticated steel products, RSP is among India’s few Plants producing 100% of the steel through the globally profuse Continuous Casting route since 1998. RSP is the only SAIL plant having capability to produce large dia pipes. Situated in Odisha, it was the first integrated steel plant in India to produce flat products and the first in Asia to introduce basic oxygen furnace (BOF) process at a time when this process was yet to receive recognition from the established steel producers at home and abroad. The plant produces a wide range of flat steel products like plates, hot and cold rolled coils and sheets, galvanized sheets, electrical steel sheets and large diameter electric resistance welded (ERW) and spiral welded (SW) pipes. The plant was expanded in the late sixties (1965-68) from 1.0 MT to 1.8 MT per annum ingot steel capacity. Continuous technological innovation has led to greater diversification in this plant’s product range. It also produces cold rolled non-grain oriented (CRNO) sheets. RSP is geared up producing defence and space quality plates through a Special Plate Plant. The Plant has undergone modernization upgradation in two phase. The Phase-I of modernization completed in 1994 and Phase-II modernization completed in 1997-98. After modernization, the capacity got augmented to 2 MTs of hot metal and 1.9 MTs of crude steel. Current production capacity of the plant is as under : Hot Metal – 4.65 MT (Million Tonnes) Crude Steel – 3.85 MT Saleable Steel – 3.67 MT Product Mix: Flat PRODUCT-MIX RSP 28 PRODUCT-MIX RSP Plate Mill Plates HR Plates HR Coils ERW Pipes SW Pipes CR Sheets & Coils Galvanized Sheets (GP& GC) CRNO steel Durgapur Steel Plant (DSP) Situated at a distance of 158 km from Calcutta, the Grand Trunk Road and the main Calcutta-Delhi railway line pass through Durgapur. It is situated on the banks of the Damodar river. Durgapur Steel Plant (DSP) set up in late fifties, is a leading producer of long products and is the pioneer in manufacturing and supply of forged Railway Wheels & Axles in the country. DSP started production with an initial crude steel capacity of 1 MPTA in 1959, which has been progressively increased to 1.8 MTPA during the modernization in nineties and further to 2.2 MTPA during recently completed Modernization & Expansion Plan (MEP). Current production capacity of the plant is as under : Hot Metal – 2.40 MT (Million Tonnes) Crude Steel – 2.20 MT Saleable Steel – 2.12 MT Unique feature of this plant is its Wheel & Axle Plant for making forged wheels and axles, catering to Indian Railways. Over the years plant has developed various types of wheels as per need of Railways. Products from DSP’s state of the art Medium Structural Mill (MSM) have been accredited with stringent CE marking certificate to promote their export. 29 Product Mix: Long Semis Product-mix Merchant products Structural Wheels and Axles Semis Bokaro Steel Plant (BSL) Bokaro Steel Plant ‘brings out before one’s eyes the vision of a massive giant in the making’. As the fourth steel plant in the Public Sector, conceived in 1959, it actually started taking shape in 1965 with the signing of an agreement with the Government of USSR on 25th January 1965. Envisaging a capacity of 1.7 MT in 1st stage and 4.0 MT in 2nd stage, its construction started on 6th April, 1968. Bokaro Steel Plant was originally incorporated as a Limited Company on 29th January 1964. After the formation of SAIL in 1973, it became a wholly owned subsidiary of SAIL and on 1st May 1978 it was eventually merged with SAIL in terms of Public Sector Iron & Steel Companies (restructuring) and Miscellaneous Provisions Act 1978. The plant was conceived as the country’s first ‘Swadeshi’ steel plant, to be built with maximum indigenisation going into the equipments, materials and know-how. Thus, this project has been a radical shift form the earlier dependence on foreign sources of know-how and consultancy, design and equipment, engineering, supervision and erection to almost a full measure of self-reliance and confidence. The Plant is hailed as the country’s first Swadeshi Steel Plant, built with maximum indigenous content in terms of equipment, material and know-how. Its first Blast Furnace started on 2nd October 1972 and the first phase of 1.7 MT Ingot steel was completed on 26th February 1978 with the commissioning of the third Blast Furnace. All units of 4 MT stage have already been commissioned and the modernisation taken subsequently has further upgraded this to 4.65 MT of liquid steel. Bokaro is designed to produce flat products like Hot Rolled Coils, Hot Rolled Plates, Hot Rolled Sheets, Cold Rolled Coils, Cold Rolled Sheets and Galvanised Plain Sheets/Coils. Bokaro is geared to provide a sure and strong raw material base for a host of modern engineering industries like motor vehicles, pipes and tubes, cold rolling units, barrel 30 and drum making and lately, LPG cylinders. Galvanized plain and corrugated sheets are finding use in industrial and domestic applications. Current production capacity of the plant is as under : Hot Metal – 5.69 MT (Million Tonnes) Crude Steel – 4.65 MT Saleable Steel – 4.24 MT Product Mix: Flat Product-mix HR Coils, HR Plates, HR sheets CR Coils and Sheets GPsheets/coils IISCO Steel Plant (ISP), Burnpur This full-fledged integrated steel plant is one of India’s oldest. Situated at a distance of about 200 kms from Kolkata in Burnpur on the banks of the perennial Damodar river in West Bengal, ISP is well connected by both South Eastern and Eastern Railways and National Highway 2. Its proximity to Kolkata and Haldia ports is an additional strength. Promoted by Burn & Co., the Indian Iron and Steel Company was incorporated on 11 March 1918. The iron works were set up at Hirapur. IISCO produced iron from an open-top blast furnace at Hirapur in West Bengal. An open-top blast furnace, had earlier been set up in 1870 at Kulti, by a company known as Bengal Iron Works Co. (BIW), founded by James Erskine. The plant was taken over by the Government in 1881. In 1889, it was taken over by the newly formed Bengal Iron & Steel Co. Around 1904, Bengal Iron & Steel Co. (BISCO) converted the open top furnaces into closed top furnaces, and installed facilities for producing steel, through open hearth furnaces. The unit held the proud distinction of being the owner of India’s “oldest unit producing pig iron by modern methods” at Kulti. BISCO was absorbed by IISCO in 1936 and steel making started as a regular measure in 1939. 31 Another company named Steel Corporation of Bengal (SCOB), incorporated in 1937, was also amalgamated with IISCO in 1952. SCOB’s Napuria Works and IISCO’s Hirapur Works in unison came to be known as the Burnpur Works of IISCO. The Burnpur Works underwent two overlapping expansion in 1953 and 1955, increasing its production capacity to 1 MT of ingot steel and 0.8 MT of saleable steel. IISCO had acquired iron ore mines at Gua and Chiria in what is today’s Jharkhand state and collieries in Chasnalla and Jitpur (also in Jharkhand) and Ramnagore (in Bengal). These captive sources of high quality raw materials gave IISCO a major competitive edge and enabled it to establish a prestigious reputation in domestic and foreign markets. It also became the first Indian blue chip company to have its shares traded at the London Stock Exchange. Despite growth plans, however, a combination of factors drove the company into stagnation and decline, resulting in lack of investment for technology upgradation to meet emerging market competition. IISCO was nationalised in 1972 and became a wholly-owned subsidiary of SAIL in 1979. The Indian Iron & Steel Company (IISCO), a SAIL subsidiary, was amalgamated with SAIL on 16th February 2006 and renamed IISCO Steel Plant (ISP). After undergoing a modernisation-cum-expansion programme, the crude steel capacity of the plant has been raised to 2.5 million tonnes per year. The facilities have been designed to produce best quality product with minimal environmental impact. The plant manufactures a range of products, over some of which it holds exclusive market dominance. Iron & steel produced by it has been acknowledged as being of the finest quality. Current production capacity of the plant is as under : Hot Metal – 2.77 MT (Million Tonnes) Crude Steel – 2.50 MT Saleable Steel – 2.42 MT Product Mix: Long Semis 32 Product-mix Wire Rod, TMT Re-bar Structurals Semis for sale Alloy Steels Plant (ASP) A pioneer in the production of alloy and special steels, Alloy Steels Plant (ASP), Durgapur was commissioned with an initial capacity of 1,00,000 tonnes of ingot steel and 60,000 tonnes of saleable steel. Through two phases of expansion and modernisation, the capacity has been revised to 2.46 lakh tonnes of liquid steel and 1.78 lakh tonnes of saleable steel. ASP is equipped with state-of-the-art technology for producing world class quality alloy and special steels. The plant has one slab-cum-twin bloom continuous casting machine, the only one of its kind in India. It is specially designed for casting special steels like Austenitic and Ferritic stainless steel and a variety of non-stainless steels including bullet-proof steel. ASP has the capacity to produce Slabs, Blooms, Bars, Plates and Forged items of over 400 grades in a wide range of sizes. Salem Steel Plant (SSP) Salem Steel Plant (SSP), is a premier producer of international quality stainless steel in India. Commissioned in 1981, Salem Steel Plant, a special steels unit of Steel Authority of India Ltd, pioneered the supply of wider width stainless steel sheets / coils in India. The plant can produce austenitic, ferritic, martensitic & low-nickel stainless steel in the form of coils & sheets with an installed capacity of 70,000 tonnes / year in Cold Rolling Mill & 3,64,000 tonnes / year in Hot Rolling Mill. Its steel melting shop can produce 1,80,000 tonnes of slabs per annum.In addition, the plant has country's first top-of-the-line stainless steel blanking facility with a capacity of 3,600 tonnes / year of coin blanks & utility blanks / circles. Under conversion scheme, value-added products like kitchen & tableware and doorframes are manufactured and supplied in bulk to corporates. SSP has also developed new applications of its products viz. LPG tanks for automobiles, stainless steel ceiling fans, exhaust fans, corrugated sheets, water tanks, etc. Visvesvaraya Iron & Steel Plant (VISP) Visvesvaraya Iron and Steel Plant (VISL) is a pioneer in production of high quality alloy & special steels and pig iron. Steel is produced through BF-BOF-LRF-VD route. The facilities include vacuum degassing, vacuum oxygen decarburisation, ladle refining furnaces, ingot teeming, continuous casting, 1600 Tonnes-hydraulic-high-speed forging press, a fully automatic horizontal long forging machine with high programmable Logic Controller system for a semi-automatic and automatic mode of 33 operation. VISL has an installed capacity of 2,16,000 tonnes of hot metal and 98,280 tonnes of alloy & special steels. Chandrapur Ferro Alloy Plant (CFP) Chandrapur Ferro Alloy Plant, (CFP) erstwhile Maharashtra Elektrosmelt Ltd. (MEL) has became a Unit of SAIL w.e.f. 12/7/2011. Chandrapur Ferro Alloy Plant is the only Public Sector Unit engaged in production of Manganese based Ferro Alloys in the Country. CFP has an installed capacity of 1,24,000 TPY Silico-Manganese. The product range of CFP includes High Carbon Ferro Manganese, Silico Manganese and Medium/Low Carbon Ferro Manganese. The Plant is accredited with Quality Assurance Certificate ISO 9001:2008. CFP's major production facilities include two nos. of 33 MVA and one no. 45 MVA Submerged Electric Arc Furnaces, two nos. Manganese Ore Sintering Plants, Furnace gas based Power Plant and 1 MVA Electric Arc Furnace for the production of MC/LC Ferro Manganese with Lime Calcination and Manganese Ore Roasting Unit. SAIL Refractory Unit (SRU) The erstwhile Bharat Refractory Limited (BRL) was merged with SAIL with effect from April 2007. Following merger it has now been renamed as SAIL Refractory Unit (SRU). It caters to the refractory needs of all SAIL Plants. Main objectives of SRU are: SRU has four production units, out of which three are situated in Jharkhand and one in Chhatisgarh. The units at Jharkhand include (i) Bhandaridah with a production capacity of 26,000 tons of Tap Hole Mass for Blast Furnace, various Castables and Fire Clay Bricks, (ii) Ranchi Road with a production capacity of 7,500 tons of Basic Masses and Magnesia carbon Bricks and (iii) IFICO, Ramgarh with a production capacity of 42,000 tons of Slide Gate Plate, different types of Castables and High Alumina Bricks. The unit at Chhattisgarh is situated in Bhilai is engaged in producing the entire range of basic and silica refractories. It also carries out calcination of lime in its high capacity rotary kiln, which is further used by Bhilai Steel Plant for iron & steel production. Captive Mines SAIL has the second largest mining outfit in the country after Coal India Ltd. Spread over the mineral rich states of Jharkhand, Odisha and Madhya Pradesh, the mines of SAIL started their operations as captive sources of raw materials of its integrated steel plants. By virtue of their locations and also having developed under the different steel plants for more than 2 to 4 decades, they present a picture of fascinating diversity, not only in the nature of their reserves/deposits but in their legacies as well, with each one of them being remarkably distinct from the other. 34 1) Iron ore Mines SAIL operates 14 iron ore mines spread over the states of Jharkhand, Odisha and Chhattisgarh. There are 22 mining leases held by SAIL for operation of these mines. Most of these leases were granted in the 50’s and 60’s or earlier and almost all of them are undergoing second/subsequent renewal/extension of lease along with various statutory clearances. State Mine JHARKHAND Kiriburu, Meghahatuburu, Gua and Chiria (4) ODISHA Bolani, Barsua & Kalta, Taldih (4) CHHATTISGARH Rajhara Mechanical, Mahamaya, Dulki, Jharandalli, Dalli Mechanical and Rowghat (6) Barring a few leases in Jharkhand, Odisha and Chhattisgarh, all other iron ore leases have been extended as per Mines & Minerals (Development & Regulation) (Amendment) Act, 2015. In addition, issue of execution of composite license for Thakurani (Block-A) is pending with Odisha Government. Iron ore Production : Iron ore mines of SAIL currently produce about 34 Million Tonne Per Annum (MTPA) of iron ore. Details of the iron ore produced during last five years including current year are placed below: Quantity: Million Tonnes MINE 2018-19 Kiriburu Meghahatuburu Gua Chiria (Manoharpur) 3.89 3.66 3.67 0.73 Bolani Barsua Taldih Kalta 5.63 1.86 0.30 1.72 Rajhara Mechanical Mahamaya Dulki Jharandalli Dalli Mechanical Rowghat TOTAL 3.52 2019-20 2020-21 JHARKHAND 3.91 3.83 3.73 2.97 3.69 3.10 0.74 0.55 ODISHA 5.92 6.24 1.75 2.26 1.01 1.09 1.71 2.49 CHHATTISGARH 3.46 3.98 2021-22 2022-23 2023-24 (Apr-Oct) 4.05 3.56 4.15 0.08 4.05 3.67 3.96 0.34 2.06 1.98 2.37 0.30 7.05 2.55 1.25 3.17 7.11 2.29 1.34 3.19 4.26 1.42 0.70 1.48 3.49 3.54 2.19 3.37 3.36 3.55 4.80 4.22 2.36 28.35 29.28 30.06 34.15 0.07 33.78 0.23 19.33 35 1.2 Coal Mines Coking Coal is critical raw material required by the steel industry. Indigenous availability of appropriate qualities of coking coal is limited due to which the steel industry is dependent upon imported coking coal. SAIL imports about 80-85% imported coal and blends it with coking coal from own washery and washed coking Coal available from CIL. SAIL has Chasnalla, Jitpur and Ramnagore working coal mines allocated to erstwhile IISCO. Chasnalla and Jitpur colliery are located in Jharia coal field, Dhanbad, Jharkhand and produce coking coal while Ramnagore Colliery is located in Raniganj coalfield which produces non-coking coal. Raw coking coal produced from Chasnalla and Jitpur mines is processed at Chasnalla Washery along with raw coal from BCCL/CCL sources. Presently about 0.7 Mtpa washed coking coal at 18% Ash is being produced from Chasnalla washery and supplied to steel plants. Middlings are also supplied to steel plants for power generation. In addition to above, washed coking coal is also supplied from BCCL/CCL washeries. Thermal coal produced from Ramnagore (West Bengal) is also supplied to steel plants through Chasnalla washery siding after blending it with the middling of Chasnalla Washery. SAIL is in the process of developing a 4 Mtpa raw coking coal mine at Tasra which is also located in Jharia coal field, Dhanbad. For development of a 4 MTPA, mine at Tasra Coal Block, Consortium of M/s Power Mech Projects Limited & M/s P C Patel Infra Pvt. Ltd. was appointed as MDO and Coal Mining Service Agreement (CMSA) was signed on 08.09.2023. 1.3 Limestone, Dolomite mines : In addition, SAIL holds captive mining leases of limestone and dolomite mines 1. Kuteshwar limestone Mines, M.P. 2. Nandini Limestone Mine, Chhattisgarh 3. Hirri Dolomite Mine, Chhattisgarh 36 Central Coal Supply Organisation (CCSO) CCSO, Dhanbad, is responsible for daily movement of washed Coking Coal and Power grade coal to all Integrated Steel Plants of SAIL and also coordinates movement of Raw Coal from BCCL to Chasnala Washery. Functions of CCSO 1) Linkage planning for all steel Plants under SAIL. 2) Proper assessment of quality of indigenous coal at loading points. 3) Liasioning with the Coal Companies to supply coal as per the desired quality and quantity to SAIL Plants. 4) Liasioning with Railways to supply rake as per the requirement plan of SAIL Plants. 5) Liasioning with third party for joint sampling of rakes at loading point. 6) Maintaining all records and statistics related to production and dispatch of coal. 7) Exploring new source of coking coal for washing at Chasnala and other Washeries. 8) Ensuring long terms security of Coking Coal for SAIL Plants through participation in linkage auction of Coking Coal conducted by CIL. 9) Meeting short term additional requirement of Coking Coal through participation in exclusive auction of Coking Coal conducted by CIL. Supply of Coal from CCSO SAIL / CCSO currently plans to supply approx. 2.6 MTPA of washed coking coal and 4 MTPA of Boiler coal from domestic sources including captive colliery at Chasnalla to different SAIL Plants. Central Marketing Organisation (CMO) : SAIL's marketing set-up, is the India's largest industrial marketing set-up. The Sales & Marketing of all prime products produced by SAIL is undertaken by Central Marketing Organisation (CMO), except for Stainless Steel produced by Salem Steel Plant (SSP) which is directly dealt by SSP. However, Mild Steel Hot Rolled Coils produced at Salem Steel Plant are sold through CMO. CMO handles prime products of the 5 Integrated Steel Plants & 2 Special Steel Plants, located across the Country in the states of West Bengal, Jharkhand, Odisha, Chhattisgarh& Karnataka. Total Sales during FY 2022-23 was about 16.2 MT, including 0.425 MT in exports. SAIL has been contributing in Nation building since inception by servicing the requirement of various Infrastructure Projects and also projects of Strategic Importance. The focus on Nation building has expressed itself in the growth of sales in different categories like TMT, Structurals and PM Plates. 37 Extensive Network: SAIL has the largest marketing network among all steel producers in the Country. As on 31st, March 2023, SAIL’s functional network of marketing offices consists of 37 Branch Sales Offices, 5 Customer Contact Offices, 18 Departmental Warehouses and 17 functional Consignment Agency yards, 2 Consignment handling agency yards. Marketing efforts are further supplemented through SAIL’s Retail Channel that reaches quality products to remote corners of India. The CMO Head Quarter is located at Kolkata. In addition to sale of steel products, other activities performed by CMO include Warehousing & Logistics, Branding & Brand promotion, Market Analysis and Research, Development of new products, Creation and Management of new Distribution Channels etc. SAIL exports steel products through its International Trade Division (ITD), New Delhi. Wide range of Products: The products handled by CMO include Hot Rolled Coils & Sheets, Cold Rolled Coils & Sheets, Galvanised Products, Plates, Reinforcement Bars, Structural, Rails, Wheels & Axles, Wire rods, Pipes & Tubes, Electrical Sheet, Semifinished Steels, Alloy Steel products, etc. in numerous grades and sizes. Inspired by the Government’s clarion call for “Atmanirbhar Bharat” and “Vocal for Local”, SAIL is relentlessly making efforts in developing grades/sizes, which can play important role in these Missions. The new grade of steel developed by SAIL’s Salem Steel Plant “Duplex Stainless Steel” is an effort in that direction. This steel has superior corrosion resistance with higher strength and formability and has been mainly imported so far. SAIL came up with new grades of steel like ISP: AWS A5.17 EM12K, 5.5 mm and AWS A5.23 EA2 (Mo bearing) at WRM for welding applications DSP: Ultra Low Nb Structural (E-350 BR) IS 2062 E410 C. Channel 300 was rolled at DSP for first time. BSP: IS 7887 CAQ Gr1 and EWNR Wire Rods 5.5/6/7mm at WRM RSP: HSFQ 450 and MC-30/40/55 at HSM II BSL: EN 10025-5/ IS 11587 HR Coils at HSM. International presence: International Trade Division of CMO, located at New Delhi, is responsible for exports of SAIL products. During 2022-23, SAIL Steel was exported to about 8 Countries. Major countries where exports of SAIL products have been undertaken in 2022-23 are UAE, Qatar, Saudi Arabia, Italy, Nepal, Sri Lanka, Bangladesh and Indonesia. During Q1 of 2023-24, 0.15 Million Tonne was exported to four Countries namely UAE, Italy, Nepal and Sri Lanka. To increase SAIL’s footprint globally, continuous efforts are being made to add new markets. Apart from traditional markets in the neighbouring region, exports are also being targeted in new markets of Europe and Canada. 38 SAIL has a leadership position in consumer mind space and is always striving to bridge the ever changing expectation gaps with improved services, products and processes. Some of the Marketing efforts and initiatives by SAIL are broadly listed below: Development of new products and customer outreach Continuous efforts are being made at SAIL to develop new products required by steel users. New products have been developed for various commercial and strategic applications like Steel for Shipping containers, Weather resistant steel for Vande Bharat Coaches, High Strength Steel for Pre-Engineered Buildings, Fire-resistant steel, Seismic grade TMT bars, Special steel plates for submarines, New Electrical steel grades, High Tensile Structurals & Plates with improved ductility for Defence, Various grades of API for Oil & Gas pipeline; High Tensile grades for EME segment, High Carbon Wire rods for Wire drawing, etc.SAIL supplied major portion of Stainless steel to Railways- Vande Bharat Coaches. SAIL has continued the thrust on ''NEX '' brand of structurals. Efforts have been made to popularise usage of steel in designing in general and increase usage of ''NEX '' Brand of SAIL Structurals through virtual meeting with customers, webinars and participated in virtual workshop sessions in-house and also by structural designers & Architects. To popularize and give impetus to the use of SAIL Structurals, company has undertaken various campaigns to promote NEX from SAIL. Further various creative designs and content have been developed which is being used in form of posters , banners , standee and hoardings during various customer meets/ Architect & Structural Designer meets to popularize NEX Brand of SAIL Structurals. In addition Tier I Distributors of Structurals are promoting NEX brand through advertisements/hoardings etc. SAIL has an extensive dealership network comprising more than 4800 dealers spread across the Country. SAIL is in the process of strengthening its retail channel to reach steel to the hinterland and individual steel consumers. In order to reach out to the end customer in the Retail Segment through an efficient distribution channel and providing value addition through products, delivery and services to customers, a 2-Tier Distributor Channel has been established by SAIL across the Country. For enhancing usage of steel in designs, SAIL has been conducting workshops/lectures at engineering colleges across the Country. Seminars have been held for architects and designers on the theme “New Challenges in Steel Design & Construction” for promoting steel structure designs. Cross functional teams comprising representatives from Marketing and Plants are formed for development of new products. Physical meetings/interactions over virtual modes are organized with various stakeholders to enhance product knowledge, facilitate product development and create product recognition and recall. 39 SAIL has been actively pursuing with various Ministries to put emphasis on Life Cycle Cost in projects and on Government initiatives aiding increased usage of Steel. SAIL participates in webinars, conferences, seminars, etc. on Steel and its’ usage conducted by Industry & professional associations and institutes, including sponsoring programs where deemed suitable. SAIL is actively utilizing its Social Media accounts like Twitter, Facebook, Instagram, LinkedIn, YouTube etc. for promoting Steel Usage. Important customers are provided single window service by a dedicated Key Account Manager. This has improved communication, quality of service and customer satisfaction, particularly for large customers who are spread over multiple locations across the Country and would otherwise need to contact SAIL at many points. Efforts to enhance Availability and Reach Towards digitalization AI based Chatbot ‘SAIL SARATHI’ has been introduced for facilitating easier navigation & information accessibility for customers and visitors. SAIL also owns an E-portal (www.sailsuraksha.com) where customers can book TMT orders online. In order to help promote and build acceptance of steel usage in rural areas, SAIL has an ongoing programme under “Gaon Ki Ore” campaign, for working with village level public decision makers, opinion makers, masons, builders, etc. Under the campaign, 363 workshops have been conducted during the financial year 2022-23 across the Country with focus on small consumers, etc. During Apr-May ’23-24, 90 workshops have been held. Research & Development Centre for Iron & Steel (RDCIS Research & Development Centre for Iron and Steel (RDCIS) is the corporate R&D unit of SAIL. Set up in 1972, RDCIS is registered under DSIR as an approved R&D unit. RDCIS is the nodal agency for product development and intellectual property management in SAIL. It undertakes R&D projects in diverse realms of iron and steel technology under the categories of Basic Research, Product Development, Plant Performance Improvement, Scientific Investigation and Development and Technical Services. RDCIS has around 121 dedicated and competent scientists and engineers who are specialists in their fields. RDCIS provides customers with prompt, innovative and cost-effective R&D solutions, develops and stabilizes new products and continually enhances the capability of its human resources to emerge as a centre of excellence. The major efforts are directed towards product development, cost reduction, quality improvement, energy 40 conservation and value-addition to products of SAIL and in providing application engineering support for products at customers’ end through a well established marketing network of SAIL. RDCIS offers technological services to various organizations in the form of transfer of know-how of technologies developed by RDCIS, consultancy services / contract research, specialized testing services and training. This helps to establish its credibility as a knowledge centre, besides generating revenue through external earning. RDCIS also enters into collaborative agreements with various institutes of national repute, Govt. of India organizations and international organizations to upgrade its knowledge base and develop new technologies and products. RDCIS plays an increasingly vital role towards meeting the current as well as future needs of the SAIL steel plants/ units and its external customers. This depends on the availability of research facilities and their utilization. The Centre has created state-of-art facilities to ensure in-depth scientific research in diverse fields of iron and steel technology. It is equipped with more than 500 advanced diagnostic equipment and 5 pilot facilities under 15 major laboratories. SAIL Safety Organisation (SSO) SAIL Safety Organization (SSO), a Corporate Unit set up in 1988 at Ranchi, monitors and guides the safety Promotional, fire and Occupational Health Services activities undertaken at different steel Plants/Units/Mines/Stockyards. To accomplish the above mentioned functions, SSO formulates and prepares appropriate safety policies, procedures, systems, action plans, guidelines etc. and follows up for their implementation and thereby helps in providing accident free work environment. Consistent efforts are also being made by SSO for competence building in the area of safety management through HRD interventions covering heads of shops, line managers, safety personnel & trade union leaders. A multi-disciplinary safety Engineering Departments exists in each of the steel plants and mines to look after their safety needs. The emphasis is now on Systematic Approach to safety Management. SSO is managing the secretariat of the Joint Committee on Safety, Health & Environment in the steel Industry (JCSSI), a bipartite forum which addresses steel plant safety, health & environment issues with active involvement of major central trade unions and management of major steel producers of the Country, on promoting safety. Occupational health and pollution control measures. Centre for Engineering & Technology (CET) Centre for Engineering & Technology (CET), is the design, engineering & consultancy unit of SAIL which was started in 1982. It has its Head Office at Ranchi, Sub Centres at 41 Bhilai, Durgapur, Rourkela, Bokaro and an IPSS Secretariat at New Delhi for formulation of Interplant Standards for Steel Industry. As a ‘solution provider for all project needs’, CET has been rendering complete range of services not only to the steel plants under SAIL but also to various clients other than SAIL – both within and outside the country. CET is also the nodal agency for acquisition and lateral transfer of technologies within SAIL plants. The range of services includes conceptualisation, project evaluation & appraisal, project consultancy, design & engineering and project management in the areas of iron and steel making. Apart from this, CET has been providing its services in the related areas like mine planning and development, infrastructural development, industrial piping, industrial warehousing, material handling system, industrial pollution control and environment management systems, water supply and sanitation, town planning, power projects, etc. CET represents a reservoir of technical & managerial expertise inherited over four decades of Indian Steel Industry. It has kept pace with changing times and made continuous efforts for updating skills of engineers through planned HRD programmes, collaborative arrangements with academia and other professional organisations of repute and acquiring up-to-date hardwares & softwares for engineering work. All of these are blended with a concern for clients’ profitability to ensure that the clients get the most cost effective solution, tailor-made for their requirement. Management Training Institute (MTI) This apex training institute for management training in SAIL was set up in 1962 in Ranchi to fulfil the managerial development needs of senior executives of the company and thereby act as a catalyst for achieving organizational goals. It is one of the first management training centres to be set up in the corporate sector in India. The Management Training Institute (MTI) assesses the training needs of senior executives, designs and executes need-based training programmes and disseminates modern management thinking through its publications. It is involved in preparing trainer manuals, case studies, exercises and business games. MTI designs company-wide HRD interventions, organizes senior level management workshops, conducts problem solving workshops for middle level executives and also leadership interventions for Junior level executives. MTI also offers some selected programmes to executives of other organisations. MTI, as a corporate institute, monitors the overall progress of training activities in SAIL. It conducts network meetings for selected and important programmes. E-abhigyan, the e-learning portal of SAIL has been developed and maintained by MTI with vast technical and managerial learning repositories and facility for online assessment and certification. E-abhigyan has helped in creating an anytime anywhere e-learning system for all employees of SAIL. 42 Environment Management Division (EMD) Environment Management Division (EMD), established on 23rd June, 1988, is the corporate unit of Steel Authority of India Limited (SAIL) headquartered at Kolkata and is certified with Quality Management System (QMS) linked with ISO 9001: 2015. The division is under the Directorate of Technical, Project & Raw Materials and headed by the Executive Director (EMD). The primary role of EMD is to apprise the management of environment and pollution control activities at plants, mines and units located across India. It also plays a pivotal role in consolidation of the efforts of the plants, mines and units towards environment protection and resource optimization through its multifarious activities. Overall activities of EMD are described below: SAIL, as a responsible corporate organization, is always committed to maintain a clean and sustainable environment in and around its plants and units by integrating sound environmental practices for control and prevention of pollution from all its activities. Growth Division (GD) Growth Division (GD) functions as a nodal agency for manufacture and supply of various spare parts and equipment to the SAIL Plants by utilizing available in-house 43 facilities and vendor base. GD functions focus on effective utilization of the engineering shops in the steel plants. Main objectives of GD are: – Effective utilization of captive engineering facilities of each steel plant. Providing technical help to manufacture specialised equipment to cater to present requirement as well as long-term expansion and modernisation. Undertake projects within SAIL plants or outside. Directorates at Corporate Office and SAIL Board Directorates at Corporate Office (CO) The main function of the Corporate Office is to integrate the functioning of Plants/Units to improve synergy of the total operations of SAIL. This is achieved through various Directorates of the Corporate Office as under: Technical, Projects & Raw Material Directorate Finance Directorate Personnel Directorate Commercial Directorate The Corporate Office is an overall policy-making body responsible for providing all the necessary help and support to the units for implementing the policies of the Company by coordinating with the various organizations and Government Departments. SAIL Board : The SAIL Board comprises of Four Functional Directors, two Government Directors & two Independent Directors and is headed by Chairman, SAIL. It enables SAIL to perform the following general functions at the corporate level. Long term strategic planning for the Company Policy formulation in consultation with plant personnel. Getting agreed action plans for implementation of the policies and ensuring their fulfillment. Achieving clarity and organizational commitment on objectives, goals and plans of action. Developing norms of performance in every functional area and ensuring commitment of progressively improved norms. Ensuring smooth and efficient operations and achievement of optimal performance of existing resources. Ensuring fulfillment of targets and orderly growth of the Company. Organizational development to maximize efficiency of the company. Reviewing performance of each unit with respect to target and suggesting corrective action where necessary. Achievement of well-coordinated functioning of different plants: improving interplant interactions, dissemination of knowledge and achieving synergy in Company’s operations. Centralized control of Finance, Sales, Purchase/ Import of inputs. 44 Capital investment decisions beyond power delegated to plant CEOs. Coordination with all external agencies, Central and State Governments Ministries, Railways, suppliers etc. in order to improve overall company operations. Development of an efficient and well-designed data bank and MIS at all levels within the organization to assist in problem identification and resolution. Projection of corporate image of the Company through media to the public in general. --- 45 Chapter – 4 Importance of MOU for SAIL 4.1 Concept of Memorandum of Understanding (MOU): The concept of MOU arose from the report of Arjun Sengupta Committee. SAIL was among the first Public Sector Undertakings to enter into MOU (first time in 1987-88). Since then, SAIL has been entering into MOU with the Ministry of Steel. Purpose and Scope of MOU: The purpose of the MoU is to measure the performance of SAIL on key selected parameters against the targets agreed upon so as to improve the critical performance indicators of the organization. The MOU envisages the performance expectations of Government of India from SAIL. The MoU enables SAIL to operate as an efficient public sector commercial enterprise within the broad policy objectives set by the Government and the requirements of Parliamentary Accountability. The MoU in respect to SAIL is being finalized by Department of Public Enterprises [DPE] on consolidated basis only (i.e. including all subsidiaries and JVs of SAIL). MoU target setting and its evaluation in respect of SAIL’s subsidiary maybe done by SAIL on the same principles as being followed for SAILby DPE. 4.2 The MOU Framework: The parameters included in the MoU process are market oriented reflecting the shareholders· interest in terms of growth in revenue, return on net worth, asset turnover ratio and market capitalization for listed CPSEs. The parameters are further indexed to past performance and future projections of the CPSE; vision of the Administrative Ministry; sectoral benchmarking and peer comparison (if any).Vision provided by the Administrative Ministry is also considered for Benchmarking. All the parameters are quantifiable and verifiable from the documents in public domain. Besides certain government's priorities/ programmes such as CSR, procurement from MSEs, etc. are alsoincluded for compliance by CPSEs. the non-compliance of which would result in deduction of full marks i.e., there would not be any partial deduction. 46 4.3 Digital dashboard: A digital dashboard with a centralized portal developed by DPE is being used for entering, signing, monitoring and evaluating MoU agreements. The CPSEs and Administrative Ministries would be on boarded with appropriate user roles. 4.4 MoU Evaluation: Once the Company’s data from its audited balance sheet and P&L Statement is available on the dashboard, the score would be automatically calculated against the benchmarked targets. There would be no adjustment in MoU agreement due to changes inMoU exchange rate, prices of raw material or finished goods or due to offset for any other reason as these are deemed to be normal business activity and audited statement of accounts declared shall prevail. The criterion for evaluation of score is as below: Proportionate marks for achievement of 50% to 100% Targets - Applicable to all parameters unless specified by DPE for a certain parameter. No marks for achievement below 50.00% of Targets. Score on all parameters would be added to arrive at aggregate score. Besides certaingovernment's priorities/ programmes such as CSR, procurement from MSEs, etc. are alsoincluded for compliance by SAIL, the non-compliance ofwhich would result in deduction offull marks i.e., there would not be any partial deduction. The Final aggregate Score is arrived at after deduction of marks towards noncompliance from the aggregated score. MoU Rating: The MoU rating ofCPSEs will be assigned as per the following Table: MoU Score >= 90 >=70 >=50 >=33