Rizal Technological University Civil Engineering Department PDF
Document Details
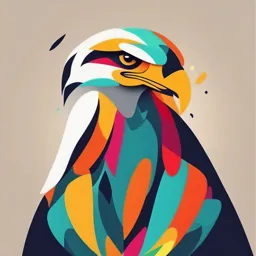
Uploaded by IrreproachableConflict2970
Rizal Technological University
Tags
Summary
This is a report on the Electrical Code, Fire Code, National Plumbing Code, and Sanitation Code of the Philippines from Rizal Technological University. The document contains information relevant to civil engineering.
Full Transcript
RIZAL TECHNOLOGICAL UNIVERSITY Boni Avenue, Mandaluyong City COLLEGE OF ENGINEERING CIVIL ENGINEERING DEPARTMENT ELECTRICAL CODE, FIRE CODE, NATIONAL PLUMBING CODE, AND SANITATION CODE OF THE PHILIPPINES GROUP N...
RIZAL TECHNOLOGICAL UNIVERSITY Boni Avenue, Mandaluyong City COLLEGE OF ENGINEERING CIVIL ENGINEERING DEPARTMENT ELECTRICAL CODE, FIRE CODE, NATIONAL PLUMBING CODE, AND SANITATION CODE OF THE PHILIPPINES GROUP NO. 2 ACTUAL WRITTEN NAME GROOMING REPORT REPORT 1. Aguilar, Schielouh Grace R. 2. Bautista, Althea M. 3. Cruz, Whincel Bernadette L. 4. Querubin, Jericho Ivan V. 5. Valencia, Gwyne Kole D. SUBJECT: BUILDING SYSTEM DESIGN (CE11) TIME/DAY: 7:30 AM - 9:30 AM / TUESDAY SECTION: CEIT-02-501E SUBMITTED TO: ASST. PROF. ZORAHAYDA V. CONCEPCION GROUP 2 CEIT-02-501E AGUILAR, SCHIELOUH BAUTISTA, ALTHEA GRACE R. M. CRUZ, WHINCEL QUERUBIN, JERICHO BERNADETTE L. IVAN V. VALENCIA, GWYNE KOLE D. TABLE OF CONTENTS I. Electrical Code of the Philippines Electrical Code of the Philippines (R.A. 11361)..........................1 Important Symbols Related to CE..............................................1 II. Fire Code of the Philippines Fire Code of The Philippines: R.A. 9514....................................6 Fire Protection in Civil Engineering.............................................6 Importance of Fire Code in Civil Engineering............................7 Fire-Resistant Building Materials................................................8 What to do to Prevent Fire?........................................................9 III. National Plumbing Code of the Philippines Plumbing Code of the Philippines...............................................11 Basic Principles in Plumbing Code.............................................11 Chapter 1 – Administration.........................................................13 Chapter 2 – Definitions...............................................................14 Chapter 3 – General Regulations...............................................14 Chapter 4 – Plumbing Fixtures...................................................15 Chapter 5 – Inspection and Test................................................16 Chapter 6 – Water Supply and Distribution................................16 Chapter 7 – Excreta Drainage System.......................................18 Chapter 8 – Indirect Waste Piping, Wet-Vented Systems and Special Wastes.......................................................................................20 Chapter 9 – Vents and Venting..................................................20 Chapter 10 – Traps and Interceptors..........................................20 Chapter 11 – Storm Drainage System........................................20 Chapter 12 – House Drains and House Sewers.........................21 Chapter 13 – Joints and Connections.........................................21 Chapter 14 - Quality and Weights of Materials, Plumbing Materials and Referenced Standards................................................................22 IV. Sanitation Code of the Philippines Sanitation...................................................................................23 Why Sanitation is Important?......................................................23 Sanitation Code of the Philippines (P.D. 856)............................23 Chapters of Sanitation Code of the Philippines Related to CE...23 Importance of Sanitation Code of the Philippines......................25 ELECTRICAL CODE OF THE PHILIPPINES ELECTRICAL CODE OF THE PHILIPPINES The Electrical Code of the Philippines is a set of regulations that governs the safe installation, maintenance, and operation of electrical systems in the country. It establishes the minimum standards for electrical wiring, equipment, and practices to ensure the safety of both people and property. In the Philippines, the electrical code is primarily based on the Philippine Electrical Code (PEC), which aligns with the National Electrical Code (NEC) of the United States. For civil engineering, the relevant electrical symbols are those that relate to building infrastructure and site development. IMPORTANT SYMBOLS RELATED TO CE Lighting Fixtures – Lighting fixtures are devices that hold light sources (bulbs or LEDs) and are crucial for illuminating spaces in buildings.Lighting fixtures are devices that hold light sources (bulbs or LEDs) and are crucial for illuminating spaces in buildings. Functionality and Safety: Proper lighting is essential for making spaces usable and safe. Poorly lit areas can lead to accidents or discomfort for occupants. Switches – Switches control the flow of electricity to lighting fixtures and other electrical devices. They are vital in managing the operation of electrical systems. Safety: Well-placed switches ensure that electrical devices can be turned off easily in case of an emergency or malfunction. PAGE | 1 Electrical Outlets – Electrical outlets (also known as receptacles) provide a connection point for electrical devices to access power. Power Access: Outlets provide the necessary access to electricity for devices and appliances. Without sufficient outlets, occupants may resort to unsafe practices like using multiple extension cords. PAGE | 2 Circuit Breaker and Panels – Circuit breakers and electrical panels are safety devices that manage the distribution of electrical power within a building. Electrical Safety: Circuit breakers prevent dangerous overloads and short circuits by automatically shutting off power when faults are detected, significantly reducing the risk of electrical fires and equipment damage. Conduits and Raceways – Conduits and raceways are protective systems that house electrical wiring, ensuring that wires are organized and protected from damage. Protection of Wiring: Conduits and raceways protect electrical wiring from physical damage, moisture, and environmental hazards, preventing costly repairs and ensuring system longevity. PAGE | 3 Fire Alarm and Safety System – provide early detection and notification in the event of a fire or other emergency. Life Safety: Early detection of fire through smoke and heat detectors saves lives by alerting occupants in time to evacuate. Fire alarms are a key component of building safety, reducing risks during emergencies. Emergency and Exit Lighting – guide building occupants to safety during power outages or emergency situations. Evacuation Safety: Emergency and exit lighting ensure that occupants can find their way out of a building safely during power outages or emergency situations. They are especially crucial in dark areas like stairwells or hallways. Code Compliance: Fire alarms are required by law in almost all types of buildings, and they must be installed and maintained to comply with local building and fire safety codes. PAGE | 4 Electrical Room and Spaces – an essential equipment, such as transformers, electrical panels, and other critical systems. Centralized Control: Electrical rooms house critical components like panels, transformers, and switchgear, centralizing the control and distribution of electricity throughout a building. These symbols are essential in civil engineering as they help integrate electrical elements into architectural and structural designs. The overall importance of electrical systems in civil engineering lies in their role in ensuring the safety, functionality, and efficiency of a building. Key components like circuit breakers, fire alarms, and GFCI outlets protect occupants from electrical hazards and emergencies, while lighting, outlets, and switches make spaces usable and convenient. Modern systems are also designed for energy efficiency, reducing consumption and operational costs. Additionally, all electrical installations must comply with building codes and safety regulations, ensuring the building is both legally compliant and safe for long-term use. PAGE | 5 FIRE CODE OF THE PHILIPPINES FIRE CODE OF THE PHILIPPINES: RA 9514 The Fire Code of the Philippines, or Republic Act No. 9514 (RA 9514), is legislation that outlines the country's fire safety standards. It serves as a framework that guides the Bureau of Fire Protection (BFP) in its crucial role of enforcement and implementation, particularly in its fire safety inspections and assigning the proper type of fire protection system applicable to a certain facility. It was enacted in 2008, and its Implementing Rules and Regulations (RIRR) were revised in 2019 to address current challenges. The Fire Code of the Philippines aims to raise national awareness and include everyone in fire prevention and suppression to lessen fire losses. R.A 9514 contains 17 SECTIONS FIRE PROTECTION IN CIVIL ENGINEERING Fire resistance ratings: Civil engineers must understand the fire resistance ratings of building materials and assemblies. These ratings determine how long a material or assembly can withstand fire exposure without failure. Fire-Resistant Construction: Designing structures with fire-resistant materials, such as fire-rated walls, floors, and doors, ensures occupant safety. Egress Routes: Properly designed escape routes (stairs, exits, etc.) are crucial for safe evacuation during a fire emergency. Fire Sprinkler Systems: Civil engineers collaborate with fire protection specialists to incorporate automatic sprinkler systems into building designs. Fire-Resistant Coatings: Understanding the use of fire-resistant coatings on structural elements (such as steel beams) enhances fire safety. PAGE | 6 IMPORTANCE OF FIRE CODE IN CIVIL ENGINEERING 1. Life Safety: o The primary purpose of fire codes is to safeguard human lives. By adhering to fire safety regulations, we reduce the risk of injury or loss of life during fires. o Properly designed fire exits, evacuation routes, and emergency lighting—all guided by fire codes—allow occupants to escape safely. 2. Property Protection: o Fire codes help prevent or minimize property damage during fires. They dictate fire-resistant materials, sprinkler systems, and fire alarms. o By following these codes, we reduce the impact of fires on buildings, infrastructure, and valuable assets. 3. Risk Reduction: o Fire codes address potential hazards, such as electrical wiring, flammable materials, and heating systems. Compliance minimizes fire risks. o Regular inspections ensure ongoing safety and identify any noncompliance issues. 4. Community Resilience: o A community’s resilience depends on its ability to withstand and recover from disasters. Fire codes contribute to this resilience. o When buildings meet fire safety standards, communities can recover more swiftly after fire incidents. 5. Legal and Regulatory Compliance: o Fire codes are legally binding. Noncompliance can result in fines, penalties, or even legal action. o Civil engineers, architects, and contractors must understand and apply fire codes to avoid legal repercussions. 6. Insurance Requirements: o Insurance companies often require compliance with fire codes. Buildings that meet safety standards are considered lower risk. o Compliance can lead to lower insurance premiums. PAGE | 7 7. Infrastructure Design and Construction: o Fire codes influence building design, materials, and construction methods. Engineers incorporate fire-resistant features. o From fire-rated walls to proper ventilation, fire codes guide infrastructure projects. 8. Emergency Response Coordination: o Fire codes facilitate coordination among emergency responders. They ensure that fire departments have access to water sources, hydrants, and clear routes. o Well-designed buildings aid firefighters during rescue operations. 9. Public Confidence: o When people know that buildings adhere to fire codes, they feel safer. Confidence in public spaces contributes to community well-being. 10. Preventing Large-Scale Disasters: o By implementing fire codes, we prevent catastrophic events like building collapses or widespread fires. o Tragedies can be avoided when professionals follow fire safety guidelines FIRE-RESISTANT BUILDING MATERIALS Concrete: Concrete’s behavior under high temperatures depends on its material composition. The quality of cement and aggregates affects fire resistance Steel: Steel is known for its structural integrity and high tensile strength, resisting termites, rust, and rot. However, it weakens under fire, with beams sagging and columns buckling above 600°C and melting completely at 1400°C PAGE | 8 Gypsum: Gypsum board, or drywall, is the most common fire-resistant interior finish. Its exterior paper burns slowly and doesn’t spread fire, while its noncombustible gypsum core contains water that turns to steam when heated, slowing heat transfer. Cast Iron: Cast iron is rarely used in construction due to its tendency to shatter when exposed to heat and then cooled. It is often covered with brick or concrete for stability. Stone: Stone can disintegrate under fire and sudden cooling. The effects vary by type: granite can explode under heat, requiring careful management, while limestone crumbles. Glass: Tempered glass, which is heat-treated for extra strength, and double-sided glass, which has two layers for added insulation, also provide improved fire resistance and safety. Brick and Mortar: A single brick can withstand a maximum temperature of 1200°C. This is a result of being created in a fire kiln. Although mortar is not as fire-resistant as a material, it is still effective and commonly used to create brick walls. WHAT TO DO TO PREVENT FIRE? Fire safety is crucial, whether at home, in the workplace, or anywhere else. Here are some essential tips to help you prevent fires: 1. Heating Safety: o Keep heaters, furnaces, and fireplaces clear of flammable materials. o Maintain proper clearance around space heaters. o Turn off heaters when leaving the room or going to bed. 2. Electrical Safety: o Avoid overloading electrical outlets. o Inspect cords and plugs for damage. o Never run cords under rugs or furniture. o Unplug appliances when not in use. 3. Kitchen Safety: o Stay attentive while cooking. o Keep flammable items (like towels and curtains) away from stovetops. o Use a timer to avoid forgetting food on the stove. PAGE | 9 4. Candle Safety: o Blow out candles before leaving a room or going to bed. o Use sturdy candle holders on flat surfaces. o Keep candles away from curtains and other flammable materials. 5. Smoking Safety: o Smoke outside and use proper ashtrays. o Never smoke in bed. o Dispose of cigarette butts safely. 6. Fire Alarms: o Install smoke alarms on every level of your home. o Test smoke alarms monthly and replace batteries as needed. 7. Escape Plan: o Create a fire escape plan for your home. o Practice it with your family regularly. o Know multiple ways to exit each room. 8. Fireplace Safety: o Use a screen or glass door to prevent sparks from escaping. o Never leave a fire unattended. o Dispose of ashes safely. 9. Appliance Safety: o Turn off and unplug appliances when not in use. o Regularly inspect electrical appliances for signs of wear. 10. Be Prepared: o Keep a fire extinguisher in your home. o Know how to use it. PAGE | 10 PLUMBING CODE OF THE PHILIPPINES In the late 20th century, in the time of American colonization, different kinds of sickness abrupted in the Philippines that alarmed Governor General Harrison. He ordered and issued a proper waste disposal to all municipalities and brought American Soldier - Engineers. n 1954, the third congress of the republic of the Philippines, approved after the third reading HB No. 962. The HB No. 962 became the Republic Act No. 1378 otherwise known as Plumbing Law of the Philippines on June 18, 1955 and it was signed by late President Ramon Magsaysay. On January 28, 1959, the National Plumbing Code of the Philippines was prepared by NAMPAP, and it was promulgated and approved by Malacanang, together with the passage of the law creating National Waterworks and Sewerage Authority (NAWASA). In 1966-1969, The Board of Examiners for Master Plumbers and the NAMPAP prepared a Curriculum for Plumbing Engineering that was approved by the Department of Education and was first introduced at the Feati University. The first ammendent of the Plumbing Code took on November 28, 1967 and was approved, where it includes asbestos-cement pipe material. Before Martial Law in 1972, Republic Act No. 6541 otherwise known as Building Code of the Philippines was passed and the Building Code was based and referred on the National Plumbing Code of 1959. In 1996, NAMPAP President Jaime n. Cabase spearheaded the updating of the Revised National Plumbing Code. In October 1999, NAMPAP submitted the draft code to the Board of Master Plumber chaired by Engr. Fortunato H. Amosco. After the review the Professional Regulation Commission under chairman Hermogenes Pobre adopted the Revised National Plumbing Code of 1999, which it was approved by President Joseph Ejercito Estrada last December 21, 1999 pursuant to Section 4 of R.A. 1378 known as The Plumbing Law. Basic Principles in Plumbing Code Principle No. 1 All premises intended for human habitation, occupancy or use shall be provided with a supply of pure and wholesome water, neither connected with unsafe water supplies nor subject to hazards of backflow or back-siphonage. Principle No. 2 Plumbing fixtures, devices and appurtenances shall be supplied with water in sufficient volume and at pressure adequate to enable them to function satisfactorily and without undue noise under all normal conditions use. Principle No. 3 Plumbing shall be designed and adjusted to use the minimum quantity of water consistent with proper performance and cleaning. PAGE | 11 Principle No. 4 Devices for heating and storing water shall be so designed and installed as to prevent dangers from explosion through overheating. Principle No. 5 Every building having plumbing fixtures installed and intended for human habitation, occupancy or use on premises abutting on a street, alley or easement where there is a public sewer, shall be connected to the sewer system Principle No. 6 Each family dwelling unit on premises abutting on a sewer or with a private sewage-disposal system shall have at least one water closet and one kitchen type sink. Further, a lavatory and bathtub or shower shall be installed to meet the basic requirements of sanitation and personal hygiene. Principle No. 7 Plumbing fixtures shall be made of smooth non-absorbent material, free from concealed fouling surfaces and shall be located in ventilated enclosures. Principle No. 8 The drainage system shall be designed, constructed and maintained to safeguard against fouling, deposit of solids, clogging and with adequate cleanouts so arranged that the pipes may be readily cleaned Principle No. 9 The drainage system shall be designed, constructed and maintained to safeguard against fouling, deposit of solids, clogging and with adequate cleanouts so arranged that the pipes may be readily cleaned. Principle No. 10 Each fixture directly connected to the drainage system shall be equipped with a water-sealed trap. Principle No. 11 Efficiency The drainage piping system shall be designed to provide adequate circulation of air free from siphonage, aspiration or forcing of trap seals under ordinary use. PAGE | 12 Principle No. 12 Vent terminals shall extend to the outer air and installed to preempt clogging and the return of foul air to the building. Principle No. 13 Plumbing systems shall be subjected to such tests to effectively disclose all leaks and defects in the workmanship. Principle No. 14 No substance which will clog the pipes, produce explosive mixtures, destroy the pipes or their joints or interfere unduly with the sewage- disposal process shall be allowed to enter the building drainage system. Plumbing Tests and Maintenance Principle No. 15 Proper protection shall be provided to prevent contamination of food, water, sterile goods and similar materials by backflow of sewage. When necessary, the fixture, device or appliance shall be connected indirectly with the building drainage system. Principle No. 16 No water closet shall be located in a room or a compartment which is not properly lighted and ventilated. Principle No. 17 If water closets or other plumbing fixtures are installed in buildings where there is no sewer within a reasonable distance, suitable provision shall be made for disposing of the building sewage by some accepted method of sewage treatment and disposal, such as septic tank. Plumbing Design and Implementation Principle No. 18 Where a plumbing drainage system may be subjected to backflow of sewage, suitable provision shall be made to prevent its overflow in the building. Principle No. 19 Plumbing systems shall be maintained in serviceable condition by Registered Master Plumbers. Principle No. 20 All plumbing fixtures shall be installed properly spaced, to be accessible for their intended use. Principle No. 21 Plumbing shall be installed by Registered Master Plumbers with due regard to the preservation of the strength of structural members and the prevention of damage to walls and other surfaces through fixture usage. Principle No. 22 Sewage or other waste from a plumbing system which may be deleterious to surface or sub-surface waters shall not be discharged into the ground or into any waterway, unless first rendered innocuous through subjection to some acceptable form of treatment CHAPTER 1: ADMINISTRATION Section 100 – A permit is required for any plumbing work under Republic Act No. 1378. Only Registered and Licensed Master Plumbers may perform such work. Section 101 – Permits may only be issued to licensed professionals. Section 102 – The application process involves detailed documentation of the work to be performed. PAGE | 13 Section 103-106 – Permit issuance, modifications to existing systems, and inspections are mandatory. Final connections to water, sewer, or storm drains need approval from the relevant authority. CHAPTER 2: DEFINITIONS This section states that specific terms in the Code will have the meanings given in this Chapter. Common words are not redefined unless their use is unclear or non- standard in the Code. Definitions are listed alphabetically by the first word of each term, not by the noun itself. CHAPTER 3: GENERAL REGULATIONS Section 301 – Wastewater must be properly disposed of via an approved drainage system. Section 302-307 – Regulations on the slope of horizontal drainage pipes, directions of flow, connections, and provisions for sewer access, all crucial for designing civil infrastructure. Section 315 – Hangers and Supports PAGE | 14 CHAPTER 4: PLUMBING FIXTURES Quality of Plumbing Fixtures: Dense Durable Non-absorbent material Smooth Impervious surfaces Free from unnecessary concealed fouling surfaces Acid resistant Section 409 – Floor Drains and Shower Stalls Floor Drains Considered plumbing fixtures, must have an approved hinge strainer plate. The strainer plate should have holes that allow water flow equal to the area of the drain pipe. The drain body must include a water-stop flange at mid-depth and an inside caulk outlet to ensure a watertight floor connection. Shower Receptors Also considered plumbing fixtures, they must meet specific Plumbing Material Standards. Made from materials like vitrified china, earthenware, ceramic tile, or porcelain enamel. Must meet acceptable standards before installation. Built with a finished dam, curb, or threshold at least 25.4 mm lower than the outside floor. Public shower floors should be non-skid and designed to prevent wastewater from flowing into adjacent areas. PAGE | 15 Gutters in public showers must have rounded corners, spaced no more than 4.9 meters apart, and sloped at least 2% for proper drainage. Section 410 - Plumbing Fixtures Required CHAPTER 5: INSPECTION AND TEST Scope: New plumbing work and any changes to existing systems that are affected by the new work must be inspected by the Administrative Authority. This ensures compliance with the Code and verifies that the plumbing installation meets approved plans and specifications. Advance Notice: The Registered and Licensed Master Plumber must notify the Administrative Authority at least three days before the work is ready for inspection. Responsibility: The permit holder must ensure that the work can pass all required tests before notifying for inspection. They must also provide all necessary testing equipment and facilities. CHAPTER 6: WATER SUPPLY AND DISTRIBUTION Section 601-606 – Potable water supply, proper piping materials, and cross-connection prevention (e.g., airgaps, vacuum breakers) are covered. This is directly related to civil engineering in managing municipal water supply systems. PAGE | 16 Section 603.4 – Specific Requirements Section 612 Section 613 and Section 614 Hangers and straps must not compress, distort, cut, or abrade pipes. They should allow for free movement of the pipes without damaging them. Pipe Support: Pipes must be supported at intervals of no more than 4 feet (1219 mm), especially at branches, changes in direction, or elevation. Trap arms longer than 3 feet (914 mm) must be supported as close as possible to the trap. Thrust Blocking: Thrust blocks must be installed at critical points such as: 1. Changes in direction (tees and bends), 2. Changes in pipe size (reducers), 3. Stops (dead ends), 4. Valves where thrust forces are expected. PAGE | 17 Section 612 Section 613 and Section 614 CHAPTER 7 – EXCRETA DRAINAGE SYSTEM Regulates the drainage systems for solid waste, including the design of building sewers, catch basins, and septic tanks, essential in urban planning and public health. Building Drain: That part of the lowest horizontal piping of a drainage system which receives the discharge from soil, waste and other drainage pipes inside the wall of the building and conveys it to the building sewer beginning 0.6 meter outside the building wall Building Sewer: That part of the horizontal piping of a drainage system which starts from the end of the building drain, and which receives the discharge of the building drain and conveys it to a public sewer, private sewer, individual sewage disposal system or other point of disposal. Cesspool: A non-watertight lined excavation in the ground which receives the discharge of a sanitary drainage system or part thereof, designed to retain the organic matter and solids discharging therefrom, but permitting the liquid to seep through the bottom and sides of the cesspool. PAGE | 18 Catch Basin: A receptacle in which liquids are retained for a sufficient period of time to allow settleable material to deposit. Septic Tank: A water-tight receptacle which receives the discharge of a sanitary plumbing system or part thereof, designed and constructed to retain solids, digest organic matter through a period of detention and to allow the liquids to discharge into the soil outside the tank through a system of open-jointed sub-surface pipings or a seepage pit meeting the requirements of this code. Privy and Privy Vault: An outhouse or structure used for the deposition of excrement and the vault is beneath the privy where excrement collects. Sump Pit: An approved tank or pit which receives sewage or wastewater and is located below the normal grade of the gravity system and must be emptied by mechanical means Manhole: A large opening in a sewer line or part of a plumbing system constructed with sufficient size for a man to gain access therein for maintenance purposes and facility for changes of line and/or grade of pipeline. PAGE | 19 CHAPTER 8: INDIRECT WASTE PIPING, WET-VENTED SYSTEMS AND SPECIAL WASTES Section 801 - Regulates the disposal of wastewater from systems such as evaporative coolers, cold storage rooms, and food preparation areas, emphasizing civil engineering's role in environmental sustainability. CHAPTER 9: VENTS AND VENTING Section 901-902 - Ensures that plumbing systems have adequate ventilation to avoid pressure buildup and back-siphonage, important in designing multi-story buildings and complex systems. CHAPTER 10: TRAPS AND INTERCEPTORS Section 1002 - Proper air circulation must be maintained throughout the entire drainage system using a vent pipe system that complies with the Code's requirements. CHAPTER 11: STORM DRAINAGE SYSTEM Section 1101- GENERAL Storm drainage systems are required for roofs, courts, and courtyards to collect stormwater and direct it to an approved disposal point, in compliance with relevant ordinances and regulations. PAGE | 20 CHAPTER 12: HOUSE DRAINS AND HOUSE SEWERS Section 120 l - SEWER REQUIRED Every building with plumbing or drainage piping must be connected to a public or private sewer system, unless exceptions are specified in Subsections 1201.2 and 1201.4. Exception: Single-family dwellings and accessory buildings connected to an approved private sewage disposal system before the construction of a nearby public sewer may continue using the private system, provided there is no hazard, nuisance, or unsanitary condition. Written permission from the Administrative Authority is required if there is insufficient grade for proper drainage flow to the public sewer. CHAPTER 13: JOINTS AND CONNECTIONS Section 1301 – TIGHTNESS Pressure tests on joints and connections of pipes and fittings in the plumbing system are required to ensure that they are both gas-tight and watertight. PAGE | 21 CHAPTER 14: QUALITY AND WEIGHTS OF MATERIALS, PLUMBING MATERIALS AND REFERENCED STANDARDS Section 1401- MINIMUM STANDARDS Materials Quality: All materials used in plumbing or drainage systems must be free from defects. Pipes, fittings, traps, fixtures, and devices must meet the specifications listed or labeled in Table 14-1 of this Code. TABLE 14-1 PAGE | 22 SANITATION CODE OF THE PHILIPPINES WHAT IS SANITATION? Sanitation refers to the measures, practices, and infrastructure implemented to maintain cleanliness and promote hygiene, particularly in relation to public health. It involves managing human waste, garbage, and wastewater to prevent the spread of diseases and ensure a safe and healthy environment. Proper sanitation is essential for preventing the transmission of infectious diseases and improving overall quality of life. WHY SANITATION IS IMPORTANT? Sanitation is essential for preventing the spread of infectious diseases, as it ensures that waste is properly managed and living environments are kept clean. By providing safe drinking water and reducing exposure to harmful pathogens, proper sanitation significantly improves public health, particularly in reducing child mortality. It also plays a vital role in promoting personal dignity and well-being, as access to clean facilities and hygienic practices is a basic human right. Additionally, effective sanitation contributes to economic development by enhancing productivity, reducing healthcare costs, and fostering healthier, more resilient communities. SANITATION CODE OF THE PHILIPPINES (P.D. 856) The Sanitation Code of the Philippines (Presidential Decree No. 856) serves as a comprehensive legal framework aimed at safeguarding public health and ensuring environmental protection through proper sanitation practices. Enacted in 1975, the Code establishes essential guidelines and regulations governing various aspects of sanitation, including waste management, water supply, food safety, and environmental pollution. It is designed to promote hygiene, prevent the spread of diseases, and ensure that public spaces, institutions, and businesses maintain a high standard of cleanliness. The Code plays a critical role in upholding the health and well-being of Filipinos, while also fostering sustainable development and environmental conservation across the country. CHAPTERS OF SANITATION CODE OF THE PHILIPPINES RELATED TO CE The Sanitation Code of the Philippines (Presidential Decree No. 856) covers various aspects of public health and sanitation, and many chapters are relevant to Civil Engineering in terms of planning, design, and infrastructure. Some of the most referenced chapters include: Chapter 2 - Water Supply This chapter addresses the proper design and maintenance of water supply systems, which is a key area in civil engineering. It includes standards for water sources, treatment, distribution systems, and storage facilities, ensuring safe and potable water for public consumption. PAGE | 23 Chapter 3 - Food Establishments Civil engineers may be involved in the design and construction of food establishments. This chapter sets sanitation standards for drainage, waste disposal, and ventilation systems in food-related buildings. Chapter 4 - Markets and Abattoirs Engineers are often responsible for designing these facilities, focusing on proper drainage, water supply, and sanitation to ensure the safe handling of food products and animals. Chapter 5 - Public Laundry Civil Engineers addresses the infrastructure and sanitation requirements of public laundry facilities, focusing on water and drainage systems, ventilation, and design to avoid contamination. Chapter 6 - School Sanitation and Health Services This chapter is important for civil engineers as it focuses on the design and maintenance of school buildings, including water supply, sanitation, and waste disposal systems. Engineers must ensure that schools have proper drainage, clean water access, adequate ventilation, and hygienic facilities, all of which are critical for maintaining a safe and healthy environment for students and staff. Chapter 7 - Industrial Hygiene This chapter is crucial for civil engineers involved in the design and construction of industrial facilities. It outlines standards for maintaining sanitary conditions, proper waste disposal, adequate ventilation, and drainage systems in industrial plants. Civil engineers ensure that these facilities are designed to prevent pollution, minimize health risks to workers, and maintain a safe, clean working environment. Chapter 8 - Public Swimming or Bathing Places This chapter involves standards for the design and construction of public pools, baths, and beaches, requiring civil engineers to ensure proper water quality, waste management, and drainage systems. Chapter 9 - Rest Areas, Bus Terminals, Bus Stops, and Service Stations This chapter is important for civil engineers as it provides guidelines for the design, construction, and maintenance of rest areas, bus terminals, bus stops, and service stations. It emphasizes the need for proper sanitation facilities, clean water supply, waste disposal, drainage systems, and ventilation, ensuring the safety and comfort of travelers while preventing health hazards in public transport infrastructure. PAGE | 24 Chapter 10 - Camps and Picnic Grounds This chapter is relevant to civil engineers as it sets standards for the design and maintenance of camps and picnic grounds. It highlights the need for proper sanitation, including waste disposal, drainage, water supply, and toilet facilities. Civil engineers must ensure these outdoor recreational areas are safe, hygienic, and environmentally sustainable to promote public health and protect natural resources. IMPORTANCE OF SANITATION CODE OF THE PHILIPPINES The Sanitation Code of the Philippines is crucial for building systems design as it sets forth essential standards for health and safety. By incorporating these regulations, building designs ensure that sanitation, waste management, and water supply systems are up to code, thereby preventing health hazards such as disease outbreaks and contamination. Compliance with the Code is not only a legal requirement but also a fundamental aspect of creating a safe and hygienic environment for occupants, which is essential for public health and safety. Moreover, adhering to the Sanitation Code enhances operational efficiency and environmental protection. Properly designed sanitation systems help reduce operational costs and minimize environmental impact by managing waste and water resources effectively. This leads to better public perception and comfort, as well as aligns with international standards for sustainability and health. Overall, integrating the Code's requirements into building systems design ensures that facilities are both compliant and well-suited to meet the needs of their users and the environment. PAGE | 25