Performance Evaluation of Geopolymer Bricks Incorporating GGBS and Fly-Ash PDF
Document Details
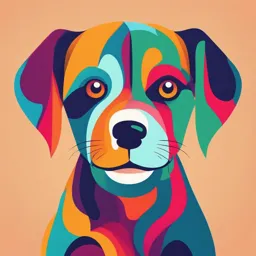
Uploaded by ConscientiousPiano
REVA University
2024
Mohammed Zaidulla
Tags
Summary
This is a presentation on the performance evaluation of geopolymer bricks incorporating GGBS and fly ash. The document includes an introduction, literature review, methodology, results, discussion, and conclusions, exploring the use of industrial byproducts in sustainable construction.
Full Transcript
Performance Evaluation of Geopolymer Bricks Incorporating GGBS And Fly-Ash BY, MOHAMMED ZAIDULLA SRN NO: R22TB026 Under the Guidance Dr. Sanjay Raj A PG Coordinator 10/08/2024 CONTENTS INTRODUCTION LITERATURE REVIEW OBJECTIVE METHODOLOGY RESULTS AN...
Performance Evaluation of Geopolymer Bricks Incorporating GGBS And Fly-Ash BY, MOHAMMED ZAIDULLA SRN NO: R22TB026 Under the Guidance Dr. Sanjay Raj A PG Coordinator 10/08/2024 CONTENTS INTRODUCTION LITERATURE REVIEW OBJECTIVE METHODOLOGY RESULTS AND DISCUSSION CONCLUSION REFERENCES 2 INTRODUCTION 3 INTRODUCTION Geopolymer bricks are a type of construction material manufactured from industrial byproducts and activated with an alkaline solution. They offer an eco-friendly alternative to conventional bricks, as they require lower energy consumption and produce fewer carbon emissions during production. Geopolymer bricks contain aluminosilicates or zeolites as the source material and utilizes an alkaline activator for the activation of polymerization reaction. Geopolymer bricks made with Fly-Ash requires higher curing temperature to achieve higher compressive strength and lower moisture absorption. 4 LITERATURE REVIEW 5 LITERATURE REVIEW SL Title Author Publisher Object Summery 1 Optimization of A.Fuzail Elsevier Optimize fly ash concrete Optimization of fly ash concrete fly ash concrete Hashmi, M. mix for sustainable mix for sustainable development. mix – a solution Shariq, A. Baqi development through for sustainable and Moinul experiments. Factors like water-binder ratio and development Haq - 2020 fly ash content affect compressive Develop regression model strength. for compressive strength based on design factors. Water-binder ratio influences concrete workability and strength Investigate the effect of values. fly ash proportion on concrete mix design. 6 LITERATURE REVIEW SL Title Author Publisher Object Summery 2 Experimental study on R Dharmaraj - Elsevier Reuse iron scrap and fly Study on iron scrap in concrete with strength and durability 2020 ash to enhance concrete fly ash for strength enhancement. properties of iron scrap strength. with fly ash based concrete Iron scrap improves concrete Determine optimal iron flexural strength, cost-effective scrap and fly ash mix for material in construction. concrete strength. Fly ash addition enhances load capacity, hardness index of iron scrap concrete. Concrete tested for compression, split tensile, prism, durability, abrasion. 7 LITERATURE REVIEW SL Title Author Publisher Object Summery 3 Fly ash for Dheeresh Kumar Else Evaluate fly ash Fly ash concrete reduces sustainable Nayak, P.P. vier conformity for concrete environmental impact by construction: A Abhilash, Rahul applications based on replacing cement in review of fly Singh, Rajesh various factors. construction. ash concrete Kumar and Studies show improved and its Veerendra Assess the impact of fly properties and durability of beneficial use Kumar - 2022 ash on concrete fly ash concrete. case studies properties and durability. Fly ash reduces water demand and enhances consistency in blended cement. FA in concrete lowers sulfate attack and improves microstructure. 8 LITERATURE REVIEW SL Title Author Publisher Object Summery 4 Effect of Fly Rahul Journal of Evaluate flexural Study evaluated flexural strength Ash on Upadhyay - Academia strength of PPC of concrete with varying fly ash Compressive 2014 and concrete with fly ash levels. Strength of Industrial replacement levels. Flexural strength increased up to Portland Research 30% fly ash replacement level. Pozzolona (JAIR) Investigate part PPC concrete showed potential Cement replacement of binder for fly ash utilization in Concrete PPC with fly ash. construction. 5 Experimental C. Indian Produce Geopolymer Study focused on geopolymer Investigation Banupriya, Journal of bricks and paver bricks and paver blocks using s on Sharon Science and blocks with Fly ash industrial waste. Geopolymer John, R. Technology and GGBS. Bricks/Paver Suresh, E. Geopolymerization process Blocks Divya and Compare strengths of involved mixing sodium D. Vinitha - Geopolymer concrete hydroxide and sodium silicate 2016 with OPC concrete. solution. 9 LITERATURE REVIEW SL Title Author Publisher Object Summery 6 Effect of Fly Alvin Journal of Compare fly ash Fly ash in concrete Ash on Harison, Academia and effect in PPC enhances strength, Compressive Vikas Industrial Research concrete with reducing natural resource Strength of Srivastava (JAIR) conventional cement consumption. Portland and Arpan concrete. Optimum fly ash Pozzolona Herbert - replacement level is 20% Cement 2014 Study fly ash as for increased strength. Concrete partial cement Workability decreases replacement on beyond 30% fly ash concrete strength. replacement due to water needs. 7 Geopolymer N. R. International Analyzing cost of Research on geo polymer Brick by Gowthami, Journal of Recent geo-polymer brick brick with multi-material using Flyash, A. Sivaji and Technology and and water absorption combination for GGBS, K. Ajay Engineering rates. sustainability. Silica Fume Kumar (IJRTE) Optimum proportions of and Kadapa Reddy - 2019 materials for compressive Slab Dust strength evaluation. 10 LITERATURE REVIEW SL Title Author Publisher Object Summery 8 Geopolyme R. Anu1 Journal of Compare geopolymer Geopolymer bricks made with M- r bricks and S. Emerging bricks with conventional sand have superior compressive using M- Thirugnana Technolog bricks in terms of strength. Sand sambandam ies and strength. - 2019 Innovative Acid resistance tests show Research Evaluate the compressive geopolymer bricks outperform (JETIR) strength, water conventional bricks. absorption, and acid resistance of geopolymer Sodium silicate and sodium bricks. hydroxide are used as activators. Geopolymer bricks with 5M NaOH have low water absorption. 11 LITERATURE REVIEW SL Title Author Publisher Object Summery 9 Experimental G. Asha Springer Study geopolymer Geopolymer concrete with GGBS and Investigation and Jiji Nature binder age effects fly ash enhances strength and durability. on Strength Antony - and microstructure. and Durability 2020 Geopolymers are eco-friendly of Fly Ash and Determine alternatives to Portland cement, reducing GGBS mechanical CO2 emissions. Based properties of Geopolymer geopolymer concrete Concrete with sisal fiber. 12 LITERATURE REVIEW SL Title Author Publisher Object Summery 10 Effect of Akshay Springer Explore Study on chemically activated fly ash Chemically Ajith and Nature phosphogypsum for concrete strength and durability. Activated Fly K. Gokul activation effect on Ash Raveendr fly ash cement Phosphogypsum enhances initial on Concrete an - 2020 systems. strength development and durability of fly ash mixes. Compare strength and durability of Activation effect occurs mainly in the chemically activated first 3-7 days. fly ash mixes. Improved strength and durability with 35% fly ash and 8% PG. 13 LITERATURE REVIEW SL Title Author Publisher Object Summery 11 Effect of Sathishraj Springer Nature Evaluate effect Investigated effect of alkaline Alkaline Mani and of alkaline solution content on geopolymer Solution Bulu Pradhan solution content concrete properties. Content - 2020 on GPC on Strength strength and Corrosion increased with higher and Chloride corrosion. alkaline solution content in Induced geopolymer concrete. Corrosion of Investigate Steel in corrosion Geopolymerization process Geopolymer behavior of influenced by various parameters Concrete steel like SiAl ratio, curing temperature. Made from reinforcement Fly Ash in geopolymer concrete. 14 LITERATURE REVIEW SL Title Author Publisher Object Summery 12 Relationship Lashhanth Springer Nature Correlate flexural Study on AAB concrete flexural Between Dhevaraju, and compressive and compressive strength Flexural E. Aakash strength of AAB correlation. and Reddy, Naga concrete using Compressive Dheeraj regression model. Regression model developed to Strength of Dogiparthy, predict flexural strength based Concrete and Develop standard on compressive strength. Made of Arkamitra equation for Alkali Kar - 2020 predicting flexural Comparison of models for Activated strength of AAB flexural and compressive Binder concrete. strength correlation accuracy. 15 LITERATURE REVIEW SL Title Author Publisher Object Summery 13 Fly Ash Based Niveditha Springer Investigate fly ash Fly ash geopolymer bricks as Geopolymer Balakrishna Nature geopolymer bricks as sustainable alternative to Bricks: n, S. Usha sustainable construction ordinary bricks. A Sustainable and Ponny materials. Construction K. Thomas - Geopolymer bricks with Material 2020 Optimize geopolymer optimized properties, brick properties for durability, and cost- durability and strength effectiveness. comparison. Comparison with cement and Study the influence of burnt clay bricks for strength curing time and and absorption. temperature on brick properties. Influence of curing time, temperature, and activator ratio on properties. 16 LITERATURE REVIEW SL Title Author Publisher Object Summery 14 Studies on the T. Saranya, Springer Develop eco-friendly Geopolymer concrete with sea Utilization of P. S. Ambily Nature GPC with sea and sand and crushed sand as fine Alternative and Bharati crushed sand as fine aggregate. Fine Raj - 2020 aggregate. Aggregate in Comparable or better Geopolymer Compare mechanical properties than river sand based Concrete and durability GPC. properties of GPC with river sand. Water absorption test results show differences between sand types. 17 LITERATURE REVIEW SL Title Author Publisher Object Summery 15 A review of Zipeng Elsevier Review studies on alternative Alternative bricks: material- studies on Zhang, Yat bricks from 1970 to 2017. oriented and process-oriented. bricks using Choy Geopolymerisation is preferable. alternative Wong, Arul Analyze properties, shaping materials Arulrajah methods, and future Glass-added brick properties: water and and Suksun opportunities in brick absorption, compressive strength, approaches Horpibulsu research. shrinkage. k - 2018 Reviewed studies: glass, plastic waste, sludge, slag, coal ash. Incorporating waste materials into bricks based on CSH or geopolymer. 18 LITERATURE REVIEW SL Title Author Publisher Object Summery 16 Geopolymer, Yanguang Elsevier Review GP materials, reaction Review of GP synthesis, green alkali Wu, Bowen kinetics, applications, and future applications, and future activated Lu , Tao Bai, challenges systematically. research cementitious Hao Wang, recommendations. material: Feipeng Du, Explore GP potential in fireproof Synthesis, Yunfei design using fly ash as materials. GP's potential in waste applications Zhang, Lu treatment, nuclear waste and Cai, Can immobilization, and challenges Jiang and ceramics. Wenjun Wang - 2019 Raw materials like metakaolin and red mud for GP synthesis. 19 LITERATURE REVIEW SL Title Author Publisher Object Summery 17 Development Rupali B. Građevinar Develop sustainable Sustainable geopolymer bricks and Kejkar and geopolymer bricks with fly ash, reduced alkaline optimisation Swapnil P. with reduced solution, good strength. of curing Wanjari - 2020 environmental temperature of burden and carbon Cured at 100-600°C, achieved energy- emissions. 10.2 MPa strength at 400°C. efficient geopolymer Minimize alkaline Economical, energy-efficient, bricks solution use and and environmentally friendly maximize fly ash solution for construction content in bricks. industry. Study effects of curing temperature on geopolymer bricks' mechanical properties. 20 LITERATURE REVIEW SL Title Author Publisher Object Summery 18 Properties of Lavanya B, IOP Develop geopolymer Geopolymer bricks with GGBS geopolymer Preet D Kuriya, Publishing bricks with fly ash and had higher compressive strength bricks made Suganesh S, GGBS. and better properties. with fly ash Indrajith R and Study properties like and GGBS Ramesh Babu compressive strength, Acid resistance increased with Chokkalingam - water absorption, and higher GGBS content in 2020 acid resistance. geopolymer bricks. 21 LITERATURE REVIEW SL Title Author Publisher Object Summery 19 Performance Preetha IOP Evaluate geo polymer Geo polymer concrete studies on Vellaichamy, Publishing concrete performance performance based on various Geo polymer Hariharan using various parameters analyzed in study. concrete Selvarajan, parameters. Arjun Analyze effects of Compressive strength Ramalingam, molarity of NaOH and increases with higher molarity and alkaline to fly ash of NaOH solutions. Kalaiyarasan ratio. Uthirasamy - Investigate split Split tensile strength improves 2020 tensile strength and with increased curing workability of geo temperature. polymer concrete. Superplasticizer enhances workability of geo polymer concrete. 22 LITERATURE REVIEW SL Title Author Publisher Object Summery 20 Investigation on Ramamohana Elsevier Investigate MOE Investigated modulus of modulus of Reddy Bellum, of fly ash-GGBS elasticity in fly ash-GGBS elasticity of fly Karthikeyan GPC at ambient geopolymer concrete. ash-ground Muniraj, and Sri curing conditions. granulated blast Rama Chand Compare MOE Proposed equation to calculate furnace slag Madduru - 2019 values with codes MOE based on compressive blended and literature for strength data. geopolymer prediction concrete accuracy. Geopolymers reduce CO2 emissions and enhance concrete performance. Geopolymer binders offer superior mechanical and durability characteristics. 23 LITERATURE REVIEW Literature Review Summary Geopolymer bricks are developing as a viable alternative to traditional clay or cement- based bricks, with significant advantages in sustainability and performance. Ongoing research and innovation are critical to overcome current constraints and promoting the wider use of geopolymer bricks as an environmentally friendly construction material. Despite some existing obstacles and downsides, geopolymer bricks are becoming more popular for their sustainability, versatility, and superior performance, making them an appealing option for modern building projects. These bricks not only offer significant sustainability, but also improved performance and energy efficiency, making them an excellent alternative for reducing the building industry's environmental footprint. 24 LITERATURE REVIEW Geopolymer bricks are poised to have a huge impact on the future of environmentally responsible construction around the world, thanks to ongoing advances in research, inventive inventions, and devoted initiatives to address adoption obstacles. 25 LITERATURE REVIEW Literature Review Gap Geopolymer Bricks and Paver Blocks: ❖ While the study explores the strength of geopolymer bricks, there is limited information on their thermal and acoustic insulation properties compared to conventional bricks. ❖ The long-term environmental impact and recyclability of geopolymer bricks have not been extensively studied. 26 LITERATURE REVIEW Effect of Alkaline Solutions on Geopolymer Concrete: The study highlights the effect of alkaline solutions on strength and corrosion but does not delve into the impact of different types and concentrations of alkalis on the microstructure of geopolymer concrete. The long-term durability and resistance to environmental degradation of geopolymer concrete exposed to varying levels of alkaline solutions need further investigation. 27 LITERATURE REVIEW Geopolymer Bricks with Fly Ash: ▪ The research discusses the compressive strength and acid resistance of geopolymer bricks but lacks detailed analysis on the brick's resistance to freeze-thaw cycles and other weathering effects. ▪ More work is needed to optimize the curing process, especially at lower temperatures, to make the production of geopolymer bricks more energy efficient. 28 OBJECTIVE 29 OBJECTIVE In the present dissertation work the following objectives are farmed, 1. To study the effects of GGBS and Fly-Ash on brick properties like Compressive strength and sustainability of Geopolymer bricks. 2. Examine the Water Absorption of Geopolymer brick via experimental research. 30 METHODOLOGY 31 METHODOLOGY Figure 1: Methodology 32 METHODOLOGY Material Preparation: Gather GGBS, Fly Ash, M-Sand, Sodium Silicate Solution and Sodium Hydroxide flakes. Ensure the materials are of high quality and meet standards. Material Specific Gravity BIS Code Book’s GGBS 2.9 IS 16714: 2018 Fly Ash 2.38 IS 3812-1&2 (2003) M-Sand 2.67 IS 2386 Sodium Silicate 2.13 IS 381 Sodium Hydroxide 1.53 IS 376 Table 1: Material Preparation 33 METHODOLOGY Mix Design: Blend ID Binders Alkaline solution S/B GGBS (%) Fly Ash (%) NaOH (8 M) NaOH (10 M) Na2SiO3 Mx1 100 0 204 - 516 0.6 Mx2 100 0 204 - 1650 1 Mx3 100 0 - 660 516 0.6 Mx4 100 0 - 660 1650 1 Mx5 75 25 204 - 516 0.6 Mx6 75 25 204 - 1650 1 Mx7 75 25 - 660 516 0.6 Mx8 75 25 - 660 1650 1 Mx9 50 50 204 - 516 0.6 Mx10 50 50 204 - 1650 1 Mx11 50 50 - 660 516 0.6 Mx12 50 50 - 660 1650 1 Table 2: Mix Design 34 METHODOLOGY Brick Formation: Mixed the materials thoroughly in the correct proportions. Made the brick blocks size of 190*90*90 Figure 2: Mixing Materials Figure 3 : Pouring in Molds Figure 4 : Bricks Obtained 35 METHODOLOGY Curing: Brick mold was left in the oven at 80°C for 24 hours. Number of bricks : According to the No of Testing days - 48 Geopolymer Bricks needed to be casted. Testing bricks: 7, 14 & 28 days Water Absorption test , Compression test 36 METHODOLOGY Figure 5 : Testing Compression Figure 6 : Placing Bricks in Oven Figure 7 : Bricks after Compression 37 RESULT & DISCUSSIONS 38 RESULT & DISCUSSIONS S No Blend ID Test 7 days 14 days 28 days (N/mm2) (N/mm2) (N/mm2) 1 Mx1 Compression Test 27.94 28.2 28.56 2 Mx2 Compression Test 16.24 17.56 18.89 3 Mx3 Compression Test 33.13 37.83 42.88 4 Mx4 Compression Test 45.48 45.91 46.48 Table 3: Compressive Strength for 7,14,28 days 39 RESULT & DISCUSSIONS S No Blend ID Test 7 days 14 days 28 days (N/mm2) (N/mm2) (N/mm2) 5 Mx5 Compression Test 59.77 62.34 65 6 Mx6 Compression Test 30.53 36.03 41.58 7 Mx7 Compression Test 29.74 31.42 33.2 8 Mx8 Compression Test 35 37.13 39.39 Table 3: Compressive Strength for 7,14,28 days 40 RESULT & DISCUSSIONS S No Blend ID Test 7 days 14 days 28 days (N/mm2) (N/mm2) (N/mm2) 9 Mx9 Compression Test 23.39 25.21 27.15 10 Mx10 Compression Test 27.94 29.46 31.19 11 Mx11 Compression Test 23.39 25.29 27.15 12 Mx12 Compression Test 27.14 28.38 29.74 Table 3: Compressive Strength for 7,14,28 days 41 RESULT & DISCUSSIONS Compressive Strength for 7 Days (N/mm 2 ) 70 59.77 60 50 45.48 Compressive Strength 40 35 33.13 30.53 29.74 30 27.94 27.94 27.14 23.39 23.39 20 16.24 10 0 7 days of 8M-0.6 7 days of 8M-1 7 days of 10M-0.6 7 days of 10M-1 100% GGBS 75%GGBS & 25% Fly Ash 50%GGBS & 50% Fly Ash Chart 1: Compressive Strength For 7 Days 42 RESULT & DISCUSSIONS Comp ressi ve S tren gth f or 14 Days (N/ mm 2 ) 100% GGBS 75%GGBS & 25% Fly Ash 50%GGBS & 50% Fly Ash 70 62.34 60 45.91 50 Compressive Strength 37.83 37.13 36.03 40 31.42 29.46 28.38 28.2 25.29 25.21 30 17.56 20 10 0 14 DAYS OF 8M -0.6 1 4 DAYS OF 8 M-1 14 DAYS OF 10M -0.6 14 DAYS OF 10M -1 Chart 2: Compressive Strength For 14 Days 43 RESULT & DISCUSSIONS Compressive Strength for 28 Days (N/mm2) 100% GGBS 75%GGBS & 25% Fly Ash 50%GGBS & 50% Fly Ash 70 65 60 50 Compressive Strength 46.48 40 41.58 42.88 39.39 30 33.2 31.19 28.56 29.74 27.15 27.15 20 18.89 10 0 28 DAYS OF 8M-0.6 28 DAYS OF 8M-1 28 DAYS OF 10M-0.6 28 DAYS OF 10M-1 Chart 3: Compressive Strength For 28 Days 44 RESULT & DISCUSSION C o m p re s s i v e S t re n g t h f o r 7 , 1 4 & 2 8 d a y s ( N / m m 2) 100% GGBS 75%GGBS & 25% Fly Ash 50%GGBS & 50% Fly Ash 70 65 62.34 59.77 60 50 45.48 45.91 46.48 Compressive Strength 42.88 41.58 39.39 40 37.83 37.13 36.03 35 33.13 33.2 30.53 31.19 31.42 29.46 29.74 29.74 30 27.94 28.2 28.56 27.94 28.38 27.15 27.15 27.14 25.21 25.29 23.39 23.39 18.89 20 17.56 16.24 10 0 7 days of 8M-0.6 14 days of 8M-0.6 28 days of 8M-0.6 7 days of 8M-1 14 days of 8M-1 28 days of 8M-1 10M-0.6 10M-0.6 28 days of 10M- 7 days of 10-1 14 days of 10-1 28 days of 10M-1 0.6 Chart 4: Compressive Strength For 7,14,28 Days 45 RESULT & DISCUSSION Analysis and Compliance with IS Specifications According to IS 1077: 1992 (Specification for Common Burnt Clay Building Bricks), the minimum compressive strength requirement for a Class 1 brick is 3.5 MPa. All bricks tested in this study far exceed this minimum requirement, indicating that they are suitable for structural applications. Mx1: 7 to 14 days: The compressive strength increased by 9.30%, demonstrating good strength development. This indicates effective pozzolanic reaction and hydration of cementitious materials. 14 to 28 days: The strength increased by 12.76%, showing continued strength gain, which is expected as the curing process progresses. The final strength of 28.56 MPa is well above the minimum requirement, showcasing the superior performance of the brick mixture. 46 RESULT & DISCUSSION Mx2: 7 to 14 days: The increase of 8.12% suggests a slower rate of strength gain compared to Mx1. However, the overall strength development remains consistent. 14 to 28 days: The 7.57% increase indicates low strength gain during the later stages of curing, resulting in a final strength of 42.88 MPa, still well above the IS specification minimum. Mx3: 7 to 14 days: The compressive strength increased by 14.18%, showing high early strength development compared to Mx1. 14 to 28 days: The increase of 13.34% indicates a plateau in strength gain, reaching a final strength of 46.48 MPa. This value, while greater than Mx1, still meets the IS requirements. 47 RESULT & DISCUSSION Mx4: 7 to 14 days: The 9.45% increase demonstrates a moderate rate of strength development. 14 to 28 days: The strength increased by 12.41%, resulting in a final strength of 65 MPa, indicating the greatest strength developed in the bricks. Mx5: 7 to 14 days: The 4.29% increase demonstrates a moderate rate of strength development. 14 to 28 days: The strength increased by 4.26%, resulting in a final strength of 41.58 MPa, indicating a balanced and consistent strength gain over time. 48 RESULT & DISCUSSION Mx6: 7 to 14 days: The 18.01% increase demonstrates a highest rate of strength development. 14 to 28 days: The strength increased by 15.40%, resulting in a final strength of 33.2 MPa, indicating a balanced and consistent strength gain over time. Mx7: 7 to 14 days: The 5.64% increase demonstrates a moderate rate of strength development. 14 to 28 days: The strength increased by 5.66 %, resulting in a final strength of 39.39 MPa, indicating a balanced and consistent strength gain over time. 49 RESULT & DISCUSSION Mx8: 7 to 14 days: The 6.08% increase demonstrates a moderate rate of strength development. 14 to 28 days: The strength increased by 6.08%, resulting in a final strength of 27.15 MPa, indicating a balanced and consistent strength gain over time. Mx9: 7 to 14 days: The 7.78% increase demonstrates a moderate rate of strength development. 14 to 28 days: The strength increased by 7.69%, resulting in a final strength of 31.19 MPa, indicating a balanced and consistent strength gain over time. 50 RESULT & DISCUSSION Mx10: 7 to 14 days: The 5.44% increase demonstrates a moderate rate of strength development. 14 to 28 days: The strength increased by 5.87%, resulting in a final strength of 27.15 MPa, indicating a balanced and consistent strength gain over time. Mx11: 7 to 14 days: The 8.12% increase demonstrates a moderate rate of strength development. 14 to 28 days: The strength increased by 7.35%, resulting in a final strength of 29.74 MPa, indicating a balanced and consistent strength gain over time. 51 RESULT & DISCUSSION Mx12: 7 to 14 days: The 4.56% increase demonstrates a moderate rate of strength development. 14 to 28 days: The strength increased by 4.79%, resulting in a final strength of 28.56 MPa, indicating a balanced and consistent strength gain over time. The compressive strength results, analyzed in terms of percentage increases and compared against IS specifications. 52 RESULT & DISCUSSION Brick samples: 1. Mx5 consistently showed the highest strength and significant strength gains over time, indicating excellent material performance. 2. Mx3, Mx4 & Mx6 also performed well, with good strength development and final strength. 3. Mx7, Mx9, Mx11, Mx12, Mx10, Mx8 & Mx1 displayed moderate but consistent strength gains. 4. Mx2 displayed lowest strength gains, meeting the IS requirements. 53 RESULT & DISCUSSION Overall, the incorporation of 78% GGBS and 25% Fly-Ash in brick formulations proved beneficial, particularly for Mx5, which demonstrated superior strength and durability. The findings support the use of GGBS and Fly-Ash as an effective supplementary cementitious material in sustainable brick production. From these results, it is evident that the mixture containing High amount of GGBS consistently outperformed other formulations. The progressive increase in Compressive Strength with curing time indicates good pozzolanic activity and effective strength development in the bricks. 54 RESULT & DISCUSSIONS S No Trails Test 28 days 1 100% GGBS Water Absorption Test 0.94% 2 75%GGBS & Water Absorption Test 2.6% 25% Fly Ash 3 50%GGBS&50 Water Absorption Test 3% % Fly Ash Table 4: Water Absorption Percentages for 28 days in 8M Brick 55 RESULT & DISCUSSIONS S No Trails Test 28 days 1 100% GGBS Water Absorption Test 0.94% 2 75%GGBS & Water Absorption Test 4.17% 25% Fly Ash 3 50%GGBS&50 Water Absorption Test 5.31% % Fly Ash Table 5: Water Absorption Percentages for 28 days in 10M Brick 56 RESULT & DISCUSSIONS Max Percentage of Water Absorbed (%) 3 Percentage of Water Absorbed 3 2.5 2.6 2 1.5 1 0.94 0.5 0 100% GGBS 75%GGBS & 25% FLY ASH 50%GGBS&50% FLY ASH Chart 5: Water Absorption Test for 28 days in 8M Bricks 57 RESULT & DISCUSSIONS Max Percentage of Water Absorbed (%) 50%GGBS&50% FLY ASH 5.31 75%GGBS & 25% FLY ASH 4.17 100% GGBS 0.94 0 1 2 3 4 5 6 Percentage of Water Absorbed Chart 6: Water Absorption Test for 28 days in 10M Bricks 58 RESULT & DISCUSSION Max Percentage of Water Absorbed (%) 6 5.31 5 Percentage of Water Absorbed 4.17 4 3 3 2.6 2 0.94 0.94 1 0 100% GGBS 75%GGBS & 25% Fly Ash 50%GGBS&50% Fly Ash Percentage of Water Absorbed (%) for 8M Percentage of Water Absorbed (%) for 10M Chart 7: Water Absorption Test for 7,14,28 days 59 RESULT & DISCUSSION Analysis and Compliance with IS Specifications According to IS 3495 (Part 2): 1992 (Methods of Tests of Burnt Clay Building Bricks), the maximum water absorption for Class 1 bricks should not exceed 20% by weight. All bricks tested in this study show significantly lower Water Absorption rates, indicating better durability and compliance with IS specifications. 60 RESULT & DISCUSSION The water absorption results, analyzed in terms of percentage increases and compared against IS specifications, provide a detailed view of the performance of the cement brick samples: Water Absorption for 8M 1. 100% GGBS consistently exhibited the lowest water absorption rates across all curing periods, suggesting excellent durability and low porosity. The final absorption rate of 0.94% is significantly below the IS specification limit. 2. 75%GGBS & 25% Fly Ash showed moderate absorption rates with a final rate of 2.6%, indicating good performance and compliance with IS standards. 3. 50%GGBS & 50% Fly Ash had a relatively higher increase in absorption towards the later stages but still maintained a final rate of 3%, within acceptable limits. 61 RESULT & DISCUSSION Water Absorption for 10M 1. 100% GGBS consistently exhibited the lowest water absorption rates across all curing periods, suggesting excellent durability and low porosity. The final absorption rate of 0.94% is significantly below the IS specification limit. 2. 75%GGBS & 25% Fly Ash showed moderate absorption rates with a final rate of 4.17%, indicating good performance and compliance with IS standards. 3. 50%GGBS & 50% Fly Ash had a relatively higher increase in absorption towards the later stages but still maintained a final rate of 5.31%, within acceptable limits. 62 RESULT & DISCUSSION The Compressive Strength results demonstrate that the incorporation of 75% GGBS and 25% Fly-Ash in bricks significantly enhances their strength over time, with Mx5 consistently showing superior performance. The progressive increase in strength with curing time confirms the beneficial effects of GGBS and Fly-Ash as a pozzolanic material. Similarly, the Water Absorption test results indicate that bricks with GGBS have lower absorption rates, suggesting better resistance to water infiltration and improved durability. Overall, the findings support the conclusion that GGBs and Fly-Ash can be effectively used to produce stronger and more durable bricks, contributing to sustainable construction practices. 63 CONCLUSION 64 CONCLUSION Compressive Strength Analysis Based on the results obtained from the compressive strength tests of Geopolymer bricks containing GGBS and Fly-Ash over 7, 14 and 28 days, several critical observations can be made: 1. Superior Performance of Geopolymer Bricks: Mx2 achieved a compressive strength of 18.89 MPa at 28 days, which is close to the maximum Compressive Strength of conventional high-strength conventional Bricks (15 MPa) and exceeds the minimum requirement of 3.5 MPa as per IS 1077:1992 clause 4.1. This indicates that incorporating GGBS and Fly-Ash significantly enhances the strength of the bricks, making them suitable for structural applications. 65 CONCLUSION 2. Comparison with Conventional Bricks: Conventional brick typically exhibit compressive strengths ranging from 3 to 15 MPa after 28 days. The experimental trials showed compressive strengths of 28.56 MPa (Mx1),18.89 MPa (Mx2),42.88 MPa (Mx3), 46.48 MPa (Mx4), 65 MPa (Mx5), 41.58 MPa (Mx6), 33.2 MPa (Mx7), 39.39 MPa (Mx8), 27.15 MPa (Mx9), 31.19 MPa (Mx10), 27.15 MPa (Mx11) and 29.74 MPa (Mx12), all within the acceptable range for Geopolymer bricks. These results demonstrate that Geopolymer bricks not only meet but can surpass the compressive strength of traditional cement bricks, particularly in optimal formulations. 3. Consistency and Reliability: The results showed a consistent increase in compressive strength over the curing period, reflecting reliable and predictable performance characteristics of Geopolymer bricks. 66 CONCLUSION Water Absorption Analysis The water absorption tests conducted on the Geopolymer bricks revealed key insights into their durability and porosity: 1. Compliance with Standards: The maximum Water Absorption percentage permitted for Geopolymer bricks, according to IS 3495 (Part 2) standards, is 15%. 10M_50%GGBS & 50% Fly Ash showed a water absorption of 5.31%, which is the highest absorption among all the Blend, which it is below the permissible limit, indicating excellent performance and lower porosity. 67 CONCLUSION 2. Performance Comparison: The Water Absorption percentages for the other trials were 0.94, 2.6, 3 and 4.17. Compared to conventional bricks, which exhibit absorption rates between 10-12%, Geopolymer bricks perform competitively, especially in terms of enhancing durability and reducing water ingress. 3. Implications for Structural Integrity: Lower Water Absorption rates in Geopolymer bricks indicate better resistance to weathering and potential for enhanced structural longevity. This is crucial for building materials exposed to varying environmental conditions. 68 CONCLUSION Implications for Sustainable Construction 1. Environmental Benefits: The use of GGBS, a byproduct of the Iron industry, promotes the recycling of waste, reducing the carbon footprint associated with conventional cement production. This aligns with sustainable construction practices by minimizing waste and conserving natural resources. 2. Cost-Effectiveness: Incorporating Fly-Ash as a partial replacement for cement can lower production costs, making eco-friendly bricks economically viable for broader use in the construction industry. 69 CONCLUSION 3. Potential for Wider Adoption: Given the promising results of compressive strength and water absorption tests, further research and optimization of Geopolymer brick formulations can lead to wider acceptance and implementation in the building sector. 70 REFERENCES 71 REFERENCES A.Fuzail Hashmi, M. Shariq, A. Baqi and Moinul Haq. Optimization of fly ash concrete mix – a solution for sustainable development. Elsevier. Volume 26, Part 2, 2020, Pages 3250-3256, DOI: https://doi.org/10.1016/j.matpr.2020.02.908 R Dharmaraj. Experimental study on strength and durability properties of iron scrap with fly ash-based concrete. Elsevier. Volume 37, Part 2, 2021, Pages 1041-1045, DOI: https://doi.org/10.1016/j.matpr.2020.06.290 Dheeresh Kumar Nayak, P.P. Abhilash, Rahul Singh, Rajesh Kumar and Veerendra Kumar. Fly ash for sustainable construction: A review of fly ash concrete and its beneficial use case studies. Elsevier. Volume 6, December 2022, 100143 DOI: https://doi.org/10.1016/j.clema.2022.100143 72 REFERENCES Rahul Upadhyay, Vikas Srivastava, Arpan Herbert and P.K. Mehta. Effect of Fly Ash on Compressive Strength of Portland Pozzolona Cement Concrete. Journal of Academia and Industrial Research (JAIR). Volume 2, Issue 8 January 2014, https://www.researchgate.net/publication/278300166_Effect_of_Fly_Ash_on_Flexural_Strength_of_Portland_Pozzolon a_Cement_Concrete C. Banupriya, Sharon John, R. Suresh, E. Divya and D. Vinitha. Experimental Investigations on Geopolymer Bricks/Paver Blocks. Indian Journal of Science and Technology. Vol 9(16), April 2016, 92209, DOI: https://doi.org/10.17485/ijst/2016/v9i16/92209 Alvin Harison, Vikas Srivastava and Arpan Herbert. Effect of Fly Ash on Compressive Strength of Portland Pozzolona Cement Concrete. Journal of Academia and Industrial Research (JAIR). Volume 2, Issue 8 January 2014, https://www.researchgate.net/publication/268688940_Effect_of_Fly_Ash_on_Compressive_Strength_of_Portland_Pozz olona_Cement_Concrete 73 REFERENCES N. R. Gowthami, A. Sivaji and K. Ajay Kumar. Geopolymer Brick by using Flyash, GGBS, Silica Fume and Kadapa Slab Dust. International Journal of Recent Technology and Engineering (IJRTE). Volume-8 Issue-3, September 2019, 2277-3878, DOI: https://doi.org/10.35940/ijrte.C4726.098319 R. Anu1 and S. Thirugnanasambandam. Geopolymer bricks using M-Sand. Journal of Emerging Technologies and Innovative Research (JETIR). February 2019, Volume 6, Issue 2, DOI: https://www.jetir.org/papers/JETIRZ006049.pdf G. Asha and Jiji Antony. Experimental Investigation on Strength and Durability of Fly Ash and GGBS Based Geopolymer Concrete. Springer Nature. vol 46, Issue 17, December 2019, pp 53–64, DOI: https://doi.org/10.1007/978-3-030-26365-2_5 74 REFERENCES Akshay Ajith and K. Gokul Raveendran. Effect of Chemically Activated Fly Ash on Concrete. Springer Nature. vol 46, Issue 17, December 2019, pp 221–235, DOI: https://doi.org/10.1007/978-3-030-26365-2_22 Sathishraj Mani and Bulu Pradhan. Effect of Alkaline Solution Content on Strength and Chloride Induced Corrosion of Steel in Geopolymer Concrete Made from Fly Ash. Springer Nature. vol 46, Issue 17, December 2019, pp 123–137, DOI: https://doi.org/10.1007/978-3-030-26365-2_12 Lashhanth Dhevaraju, E. Aakash Reddy, Naga Dheeraj Dogiparthy, and Arkamitra Kar. Relationship Between Flexural and Compressive Strength of Concrete Made of Alkali Activated Binder. Springer Nature. vol 46, Issue 17, December 2019, pp 139-145, DOI: https://doi.org/10.1007/978-3-030-26365-2_13 75 REFERENCES Niveditha Balakrishnan, S. Usha and Ponny K. Thomas. Fly Ash Based Geopolymer Bricks: A Sustainable Construction Material. Springer Nature. vol 46, Issue 17, December 2019, pp 279-290, DOI: https://doi.org/10.1007/978-3-030-26365-2_27 T. Saranya, P. S. Ambily and Bharati Raj. Studies on the Utilization of Alternative Fine Aggregate in Geopolymer Concrete. Springer Nature. vol 46, Issue 17, December 2019, pp 851-859, DOI: https://doi.org/10.1007/978-3-030-26365-2_78 Zipeng Zhang, Yat Choy Wong, Arul Arulrajah and Suksun Horpibulsuk. A review of studies on bricks using alternative materials and approaches. Elsevier. Volume 188, 10 November 2018, Pages 1101-1118, DOI: https://doi.org/10.1016/j.conbuildmat.2018.08.152 76 REFERENCES Yanguang Wu, Bowen Lu, Tao Bai, Hao Wang, Feipeng Du, Yunfei Zhang, Lu Cai, Can Jiang and Wenjun Wang. Geopolymer, green alkali activated cementitious material: Synthesis, applications and challenges. Elsevier. Volume 224, 10 November 2019, Pages 930-949, DOI: https://doi.org/10.1016/j.conbuildmat.2019.07.112 Rupali B. Kejkar and Swapnil P. Wanjari. Development and optimisation of curing temperature of energy-efficient geopolymer bricks. Građevinar. 72 (2020) 5, DOI: https://doi.org/10.14256/JCE.2637.2019 Lavanya B, Preet D Kuriya, Suganesh S, Indrajith R and Ramesh Babu Chokkalingam. Properties of geopolymer bricks made with fly ash and GGBS. IOP Publishing. Volume 872, 10 April 2020, DOI: https://doi.org/10.1088/1757-899X/872/1/012141 77 REFERENCES Preetha Vellaichamy, Hariharan Selvarajan, Arjun Ramalingam, and Kalaiyarasan Uthirasamy. Performance studies on Geo polymer concrete. IOP Publishing. Volume 955, 4 September 2020, DOI: https://doi.org/10.1088/1757-899X/955/1/012036 Ramamohana Reddy Bellum, Karthikeyan Muniraj, and Sri Rama Chand Madduru. Investigation on modulus of elasticity of fly ash-ground granulated blast furnace slag blended geopolymer concrete. Elsevier. Volume 27, Part 2, 2020, Pages 718-723, DOI: https://doi.org/10.1016/j.matpr.2019.11.299 IS 16714:2018: Ground Granulated Blast Furnace Slag for Use in Cement, Mortar & Concrete- Specification by Bureau of Indian Standards IS 3812-1:2013: Specification for Pulverized Fuel Ash, Part 1: For Use as Pozzolana in Cement, Cement Mortar and Concrete (Third Revision) by Bureau of Indian Standards 78 REFERENCES IS 3812-2:2013: Specification for Pulverized Fuel Ash, Part 2: For Use as Admixture in Cement Mortar and Concrete (Third Revision) by Bureau of Indian Standards IS 2386-3:1963: Methods of test for aggregates for concrete, Part 3: Specific gravity, density, voids, absorption and bulking by Bureau of Indian Standards IS 381:1995: Sodium silicate – Specification (Second Revision) by Bureau of Indian Standards IS 376:2023: Sodium hydroxide, analytical reagent specification (Fourth Revision) by Bureau of Indian Standards IS 12894:2002: Pulverized Fuel Ash-Lime Bricks - Specification (First Revision) by Bureau of Indian Standards IS 3495: Part 2: 2019: Burnt Clay Building Bricks — Methods of Tests Part 2 Determination of Water Absorption (Fourth Revision) by Bureau of Indian Standards 79 THANK YOU