Yanbu Boiler Training - Auxiliary Equipment Student Training Manual PDF
Document Details
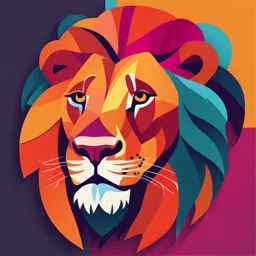
Uploaded by WiseMood
2024
Tags
Related
- ASME BPVC Section VII - Recommended Guidelines for Power Boiler Care PDF
- ASME BPVC Section VI - Recommended Rules for Care and Operation of Heating Boilers PDF
- ASME BPVC Section VII Recommended Guidelines for Power Boiler Care PDF
- ASME BPVC Section VI - Recommended Rules for Care and Operation of Heating Boilers PDF
- Boiler Plant Startup 4th Class Edition PDF
- Marine Engg Midterm Reviewer PDF
Summary
This document is a student training manual for Yanbu Boiler Operation, focusing on auxiliary equipment. It covers various components including air heaters, soot blowers, safety valves, fans, and pumps. The manual provides basic information and typical values for understanding the operation concept, emphasizing that project-specific documents and equipment manuals are crucial for detailed understanding and operation.
Full Transcript
GE Vernova Course Reference: Boiler Operation Auxiliary Equipment Yanbu Student Information Manual GE Vernova Boiler Operation Training Yanbu Auxiliary Equipment GE Vernova reserve all rights in this do...
GE Vernova Course Reference: Boiler Operation Auxiliary Equipment Yanbu Student Information Manual GE Vernova Boiler Operation Training Yanbu Auxiliary Equipment GE Vernova reserve all rights in this document and in the information contained therein. Reproduction, use or disclosure to third parties, in part or in full, without express authority is strictly forbidden. Copyright by GE Vernova 2024 This is a training lesson. It provides overall information about the specific system only. To understand the operation concept in detail the project specific documents have to be included together with this lesson. Equipment specific manuals must be consulted before operating or maintaining the plant. Where GE Vernova describes Vendor supplied equipment not directly provided by GE then that Vendor`s Manuals must also be reviewed and understood before operating and maintaining the plant. All mentioned / attached values and settings are for information and illustrative purposes only. Typical values are used to clarify particular subjects. Settings furthermore are subject to change at site. Yanbu Auxiliary Equipment - Student Handout GE -CONFIDENTIAL- V3.docx For Training Only Page 2 GE Vernova Boiler Operation Training Yanbu Auxiliary Equipment Table of Contents Insert / Index and Tables / Table of Contents / From template 1 Typical References.................................................................................................................... 7 2 O&M Documentation.................................................................................................................. 7 3 Lesson Objectives...................................................................................................................... 8 4 Overview.................................................................................................................................... 8 5 References................................................................................................................................. 8 6 Auxiliaries Introduction............................................................................................................... 9 7 Air Heaters............................................................................................................................... 10 7.1 Factors Affecting Airheater Performance.................................................................................. 11 7.2 Data Sheet (typical).................................................................................................................. 12 7.3 General Arrangement............................................................................................................... 12 7.4 Leakage Control System.......................................................................................................... 24 7.5 TTMD™ - Thermocouple Temperature Monitoring Device....................................................... 27 7.6 Air Heater Cleaning Devices.................................................................................................... 27 7.7 Air Heater Pre-Operational Procedures.................................................................................... 31 7.8 Normal Air Heater Operation.................................................................................................... 32 7.9 Air Heater Shutdown Sequences............................................................................................. 33 7.10 Air Heater Shutdown to Hot Standby........................................................................................ 33 7.11 Fan Protection to APH.............................................................................................................. 33 7.12 Abnormal Operation................................................................................................................. 33 7.13 Extinguishing an Air Heater Fire............................................................................................... 34 8 Soot Blowers............................................................................................................................ 36 8.1 Sootblower Use Philosophy..................................................................................................... 37 8.2 Blower Locations...................................................................................................................... 38 8.3 Sootblower Specifications........................................................................................................ 40 8.4 Soot Blower Operational Principles.......................................................................................... 45 9 Safety Valves & Electromatic Relief Valves (ERVs)................................................................. 46 9.1 Superheat Safety Valve System............................................................................................... 47 9.2 Reheat Safety Valve System.................................................................................................... 48 9.3 Typical Sequence..................................................................................................................... 49 9.4 Safety Valve Exhaust Piping Arrangement............................................................................... 50 9.5 Valve Description..................................................................................................................... 51 9.6 Electric (Power Operated) Relief Valve (ERV).......................................................................... 53 10 Fans: Gas Recirculation (GR), Forced Draft (FD) Fans and Systems....................................... 58 10.1 General (typical)....................................................................................................................... 58 10.2 Air & Gas Flow......................................................................................................................... 63 10.3 Draft System Description.......................................................................................................... 63 Yanbu Auxiliary Equipment - Student Handout GE -CONFIDENTIAL- V3.docx For Training Only Page 3 GE Vernova Boiler Operation Training Yanbu Auxiliary Equipment 10.4 FD Fan System Description...................................................................................................... 67 10.5 FD Fan Operational Condition Requirements........................................................................... 70 10.6 FD Fan Typical Starting Sequence........................................................................................... 71 10.1 FD Fan Typical Shutdown Sequence....................................................................................... 73 10.2 Axial Flow Fans (FD) auxiliaries............................................................................................... 75 10.3 Gas Recirculation Fan.............................................................................................................. 80 10.4 GRF Criteria for normal operation............................................................................................. 85 11 Steam Coil Air Pre-Heater........................................................................................................ 89 11.1 System Overview..................................................................................................................... 89 11.2 SCAPH Location...................................................................................................................... 90 11.3 SCAPH Design......................................................................................................................... 91 11.4 SCAPH Operation.................................................................................................................... 95 12 Boiler Circulation Pump............................................................................................................ 96 12.1 Location & Purpose.................................................................................................................. 96 12.2 Description of the Pumping Set................................................................................................ 96 12.3 Operations................................................................................................................................ 98 13 P&IDs..................................................................................................................................... 100 Yanbu Auxiliary Equipment - Student Handout GE -CONFIDENTIAL- V3.docx For Training Only Page 4 GE Vernova Boiler Operation Training Yanbu Auxiliary Equipment Table of Figures Insert / Index and Tables / Table of Contents / Figures / From template Figure 1 - Principle of Operation of Air Preheater (typical).................................................................................................................. 10 Figure 2: Air Heaters “A” and “B” (Typical)......................................................................................................................................... 13 Figure 3: APH (Typical)...................................................................................................................................................................... 14 Figure 4: Hot End Basket (Typical)..................................................................................................................................................... 16 Figure 5: Hot End Plates (Typical)...................................................................................................................................................... 16 Figure 6: Cold End Basket (Typical)................................................................................................................................................... 16 Figure 7: Cold End Plates (Typical).................................................................................................................................................... 16 Figure 8: Drive Motor & Aux Motor (typical)....................................................................................................................................... 17 Figure 9 - Aux Drive Motor (typical)..................................................................................................................................................... 18 Figure 10 - Yanbu Airheater Drive System.......................................................................................................................................... 18 Figure 11: Air Heater Bearings’ and Lubrication Systems (Typical)................................................................................................... 20 Figure 12 - Rotor Stoppage Alarm System.......................................................................................................................................... 21 Figure 13: Air Heater Flow & Movement (Typical).............................................................................................................................. 22 Figure 14: Rotor Seals (Typical)......................................................................................................................................................... 23 Figure 15 - Effects Of Rotor Deformation in Hot Condition.................................................................................................................. 24 Figure 16: Leakage Control Drive Actuator and sensor(Typical)........................................................................................................ 25 Figure 17 - Leakage Control System Isometric (typical)...................................................................................................................... 25 Figure 18: Leakage Control Drive Panel (Typical).............................................................................................................................. 26 Figure 19 - TTMD Grid Arrangement (typical)..................................................................................................................................... 27 Figure 20: Air Heater Soot Blower (Typical)....................................................................................................................................... 28 Figure 21: Air Heater Soot Blower (Typical)....................................................................................................................................... 29 Figure 22 – Air Heater Sootblower Specifications............................................................................................................................... 30 Figure 23: Air Heater Performance Thermocouples (Typical)............................................................................................................ 35 Figure 24: Air Heater TTMD Fire Sensor Thermocouple (Typical)..................................................................................................... 35 Figure 25 Typical Long Retract Sootblower........................................................................................................................................ 37 Figure 26 - Types of Sootblowers used in Yanbu................................................................................................................................ 38 Figure 27 - Sootblower Locations........................................................................................................................................................ 39 Figure 28 - Sootblower Specifications................................................................................................................................................. 40 Figure 29 - General View of Retractable Sootblower (typical)............................................................................................................. 40 Figure 30 - Sootblowers P&ID 1/2....................................................................................................................................................... 41 Figure 31 - Sootblowers P&ID 2/2....................................................................................................................................................... 42 Figure 32: Blowing Nozzle (Typical)................................................................................................................................................... 43 Figure 33: Helical Blowing Pattern (Typical)....................................................................................................................................... 43 Figure 34 - Sootblower Nozzle End..................................................................................................................................................... 44 Figure 35: Long Retract Blower Lance to Roller Positions, Left or Right-Hand Rotation (Typical)..................................................... 44 Figure 36 - P&ID extract showing arrangement of SH ERV and Spring-loaded safety valves (drg E2B-000109-1E8509-00_001).... 46 Figure 37 - Reheat Safety Valves P&ID extract from drawing E2B-000109-1E8512........................................................................... 49 Figure 38: Safety Valve – Cross Sectional View (Typical).................................................................................................................. 52 Figure 39: Safety ERV & Controller (Typical)..................................................................................................................................... 53 Figure 40 Superheat System P&ID showing Safety Valves (typical)................................................................................................... 55 Figure 41 - Superheat System P&ID................................................................................................................................................... 56 Figure 42 - Reheat System P&ID showing safety valves (typical)....................................................................................................... 57 Figure 43 - Construction view of four axial-flow type fans serving a large pulverized-coal steam generator....................................... 58 Yanbu Auxiliary Equipment - Student Handout GE -CONFIDENTIAL- V3.docx For Training Only Page 5 GE Vernova Boiler Operation Training Yanbu Auxiliary Equipment Figure 44 - Typical Gas Recirculation System – note Yanbu furnace entry is located under the burners........................................... 62 Figure 45 - Arrangement of Air and Gas Flows................................................................................................................................... 64 Figure 46: FD Fan Combustion Air System to Air Heater (Typical).................................................................................................... 65 Figure 47: Single vs. Two-Stage Axial Flow Fan (Typical)................................................................................................................. 66 Figure 48 - FD Fan and Silencer location at Yanbu............................................................................................................................. 67 Figure 49: Yanbu FD Fan (Typical).................................................................................................................................................... 69 Figure 50 - Yanbu FD Fan................................................................................................................................................................... 69 Figure 51 - Typical Axial Fan Curve.................................................................................................................................................... 76 Figure 52 - FD Fan Curve - Typical..................................................................................................................................................... 77 Figure 53: Axial Fan Systems, Single-Stage (Typical)....................................................................................................................... 79 Figure 54 - Extract from I2B-000120-1E8521...................................................................................................................................... 80 Figure 55 - GR Fan Location at Yanbu, only one is shown, the other is hidden behind the boiler...................................................... 81 Figure 56 - Gas Recirculation System................................................................................................................................................. 82 Figure 57 Dual Inlet Centrifugal Fan (Typical)..................................................................................................................................... 82 Figure 58 GR fan installed at Yanbu................................................................................................................................................... 83 Figure 59 GR Fan Curve EQU-906529-B............................................................................................................................................ 87 Figure 60 - Scanner Air System.......................................................................................................................................................... 88 Figure 61 SCAPH (typical).................................................................................................................................................................. 90 Figure 62 - Location of SCAPH........................................................................................................................................................... 91 Figure 63 - SCAPH Arrangement Drawing.......................................................................................................................................... 93 Figure 64 - Location of BCP................................................................................................................................................................ 96 Figure 65 - Boiler Circulation Pump (typical)....................................................................................................................................... 97 Figure 66 - Boiler Circ Pump - Detection Hole for Water Leakage...................................................................................................... 99 Figure 67 - P&ID Safety Valve Drains............................................................................................................................................... 101 Figure 68 - P&ID Symbols................................................................................................................................................................. 102 Figure 69 - P&ID Startup and Warmup System................................................................................................................................. 103 Figure 70 - P&ID Circ Pump.............................................................................................................................................................. 104 Figure 71 - P&ID Boiler SH System................................................................................................................................................... 105 Figure 72 - P&ID Reheater System................................................................................................................................................... 106 Figure 73 - P&ID Scanner Cooling Air System.................................................................................................................................. 107 Figure 74 - P&ID Windbox................................................................................................................................................................. 108 Figure 75 - P&ID Combustion Air and Flue Gas 1/2.......................................................................................................................... 109 Figure 76 - P&ID Combustion Air and Flue Gas 2/2......................................................................................................................... 110 Figure 77 - P&ID SOFA System........................................................................................................................................................ 111 Figure 78 - P&ID Sootblower System 1/2.......................................................................................................................................... 112 Figure 79 - P&ID Sootblower System 2/2.......................................................................................................................................... 113 Yanbu Auxiliary Equipment - Student Handout GE -CONFIDENTIAL- V3.docx For Training Only Page 6 GE Vernova Boiler Operation Training Yanbu Auxiliary Equipment Document Reference 1 Typical References Typical references are used to describe general industry practice and use in this lesson. These typical documents may not show project specific contents, deviations are possible. 2 O&M Documentation Operations & Maintenance (O&M) Documents are plant specific and form an important part of each training course. A selection of the most relevant O&M Documents has been made and included in the training course material. These documents provide a basis for exercises and personal notes, markings, etc. The most relevant documents for the operation training are: P&IDs with legend Design & Operations (D&O) and Maintenance & Vendor (M&V) manuals Yanbu Auxiliary Equipment - Student Handout GE -CONFIDENTIAL- V3.docx For Training Only Page 7 GE Vernova Boiler Operation Training Yanbu Auxiliary Equipment 3 Lesson Objectives Upon completion of this lesson, the trainee is able to: Locate Auxiliary equipment on a General Arrangement Drawing. Describe Auxiliary Equipment Functions and operation practices. Identify solutions for common problems 4 Overview In this course, we will discuss the major auxiliary equipment provided with a contract, the function, major components, and operation of this auxiliary equipment. Included are: Air Preheaters Soot Blowers Safety Valves Fans Steam Coil Air Preheater Boiler Circulation Pump 5 References Specific References are made in the text, however the main references are: References Doc Description Reference Number type Manual Air and Flue Gas Systems DO Vol 5 Part 5 Sec 1 Air Preheater and AccessoriesARVOS/Alstom MV Vol 14 Part 5 Sec Manual Power Air Preheater Operating Instructions 17 Tab 1 Sec 4 Manual Scanner Air System DO Vol 5 Part 5 Sec 2 Manual Gas Recirc (GR) System DO Vol 5 Part 5 Sec 3 Manual Gas Recirc (GR) Fans MV Vol 10 Part 5 Sec 3 Forced Draft Air Fans and DrawingsSiemens Manual MV Vol 6 Part 5 Sec 1 Energy/TLT Turbo Manual Safety Valves MV Vol 5 Part 4 Sec 1 Manual Electromatic Relief (Power Control) Valves MV Vol 5 Part 4 Sec 2 Manual Sootblowing DO Vol 5 Part 5 Sec 4 Half Retract & Full Retract Soot Blowers MV Vol 16 Part 5 Sec Manual Clyde Bergemann 18 Yanbu Auxiliary Equipment - Student Handout GE -CONFIDENTIAL- V3.docx For Training Only Page 8 GE Vernova Boiler Operation Training Yanbu Auxiliary Equipment MV Vol 13 Part 5 Sec Manual Steam Coil Airheater Manual 12 Manual Water Recirc Startup System DO Vol 4 Part 3 Sec 3 Manual Water Recirc Pump MV Vol 1 Part 3 Sec 1 P&ID Safety Valve Drains I2B-000120-1E8418 P&ID Symbols and Legends I2B-000120-1E8500 P&ID High Pressure Startup and Warmup System I2B-000120-1E8503 P&ID Boiler Circ Pump System I2B-000120-1E8504 P&ID Boiler SH System 2/2 I2B-000120-1E8510 P&ID Reheater System I2B-000120-1E8512 P&ID Scanner and Cooling Air I2B-000120-1E8515 P&ID Windbox I2B-000120-1E8516 P&ID Combustion and Flue Gas System 1/2 I2B-000120-1E8521 P&ID Combustion and Flue Gas System 2/2 I2B-000120-1E8522 P&ID SOFA Windbox Air System I2B-000120-1E8523 P&ID Sootblower System 1/2 I2B-000120-1E8524 P&ID Sootblower System 2/2 I2B-000120-1E8525 6 Auxiliaries Introduction This document describes power-plant equipment such as fans, air heaters, sootblowers, and the boiler-water circulating pumps. This equipment is usually designated as boiler auxiliaries. Although boiler auxiliary components are secondary to the design of the boiler itself, they are essential to its operation. Together, they represent a very sizable portion of the overall steam-generator investment. As differentiated from equipment considered auxiliary to the remainder of a steam power plant, a boiler auxiliary is equipment which is an integral part of, or is required for the operation of, the boiler. For example, compressors for air soot-blowers and certain sealing requirements, are part of the overall power-plant equipment and are not boiler auxiliaries. Pumps within the boiler circuit are boiler auxiliaries, but feed- water pumps are part of the power-plant cycle. Equipment is described here to help familiarize the reader with the different components and their specific applications in boiler work. For soot-blower selection, the designer must consider the boiler configuration and the probable dirtying characteristics of the oil ash. For air-heater sizing, air and gas flows and temperatures have to be calculated, as will allowable static pressure losses. It is important to realize that there are instances in which some of this auxiliary equipment is purchased separately from the boiler contract and hence the coverage here is not comprehensive. Yanbu Auxiliary Equipment - Student Handout GE -CONFIDENTIAL- V3.docx For Training Only Page 9 GE Vernova Boiler Operation Training Yanbu Auxiliary Equipment 7 Air Heaters References Doc Description Reference Number type Manual Air and Flue Gas Systems DO Vol 5 Part 5 Sec 1 Air Preheater and AccessoriesARVOS/Alstom MV Vol 14 Part 5 Sec Manual Power Air Preheater Operating Instructions 17 Tab 1 Sec 4 P&ID Symbols and Legends I2B-000120-1E8500 P&ID Windbox I2B-000120-1E8516 P&ID Combustion and Flue Gas System 1/2 I2B-000120-1E8521 P&ID Combustion and Flue Gas System 2/2 I2B-000120-1E8522 Function The function of the air heater is to transfer waste heat energy from the boiler flue gas to the combustion air systems, thus increasing the overall boiler efficiency. The reduction of flue gas outlet temperature can contribute as much as 1% of efficiency improvement for each twenty-two°C of gas temperature reduction. The heat added to the incoming combustion air contributes to more stable and complete fuel firing. As the rotor slowly revolves, the mass of elements travels through the gas and air passages. Heat is absorbed by the elements passing through the outgoing hot gas stream; heat is released when these same surfaces are carried through the incoming air stream. The Ljungström Air Preheater contains thousands of specially formed, and spaced, steel sheets. These steel sheets collectively make up the heat transfer surface, commonly referred to as an “element.” The elements are arranged in a cylindrical structure called the rotor. The rotor revolves slowly, within a structure that is separated into an arrangement of counterflow flue gas and combustion air ducts. As the rotor rotates through the flue gas duct, spaces between the element sheets allow the gas stream to flow across the surface of each metal sheet. As the flue gas flows across the sheet, the element absorbs the waste heat that would normally exit the stack. As the rotor continues to rotate through the air duct, spaces between the element sheets allow the combustion air stream to flow across the heated surface of each sheet (in the opposite direction of the gas flow). As the air flows across the heated sheet, the element releases its heat to the incoming combustion air. Because the rotor carries the element alternately through the air Figure 1 - Principle of Operation of and gas streams, the transfer of heat is continuous. Air Preheater (typical) Yanbu Auxiliary Equipment - Student Handout GE -CONFIDENTIAL- V3.docx For Training Only Page 10 GE Vernova Boiler Operation Training Yanbu Auxiliary Equipment 7.1 Factors Affecting Airheater Performance Air Heater Exit-Gas Temperature with Leakage (corrected)—This is the observed or Temperature measured exit-gas temperature and includes the dilution effect of leakage through the Terminology air-heater seals. Exit-Gas Temperature, No Leakage (uncorrected)—This is the temperature at which the gas would leave the heater if there were no leakage in the heater. This temperature cannot be measured directly but is arrived at by accounting for the cooling effect of the leakage air by calculation. Gas Drop—Temperature of the gas entering heater minus temperature of the gas leaving heater (not including leakage). Air Rise—Temperature of the air leaving heater minus that of the air entering heater. Temperature Head—Temperature of the gas entering heater minus air temperature entering heater. Gas Side Efficiency, percent — deg 100 × deg Entering Air A change in entering air temperature will cause the exit-gas temperature to change in Temperature the same direction. Changes in entering air temperature result in a change in temperature head which directly affects the drop in gas temperature. For example, if the entering air temperature increases 10°, the exit-gas temperature will increase by 10 x (gas-side efficiency/ 100)°. Entering Gas A change in entering gas temperature causes the exit-gas temperature to change in Temperature the same direction. Changes in entering gas temperature result in a change in temperature head which directly affects the drop in gas temperature. For example, a 10° increase in entering gas temperature will cause the exit-gas temperature to increase by 10 x [1 — (gas-side efficiency/ 100))°. Gas Weight An increase in gas weight to the heater will result in a higher exit-gas temperature, while conversely, a lower exit-gas temperature results from a lower gas weight entering the unit. Heat-Capacity Also called the "X" ratio, the heat-capacity ratio (HCR) Ratio Ratio of heat capacity of air passing through the air heater to the heat capacity of flue gas passing through the air heater mass flow of air × avg specific heat of air HCR = mass flow of gas × avg specific heat of gas A decrease in the HCR results in an increase in the exit-gas temperature. A 10% change in this ratio may alter exit-gas temperature by as much as 30° to 35°F (15° to 20°C). Factors that affect the HCR include tempering air, overall boiler-system infiltration, and air-heater bypass for cold-end protection. Pressure Drop The air and gas side pressure drops will change approximately in proportion to the Across Air square of the air and gas weights through the heater. If excess air is greater than Heater anticipated, the air-heater pressure drop will be greater than expected. A build-up of heating element deposits will result in higher air heater resistances with the consequence of an increase in pressure drop. Pressure drop will also vary directly with the mean absolute temperatures of the fluids passing through the heater as a result of changes in density. Yanbu Auxiliary Equipment - Student Handout GE -CONFIDENTIAL- V3.docx For Training Only Page 11 GE Vernova Boiler Operation Training Yanbu Auxiliary Equipment Air Heater A change in the temperature of the fluid leaking past the seals will, by reason of Leakage density change, have a slight effect on the amount of leakage. Variations in pressure levels between the high- and low-pressure sides of the heater will, likewise, alter the air heater leakage. An increase in the pressure differential will increase the leakage while a decrease in pressure differential will reduce the leakage. Improper settings of the heater radial and circumferential seals will also result in an increase in leakage. 7.2 Data Sheet (typical) 7.3 General Arrangement Location The Air Heaters are located as the last heat transfer device in the boiler. They are located at the boiler backend after the economizer, the gas outlet duct from the economizer splits in two and goes to the gas entry of each Airheater. Ref Figure 2 The air to the Airheater is ducted from the FD fans via the SCAPH and a crossover duct to the Airheater air inlets. Use Regenerative bisector air heaters (Figure 2) are provided to improve efficiency by recovering energy (heat) from the flue gas. In doing so preheat is applied the combustion air. The term "bisector" refers to the division of the air and gas sections of the air heater into two sections. One side of the air heater is dedicated to reducing exiting flue gas temperature; the other side increases the temperature of incoming combustion air. The sections have distinct ductwork leading to and from the air heater. Yanbu Auxiliary Equipment - Student Handout GE -CONFIDENTIAL- V3.docx For Training Only Page 12 GE Vernova Boiler Operation Training Yanbu Auxiliary Equipment The term "regenerative" refers to the process design by which the heat transfer elements are passed sequentially through the hot flue gas and cooler air paths so as to cyclically pick up heat from the flue gas and give off heat to the incoming air. This process raises the combustion air temperatures from approximately 54ºC to approximately 330ºC. The flue gas temperature is reduced from approximately 380ºC to approximately 150ºC. Gas Outlet Gas Inlet Ai r Gas o Inlet Figure 2: Air Heaters “A” and “B” (Typical) Airheater To accomplish this, the Air Heaters are made up of the following components: Components Rotor Rotor housing Yanbu Auxiliary Equipment - Student Handout GE -CONFIDENTIAL- V3.docx For Training Only Page 13 GE Vernova Boiler Operation Training Yanbu Auxiliary Equipment Heat transfer element modules with three layers Rotor bearings Rotor drive Sealing system Leakage Control System Figure 3: APH (Typical) Yanbu Auxiliary Equipment - Student Handout GE -CONFIDENTIAL- V3.docx For Training Only Page 14 GE Vernova Boiler Operation Training Yanbu Auxiliary Equipment 7.3.1 Rotor The rotor is made up of pie-shaped modules, which are attached to the rotor post. The hot end of each module has division plates to form compartments for two tiers of heat transfer element "baskets," which are loaded vertically down into the module. At the cold end, there is support for the cold end heat transfer element baskets. The cold end baskets are loaded radially through an access door on the outer plate of the module. The rotor post supports the rotor modules by transmitting the rotor load to the support and guide trunnions. The guide trunnion is bolted to the top of the rotor post and is supported by the upper guide bearing. The support trunnion is bolted to the bottom of the rotor post and is supported by the lower support bearing. 7.3.2 Rotor Housing The rotor housing provides the cylindrical enclosure for the air heater rotor. The upper and lower connecting plates, which connect the heater to the air and gas ductwork, are mounted to the rotor housing. Gas Inlet The air heater is oriented with vertical air and gas flow paths. The top is termed the "hot end" since the flue gas inlet and heated air outlets are located here. Conversely, the bottom is termed the "cold end" as this is the air inlet and cooled flue gas outlet. Module baskets are layered: HE – Hot End Layer CE – Cold End Layer Duct work The air heater is connected to the ductwork by upper (hot end) and lower (cold end) connecting plates. The lower (cold end) connecting plate is made up of a center section with air and gas side transition ducts. The center section forms the supporting girder for the rotor support bearing. This center section is welded to the main housing pedestals. Included are walkways for access to the main bearing, the rotor post stationary spool (a seal on the rotor post), the infrared hot spot detection sensors and operating mechanisms, and the sensor for the rotor stop alarm. The interior surface of the top plate of this center section also contains the support brackets and adjusters for the cold end sector sealing plates Yanbu Auxiliary Equipment - Student Handout GE -CONFIDENTIAL- V3.docx For Training Only Page 15 GE Vernova Boiler Operation Training Yanbu Auxiliary Equipment 7.3.4 Heat Transfer Elements Baskets The heat transfer elements are metal plates, formed to provide both good heat transfer and adequate airflow, when assembled. The elements are assembled into pie-shaped modules, also called baskets. Typically, the modules are installed in two to four layers each layer having distinct heat transfer basket-plates Flow Channels The elements are crimped in such a fashion as to provide flow channels between the plates when they are stacked vertically side-by-side. The elements in the top hot end layer are "double crimped" or "undulated" shapes, providing a more complex flow path for gases and maximizing heat transfer to the plates. The hot end elements are usually made of mild steel. The plates in the cold end elements alternate between "notched" and flat shapes, providing a more direct flow path between the plates and minimizing blockage. The cold end elements are usually made of a more corrosion resistant material. Refer to Figure 4, Figure 5, Figure 6, Figure 7 Figure 5: Hot End Plates (Typical) Figure 4: Hot End Basket (Typical) Figure 7: Cold End Plates (Typical) Figure 6: Cold End Basket (Typical) 7.3.5 Rotor Bearings (typical) Guide Bearing The upper guide bearing (Figure 11) is a self-aligning roller radial bearing designed to withstand radial loads. The bearing housing is designed to accommodate the vertical expansion of the rotor post and is also equipped with a thermostat and a thermocouple. Support Bearing The lower support bearing (Figure 11) is a self-aligning roller thrust bearing Yanbu Auxiliary Equipment - Student Handout GE -CONFIDENTIAL- V3.docx For Training Only Page 16 GE Vernova Boiler Operation Training Yanbu Auxiliary Equipment designed to withstand both the vertical and radial loads. Radial loads are due to airflow loading, resulting from the difference between the air and gas pressures on the rotor. The bearing housing is equipped with a thermostat and a thermocouple. Lubrication The rotor support and guide bearings are bath lubricated although each is (typical) furnished with an integral oil circulating system for the purpose of cooling and filtering the oil. The oil circulating units for both the guide and support bearings are usually similar, except that there is typically a separate oil tank for the lower support bearing, whereas the upper guide bearing housing forms the sump for the lubrication system. The lubrication system typically consists of a pump with an electric motor, a duplex filter, a pressure gauge, a temperature gauge, and a flow switch and heat exchanger. 7.3.6 Rotor Drives Motors The air heater rotor has two drives (Figure 8: Drive Motor & Aux Motor ) the main drive motor, and an auxiliary DC motor. Auxiliary motors keep the air heater rotating at a very slow speed in the event of a main drive motor failure or an electrical failure. Failure to keep the air heater moving while exposed to hot flue gases could result in serious warping of the air heater rotor and a long outage for repairs. The primary drive consists of a main drive motor, gear reducer, and a drive sprocket, which engages a pin rack around the outer circumference of the rotor. The speed of the main drive motor is reduced through the gear reducer. The output of the gear reducer drives the sprocket. The sprocket engages the pin rack on the rotor, turning the rotor at approximately one revolution per minute. Figure 8: Drive Motor & Aux Motor (typical) Yanbu Auxiliary Equipment - Student Handout GE -CONFIDENTIAL- V3.docx For Training Only Page 17 GE Vernova Boiler Operation Training Yanbu Auxiliary Equipment The auxiliary motor is connected to a secondary high speed shaft input of the main speed-reducer by a coupling. The auxiliary motor is used in case of emergencies such as a power loss to the main drive motor. When power is lost to the main electric drive motor, natural momentum will allow the rotor to keep turning (coasting) until the automatic auxiliary motor drive takes over. Figure 9 - Aux Drive Motor (typical) Figure 10 - Yanbu Airheater Drive System Yanbu Auxiliary Equipment - Student Handout GE -CONFIDENTIAL- V3.docx For Training Only Page 18 GE Vernova Boiler Operation Training Yanbu Auxiliary Equipment Yanbu Auxiliary Equipment - Student Handout GE -CONFIDENTIAL- V3.docx For Training Only Page 19 GE Vernova Boiler Operation Training Yanbu Auxiliary Equipment Figure 11: Air Heater Bearings’ and Lubrication Systems (Typical) Yanbu Auxiliary Equipment - Student Handout GE -CONFIDENTIAL- V3.docx For Training Only Page 20 GE Vernova Boiler Operation Training Yanbu Auxiliary Equipment Rotation The air preheater has been equipped with a Rotor Stoppage Alarm (RSA) to Stoppage Alarm detect if the rotor stops turning or slows to an unacceptable speed of rotation, for any reason. A proximity switch is mounted in the lower center section of the air preheater and is activated by targets that are mounted on the support nearing housing. If a target fails to pass the proximity switch within a pre-set period of time, the counter in the local control panel assumes the rotor has stopped rotating and energizes the alarm circuit. Figure 12 - Rotor Stoppage Alarm System The RSA unit is ready for operation when energized. As the rotor starts turning and a vane passes within close proximity of the switch sensor, the timer is set. If a vane fails to pass the proximity switch within a pre-set period of time, the programmable logic controller logic assumes that the rotor has stopped rotating and energizes the alarm circuit. In the event that there is a power failure to the alarm circuit, or the switch leads are broken or shorted to ground, the programmable logic controller output contact will energize the alarm circuit. Yanbu Auxiliary Equipment - Student Handout GE -CONFIDENTIAL- V3.docx For Training Only Page 21 GE Vernova Boiler Operation Training Yanbu Auxiliary Equipment Figure 13: Air Heater Flow & Movement (Typical) 7.3.8 Sealing System A sealing system (Figure 14) is provided to minimize leakage of air from the combustion air side of the air heater to the flue gas side due to gaps between the rotor and rotor housing and air/gas pressure differentials. Various seals provide barriers on both moving and stationary members of the air heater: Radial Seals - Radial seals are attached to the rotor along the radial dividing walls’ "diaphragms" between the pie-shaped sectors at the hot and cold ends. These seals work in conjunction with the leakage control system. Rotor Post Seals - Rotor post seals are attached to the circumference of the rotor post at both hot and cold ends. Circumferential Seals - Circumferential seals form a seal around the perimeter of the rotor at the hot and cold ends. These prevent bypassing of the rotor, which would cause loss of heat recovery. Located on the upper and lower connecting plates, they have a "cold setting" gap relative to the "T" bars on the outer circumference of the rotor. Axial Seals - An axial seal is attached to each rotor module. Working with the axial seal plate, which is fixed to the main pedestal, this sealing system forms a seal between the rotor shell and the rotor housing. This guards against leakage along the sides of the air heater. Static Seals - The static seals are fitted between the sector sealing plates and Yanbu Auxiliary Equipment - Student Handout GE -CONFIDENTIAL- V3.docx For Training Only Page 22 GE Vernova Boiler Operation Training Yanbu Auxiliary Equipment the upper and lower center sections of the connecting plates, also between the curved axial seal plates and the main pedestals. Figure 14: Rotor Seals (Typical) Yanbu Auxiliary Equipment - Student Handout GE -CONFIDENTIAL- V3.docx For Training Only Page 23 GE Vernova Boiler Operation Training Yanbu Auxiliary Equipment 7.4 Leakage Control System Gas Flow As hot flue gas starts to pass through the air heater, a temperature gradient forms across the rotor (hot to cold ends). With one end (hot end) of the rotor hotter than the other end (cold end), the rotor expands unevenly, causing the rotor to bow or "turndown" toward the cold end. The rotor's hot end radial seals move away from the sector plates. To reduce air heater hot end leakage, the air heater is equipped with automatically actuated hot end sector plates. In operation, these sector plates move toward the rotor, reducing the gap (leakage area) between the sector plate and the rotor's radial seals. The result is a saving in fan horsepower, increased downstream air duct pressures, and the potential for maintaining generating capacity. Figure 15 - Effects Of Rotor Deformation in Hot Condition 7.4.1 Leakage Control Motorized Drive Each hot end sector plate is attached to a pivot point on its inboard end and to a drive system near its outboard end. The outboard end simply moves toward the rotor as dictated by the control system. The face of the sector plate is machined to provide a flat, straight sealing surface. Inside the top cover scale actuated by a pushrod that extends all the way down the support tube and is attached to a hardened probe at the sensor's lowest point. At timed intervals, the sector plate, with the attached rotor position sensor, "searches" for the rotor. When the sensor probe locates the hot end rotor T-bar, the sensor triggers the control panel to stop the sector plate. The controls then reverse the sector plate (retract), after a nominal two-second delay to allow the drive motor to stop rotation until the desired sector plate-to-radial seal gap is established. The 3-position scale controls the ends-of-travel of the sector plate. The sensor must also cause sector plate retraction any time the rotor turns up due to slackening load conditions. In this case the sector plate retracts for the same interval of time as discussed above. The sensor requires a low pressure (0.2 – 0.34 bar) source of clean compressed air for sealing the area between the outer support tube and the inner Yanbu Auxiliary Equipment - Student Handout GE -CONFIDENTIAL- V3.docx For Training Only Page 24 GE Vernova Boiler Operation Training Yanbu Auxiliary Equipment pushrod. All connections to the sensor must be flexible. Figure 16: Leakage Control Drive Actuator and sensor(Typical) Figure 17 - Leakage Control System Isometric (typical) 7.4.2 Leakage Control Functional Operation Expansion The sector plate's inboard end "tracks" the expansion of the rotor post. Utilizing the Tracking system, the inboard end of the sector plate moves with the rotor during the thermal expansion phase (start-up or load increase) to reduce radial seal to sector plate contact at the inboard end. At all times, the sector plate is still free to pivot as required to accommodate the leakage control system. Control Panel The main control panel is located on the air heater operating level. The panel contains a PLC for control of both the Leakage Control System and the Hot Spot Yanbu Auxiliary Equipment - Student Handout GE -CONFIDENTIAL- V3.docx For Training Only Page 25 GE Vernova Boiler Operation Training Yanbu Auxiliary Equipment Detection System for both air heaters. Air heater Emergency Stop pushbuttons, alarm horns, alarm test and alarm silence pushbuttons are provided. Figure 18: Leakage Control Drive Panel (Typical) Sector Bending Each sector plate has an independent drive system consisting of a fractional Drive horsepower electric motor, a gear reducer, two linear actuators, a torque-limiting coupling, and drive shaft couplings. If needed, an operator can manually move the sector plate using a hand crank. This feature is important at times when electrical power is unavailable, a drive component has failed, or if the torque-limiting coupling requires reengagement. The drive system's connecting linkage is a simple pushrod arrangement. The two pushrods screw onto their respective actuator's lifting screw at the upper end and pass through a stuffing box at the lower end. Inside the rotor housing, the lower end of each pushrod is pinned to the sector plate lifting lugs. The stuffing box is equipped with a lubrication fitting with which to introduce an anti-seize compound into the box. Stuffing boxes are filled with an anti-seize compound before shipment. 7.4.3 Leakage Control System Retraction Standby To accommodate a system "hot standby" condition, the sector plates can retract to a position farther from the rotor than standard non-actuated hot end sector plates. This reduces the likelihood of radial seal wear during this time when considerable upward rotor expansion exists. Yanbu Auxiliary Equipment - Student Handout GE -CONFIDENTIAL- V3.docx For Training Only Page 26 GE Vernova Boiler Operation Training Yanbu Auxiliary Equipment 7.5 TTMD™ - Thermocouple Temperature Monitoring Device TTMD™ The purpose of the Thermocouple Temperature Monitoring Device (TTMD) system is to Purpose monitor the air temperature leaving the air preheater. Field experience indicates that most air preheater fires originate in small areas and are caused by ignition of incompletely burned fuel that gets deposited on the heat transfer surfaces (element sheets). When the TTMD system detects an unexpectedly high, local air-outlet temperature, the system sends an alarm signal to the plant operators. This system is designed to allow the operator to investigate and take corrective action in advance of a major problem. Figure 19 - TTMD Grid Arrangement (typical) TTMD™ The Thermocouple Temperature Monitoring Device uses an array of thermocouples to Devices measures air and gas stream temperatures. One thermocouple measures the air-inlet temperature, one thermocouple measures the gas-inlet temperature, and a group of thermocouples measure the air-outlet temperature at various radial locations in the air outlet duct. The group of thermocouples that monitor the air-outlet temperatures are located as close as possible to the heat transfer surface, where fires are most likely to originate. When the TTMD system is in operation, millivolt signals from the array of thermocouples are sent to the thermocouple input-modules in the main control panel. The input- modules in the main control panel convert the signals to temperature values. The control system logic uses the gas-inlet temperature, air-inlet temperature, and each of the air- outlet temperatures to calculate a group of real-time thermal effectiveness values. 7.6 Air Heater Cleaning Devices 7.6.1 Sootblowers Air heater soot blowers are located in the upper connecting plate on the gas inlet Yanbu Auxiliary Equipment - Student Handout GE -CONFIDENTIAL- V3.docx For Training Only Page 27 GE Vernova Boiler Operation Training Yanbu Auxiliary Equipment and outlet side of the air heater. Complete coverage of the heating element is accomplished by the traversing movement of the soot blower lance tube as the heating elements rotates 360 degrees beneath the nozzles. Multiple in-line nozzles are spaced on the lance tube as a function of the travel distance and are individually sized to obtain optimum cleaning efficiency of the coverage area. The travel speed of the nozzle across the face of the element is a factor of the effective coverage area of the nozzles and the rotor rpm. The cleaning cycle is initiated to energize the drive motor to begin the forward stroke of the nozzle lance tube across the preheater heating elements. The lance travels at a factory set speed until it reaches the forward travel limit switch. The forward limit switch then trips and reverses the motor direction to begin the reverse stroke. The lance tube continues until the reverse travel limit switch is reached. The reverse limit trips to shut off the power to the motor. The soot blowing medium is dry steam. The recommended blowing cycle during normal preheater operating conditions when firing oil is: For the cold end soot blower: once every 8-hour shift (3 times a day) For the hot end soot blower: once every 24 hours When firing natural gas the sootblowers may be used as needed to maintain conditions. Operation weekly or other such frequency to maintain operational readiness is recommended. Figure 20: Air Heater Soot Blower (Typical) Yanbu Auxiliary Equipment - Student Handout GE -CONFIDENTIAL- V3.docx For Training Only Page 28 GE Vernova Boiler Operation Training Yanbu Auxiliary Equipment Figure 21: Air Heater Soot Blower (Typical) Complete coverage of the heat transfer surface (element sheets) is accomplished by the traversing movement of the sootblower lance tube as the heat transfer surface rotates pass the nozzles. Multiple in-line nozzles are spaced on the lance tube as a function of the travel distance and are individually sized to obtain cleaning efficiency of the coverage area. The travel speed of the nozzle across the face of the heat transfer surface is a factor of the effective coverage area of the nozzles and the rotor RPM. The cleaning cycle is initiated by energizing the drive motor to begin the forward stroke of the nozzle lance tube across the air preheater heat transfer surface. The lance travels at a factory set speed until it reaches the forward travel limit switch. The forward limit switch then trips and reverses the motor direction to begin the reverse stroke. The lance tube continues until the reverse travel limit switch is reached. The reverse limit trips to shut off the power to the motor. A mechanically operated poppet valve is mounted to the sootblower feed tube to control the supply of blowing medium to the air preheater heat transfer surface. When the cleaning cycle is initiated, the lance tube moves forward and engages a trip lever to open the sootblower poppet valve. The valve remains open during both the forward and reverse stroke. When the valve trip lever is reached at the end of the reverse stroke, the poppet valve is closed. Superheated steam is the cleaning medium. The steam or air is delivered through specially designed nozzles to concentrated areas of the heat transfer surface. If moisture is present in the steam or air, harmful conditions may result including: the moisture may combine with deposits on the element sheets to form a sticky mass that can bake on and become extremely difficult to remove. the entrained moisture can increase the impact energy of the blowing medium against the rotor components to a level that can damage the heat Yanbu Auxiliary Equipment - Student Handout GE -CONFIDENTIAL- V3.docx For Training Only Page 29 GE Vernova Boiler Operation Training Yanbu Auxiliary Equipment transfer surface and/or the rotor seals. Figure 22 – Air Heater Sootblower Specifications 7.6.2 Water Washing of the Air Heater, General Precautions Nozzles The High-Pressure Water Washing Device is used OFF-LINE ONLY to remove strong combustion deposits build-up on the heating elements which cannot be removed by the soot blowers. The preheater is out of service, but the rotor drive unit is engaged to keep the rotor turning continuously using the auxiliary AC motor. Stationary water washing nozzles are also positioned on the gas side of the upper and lower connecting plates. These nozzles are not normally used with the air heater online; it is normally recommended that the air heater be isolated for water washing. Ensure air duct drains are open to expel water prior to initiating the water washing system. During normal preheater operations, seal air must be supplied to the high-pressure nozzles continuously to prevent nozzle blockage. Station air must be supplied to the high-pressure nozzles for 5 minutes after soot blowing. When a high-pressure water washing device is initiated, the inlet piping must be changed from seal air piping to high pressure water piping. Off-load high pressure water washing should be conducted only when required to reduce the gas side pressure drop to within acceptable operating limits. Due to the effects of exposing the heating elements to high pressure water and subsequent surface oxidation during the drying process, high pressure water washing the heating elements should only be carried out as necessary with the air preheater out of service. In general, high pressure water washing should be considered when the gas side pressure differential increases by approximately 50% over the design value. The out of service water washing affords an opportunity for making a thorough inspection through the observation ports of the heating surface, both during and after washing. DO NOT ENTER THE AIRHEATER while the rotor is turning or without the proper permits to enter the gas path. The air preheater may be water washed after the boiler has been shut down and Yanbu Auxiliary Equipment - Student Handout GE -CONFIDENTIAL- V3.docx For Training Only Page 30 GE Vernova Boiler Operation Training Yanbu Auxiliary Equipment the preheater has been vacuumed clean of any ash, debris, and loose particles. For planning purposes, allow 24 – 48 hours to complete the washing, drying, and inspection process. The water washing water should be as free as possible of foreign materials to avoid plugging the strainers or nozzles. The water pH range should be kept between 6 and 9. Hot Spot Before washing the air heater rotor with water, ensure the hot spot detection Detection system sensor heads are parked. Fire Prevention Water washing is often performed after the boiler has been removed from service to remove any deposits and prevent future fires. 7.7 Air Heater Pre-Operational Procedures Pre-operational checks: Check sootblower for operation Check all oil levels Check seal caps on hopper bottom outlet Check water supply to water washing cleaning devices Operate motors for current and temperature rise Note To initiate start-up of the leakage control system, the air heater rotor must be turning at normal speed, energize and place the LCS and HSD in auto. Yanbu Auxiliary Equipment - Student Handout GE -CONFIDENTIAL- V3.docx For Training Only Page 31 GE Vernova Boiler Operation Training Yanbu Auxiliary Equipment 7.8 Normal Air Heater Operation Start the air heater before the FD and ID or Gas Recirculation fans. At start-up, operate soot blowers. If unit trips, keep rotor turning and airflow maintained until gas inlet temperature reaches ~204ºC. Average cold end temperature must be kept above dew point to prevent corrosion. Track pressure drop and inlet/outlet temperatures. Suggested data points to track air heater performance: Gas Drop, Econ. Outlet to A.H. Outlet Gas Temp. Ent. Air Heater Gas Temp. Leaving. Air Heater, Uncorrected. Gas Temp. Leaving. Air Heater, Corrected. Air Temp. Ent. Air Heater Air Temp. Leaving. Air Heater Air Press. Ent. Air Heater Ambient Air Temp. Develop a cleaning schedule to maintain performance based on such factors as fuel quality. If the amount of ash per heat input increases, the cleaning may need to be more frequent. During normal operation, the sensor heads scan until a hot spot is detected. When a hot spot is detected, the scan drive motor stops for one complete revolution of the air heater rotor, leaving the sensor heads in the same position to verify the presence of a hot spot. If the hot spot still exists, and alarm is issued from the control panel. If the hot spot is not found, scanning resumes. If a hot spot alarm sounds, the operator should not wait for the sensor heads to park before activating the water washing system to quench the hot spot. Yanbu Auxiliary Equipment - Student Handout GE -CONFIDENTIAL- V3.docx For Training Only Page 32 GE Vernova Boiler Operation Training Yanbu Auxiliary Equipment 7.9 Air Heater Shutdown Sequences If the boiler is at low loads: Cleaning devices must be used on air heater. Maintain stable combustion and avoid carryover of unburned fuel. Once all fuel firing has been removed from service purge the unit with 30% airflow for at least five minutes. Reduce airflow to minimum. Keep the air heaters operating until gas inlet temperatures to the air heater have dropped below ~204ºC. Note Upon shutdown of the burners, the hot spot detection system may be removed from service. 7.10 Air Heater Shutdown to Hot Standby During a shutdown to hot standby, it is assumed that the unit will be shut down for a relative short period of time: Keep fans and air heaters running until the air heater gas inlet temperatures have dropped below ~204ºC. Close all gas duct and combustion air dampers after the air heaters and fans are shutdown. Keep the scanner air fans running. 7.11 Fan Protection to APH If the fans are shutdown with an air heater gas inlet temperature above ~204ºC, the air heater must be kept rotating, however, running the air heater with the gas inlet temperature above ~204ºC and no airflow through the air heater will cause seal damage followed by excessive leakage during operation. The decision to bottle up the unit above ~204ºC must be made with this in mind. Refer to the Air Preheater manual for further information. 7.12 Abnormal Operation Rotor Stops (Motor Failure) Isolate the Airheater with the dampers as necessary Keep incoming flue gas temperature below ~380ºC (typical). Unit load may need to be lowered. Keep a careful watch for fire as reduced combustion air temperatures can affect combustion conditions, resulting in gas lane blockage in the air heater. If rotor has remained idle for some time, the side of the rotor exposed to hot gas may expand and cause the seals to bind. If binding occurs due to rotor stoppage, Yanbu Auxiliary Equipment - Student Handout GE -CONFIDENTIAL- V3.docx For Training Only Page 33 GE Vernova Boiler Operation Training Yanbu Auxiliary Equipment use the following procedure: Engage motor for full five seconds; wait five seconds and repeat several times to allow expansion to equalize. If the above is not successful, use hand crank to rotate air heater, which will eventually equalize expansion and allow the motor to turn the rotor. Once the rotor is turning freely, place soot blowers into service until air heater is free of deposits. 7.13 Extinguishing an Air Heater Fire The Fire Detecting Device (FDD) measures flue gas steam temperatures with an array of thermocouples. The group of thermocouples are located as close as possible to the heat transfer surface, where fires are most likely to be located. When any of the temperature-values show an increase beyond the pre-set value, an alarm signal is produced. The FDD monitors the operation of the thermocouples. Should a thermocouple fail to register a temperature, the system will recognize this as a burn- out condition and activate an alarm different than the fire alarm. The local panel will identify which thermocouple needs to be replaced. The fire extinguishing device consists of two stationary multi-nozzle pipes, one is located in the gas inlet duct of the air preheater, another is located combustion air inlet duct. The system is design to emit large volumes of water onto a concentrated area of the heating element, WARNING: Water should NEVER be administered to the heating element with the air preheater in operation UNLESS A FIRE HAS BEEN VISUALLY VERIFIED BY THE OPERATOR. Isolate the air heater – the boiler may temporarily keep operating on the other In the event air heater at reduced load pending outcome of the fire. of an Air Heater Be certain hopper drains are clear; large quantities of water are heavy and Fire: must be drained. Admit water in sufficient quantities through firefighting manifolds. There is a manifold on the flue gas inlet and one on the outlet. If the fire gets hot enough to ignite the air heater elements, temperatures will reach ~1650 to ~2200ºC. The fire then becomes self-sustaining and almost impossible to extinguish. If source of fire is isolated, stop rotor and combat fire in the localized area. If the source of fire were widespread, it would be more beneficial to keep rotor turning so that complete water coverage of the elements is possible. Yanbu Auxiliary Equipment - Student Handout GE -CONFIDENTIAL- V3.docx For Training Only Page 34 GE Vernova Boiler Operation Training Yanbu Auxiliary Equipment Figure 23: Air Heater Performance Thermocouples (Typical) Figure 24: Air Heater TTMD Fire Sensor Thermocouple (Typical) Yanbu Auxiliary Equipment - Student Handout GE -CONFIDENTIAL- V3.docx For Training Only Page 35 GE Vernova Boiler Operation Training Yanbu Auxiliary Equipment 8 Soot Blowers References Doc Description Reference Number type Manual Air and Flue Gas Systems DO Vol 5 Part 5 Sec 1 Manual Sootblowing DO Vol 5 Part 5 Sec 4 Half Retract & Full Retract Soot Blowers Clyde Manual MV Vol 16 Part 5 Sec 18 Bergemann P&ID Symbols and Legends I2B-000120-1E8500 P&ID Combustion and Flue Gas System 1/2 I2B-000120-1E8521 P&ID Combustion and Flue Gas System 2/2 I2B-000120-1E8522 P&ID Sootblower System 1/2 I2B-000120-1E8524 P&ID Sootblower System 2/2 I2B-000120-1E8525 Introduction An important boiler auxiliary operation is the on-line cleaning of heat-absorbing surfaces. Not only is it important for proper heat transfer, but also to prevent sections of the boiler from becoming plugged. Plugged sections can restrict gas flow and cause load limitations. Sootblowing systems are required on oil-fired furnaces. Oil has a low ash content which produces a thin water-soluble deposit on the furnace walls that is normally removed by annual water washing. Furnace-wall soot-blowers are, therefore, not required on oil-fired units. In the superheater and reheater sections of an oil-fired unit, ash deposits do accumulate on the tubing surface. This is especially true of high-vanadium oils where additives are used to combat high-temperature corrosion. But with the use of additives, ash deposits in the high-gas-temperature areas increase markedly. Ordinarily quite friable, such deposits are easily removed with sootblowers. The soot blowing system for this unit has been designed on the basis of specific parameters. That is, in determining the number and type of blowers, blower location and operating sequences, the characteristics of the fuel to be burned, the configuration of the heat-absorbing surfaces of the boiler and past experience in this type of unit, were considered. However, it is impossible to predict the performance of the soot blowing equipment for all operating conditions and for each individual unit. Factors such as variation in fuel characteristics, load changes, fluctuations in furnace temperatures and air flow conditions can affect the soot blowing requirements. Therefore, operation of the soot blowers must be continuously evaluated and reviewed on the basis of changing operating conditions. The Soot Blowing System includes retractable soot blowers, pressure reducing station, thermal drain valves and controls. Steam is the blowing medium. Refer to the Operations manual DO Vol 5 Part 5 Section 4 for more details. Yanbu Auxiliary Equipment - Student Handout GE -CONFIDENTIAL- V3.docx For Training Only Page 36 GE Vernova Boiler Operation Training Yanbu Auxiliary Equipment Figure 25 Typical Long Retract Sootblower 8.1 Sootblower Use Philosophy Any sootblowing system is designed on the basis of specific parameters. In determining the number and type of blowers, the blowing medium, blowing pressure, blower location and operating sequences, it is necessary to take into consideration the following: Specified characteristics of the oil to be burned Boiler design standards Configuration of the heat-absorbing surfaces of the unit Past experience Unit cleanliness at any reasonable load and firing rate. An important tool to promote optimum use of soot blowers is an accumulation survey. Operating practices should be modified as the needs change. For this reason, flexibility is provided in the system to enable manual selective operation in addition to automatic control. Intelligent use of the soot blower system offers: 1. It can prevent troublesome accumulations of ash deposits that, in turn, may cause additional unit operating problems. 2. It provides for maximum cleaning of the heat absorbing surfaces. In addition, minimizing the number of blowing cycles will save blowing medium. More efficient, selective use of the equipment will result in reduced maintenance. There are several indicators of ineffective use of the soot blowing equipment, such as response of steam temperature control, changes in draft loss, etc. The best way to monitor the effectiveness of soot blowing is by frequent observation. If operation of a blower or a series of blowers does not produce the expected results, the affected area involved should be observed and the blower(s) in question checked. Blowing pressures should be checked periodically (every six months) to determine whether they have changed from their initial effective settings. To determine if proper cleaning is taking place, the operator should have a basic knowledge of the types of ash deposits that can build up in the various parts of the Yanbu Auxiliary Equipment - Student Handout GE -CONFIDENTIAL- V3.docx For Training Only Page 37 GE Vernova Boiler Operation Training Yanbu Auxiliary Equipment unit. Sintered or dust-like ash deposits or buildups are prevalent on convection surfaces, such as superheater and reheater elements, and in the back pass. 8.2 Blower Locations 8.2.1 Superheater, Reheater, Economizer and Air Heater Areas Long Retracts Long retract soot blowers are provided in the convection pass, backpass and air preheater for cleaning ash deposits from convective surfaces. Removal of ash improves heat transfer and prevents draft loss due to fouling. All sootblowers used in Yanbu are retract type in three sub types as shown in the Figure 26 Figure 26 - Types of Sootblowers used in Yanbu The Sootblower is a long retractable sootblower designed for the cleaning of boiler heating surfaces. The long retractable sootblower uses the potential energy in the blowing medium and transforms it into kinetic energy by means of venturi nozzles. Nozzle selection is based on tube assembly spacing and the composition of the ash. Using the long retractable blowers in the convection superheater and reheater areas should remove accumulated surface deposits. This will improve heat absorption in these sections. If the steam temperature controls are on automatic, this may cause the GR flow to lower and/or spray water flow to increase (when firing oil) or tilts to change position (when firing gas). Selective blowing of long, retractable blowers in the superheater and reheater zones can also be utilized to balance superheater and reheater outlet temperatures. In any case, draft loss across convection surfaces should be observed. Increased draft loss indicates an increased plugging condition. If a plugging condition is allowed to progress too far, it may be impossible to clean the convection surfaces except by removing the unit from service for water washing. Refer Figure 27 for details Yanbu Auxiliary Equipment - Student Handout GE -CONFIDENTIAL- V3.docx For Training Only Page 38 GE Vernova Boiler Operation Training Yanbu Auxiliary Equipment Figure 27 - Sootblower Locations 8.2.2 Air Heater Sootblowers There are also sootblowers located at the Airheaters for the purpose of cleaning the Airheater surfacing. These are described in the section under Airheaters. See section 7.6 Yanbu Auxiliary Equipment - Student Handout GE -CONFIDENTIAL- V3.docx For Training Only Page 39 GE Vernova Boiler Operation Training Yanbu Auxiliary Equipment 8.3 Sootblower Specifications Figure 28 - Sootblower Specifications Figure 29 - General View of Retractable Sootblower (typical) Yanbu Auxiliary Equipment - Student Handout GE -CONFIDENTIAL- V3.docx For Training Only Page 40 GE Vernova Boiler Operation Training Yanbu Auxiliary Equipment Figure 30 - Sootblowers P&ID 1/2 Yanbu Auxiliary Equipment - Student Handout GE -CONFIDENTIAL- V3.docx For Training Only Page 41 GE Vernova Boiler Operation Training Yanbu Auxiliary Equipment Figure 31 - Sootblowers P&ID 2/2 Yanbu Auxiliary Equipment - Student Handout GE -CONFIDENTIAL- V3.docx For Training Only Page 42 GE