Engine Operator Training PDF
Document Details
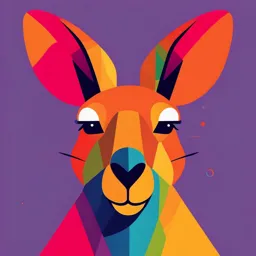
Uploaded by MeticulousSchrodinger
Oklahoma State University
Tags
Summary
This document covers engine operator training, including skills, emergency pump procedures, and cold weather operations for fire trucks. It details procedures like vent fan operation, ladder raises, setting pump discharge pressures, and loss of water/prime scenarios.
Full Transcript
Engine Operator Training We are going to discuss and practice the things that drivers are expected to do when they are pumping a re. During our evolutions we usually focus on pulling hose and the skills needed for the interior attack. The things we need to have the drivers start doing during these...
Engine Operator Training We are going to discuss and practice the things that drivers are expected to do when they are pumping a re. During our evolutions we usually focus on pulling hose and the skills needed for the interior attack. The things we need to have the drivers start doing during these drills is getting vent fan set up, getting tools to the front of the building, ladder the upper story windows in case we need to bail out. The things that will be practiced can be done without letting command know, it is being proactive and not freelancing. These things come second to getting the pump and pressure set up. We are going to practice pumping multiple lines and discuss the pressures at which we are going to pump these lines at. We are going to pump our 1-3/4 inch handlines at 160 psi (this is just at my station) this will give us 150 Gallons Per Minute. We are going to pump the 2-1/2 inch handlines with a smoothbore nozzle at 78 psi. If we have the combination nozzle on then we will have to pump it at 120 psi. We need to know how we are going to gate the 2-1/2 inch down when we are pumping the 1-3/4 too. Also remember to keep the tank to pump open and the tank ll line cracked this keeps the pump from building up pressure while we are driving. When we keep these closed the truck seems to build pressure while we are driving even though it isn’t supposed to do this. We needed to talk about how many psi max for the ground monitor and ladder pipe also. The max pressure for the ground monitor on Ladder 1 is 175psi but the smoothbore tips and the pressure gauge says 80 to 110 is in the green. The maximum on the ladder pipe is 200 psi. You need to remember that if you are pumping under 1000gpm then you have full range of motion of the nozzle. But if you are over 1000gpm then you can not point the nozzle upwards and you have to keep it inside the rails of the ladder side to side. Once you are done pumping the truck you have to drain the ladder pipe or you will damage the equipment when you retract it. When we catch a hydrant you need to know that according to the PUC manual you do not want to go under 20psi on the intake pressure. We will go over pumping multiple handlines and how to keep the water owing while doing so. When setting the pump discharge pressure we are going to set it at 160psi (my station only not department wide) so if we pull a 2-1/2 inch handline rst then you will only partially open the valve to get the correct pressure. The only way to get the correct pressure on the 2-1/2 inch handline is to open the nozzle until the operator can set the pressure. fi fl fi fi Skills 1. Vent fan operation- how to start the fan and where to set it up and what to check for prior to turning the fan into the building. 2. Practice one man ladder raises this could be with a 24’ extension ladder or the roof ladder to ladder a window or the roof if needed. 3. What tools are going to be needed and where are they going to be needed. Make sure we have a RIT pack and stokes basket in the front yard ready for deployment. Possibly a K12 also. 4. Pump discharge pressure- (my station only on these pressures the preset is di erent than what my station pumps) what pressures do we need to have at the pump for the desired ows of 150 gpm’s on the small handlines and 265 gpm’s on the deuce and a half. 1.75 inch preconnect handline needs to be pumped at 160 psi to get 150 gallons per minute. 2.5 inch smoothbore preconnect needs to be pumped at 68 psi to get 265 gallons per minute. Emergency Pump Procedures 1. Loss of Water- What actions can we take and how can we tell that we are having a loss of water problem. If you do have a loss of water and it xes itself we need to notify command and make sure we have another water supply. One main thing is we need to make sure and watch our intake to tell if we have water or not. You can also check your supply line from time to time. 2. Loss of Prime- If we lose prime how are we going to prime the truck. The Pierce trucks have an air primer and the owners manual states that for optimal operation of the primer you need to have 1,000 rpms. Hold it down until you hear that all of the air has been emptied out of the pump. One key way to know that you do not have prime is that the truck will not build pressure when you are throttling the pump up. 3. Pump will not pump when at panel- Maybe you forgot to put the truck in pump gear in the cab. We have a pump shift switch at the pump panel which can be used if you forget to do it in the cab. 4. If the intake valve is opened too quickly or the line isn’t bleed out then the truck will automatically shut down because it reads the air and shuts itself down. If this happens then you have to start all over and bleed the line out and may have to prime the truck to relieve the air out of the system. Other Considerations If you forget to put the truck in pump and you cant gure out why you aren’t able to build up pressure then you should switch the manual pump shift switch at the pump panel this will allow you to pump normally. ff fl fi fi Another thing we forget about a lot of times especially during icy weather or snow is that this truck is equipped with chains that drop down allowing you to have some traction. The chains drop down and there is a wheel that sits against the tire and as the tire spin it moves the wheel attached to the chains and slings them under the tire for traction. Also important to note is that if roads are slick or even during rain we need to turn the engine brake to the o position as it can cause the truck to skid. But during all other operations I expect you to have the engine brake on and in the highest setting on ladder 1 if you are on squad 1 then you can have it in the medium setting. -Its a good idea to drain the pump from time to time to get all the sediment out of the pump. Just make sure that after you do so that you ll it back up because that is how we have decided we are going to operate. Cavitation If you bring the rpm’s up and the pressure isn’t going with it then you are cavitating the pump. The sound of sand or something in the pump is a sign also. Overheating Not having water in the pump or not owing water. When you dead head the pump then it gets hot. If it has no where to go then the pump is moving and heating the water up to boiling temperatures and then that causes damage to the impeller. Always keep water moving. If you have the water recirculating then the hot water will dissipate in the tank because the water in the tank isn’t hot. Cold Weather Operations If the weather is below freezing we are going to put the truck in pump gear and recirculate water anytime we are out in the weather. The only other option would be to completely drain the pump. If you completely drain the pump and all lines then you do not have to put the truck in pump gear because the pump should not have any water in it to freeze. When you are on the Engines we still need to make sure we are draining the turret and the booster line because they are smaller lines that are down lower and exposed to the cold so they could still freeze. We need to make sure all of the lines are drained but keep water in the pump and keep the tank to pump open and the recirculate line cracked. The tank to pump and recirculate lines should be open and cracked at all times this keeps the truck from building up pressure while we drive the apparatus. fl fi ff