Engine Control System PDF
Document Details
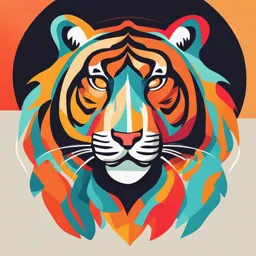
Uploaded by LoyalAntimony
Dr. Nurul Musfirah Mazlan
Tags
Summary
This document provides an overview of aircraft engine control systems, covering various aspects such as the different types of aircraft engines (turbojet, turboprop, turbofan, and turboshaft), their components, functionalities, operating environments, costs, reliability, and regulatory requirements.
Full Transcript
ESA 272: Aircraft Sub-systems Element Engine Control System Dr. Nurul Musfirah Mazlan Introduction Aircraft view on Engine Fuel Control System… – What are the main components? – What are their purpose? – How do they operate? – What are the design driver...
ESA 272: Aircraft Sub-systems Element Engine Control System Dr. Nurul Musfirah Mazlan Introduction Aircraft view on Engine Fuel Control System… – What are the main components? – What are their purpose? – How do they operate? – What are the design drivers? – What are the significant issues? Introduction Cockpit control Fuel tanks and fuel pumps Engine and FADEC system Introduction Fuel Tanks and Aircraft Fuel Pumps – Fuel stored in tanks located in wings (horizontal stabiliser) – Fuel supplied to engines (and Auxiliary Power Unit, APU) – Fuel can be transferred around tanks to manage A/C center of gravity (CoG) When in cruise the system can optimise the CoG positon Increase fuel economy by reducing the drag of the aircraft – Fuel circulated for cooling (e.g. Integrated Drive Generator) Introduction Fuel Tanks and Aircraft Fuel Pumps – Main fuel pump system supplies fuel from wing tanks to engines – Fuel flow can be halted by Low Pressure Fuel Valve in Fuel Tank Normally under control of engine MASTER switch FIRE switch/handle can also close valve – Fuel can be supplied across engines A cross-feed system is often utilised Both engines can be fed from one tank One engine can be fed from both tanks Introduction Engines – Fuel is supplied to engine combustion system in accordance with: Setting of the Engine Throttle Lever Aircraft Operating Conditions – Many of today’s Aero-Engines are controlled with FADEC system FADEC: Full Authority Digital Engine Control Comprises All accessories required to control engine including… – Electronic Engine Controller (EEC) – Hydro-mechanical Control Units – Associated sensors, actuators and connecting harness Introduction Cockpit Controls Throttle lever Fuel-On/MASTER Switch Start Switch Cockpit Indication Airbus – A330 cockpit Engine parameters Warning/caution Messages Maintenance Data Introduction Cockpit Indications Engine Pressure Exhaust Gas Ratio indicates the Temperature engine thrust Fuel Flow Fuel on Board Shaft Speed Maintenance Crew Alerting Indication Indication Engine Display (Upper ECAM) on the A330 Introduction What “SHAPES” the design of an Engine Control System – Functionality – Environment – Cost – Regulatory Requirements Introduction Functionality – Optimised architecture Design option “trade-off” to optimise overall aircraft system Functional Partitioning – Pilot Workload Simplified control interface Provision of Auto-functions Increased levels of Diagnostics/Prognostics – Integration with Airframe services Communication with Aircraft Systems Management of power off-takes Introduction Operating Environment – Challenging routes Climate Location Geographic Location Runway Size Introduction Operating Environment – Challenging routes Climate Location Geographic Location Runway Size Introduction The ‘Environment’ – Noise – Emissions – Environmental Standards Effect on Material Usage – Asbestos – Cadmium – Beryllium Effect on Manufacturing Process – Development of new techniques to accommodate lead-Free solder – Selection of alternative chemicals for use as cleaning agents Introduction Cost – Of-the-shelf price on aircraft-engine combination Credible costs in a world of intense competition – Revenue earning capability Payload, range and flexibility – Operating costs Increased fuel efficiency – high specific fuel consumption (SFC) Cost of ownership – reliability and despatchability Introduction Cost of Ownership – Reliability Cost of maintaining spares holding and associated logistics tail Periodic scheduled maintenance to keep airplane airworthy Ongoing scheduled maintenance to rectify system failures – Despatchability Costs associated with aircraft failing to depart on schedule – Passenger compensation for delays/cancellation – Crew ‘time-out’ – May require spare aircraft for significant system failure Despatch reliability is a key metric for an aircraft operator Introduction Regulatory Requirements – Engine Control Certification is managed by Regulatory Authorities The body responsible for the UK is the Civil Aviation Authority (CAA) Others include FAA (in USA), DGAC (in France and Transport Canada) Ministry of Defence (MoD) are responsible for military item certification – CAA Safety Regulation Group (SGP) are responsible for: Checking that an aircraft’s design and systems meet requirements Monitoring the aircraft’s airworthiness throughout its life – An aircraft must be certified before it can be put into operation Analysis and qualification test to demonstrate compliance Introduction Qualification Test – Evidence to support Type Certification approval – Demonstrate system survives environment: Extreme temperatures Vibration Humidity Fungus Salt fog Contaminated Fuel Fire resistance EMC, HIRF and Lightning Strike Introduction Effect of Aircraft/Engine goals on control system design – A reduction in weight and cost will drive the use of alternative architectures and technologies – Flow-down of safety requirements combines with availability guarantees will further drive selection or architecture and fault detection systems Enhanced techniques for fault isolation, re-configuration and health monitoring Development of advanced diagnostic and prognostic capabilities – Advances engine topologies may necessitate more complex/faster control loops System Overview Why do we need an engine control system? – To control a flow of fuel and air to the engine – As well as managing fuel flow the engine control system has to: Manage the goals and objectives of engine and aircraft design Handle the ever increasing complex functions of modern engines – Vary the aerodynamic and geometry of the engine – Manage faults and monitor engine health – Engine protection – Control cabin bleeds and power off-takes Gas Turbine Engine Main components Combustion chamber Compressor Nozzle Intake case Turbine Types of Aircraft Engine Turbojet Types of Aircraft Engine Turboprop Types of Aircraft Engine Turbofan Types of Aircraft Engine Turboshaft Environment within Gas Turbine Operational Limits Structural limits – Maximum fan and core speeds: N1 (rotational speed of LPC) and N2 (rotational speed of HPC) – both in rpm – Maximum turbine blade temperature Safety limits – Adequate stall margin – compressor and fan – Lean burner blow out – minimum fuel Operational limit – Maximum turbine inlet temperature – To provide long life for the engine Why important? Maximum fuel limit protects against surge/stall (flow instability), over-temperature, over-speed, and over-pressure Minimum fuel limit protects against combustor blow-out (flame failure occurs at high altitude operation) System Overview Fuel Flow Control – Power or thrust can be controlled by regulating the fuel flow into the combustor – When higher thrust is required, throttle is opened and fuel pressure to the burner increases due to higher fuel flow. – Increases in fuel pressure increase gas temperature which in turn increase the acceleration of the gases through the turbine to give a higher engine speed, greater air flow which resulting in increase in thrust. – Changes in altitude, air temperature, and aircraft speed change the density of the air at the engine intake and the mass of air flowing through the engine. – To maintain conditions demanded by pilot, fuel control unit (FCU) or fuel management unit (FMU) is used System Overview Air flow Control – To ensure efficient operation over a wide range of environmental condition to maintain a safe margin from the engine surge line. – It can be control through variable inlet guide vanes (VIGVs) or variable stator vanes (VSVs) – VIGVs – affect the airflow at the inlet of the compressor and are used predominantly on smaller engine (e.g. : AE3007) – VSVs- are used on larger aircraft (Trent 700). VSVs will vary the airflow within the compressor – For military aircraft – the exhaust gas and bypass air are configured to provide either forward thrust or lift, or combination of the two (e.g.: Harrier) System Overview FCU/FMU – Hydro-mechanical device mounted on the engine – Contain valves to direct fuel and to restrict fuel flow – Contain pneumatic capsules to modify flows according to prevailing atmospheric conditions – Contain dashpot/spring/damper combinations to control acceleration and deceleration rates System Overview Evolution of Engine Control System based on system requirements and constraints – Prior to 1970: Evolution of Hydro-mechanical Control – 1970 – 1990: Evolution of Electronic/Hydro-mechanical Control – After 1990: Evolution of FADEC FADEC System Overview Public Release Photo Courtesy of Pratt & Whitney FADEC System Overview Why use FADEC system? – Hydro-mechanical vs FADEC FADEC System Pilot Harness FADEC Fuel Control Hydro-mechanical System Pilot Linkage Fuel Control Unit FFR MK105 FMU 603 Difference FFR – Fuel Flow Regulator FMU – Fuel Metering Unit Reliability 21,830 33,708 54% MTBF – Mean Time Before (MTBF) Failure Weight (Ib) 52 20 62% Cost (£) 60,000 22,000 63% FADEC System Overview Why use FADEC system? – FADEC verses Control System Objectives Enables flexible and complex control Fault detection and accommodation Continual health monitoring Airframe interface – Fault reporting (Flight & Maintenance crew) – Sensor Information – Command Inputs Reduced weight and cost Increased reliability FADEC System Overview FADEC background – Full Authority Digital Engine Control system – able to autonomously control the engine throughout its whole operating range from demanded engine start until demanded engine shutdown, in both normal and fault conditions – Comprises of Electric Engine Control (EEC) and other accessories that control all aspects of aircraft engine FADEC System Overview FADEC background – Components in FADEC Two Master Power Control Units("MPC-1" And "MPC-2") Sensors For Manifold Temperature And Pressure Cylinder Head Temperature (CHT) Sensor Exhaust Gas Temperature (EGT) Sensor Speed Sensors Speed Sensor Assembly Fuel Pressure Sensors Low Voltage Harness High Voltage Harness Throttle Body Assembly Health Status Annunciator(HSA) Fuel Injection System FADEC System Overview How it works? – FADEC works by receiving multiple input variables of the current flight condition including air density, throttle lever position, engine temperatures, engine pressures, and etc – Engine operating parameters such as fuel flow, stator vane position, bleed valve position, and others are computed from this data and applied as appropriate FADEC System Overview How it works? – It controls engine starting and restarting – It basic purpose is to provide optimum engine efficiency for a given flight condition – It also allows the manufacturer to program engine limitations and receive engine health and maintenance reports. E. g: To avoid exceeding a certain engine temperature, the FADEC can be programmed to automatically take the necessary measures without pilot intervention FADEC System Overview Report Engine Airframe Status Communication Engine Control Receive Engine Power Command Acquire sensor FADEC data Process Engine Health Control Laws Monitoring Command Actuators Diagnostic Prognostic Adaptive FADEC System Overview FADEC System Architecture Example of FADEC used in Rolls Royce and Pratt & Whitney engine Contains EEC, sensors, FMU/HMU EEC is the core of the system FADEC Alternator provides power supply in case of electrical power from aircraft fail The system architecture of FADEC system with the centralised arrangement of servo-valves in HMU Data & Sensors Sensors located within the gas turbine engine Data & Sensors Signals Sensors Throttle position Transducer - connected directly to the throttle level (either by electrical signaling or connected to the end of control rods for mechanical operation) Air data (altitude and Using air data computer (ADC) or flight control airspeed) system air data sensors Total temperature Using temperature probe mounted at the engine face, intakes or on aircraft structure Engine speed Using pulse probes – function to have magnetic field interrupted by moving metallic parts of the engine or gear box Engine temperature Using thermocouples- arrange as a ring of parallel connected thermocouples to obtain mean gas temperature Data & Sensors Signal Sensors Pressure ratio Diaphragm operated device Two high accuracy pressure sensors and electronics Nozzle position Position sensors located to the nozzle actuation mechanism Fuel flow Turbine flow meter installed in fuel pipework Fuel control unit (FCU) Fuel flow control Solenoid, torque motor or stepper motor Air flow control Inlet Guide Vanes (IGV) or bleed valves located between engine stages