Electrical and Avionics Systems PDF
Document Details
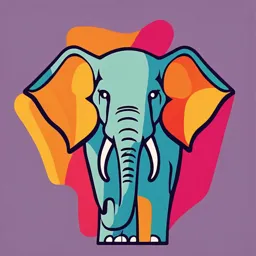
Uploaded by ProfoundMoscovium
Tags
Summary
This document provides an overview of electrical and avionics systems, specifically focusing on lighting. It discusses different types of lights, power supplies, safety precautions, and installations on aircraft.
Full Transcript
ELECTRICAL AND AVIONICS AMTP017 | ELECTRICAL AND AVIONICS | ISSUE2 REV 1 | Page 1 of 286 CONTENTS (ATA 33) LIGHTS (ATA 24) ELECTRICAL POWER (ATA 31) INSTRUMENTS/RECORDING SYSTEMS (ATA 23) COMMUNICATION SYSTEMS (ATA 34) NAVIGATION SYSTEMS (ATA 22)...
ELECTRICAL AND AVIONICS AMTP017 | ELECTRICAL AND AVIONICS | ISSUE2 REV 1 | Page 1 of 286 CONTENTS (ATA 33) LIGHTS (ATA 24) ELECTRICAL POWER (ATA 31) INSTRUMENTS/RECORDING SYSTEMS (ATA 23) COMMUNICATION SYSTEMS (ATA 34) NAVIGATION SYSTEMS (ATA 22) AUTO PILOT SYSTEMS (ATA 45/46) ON BOARD MAINTENANCE SYSTEMS/FANS OBJECTIVES The course aims to provide technicians in the mechanical trade of the basic knowledge of aircraft’s electrical and avionics systems. AMTP017 | ELECTRICAL AND AVIONICS | ISSUE2 REV 1 | Page 2 of 286 (ATA 33) LIGHTS AMTP017 | ELECTRICAL AND AVIONICS | ISSUE2 REV 1 | Page 3 of 286 LIGHTS Introduction Design considerations for lighting system usually depends on the following: For passenger cabin, lighting must be appealing and efficient. Operational flexibility and safety should be kept in mind, but with minimal weight penalty. The flight deck general and instrument lighting must allow the crew to read the instruments easily under all natural light conditions. Warning lamps should not be dimmed under all circumstances AMTP017 | ELECTRICAL AND AVIONICS | ISSUE2 REV 1 | Page 4 of 286 LIGHTS AMTP017 | ELECTRICAL AND AVIONICS | ISSUE2 REV 1 | Page 5 of 286 POWER SUPPLIES The degree of importance of the lighting dictates the power supply to be used. It should be noted that even with all generators failed, safe lighting levels are maintained in the flight deck and cabin as a fail-safe design. As an example, supplies may be classed as follows: General illumination: 28V A.C. or lower (transformed A.C. output) Standby lighting: 28V D.C. or lower (i.e. emergency lights battery) Fluorescent lights: 115V/200V A.C. (normal A.C. generation) Note: Aircraft lights are different type from industrial lights. AMTP017 | ELECTRICAL AND AVIONICS | ISSUE2 REV 1 | Page 6 of 286 EXTERIOR LIGHTS Exterior lights provide visibility to other airplanes in flight and illuminate the airplane (wings and engines) and landing and taxiing areas during flight and ground operations. It also provides lighting for airline emblem illumination (Logo lights). NAVIGATION WING TIP AND TAIL LIGHTS To achieve compliance with international regulations, there is a need to install navigation lights on the wing tips (red left, green right) and tail (white). “Tail” lights may be fitted to wing trailing edges for easier access. These provide high intensity light for identification of airplane position (navigation) and orientation. Navigation lights must be available during towing, hence there should be means to supply power to them from the battery or APU. AMTP017 | ELECTRICAL AND AVIONICS | ISSUE2 REV 1 | Page 7 of 286 ANTI-COLLISION BEACON LIGHTS These are red ‘flashing’ (or rotating) lights, one mounted on top, the other at the bottom, of the fuselage. These are to be turned on anytime an aircraft engine (not APU) is running. This is to provide an anti-collision warning on ground operation. Has lower intensity compared to strobe lights STROBE LIGHTS In some countries, it is mandatory to have white high intensity anti- collision lights at wing tips and tail (strobe lights). Some are designed to automatically operate during flight (weight off wheels). This is to provide an anti-collision warning in flight. LOGO LIGHTS Logo lights are normally installed on the upper surface of the horizontal stabilizers. They are to illuminate the emblem/logo painted in the vertical stabilizers. These are normally available on low altitude (such as take-off and landing) and on ground operation. AMTP017 | ELECTRICAL AND AVIONICS | ISSUE2 REV 1 | Page 8 of 286 1 – Navigation lights (Wings) 2 – Navigation lights (Tail) 3 – Anti-collision lights (Beacon and strobe) 4 – Logo lights EXTERIOR LIGHTS - LOCATION AMTP017 | ELECTRICAL AND AVIONICS | ISSUE2 REV 1 | Page 9 of 286 As an example of wing tip anti-collision lights, a strobe (xenon flashtube) anti-collision light is installed in each forward wing tip fairing on commercial aircraft. It is protected behind a clear acrylic lens. A cable assembly connects the light to its power supply unit. The power supply is mounted near the light assembly which provides high voltage output. However, later types of strobe lights using Light Emitting Diodes (LED) are now being introduced to commercial aircrafts with minor difference. AMTP017 | ELECTRICAL AND AVIONICS | ISSUE2 REV 1 | Page 10 of 286 SAFETY PRECAUTIONS Flash frequency of the lights should be between 40-100 cycles per minute. Strobe light units (e.g. quartz iodine crystal bulbs) use high voltage pulses (~500V) to release and accelerate electrons. The high- speed electrons bombard gas atoms, in turn producing light. - Direct and proximate exposure to the intense light flashes should be avoided as this can cause permanent eye damage. - Direct handling of quartz bulbs (used in discharge and some navigation lamps) with bare hands should be avoided as contamination causes premature failure. They should be handled using paper or cloth. - When performing maintenance on the anti-collision lighting system components, wait 10 minutes after power has been removed from system before handling components. This will permit high voltage capacitors to discharge. - The high intensities of strobe light flashes may cause some eye discomfort if observed from a close range. All personnel working in areas close to strobe light(s)are advised to avoid looking directly at strobe light when it is flashing AMTP017 | ELECTRICAL AND AVIONICS | ISSUE2 REV 1 | Page 11 of 286 SAFETY PRECAUTIONS AMTP017 | ELECTRICAL AND AVIONICS | ISSUE2 REV 1 | Page 12 of 286 LANDING LIGHTS Landing lamps are normally installed on wing leading edges. Some types of landing lamps are retractable (usually near wing tips or possibly on the fuselage), but the risk of mechanical failure discourages their use. At high speed, forces of high velocity air can partially retract the lamps. AMTP017 | ELECTRICAL AND AVIONICS | ISSUE2 REV 1 | Page 13 of 286 ICE INSPECTION LIGHTS Used to illuminate the wing leading edges and engine nacelles for visual inspection purposes. Normally 28 V A.C. ground supplies with local switches. The number of the lights installed depends on the aircraft type as well as the name of the system. As example, airbus calls it as “wing and engine” scan lights for the purpose of checking visually the leading edge and engine nacelle for its condition including ice build-up. AMTP017 | ELECTRICAL AND AVIONICS | ISSUE2 REV 1 | Page 14 of 286 TAXI LAMPS May be located on wing leading edges, fuselage or the nose landing gear. These are normally 28 V A.C. sealed beam (250-600W). RUNWAY TURNOFF LIGHTS The two runway turnoff lights use sealed beam incandescent lamps and are mounted in the nose wheel light control panel housing on the nose gear. The lamps are aimed approximately 65 degrees left and right of the airplane centerline. TAKE OFF LIGHTS Normally used with taxi lights or a taxi lamp which illuminates on a higher intensity (multiple filaments) with switch/es on take-off configuration. AMTP017 | ELECTRICAL AND AVIONICS | ISSUE2 REV 1 | Page 15 of 286 EXAMPLE OF TAXI, TAKEOFF AND RUNWAY TURNOFF LIGHT INSTALLATION (A320) AMTP017 | ELECTRICAL AND AVIONICS | ISSUE2 REV 1 | Page 16 of 286 COMPARTMENT LIGHTS Compartment illumination lights can be found in cargo compartments, stabilizer access, electronics equipment, landing gear, refueling etc. They operate on 28 V A.C. ground supplies with local switches. A different power supply is used if the crew needs to view or enter an area in flight, (e.g. view ports in the floor for aft cargo bays or landing gear lock mechanisms). Service interphone points are normally co-located with compartment light switches. AMTP017 | ELECTRICAL AND AVIONICS | ISSUE2 REV 1 | Page 17 of 286 INTERNAL LIGHTS FLIGHT DECK General lighting in the flight deck is designed to give maximum illumination for access and servicing when aircraft is on the ground, or to overcome temporary vision difficulties caused by lightning when airborne. Instrument panels and surrounding areas are illuminated by 115V white fluorescent tubes, (not "warm white") located under glare shields, which function to prevent direct sunlight shining onto the panels. Individual switches are provided for pilots, flight engineer and navigator, plus a pilot's "storm" override switch, which turns on all of the tubes Subdued general/background lighting is provided by small dome and glare shield incandescent filaments powered on 28V A.C. supplies. Whenever A.C. is unavailable, 28V D.C. (battery) should automatically supply such lights. Access to internal lights is from the rear, by lowering the panel, or requires removal of the instrument to a dust free workshop. Use of electroluminescent materials is becoming more popular to solve the filament failure problem. They are highly reliable and can operate at low voltage (and current). AMTP017 | ELECTRICAL AND AVIONICS | ISSUE2 REV 1 | Page 18 of 286 AMTP017 | ELECTRICAL AND AVIONICS | ISSUE2 REV 1 | Page 19 of 286 TRANS-ILLUMINATED COVERS Some flight deck panels have trans-illuminated covers. Holes are cut for instruments, switches and warning lamps; controls and indicators are identified with etched markings Besides the etching, the rest of the surface of the plastic cover is painted black (or grey), to allow light from the lamps to shine through the etching only. Faulty lamps can be easily replaced by unscrewing the cap on the front of the panel. AMTP017 | ELECTRICAL AND AVIONICS | ISSUE2 REV 1 | Page 20 of 286 Panel lights illuminate the instrument panels and include floodlights for external panel illumination and integral panel lights (light plates, lighted instruments and switch lights). Flight deck panel lighting circuits are for captain’s panel lights, first officer’s panel lights, overhead panel lights, glare shield panel lights and aisle stand lights. The integral panel lights include the internally lighted individual instruments, switch lights (which generally have one of the segments, the switch position indicator, illuminated) and panel lettering and panel schematics (lighted by light plates). External floodlights are provided for the pilots main and center panels, the glare shield panel and the aisle stand. Overhead dome lights provide overall illumination. These incandescent dome lights are controlled by a knob on the left light control module. An optional storm light switch overrides the dome light control. AMTP017 | ELECTRICAL AND AVIONICS | ISSUE2 REV 1 | Page 21 of 286 FLIGHT DECK LIGHTING AMTP017 | ELECTRICAL AND AVIONICS | ISSUE2 REV 1 | Page 22 of 286 PASSENGER CABIN Small 28V incandescent filaments in the cabins provide soft lighting for "night" settings, as well as aisles doorways and reading lights. Additional lighting comes from fluorescent wall, window and ceiling tubes. Conventional "hot cathode" fluorescent tubes impose a weight penalty, as they require a heated starting switch and an inductor to "strike". Such tubes may exhibit an unpredictable time lag and flicker when initially turned on, or when power supply is temporarily interrupted. Hence, they are unsuitable for large passenger cabins. Using cold cathode tubes eliminates the weight and starting problems. They generally have better efficiency and reliability but they require considerably higher voltages, (200 500 V. approx.) and can be very hazardous when fittings are exposed. Their intensity can be changed by use of extra components (and wiring). Another method employed by the aircraft manufacturer is to arrange tubes in groups, which may be switched off independently to achieve less brightness. Generally, control of the passenger cabin lights depends on the system used by different manufacturers, but the concept remains the same that a centralized control/system should be available for a large number of lights used on commercial aircraft. System and wiring design may also differ from each manufacturer’s perspective. One example being used by Airbus commercial aircraft is the CIDS (Cabin Intercommunication Data System) which provides majority of the control for the cabin system including audio, interphone system and lights. AMTP017 | ELECTRICAL AND AVIONICS | ISSUE2 REV 1 | Page 23 of 286 PASSENGER CABIN LIGHTING AMTP017 | ELECTRICAL AND AVIONICS | ISSUE2 REV 1 | Page 24 of 286 GALLEYS AND TOILETS Lights are usually uses different power supply for some halogen lamps (i.e. mirror light) and fluorescent lamps (tubes). These lights normally connected with the door locking mechanism for switching and/or dimming functions. Some may have different logic for maintenance condition such as removing the dimming function on ground maintenance to provide full illumination of the lavatories whichever is the condition of the door locking mechanism. AMTP017 | ELECTRICAL AND AVIONICS | ISSUE2 REV 1 | Page 25 of 286 LIGHTS CONTROL Cabin lights are controlled by a centralized system such as the ACESS (Advanced Cabin Entertainment/Service System) in some Boeing aircraft and CIDS (Cabin Intercommunication Data System) in Airbus. The purpose is to have a common computer or system that manages the illumination of the cabin integral lights, thus eliminating the need of individual switches. We can use the CIDS as an example. Although CIDS is also used with various system such as Cabin Interphone (ATA23), water and waste system (ATA38), Passenger Address, Passenger service and others, it is well known that the system is also capable to control and manage the cabin lights (dimming and mode selections), passenger lights, and information lights (no smoking and fasten seat belts) Using the CIDS as example, the system will require a series of components for routing the signals and information from the control to the lights. CABIN INTERCOMMUNICATION DATA SYSTEM (CIDS) DIRECTORS CIDS data are processed by two directors, one is normally active and the other in standby. FAP In enhanced system, a Flight Attendant Panel is used as an input device to control the cabin systems such as the Cabin Lights and its other functions. The FAP is a touch screen device which provides indication and control to the cabin systems. DEUs Decoder/Encoder Units are used as an interface for the directors and the output devices. (i.e. lights, loud speaker, information signs, intercom handset, chimes) AMTP017 | ELECTRICAL AND AVIONICS | ISSUE2 REV 1 | Page 26 of 286 CIDS components (A320 Enhanced) AMTP017 | ELECTRICAL AND AVIONICS | ISSUE2 REV 1 | Page 27 of 286 PASSENGER SIGNS They are used to indicate messages of "no smoking" and "fasten belts" or "return to seat" and can be found at seat overhead service units and galleys. They are operated from the flight deck and supplied by a high priority bus. Indicators for cabin crew are at strategic points within the cabin and an aural chime accompanies the pilot’s switching action. "No smoking" signs normally come on automatically when emergency oxygen system is deployed. "Toilets occupied" signs are wired in series with door bolt switches of toilets at same galley. AMTP017 | ELECTRICAL AND AVIONICS | ISSUE2 REV 1 | Page 28 of 286 CALL SYSTEMS They alert the cabin crew to passenger needs, and can be activated from seats or toilets. A ‘chime’ is sounded and a "hold in" circuit, (cancelled by the crew) illuminates indication lights at crew stations and the seat or toilet, until cancelled by the crew. Communication between cabin crew at different stations in the cabin or with flight crew is normally carried out with handsets that activate call lights and chimes. Similar systems are in place for ground/flight deck communications. In large aircraft, multiplexed systems are used to achieve cable and component weight savings AMTP017 | ELECTRICAL AND AVIONICS | ISSUE2 REV 1 | Page 29 of 286 STANDBY AND EMERGENCY LIGHTS The flight deck and passenger cabin have standby lights which automatically operate from the main aircraft battery should the generated supplies fail. They are either separate lamps or a number of normal lamps, which are switched on at full brightness by a relay action. When essential supplies fail, emergency lights and signs indicating exits, exit paths and “over-wing” routes come on automatically. A totally independent power supply is mandatory. Each light is powered either by centralized alkaline batteries, or individual cells. Under normal conditions, they are trickle charged; when the charging supply fails, they provide power to the lights Certain aircraft have units that can be removed and used as torches, but the trend is towards centralized systems. Electro-luminescent light units are in use and have the advantage of giving a reflective exit sign should the batteries fail. AMTP017 | ELECTRICAL AND AVIONICS | ISSUE2 REV 1 | Page 30 of 286 EMERGENCY LIGHTING – CABIN AMTP017 | ELECTRICAL AND AVIONICS | ISSUE2 REV 1 | Page 31 of 286 EMERGENCY LIGHTS – TYPICAL LOCATION AMTP017 | ELECTRICAL AND AVIONICS | ISSUE2 REV 1 | Page 32 of 286 (ATA 24) ELECTRICAL POWER AMTP017 | ELECTRICAL AND AVIONICS | ISSUE2 REV 1 | Page 33 of 286 BATTERIES INTRODUCTION DC Electrical Power storage devices are divided in two types i.e. Primary Cells and Secondary Cells. Main difference between them is recharging capability. Secondary cells can be recharged while primary cells must be disposed-off when used up. Dry primary cells are not very common on aircraft as they require frequent checking and replacement. Some applications are door mounted escape slides (gas cylinder low pressure lights), crew torches and megaphones. Water activated cells are fitted to life jackets to power torches (about 1.2 V. for 16 - 20 hours), ULBs for the CVR and DFDR etc. Small sealed secondary cells (alkaline) are used to power emergency lighting (usually installed in "power packs" with a "trickle" charge circuit). The charge current of sealed units has to be limited to avoid thermal "runaway" and explosion. Main batteries are made of high capacity secondary cells to supply important circuits and systems (should generators fail): Radio and inter-communication Fuel Controls (e.g. shut-off and transfer valves) Vital instrumentation Fire extinguishing Standby lighting and other vital functions ATA 34: Navigation systems may have separate standby batteries to avoid computer power supply interruptions. AMTP017 | ELECTRICAL AND AVIONICS | ISSUE2 REV 1 | Page 34 of 286 If vital systems operate from higher voltage, or A.C., the battery output has to be converted by inverters, or an alternative supply must be available (e.g. ram air driven generator). The main battery may also be required for: Engine or A.P.U. starting. Brake pressure when towing, (and navigation lights) ‘Main’ batteries on the aircraft can be Acid or Alkaline type. Before about 1970, mostly lead-acid batteries were employed as they are reliable and easy to monitor. Furthermore, their voltage variation could be tolerated. Many essential systems now depend on strictly regulated voltage and nickel-cadmium alkaline batteries meet this requirement. LEAD ACID BATTERIES Main elements in the batteries are positive (lead peroxide) and negative plates (pure lead) dipped in an electrolyte solution (dilute sulfuric acid) contained in a suitable container. When fully charged, off-load voltage, and electrolyte S.G., are high. Charge current practically falls to zero near full charge. Under load, the voltage decreases, but must not fall below 22.5 Volts under prescribed test conditions. Nominal voltage of a lead-acid cell is 2 V; so twelve cells are needed for 24 V. If a cell voltage falls below 1.8 V under specified workshop load test conditions, it is discarded for aviation applications. Constant voltage charged – Battery is directly connected to the bus (conductive bus bar). No special charger is required for lead acid type of batteries. Take note that recent models of commercial aircraft no longer use this type of aircraft battery. AMTP017 | ELECTRICAL AND AVIONICS | ISSUE2 REV 1 | Page 35 of 286 NICKEL CADMIUM BATTERIES ("NI- CD") The plates are nickel hydroxide in the positive plates and cadmium hydroxide in the negative plates. Electrolyte is a solution of potassium hydroxide (KOH) in distilled water. An aircraft charger (i.e. BCL – Battery Charge Limiter) is designed to reduce overcharging by regulating the duration of charge current. In overcharge, the charging current decomposes the water in the electrolyte to hydrogen and oxygen gas, which results in water loss from the cells. This loss of water from the cells will not damage until the electrolyte level falls below the top of the plates. To prevent battery damage due to overheating, a thermostat mounted on a battery link controls the charger. The battery charger also prevents sleepiness of the batteries. Sleepiness – ni-cd battery losing its capacity when exposed to abnormal charge and discharge cycle over a period of time. Advantages of NI-CD Has a longer life span provided that it is installed with a special battery charger (constant current charger). During battery discharge, voltage and specific gravity hardly vary. Voltage maintains very well until almost fully discharged with very little drop even under heavy loads. Disadvantages More sensitive – thermal runaway is more likely to occur with Ni-Cd when exposed to high temperatures. Needs special charger to avoid sleepiness due to abnormal cycles of being charged and discharged. AMTP017 | ELECTRICAL AND AVIONICS | ISSUE2 REV 1 | Page 36 of 286 NICKEL CADMIUM BATTERIES AS INSTALLED IN AIRCRAFT AMTP017 | ELECTRICAL AND AVIONICS | ISSUE2 REV 1 | Page 37 of 286 Thermal runaway This is a condition most likely to occur when a heavy charge current is flowing in warm conditions. As lead-acid batteries are normally constant voltage charged, the charge current would increase as rising temperature causes internal resistance to fall. This generates more heat, further reducing resistance in a "runaway" cycle and causing over-heating of the cells, damaging them and resulting in over-flow of the acid solution and damage to the surrounding structure. Careful monitoring is therefore necessary on the ground. Batteries’ fumes should be vented out so the location of these batteries may be on an unpressurized area such as the nose landing gear wheel well or in a pressurized area but must have vent hose installation The batteries are located in an area where it will create minimal damage to aircraft structures and components once a thermal runaway occurs. This is as designed by the manufacturer. AMTP017 | ELECTRICAL AND AVIONICS | ISSUE2 REV 1 | Page 38 of 286 SAFETY PRECAUTIONS AND FIRST AID If electrolyte is splashed on skin or eyes: 1. Thoroughly rise with water immediately. 2. Seek immediate medical attention if eves (or cuts) are affected. 3. After washing, for alkaline spillage neutralize with vinegar, lemon juice or boric acid solution; for acid use bicarbonate of soda solution. For electrolyte spillage on metal: 1. Soak up with sawdust or similar. 2. For acid, neutralize with a saturated solution of bicarbonate of soda. 3. For alkali neutralize with a saturated solution of boric acid. 4. Thoroughly wash, dry and re-protect, seeking advice if in doubt. For electrolyte spillage on fabric: 1. For acid, dab with ammonia. 2. For alkali, dab with boric acid solution. 3. Thoroughly water rinse. 4. Replace if in doubt. These are the normal safety procedures but take note that you must always use the procedure listed in the Aircraft Maintenance Manual (AMM) of the applicable aircraft as “Warning” and/or “Caution” messages. AMTP017 | ELECTRICAL AND AVIONICS | ISSUE2 REV 1 | Page 39 of 286 DC POWER GENERATION INTRODUCTION Main power system on large commercial aircraft is A.C. for the majority of equipment. However, they are dependent on D.C. from batteries for emergency/standby supplies. As the batteries are charged by 28 V.D.C. rectified from the A.C. supplies, D.C. generators are not fitted. Light aircraft, "commuter" aircraft and some larger turbo-prop types require a different approach. AMTP017 | ELECTRICAL AND AVIONICS | ISSUE2 REV 1 | Page 40 of 286 DC GENERATOR An aircraft D.C. generator should be able to supply full power at constant voltage over the operational speed range of the engine. Aircraft DC generators are self-excited even though the field winding appears to be wired separately. The field current is tapped from the generator output via a voltage regulator, making the generator effectively self-contained and independent of other supplies. E.M.F. variations must be automatically controlled to maintain steady output voltage regardless of engine speed or electrical load. This is achieved by a voltage regulator. BASIC PRINCIPLE AMTP017 | ELECTRICAL AND AVIONICS | ISSUE2 REV 1 | Page 41 of 286 Splits rings reverse the direction of electric current after every half revolution ensuring continuous flow of current in one direction. The role of commutator is to make continuous flow of current in same direction and also reversing the direction of current thus split ring is also a commutator. AMTP017 | ELECTRICAL AND AVIONICS | ISSUE2 REV 1 | Page 42 of 286 AC POWER GENERATION INTRODUCTION The following are some of the major considerations that resulted in the A.C. supplies now in use: Avionic equipment usually needs quite high and constant frequency/voltage A.C. A.C. can be readily transformed with practically no losses and alternators can simultaneously give different outputs. Cable weight and voltage drop can be minimized by using A.C. Fluorescent lighting and other A.C. loads require less power than D.C. equivalents. A.C. motors are more reliable at high altitudes and at temperature extremes, particularly for heavy loads, but require a constant frequency supply. AMTP017 | ELECTRICAL AND AVIONICS | ISSUE2 REV 1 | Page 43 of 286 ALTERNATOR A constant frequency alternator (or "A.C. generator") on the aircraft has to support full load at constant voltage and frequency regardless of engine speed. Commercial aircraft have 30-90 KVA continuous rated generators. Ratings of 150 KVA + are in use on some military aircraft. Achieving high performance depends largely on efficient cooling and "brushless" design. Optimum cooling can be obtained by: 1. Using very cold ram air (-56oC at 36000ft) for cooling. Very efficient induced air mass flow on the ground is also achieved by utilizing jet engine front stage compression. 2. Oil cooling is employed in some designs. Alternators with brush-slip rings have a serious limitation of altitude. Above about 25,000 ft. brushes wear off fast, making frequent maintenance necessary. High resistance and other brush problems also limited alternator ratings. Problems associated with brushes are avoided by the “Brushless” design. CONVENTIONAL ALTERNATOR A.C. generators may be "initially" self-excited by permanent magnets but require D.C. from an external source for sufficient field strength (and control), so are referred to as separately excited. Should the field circuit fail, only "residual" voltage from the magnets is produced. In a conventional design, rotating magnets induce a stator output. The transformed output is rectified and regulated to D.C. Controlled D.C. field is supplied via brushes and slip rings. AMTP017 | ELECTRICAL AND AVIONICS | ISSUE2 REV 1 | Page 44 of 286 CONVENTIONAL ALTERNATOR - PRINCIPLE AMTP017 | ELECTRICAL AND AVIONICS | ISSUE2 REV 1 | Page 45 of 286 Brushless Alternator Magnets induce three-phase A.C. in rotor "A.C. exciter" windings. The three-phase is full-wave rectified by diodes (in the rotor shaft) to give a rotating D.C. field. Three-phase A.C. is induced in stator "output" armature windings. The transformed output is rectified and regulated to D.C. D.C. is applied to stationary exciter. AMTP017 | ELECTRICAL AND AVIONICS | ISSUE2 REV 1 | Page 46 of 286 Control & Protection Control & Protection features are necessary, even in the simplest generator systems, to isolate the faulty part, like the generator. These features may be simple devices like fuses and circuit breakers or elaborate electronic circuits. Reverse current protection: A generator must always be protected against flow of current from the Load Bus to the generator. Hence it is necessary to ensure prompt isolation of a generator when its E.M.F. falls. The protection can also be adopted to provide automatic reconnection of the generator when it is once again ready to accept loads. Over voltage protection may be incorporated as part of a combined regulator/controller. Over voltage relay trips generator field circuit and line contactor. STARTER GENERATORS These are fitted to some DC powered aircraft to save cable and component weight. They are permanently coupled via a drive shaft and gear train. For starting, it runs as a fully compounded motor with the shunt winding supplied via a field change-over relay. When the relay is de-energized it connects the shunt field to the voltage regulator. AMTP017 | ELECTRICAL AND AVIONICS | ISSUE2 REV 1 | Page 47 of 286 APU STARTER-GENERATOR AMTP017 | ELECTRICAL AND AVIONICS | ISSUE2 REV 1 | Page 48 of 286 DRIVE AND FREQUENCY CONTROL Output voltage depends on number of conductors, field strength, and rate at which flux is cut. As such, generator rotation speed needs to be controlled. Constant frequency alternator systems were made possible by the development of constant speed drive units, ("CSD" or "CSU"). Within a range of engine speed or electrical load, the unit will always drive the alternator at the speed required for constant output frequency. Typical input speed range is 4300 - 8600 rpm for constant 6000 (or 8000) rpm output. The CSD is a self-contained hydraulic motor-pump unit that could compensate for a higher or lower engine drive speed. The CSD is mounted on the engine gearbox and drives the generator. The engine makes the effort in all cases (the CSD oil system cools and lubricates the pump/motor and replenishes losses). Electrical load changes should not affect alternator speed, as the rate of energy transfer should readily alter. When load increases, the engine puts in more effort, to supply it (more torque needed, so more fuel is demanded). AMTP017 | ELECTRICAL AND AVIONICS | ISSUE2 REV 1 | Page 49 of 286 CONSTANT SPEED DRIVE AMTP017 | ELECTRICAL AND AVIONICS | ISSUE2 REV 1 | Page 50 of 286 The functioning and condition of CSD are monitored using various sensors. Mounted on the CSD for the purpose are: Low oil pressure switch (warning lamp in flight deck). Over/under speed pressure switch (typically normally closed switch that opens with correct control pressure. Switch closes when overpressure or under speed condition occurs). Temperature sensing is carried out by an overheat switch and/or inlet and outlet temperature probes. Solenoid actuated disconnect mechanism. Electromagnetic governor trim (fitted if the aircraft has a parallel A.C. distribution system). Tachogenerator (for more sophisticated systems to monitor speed for indication/protection). AMTP017 | ELECTRICAL AND AVIONICS | ISSUE2 REV 1 | Page 51 of 286 SIMPLE CSD DISCONNECT MECHANISM DISCONNECTED CONNECTED AMTP017 | ELECTRICAL AND AVIONICS | ISSUE2 REV 1 | Page 52 of 286 Ground (external) Power Units (G.P.U) and airborne Auxiliary Power Units (A.P.U.) Operates at constant speed using fuel control. They do not need a CSD to drive the generator at constant speed. Frequency Wild alternator systems were commonly used before CSD development. The alternator is directly coupled to the engine gearbox. FREQUENCY WILD ALTERNATOR SYSTEM Such a system cannot be used for Reactive loads (consisting of inductances and capacitances), as the frequency is not constant. It can be only used for "real" (purely resistive) loads such as heaters. Other loads must be supplied by D.C. from large transformer - rectifier units. However, it was preferable to do so as, even with slip rings, alternators were able to give better high altitude performance than D.C. generators. The principle is still applied for smaller low altitude aircraft as the added weight and complexity of a CSD is usually not practical. AMTP017 | ELECTRICAL AND AVIONICS | ISSUE2 REV 1 | Page 53 of 286 Control & Protection The following figure shows a typical 3F constant frequency electrical generation system. The Voltage Regulator supplies and controls the generator field. TYPICAL THREE-PHASE STAR-CONNECTED CONSTANT FREQUENCY SYSTEM AMTP017 | ELECTRICAL AND AVIONICS | ISSUE2 REV 1 | Page 54 of 286 A Load Controller is necessary if a generator is to be operated in parallel with other generators. It is used to synchronize generator outputs by trimming C.S.D. governors. AMTP017 | ELECTRICAL AND AVIONICS | ISSUE2 REV 1 | Page 55 of 286 The C.S.D. Disconnect mechanism is solenoid controlled. The solenoid is energized by a guarded & wire-locked switch to disconnect the CSD from the engine gearbox. The switch may be placarded as "can only be re-connected on the ground". Operating the disconnect switch will also cause the GB (generator breaker) to trip. AMTP017 | ELECTRICAL AND AVIONICS | ISSUE2 REV 1 | Page 56 of 286 Control and Protection Panel contains the generator control relay or GCR (also termed as Field Relay) and also serves various contactor control and protection functions. AMTP017 | ELECTRICAL AND AVIONICS | ISSUE2 REV 1 | Page 57 of 286 GCR is normally closed (mechanically or electronically "latched") and trips (opens) when a fault occurs in the generator or its voltage regulator or wiring ("feeders" or GB/BTB). It can also be controlled by a switch in the flight deck. AMTP017 | ELECTRICAL AND AVIONICS | ISSUE2 REV 1 | Page 58 of 286 GB (generator breaker) or GCB (generator control breaker) connects the generator output to its bus. A control switch in the flight deck controls the GB. It is a mechanically latching contactor, which ensures that coil/supply failure does not cause it to open when it is required to be closed. The GCB trips under various conditions like CSD faults, GCR Trip, transfer of auxiliary power on bus. This ensures that an alternative supply to the bus does not "motor" the generator. AMTP017 | ELECTRICAL AND AVIONICS | ISSUE2 REV 1 | Page 59 of 286 Usually the Bus Tie Breaker (BTB) and GB are physically identical. A switch is provided on the control panel to control the BTB. Synchronizing (paralleling) control and/or protection are also functions of the control and protection unit. BTB INTER-CONNECTS LOAD BUSES AMTP017 | ELECTRICAL AND AVIONICS | ISSUE2 REV 1 | Page 60 of 286 EXAMPLE: A320 VOLTAGE REGULATION AND PROTECTION AMTP017 | ELECTRICAL AND AVIONICS | ISSUE2 REV 1 | Page 61 of 286 Various situations can lead to automatic tripping of the breakers: Instability can trip the GCR (and GB), possibly due to generator field stability winding open circuit. Over or under voltage, presumably resulting from a voltage regulator or generator field circuit fault, will automatically trip the GCR (and GB) Over or under excitation: Unequal excitation (field) current when operating in parallel. The BTB trips to isolate the affected generator along with its load bus. If the generator improves, it continues to supply its loads in isolation. If the isolation results in over or under voltage, the GCR (and GB) will also trip. Obviously in this case, the BTB will have to be reclosed. Over or under speed is sensed by the CSD speed switch, or by a tacho-generator, to trip the G.B. Nuisance trip protection is necessary when the engine is shut down after a flight and the GB's are tripped to allow external power supply to the buses. The external power contactor (not shown) has to close and its control circuit automatically trips the G.B's. If the CSD speed switch senses low speed, it will cause GB trip. e.g. for engine in-flight "shut down". If CSD is disconnected in flight, it will trip G.B. before speed switch. In such cases of speed related tripping, the GCR and BTB are not required to trip. The GCR need not trip as the generator is not bad and the BTB must not trip to allow an alternative supply, (another engine's generator or external power), to reach the load bus. The under voltage and under excitation protection circuits therefore have to be prevented from causing such "nuisance" tripping of the GCR and BTB so the speed switch is used to "block" their trip functions: Engine fire handle operation causes the G.C.R. and G.B. to trip (after a time delay to ensure operation of air and fuel valves etc. that are also controlled by the fire handle and possibly depending on the generator's output). AMTP017 | ELECTRICAL AND AVIONICS | ISSUE2 REV 1 | Page 62 of 286 The voltage regulation, control and protection features may all be contained in one generator control unit (GCU) for each generator (including the APU generator). A separate bus control unit (BCU) may be used for distribution (and paralleling) control and protection. Differential current protection is the most usual means adopted to protect against AC system distribution faults. Conventional fuses, circuit breakers or other devices are not practical for the protection of the supplies to buses. The high currents would demand cumbersome devices and failure of a device could result in unnecessary loss of supply. Differential protection system provides highly reliable monitoring of current diversion due to any fault within its zone. It is fully automatic and does not involve flight deck controls. The system makes use of various current transformers (CT) installed in the generation and distribution system. They are installed on the "cold" (neutral) generator wiring, on the engine, as well as the "hot" wiring at the distribution center. These CTs monitor current returning via the "star" point and distribution feeders downstream of GB. They are mounted inside the generator and at the power distribution centers. The small gauge transformer output wiring is connected so that the output of each cold transformer opposes the output of the hot transformer for the same line. The aircraft manufacturer takes care to ensure that all the current delivered by each phase of the generator has to pass through the appropriate hot transformer. In that case, the current returning to the generator, through a cold transformer, must also pass through the corresponding hot transformer and the resultant of their outputs will be zero. If a short circuit occurs in the protected zone, (the generator or its wiring or, in the case shown, the GB or BTB) hot transformer output will be zero (or certainly less than cold transformer), allowing input to the differential protection circuit of the control and protection unit (panel). Line to line fault protection may be less readily understood but can be explained by considering the circuits offered: AMTP017 | ELECTRICAL AND AVIONICS | ISSUE2 REV 1 | Page 63 of 286 HOT TRANSFORMERS (CT) (DISTRIBUTION PART) COLD TRANSFORMERS (CT) (GENERATION PART) The two generated phases connected by the faults will have a potential difference (p.d.) at any instant, causing current flow between them. It is therefore unlikely that sufficient supply can reach the distribution point for any current to pass through either hot transformer. AMTP017 | ELECTRICAL AND AVIONICS | ISSUE2 REV 1 | Page 64 of 286 Current transformer principle Current transformer Example AMTP017 | ELECTRICAL AND AVIONICS | ISSUE2 REV 1 | Page 65 of 286 Over-current protection may supplement the differential protection system to trip the G.B. if the system places excessive load on the generator. Three additional current transformers may be fitted to monitor the current of each phase (or the "hot" differential transformers may serve a dual role.) AMTP017 | ELECTRICAL AND AVIONICS | ISSUE2 REV 1 | Page 66 of 286 EXAMPLE: A320 EGS Control and Protection system AMTP017 | ELECTRICAL AND AVIONICS | ISSUE2 REV 1 | Page 67 of 286 EMERGENCY POWER GENERATION INTRODUCTION The emergency AC generation enables part of the distribution network to be recovered in case of loss of the main generation sources and of non-availability of the auxiliary generation (emergency configuration). The Emergency AC power can be obtained from two different ways and is mainly composed of: 1. The 5000VA(7000VA), AC three-phase, 115 volts standby generator which is driven by a hydraulic motor driven by the hydraulic system and which mainly supplies the AC emergency bus bar and a part of the AC essential bus bars. 2. A 1000VA single-phase static inverter supplied by the onboard batteries through the DC essential bus bar and essentially supplying the AC emergency bus bar. 3. Some are installed with Ram Air Turbine Generators. EXAMPLE: A320 Emergency Generation System Summary: The A320 uses an emergency generator called CSM/G (Constant Speed Motor/Generator). On the A320, when the electrical emergency condition is met, the CSM/G is driven by the blue hydraulic system via the Ram Air Turbine. Please take note that the Ram Air Turbine of the A320 has no internal generator, it only provides hydraulic pressure (blue system) to the CSM/G. AMTP017 | ELECTRICAL AND AVIONICS | ISSUE2 REV 1 | Page 68 of 286 A320 ELECTRICAL SYSTEM EMERGENCY CONFIGURATION (OVERVIEW) AMTP017 | ELECTRICAL AND AVIONICS | ISSUE2 REV 1 | Page 69 of 286 A320 EMERGENCY GENERATION (AUTOMATIC) OPERATION If AC BUS 1 and 2 are lost above a given airspeed (100 kts), the Ram Air Turbine (RAT) will extend automatically. As the AC generator is not yet available, the AC ESSential BUS and DC ESS BUS are respectively supplied by the STATic INVerter and battery 2. The activation of the emergency generator via the blue hydraulic system takes place only if the landing gear is not compressed. When the emergency generator is available, it supplies the AC ESS BUS and via ESS Transformer Rectifier (TR), the DC ESS BUS. As the nose landing gear is compressed, the AC ESS BUS and DC ESS BUS are respectively supplied by the STAT INV and the battery 2. AMTP017 | ELECTRICAL AND AVIONICS | ISSUE2 REV 1 | Page 70 of 286 EXAMPLE: A320 EMERGENCY GENERATOR – DEPLOYMENT OPERATION AMTP017 | ELECTRICAL AND AVIONICS | ISSUE2 REV 1 | Page 71 of 286 STATIC INVERTER Semi-conductor development has made high power solid-state "static" inverters possible doing away with noisy rotary invertors in the early days. There is a need for inversion of D.C. to A.C. to supply the following: "Standby" or emergency A.C. bus bars on aircraft with constant frequency A.C. systems. Peculiar frequencies of A.C. within Avionic components (or for razor sockets). Constant frequency A.C. busses for avionic equipment on aircraft with D.C., or frequency wild A.C./D.C. systems. EXAMPLE: A320 STATIC INVERTER A STATic INVerter transforms the direct current from battery 1 into a single-phase alternating current. The STAT INV characteristics are: - 1 kVA nominal power, - 115V AC, 400 Hz, single phase. The STAT INV is used in the following cases: - APU start (supply of fuel pump), - Ram Air Turbine (RAT) deployment, - engine start on battery (ignition), - emergency configuration. AMTP017 | ELECTRICAL AND AVIONICS | ISSUE2 REV 1 | Page 72 of 286 EXAMPLE: A320 EPGS COMPONENT LOCATIONS AMTP017 | ELECTRICAL AND AVIONICS | ISSUE2 REV 1 | Page 73 of 286 EXAMPLE: A320 EPGS COMPONENT LOCATIONS AMTP017 | ELECTRICAL AND AVIONICS | ISSUE2 REV 1 | Page 74 of 286 EXAMPLE: A320 EPGS COMPONENT LOCATIONS AMTP017 | ELECTRICAL AND AVIONICS | ISSUE2 REV 1 | Page 75 of 286 RAT GENERATOR The configuration on the B777 differs from that on the A320 and will be discussed to illustrate that there are other possibilities for emergency power generation depending on the design by airplane manufacturers. The Ram Air Turbine (RAT) generator supplies 115 Volts three-phase emergency AC power when normal power sources are not available. This generator on the B777 has a capacity of 7.5 KVA. When the RAT deploys, the propeller/governor unit turns the input shaft of the generator and hydraulic pump. The generator changes the energy of the turning shaft into ac power. The frequency is the result of the rotational speed of the of the RAT propeller/ governor unit. The frequency range is from 392 Hz to 510 Hz. AMTP017 | ELECTRICAL AND AVIONICS | ISSUE2 REV 1 | Page 76 of 286 RAT GENERATOR (B777) AMTP017 | ELECTRICAL AND AVIONICS | ISSUE2 REV 1 | Page 77 of 286 TRANSFORMERS AND RECTIFIERS Roles of Transformers may be summarized as: Increasing voltage to supply fluorescent tubes. Supplying 28 V. A.C. bus bars (mainly for lights and instruments). Supplies "built-in" to avionic equipment. Monitoring voltage or current for control or indication ("metering"). Saving cable weight by "stepping down" with local transformers at equipment. REDUCING CURRENT/CABLE WEIGHT The weight added by the transformer is significantly less than that of a heavier gauge cable running the length of a cabin or along a wing. AMTP017 | ELECTRICAL AND AVIONICS | ISSUE2 REV 1 | Page 78 of 286 Roles of Rectifiers may be summarized as: 1. “BLOCKING": (isolation of one circuit from another whilst allowing a common function to be served, either in component internal circuits or in aircraft wiring). 2. D.C. SUPPLY: The aircraft's regulated three phase power supply is stepped down, (by transformers), and then rectified in combined transformer/rectifier units (TRU), to supply the 28V. D.C. bus bars for battery charging and other D.C. loads. Small, similar, power supply units may be included in avionic equipment, which will also have many "diode" rectifier applications. “In most aircraft, the term TRU (Transformer Rectifier Unit) is a combination of the Transformer which steps down 115VAC to a smaller voltage and Rectifier which converts this lower voltage into a 28VDC supply.” TRANSFORMER SAFETY Connections are often exposed and severe burns or shock can occur. As autotransformers are often used remember that the secondary is not isolated from the primary. Avoid working near transformers with power applied and never wear rings or bracelets at work as they can become welded to connections, making an error a fatality! Current transformer secondary connections must be short-circuited (whilst the primary is "dead") if any part of their circuit is to be disturbed. AMTP017 | ELECTRICAL AND AVIONICS | ISSUE2 REV 1 | Page 79 of 286 POWER DISTRIBUTION MULTI-GENERATOR DISTRIBUTION A typical switchgear arrangement to connect alternators to loads is shown in the following "line" diagram. EXAMLE 1 (B747 AC ELEC SYS) AMTP017 | ELECTRICAL AND AVIONICS | ISSUE2 REV 1 | Page 80 of 286 EXAMPLE 2 (A320 ELECTRICAL SYSTEM OVERVIEW) AMTP017 | ELECTRICAL AND AVIONICS | ISSUE2 REV 1 | Page 81 of 286 NON-PARALLELED SYSTEM A non-paralleled system would normally operate with the (GB,GCB)GLC's closed and the (BTB)BTC's open. Contactor interlock ensures that BTC's close if a GLC opens (fault detection or using external/APU power). Such systems are usually restricted to smaller two or three engine jet aircraft designed for operation without a flight engineer and minimizing the control and monitoring tasks of the pilots. The design engineer has to ensure that loads are equally allocated to the generator busses. A load controller is not necessary and the voltage regulators will individually respond to reactive load. PARALLELED AND SYNCHRONIZED SYSTEM Most constant frequency aircraft systems have a synchronized bus bar system, with loads equally shared by each alternator. Connection of alternators to common bus bars is known as parallel operation (using the BTB's). If the output of one alternator is at its maximum whilst another is at its minimum, a heavy current will flow between them if they are connected. The "high" output will be practically short-circuited by the low resistance armature windings of the other. The "low" output alternator will be motored against its drive (which may shear). To avoid this, the following conditions are necessary before paralleling: Voltage and frequency the same (200V line, 400Hz) Phase rotation the same (A-B-C) Output synchronized (same f of each reaching peak same time) In summary, the adjustment of an alternator’s output to synchronize with the other alternator (of the other engine/s) is achieved by adjusting the CSD (input) speed via the load controllers or governor trimmer, and by adjusting the excitation field to either stronger or weaker excitation via the voltage regulator (function of the Generator Control Unit). Note that the APU generators are not synchronized. APU Generators are high capacity generators that is able to supply most of aircraft’s electrical loads. AMTP017 | ELECTRICAL AND AVIONICS | ISSUE2 REV 1 | Page 82 of 286 EXTERNAL/GROUND POWER The Connected Light illuminates when the truck supply is available on the aircraft. (The voltage and frequency should have been checked, by referring to meters on the truck, and a heavy-duty relay on the truck will have closed in response to a switch on the truck). Most aircraft have protection features against connection of a faulty external supply. With the plug properly connected, pushing and holding the control switch on the truck will cause the truck's relay to energize and supply the aircraft. The logic in the aircraft's external power control unit will output if its conditions are OK and, provided the plug is properly pushed into the aircraft's receptacle, the truck's relay will hold. The flight deck selector switch can then be used (and the connected lights will indicate). Should the plug be wholly or partially removed, the magnetically held flight deck switch will automatically return to "off". Also, the truck's relay should disengage before the three phase supply pins' contact is broken. AMTP017 | ELECTRICAL AND AVIONICS | ISSUE2 REV 1 | Page 83 of 286 EXAMPLE: A320 EXTERNAL POWER RECEPTACLE AMTP017 | ELECTRICAL AND AVIONICS | ISSUE2 REV 1 | Page 84 of 286 LATER GENERATION SYSTEM EXAMPLE Modern aircraft combines the CSD and Generator into an integrated unit called Integrated Drive Generator (IDG). The A320 is equipped with two IDGs. The generator portion delivers 3 phase, 400 Hz, 115 Volts ac at 90 KVA. The CSD portion maintains the generator at a constant 12,000 rpm during normal operating conditions (input of 4,900 to 9,120 rpm). This ensures that the generator delivers a steady 400 Hz of frequency. AMTP017 | ELECTRICAL AND AVIONICS | ISSUE2 REV 1 | Page 85 of 286 No Break Power Transfer (NBPT) This term is used to electrical systems that is not using any paralleling or synchronizing, the main concept of NBPT is to allow transfer of supply from one generator to another without any power interruptions. This means that two generators will be allowed to be synchronized for a very short period of time before one of them disengages to allow transferring of supply without any interruptions (break). Note that power interruptions even in a short period of time can damage electrical components and LRUs, some may also malfunction from their normal operation. Most of the modern aircraft uses this approach in their non-paralleled electrical system design. AMTP017 | ELECTRICAL AND AVIONICS | ISSUE2 REV 1 | Page 86 of 286 (ATA 31) INSTRUMENTS/RECORDING SYSTEM AMTP017 | ELECTRICAL AND AVIONICS | ISSUE2 REV 1 | Page 87 of 286 PITOT-STATIC SYSTEM An aircraft’s Pitot-Static system senses the total pressure generated as a result of forward movement of the aircraft and the static pressure of the atmosphere surrounding it. It outputs these data to different instruments in terms of speed, altitude and rate of change of altitude (vertical speed). A simple system consists of a pitot-static tube (combination), or pressure head, three primary flight instruments (airspeed indicator, altimeter and vertical speed indicator) and interconnected pipelines and drains. Additional note: some term may define the pitot pressure to be a positive pressure while some term may define the static pressure to be a negative pressure due to suction capability due to Bernoulli’s principle. AMTP017 | ELECTRICAL AND AVIONICS | ISSUE2 REV 1 | Page 88 of 286 BASIC PITOT-STATIC SYSTEM AMTP017 | ELECTRICAL AND AVIONICS | ISSUE2 REV 1 | Page 89 of 286 PITOT-STATIC TUBE (Principle) The pitot static tube supplies the dynamic (pitot) and/or static pressure to the air speed indicator, altimeter, vertical speed indicator and Mach meter. L D B G I A E J C AMTP017 | ELECTRICAL AND AVIONICS | ISSUE2 REV 1 | Page 90 of 286 It is installed outside the aircraft in a region of undisturbed air (near the nose or leading edges). In reference to the previous figure, oncoming pressure of the air stream at A is transmitted around the baffle B and along the tube to C, then through the tube D to the instrument. Accumulated moisture is allowed to escape through drain hole E. Hole G allows the static pressure to enter and this is transmitted along the tube I to the instrument. Ice is prevented from forming by the heater element J. Lead L connects these to the aircraft power supply. STATIC VENTS Air disturbances causes the static-pressure measuring section of a pitot-static system to measure higher pressure than free-stream static pressure, resulting in what is known as a position error. Hence, the straightforward and logical solution is to remove them from the pitot probe and locate elsewhere on the aircraft. This is adopted by many types of aircraft, using a probe that senses pitot pressure only, together with a static vent at the sides of the fuselage. The static vent for some light aircraft is simply a hole drilled in the fuselage skin, while for more complex aircraft systems specially contoured metal vent plates are fitted to the skin. AMTP017 | ELECTRICAL AND AVIONICS | ISSUE2 REV 1 | Page 91 of 286 PITOT PROBE STATIC PORTS AMTP017 | ELECTRICAL AND AVIONICS | ISSUE2 REV 1 | Page 92 of 286 LOCATION OF PRESSURE HEAD AND STATIC VENTS Aircraft that operates at speeds below that of sound typically have their probes located ahead of a wing tip, ahead of a vertical stabilizer, or at the side of a fuselage nose section. At speeds above that of sound, the preferred location for the probe is ahead of the fuselage nose. Independent static vents, if available, are always installed one on either side of the fuselage skin. They are interconnected so as to minimize dynamic pressure effects due to yawing or sideslip of the aircraft. ALTIMETER The altimeter indicates the altitude at which an airplane is flying by measuring atmospheric pressure. It is similar therefore to an aneroid barometer. The height of the column of air above an aircraft decreases as an aircraft climbs away from the earth's surface. The weight of the column decreases and hence exerts less pressure; therefore, atmospheric pressure decreases with height. The pressure at any point above sea- level can be used to determine the altitude, if the atmospheric pressure at sea-level and the rate of decrease of pressure with height is known. Flight operating techniques stipulates the setting of altimeters to the barometric pressures prevailing at various flight levels and airfields. Setting, or barometric correction, of the altimeters is to make it read zero at that set pressure reference. Setting is crucial in maintaining adequate altitude separation between aircraft, and terrain clearance during take-off and landing. The pilot makes the settings through requesting ground control centers to transmit current meteorological data. AMTP017 | ELECTRICAL AND AVIONICS | ISSUE2 REV 1 | Page 93 of 286 THE SIMPLE ALTIMETER (Principle) The simple altimeter has a single diaphragm that has been evacuated and sealed operating a single pointer. The instrument is an airtight case, the interior of which is supplied with atmospheric pressure by a tube connecting it to the static line. Within the instrument, a partially evacuated aneroid capsule is secured at the center of one of its faces to a base rigidly fixed to the casing. It tends to collapse under surrounding atmospheric pressure but a strong leaf spring prevents this. As the aircraft gains height, atmospheric pressure drops and the new relatively stronger spring force pull the capsule faces further apart. A system of levers magnifies this movement and transmits this to a pointer moving across a calibrated dial. AMTP017 | ELECTRICAL AND AVIONICS | ISSUE2 REV 1 | Page 94 of 286 The vertical speed indicator (VSI) is used to assist the pilot in establishing a climb or descent so as to gain or lose a specified altitude within a set amount of time. It is also known as rate-of-climb (ROC) indicator. AMTP017 | ELECTRICAL AND AVIONICS | ISSUE2 REV 1 | Page 95 of 286 The instrument case is sealed and airtight except an opening at the rate from which static pressure is admitted. A zero adjustment screw for setting the pointer is provided on the front of the instrument, either at the bottom right or bottom center. In the rate of climb indicator, the rate of change of atmospheric pressure is measured and the change is displayed in terms of rate of climb or descent. It utilizes the principle of measuring the differential pressure between two chambers, one within the other. Atmospheric pressure is delivered directly to the inner chamber, and through a calibrated restrictor to the outer chamber. During a climb, atmospheric pressure decreases, the lag rate between the outer and inner chambers is a measure of the rate of climb of the aircraft. During aircraft descent, a similar lag rate results from the pressure increase and this is a measure of the rate of descent. The resultant differential pressure causes capsule movement, which gets transmitted to the pointer to indicate climb or descent. In level flight, equal pressures exist inside the capsule and case and the pointer therefore remains stationary on zero. AMTP017 | ELECTRICAL AND AVIONICS | ISSUE2 REV 1 | Page 96 of 286 (a) Level Flight Zero differential pressure cross capsule AMTP017 | ELECTRICAL AND AVIONICS | ISSUE2 REV 1 | Page 97 of 286 b) Aircraft Descending Metering unit maintains case pressure lower than capsule pressure, changing it at the same rate and thereby creating a constant differential pressure across capsule c) Aircraft Climbing Metering unit creates a constant differential pressure across capsule by maintaining case pressure higher than capsule pressure AMTP017 | ELECTRICAL AND AVIONICS | ISSUE2 REV 1 | Page 98 of 286 AIRSPEED INDICATOR The Airspeed Indicator shows how fast an airplane is travelling relative to the air through which it is flying. It provides the pilot with the indicated airspeed (IAS) of his aircraft. Airspeed is an important parameter in flight as it determines the amount of aerodynamic lift acting on the aircraft and also its performance. For instance, every aircraft has a minimum airspeed and operating it below this speed will cause it to stall. Each individual aircraft is also designed to withstand a maximum safe airspeed and a cruising airspeed for efficiency. AMTP017 | ELECTRICAL AND AVIONICS | ISSUE2 REV 1 | Page 99 of 286 IAS AND TAS RELATIONSHIP Calibration of the A.S.I for correct reading can be done only for a single density (sea-level). When operating at a given true air speed (T.A.S.) under such conditions, the A.S.I. would show an indicated air speed (I.A.S.) equal to the T.A.S. At altitudes higher than sea-level, density decreases and the same T.A.S. will produce a lower dynamic pressure so that the I.A.S. is reduced. To overcome the problem of lower air density on hot days and at high- elevation aerodromes, an aircraft must accelerate to a higher speed (i.e. TAS) to generate sufficient lift for take-off. (IAS shown on the ASI will remain the same.) This, coupled with possibly poorer performance from the engine-propeller, will mean a longer take-off distance is required. AMTP017 | ELECTRICAL AND AVIONICS | ISSUE2 REV 1 | Page 100 of 286 TOTAL AIR TEMPERATURE (TAT) Total air temperature (TAT) is the static air temperature (SAT) plus the rise in temperature due to the pitot effect. Pitot pressure is static pressure increased by a pressure factor that results from forward motion of the airplane through the air. Similarly, total air temperature is static air temperature increased by an amount accounted for by the forward motion of the airplane through the air. Total air temperature is of great importance in setting up the operating conditions of a jet engine since the temperature of the air into the jet engine is static air temperature increased by the pitot factor. It is also possible to derive static air temperature from total air temperature and pitot pressure information. A pitot pressure sensing tube can be dead-ended because there is no need for airflow through the pitot pressure system. A total air temperature probe, however, needs some airflow through it to avoid heating of the measured air by the anti-icing heating element, and so as always to be measuring ambient, not static air. The amount of airflow through the metered orifices is quite small and, therefore, has only a minor influence on the pitot effect. The total air temperature sensing element is shielded as well as possible from the anti-icing heat, and therefore senses the temperature of air which has been affected very little by it. AMTP017 | ELECTRICAL AND AVIONICS | ISSUE2 REV 1 | Page 101 of 286 TAT indication can be in the form of dial and pointer or digital readout as in modern airplanes. TAT Probe High temperature bleed air AMTP017 | ELECTRICAL AND AVIONICS | ISSUE2 REV 1 | Page 102 of 286 AIR DATA SYSTEM (ADS) Modern air data instruments are electrically driven by centralized computers. The term “Air Data Reference” (ADR) is used to describe the computer which calculates all necessary parameters to provide the Air Data computation for other computer’s reference and also for cockpit indications, typically the pitot and static sensors provide analog pressure signals, that’s why modern aircraft uses the term “Air Data Module” (ADM) which refers to one that converts these analog pressure signals into a digital output needed. The next figure shows is a layout of a typical system (A320). It shows that only the standby altimeter and airspeed indicator are mechanically driven by the pressure signals directly from the sensors. Note that some aircraft integrated the function of the Air Data Reference with the Inertial Reference (to be discussed on a later part) in one computer, on the A320, this is called Air Data Inertial Reference Unit (ADIRU). The name of the computers may vary from one aircraft to another but the purpose is the same, to centralize the air data system. AMTP017 | ELECTRICAL AND AVIONICS | ISSUE2 REV 1 | Page 103 of 286 EXAMPLE: A320 AIR DATA SYSTEM AMTP017 | ELECTRICAL AND AVIONICS | ISSUE2 REV 1 | Page 104 of 286 The static pressure sources can be switched to the computers by operating static source selector valves for analog pressure input switching (conventional) or by electrical switching (modern). Such switching could be used to recover from a faulty sensor or comparison checking during fault isolation. Pitot and static lines must be carefully protected from leaks and from water accumulation. Drain parts are provided where they are periodically drained. Due to the criticality of air data, triple redundancy is common as on the A320s. Its air data computer (ADIRU) system has three digital computers and a variety of associated sensors, switches and relays used for input and control. Each computer operates independently of the others and supplies multiple air data values to many different airplane systems. The ADIRU gets pitot-static air data (Pt and Ps) from the pitot-static system with pilot’s input for barometric reference correction. Angle-of- attack (AOA) sensor and total-air-temperature (TAT) sensor also provide inputs to the ADIRU. AMTP017 | ELECTRICAL AND AVIONICS | ISSUE2 REV 1 | Page 105 of 286 STALL WARNING SYSTEM The angle between the chord line of the wing of an aircraft and the direction of the relative airflow, is known as the angle of attack (AOA), or alpha (a) angle. It has a huge influence on the amount of lift that a wing generates. Lift increases as a increases, until it reaches some critical value. From this point onwards, lift starts decreasing due to separation of the slow-moving air (the boundary layer) from the upper surface of the wing, which, in turn causes separation and turbulence of the main airflow. Hence, this results in the wing going into a stalled condition, and because this happens at a particular angle rather than a particular speed, the critical AOA is also termed the stalling angle. The angle is unique for the design of airfoil section used for the wings of a certain aircraft type, and hence it varies from one aircraft to another, normally in the range 12° to18°. Warning of a stalled condition will be provided by an aircraft in its own characteristic way, e.g. by buffeting, gentle or severe pitch-down attitude change, and/or 'wing drop'. Though recovery is possible, these inherent warnings may arrive too late, for example, in an approach when the airspace under an aircraft is rapidly diminishing. Therefore, there is a need to have a means of sensing the a directly, so that an early warning of a stall condition can be triggered at some value just below that which it can occur. The stall warning systems of modern, larger types of aircraft are designed to perform an active function. They are either of the 'stick- shaker' or 'stick push or nudger' type, with a combination being used for some aircraft configurations. The type of sensor these systems typically use is illustrated in the following figure. AMTP017 | ELECTRICAL AND AVIONICS | ISSUE2 REV 1 | Page 106 of 286 Note: Some aircraft also uses a probe type AOA sensor which uses air pressure difference to calculate and know the angle of attack. These probes will determine the AOA with the use of air holes. The pressure on the air holes (upper and lower holes) will vary depending on the airflow passing around it which changes with the aircraft’s angle of attack. Getting back to the vane type AOA sensor: It comprises of a precisely counter-balanced aerodynamic vane connected to turn the rotor of a synchro transmitter. An internal heater element prevents ice from forming on the vane. Accurate alignment of the whole unit is done using index pins. Since extension of the flaps also modifies the pitch attitude, the sensor synchro is also interconnected with a synchro within the transmitter of the flap position indicating system, so that the angle of attack signal output is altered as a function of flap position. A motor, connected to a control column and which drives a weighted ring that is deliberately unbalanced to set up vibrations of the column is used to provide the stick-shaking motion. This is meant to simulate the natural buffeting brought about a stalled condition. As an example of a system, the one on the Learjet 45 airplane consists of a dual channel computer that is really 2 independent systems which process the AOA, flaps position, airspeed and altitude to determine if the airplane AOA exceeds the stall warning trip point. If exceeded, warnings are triggered. The eccentric weighted motor in the control column shakers will be activated to vibrate the control column. This is accompanied by an aural voice message “STALL” that is repetitive. Also, AOA needles in the AOA Indicators which shows the airplane AOA will enter into a red band on the indicator. At the same time, the low airspeed awareness red cue bars will extend upwards to the current airspeed indication on the speed tape of the Primary Flight Display (PFD). On the ground (weight-on-wheels), warnings are inhibited. An electronic screen message appears if the system fails. AMTP017 | ELECTRICAL AND AVIONICS | ISSUE2 REV 1 | Page 107 of 286 EXAMPLE: STICK SHAKER FOR STALL WARNING AMTP017 | ELECTRICAL AND AVIONICS | ISSUE2 REV 1 | Page 108 of 286 AMTP017 | ELECTRICAL AND AVIONICS | ISSUE2 REV 1 | Page 109 of 286 GYROSCOPIC INSTRUMENTS GYROSCOPIC PRINCIPLES A gyroscope is basically a mechanical device, with the essential element being a heavy metal wheel, or rotor, spinning at high angular velocity about a spin axis. Power to spin the gyroscope may be obtained from high speed air jets or either D.C. or A.C. electrical supplies. The rotor of the gyro is pivoted about a perpendicular axis through its center, XX, and mounted in a ring shaped frame or inner gimbal ring, which is itself pivoted in a second or outer gimbal ring. The outer ring is also pivoted and the three sets of pivots, rotor, inner and outer gimbal, are arranged to be normally at right angles to each other and intersect at the center of gravity of the rotor. Z X X Y AMTP017 | ELECTRICAL AND AVIONICS | ISSUE2 REV 1 | Page 110 of 286 When the rotor is caused to spin at high speed, it exhibits two important main properties: Gyroscopic Inertia or Rigidity Precession The rigidity of a gyro is defined as the force of the gyro that opposes any other force that tends to change its plane of rotation in space. AMTP017 | ELECTRICAL AND AVIONICS | ISSUE2 REV 1 | Page 111 of 286 Precession can be defined as the angular displacement of plane of rotation of gyro when an external force is applied. Precession is not in the same direction as applied force, but at a point 90o away in the direction of rotor. AMTP017 | ELECTRICAL AND AVIONICS | ISSUE2 REV 1 | Page 112 of 286 GYRO HORIZON The gyro horizon, or artificial horizon (AH) is an instrument that gives the pitch and bank attitude of an aircraft relative to the vertical. The instrument contains a gyroscope with a spin axis that is kept vertical by a gravity-sensing device. The relative position of two elements: a tiny aircraft symbol in the canter of the instrument, and a horizontal bar representing the natural horizon and held stable by the gyroscope, is used to present indications of pitch and bank attitude. The instrument also presents supplementary indications of bank by a gyro-stabilized pointer moving across a stationary bank scale. Two possible methods of presentation are shown. Gyro Horizon Presentations (a) Bottom Bank Scale (b) Top Bank Scale AMTP017 | ELECTRICAL AND AVIONICS | ISSUE2 REV 1 | Page 113 of 286 ATTITUDE DIRECTOR INDICATOR (ADI) The ADI combines attitude information with other flight information making it easier for the pilot to view essential indications, reducing the need to scan other instruments. AMTP017 | ELECTRICAL AND AVIONICS | ISSUE2 REV 1 | Page 114 of 286 The attitude sphere is servo-driven by electrical signals from a remote vertical gyro (VG). Airplane pitch attitude is read on the moving scale carried by the sphere at the point under the fixed airplane symbol whereas airplane roll is shown by the moving roll indicator upon the fixed roll scale at the top of the ADI. Turn and slip indications are integrated into the ADI at the bottom. Flight Director (FD) commands that the pilot follows to achieve selected flight targets are shown as a moving inverted “V” command bar in the example. The pilot is directed to “fly into the V” such that when the pitch and roll commands are satisfied, the command bar sits aligned with the airplane symbol as shown in the figure. Another type of flight director command presentation could be individual vertical moving pitch bar and lateral moving roll bar with them forming a cross when both commands are satisfied. Operation of the flight director will be discussed later in another topic. There is also the Instrument Landing System (ILS) commands and other indications that will be discussed in their respective system description later in the course. Nowadays with “glass cockpit”, electromechanical instrumentation is replaced by electronic ones (CRT, LCD); examples: Electronic ADI (EADI) on the B757 and Primary Flight Display (PFD) on the B747-400, A320. AMTP017 | ELECTRICAL AND AVIONICS | ISSUE2 REV 1 | Page 115 of 286 EXAMPLES: GLASS COCKPIT PRIMARY FLIGHT DISPLAY (PFD) AMTP017 | ELECTRICAL AND AVIONICS | ISSUE2 REV 1 | Page 116 of 286 DIRECTIONAL GYROSCOPE The directional gyroscope (DG) is one of the earliest gyroscopic instruments to be used as a heading indicator. A horizontal-axis gyroscope is utilized in the instrument, and since it is non-magnetic, is used together with the magnetic compass; it indicates the short-term heading changes when the aircraft is turning, while the magnetic compass supplies a trustworthy long-term heading reference in prolonged straight and level flight. The directional gyroscope has the advantage of being unaffected by effects of magnetic dip, and of turning and acceleration errors inherent in the magnetic compass. The simplest form of the instrument includes an outer ring pivoted about the vertical axis ZZ1, with a circular card graduated in degrees fixed to it. The card is read against a lubber line fixed to the gyroscope frame. The gimbal system and card are stabilized when the rotor spins at high speed and when the instrument frame is turned, the number of degrees through which it has turned may be read on the card against the lubber line. AMTP017 | ELECTRICAL AND AVIONICS | ISSUE2 REV 1 | Page 117 of 286 A caging and setting knob at the front of the case allows the instrument to be set to show the same heading as the magnetic compass. Pushing in the knob lifts an arm to lock the inner ring at right angles to the outer ring, while simultaneously meshing a bevel gear on the end of the caging- knob spindle with another bevel gear integral with the outer ring. Turning the caging knob in this position hence allows a heading to be set and the complete gimbal system to turn together. After being set correctly, the knob may be pulled out to free the gyroscope. As in the DG previously described, older directional gyros do not have a compass rose, but rather a circular strip card that can rotate, with heading shown under a lubber line. It is a more difficult presentation to interpret than the modern Heading Indicator, since only 30° either side of heading is shown. Other Heading Indicator cockpit display is a vertical compass rose of 360° that can rotate around a model aeroplane fixed in the center of the dial with its nose pointing up. The compass rose can be rotated using a slaving knob until the direction determined from the magnetic compass appears at the top of the dial. As heading changes, the compass rose rotates until the new heading is at the top of the dial, either under a fixed marker or at the nose of the model airplane. AMTP017 | ELECTRICAL AND AVIONICS | ISSUE2 REV 1 | Page 118 of 286 HORIZONTAL SITUATION INDICATOR (HSI) The HSI is a remotely driven electromechanical instrument like the ADI but it presents a pictorial display of navigation situation instead. This situation is shown as a plan view of the airplane’s position and heading with respect to a selected heading (HDG) and course (CSE). Selector knobs at the bottom corners in the type shown in the figure are provided for this use. Other types of HSI may have these selections remotely controlled from other panels electrically. The triangular bug on the 20-degree mark of the compass card shows the selected heading for the figure previously shown, whereas the selected course is shown by the inner arrowhead for a 55-degree course. The airplane magnetic heading is read on the rotating compass card under a fixed lubber line (shown as an inverted triangle at the top of the HSI in the figure). The compass card is synchronously linked with the airplane’s remote indicating compass. DME readouts and other radio navigational information are also presented on the HSI. The operation of these radio systems will be discussed later in the course. AMTP017 | ELECTRICAL AND AVIONICS | ISSUE2 REV 1 | Page 119 of 286 Modern electronic derivatives are the Electronic HSI (EHSI) on the B757 and the later Navigation Display (ND) on the B747-400. As shown in the above figure, the pilot can select to display only a part of the compass rose in the Expanded mode instead of the full compass rose in Centered mode of display. AMTP017 | ELECTRICAL AND AVIONICS | ISSUE2 REV 1 | Page 120 of 286 TURN & BANK The turn & bank indicator is still a primary instrument in certain small aircraft, though for larger civilian aircraft, it is merely used as a supplement to other ways of determining whether a turn is being made at the desired rate. Two independent mechanisms are present inside a turn & bank indicator: a pointer which indicates the aircraft rate of turn (ROT), driven by a gyro detecting mechanism, and a system which sense and indicates bank and/or slip. The dial presentations of two typical indicators are shown in the following figure. AMTP017 | ELECTRICAL AND AVIONICS | ISSUE2 REV 1 | Page 121 of 286 INDICATION PRINCIPLE AMTP017 | ELECTRICAL AND AVIONICS | ISSUE2 REV 1 | Page 122 of 286 The fundamental property of gyroscopic precession is used in sensing the rate of turn, and a rate gyroscope is employed for this purpose. Compared to the previously discussed displacement gyros, rate gyros are different in two ways: there is only one gimbal ring and movement about the longitudinal axis is restrained by a spring connected between the gimbal ring and casing. AMTP017 | ELECTRICAL AND AVIONICS | ISSUE2 REV 1 | Page 123 of 286 A left turn has the same effect as a force applied at the front pivot of the gimbal ring, and this is the same as trying to push the rotor round at the point F on its rim. This causes precession to happen at point P, following through 90° in the direction of rotation, and the gimbal ring and rotor will hence tilt about the longitudinal axis. The spring restrains gimbal movement so that eventual pointer deflection is a measure of rate of turn. An indication that the aircraft is correctly banked for the particular turn is also required to supplement the basic indication of turn rate. This is done by means of a secondary indicating mechanism that is operated by utilizing the effects of effects of gravitational and centrifugal forces. There are two main mechanical methods used: Gravity weight and pointer Ball in a curved liquid-filled glass tube AMTP017 | ELECTRICAL AND AVIONICS | ISSUE2 REV 1 | Page 124 of 286 Gravity-Weight Method of Indication Underbanked Overbanked Level Flight Correctly Banked (skidding out (slipping into turn) turn) AMTP017 | ELECTRICAL AND AVIONICS | ISSUE2 REV 1 | Page 125 of 286 MAGNETIC COMPASS DIRECT-READING COMPASS The direct-reading magnetic compass is used to indicate the direction an aircraft is heading in comparison to the earth’s magnetic meridian. Many smaller aircraft rely on the magnetic compass as the main heading indicator. However, for aircraft using the remote-indicating compasses and other advanced navigational aids, the compass is merely used as a standby heading indicator. The principle of operation of the direct-reading compass is that of interaction of the earth’s magnetic field with the field of an appropriately suspended permanent magnet. The earth can be considered as having a giant magnet within itself, with poles at some distance under its surface. Though only a weak magnetic field is produced, its effect can be sensed everywhere on the surface of the earth. The two poles of the magnet are the North magnetic and South Magnetic poles and they can be found near the North and South “true” or geographical poles. AMTP017 | ELECTRICAL AND AVIONICS | ISSUE2 REV 1 | Page 126 of 286 AMTP017 | ELECTRICAL AND AVIONICS | ISSUE2 REV 1 | Page 127 of 286 Since a freely suspended magnet will lie along the lines of force of magnetic field, therefore a magnet within the earth’s magnetic field will align itself accordingly. Hence a freely suspended magnet lies roughly North and South. The angle between the true and magnetic meridian is called variation. AMTP017 | ELECTRICAL AND AVIONICS | ISSUE2 REV 1 | Page 128 of 286 Many different types of compasses are used in aircraft but they all share the following common principal features: Magnet system housed in a bowl Liquid damping Liquid expansion compensation In the compass shown below, an annular cobalt-steel magnet with a light- alloy card mounted on it makes up the magnet system. Scale of the card are calibrated in increments of 10o with interpolation used to estimate intermediate indications. Indications are read against a lubber line molded on the interior of the bowl. The lubber line should be aligned to the longitudinal axis of the aircraft. AMTP017 | ELECTRICAL AND AVIONICS | ISSUE2 REV 1 | Page 129 of 286 Compass Swing Check must be made in situations that could affect the accuracy like the installation of electrical equipment near the compass among others. This is a process of swinging and compensating the compass by determining and reducing the deviation coefficients and recording the residual deviations. It is necessary for swinging to be undertaken at a location where only these aircraft field components, and the earth's magnetic field, can affect the readings of compasses. The location must be carefully chosen and surveyed to prove that it is free from any interfering local magnetic field, and also to establish it as the base on which all aspects of swinging procedures are to be carried out. A newly installed compass also requires a compass swing. NOTE: USE ONLY NON-MAGNETIC TOOLS FOR REMOVAL AND INSTALLATION TO AVOID INSTRUMENT DAMAGE. AMTP017 | ELECTRICAL AND AVIONICS | ISSUE2 REV 1 | Page 130 of 286 REMOTE INDICATING COMPASS A remote indicating compass combines the functions of a magnetic compass and the heading indicator. It employs a magnetic field sensor, known as a magnetic flux detector (or flux valve) that is positioned well away from other magnetic influences in the airframe, usually at a wingtip. The sensor detects magnetic direction and sends electrical signals to the heading indicator to automatically align it with the current magnetic heading of the aircraft – a process known as slaving. This eliminates the need for the pilot to periodically align the heading indicator, which now becomes known as a remote indicating compass. AMTP017 | ELECTRICAL AND AVIONICS | ISSUE2 REV 1 | Page 131 of 286 As shown in the following figure, the flux valve gives aircraft magnetic heading to the heading indicator via a synchro, which compares with the position of the heading indicator (i.e. the indicated heading). Any difference (the error) is applied to the slaving amplifier for amplification and then drives a slaving torquer that will process the directional gyro to the position which makes the indicated heading agree with the magnetic heading. AMTP017 | ELECTRICAL AND AVIONICS | ISSUE2 REV 1 | Page 132 of 286 AMTP017 | ELECTRICAL AND AVIONICS | ISSUE2 REV 1 | Page 133 of 286 GROUND PROXIMITY WARNING SYSTEM The GPWS is a computer-based system that, among other things, provides the flight crew with adequate warning (both aural and visual) of inadvertent contact of the airplane with the terrain or other obstacles, taking into account such items as crew recognition and reaction times. Enhanced Ground Proximity Warning System (EGPWS) is basically a conventional GPWS with additional features like Terrain Look Ahead Alerting and Terrain Awareness Display. It operates with a database of airports and can also consider the terrain surrounding these airports, referenced to altitude above mean sea level, during an approach. AMTP017 | ELECTRICAL AND AVIONICS | ISSUE2 REV 1 | Page 134 of 286 AMTP017 | ELECTRICAL AND AVIONICS | ISSUE2 REV 1 | Page 135 of 286 Different hazardous conditions that can be encountered in flight are divided into seven GPWS modes as follows: MODE CONDITIONS Mode 1 Excessive descent rate Mode 2 Excessive closure rate with respect to rising terrain Mode 3 Excessive altitude loss during climb-out (in takeoff or during go-around) when not in landing configuration (landing gear up and/or flaps less than 25o) Mode 4 Insufficient terrain clearance when not in landing configuration (landing gear up and/or flaps less than 25o) Mode 5 Excessive deviation below glide slope when making a front course approach with the gear down. Mode 6 Altitude Callout Mode 7 Windshear Aural messages and visual indications in the flight deck alert the flight crew to the occurrence of the Ground Proximity Warning System modes. There may be switches in the cockpit to allow inhibition of Mode 5 and terrain awareness alerts and for simulation of flaps extension and gear down (overrides). Different aircraft may have different modes, methods of annunciation and override functions. AMTP017 | ELECTRICAL AND AVIONICS | ISSUE2 REV 1 | Page 136 of 286 For the Ground Proximity Warning System computer to produce the required output signals to ensure proper operation of the GPWS, it requires several different inputs especially radio altitude which is terrain clearance altitude as opposed to barometric altitude. AMTP017 | ELECTRICAL AND AVIONICS | ISSUE2 REV 1 | Page 137 of 286 Possibly the most significant, if not the most colourful addition to a conventional GPWS comes in the form of Terrain Awareness Display. Display is available on either the Navigation Display (ND) or the Weather Radar (WX) display. As compared to a WX output with equal density full colour paint, it consists of a varying density dot display. Blocks of dotted colours are used to denote terrain. Even when not selected, the terrain alert function can ‘pop-up’ to alert or warn if the aircraft penetrates the envelope AMTP017 | ELECTRICAL AND AVIONICS | ISSUE2 REV 1 | Page 138 of 286 AMTP017 | ELECTRICAL AND AVIONICS | ISSUE2 REV 1 | Page 139 of 286 AMTP017 | ELECTRICAL AND AVIONICS | ISSUE2 REV 1 | Page 140 of 286 AMTP017 | ELECTRICAL AND AVIONICS | ISSUE2 REV 1 | Page 141 of 286 CLOCKS The primary function of the clock is to give time reference to other airplane systems and to display universal time coordinated (UTC). Universal time coordinated was previously known as Greenwich Mean Time (GMT). The secondary function of the clock is to give a display of elapsed time or chronograph time. Controls are integrated with the clocks themselves; however, in addition to the clock’s chronograph button, remote CLOCK switches are commonly installed to provide the same function. The number of clocks installed on the aircraft depends on the manufactu