A400M Training Manual ATA 24 Electrical Power System PDF Nov 2020
Document Details
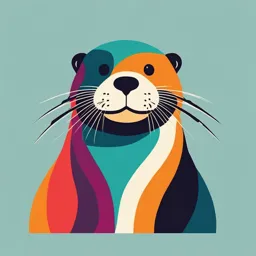
Uploaded by ProminentRoentgenium
null
2020
Tags
Related
- Maharashtra State Board of Technical Education PDF Learning Manual: Emerging Trends in Electrical Engineering, Semester-VI (22628)
- Basic Electrical Engineering PDF
- Introduction to Electrical Engineering PDF
- Introduction To Electrical Engineering PDF
- Introduction to Electrical Engineering (USTP) PDF
- Introduction to Electrical Engineering Week 4.1 PDF
Summary
This document is a training manual for the ATA 24 electrical power system on the A400M aircraft. It provides detailed descriptions and operations of electrical generation, distribution, and maintenance subsystems, including components, controls, and indications. The manual is organized into chapters covering electrical networks, generation, distribution, and maintenance, featuring comprehensive information.
Full Transcript
Table of contents Chapter 1. Electrical Network - Description & Operations 1.1 Electrical Network (SubSystem) - Description 1.1.1 General Description 1.1.2 Controls & Indications 1.1.3 Detailed Description Chapter 2. Electrical Generation SubSystem - Description & Operations 2.1 Electrical Generatio...
Table of contents Chapter 1. Electrical Network - Description & Operations 1.1 Electrical Network (SubSystem) - Description 1.1.1 General Description 1.1.2 Controls & Indications 1.1.3 Detailed Description Chapter 2. Electrical Generation SubSystem - Description & Operations 2.1 Electrical Generation SubSystem - Description - AC Main Generation 2.1.1 General Description 2.1.2 Controls & Indications 2.1.3 Component Location 2.1.4 Detailed Description 2.1.5 Variable Frequency Generator 2.2 Electrical Generation SubSystem - Description - AC Auxiliary Generation 2.2.1 General Description 2.2.2 Controls & Indications 2.2.3 Component Location 2.2.4 Detailed Description 2.3 Electrical Generation SubSystem - Description - AC External Power 2.3.1 General Description 2.3.2 Controls & Indications 2.3.3 Component Location 2.3.4 Detailed Description 2.4 Electrical Generation SubSystem - Description - AC Domestic Generation 2.4.1 General Description 2.4.2 Controls & Indications 2.4.3 Component Location Released in November 15, 2020 TRAINING USE ONLY Training Use Only 1 / 490 This document shall be used in accordance with the provisions described on the front page. NTCSS Release 2023-01 49_ATA24_Lv2&3_CAT B2_P_NOV20.pdf 2.4.4 Detailed Description 2.5 Electrical Generation SubSystem - Description - DC Main and Essential Generation 2.5.1 General Description 2.5.2 Controls & Indications 2.5.3 Component Location 2.5.4 Detailed Description 2.6 Electrical Generation SubSystem - Description - Battery DC Generation 2.6.1 General Description 2.6.2 Controls & Indications 2.6.3 Component Location 2.6.4 Detailed Description 2.7 Electrical Generation SubSystem - Description - AC Emergency Generation 2.7.1 General Description 2.7.2 Controls & Indications 2.7.3 Component Location 2.7.4 Detailed Description - Ram Air Turbine System 2.7.5 Detailed Description - Electrical Architecture 2.8 Electrical Generation SubSystem - Description - Static Inverter AC Generation 2.8.1 General Description 2.8.2 Controls & Indications 2.8.3 Component Location 2.8.4 Detailed Description 2.9 Electrical Generation SubSystem - Operation 2.9.1 Variable Frequency Generator Operation 2.9.2 APU Generator Operation 2.9.3 External Power Operation 2.9.4 Batteries Check and Batteries Connection/Disconnection 2.9.5 Ram Air Turbine Extension and Retraction 2.9.6 Static Inverter Check Chapter 3. Electrical Distribution SubSystem - Description & Operations Released in November 15, 2020 TRAINING USE ONLY Training Use Only 2 / 490 This document shall be used in accordance with the provisions described on the front page. NTCSS Release 2023-01 49_ATA24_Lv2&3_CAT B2_P_NOV20.pdf 3.1 Electrical Distribution SubSystem - Description - Distribution Network 3.1.1 General Description 3.1.2 Controls & Indications 3.1.3 Detailed Description 3.2 Electrical Distribution SubSystem - Description - Primary Power Distribution 3.2.1 General Description 3.2.2 Component Location 3.2.3 Detailed Description 3.3 Electrical Distribution SubSystem - Description - Secondary Power Distribution 3.3.1 General Description 3.3.2 Component Location 3.3.3 Detailed Description 3.4 Electrical Distribution SubSystem - Description - Emergency Power Distribution 3.4.1 General Description 3.4.2 Component Location 3.4.3 Detailed Description 3.5 Electrical Distribution SubSystem - Description - Power Distribution Maintenance Interface 3.5.1 General Description 3.5.2 Controls & Indications 3.5.3 Component Location 3.5.4 Detailed Description 3.6 Electrical Distribution SubSystem - Operation 3.6.1 Electrical Distribution SubSystem 3.6.2 Power Distribution Maintenance Terminal Operation Chapter 4. Electrical Power System - Maintenance 4.1 On Board maintenance System 4.1.1 OMS Pages 4.2 Maintenance Tasks 4.2.1 Servicing Tasks Released in November 15, 2020 TRAINING USE ONLY Training Use Only 3 / 490 This document shall be used in accordance with the provisions described on the front page. NTCSS Release 2023-01 49_ATA24_Lv2&3_CAT B2_P_NOV20.pdf A400M Training Manual ATA 24 Electrical Power System Released in November 15, 2020 TRAINING USE ONLY Training Use Only 4 / 490 This document shall be used in accordance with the provisions described on the front page. NTCSS Release 2023-01 49_ATA24_Lv2&3_CAT B2_P_NOV20.pdf A400M Training Manual Electrical Network - Description & Operations General Description Chapter 1. Electrical Network - Description & Operations 1.1 Electrical Network (SubSystem) - Description 1.1.1 General Description General Description Electrical Network Architecture The AC electrical network has two parts, generation and distribution. The DC electrical network is divided in three parts: - The DC generation subsystem that includes the rectifiers - The DC distribution - The DC generation subsystem that includes the batteries. The power sources of the AC generation subsystem supply an electrical power of 115 VAC to the AC distribution subsystem which has: - Four main AC buses which can receive power from the related Variable Frequency Generator (VFG), the APU generator or the external power - One AC essential bus which can receive power from AC bus 1, AC bus 4 or the RAT emergency generator - One AC emergency bus which can receive power from the AC essential bus or the static inverter. Power transfers between buses are possible depending on sources availability. The rectifiers of the DC generation subsystem, which receive AC power from different buses, transform the AC input into a DC power of 28 VDC to supply the DC distribution subsystem. It has: - Two main DC buses receiving power from the related Battery Charger Rectifier Unit (BCRU) or Transformer Rectifier Unit (TRU) - One DC essential bus which receives power from the essential BCRU - One DC APU bus which receives power from the TRU and is used to supply the APU starter motor. Released in November 15, 2020 TRAINING USE ONLY Training Use Only 5 / 490 This document shall be used in accordance with the provisions described on the front page. NTCSS Release 2023-01 49_ATA24_Lv2&3_CAT B2_P_NOV20.pdf A400M Training Manual Electrical Network - Description & Operations General Description Power transfers between buses are possible depending on sources availability. The batteries of the DC generation subsystem are connected to the DC buses. For charging, each battery receives 28 VDC from the related bus. The batteries can supply the buses for a short time during BCRUs power interruptions. Battery 2 can also supply the DC APU bus for APU starting. Released in November 15, 2020 TRAINING USE ONLY Training Use Only 6 / 490 This document shall be used in accordance with the provisions described on the front page. NTCSS Release 2023-01 49_ATA24_Lv2&3_CAT B2_P_NOV20.pdf A400M Training Manual Released in November 15, 2020 TRAINING USE ONLY Training Use Only Electrical Network - Description & Operations General Description 7 / 490 This document shall be used in accordance with the provisions described on the front page. NTCSS Release 2023-01 49_ATA24_Lv2&3_CAT B2_P_NOV20.pdf A400M Training Manual 1.1.2 Electrical Network - Description & Operations Controls & Indications Controls & Indications Control Panels Electrical Control Panel The Electrical Control Panel represents a synoptic of the AC network and contains several illuminated push button-switches to allow: - The control of the batteries - The management of the electrical loads - The control of the AC normal generation sources. Released in November 15, 2020 TRAINING USE ONLY Training Use Only 8 / 490 This document shall be used in accordance with the provisions described on the front page. NTCSS Release 2023-01 49_ATA24_Lv2&3_CAT B2_P_NOV20.pdf A400M Training Manual Released in November 15, 2020 TRAINING USE ONLY Training Use Only Electrical Network - Description & Operations Controls & Indications 9 / 490 This document shall be used in accordance with the provisions described on the front page. NTCSS Release 2023-01 49_ATA24_Lv2&3_CAT B2_P_NOV20.pdf A400M Training Manual Electrical Network - Description & Operations Controls & Indications Control Panel for Electrical Maintenance The Electrical Maintenance Control Panel provides the crew with the controls to allow: - The checking of the batteries - The control of some electrical services related to the aircraft maintenance. Released in November 15, 2020 TRAINING USE ONLY Training Use Only 10 / 490 This document shall be used in accordance with the provisions described on the front page. NTCSS Release 2023-01 49_ATA24_Lv2&3_CAT B2_P_NOV20.pdf A400M Training Manual Released in November 15, 2020 TRAINING USE ONLY Training Use Only Electrical Network - Description & Operations Controls & Indications 11 / 490 This document shall be used in accordance with the provisions described on the front page. NTCSS Release 2023-01 49_ATA24_Lv2&3_CAT B2_P_NOV20.pdf A400M Training Manual Electrical Network - Description & Operations Controls & Indications Control Panels for Emergency Electrical Power The Emergency Electrical Power Control Panel provides the pilots with: - One fault light for the Emergency Generator - One guarded push button to manually control the Ram Air Turbine (RAT). The Stow Panel for the RAT provides the maintainers with switches and lights to control the RAT stowing. This panel is used only on ground. Released in November 15, 2020 TRAINING USE ONLY Training Use Only 12 / 490 This document shall be used in accordance with the provisions described on the front page. NTCSS Release 2023-01 49_ATA24_Lv2&3_CAT B2_P_NOV20.pdf A400M Training Manual Released in November 15, 2020 TRAINING USE ONLY Training Use Only Electrical Network - Description & Operations Controls & Indications 13 / 490 This document shall be used in accordance with the provisions described on the front page. NTCSS Release 2023-01 49_ATA24_Lv2&3_CAT B2_P_NOV20.pdf A400M Training Manual Electrical Network - Description & Operations Controls & Indications Reset Buttons for Electrical Power The RESET panels contain the buttons that allow the reset of: - The BCRUs and TRU - The emergency Generator Control Unit (GCU). Released in November 15, 2020 TRAINING USE ONLY Training Use Only 14 / 490 This document shall be used in accordance with the provisions described on the front page. NTCSS Release 2023-01 49_ATA24_Lv2&3_CAT B2_P_NOV20.pdf A400M Training Manual Released in November 15, 2020 TRAINING USE ONLY Training Use Only Electrical Network - Description & Operations Controls & Indications 15 / 490 This document shall be used in accordance with the provisions described on the front page. NTCSS Release 2023-01 49_ATA24_Lv2&3_CAT B2_P_NOV20.pdf A400M Training Manual Electrical Network - Description & Operations Controls & Indications Power Distribution Maintenance Terminals There are two identical Power Distribution Maintenance Terminals (PDMTs 1 and 2). They provide the maintainers with the humanmachine interface for the management of the circuit breakers. The PDMTs can be used only on ground. Released in November 15, 2020 TRAINING USE ONLY Training Use Only 16 / 490 This document shall be used in accordance with the provisions described on the front page. NTCSS Release 2023-01 49_ATA24_Lv2&3_CAT B2_P_NOV20.pdf A400M Training Manual Released in November 15, 2020 TRAINING USE ONLY Training Use Only Electrical Network - Description & Operations Controls & Indications 17 / 490 This document shall be used in accordance with the provisions described on the front page. NTCSS Release 2023-01 49_ATA24_Lv2&3_CAT B2_P_NOV20.pdf A400M Training Manual Electrical Network - Description & Operations Controls & Indications Control Panel for Electric Converters The control panel for electric converters allows the control of: - Both Medical Evacuation (MEDEVAC) converters - The 110 V converter. Released in November 15, 2020 TRAINING USE ONLY Training Use Only 18 / 490 This document shall be used in accordance with the provisions described on the front page. NTCSS Release 2023-01 49_ATA24_Lv2&3_CAT B2_P_NOV20.pdf A400M Training Manual Released in November 15, 2020 TRAINING USE ONLY Training Use Only Electrical Network - Description & Operations Controls & Indications 19 / 490 This document shall be used in accordance with the provisions described on the front page. NTCSS Release 2023-01 49_ATA24_Lv2&3_CAT B2_P_NOV20.pdf A400M Training Manual Electrical Network - Description & Operations Controls & Indications Indicating Lights for External Power There are two lights to indicate the status of the external power connected to the aircraft. One test pushbutton allows the test of all panel lights. Released in November 15, 2020 TRAINING USE ONLY Training Use Only 20 / 490 This document shall be used in accordance with the provisions described on the front page. NTCSS Release 2023-01 49_ATA24_Lv2&3_CAT B2_P_NOV20.pdf A400M Training Manual Released in November 15, 2020 TRAINING USE ONLY Training Use Only Electrical Network - Description & Operations Controls & Indications 21 / 490 This document shall be used in accordance with the provisions described on the front page. NTCSS Release 2023-01 49_ATA24_Lv2&3_CAT B2_P_NOV20.pdf A400M Training Manual Electrical Network - Description & Operations Controls & Indications Indications on ECAM ELEC AC Page A synoptic of the AC network status is presented on the ELEC/AC page. It contains information for the flight crew related to: - The power sources of the AC emergency generation system - The configuration of the AC distribution network - The power sources of the AC normal generation system. Released in November 15, 2020 TRAINING USE ONLY Training Use Only 22 / 490 This document shall be used in accordance with the provisions described on the front page. NTCSS Release 2023-01 49_ATA24_Lv2&3_CAT B2_P_NOV20.pdf A400M Training Manual Released in November 15, 2020 TRAINING USE ONLY Training Use Only Electrical Network - Description & Operations Controls & Indications 23 / 490 This document shall be used in accordance with the provisions described on the front page. NTCSS Release 2023-01 49_ATA24_Lv2&3_CAT B2_P_NOV20.pdf A400M Training Manual Electrical Network - Description & Operations Controls & Indications ELEC DC Page A synoptic of the DC network status is presented on the ELEC/DC page. It contains information for the flight crew related to: - The batteries - The configuration of the DC distribution network - The power sources of the DC generation system. Released in November 15, 2020 TRAINING USE ONLY Training Use Only 24 / 490 This document shall be used in accordance with the provisions described on the front page. NTCSS Release 2023-01 49_ATA24_Lv2&3_CAT B2_P_NOV20.pdf A400M Training Manual Released in November 15, 2020 TRAINING USE ONLY Training Use Only Electrical Network - Description & Operations Controls & Indications 25 / 490 This document shall be used in accordance with the provisions described on the front page. NTCSS Release 2023-01 49_ATA24_Lv2&3_CAT B2_P_NOV20.pdf A400M Training Manual Electrical Network - Description & Operations Controls & Indications C/B Page The circuit breakers page is a list of the tripped circuit breakers. Released in November 15, 2020 TRAINING USE ONLY Training Use Only 26 / 490 This document shall be used in accordance with the provisions described on the front page. NTCSS Release 2023-01 49_ATA24_Lv2&3_CAT B2_P_NOV20.pdf A400M Training Manual Released in November 15, 2020 TRAINING USE ONLY Training Use Only Electrical Network - Description & Operations Controls & Indications 27 / 490 This document shall be used in accordance with the provisions described on the front page. NTCSS Release 2023-01 49_ATA24_Lv2&3_CAT B2_P_NOV20.pdf A400M Training Manual Electrical Network - Description & Operations Controls & Indications Electrical Alerts All level alerts are provided by the Electrical System on the Engine and Warning Display (EWD). Some examples are shown. Released in November 15, 2020 TRAINING USE ONLY Training Use Only 28 / 490 This document shall be used in accordance with the provisions described on the front page. NTCSS Release 2023-01 49_ATA24_Lv2&3_CAT B2_P_NOV20.pdf A400M Training Manual Released in November 15, 2020 TRAINING USE ONLY Training Use Only Electrical Network - Description & Operations Controls & Indications 29 / 490 This document shall be used in accordance with the provisions described on the front page. NTCSS Release 2023-01 49_ATA24_Lv2&3_CAT B2_P_NOV20.pdf A400M Training Manual 1.1.3 Electrical Network - Description & Operations Detailed Description Detailed Description Detailed Description Electrical Network Architecture (I) When the engines operate, the VFGs are available to supply the AC network. Each VFG is connected to its related AC bus through one Generator Line Contactor (GLC). If the APU is running, the AC network can be supplied by the APU generator which is connected through the APU Generator Contactor (AGC). When the AGC is closed the APU generator supplies the AC buses through the Bus Tie Alternate-Contactors (BTACs) and System Isolation Contactors (SICs). On ground, the external power supplies the AC buses through the External Power Contactor (EPC), the BTACs and the SICs. All the contactors are automatically managed according to sources availability. To supply the cargo electrical loads there are four Reconfigurable (R) buses (or transfer buses). Each one is connected, in normal conditions, to its related AC bus through one Reconfigurable Line Contactor (RLC). When necessary, the crew can shed the reconfigurable buses. In normal configuration, the AC essential bus can be supplied by: - AC bus 1 through Essential Contactor (ESSC) 1 and Normal to Emergency Interlock-Contactor (NEIC) 1, or - AC bus 4 through ESSC 2 and NEIC 2, if AC bus 1 is not available. In emergency configuration, the AC essential bus is supplied by the RAT generator through the Emergency Generator Contactor (EGC). The AC emergency bus is supplied in all configurations through the Emergency Interlock Line Contactor (EILC) by: - The AC essential bus when available, or - The static inverter which is powered through the Static Inverter Contactor (STIVC). Depending on network configuration and sources availability, power transfers are possible. This is automatically managed by closing: - The BTACs and SICs for power transfers between the AC buses - The Reconfigurable Transfer Contactors (RTCs) for power transfers between the reconfigurable buses. Released in November 15, 2020 TRAINING USE ONLY Training Use Only 30 / 490 This document shall be used in accordance with the provisions described on the front page. NTCSS Release 2023-01 49_ATA24_Lv2&3_CAT B2_P_NOV20.pdf A400M Training Manual Released in November 15, 2020 TRAINING USE ONLY Training Use Only Electrical Network - Description & Operations Detailed Description EILC =ermg interlock line con 31 / 490 This document shall be used in accordance with the provisions described on the front page. NTCSS Release 2023-01 49_ATA24_Lv2&3_CAT B2_P_NOV20.pdf A400M Training Manual Electrical Network - Description & Operations Detailed Description Electrical Network Architecture (II) The BCRUs receive power from AC bus 2, AC essential bus and AC bus 3. Each BCRU supplies power to its related DC bus through the BCRU Line Contactor (BLC). The TRU, which receives power from AC bus 4, supplies the DC APU bus through the TRU Line Contactor (TRLC). The TRU can also supply DC bus 2 through the TRU Line Contactor Backup (TRLC BKUP). This contactor automatically closes if BCRU 2 fails. Depending on sources availability, power transfers between DC buses are possible. This is automatically managed by closing the Bus Tie Continuous-Contactors (BTCCs). Three batteries ensure the voltage stability and the No Break Power Transfer (NBPT) function on the DC buses during reconfiguration processes. Each battery is connected to the corresponding bus through a Battery Contactor (BATC). The battery charging is provided by the associated BCRU. Battery 2 can also supply the DC APU bus through the Battery APU Contactor (BAC). This contactor automatically closes during APU starting if the TRU is not available. Then the BATC 2 contactor opens to disconnect the battery from the DC bus to prevent under-voltage on the normal network. The APU starter motor is connected to the DC APU bus through the APU Start Contactor (ASC). This contactor closes when the starting is requested. The hot buses are directly connected to the batteries. They provide a non-interruptible power supply for fire extinguishers and other systems. Released in November 15, 2020 TRAINING USE ONLY Training Use Only 32 / 490 This document shall be used in accordance with the provisions described on the front page. NTCSS Release 2023-01 49_ATA24_Lv2&3_CAT B2_P_NOV20.pdf A400M Training Manual Released in November 15, 2020 TRAINING USE ONLY Training Use Only Electrical Network - Description & Operations Detailed Description 33 / 490 This document shall be used in accordance with the provisions described on the front page. NTCSS Release 2023-01 49_ATA24_Lv2&3_CAT B2_P_NOV20.pdf A400M Training Manual Electrical Generation SubSystem - Description & Operations General Description Chapter 2. Electrical Generation SubSystem - Description & Operations 2.1 Electrical Generation SubSystem - Description - AC Main Generation 2.1.1 General Description General Description AC Main Generation The AC main generation is used in normal electrical configuration to power the entire electrical network when the engines are running. The AC main generation is provided by four Variable Frequency Generators (VFGs) connected to the main AC buses. Each VFG independently supplies its own bus with a three-phase 115 VAC electrical power. An internal oil system lubricates and controls the temperature of each VFG. The Air-Cooled Oil Cooler (ACOC) controls the temperature of the VFG oil. Each VFG is monitored, controlled and protected by its relative Generator and Ground Power Control Unit (GGPCU). The GGPCUs transmit data to the displays of the Electronic Centralized Aircraft Monitoring (ECAM) system in order to provide the crew with generators information. Two pushbutton-switches, located on the overhead Electrical (ELEC) panel, control each VFG. Released in November 15, 2020 TRAINING USE ONLY Training Use Only 34 / 490 This document shall be used in accordance with the provisions described on the front page. NTCSS Release 2023-01 49_ATA24_Lv2&3_CAT B2_P_NOV20.pdf A400M Training Manual Released in November 15, 2020 TRAINING USE ONLY Training Use Only Electrical Generation SubSystem - Description & Operations General Description 35 / 490 This document shall be used in accordance with the provisions described on the front page. NTCSS Release 2023-01 49_ATA24_Lv2&3_CAT B2_P_NOV20.pdf A400M Training Manual Electrical Generation SubSystem - Description & Operations General Description VFG and GGPCU The drive shaft of the VFG is mechanically connected to the accessory gear box of the engine. An internal drive-disconnect mechanism is used to separate the VFG rotor from the drive shaft. The VFG has: - A terminal block - Oil ports for the interface with the ACOC - Electrical connectors for the interface with the GGPCU. The GGPCU provides: - Generator control and protection functions - Oil monitoring functions - Drive-disconnect orders. Released in November 15, 2020 TRAINING USE ONLY Training Use Only 36 / 490 This document shall be used in accordance with the provisions described on the front page. NTCSS Release 2023-01 49_ATA24_Lv2&3_CAT B2_P_NOV20.pdf A400M Training Manual Released in November 15, 2020 TRAINING USE ONLY Training Use Only Electrical Generation SubSystem - Description & Operations General Description 37 / 490 This document shall be used in accordance with the provisions described on the front page. NTCSS Release 2023-01 49_ATA24_Lv2&3_CAT B2_P_NOV20.pdf A400M Training Manual 2.1.2 Electrical Generation SubSystem - Description & Operations Controls & Indications Controls & Indications Controls and Indications Drive Pushbuttons The DRIVE pushbuttons enable the crew to mechanically disconnect the related VFG from its drive shaft (they are guarded in order to avoid inadvertent actions). Each DRIVE pushbutton has three statuses: - The lights are off in normal conditions when the generator is driven by the engine - The DISC light illuminates when the generator is mechanically disconnected from its drive shaft - The FAULT light illuminates when a low oil-pressure condition occurs in the generator. Notes: - The disconnection action is not reversible - The manual disconnection is inhibited if the engine is stopped. Released in November 15, 2020 TRAINING USE ONLY Training Use Only 38 / 490 This document shall be used in accordance with the provisions described on the front page. NTCSS Release 2023-01 49_ATA24_Lv2&3_CAT B2_P_NOV20.pdf A400M Training Manual Released in November 15, 2020 TRAINING USE ONLY Training Use Only Electrical Generation SubSystem - Description & Operations Controls & Indications 39 / 490 This document shall be used in accordance with the provisions described on the front page. NTCSS Release 2023-01 49_ATA24_Lv2&3_CAT B2_P_NOV20.pdf A400M Training Manual Electrical Generation SubSystem - Description & Operations Controls & Indications Generators Pushbutton-switches The GEN pushbutton-switches control the electrical connection and disconnection of the VFGs to the electrical network. Each GEN pushbutton-switch has three statuses: - ON (pushed position): The lights are off. The generator is connected to the electrical network. It is the normal position. - OFF (released position): The OFF light illuminates. The generator is disconnected from the electrical network. - FAULT (pushed position): The FAULT light illuminates when the generator is faulty and disconnected from the electrical network. When the pushbutton is released the light goes off. Released in November 15, 2020 TRAINING USE ONLY Training Use Only 40 / 490 This document shall be used in accordance with the provisions described on the front page. NTCSS Release 2023-01 49_ATA24_Lv2&3_CAT B2_P_NOV20.pdf A400M Training Manual Released in November 15, 2020 TRAINING USE ONLY Training Use Only Electrical Generation SubSystem - Description & Operations Controls & Indications 41 / 490 This document shall be used in accordance with the provisions described on the front page. NTCSS Release 2023-01 49_ATA24_Lv2&3_CAT B2_P_NOV20.pdf A400M Training Manual Electrical Generation SubSystem - Description & Operations Controls & Indications Generators Indications on ECAM The following generators information is presented on the SD ELEC AC page of the ECAM: - Generator title (in amber if the generator does not operate) - Engine index (in amber if the engine does not operate) - Generator load and voltage (or OFF status) - Overheat and disconnection messages - Line contactor status (in white if it is open). Released in November 15, 2020 TRAINING USE ONLY Training Use Only 42 / 490 This document shall be used in accordance with the provisions described on the front page. NTCSS Release 2023-01 49_ATA24_Lv2&3_CAT B2_P_NOV20.pdf A400M Training Manual Released in November 15, 2020 TRAINING USE ONLY Training Use Only Electrical Generation SubSystem - Description & Operations Controls & Indications 43 / 490 This document shall be used in accordance with the provisions described on the front page. NTCSS Release 2023-01 49_ATA24_Lv2&3_CAT B2_P_NOV20.pdf A400M Training Manual Electrical Generation SubSystem - Description & Operations Controls & Indications Generators Alerts on ECAM The generators alerts on the Warning Display are the following: - DRIVE 1 (2, 3 or 4) OIL LEVEL LOW - GEN 1 (2, 3 or 4) FAULT - GEN 1 (2, 3 or 4) OFF - DRIVE 1 (2, 3 or 4) DISCONNECTED - DRIVE 1 (2, 3 or 4) OIL PRESSURE LOW - DRIVE 1 (2, 3 or 4) OIL OVERHEAT. In addition, if some maintenance operation has to be performed, the following maintenance status alert is displayed on the "STATUS MORE" page of the system display: - ELEC. Released in November 15, 2020 TRAINING USE ONLY Training Use Only 44 / 490 This document shall be used in accordance with the provisions described on the front page. NTCSS Release 2023-01 49_ATA24_Lv2&3_CAT B2_P_NOV20.pdf A400M Training Manual Released in November 15, 2020 TRAINING USE ONLY Training Use Only Electrical Generation SubSystem - Description & Operations Controls & Indications 45 / 490 This document shall be used in accordance with the provisions described on the front page. NTCSS Release 2023-01 49_ATA24_Lv2&3_CAT B2_P_NOV20.pdf A400M Training Manual 2.1.3 Electrical Generation SubSystem - Description & Operations Component Location Component Location Component Location VFG Location The VFG is installed on the rear face of the Accessory Gear Box of the engine. It is secured using a V-Band clamp. Released in November 15, 2020 TRAINING USE ONLY Training Use Only 46 / 490 This document shall be used in accordance with the provisions described on the front page. NTCSS Release 2023-01 49_ATA24_Lv2&3_CAT B2_P_NOV20.pdf A400M Training Manual Released in November 15, 2020 TRAINING USE ONLY Training Use Only Electrical Generation SubSystem - Description & Operations Component Location 47 / 490 This document shall be used in accordance with the provisions described on the front page. NTCSS Release 2023-01 49_ATA24_Lv2&3_CAT B2_P_NOV20.pdf A400M Training Manual Electrical Generation SubSystem - Description & Operations Component Location VFG Feeders Routes The routing along the aircraft of the VFG feeders takes into account segregation due to safety and vulnerability requirements. Separation of feeders from other categories of routes is also necessary for electromagnetic compatibility. Released in November 15, 2020 TRAINING USE ONLY Training Use Only 48 / 490 This document shall be used in accordance with the provisions described on the front page. NTCSS Release 2023-01 49_ATA24_Lv2&3_CAT B2_P_NOV20.pdf A400M Training Manual Released in November 15, 2020 TRAINING USE ONLY Training Use Only Electrical Generation SubSystem - Description & Operations Component Location 49 / 490 This document shall be used in accordance with the provisions described on the front page. NTCSS Release 2023-01 49_ATA24_Lv2&3_CAT B2_P_NOV20.pdf A400M Training Manual Electrical Generation SubSystem - Description & Operations Component Location GGPCUs Location The GGPCUs are located in the Nose Fuselage, on the mezzanine. Released in November 15, 2020 TRAINING USE ONLY Training Use Only 50 / 490 This document shall be used in accordance with the provisions described on the front page. NTCSS Release 2023-01 49_ATA24_Lv2&3_CAT B2_P_NOV20.pdf A400M Training Manual Released in November 15, 2020 TRAINING USE ONLY Training Use Only Electrical Generation SubSystem - Description & Operations Component Location 51 / 490 This document shall be used in accordance with the provisions described on the front page. NTCSS Release 2023-01 49_ATA24_Lv2&3_CAT B2_P_NOV20.pdf A400M Training Manual 2.1.4 Electrical Generation SubSystem - Description & Operations Detailed Description Detailed Description Detailed Description VFG Electrical Description The VFG converts mechanical rotating power coming from the drive shaft into three-phase 115 VAC electrical power with a variable frequency. Its power output is connected to the electrical network through the terminal block. Each VFG has a continuous power capacity of 75 KVA. Two electrical connectors are used for control signals. The VFG is a brushless generator which has three electrical machines mechanically connected to the drive shaft through a drivedisconnect device: - The first machine is the Pilot Exciter. It is a Permanent Magnet Generator (PMG) that has a rotor with magnets and a threephase stator - The second machine is the Main Exciter. The stator provides the excitation field. In the rotor, shaft-mounted diodes rectify the output of the three-phase star-connected winding - The third machine is the Main Alternator. It receives excitation for the rotor poles field from the output of the main exciter diodes. The main alternator has a three-phase star-connected stator winding with the three phases connected to the generator output terminals. A Current Transformer (CT), installed on the main stator winding, measures the three-phase output current. Released in November 15, 2020 TRAINING USE ONLY Training Use Only 52 / 490 This document shall be used in accordance with the provisions described on the front page. NTCSS Release 2023-01 49_ATA24_Lv2&3_CAT B2_P_NOV20.pdf A400M Training Manual Released in November 15, 2020 TRAINING USE ONLY Training Use Only Electrical Generation SubSystem - Description & Operations Detailed Description 53 / 490 This document shall be used in accordance with the provisions described on the front page. NTCSS Release 2023-01 49_ATA24_Lv2&3_CAT B2_P_NOV20.pdf A400M Training Manual Electrical Generation SubSystem - Description & Operations Detailed Description GGPCU Description The GGPCU is an electronic unit that monitors and controls its related VFG and associated network contactors. The GGPCU has two types of functions: - Generator control which includes: o Voltage regulation o Contactors management o Oil monitoring o Protection o Mechanical disconnection. - Processing and communication which includes: o Data transmission o BITE functions. The GGPCU also has functions to control the external power but they are not used when the unit is installed in the positions 1, 2, 3 or 4. Released in November 15, 2020 TRAINING USE ONLY Training Use Only 54 / 490 This document shall be used in accordance with the provisions described on the front page. NTCSS Release 2023-01 49_ATA24_Lv2&3_CAT B2_P_NOV20.pdf A400M Training Manual Released in November 15, 2020 TRAINING USE ONLY Training Use Only Electrical Generation SubSystem - Description & Operations Detailed Description 55 / 490 This document shall be used in accordance with the provisions described on the front page. NTCSS Release 2023-01 49_ATA24_Lv2&3_CAT B2_P_NOV20.pdf A400M Training Manual Electrical Generation SubSystem - Description & Operations Detailed Description Generator Electrical Management (I) In order to control the generator connection and disconnection, the GGPCU exchanges the following discrete signals with the Integrated Control Panel System (ICPS): - On/off command from the GEN pushbutton-switch which is used to control the generator connection and to reset the protection functions - FAULT and OFF signals to the GEN pushbutton-switch to illuminate the lights that show the status of the generator - Off status from the engine master switch to provide the engine shutdown indication - Pushed status from the FIRE pushbutton which is used to remove the excitation and disconnect the generator. When the engine is running, the pilot exciter provides the GGPCU with three-phase power supply and generator frequency information. The GGPCU supplies the excitation current for the main exciter. The main alternator generates the three-phase (A, B and C) electrical power output to supply the Primary Electrical Power Distribution Center (PEPDC). The GGPCU regulates the excitation current in order to control the generator output voltage, which is measured at the Point Of Regulation (POR) in the PEPDC. A Lightning Protection Unit (LPU), connected in parallel to the power output lines, protects against the high voltage of the lightning strikes. In order to connect the generator power output to the AC bus, the GGPCU controls the Generator Line Contactor (GLC) by means of: - The connect command which supplies the coil of the GLC - The POWER READY signal which is sent to the Electrical Network Management Function (ENMF). The GLC is closed when the generator power is available and the electrical network configuration makes it possible. A Current Transformer (CT) in the generator and another one in the PEPDC measure the current in the three phases. They are used to: - Know the generator load - Detect current overload and phase imbalance - Provide feeder differential protection. In case of a current overload, the GGPCU sends an overload signal to the ENMF which sheds predetermined loads in order to protect the generator. Released in November 15, 2020 TRAINING USE ONLY Training Use Only 56 / 490 This document shall be used in accordance with the provisions described on the front page. NTCSS Release 2023-01 49_ATA24_Lv2&3_CAT B2_P_NOV20.pdf A400M Training Manual Released in November 15, 2020 TRAINING USE ONLY Training Use Only Electrical Generation SubSystem - Description & Operations Detailed Description 57 / 490 This document shall be used in accordance with the provisions described on the front page. NTCSS Release 2023-01 49_ATA24_Lv2&3_CAT B2_P_NOV20.pdf A400M Training Manual Electrical Generation SubSystem - Description & Operations Detailed Description Generator Electrical Management (II) When the engine is not running, the DC essential bus provides the GGPCU with backup power supply for the processing and communication functions. The GGPCU sends generator load data to the Core Processing Input Output Modules (CPIOMs) for the Electrical Load Management Function (ELMF). In order to prevent generator overloading, the ELMF can shed predetermined electrical loads. The GGPCU has interfaces with the Network Server System (NSS) to exchange BITE data with the Central Maintenance System (CMS). The BITE interactive mode is inhibited if there is not an on-ground condition. The GGPCU uses a discrete signal from the GPS Air Data Inertial Reference System (GADIRS) to sense the on-ground condition. The GGPCU transmits through the Input Output Modules (IOMs) and Avionics Data Communication Network (ADCN): - Generator data to the ECAM - Alerts to the Flight Warning System (FWS). Released in November 15, 2020 TRAINING USE ONLY Training Use Only 58 / 490 This document shall be used in accordance with the provisions described on the front page. NTCSS Release 2023-01 49_ATA24_Lv2&3_CAT B2_P_NOV20.pdf A400M Training Manual Released in November 15, 2020 TRAINING USE ONLY Training Use Only Electrical Generation SubSystem - Description & Operations Detailed Description 59 / 490 This document shall be used in accordance with the provisions described on the front page. NTCSS Release 2023-01 49_ATA24_Lv2&3_CAT B2_P_NOV20.pdf A400M Training Manual 2.1.5 Electrical Generation SubSystem - Description & Operations Variable Frequency Generator Variable Frequency Generator Variable Frequency Generator VFG Mechanical Description (I) The VFG is installed on the rear face of the accessory gear box of the engine. The VFG has an oil system that lubricates and controls its temperature. The oil system has one replaceable filter. Released in November 15, 2020 TRAINING USE ONLY Training Use Only 60 / 490 This document shall be used in accordance with the provisions described on the front page. NTCSS Release 2023-01 49_ATA24_Lv2&3_CAT B2_P_NOV20.pdf A400M Training Manual Released in November 15, 2020 TRAINING USE ONLY Training Use Only Electrical Generation SubSystem - Description & Operations Variable Frequency Generator 61 / 490 This document shall be used in accordance with the provisions described on the front page. NTCSS Release 2023-01 49_ATA24_Lv2&3_CAT B2_P_NOV20.pdf A400M Training Manual Electrical Generation SubSystem - Description & Operations Variable Frequency Generator VFG Mechanical Description (II) The drive shaft of the VFG receives the rotating mechanical energy from the accessory gear box. A V-band clamp ensures the attachment to the accessory gear box. Two bosses are used to attach a bracket for the feeder cables which are connected to the terminal block. The boss for lifting sling can be used in the removal/installation procedure. One oil outlet and one oil inlet connect the VFG with an external cooler. The VFG has the items that follow for the servicing of the oil system: - An oil fill port to fill the generator with oil - An oil spill plug to let oil spill during the filling operation of the generator - A sight glass to check the oil level - An oil drain plug to drain the sump during the emptying operation of the generator - A magnetic chip detector installed in the oil drain plug - An oil filter that must be replaced periodically. Released in November 15, 2020 TRAINING USE ONLY Training Use Only 62 / 490 This document shall be used in accordance with the provisions described on the front page. NTCSS Release 2023-01 49_ATA24_Lv2&3_CAT B2_P_NOV20.pdf A400M Training Manual Released in November 15, 2020 TRAINING USE ONLY Training Use Only Electrical Generation SubSystem - Description & Operations Variable Frequency Generator 63 / 490 This document shall be used in accordance with the provisions described on the front page. NTCSS Release 2023-01 49_ATA24_Lv2&3_CAT B2_P_NOV20.pdf A400M Training Manual Released in November 15, 2020 TRAINING USE ONLY Training Use Only Electrical Generation SubSystem - Description & Operations Variable Frequency Generator 64 / 490 This document shall be used in accordance with the provisions described on the front page. NTCSS Release 2023-01 49_ATA24_Lv2&3_CAT B2_P_NOV20.pdf A400M Training Manual Electrical Generation SubSystem - Description & Operations Variable Frequency Generator VFG Oil System The VFG uses an engine-mounted Air-Cooled Oil Cooler (ACOC) to cool the oil. The external air flows through the ACOC from an inlet duct to an outlet duct. The VFG has an internal oil pump mechanically driven by the rotor. The pump gets the oil from the sump and sends it to the ACOC through the filter. A differential pressure switch, installed in parallel with the filter, detects a clogged filter condition. In case the oil is too cold, to prevent overpressure, a cold start valve lets oil flow directly to the generator. The hot oil circulates through the cooler matrix and the cold oil goes back to the VFG. A bypass valve is also installed in the ACOC to prevent overpressure in the event of the cooler matrix becoming blocked. The VFG inlet oil goes to the generator to cool the rotor and the stator, and lubricate the shaft bearings. Then, the oil drains by gravity to the sump. A pressure relief valve regulates the supply of oil to the rotor; the excess oil goes to the sump. The VFG oil level is electrically monitored by the level sensor which provides two signals: low level and very low level. The VFG temperature is monitored by two sensors: - The oil temperature sensor which is located in the sump - The bearing temperature sensor which is located adjacent to the rotor front bearing. The VFG oil pressure is monitored by a low pressure switch which detects a low oil-pressure condition in the internal circuit. Released in November 15, 2020 TRAINING USE ONLY Training Use Only 65 / 490 This document shall be used in accordance with the provisions described on the front page. NTCSS Release 2023-01 49_ATA24_Lv2&3_CAT B2_P_NOV20.pdf A400M Training Manual Released in November 15, 2020 TRAINING USE ONLY Training Use Only Electrical Generation SubSystem - Description & Operations Variable Frequency Generator 66 / 490 This document shall be used in accordance with the provisions described on the front page. NTCSS Release 2023-01 49_ATA24_Lv2&3_CAT B2_P_NOV20.pdf A400M Training Manual Electrical Generation SubSystem - Description & Operations Variable Frequency Generator Oil Monitoring The VFG oil-monitoring sensors send several analogue and discrete signals to the GGPCU. They will trigger alerting messages on the ECAM as follows: - Low Level signal: The maintenance status message “ELEC” is displayed - Very Low Level signal: The alert “DRIVE OIL LEVEL LOW” is displayed - Oil and Bearing Temperature signals: When the oil temperature or the bearing temperature is excessive the alert "DRIVE OIL OVERHEAT" is shown - Low Pressure signal: The alert "DRIVE OIL PRESS LOW" is shown and the FAULT light illuminates on the DRIVE pushbutton - Filter Difference Pressure signal: When the filter is clogged, the maintenance status message “ELEC” is also displayed. The manual disconnection of the Drive Disconnect device is requested by the DRIVE push button. When it is pushed, a discrete signal is sent to the GGPCU. Another discrete feedback causes the illumination of the DISC light. On the ECAM, the alert “DRIVE DISCONNECTED” is shown. The mechanical disconnection is commanded by a signal from the GGPCU to the Drive Disconnect device in the VFG. If the drive is not manually disconnected, the drive disconnection is automatically commanded if the following abnormal conditions persist: - Excessive oil temperature - Excessive bearing temperature - Low pressure. The table summarizes the thresholds and time delays. For the oil monitoring function, the GGPCU communicates with the following systems: - NSS: To exchange BITE information related to sensors failures and detection of oil abnormal conditions - FADEC: To send the oil temperature and to receive the “engine starting in progress” condition - ECAM: To send the drive status - FWS: To send the oil alerts which are shown on the ECAM displays. Released in November 15, 2020 TRAINING USE ONLY Training Use Only 67 / 490 This document shall be used in accordance with the provisions described on the front page. NTCSS Release 2023-01 49_ATA24_Lv2&3_CAT B2_P_NOV20.pdf A400M Training Manual Released in November 15, 2020 TRAINING USE ONLY Training Use Only Electrical Generation SubSystem - Description & Operations Variable Frequency Generator 68 / 490 This document shall be used in accordance with the provisions described on the front page. NTCSS Release 2023-01 49_ATA24_Lv2&3_CAT B2_P_NOV20.pdf A400M Training Manual Electrical Generation SubSystem - Description & Operations General Description 2.2 Electrical Generation SubSystem - Description - AC Auxiliary Generation 2.2.1 General Description General Description AC Auxiliary Generation The AC auxiliary generation can be used on ground or in flight to supply three-phase 115 VAC power, with a constant frequency of 400 Hz, to part or the entire electrical network. The AC auxiliary generation is provided by one APU Generator (APU GEN) which can be connected to the main AC buses. The BUS TIE interconnects both sides of the network. The APU GEN is lubricated and cooled by the APU oil system. GGPCU 5 controls the APU GEN and transmits generator data to the ECAM displays. The APU GEN pushbutton-switch, installed on the overhead ELEC panel, controls the APU generator. Released in November 15, 2020 TRAINING USE ONLY Training Use Only 69 / 490 This document shall be used in accordance with the provisions described on the front page. NTCSS Release 2023-01 49_ATA24_Lv2&3_CAT B2_P_NOV20.pdf A400M Training Manual Released in November 15, 2020 TRAINING USE ONLY Training Use Only Electrical Generation SubSystem - Description & Operations General Description 70 / 490 This document shall be used in accordance with the provisions described on the front page. NTCSS Release 2023-01 49_ATA24_Lv2&3_CAT B2_P_NOV20.pdf A400M Training Manual Electrical Generation SubSystem - Description & Operations General Description APU Generator and GGPCU 5 The drive shaft of the APU generator is mechanically connected to the accessory gear box of the APU. The APU generator has: - A terminal block - Oil ports for the interface with the APU oil system - An electrical connector for the interface with GGPCU 5. GGPCU 5 provides generator control and protection functions. Released in November 15, 2020 TRAINING USE ONLY Training Use Only 71 / 490 This document shall be used in accordance with the provisions described on the front page. NTCSS Release 2023-01 49_ATA24_Lv2&3_CAT B2_P_NOV20.pdf A400M Training Manual Released in November 15, 2020 TRAINING USE ONLY Training Use Only Electrical Generation SubSystem - Description & Operations General Description 72 / 490 This document shall be used in accordance with the provisions described on the front page. NTCSS Release 2023-01 49_ATA24_Lv2&3_CAT B2_P_NOV20.pdf A400M Training Manual 2.2.2 Electrical Generation SubSystem - Description & Operations Controls & Indications Controls & Indications Controls and Indications APU Generator Pushbutton-switch The APU GEN pushbutton-switch is used to control the connection and disconnection of the APU generator to the electrical network. It has three statuses: - ON (pushed position): The lights are off. The generator connection and disconnection is automatically managed by GGPCU 5. It is the normal position. - OFF (released position): The OFF light illuminates. The generator is disconnected from the electrical network. - FAULT (pushed position): The FAULT light illuminates when the generator is faulty and disconnected from the electrical network. When the pushbutton is released, the FAULT light goes off. Released in November 15, 2020 TRAINING USE ONLY Training Use Only 73 / 490 This document shall be used in accordance with the provisions described on the front page. NTCSS Release 2023-01 49_ATA24_Lv2&3_CAT B2_P_NOV20.pdf A400M Training Manual Released in November 15, 2020 TRAINING USE ONLY Training Use Only Electrical Generation SubSystem - Description & Operations Controls & Indications 74 / 490 This document shall be used in accordance with the provisions described on the front page. NTCSS Release 2023-01 49_ATA24_Lv2&3_CAT B2_P_NOV20.pdf A400M Training Manual Electrical Generation SubSystem - Description & Operations Controls & Indications APU Generator Indications on ECAM When used, the following information relative to the APU generator is presented on the SD ELEC AC page and APU page: - Contactor symbol - Load - Voltage - Frequency. When not used, the APU Generator is in standby state and only the APU GEN label is displayed. When the APU is running but the APU GEN is disconnected, the OFF label is displayed. Released in November 15, 2020 TRAINING USE ONLY Training Use Only 75 / 490 This document shall be used in accordance with the provisions described on the front page. NTCSS Release 2023-01 49_ATA24_Lv2&3_CAT B2_P_NOV20.pdf A400M Training Manual Released in November 15, 2020 TRAINING USE ONLY Training Use Only Electrical Generation SubSystem - Description & Operations Controls & Indications 76 / 490 This document shall be used in accordance with the provisions described on the front page. NTCSS Release 2023-01 49_ATA24_Lv2&3_CAT B2_P_NOV20.pdf A400M Training Manual Electrical Generation SubSystem - Description & Operations Controls & Indications APU Generator Alerts on ECAM The AC Auxiliary Generation system will provide the following level 2 alert on the Warning Display: - APU GEN FAULT. Released in November 15, 2020 TRAINING USE ONLY Training Use Only 77 / 490 This document shall be used in accordance with the provisions described on the front page. NTCSS Release 2023-01 49_ATA24_Lv2&3_CAT B2_P_NOV20.pdf A400M Training Manual Released in November 15, 2020 TRAINING USE ONLY Training Use Only Electrical Generation SubSystem - Description & Operations Controls & Indications 78 / 490 This document shall be used in accordance with the provisions described on the front page. NTCSS Release 2023-01 49_ATA24_Lv2&3_CAT B2_P_NOV20.pdf A400M Training Manual 2.2.3 Electrical Generation SubSystem - Description & Operations Component Location Component Location Component Location APU GEN Location The APU Generator is installed on the accessory gear box of the APU. Released in November 15, 2020 TRAINING USE ONLY Training Use Only 79 / 490 This document shall be used in accordance with the provisions described on the front page. NTCSS Release 2023-01 49_ATA24_Lv2&3_CAT B2_P_NOV20.pdf A400M Training Manual Released in November 15, 2020 TRAINING USE ONLY Training Use Only Electrical Generation SubSystem - Description & Operations Component Location 80 / 490 This document shall be used in accordance with the provisions described on the front page. NTCSS Release 2023-01 49_ATA24_Lv2&3_CAT B2_P_NOV20.pdf A400M Training Manual Electrical Generation SubSystem - Description & Operations Component Location APU Generator Feeder Route The feeders of the APU generator are routed through the fuselage and connected to the PEPDC 1. Released in November 15, 2020 TRAINING USE ONLY Training Use Only 81 / 490 This document shall be used in accordance with the provisions described on the front page. NTCSS Release 2023-01 49_ATA24_Lv2&3_CAT B2_P_NOV20.pdf A400M Training Manual Released in November 15, 2020 TRAINING USE ONLY Training Use Only Electrical Generation SubSystem - Description & Operations Component Location 82 / 490 This document shall be used in accordance with the provisions described on the front page. NTCSS Release 2023-01 49_ATA24_Lv2&3_CAT B2_P_NOV20.pdf A400M Training Manual Electrical Generation SubSystem - Description & Operations Component Location GGPCU 5 Location GGPCU 5 is located in the Nose Fuselage on the mezzanine. It is installed on the left side, close to GGPCUs 1 and 2. Released in November 15, 2020 TRAINING USE ONLY Training Use Only 83 / 490 This document shall be used in accordance with the provisions described on the front page. NTCSS Release 2023-01 49_ATA24_Lv2&3_CAT B2_P_NOV20.pdf A400M Training Manual Released in November 15, 2020 TRAINING USE ONLY Training Use Only Electrical Generation SubSystem - Description & Operations Component Location 84 / 490 This document shall be used in accordance with the provisions described on the front page. NTCSS Release 2023-01 49_ATA24_Lv2&3_CAT B2_P_NOV20.pdf A400M Training Manual 2.2.4 Electrical Generation SubSystem - Description & Operations Detailed Description Detailed Description Detailed Description APU Generator Description (I) The APU generator is driven by the APU gearbox. The APU generator has: - A terminal block to connect the feeder cables - An electrical connector for the interface with GGPCU 5. Released in November 15, 2020 TRAINING USE ONLY Training Use Only 85 / 490 This document shall be used in accordance with the provisions described on the front page. NTCSS Release 2023-01 49_ATA24_Lv2&3_CAT B2_P_NOV20.pdf A400M Training Manual Released in November 15, 2020 TRAINING USE ONLY Training Use Only Electrical Generation SubSystem - Description & Operations Detailed Description 86 / 490 This document shall be used in accordance with the provisions described on the front page. NTCSS Release 2023-01 49_ATA24_Lv2&3_CAT B2_P_NOV20.pdf A400M Training Manual Electrical Generation SubSystem - Description & Operations Detailed Description APU Generator Description (II) The drive shaft of the APU generator receives mechanical power from the accessory gear box. The APU generator operates at a constant speed to supply three-phase 115 VAC electrical power at a constant frequency of 400 Hz. The continuous power capacity is 90 KVA. The APU oil system supplies the oil to the APU GEN through ports integrated on the installation flange of the generator. The supplied oil cools the rotor and stator windings and lubricates the bearings and shaft splines. A temperature sensor in the generator measures the oil temperature. The electrical architecture of the generator is similar to the VFG architecture (refer to “VFG Electrical Description”). Released in November 15, 2020 TRAINING USE ONLY Training Use Only 87 / 490 This document shall be used in accordance with the provisions described on the front page. NTCSS Release 2023-01 49_ATA24_Lv2&3_CAT B2_P_NOV20.pdf A400M Training Manual Released in November 15, 2020 TRAINING USE ONLY Training Use Only Electrical Generation SubSystem - Description & Operations Detailed Description 88 / 490 This document shall be used in accordance with the provisions described on the front page. NTCSS Release 2023-01 49_ATA24_Lv2&3_CAT B2_P_NOV20.pdf A400M Training Manual Electrical Generation SubSystem - Description & Operations Detailed Description APU Generator Management In order to control the generator connection and disconnection, GGPCU 5 exchanges the following discrete signals: - APU READY from the Electronic Control Box (ECB) (which receives the oil temperature signal from the temperature sensor) - On/off command from the APU GEN pushbutton-switch which is used to control the generator connection and to reset the protection functions - FAULT and OFF signals to the APU GEN pushbutton-switch to illuminate the lights that show the status of the generator - Off status from the APU master switch to provide the APU shutdown request signal for generator control logics - Pushed status from the FIRE pushbutton which is used to remove the excitation and disconnect the generator. The generator control, contactor (AGC) control, and communication functions are similar to those of the VFG (refer to “Generator Electrical Management” in the lesson “AC Main Generation”). Released in November 15, 2020 TRAINING USE ONLY Training Use Only 89 / 490 This document shall be used in accordance with the provisions described on the front page. NTCSS Release 2023-01 49_ATA24_Lv2&3_CAT B2_P_NOV20.pdf A400M Training Manual Released in November 15, 2020 TRAINING USE ONLY Training Use Only Electrical Generation SubSystem - Description & Operations Detailed Description 90 / 490 This document shall be used in accordance with the provisions described on the front page. NTCSS Release 2023-01 49_ATA24_Lv2&3_CAT B2_P_NOV20.pdf A400M Training Manual Electrical Generation SubSystem - Description & Operations General Description 2.3 Electrical Generation SubSystem - Description - AC External Power 2.3.1 General Description General Description AC External Power (I) The external power supplies the entire aircraft electrical network with three-phase power of 115 VAC, with a constant frequency of 400 Hz, through: - An External Power Ground-Connector (EPGC) - An AC filter. The BUS TIE interconnects both sides of the network. GGPCU 5 is used to: - Control the external power and exchange interlock signals through a DC filter - Transmit data to the ECAM displays - Receive commands from the EXT pushbutton in order to control the connection and disconnection of the external power. Released in November 15, 2020 TRAINING USE ONLY Training Use Only 91 / 490 This document shall be used in accordance with the provisions described on the front page. NTCSS Release 2023-01 49_ATA24_Lv2&3_CAT B2_P_NOV20.pdf A400M Training Manual Released in November 15, 2020 TRAINING USE ONLY Training Use Only Electrical Generation SubSystem - Description & Operations General Description 92 / 490 This document shall be used in accordance with the provisions described on the front page. NTCSS Release 2023-01 49_ATA24_Lv2&3_CAT B2_P_NOV20.pdf A400M Training Manual Electrical Generation SubSystem - Description & Operations General Description AC External Power (II) The AC external power is supplied by one Ground Power Unit (GPU). It can be connected to the aircraft through the EPGC, which is installed in a servicing panel located on the right hand side of the forward fuselage. A door permits access to the EPGC servicing panel which contains: - The external power panel with several indication lights - The EPGC which accepts the GPU connector. Released in November 15, 2020 TRAINING USE ONLY Training Use Only 93 / 490 This document shall be used in accordance with the provisions described on the front page. NTCSS Release 2023-01 49_ATA24_Lv2&3_CAT B2_P_NOV20.pdf A400M Training Manual Released in November 15, 2020 TRAINING USE ONLY Training Use Only Electrical Generation SubSystem - Description & Operations General Description 94 / 490 This document shall be used in accordance with the provisions described on the front page. NTCSS Release 2023-01 49_ATA24_Lv2&3_CAT B2_P_NOV20.pdf A400M Training Manual 2.3.2 Electrical Generation SubSystem - Description & Operations Controls & Indications Controls & Indications Controls and Indications External Power Pushbutton The EXT pushbutton controls the connection and disconnection of the external power. The EXT pushbutton has three statuses: - The lights are off: No power on EPGC or the external power characteristics are out of the normal range. - The AVAIL light illuminates when external power is available in the EPGC and the electrical characteristics are within the normal range. - The ON light illuminates when external power is in use, supplying the electrical network. Released in November 15, 2020 TRAINING USE ONLY Training Use Only 95 / 490 This document shall be used in accordance with the provisions described on the front page. NTCSS Release 2023-01 49_ATA24_Lv2&3_CAT B2_P_NOV20.pdf A400M Training Manual Released in November 15, 2020 TRAINING USE ONLY Training Use Only Electrical Generation SubSystem - Description & Operations Controls & Indications 96 / 490 This document shall be used in accordance with the provisions described on the front page. NTCSS Release 2023-01 49_ATA24_Lv2&3_CAT B2_P_NOV20.pdf A400M Training Manual Electrical Generation SubSystem - Description & Operations Controls & Indications Indicating on the External Power Panel Two indication lights show the status of the external power: - EXT PWR NOT IN USE: It comes on when the GPU is connected to the EPGC and it is available but the external power is not connected to the electrical network (EXT pushbutton on ELEC panel not pushed). - EXT PWR AVAIL: It comes on when the GPU is connected to the EPGC and it is available. The LIGHT TEST pushbutton is used to test the indication lights. Released in November 15, 2020 TRAINING USE ONLY Training Use Only 97 / 490 This document shall be used in accordance with the provisions described on the front page. NTCSS Release 2023-01 49_ATA24_Lv2&3_CAT B2_P_NOV20.pdf A400M Training Manual Released in November 15, 2020 TRAINING USE ONLY Training Use Only Electrical Generation SubSystem - Description & Operations Controls & Indications 98 / 490 This document shall be used in accordance with the provisions described on the front page. NTCSS Release 2023-01 49_ATA24_Lv2&3_CAT B2_P_NOV20.pdf A400M Training Manual Electrical Generation SubSystem - Description & Operations Controls & Indications External Power Indications on ECAM In flight there are not external power indications. When the external power is used, the following information is presented on the SD ELEC AC page: - Contactor symbol - Label EXT - Voltage indication - Frequency indication. When the external power is not available, and the A/C is on ground, only the label EXT and contactor symbol are displayed in white. Released in November 15, 2020 TRAINING USE ONLY Training Use Only 99 / 490 This document shall be used in accordance with the provisions described on the front page. NTCSS Release 2023-01 49_ATA24_Lv2&3_CAT B2_P_NOV20.pdf A400M Training Manual Released in November 15, 2020 TRAINING USE ONLY Training Use Only Electrical Generation SubSystem - Description & Operations Controls & Indications 100 / 490 This document shall be used in accordance with the provisions described on the front page. NTCSS Release 2023-01 49_ATA24_Lv2&3_CAT B2_P_NOV20.pdf A400M Training Manual Electrical Generation SubSystem - Description & Operations Controls & Indications External Power Alerts on ECAM The AC External Power system will provide the following alerts on the Warning Display: - EXT PWR (memo): External power available - EXT PWR FAULT: A protective function has disconnected the external power. The fault condition is reset by pressing the EXT pushbutton. Released in November 15, 2020 TRAINING USE ONLY Training Use Only 101 / 490 This document shall be used in accordance with the provisions described on the front page. NTCSS Release 2023-01 49_ATA24_Lv2&3_CAT B2_P_NOV20.pdf A400M Training Manual Released in November 15, 2020 TRAINING USE ONLY Training Use Only Electrical Generation SubSystem - Description & Operations Controls & Indications 102 / 490 This document shall be used in accordance with the provisions described on the front page. NTCSS Release 2023-01 49_ATA24_Lv2&3_CAT B2_P_NOV20.pdf A400M Training Manual 2.3.3 Electrical Generation SubSystem - Description & Operations Component Location Component Location Component Location EPGC Location The EPGC is installed in a servicing panel located on the forward fuselage. Released in November 15, 2020 TRAINING USE ONLY Training Use Only 103 / 490 This document shall be used in accordance with the provisions described on the front page. NTCSS Release 2023-01 49_ATA24_Lv2&3_CAT B2_P_NOV20.pdf A400M Training Manual Released in November 15, 2020 TRAINING USE ONLY Training Use Only Electrical Generation SubSystem - Description & Operations Component Location 104 / 490 This document shall be used in accordance with the provisions described on the front page. NTCSS Release 2023-01 49_ATA24_Lv2&3_CAT B2_P_NOV20.pdf A400M Training Manual Electrical Generation SubSystem - Description & Operations Component Location Filters Location In some aircraft versions, two filters are installed close to the EPGC: The AC and DC External Ground Power Filters. Released in November 15, 2020 TRAINING USE ONLY Training Use Only 105 / 490 This document shall be used in accordance with the provisions described on the front page. NTCSS Release 2023-01 49_ATA24_Lv2&3_CAT B2_P_NOV20.pdf A400M Training Manual Released in November 15, 2020 TRAINING USE ONLY Training Use Only Electrical Generation SubSystem - Description & Operations Component Location 106 / 490 This document shall be used in accordance with the provisions described on the front page. NTCSS Release 2023-01 49_ATA24_Lv2&3_CAT B2_P_NOV20.pdf A400M Training Manual Electrical Generation SubSystem - Description & Operations Component Location External Power Feeder Route A feeder cable connects the EPGC and AC-EGPF to PEPDC 2. Released in November 15, 2020 TRAINING USE ONLY Training Use Only 107 / 490 This document shall be used in accordance with the provisions described on the front page. NTCSS Release 2023-01 49_ATA24_Lv2&3_CAT B2_P_NOV20.pdf A400M Training Manual Released in November 15, 2020 TRAINING USE ONLY Training Use Only Electrical Generation SubSystem - Description & Operations Component Location 108 / 490 This document shall be used in accordance with the provisions described on the front page. NTCSS Release 2023-01 49_ATA24_Lv2&3_CAT B2_P_NOV20.pdf A400M Training Manual 2.3.4 Electrical Generation SubSystem - Description & Operations Detailed Description Detailed Description Detailed Description Description of EPGC and Filters The EPGC accepts three-phase 115VAC electrical power at a constant frequency of 400 Hz and has a maximum power capacity of 90 kVA. The EPGC has a shell and a receptacle with a terminal block. The AC and the DC External Ground-Power Filters are TEMPEST filters used to avoid the emissions of compromising signals. They have several connectors. Released in November 15, 2020 TRAINING USE ONLY Training Use Only 109 / 490 This document shall be used in accordance with the provisions described on the front page. NTCSS Release 2023-01 49_ATA24_Lv2&3_CAT B2_P_NOV20.pdf A400M Training Manual Released in November 15, 2020 TRAINING USE ONLY Training Use Only Electrical Generation SubSystem - Description & Operations Detailed Description 110 / 490 This document shall be used in accordance with the provisions described on the front page. NTCSS Release 2023-01 49_ATA24_Lv2&3_CAT B2_P_NOV20.pdf A400M Training Manual Electrical Generation SubSystem - Description & Operations Detailed Description GGPCU-5 Description GGPCU 5, which is the same unit that controls the APU generator, provides the following functions: - External power control, including: o Voltage monitoring o Protection o Contactors management. - Processing and communication, including: o Data transmission o BITE functions. Released in November 15, 2020 TRAINING USE ONLY Training Use Only 111 / 490 This document shall be used in accordance with the provisions described on the front page. NTCSS Release 2023-01 49_ATA24_Lv2&3_CAT B2_P_NOV20.pdf A400M Training Manual Released in November 15, 2020 TRAINING USE ONLY Training Use Only Electrical Generation SubSystem - Description & Operations Detailed Description 112 / 490 This document shall be used in accordance with the provisions described on the front page. NTCSS Release 2023-01 49_ATA24_Lv2&3_CAT B2_P_NOV20.pdf A400M Training Manual Electrical Generation SubSystem - Description & Operations Detailed Description System Functions External Power Management The EPGC plug receives the three-phase electrical power and neutral from the GPU. The EPGC output is connected to PEPDC 2 through the AC filter. GGPCU 5 controls the connection between the external power and the electrical network. The power supply for GGPCU 5 is provided by: - The POR in the PEPDC, or - The DC essential bus as backup. Two 28 VDC interlock signals are exchanged, through the DC filter, between the GGPCU and the GPU. One is used by the GPU to maintain the supply, the other one is received by the GGPCU to know if the GPU is connected or not. The EXT pushbutton controls the connection and disconnection of the external power supply. The pushbutton sends the ON COMMAND to the GGPCU, and receives signals for the illumination of the AVAIL or ON lights. The GGPCU monitors the voltage at the POR. If the voltage is correct and the EXT pushbutton is on, the GGPCU controls the External Power Contactor (EPC) by means of: - The CONNECT COMMAND which supplies the driver of the EPC - The POWER READY and the CONNECT DEMAND signals, which are sent to the ENMF. The ENMF provides the ground to close the EPC when the power is available and the electrical network configuration makes it possible. The indication lights on the EPGC panel show the availability and status of the connection. The lights are controlled by the signals sent from the PEPDC. A Current Transformer (CT) measures the current supplied to the electrical network. The GGPCU communicates with the CMS to do the BITE function of the External Power Control. The GGPCU transmits, via IOMs and ADCN, the following data: - External power data to the ECAM - Alerts to the FWS. Released in November 15, 2020 TRAINING USE ONLY Training Use Only 113 / 490 This document shall be used in accordance with the provisions described on the front page. NTCSS Release 2023-01 49_ATA24_Lv2&3_CAT B2_P_NOV20.pdf A400M Training Manual Released in November 15, 2020 TRAINING USE ONLY Training Use Only Electrical Generation SubSystem - Description & Operations Detailed Description 114 / 490 This document shall be used in accordance with the provisions described on the front page. NTCSS Release 2023-01 49_ATA24_Lv2&3_CAT B2_P_NOV20.pdf A400M Training Manual Electrical Generation SubSystem - Description & Operations General Description 2.4 Electrical Generation SubSystem - Description - AC Domestic Generation 2.4.1 General Description General Description AC Domestic Generation The AC Domestic Generation System has four converters connected to the Primary and Secondary Power-distribution system. The converters receive 115 VAC and independently supply different voltages. Two converters for Medical Evacuation (MEDEVAC) generate 230 VAC. There are two pushbutton-switches and two overload lights installed on the ELEC CONV panel that control the status of the converters. One converter for military equipment generates 110 VAC. There is one pushbutton-switch installed on the ELEC CONV panel that controls the status of the converter. One converter for the cockpit and LMWS generates 230 VAC. There is one pushbutton-switch installed on the ELEC panel that controls the status of the converter. The Primary and Secondary Power-Distribution system distributes the different voltages generated by the converters to several AC electrical power outlets in the cargo hold, cockpit and loadmaster workstation. Released in November 15, 2020 TRAINING USE ONLY Training Use Only 115 / 490 This document shall be used in accordance with the provisions described on the front page. NTCSS Release 2023-01 49_ATA24_Lv2&3_CAT B2_P_NOV20.pdf A400M Training Manual Released in November 15, 2020 TRAINING USE ONLY Training Use Only Electrical Generation SubSystem - Description & Operations General Description 116 / 490 This document shall be used in accordance with the provisions described on the front page. NTCSS Release 2023-01 49_ATA24_Lv2&3_CAT B2_P_NOV20.pdf A400M Training Manual 2.4.2 Electrical Generation SubSystem - Description & Operations Controls & Indications Controls & Indications Controls & Indications Converters Control and Indicating on the ELEC CONV Panel For the MEDEVAC converters, the OVLD legend indicates an overload condition. In this case the procedure will be to unplug the latest equipment that was connected to the outlets of the related converter. If the overload condition is not removed after a maximum of 15 minutes, the OVLD legend goes off and the converter is in a failure condition. For the MEDEVAC and the 110 V converters there are three pushbutton-switches. Each one has the following statuses: - ON (pushed): The lights are off. The converter supplies power normally - OFF (released): The converter is disconnected and the protections are reset - FAULT (pushed): Converter failure or overload. The converter is de-energized. It can be reset recycling the pushbuttonswitch. Released in November 15, 2020 TRAINING USE ONLY Training Use Only 117 / 490 This document shall be used in accordance with the provisions described on the front page. NTCSS Release 2023-01 49_ATA24_Lv2&3_CAT B2_P_NOV20.pdf A400M Training Manual Released in November 15, 2020 TRAINING USE ONLY Training Use Only Electrical Generation SubSystem - Description & Operations Controls & Indications 118 / 490 This document shall be used in accordance with the provisions described on the front page. NTCSS Release 2023-01 49_ATA24_Lv2&3_CAT B2_P_NOV20.pdf A400M Training Manual Electrical Generation SubSystem - Description & Operations Controls & Indications Converter Control and Indicating on the ELEC Maintenance Panel The 230 VAC converter pushbutton-switch has three statuses. They are similar to the statuses of the pushbutton-switches on the ELEC CONV panel, with the difference of the FAULT light that also indicates an overload condition. Released in November 15, 2020 TRAINING USE ONLY Training Use Only 119 / 490 This document shall be used in accordance with the provisions described on the front page. NTCSS Release 2023-01 49_ATA24_Lv2&3_CAT B2_P_NOV20.pdf A400M Training Manual Released in November 15, 2020 TRAINING USE ONLY Training Use Only Electrical Generation SubSystem - Description & Operations Controls & Indications 120 / 490 This document shall be used in accordance with the provisions described on the front page. NTCSS Release 2023-01 49_ATA24_Lv2&3_CAT B2_P_NOV20.pdf A400M Training Manual 2.4.3 Electrical Generation SubSystem - Description & Operations Component Location Component Location Component Location Domestic Converters Location (I) The 230 V converter and the MEDEVAC 2 converter are mounted together on a shelf on the right hand side of the lower-deck avionics bay. Released in November 15, 2020 TRAINING USE ONLY Training Use Only 121 / 490 This document shall be used in accordance with the provisions described on the front page. NTCSS Release 2023-01 49_ATA24_Lv2&3_CAT B2_P_NOV20.pdf A400M Training Manual Released in November 15, 2020 TRAINING USE ONLY Training Use Only Electrical Generation SubSystem - Description & Operations Component Location 122 / 490 This document shall be used in accordance with the provisions described on the front page. NTCSS Release 2023-01 49_ATA24_Lv2&3_CAT B2_P_NOV20.pdf A400M Training Manual Electrical Generation SubSystem - Description & Operations Component Location Domestic Converters Location (II) The 110 V converter and the MEDEVAC 1 converter are installed on the nose landing gear box, in the lower-deck avionics bay. Released in November 15, 2020 TRAINING USE ONLY Training Use Only 123 / 490 This document shall be used in accordance with the provisions described on the front page. NTCSS Release 2023-01 49_ATA24_Lv2&3_CAT B2_P_NOV20.pdf A400M Training Manual Released in November 15, 2020 TRAINING USE ONLY Training Use Only Electrical Generation SubSystem - Description & Operations Component Location 124 / 490 This document shall be used in accordance with the provisions described on the front page. NTCSS Release 2023-01 49_ATA24_Lv2&3_CAT B2_P_NOV20.pdf A400M Training Manual 2.4.4 Electrical Generation SubSystem - Description & Operations Detailed Description Detailed Description Detailed Description Converters Description – MEDEVAC CONVERTER The MEDEVAC converter has a fan in the equipment case to decrease the internal temperature. The converter has three connectors: - AC power input - AC power output - Signals. A circuit breaker that is on the equipment case is used to protect the converter. The MEDEVAC converter supplies the electrical outlets used to connect medical evacuation equipment with an electrical power of single-phase 230 VAC and a frequency of 50 Hz. The maximum power is 3 KVA. Released in November 15, 2020 TRAINING USE ONLY Training Use Only 125 / 490 This document shall be used in accordance with the provisions described on the front page. NTCSS Release 2023-01 49_ATA24_Lv2&3_CAT B2_P_NOV20.pdf A400M Training Manual Released in November 15, 2020 TRAINING USE ONLY Training Use Only Electrical Generation SubSystem - Description & Operations Detailed Description 126 / 490 This document shall be used in accordance with the provisions described on the front page. NTCSS Release 2023-01 49_ATA24_Lv2&3_CAT B2_P_NOV20.pdf A400M Training Manual Electrical Generation SubSystem - Description & Operations Detailed Description Converters Description – 110 V Converter The 110 V converter has similar external components than the MEDEVAC converter (already described). The 110 V converter supplies the electrical outlets used to connect military equipment with an electrical power of single-phase 110 VAC and a frequency of 60 Hz. The maximum power is 1 KVA. Released in November 15, 2020 TRAINING USE ONLY Training Use Only 127 / 490 This document shall be used in accordance with the provisions described on the front page. NTCSS Release 2023-01 49_ATA24_Lv2&3_CAT B2_P_NOV20.pdf A400M Training Manual Released in November 15, 2020 TRAINING USE ONLY Training Use Only Electrical Generation SubSystem - Description & Operations Detailed Description 128 / 490 This document shall be used in accordance with the provisions described on the front page. NTCSS Release 2023-01 49_ATA24_Lv2&3_CAT B2_P_NOV20.pdf A400M Training Manual Electrical Generation SubSystem - Description & Operations Detailed Description Converters Description – 230 V Converter The 230 V converter has similar external components than the MEDEVAC converter (already described). The 230 V converter supplies the electrical outlets in the cockpit and LMWS used to connect equipment, like the Portable Multipurpose Access Terminal (PMAT). The electrical power is single-phase 230 VAC with a frequency of 50 Hz. The maximum power is 500 VA. Released in November 15, 2020 TRAINING USE ONLY Training Use Only 129 / 490 This document shall be used in accordance with the provisions described on the front page. NTCSS Release 2023-01 49_ATA24_Lv2&3_CAT B2_P_NOV20.pdf A400M Training Manual Released in November 15, 2020 TRAINING USE ONLY Training Use Only Electrical Generation SubSystem - Description & Operations Detailed Description 130 / 490 This document shall be used in accordance with the provisions described on the front page. NTCSS Release 2023-01 49_ATA24_Lv2&3_CAT B2_P_NOV20.pdf A400M Training Manual Electrical Generation SubSystem - Description & Operations Detailed Description Domestic Generation Architecture Each domestic converter is connected to a different distribution center. The MEDEVAC 1 and 2 converters are respectively supplied by the reconfigurable buses 1 and 4. These buses are shed if the crew operates the LOAD SHED pushbutton-switch. Consequently, the MEDEVAC converters are de-energized. The 110 V converter and the 230 V converter are respectively supplied by the SEPDC 1 and 2. The converters outputs are connected to the PEPDCs which distribute the different voltages to the electrical outlets. Each converter exchanges with its respective pushbutton-switch the following discrete signals: - ON/OFF command - Overload condition (except for the 110 V converter) - Failure condition. All converters have an internal BITE function. The BITE information is interchanged with the CMS through discrete signals. Released in November 15, 2020 TRAINING USE ONLY Training Use Only 131 / 490 This document shall be used in accordance with the provisions described on the front page. NTCSS Release 2023-01 49_ATA24_Lv2&3_CAT B2_P_NOV20.pdf A400M Training Manual Released in November 15, 2020 TRAINING USE ONLY Training Use Only Electrical Generation SubSystem - Description & Operations Detailed Description 132 / 490 This document shall be used in accordance with the provisions described on the front page. NTCSS Release 2023-01 49_ATA24_Lv2&3_CAT B2_P_NOV20.pdf A400M Training Manual Electrical Generation SubSystem - Description & Operations General Description 2.5 Electrical Generation SubSystem - Description - DC Main and Essential Generation 2.5.1 General Description General Description DC Main and Essential Generation The DC Main Generation and Essential Generation systems are used to power the whole DC electrical network as soon as the AC distribution network is powered. The DC Main Generation system is composed of two Battery Charger Rectifier Units (BCRU 1 and BCRU 2) and one Transformer Rectifier Unit (TRU). The DC Essential Generation system has one Battery Charger Rectifier Unit (BCRU ESS). Each unit receives three-phase 115 VAC power from one AC bus and transforms this power into 28 VDC power to supply its related DC bus. DC bus 2 can be supplied by BCRU 2 or, as a backup, by the TRU. All the units have interfaces with: - The RESET buttons - The Avionics Equipment Ventilation (AEV) system which provides suction airflow for heat dissipation - The Battery DC Generation system for batteries control and monitoring - The ECAM displays which show BCRUs and TRU data. Released in November 15, 2020 TRAINING USE ONLY Training Use Only 133 / 490 This document shall be used in accordance with the provisions described on the front page. NTCSS Release 2023-01 49_ATA24_Lv2&3_CAT B2_P_NOV20.pdf A400M Training Manual Released in November 15, 2020 TRAINING USE ONLY Training Use Only Electrical Generation SubSystem - Description & Operations General Description 134 / 490 This document shall be used in accordance with the provisions described on the front page. NTCSS Release 2023-01 49_ATA24_Lv2&3_CAT B2_P_NOV20.pdf A400M Training Manual 2.5.2 Electrical Generation SubSystem - Description & Operations Controls & Indications Controls & Indications Controls and Indications BCRU/TRU Reset Buttons There are four reset buttons installed on the RESET panels of the cockpit overhead panel. After a unit failure, when pulled and pushed, they do a reset of the protection functions of the related BCRU or TRU. Released in November 15, 2020 TRAINING USE ONLY Training Use Only 135 / 490 This document shall be used in accordance with the provisions described on the front page. NTCSS Release 2023-01 49_ATA24_Lv2&3_CAT B2_P_NOV20.pdf A400M Training Manual Released in November 15, 2020 TRAINING USE ONLY Training Use Only Electrical Generation SubSystem - Description & Operations Controls & Indications 136 / 490 This document shall be used in accordance with the provisions described on the front page. NTCSS Release 2023-01 49_ATA24_Lv2&3_CAT B2_P_NOV20.pdf A400M Training Manual Electrical Generation SubSystem - Description & Operations Controls & Indications BCRUs/TRU Indications on ECAM The following information relative to BCRU 1, BCRU Essential, BCRU 2, and TRU is presented on the ELEC DC page: - Title (in amber if the unit does not operate) - Power supply source (in amber if the unit is not supplied) - Voltage - Current. Released in November 15, 2020 TRAINING USE ONLY Training Use Only 137 / 490 This document shall be used in accordance with the provisions described on the front page. NTCSS Release 2023-01 49_ATA24_Lv2&3_CAT B2_P_NOV20.pdf A400M Training Manual Released in November 15, 2020 TRAINING USE ONLY Training Use Only Electrical Generation SubSystem - Description & Operations Controls & Indications 138 / 490 This document shall be used in accordance with the provisions described on the front page. NTCSS Release 2023-01 49_ATA24_Lv2&3_CAT B2_P_NOV20.pdf A400M Training Manual Electrical Generation SubSystem - Description & Operations Controls & Indications BCRU/TRU Alerts on ECAM The DC Main Generation system will provide the following level 1 alerts on the Warning Display: - TR 1 FAULT - TR 2 FAULT - TR ESS FAULT - TR APU FAULT. Only for BCRU 1, one level 2 alert will be triggered if the temperature exceeds a define threshold: - TR 1 OVERHEAT. The level 3 alert DC ESS BUS ON BAT warns the crew of the loss of Essential BCRU when the aircraft is in emergency configuration. Released in November 15, 2020 TRAINING USE ONLY Training Use Only 139 / 490 This document shall be used in accordance with the provisions described on the front page. NTCSS Release 2023-01 49_ATA24_Lv2&3_CAT B2_P_NOV20.pdf A400M Training Manual Released in November 15, 2020 TRAINING USE ONLY Training Use Only Electrical Generation SubSystem - Description & Operations Controls & Indications 140 / 490 This document shall be used in accordance with the provisions described on the front page. NTCSS Release 2023-01 49_ATA24_Lv2&3_CAT B2_P_NOV20.pdf A400M Training Manual 2.5.3 Electrical Generation SubSystem - Description & Operations Component Location Component Location Component Location Main BCRUs Location BCRUs 1 and 2 are installed in the upper deck of the forward fuselage, on top of distribution centers. Released in November 15, 2020 TRAINING USE ONLY Training Use Only 141 / 490 This document shall be used in accordance with the provisions described on the front page. NTCSS Release 2023-01 49_ATA24_Lv2&3_CAT B2_P_NOV20.pdf A400M Training Manual Released in November 15, 2020 TRAINING USE ONLY Training Use Only Electrical Generation SubSystem - Description & Operations Component Location 142 / 490 This document shall be used in accordance with the provisions described on the front page. NTCSS Release 2023-01 49_ATA24_Lv2&3_CAT B2_P_NOV20.pdf A400M Training Manual Electrical Generation SubSystem - Description & Operations Component Location Essential BCRU Location The Essential BCRU is installed in the lower deck of the forward fuselage. Released in November 15, 2020 TRAINING USE ONLY Training Use Only 143 / 490 This document shall be used in accordance with the provisions described on the front page. NTCSS Release 2023-01 49_ATA24_Lv2&3_CAT B2_P_NOV20.pdf A400M Training Manual Released in November 15, 2020 TRAINING USE ONLY Training Use Only Electrical Generation SubSystem - Description & Operations Component Location 144 / 490 This document shall be used in accordance with the provisions described on the front page. NTCSS Release 2023-01 49_ATA24_Lv2&3_CAT B2_P_NOV20.pdf A400M Training Manual Electrical Generation SubSystem - Description & Operations Component Location TRU Location The TRU is installed in the upper deck of the forward fuselage, next to the right-side distribution centers. Released in November 15, 2020 TRAINING USE ONLY Training Use Only 145 / 490 This document shall be used in accordance with the provisions described on the front page. NTCSS Release 2023-01 49_ATA24_Lv2&3_CAT B2_P_NOV20.pdf A400M Training Manual Released in November 15, 2020 TRAINING USE ONLY Training Use Only Electrical Generation SubSystem - Description & Operations Component Location 146 / 490 This document shall be used in accordance with the provisions described on the front page. NTCSS Release 2023-01 49_ATA24_Lv2&3_CAT B2_P_NOV20.pdf A400M Training Manual Electrical Generation SubSystem - Description & Operations Component Location BCRU and TRU Feeders Routes The BCRUs and TRU feeders are routed in the forward fuselage to connect each unit with its corresponding distribution center. Released in November 15, 2020 TRAINING USE ONLY Training Use Only 147 / 490 This document shall be used in accordance with the provisions described on the front page. NTCSS Release 2023-01 49_ATA24_Lv2&3_CAT B2_P_NOV20.pdf A400M Training Manual Released in November 15, 2020 TRAINING USE ONLY Training Use Only Electrical Generation SubSystem - Description & Operations Component Location 148 / 490 This document shall be used in accordance with the provisions described on the front page. NTCSS Release 2023-01 49_ATA24_Lv2&3_CAT B2_P_NOV20.pdf A400M Training Manual 2.5.4 Electrical Generation SubSystem - Description & Operations Detailed Description Detailed Description Components Description BCRU Description (I) The BCRU has the following external parts: - Air collector which is connected to suction airflow for heat dissipation - AC power connector - Commands/signals connector - Positive and negative DC outputs - Air intake. In the particular case of the Essential BCRU, a dust filter was installed in the air intake, in the lower part. This filter has been suppressed after a design modification. Released in November 15, 2020 TRAINING USE ONLY Training Use Only 149 / 490 This document shall be used in accordance with the provisions described on the front page. NTCSS Release 2023-01 49_ATA24_Lv2&3_CAT B2_P_NOV20.pdf A400M Training Manual Released in November 15, 2020 TRAINING USE ONLY Training Use Only Electrical Generation SubSystem - Description & Operations Detailed Description 150 / 490 This document shall be used in accordance with the provisions described on the front page. NTCSS Release 2023-01 49_ATA24_Lv2&3_CAT B2_P_NOV20.pdf A400M Training Manual Electrical Generation SubSystem - Description & Operations Detailed Description BCRU Description (II) The BCRU has three modules: - The AC/DC converter. This module converts the three-phase 115 VAC power input into DC power - The DC/DC converter which receives the internal DC power and provides the DC power output. The output voltage is regulated from 28 VDC to 32 VDC - The Battery Management Unit (BMU). This module receives control and monitoring information in order to: o Control the converter for managing the charge of the battery o Transmit commands to the network contactors o Send data to other systems. The maximum output current of the BCRU is 350 A. Released in November 15, 2020 TRAINING USE ONLY Training Use Only 151 / 490 This document shall be used in accordance with the provisions described on the front page. NTCSS Release 2023-01 49_ATA24_Lv2&3_CAT B2_P_NOV20.pdf A400M Training Manual Released in November 15, 2020 TRAINING USE ONLY Training Use Only Electrical Generation SubSystem - Description & Operations Detailed Description 152 / 490 This document shall be used in accordance with the provisions described on the front page. NTCSS Release 2023-01 49_ATA24_Lv2&3_CAT B2_P_NOV20.pdf A400M Training Manual Electrical Generation SubSystem - Description & Operations Detailed Description TRU Description The TRU has the following external parts: - Air outlet which is connected to suction airflow for heat dissipation - Positive and negative DC outputs - AC power input connector - Commands/signals connector - Air inlet. The TRU has two internal modules: - The AC/DC converter. This module converts the three-phase 115 VAC power input into the non-regulated 28 VDC power output - The control board which receives control and monitoring information in order to: o Transmit commands to the network contactors o Send data to other systems. The maximum output current of the TRU is 300 A. Released in November 15, 2020 TRAINING USE ONLY Training Use Only 153 / 490 This document shall be used in accordance with the provisions described on the front page. NTCSS Release 2023-01 49_ATA24_Lv2&3_CAT B2_P_NOV20.pdf A400M Training Manual Released in November 15, 2020 TRAINING USE ONLY Training Use Only Electrical Generation SubSystem - Description & Operations Detailed Description 154 / 490 This document shall be used in accordance with the provisions described on the front page. NTCSS Release 2023-01 49_ATA24_Lv2&3_CAT B2_P_NOV20.pdf A400M Training Manual Electrical Generation SubSystem - Description & Operations Detailed Description Architecture DC Generation Architecture - BCRU 1 (BCRU 2 similar) The AC/DC converter of the BCRU receives three-phase 115 VAC electrical power from the AC bus. The DC/DC converter of the BCRU provides: - The 28 VDC power output for the PEPDC - The internal power supply for the BMU. The BMU receives the following signals: - The reset command from the TR reset button - The OFF (or ON) command from the battery pushbutton-switch - The Point Of Regulation (POR) voltage measured in the PEPDC - The statuses (close/open) of the line contactor (BLC) and battery contactor (BATC) - The battery data (voltage, current and temperature) that are used to monitor the status of the battery. In normal conditions, the BMU provides commands to close the line contactor and the battery contactor. Then the BCRU supplies the DC bus, and the battery is connected to the DC bus. The BMU regulates the DC/DC converter output voltage according to: - The POR voltage measurement - A voltage reference that is calculated from the battery data and a battery charging law. If the BMU detects abnormal conditions, the following discrete signals can be provided: - Battery failure which illuminates the FAULT light of the battery pushbutton-switch - BCRU overload to the ENMF which can command load shedding actions and inhibit network reconfigurations - BCRU fault to the ENMF which performs network reconfigurations. If there is a failure, the BMU will open the contactors. If the internal power supply for the BMU is not available, as backup, the battery Hot Bus can supply the BMU through a relay that is closed if: - The battery pushbutton-switch is ON, or - The “Refuel on Battery” mode is active (refer to “Distribution Network - Detailed Description”). Released in November 15, 2020 TRAINING USE ONLY Training Use Only 155 / 490 This document shall be used in accordance with the provisions described on the front page. NTCSS Release 2023-01 49_ATA24_Lv2&3_CAT B2_P_NOV20.pdf A400M Training Manual Released in November 15, 2020 TRAINING USE ONLY Training Use Only Electrical Generation SubSystem - Description & Operations Detailed Description 156 / 490 This document shall be used in accordance with the provisions described on the front page. NTCSS Release 2023-01 49_ATA24_Lv2&3_CAT B2_P_NOV20.pdf A400M Training Manual Electrical Generation SubSystem - Description & Operations Detailed Description DC Generation Architecture – BCRU ESS The AC/DC converter of the Essential BCRU receives three-phase 115 VAC electrical power from the AC essential bus. The DC/DC converter of the Essential BCRU provides: - The 28 VDC power output for the EEPDC - The internal power supply for the BMU. The Essential BCRU input/output signals architecture is similar to the BCRU 1 signals architecture (already explained). In addition: - The battery contactor (BATC ESS) can be commanded either by the BMU or by the relays logics of the EEPDC - The BMU receives the Electrical Emergency Configuration (EEC) from the relays logics. The EEC signal is used to inhibit all the protection functions and to enable the backup power supply from the battery hot bus - The BMU sends to the relays logics the battery “fault” and low “State of Charge (SOC)” signals. They will disconnect the battery contactor. Released in November 15, 2020 TRAINING USE ONLY Training Use Only 157 / 490 This document shall be used in accordance with the provisions described on the front page. NTCSS Release 2023-01 49_ATA24_Lv2&3_CAT B2_P_NOV20.pdf A400M Training Manual Released in November 15, 2020 TRAINING USE ONLY Training Use Only Electrical Generation SubSystem - Description & Operations Detailed Description 158 / 490 This document shall be used in accordance with the provisions described on the front page. NTCSS Release 2023-01 49_ATA24_Lv2&3_CAT B2_P_NOV20.pdf A400M Training Manual Electrical Generation SubSystem - Description & Operations Detailed Description DC Generation Architecture - TRU TRU AS SUPPLY OF DC APU BUS The AC/DC converter of the TRU receives three-phase 115 VAC electrical power from the AC bus 4. The AC/DC converter of the TRU provides: - The 28 VDC power output for the PEPDC - The internal power supply for the control board. The control board receives the following signals from PEPDC 2: - The Point Of Regulation (POR) voltage - The statuses (close/open) of the four contactors. In normal conditions, the control board provides a command to the ENMF which closes the TRLC contactor. Then the TRU supplies the DC APU bus. The control board also receives the APU “Start in Progress” signal from the Electronic Control Box (ECB). TRU AS BACKUP OF BCRU 2 In case of BCRU 2 failure, the TRU is used as backup to supply DC bus 2 and to control battery 2. In this case, the control board, through ENMF, closes the TRLC BKUP contactor. Then the control board: - Uses the OFF (or ON) command from the battery pushbutton-switch - Closes the BATC 2 contactor to connect battery 2 to DC bus 2 - Uses the battery data (voltage, current and temperature) to monitor the status of battery 2 - Provides the battery failure signal which illuminates the FAULT light. TRU ABNORMAL CONDITIONS If the control board detects abnormal conditions, the following discrete signals can be provided: - TRU overload to the ENMF which inhibits network reconfigurations - TRU fault to the ENMF which performs network reconfigurations. If there is a failure, the control board will open the contactors. A reset command can be received from the TR APU reset button. If the normal power supply for the control board is not available, as backup, battery Hot Bus 2 can supply the control board through a relay that is closed if: - The battery 2 pushbutton-switch is ON, or - The “Refuel on Battery” mode is active (refer to “Distribution Network - Detailed Description”). TRU AS CONTROL OF APU BATTERY STARTING If the AC network is not available (AC bus 4 not supplied): Released in November 15, 2020 TRAINING USE ONLY Training Use Only 159 / 490 This document shall be used in accordance with the provisions described on the front page. NTCSS Release 2023-01 49_ATA24_Lv2&3_CAT B2_P_NOV20.pdf A400M Training Manual Electrical Generation SubSystem - Description & Operations Detailed Description - The AC/DC converter is not supplied - The control board is supplied by the hot bus. In these conditions, when an APU battery starting is performed, the control board: - Receives the “Start in Progress” signal - Opens the BATC 2 contactor to disconnect the battery from DC bus 2 - Closes the BAC through the ENMF. Then battery 2 supplies the DC APU bus. Released in November 15, 2020 TRAINING USE ONLY Training Use Only 160 / 490 This document shall be used in accordance with the provisions described on the front page. NTCSS Release 2023-01 49_ATA24_Lv2&3_CAT B2_P_NOV20.pdf A400M Training Manual Released in November 15, 2020 TRAINING USE ONLY Training Use Only Electrical Generation SubSystem - Description & Operations Detailed Description 161 / 490 This document shall be used in accordance with the provisions described on the front page. NTCSS Release 2023-01