Classification of Yarns PDF
Document Details
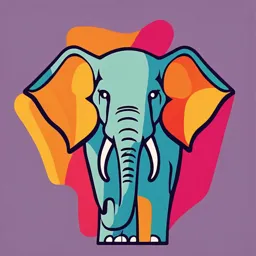
Uploaded by DeadOnLyre
University of Mauritius
Tags
Summary
This document provides a comprehensive overview of yarn classification, covering various types, processes, and applications. It details simple, novelty, textured, stretch, and bulk yarns. The document also explains compound or core-sheath yarns.
Full Transcript
Classification of Yarns Yarns may be classified according to ‘PROCESSES’ COTTON YARNS WOOL YARNS Yarns may also be classified according to ‘Types’ STRETCH YARNS There is also Compound or Core-Sheath Yarn SIMPLE YARNS: Single...
Classification of Yarns Yarns may be classified according to ‘PROCESSES’ COTTON YARNS WOOL YARNS Yarns may also be classified according to ‘Types’ STRETCH YARNS There is also Compound or Core-Sheath Yarn SIMPLE YARNS: Single, multiple, plied/folded, cable YARNS Spun or Filament yarn SingleYarn Two or more single yarns with no twisting Multiple Wound Yarn Two or more single yarns with twisting Folded or Plied Yarn Two or more folded yarns with twisting Cord ROPES/CABLES Use of multiple wound yarn, esp as weft yarn in specific weave for shirting fabric Oxford weave: using double yarn with no twisting operation Once the raw material has been spun into yarn, it could be used right away to weave them into fabrics. In this case, the fabric would be a “single-ply” fabric. For improved fabric quality such as drape and softness, two yarns are twisted into a folded or plied yarn. The resultant yarn is called a ‘two-ply’ yarn. If we use a ‘two-ply’ spun yarn for the warp as well for the weft, we would have a “two ply” 2×2 fabric. Sometimes the term “two ply” is used for fabrics that have only one yarn (either the warp or the weft) that is ‘two- ply’ whereas the other yarn is not. This is just a “two-ply” 2 x 1 fabric. Two-ply fabrics are generally superior to single-ply fabrics. Why use folded/plied yarns? Fabrics made of folded or plied yarns give softer feel and ‘silkier’ handle because of lower bending rigidity of the folded yarn. The drape of the fabric is better too. For formal shirting, the fabric is less prone to wrinkling. For sewing threads, the folded yarns can be made stronger as weaker spots are reinforced. Shirting Fabrics NOVELTY or FANCY YARNS STRETCH YARNS Novelty yarn = Base yarn + effect strand + binder yarn https://www.slideshare.net/fancyyarns/fancy-yarns-final Slub Yarn Slub yarn refers to yarn that has been purposely spun with slubs (thicker sections along the yarn). While it was once seen as a defect, slub yarn is now intentionally created to give fabric a natural ‘linen’ look with special texture and visual appearance. Slub Yarns Fabric made from flake or flock yarns Knot/slub/nub/spot multicoloured yarn Fabric made from uni-coloured slub/knot yarn Marl yarns Fabric made from boucle/ loop yarn Fabrics made from marl or corkscrew yarns Fabrics made from chenille yarns Textured Yarns: Stretch & Bulk Yarns STRETCH YARNS STRETCH YARNS Texturization or Texturing Variations in texture, stretch and bulk of thermoplastic yarns (SYNTHETICS) can be done by application of heat by a process called texturization or crimping. “Texturization is the process by which filaments are distorted to impart crimp, curl, coil and loop structures along their length to achieve mainly bulk and stretch.” In texturization process, untextured yarns are heated to plastic condition after it is distorted by texturing element (spindle, gear, knife etc.). Then they are cooled to retain the required shape. Texturization processes are used to produce Stretch and Bulk Yarns. Bulk Yarns Stretch Yarns Texturizing processes were originally applied to synthetic fibres to reduce such characteristics as gloss, transparency, and slipperiness. Texturizing processes make yarns more opaque, change appearance and texture, and increase warmth and absorbency. Textured yarns are synthetic continuous filaments, modified to impart special texture and appearance. www.britannica.com/topic/textile/Types-of-yarn#ref359366 Stretch Yarns The two main types of stretch yarns are: (i) Heat-set thermoplastic, and (ii) Elastomeric. Heat-set Thermoplastic: Stretch yarns may be produced by texturization of thermoplastic yarns. The stretch textured yarns may be produced by different methods such as false twist and edge crimping method. The resultant yarn has 300 to 500 percent elongation. They are used in swimsuits, lingerie, stockings, one-sized garments where a form-fitting resilience without pressure is required. Elastomeric Stretch Yarns Elastomeric stretch yarns: Stretch yarns may be produced by the use of elastomeric materials such as Lycra (tradename), elastane or spandex. The stretch yarns may be produced by different methods such as core spinning to produce core-spun yarn. The core is an elastomeric polymer and the sheath may be staple fibres or filament yarn. Elastomeric stretch yarns are NOT produced by texturization process Bulk Yarn Bulk Yarn: Mainly Gear crimping, Stuffer box and Air Jet methods are used to produce these yarns of increased bulk but minimum stretch. These processes can increase bulk from 100 to 300 percent. They are used as carpet yarns and in sweater fabrics. The resultant fabrics are usually soft with some degree of bulk and warmth but are light in weight. Compound or Core-sheath YARNS A compound yarn typically consists of two or more different fibre strands in a core–wrap structure with the idea being to get a net effect combining the characteristics of the core and the cover/wrap/sheath components. Examples of a compound yarns are: covered-spun and core-spun yarns. Many core–wrap yarns consist of core filament(s) wrapped or covered by a yarn. These may be categorized as covered- spun compound yarns. The wrap can be a spun or filament yarn. They are produced by wrap spinning Different combinations of core-spun yarns: filament core/staple-fiber wrap , staple-fiber core/filament wrap and staple-fibre core/staple-fibre wrap. The wrap may be multifilament or staple fibres. Most common spinning systems are: ring spinning, air-jet spinning and friction spinning