DM308 Part 1 Other Half Non Traditional PDF
Document Details
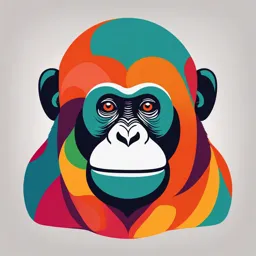
Uploaded by SafeDiscernment
University of Strathclyde
Tags
Summary
This document discusses various types of Additive Layer Manufacturing (ALM) systems, including FDM (Fused Deposition Modelling), SLS (Selective Laser Sintering/Melting), and Binder Jetting. It explores different materials, processes, and design considerations. The document provides a broad overview of the subject, covering key concepts for understanding ALM processes and technologies.
Full Transcript
Material extrusion Fused deposition modelling FDM generated cross section Filament Heated FDM Head Molten Filament Supply Scott & Lisa Crump are the inventor of fused deposition modelling (FDM) and co-founders of Stratasys, Ltd. The Crumps invented and patented FDM technology in 1989. Notice that th...
Material extrusion Fused deposition modelling FDM generated cross section Filament Heated FDM Head Molten Filament Supply Scott & Lisa Crump are the inventor of fused deposition modelling (FDM) and co-founders of Stratasys, Ltd. The Crumps invented and patented FDM technology in 1989. Notice that the FDM filament cannot cross itself, as this would cause a high spot in the given layer Synonymous with consumer “3D printing” Understanding process windows The process window for a CNC machine tool, forget the values look at the axes and the boundaries. These tell use what the key limitations of the process are. Qualitative knowledge is enough. Know the units of the quantities but NO need to know values (they vary with machines and materials) The parameter on each axis What you should know The shape of the window (e.g. square, circle, triangle etc.) What happens at the limits (i.e. boundaries) of the window and why? The parameter on each axis Process window for FDM Cooling too slow The relationship between air and nozzle temperature is the key parameter too hot or too cold and bad things happen Cooling too fast Fused deposition modelling Two colours of “almost” Molten Plastic extruded through a nozzle New materials for FDM LAYWOO-D3 is a wood-based 3D printing filament invented by Kai Parthy and is designed for the FDM and similar machines. It is a wood/polymer composite - the filament contains 40% recycled wood and harmless binding polymers. The material has similar thermal durability as PLA and can be printed between 175°C and 250°C. Thermal transitions in polymers Too cold and the filament will not soften enough, too hot and it will run through the nozzle. There are three main states in which a polymer can exist and therefore there are two types of typical transitions the polymer can go through. In the Glassy state, the plastic is brittle; in the Rubbery or Viscoelastic state, the plastic is soft and/or tough and in the Melt state the plastic is molten. The transition temperature at which the polymer changes from brittle to soft/tough is called the Glass Transition Temperature (Tg). The transition temperature at which the polymer changes from soft/tough to a melt is called the Melt Temperature or Tm. Amorphous polymers do not show a clear transition into the melt and therefore do not exhibit a Tm. The change is gradual and the polymer softens with increasing temperature. Therefore, in injection molding, amorphous materials (ABS) have a wide melt processing window compared to crystalline materials (Nylons). Sheet lamination Sheet lamination Paper bulk additive layer http://www.mcortechnologies.com/ Powder bed fusion SLS: Selective laser sintering/melting Layer deposition Heating by scanning laser beam Commercially, SLS is very significant SLS: Selective laser sintering/melting Selective Laser Melting 3d geometry model Application of a Powder layer of powder material is material solidified into a crosssection of the model Building platform is lowered The next layer of powdered material is applied The process repeats itself until the part is complete Completed Loose powder is part removed Selective Laser Melting Process Window Energy put into the powder will depend on beam diameter and speed. Slow cooling -> harder metal ss ne d r Ha ed uc d e r De nsi ty r Not enough energy to fully melt the powder ed uc ed Su rfa ce fin ish d or Po eg rad Moving so fast, less merging between layers es i on cis e pr High power, slow speed full melt, slow cooling so difficult to define the walls of small features like holes Close-up its much more complex! Video’s from papers of Prof. Andrew J. Moore Earl Mountbatten Building Institute of Photonics and Quantum Sciences School of Engineering and Physical Sciences Heriot-Watt University Edinburgh, EH14 4AS Selective Laser Sintering/Melting Design for AM example E.g. conformal cooling of injection moulds. Metal AM was an early example of designs that used “complexity for free” Conformal cooling More intricate water cooling channels can be manufactured with ALM SLM than with with subtractive manufacturing (e.g. spirals). Binder jetting A different powder based system A binder compound is deposited onto each layer of powder using similar technology to that used in paper inkjet printers. Commercial example: Z-Corporation The Z-Corp printer uses inkjet printer technology to print fine patterns of glue onto a smooth bed of plaster powder (so smooth it looks like paper). The bed is lowered, and a roller spreads a very fine layer (.004”) over it to print a new layer. Pros No support structure means that parts can be made with very complex geometries; when done simply “blow out” the powder Inkjet technology makes this a very high speed option – most builds take a few hours and the largest, most complex builds still take less than a day Color capacity for full-color models with little postprocessing Cons The plaster material yields low strength, delicate parts; thin parts are sometimes subject to minor warping Messy powders, dyes, and resins require more time to set up and clean; complex nature of the machine requires operation by specialized personnel Binder Jet Metallic ALM Metal Powder Beds Material jetting Direct energy deposition Wire arc additive manufacturing Eight Generic Categories of ALM System www.lboro.ac.uk/research/amrg/about/the7categoriesofadditivemanufacturing/ +WAAM Be aware that other taxonomies exist Taxonomy of layer formation methods Liquid Solid Powder 1 Component Selective Laser Sintering Component & Binder 3D Printing & Gluing Bulk Gluing Sheets Laminated Object Manufacturing Polymerisation Foil Polymerisation Next Week: more powder based metal systems Liquid Polymerisation Light Two frequencies Beam Interference solid Heat Thermal Polymerisation Melting & Solidification Shape Melting Fused Deposition Modeling Ballistic Particle Manufacturing Solid Base Curing One Lamps Photosolid. Layer at a Time frequency Lasers Stereolithography 2019 ALM taxonomy Next week Homework: - Watch videos on MyPlace - Visit: http://www.lboro.ac.uk/research/amrg/about/the7categoriesofadditivemanufacturing/ Next week’s topics: Some more types of metal ALM System How to comparing systems Assessment of Technical and Economic Feasibility CAD Interface